Battery surface analysis
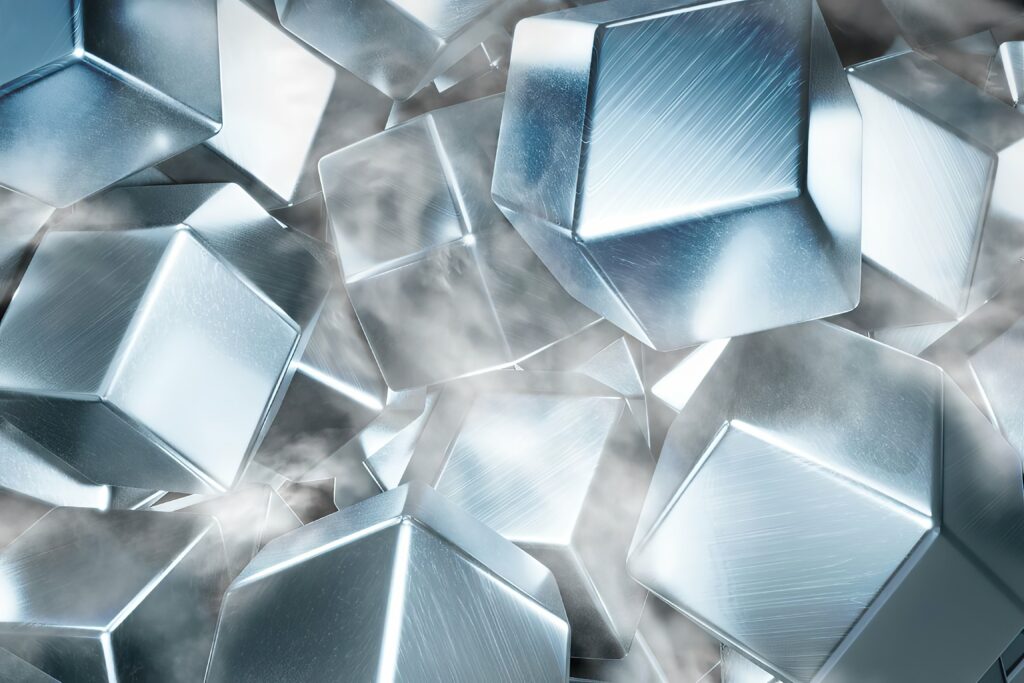
(Courtesy of UCLA)
Crystal clear
Nick Flaherty explains how techniques for analysing the surface of battery materials are leading to better cell designs
Materials analysis is essential in developing new battery components and ensuring they meet high standards of quality. Thermal analysis plays an important part in raw material characterisation, especially for thermal runway issues.
Lithium-ion technology is still in development to increase performance in terms of energy density and longevity. Issues with safety that have caused fire and explosion in vehicle battery packs have not been completely resolved, so materials analysis is vital during the development, manufacturing and recycling processes.
There are many different techniques for analysing the surface of materials. New techniques such as cryo-EM are showing the crystal structure of metals in batteries, and digital twin technology is enhancing that analysis.
X-ray analysis is one technique for rapid battery quality control and failure analysis, while handheld X-ray fluorescence (XRF) excels at identifying key battery elements during the end-of-life recycling process.
The energy storage capacity of lithium-ion cells fades over time owing to chemical and structural changes in their components, via different degradation mechanisms. Understanding and mitigating those degradation mechanisms are key to reducing capacity fade, thereby enabling improvements in the performance and lifetime of lithium-ion batteries.
Surface analysis techniques are commonly used to characterise the chemistry and structure at reactive interfaces, where most changes are observed as batteries age. However, battery electrodes are complex systems containing unstable compounds, with large heterogeneities in the properties of their materials.
Different degradation mechanisms can affect multiple material properties and occur simultaneously, so a range of complementary techniques must be used to obtain a complete picture of electrode degradation. The combination of these issues and the lack of standard measurement protocols and guidelines for data interpretation can lead to a lack of trust in the resulting data. This can present test engineers and materials researchers with a major challenge.
Several surface analysis techniques are being used for lithium-ion battery degradation studies, such as focused ion beam scanning electron microscopy, X-ray photoelectron spectroscopy, Raman spectroscopy and time-of-flight secondary ion mass spectrometry as well as laser diffraction for nanoparticles.
X-ray photoelectron spectroscopy (XPS) is a key surface analysis technique that provides quantitative elemental and chemical state information about the top layers of a material.
XPS is essential for understanding the interface between electrolytes and electrodes. The cathode and anode materials of lithium-ion cells can be studied to confirm post-cycling changes in composition, to understand changes in the chemistry of the electrode components, and to determine how the solid electrolyte interface layer varies in depth as it develops.
This technique has proved useful in studying the surface pre-treatment of graphite electrode materials to slow the irreversible consumption of material during battery charging.
Surface analysis tools include vacuum transfer modules for safe transport of sensitive battery samples from the glove box, where the samples are prepared for the instrument where the properties are measured without exposure to ambient atmosphere.
This multi-technique analysis is used for the analysis of cathodes, anodes and separator materials, such as looking at the surface chemistry of pristine electrodes and comparing that to the surface chemistry of used electrodes.
Cathode materials such as lithium, nickel, manganese and cobalt (NMC) change in stoichiometry depending on whether the cell is charged or discharged. To demonstrate that, one experiment profiled two NMC cathode samples on an XPS system.
One sample was taken from a pristine, unused cell, while the other was from a cell that had been through several charge-discharge cycles and was in a charged state when the cell was disassembled. Because lithium is highly sensitive to air and moisture, the electrode materials were loaded into a vacuum transfer module in a glove box for transport to the XPS system.
The survey spectra in the figure above/below shows peaks for the cathode materials with lithium, nickel, manganese, cobalt and oxygen and the binder medium and oxygen-containing polymers) that holds the materials together.
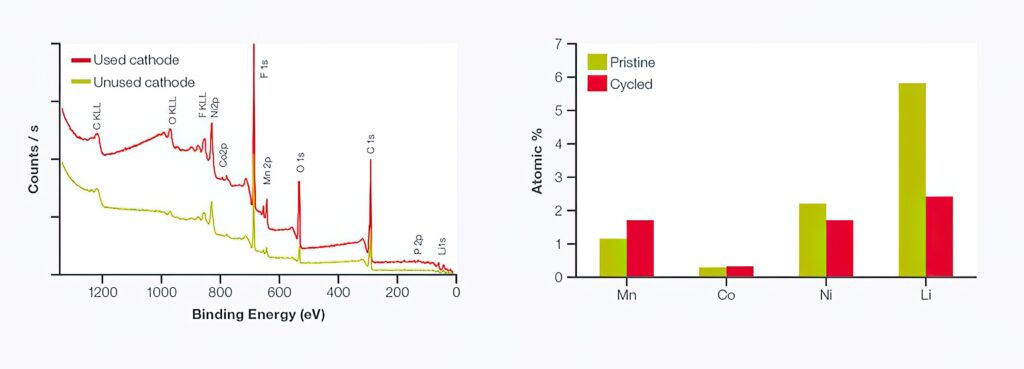
In the pristine sample (green), the binder is evident as a significant amount of residue on the surface. This could be important when first using the cathode, if the binder residue is mobile within the electrolyte or reacts to begin the formation of a surface layer that impedes ion transport. The cycled cathode (red) still shows the presence of the binder as well as residue from the electrolyte at the surface.
Comparing the NMC components (excluding oxygen) between the two samples (right figure), the relative intensities of lithium, nickel, manganese and cobalt were similar. However, the amount of lithium detected in the cycled cathode was around 40% of that observed in the pristine cathode. This was to be expected in a sample from a charged cell, where the lithium ions have been transported towards the anode, depleting the lithium level in the cathode.
Depth profiling analysis of the lithium phosphorus oxynitride solid electrolyte can help determine the structure of the film as a function of depth. A 1 keV monatomic argon ion beam induces lithium ‘pile-up’ at the interface because the monatomic ion beam induces lithium mobility in the sample. Using a cluster ion source prevents this from happening, resulting in an accurate measurement of the composition of the electrolyte film.
Depth distribution of elemental and chemical states can be determined by combining argon ion sputtering to break up the surface. A spectrometer can be configured with a monatomic argon ion source or a more advanced ion source with a cluster of argon ions (Arn+) , which has proved important in the correct determination of lithium concentration through solid electrolyte materials.
A conventional monatomic argon ion source can induce lithium ion migration through the electrolyte material towards the electrolyte-electrode interface as the implanted argon ions repel the small, mobile lithium ions. This bulk migration accounts for the errors seen in lithium concentration in monatomic argon depth profiles and the increase in lithium concentration at the interface with the electrode.
XPS is also suited to providing information relating to the interfacial material properties that are critical to performance of batteries. Information derived from the technique can give insights into chemical composition, elemental or chemical distribution of species, defect sites or functional groups.
Recent development of accessories for the spectrometers allows these materials to be studied in situ and in operation characterisation of the layers, which is also key for improving the computation models used in digital twins.
Spatially resolved surface analysis is easily achieved using XPS imaging available as standard with a spectrometer. Images of surface chemistry with a spatial resolution of a few microns over several millimetres can be acquired.
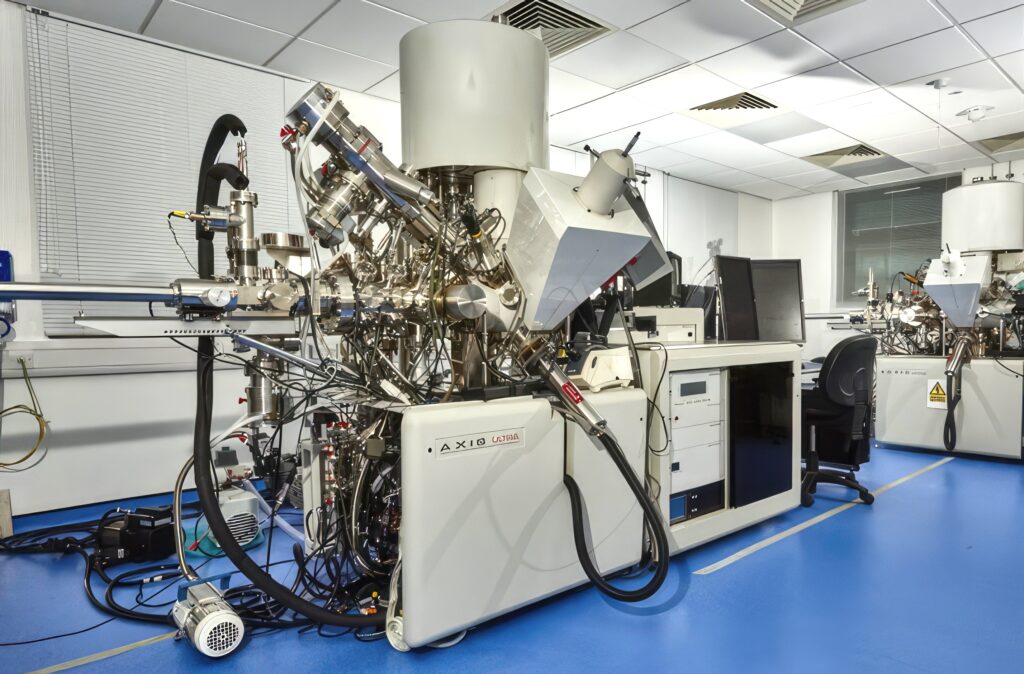
(Courtesy of University of Nottingham)
Battery production, development, and recycling
Combining XPS with XRF analysis helps to verify the type and behaviour of raw materials, and gives a detailed picture of metal contaminants. This combination can provide a complete picture of the type, size and distribution of metal contaminants that are so detrimental to lithium-ion battery performance. Automated analysis, including the ability to detect contaminants beneath the surface, provide the accuracy needed for quality control and the speed for production use.
For battery cells that are made in-house or come from a third-party supplier, or components that have failed in testing, the analysis shows the size, type and distribution of metal contaminants that could cause an internal short.
Thermal analysis will show how novel materials behave at elevated temperatures, showing the distribution of particles within the battery before and after use, while handheld XRF can identify these elements in end-of-life batteries.
A particle contaminant analyser with two X-ray sources is designed to help battery manufacturers improve the safety, performance and yield of the product. The analyser is engineered to rapidly detect and identify the unwanted metal particles within the battery that can cause sudden catastrophic failure of the batteries, often accompanied by fire or explosion.
Metal contaminants can be introduced into the battery from the raw materials or from the actual processing, as in metal particles from machinery. XPS is versatile enough to check for these in many stages during production, including as a final check before shipping the materials.
X-ray transmission imaging can find metal particles in the material and show the size and shape while XRF to determine which metal elements are present in the contaminated sites.
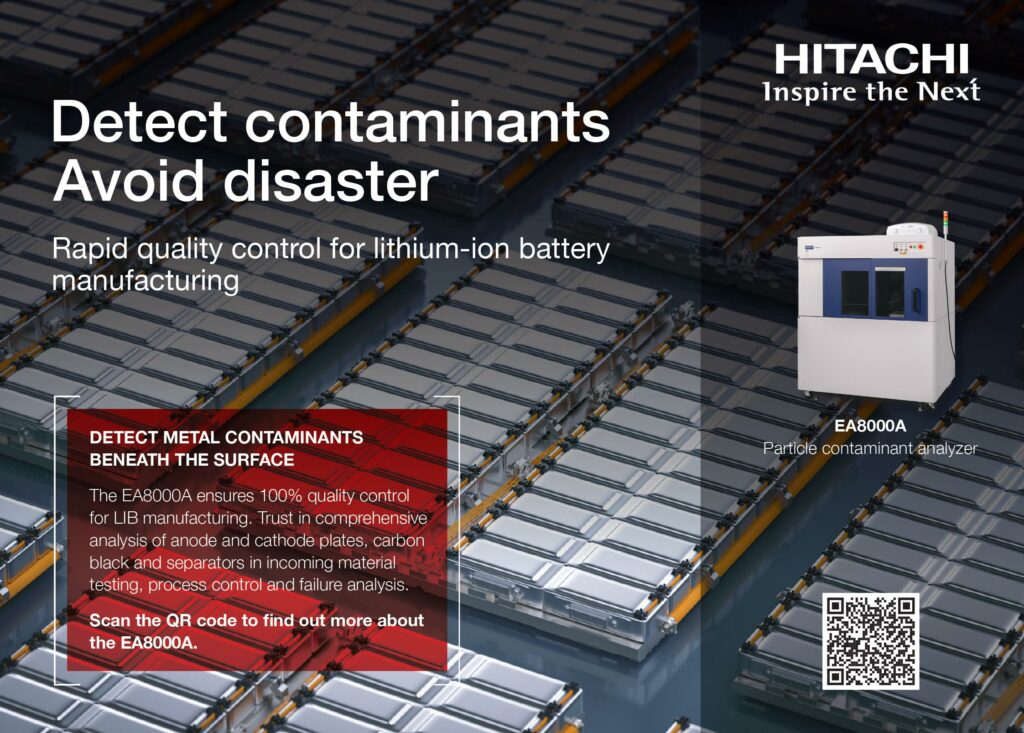
Many of the components used in production, including carbon-based powders used in anodes for enhancing conductivity, cathode materials, the cell separator and the outer casing of the cell can be tested in the analyser. Solid components can be laid flat on the measurement platform, called a stage, while powders and slurries can be spread out in a transparent plastic container.
The analyser is capable of detecting and analysing metal particles down to 20 µm in size, and rapid measurement allows large cathode plates for A4-size layers used in a production environment to be analysed.
The X-ray transmission scan builds up an image of the material where the size and shape of any metal particles can be clearly seen. This gives important information on the size and density of the contaminants, and allows a part to be rejected if it is out of specification. XRF analysis of the contaminants tells you which elements are present, which again gives a complete picture of the contaminants present, and which can be correlated with actual battery performance.
Process control
Having established that the raw materials are within specification regarding metal particle contamination, the next possible route for contaminants is from the production process itself. One way that can happen is from dust produced by production machinery.
The contaminant analyser can scan the materials for levels of metal particles typically present in the dust. As well as identifying a source of contamination in the battery cell, this technique is useful for checking for potential problems in the machinery itself; a change in the amount or type of dust emitted could mean that a service is due or a part in the equipment needs replacing.
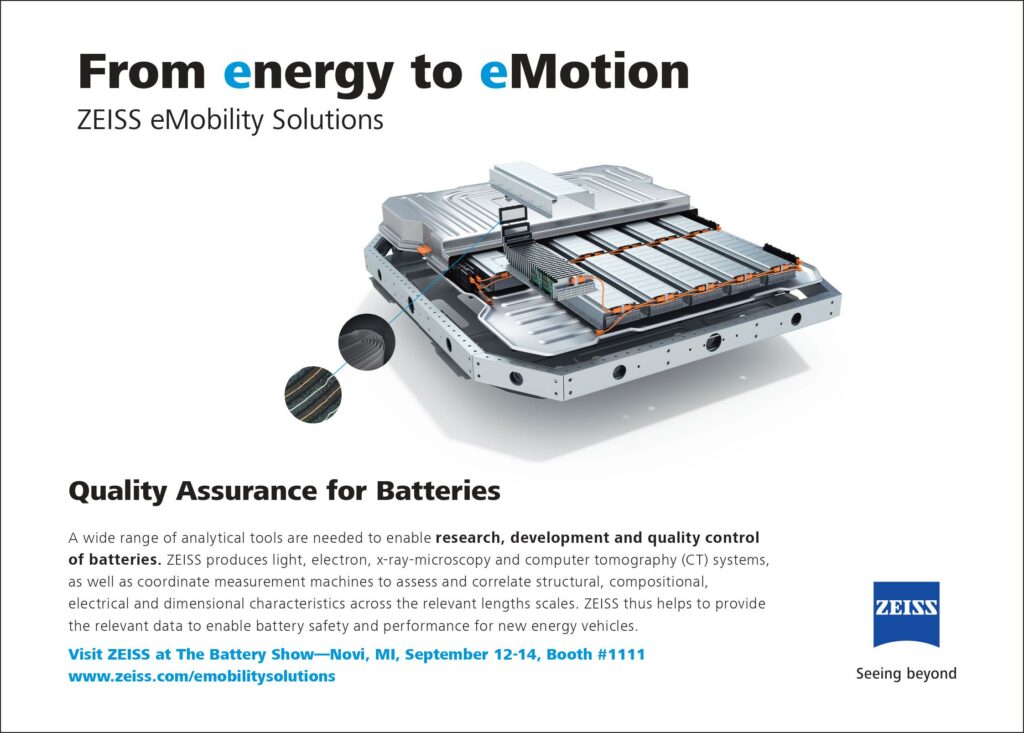
Failure analysis
This technique can also be used to determine the root cause of battery failure during the final testing phase of manufacturing. The surface analysis can determine whether any metal particles are present on the cell separator or electrodes that could have caused a short-circuit within the cell.
XRF compositional analysis will determine exactly which metals are present, in what size and quantity, to identify where the contaminants came from. This allows the correlation of specific patterns of contamination with performance, so that only the parts where the contamination compromises the performance are rejected.
Analysis of dry electrode layer manufacture
Research in the US has shown there are significant benefits to a dry battery manufacturing process but such a process needs a detailed analysis of the resulting material surfaces.
The dry anode process eliminates the solvents used in manufacturing to reduce the inactive elements and so increase energy density. Dry processing is a relatively new alternative that saves factory floor space as well as time, energy, waste disposal and start-up expenses, yet until now, researchers have had limited understanding of how and why it works.
The process involves mixing dry powders with a binder, then compacting the material to improve contact between the particles. The electrochemical performance of the material in different conditions is measured over various time frames to determine how the dry-processed electrodes degrade.
These measurements show that the dry anode structure allows lithium ions to take a more direct path between the anode and cathode, allowing the electrodes to be thicker for higher energy loading while reducing inactive ingredients that merely increase size and weight. The electrode also bends and flexes well, demonstrating excellent mechanical strength and the winding capability needed for mass production of batteries with fewer cracks than other techniques.
The next step in the research is to stabilise the material that attaches the anode components to a thin metal current collector. A main goal for the project is to develop or identify a better binder for the dry process, because the present one is not very stable for the anode environment. The researchers are also working on reducing the amount of carbon black used in the binder material.
Another technique for analysing the surface of battery materials is secondary ion mass spectrometry added to existing focused ion beam systems. This provides measurement for light elements such as lithium with sub-ppm sensitivity.
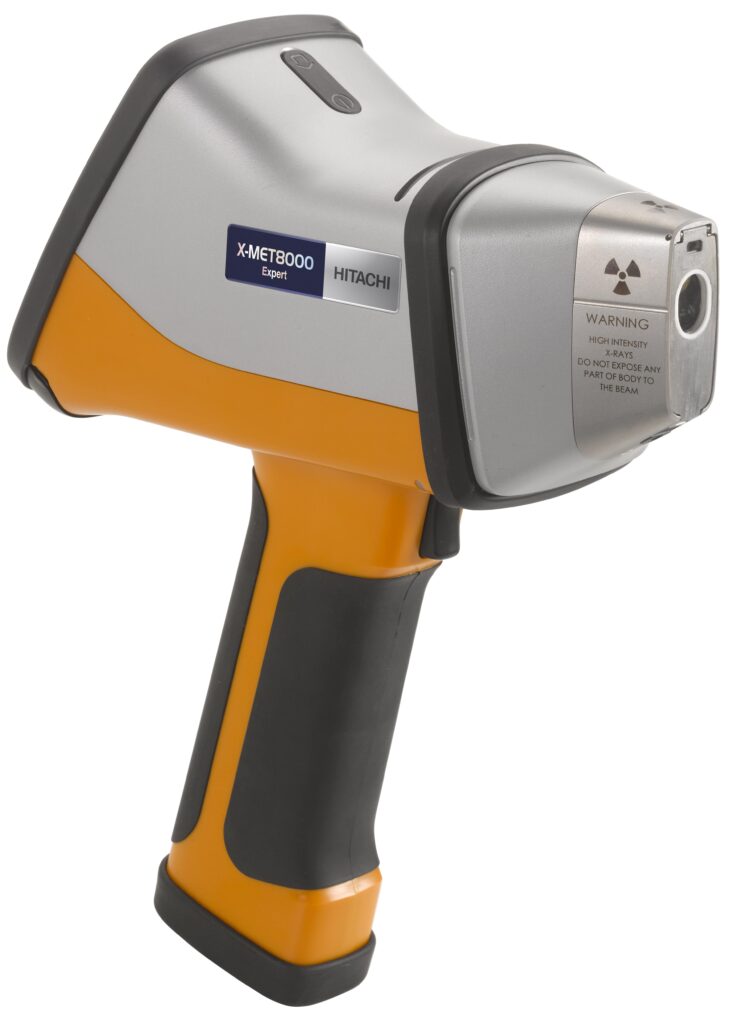
(Courtesy of Hitachi Hightech)
Laser diffraction
Rechargeable lithium-ion batteries use an intercalated lithium compound as the electrode material. A lithium titanate battery is a modified lithium-ion battery that uses lithium titanate nanocrystals on the surface on the anode.
These have a range of materials, from lithium cobalt oxide (LiCoO2), lithium nickel oxide (LiNiO2), lithium manganese oxide (LiMn2O4) and lithium iron phosphate (LiFePO4) for the cathode to carbon, lithium and lithium titanate (Li2TiO3) for the anode.
Laser diffraction can be used to determine the particle size distribution (PSD) of the battery materials used in r&d as well as quality control for product acceptance, as a PSD specification typically exists for a material used in production. Particle size influences capacity and coulomb efficiency, and reducing the PSD will increase the specific surface area, changing important battery characteristics as it also changes the size of the voids between electrode particles, reducing battery capacity.
LiCoO2 has served as the archetypical cathode material for rechargeable lithium-ion batteries since the 1980s, and five different lots of LiCoO2 used as cathode material were analysed by Horiba on a laser diffraction particle size analyser. The powder was dispersed in water containing 0.2% sodium hexametaphosphate, and laser diffraction was used for pass/fail testing to determine if the material met the incoming material particle size specification.
Companies with multiple sites often need to compare data from the different laboratories. Samples of lithium manganese oxide and lithium titanate were analysed on two different systems in order to quantify the instrument to instrument agreement.
The laser diffraction systems have high levels of reproducibility and agreement between systems when measuring the PSD of several battery materials.
The researchers used ultrasound to disperse the LiMn2O4 in deionised (DI) water containing 0.2% sodium hexametaphosphate to improve the measurement process. The sample was analysed without ultrasound, and then with 1, 3, and 5 minutes of it, with 3 minutes being the optimum time.
Lithium titanate
Li2TiO3 is often used as the anode material for fast recharging lithium titanate batteries. Again, ultrasound was used to disperse the lithium titanate in DI water containing 0.2% sodium hexametaphosphate and the samples were analysed without ultrasound, and then with 3 minutes of ultrasound. This time the dispersion of the sample did not improve with the addition of ultrasound.
Light scattering
Polarised imaging dynamic light scattering ((PIDLS) is another technique for measuring the size of nanoparticles and their shape as well as distribution in battery materials.
A dimensionless quantity named optical sphericity is used to describe the degree of deviation of nanoparticles from spheres. This method will greatly contribute to in situ synthesis, structure-function analysis, and quality assessment of nanoparticles.
The performance of nanoparticles is often influenced by factors such as particle size and shape. Traditionally, electron microscopy or atomic force microscopy is used to analyse the size and shape of nanoparticles, but this has challenges such as complex sample preparation, time-consuming processing, and difficulties in achieving quantitative characterisation.
Unlike electron microscopy and atomic force microscopy methods, the PIDLS method does not directly measure the nanoparticle size and morphology. It is a combination of the imaging dynamic light scattering (IDLS) and polarised light scattering (PLS) methods.
By illuminating a sample of nanoparticles with a polarised laser beam, a camera with a polarised filter receives the scattered light and obtains scattering images in the 0, 45, 90 and 135º polarisation directions. Owing to the continuous random Brownian motion of the particles, the spatial positions and orientations of the particles vary constantly, resulting in fluctuations in the intensity and polarisation state of the scattered light.
The rate of intensity fluctuations in the scattered light is related to the particle size, and according to the light-scattering theory, the polarisation state of the scattered light is related to the particle shape.
By calculating the spatial correlation of two consecutive scattering images in the 0º polarisation direction, the rate of intensity fluctuations in the scattered light can be determined, giving the particle size.
Continuous measurements can provide multiple particle size measurement results, including the average value and the dispersion. By analysing the intensity of scattered light from four polarisation images in the 0, 45, 90 and 135º polarisation directions taken at the same time, the degree of linear polarisation – or optical sphericity – is obtained that gives the degree of approximation of particles to a sphere.
A value of 1 indicates a perfect sphere, while a smaller value indicates a deviation from a sphere. Continuous measurements can provide the optical sphericity of the nanoparticles, giving the statistical shape distribution.
This technique has been tested on spherical, octahedral, flat, rod-shaped, and filamentous nanoparticles. The results of particle size, morphology, and distributions obtained from the PIDLS method were consistent with those obtained from electron microscopy.
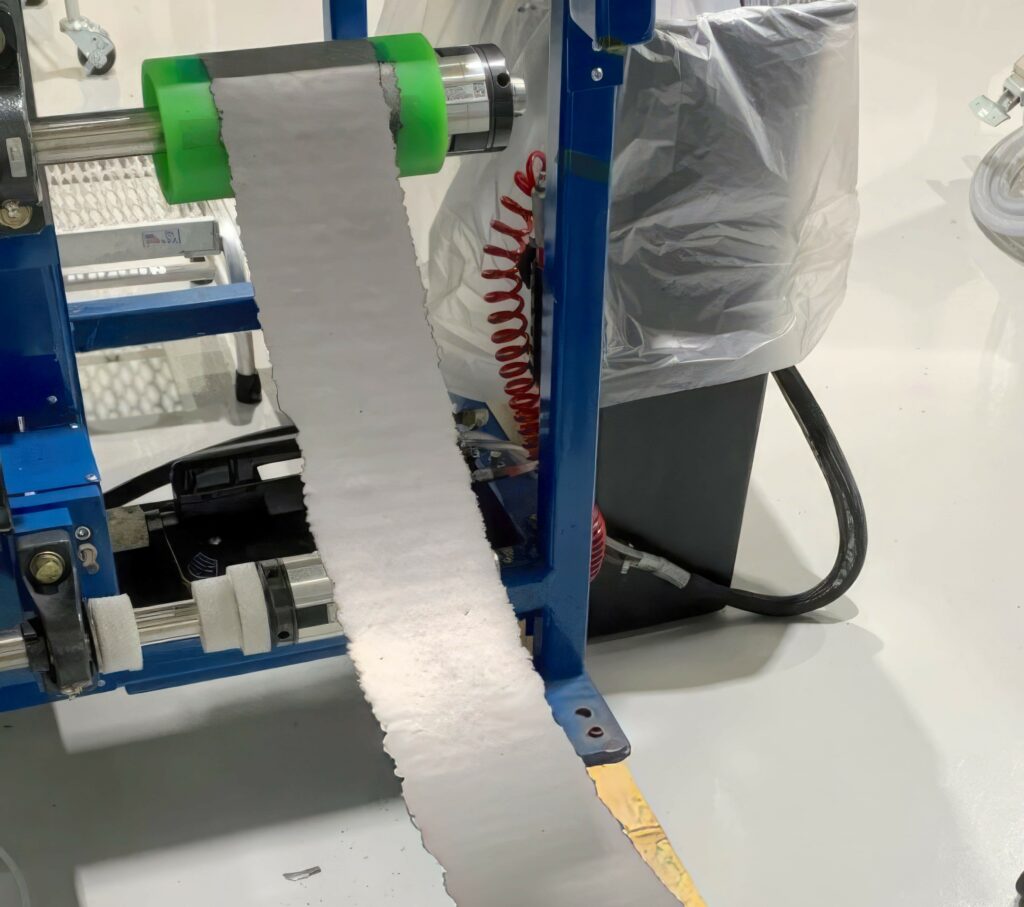
(Courtesy of Oak Ridge National Laboratory)
Cryo-EM
Researchers in the US have used a technique from biological imaging to determine the structure of lithium crystals.
Metallic lithium reacts so easily with chemicals that, under normal conditions, corrosion forms almost immediately while the metal is being laid down on a surface such as an electrode. Without that layer, lithium atoms assemble into a surprising shape — a 12-sided figure known as a rhombic dodecahedron.
Many papers on lithium metal describe its crystal structure as ‘chunky’ or ‘column-like’, but looking at the true shape of the lithium crystals suggests that the explosion risk for lithium metal batteries can be reduced as the atoms accumulate in an orderly form.
The researchers have developed a new technique for depositing lithium faster than corrosion forms. They ran current through a much smaller electrode without creating dendrite filaments, laying down lithium on surfaces using four different electrolytes, comparing the results using cryo-electron microscopy, or cryo-EM.
This technique uses electron beam imaging through frozen samples in order to show details down to the atomic level while inhibiting damage to the samples. It has been widely used to determine the structure of proteins and viruses, and several cryo-EM instruments have been customised to accommodate the types of samples used in materials research.
Laser scribing
Laser pulses have been used to modify the structure of a 2D material called MXene to boost its energy capacity for use as a battery material.
MXenes are a fast-growing family of 2D transition metal carbides/nitrides, and hold promise for electronics and energy storage applications. Mo2CTx MXene in particular has demonstrated a higher capacity than other MXenes as an anode for lithium-ion batteries.
Graphite contains flat layers of carbon atoms, and during battery charging, lithium atoms are stored between these layers in a process called intercalation. MXenes also contain layers that can accommodate lithium, but these are made of transition metals such as titanium or molybdenum bonded to carbon or nitrogen atoms, which make the material highly conducting. The surfaces of the layers also feature additional atoms such as oxygen or fluorine.
MXenes based on molybdenum carbide have particularly good lithium storage capacity, but their performance soon degrades after repeated charge-discharge cycles. This degradation is caused by a chemical change that forms molybdenum oxide within the MXene’s structure.
To tackle this problem, the researchers used infrared laser pulses to create small ‘nanodots’ of molybdenum carbide within the MXene, a process called laser scribing. The nanodots, roughly 10 nm wide, were connected to the MXene’s layers by carbon materials.
This offers several benefits. First, the nanodots provide additional storage capacity for lithium and speed up the charging and discharging process. The laser treatment has also been shown to reduce the oxygen content in the layer, helping to prevent the formation of problematic molybdenum oxide.
Finally, strong connections between the nanodots and the layers improve the MXene’s conductivity and stabilise its structure during charging and discharging. This provides a cost-effective and fast way to tune battery performance.
An anode constructed from the laser-scribed material was tested it in a lithium-ion battery over 1000 charge-discharge cycles. With the nanodots in place, the material had a fourfold higher electrical storage capacity than the original MXene, at 340 mAh/g versus 83 mAh/g, and an improved cycling stability with a capacity retention of 106.2% versus 80.6% for pristine over 1000 cycles.
This laser scribing could be applied as a general strategy to improve the properties of other MXenes for a new generation of rechargeable batteries that use cheaper and more abundant metals than lithium such as sodium and potassium ions.
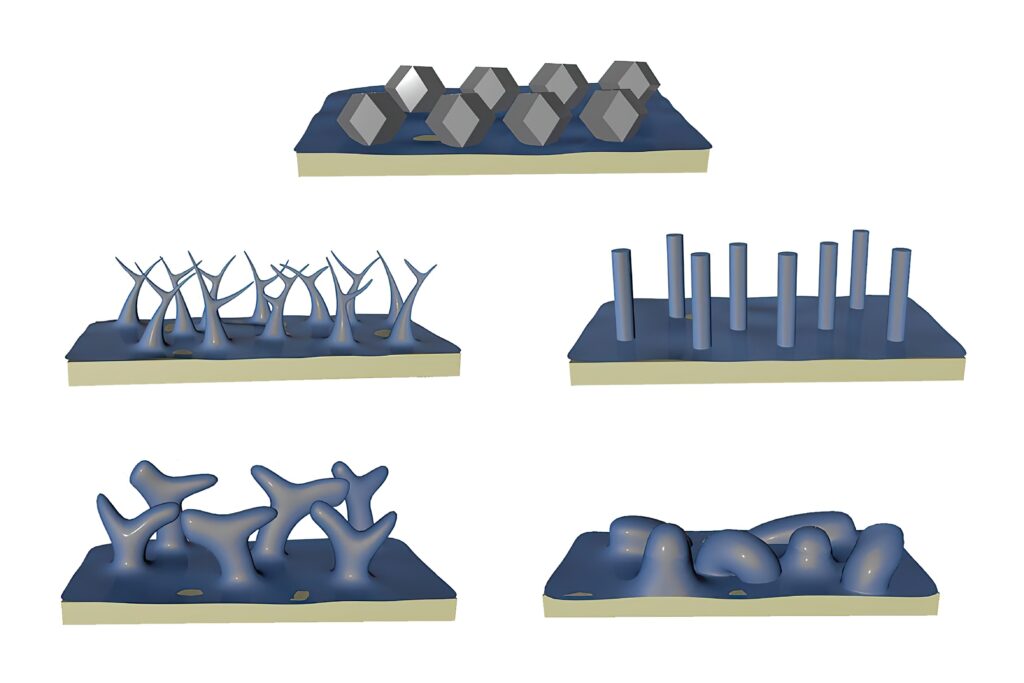
(Courtesy of UCLA)
Digital twin analysis
Digital twin technology can be used to evaluate battery materials’ characteristics using computational models, minimising the need for complex equipment and speeding up analysis.
A battery electrode degradation diagnosis technology has been developed in Korea that uses a particle-level multi-physics model of high-nickel active materials to identify the root causes of performance degradation within battery particles. It offers optimal particle designs through a more detailed analysis of their electrochemical and mechanical properties.
The model accurately diagnoses the internal structure by replicating the intricate particle arrangement found in actual batteries within a virtual environment. The model isolates and evaluates the numerous micrometre-sized particles in the electrode, effectively eliminating external factors that have an impact on battery performance.
The model reveals the actual characteristics of the active materials responsible for generating electrical energy, enabling highly precise measurements and ways to develop optimal particle designs.
The structures in digital twins closely resemble real particles and accurately predict volume changes during battery operation. The technology not only enables the diagnosis of electrode particle degradation but also offers opportunities for optimising designs to overcome such challenges.
Conclusion
There are many techniques for analysing the surface of battery materials, from X-ray spectrometry to laser diffraction. But new techniques, from in situ XPS analysis to cryo-EM and new ways to measure the shape of nanoparticles, are improving the accuracy of the analysis and the understanding of the way the layers interact with each other in a battery cell over time.
All this enhanced data is also helping to improve the computational models that are used in digital twins of the battery cells. The improved accuracy of the twins is helping to develop new battery cell designs without having to use expensive analysis equipment all the time. Developing new designs and then testing the materials is leading to longer lifetimes and higher energy density in the cells to boost the range and performance of e-mobility platforms.
Acknowledgements
The author would like to thank JJ Kim and Johannes Eschenauer at Hitachi Hightech for their help with researching this article.
Some suppliers of battery surface analysis equipment
Germany
Hitachi Hightech
Horiba Europe
+49 2151 64350
+49 6172 1396 0
UK
Blue Scientific
Kratos Analytics
Hiden Analytical
+44 1223 422269
+44 161 888 4400
+44 1925 445225
USA
Jeol
Nanoscience Instruments
Thermo Fisher Scientific
+1 978 535 5900
+1 480 758 5400
+1 781 622 1000
ONLINE PARTNERS
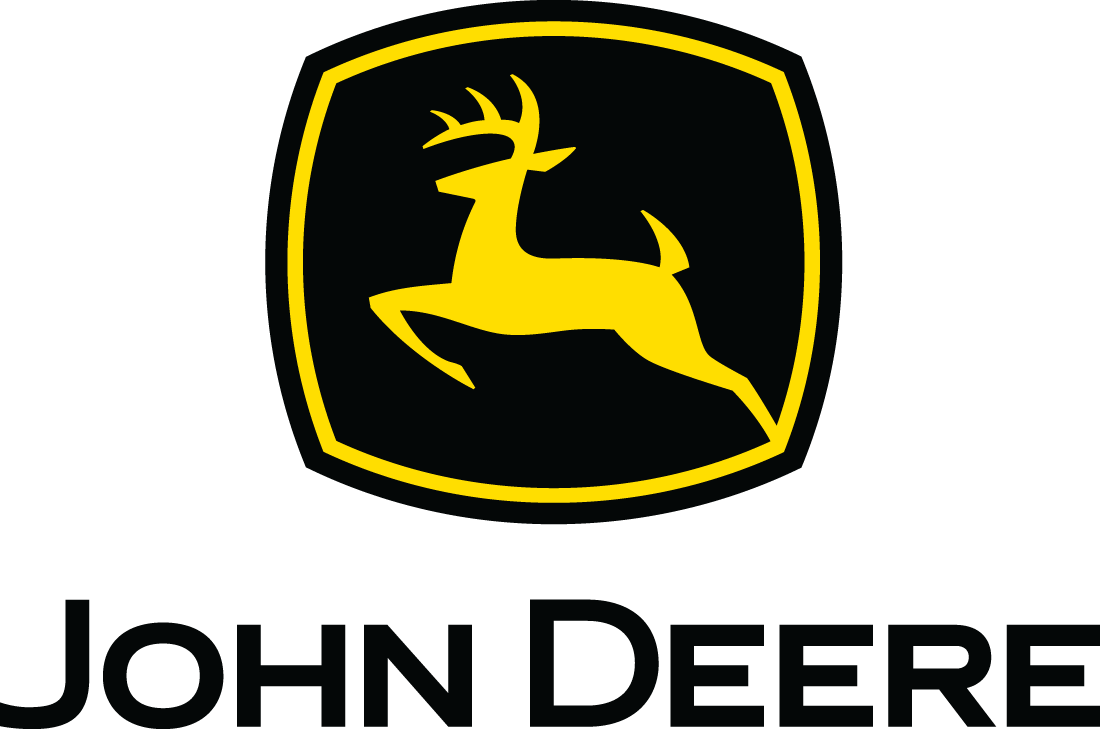
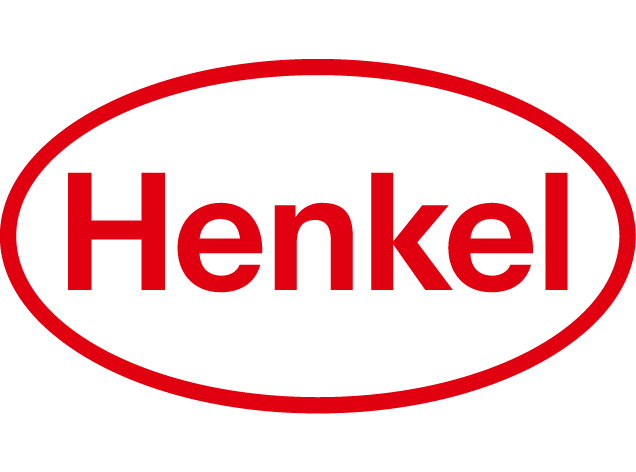
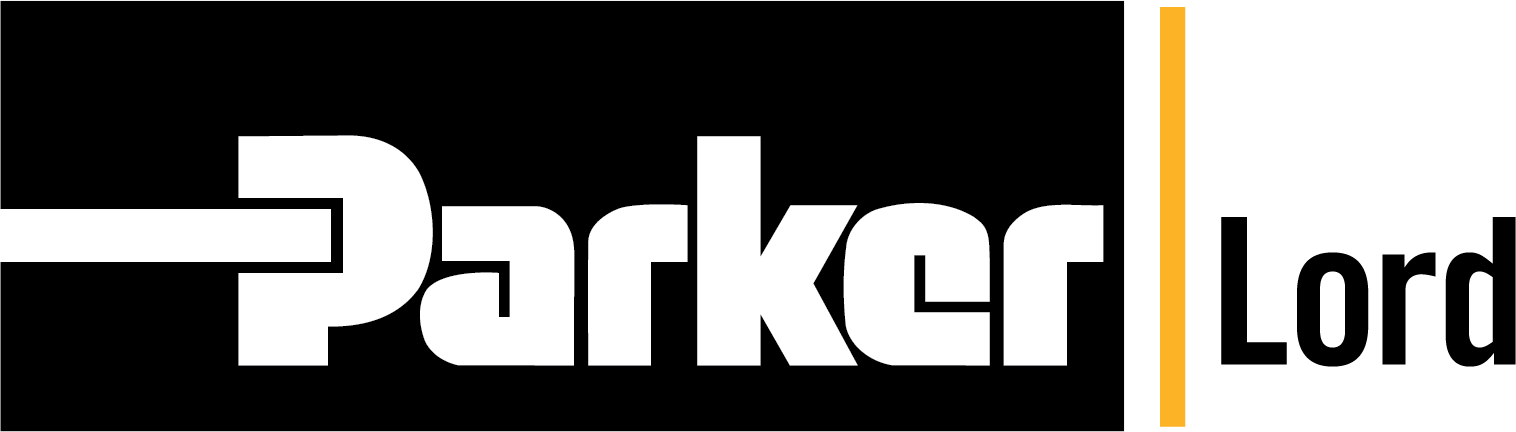
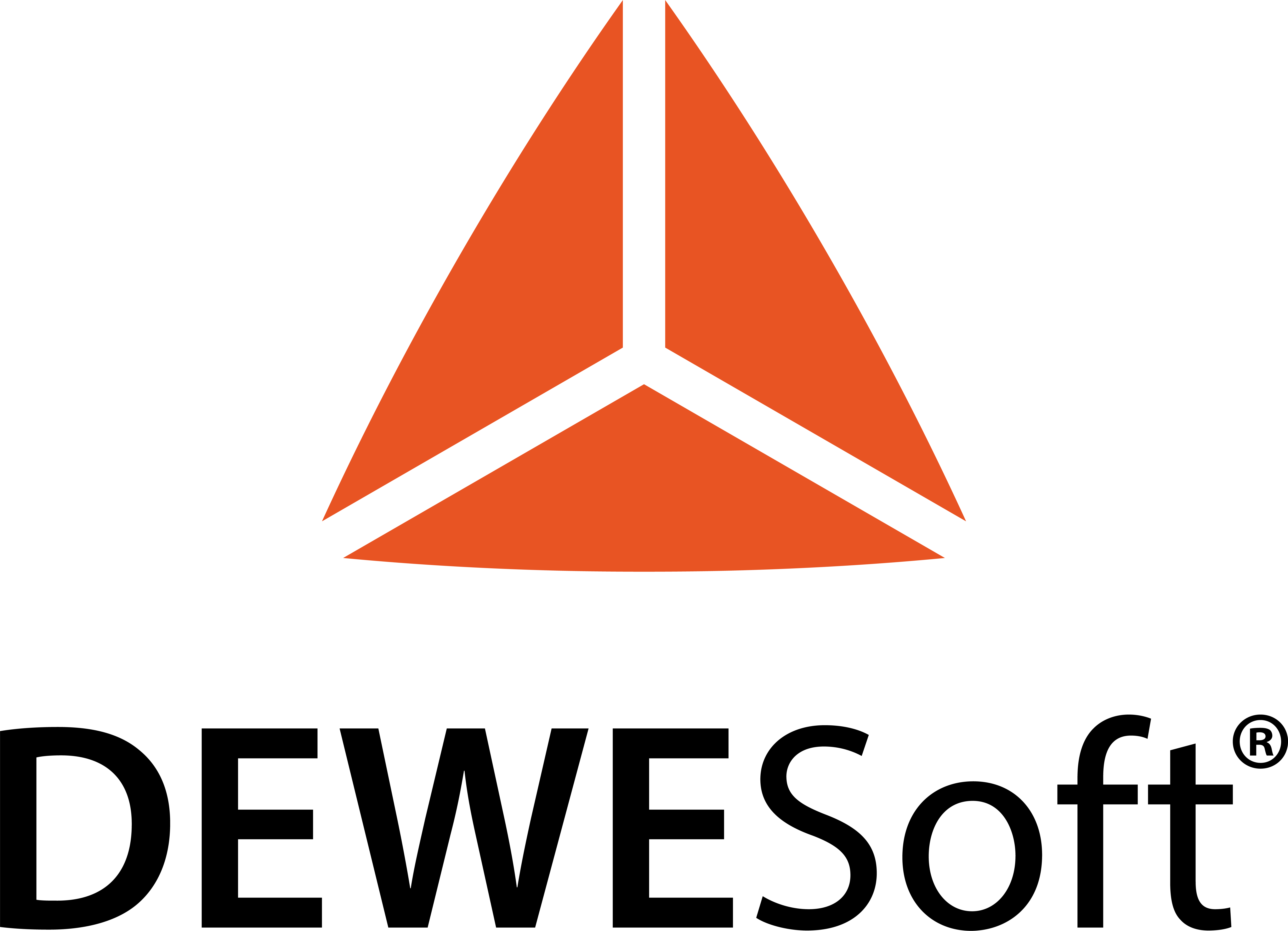
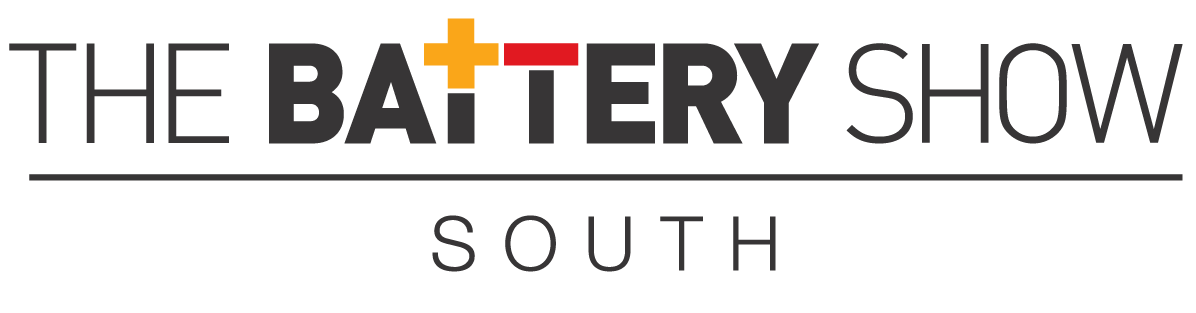
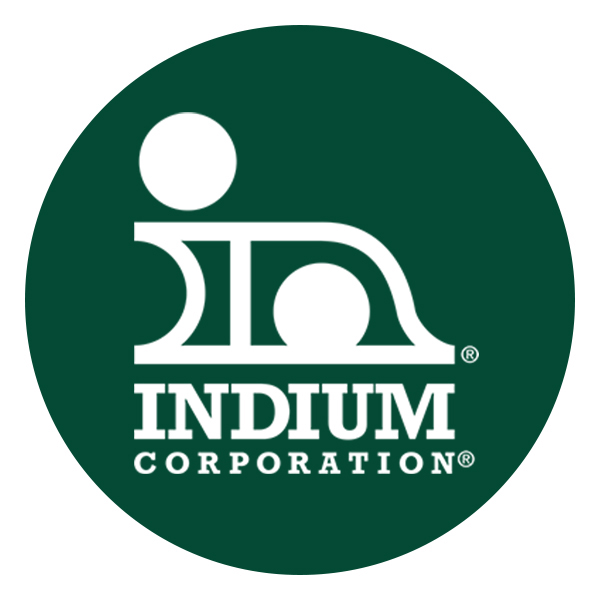

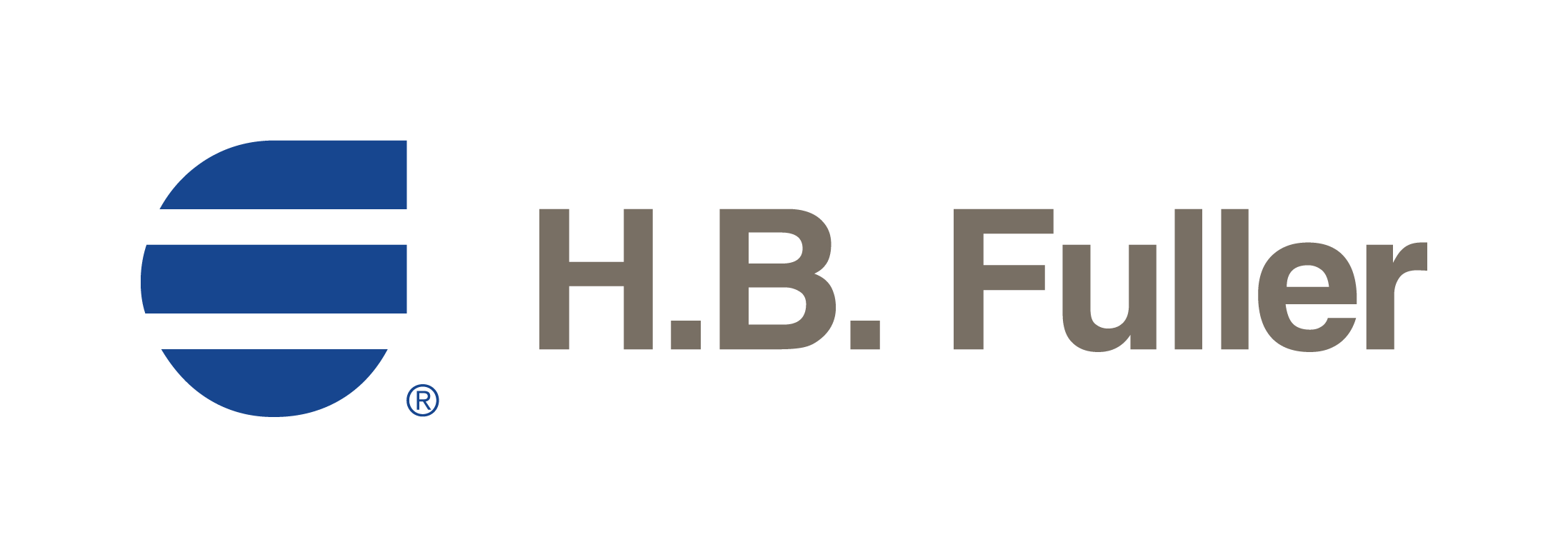
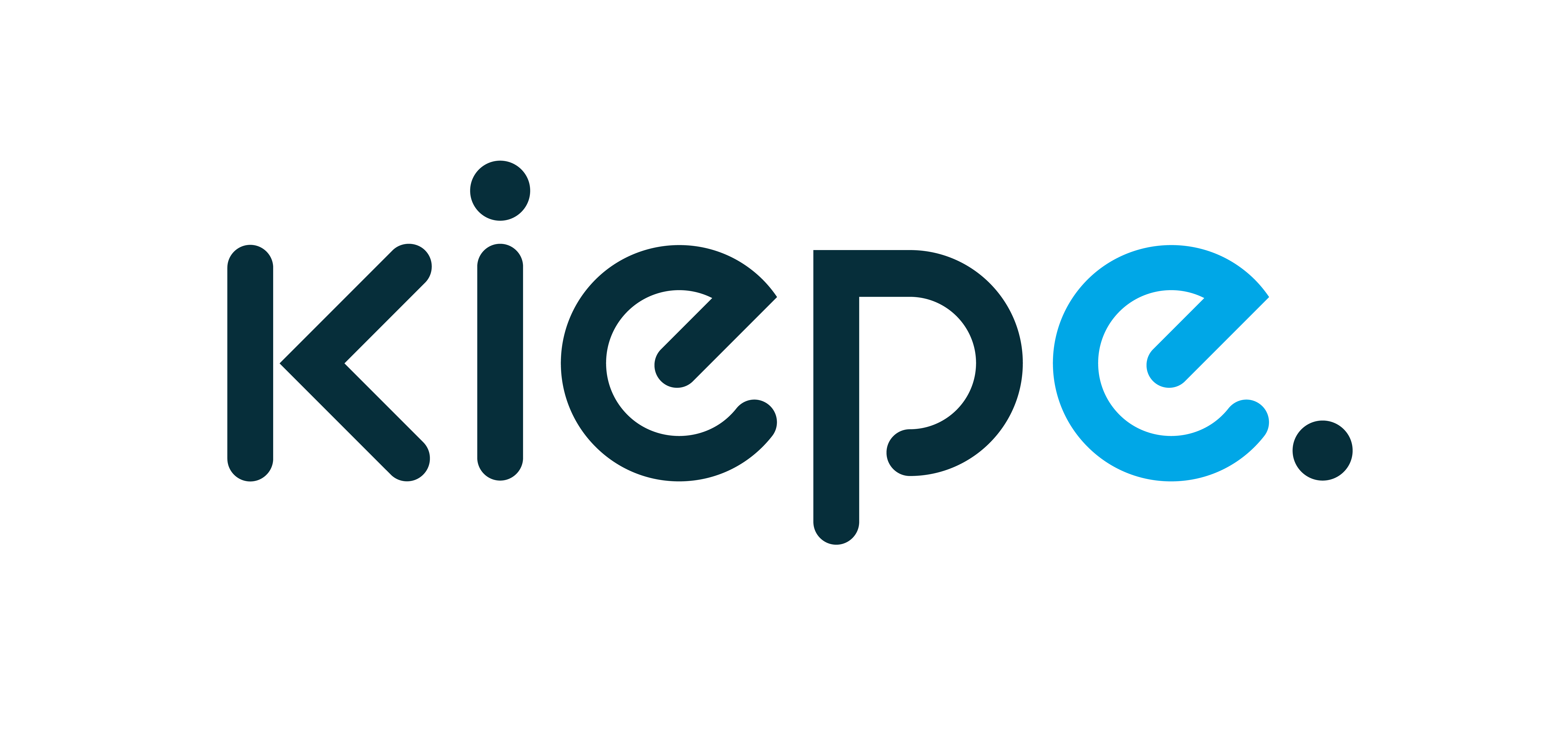
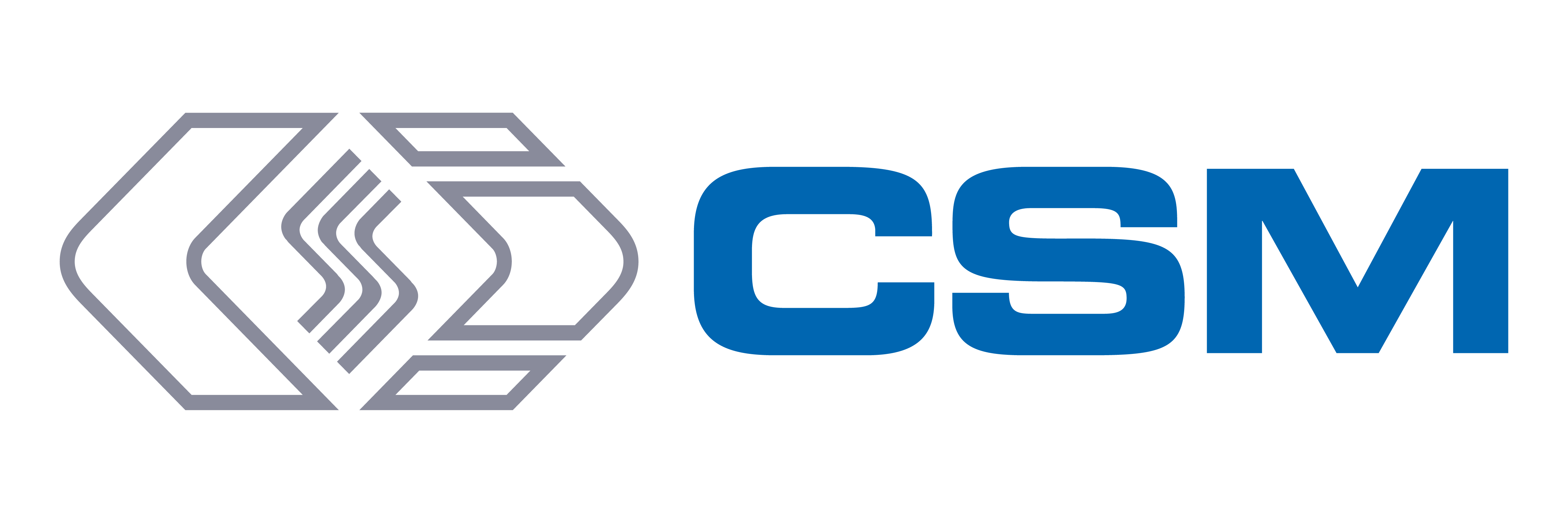