Battery coatings
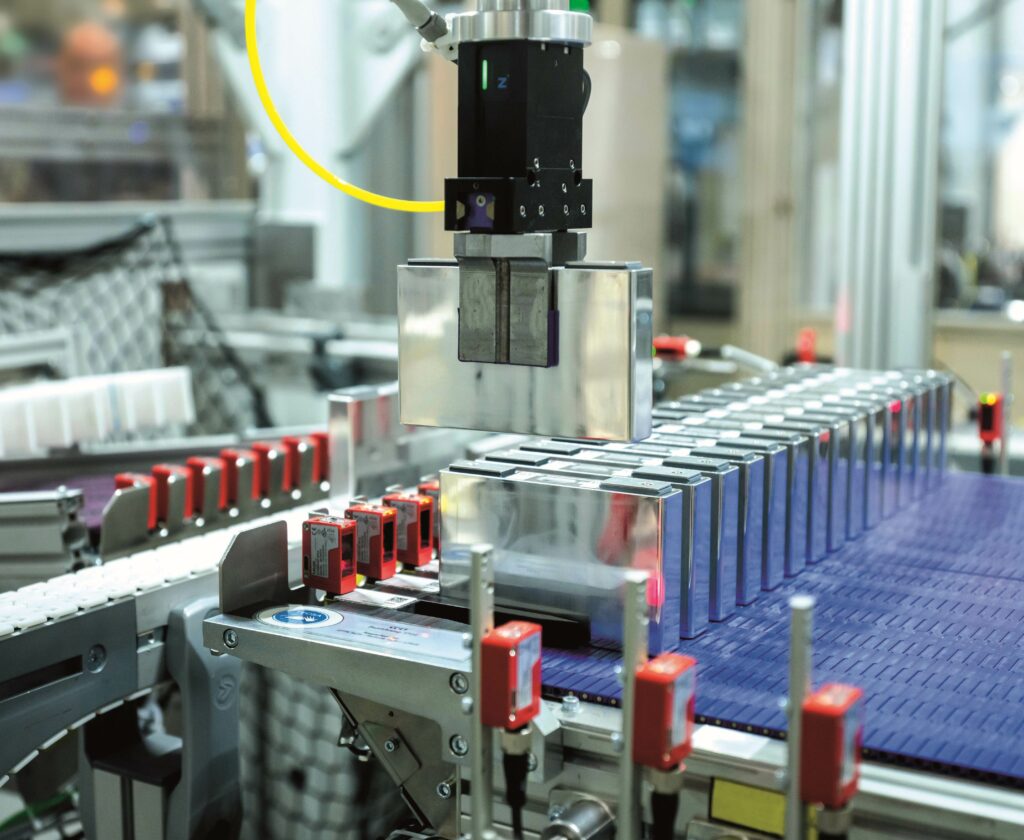
(Image courtesy of BMW)
Bending the laws of physics
Peter Donaldson finds complex challenges within the development of coatings for battery applications
Coatings play a crucial role in battery cells, modules and packs. Evolving continuously, they are engineered to enhance performance, safety, reliability and longevity in these complex, high value electrochemical systems. While the active materials that constitute the core components of cells – the anode and cathode – are applied to their substrates as coatings, this article will focus mainly on the supporting players. These are coatings that perform functions such as electrochemical protection, thermal management, fire protection, dielectric insulation, or serve as barriers against moisture and contaminants. They may not be the stars of the show, but the show won’t go on without them.
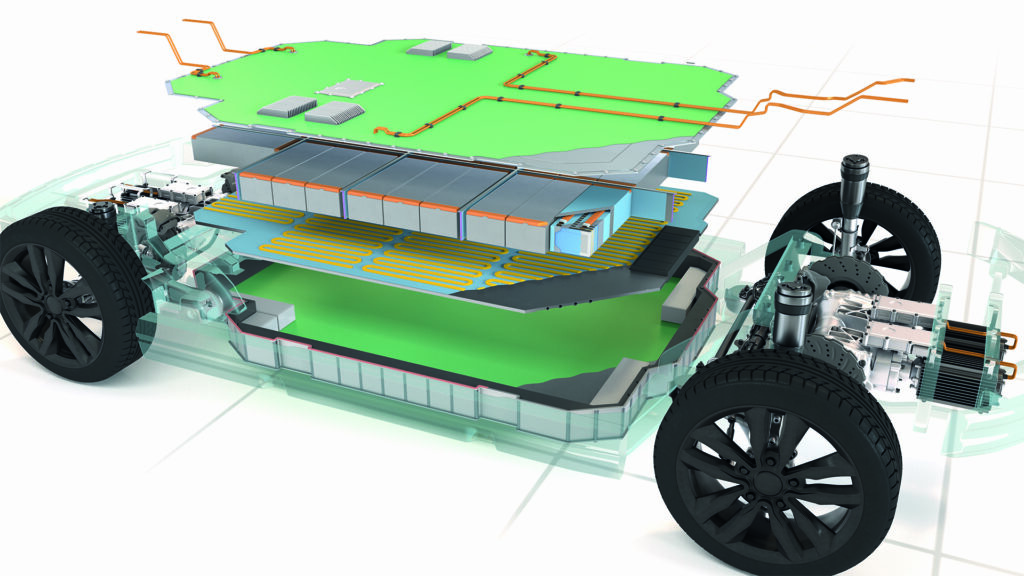
(Image courtesy of PPG Industries)
Functional variety
Inside the cells, coatings are applied to enhance mechanical and thermal stability; particle coatings to improve the cycle life of active materials and conductivity of the current collector foils, to reduce cell resistance and improve adhesion of the active material on these foils, explains Dr. Tobias Knecht, battery cells specialist at Henkel. The company is working on a variety of different products ranging from fire resistant coatings of battery lids, metal pre-treatments that suppress corrosion of battery housings, dielectric coatings for that are typically applied on battery cans and conductive coatings of current collector foils.
Also within the cell are coatings that go on to the separators. The separators themselves are selective insulators generally made from polymer materials that block the movement of electrons but allow ions to pass through them, so they are fundamental components of cells. Increasingly, coatings are applied to separators to enhance their electrical isolation. “We want to make sure electricity can flow in some places but is not able to flow in others,” says Calum Munro, associate fellow at PPG.
Coatings on the outer surface of each cell provide electrical isolation between cells and other components, but also provide protection from corrosion. The electrical demands on dielectric coatings are growing in-line with battery voltages, which regularly reach 800 V, with many new systems exceeding 1000 V. “With those high voltage systems, we’ve got to make sure that electricity doesn’t do what it likes to do, which is find the path of least resistance. Sometimes that’s just jumping across spaces between components,” says Jacob Collison, global strategic product manager at PPG.
Coatings are applied throughout an EV battery pack, from fire protection materials on the lid, anti-corrosion protection inside and out, on cooling plates and pipes, on busbars and in cells. Corrosion protection is also vital on the outside of the pack, he adds. “There are a lot of warranty failures that are associated with corrosion on the battery structure itself. Even if it doesn’t penetrate the casing, it can lead to other electrical failures.”
Lithium-ion cells only operate efficiently over a very narrow temperature range, Collison notes, and coatings are part of the thermal management solution, variously moving and blocking heat, and containing battery fires. “There’s a holistic approach to fire management in the industry, and we feel that we can commit as a last line of defence,” he says.
“Typically, we’ll try to keep the fire within a module or, with the newest designs, within the pack, to make sure that the fire doesn’t get into the cabin. The best way to compartmentalise a fire is to protect the battery box, and our coatings are able to maintain the integrity of the enclosure under these very extreme, high temperature, highly erosive conditions.”
Polymer composite materials increasingly used in vehicle and battery structures are often effectively transparent to electromagnetic radiation. That potentially causes interference problems with electronics in the battery such as the battery management system (BMS), general vehicle management and safety systems. “We need to make sure that they are protected from crosstalk that would diminish their effectiveness. So we’ve got a range of coatings and other speciality surface materials that help with electromagnetic shielding,” Collison says.
Parker Lord provides battery, cooling plate and enclosure coatings to provide electrical insulation and enhance thermal management, with material options including PET film, powder coating, thermally cured and UV cured coatings, says Eric Dean, global bd manager with Parker Lord’s Engineered Materials Group. The company’s thermally cured JMC-700K epoxy resin coating, for example, is routinely used on battery enclosures and cooling plates, while its UV cured Sipiol UV line is also used in these applications and additionally on cells. Both have high thermal conductivity, which enables good heat transfer and helps ensure long-term reliability.
“We design our solutions from the resin molecules up and then we formulate them into composite solutions for situations where a single material would not give the right balance of performance. We’re able to get that balance from the formulated composite that makes up the coating,” says Munro.
The company has deep expertise in epoxies, for example, and uses them very broadly, he adds. “We formulate those in ways to give exceptional corrosion performance. We’re also able to adapt them to become very strong adhesive materials, or we can adapt them so that they can change their nature when exposed to high temperatures, to become a thermal barrier coating. All of those are based on one chemistry set.”
PPG engineers coatings from polyesters, polyurethanes and acrylics, and combinations of them. “We’ve got different tools and approaches that we use to join those polymers together so that they form cross-linked functional coatings. There is a host of approaches to that chemistry that influences whether we end up with a polyurethane or a polyurea at the end of the day,” Munro says. “That allows us to meet a lot of challenges in terms of curing characteristics. We can make things cure at very low temperatures, under ambient conditions,” Munro says.
“Also, the way that we design the polymers and link them together, we’re able to make materials that are liquid as they’re applied, but form a solid without requiring any solvent,” he says. This provides advantages in the management of volatile organic compounds (VOCs). “If we’re not putting any solvent in, we’re able to reduce the carbon footprint associated to their production and abatement, allowing us to get to a very low or no VOC emissions, thus avoiding air pollution.”
PPG also makes other liquid coatings to which functional groups can be added to make them react to electromagnetic radiation of various wavelengths, triggering the curing process. “We don’t need to heat up a massive oven to get the coating to cure. We’re able to do that very effectively with low-energy light sources that can include ultraviolet, near infrared and others,” he says.
Coatings can also be applied as dry powders, which can be sprayed or parts can be put into a cloud of powder, usually with opposite electrostatic charges applied to part and powder to aid adhesion before the cure. Dry powder coating, Munro says, also eliminates solvents and associated VOCs. Both powder and liquid process provide for options to recover excess coatings for reuse.
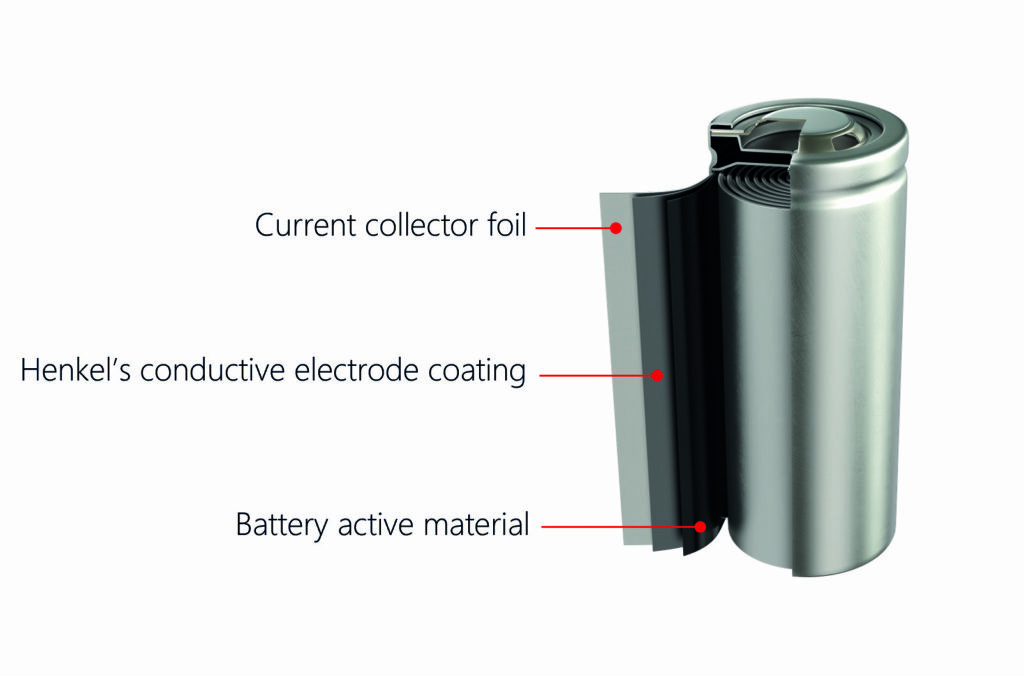
(Image courtesy of Henkel)
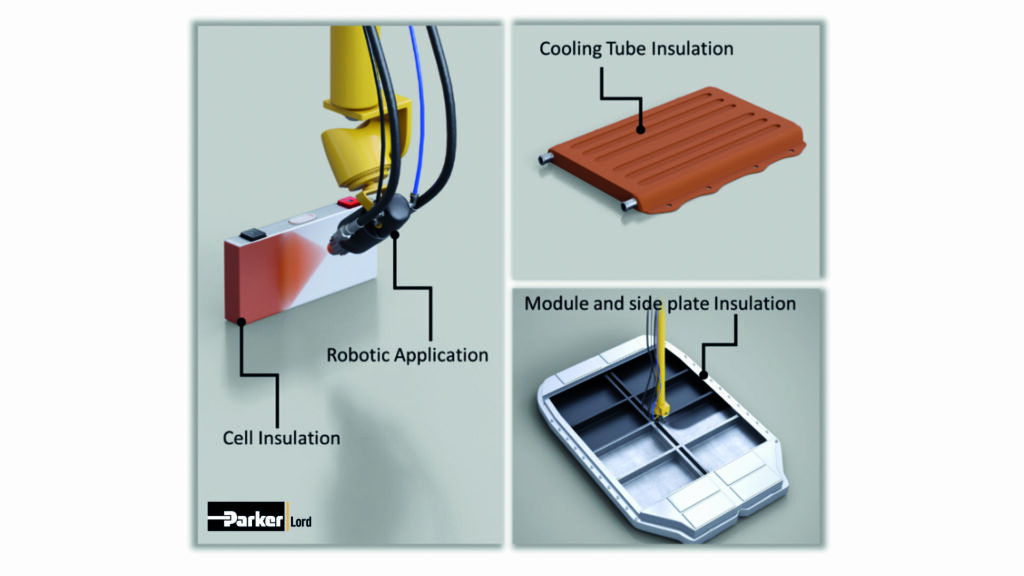
(Image courtesy of Parker Lord)
A decade of progress
The current period of rapid expansion of e-mobility is still fairly young, and the last decade or so has seen many significant improvements in coatings in both materials and application techniques. Henkel’s Dr. Knecht highlights fire-resistant coatings, UV cured dielectric materials, and carbon-based conductive coatings. Fire-resistant coatings can greatly increase the temperature stability of steel and aluminium lids, improving the safety of the pack, he says, adding that coatings have become thinner and are more durable against flame and particle penetration.
UV cured dielectric coatings have been developed that can be applied to cells after production. They are designed to adhere strongly to the cells and to provide reliable dielectric protection over their lifetimes. “In contrast with adhesive films, the adhesion is stronger, and in combination with thermal or structural adhesives, these coatings can enable cell-to-pack battery designs,” he says.
It is a similar story with electrically conductive coatings used in electrodes. “Carbon coatings for energy storage applications emerged more than 20 years ago and have been continuously improved to work with the latest lithium-ion cell technologies” Dr. Knecht remarks. “They have become thinner, more conductive and have enabled stronger adhesion between the active materials and current collector foils.”
With its JMC epoxy product line, Parker Lord’s development focus has been on improving resistance to corrosion and heat, and increasing both dielectric strength and thermal conductivity. “About five years ago, we noticed that the PET films were the weakest link in the stack of battery enclosures in terms of bond strength, and finding an adhesive that could bond to them was difficult,” Eric Dean says. “So we invented Sipiol UV, which could be applied and safely cured in seconds using UV light, offering high dielectric strength, edge coverage, and adhesion. After improving the thermal conductivity, applications like enclosure and cooling plates came next.”
Massive change in the industry over the last 10 years has mainly been driven by accelerated adoption of EVs, and many players are at different points on the learning curve, Collison at PPG considers. This has necessitated a shift to large scale manufacturing and the need to learn rapidly as unanticipated problems drive changes to designs.
One kind of change this has driven is what Munro calls an “evolution from parts to paints” (most coatings can be thought of as paints, he says). He explains that when some of the challenges were first recognised as such, there were solutions that could be adopted from other industries that had experienced similar problems. However, these tended to involve the addition of extra parts.
“Any time you add a part you’re adding complexity”, he notes. “It’s another thing that has to be attached, integrated or managed. So we’ve seen a shift from parts to paints where specialised functional coatings can be directly applied to existing components to manage the problem.
“There’s been a move during that time frame to minimise complexity while maximising productivity and sustainability,” he adds. “Instead of trying to solve, say, six different problems with six different paints, the aim has been to solve those six problems with maybe two paints or speciality materials, and to try to drive performance up so we need less to do more.”
Collison notes that, today, change in the automotive space is at its fastest since the 1920s and ‘30s. “We have new designs every six to nine months that we’re having to manage. And this is because of the rate at which engineers are finding new development pathways that increase the longevity, power density, drivability and range of the next generation of vehicles.
“And modelling has gotten better, to where we have a clear picture of what we need today, but that could be radically different in two years time,” he observes. “So we have to look into the crystal ball a little to understand what we’re going to offer in two, three or five years.”
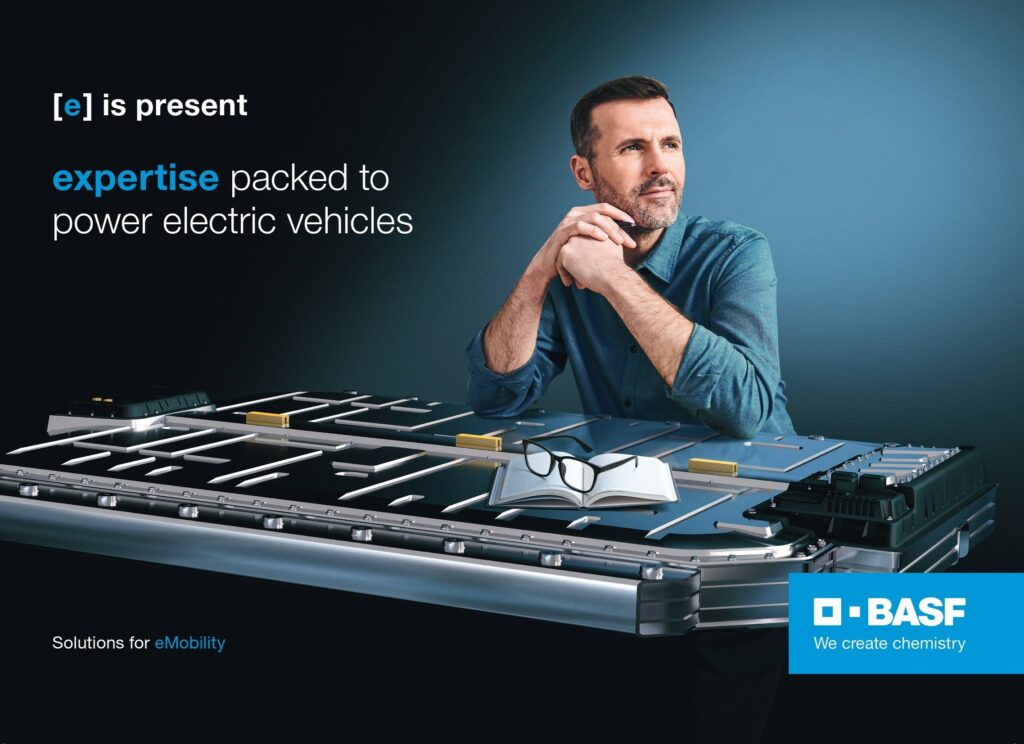
Development challenges
In this environment, developing coatings for such demanding requirements presents many challenges. According to Henkel’s Dr Knecht, the principal problems in the realm of electrical protection of key battery components include ensuring the coating’s own ability to be stable at extraordinary high voltages, along with typically challenging lifetime requirements.
With coatings that contribute to thermal management, thermal runaway containment and the prevention and mitigation of fire, the challenge is to ensure that they achieve the right thickness, temperature stability and mechanical stability, and resistance to penetration by energetic particles, along with ease of automated application.
Getting the thickness right is also important for dielectric coatings, as are selecting and fine tuning the curing technology, such as UV curing of coatings on cell cans. Here, ensuring that the coating adheres strongly to the can through the life of the cell preserves structural integrity, Dr Knecht remarks.
“Ultimately, any one of these requirements is probably pretty easy to tackle in isolation,” emphasises Dean at Parker Lord. “What makes the work we do fascinating is finding novel approaches to balancing these properties.”
Such balancing acts, he says, include developing sprayable materials with exceptional edge coverage, along with achieving high thermal conductivity and high dielectric insulation in less than 100µ thickness while maintaining compliance with UL 94V0. This is the standard that covers flammability of plastic materials used for parts in a wide variety of devices and appliances, including batteries.
At PPG, Munro describes balancing multiple properties as a game of trade-offs. “There’s never going to be something that’s the best in every category. So understanding issues that are specific to the system, the environment and the component is critical. A good example is thermal conductivity and flexibility, which tend to be opposing properties,” he explains.
“So the higher your thermal conductivity, the more balancing is required in achieving goals for the bending or impact resistance. This high thermal conductivity is fine if the application is on a cooling plate, which is stiff and rigid, as it helps it shed heat. But if on flexible cooling tubes it could potentially face cracking problems.”
One way of tackling this kind of problem is by developing engineered systems using multiple different layers that build upon one another, Munro explains. This may include a corrosion protection coating as a base layer, such as a typical e-coat or pre-treatment with a dielectric coating, perhaps applied as a powder, on top of that, and then a fire protection layer.
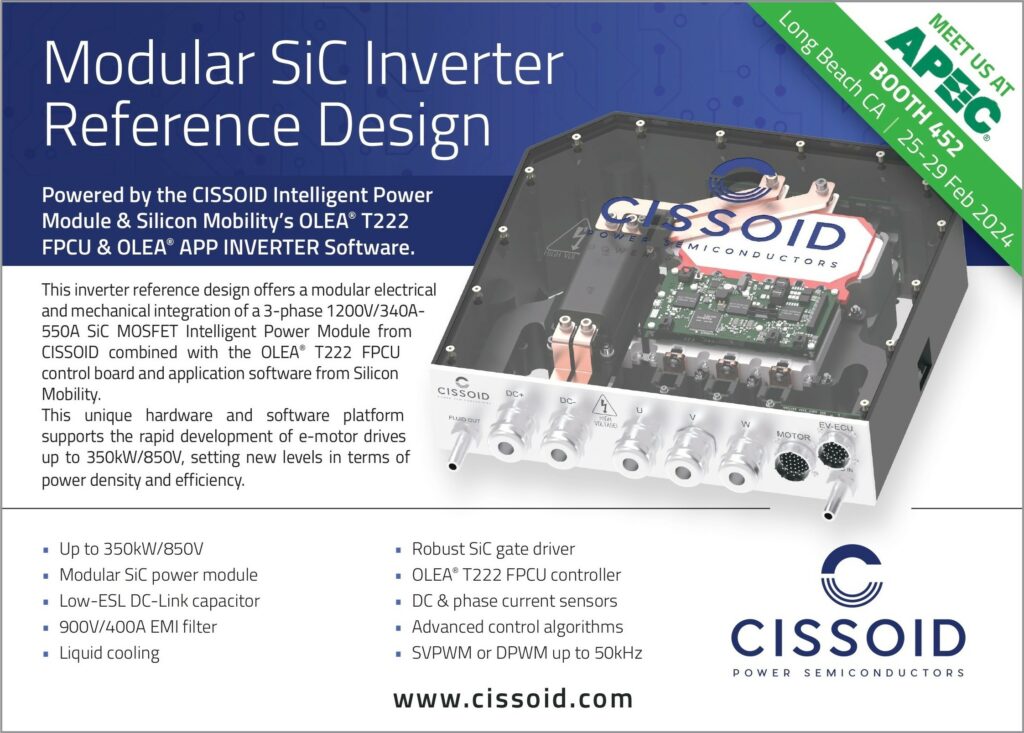
Developing multi-functional coatings is a challenge, particularly if two or more of the required functions seem incompatible. Solutions to this kind of problem have been found in material design, Dr Knecht at Henkel argues, along with selection of filler packages that can, for example, enable thermal conductivity while maintaining dielectric protection.
“A lot of functions the industry thinks are incompatible just haven’t been figured out yet, excluding those few prohibited by the laws of physics,” argues Parker Lord’s Dean. “We have extensive expertise in all the primary chemistries: acrylic, silicone, urethane, and epoxy, and we make materials that flow like water or stretch like rubber bands,” he says.
“The all-in-one coating system is on everyone’s wish list, but we have to come to terms with the fact that not all desired functions can be combined,” says PPG’s Collison. “This is why in standard automotive painting you have a primer, a base coat and a clear coat working cohesively together. We have to think about the engineered battery pack in the same way.”
Munro adds that this is not a new set of challenges. “We’re constantly seeing a desire to be able to do things that feel diametrically opposed,” he adds. “We realise that we can’t break the laws of physics, but very often we find that we can bend them, and that there are typically exceptions to the rules.”
Munro explains that most coatings are composite materials with, from an engineering point of view, similar benefits to those embodied in bulk materials but scaled down. “We’re very good at engineering at a nano scale, up through meso scale and micro scale in different materials, and that allows us to bend the rules pretty significantly.”
Engineering a surface material that is both flexible and thermally conductive is one of these rule bending exercises. “By developing a composite approach on a microscopic scale, we’ve been able to use vibrations to make heat move while we’re actually dampening other vibration, he reports.”
Further, both time and external stimulus can be taken into account when creating a material to meet conflicting requirements. “If we take a step back and think about it, the material is not always expected to do opposing things at the same time,” Munro says. “Some of the coatings that we’re applying can switch their thermal characteristics so that under most conditions they do a great job of moving heat, but if the temperature exceeds a threshold it will activate and become a thermal barrier instead.”
“With the industry, there has not been much consolidation at this point in terms of design approach,” adds Munro. “And so all those trade-offs are going to be specific to individual designs and customer preferences. We are very aware that there is not necessarily a single solution that will fit everybody’s needs,” he reflects, “so we can work to understand what our customers are really trying to achieve and help guide them to the best approach.”
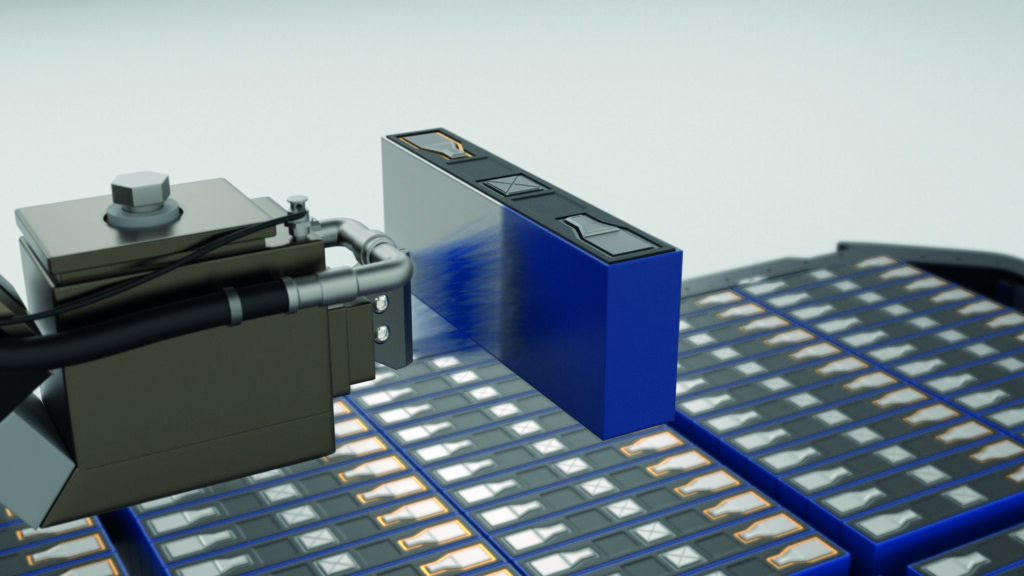
(Image courtesy of Henkel)
Application issues
Several methods are used for applying coatings to battery components, and all have their pros and cons. With dielectrics, Henkel’s Dr Knecht explains, the typical method is spray coating, which is good for laying down homogeneous material thickness on 3D shapes. The downsides stem from overspray, which leads to relatively high waste – unless the material can be recovered for reuse – and might require masking.
Spraying is the standard method of applying fire protection coatings, he continues, as it is compatible with many materials, in addition to suiting 3D application well. The main alternative is flat stream coating, which produces less waste as it eliminates overspray and makes the whole process more efficient.
When applying conductive materials, roll-to-roll (RTR) gravure coating (also referred to as roll coating) is the preferred technology. This is because it is a fast process that produces very uniform results, compared with alternatives such as slot-die coating.
RTR gravure coating is a continuous process used for applying thin coatings onto flexible substrates, such as films and foils. The process is based on three rolls: the gravure roll has a pattern of cells or wells engraved onto its surface, and works with a smooth backing roll, plus a roll of substrate material between them.
The gravure roll is partially immersed in the coating material and the excess wiped off, only leaving the material in the engraved cells. As the roll of substrate film passes between the gravure roll and the backing roll, the coating material in the engraved cells is transferred onto the substrate. The engraved pattern determines the thickness and distribution of the coating.
Coatings for cooling plates are almost always sprayed on or deposited electrostatically, notes Dean at Parker Lord. “This ensures more uniform coverage on large parts with interesting geometries.” He notes that overspray from the company’s Sipiol UV dielectric coating is collected for reuse during the application process. “Cylindrical cells are a good option for roll coating because of their flat surface and relatively small surface area.”
With dielectric coatings, the main application technologies are electrodeposition coating (e-coating), powder coating and UV-cured liquid coatings, or some combination of these, explains Munro at PPG.
In general, e-coats are applied as liquids. The coating material is contained in a bath and is given a positive electrical charge, while the parts dipped into the bath are given a negative charge. The attraction between the charges ensures that the coating sticks to the parts.
E-coat application systems require significant manufacturing space, can be capital-intensive, and make it difficult to change coating material. “But it is a very robust system” Munro notes, “providing uniform coverage of complex parts and shapes, high productivity, typically smaller maintenance cost in the long run, and great usage of material with minimal solid waste. In essence, e-coat systems are great for large production components such as lids, trays, frame plates, module racking, or anything of that sort.”
The next major option is powder coating, which can be fully automated with robotics or inline spraying. As with e-coating, powder coatings are typically electrostatic processes, and they also have a significant manufacturing footprint, although some reductions can be achieved through the use of IR curing systems, Munro notes.
One of the drawbacks of powder coating is that the complex shapes of some components causes them to form Faraday cages, which shield some areas from the electrostatic charge, resulting in some areas not receiving the coating as intended. “The benefits of powder coating far outweigh most of the negatives, though,” Munro argues.
“They have great mechanical properties, ensuring components hold up over the battery’s lifetime, offer high utilisation of the coating material through recycling, and are applicable to many different part types and shapes within the pack, including lids, treys, frame plates, module racking and cooling tubes,” he says. “We coat millions of cooling tubes with our ENVIROCRON® Dielectric PRO.”
UV cured coatings are the newest option for applying dielectric coatings to battery components but have some drawbacks. These include limited options among equipment suppliers along with an early focus on cell applications, which today limits the technology’s suitability for other components. Also their mechanical properties are not as robust as those of powder or e-coats, Munro reports.
“UV coatings do a few things really well though,” he adds. “Those are fast, high-volume production along with the ability to coat filled battery cells, which other systems are unable to do safely. They also offer significantly lower energy costs compared with some of the other methods, which benefits manufacturers who are attempting to maximise throughput.
“What’s consistent across all of these application methods is that they’re highly automated,” Munro adds. “That can drive us to very high efficiencies and first-run rates on the production of these types of materials.”
He emphasises that PPG tailors its coating solutions to customers’ preferences and established capital assets and supply chains. “Anywhere we can take advantage of things that are already deployed, it’s just going to help them progress far more rapidly to scale.”
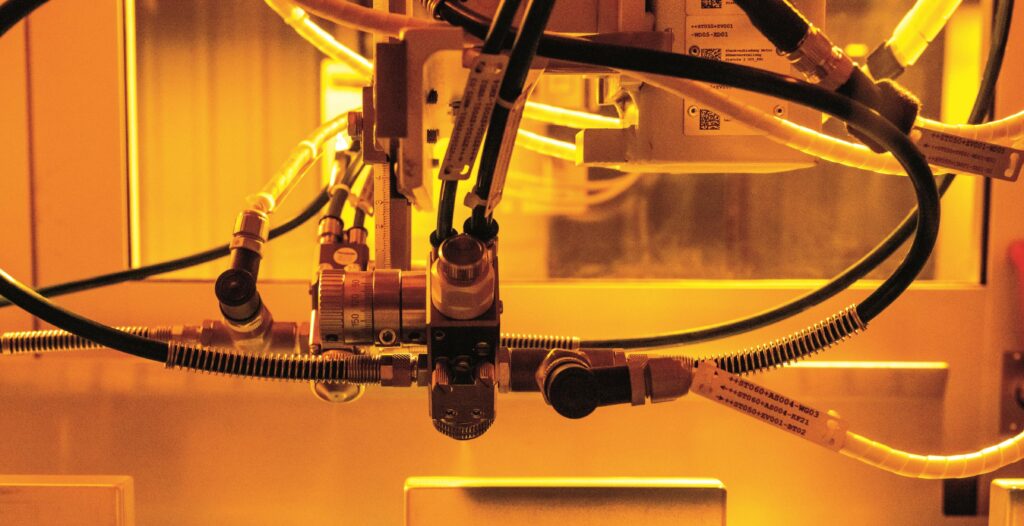
(Image courtesy of BMW)
Near term predictions
In the realm of promising new coating technologies, Dr Knecht points to Henkel’s conductive electrode coatings for cells. Parker Lord’s Dean reckons that the limitations of PET films and powder coatings will lead to more adoption of coatings applied as liquids for dielectric protection. “The volumes, throughput, cost, and more demanding OEM requirements around voltage, durability, and multifunctionality will drive this adoption.”
With dielectric coatings, Munro at PPG anticipates much greater use of UV-cured materials because they are solids, their application consumes relatively little energy and yields faster throughput when coating filled cells. “This is the next large movement in coatings for the battery pack, along with fire protection considerations.”
ONLINE PARTNERS
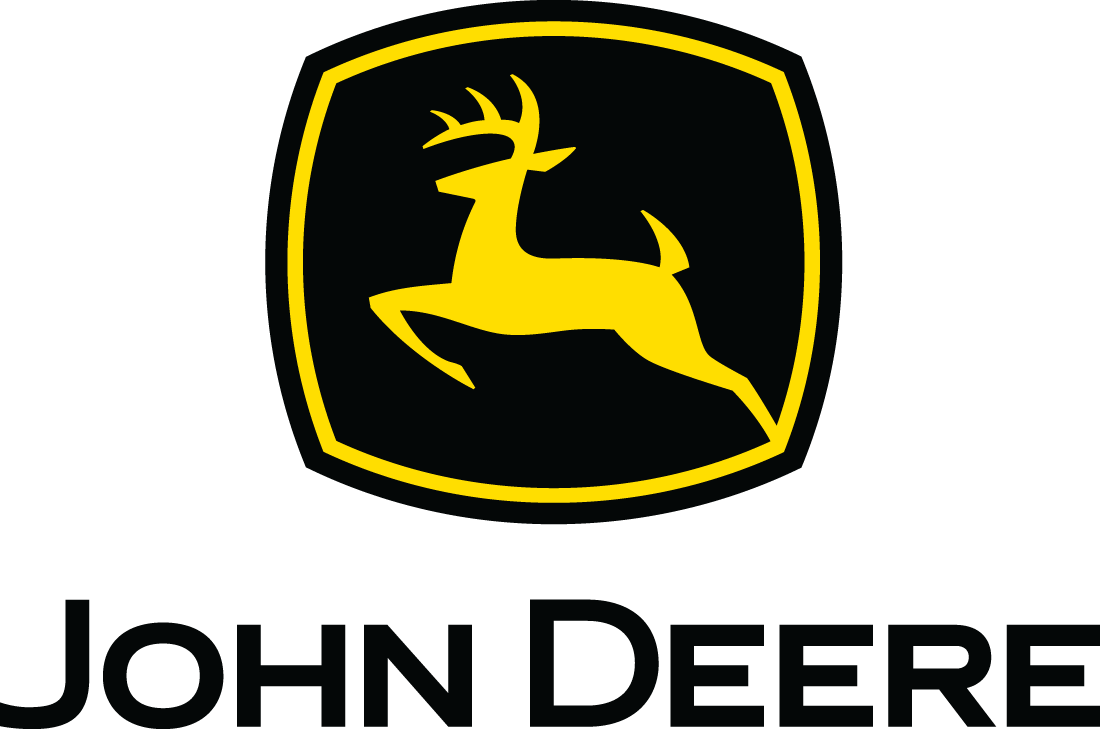
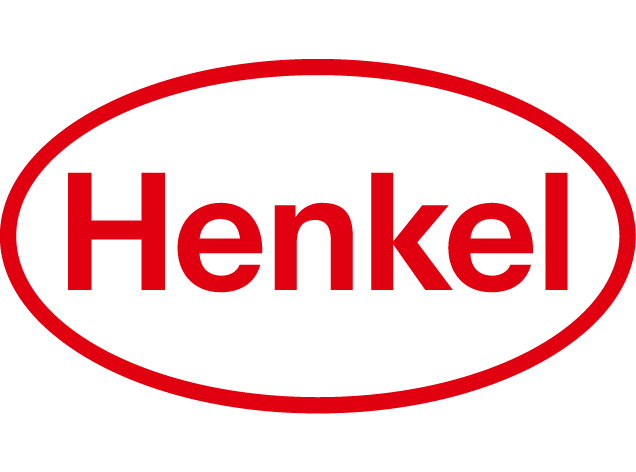
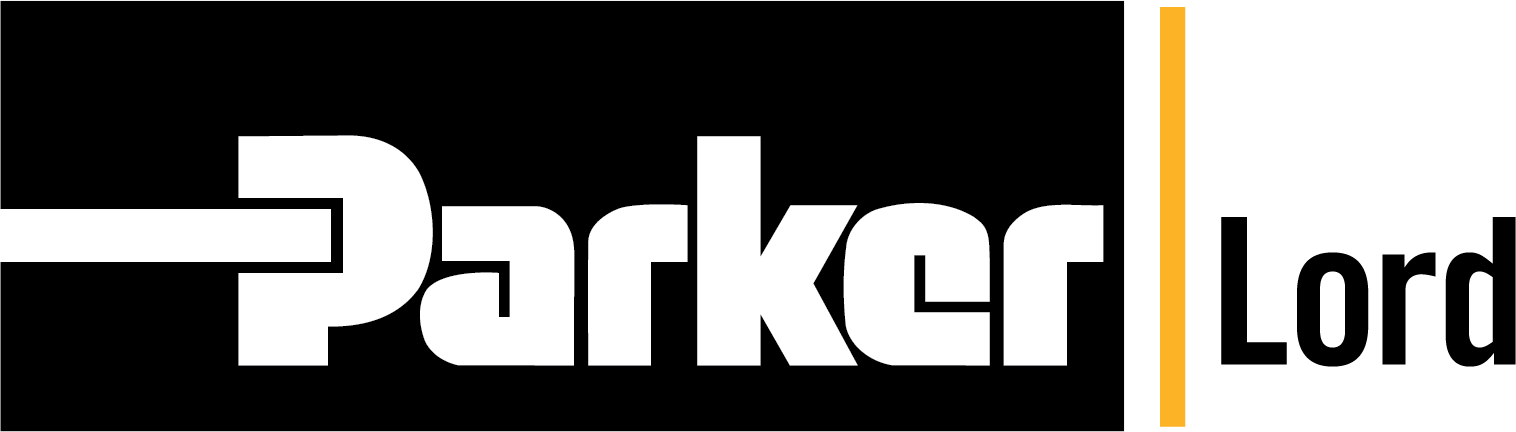
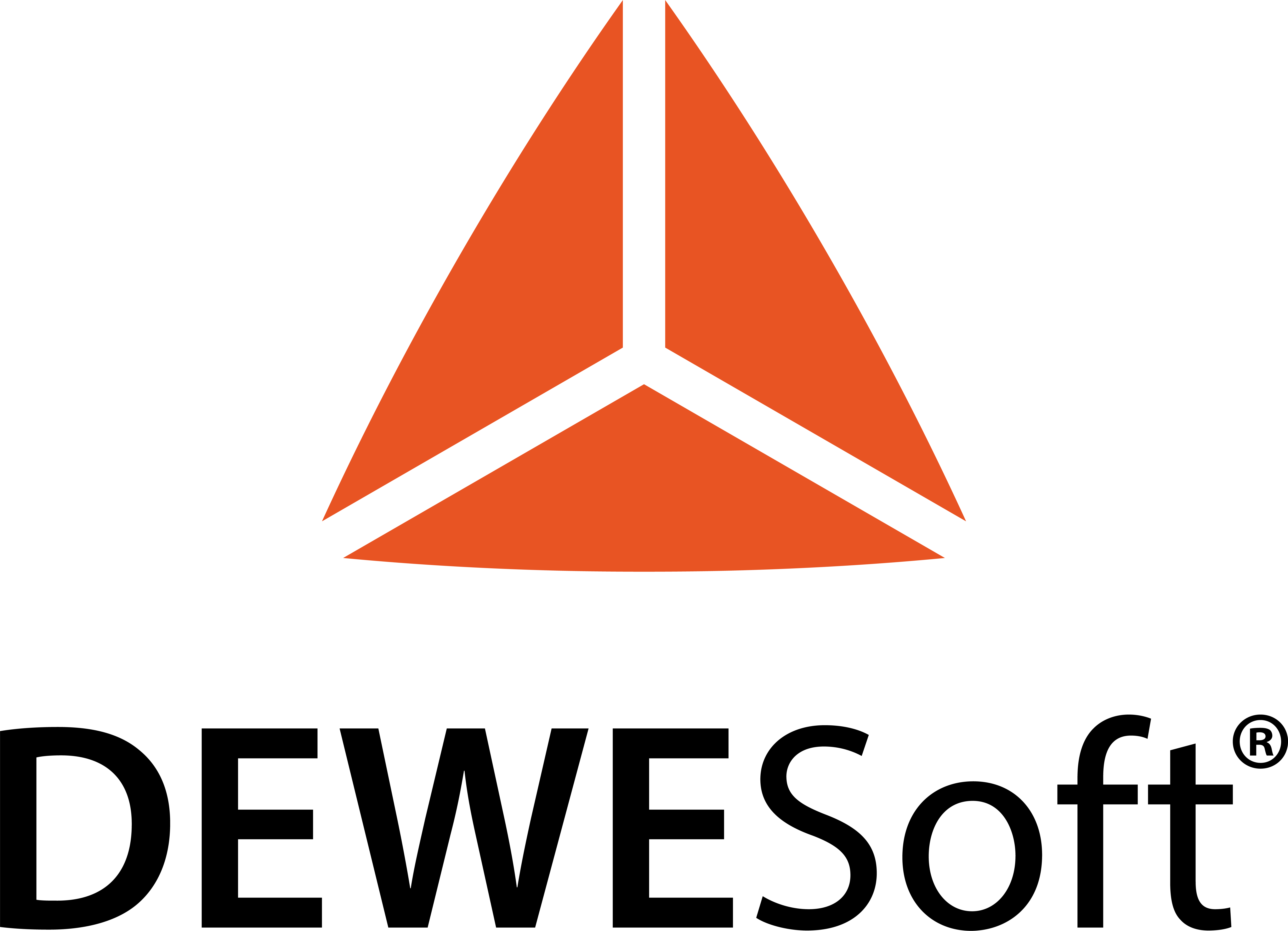
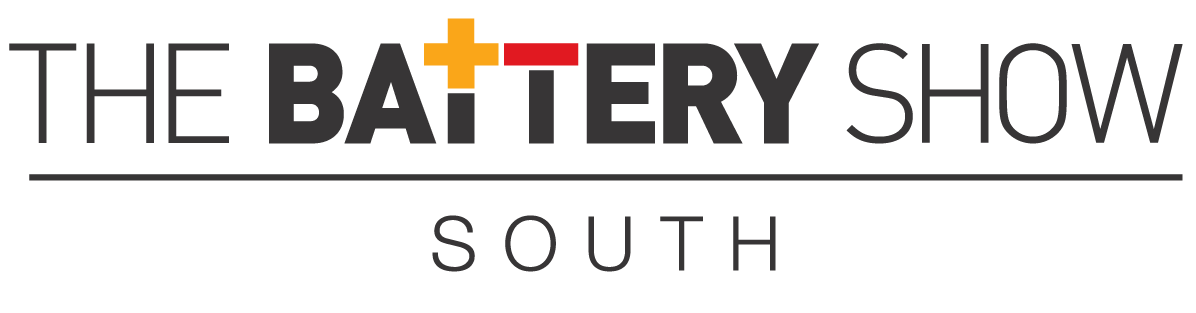
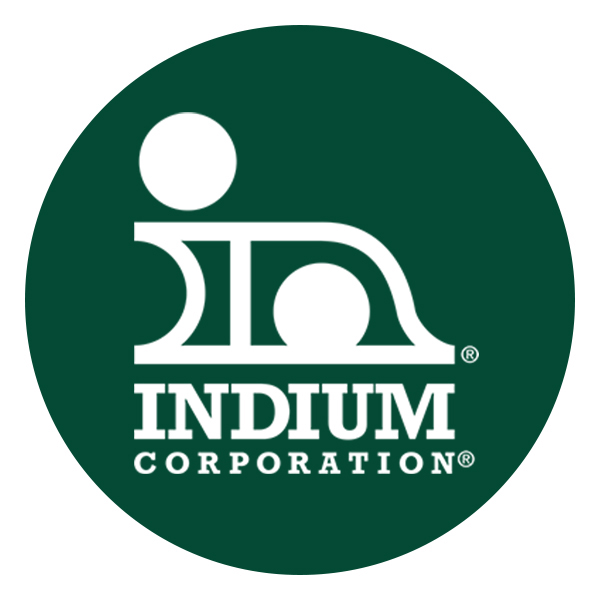

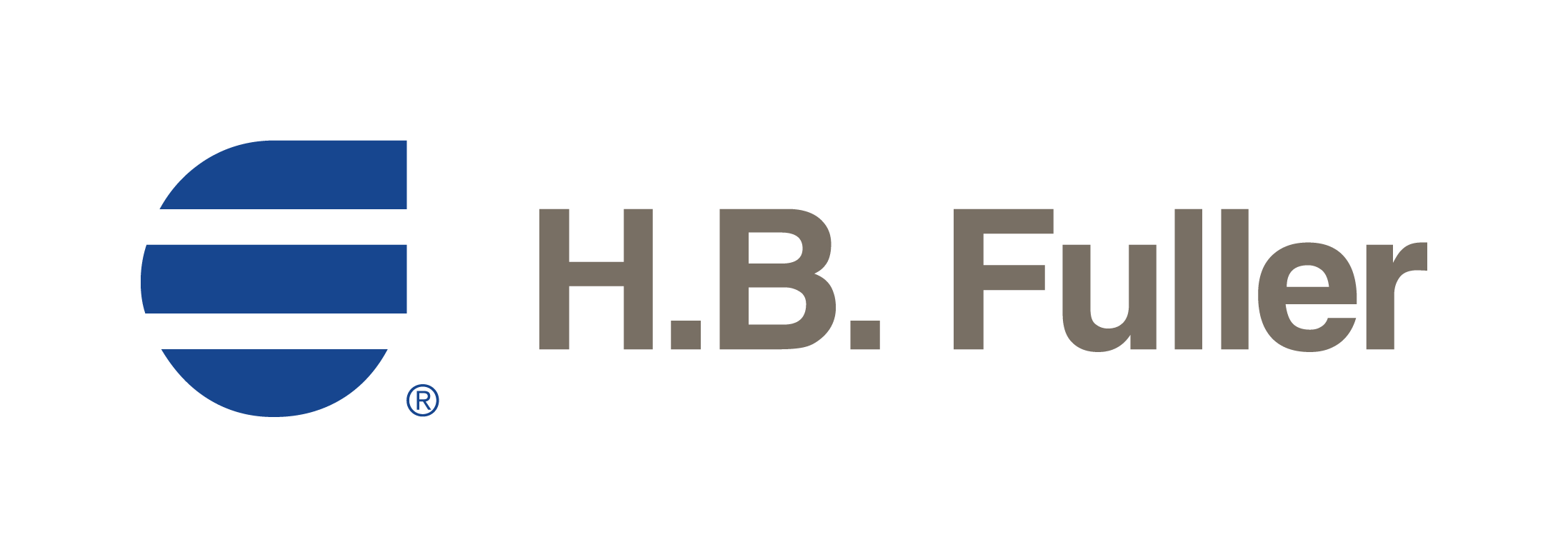
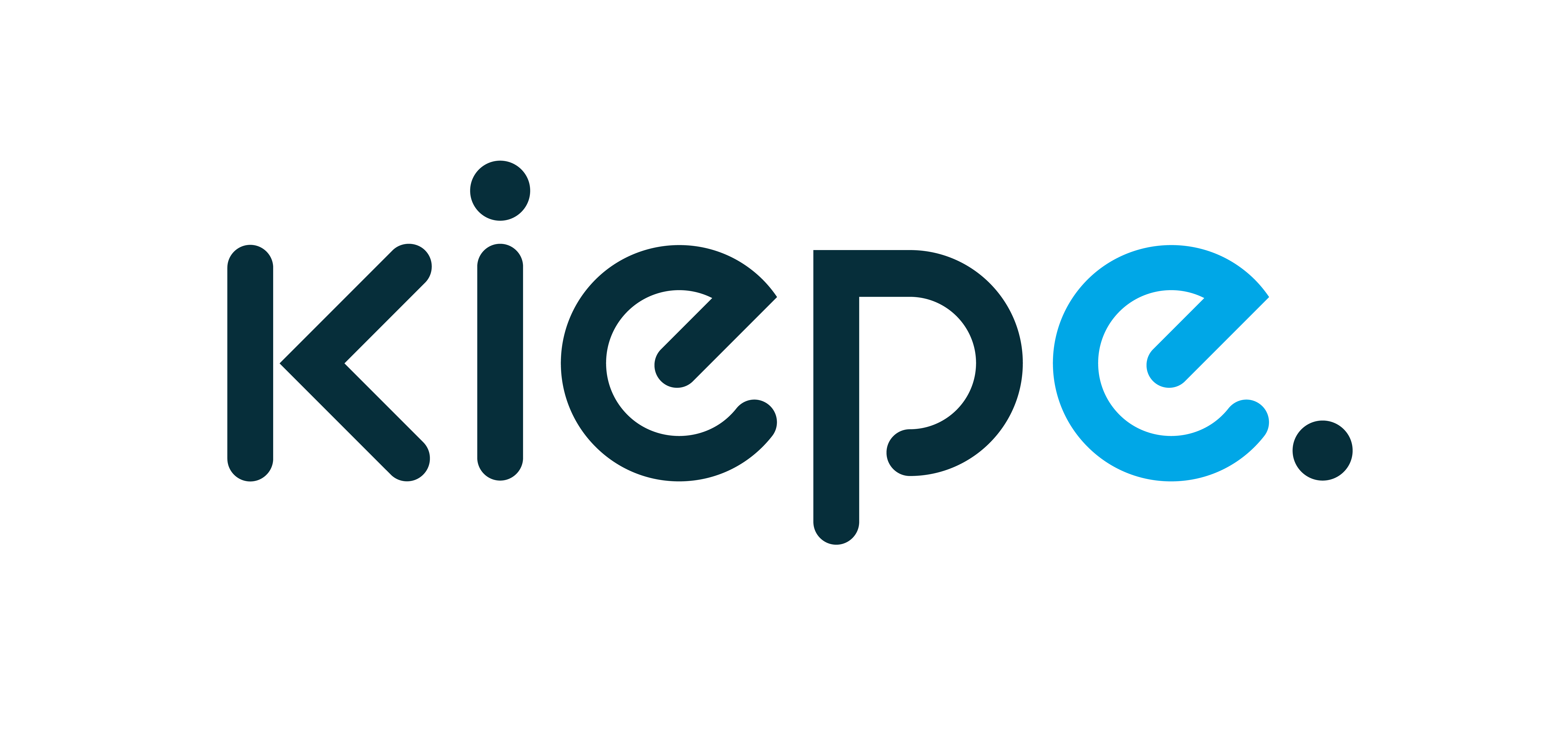
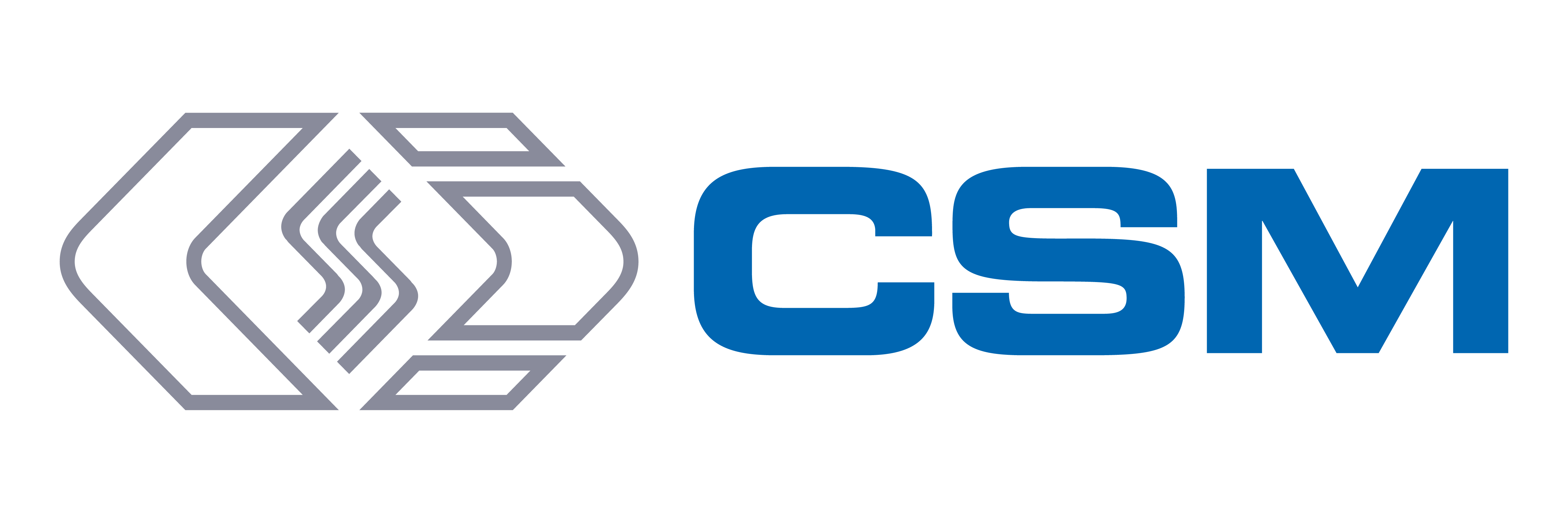