Sealing cell module controllers using the CIPG process
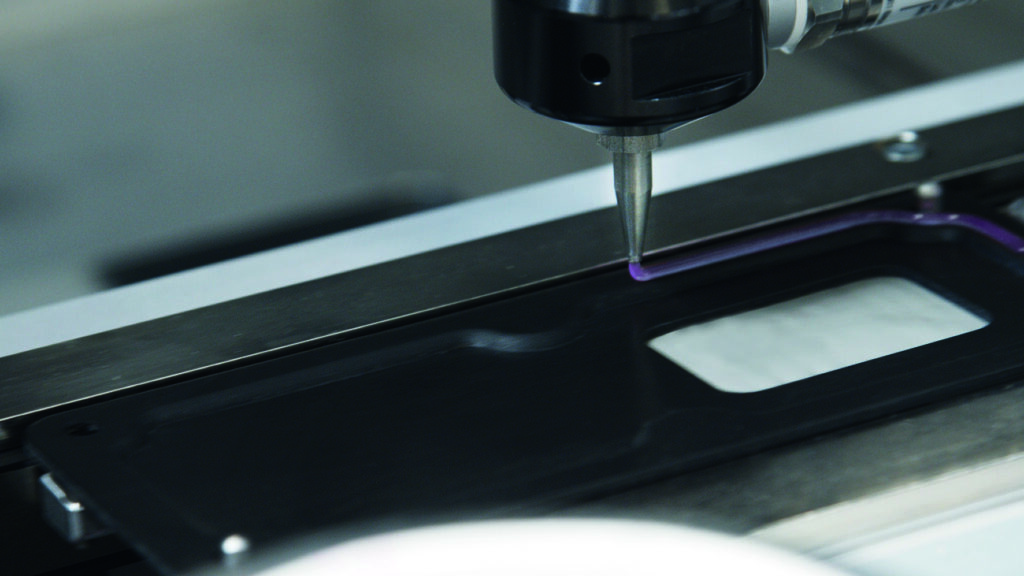
bdtronic and Hönle have teamed up to develop a solution for dispensing and curing liquid gaskets for cell module controllers using the CPIG method.
Battery sensors play a crucial role in controlling and managing the performance and safety of EV batteries, monitoring temperature to voltage. During their production, highly viscous liquid sealants are used to protect the sensitive electronic components from dust, road salt and moisture, as well as temperature-related stress, physical shock and vibrations.
These liquid sealants are typically identified as cured-in-place-gaskets (CIPG). The collaboration between bdtronic and Hönle has created an inline, five-step process for CIPG dispensing and curing.
In the first step, the component contours are pretreated with atmospheric pressure plasma to achieve better adhesion of the sealant. In the second and third steps, the highly viscous CIPG is applied in contours. In the fourth step, curing is carried out using a Hönle UV curing system. Step five involves the optical inspection of the finished part to ensure the highest level of quality and consistency.
“To achieve the best possible process, it is essential to work closely with the customer and all involved technology providers from the very beginning,” says Fabian Tremmel, head of engineering dispensing at bdtronic.
“Our decades of experience in UV curing, and our uniquely extensive portfolio of LED-UV and UV systems allow us to quickly find the optimal solution for the customer,” says Mina Kamal, sales engineer at Hönle.
The production line delivers a high-quality battery sensor seal every 13 seconds – a small but significant step on the path to e-mobility.
Click here to read the latest issue of E-Mobility Engineering.
ONLINE PARTNERS
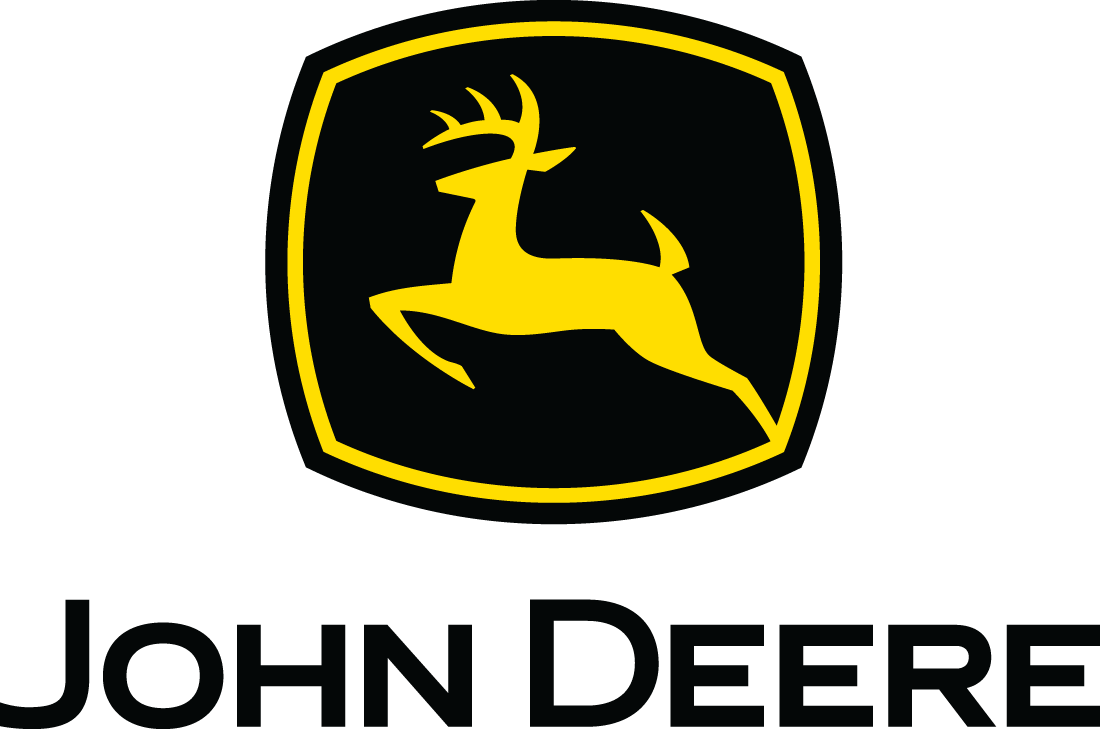
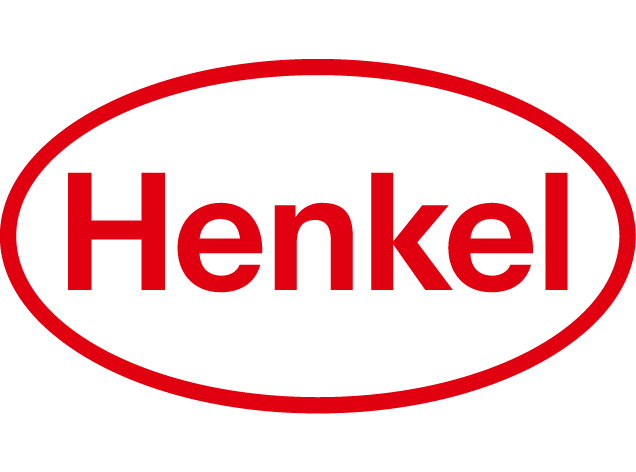
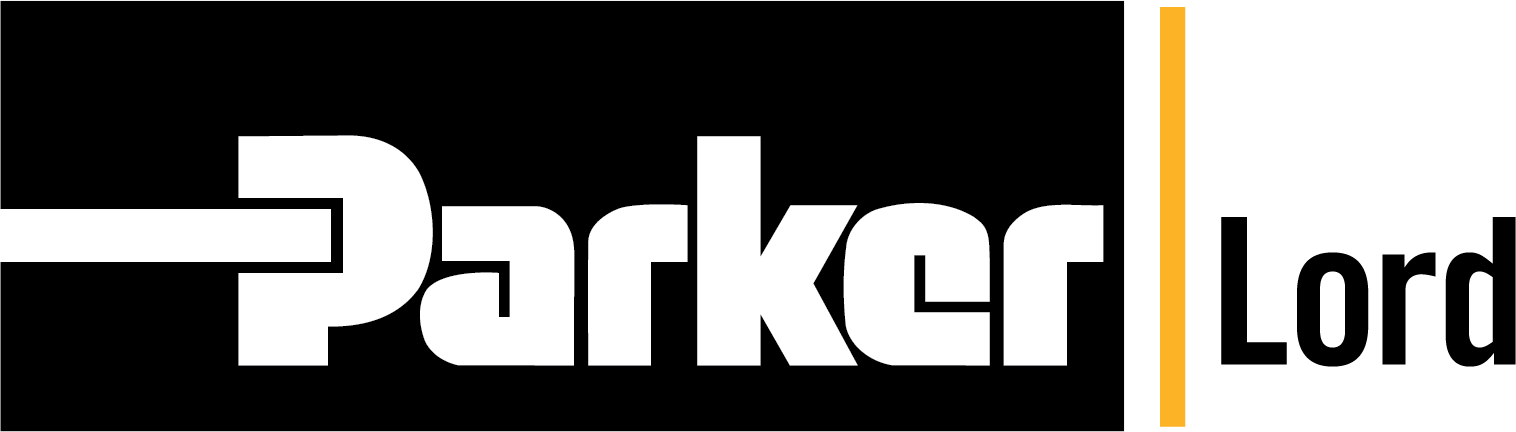
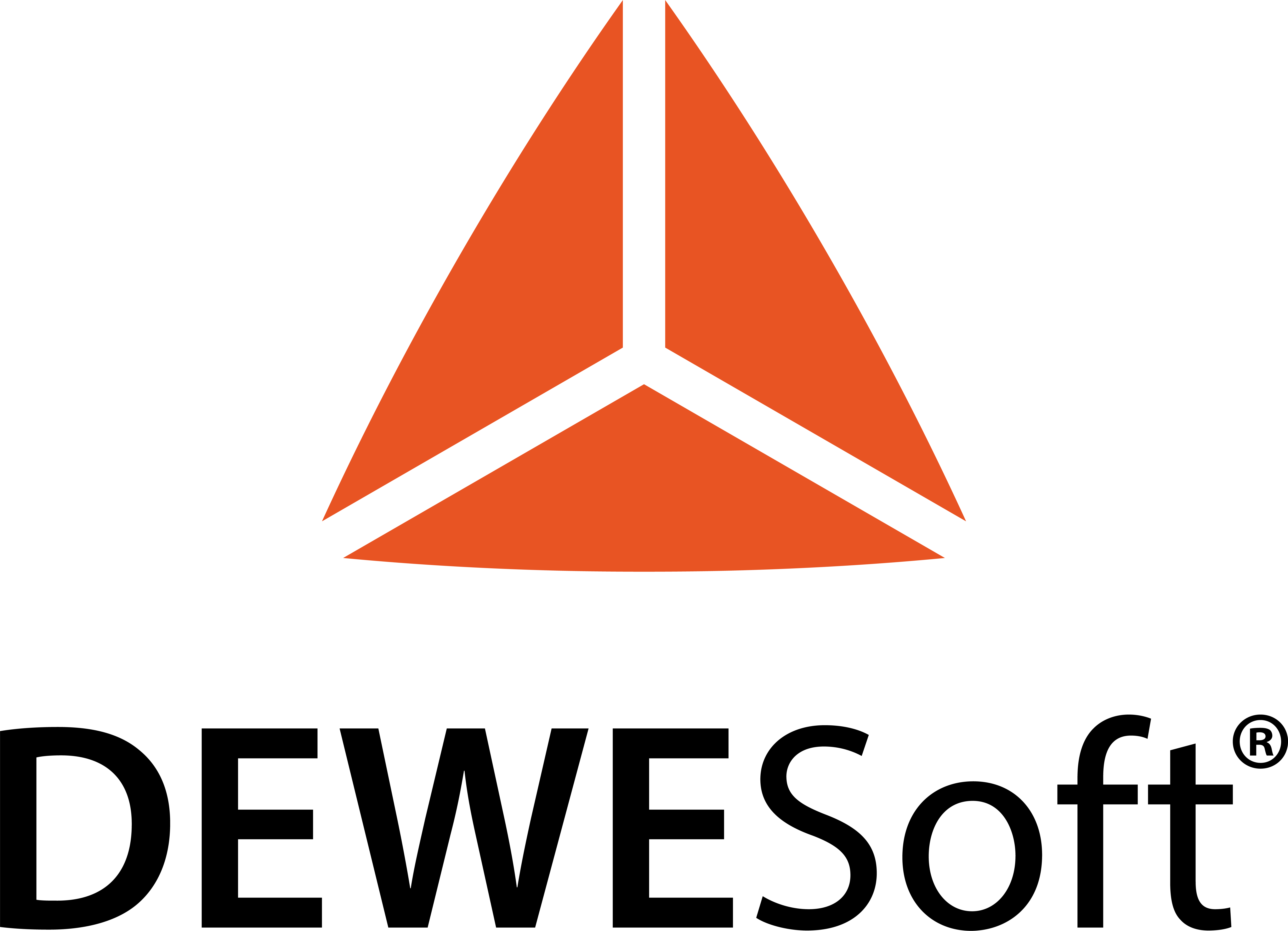
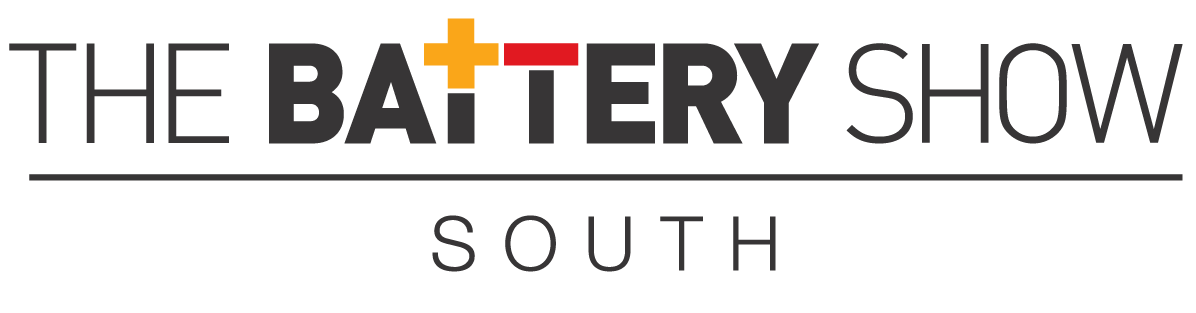
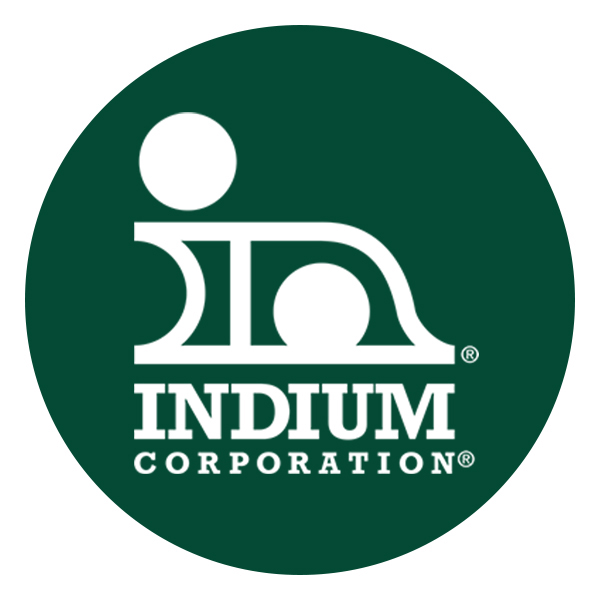
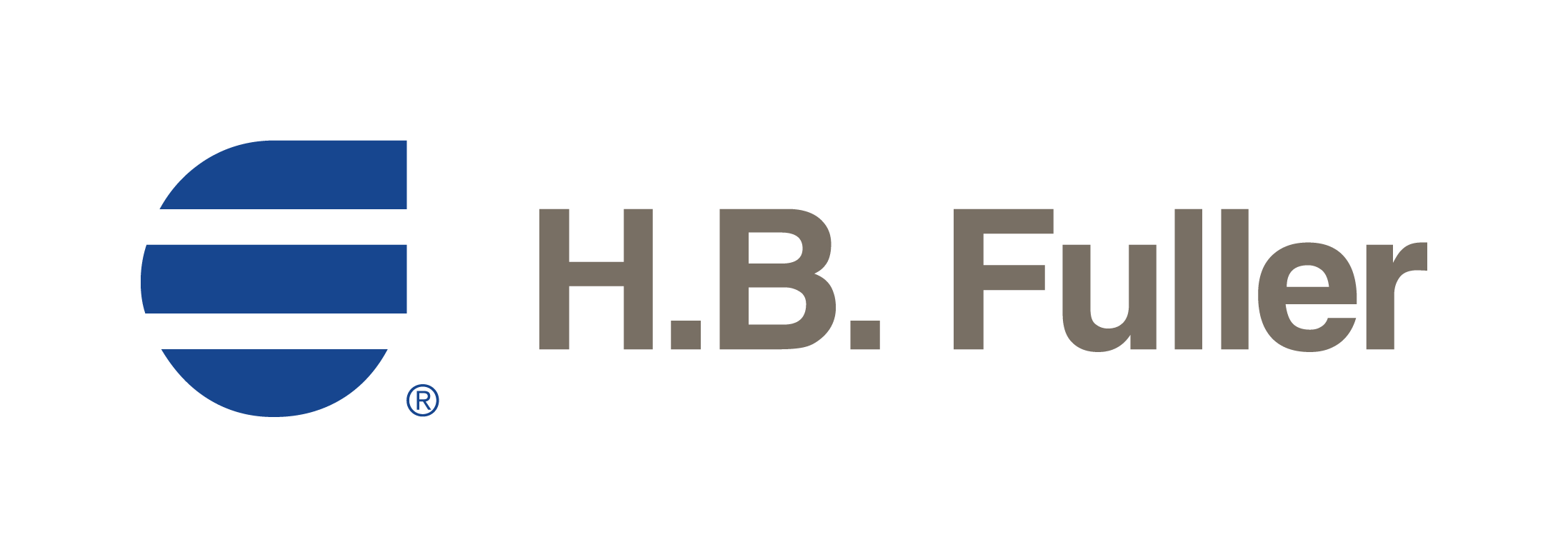