New pump system promises to improve EV battery efficiency
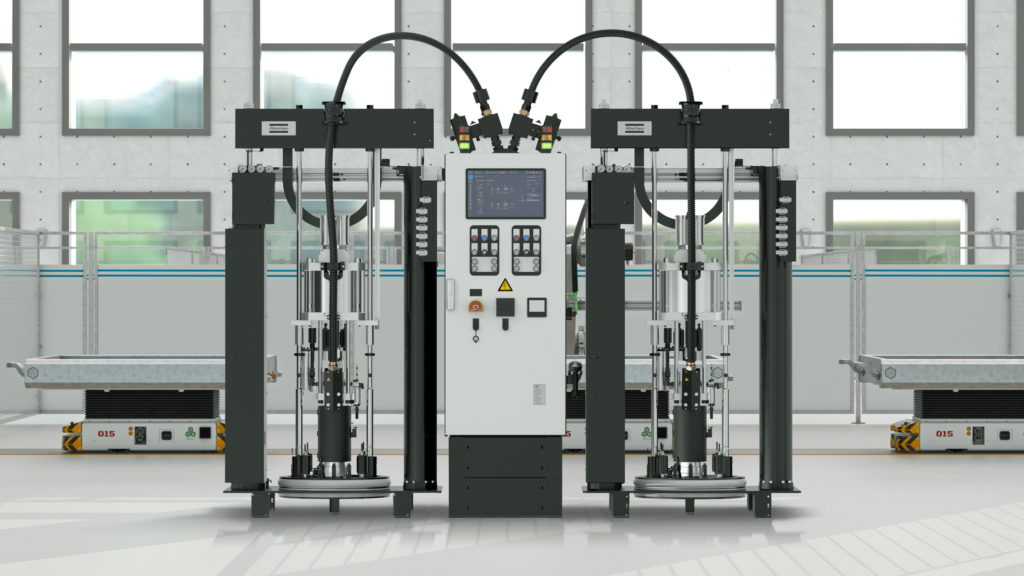
A new pumping system has been developed to improve the way Thermal Interface Materials (TIMs) are applied within the battery manufacturing process. The Enso 7000 Plus.Supply, from Atlas Copco, promises to deliver higher filling efficiency, reducing manufacturing costs and potentially improving the performance and sustainability of e-mobility vehicles.
Effective management of the heat generated during charging and discharging is crucial for battery performance, safety and longevity and manufactures use TIMs to provide passive cooling. However, the need to feed these materials into the area between the battery tray and cell modules during manufacturing can lead to filling inefficiencies.
The new TIM filling solution combines a specially designed vacuum pump and a unique Flat Follower Plate to increase the material yield, prevent pumping discard and reduce the number of barrel changes needed. As a result, it offers a potential reduction in waste and a reduction in CO2 emissions.
The filling challenge
TIMs are placed between the battery compartment and the cell module, but these involve tight tolerances and often the standard application results in air pockets and waste from material squeeze-out. This not only causes less efficient battery cooling when in operation, but also leads to high material waste and CO2 emissions.
To deliver positive thermal efficiencies, TIMs are fortified and enriched with special filler particles but their added weight can also cause range reduction for the vehicle and higher manufacturing costs. As a result, the more efficient the filling process is, the better the battery will perform and the less waste there will be.
The high density and the resulting high weight of the TIM materials means that barrels are often only half-filled, increasing the number of barrel changes needed. Conventional pumps typically fail to empty a barrel entirely and must be ventilated and purged manually after a barrel change, resulting in decreased productivity and material waste in the supply process.
The new material supply system aims to overcome these issues through the combination of two new products: an improved pump and an innovative follower plate.
Pumping system
The Atlas Copco Plus.Supply system uses a durable barrel pump that is available as either a single or a double barrel. It has been specifically designed for use in the material supply process in EV battery assembly, with consideration made to the highly abrasive and corrosive materials that are involved.
The stainless steel UP301 HD creates a pressure environment within the material supply system, facilitating efficient material flow from the barrel to the dispensing unit. It allows precise control over the flow rate and material quantity and helps to prevent material contamination during handling.
Two new base variations – a u-frame for a quick-change pallet and a slide-out plate with a 360° turntable – make barrel changes faster, easier and more ergonomic. Combined with the half-automated, sensor-controlled technology, this achieves further increases in safety, quality and productivity of the process.
The inner geometries and the valve technology of the UP301 HD were designed to allow a better material supply, while Atlas Copco says consideration of the nature of the materials used in the process has resulted in an increased lifetime for the pump, with a longer period allowed between maintenance intervals.
Follower plate
It is the combination of this efficient vacuum pump with the Enso 7000 Flat Follower Plate that achieves an uplift in material yield – and this is perhaps the most interesting aspect: the plate can be supplied with the full pump system or as a stand-alone retrofit upgrade for other SCA material pumps, improving efficiency without replacing all existing equipment.
Its ultra-flat shape contributes to the optimisation of material use and the reduction of waste as it enables the feeder barrels to be almost completely emptied. Depending on the material, this will achieve up to 7 % more material use per barrel, delivering cost savings and reducing the number of barrel changes.
The Flat Follower Plate includes a material-specific grid on the underside, which prevents any potential plastic inliner to be sucked in the pump and protects the operator against injuries. Two O-rings seal the follower plate against the barrel. The grid prevents material from falling back in.
When it comes to barrel changing, the half-automated ventilation of the pump will start to extract the Follower Plate without any operator involvement. The operator must switch to manual operation for final extraction, but no manual ventilation is required and the process can be switched back to automatic for sensor-controlled retraction.
Three base plate variations are available, depending on the material supply processes. The standard base plate is a cost-effective solution that requires two operators to change the barrel. If a faster change is needed, a quick change pallet or a slide-out plate with a 360-degree turntable can be used to enable a single operator to perform this task. The last option can also be retrofitted to existing material supplies.
Cost and environmental savings
Atlas Copco claims that the full system could offer up to €480k savings within five years of operation because of the reduction in waste materials and the need to dispose of them, as well as the improvements in operational efficiency through reduced staff costs, overheads and transportation.
According to their calculations, a standard pump extracts 95.9 % of useable material from the tank, leaving around 5.5 litres of residue. In contrast, a machine retro-fitted with a Flat Follower Plate will achieve 97.9 % efficiency, leaving 2 litres of residues and achieving 35 t of CO2 savings per system per year while a fully integrated system with the new pump and plate will deliver 99.4 % efficiency, leaving just 1 litre of waste and saving 65 t of CO2.
ONLINE PARTNERS
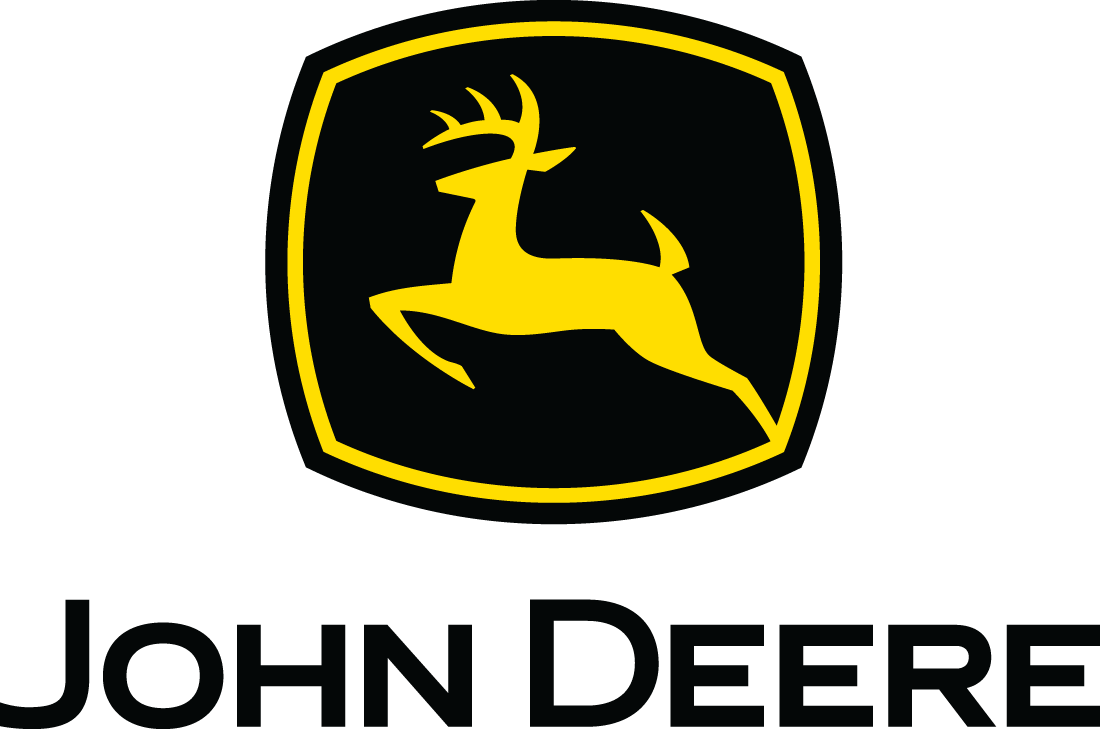
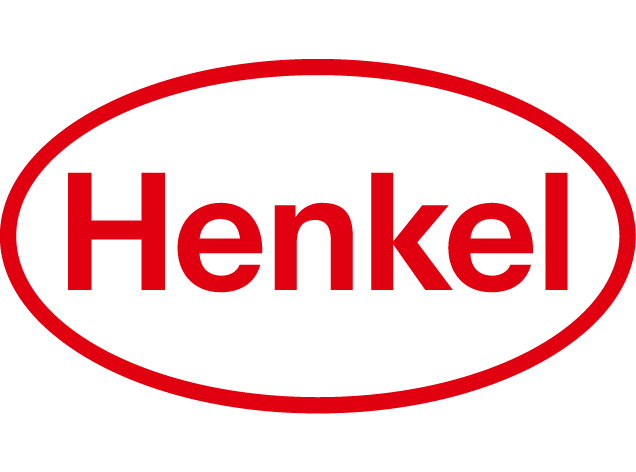
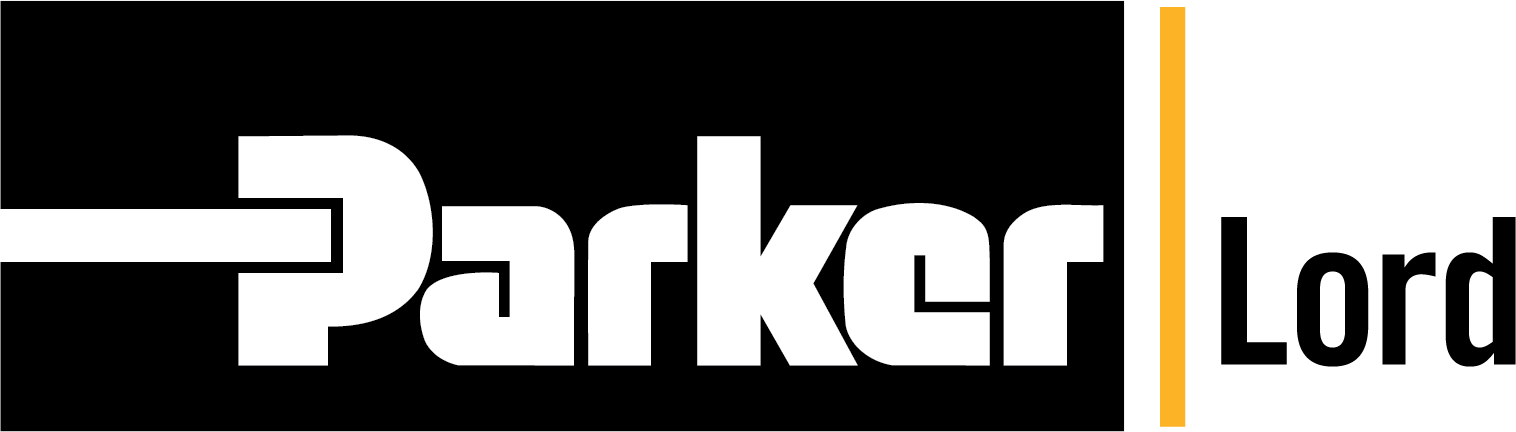
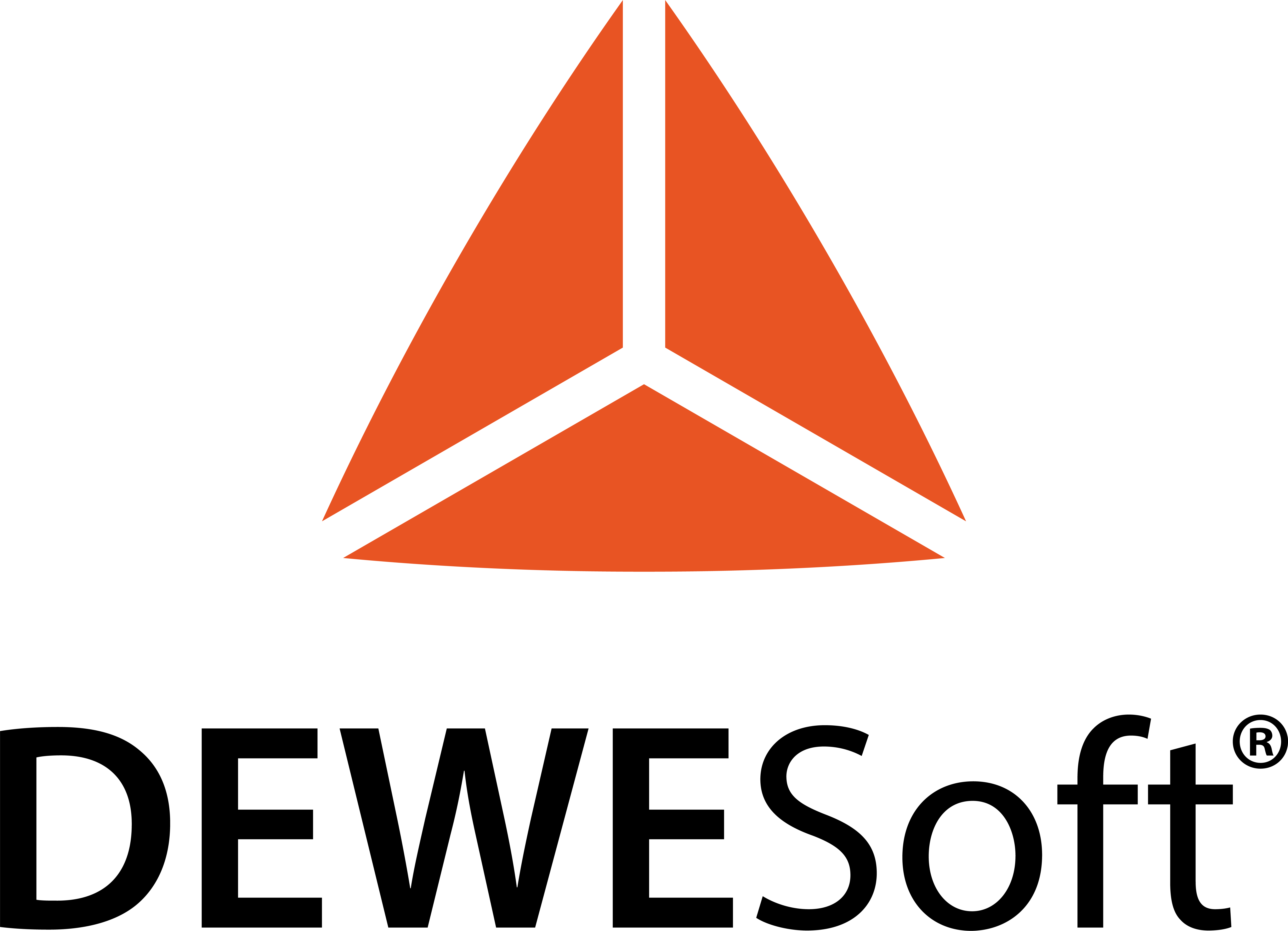
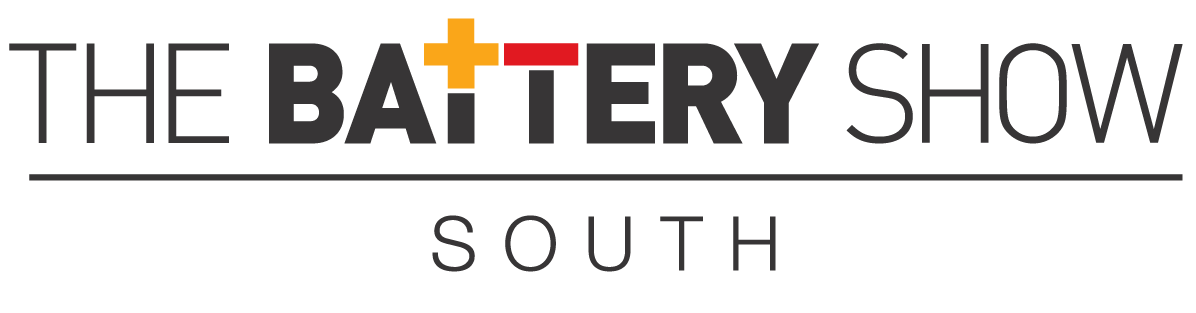
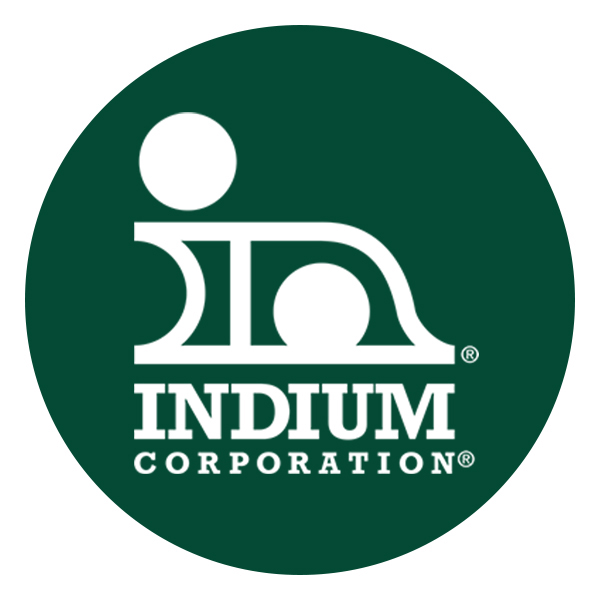

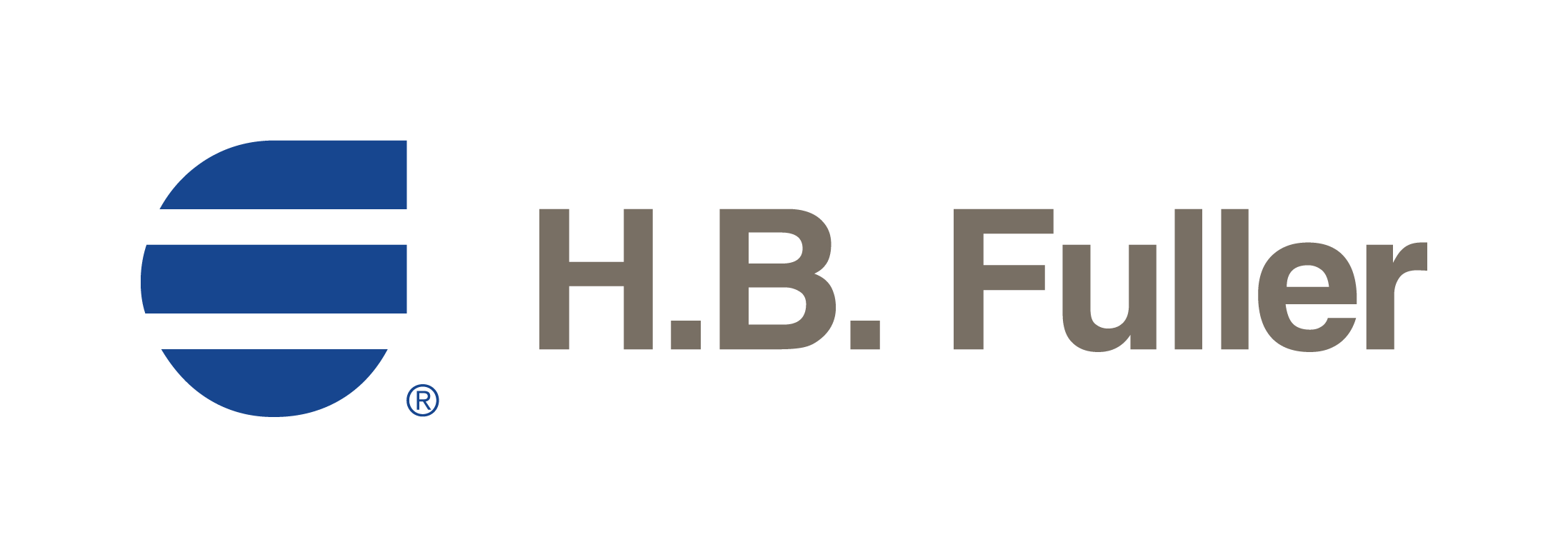
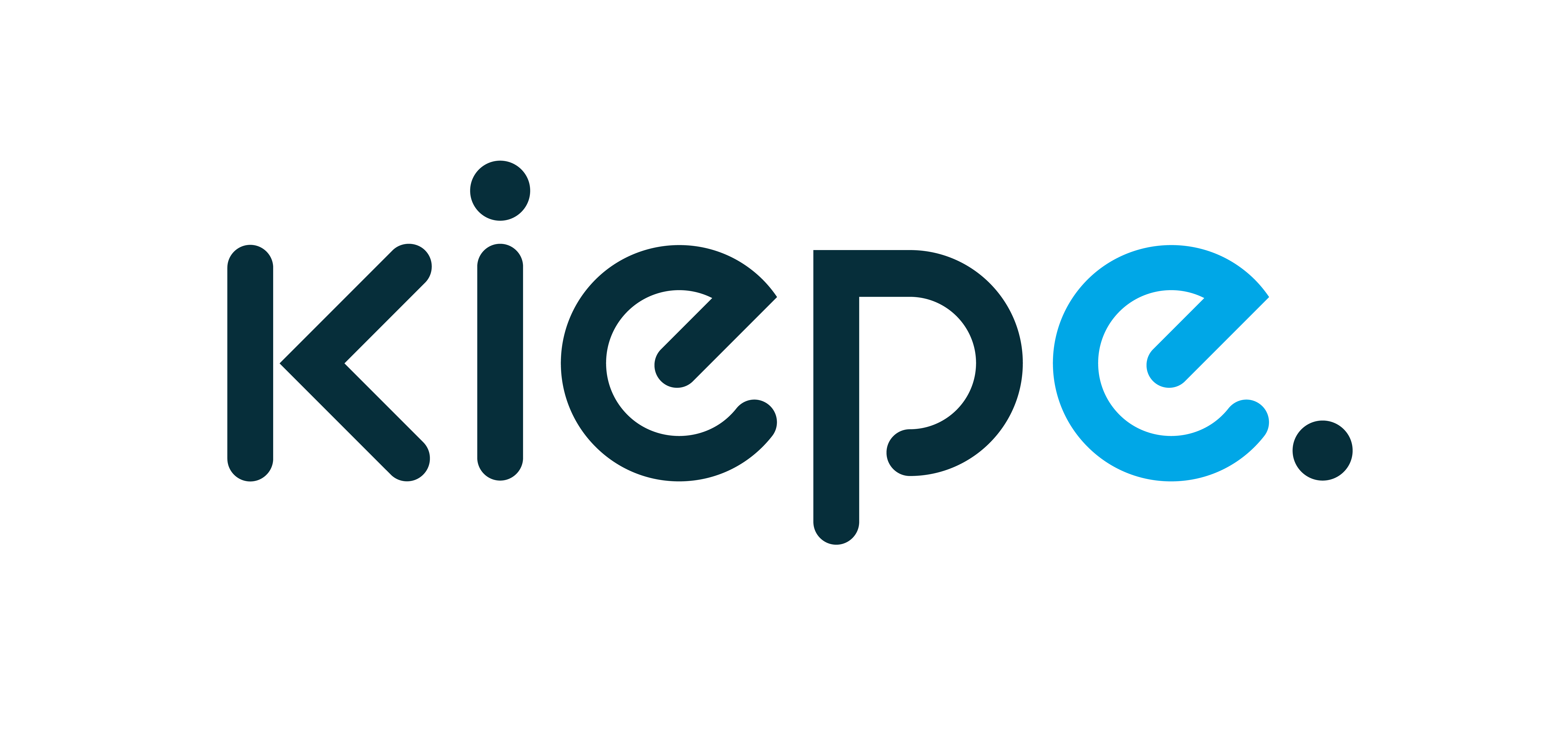
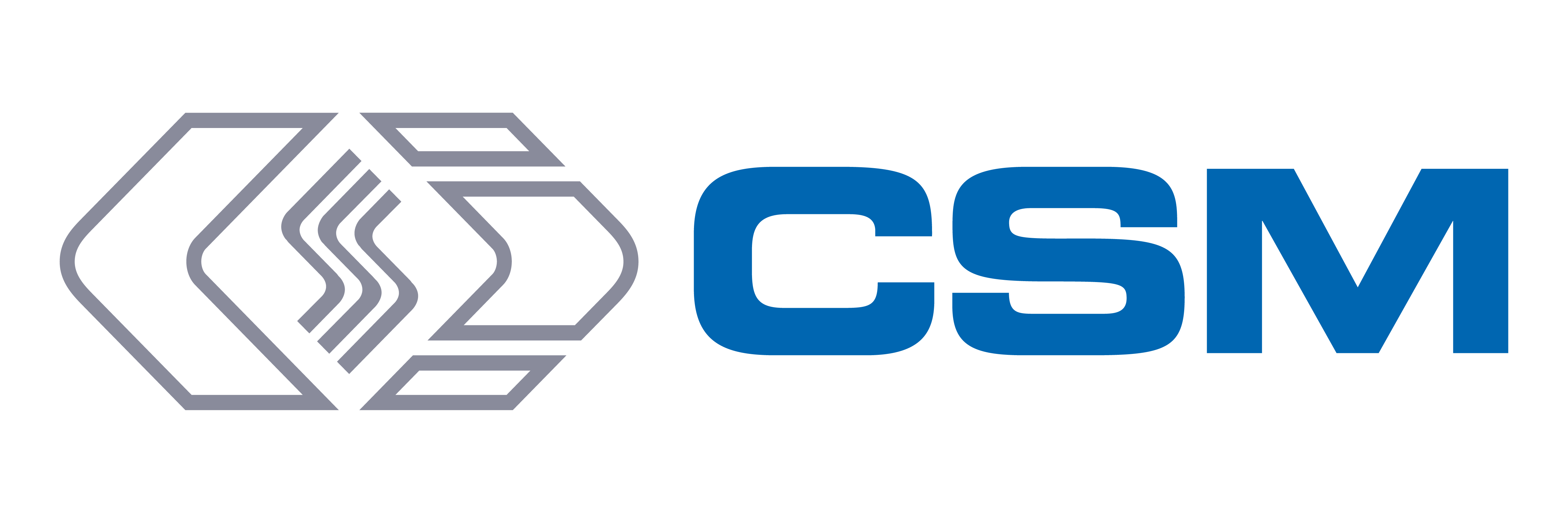