Battery vent protects against rapid rises in pressure
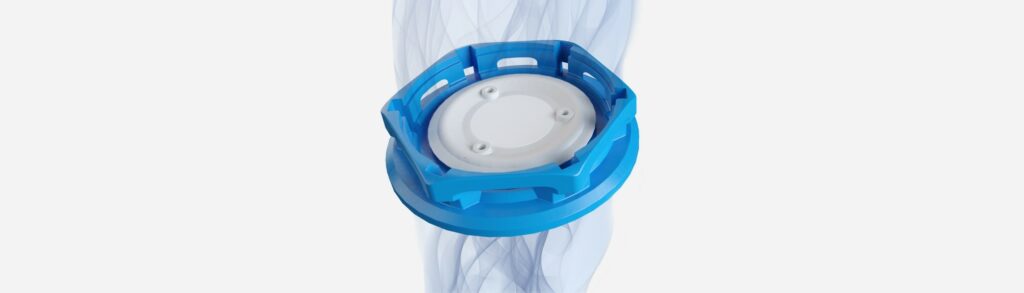
(Images courtesy of Donaldson)
As the battery pack is the single heaviest and costliest component of an EV drivetrain, weight reductions in the pack pay dividends in terms of range as well as performance and handling. One of the ways battery manufacturers are looking to reduce weight is to produce packs with thinner walls, which means that they must operate at lower internal pressures and with those pressures carefully controlled.
To meet that need, Donaldson Filtration Solutions has developed its Dual-Stage Flex battery vent that allows the pack to ‘breathe’ through an ePTFE membrane in response to normal pressure changes, maintaining a lower pressure overall. It also provides ingress protection and the ability to protect the pack from large, rapid pressure increases with a second venting stage, as Shane Campbell, product manager for integrated venting solutions, explains to Peter Donaldson (no relation).
“The pressures inside the battery pack really depend on the venting solution,” he says. “If you add more vents, select a larger vent or one with higher permeability, you will see lower pressures during normal operation.
“But in terms of maximum pack-pressure, we had several customers come to us with requirements that were lower than the burst pressure of our dual-stage burst product. That is why we designed the Dual-Stage Flex vent.”
The vent consists of an umbrella-shaped valve with a disc of the company’s Tetratex ePTFE waterproof breathable membrane in the centre. ePTFE is naturally hydrophobic, but Donaldson applies a coating that makes it also oleophobic so that it resists oils and other contaminants.
“During normal operation at low pressures the umbrella stays closed and airflow is allowed to pass in and out through the membrane, but once you hit 20 mbar of pressure inside the pack, the umbrella will open and provide a direct path for rapid degassing,” Campbell says.
He explains that the Dual-Stage Flex vent will reseal after the umbrella valve has opened. “That is something we test through pressure cycling, but if your pack does experience full thermal runaway we would not recommend reusing the product.”
The main challenge in developing the vent, he says, was finding the right performance trade-offs.
“For battery vents it’s always a balance between achieving very high degassing airflow while also offering spray protection to the internals of your battery. You could have a design that is very open – allowing high degassing airflow – but then there would not be as much spray protection, so balancing those two to find the optimal design was challenging.”
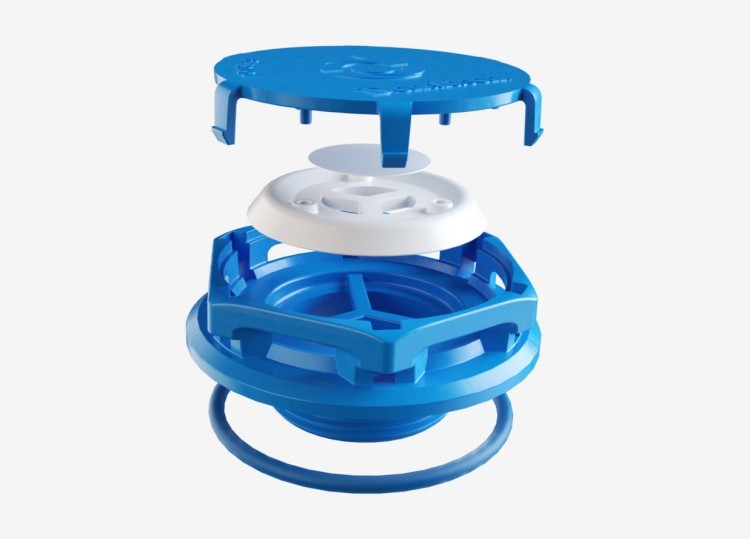
Early in the process, he says, the team used CFD tools to work out the ideal shaping for the valve’s plastic body, the umbrella valve and openings to achieve the highest airflow for a given pressure. On the ingress protection side they used testing equivalent to IP67 to gauge its performance against water spray and immersion.
Maximum allowable pack pressures are getting lower, he notes, and this is driven by the strength of the seals and the structural materials.
“If you were to exceed the yield stress of a certain material you could have uncontrolled rupture of the battery pack. Customers come to us with the maximum pressure that the pack can handle and the size of the pack, and ask us to help them select the type and number of vents.”
Dual-Stage Flex vents are integrated at pack or module level, making them compatible with any cell format, including cylindrical, prismatic and pouch, Campbell adds.
ONLINE PARTNERS
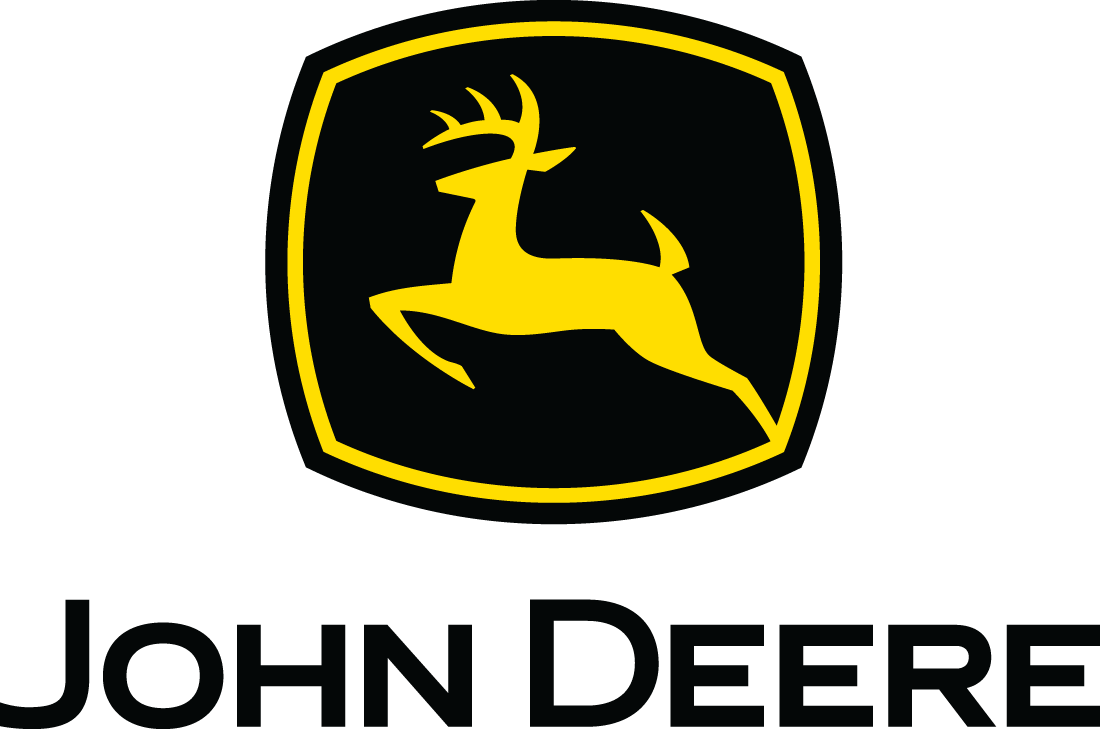
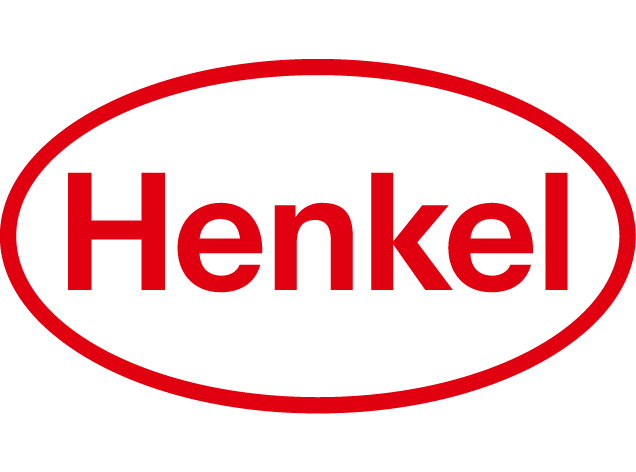
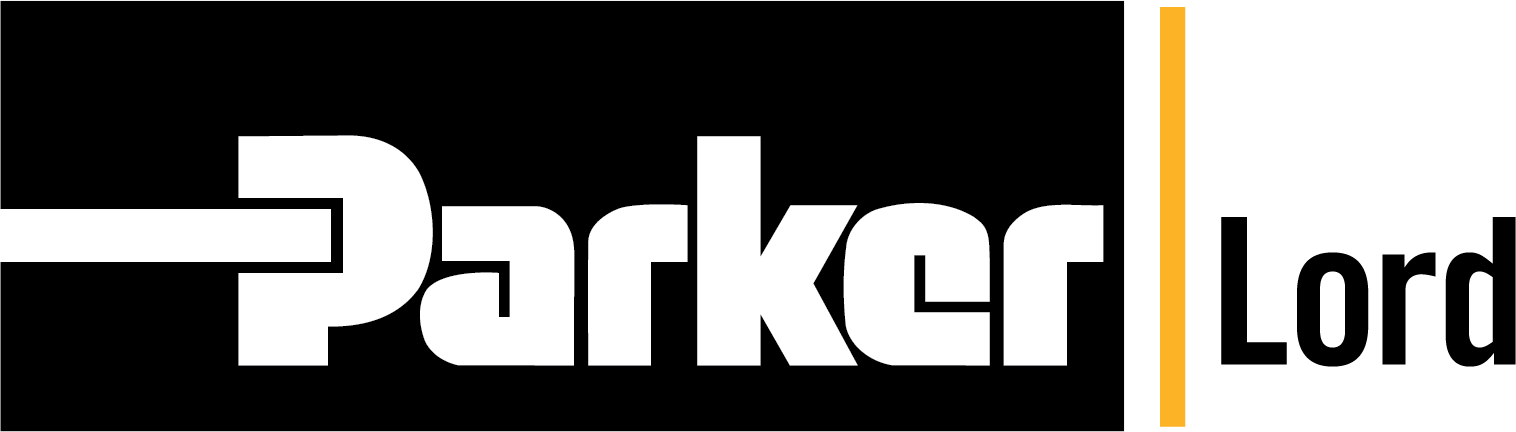
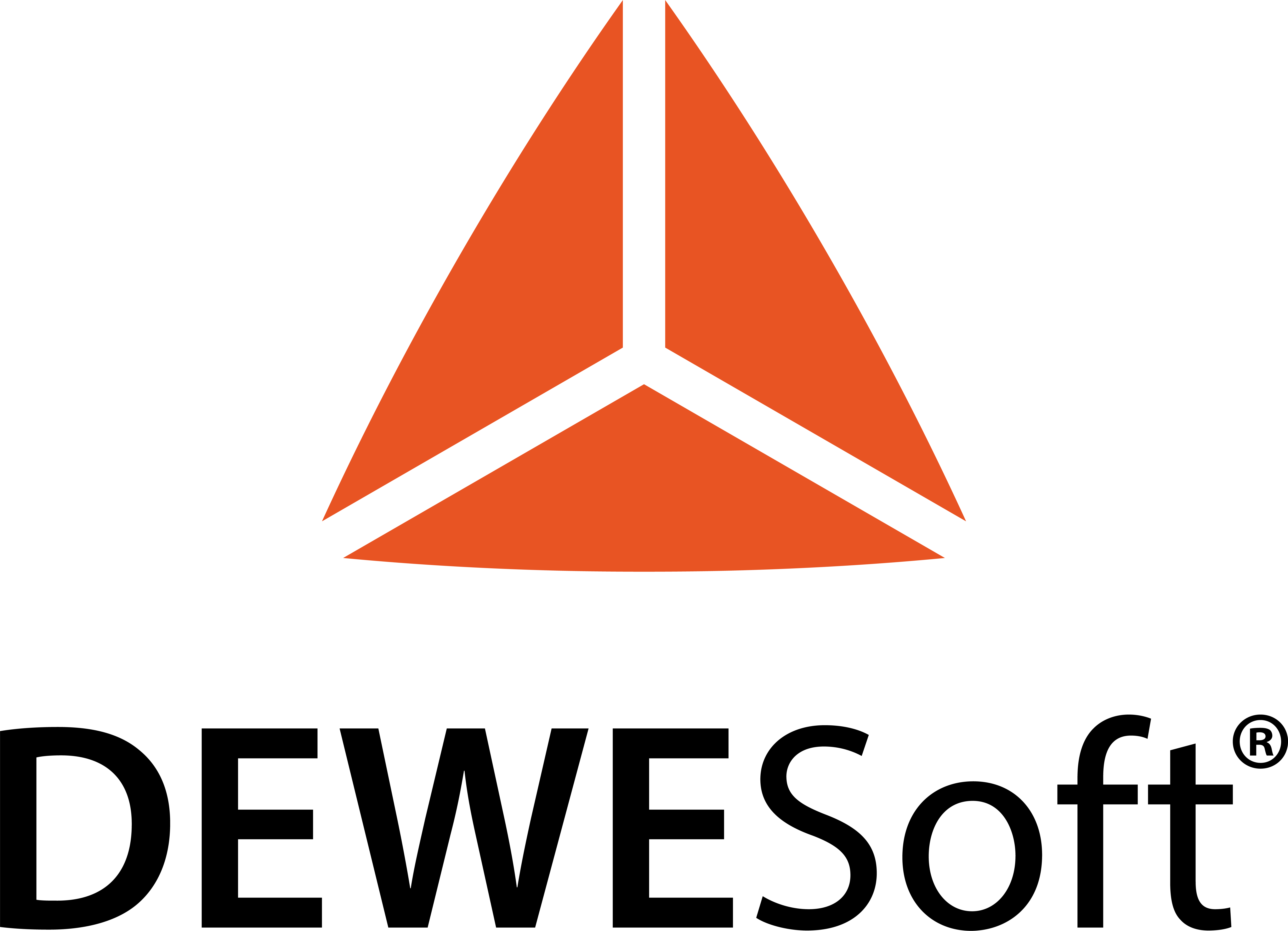
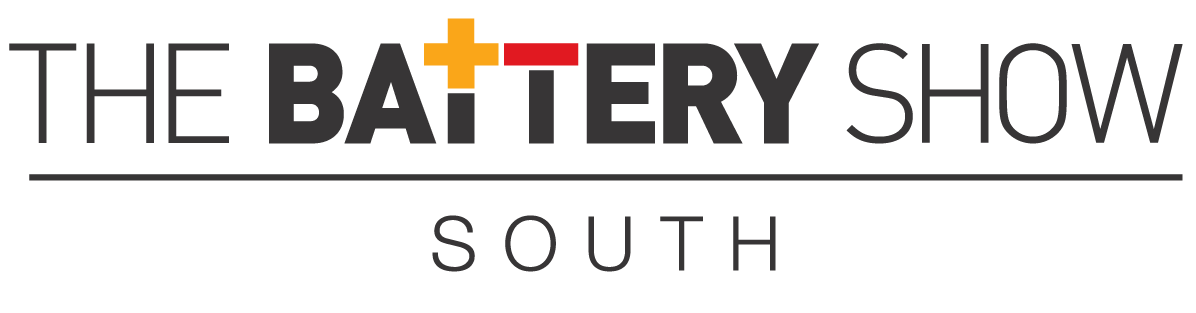
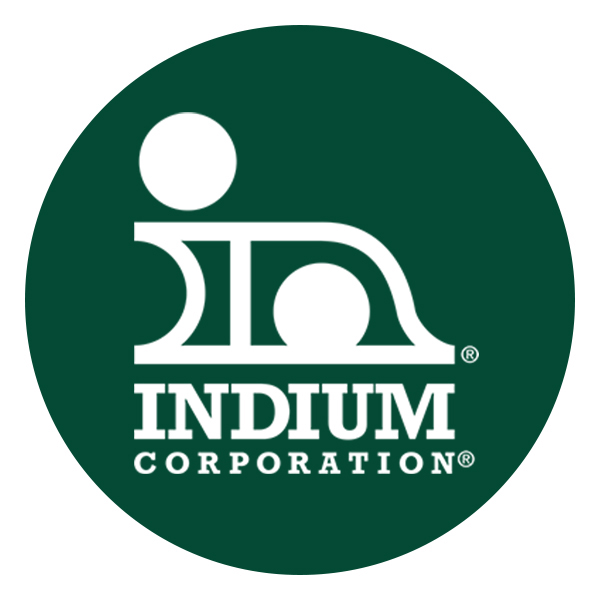

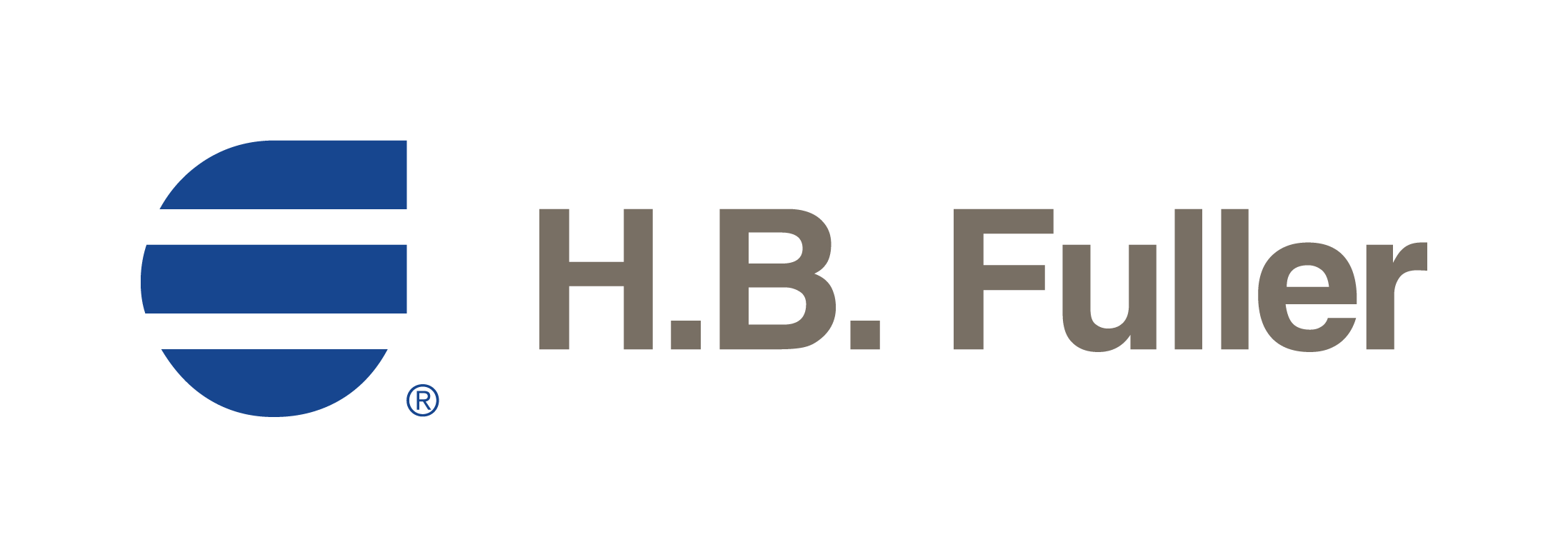
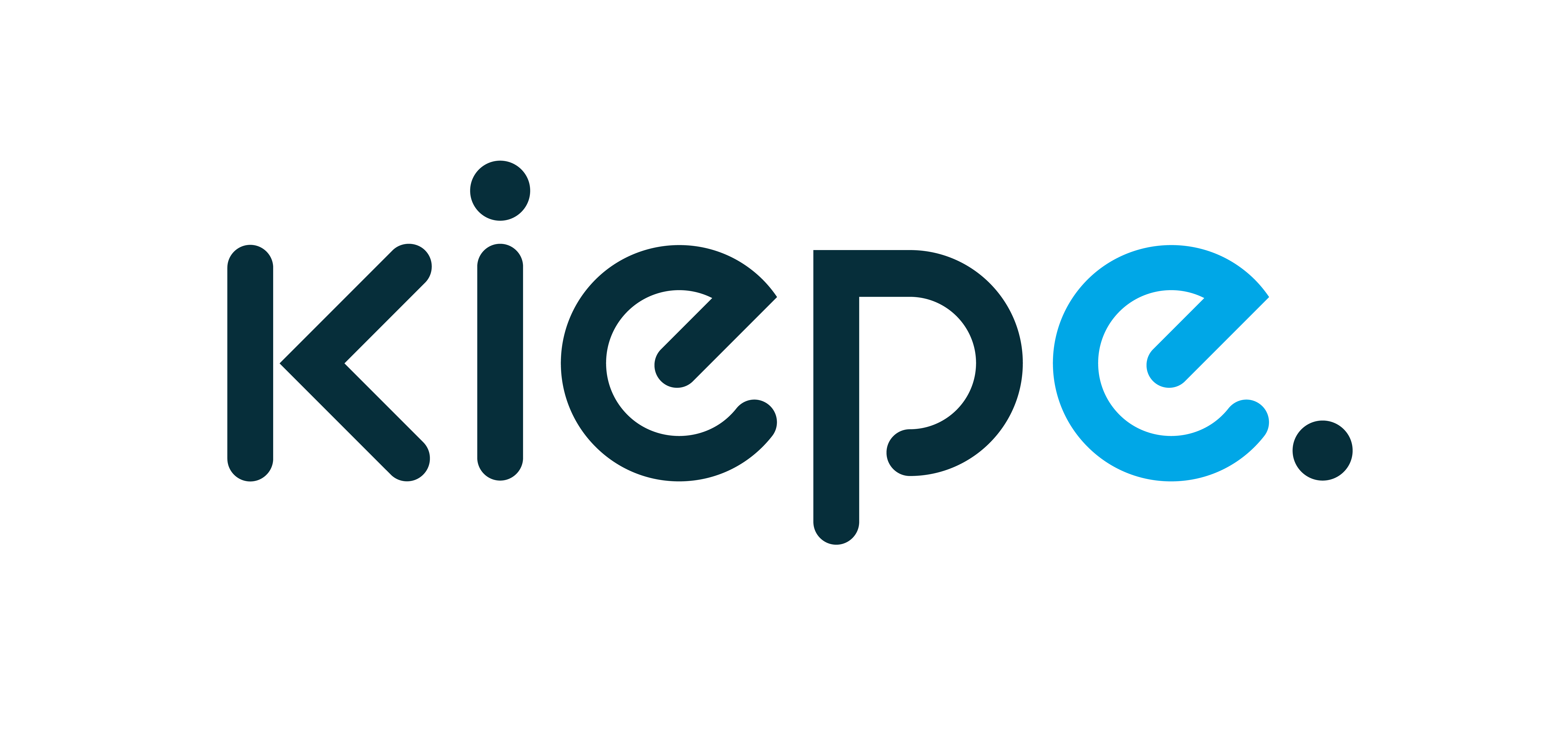
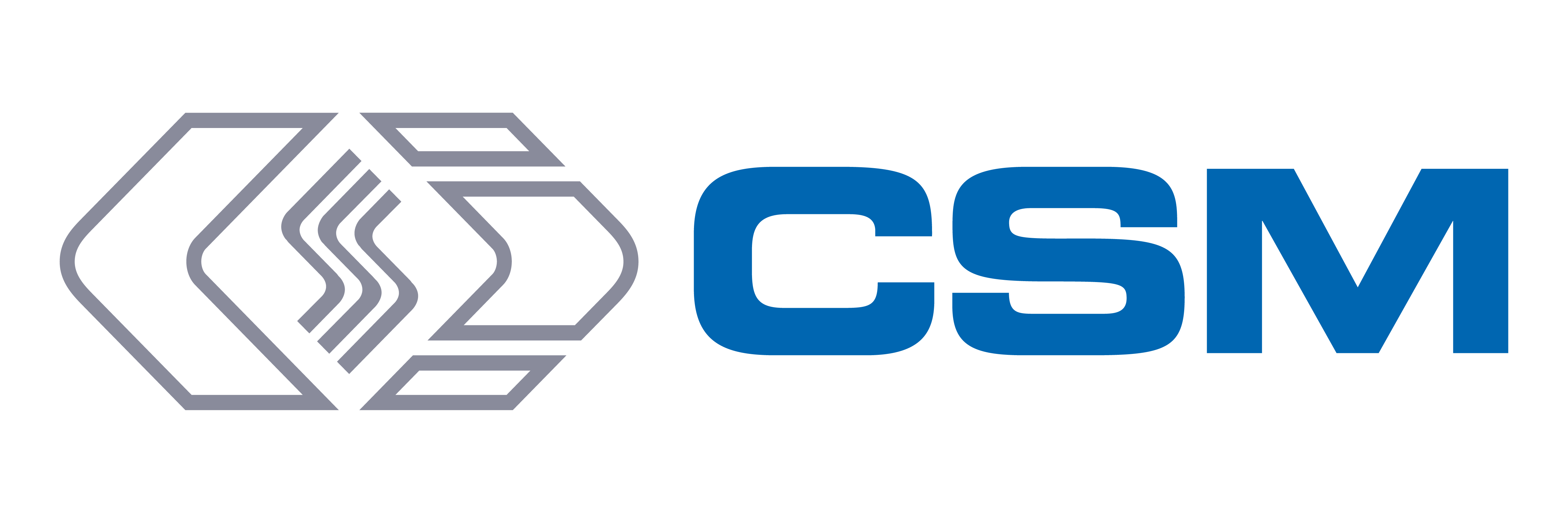