Keeping batteries and electronics cool with liquid plates
The lifespan and efficiency of batteries and power electronics are highly dependent on temperature management. As these components become more powerful and compact, traditional air-cooling methods often struggle to prevent them overheating. This is where liquid cold plates step in, offering a superior thermal management solution.
Liquid cooling has become increasingly popular for dissipating heat in various applications, including batteries and power electronics.
How liquid cold plates work
A liquid cold plate is metallic and absorbs heat from a heat source, such as a battery pack or a power converter. It contains channels or microchannels through which a coolant flows, typically water or a water-glycol mixture. The cold plate absorbs heat from the heat source and transfers it to the coolant, which carries it away to a heat exchanger, where it is ultimately dissipated.
Features:
- High thermal conductivity: liquid cold plates offer excellent thermal conductivity due to their direct contact with the heat-generating components, enabling efficient heat dissipation.
- Compact design: cold plates are thin and lightweight, making them ideal for tight spaces in EVs, fuel-cell vehicles (FCVs) and other applications. Their compactness ensures efficient cooling without compromising the available space.
- Reduced risk of thermal runaway: liquid cold plates enhance safety and reliability by preventing overheating, and in battery applications, avoiding thermal runaway is critical to prevent catastrophic failure.
- Energy efficiency: liquid cooling plates require less power than traditional, air-cooling solutions. Unlike high-speed fans used in air cooling, liquid cooling operates at lower flow rates, resulting in energy savings and reduced electricity consumption.
- Compatibility with coolants: liquid cold plates are compatible with various coolants, including water and water-glycol mixtures. This flexibility allows for customisation, based on application requirements.
- Low pressure drop: cold plates exhibit minimal pressure drop, ensuring efficient fluid flow without excessive pumping power.
Stamped and brazed cold plates
Stamped and brazed cold plates are made by stamping thin, metal sheets, one flat sheet and another sheet with formed channels, and then brazing them together. This process creates a sealed channel network for the cooling fluid.
Features:
- High precision: stamping allows intricate channel designs, optimising fluid flow paths.
- Uniform heat distribution: the brazed joints ensure consistent heat transfer across the plate.
- Customisable: stamped cold plates can be tailored to specific geometries and layouts.
- Cost-effective: they are a good choice for high-volume applications due to the relatively simple manufacturing process.
- Lightweight: aluminum construction makes them ideal for weight-sensitive applications, such as electric vehicles and aerospace.
- Efficient heat transfer: the combination of precise channels and brazed joints maximises heat dissipation.
- Reliability: sealed channels prevent leaks and maintain long-term performance.
Roll-bonded cold plates
The manufacturing process involves silk screening the channel on one plate, rolling both plates under high pressure and temperature, and inflating the channel using high-pressure gas.
Features:
Cost-effective: roll-bonding is a simple manufacturing method.
Lightweight: aluminum, roll-bonded plates are light and easy to handle.
Affordability: roll-bonded cold plates are budget-friendly.
Simplicity: the manufacturing process is straightforward.
Suitable for moderate heat loads: roll-bonded plates are ideal for applications with moderate heat dissipation requirements.
Comparing the two methods
- Stamped and brazed plates offer better size control, and have minimum tolerance variation.
- If cost is a significant factor and the heat load is moderate, roll-bonded plates offer an economical solution.
- In tight spaces, both types are suitable, but stamped and brazed plates allow more customisation.
- A stamped and brazed plate is a good choice for high-performance applications, while roll-bonded plates are cost-effective and suitable for moderate heat loads.
- Liquid cold plates play a crucial role in maintaining the reliability and safety of electronic systems.
By understanding all of the features and benefits of stamped and brazed, roll-bonded and liquid cold plates, you can select the optimal solution to keep your batteries and power electronics operating efficiently and within a safe temperature range.
Click here to read the latest issue of E-Mobility Engineering.
ONLINE PARTNERS
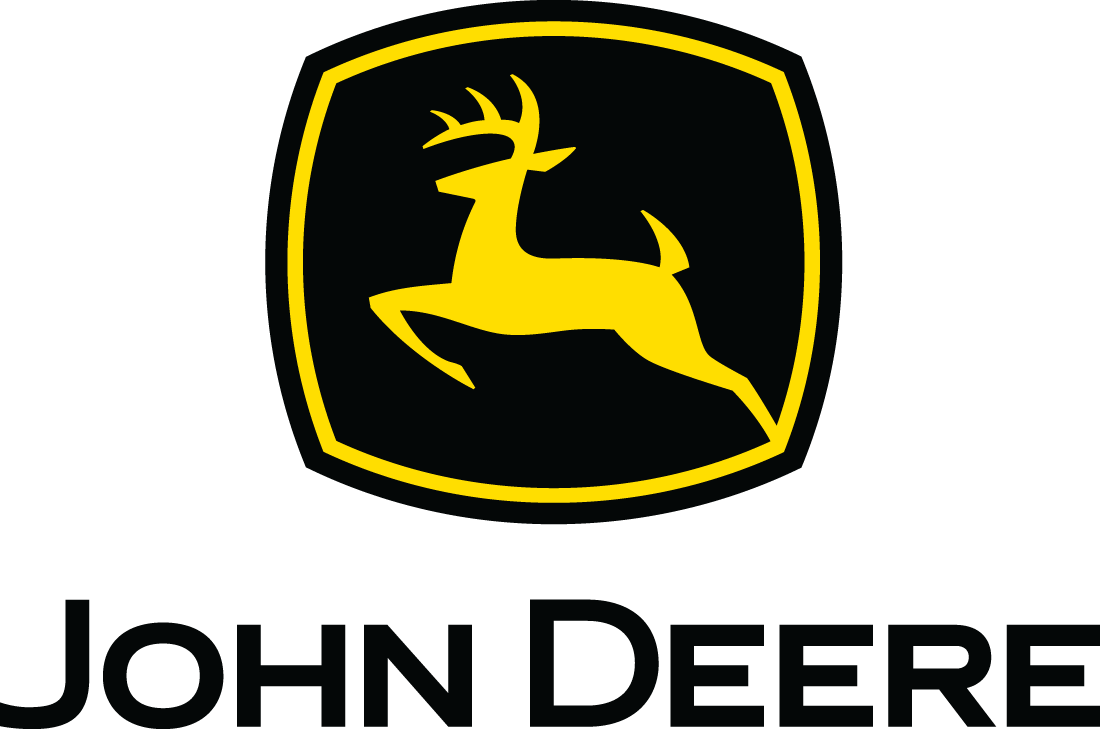
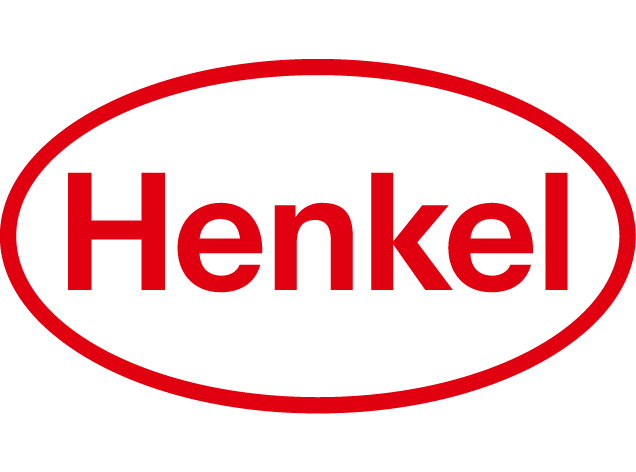
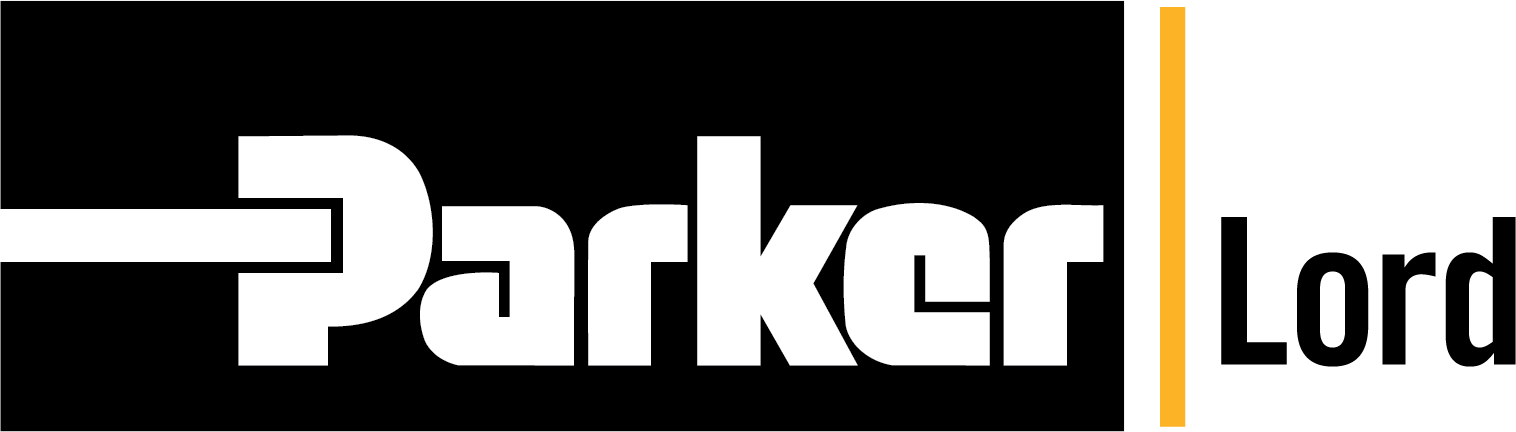
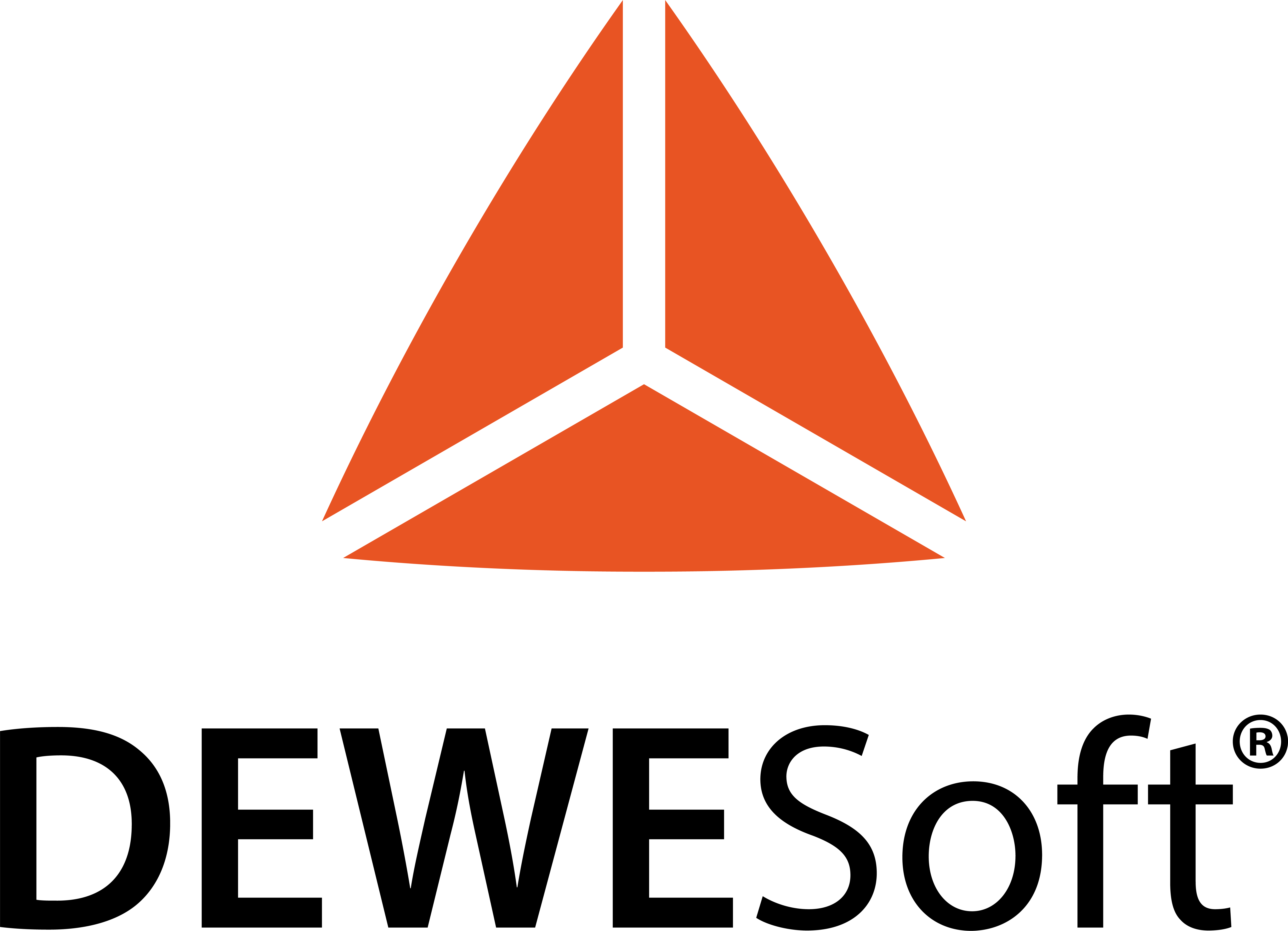
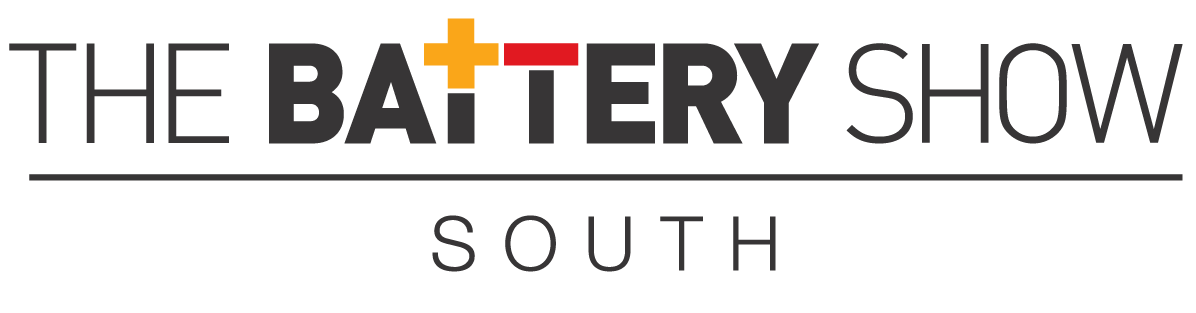
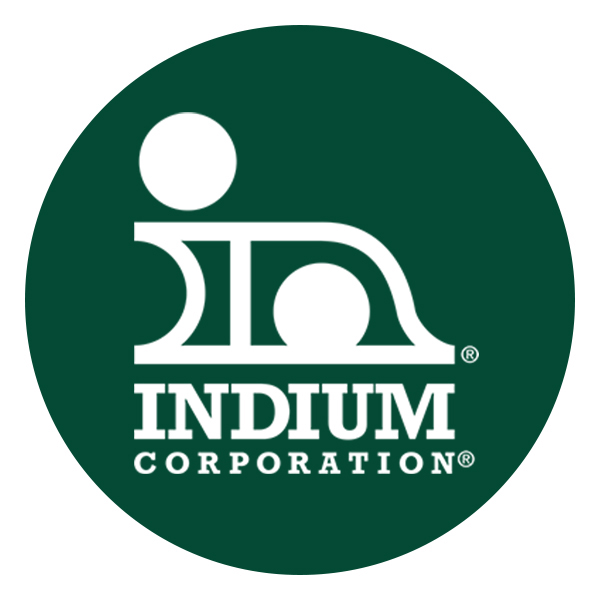
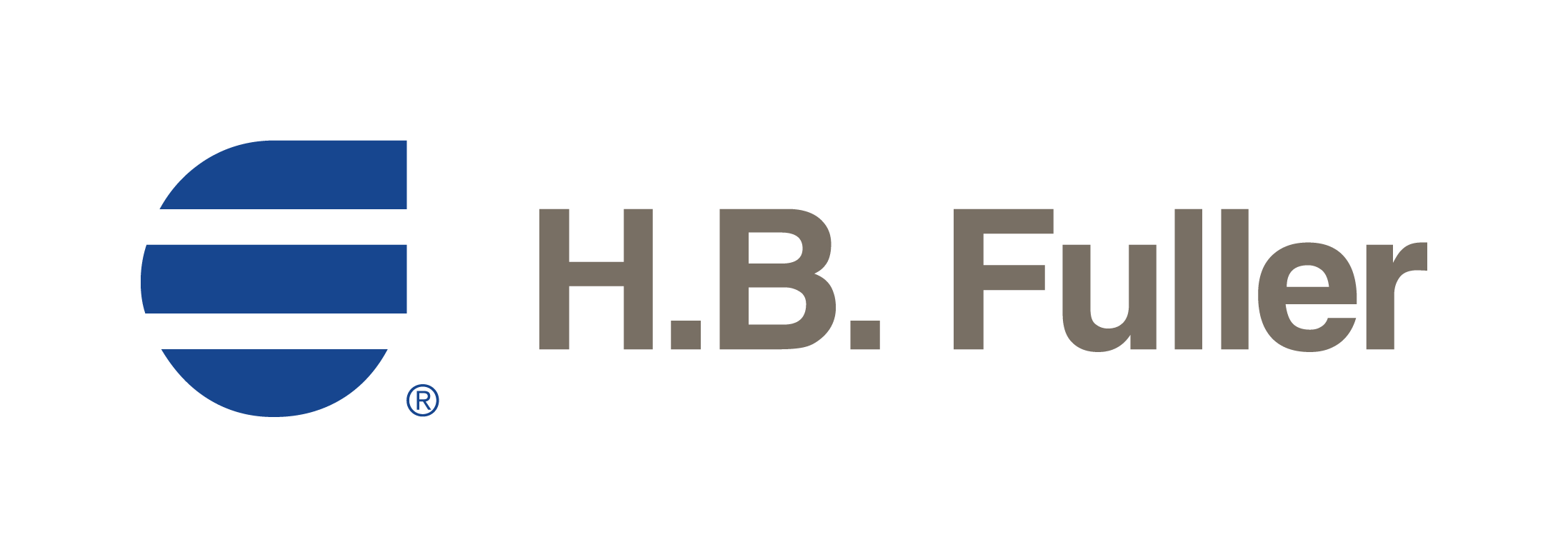