Allan Paterson
On the home straight
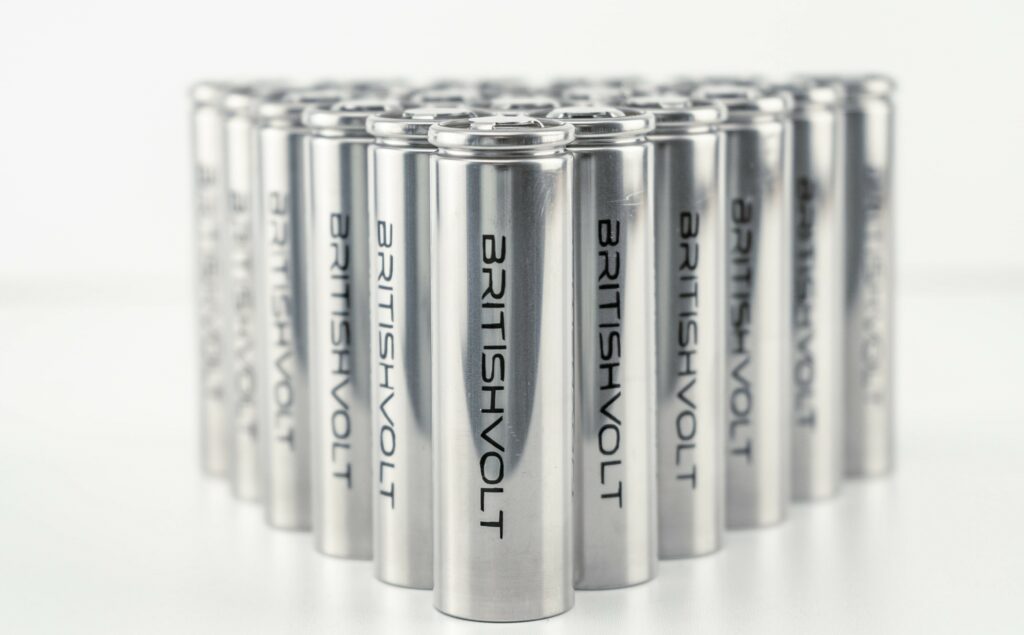
(Images courtesy of Britishvolt)
Britishvolt’s head of r&d tells Rory Jackson how his experience in battery cell technology has led to him being involved in setting up the UK’s first gigafactory
In high-tech industries such as the EV world, supply chain resilience is now regarded as a strategic imperative, and many nations now push for domestic production of their critical material and component inputs (or at least to import them from a trusted neighbour). And with climate change now at the forefront of the global agenda, domestic manufacturing of EV batteries is desperately sought by all countries looking to decouple mobility from harmful emissions.
In the UK, this demand has led to the advent of Britishvolt, which was founded in December 2019 and is already building its first battery gigafactory in Blyth, northern England. The design, manufacturing and quality of the batteries produced at the facility will exploit a huge body of scientific knowhow that the company has amassed through its r&d, conducted both internally and through numerous valued partnerships.
This r&d has been led since late 2020 by Dr Allan Paterson, Britishvolt’s chief technical officer. His life and career have encompassed a plethora of projects and ventures across electrochemistry, as he has long sought to bridge the gap between breakthroughs at the laboratory level and commercial production at the plant level (even before the current supply chain concerns came about).
STEM to chem
Growing up in a rural community in Scotland, Dr Paterson took a keen interest in scientific studies early in life. In his late teens he planned to undertake a joint physics and chemistry degree at the University of St Andrews, one of the UK’s oldest and most highly regarded institutions, particularly in terms of mathematics and the sciences.
“That was driven by some very inspirational instructors – especially one of my chemistry teachers, a woman who had a PhD in the subject – and it was mainly because of her guidance that I went into doing chemistry in the end, and ended up spending 10 years at the university,” Dr Paterson recounts.
“My undergraduate degree actually started as maths, physics and chemistry, but I soon dropped the first two in favour of chemistry because I found it far more fun. It offered the most opportunity for experiments and other practical things, including ways to get away from lithium cobalt oxide and other cobalt-dominated cathode chemistries by using less expensive, more sustainable and non-rare earth elements such as manganese.
“That eventually became the focus of my PhD and subsequent research, especially in trying to make NMC cells with more manganese and less nickel and cobalt.”
It was also in his undergraduate years that he began engaging with industry, including two placements with Imperial Chemical Industries (later acquired by AkzoNobel in 2008) involving work on sunscreen products.
“It might sound strange, but the sunscreens used nano-particle oxide materials, including zinc and titanium oxides for high solar protection factors, and the way in which you make those materials is pretty close to how you made battery material oxides,” he remarks.
“Those projects led me towards solid-state chemistry and then, towards the end of my undergraduate years I was invited to do a PhD in either fuel cells or batteries, again at St Andrews. It was a close choice, but I went with batteries as I got to work with Professor Peter Bruce, who was one of the premier battery authorities in the UK at the time.”
The PhD programme lasted 4 years, and was followed by a further 4years in postdoctoral research at the Faraday Institution’s Beyond Lithium Ion group, where areas of project focus include solid-state batteries, sodium-ion chemistries and lithium-sulphur chemistries.
In 2009 he was asked to join Axeon, a battery pack designer and integrator that was later acquired by the chemical and metals multinational Johnson Matthey (JM) in 2012. That, and Dr Paterson’s expertise rapidly led to his promotion to the role of chief electrochemist for JM Battery Systems in 2013.
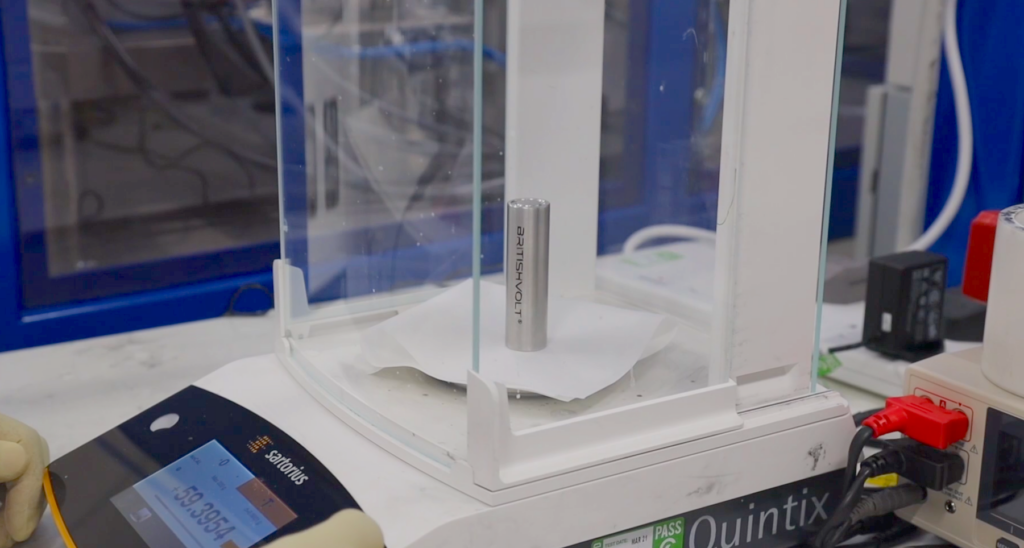
Commercialising electrochemistry
“At the time, JM was getting involved in lithium-ion pack design for a whole range of stuff, from the McLaren P1 and many other sportscars we can’t talk about, to all sorts of buses and trucks, and even into e-mobility as it existed back then,” he recounts.
“We were designing and building e-bike packs for a major EU Tier 1 supplier to bicycle manufacturers, and our work went all the way down to single-cell and BMS technologies. All those different projects meant we were ordering something close to 100 million cells a year, from Samsung, LG and similar companies.
“Since even the very successful JM couldn’t grow its battery r&d team quickly enough to match its ambitions in that space, it acquired numerous teams and facilities in LFP, NMC, the highly complex and nickel-rich eLNO chemistries and other materials, across North America and elsewhere.”
As the e-mobility market grew, Dr Paterson found himself working on Cummins’ large EV bus programme. The success of that project drove Cummins to acquire JM Battery Systems in 2018, and to keep Dr Paterson in his role as chief electrochemist.
“Already though, I was feeling a strong pull towards returning to the more fundamental elements of battery science in the UK, and around that time I’d been talking with the people involved in installing the Faraday Institution and Faraday Battery Challenge as the central pillars for funding for academic research into batteries in Britain,” he says.
“Back in my early JM days I’d been involved with the UK Auto Council, discussing where British industry was suffering gaps in capability. We had loads of great fundamental research, and lots of companies and teams making cars, but not a whole lot in the middle.
“So we set up what became Warwick Manufacturing Group’s [WMG’s] pilot line laboratory, the High Value Manufacturing Catapult, to accelerate laboratory innovations into commercial realities. Meanwhile, Faraday further widened its academic research programmes into batteries, and also set up the UK Battery Industrialisation Centre [UKBIC], itself now also a major active accelerator for automotive batteries.”
Five months after the Cummins acquisition, Paterson therefore leapt at the opportunity to join Faraday science as its head of programme management, not only to return to fundamental battery sciences but to oversee, guide and steer about 25 university departments and 500 researchers.
“The mass research, the industry accelerators and soaring government investment really all came together to form the nucleus of Britishvolt,” Dr Paterson says. “All those excellent resources interplaying with each other and being so quickly and directly accessible meant that a company focused on an EV battery development programme was bound to be formed, and sooner rather than later.
“So I overlapped with Isobel Sheldon at JM [now chief strategy officer for Britishvolt] over about 18 months. While she went to UKBIC, I went to Faraday for about two-and-a-half years, and one day I got a phone call from her, telling me about this somewhat scary but very exciting plan to create Britishvolt and build a gigafactory in the UK, so I joined them in October 2020.”
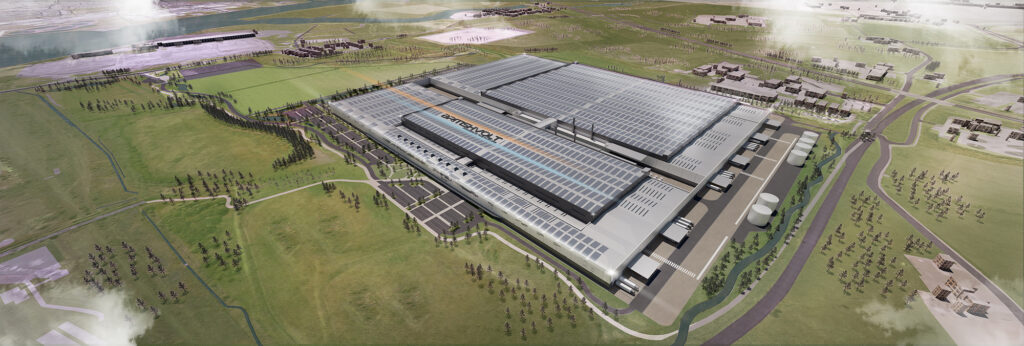
Britishvolt r&d
Much of Dr Paterson’s time is spent continuing the research into optimising cathode materials for sustainable energy storage solutions, although naturally the scientific knowledge and tools have advanced hugely since then.
“Calculations and simulations used to take upwards of an hour, now they’re often instant, and the increase in computing power means less of the work has to be done empirically,” he comments.
Britishvolt’s research into cell design for manufacture is divided essentially into three main elements. The first is theory and experimentation with the active and inactive material mixtures that comprise the electrode chemistries.
The second element is the mechanical design and integration of modules and packs, while the third is the physical handling of materials. The latter encompasses the stages, skills and tools needed to process discrete components and black powders into subcomponents ready for assembly, with cells that bear all the correct structural densities, porosities and other parameters to result in all the behaviours expected from laboratory findings, within a fully integrated device.
“A cell by itself is a highly complex system: the way material A interacts with materials B and C, and how they interact with D all link together,” he notes. “If you change one material, you can easily trigger three behavioural changes in each of your other materials. The three elements of our research are increasingly coupled together, because the behaviours of materials are closely linked to how you process them, and that influences the cell’s final electrochemistry.”
A lot of research also goes into cell form factors, not only the well-known ones such as 18650 and 21700 cylindrical cells, but non-commoditised designs such as many pouch cells or large prismatic assemblies, and how these latter types might lead to variations and advantages in holistic design practices such as thermal management or chassis-specific engineering.
“Holistic customisation is one area where we’re working especially hard to differentiate our products,” Dr Paterson continues. “European carmakers are looking for premium performance batteries, not so much in terms of straight maximisation of energy or power but how the performance parameters can be tailored at the cell level so that you get a pack with specs that match the application.
“So two cells can have the same ingredients, but with a slightly different recipe you can get a slightly differently structured electrode, which can also entail a slightly different cell form factor. The way you connect a group of that cell type can then further tweak and differentiate your resulting performance, in terms of, say, energy, power, safety, life and cost – you can think of those as your ‘top five’ parameters.
“Say you want a long-lasting, durable series of packs for a fleet of big trucks, then you can lose maybe a little energy or power for more life and safety. Or consider a high-performance sportscar EV: it’ll probably only get used occasionally, so you can lose some life and durability for some high-performance power stats. By understanding cell technology at the most granular level, we can really drill down to deliver products tailored exactly to what different vehicle applications need.”
Britishvolt is also positioning its resources to be ready for mass recycling and re-use of its battery materials, anticipating that around 7.5 years after its packs enter production and use in 2024, re-manufacturing facilities will become enormously useful for sustainability and expanding productivity for its battery products around 2031.
Gigaplant plans and progress
Blyth, in the north-east of England, was announced in December 2020 as the site chosen to host Britishvolt’s first gigafactory (referred to by the company as the Gigaplant); it is also Britain’s first mass EV battery production facility and the second in Europe, following the establishment of Northvolt’s facility in Sweden. Construction of the plant began in July last year.
“The Blyth site is a giant, flat, former power station zone, with rail facilities and a deep water port. That helps a lot in developing the site quickly, which we’ll do in four phases between now and 2024,” Dr Paterson remarks.
“There’s a lot to be excited about with this plant’s future, not just the 3000 jobs it will directly create. Consistent with our goal of accelerating clean mobility, it’ll be entirely electric-powered, unlike some gigafactories that use gas. Our site houses part of the landing station for offshore wind facilities such as the Dogger Bank wind farm and the one further north at the Firth of Forth, as well as the landing station for the interconnector to Norway’s hydro-renewable grid.
“We are incredibly lucky to have access to 1.3-1.4 GW of renewable electricity, and of course the entire roof of the facility – within a 93 hectare site – will be covered in PV panels, with energy storage on site.”
In addition to energy inputs, material supply chains have also largely been secured with European partners, compliant with bilateral rules of origin on materials to prevent the gigafactory’s 300,000 EV batteries produced annually from being hit with EU trade tariffs.
“So all the cathode materials effectively need to come from Europe,” Dr Paterson adds. “Fortunately we’ve made agreements with companies such as Glencore, who will supply a portion of cobalt, that especially vital material.
“That will change over time though as the rules get tougher. We expect we’ll also need to comply with things such as anode materials and meeting minimum target percentages of recycled materials in our cells in the years ahead, but we’re well-positioned to incorporate those as legislation requires.”
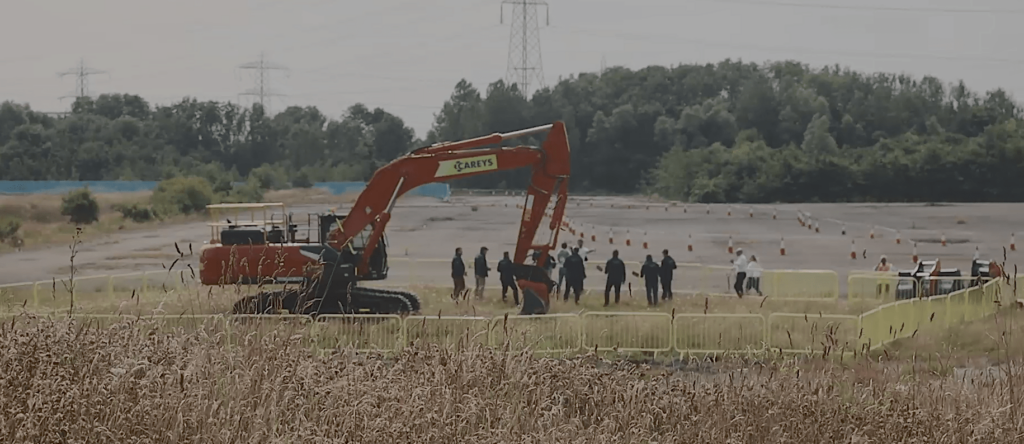
Beyond the Gigaplant
Britishvolt is working aggressively to ensure the gigafactory’s production readiness in 2024, with an anticipated eventual output capacity of 30 GWh of packs a year (300,000 packs of 100 kWh each), and cell r&d continues to accelerate.
Paterson however also points towards numerous ventures, especially additional partnerships beyond not only the Blyth area but outside Britain that he sees as vital to the future success of electric mobility across Europe – and not just in clean energy and raw material supplies.
“If we wanted to produce identical cylindrical cells to those made in China, we could have bought turnkey manufacturing lines, but as I say, we’re going to offer far better products than those, specific to application requirements,” he says. “So for the past 2 years we’ve been choosing and working with developers of that equipment, far and wide, to get exactly what we need for highly optimised but still flexible cell-to-pack manufacturing.
“For instance, we’re working with Manz in Germany, who are experts at welding and mechanics for high-throughput automated battery manufacturing, and internally we have experts such as our projects director, who effectively built the Jaguar Land Rover plant in Nitra, our chairman, our COO Isobel of course, and many others who have come together to push us on that accelerated path.
“We are also continuing to use UK facilities such as the universities, UKBIC, and research facilities and partners on everything from prototyping to fabrication. That has also leveraged widespread advances in CAE and digital twinning for cells, packs and factory layouts; Siemens and Imperial College London have been hugely helpful there.
“Lastly, WMG’s facilities have been vital to testing and validating batches of our cells, which allows us to really optimise our material formulations and chemistries. We’ll often take tested batches from there directly to UKBIC, to make GWh-representative samples. So we’re now at the true gigawatt-hour scale, we’ve matured our cell chemistries, and we have all the data we need for our next-stage concept validations and engagements with our customers, so they in turn can design and specialise their EVs around our batteries.”
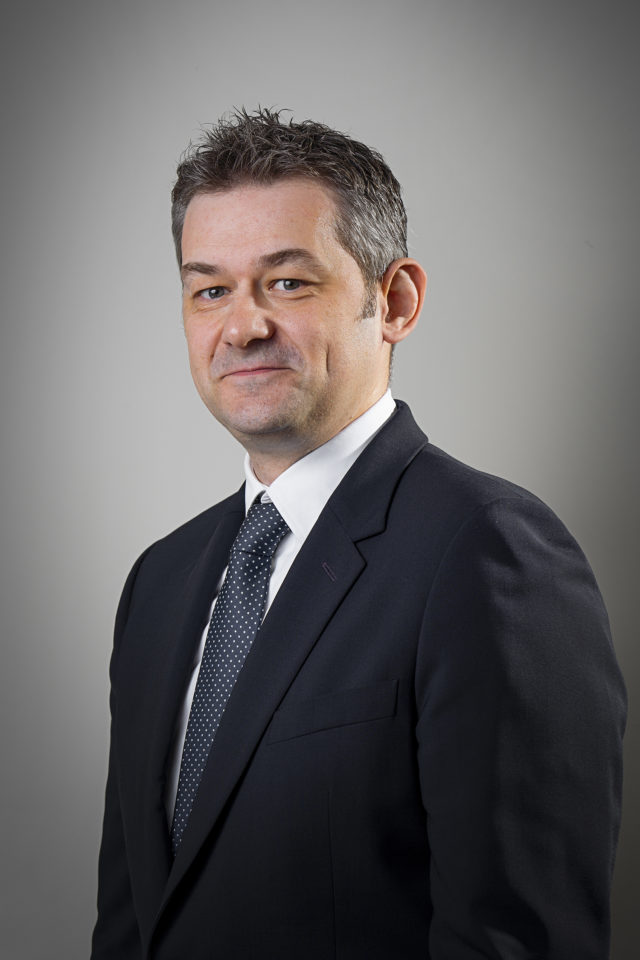
Dr Allan Paterson
Dr Allan Paterson was born in Edinburgh in 1977 and raised in Selkirk. He began his university studies at St Andrews, in Fife, Scotland, where he initially studied mathematics, physics and chemistry before specialising in – and eventually achieving a PhD in – chemistry.
He completed his chemistry undergraduate programme in 1999 before starting a 4-year PhD also in chemistry, which led to 4 years of postdoctoral research.
Dr Paterson joined Axeon in 2009, which was bought by Johnson Matthey in 2012 and renamed Johnson Matthey Battery Systems in 2013, with him becoming chief electrochemist. The company was acquired by Cummins in 2018, after which he moved to the Faraday Institution to become its head of programme management, overseeing battery r&d by about 25 universities and 500 researchers.
He joined Britishvolt as CTO in October 2020, and now oversees much of its progress across battery r&d, validation, material supplies, manufacturing line development and other areas.
ONLINE PARTNERS
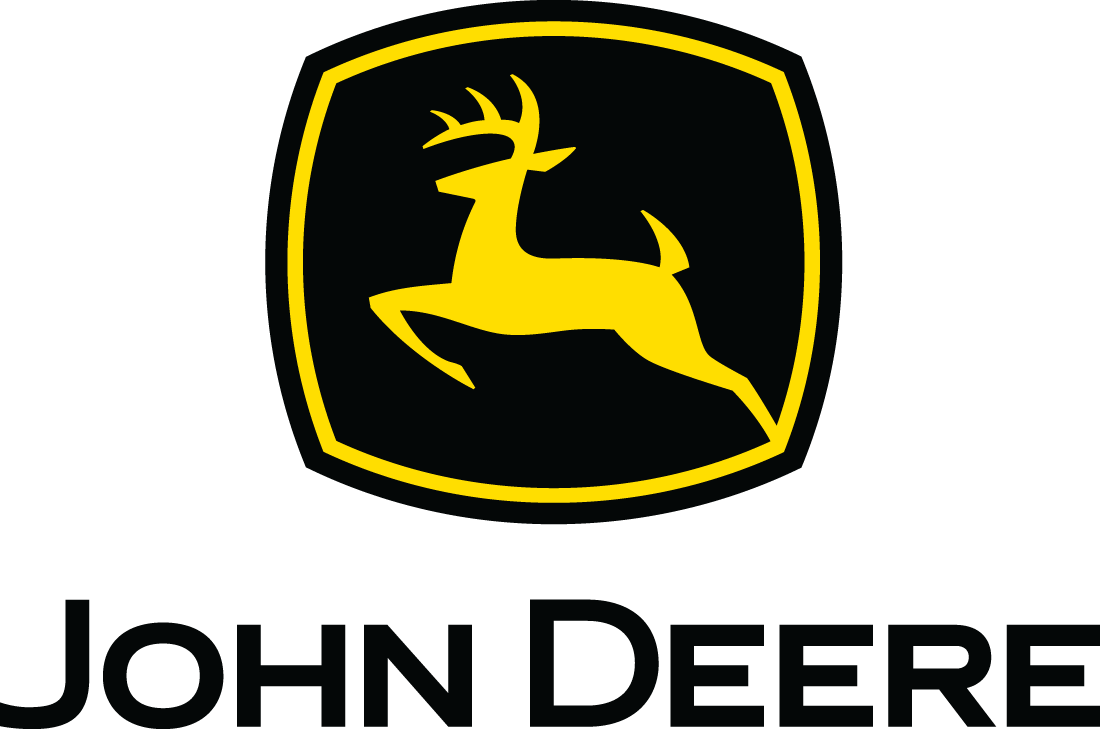
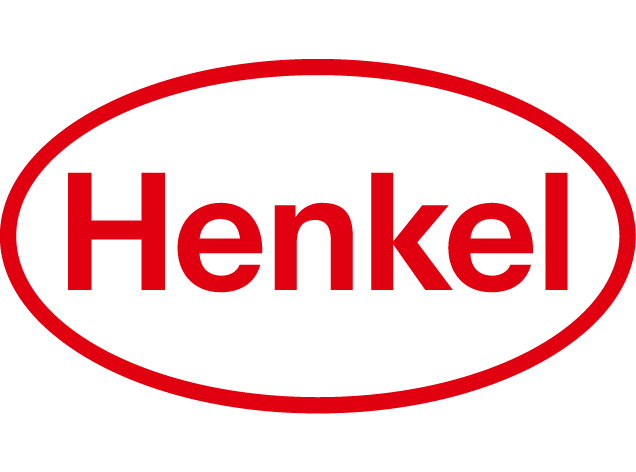
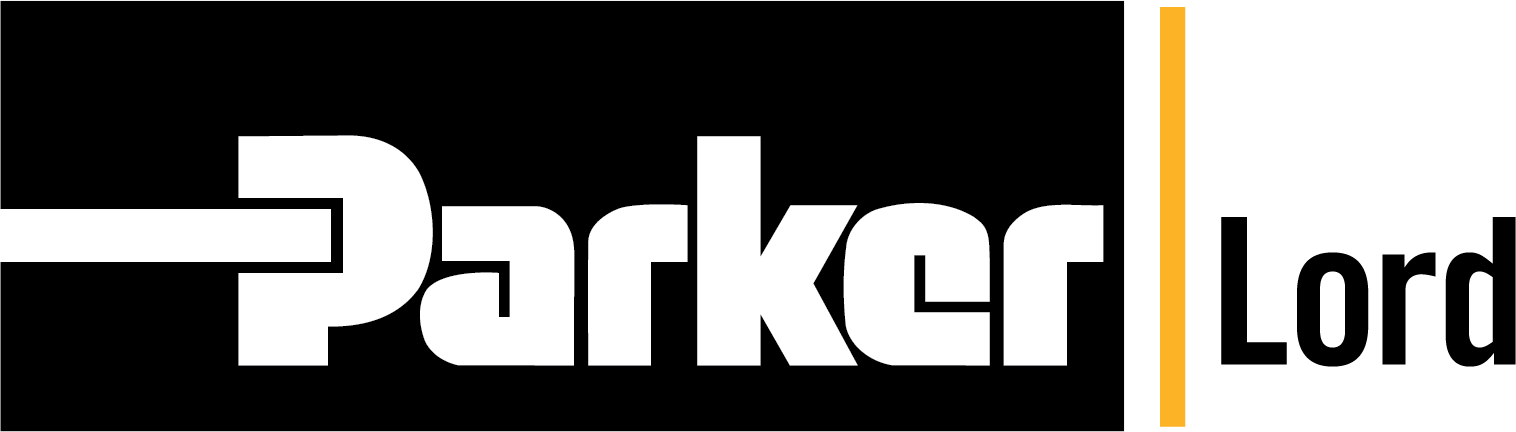
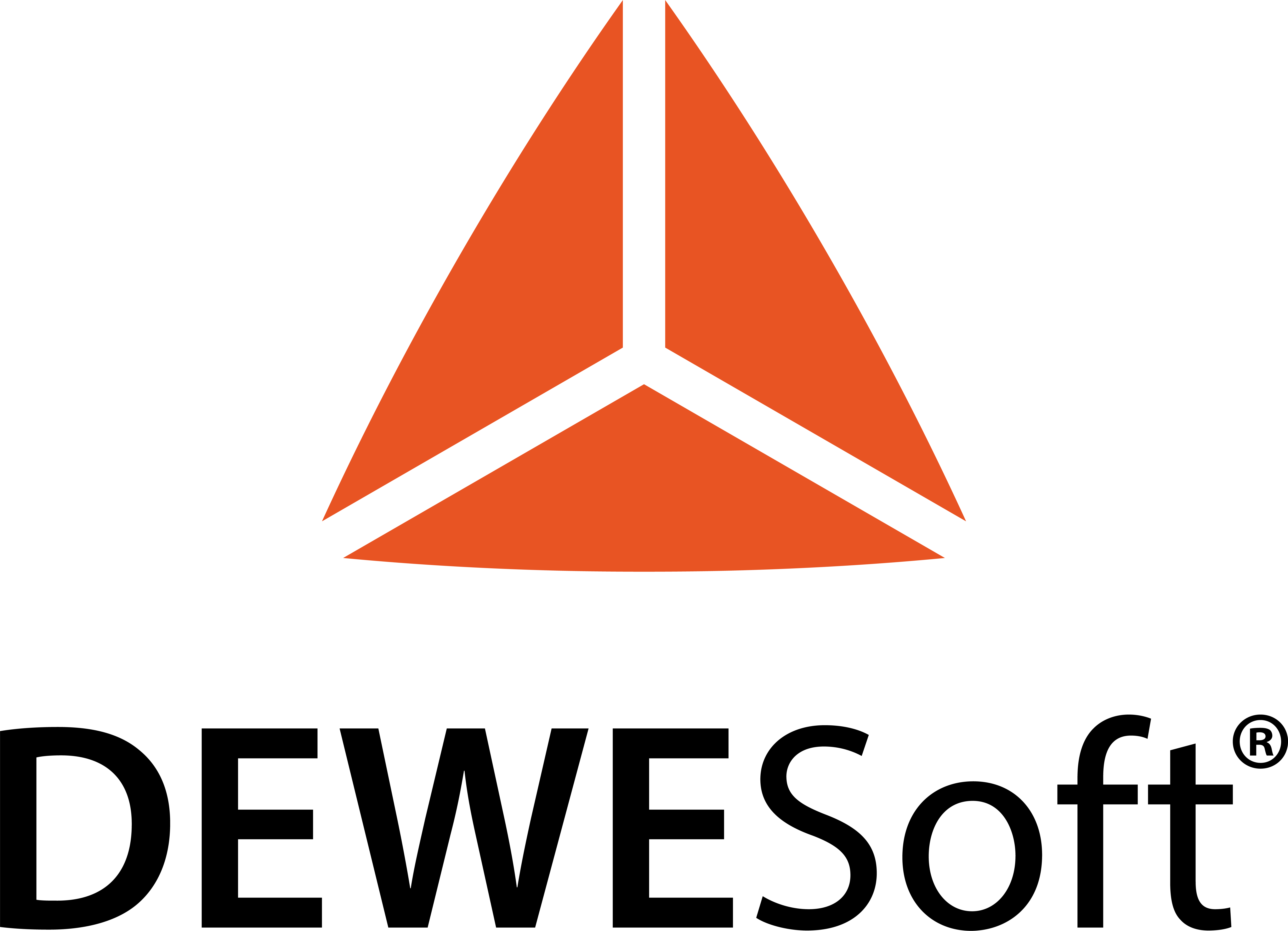
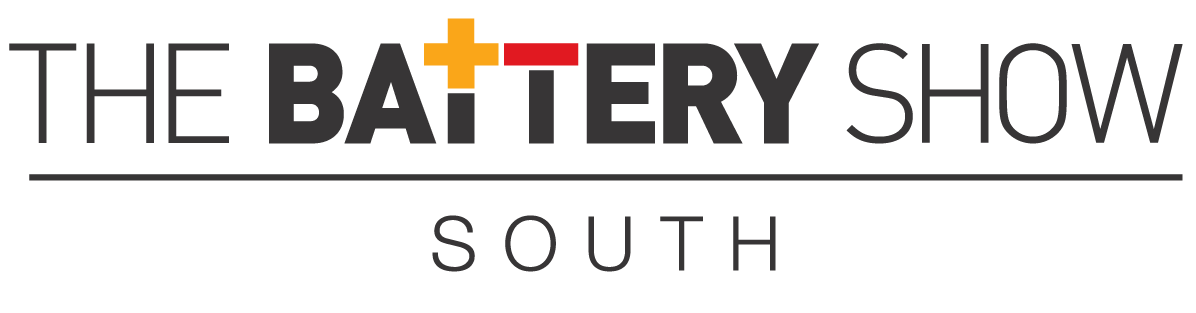
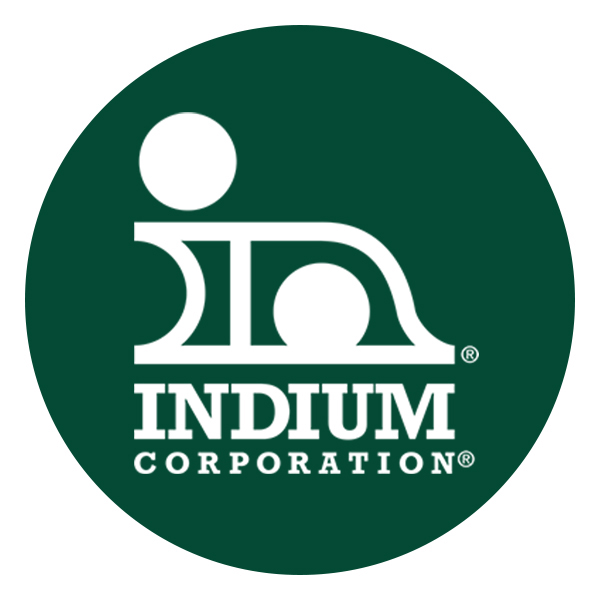
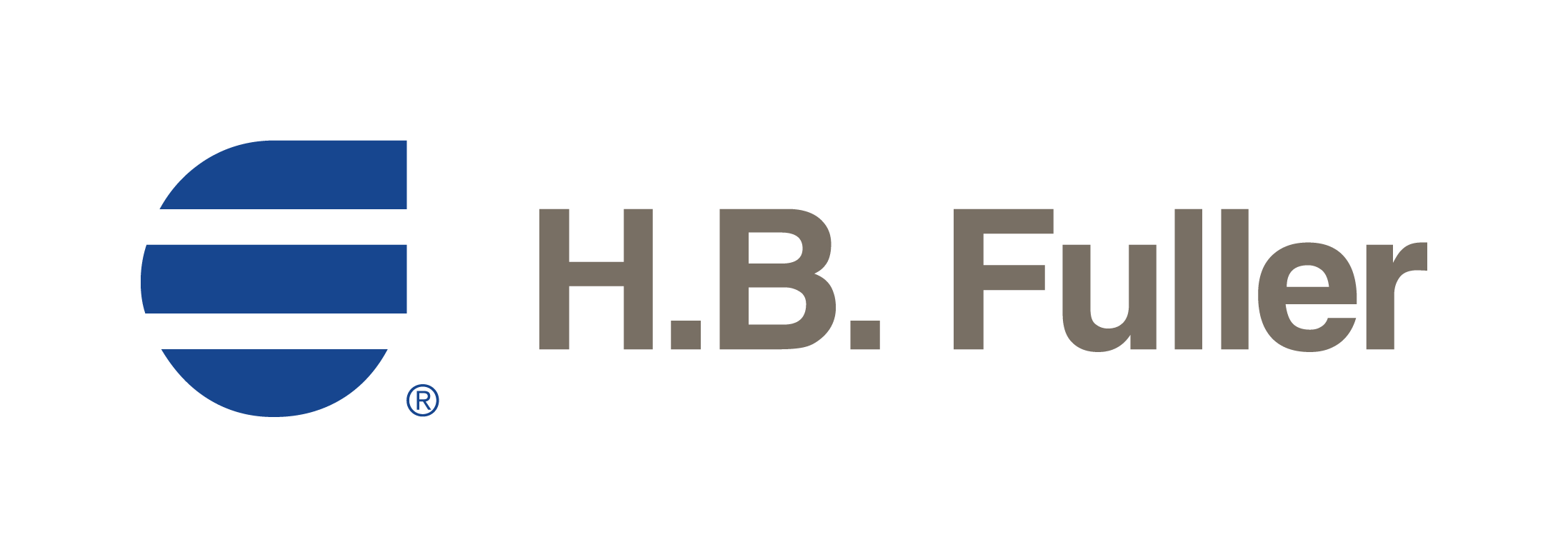