Battery dielectric protection
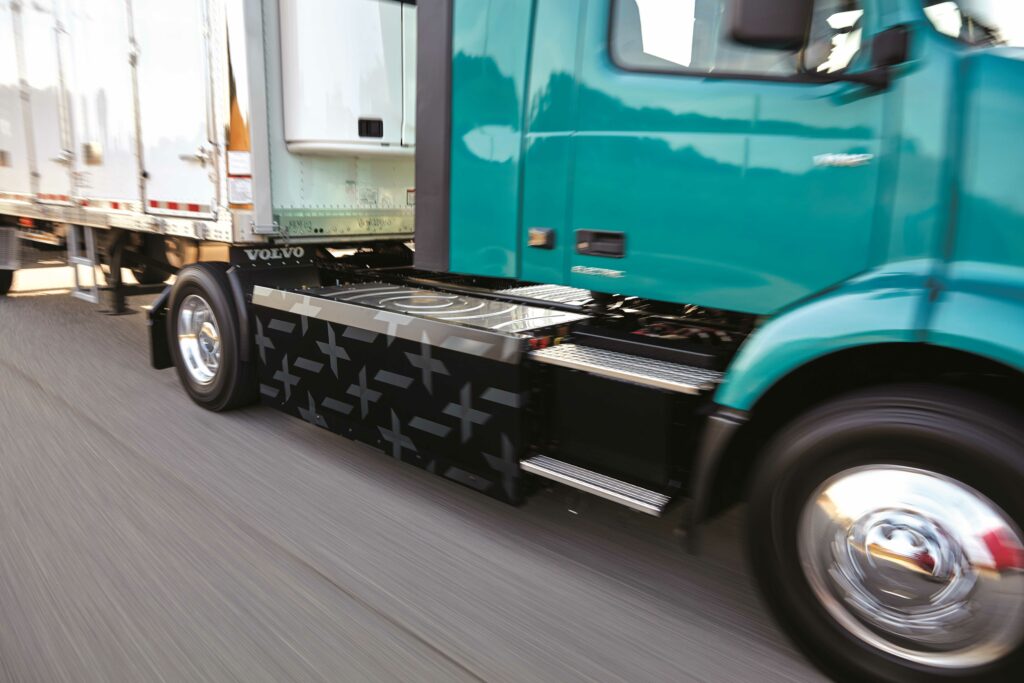
(Image courtesy of Volvo)
Containing high voltage
Peter Donaldson examines multi-function dielectric materials for battery systems
Dielectric protection materials are critical in EV battery systems, where they serve to insulate components from one another, reduce the risks to technicians working on them, and often also contribute to structural strength and thermal management. The wide variety of materials and forms present various advantages and limitations, making selection a complex process that is increasingly focused on the specific demands of each application.
The need for dielectric protection extends across multiple components in battery systems, including the cells, cooling systems and electrical connections within the pack.
As well as exhibiting the insulating strength needed to prevent electrical failures such as arcing and short-circuiting, materials must be robust enough to maintain their performance under the diverse, harsh environmental and operational conditions encountered in automotive applications.
Such materials are available in many forms, including coatings, tapes and fluids such as immersion coolants, offering a wide range of properties that have to be combined and balanced to meet often conflicting and rapidly changing demands.
Ceramic coatings and sheets, for example, are often used in batteries because of their combination of high dielectric strength and thermal stability. They can withstand extremely high temperatures without degradation and their low thermal expansion reduces the risk of cracking, while their non-flammable nature enhances safety by resisting thermal runaway.
However, the brittle nature of ceramics poses challenges during assembly and operation, where mechanical damage is a concern. Their rigidity also limits their use in complex geometries, while their generally higher cost complicates their widespread adoption.
Polyimide films, such as Kapton, offer excellent dielectric strength and thermal stability, withstanding temperatures up to 400 C, and their flexibility makes them well-suited to applications requiring insulation in complex geometries. These films are also lightweight and chemically resistant, contributing to both battery safety and weight reduction. However, their relatively high cost and susceptibility to UV degradation mean they may require additional, protective layers in certain situations, particularly for applications with prolonged outdoor exposure, although if they are inside battery enclosures this is unlikely to be an issue.
Mica sheets and tapes are notable for their extremely high dielectric strength and thermal resistance, capable of withstanding temperatures up to 1000 C. Mica’s natural insulation properties and non-flammability make it a reliable choice for preventing heat transfer between battery components.
However, its brittleness and lack of flexibility pose challenges, particularly in applications requiring tight bends, and the dust can be a health hazard in manufacturing, maintenance and repair situations, so efforts are under way to find alternatives.
Additionally, mica can be bulkier than its thin-film alternatives, potentially adding to the size of the battery assembly.
Epoxy resins and potting compounds are another popular choice for dielectric protection in EV batteries, particularly but not exclusively in cell-to-pack architectures, offering both high strength and mechanical robustness. Epoxies can be customised with fillers to improve properties such as thermal conductivity, and they provide excellent adhesion to various substrates, suiting them well to sealing and protection.
However, the rigidity of cured epoxies can make repairs or modifications difficult, and standard formulations may offer limited thermal conductivity unless enhanced with additives. Additionally, long curing times can slow down the manufacturing process.
Silicone-based materials, including sheets, coatings and potting compounds, provide excellent flexibility and elasticity, making them ideal for applications where movement or vibration is common. Silicones offer good dielectric strength and thermal stability across a broad temperature range, from -60 C to 200 C, as well as resistance to moisture, chemicals and UV exposure.
The use of silicones is sometimes avoided, however, because of the potential contamination of other components. For example, in assembly processes such as soldering and adhesive bonding, silicone can cause de-wetting of materials from surfaces, resulting in bonding failure. Silicones also typically have lower mechanical strength than more rigid materials such as ceramics, and their higher cost can be a limiting factor.
Lastly, polyethylene terephthalate (PET) films and fluoropolymer films such as PTFE and FEP provide lightweight and cost-effective solutions for dielectric protection. PET films are flexible and easy to handle, although they are less thermally stable than polyimide or ceramic materials.
Fluoropolymer films, while more expensive, provide superior dielectric properties and resistance to chemicals, UV radiation and ageing, making them well-suited to demanding environments. However, their low mechanical strength often necessitates additional support in structural applications.
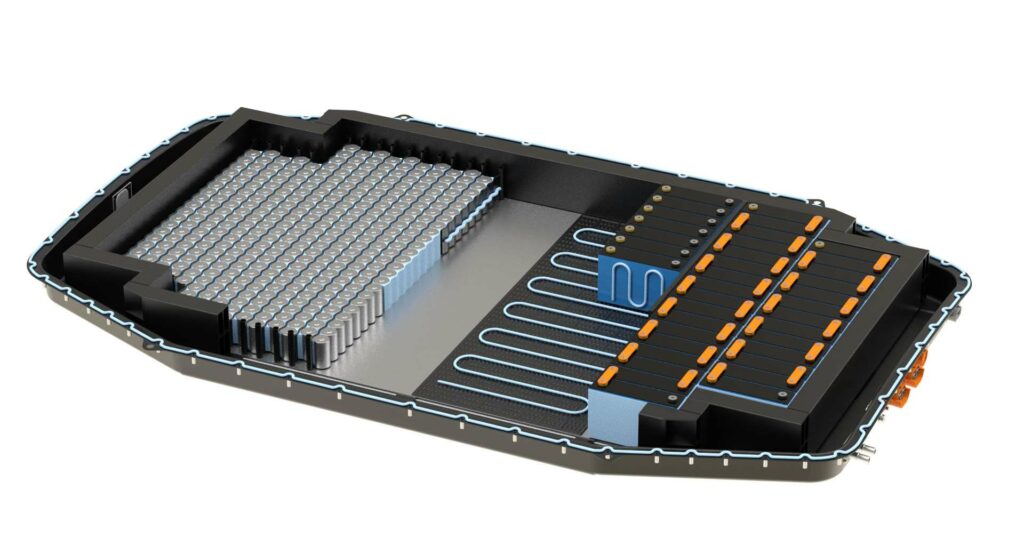
(Image courtesy of PPG Industries)
Dielectric strength
Typically measured in kilovolts per millimetre (kV/mm) of thickness, dielectric strength is the defining characteristic of these materials and is consequently one of the primary performance indicators.
A high dielectric strength ensures the material can effectively insulate electrical components, reducing the risk of electrical breakdown, particularly in the high-voltage environments of EV battery systems. Several companies have developed materials with dielectric strengths well above typical system requirements, providing a buffer of safety in increasingly energetic and powerful battery packs.
Some coatings specifically designed for these applications offer dielectric strengths exceeding 55 kV/mm, ensuring that even when applied in thin layers, they provide robust protection against electrical failure. This is critical for applications where space and weight are at a premium, especially as EV manufacturers strive for greater energy and power density in their batteries.
These coatings are engineered to maintain their dielectric properties, even after prolonged exposure to extreme temperatures, high humidity and other challenging environmental conditions, ensuring long-term reliability in the field. In addition to coatings, certain thermal interface materials (TIMs), which are used to manage heat flows in the battery pack, also exhibit high dielectric strength, providing both thermal management and electrical insulation.
Other materials, such as dielectric fluids used in immersion-cooled battery systems, also play a vital role in electrical insulation as they come into direct contact with cells, tabs and interconnect systems.
These fluids typically have dielectric strengths greater than 30 kV/mm, providing ample protection in typical battery configurations. However, because dielectric fluids can be susceptible to water ingress, which can lower their breakdown voltage, careful attention must be given to the sealing of the system to maintain insulation integrity.
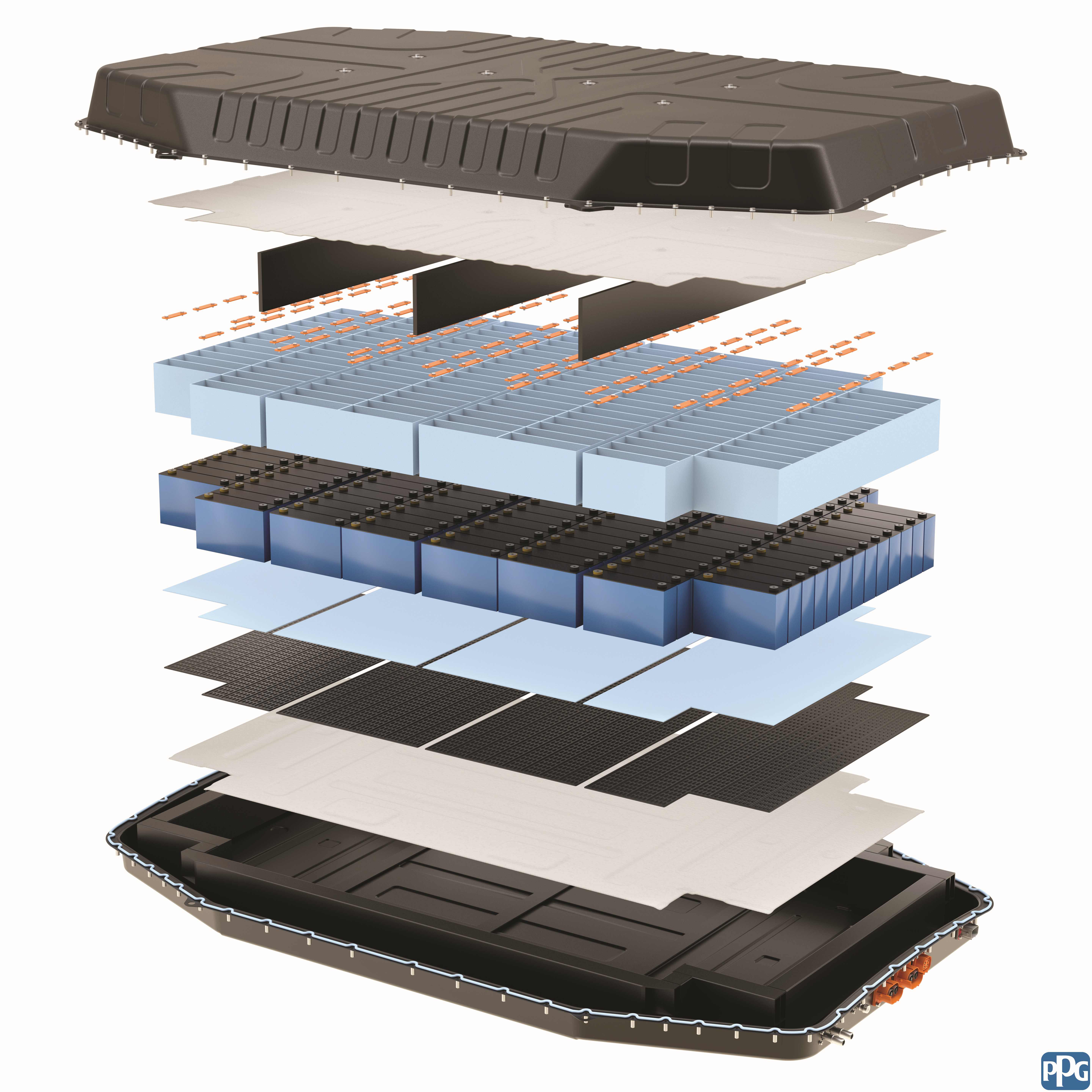
(Image courtesy of PPG Industries)
Dielectric and thermal combined
Thermal conductivity is also an important – if usually secondary – characteristic of battery dielectric materials, playing a crucial role in safety and efficiency, particularly in managing heat dissipation in high power-density applications. Increasingly, manufacturers are focusing on optimising both thermal and dielectric properties to meet the growing demands of high power-density EV battery systems.
For example, cold-plate coatings need higher thermal conductivity compared with other dielectric materials, effectively facilitating heat dissipation between battery cells and cooling components, such as cooling plates or tubes. This minimises the strain on battery management systems (BMSs), ensuring safer and more efficient operation.
Similarly, TIMs that fill air gaps between irregular surfaces to improve heat transfer must also have strong dielectric properties when in contact with electrical components.
The performance of a battery pack’s thermal management system is significantly influenced by the materials layered between the battery cells and cooling components, including those for dielectric protection. Lower thermal conductivity in these materials can hinder heat transfer, leading to excess heat retention, jeopardising safety and performance. To address this, one company has developed a dielectric coating with significantly higher thermal conductivity, nearly doubling that of traditional epoxy-based coatings commonly used in battery packs.
Pressure-sensitive adhesives and tapes are another commonly used form factor for dielectric materials in which thermal conductivity is important. One company reports a growing, though still small, demand for thermally conductive dielectric tapes in the EV sector. Their offerings include polyimide-based tapes with moderate thermal conductivity, along with metal-backed tapes.
Additionally, the firm produces silicone rubber and sponge-like materials that provide both thermal conductivity and dielectric protection. While these products are not considered cutting-edge in thermal conductivity, they strike a balance between dielectric and thermal performance.
Another manufacturer discusses the potential to modify adhesive filler packages to enhance thermal conductivity. It suggests that, depending on the customer’s requirements, materials could be designed to either increase or decrease thermal conductivity. However, they note that, to date, customer demand for this capability has been limited.
The company says some high-voltage insulation materials might benefit from higher thermal conductivity to prevent localised hotspots in high-power systems, but it has not yet encountered specific customer requests for such designs in EV applications. It expresses interest in exploring this area in collaboration with industry partners or institutions, especially given their access to high-performance ceramic fillers, which could be leveraged to create advanced, thermally conductive, dielectric materials.
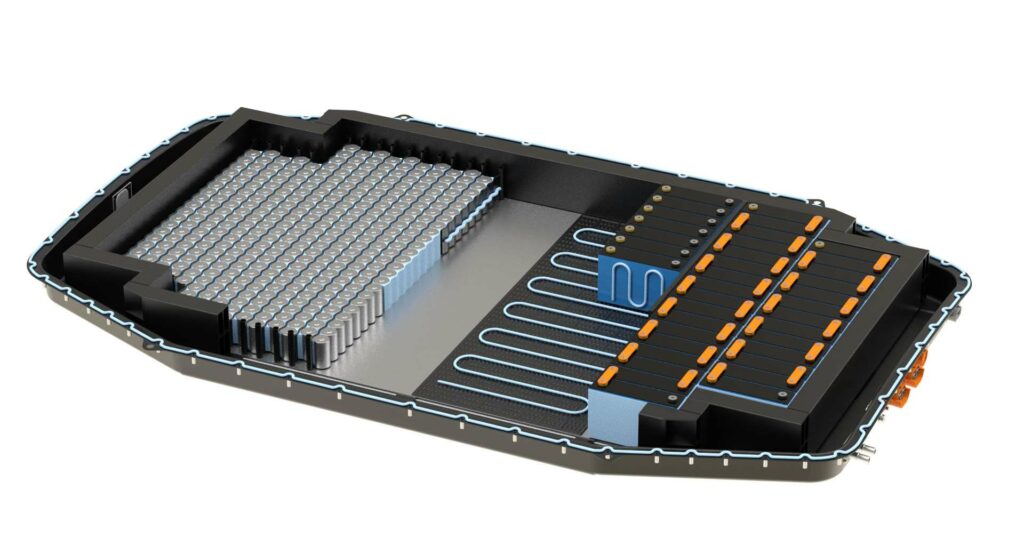
(Image courtesy of PPG Industries)
Environmental stress
The choice of dielectric material is strongly influenced by the specific environmental conditions that it must withstand in service while maintaining its key performance characteristics. For instance, a high-performance polymer tape might be selected for its ability to withstand extreme temperatures, while a fluoropolymer material might be used in areas exposed to high humidity or aggressive chemicals.
In addition to the backing material of the tape, the adhesive used to secure it to the component it insulates plays a critical role in determining overall dielectric performance. Custom combinations of adhesives and backings are frequently developed to meet the specific needs of EV manufacturers, with hundreds of different adhesives available, depending on the environmental exposure expected.
The need for resistance to battery electrolytes is particularly pressing, as exposure to these chemicals can degrade the performance of some dielectric materials over time. In response, materials have been developed that are resistant to a wide range of electrolytes.
The most common electrolytes are lithium salts such as lithium hexafluorophosphate (LiPF₆), lithium bisimide (LiTFSI) and lithium perchlorate (LiClO₄); LiPF₆ is the most prevalent due to its good conductivity and stability. They also typically include organic solvents such as ethylene carbonate (EC), diethyl carbonate (DEC), dimethyl carbonate (DMC) and propylene carbonate (PC), which are frequently used.
EC is often combined with other carbonates to enhance performance. Some formulations may also include solvents such as methyl acetate.
Additionally, fire resistance is becoming a more common requirement in EV battery systems, particularly due to the risks associated with thermal runaway. For example, materials such as mica tapes, which, in addition to their ability to withstand extreme temperatures, can also resist direct flame impingement, are being used more frequently.
Some materials are even designed to ‘ceramify’ under extreme heat, providing flame resistance without the dust or flaking that can occur with traditional mica tapes.
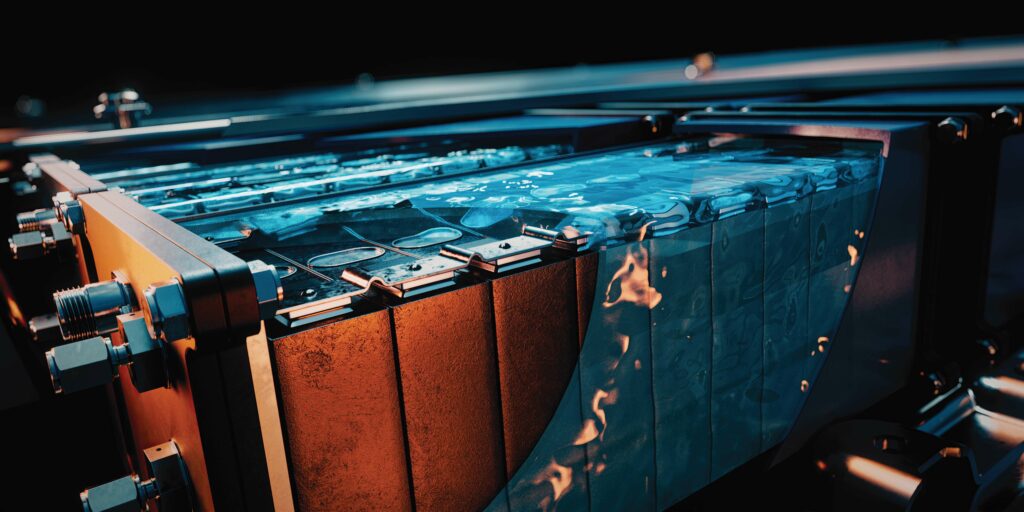
(Image courtesy of Lubrizol)
Complexity in flammability
Material developers are increasingly focused on dielectrics that meet stringent fire-safety standards, such as UL 94 and IEC 60695. The former categorises materials based on their ability to resist ignition and control flame spread, with ratings of V-0 (most flame-resistant) to V-2.
A robust flammability profile is essential for these materials, because added fuel – which any flammable material essentially represents – could exacerbate a thermal runaway. For instance, some dielectric coatings, designed for use in EV batteries, have been formulated to meet or exceed the UL 94 V-0 rating, even in the thin layers in which they are often applied.
Such materials provide an additional safety barrier, preventing ignition and minimising flame spread during potential fault conditions. This is also important for thermal interface materials, including thermally conductive, dielectric structural adhesives; the latter of which not only bond components together, but also provide critical electrical insulation and thermal conductivity.
Newer technologies, such as immersion cooling, pose unique challenges in assessing flammability. The regulatory framework for these advanced thermal-management systems is still developing, requiring manufacturers to work closely with customers to tailor dielectric fluids and coatings exposed to them, based on flash-point tests (ASTM D92 or ASTM D93) and specific application needs. By integrating additives that enhance flame retardance, manufacturers can ensure immersion coolants do not contribute to fire risk and still maintain thermal management efficacy.
To further enhance fire resistance, some dielectric materials incorporate ceramifiable components – typically silicone-based materials that transform into a ceramic-like state under high-temperature conditions. By adjusting their formulation, manufacturers can control the temperature and rate at which the conversion process initiates and proceeds.
Designing flame-retardant systems is inherently complex due to the interaction between different materials. The flame resistance of a system is not solely dependent on the individual components, but rather on the entire assembly. A backing material rated V-0 might not retain this classification when combined with an adhesive, depending on how the materials react under heat or flame exposure.
Therefore, a comprehensive approach that considers the interplay of materials within the final application is critical to achieving the desired flammability ratings. It also underscores the need for a tailored approach where manufacturers work closely with customers to understand the specific applications and requirements.
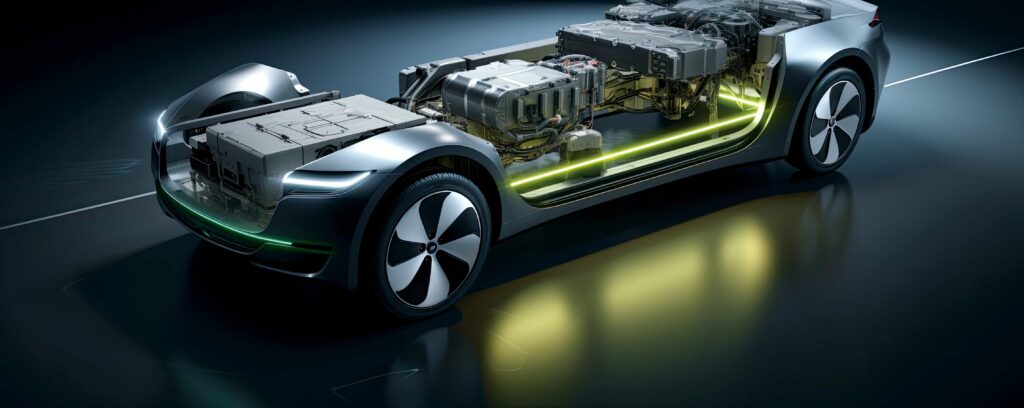
(Image courtesy of Parker Lord)
Testing, validation and ageing
To ensure the reliability and performance of dielectric materials in EV battery applications, rigorous testing and validation processes are used. Testing encompasses a variety of conditions, including thermal cycling, ageing and mechanical stress. A common method is fatigue testing, which evaluates the material’s shear strength over time, providing insights into its long-term performance through S-N curves.
The durability of dielectric materials under conditions typical of EV battery operations is vital. The combination of high voltage and thermal cycling presents a significant challenge, requiring these materials to maintain their properties over time, and through numerous changes in the temperatures and electrical potentials to which they are exposed.
Ageing can affect both electrical insulation and thermal conductivity, making it crucial for manufacturers to conduct rigorous testing and analysis.
One standard method of evaluating ageing resistance involves subjecting dielectric materials to extreme temperature fluctuations under controlled conditions for periods of time, which, while inevitably shorter than the anticipated service life, provides accelerated exposure to these stresses, and that is regarded as a useful equivalent to that service life. Such tests often include exposing materials to cycles ranging from -40 C to 85 C for extended periods – typically, 1000-2000 hours, and assessing the materials’ dielectric properties before, during and after the process.
High-voltage exposure is especially important for dielectric coatings, with one company revealing that it conducts rigorous ‘hipot’ (high-potential) testing of their robustness and durability.
It is crucial that materials are tested for both dielectric strength and resistivity after prolonged exposure to high-voltage conditions, as these parameters are different. Dielectric strength is the maximum electric field that a material can withstand without experiencing electrical breakdown (the point at which it becomes conductive), while resistivity is a measure of how strongly a material opposes the flow of electric current and it is measured in ohm-meters (Ω·m).
Coating manufacturers implement extensive testing to assess how environmental factors, such as humidity, corrosion and immersion, affect dielectric materials. By challenging materials to conditions beyond their expected operational environment, manufacturers can better predict their long-term performance.
One company says its products are tested for resilience against cyclic corrosion and high humidity to simulate real-world conditions experienced by vehicle exteriors. After testing, these materials are subjected to performance tests to ensure the dielectric properties have remained intact.
Specific testing for immersion cooling fluids is critical, especially regarding thermal runaway scenarios. Companies conduct extensive thermal performance tests to develop optimised fluid formulations that prevent cell-to-cell thermal propagation.
These tests are particularly relevant in high-performance applications, such as racing, where thermal management is paramount. In addition to thermal tests, comprehensive quality control measures are established to ensure batches of dielectric materials meet predefined specifications before they are released for use.
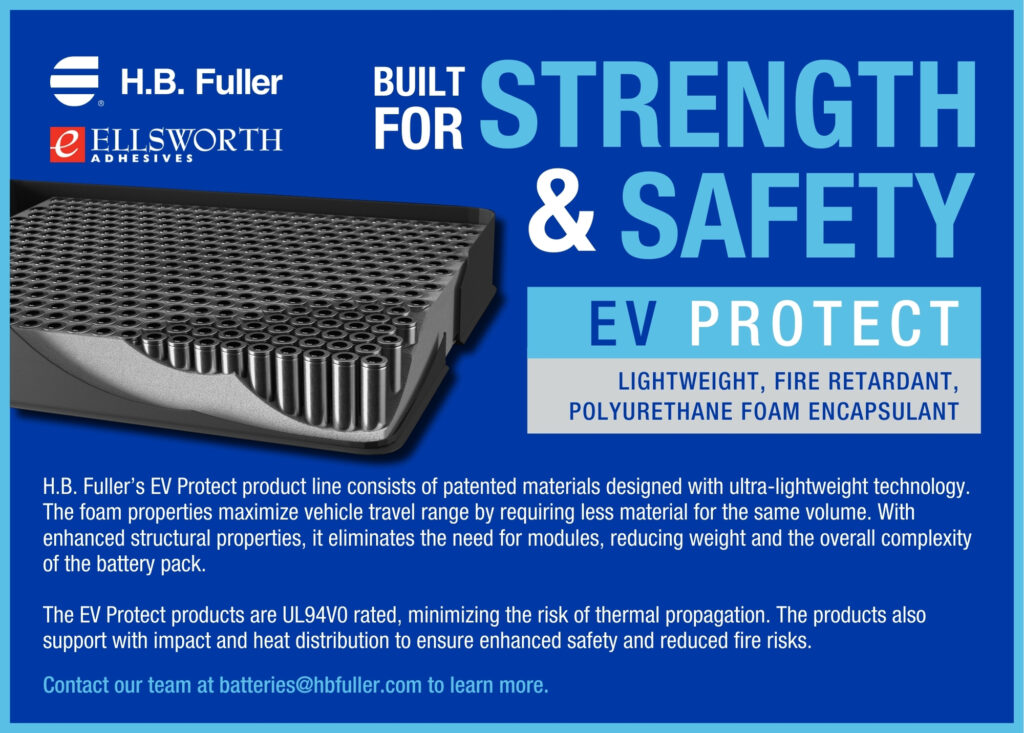
Additionally, dielectric fluids used in cooling applications are formulated with additives that mitigate oxidation and corrosion, extending their operational lifespan. The durability of these fluids is similarly tested through accelerated ageing processes. The results help to fine-tune formulations to enhance their longevity while retaining their essential performance metrics.
The type of ageing tests needed are often customer-specific, and manufacturers typically customise their testing to align with individual requirements; an approach which involves creating tailored ageing scenarios that mimic expected operational conditions.
Manufacturers use advanced ageing setups and simulations to extrapolate the expected lifespan of dielectric materials, assessing their performance metrics before and after ageing, resulting in more accurate predictions of durability under various environmental influences.
The complexity of assessing ageing properties creates a need for reliable predictive models. Manufacturers often rely on both empirical data and simulations to estimate long-term performance, using accelerated ageing chambers that can replicate a range of environmental conditions.
In one example, the firm is part of a business that supplies architectural construction materials and offers warranties lasting up to 50 years, and it has extensive and varied ageing test facilities. These can be used for combinations of accelerated ageing methods, static methods and simulations, all of which it regards as critical to use to ensure the right failure modes are addressed.
Understanding the failure modes of dielectric materials is critical for accurate predictions and product development timelines, especially in industries where the lifecycle of products far exceeds the time required for their design and testing.
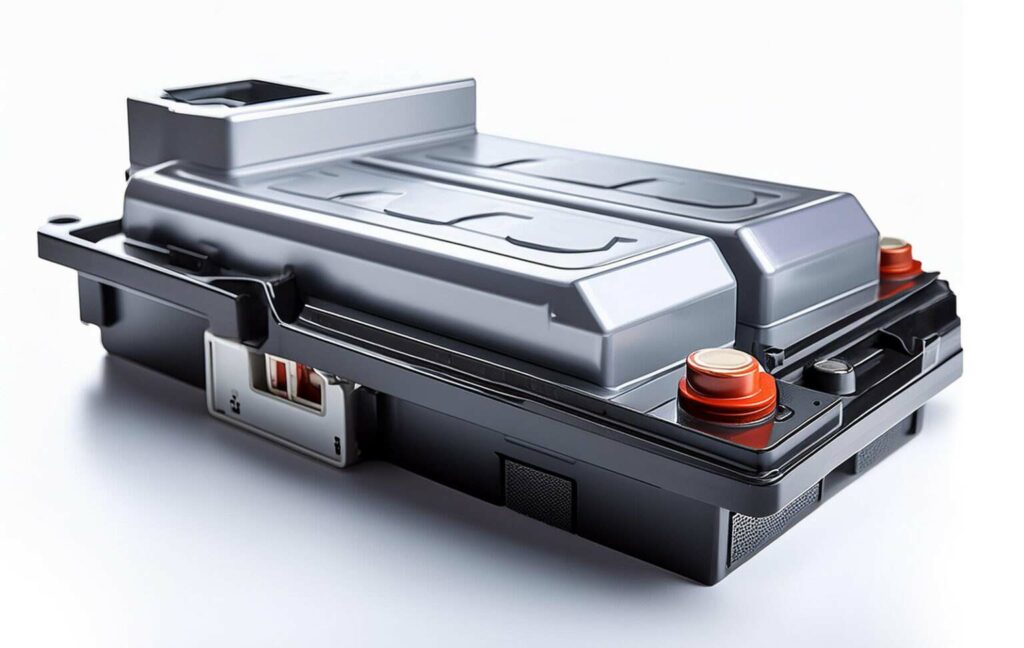
(Image courtesy of AkzoNobel)
Self-healing properties
The concept of self-healing materials has garnered attention in various fields as this capability could extend life and reliability in the event of partial discharge or minor dielectric breakdown.
While the exploration of self-healing properties is still in its nascent stages, some standard dielectric materials exhibit a degree of natural self-healing. For instance, certain thermoplastic materials may exhibit behaviour where small defects can close up under heat exposure. However, comprehensive engineering specifically aimed at self-healing capabilities in dielectric materials remains limited and current market offerings do not prominently feature this attribute as a designed property.
A dielectric fluid manufacturer notes that it doesn’t anticipate any dielectric breakdown events in these applications, given the exceptionally high breakdown voltage of its fluid. In the unlikely event that a breakdown event occurs, the trace quantities of by-products produced by the event would dissipate into the bulk fluid, causing no additional problems.
A different view is expressed by a coatings manufacturer, which says any imperfection in the coated surface would lead to dielectric breakdown and failure. Consequently, self-healing is not an appropriate concept in this space as any damage to the component/coating should be isolated, repaired or replaced. The company points out that electricity is always trying to find the path of least resistance and any imperfection can lead to failure.
Others say the idea presents an opportunity for future research and development that could lead to significant advancements in the reliability and longevity of EV battery systems.
Working with others
Compatibility between dielectric materials and other components is essential to ensure the integrity and efficiency of the entire battery, so compatibility testing is standard practice among manufacturers. This includes evaluating the performance of dielectric materials in conjunction with adhesives, gap fillers, electrolytes, coolants and so forth to verify they will maintain their dielectric properties over time, and in all the conditions to which they are exposed.
In immersion-cooled systems, where fluids circulate throughout the battery pack, the challenge of compatibility becomes more pronounced. Manufacturers typically conduct extensive testing to identify any potential weak points where incompatibility could lead to material failure. For example, materials such as ethylene propylene diene monomer (EPDM) used in hoses might not be compatible with certain dielectric fluids, necessitating alternative materials such as nitrile butadiene rubber (NBR).
It is essential to consider the specific chemical nature of coolants and electrolytes during the selection process. Pressure-sensitive adhesives, for instance, require careful consideration of their solubility parameters in relation to the chemicals they will encounter.
Ongoing collaborations between manufacturers and clients facilitate the identification of compatible materials and inform the development of tailored solutions.
The interconnected nature of these components calls for a synergistic approach to testing, where the combined effects of coatings, adhesives and other materials are evaluated.
Customisation becoming the norm
Customisation is a significant aspect of the development process, with companies providing materials tailored to meet specific design requirements, and accommodating a range of form factors and thickness variations.
The lead times and costs associated with customisation vary, influenced by factors such as minimum order quantities and the complexity of requested modifications.
For instance, rapid prototyping capabilities enable a quick turnaround for samples, while industrial trials can typically be conducted within a month to six weeks, depending on product availability and complexity.
The need for customisation arises from the dynamic nature of EV battery design, where manufacturers seek innovative solutions to optimise performance and reliability. Dielectric materials must meet stringent specifications, and suppliers often engage in iterative testing and development processes to ensure the materials align with the evolving requirements of original equipment manufacturers (OEMs). Collaboration with OEMs is essential to fine-tune material properties and application methods for seamless integration into manufacturing processes.
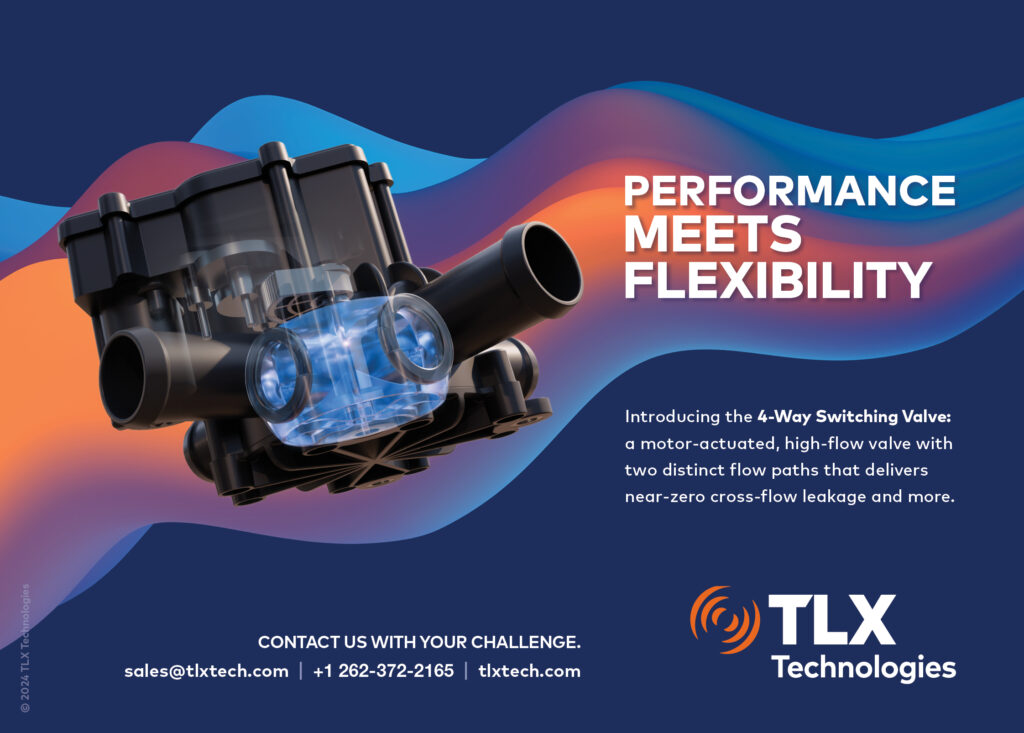
Sustainability cycles
The sustainability of dielectric materials is becoming more important as the EV market expands. Various approaches focus on recyclability and the inclusion of environmentally friendly components. Suppliers prioritise developing products that not only perform well, but also facilitate the recycling and reworkability of battery systems.
For example, certain UV-curable dielectric coatings enable multiple repair cycles, with one supplier emphasising that one of its families of coatings is reworkable and repairable as many times as is needed before being sent down the UV-lamp conveyor belt to be cured in seconds. This significantly reduces waste and energy consumption compared with traditional curing processes that require drying ovens.
Also, suppliers are moving away from high global-warming potential (GWP) materials, and favouring hydrocarbon-based fluids and biodegradable components wherever feasible. The latter have a lower GWP and environmental impact than, for example, fluorinated fluids that use per- and polyfluoroalkyl substances (PFAS), which fall into the category of ‘forever chemicals’.
The integration of recycled content into coatings is another strategy to enhance sustainability. Suppliers are also exploring new bonding and
debonding solutions that could promote sustainability by simplifying the disassembly and recycling of battery packs at the end of their life cycle.
Lifecycle assessments and environmental product declarations (EPDs) are used to inform OEMs about the carbon footprint of dielectric products. These provide valuable insights into the embedded carbon of the materials and help suppliers to show their commitment to sustainability goals, such as net-zero emissions.
Co-operation efforts extend to exploring end-of-life considerations, where suppliers work with OEMs to identify degradation mechanisms and develop strategies for disassembly and recycling.
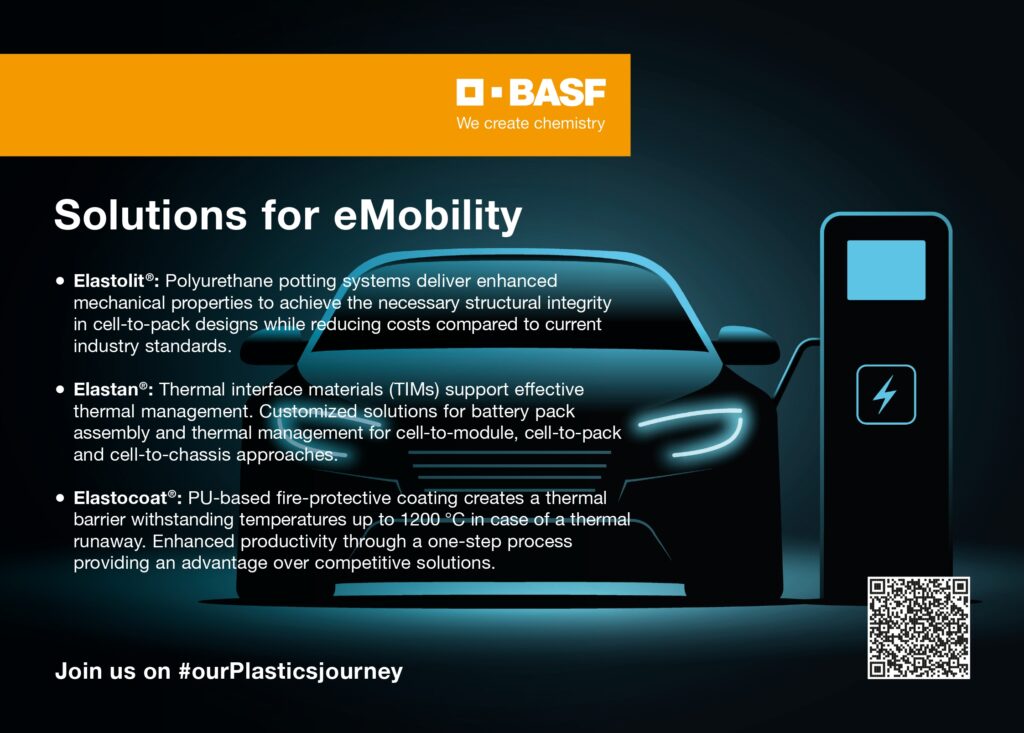
Technical support
Technical documentation and support during the design and development phases are vital in ensuring the successful integration of dielectric materials. Leading companies work to provide a comprehensive array of documentation, including technical data sheets, safety data sheets, application notes and compliance documents. These resources aid engineers in understanding material properties, safety considerations and application methods.
Collaboration is emphasised as a crucial element in the development process. Suppliers engage closely with their customers, offering engineering support for designing thermal management systems and integrating monitoring solutions. This collaborative approach ensures manufacturers receive tailored solutions that meet their specific needs.
The transition from concept to manufacturing at scale is a significant challenge for many battery makers. To facilitate this process, suppliers offer turnkey support and solutions, focusing on optimising manufacturing capabilities. Dedicated teams provide expertise in designing application processes and coating products to ensure a smoother transition from laboratory-scale to industrial-scale production.
One supplier works hand-in-hand with customers to determine the best product for their needs by providing technical documentation, test reports and guidance from its team of in-house experts. Specific testing can be carried out at its global r&d facility/corporate headquarters, including a wide range of formulating, analytical, mechanical, ageing/cycling and dispensing tests.
The team also provides hands-on, on-site support when needed, so the client is fully prepared with the best product and ready to seamlessly implement it into their manufacturing process.
Ensuring compliance with industry standards and maintaining high-quality production processes are critical components of dielectric material development. Leading suppliers adhere to automotive quality standards, such as IATF 16949 and ISO 9001, which encompass rigorous documentation and quality control systems. These standards dictate the processes for product development, quality assurance and measurement systems, ensuring materials meet the performance expectations of OEMs.
As the EV industry continues to evolve, the importance of these materials will only grow, driving ongoing innovation and adaptation by suppliers and manufacturers alike. The shared goal remains clear: to develop high-performance, environmentally responsible dielectric solutions that enhance the safety and efficiency of battery systems.
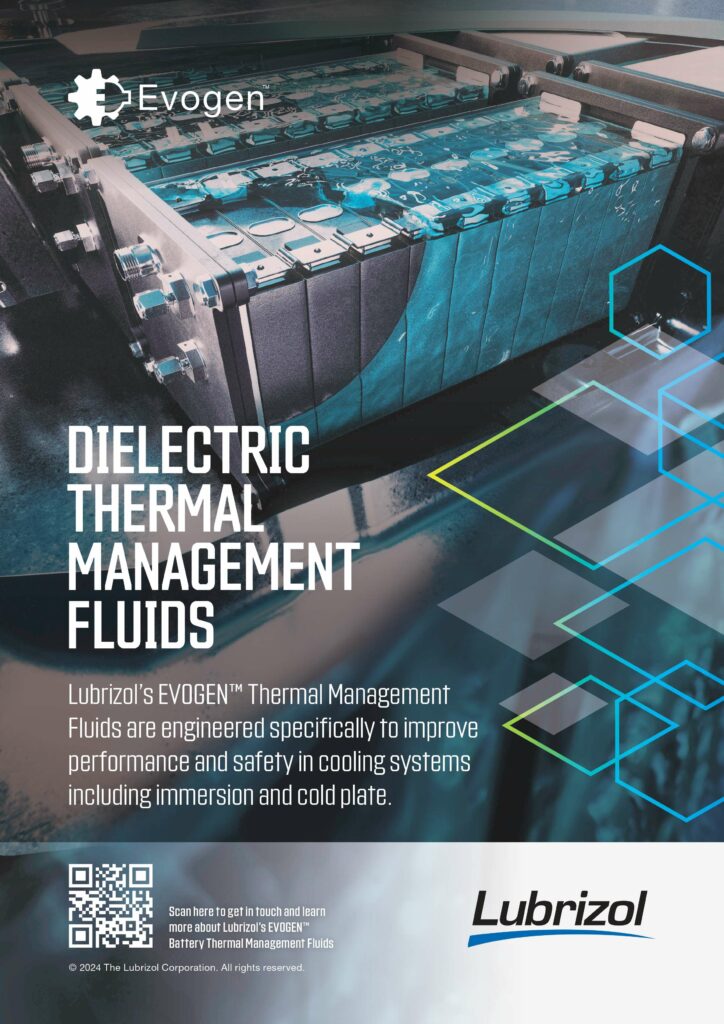
Acknowledgements
The author would like to thank the following for their help with this feature: Germaine Mariaselvaraj, senior technical specialist at H.B. Fuller; Andy Richenderfer, senior research engineer at Lubrizol; Jacob Collison, global market manager, electrification, automotive coatings, at PPG; and Jeff Peet, r&d manager, adhesives systems, and Fei Wang, r&d manager, EV platform, at Saint-Gobain Tape Solutions.
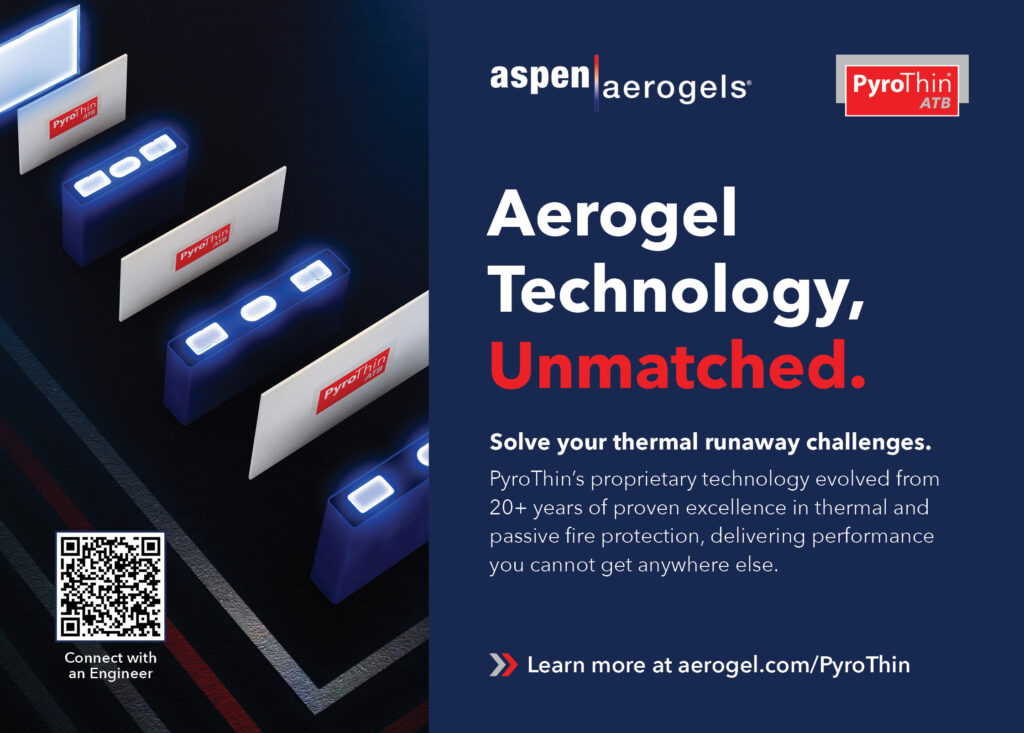
Some suppliers of battery dielectric protection
AkzoNobel
Arkema
Avery Dennison Tapes
Axalta
Cargill
Castrol
Exoes
H.B. Fuller
Lubrizol
Parker Lord
PPG
Saint Gobain Tape Solutions
Specialty Coating Systems
Shell
The Chemours Company
TotalEnergies Lubricants
+31 88 969 7809
+33 1 49 00 80 80
+1 866 462 8379
+1 855 629 2582
+1 800 227 4455
+44 1932 775 644
+33 9 72 50 30 86
+1 651 236 5900
+1 440 943 4200
+1 800 272 7537
+1 412 434 3131
+1 518 686 7301
+1 317 244 1200
+1 832 337 200
+1 800 441 9484
+33 1 4744 4546
ONLINE PARTNERS
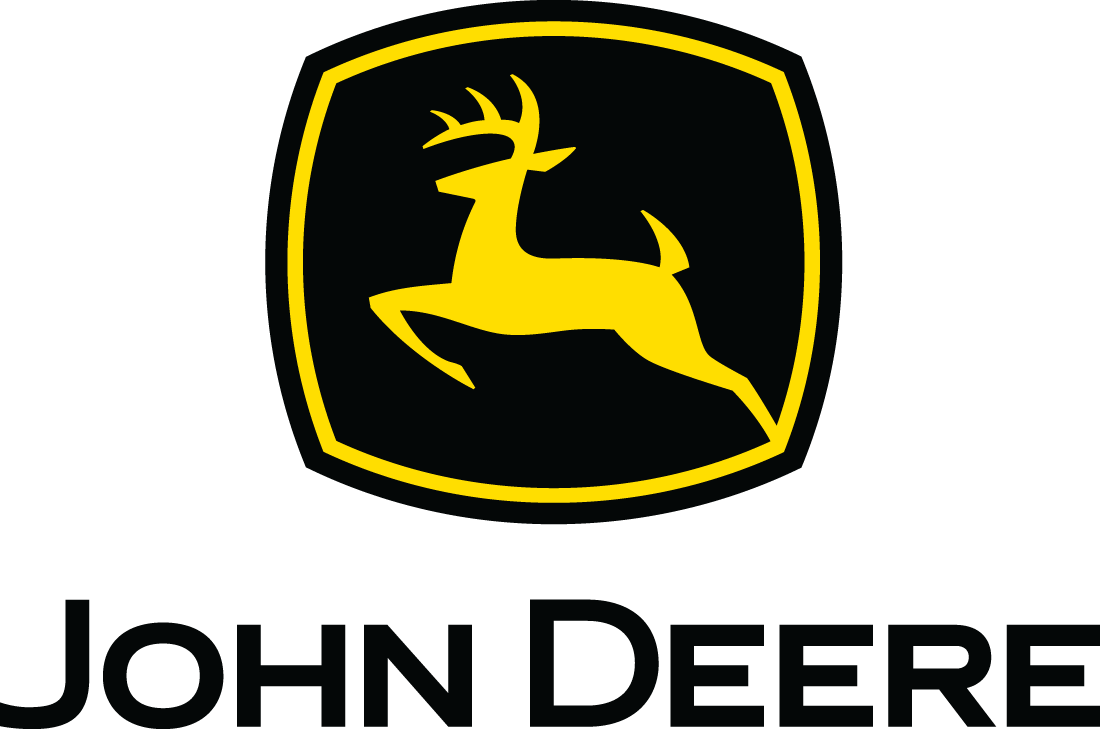
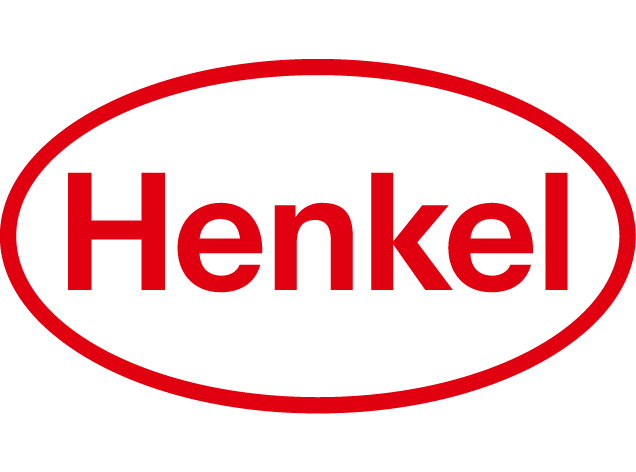
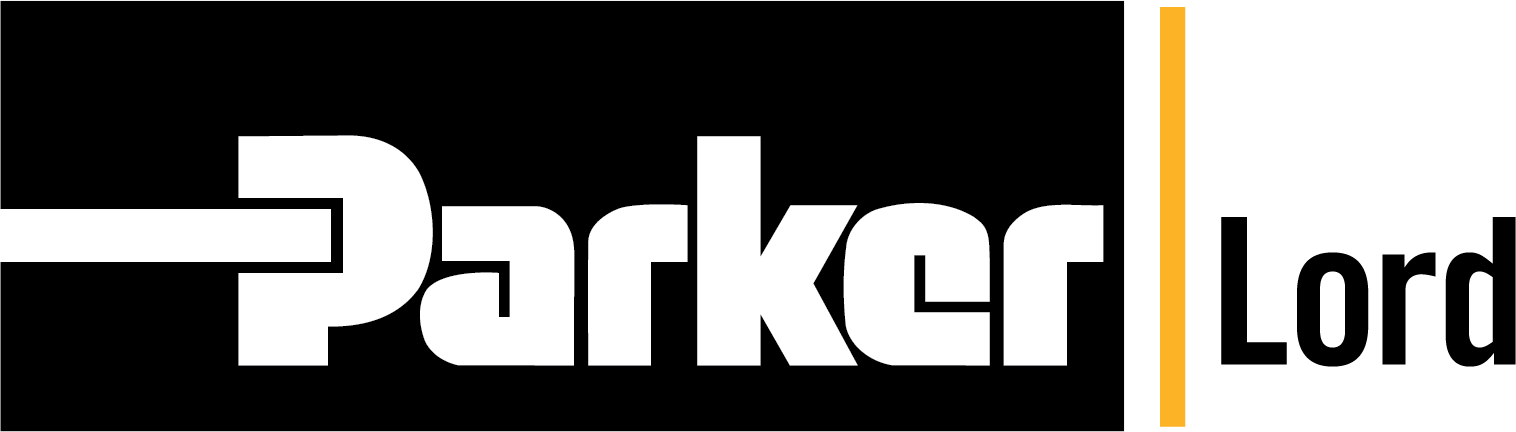
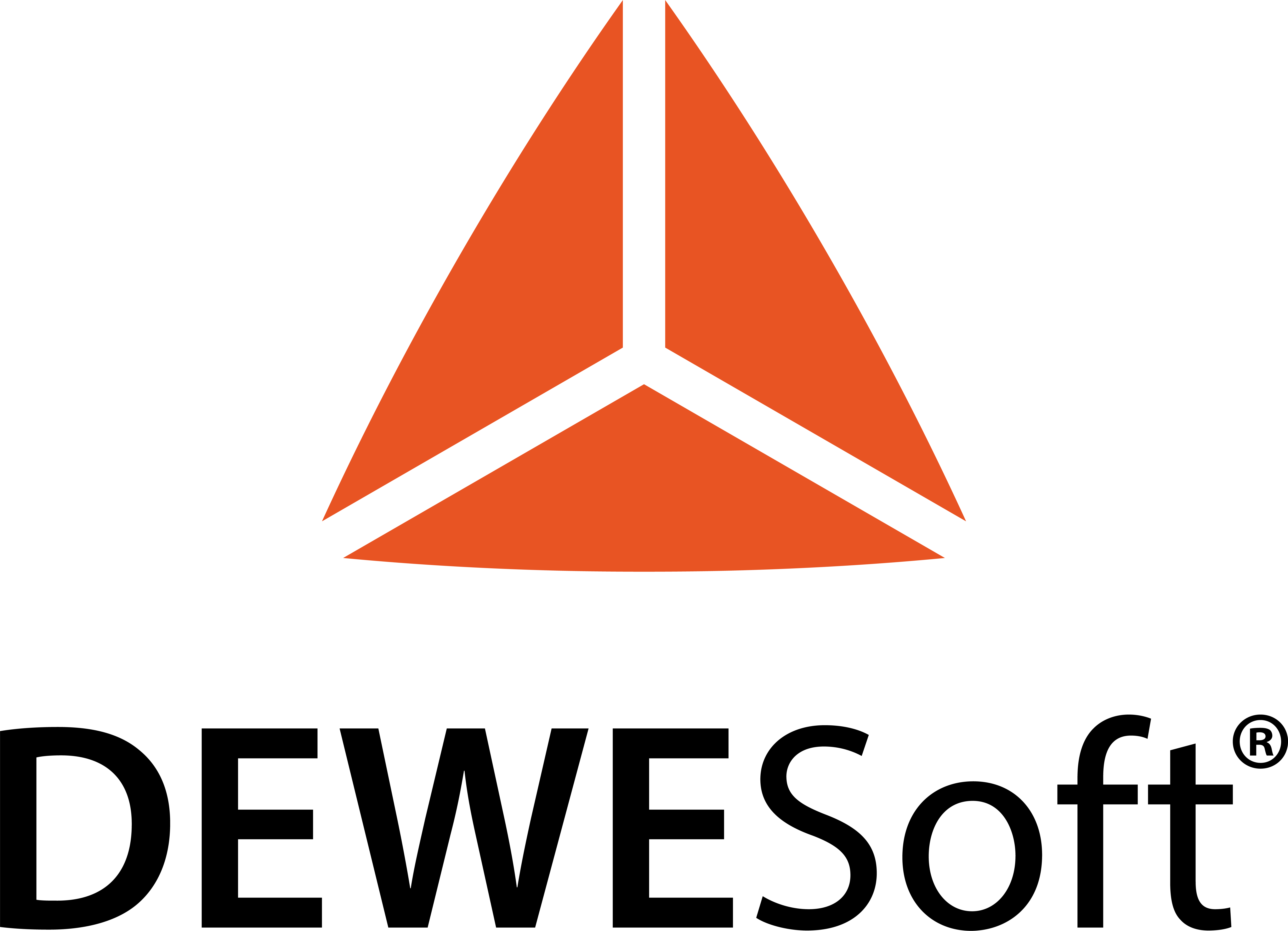
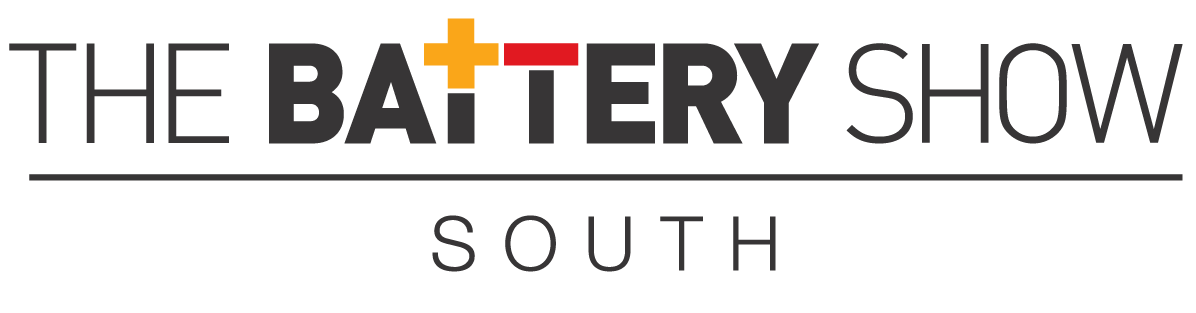
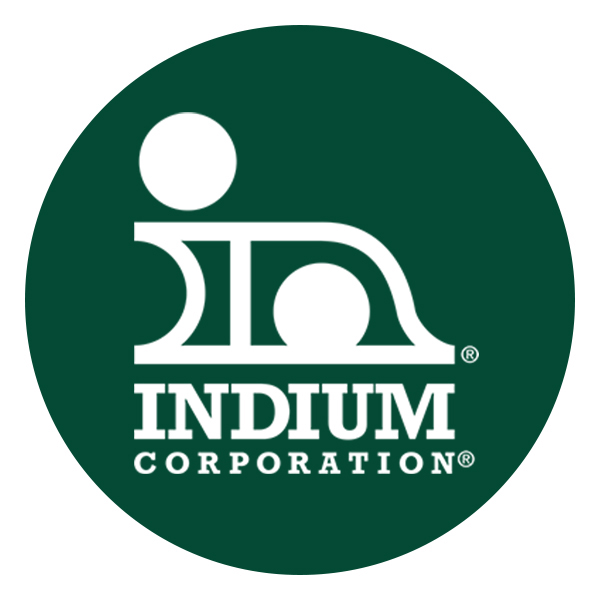

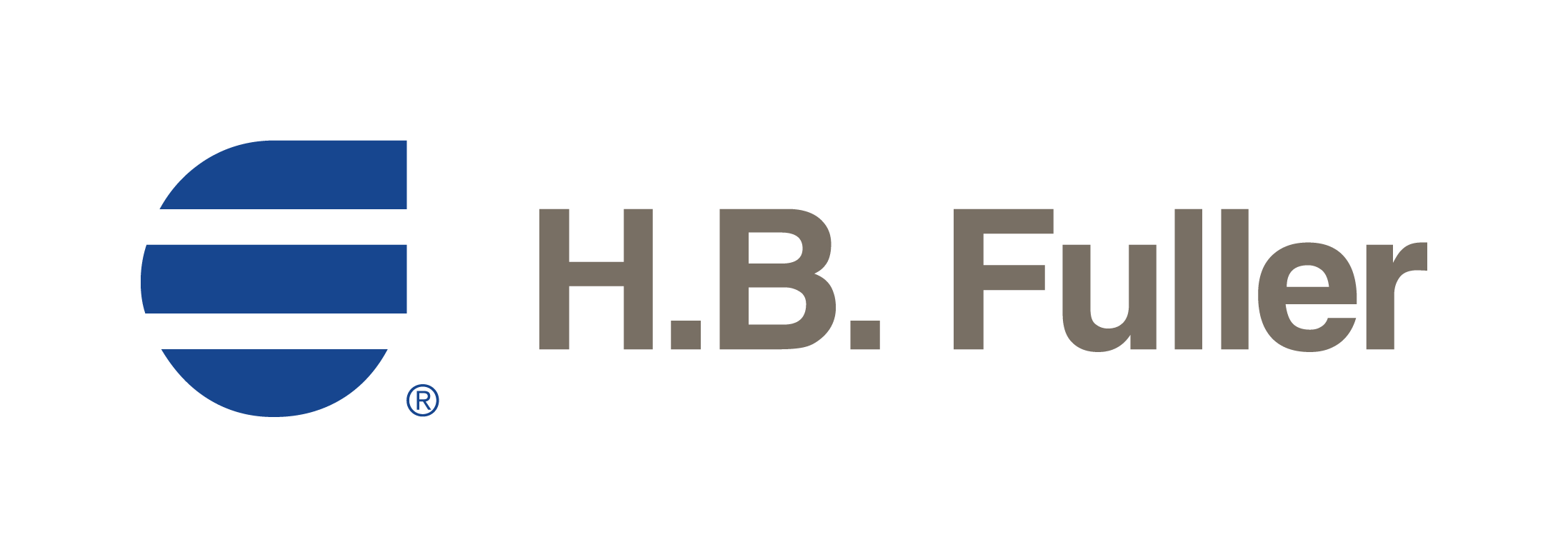
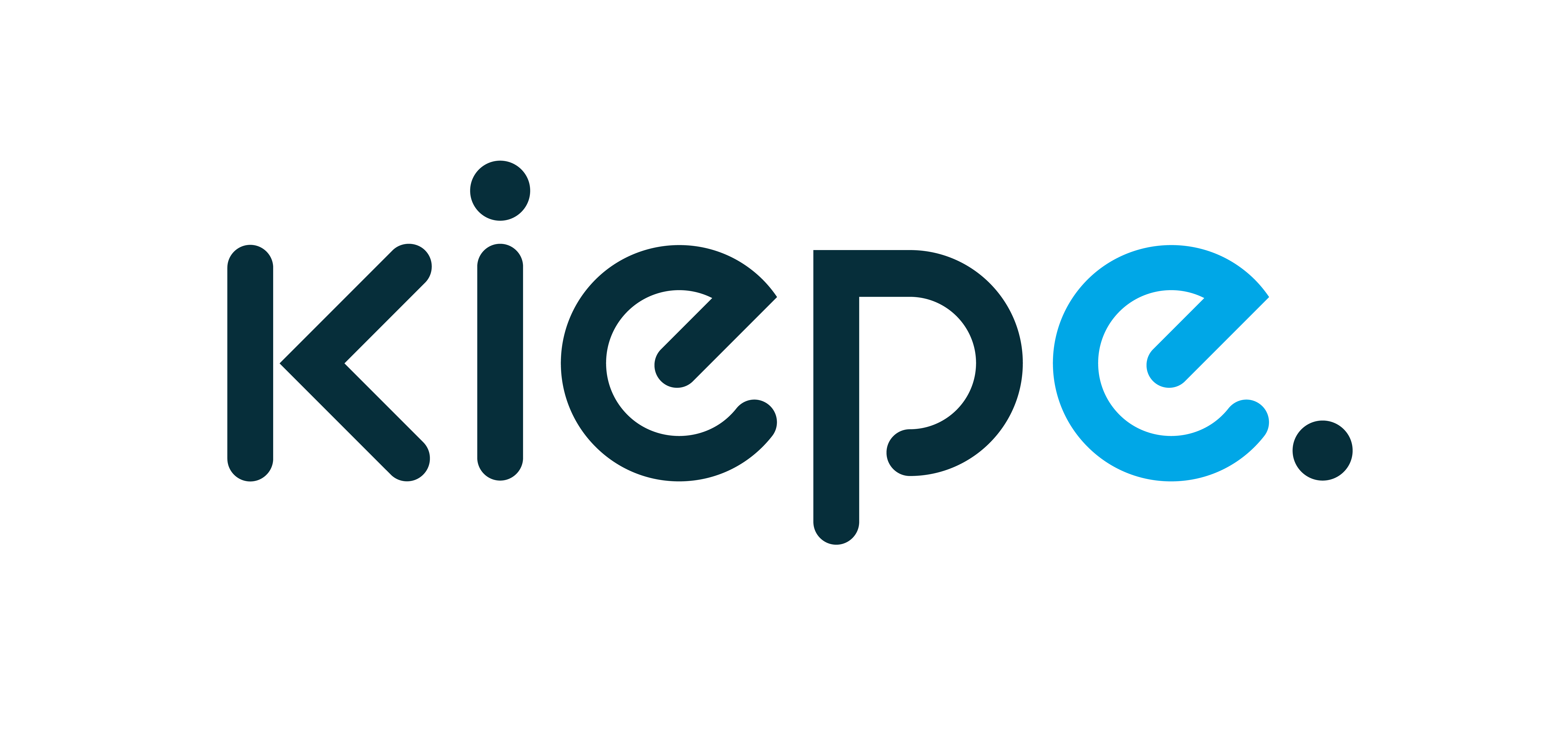
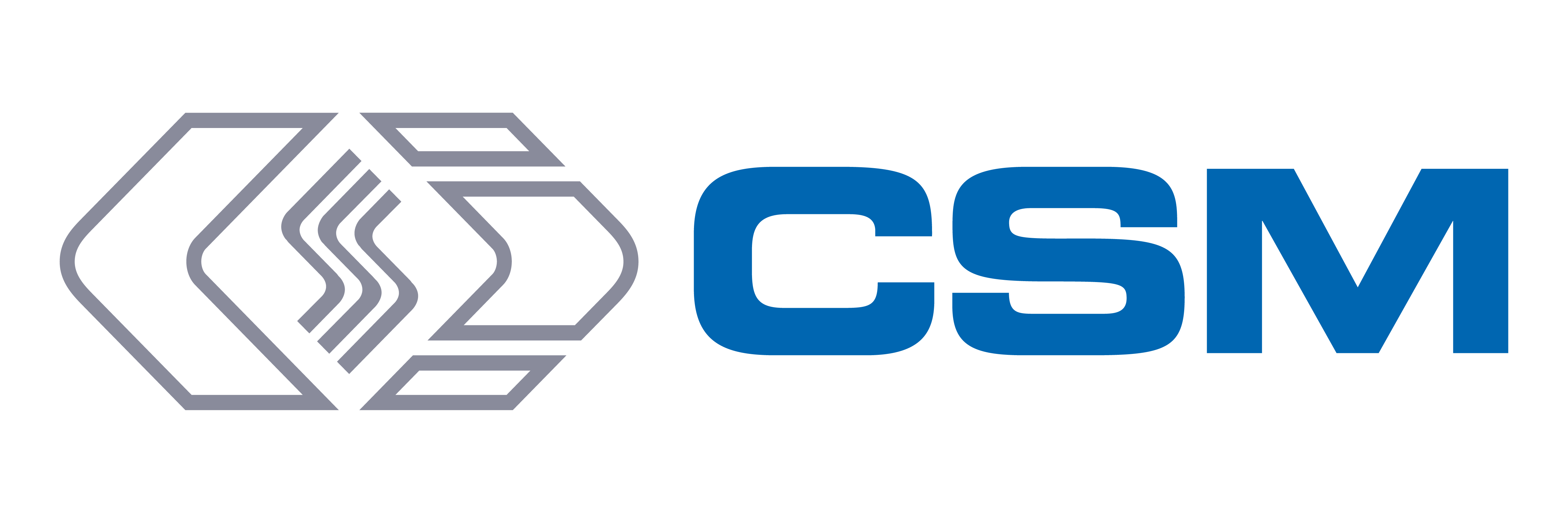