Audi’s more powerful & smarter HV battery
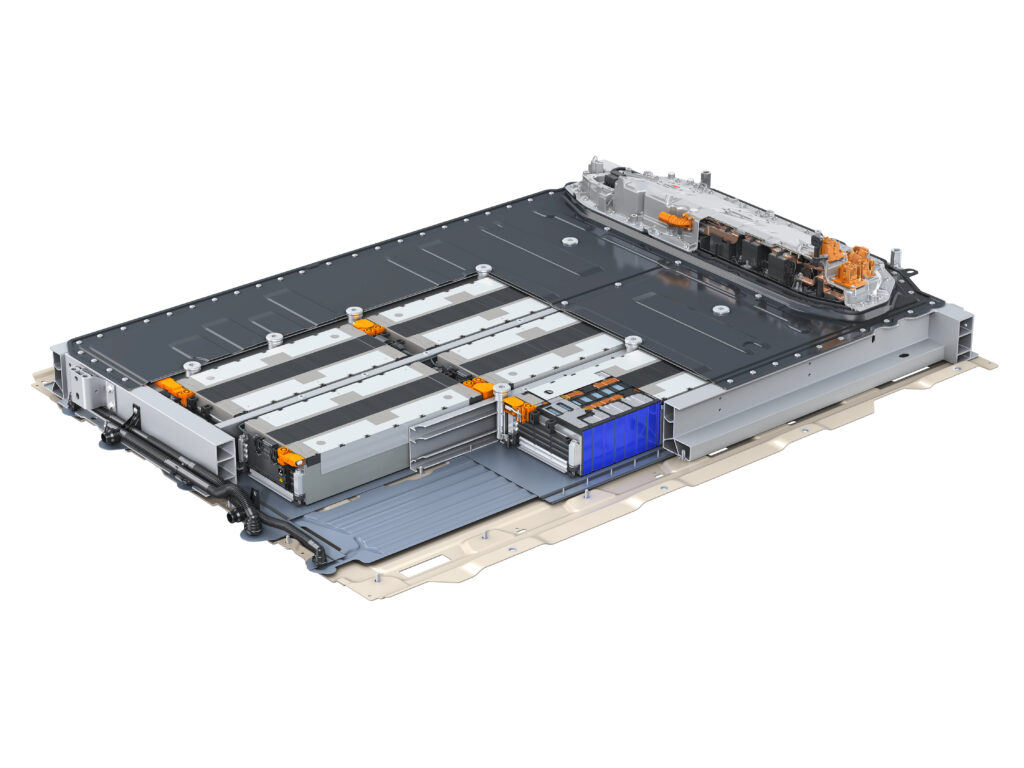
(Image courtesy of Audi)
The completely newly developed high-voltage battery (HV battery) is largely responsible for the longest electric range in the current Audi portfolio. With an impressive range of 625 kilometers (388 mi), the Audi Q6 e-tron1 is highly suitable for everyday use, making it one of the models with the longest range in its segment. The two model variants, Audi Q6 e-tron quattro1 and Audi SQ6 e-tron2, each have an HV battery with a gross storage capacity of 100 kWh (net 94.9 kWh). Compared to the battery systems previously used by Audi, the battery consists of just twelve modules with a total of 180 prismatic cells. The 15 cells per module are connected in series. For comparison, the HV battery in the Audi Q8 e-tron consists of 36 modules and 432 cells.
A rear-wheel drive variant with ten modules and a gross capacity of 83 kWh will follow after the market launch. A second rear-wheel drive model to come will have the large battery with twelve modules and will offer a significantly greater range compared to the models offered at market launch.
The significant increase in cell size corresponds almost perfectly to the 800-volt architecture in order to achieve the best possible compromise between range and charging performance. The ratio of nickel, cobalt, and manganese in the cells is 8:1:1, meaning the cobalt content has been reduced, and the nickel content, which is particularly relevant for energy density, has been increased.
The decision to reduce the number of modules in the PPE batteries has a number of advantages. As a result, the battery, which can be used modularly for high and flat floor models, requires less installation space, is lighter and can be better integrated into the vehicle’s crash structure and cooling system. It also requires fewer cables and high-voltage connectors. The number of screw connections has been significantly reduced. In addition, the electrical connections between the modules are shorter, which significantly reduces power loss and weight. A cooling plate integrated into the battery housing ensures homogeneous heat transfer and, therefore, almost optimum conditioning of the battery. The protective side skirts made of hot-formed steel are not attached to the battery but instead to the body for extra stability. Another new feature is the underbody protection made of fiber composite material. This design also reduces weight, protects the lithium-ion battery from damage, and improves the thermal insulation of the battery from the environment. In this way, the battery for the PPE can be cooled or heated more efficiently.
The central control unit specially developed for the PPE, the Battery Management Controller (BMCe), is responsible for the current regulation required for fast and battery-friendly charging. The BMCe, the “electrical control center,” is fully integrated into the HV battery.
As part of permanent monitoring, the twelve Cell Module Controllers (CMC) send data such as the current module temperature or cell voltage to the BMCe, which sends its information, for example, regarding the State of Charge (SoC), to the high-performance computer HCP4 (part of the new electronic architecture E3 1.2). This computer, in turn, sends the data to the new predictive thermal management system, which regulates cooling or heating as required for optimum battery performance.
The high-voltage batteries are assembled in Ingolstadt. “With battery assembly, we are increasing vertical integration and bringing important skills to the site,”,” says Gerd Walker, Member of the Board of Management for Production. And Xavier Ros, Member of the Board of Management for Human Resources adds: “At the same time, we are creating new job opportunities at our sites because a successful transformation can only work together with the staff. This change is only possible thanks to Audi employees who are continuing to gain further qualifications and reinvent themselves professionally.”
Audi has so far trained 8,300 employees from Production, Technical Development, and Sales in Ingolstadt for the launch of the Q6 e-tron model series. Numerous experts were also trained for electrification at the Hungarian site in Győr. In total, AUDI AG has invested more than 250 million euros in the training and development of its employees over the past two years. “As we are switching to electric mobility, we are relying on our existing plants and renewing ourselves from the inside out. This is sustainability in action, in social, ecological, and economic terms,” says Walker.
Impressive charging performance
Another key component of the product experience is the charging performance of the Audi Q6 e-tron1. Sophisticated thermal management of the high-voltage battery, the 800-volt electrical system, and its ecosystem make charging a convenient all-round carefree experience. The Audi Q6 e-tron1 only needs ten minutes at a fast-charging station to generate a range of up to 255 kilometers (158 mi) under ideal conditions with a maximum charging capacity of up to 270 kW. Only 21 minutes are needed to charge the high-voltage battery from 10 to 80 percent. If a charging station works with 400-volt technology, the Audi Q6 e-tron1 can be bank-charged for the first time. The 800-volt battery is automatically divided into two batteries at equal voltage, which can then be charged in parallel with up to 135 kW. Depending on the state of charge, both halves of the battery are first equalized and then charged together. The Audi Q6 e-tron1 can be fast-charged at HPC charging stations with up to 270 kW as standard.
The Audi Q6 e-tron1 charges at an AC charging station or home charger with up to 11 kW as standard. This fills an empty battery overnight. Audi will offer AC charging with 22 kW as an option at a later date. The charging inlet can be opened electrically via the MMI display or on the cap itself. Once the charging cable has been disconnected, the inlet closes automatically. In addition, all drivers of fully electric Audi models benefit from the Audi charging service and, last but not least, from the increasingly dense network of the Audi charging hub inner-city fast-charging concept.
The charging management supports the international charging standard CCS (Combined Charging System). The HCP5 high-performance computer ensures fast and reliable charging processes as part of the new domain computer structure of the E3 1.2 electronic architecture. A communication control device, the Smart Actuator Charging Interface Device (SACID), establishes a connection between the charging socket and the charging station as an interface and forwards the incoming standardized information to the HCP5 domain computer.
For the PPE models, Audi provides DC and AC charging options for the European market via a standard CCS Combo inlet on the rear left of the vehicle. An additional AC charging inlet is installed on the opposite side of the vehicle. The standard equipment of the Q6 e-tron series includes the familiar Plug & Charge function. At compatible charging stations, the vehicle authorizes itself when the charging cable is plugged in and begins the charging process. Charging is fully automatic.
Intelligent calculation: the e-tron route planner
The e-tron route planner, a service from Audi connect, calculates the fastest route with the shortest possible charging stops. This is based on the total journey time, i.e., driving time and charging time, taking into account forecasts about the traffic situation and the occupancy of the charging points. In any case, it plans the sections between charging stops in such a way that drivers reach their destination as quickly as possible – to this end, it may recommend two short charging stops with high power instead of one long, slow charging stop. The list of charging points is updated daily.
The route planner can be conveniently used either in the vehicle or in advance of the journey via the myAudi app. Users receive information such as charging capacity or charging connections and plug type for the respective charging points. The system also shows dynamic availability, such as whether charging points are free or occupied. Alternative routes with better charging infrastructure are also taken into account when calculating the optimum total journey time. The daily updated data includes detailed information such as payment and authentication options, precise operator data, and any access restrictions. The e-tron route planner preferentially selects high-performance HPC charging stations.
Efficient interaction between recuperation and friction brake
Recuperation is an important component in increasing the efficiency and, therefore, the range of the Audi Q6 e-tron1. During development, particular focus was therefore placed on increasing maximum efficiency and availability during standstill blending at low speeds. This means that in the Audi Q6 e-tron1, around 95 percent of all everyday braking processes can be covered by regenerative braking, i.e., by the electric motors. Under ideal conditions, the Audi Q6 e-tron1 recuperates up to 220 kW. The temperature and state of charge of the battery play a key role here. Recuperation takes place on the front and rear axles, with smaller decelerations handled by the rear axle alone for reasons of efficiency. Higher recuperation rates arepossible on the rear axle.
The Intelligent Brake System (iBS) familiar from previous e-tron models has been significantly enhanced as part of the Premium Platform Electric. Axle-specific brake blending as described above is now possible for the first time.
As is typical for Audi, the Audi Q6 e-tron1 also offers the option of two-stage recuperation, which can be adjusted using the paddles on the steering wheel. Sailing is also possible. Here, the electric SUV rolls freely, without additional drag, when the foot is taken off the accelerator pedal. Another variant of the Audi Q6 e-tron1 is the “B” driving mode, which comes close to what is colloquially called “one-pedal feeling.” In this way, Audi covers the entire spectrum of customer wishes.
ONLINE PARTNERS
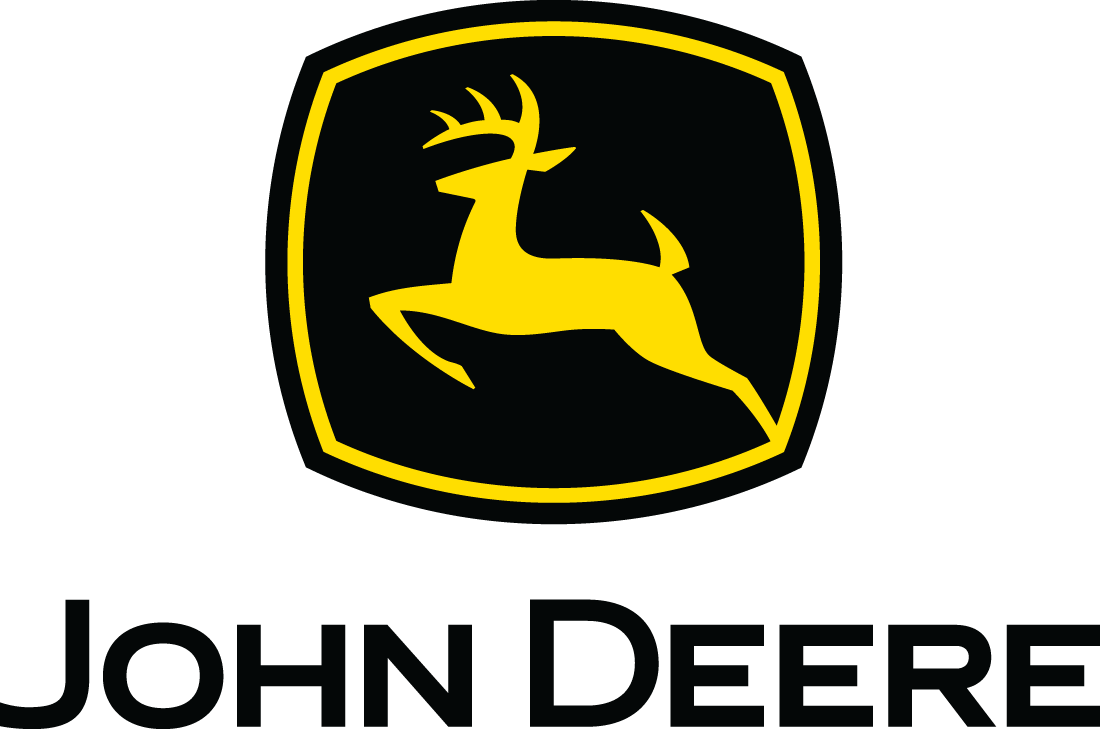
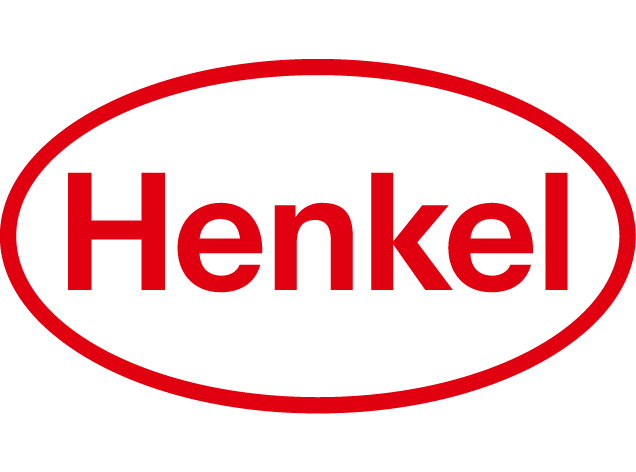
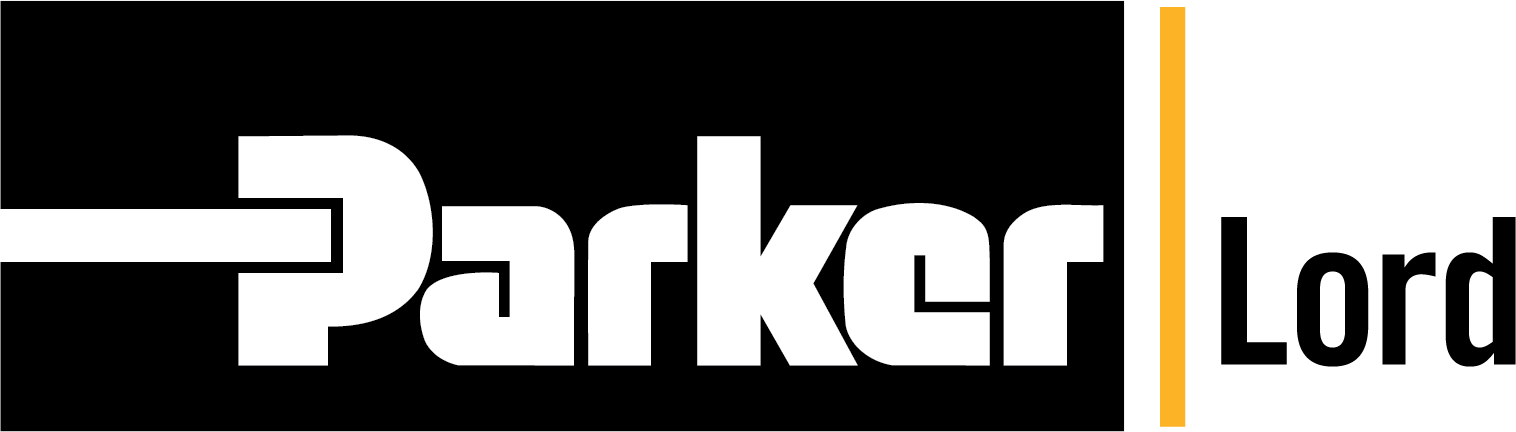
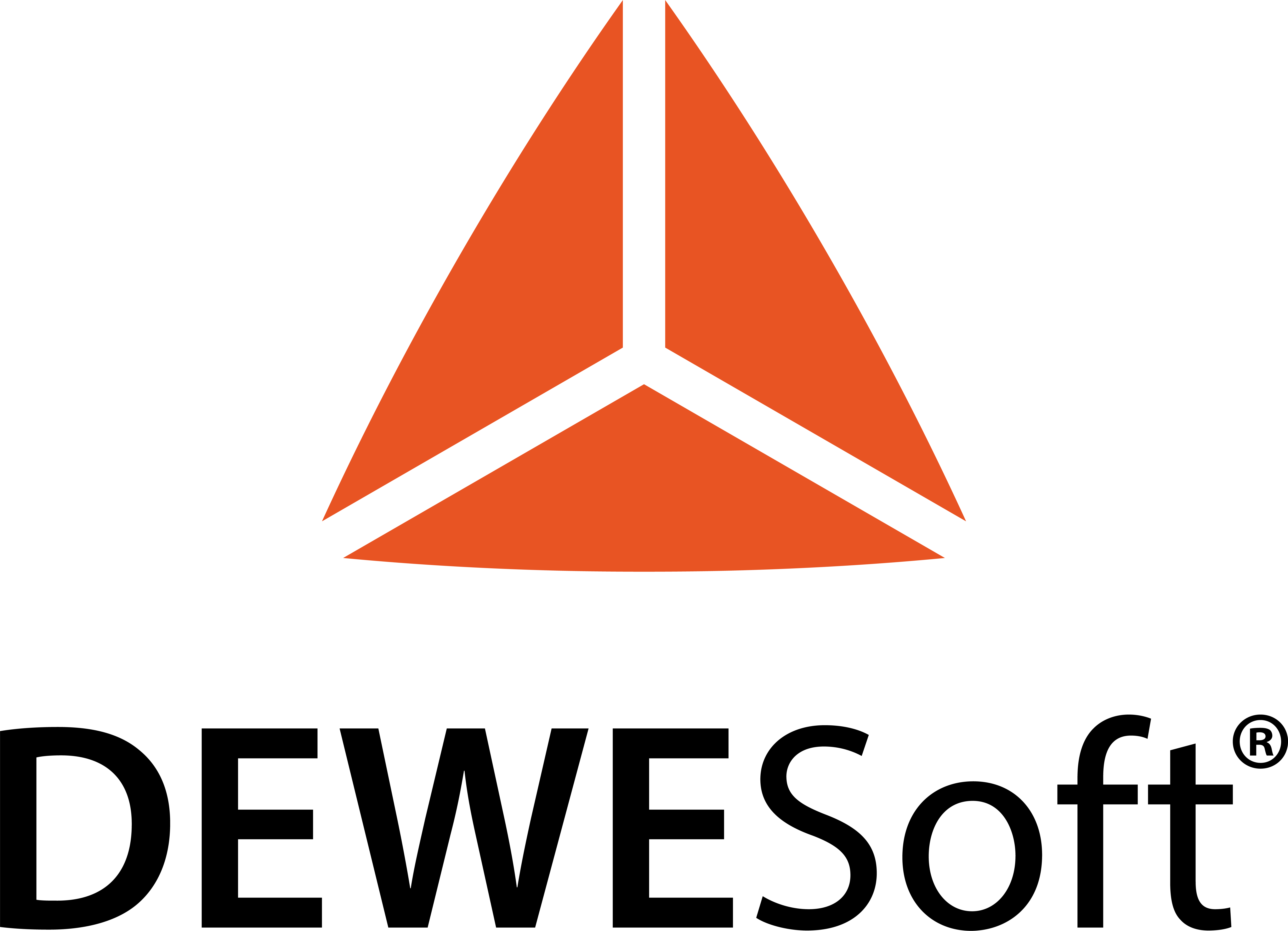
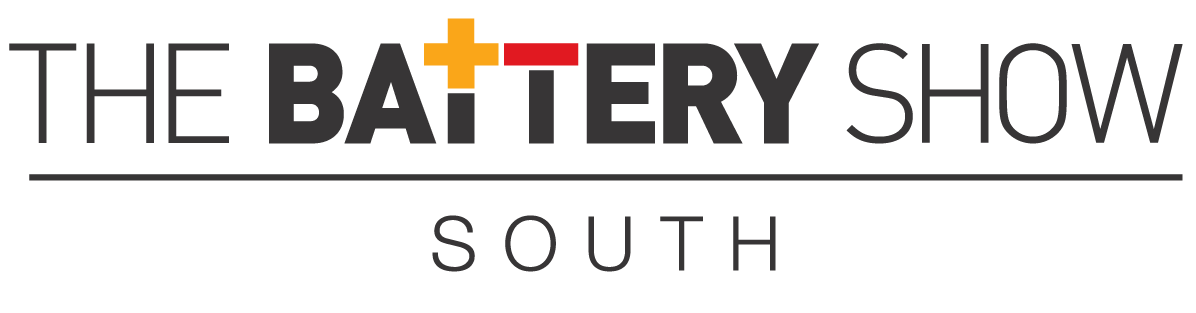
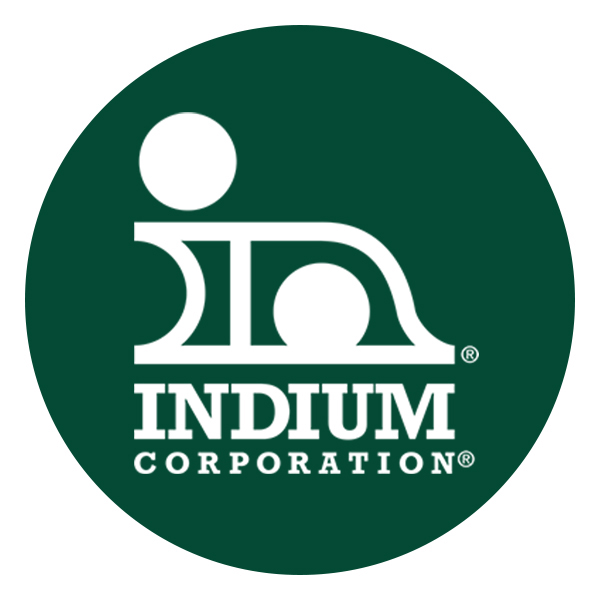

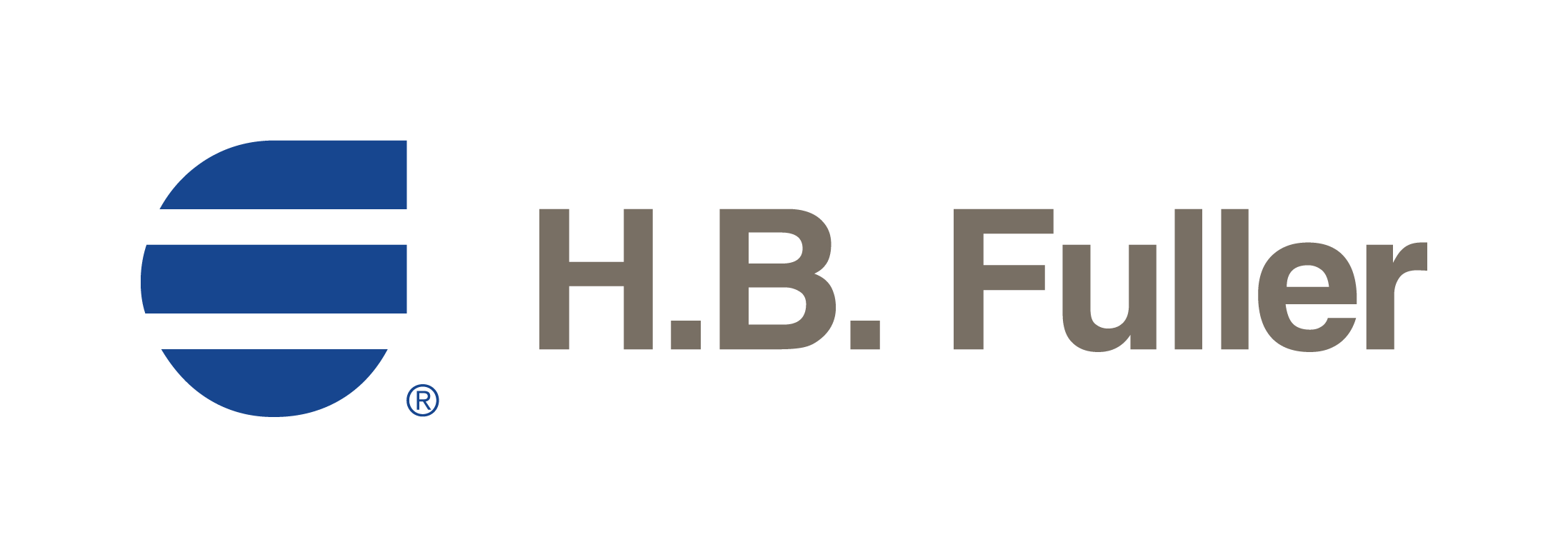
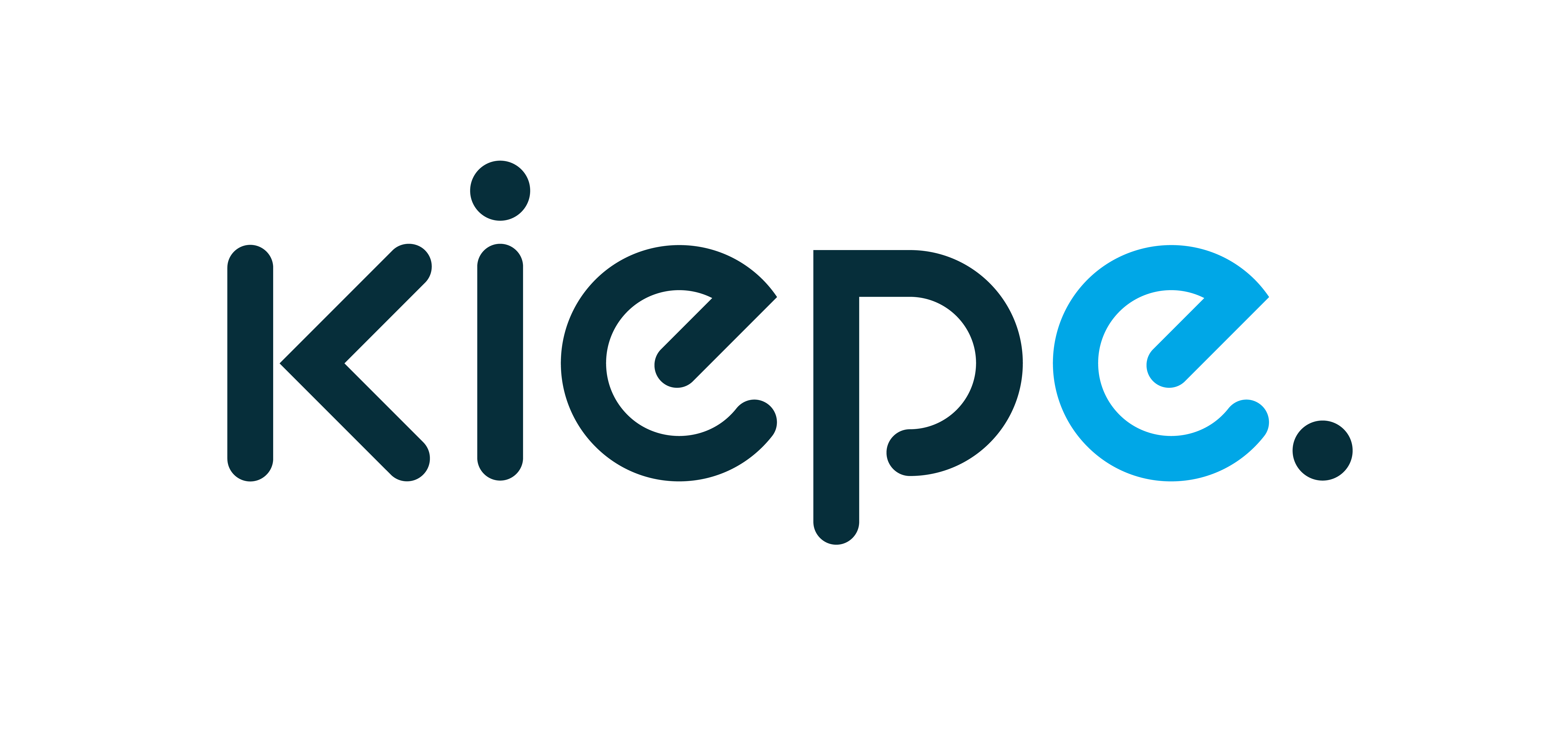
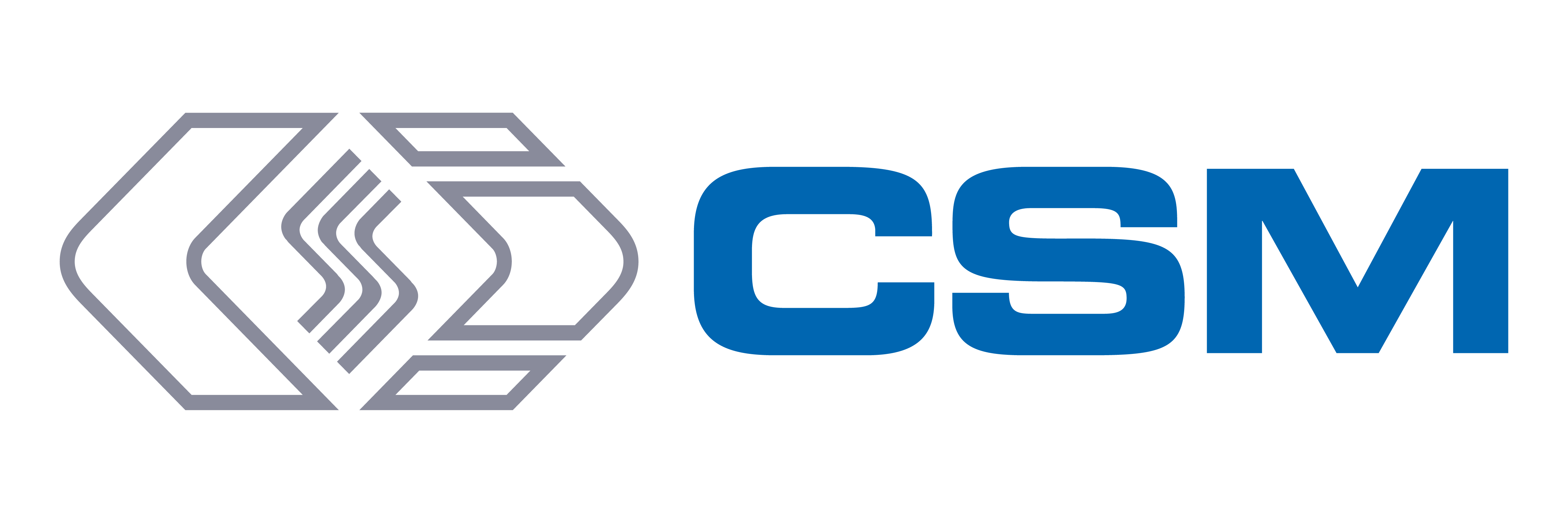