Bloomy rolls out compact battery simulator
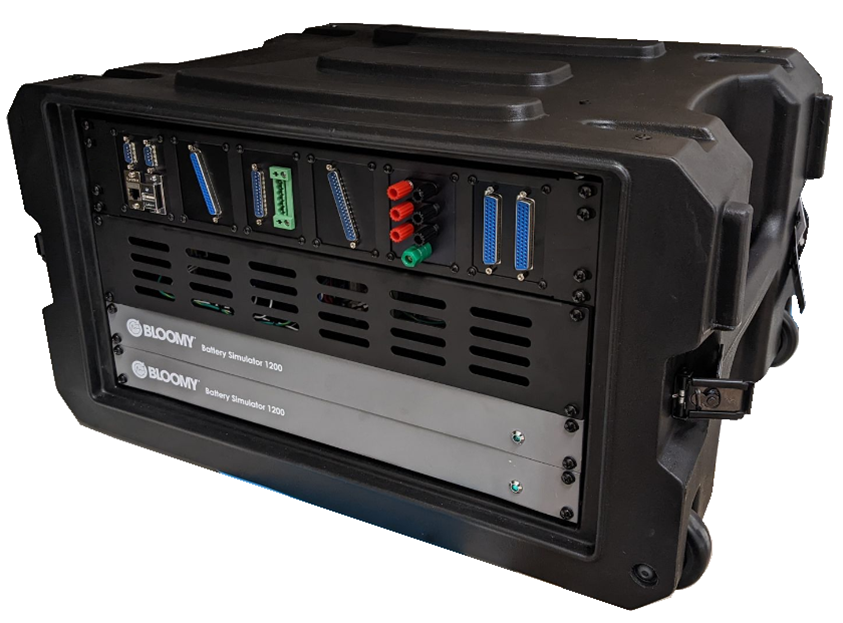
(Image courtesy of Bloomy)
Bloomy Controls has launched the Desktop BMS HIL Test System, a small, compact and transportable system for users to simulate battery cells safely for development projects.
The system increases the accessibility and convenience of hardware-in-the-loop testing, with the aim of boosting productivity and reducing the time-to-market of battery electrification development projects – ranging from EVs to uncrewed aerial vehicles (UAVs), and electric vertical takeoff and landing (eVTOL) vehicles to satellites and robots.
The system simulates 12 to 36 battery cells, temperature sensors and digital communications using real electronic signals.
In large applications, such as EVs, these signals simulate a centralised or distributed battery module to test the electronics and embedded software of any battery-sensitive system. In smaller applications, such as UAVs, light mobility vehicles or power tools, the system simulates the entire battery.
Combined with Bloomy’s Battery HIL Software Architecture, users can configure both manual and fully automated test scenarios, including simulated drive cycles and fault-case scenarios.
Testing dangerous scenarios
HIL validation testing is the de facto industry standard for control system validation testing because it maximises test coverage, including scenarios that are dangerous or impossible to test, on the actual vehicle or plant.
The Desktop BMS HIL Test System uses Bloomy’s Battery Simulator 1200. It has 12 simulated cells in a one-rack unit package that sink and source current in a similar way to a real battery. It is safe, fast and efficient.
“HIL simulator testing, once confined to the lab and requiring specific workflows and resources, is now more convenient and accessible,” Bloomy president Peter Blume.
Click here to read the latest issue of E-Mobility Engineering.
ONLINE PARTNERS
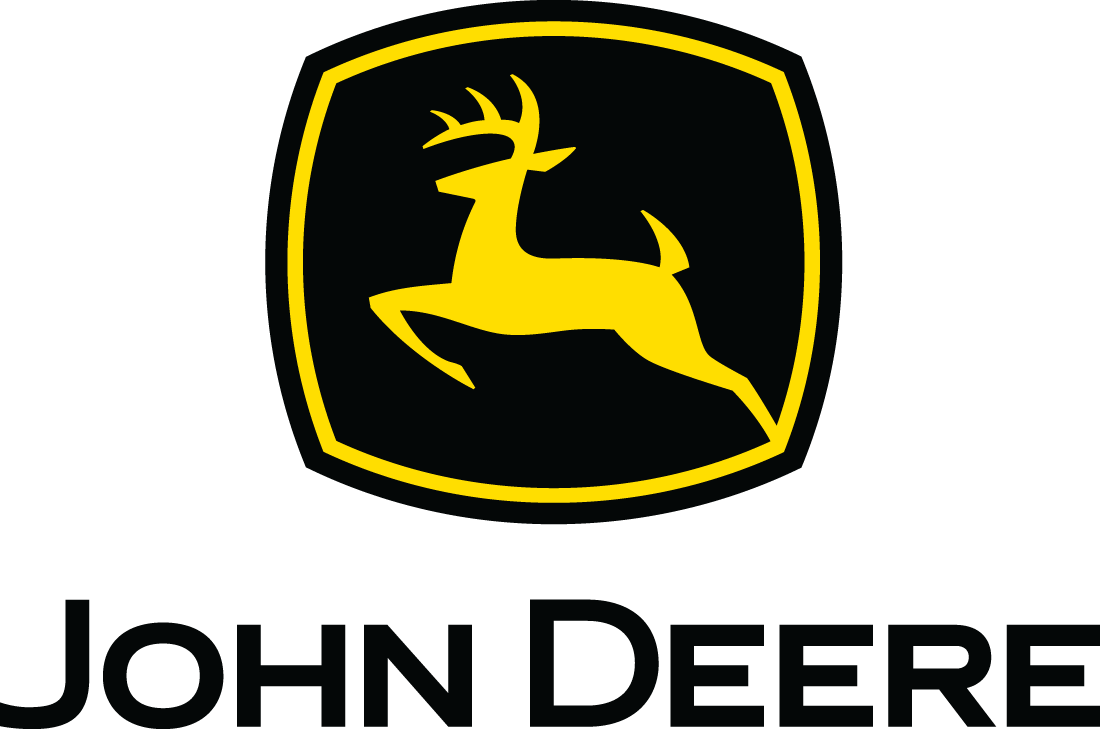
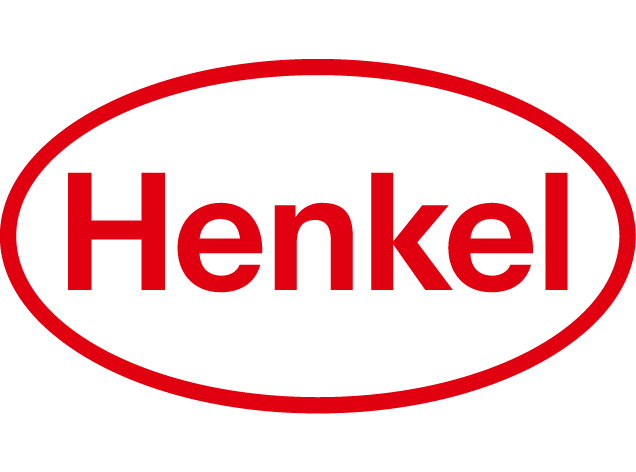
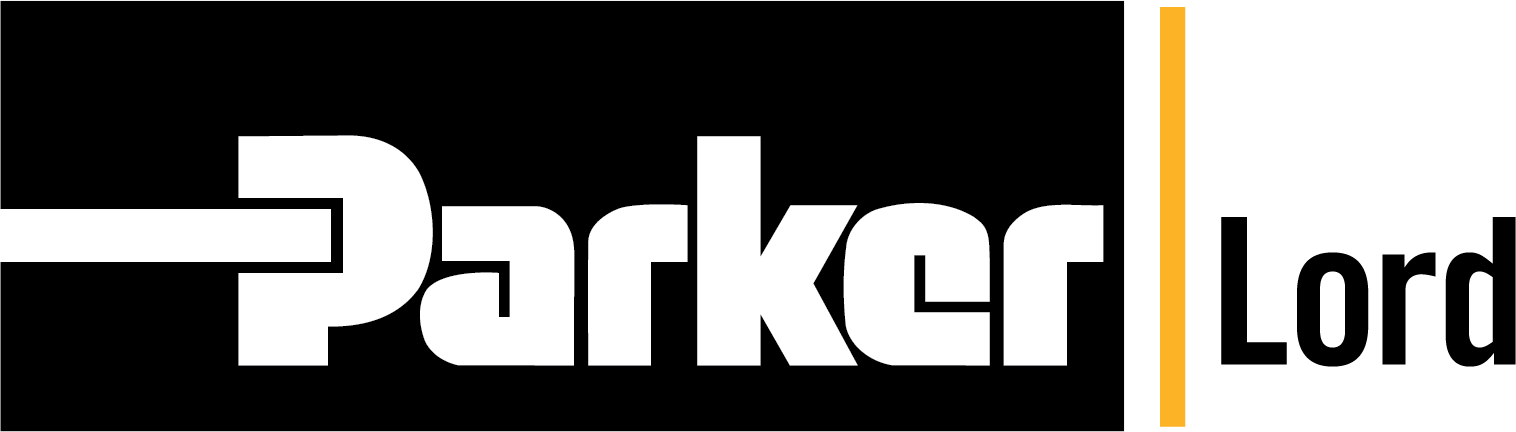
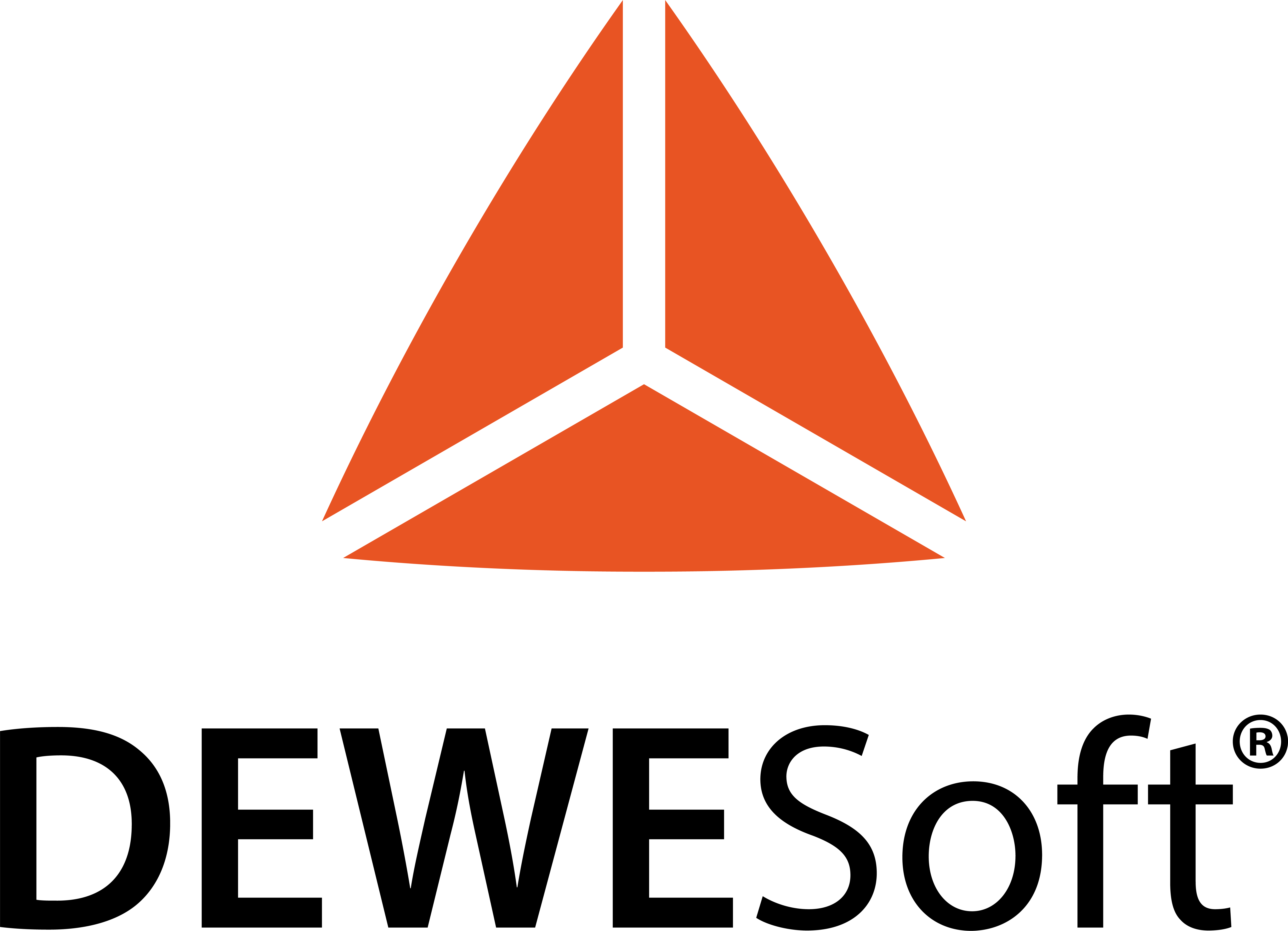
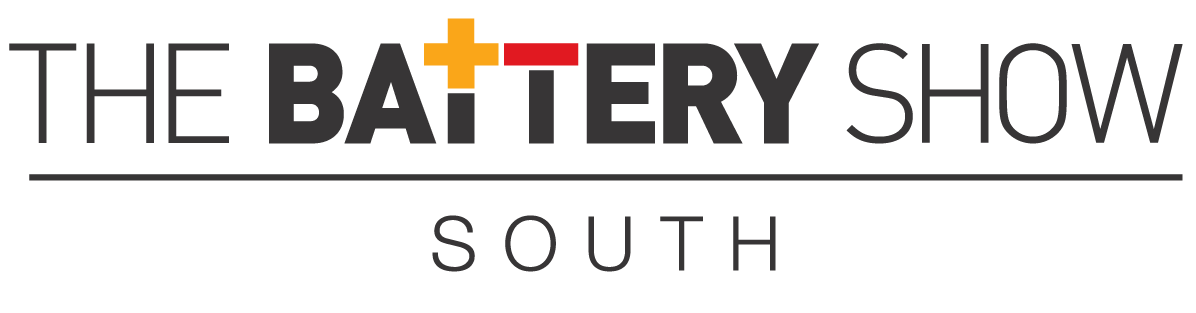
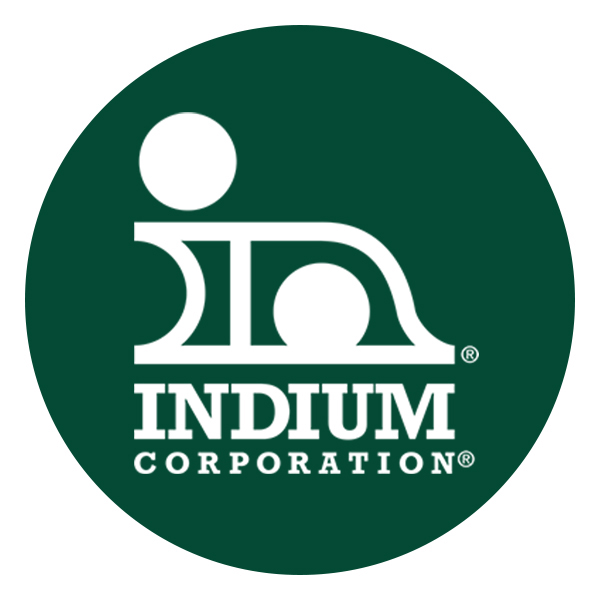
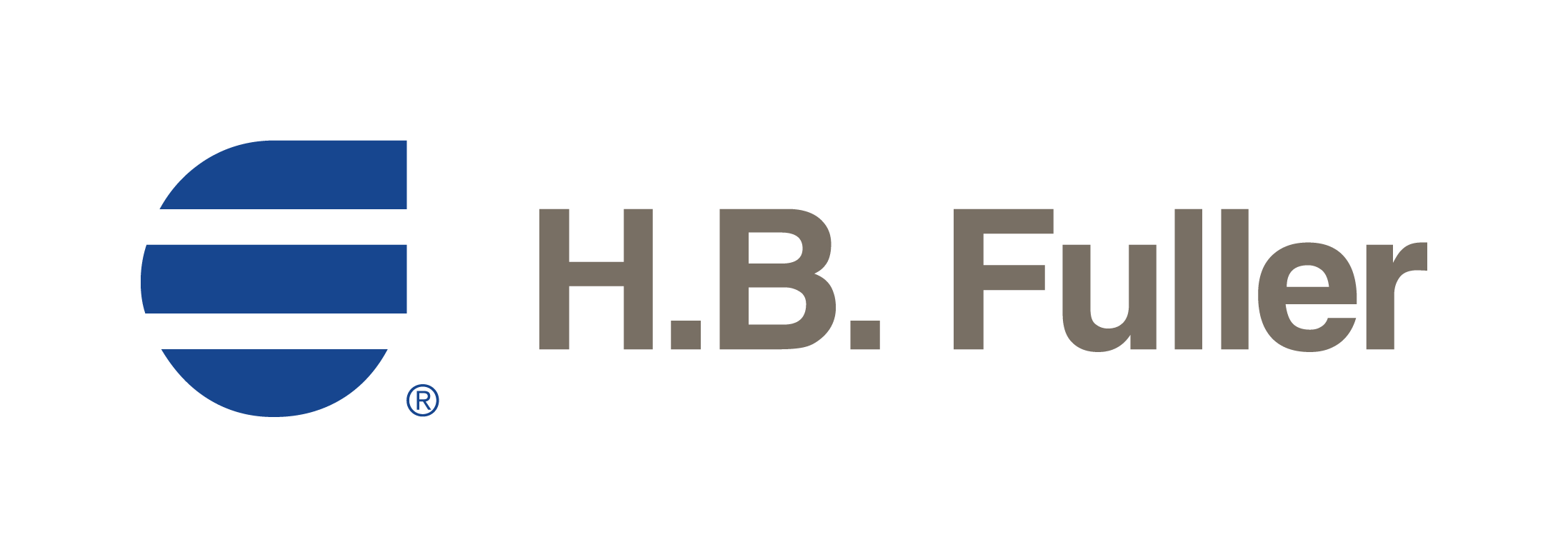