Battery sealing
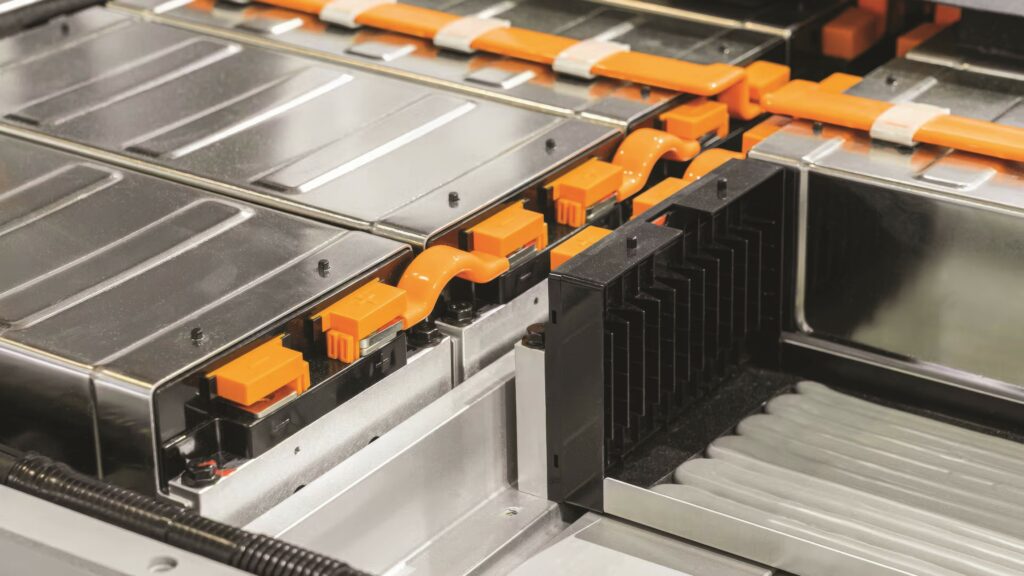
(Image courtesy of bdtronic)
Sealing the deal
Nick Flaherty assesses the various materials and processes used to seal and protect a battery pack
Sealing a battery pack safely is a key requirement for e-mobility systems. While there may be concerns about the ingress of moisture or dirt, there are also issues over venting gasses and preventing electromagnetic interference. As a result, the choice of materials and the processes for sealing a battery pack, including cleaning the surfaces, are a series of engineering trade-offs.
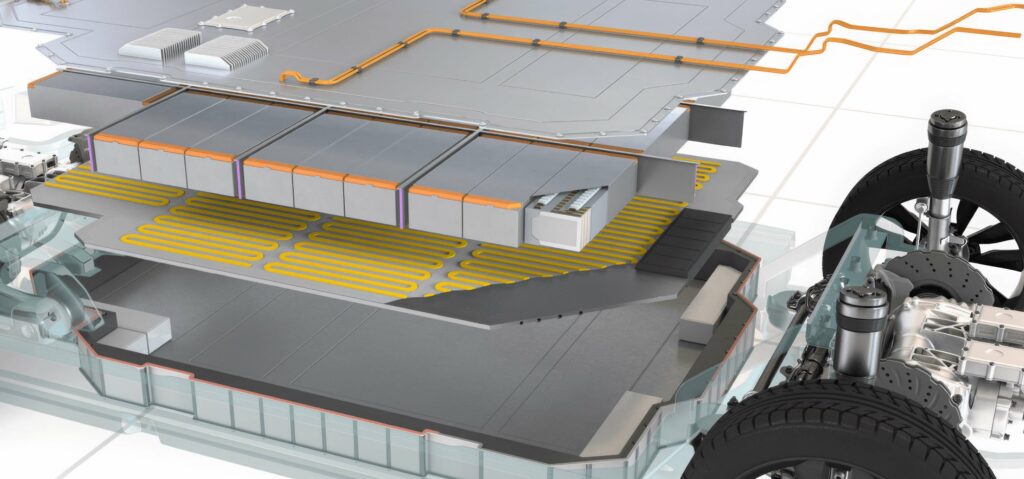
(Image courtesy of PPG)
Hot riveting
The applications of hot riveting are wide ranging. Sometimes it is used to pre-fix a component, such as a busbar or a lead frame, in the production flow before casting, soldering, welding or wire bonding. It can also be used to post-fix a cover to the housing after applying a sealing adhesive to enable the assemblies to be transported while the adhesive is curing.
In most cases, however, it is used for connections that need to withstand defined forces with vibration and climatic loads over the service life of a vehicle.
Likewise, the range of products for which hot riveting is used is extensive. Typical uses include permanently fixing circuit boards in and on a battery pack or fixing covers with housings, joining busbars, insulators, cooling plates or microelectronic components.
Processing battery cells requires special process know-how and a lot of experience, and different hot-riveting applications are used for battery packs. Busbars are fixed with rivet points, while the insulators, cooling plates or frames, and side parts or stiffening plates and spacer plates are caulked. There are also various material pairings, including plastic-metal, plastic-plastic, plastic-FR4 and plastic-isothermal, that have to be considered.
Since a large number of closely positioned rivet points are provided due to the component size, and the necessary holding force and stability, custom machines are used for these battery applications.
When joining the assemblies, the expansion of the battery cells must be taken into account, so they must have a high assembly tolerance and be put together securely without any critical temperature input to the cells. At the same time, the joining applications must maintain high levels of strength. Depending on the application and specification, different caulking methods are used.
All in all, only thermal riveting processes can be used, as both the electronic components and metal sheets must be processed without vibration. The size and weight of the modules, along with the high number of rivet points located at short intervals, means a custom system must be developed for the hot-riveting process for the battery packs for both prototyping and series production.
The hot air heat-staking process separates heating and forming, so they can be carried out in parallel by two modules in two stations, allowing the cycle time of the machine to be significantly reduced. A particular advantage of this process is that it always ensures consistently good riveting results without melt leakage, even over high-volume fluctuations due to component tolerances.
Fully-automatic inline hot-riveting systems have been developed for the hot air process. Up to 12 rivet points can be processed as standard, with an integrated transport system bringing the workpiece carrier or panel into the manufacturing cell. The component is processed in the cell in the required cycle time, which is determined purely by the heating cycle rather than the riveting time.
For larger battery packs, a larger machine takes the assembled component from the conveyor belt to the processing stations and automatically returns it to the conveyor belt after processing. The concept, as a modular platform, enables the construction of several stations for a high number of riveting points and/or processes in a hot-riveting system.
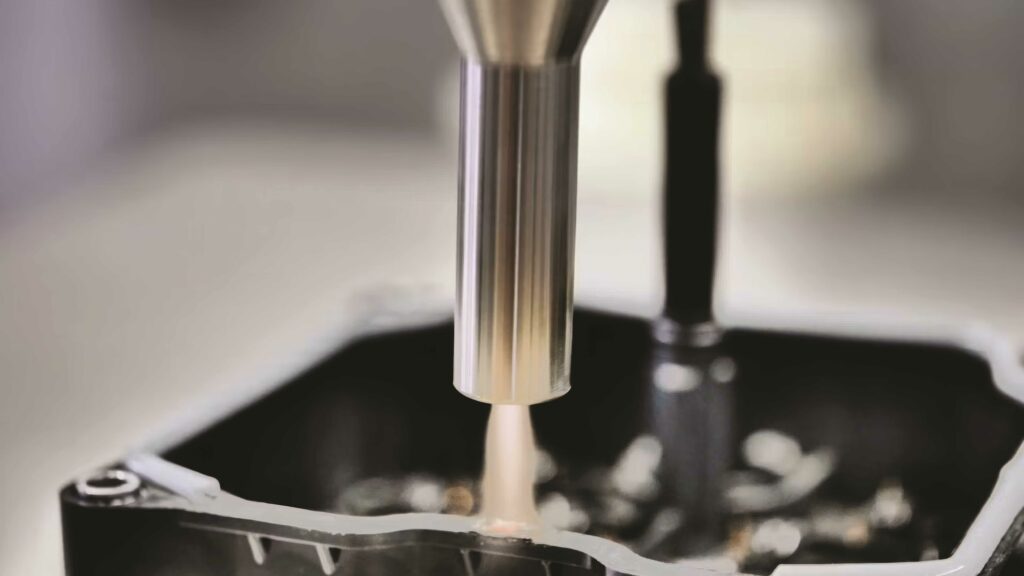
(Image courtesy of bdtronic)
Plasma cleaning
Bonding is becoming increasingly important in modern industry. Mixed material connections (so-called sandwich connections), complex geometries, new materials, minimal amounts of adhesive – these are all challenges that material and system manufacturers have to face. For a long time, plasma has been used to improve adhesion; i.e. cleaning and activating surfaces.
Plasma ensures impurities are removed from the surface and functional groups are created. This leads to several effects. On the one hand, the wettability of the surface is increased, so that the applied material can be optimally distributed over the surface.
On the other hand, the functional groups form a strong bond with conventional adhesives and casting compounds, and thus ensure better, more long-term, stable adhesion, strength and tightness of the connection.
In preparation for subsequent processes, such as bonding and coating, the surface is pretreated using plasma technology, so unwanted raw materials and dust particles are removed. Plasma technology makes it possible to further process the materials immediately after plasma cleaning.
The surface of plastics, metals and other materials is changed through the use of plasma technology in such a way that the surface tension increases to the desired level, thereby significantly improving wettability.
Plasma treatment and plasma cleaning optimally prepare surfaces on plastics, metals and many other materials for subsequent processes, such as bonding and coating. The material surfaces are removed in the gentlest way from unwanted raw materials and even the smallest dust particles. Safe plasma fine-cleaning removes additives, hydrocarbons, mould-release agents and plasticisers from plastic surfaces. The plasma-treated materials can be further processed immediately after.
Plasma activation modifies the surfaces of plastics, metals and other materials to increase the surface tension required for subsequent processes, such as bonding and printing. Plasma activation significantly improves wettability on material surfaces.
Using atmospheric pressure plasma enables a significant improvement in surface energy on thermally sensitive surfaces. This means polymer surfaces can be easily glued, printed and coated in subsequent processes.
Plasma passivation protects surfaces on metallic material from corrosion. The passivation layer created slows corrosion by increasing protection. Plasma pre-treatment can reduce the surface roughness of insulating and metallic layers without affecting their physical properties.
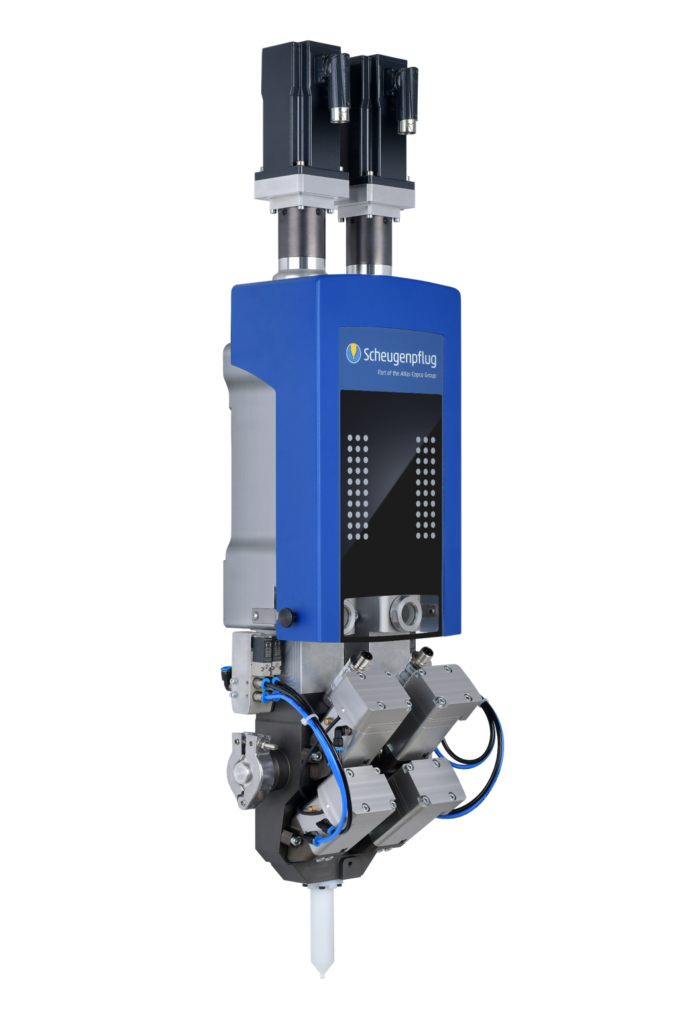
(Image courtesy of Scheugenpflug)
Sealants
Liquid seals have proven themselves in numerous areas as an alternative to moulded seals. This also applies to electronic components that often function under extreme conditions and need to be protected against dust, moisture, corrosive media or temperature-dependent influences.
A wide variety of mostly highly viscous sealing materials is available today that can be applied with precision and repeat accuracy on increasingly complex components. This requires the dispensing system to be carefully tailored to these requirements to address directional changes, acceleration and deceleration during bead application, and a uniform transition when closing off the bead.
To achieve this requires a combination of a material feed system, a dispenser and a dispensing cell. The feed and dispenser are designed for processing highly viscous sealing materials. The dispensing material is fed from the material drum via feed lines to the dispenser, which applies it continuously along the required contour on the component. Precise application of the material in three dimensions is ensured by installing the dispenser on the CNC axis system of the dispensing cell.
Adhesive sealants
Choosing an adhesive system that meets all of the end-product’s needs is like searching for the proverbial needle in a haystack. Material manufacturers can use their experience to help customers validate a suitable system.
Modern, lightweight construction using materials such as glass and carbon-fibre composites is one of the main uses for epoxy resins for lamination of the fibre layers, but epoxy resin is also used as an adhesive for joining individual components. Epoxy resin is used as an electrical casting resin wherever protection against media and high-temperature resistance is necessary. In addition, the highly filled variants are characterised by low flammability and low ember formation in the event of thermal runaway.

(Image courtesy of PPG)
Epoxy resins
Low-viscosity epoxy resins are usually available commercially as two-component systems.
They must be mixed and dosed precisely in accordance with the manufacturer’s instructions and the technical data sheet in the specified mixing ratio. As polyaddition adhesives, epoxies and polyurethanes are very sensitive to fluctuations in the mixture.
The A component usually corresponds to the epoxy resin, while the B component contains the hardener, which is often based on amine or thiol. The B component is usually significantly lower in viscosity than A.
After mixing the resin and hardener, the reactive volume is subject to a
time-limited processing time, as the chemical reaction of hardening begins from the first contact between the resin and hardener, leading to a more or less rapid increase in viscosity. This time interval is called the pot life.
One property of epoxy casting resins is the high exothermicity of the curing reaction, where larger amounts of the reactive mixture can give off a considerable amount of heat during the cross-linking reaction. This can lead to components being damaged, particularly with high-volume applications. An appropriate potting strategy with sequential application can control this effect.
With the material preparation system (MPS), the material is permanently recirculated in the pipe system, tempered and processed under vacuum without gas voids. The pressure-sensor control at critical points in the processing system guarantees complete command throughout every production cycle. In addition, refilling is possible during operation, so machine availability is not lost due to unnecessary downtime.
With the exception of a few examples, pasty adhesive systems based on epoxy resin are formulated as 1K, which means the resin and hardener are present side by side. To ensure the reaction does not occur during shipping, storage and processing, the hardener component is often finely distributed as solid particles in the resin or chemically immobilised.
The processing time of these materials – the pot life – is therefore often very long. If the component is heated using an oven, infrared lamp or microwave after application, the hardener component melts, or the immobilisation of the hardener is removed and the chemical reaction takes place at a very high temperature in a matter of minutes until it reaches handling strength. Since it is not necessary to mix resin and hardener, it is often possible to apply the 1K epoxy resin directly from the dosing pump.
Sealing is an effective dosing process to protect components from external influences through a barrier. A usually highly viscous sealing material is applied to the components, according to a defined 2D or 3D sealing contour.
The most common area of application is the sealing of housings and their covers, and it is also used to connect components to one another. This is used to eliminate dust, temperature-related influences, moisture, and protect sensitive components and other external influences. To achieve the optimal sealing contour, a continuous, precise dosing application is essential.
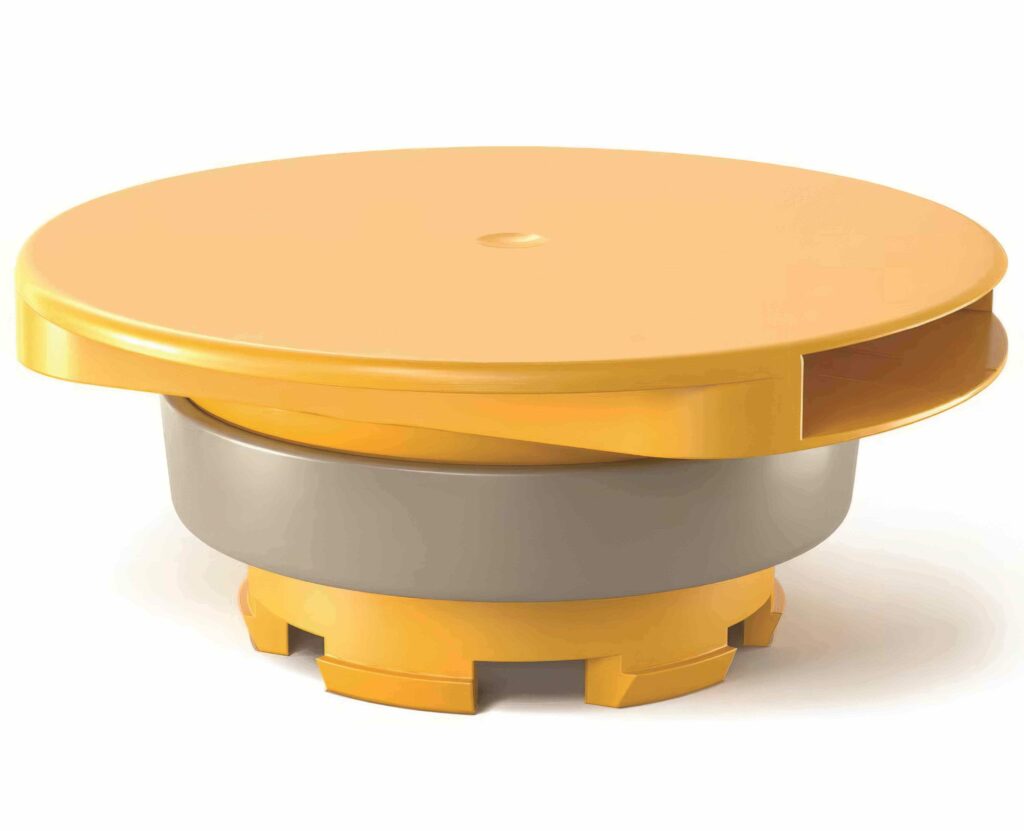
(Image courtesy of Parker Hannifin)
CIPG vs FIPG
Two dosing methods are typically used: cured-in-place gasket (CIPG) or formed-in-place gasket (FIPG). With CIPG, liquid seals are applied to a housing and the cover is then joined. This process is a soluble compound and allows the lid to be opened to repair the component. The FIPG is an inseparable connection that sticks to both the housing and the lid.
Liquid seals are especially useful for sealing complex 3D geometries that cannot be reliably sealed with conventional seals, gaskets, punched parts or weather seals.
Using adhesives as FIPG or CIPG has an advantage over silicone in that they have much shorter curing times. In addition, FIPGs and CIPGs can be released from the components, so they are reusable. Liquid seals also have a restoring capability, so they partly or fully return to their original shape.
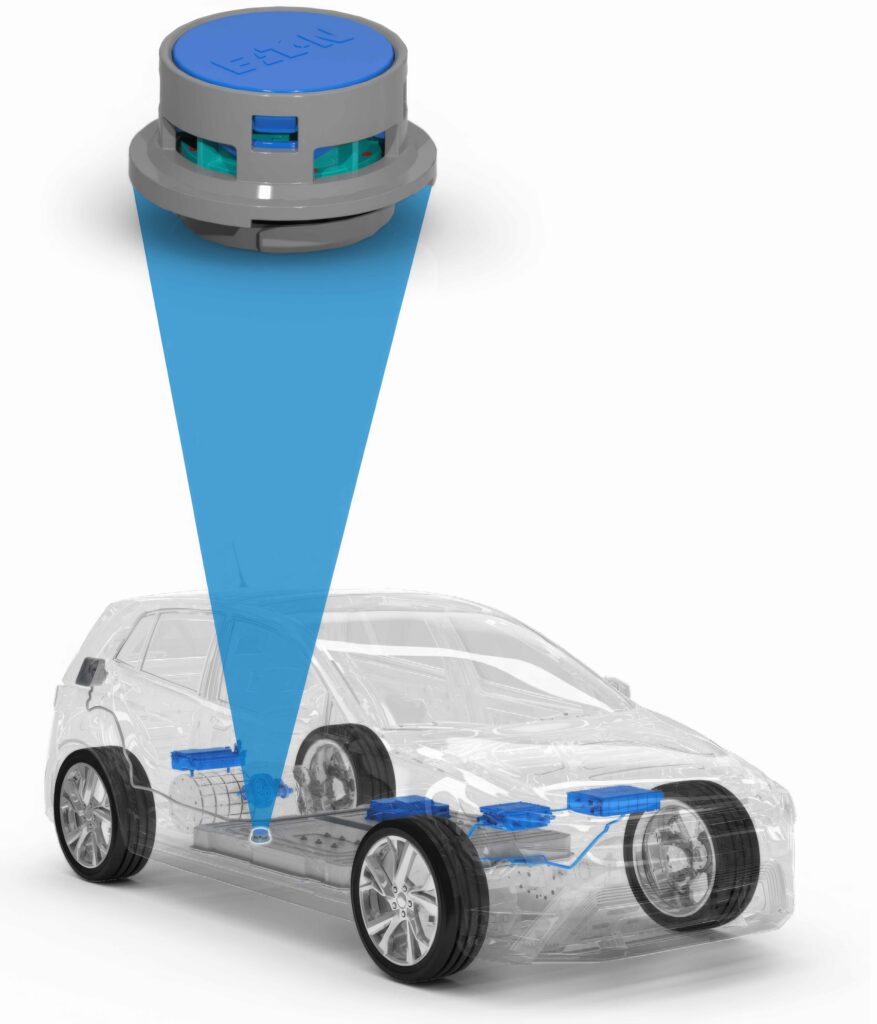
(Image courtesy of Eaton)
Structural adhesives
Structural adhesives can be used to seal battery packs. These have higher levels of shear strength to avoid any weak spots in the structure of the pack, with high levels of corrosion and hygrothermal resistance from the movement of both heat and moisture. These rubber-based materials are one component that is applied in the body shop during the assembly of the e-mobility platform.
Fracture toughness is the crucial property for crash-resistant structural adhesives. The latest versions allow the bonded structure to absorb a high degree of impact energy. They use a core of rubber with pre-dispersed nanoparticles in the secondary phase to increase the fracture toughness of the epoxy polymers. The cavitation and debonding of rubber particles make the structure of the material more prone to shear-yielding instead of cracking.
The resulting ability to resist the growth of cracks increases the adhesive’s load-bearing capacity, which allows impact energy to be absorbed more effectively, thus protecting the battery cells in the event of a crash.
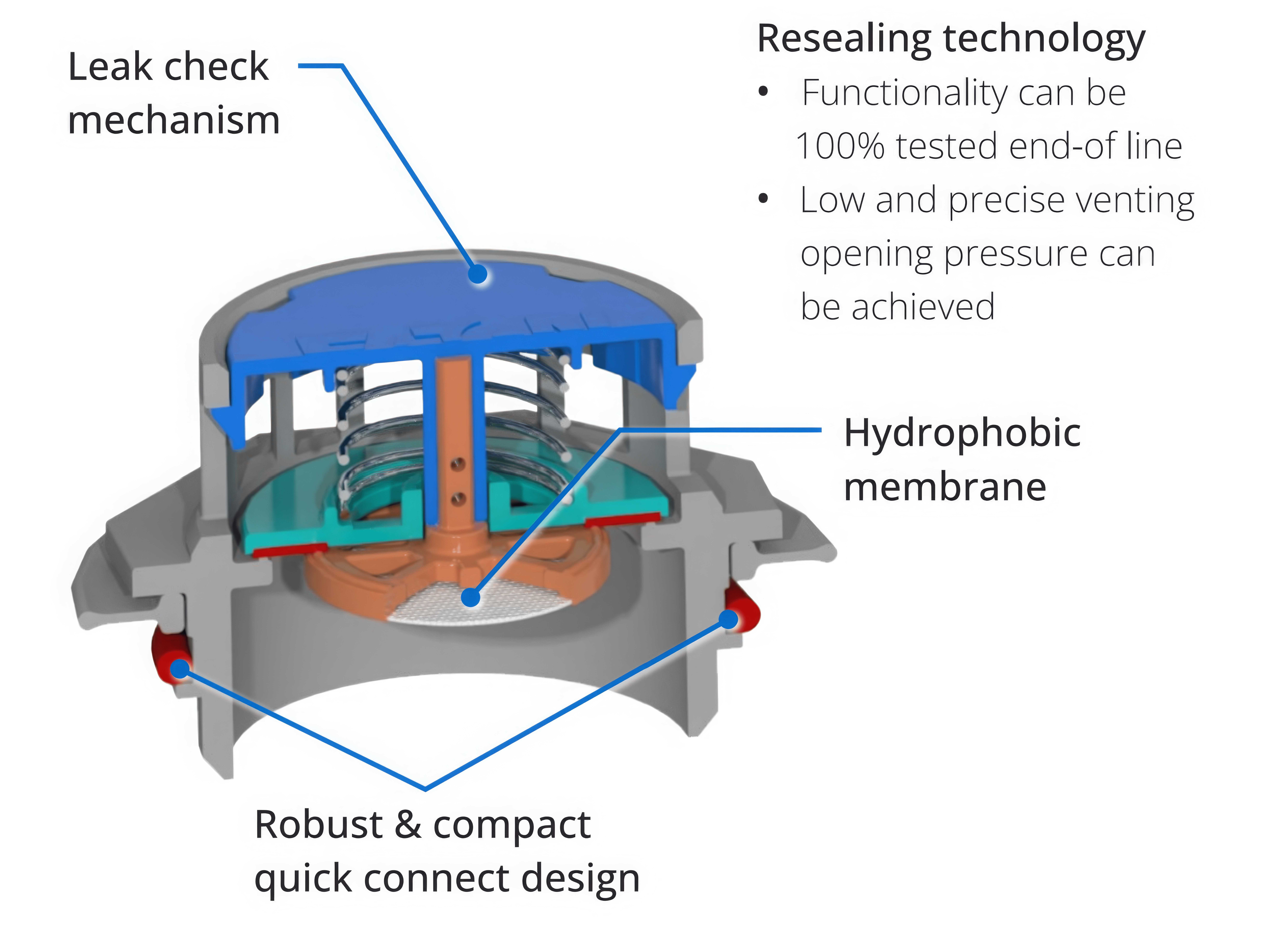
(Image courtesy of Eaton)
Pressure relief
Having a totally hermetically sealed housing is not always advantageous for a battery pack. These larger housings can be prone to pressure differences caused by changes in ambient temperature or air pressure. As this can pose a risk to the mechanical stability of the pack, to prevent deformation or other damage, it can be protected with a pressure-relief system.
Minor pressure variations or a sudden increase in pressure due to cell defects can jeopardise the integrity of the battery pack. This can happen at the start of thermal runaway, and the extra pressure can rupture the pack, rendering any thermal prevention materials irrelevant. The pressure release valve can prevent this and protect the housing.
A pressure relief valve protects against mechanical damage that may occur in the event of pressure differences between the interior of the housing and the outside environment. They also seal against external liquids and dirt. The elastomer membrane is designed to open under pressure to release the gas, closing again to provide a secure seal against the ingress of dust and water to protect the interior of the pack.
But, as battery packs become progressively more powerful and create more heat, the vent valve plays a crucial role in maintaining safety. In case of overpressure or excessive gas build-up within the battery, the vent valve allows the release of gases to prevent hazardous situations.
Testing ensures the valve operates correctly, allowing for proper heat dissipation and to prevent overheating.
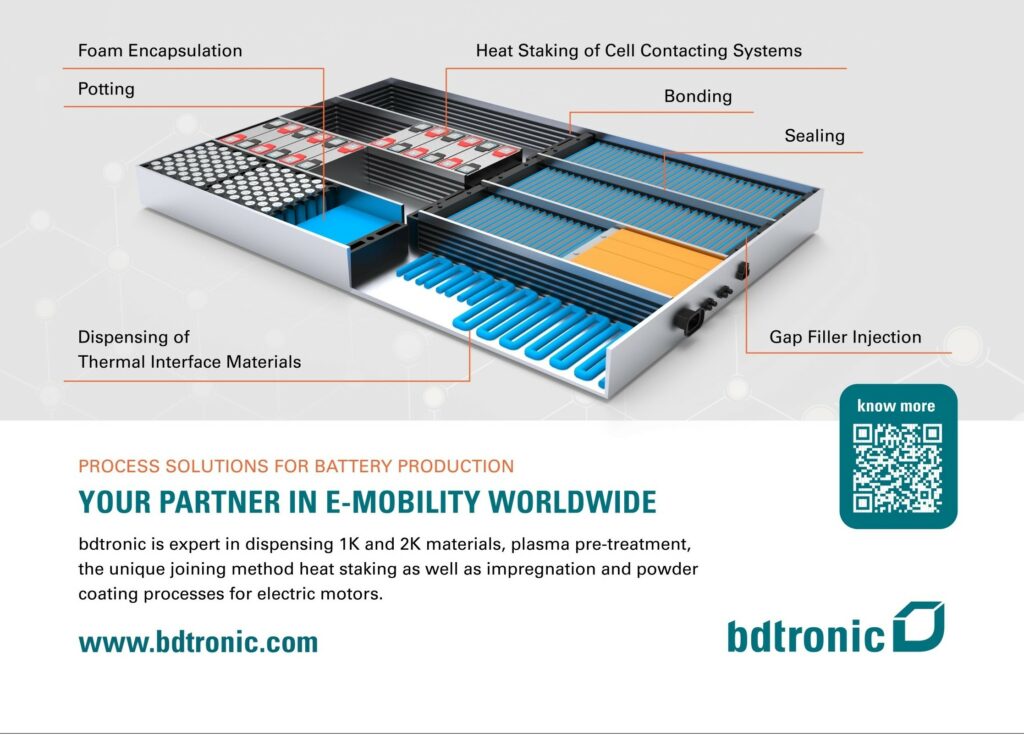
Testing for leaks
Leak testing is vital because it helps to ensure the safety and reliability of electric vehicle (EV) batteries. Leaks can allow moisture, dust or other contaminants to enter the battery and cause problems, from reducing performance by corrosion to increasing the risk of a thermal event.
Dust and other contaminants can block the battery’s cooling system, leading to overheating and a shorter battery life. If moisture creates a short circuit, it could render a vehicle inoperable.
For these reasons, it is important to perform leak testing on EV battery packs to ensure they are safe and reliable. This can be done using a variety of methods, from pressure testing to vacuum testing. With a pressure test, the battery pack is pressurised with a gas, and any leaks are detected by the loss of pressure. With a vacuum test, the pack is placed in a vacuum and any leaks are detected by the inflow of air.
A helium leak check pumps helium inside the battery case and uses sensors on the outside to detect any leak points. This is an important part of the quality control process for battery packs for all kinds of e-mobility platforms, from EVs to construction equipment and the EV take-off and landing (eVTOL) aircraft that are now being certified as airworthy.
By ensuring packs are leak-free, EV battery engineers can help prevent thermal events, reduce the risk of batteries failing and extend their lifespan.
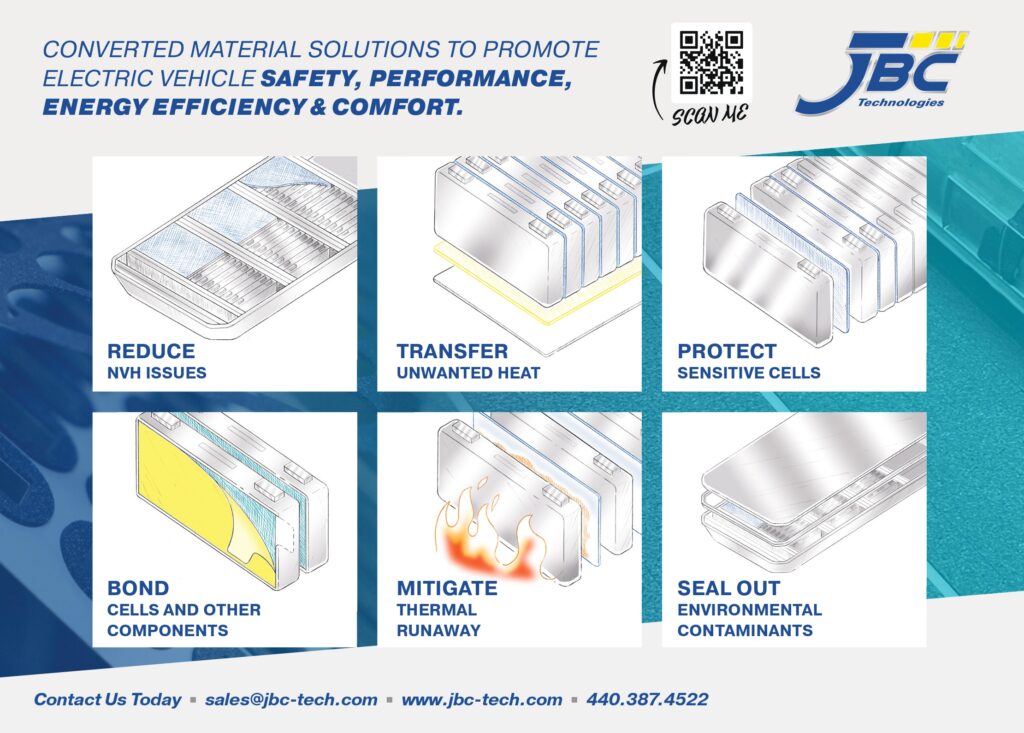
Three-way vent valve
A three-way vent valve has three unique functions: a battery case leak-check mechanism, and passive and active venting to supply overpressure relief for the vehicle’s battery pack.
Unlike traditional testing methods, where a valve is left off to conduct leak testing and then replaced, the three-way vent allows testing through the valve, so the entire battery pack is tested while fully assembled.
Some solutions require several breathing valves on the battery pack casing, which must be masked off before testing, but the three-in-one design meets all flow requirements and overpressure relief with just one valve, so no masking is needed.
The battery case leak-check feature eliminates the need to install the vent valve as the final step of the battery assembly process, which is standard in today’s EV architectures. It is also more thorough than traditional methods, as it includes testing the sealing surface of the vent itself when the battery vent valve is already assembled.
A custom tool actuates the leak-check mechanism on the assembly lines, allowing for testing through pressurisation or a vacuum, which ensures a proper seal to improve safety.
Sealed battery enclosures must compensate for temperature and pressure changes, and they keep water and dirt outside the pack. The vent prevents the enclosure from exceeding a pressure that would cause catastrophic failure during a thermal runaway event, when gases and heat are generated quickly. A battery thermal runaway situation can occur when individual cells inside the unit fail through physical impact or a short circuit. This is where the rising temperatures and pressures released by cells exceed the venting capability of low-flow breathing vents.
The battery vent valve can be precisely designed to meet specific opening pressures and optimise venting. Developers can specify low opening pressures in contrast to the conventional, burst-valve technology commonly used today, and a low-flow breathing mode that allows air to move through porous material to normalise pressure during regular operation.
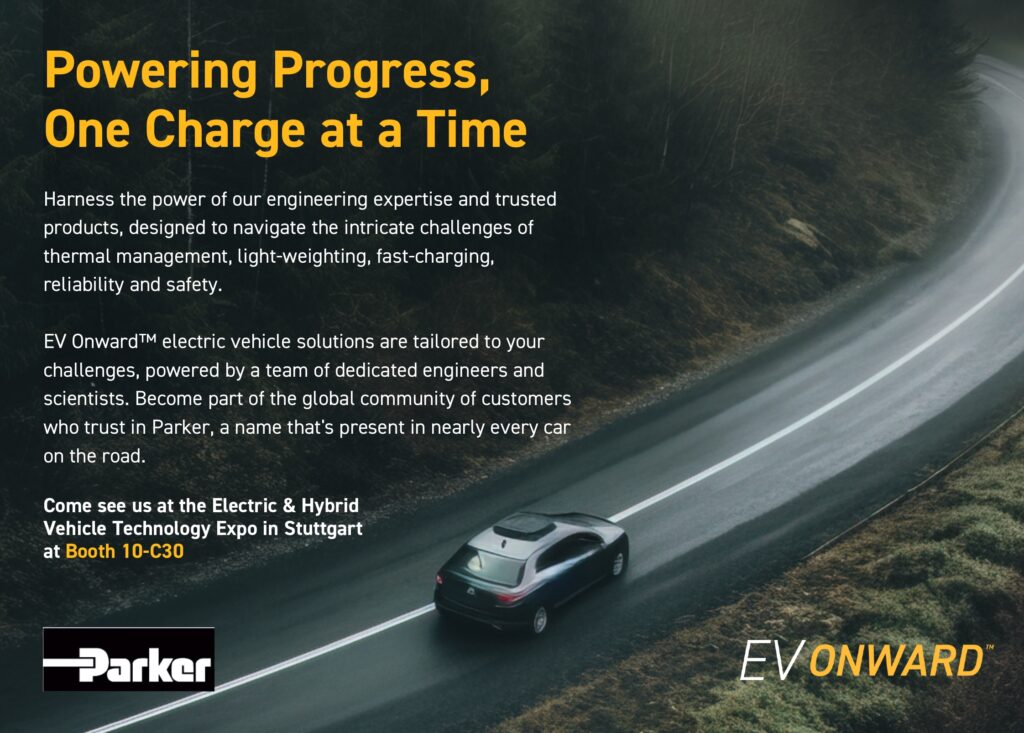
The battery vent valve can be assembled through a robust, quick-connect feature or by a screwed-on, metal-to-metal connection, which gives developers flexibility while ensuring a sturdy connection that stays in place.
A hydrophobic membrane always allows the passage of air in and out of the battery case, but it will not allow liquids or dirt to enter. Also, the valve is made of materials that meet a UL94 V-0 rating, a standard set by United Laboratories for testing plastics and rubber for flammability. Meeting a V-0 rating is the most stringent rating and means the materials can withstand a vertical flame test, which is required by most customers.
This porous membrane maintains the pressure within the battery case at atmospheric pressure. To meet the ISO standard for ingress protection, all sealing mechanisms within the valve must not allow the passage of debris or water.
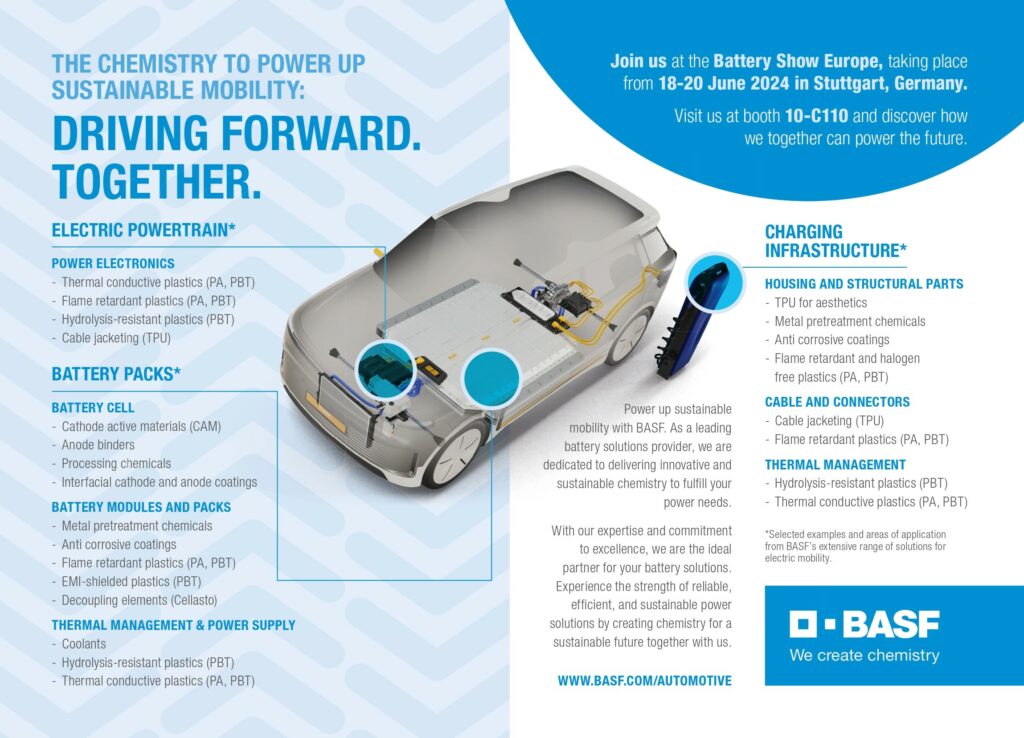
To maintain the ability to contain debris within a battery case in the event of thermal runaway, the three-in-one valve can include a metal mesh.
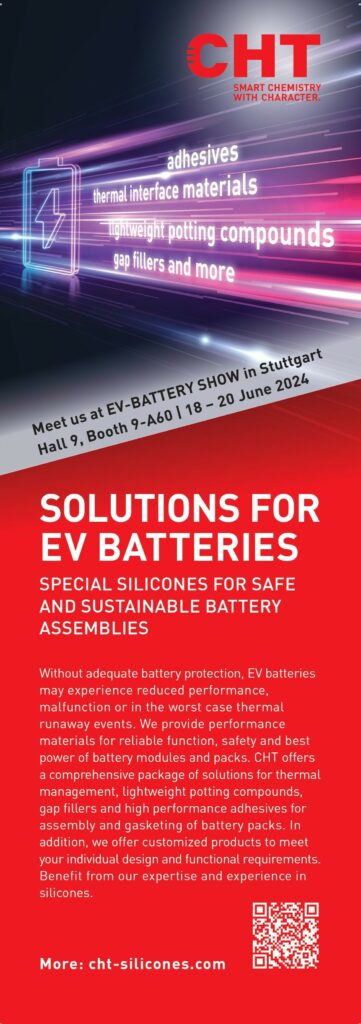
Tape sealing
Keeping the battery pack sealed from external elements is key to an EV’s performance and longevity. Seals range from foam-in-place gasketing and silicone foam rubbers to
butyl-coated PVC and micro-cellular polyurethane (PUR) foams. These can protect batteries from the external environment with low-compression and fire-blocking solutions.
EMI gaskets
Another key element of sealing the battery pack is electromagnetic performance. Preventing high currents from generating electromagnetic noise that interferes with other components is a key requirement in protecting electronic hub cases, displays, telemetric systems, advanced driver assistance system (ADAS) sensors, autonomous vehicle (AV) sensor fusion systems, battery management system cases, and battery chargers and inverters. Nickel, silver and copper sprayable, conductive coatings provide shielding in EV applications, and they are compatible with sensitive plastics that may be used in the assembly of the battery pack.
Outdoor sealing
Since many charging stations are installed outdoors, materials for housing need to be resistant against weather, shock, extreme temperatures, dirt and chemicals. The gaskets used for sealing a battery pack can also be used for charging systems that stay outdoors in all kinds of conditions.
Soft and lightweight silicone foams
provide flame resistance with low toxicity and smoke generation, meeting the highest flame rating of UL94 V-0 in a pressure-sensitive tape form. Multi-functional materials such as a polyurethane foam combine water- and airtight sealing with high conformability, UV resistance, dampening and fire-protection properties, while for sealing up to 70 C, micro-cellular polyurethane foam is a silicone-free alternative for gasket designs in charging systems.
Conclusion
Sealing a battery pack or a charging system requires a range of design trade-offs. Various materials may help to reduce the weight of the pack, but they have issues with how they can be held together.
Plasma processing can help to provide a surface that is more suitable for adhesives or sealants, while hot riveting can tackle a wider range of materials. All of these solutions need inline processes that minimise assembly time for cost-effective manufacturing processes.
Acknowledgements
With thanks to Dr Stefan Reichle at Parker Hannifin, Cedric Zipperlin at PPG, Markus Rieger at bdtronic and Jens Buhlinger at Eaton.
Suppliers list of battery sealing materials, components and equipment
3M
Atlas Copco
bdtronic
Bostik
CHT Silicones
Coroplast
Eaton
Freudenberg Sealing Technologies
Graco
HB Fuller
Henkel
JBC Technologies
Parker Hannifin
PPG
Prostech
Saint-Gobain Tape Solutions
Scheugenpflug
Sika
Universal Science
–
+44 1442 222 350
+49 7934 104 140
+44 1785 272625
+49 7071 154 202
+1 450 378 3995
+1 269 342 3000
+49 6201 800
+32 89 770 847
+1 833 672 1482
+49 211 797 0
+1 440 327 4522
+1 937 278 9431
+41 21 822 3000
+84 984 695 398
+1 949 238 0482
+49 9445 95640
+41 58 436 6800
+44 1908 222211
ONLINE PARTNERS
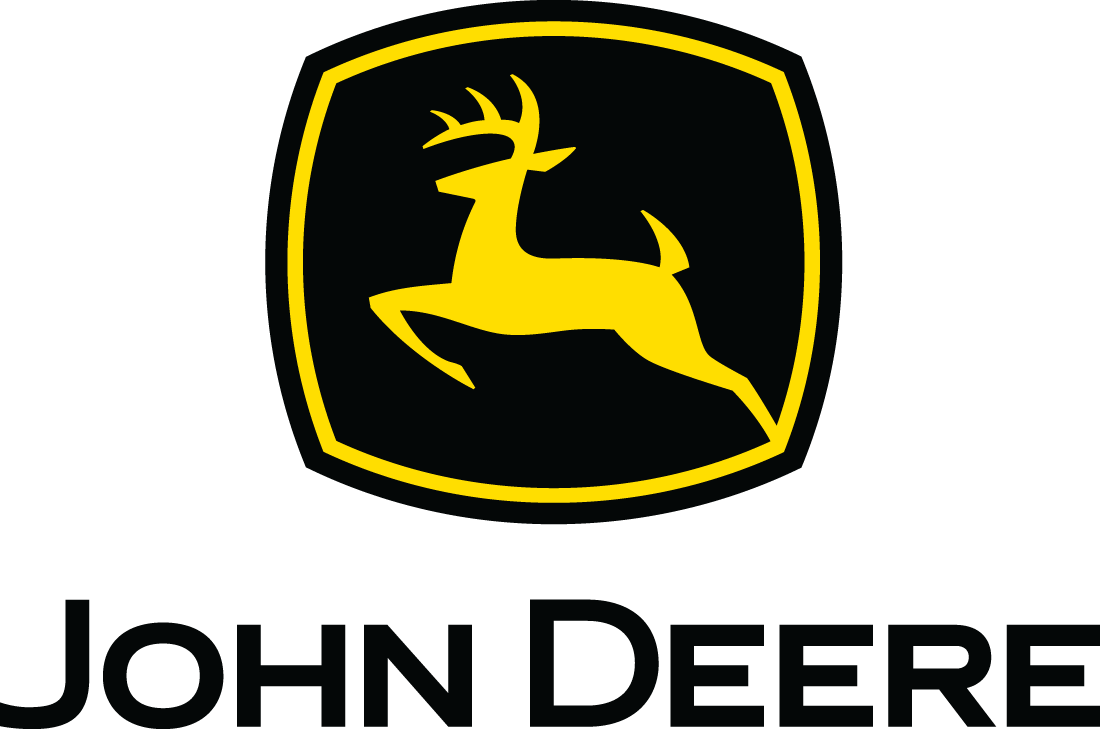
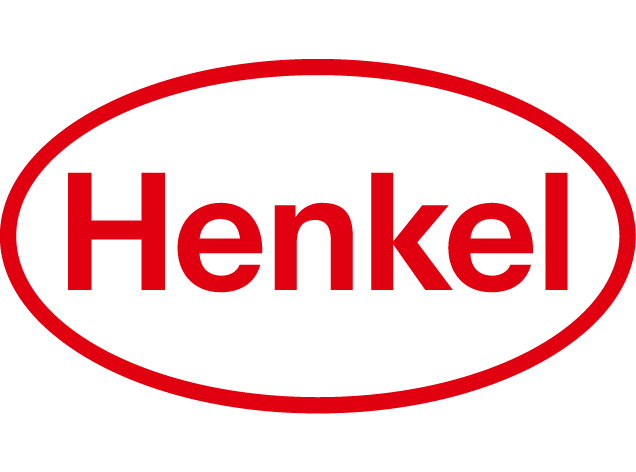
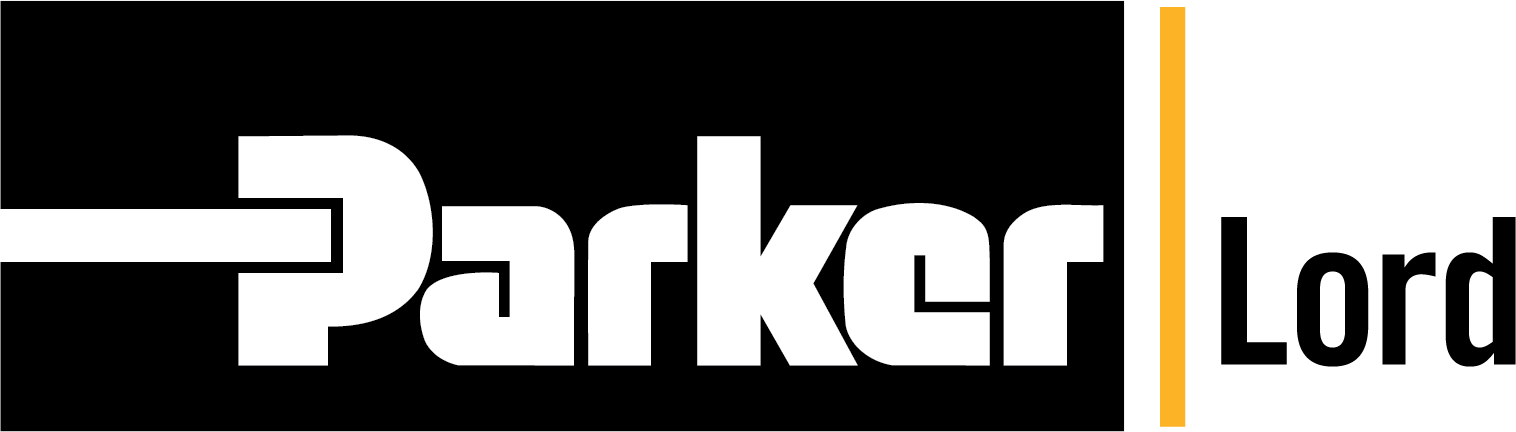
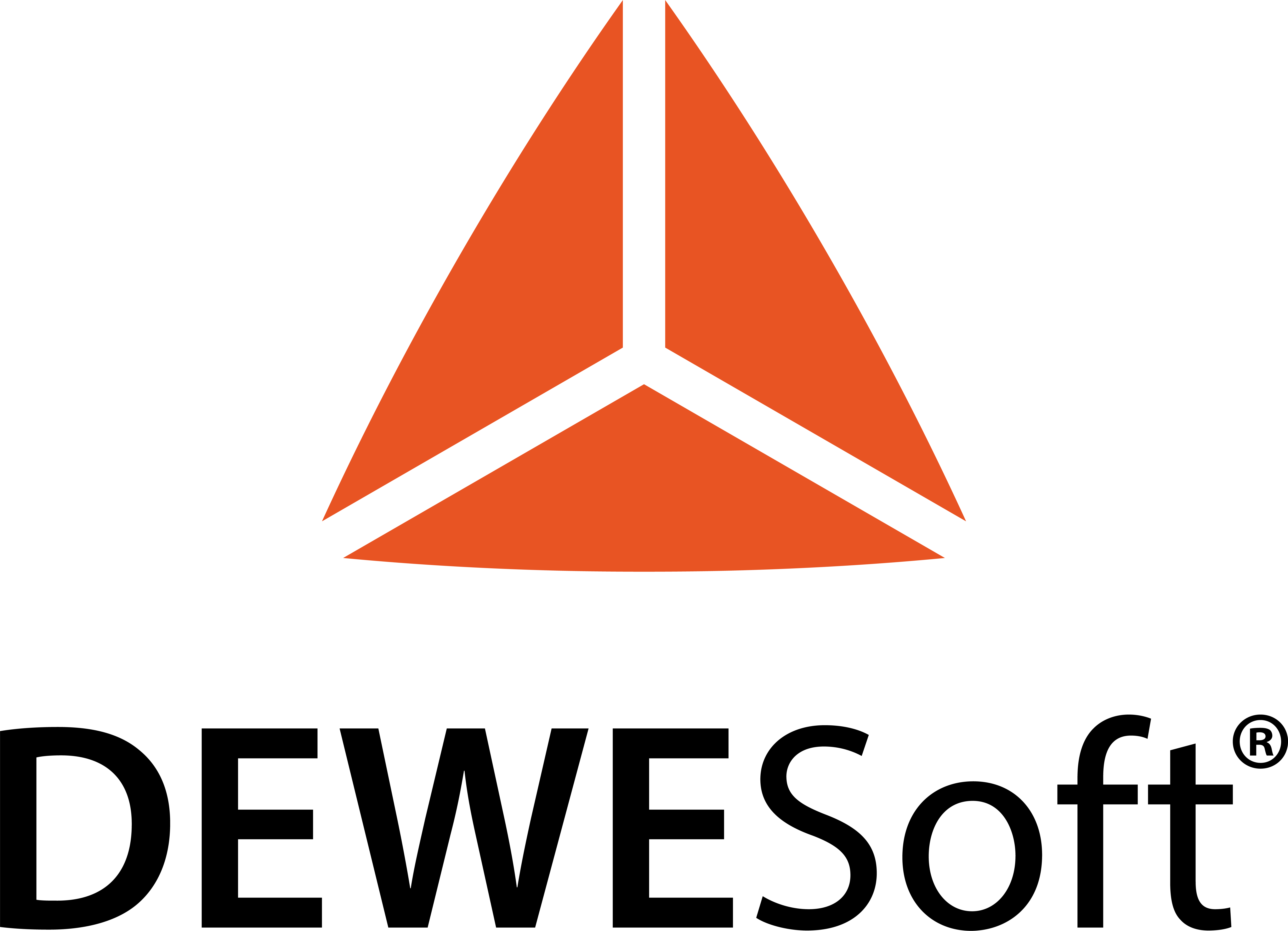
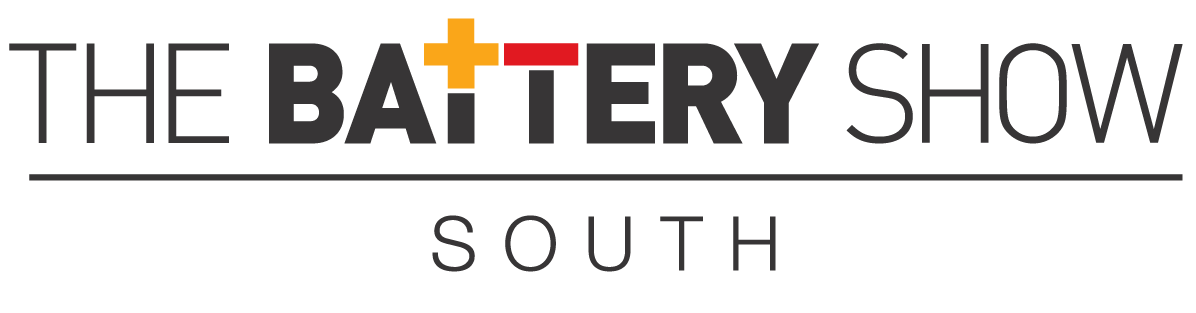
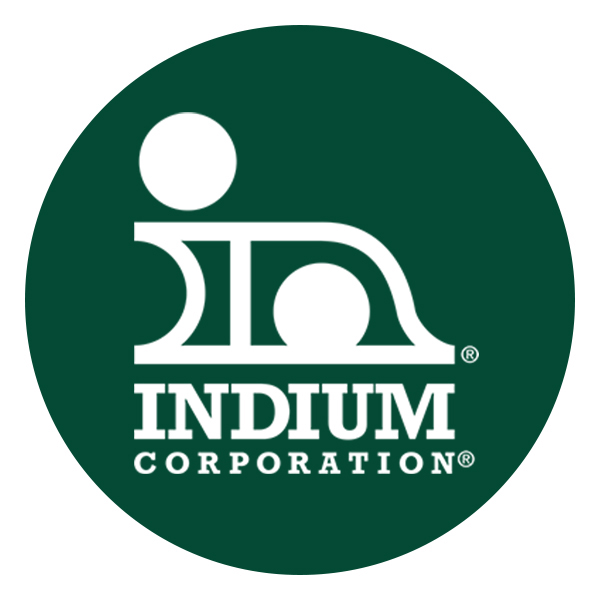

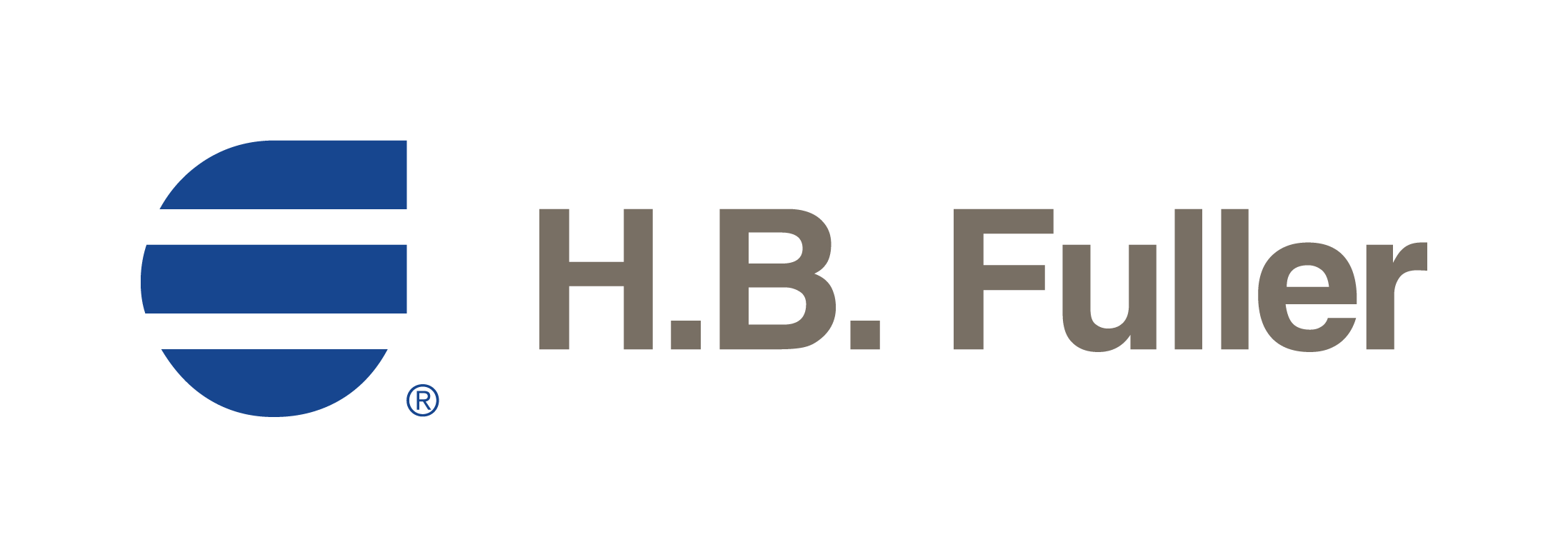
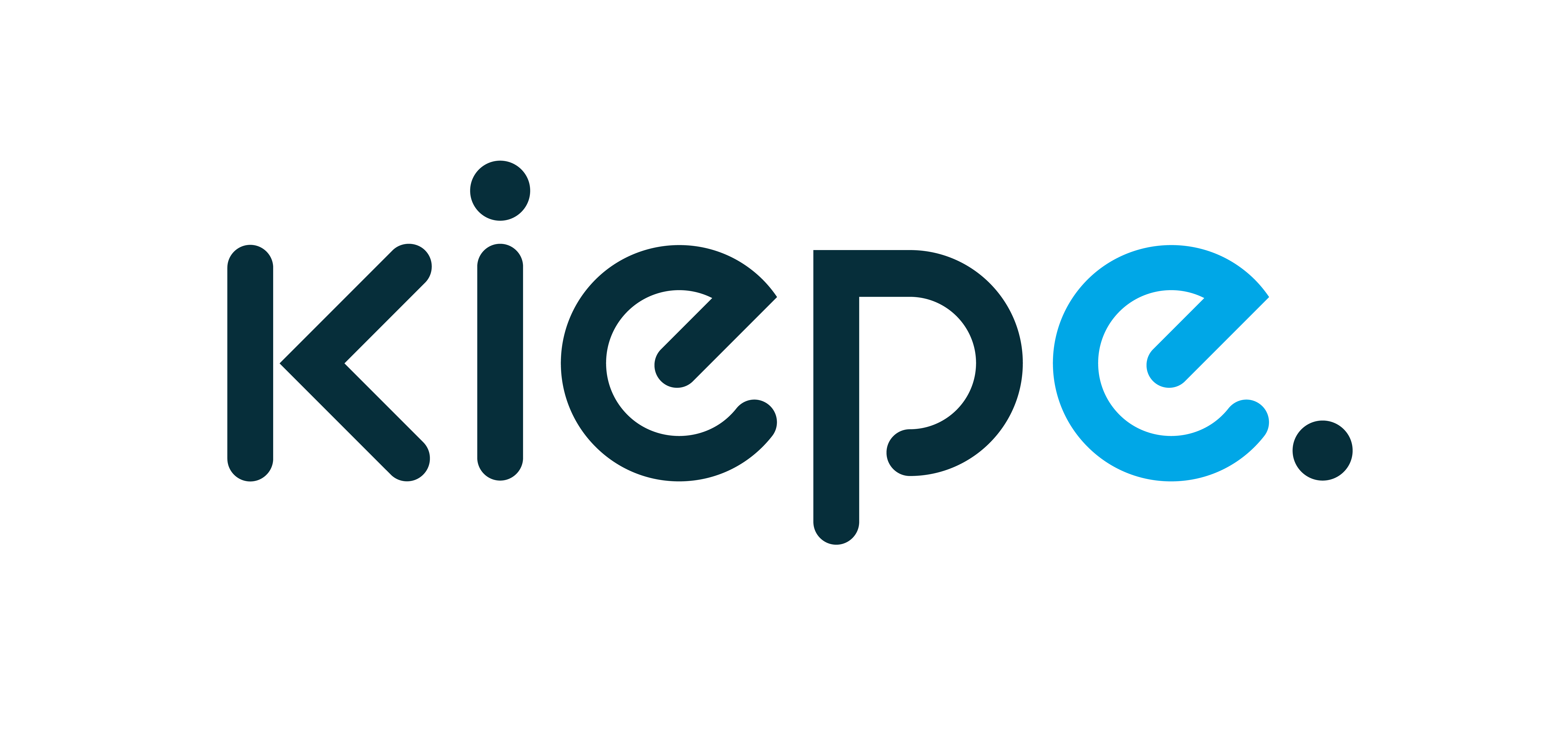
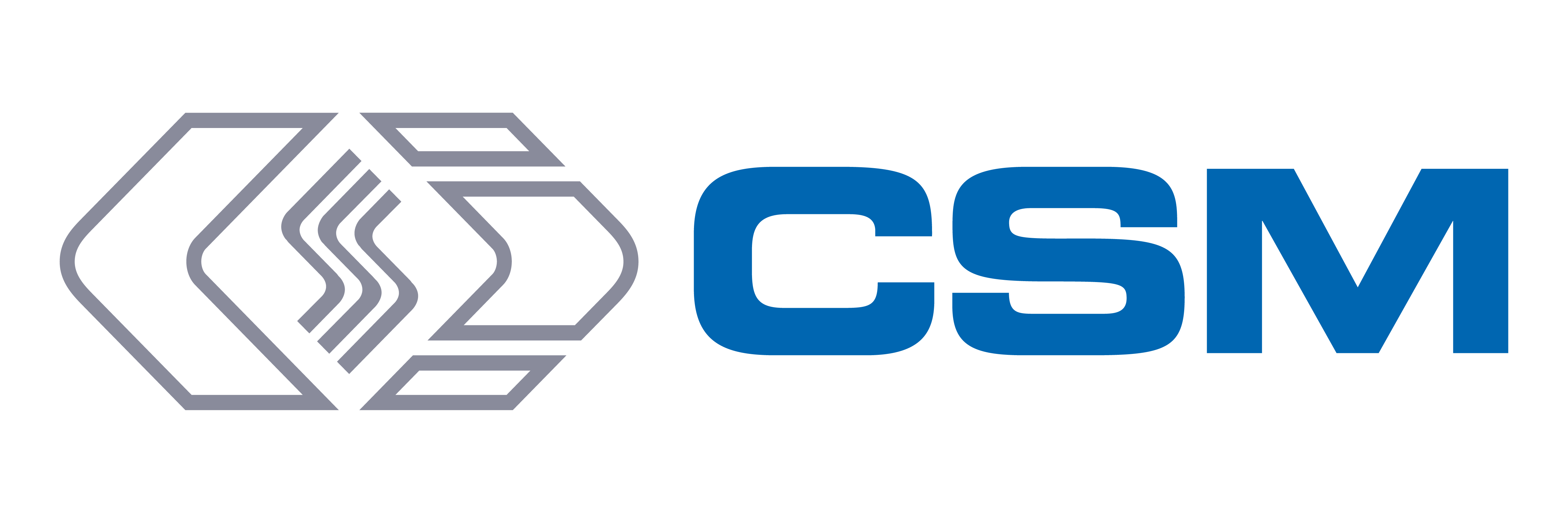