Ariel Hipercar
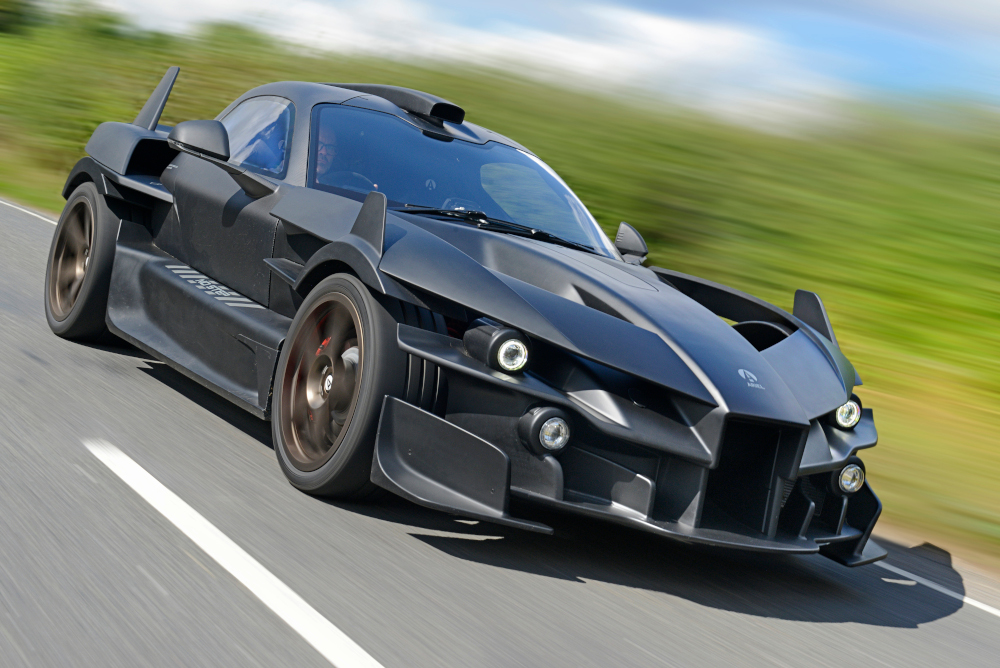
(Courtesy of Ariel Motor)
Fast forward
There’s more to this e-sportscar than its blistering acceleration, writes Peter Donaldson, it is also designed to advance EV technology
“High performance carbon reduction” is a statement of intent for niche sportscar manufacturer Ariel Motor. Contraction of the phrase yields Hipercar, the name of Ariel’s road-focused, track-capable EV designed to reach 60 mph in a little over 2 seconds, 100 mph in under 4 seconds and a top speed limited to 150 mph. Its CO2 reduction credentials come from its battery-electric powertrain that applies up to 1180 bhp (880 kW) and 1330 lb-ft (1800 Nm) of torque to propel the car’s 3300 lb (1500 kg) target mass, which is light for a BEV.
Dramatic though these numbers are, the Hipercar is more than a headline-grabber, it is a technology demonstrator and incubator intended to move the industry forward, particularly in the UK. It will also be a production car with a target price of just under £1 million.
“The project is not about Ariel making a sportscar; it’s about advancing the technology,” says Simon Saunders, Ariel Motor’s founder. For example, the traction motor developed for the Hipercar, by Equipmake, will also drive electric buses and coaches, and the battery technology is also going into other vehicles.
Simulations that generated the specifications for the battery revealed that the heat generated in going from extreme road use to track use would increase tenfold. The battery also had to be as light as possible, as performance through low weight rather than sheer brute force is central to Ariel’s philosophy, he explains.
Saunders emphasises that one of the overarching requirements for the car is that it must be practical to build. That means key components such as cells have been chosen because they are affordable and obtainable, not because they represent the latest technology.
Specifying the battery
Ariel’s battery partner for the Hipercar is Delta Cosworth, which is also developing the gas turbine range extender.
Simon Dowson, managing director at Delta Cosworth, recalls that Ariel approached its battery requirements by specifying the level of road and track performance it wanted from the car.
“The requirements were quite loose initially, but we narrowed them down by focusing on available technology, packaging space and weight targets, and then worked with Ariel on those things.”
Prioritising acceleration and speed over range drove the selection of the battery chemistry and the option of the range extender. “The battery is more focused on power than energy, but over the years that the vehicle has been in development we have seen an improvement in the power-energy balance of cells anyway,” he explains.
The battery is built from cylindrical 21700-format lithium iron phosphate cells, which represent a conservative choice.
“Through our cooling system and management of the battery we can extract the maximum performance from a fairly production-ready cell,” Dowson says. “Obviously we needed to end up with something that is not too exotic, otherwise the price point would be too high.”
Initially, Cosworth made two versions of the battery, one with 18650 cells and the other with 21700s, eventually choosing the latter as it emerged that the format offers a better power-energy balance.
The 62.5 kWh pack uses Cosworth’s Cylindrical Scalable Module (CSM) technology and provides a nominal voltage of 690 V, a maximum of 800 V and supplies a peak current of 1450 A.
CSM modules contain a carrier that holds the cells and what Dowson describes as a conduit cooling system in the form of a soft-walled tube that conforms to the shape of each cell from two sides as it fills with liquid coolant, making contact with as much of the cells’ surface area as possible to maximise heat transfer. This provides almost as much contact area as immersion cooling, but without the extra expense of a dielectric coolant and the mass of the extra liquid.
“And because of the way the modules are built up we’re able to control their temperature equally,” he says.
Heat on track
Giving the Hipercar’s battery the ability to stand up to track use is a thermal management issue that also affects the whole powertrain.
“You see it in any form of track environment; anyone who takes an EV on track knows that they don’t do many laps before they tell you to stop,” Dowson notes.
“You are balancing the size, weight and thermal management of the system for a track application, in particular for the battery. If you want it to give ultimate performance you might want to preheat it to get the cells up to a good operating temperature to minimise the internal resistance, then you need to maintain the temperature within a narrow window.”
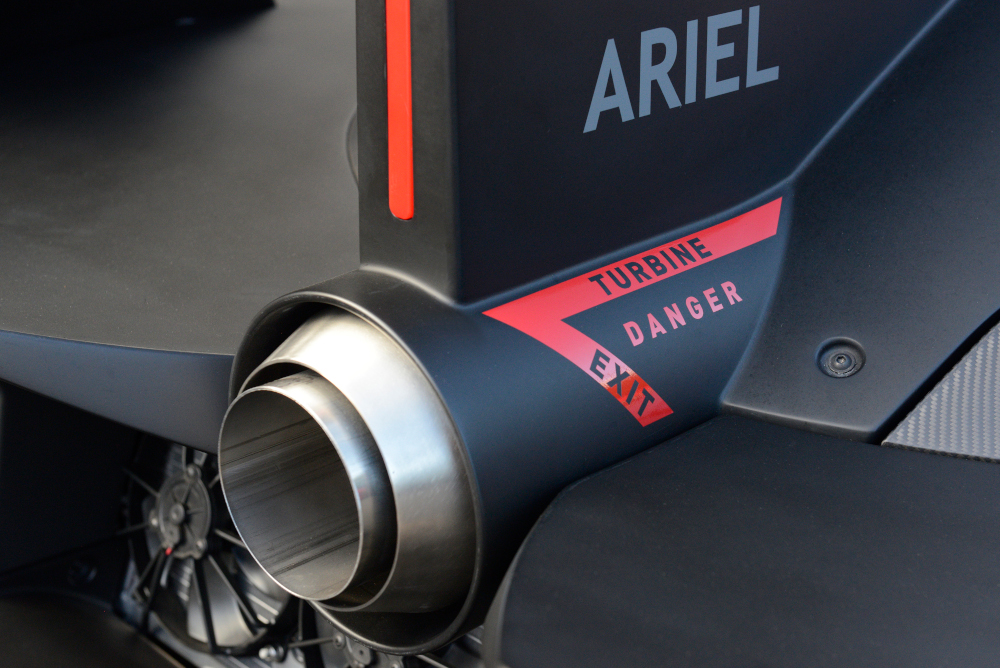
(Courtesy of Ariel Motor)
PTC heaters in the thermal management circuit heat the coolant to bring the cells up to temperature, using valving to bypass the radiators so that heat is not rejected unnecessarily, he explains.
The size, number and location of heat exchangers, however, are Ariel’s responsibility as the vehicle integrator.
“We gave them a heat rejection target,” Dowson says. “We have also given them some guidance because it is something we have a lot of experience of across the group.”
Designed to operate over an ambient temperature range of -20 to +45 ºC, the thermal management system is a multi-circuit heated and cooled water-glycol system that serves the cabin’s HVAC, battery pack, power electronics and drivetrain. Eight separate cooling circuits serve 10 systems.
In building the battery, Cosworth takes advantage of the CSM technology’s modularity to shape the pack to meet the vehicle’s weight distribution requirements.
“All the modules can be built in any length, so when there are shapes with which we have to conform we can adjust the lengths of the modules and stack them up,” Dowson explains.
“With Ariel, because they were developing the chassis from scratch, we were able to put all the modules on a flat baseplate. Then we just needed a raised section in the middle, which would traditionally be a transmission tunnel, to carry all the electrical distribution systems, contactors, fusing and so on.”
While minimising battery weight was extremely important, so was keeping the vehicle within the target price range, so Cosworth mostly avoided exotic materials. “We just have to do more simulation and finite element analysis [FEA] on the construction of the system to ensure we have got the right stiffness and weight balance,” Dowson says. “We use a little composite material in there, but we try to minimise that.”
The battery casing is made from HyLight, a material based on a patented bonded aluminium composite sandwich, which protects both battery and underbody from impact and puncture. Although the battery pack is solidly mounted to the chassis, it is not fully stressed.
Optimal battery management
Cosworth is also responsible for the BMS, which is the focus of considerable engineering effort.
“The main thing is that we populate the BMS with the knowledge that we have of the cell,” Dowson says. “So we characterised the cell and are able to set the limits, understand where the optimum performance is and ensure that the system operates within that window.
“Because it’s a prototype, we’ve got a lot of voltage and temperature sensing within the pack, just so we can see how far we can push it. As we go into volume production we will take some of that sensing out, because we will have more experience with the system.”
The conduit cooling system allows the battery to be pushed further than would otherwise be safe, but Dowson emphasises that the overall task is one of optimisation. “Everything we do is about optimising the system, downsizing and pursuing weight efficiency and performance targets in terms of power and energy,” he says.
That involves using the BMS to calculate the battery’s state of health and to work out its likely service life. Dowson says that is a challenge, because it is not clear how much time each individual car will spend on track, so Cosworth carries out extensive testing, typically at module level.
“We put them through a harsh duty cycle to generate state of health information over time,” he says. “Obviously this is important for Ariel when considering warranties and so on. We have a safety factor in there, so I think we are happy with where we are.”
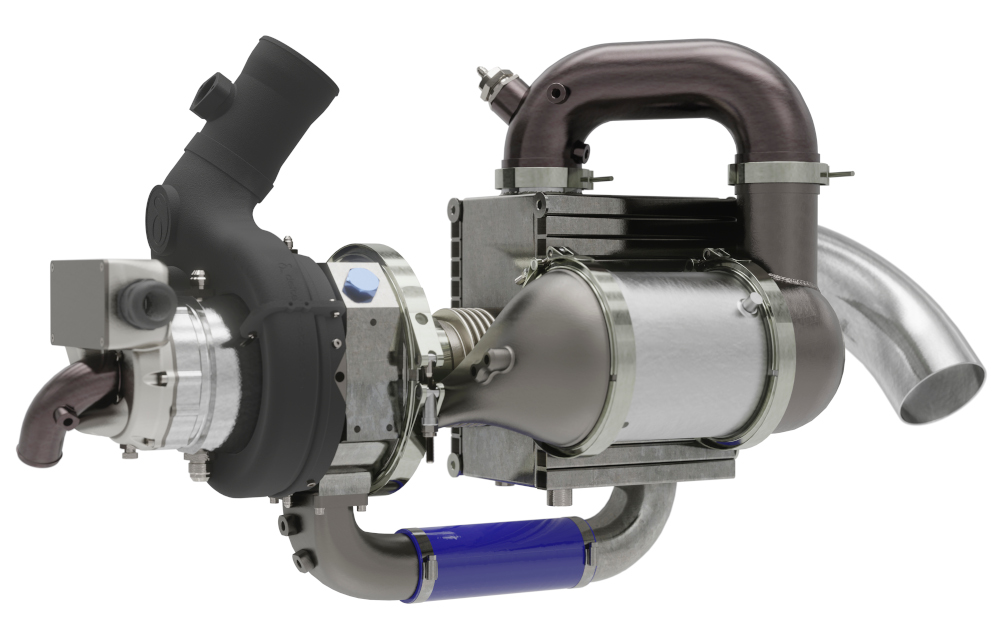
(Courtesy of Cosworth)
Simulation, FEA and physical testing are also crucial to other aspects of battery safety, such as the risk of pack penetration and thermal runaway.
“There are regulatory criteria in terms of possible ingress,” Dowson explains. “When you run over a stone at high speed for example and it fires into the baseplate, it is not allowed to penetrate, so we do a lot of FEA-based simulation work on that.
“In terms of thermal propagation we perform physical testing. We will encourage a cell to go into thermal runaway at our test facility, then manage that runaway within the module construction and the pack.
“The first line of defence is to sense that you have an unhappy cell or group of cells, and you start looking at how to shut the system down. If that thermal runaway continues, we have to look at what happens then, whether we can limit it to one cell and work out what damage one cell might do to the rest of the system.”
While Cosworth is happy with the results of that work, Dowson points out that such testing is an ongoing process, as the car is likely to go into production with new 21700 cells with a different chemistry that offers a better power-energy balance.
“That will require a lot more characterisation testing. The temperature window the new cell operates in can vary, and what happens in thermal runaway changes,” he says.
Catalytic range extender
Although it is an option, the 35 kW gas turbine range extender had a profound effect on the Hipercar’s powertrain because it allowed the battery chemistry to be weighted more towards power density than energy density. It also allowed the pack to be smaller and lighter without sacrificing too much range, although its contribution to the car’s performance on track is limited.
“At the beginning of the project we ran lots of simulations, ranging from the WLTP cycle through to track use,” Saunders explains. “One of them we called – and this is the polite version – ‘driving stupidly on the road’. The range extender will keep up with that all day, but take it onto the track and it will not keep up with the power demands of the battery.
“We can probably do 20 minutes on track before the car needs charging. Then you could leave the range extender running for 45 minutes and it will have the battery back to a useful state of charge again, but it is not designed to drive around a track all day. We decided it needed a track capability to measure its performance against petrol-driven cars.”
Although the range extender is a gas turbine, it is not a conventional one. Delta Cosworth calls the device its Catalytic Generator (Cat Gen), because the exothermic chemical reaction between the fuel and the air is promoted by a catalyst rather than being ignited by a spark and sustained by the continuous flame, as happens in a conventional gas turbine. Johnson Matthey supplies the catalyst.
To start the turbine, an electric motor spins the compressor, shaft and turbine up to 30,000 rpm, an electric heater brings the catalyst up to temperature and the fuel is injected. With the reaction under way, the machine spins up to a steady 110,000 rpm.
At the moment, the Cat Gen runs on petrol, but Delta Cosworth notes that using it as a battery charger allows it to run at an optimised speed and load, and that the catalytic reaction can be controlled very precisely. Together, these factors ensure that emissions are reduced to “negligible levels” without after-treatment.
The device will run on any liquid or gaseous fuel, but in the long term the intention is to run it on hydrogen, when the Hipercar will qualify as a zero-emissions vehicle.
The Cat Gen’s 35 kW is a continuous rating, while the core hardware weighs 50 kg and the coupled DC generator can supply current at a wide range of voltages.
Ariel claims a range of 150 miles on the WLTP cycle, and more with use of the range extender, which can be switched on and off manually or automatically under the control of the BMS.
The car can also be charged from existing home or public infrastructure. Compatible with CHAdeMO and Type 2 hardware, the split charging system enables the car to use infrastructure designed for less than 500 V while being ready for 800 V infrastructure when it arrives, says the company.
Bespoke spoke motors
While rear-wheel drive is an option, the Hipercar prototype is fitted with four custom-designed 220 kW APM-200 interior permanent magnet radial flux spoke motors from Equipmake.
Mounted inboard and spinning at up to 10,000 rpm, each motor has an integrated inverter and single-stage 5.43:1 epicyclic reduction gearbox producing a maximum output speed of 1842 rpm. The motor weighs 40 kg, its reduction gearbox 9 kg and the inverter adds 12 kg.
In a spoke motor, the magnets are arranged like the spokes of a wheel, explains Ian Foley, Equipmake’s founder and managing director.
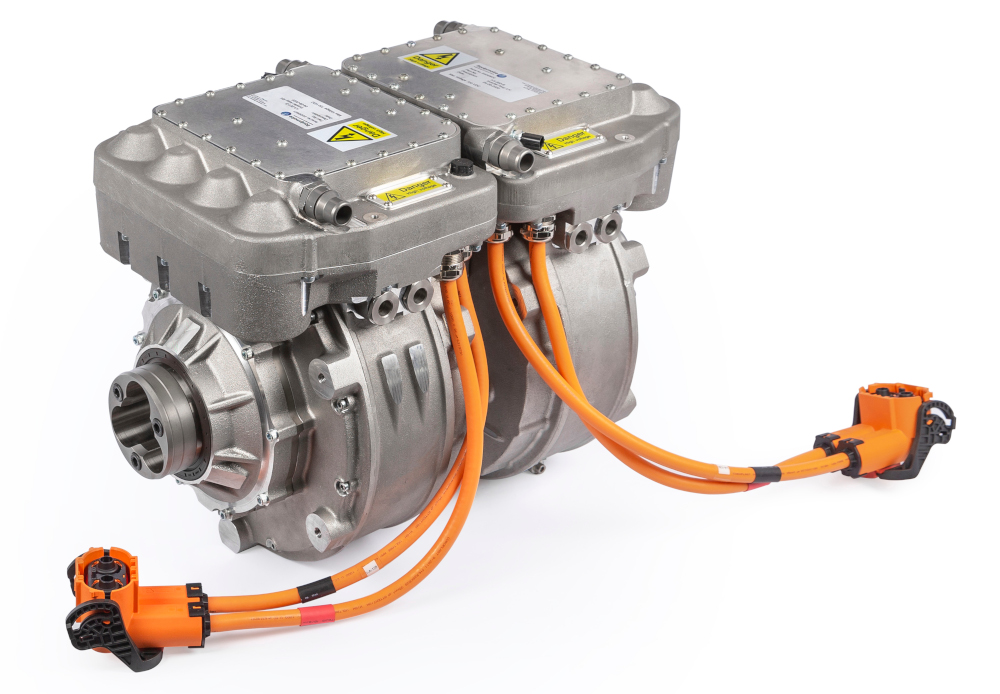
(Courtesy of Equipmake)
“It’s an architecture known to give the highest combination of torque and power density, and we believe our motor is of comparable torque density to the best axial flux motors,” he says.
He explains that while the magnets in a conventional radial flux motor tend to be arranged in vee shapes around the rotor, the magnets in a spoke motor are “vertical”, lining up radially around the rotor. The flux comes out of either side of each magnet and then through the laminations of the rotor.
“The flux path is radial, but the way the flux is generated by the magnet arrangement is different and gives what we believe is a better use of the flux,” he says.
He adds that the design benefits from the more established techniques for manufacturing radial flux motors, and that the architecture makes it easier to get liquid coolant under the base of each magnet, allowing the motor to achieve higher continuous power without overheating.
The integral inverter developed to drive the APM-200 is the HPI-450, which incorporates IGBT power electronics. However, it is also available with silicon carbide diode technology combined with IGBTs to improve its power transmission and enable it to run at high switching frequencies. Designed to run at 750 V DC, it has a peak current rating of 450 A rms.
In its current state of development, the Hipercar has adjustable traction control, while the production car will feature adjustable torque vectoring, enabling the motors to drive the wheels at different speeds to further improve cornering performance.
The motors also serve as a regenerative braking system, both to improve the Hipercar’s energy efficiency and to add an extra element of driver involvement, as the level of regen is adjustable with paddles on the steering wheel, and can be turned off.
Structure and bodywork
The Hipercar has an aluminium alloy chassis, which Ariel describes as a laser-cut and CNC-folded, bonded aluminium monocoque. Attached to the front and rear of the chassis are aluminium subframes that serve as crush structures and suspension mounting points.
While the production version will have bodywork moulded completely from carbon fibre-reinforced plastic, the prototype uses several 3D-printed panels, particularly at the front, to allow for rapid design changes without having to replace expensive moulds.
Saunders adds that the car is around 200 kg overweight because of the 3D-printed panels, so on that basis the production Hipercar should accelerate even harder than the prototype, aided by further weight reduction from the use of carbon fibre wheels in place of the forged alloy items.
“If we just replaced everything with carbon we would be just over 1500 kg,” he says. “So we want to get it under 1500 kg, which for this sort of car is light.”
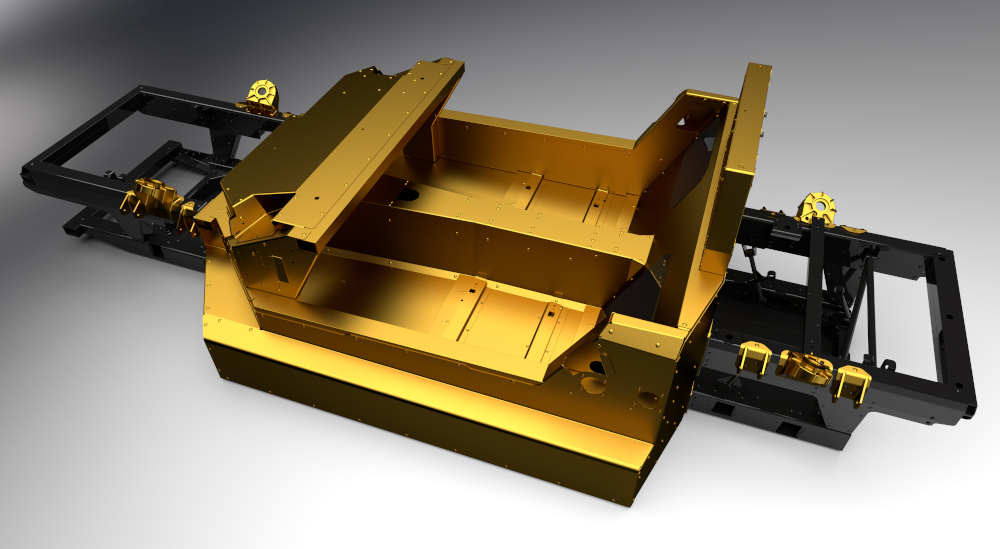
(Courtesy of Ariel Motor)
Aerodynamics have shaped the body to balance drag reduction against downforce, stability and thermal management, and Ariel has worked closely with TotalSim to develop the Bramble computational fluid dynamics system used to help design the car’s aero.
Air is channelled over, under and through the bodywork with, for example, two large heat exchangers for the thermal management system and four fans prominent across the rear. Other examples include the fins on the front wings that reduce drag on the mirrors, the roof scoop that supplies air to the Cat Gen and the Le Mans Prototype-style central fin and the ‘shark fins’ on the rear wings to aid stability and cornering.
Testing remains a central part of the development programme, and has encompassed WLTP and abuse tests, thousands of simulated laps on race circuits, plus sessions in climate chambers, shaker rigs, noise, vibration and harshness and electromagnetic compatibility testing. Aerial has also worked on multiple computer simulations, cooperating with TotalSim to refine the aerodynamics and on both FEA and safety with Tecosim.
“We probably have another a year or two before the car is ready for sale,” Saunders says. “There is a lot of detail development, testing, reliability and endurance testing still to do.”
ONLINE PARTNERS
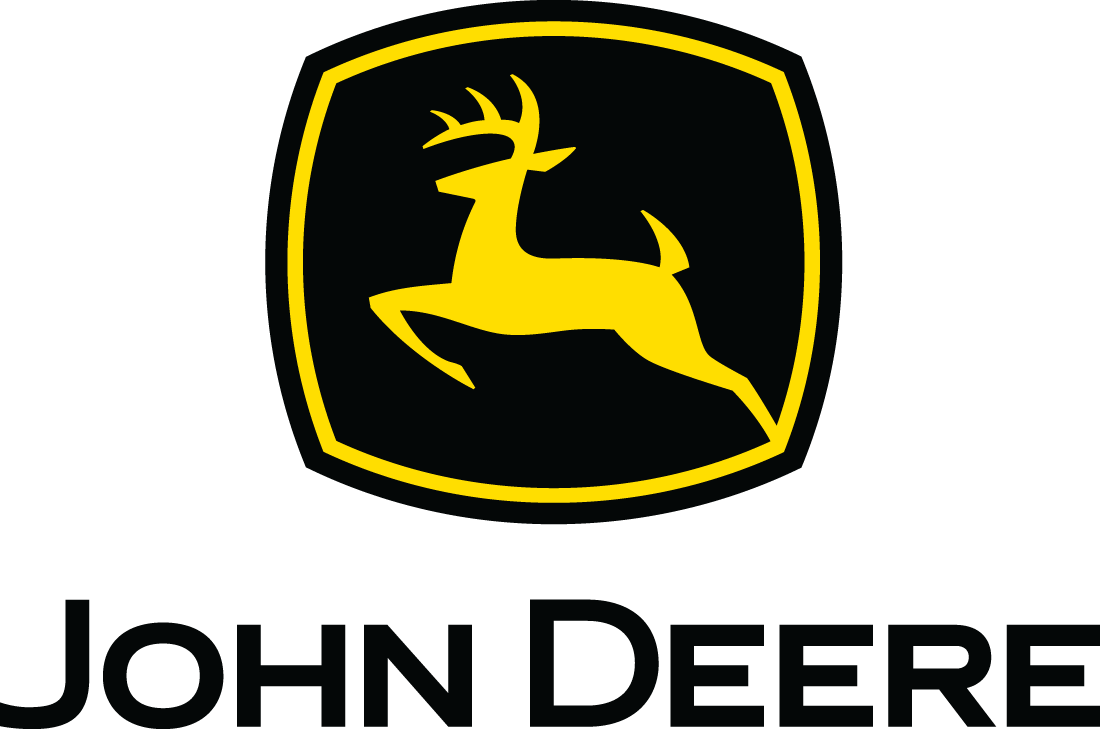
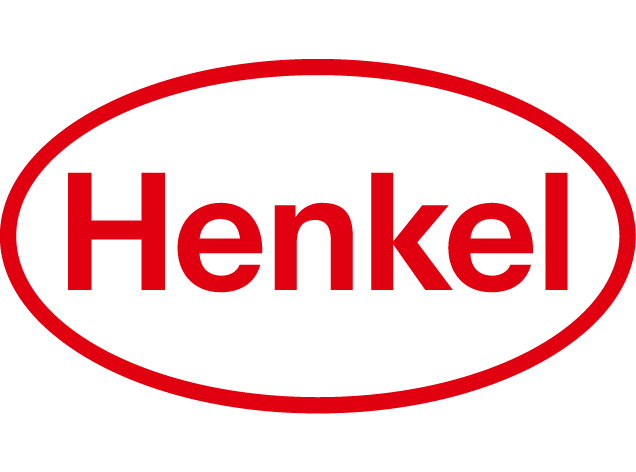
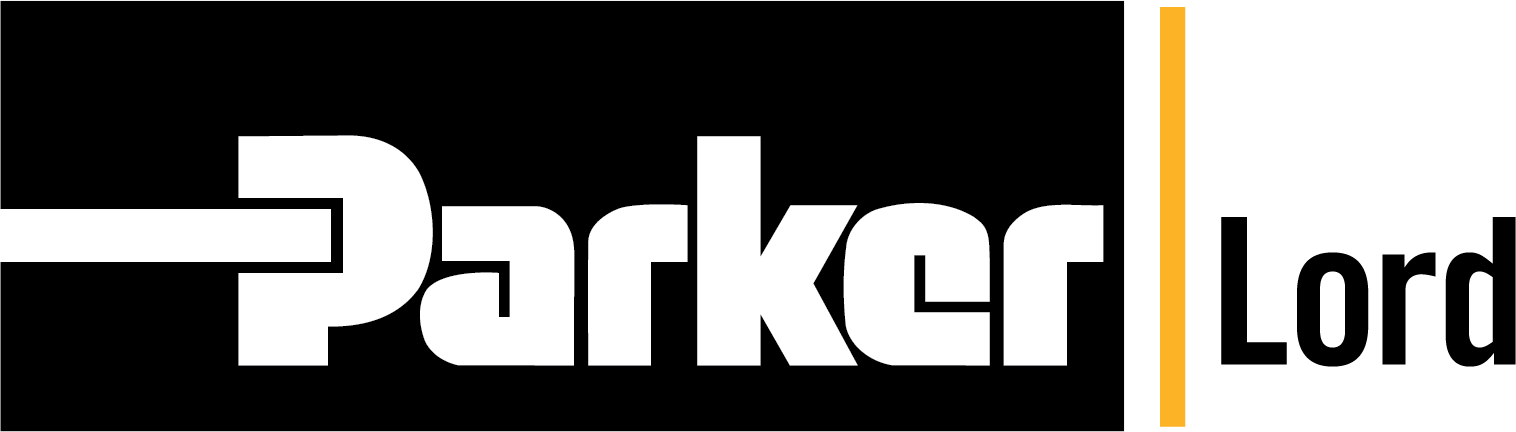
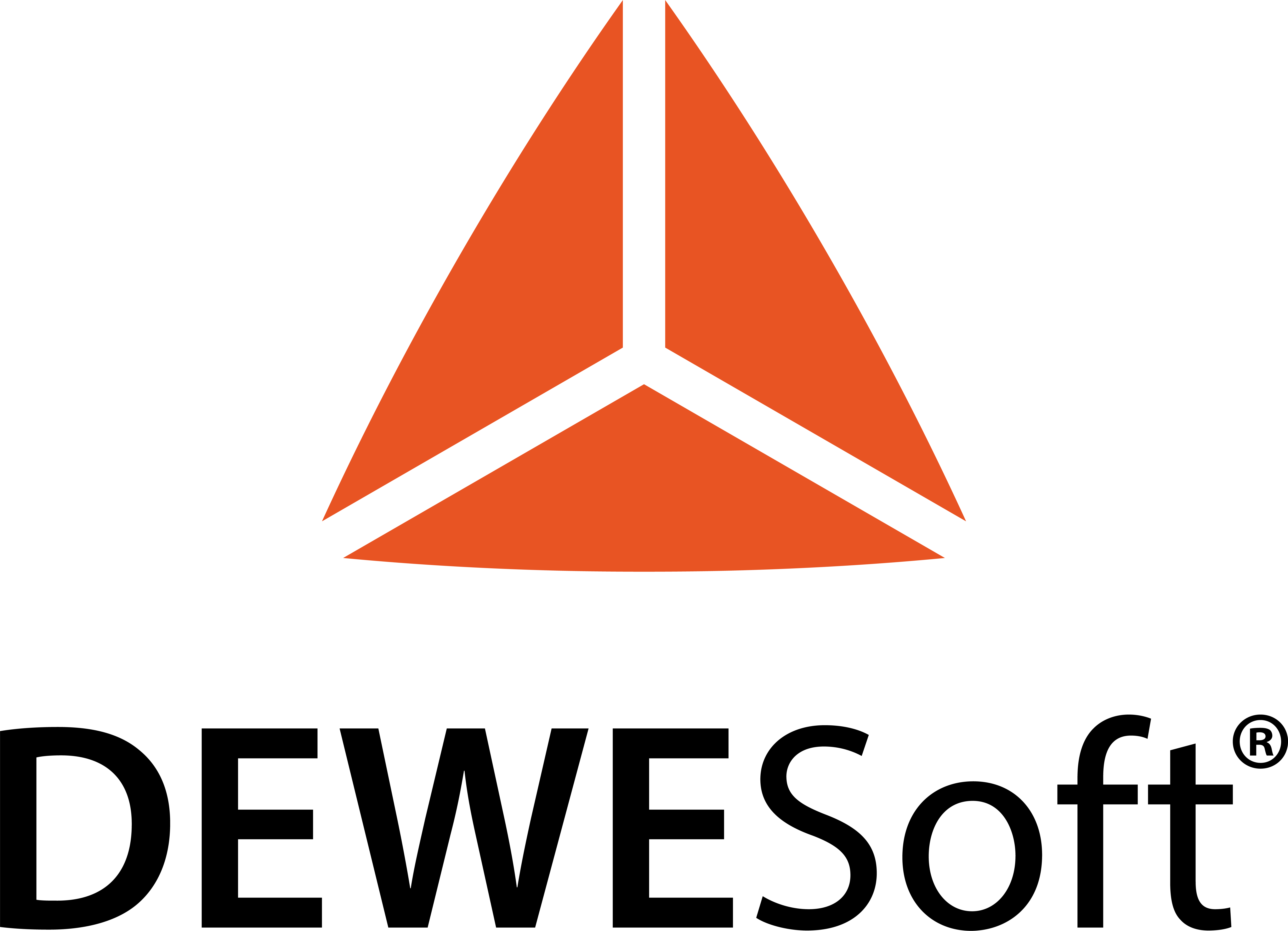
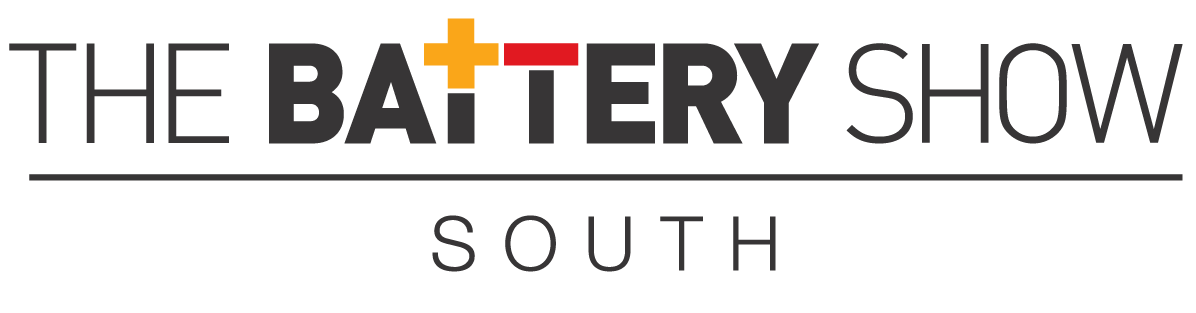
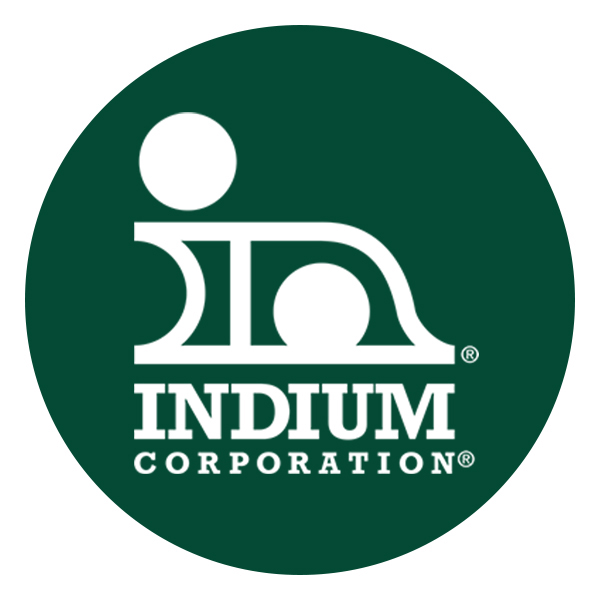

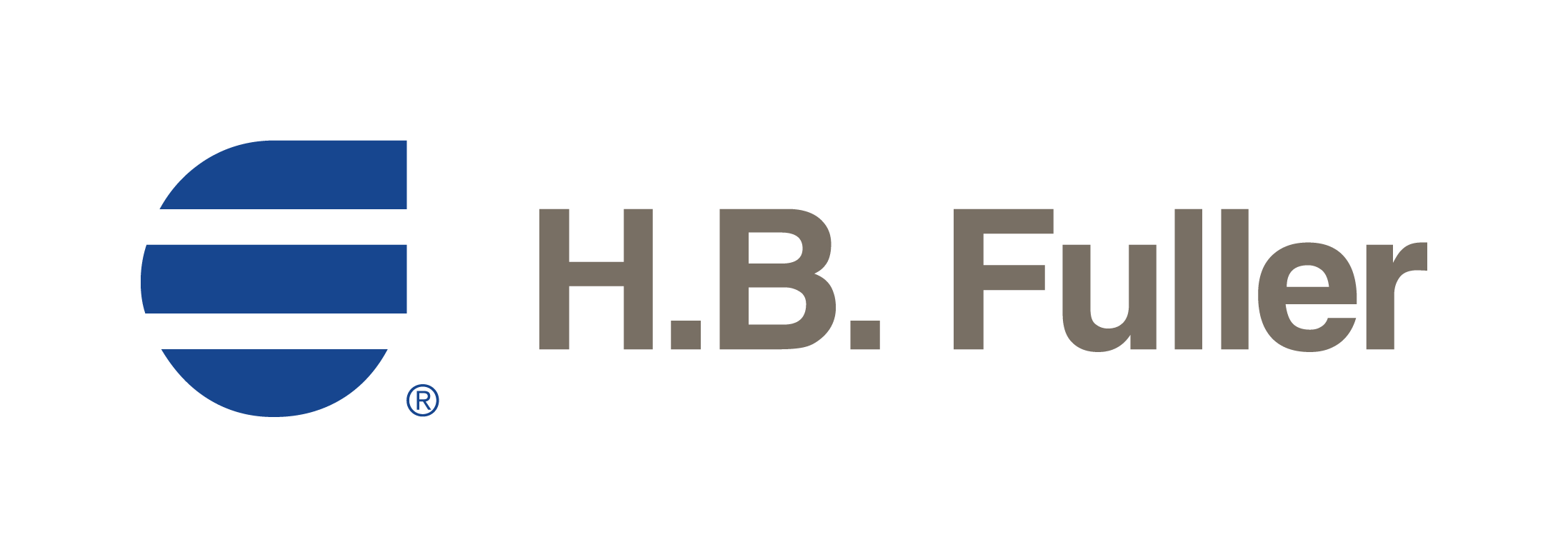
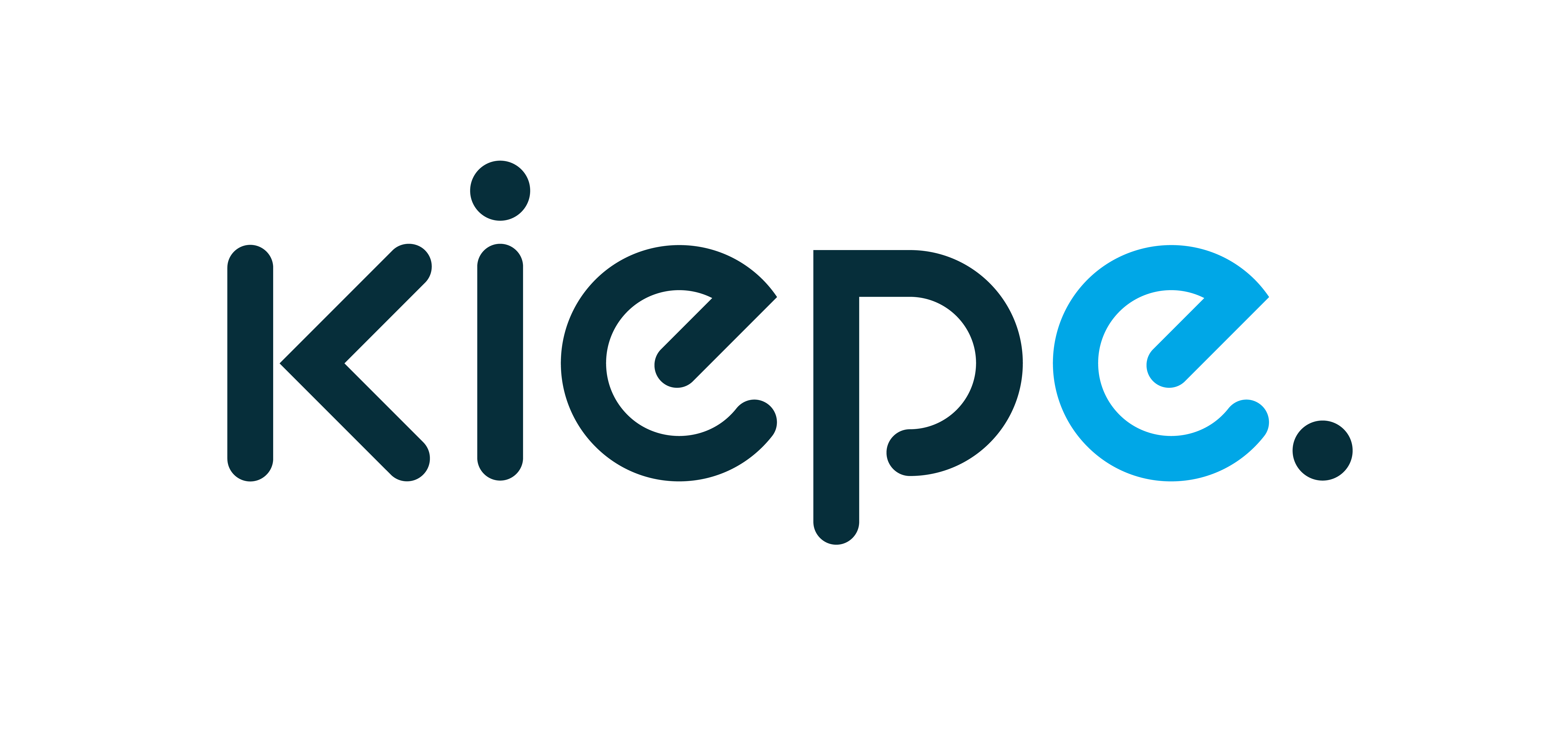
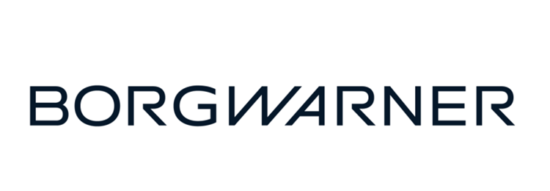