Andrew Cross
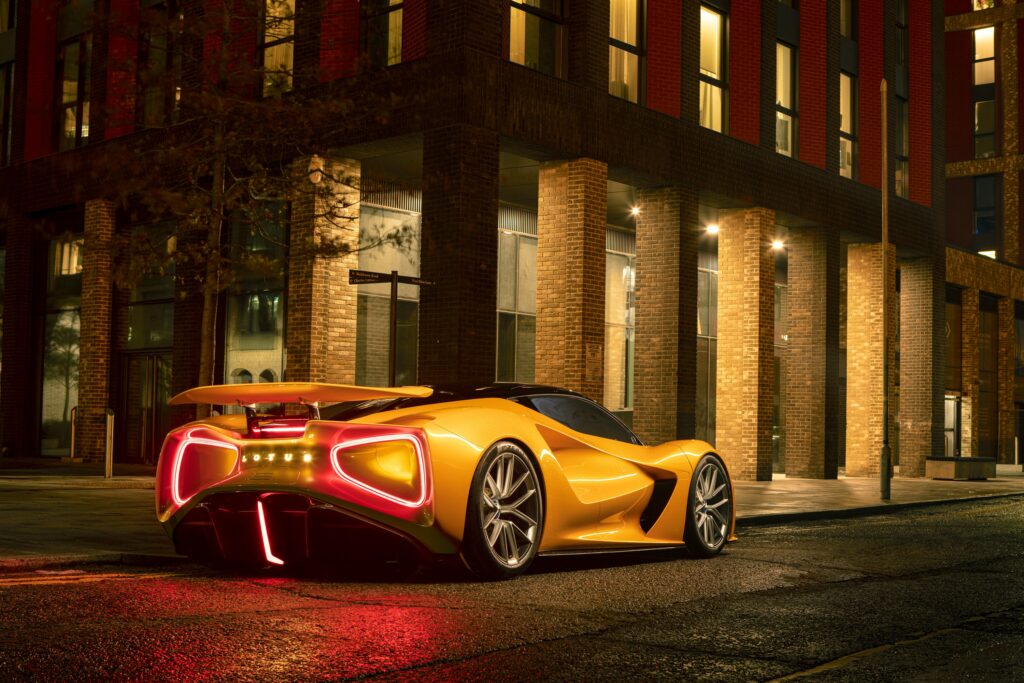
(Image courtesy of Integral Powertrain)
Theory into practice
Integral Powertrain’s CTO tells Rory Jackson how he has come to lead the company’s development of high performance consumer EV drives.
One of Andrew Cross’ most prominent early memories is the engineering company his father owned and ran, designing and manufacturing polymer parts, and developing much of his own production systems and tooling to enable their manufacture.
It is a legacy that Cross has indirectly continued throughout most of his professional life. As the CTO of UK e-mobility systems designer Integral Powertrain, he has led the engineering and supply of a range of highly customised electric machines for automotive traction and control across numerous projects, and now directs his company’s work across some of the most high-profile collaborations in the electric road vehicle world.
“While my father’s work gave me my first exposure to the engineering world, throughout my education I always really enjoyed physics and applied maths, and getting a deep understanding of the way machines work,” he recounts.
“My engineering degree, in Automotive Engineering from Loughborough [University, in England] largely predated the era of electrification, but even then I was always most drawn to the ‘difficult’ problems of engineering. I started with the fundamentals of IC engines but I really liked working on anything that needed a lot of core physics work or towards the application end, for example vehicle design.
This interest in physics-heavy theoretical work drove him to gravitate towards more experimental and high performance projects. From 1998 to 1999, he worked at automotive and race engineering firm Cosworth as part of his degree.
As an engineer at a relatively small company known for taking on large and high-profile tasks, he worked on the physics of several new engines being designed for niche vehicle applications. It was also during his time there that he met four key managers at Cosworth who would later become the directors of Integral Powertrain.
“Around that time, Volkswagen Audi Group bought Cosworth from Vickers,” he says. “They sold the racing part to Ford, and with that the supply of Formula One engines to Stewart Grand Prix, who would become Jaguar Racing and then Red Bull Racing, and kept the automotive engineering part. So rather than staying with Cosworth, those managers decided they wanted to maintain their autonomy to carry on their work in high-tech powertrain engineering.
“That motivated them to found Integral Powertrain. When I graduated, in 2000, I had the choice of going back to Cosworth – which was the ‘safe bet’, it being a 42-year-old company with 200 employees – or joining the former, which was a start-up with maybe eight people.
“Choosing Integral Powertrain might have been something of a leap of faith, but I’d seen the power of a strong first-principles approach when it came to rigorous engineering – particularly from now-director Luke Barker – in terms of building tools and templates not just for motors and inverters but across all aspects of how we run the business. That rules-based approach has become the core of our philosophy regarding bespoke technology development.”
Into e-mobility
For Cross and much of Integral Powertrain, the first foray into electric drives came in 2005, working on a variable-ratio centrifugal compressor for use as an IC engine supercharger. It needed two electric machines, one to generate power and another to add or subtract speed from the blower to control boost pressure.
“Before that, we’d been outsourcing our electric systems but things weren’t going well with our supplier,” Cross says. “That prompted us to consider making electric machines ourselves, and we thought, ‘How hard can it be?’ The rest is history.”
Although he took a brief sojourn to work for Mercedes-Benz in Formula One in 2007, out of an interest in a rule change on boosting which provided numerous high-technology challenges that he cannot comment on, he returned to Integral Powertrain in 2010.
“Since 2010 I’ve been working solidly on electric drive technology,” he says. “Initially, a lot of my focus was on motors, but motor control quickly grew as an area I was called to work on, particularly in the mathematics and physics of motor control methodologies.”
His first major project in automotive e-mobility was in 2010, when Integral Powertrain produced an all-new electric motor for a high-performance HEV, which would go into production in 2013. That e-motor was designed from a blank sheet, and achieved a power density of more than 5 kW/kg, far more than what was available commercially at the time.
This project also broke new ground in thermal management and vibration tolerance, as the motor was directly mounted to a powerful IC engine. The e-motor’s enclosures were made from sand castings and were specially designed to withstand the environmental harshness created by the fuel engine’s outer surface frequently breaching 140 C and 40 g vibration loads during operation.
“We made around 500 of those electric machines, and that project led to further programmes enabling us to go beyond its parameters,” Cross says. “Initially we were approached largely by motorsport companies, who wanted motors with a continuous power output of 20 kW/kg and more and 30 kW/kg peak. Those systems were the best in the world in terms of power density at the time, and getting that many kilowatts per kilo is still pretty challenging now.”
Just as high-performance racing has often influenced high-end automotive engineering, these days Cross leads Integral Powertrain’s efforts on several high-speed electric consumer vehicles for EV manufacturers Manifattura Automobili Torino (MAT), Lotus and now Triumph Motorcycles, as the former British motorbike giant switches from fuel vehicles to e-mobility.
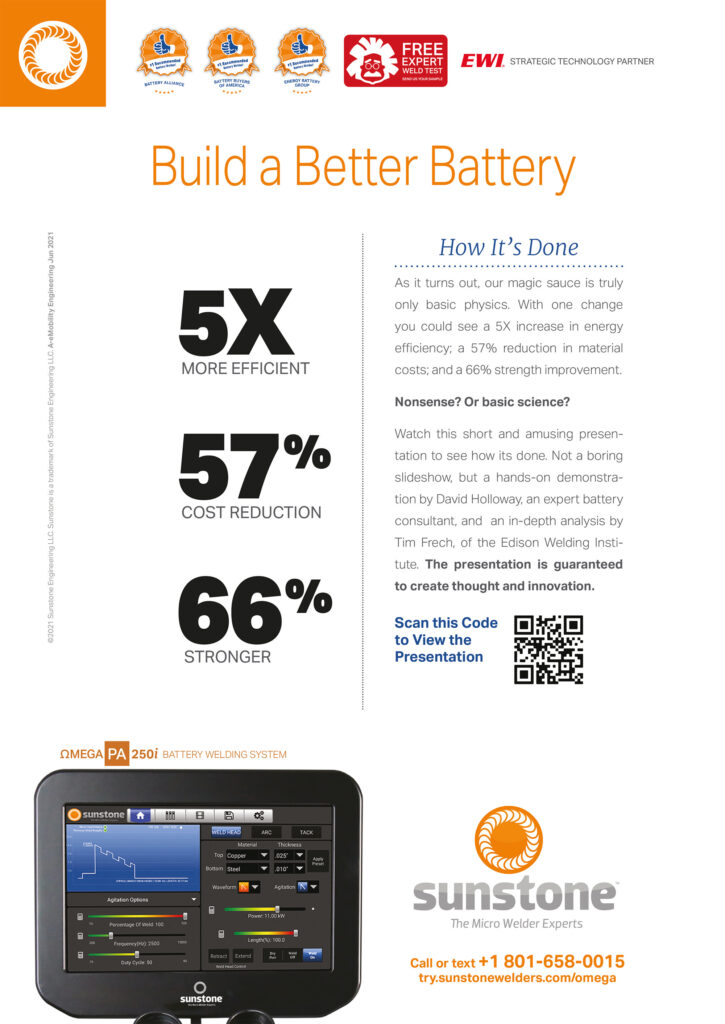
Parts and processes
All these projects use the same fundamentals in terms of motor and inverter design, while being scaled to suit each application’s requirements through the company’s rules-based tools and techniques. This allows the company to meet customers’ physical and performance parameters without having to start from a blank sheet each time.
“We use fundamental 2D finite element packages for the early design stages, especially for electromagnetic simulations,” Cross explains. “Beyond that though we use a lot of our own 1D, 2D and 3D tools and templates, with automated throughputs of data and simulation results between those tools.
“We start with concept simulations, often with just basic, superficial customer targets for maximum continuous peak and power output, speed and torque to determine how big or long the e-motor would need to be,” he says. “And we can output simulated datasheets for electric machines based on customer requests within minutes, if needed, with a couple of hours of refinement if more accuracy is desirable early on.
“We automate those outputs for use as inputs in 2D FEA and thermal analysis, and into application tools that allow us to design the different sections of the motor in a fairly rigorous and benchmarked fashion.
“It’s the same tools, processes and fundamental engineering across 14 different motor diameters, from a small 84 mm-diameter motorsport type machine to a 242 mm roadcar e-motor to machines over 400 mm. Over the years, we’ve just incrementally improved the reliability and autonomy with which we design everything inside, regardless of differences in voltages, power outputs or parts.”
Key to better optimisation of the performance and control of their powertrains has been advances in processors as well as integrated circuit board designs. These have helped to maximise the functionality of the company’s electric machines while keeping their electronics packages to a reasonable size.
“Better thermal insulation and management materials have been very important too,” Cross adds. “We have some proprietary thermal materials that we choose from depending on the thermal load, and we’ve also grown our understanding of the factors causing and reducing high-frequency losses.”
To achieve the high efficiency, low weight and compact packaging needed for their customers’ high-end inverter systems, Integral Powertrain uses silicon carbide (SiC) MOSFETs. Incorporating this transistor technology into their power stages also minimises switching losses to enable higher electrical frequencies and motor speeds.
“In some projects, those frequencies and speeds are a must-have; in others they provide efficiency benefits across cycles that can fully offset the extra cost of energy storage they might merit,” Cross explains. “For example, if you take a Tesla Model S with a battery pack of 100 kWh and estimate a cost of maybe $100/kWh, saving 7% of energy usage on-cycle will save $700 per pack, which you can reinvest in your powertrain and reduce your battery weight by 7% to get a lighter EV.
Although advanced transistor technologies are sometimes associated with concerns over supply chains and lead times, Cross notes that he and his company have reached agreements with their suppliers to commit fully before every project, and ongoing advances in SiC wafer fabrication are expected to expand output volumes in the future.
He adds, “While all these different technologies can be used to get the last 1% of performance out of a drivetrain, and we can choose components like the highest-remanence permanent magnets and best thermal-performance materials available, more and more of the time we’re designing for mass production, to create something that’s cost-effective to manufacture and assemble at scale, and relies on secure supply chains for delivering or finishing parts.”
Triumph Motorcycles
The return of Triumph to the forefront of global motorcycle manufacturing is centred on Project Triumph TE-1, a demonstrator prototype for the EV bikes it intends to develop. First announced in August 2019, the second phase of the project was declared complete earlier this year with the unveiling of the powertrain and initial performance results produced by Cross and his team
The combined motor-inverter system features a motor with a power density of 13 kW/kg, an overall weight of 16 kg and a peak power output of 130 kW. In producing the motor and inverter for Triumph, Integral Powertrain is also collaborating with Williams Advanced Engineering and Warwick Manufacturing Group. This is to ensure the scalability of the e-drive systems by working directly with the companies overseeing the long-term production and maintenance of the bikes.
“We have created a highly integrated and compact package for the motor inverter combination,” Cross says. “It’s a surface-mounted permanent magnet AC motor, with an in-runner rotor and external stator. It follows our platform derivative approach but with the motor length and windings optimised for the voltage and performance requirements.
“While Triumph is working principally on a demonstrator, what we’re making for them is an inherently scalable powertrain architecture,” he says.
“We’ve put particular work into the design of the power stage of the inverter to create something highly manufacturable and repeatable. That way, if they decide they want to increase the stator and rotor slot count while keeping the electromagnetics similar, it’s a reasonably straightforward matter of increasing the transistor count proportionally.
“The integration between the motor and the inverter includes a shared water-glycol cooling circuit running between the stator coils and SiC switches, to reduce weight and make the design simpler.”
Cross adds that the motor design exploits a rotor cooling system patented by himself and Integral Powertrain. The resulting architecture features a number of helical internal paths for the flow of liquid coolant through the radial length of the rotor, which run amid the stator and inverter cooling circuits.
“That technology allows us to be flexible with the permanent magnets we use, giving us a trade-off between cost and performance,” he says. “It also gives us more consistency during operation – a motor and its magnets can warm up gradually over a duty cycle and suffer increased losses, so inventing our own cooling approach has helped reduce that significantly.”
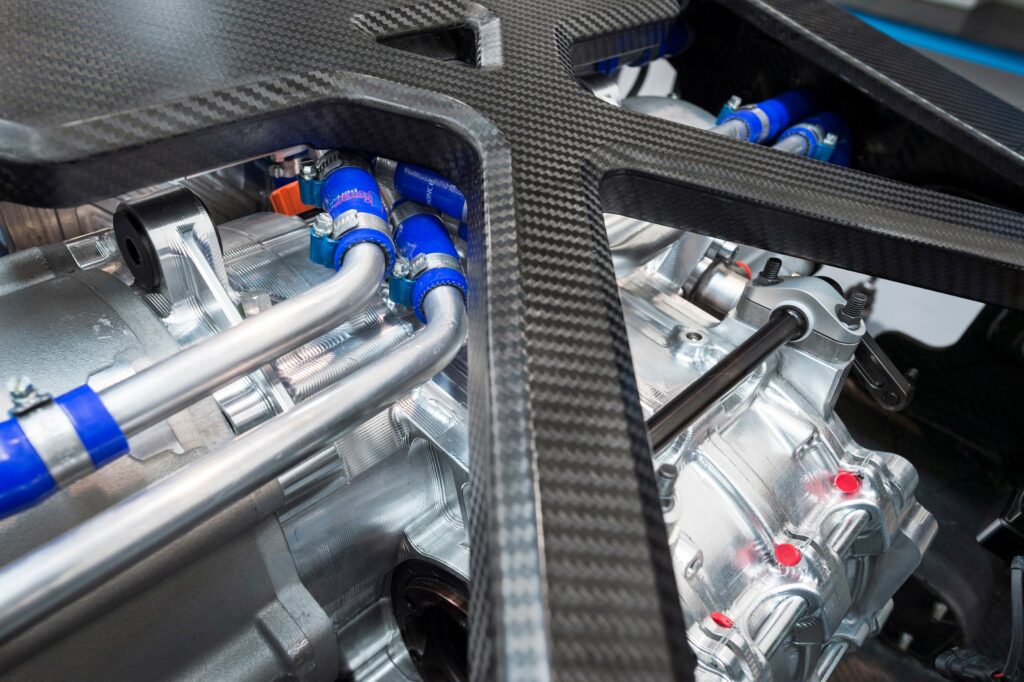
(Image courtesy of Integral Powertrain)
Hypercar powertrains
Cross and his colleagues are also working to supply the powertrain for the Owl Hypercar, which is being developed by Japanese company Aspark and will be built by MAT.
This all-electric car is slated to be the fastest-accelerating roadcar in the world (going from 0-100 kph in 1.9 seconds, and 0-299 kph in 10.6), and only 50 are expected to be produced worldwide. It will have a 69 kWh lithium-ion battery, enabling a maximum range of 450 km.
“The Aspark Owl will be a four motor car, and we will need to get 500 bhp or 360 kW out of each of those continuously,” he remarks.
As with the Triumph Motorcycle project, the Owl’s motors are in-runner e-motors with surface-mounted permanent magnets, although with cast housings rather than machined, as for the TE-1.
“Each of those motors is run through a transmission, in order to translate their high speeds and high power density into high wheel torque,” Cross explains.
“The rotor-stator air gap is where the force comes from, and there’s a limit to how much can be derived from optimising the windings and magnets. While you certainly want to maximise the air gap’s shear stress or force density to pull on the rotor as hard as you can, the other way to get power out of a motor is to move it as fast as possible.
“To make a faster motor, you can make the diameter larger to increase the distance per rotation for a given rpm, or you can drive it to spin at higher revs. Obviously, if you’re designing for a fixed wheel and package size like we are with the Owl, and you want a higher power density, the only way to do that is with a very fast and highly geared drivetrain.”
Integral Powertrain is also working on the forthcoming Lotus Evija. This is the first EV from UK-based Lotus Cars and is due to enter production later this year. It will have a 70 kWh lithium-ion battery pack for 400 km of endurance and a top power output of 1470 kW.
“That has a similar power level to the Owl, with a heavily integrated package – inverters on the inboard side, followed by motors and narrow planetary gearsets going outwards to the wheels,” Cross says.
“That means two packaged systems in total, with a shared cooling and lubrication system in each enclosure for the motors, inverters and gears, to achieve a torque-vectoring approach with one motor and inverter per corner of the car.”
Future plans
In addition to innovations in SiC fabrication, Cross and his team are keeping their eyes out for any future technologies that stand to reduce the lead times and costs, and increase the output volumes, of EVs and e-drives.
“This is a really exciting time to be involved in the world of EVs, and we’ll be interested to see all the new kinds of vehicles and powertrains that come up over the years ahead,” he says.
Andrew Cross
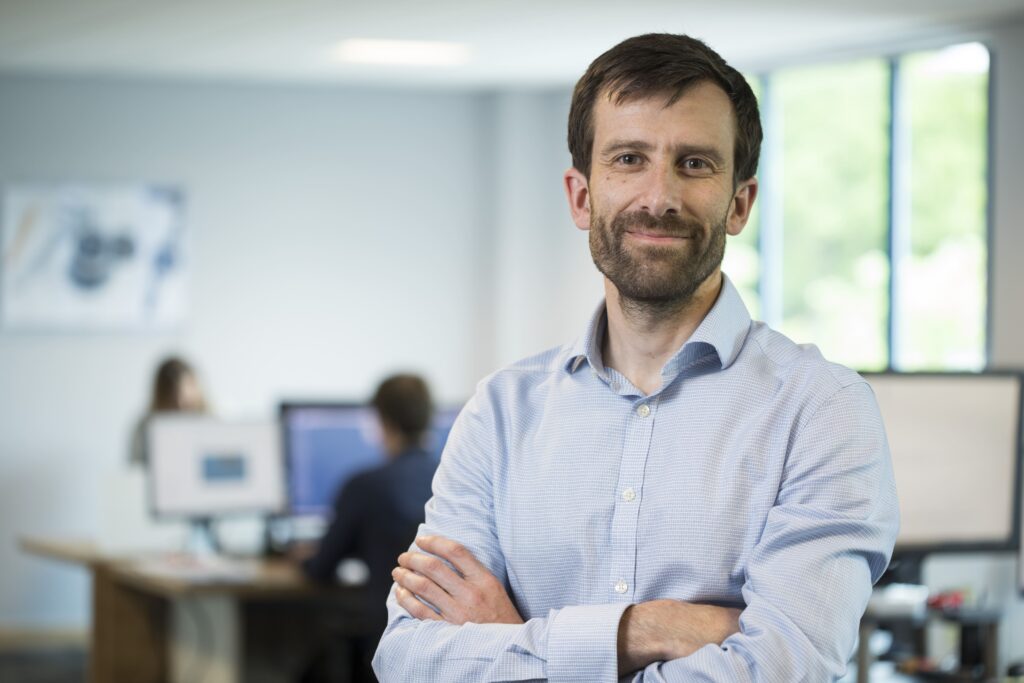
Andrew Cross is the chief technical officer at Integral Powertrain. He attended Loughborough University, in the UK, from 1996 to 2000 and achieved a bachelor’s degree with honours in Automotive Engineering.
From 2000 until 2007 he worked as an engineer, senior engineer then principal engineer at Integral Powertrain, before spending three years in Formula One at Mercedes Benz High Performance Engines.
He returned to Integral Powertrain as a principal engineer in 2010, before being promoted to chief engineer in 2014 and then CTO in 2018.
ONLINE PARTNERS
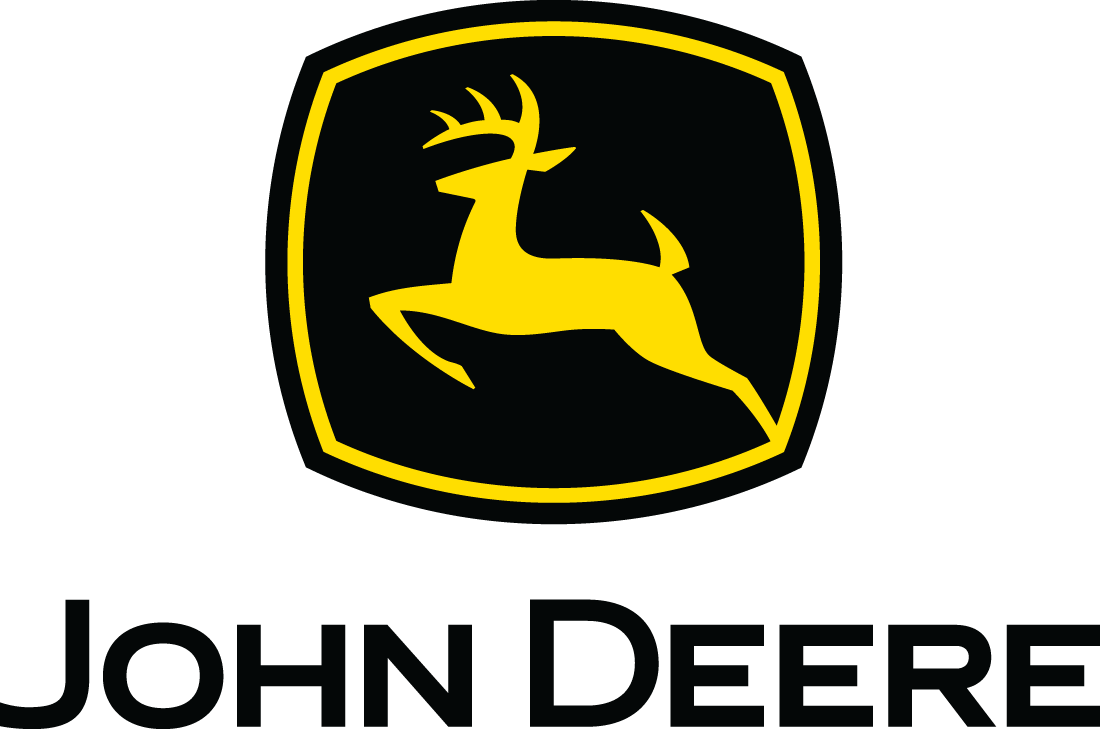
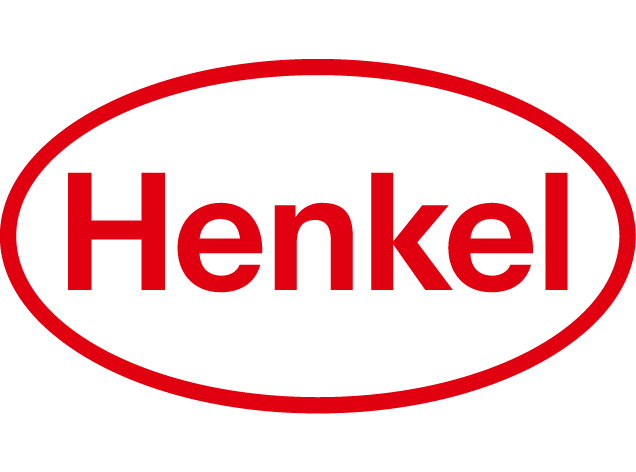
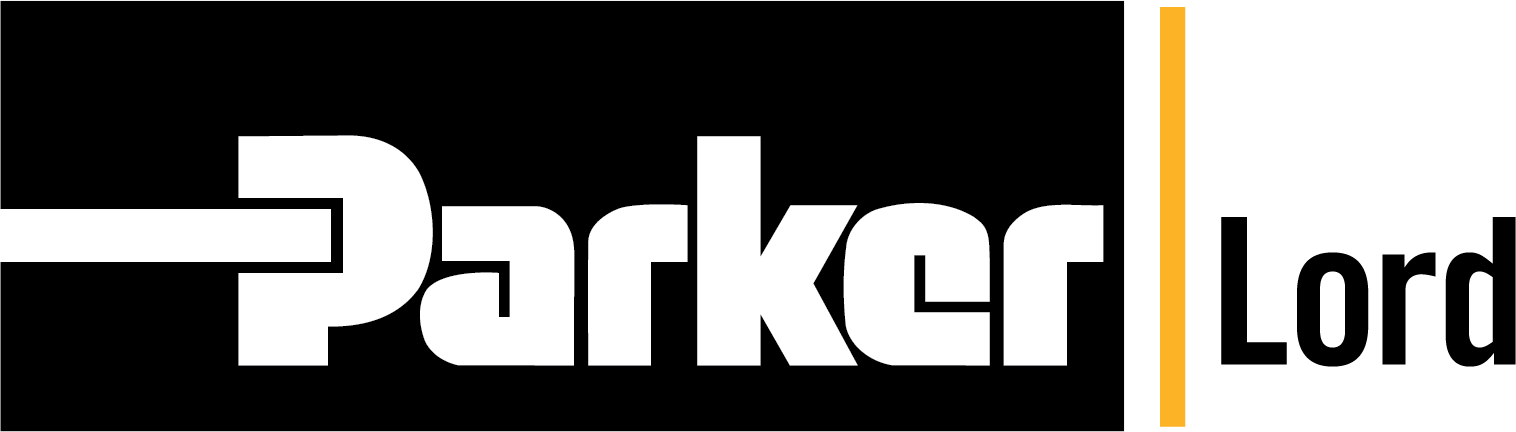
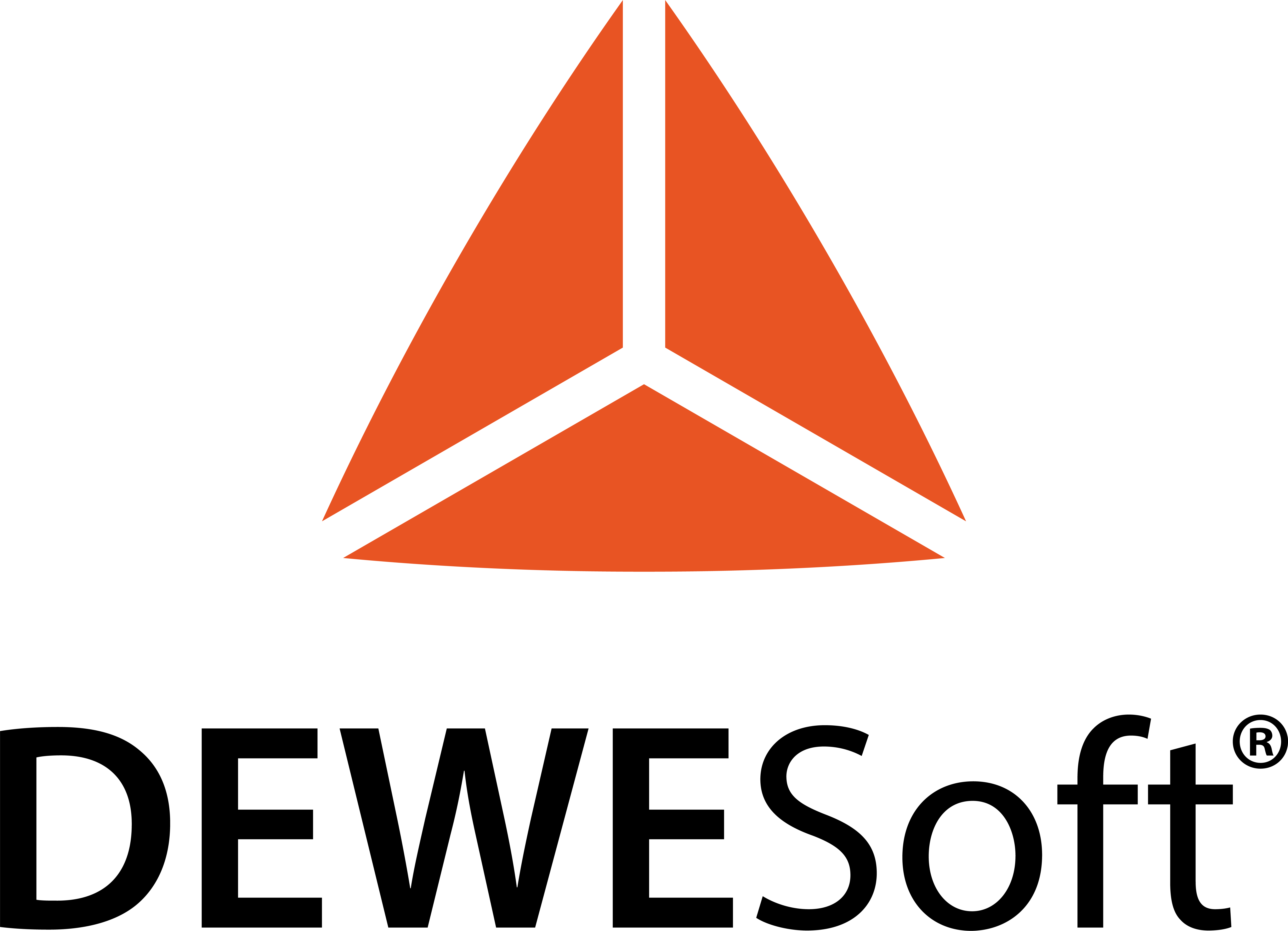
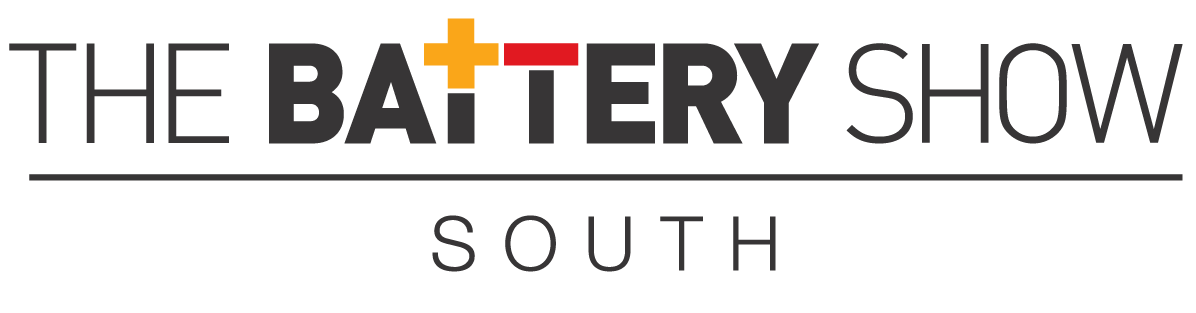
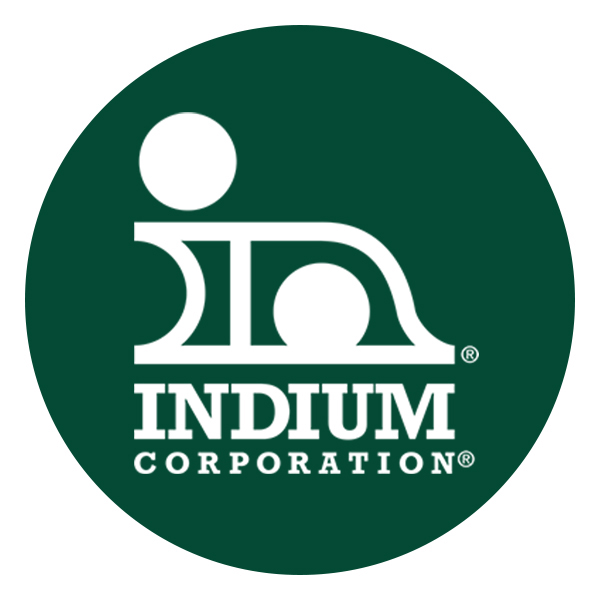

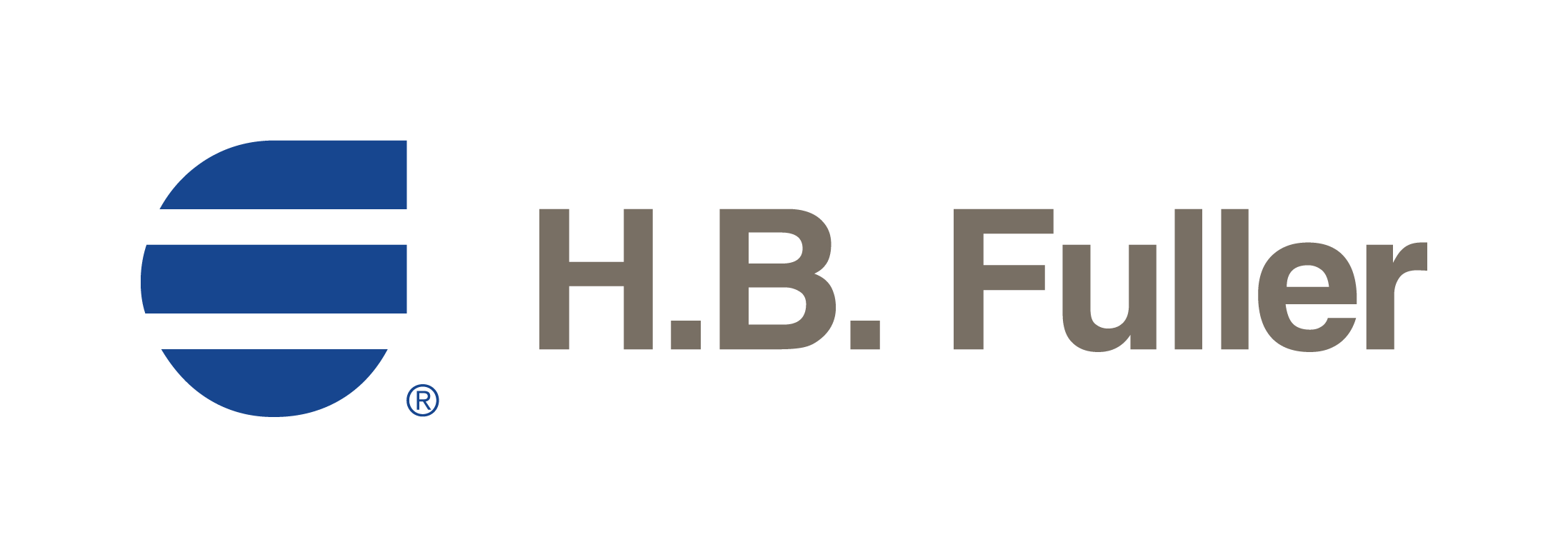
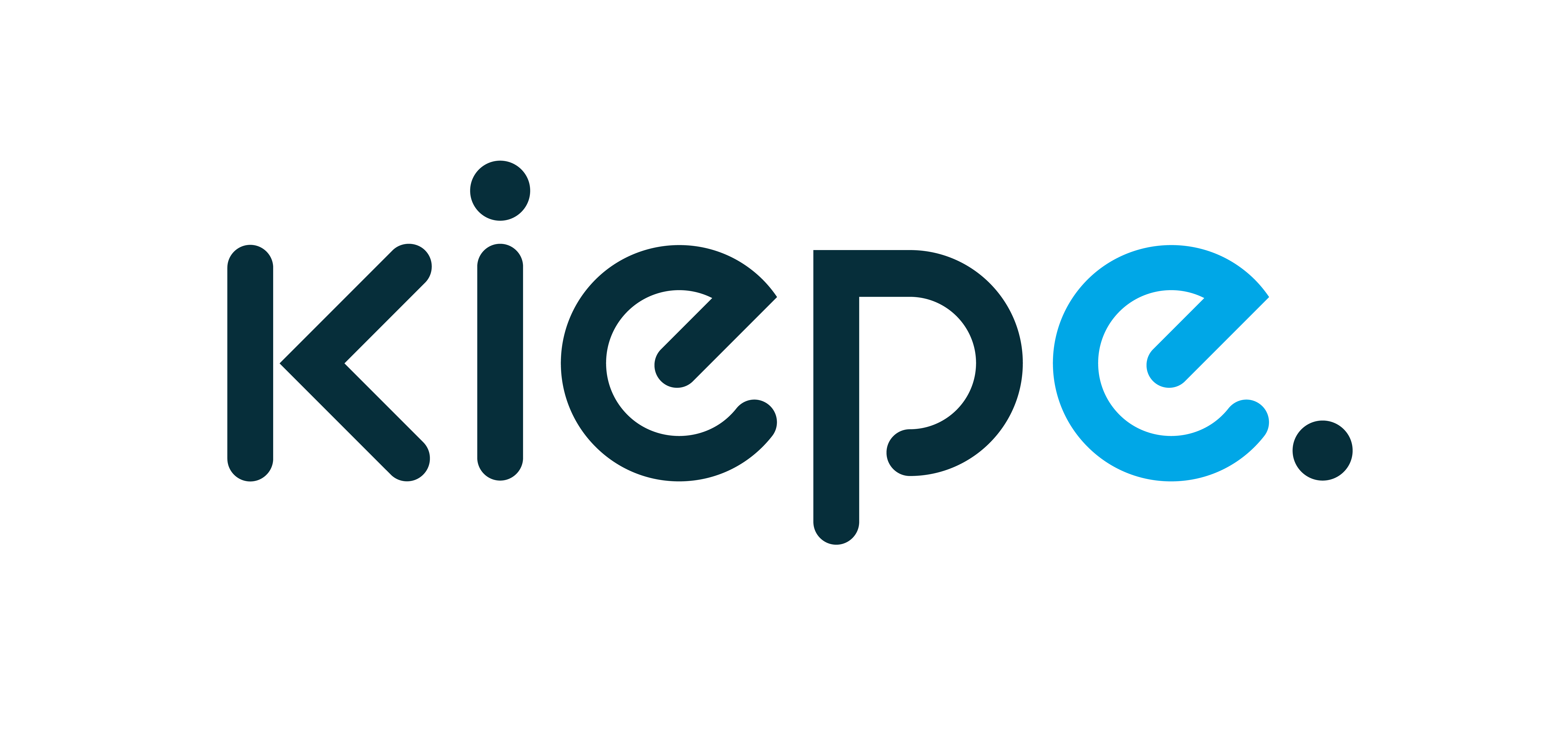
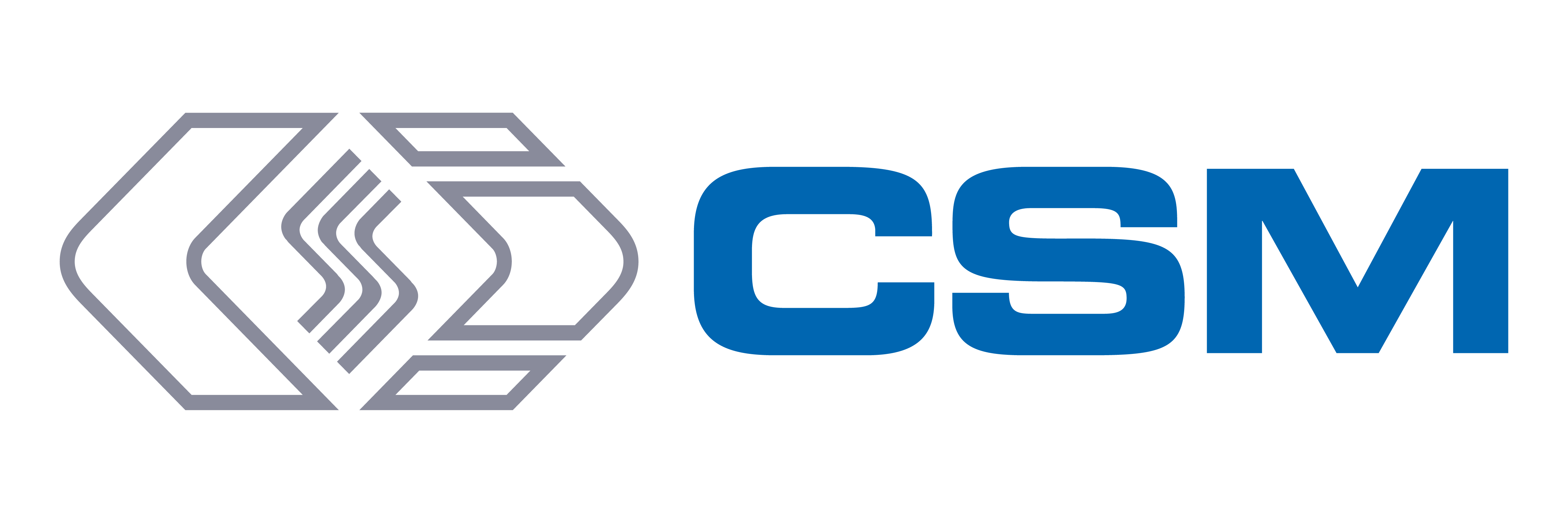