Battery energy density
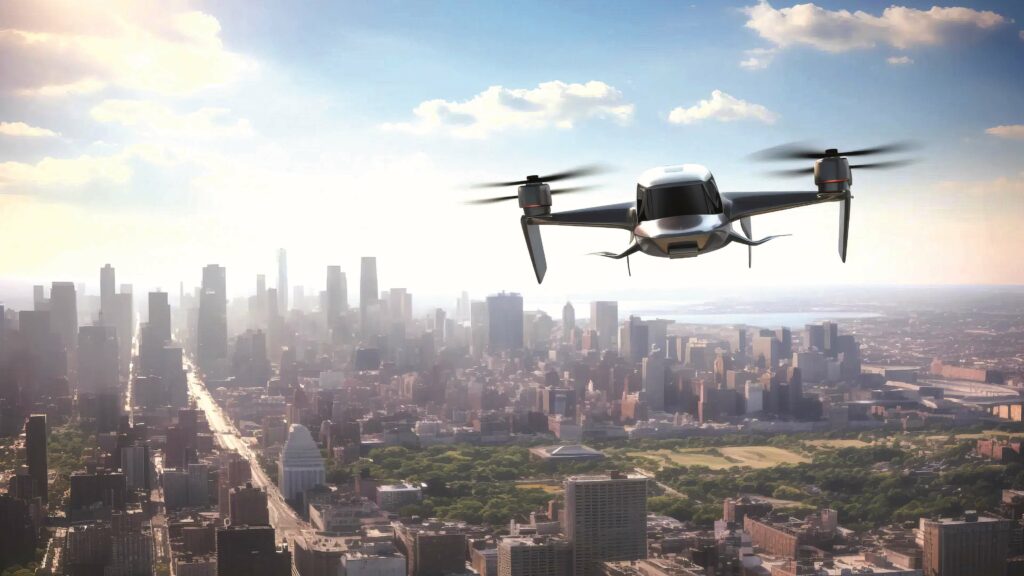
(Image courtesy of Amprius)
Packing more punch
Nick Flaherty looks at strategies to get more power out of battery cells, which brings thermal management challenges
There are many ways to boost the energy density of an e-mobility platform’s powertrain. The materials in a battery cell can be improved to produce more energy, from silicon in the anode to new electrolytes. Solid state batteries under development, for example, can provide higher energy densities, stacking more cells closer together by addressing the materials and the packaging.
There are strategies to include more cells in packs to improve energy density with structural designs that eliminate much of the overhead of the packaging. Then there is the challenge of getting all the available energy out of a cell to provide the maximum possible power across its lifetime. Here, the modelling and testing of cells is key, with implications for the design of the battery management system (BMS).
There are even opportunities to integrate elements of the chargers and inverters into the battery pack to improve the energy density of the entire powertrain. However, increasing energy density brings challenges in thermal management as smaller cells and more compact packs have more power. Faster charging also generates more heat, which can be more difficult to dissipate.
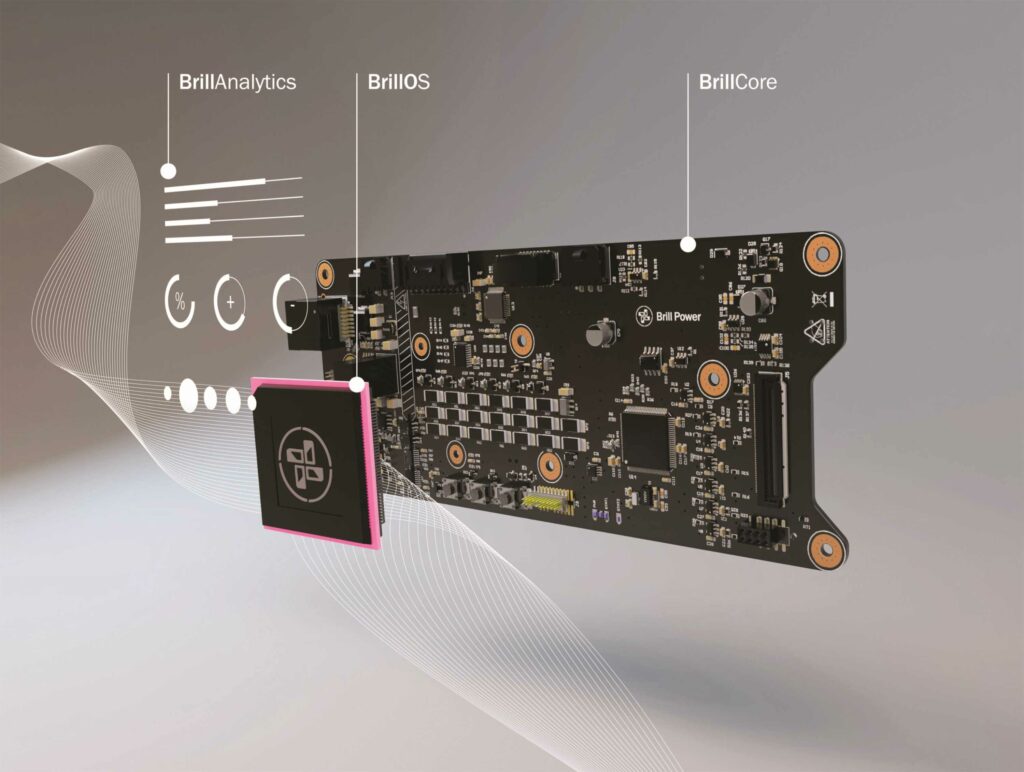
(Image courtesy of Brill Power)
Volumetric energy density
The amount of energy that can fit into a given physical volume is most important for applications that are volume-constrained, such as passenger vehicles. To add more range in an EV with conventional lithium-ion batteries, the battery pack must be made physically larger, which means the car itself must also be larger.
As the vehicles cannot easily be made bigger to accommodate more batteries, the cells need to pack more energy into the available space. While weight is important, better volumetric energy density is a bigger priority, as it allows passenger vehicles to be smaller and lighter, with more interior space for legroom or cargo.
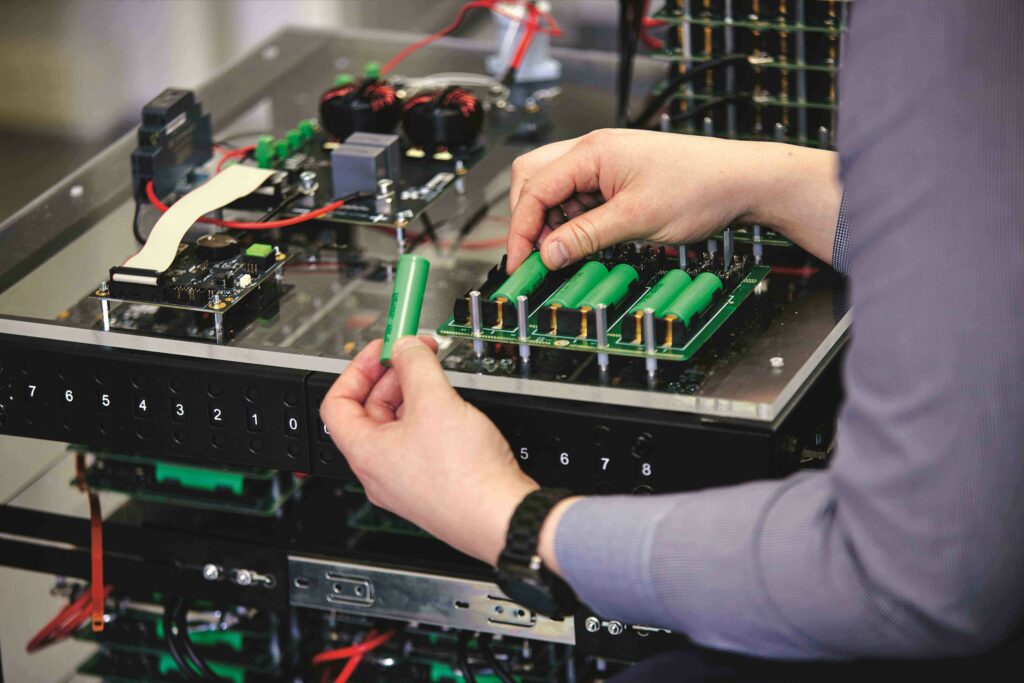
(Image courtesy of Brill Power)
Gravimetric energy density
Weight is at an absolute premium for applications such as aerospace for electric vertical take-off and landing (eVTOL) air-taxi designs. In such cases, a bulkier battery can be accommodated by good design, but increased weight constrains performance, so the lighter, the better.
In heavy-duty trucking there are legal maximum weight limits to avoid damaging roadways. For an electric truck, the less weight taken up by batteries, the more payload can be hauled, enabling it to earn more per trip. In cases such as high-performance sports cars, lighter models can handle better and accelerate faster. For these types of applications, gravimetric energy density, also known as specific energy, may be the bigger pain point.
Battery energy density has slowly but steadily increased over the past few decades, and lithium-ion batteries are now so energy dense that they can power EVs for hundreds of miles.
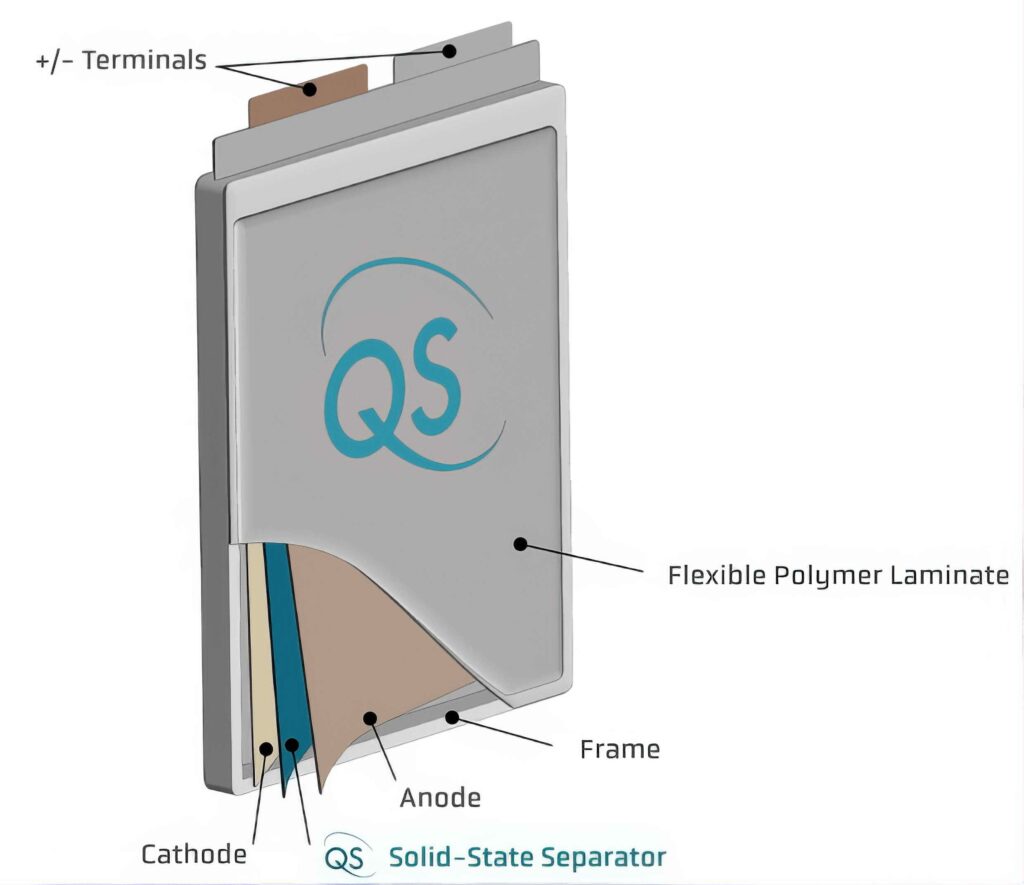
(Image courtesy of QuantumScape)
Energy density
“You can break the battery issues down into three elements. There’s the cell chemistry, dominated by lithium NMC, and in the short term, for five to seven years, that will continue to dominate,” says Peter Freedman, chief commercial officer at Brill Power.
“Over the last couple of years, the companies we deal with in automotive have seen advances in cell-to-pack technology that have really helped improve the overall energy density. In electric bus design everyone wants to put the batteries on the roof or at the rear, as you need a low floor, so that’s where you find the biggest advancements. So, it’s about improving efficiency over the lifetime to reduce the size of the packs.”
Brill Power is developing technology across three areas, with a combination of the BrillOS software, the BrillCore module hardware and BrillAnalytics.
“We are designing the control system, a battery intelligence platform, as it’s more than a BMS hardware, called BrillOS. This is chemistry and hardware agnostic as no one is clear what chemistry will play out in the future.
“The third element is cloud-based analytics with battery insights, and in a perfect world this would update the platform over the air and continuously improve performance over the life of the vehicle, extracting the maximum energy from the pack.”
“BrillCore uses a different way of controlling cells, modules or streams,” says Francesco Tardelli, principal engineer at Brill Power.
“We have active loading, which is different from active balancing. We integrate a more granular control to remove the weakest link in the battery pack. You have several modules in series, but the energy that can be extracted is determined by the weakest cell in a module. Instead, we actively load every module, depending on its state of health (SoH) or state of charge (SoC), or other parameters.
“Each module is interfaced to the other modules through our technology, so we can actively control the current flows in each module. What we would do is link six cells in series by a module board measuring the SoC and SoH to load each module,” he says.
Brill Power has already deployed the technology in stationary storage, where the granularity is six cells. “There’s still work to be done in automotive to work with OEMs to understand the right level of granularity, depending on the use case. This allows you to extract more energy from the pack, especially as vehicles get older and the cells degrade,” says Freeman.
Tardelli says: “It’s always a trade-off of how granular you want the control and weight of the system,” says Tardelli. “You can do clever stuff with granular control. You can effectively integrate the power conversion needed in the powertrain. Within stationary storage we already integrate DC-DC conversion in the module, but we could do power conversion from DC to AC that can be flexible.”
This could reduce the overall weight of the powertrain by integrating elements of the inverter or charge into the pack.
“Another one is to scale up the battery pack with basic building blocks at a much lower voltage than the full pack. You still need to monitor all the cells in the pack, and we leave a lot of control at the module level,” says Freeman.
“If you keep fast-charging a battery, regardless of the chemistry, it will degrade, so the integration of the power conversion gives you the opportunity to match the operation of the charging station. By properly interfacing the battery to the charging station you can make sure you have the maximum charging power, and we can charge batteries 8-10% faster. In the commercial space this is interesting for DC fast charging,” he says.
However, a key challenge is the accuracy of the algorithms in the BMS and how the performance of the cells changes over time.
“One of the biggest challenges is that the embedded algorithms massively diverge from reality over time, and the way we are addressing that is being able to have this firmware platform, taking the data to the cloud and updating the algorithms. This reduces the size and weight of the module,” says Freeman.
“If the BMS is giving you inaccurate SoH and SoC readings, you cannot use all the energy in the pack; it will stop you. But if you can update those algorithms, you get more energy out.”
This will be key for new chemistries, including sodium for smaller city-car designs. “Sodium is interesting from a commercial and cost perspective, rather than energy density. We are chemistry agnostic, and we have our BMS operating with sodium ion batteries, and they will have a part to play in automotive,” says Freeman.
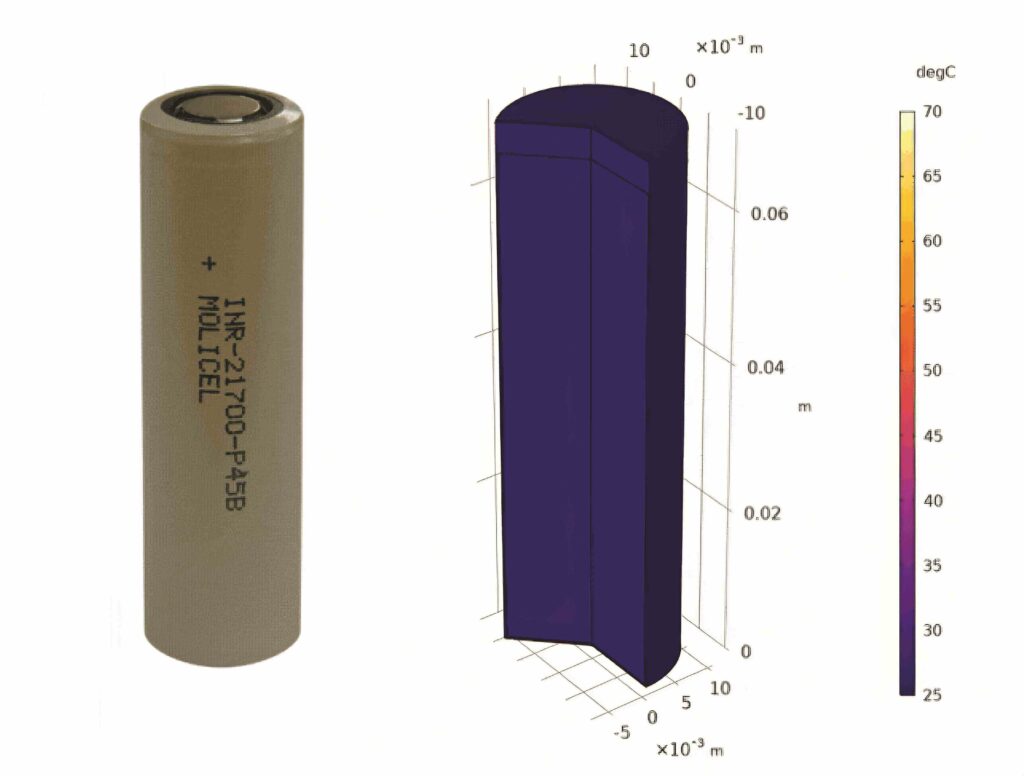
(Image courtesy of About:Energy)
Sizing a pack
“People are sizing their battery packs for the power requirement in years six, seven and eight for commercial platforms, which is different from car designs that are about capacity on the first day,” says Freeman. “So, if you can minimise the size of the pack by increasing the energy density of the cell, and use a cell-to-pack architecture, this minimises oversizing the pack. This gives you the smallest pack on day one that will still provide what you need in year seven.”
The cell-to-pack technology developed by CATL, for example, has significantly boosted the volumetric use efficiency of the battery pack, which has risen from 55% for the first-generation CTP battery to 72% for the third-generation battery, called Qilin. The energy density of Qilin using lithium NMC cells can reach 255 Wh/kg, while that of the LFP one amounts to 160 Wh/kg.
Cell-to-chassis (CTC) technology integrates the battery cell with the vehicle body, chassis, electric drive and thermal management, as well as various high and low-voltage control modules. This extends the driving range to over 1,000 km. It optimises power distribution and reduces power consumption to less than 12 kW/h per 100 km.
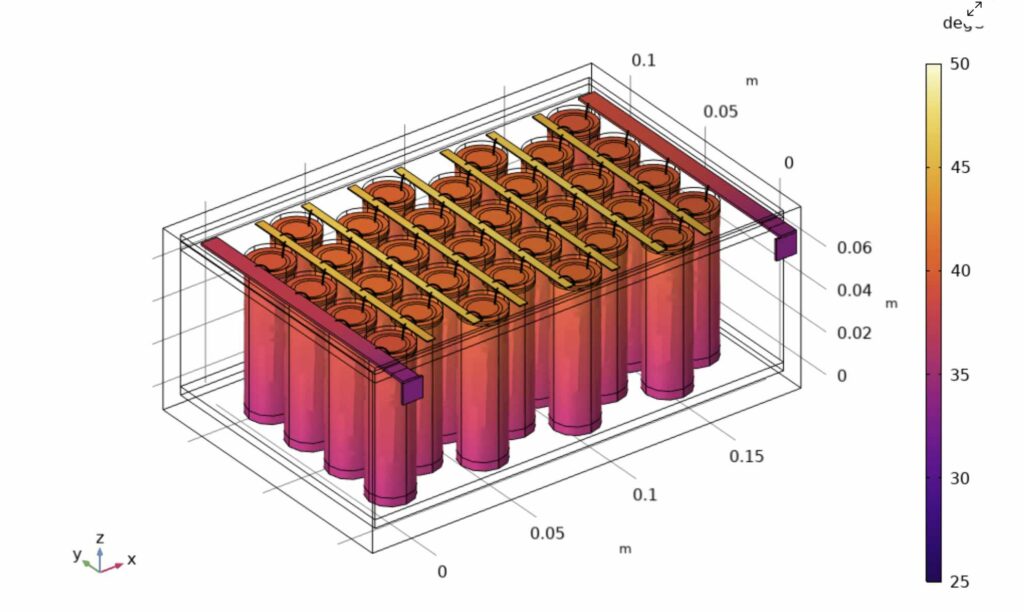
(Image courtesy of About:Energy)
Lithium-metal, solid state batteries
Lithium metal poses some unique challenges that require innovations in cell architecture. For example, QuantumScape’s solid state, lithium-metal battery technology uses FlexFrame, which is a cross between a conventional pouch cell and a prismatic cell, and it is intended to enable a step-change improvement through the simplicity of design.
There are two fundamental features of the FlexFrame architecture: a frame that wraps around the edge of the cell stack, and a flexible outer layer of polymer laminate, similar to conventional pouch-cell material.
When manufactured, the cell is anode-free, and the cell stack is in its most contracted position, with the face of the cell sitting about 1 mm below the frame. As the cell charges and the anodes of each layer are plated with pure lithium metal, the cell face is pushed out, along with the flexible packaging material. When fully charged, the face of the cell is designed to be almost totally flush with the frame.
In addition to accommodating expansion and contraction, FlexFrame is designed to allow the cell to simultaneously dissipate excess heat during fast charging and function, with or without externally applied pressure. This offers good packaging efficiency to achieve cell-level energy density targets.
The cell has a frame that wraps around the edge of the cell stack and a flexible, polymer outer layer, and it is designed to accommodate the uniaxial expansion and contraction that lithium-metal batteries experience during charge and discharge. The cell is designed to dissipate excess heat during fast charging and deliver good packaging efficiency to achieve higher cell-level energy density.
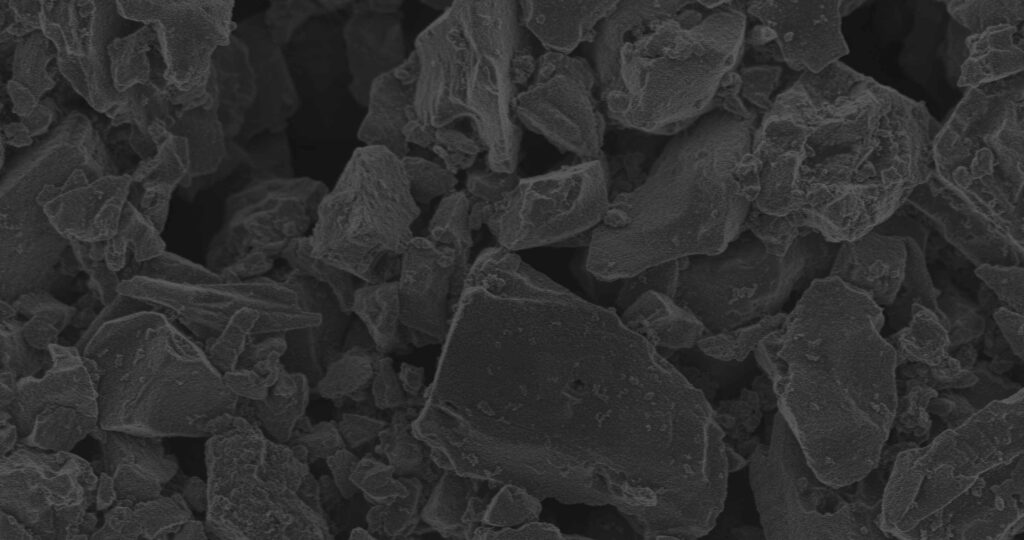
(Image courtesy of Sila Nano)
Temperature and pressure
All batteries generate a certain amount of heat during operation, and higher rates of power typically result in more heat. This means that to enable vehicles with quick acceleration and fast charging, you need a BMS that can quickly pull heat out of the individual battery cells to keep them at their optimal operating temperature. In this context, a high-performance battery cell not only needs good fundamental chemistry, but also intelligent cell design to enable good thermal performance.
Conventional cell designs all manage heat in more or less the same way: as the cell heats up during operation, the thermal energy must move from the layers of the cell to the external casing, where the pack-cooling system draws it away. However, a lithium-metal cell format must expand and contract, and it is difficult to engineer a mechanism, such as a spring or foam, which can move flexibly while conducting heat effectively from the cell face.
To address this challenge, the FlexFrame design splits these tasks in two. While the exterior face of the cell can expand and contract as necessary, the heat generated can be transferred directly from the individual cell layers to the exterior frame, which can then be cooled from the back or sides. Thermal management systems incorporating the FlexFrame cell design are currently being developed and validated.
FlexFrame is designed to work with or without external pressure. If required, pressure can be applied to the external face of the cell, and because heat can be transferred out to the sides of the frame, it is possible to apply pressure externally while cooling the cell at the same time. Data from testing the single-layer cells has shown that the solid-state lithium-metal cell can deliver a long cycle life with zero externally applied pressure, and FlexFrame is intended to be able to operate under these conditions as well.

(Image courtesy of About: Energy)
Manufacturing and pack integration
As a hybrid of conventional prismatic and pouch designs, FlexFrame fits into the existing manufacturing flow. The exterior polymer laminate material is similar to what is found in conventional, lithium-ion pouch cells, and the frame gives the cell good mechanical stability, which is provided at the module level for a conventional pouch cell.
Assembly of the cell uses conventional stacking and sealing techniques, which will help high-volume manufacturing. Unlike cylindrical cells, FlexFrame cells can fit neatly next to one another with minimal wasted volume. This is a key step in improving the overall pack energy density relative to a cylindrical cell format.
The energy density at cell level is not just about chemistry; packaging also plays an important role. One goal of any cell format is to minimise the amount of dead weight and wasted volume taken up by inactive materials, such as the cell casing, and maximise the proportion of the cell’s active materials – the part of the cell that stores energy. Optimising this packaging efficiency is key to enabling high cell-level energy density.
Because the lightweight pouch cell material and low-profile frame add minimal overhead, the QSE5 cell format developed by QuantumScape with the FlexFrame packaging can deliver energy density above 800 Wh/L in a 5 Ah cell, with room for improvement in a higher-capacity design.
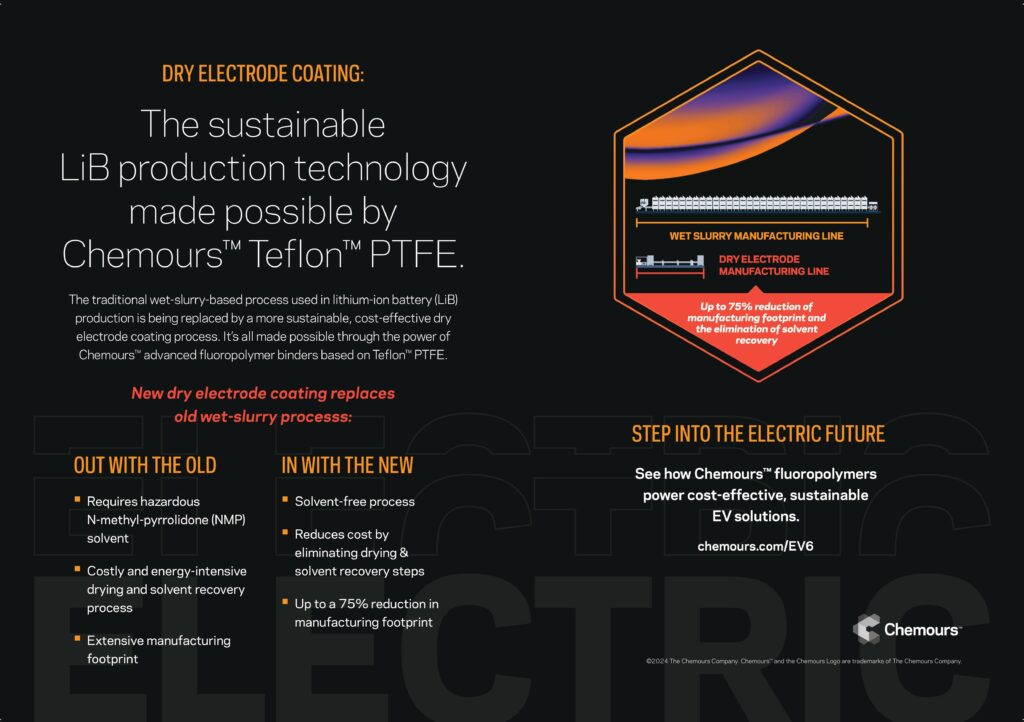
Modelling
“What I’ve seen in the last five years is lots of novel material breakthroughs, but I’m also highly sceptical about the commercialisation; the trade-off of lifetime, power and cost,” says Kieran O’Regan, co-founder and chief operating officer at About:Energy.
The company analyses the performance of a wide variety of battery cells. It has developed simulation and modulation tools using data from the analysis.
“For me, it’s the incremental improvements over the last five, 10 and 15 years that have made a huge difference, particularly with maritime and aerospace. There are so many different paths to improve energy density, from the materials to components, cells, packs and software. It is really holistic. It’s all of those topics moving together,” says O’Regan.
“What we do is supply data and simulation tools to help battery developers move more quickly, whether that’s cells or BMS software. We help people design cells, packs and BMS, rather than develop materials. Collecting data for development is expensive and time-consuming, so we have our own labs and we test them. It can take years. Understanding degradation is not a process you can hurry,” O’Regan continues.
“A lot of companies use the same batteries, which is surprising as they are very different; for example, the cells from Molicell are used, from eVTOL to satellites. But the way companies build that into a cell or a pack is very different.
“We facilitate the power versus energy density decision to be made by the customer, and they are the ones that make the trade-off – how many cells to improve the power, but it’s heavier, so you reduce the energy density. Our tools are used to make those trade-offs across all of that.”
Materials
“Some of the big trends are about optimising the electrodes in the cell. The main way is adding silicon to the graphite anode, but it does have limitations on lifetime, and 40% of silicon in the anode is perhaps the sensible limit,” says O’Regan.
“At this point there is more voltage hysteresis, and that makes BMS and prediction very hard. It can be a drop-in replacement in manufacturing, but it can be an issue with the BMS and the lifetime. That’s where simulation can be used very effectively to use models to provide the lifetime over five, 10 and 15 years, and find a way to make those trade-offs a lot quicker.
“On the cathode, it’s NMC, and now companies are moving to higher nickel chemistries. We are seeing a slow transition to new chemistries for LFP, solid state, niobium, sodium, but they are not necessarily more energy dense. Lithium sulfur is also on the horizon, but it’s more early-stage.
“The electrolyte is one of the main ways to make the cell more energy dense, and there are new coatings and materials to mitigate the degradation of the cell. A lot of that is through repeated trial and error,” O’Regan adds.
Amprius Technologies is working with an eVTOL maker on a custom battery cell using its 100% Silicon Anode technology. This is based on silicon wires grown on the copper current collector, and the custom cell is in internal qualification with the customer.
The 400 Wh/kg cell is capable of a continuous discharge rate of 10 C to power the motors during take-off, cruise and landing without sacrificing performance. In addition, it has fast charging capabilities, allowing it to reach an 80% charge in six minutes or less, to speed up turnaround times. These will be used in pre-production units of the eVTOL in 2025.
Panasonic Energy, one of the major cell manufacturers supplying e-mobility system makers, is working with Sila Nano in the US to nano-composite silicon into that anode. The Titan Silicon material will boost the volumetric energy density to 1000 Wh/L by 2030.
“By integrating Sila’s groundbreaking battery material with our advanced cell-manufacturing capabilities, we believe we can address concerns such as range anxiety and charging time, and contribute to accelerating the adoption of EVs,” says Shoichiro Watanabe, executive vice-president of Panasonic Energy.
“Panasonic is the world’s leading battery technology company, pushing the boundaries for performance, and we look forward to optimising Titan Silicon to help achieve these momentous goals,” says Gene Berdichevsky, co-founder and CEO of Sila. “This partnership represents a significant milestone for Sila, our customers and the industry at large, and will be key to accelerating consumer EV adoption.”
Electrolytes
Developing new electrolytes is where simulation has its limits, and this is where AI is finding gaps in data and forecasting new materials. This can be used to combine physics-based models with AI to extend the lifetime of cells. The physical models offer great insights to improve fast charging times and forecast how batteries age, but they cannot account for all the physics. About:Energy is working with Eatron to develop an AI ‘decision engine’ for a BMS that combines machine learning and the About:Energy electrochemical model, Voltt.
The aiMAGINE project aims to use machine-learning frameworks in the BMS to extend the life of a battery pack in EVs and scooters, providing accurate assessments of SoC, SoH and patented remaining useful life (RUL) predictions.
AI complements the electrochemical models, enhancing predictions by accounting for complex physical behaviours that cannot be modelled. This allows the AI-powered decision engine (AI-DE) to provide highly accurate operational parameters to the BMS, significantly increasing battery pack longevity and simplifying integration.
“Implementing our novel, AI-powered, intelligent battery software layer with this revolutionary AI-DE can extend a battery pack’s first life by up to 20%,” says Dr Umut Genc, CEO of Eatron Technologies. “This makes it possible for OEMs to design optimally sized, more cost-effective battery packs.”
O’Regan says: “The use of our advanced electrochemical models vastly streamlines AI model training, and this facilitates both ease of integration and a reduced time-to-market for OEMs and Tier 1s. The high-fidelity modelling reduces the need for physical experiments while delivering a clearer, more accurate picture of battery health. Armed with this information, an AI-DE-equipped BMS can deliver not just a longer battery lifetime, but faster charging times too.”
About:Energy is also working with the universities of Portsmouth and Southampton on a more accurate approach to battery modelling, which will provide more data about the energy in the cells.
The Voltt models can be downloaded to modelling and simulation tools from Comsol and Matlab, but About:Energy is developing a cloud-based tool to download the model and use the Python programming language to develop a drive cycle to assess the performance of the cells in specific applications, particularly automotive and aerospace.
Future directions
Boosting the energy density of an e-mobility system’s powertrain is a complex balance. Improvements in materials – whether for existing lithium NMC graphite cells, silicon anodes or lithium-metal solid state cells – can improve output, but the cell format, whether cylindrical or a mix of prismatic and pouch, can reduce wasted space and increase energy density. Then, cell-to-pack and other topologies can further reduce the passive elements in the system.
When it comes to getting the most out of cells over the lifetime of a vehicle, new architectures and battery management systems can help. Accurately modelling the performance of a cell over the lifetime of operation can ensure power is delivered as expected. This can help avoid oversizing to meet future requirements and reduce the size of the pack overall to improve the energy density of the powertrain design.
ONLINE PARTNERS
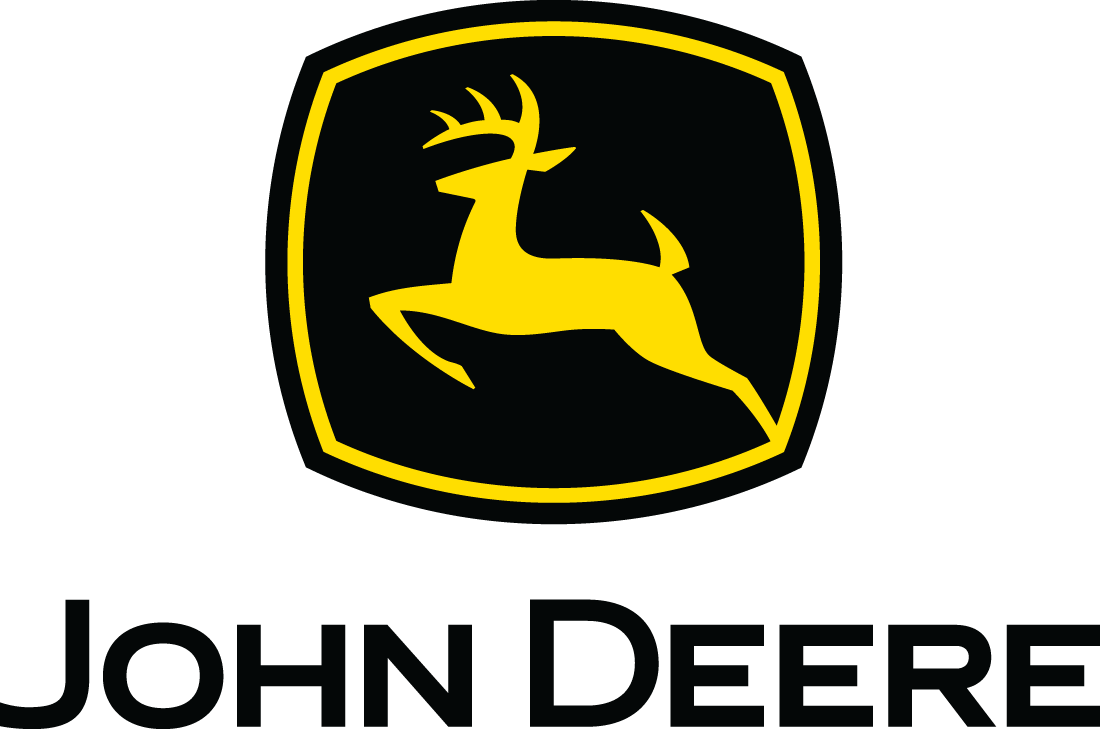
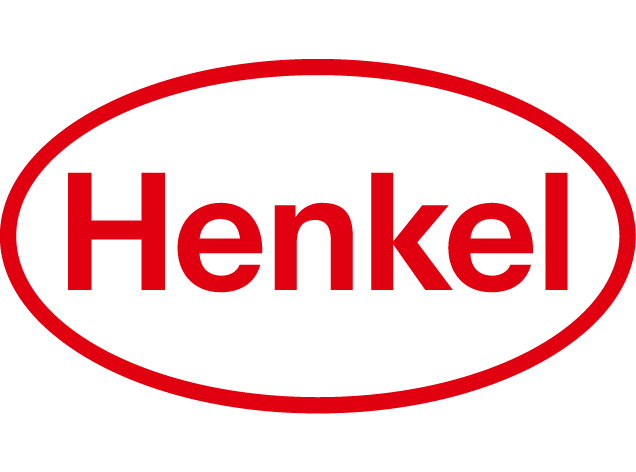
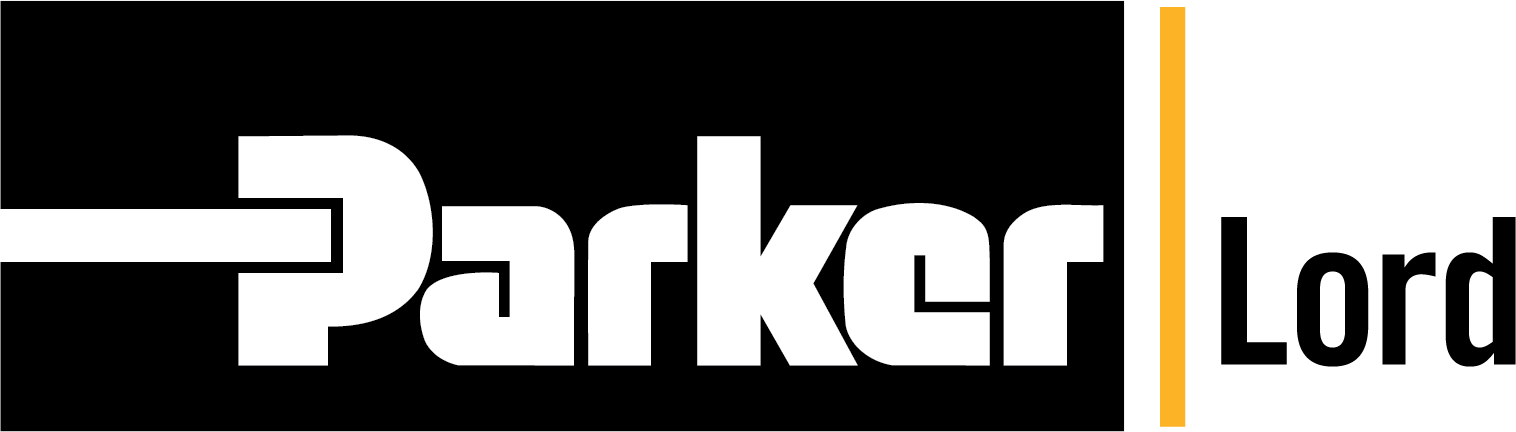
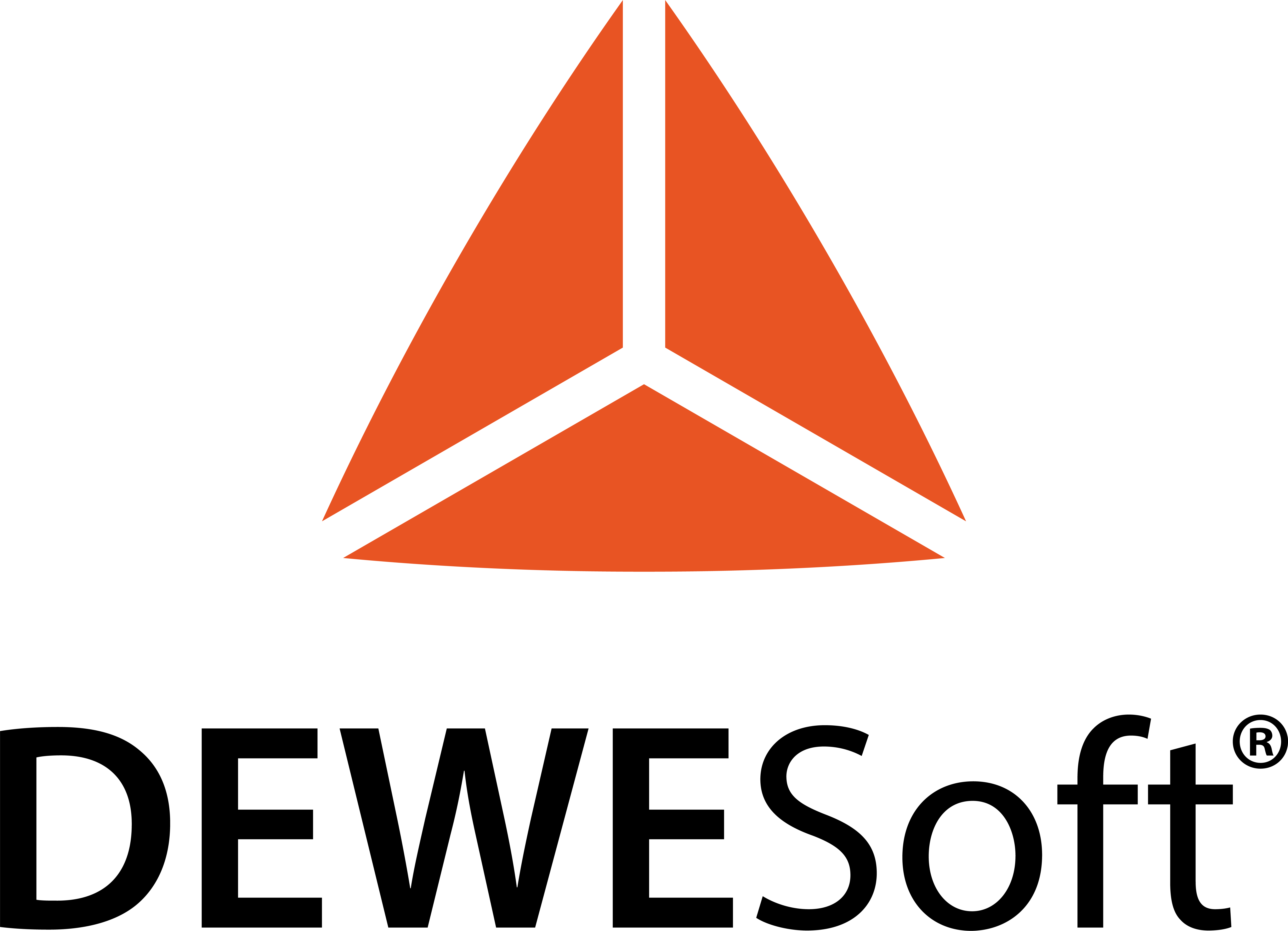
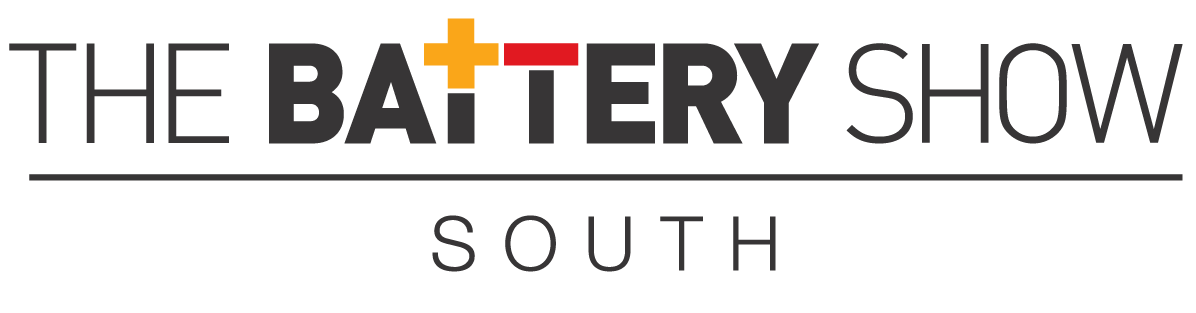
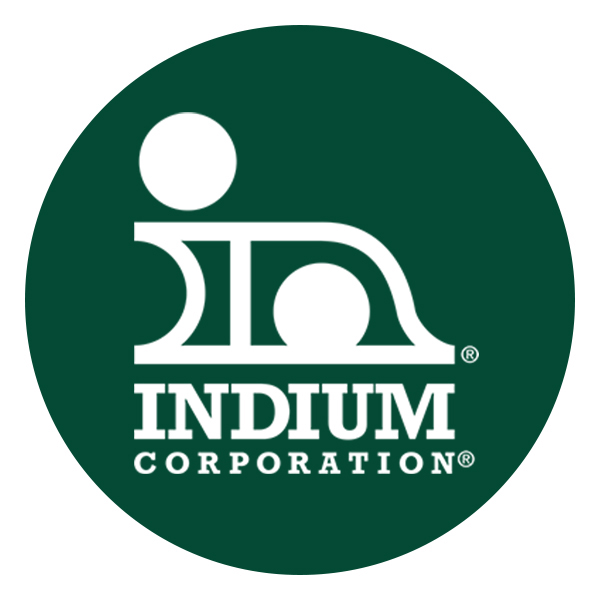

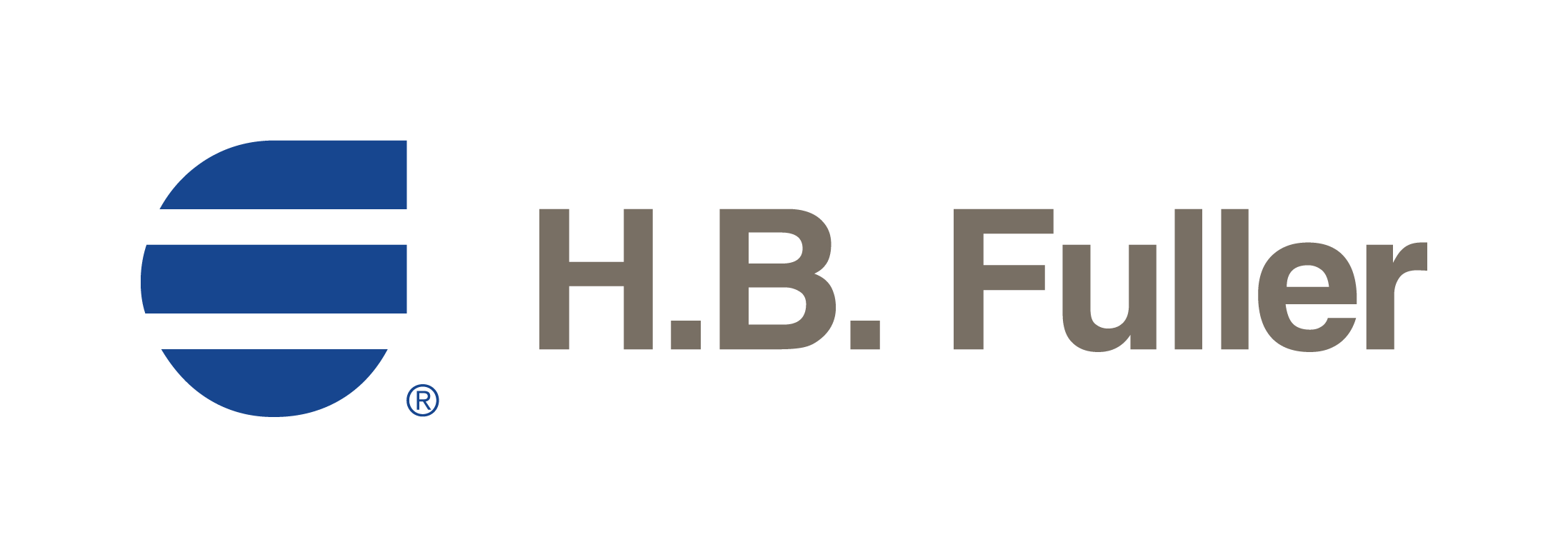
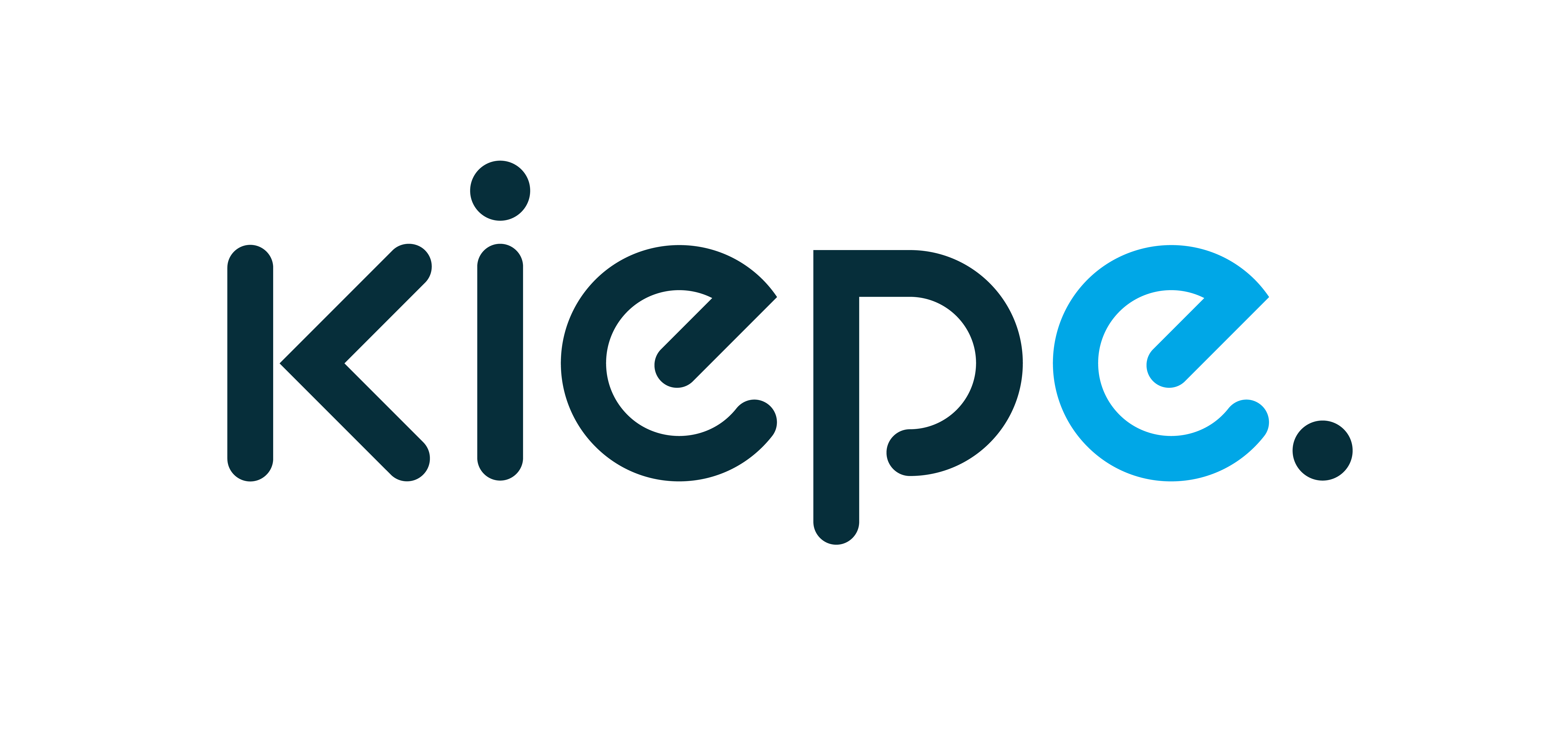
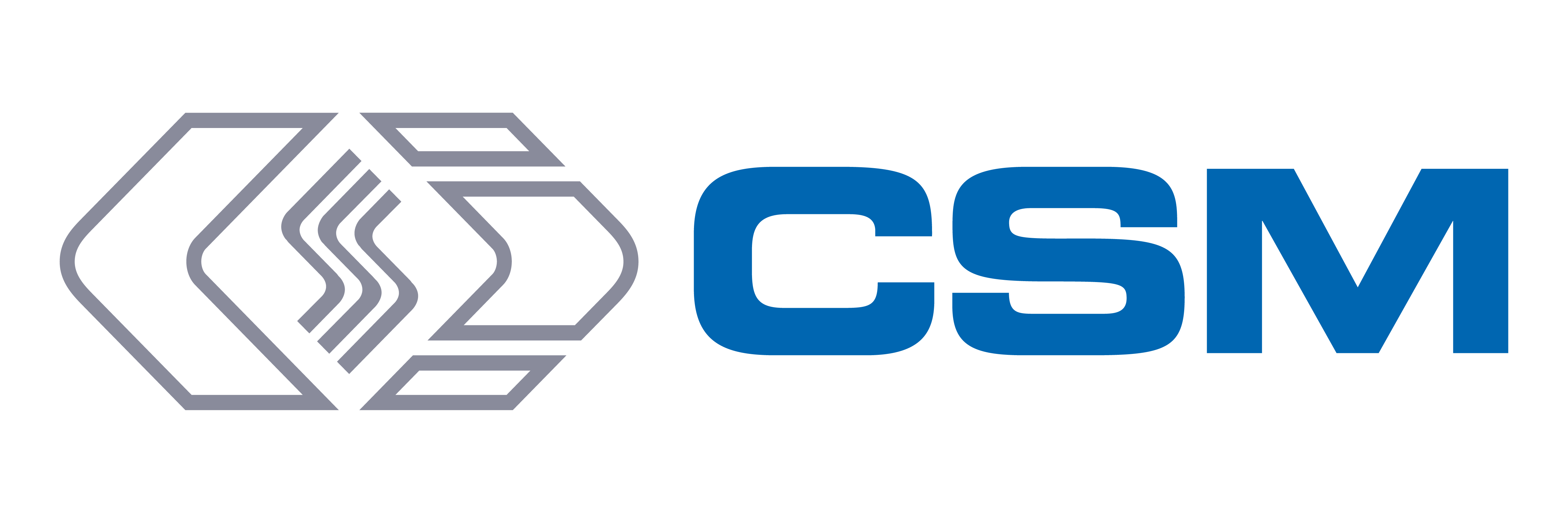