Airbus discusses role of hybridisation in aviation’s future
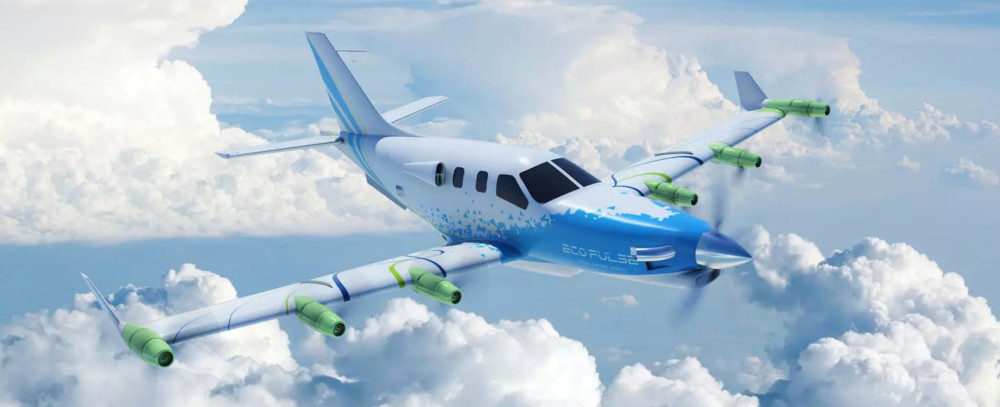
(Courtesy of Airbus)
Airbus says it believes hybrid-electric power can reduce aircraft CO2 emissions by up to 5%, and by up to 10% for helicopters.
It has already flight tested a hybrid-electric system that takes over from the thermal engine should it fail. Its Engine Back-up System is the forerunner of larger hybrid propulsion systems that will be tested at a later stage, using a demonstrator rotorcraft.
Also under development is Ecopulse, the result of a collaboration between Airbus, Daher and Safran. Based on a light aircraft demonstrator, it uses a lightweight, compact high voltage lithium-ion battery developed by Airbus Defence and Space.
However, reaching the 5% CO2 reduction target has prompted Airbus and engine manufacturers to jointly develop a more efficient class of gas turbine. To that end, Airbus has initiated a number of projects to demonstrate different hybrid engine concepts with varying power levels.
Deciding which type of electric motor will support them is also important though, it says. For hybrid-electric aircraft, the choice is between two architectures: serial and parallel.
In a serial architecture, a single mechanical power source drives the propeller or fan. Batteries aren’t the only power source – alternatives include hydrogen fuel cells – but the propeller is always driven by an electric motor, enabling distributed propulsion.
As far as hybridisation is concerned, that is serial architecture’s biggest advantage, but it means adding weight in the shape of a generator, to convert the mechanical power into electrical power.
In a parallel architecture, the gas turbine sometimes operates below peak efficiency. However, a smaller and lighter electric motor is enough to meet requirements, so a parallel architecture is better suited to hybrid applications.
As for the battery that powers the motor, the main shortcoming of current-generation batteries is their low energy density compared to kerosene and hydrogen. For instance, the density of the lithium-ion batteries widely used by the automotive sector reaches around 200 Wh/kg; kerosene’s energy density is some 50 times higher.
A compromise therefore has to be found between performance, volume and mass in an aircraft’s weight-sensitive, aerodynamically optimised environment, and Airbus says the holy grail is the solid-state battery.
Unlike the liquid electrolytes found in lithium-Ion batteries, ‘solid’ electrolytes mitigate the risk of thermal runaway. The risk remains, but the consequences are far less severe, making it easier to design a safe battery system.
Mitigating thermal runaway also makes the battery design simpler. Fewer parts are needed to ‘dress’ its cells, which has a positive impact on weight.
Whatever the technology though, batteries need to be charged. For commercial aviation, two options are swapping depleted units for new ones on the ground, or installing charge points at the gate, potentially using renewable energy. The latter requires investment in infrastructure, but in the long term that would be offset by fuel savings.
Alternatively, where ground infrastructure is lacking, the aircraft’s engines could recharge the batteries during the cruise phase of a flight. Airbus says the reality could well be a mix of all three, depending on the individual airline and airport choices.
ONLINE PARTNERS
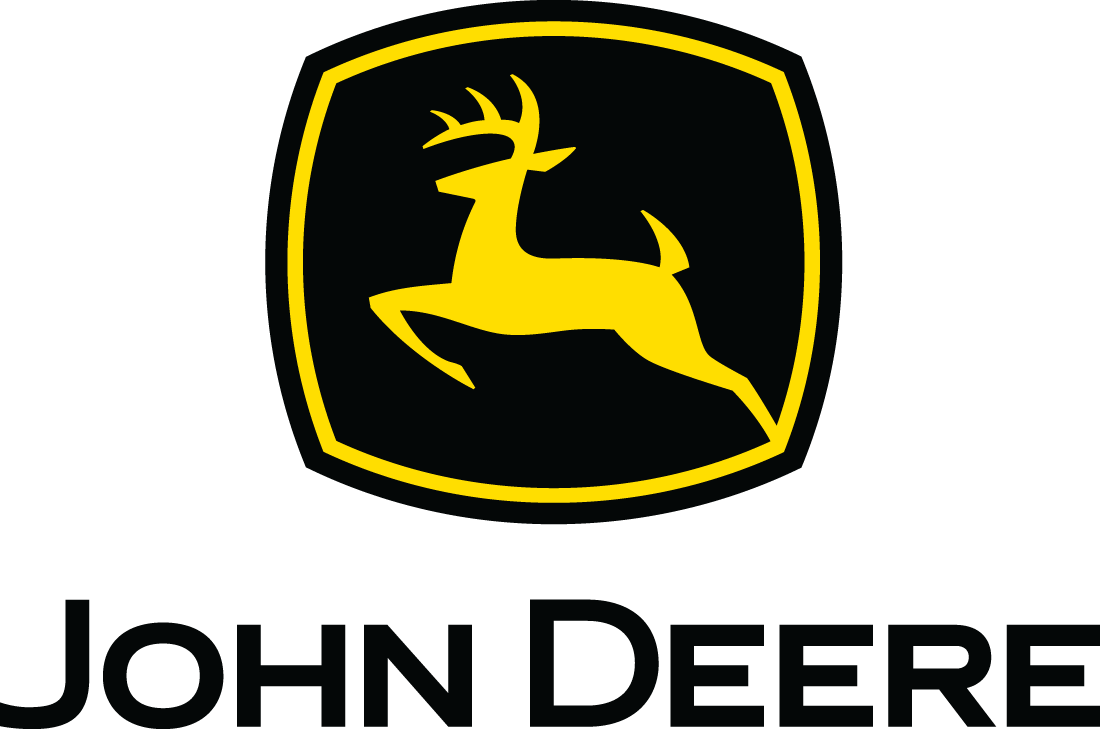
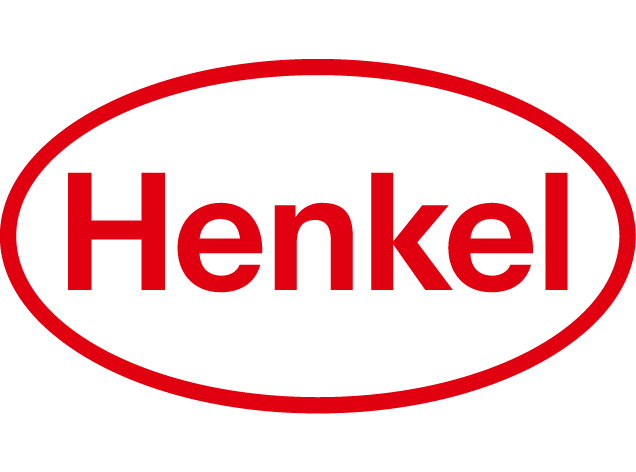
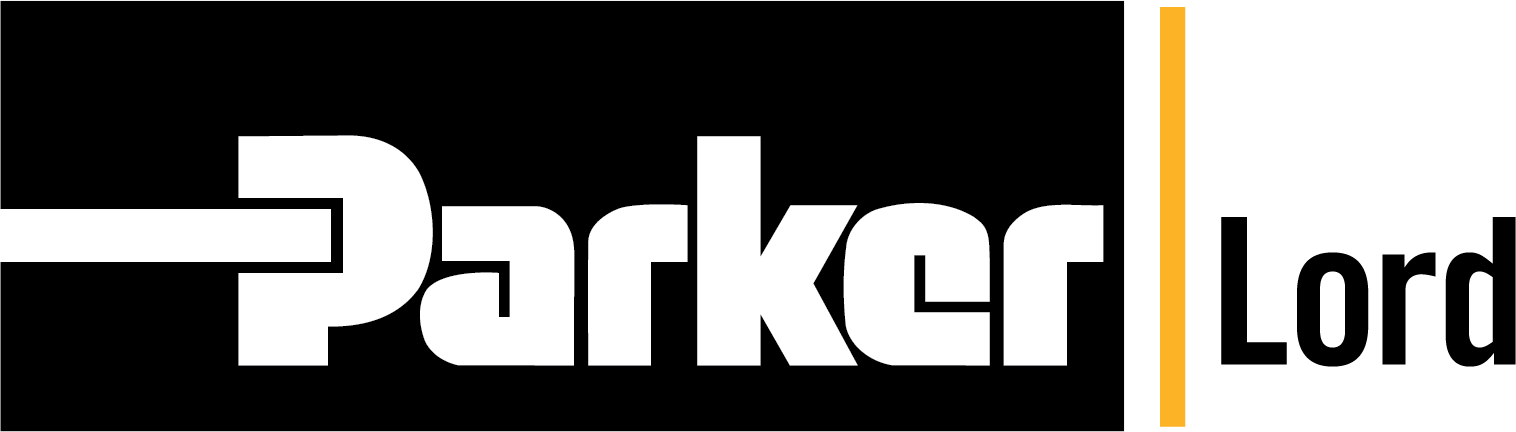
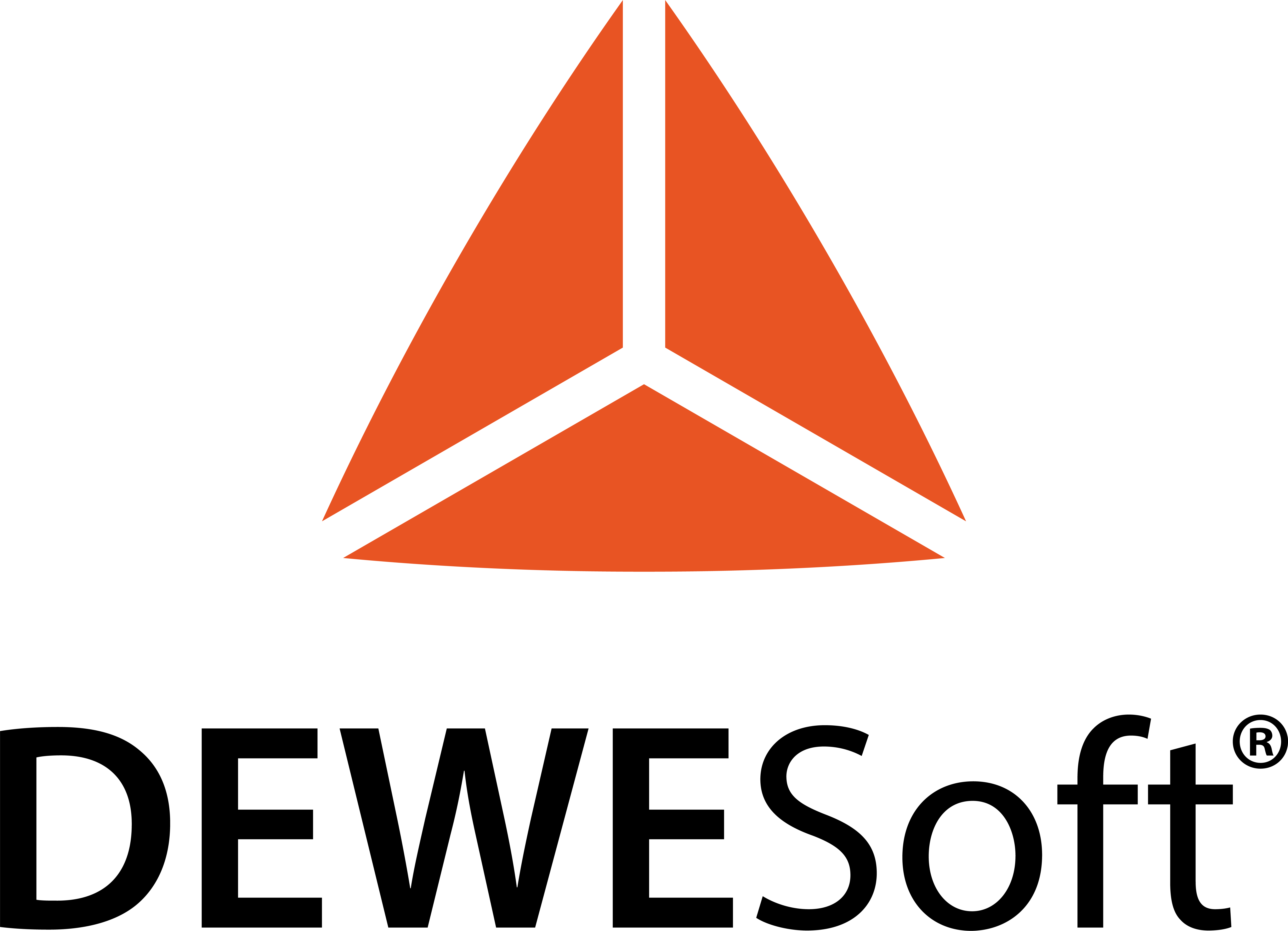
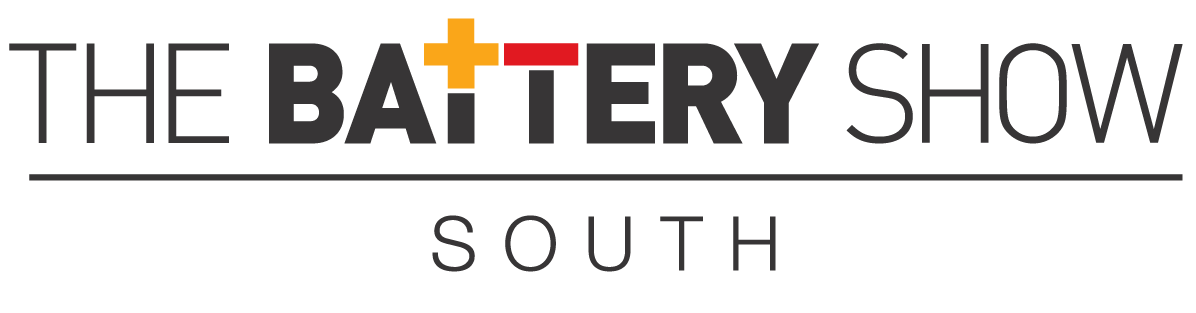
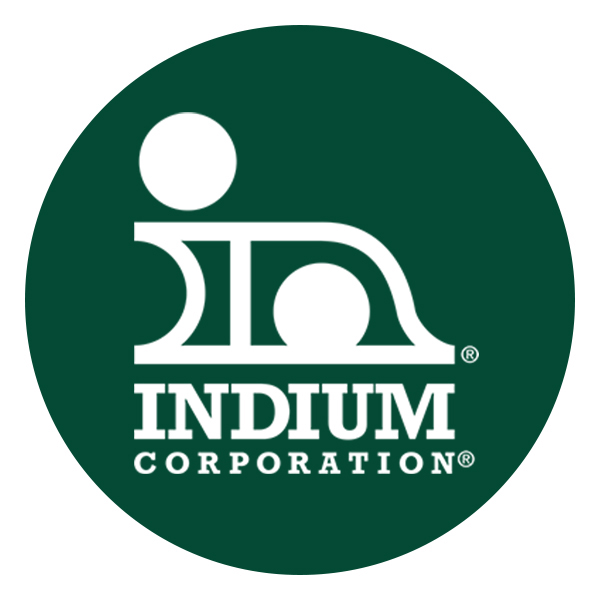
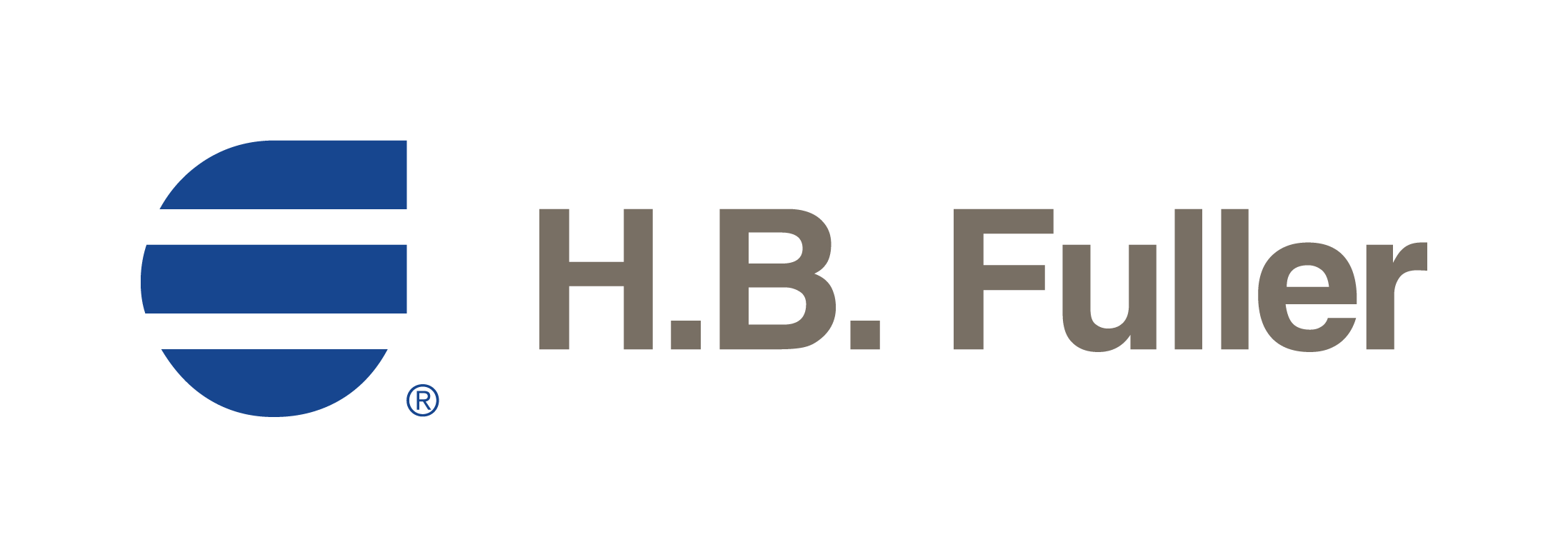