A case of plastic over aluminium
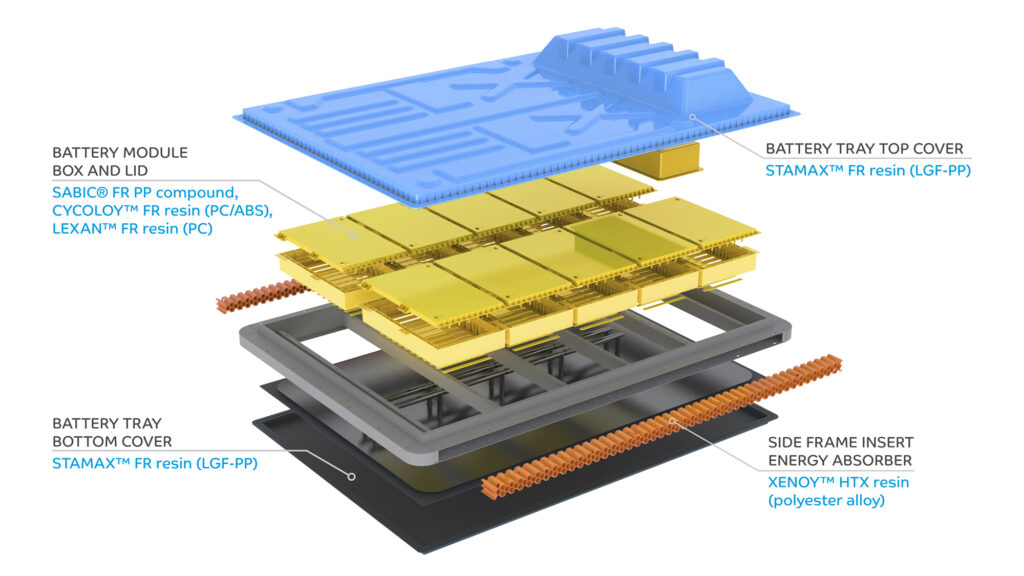
(Courtesy of SABIC)
Containing thermal runaway, protecting EV occupants from fire and saving weight are all drivers for the application of new materials to batteries, and the battery case is a prime target for replacing aluminium alloy with plastics (writes Peter Donaldson).
Multi-industry plastics specialist SABIC has recently re-engineered existing EV battery cases in two proof-of-concept exercises that showed benefits in these areas. The first subject of this work was the Jaguar I-Pace battery pack, which SABIC redesigned using glass-reinforced polypropylene (PP).
“We then fully costed it out and did a computer analysis to assess its crashworthiness,” says Dave Sullivan, senior manager, vehicle electrification marketing for the Americas at SABIC. “We determined that we can definitely take a complete battery case and convert it to plastic.”
The next step was to take a Volkswagen ID4 and remove the battery pack. SABIC then brought in manufacturing consultancy Munro & Associates and worked with key industry players to figure out how to make a better case. “We held a workshop with suppliers including machinery manufacturer Engel, materials specialist Henkel, moulding companies, Tier 1 automotive suppliers and OEMs,” Sullivan says.
With all the cell-containing modules installed, the original ID4 pack weighed 489 kg. “We tried to come up with crazy ideas of how to make this all-aluminium case lighter, safer and stronger out of plastic,” he says.
When they ran all their selected ideas through a computer simulation, he adds, the weight came out at a little less than 427 kg, most of which (around 370 kg) was in the modules rather than the case.
SABIC and Munro built mock-ups of the case in foam and wood to demonstrate some of their ideas, which led to a 3D-printed model representing a case into which the ID4 pack’s existing modules and busbars could be integrated.
One idea that emerged from this process was to replace the large aluminium cold plate that spans the bottom of the battery tray with a plastic equivalent. Sullivan says the conventional wisdom held that this would not work because aluminium conducts heat much better than plastics do.
The solution, he explains, was to bring the modules into contact with the liquid coolant. “We can take a module, place it directly on the cooling channels, and seal around the module,” he says.
While getting rid of the aluminium saved most of the weight, there were additional savings to come from the direct cooling concept. “There were probably 20 lb of thermal interface material underneath the modules just to get the heat from the modules into the cooling medium,” Sullivan says. “We can get rid of that if we do direct cooling, so we have been working with suppliers to come up with the proper adhesive.”
The next step was to make tools for compression moulding the ID4 battery case in fire-retardant Stamax glass-reinforced PP. This comes in the form of 15 mm-long PP pellets with a proprietary fire-retardant additive mixed in. The reinforcement is in the form of a bundle of short glass strands enclosed by the PP. The glass strands make up about 30% of each pellet.
In tests, a flame at 1100 C blew a hole in a standard 1.5 mm-thick aluminium battery cover in a few moments, but a 2.6 mm sample of the Stamax PP formed into a representative section of battery case wall, which Sullivan showed the author at the Battery Show in Stuttgart, performed much better. “It survived for 5 minutes with a flame at 1100 C without burning through, and it retained its integrity,” he says.
Further, the geometry of the sample helped to confine the damage to a small area, while the side of the sample opposite to the side subjected to the flame did not get hotter than 200 C. Taken together, these properties mean the material is also suitable for use in thermal barriers between modules, Sullivan says.
ONLINE PARTNERS
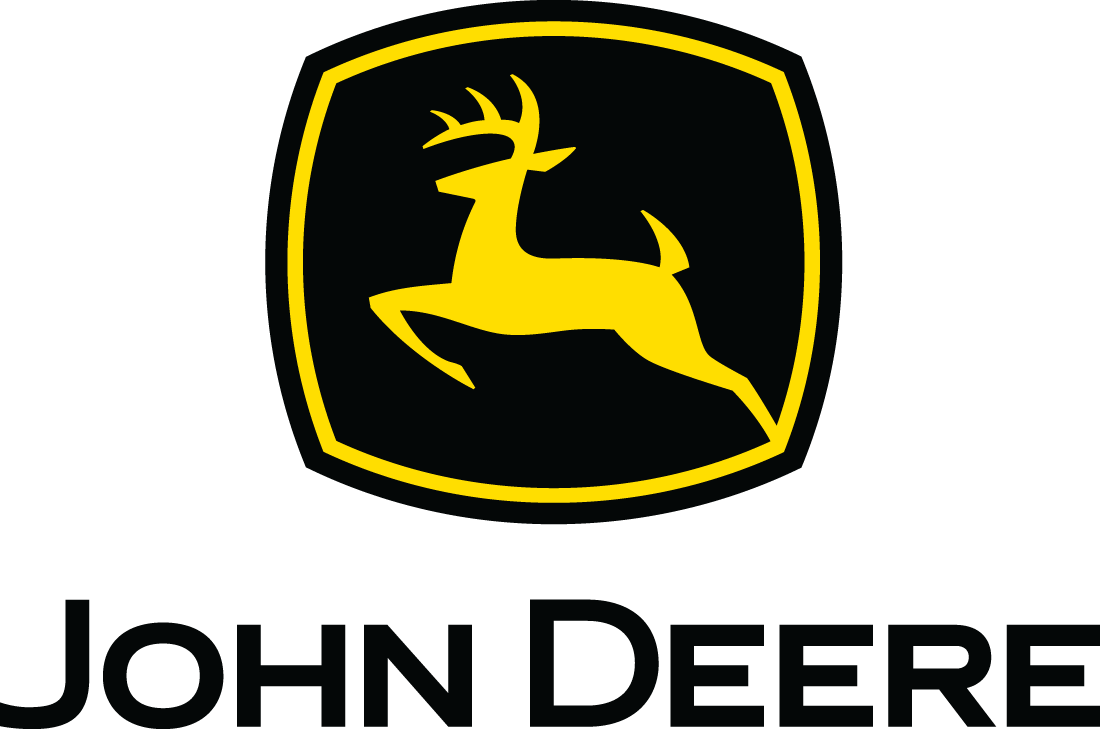
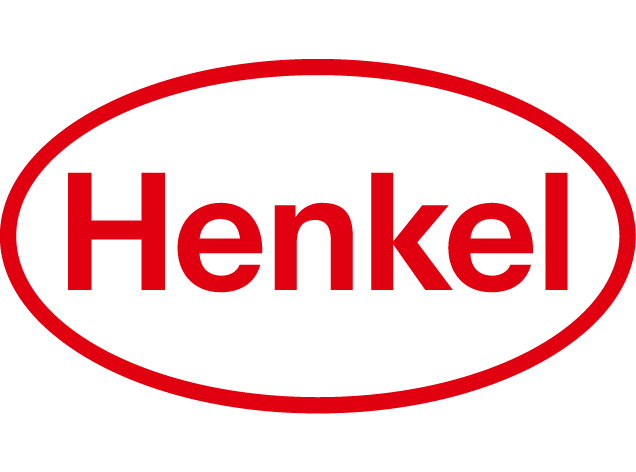
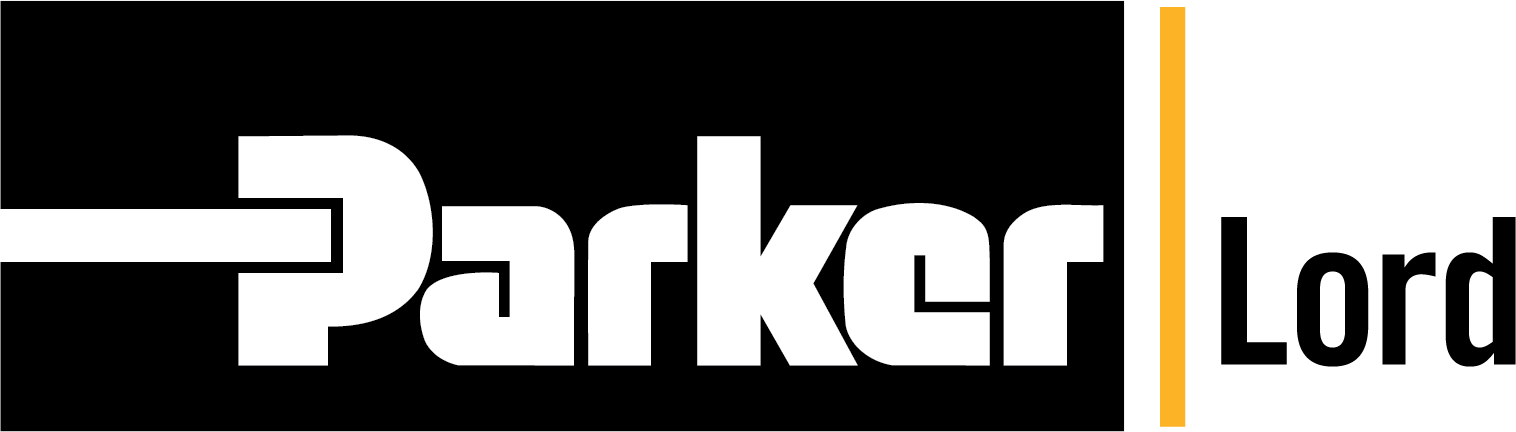
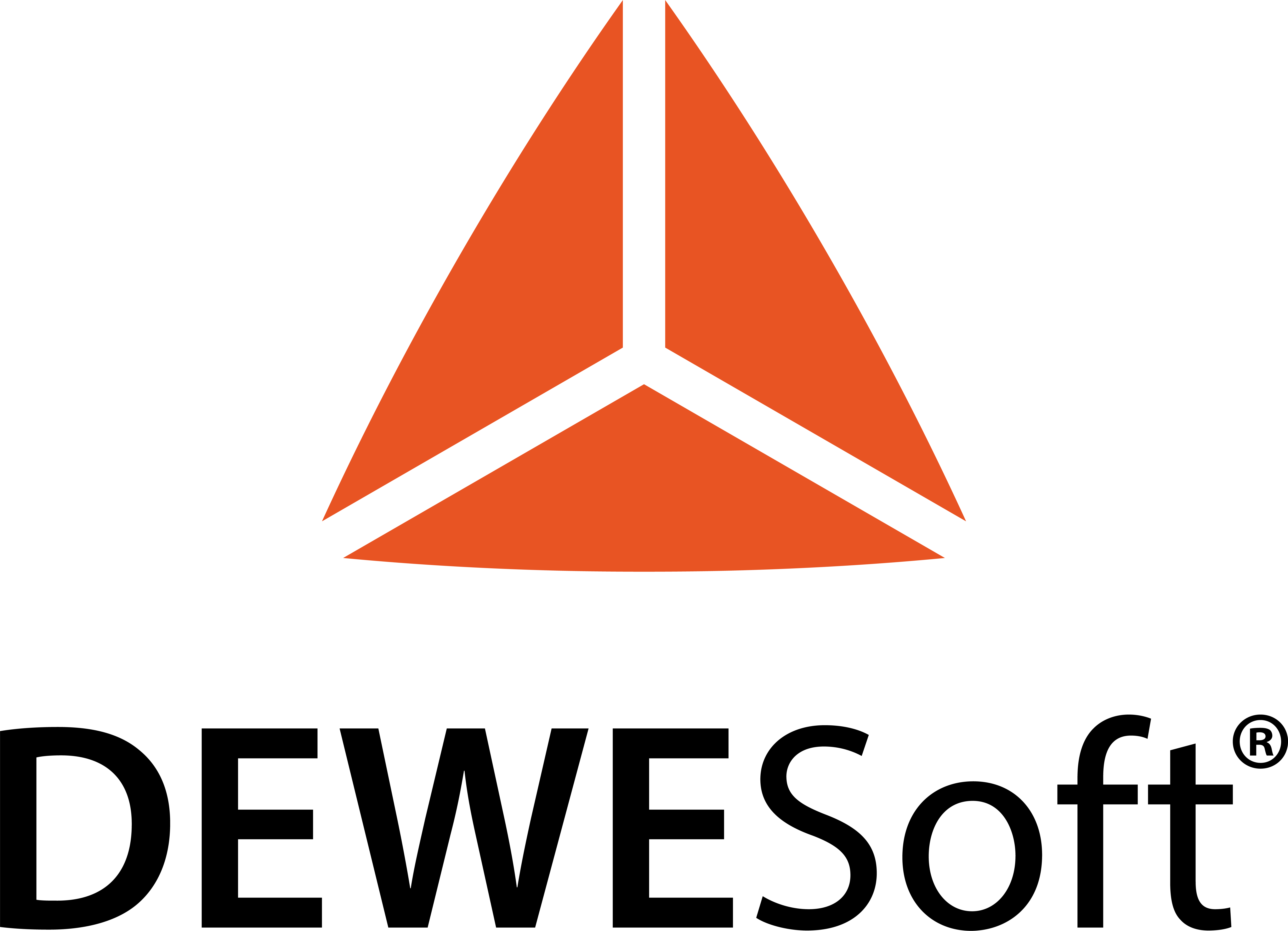
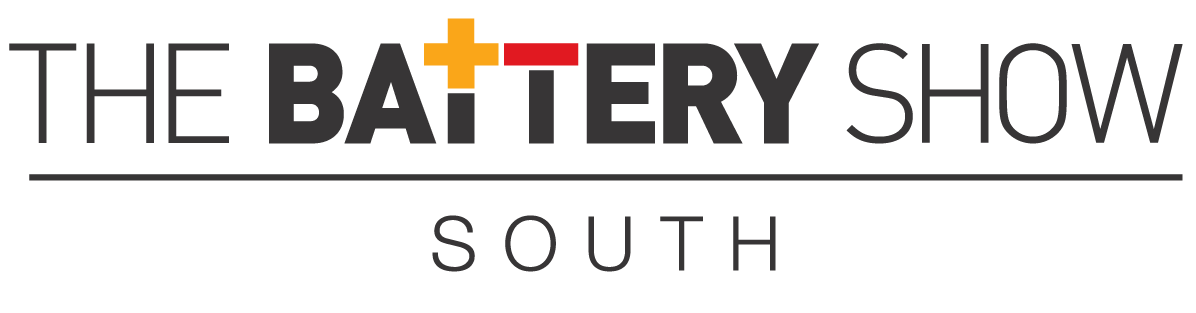
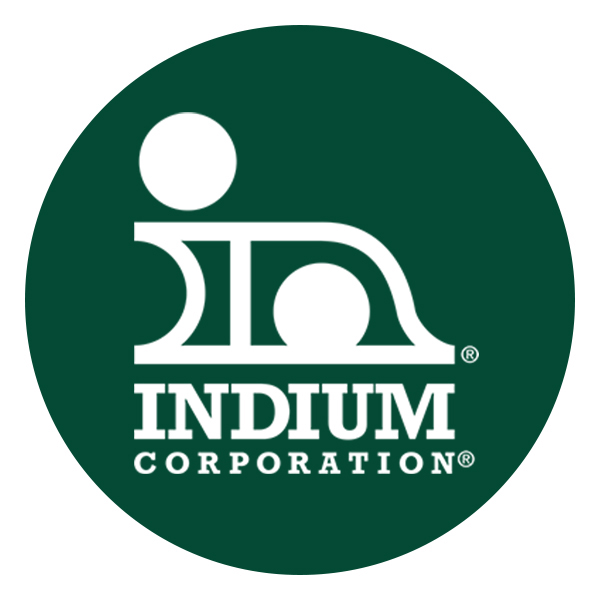
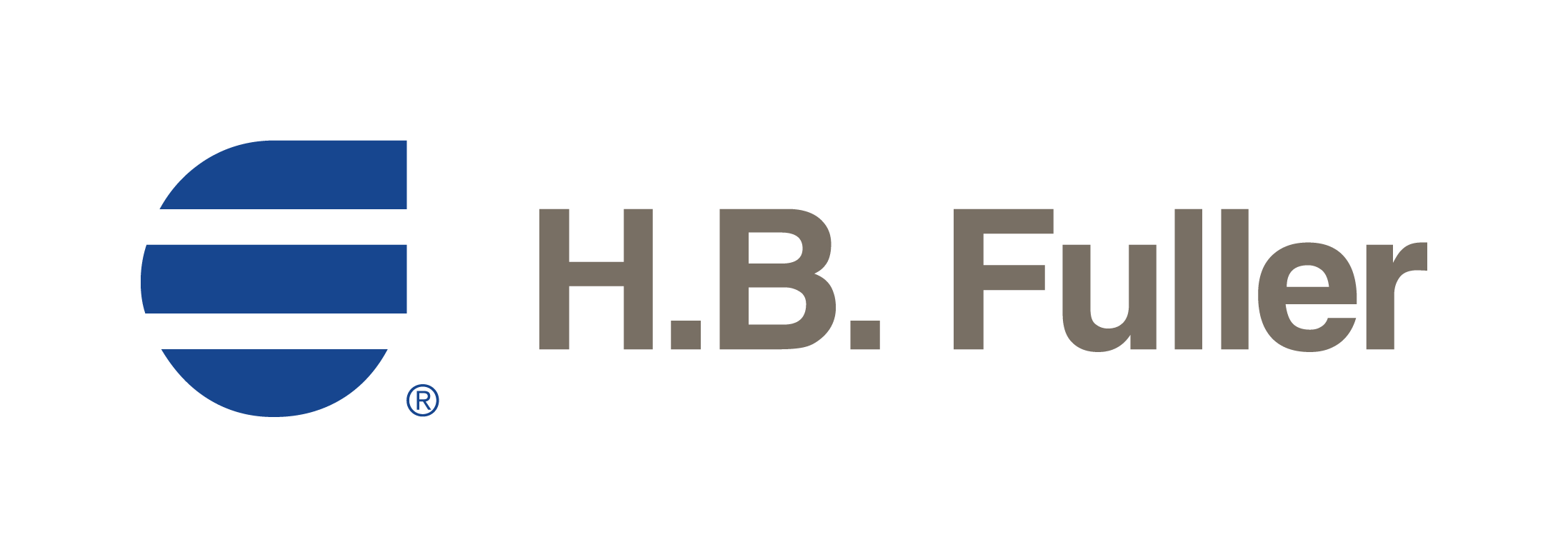