Battery production technology
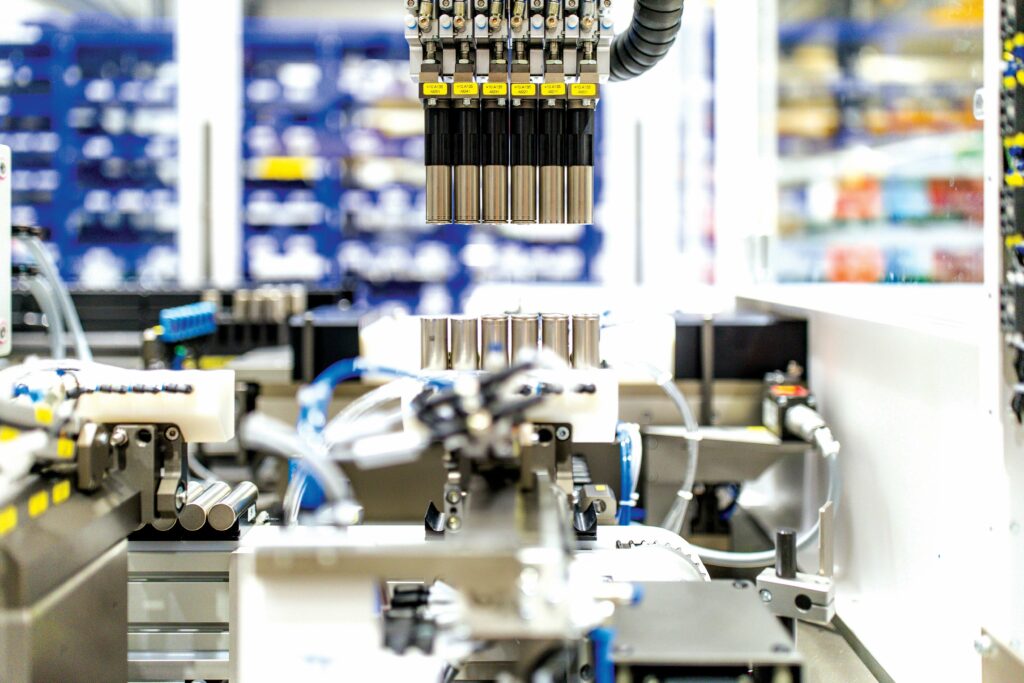
(Image courtesy of Dürr Systems)
Clever chemistry
Peter Donaldson looks at the myriad processes enabling more efficient manufacturing of lithium ion batteries
Manufacturing lithium-ion batteries for e-mobility applications is a complex, costly and capital-intensive undertaking, involving multiple processes and consuming large amounts of energy and time. The process involves several critical steps, each requiring precision and advanced technology to ensure a battery achieves its design performance, safety and longevity goals.
Material preparation is the first stage and it starts with the procurement of essential raw materials, such as lithium, cobalt, nickel, manganese and graphite, from which cathode materials such as lithium nickel cobalt manganese oxide are synthesised, while the graphite is prepared for anode formation.
In the next stage, electrode manufacturing, these substances are mixed with binders and liquid solvents to create slurries that will form the active components of each electrode – one for the cathode and the other for the anode. Each slurry is then applied to a metal foil (typically aluminium for the cathode and copper for the anode) using techniques such as slot-die coating.
When the coating is complete, the foils are dried to remove solvents, resulting in solid, electrode layers. This is followed by calendaring, in which these layers are compressed to a specified thickness and density to optimise the electrode’s performance and consistency.
The foils are then slit to the required width, and cut to the lengths and shapes required for assembly into cells, then the anode and cathode form the outer layers of a sandwich, with their active materials prevented from coming into contact by a separation layer, which prevents electron flow but allows ion flow between them. This layer is typically a coated polymer.
For cylindrical cells, the electrode and separator layers are wound into a ‘jelly roll’ form, while they are stacked to make the cores of prismatic and pouch cells. The cell cores are then inserted into their containers, which are injected with electrolyte to enable ion transport between the electrodes before sealing.
Pouch cells generally have polymer envelopes that are heat-sealed, while cylindrical and prismatic cells have metal cans that are sealed by welding. At this stage, sealing is not complete as a vent is left for the removal of gases during the formation and ageing processes that follow.
Formation is the initial cycle of charging and discharging to form the solid electrolyte interphase (SEI) on the anode, which is critical for the battery’s performance, capacity retention and service life.
A good SEI is essential to provide a combination of electrical insulation and ionic conductivity. It needs to be thin to minimise the loss of cyclable lithium ions, and mechanically stable to accommodate expansion and contraction during charge/discharge cycles. Finally, the SEI is essential to inhibit the growth of lithium dendrites that could cause internal short circuits. Gasses generated during the formation process must be discharged safely.
The purpose of ageing is to ensure the electrolyte completely wets the anode, cathode and separator, and to allow the SEI layer to stabilise, and to extract residual gases before the cells are sealed. The process normally takes several weeks, depending on factors such as temperature and the formation protocol.
The next step is assembly of the cells into modules and then into packs, or directly into packs in the case of cell-to-pack architectures. At this stage, the cells are connected in groups in series to achieve the required voltage, and these groups are connected in parallel to achieve the required capacity.
While battery production can be improved with better machinery, the entire process can benefit from an extension of the digital-twin concept, according to Roland Echter at ATS Industrial Automation.
“Where digital twin refers to the virtual replication of a single machine or device within a digitalised environment, ‘system twin’ is the 3D digitalisation of the entire production line at a system level, including all the individual machines and devices contained within that line,” he says.
“This enables the complete system and components to be simulated in a virtual environment, driving significant time and cost savings, and speeding time-to-market for battery manufacturers by accelerating development, mitigating risk and streamlining on-site commissioning of the line.” More on that later.
Developments in battery production machinery are focused on efficiency, scalability, quality and sustainability.
The implementation of a continuous process, from mixing to ageing, including the ability to track and trace individual cells in modern gigafactories, is one of the latest advances, says Jörg Rottkord, global industry manager, automotive, at Beckhoff Automation.
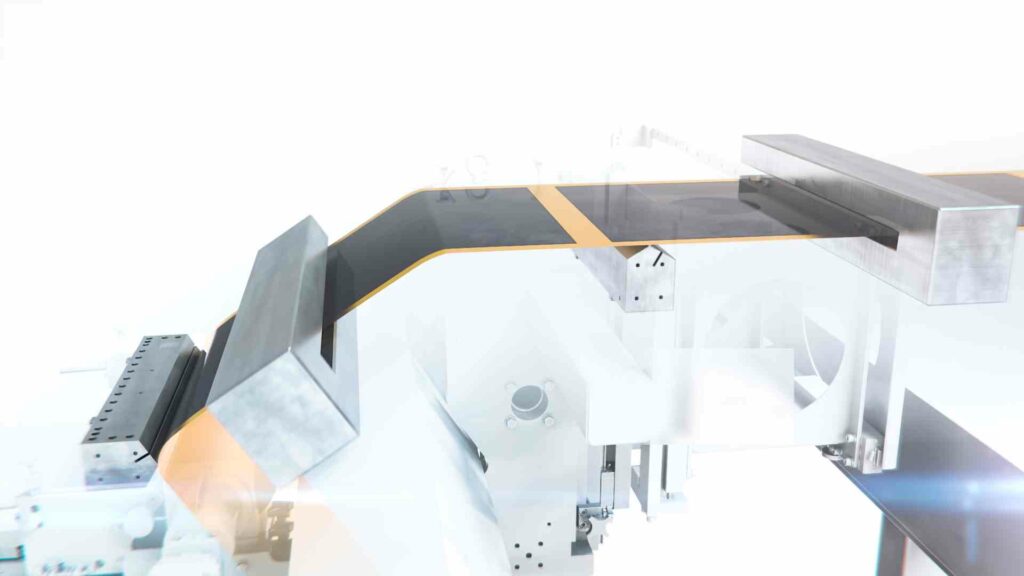
(Image courtesy of Dürr Systems)
Continuous mixing
In mixing, conventional practice is to prepare electrode slurries in discrete batches, which is suited to small-scale production and custom formulations. The alternative for volume production is continuous mixing; innovations aim to achieve more uniform electrode slurries, in turn improving the quality and consistency of anodes and cathodes. The use of high-performance, twin-screw extruders is coming to the fore.
“This process enables more efficient production with highest-end product quality and minimal waste. In addition, it gives manufactures high flexibility regarding recipe and the electrode production process itself, producing slurries or electrodes in a semi-dry or dry process,” says Massimo Bernert, sales manager at Coperion.
“We see a growing demand in highly accurate feeding to optimise both active material production and continuous manufacturing of battery masses. The precise feeding of ingredients plays a crucial role in the process.”
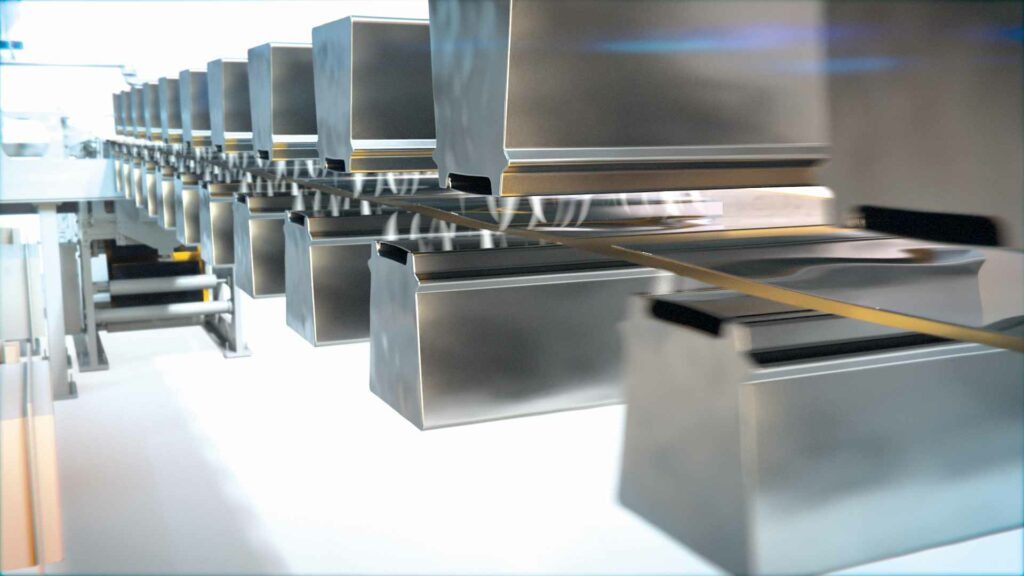
(Image courtesy of Dürr Systems)
Two-sided coating
As well as speeding up the process, advances in slot-die coating are intended to enhance precision to create electrode layers that are as uniform in thickness as possible, which improves battery performance and reduces waste.
Dürr has developed a simultaneous, two-sided coating process that features a straight-path product flow through a single coating station, offering unique benefits, such as a smaller manufacturing footprint and no edge curl after drying.
Bernhard Bruhn, vice-president of the lithium-ion battery global business unit at Dürr Systems, says the process consists of slot-die coating on a backing roll and tensioned-web, slot-die coating of both sides of the foil in one pass.
He says the simultaneous coating process optimises drying. Air bars suspend the coated film to protect it from damage, while an even circulation of warm air on both sides creates a floating cushion effect, ensuring there is no contact with the film in the dryer. Measuring systems check the basis weight to ensure the film is completely dry. The need for post-processing steps such as smoothing is eliminated.
Space and energy savings are the main efficiency drivers associated with this process. It simplifies the coating by positioning the coater and dryer on one level, reducing the required ceiling height by about 5 m and improving access, he explains. Drying both sides of the electrode at once also saves energy.
French calendaring specialist Ingecal, part of Dürr group since 2023, uses ‘dynamic gap control’ for closed-loop handling of coating thickness, based on accurate measurement. This enhances energy density and performance.
Turning to winding and stacking machinery for cylindrical and prismatic/pouch cells, respectively, progress is also being directed towards greater speed and precision.
Beckhoff’s cylindrical cell winding-control systems are based on a central, PC-based automation platform that controls vision systems, motion tasks and communications to inputs and outputs (I/Os) with a high level of synchronicity, which enables high-volume output and great accuracy, the company explains.
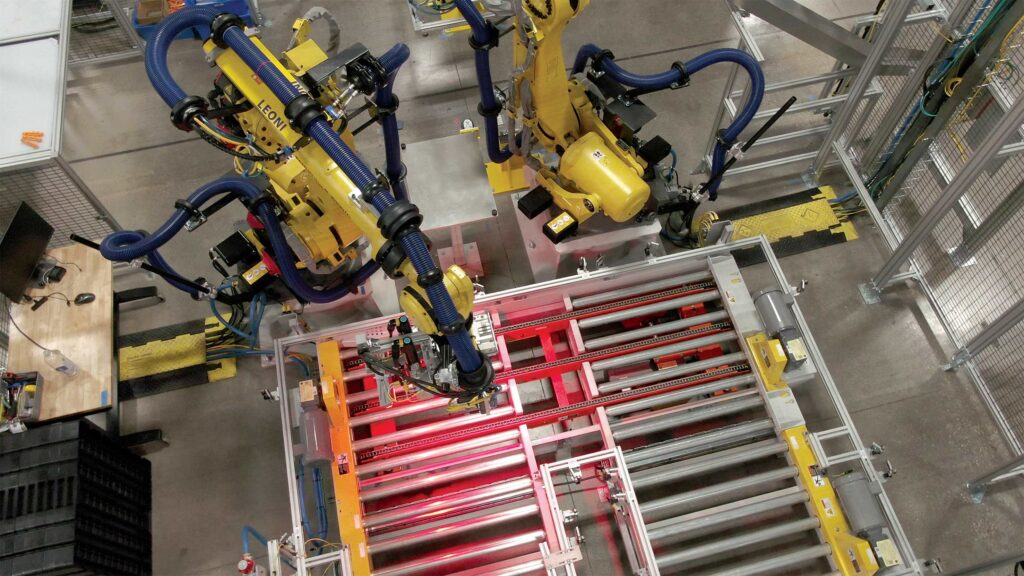
Efficiency and quality
The way data is handled has a big impact on quality, says Beckhoff’s Rottkord: “The fact that process data, parameter sets and recipe data, besides diagnostics and measurement, can all be handled on the same control unit make the systems more seamless, reliable and scalable. Potential problems are detected immediately and can be reacted to right away.”
Virtualisation technologies such as system twin are intended to improve efficiency, throughput and quality by enabling battery manufacturers to benchmark the performance and troubleshoot automated production systems before their lines are built, says ATS Industrial Automation’s Echter.
“By identifying and mitigating risks before physical build, battery companies can develop more cost-efficient processes that have a higher throughput,” Echter says. “What’s more, they can test and optimise these processes as often as needed within the simulated environment. They don’t need expensive physical parts or prototypes for testing.”
System-twin technology can be used to mitigate the risks inherent in designing, testing and commissioning a battery line, and also cut costs and lead times.
“Both system twinning and digital twinning of individual machines can enable error handling and the offline programming of robotics, programmable logic controllers (PLCs) and third-party equipment to debug and troubleshoot errors early on in the design process. What’s more, system twinning can also run in parallel with live production lines, making it possible to test, validate and apply continuous improvements without machine downtime,” says Echter.
Improvements in throughput, efficiency and quality can also be achieved through the continuous mixing of active electrode compounds, says Coperion’s Bernert. When combined with high-accuracy feeders, twin-screw extruders offer good process stability, precision and reliability. Further benefits include a reduction in the space and number of people required, compared with batch-mixing processes, as well as less downtime and lower costs.
Generating a specific torque of 18 Nm per cm3 of mixture volume, the company’s ZSK Mc18 twin-screw extruder offers highly dispersive mixing and high throughput. Subsequent distributive mixing ensures the high level of homogeneity required in electrode compounds, he says. “The process section’s modular construction allows for flexible and individual modifications to recipes and changes within the process.”
ZSK twin-screw extruders can mix and output materials that are completely dry. Accurate feeding of PTFE is critical and such expertise is provided by Coperion’s K-Tron division. “Key to achieving this is the capability to thoroughly test feeders and their refilling devices,” says sales manager Keith Melton. “Coperion is developing a new technology to distribute mixed, dry electrode masses evenly across electrode foils during the calendaring process.”
Dürr is creating sustainable and alternative drying technologies for processes involving liquids. Laser drying of wet-coated electrodes shows significant potential due to its high energy densities and heating rates, resulting in significantly improved energy efficiency and quick process control. Bruhn says: “The main trend is developing technologies for dry coating. Initial lab and pilot productions have proven this technology works, but the challenge lies in scaling up these technologies and the equipment for mass production.”
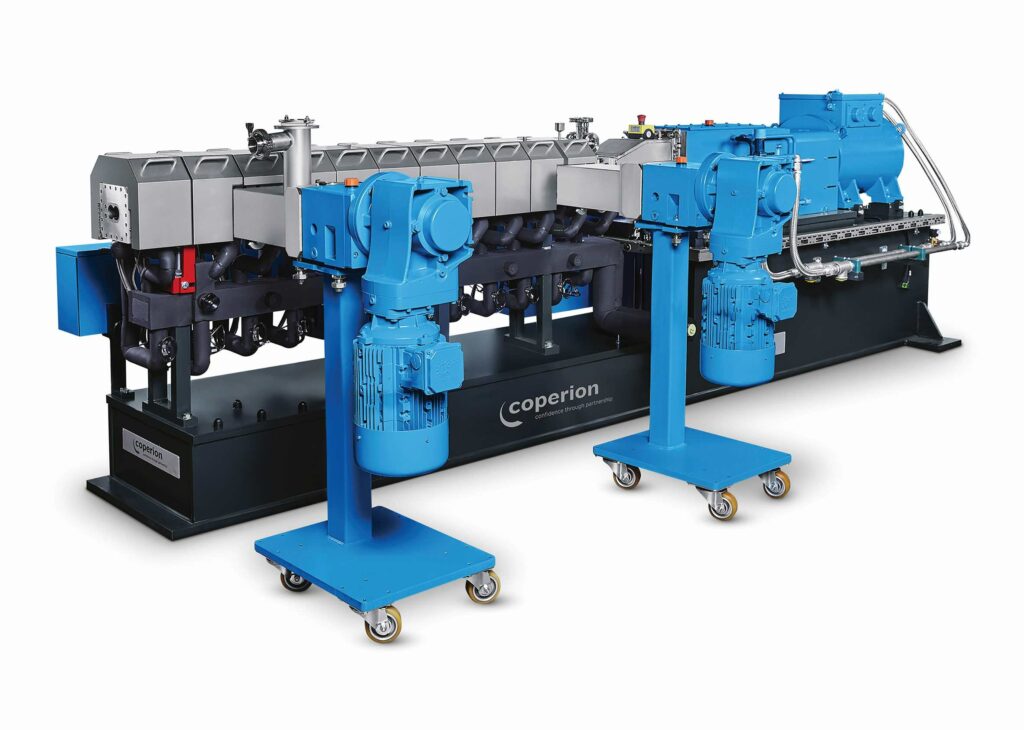
(Image courtesy of Coperion)
Targeting waste
Reducing material waste and energy consumption is another area in which system-twin virtual simulation technology can help, says ATS Industrial Automation’s Marie Kühnast.
“By running quality control scenarios to test for possible failure points on the simulated line, companies can modify and correct for potential failures in a risk-free environment,” she says. “It is then a matter of implementing accurate inline quality processes, based on those validated optimisations. This will allow defects to be identified for rework rather than scrap.”
Once the production line is running, monitoring and intelligence software, such as Illuminate from ATS Global Service, can diagnose overall equipment effectiveness (OEE), identify high scrap rates and energy wastage, and plan for maintenance downtime, Kühnast adds.
More accurate and efficient end-of-line testing can reduce part-scrap, and the associated energy costs of having to build a replacement part, says ATS Industrial Automation’s Marco Melischko.
Electrode drying is a big energy consumer in battery manufacture, so the dry and semi-dry processing of twin-screw extruders is an effective means of reducing it. Coperion’s Bernert says the ZSK extruder’s interlocking, intermeshing twin screws have constantly high conveying efficiency, while their self-cleaning function minimises residual material in the extruder.
The use of accurate metering equipment such as K-Tron’s loss-in-weight feeders improves material efficiency and reduces waste.
“The interplay between mechanical construction, the latest weighing technology and advanced control is critical for achieving highly accurate feeding performance,” says Melton. “Precise control and process data on the bulk material allow manufacturers to profit not just from adherence to precise formulation, but also from less maintenance and downtime.”
Dürr has implemented closed-loop controls and inline quality measurements, significantly reducing scrap rates, energy consumption and pollution in electrode production. “Our drying ovens can be designed to use electricity, which helps reduce exhaust gases,” Bruhn says.
“We achieve a 99.8% solvent recovery rate, helping to protect the environment by preventing harmful emissions. Furthermore, the recovered solvents can be distilled to electronic-grade purity, with 95% reuse of the solvents in the process.”
Even state-of-the-art battery and electrode manufacturing show potential for increasing yields to reduce scrap and energy consumption, he adds. “Automotive-grade quality standards have not yet been widely introduced. Accurate coat-weight measurement technology is evolving.”
Another enabler Bruhn mentions is end-to-end digitalisation of the production process to offer transparency and optimisation insights.
Maximising output with less energy consumption and waste also depends on a responsive automation and computing environment, Beckhoff’s Rottkord says.
“Short control cycle times in combination with a fast and efficient fieldbus protocol (like the widely accepted EtherCAT fieldbus system) lead to fast transitions in the programmable logic controllers and motion-control units, ideally on the same powerful CPU,” he adds.
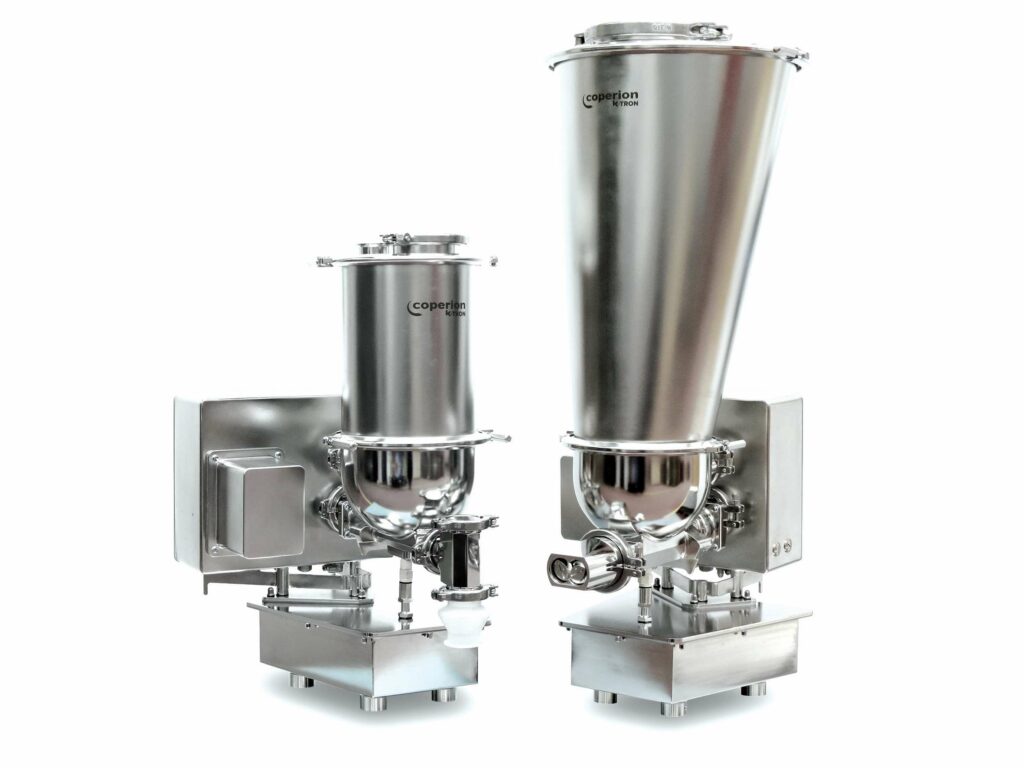
(Image courtesy of Coperion)
Quality control
Quality control is increasingly being integrated into manufacturing processes, characterised by advanced sensors and machine vision, significantly increasing the probability of defects being detected and corrected swiftly.
“With increasing demands on cell performance and durability, end-of-line test systems offer a broad portfolio of electrical, mechanical and optical inspection options,” Dürr’s Bruhn notes. “These include visual cell-can inspection, extensive electrical testing in the cell and pack area, and tactile length measurement in the installed state. Furthermore, 100% inline monitoring of welding and gluing processes is standard in our production lines.”
Battery cell quality and reliability begins before the production line starts, says ATS Industrial Automation’s Melischko. System and organisational control (SOC) checks, and parts/equipment traceability begin during procurement, and they are maintained throughout the supply chain lifecycle.
Traceability and documentation cover in-line and end-of-line testing station equipment, and the tests conducted at each station – these check electrical function, look for leaks, examine protection against liquid ingress (to IPX 6-7) and thermal monitoring, and more.
Where laser welding is employed, an intelligent laser inspection system should be used to ensure no gaps are left and the process is stable. “It’s about using the right testing device and test method at each quality inspection checkpoint,” Melischko says.
“Testing devices and processes need robust data-management systems for configuring test requirements and parameters, maintaining parts standards, enabling traceability and auditing, planning and executing build processes and instrumentation control, analysing production line performance, and more.
“These data-management systems are an integral part of any manufacturing execution system (MES) and provide the basis for accurate quality assurance and performance validation.”
Continuous r&d testing of new materials is essential for maintaining quality and reliability, Melischko adds, especially as key battery parameters such as size, electrical connections and power output change, and advanced technologies such as solid-state batteries are developed.
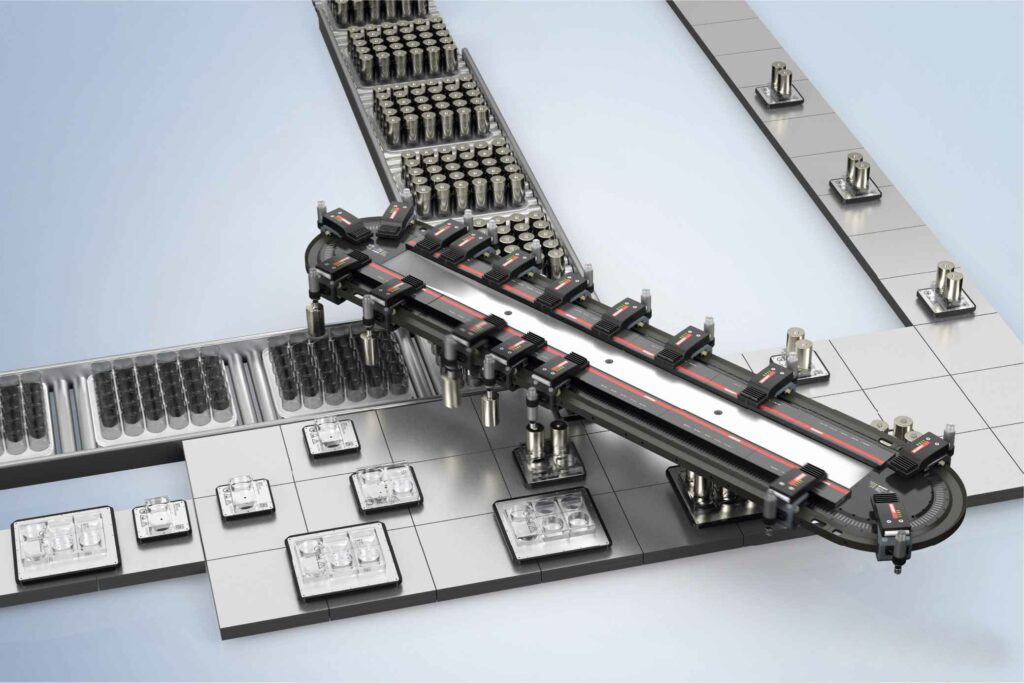
(Image courtesy of Beckhoff)
Automation and robotics
Automation and robotics are already well integrated into battery production lines, says Kühnast. They are focused on high throughput and/or high-precision operations, particularly for assembly tasks that may be unsafe for human operators, with the degree of automation required for efficient production increasing with volume, she adds.
“Automated assembly and testing lines drive value in reducing OPEX costs, while automation and robotics together improve OEE, yield and quality control benchmarks. We are also seeing increased use of automated guided vehicles (AGVs) for transporting large battery packs within the production site.”
A continuous system offers more automation than using a batch process, says Coperion’s Bernert. “System solutions with integrated extrusion, feeding and refilling technologies enable a higher degree of automation.”
The roll-to-roll aspect of electrode manufacturing is mostly automated, except for the loading and unloading of the film and coated material coils, notes Dürr’s Bruhn, and these steps are expected to be automated in the future using AGVs with grippers for coil handling. The additional steps of cell and module assembly, and testing are already highly automated with handling robots.
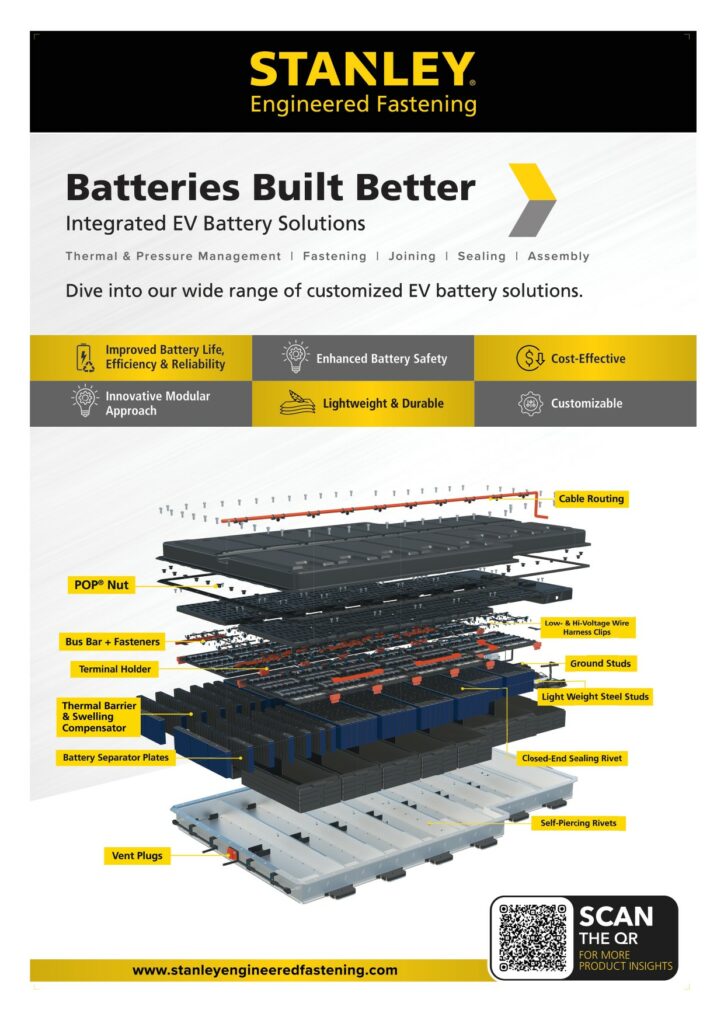
Flexibility and diversity
Implemented correctly, automated systems can improve production flexibility, scalability and adaptability to changing market demands. Here, a standardised and modular approach can be very effective, says ATS Industrial Automation’s Roland Spiess.
“Standardising your machinery, processes and documentation to allow for quicker and more efficient scaling of new lines, as does being modular in terms of the line’s configuration (footprint), and designating spots on the line for embedding future cells and stations. Technologies like system twin can help you plan future production line operations and configurations,” he says.
With flexible automation, different equipment can be easily reconfigured or retasked for new assemblies, with little or no changeover or downtime, he notes.
This principle applies even in the earliest stages of manufacture, including electrode mixing. The process section of all Coperion’s ZSK series extruders are of modular design, consisting of several barrel segments in which the co-rotating screws operate, Bernert says.
“Using this construction, a broad variety of recipes can be produced on one machine by configuring the barrel and screw elements individually,” he adds.
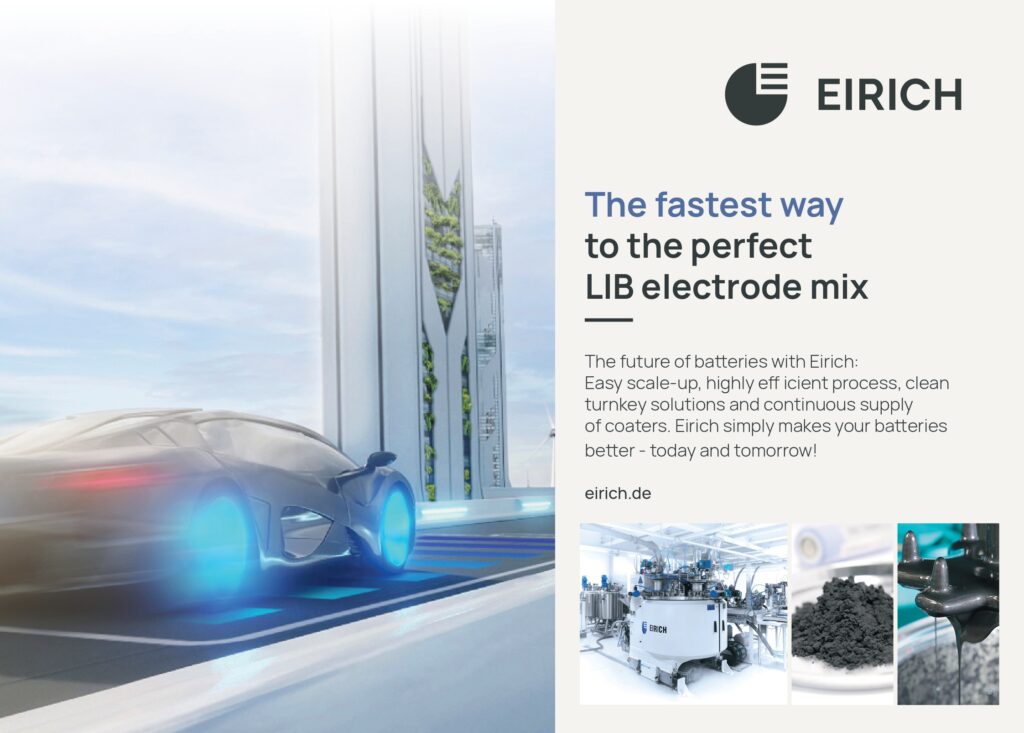
Increasing standardisation in cell packaging and geometry gives automated systems the flexibility to process a wide variety of cells and components with minimal effort, Dürr’s Bruhn adds, while new grippers with adjustable grid sizes and end-effectors enable the processing of a wide variety of products with the same manipulator.
Another flexibility enhancing development is the interconnection of production processes using AGVs, which eliminates fixed connections.
Digitised manufacturing operations management (MOM) solutions, such as that offered by Dürr and iTAC, make process flows more transparent and easier to control, he adds.
Production lines can be adapted for batteries of the same cell format, such as cylindrical cells with different diameters, but they need modifications to handle different cell formats, ATS Industrial Automation’s Kühnast notes.
She adds that while some production requirements are similar across all cell types, such as high-precision laser welding, the specific requirements for each type vary.
These requirements are tied to cell formats – cylindrical, prismatic and pouch – and whether they are handled as individual cells or in modules or packs. There are other factors such as electrical connection schemes and power output that also have an impact on automation, testing and benchmarking requirements.
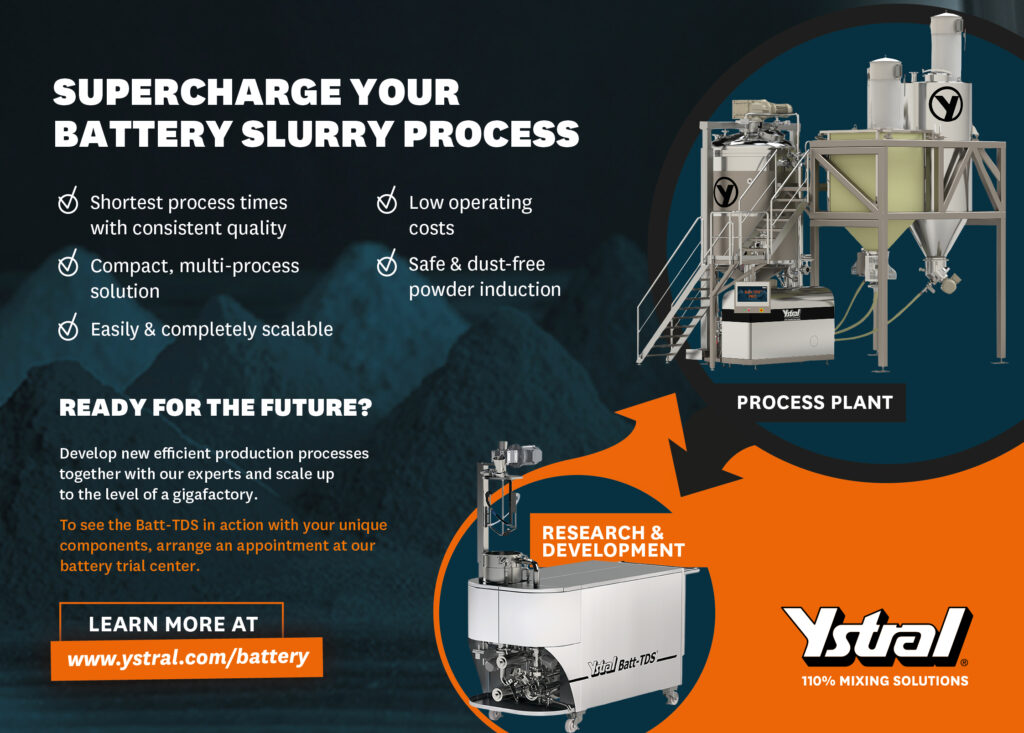
Scaling up
A modular approach to the production line allows scalability to be incorporated directly into its design, Spiess says. Designating spots for future cells and stations to be added ensures they fit within the line’s existing footprint.
Modern tool chains, such as continuous integration/continuous deployment and test-driven development, often better known from the IT world, can easily be used in PC-based automation, as seamless integration is possible and standard interfaces to databases are already included, Beckhoff’s Rottkord notes. “The result is a high-performance, scalable architecture that makes extension of the line and automation system easy.”
Taking a long-term view at the pre-production stage can equip companies for future scalability, Melischko says. “Designing a standardised production line that is modular and flexible in its configuration [means] new CAPEX costs are planned for and readily absorbed. Understanding the right level of automation and identifying future opportunities for adding automation can increase throughput.”
Dürr is involved in the early planning stages for gigafactories, Bruhn says. “We plan and simulate complete, end-to-end factories, balancing throughputs, yields and our customers’ production scaling requirements on a case-by-case basis.”
Gigafactories for cell manufacturing are typically built and extended in steps of 15-20 GWh using largely standardised equipment in modular layouts, he says. “Focusing on overall system efficiency while considering potential strategic challenges or product changes is important for establishing feasible concepts for long-term use.”
Battery manufacture at scale is a rapidly evolving discipline that must be prepared to accommodate profound changes in the product’s core technologies in the design of production facilities – a conundrum that will continue to challenge the industry.
ONLINE PARTNERS
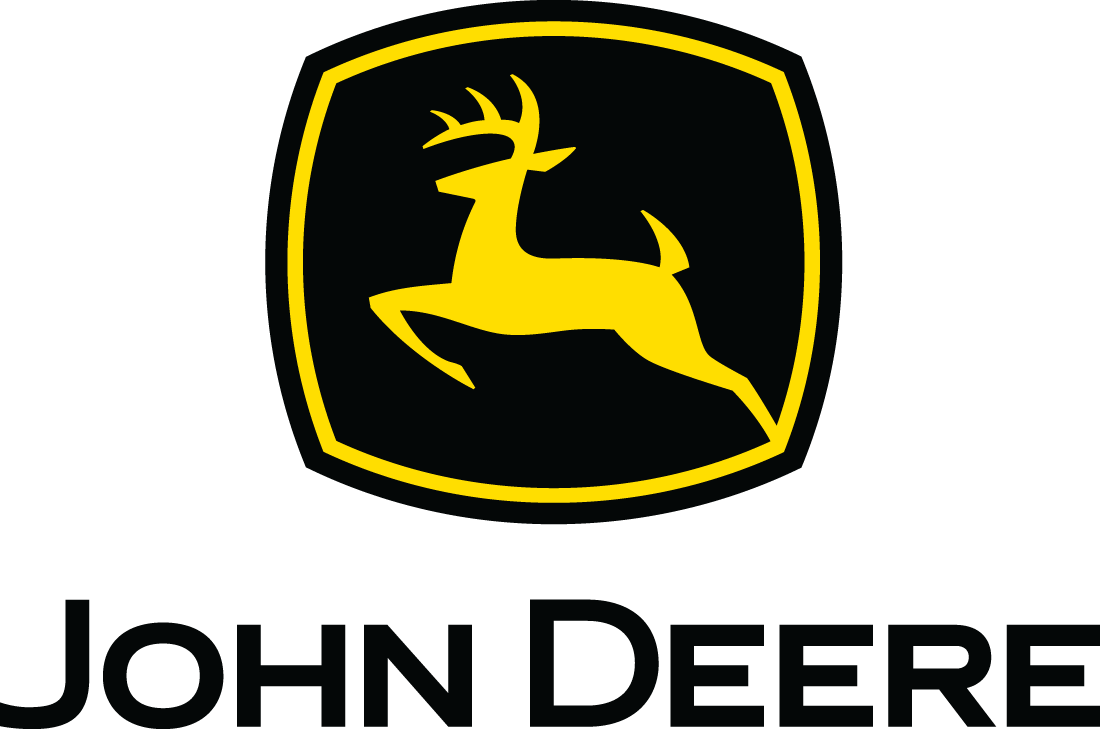
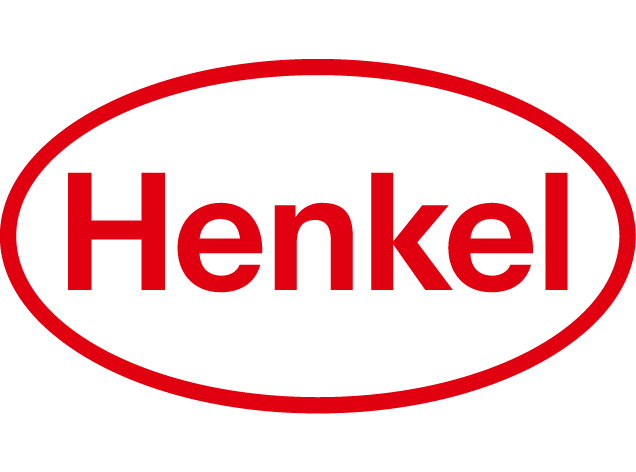
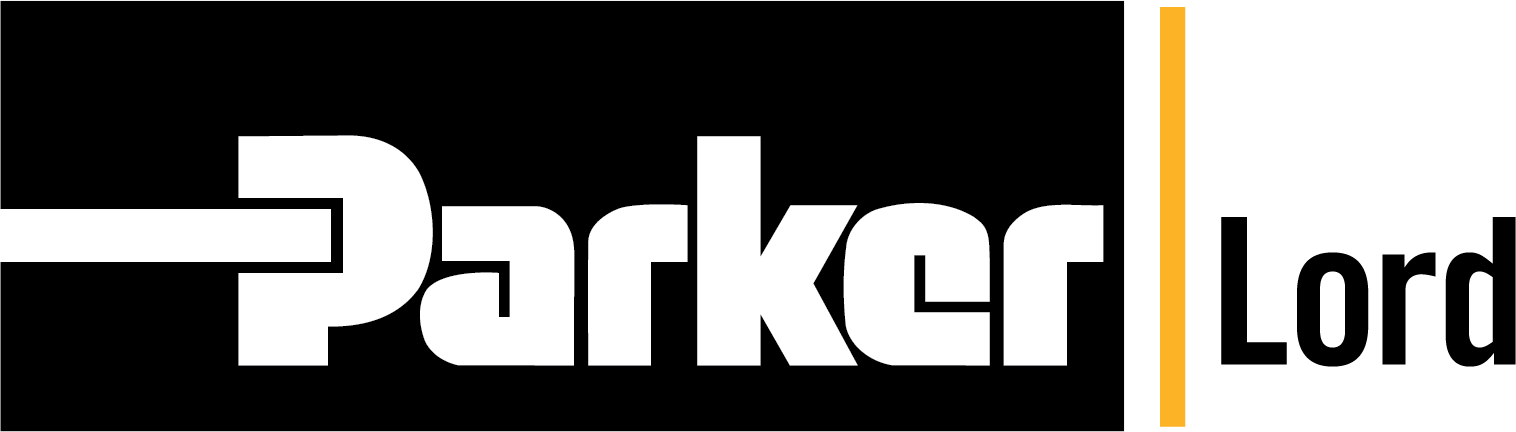
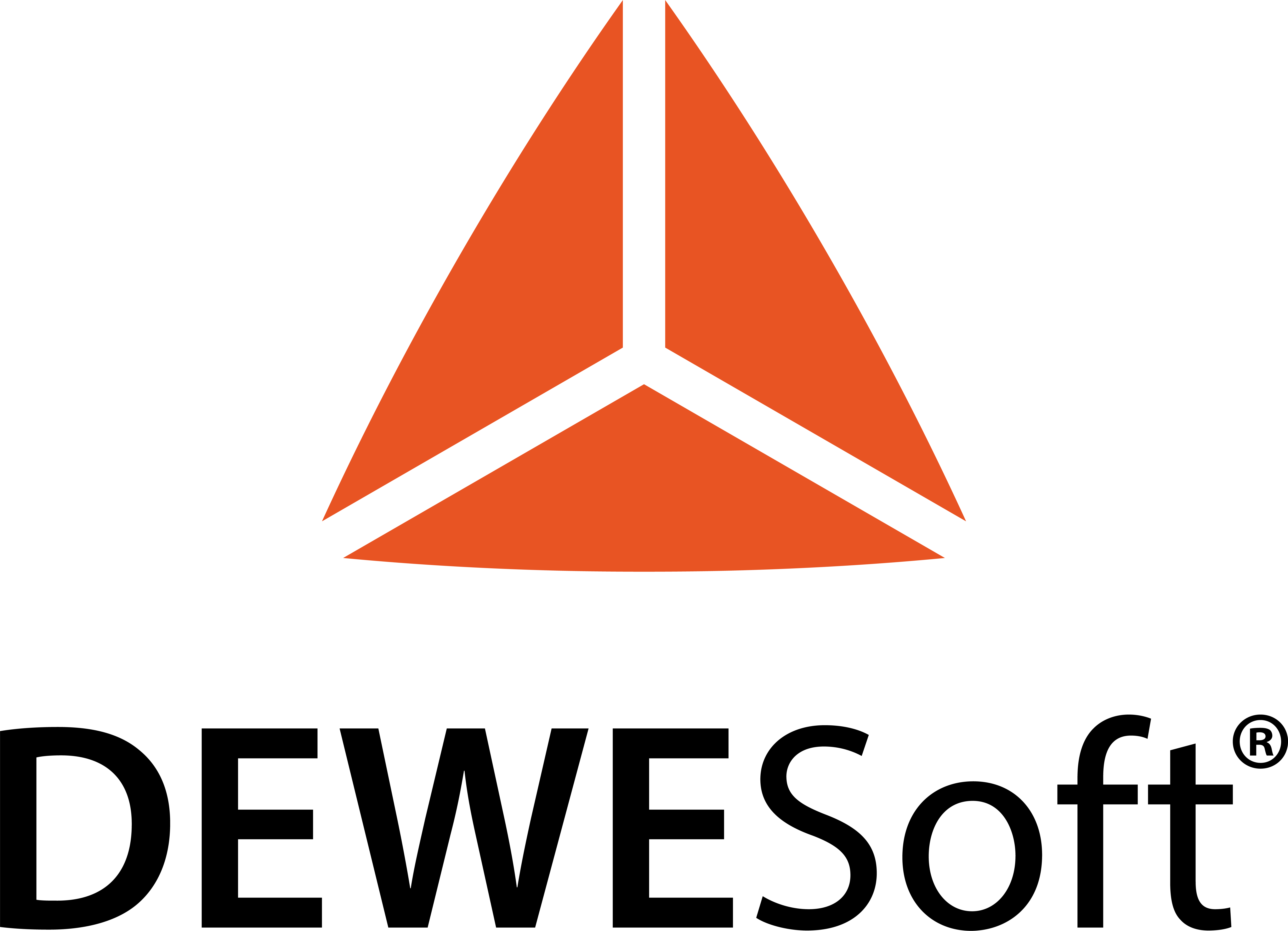
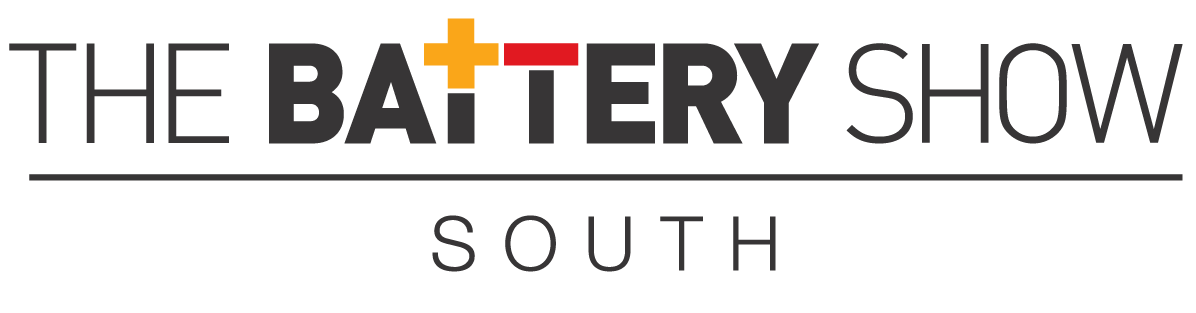
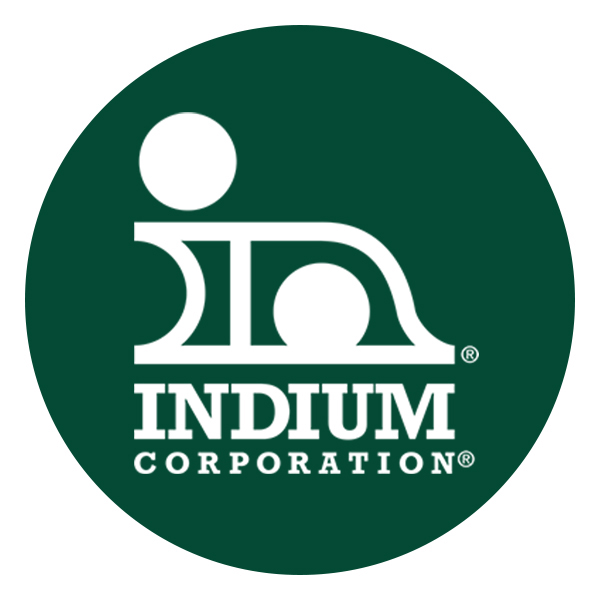

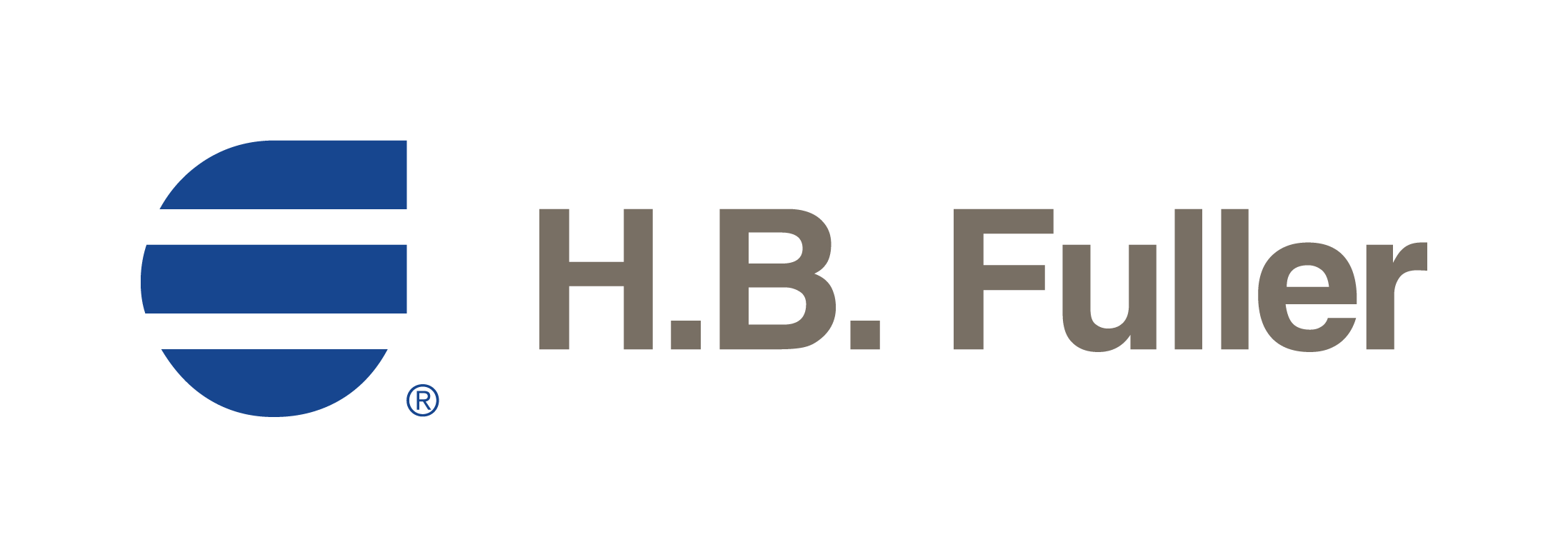
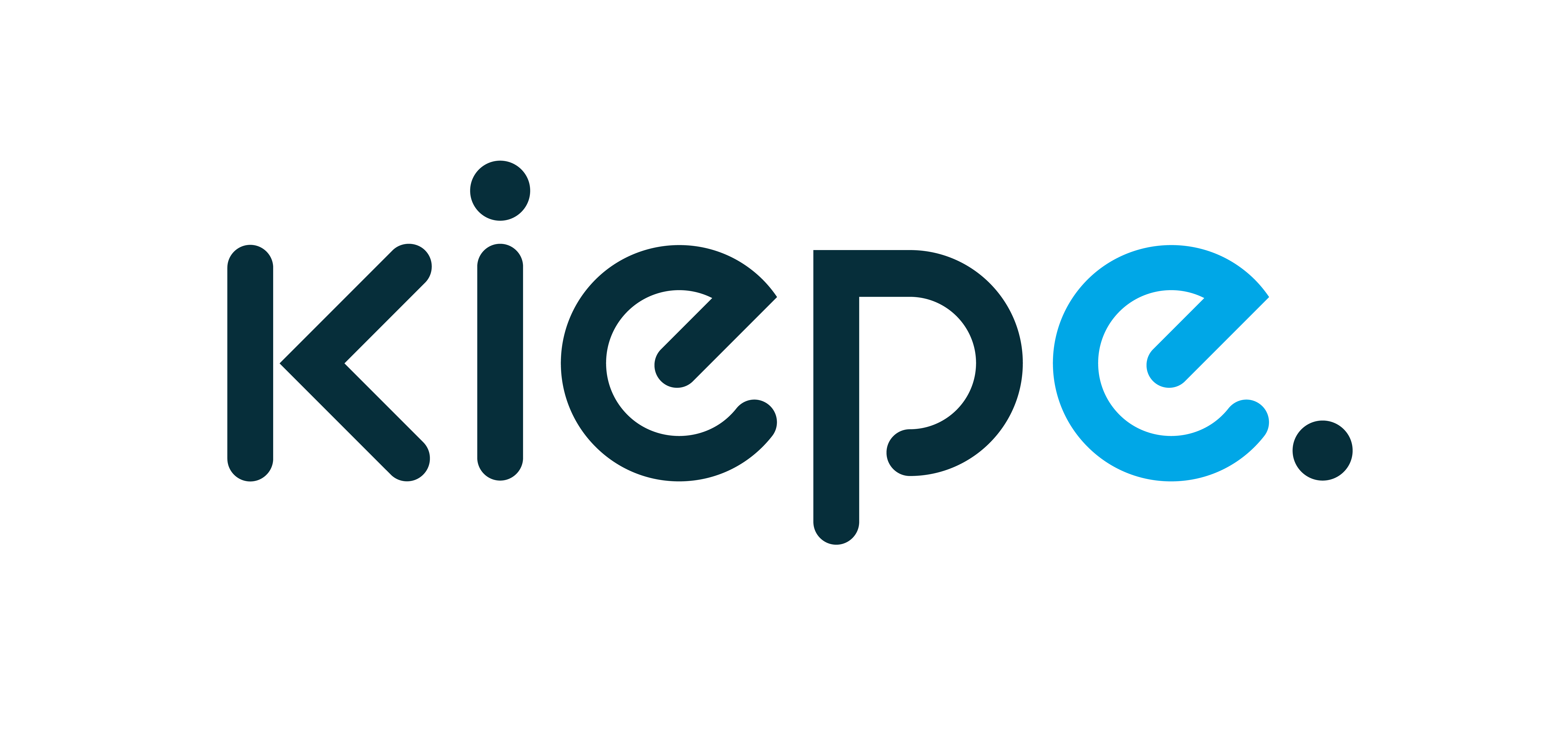
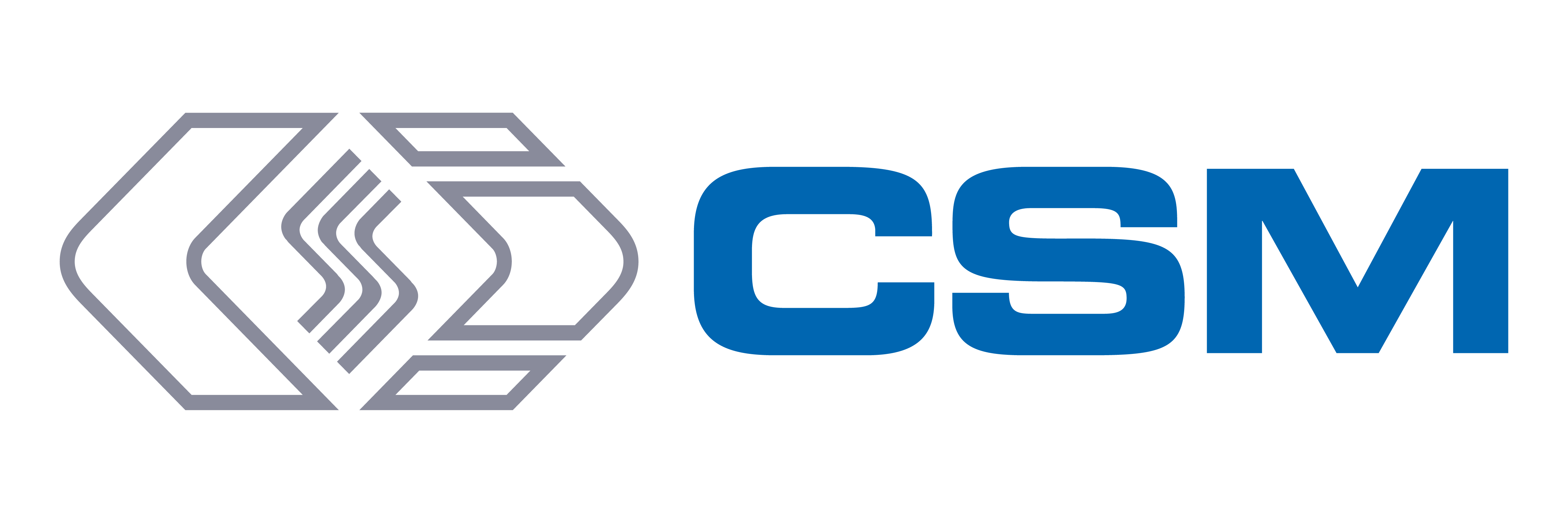