Sodium Batteries
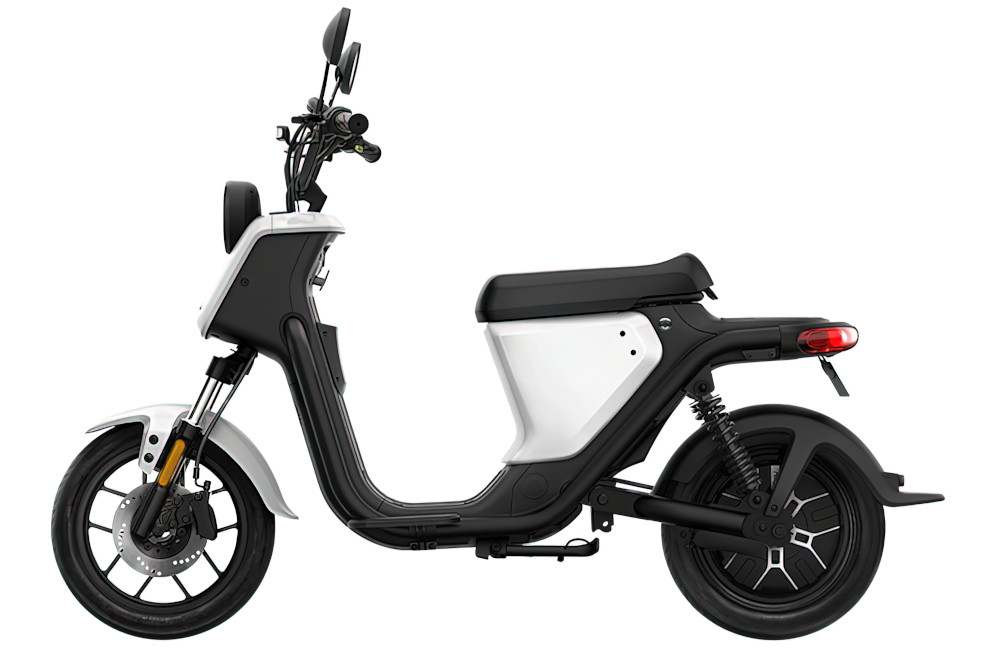
(Courtesy of NIU)
Charging back
Issues with lithium-ion cells are promoting a resurgence in sodium cell technology, reports Nick Flaherty, if certain challenges can be overcome
Research into sodium-ion batteries (NIBs) began in the 1970s and ’80s but was overtaken by lithium-ion battery (LIB) research in the 1990s. However, NIBs have recently re-emerged as a potential sustainable and less expensive alternative to LIBs as the demand for lithium drives up its cost, and there is growing concern over the safety of LIB cells, which can be prone to short-circuits and thermal runaway.
NIB cells can be constructed from abundant materials in the same way as LIBs. However, the combination of materials has so far struggled to reach the energy levels of LIBs, but research over the past decade has brought the performance of sodium cells up to that of lithium iron phosphate (LFP) cells.
Sodium can be extracted from seawater, the anode materials can be obtained from renewable sources, and the cathodes generally contain iron and manganese rather than high levels of cobalt and nickel, says Emma Kendrick at the School of Metallurgy and Materials, University of Birmingham, in the UK.
The manufacturing processes are expected to be the same as those for LIBs, so no investment in new manufacturing lines will be needed. The cost difference between LIBs and NIBs can therefore be considered to be due to materials and performance only.
However, Kendrick points to the challenges of increasing the lifespan of the cells. This is governed by various chemical and cell engineering optimisations relating not only to the materials but also to the design of electrodes and cells and their operation. For example, dendrites and plating can occur very readily in sodium-ion cells, and this is controlled not only by the electrolyte’s composition and the ability to form low-resistance, stable interfaces, but also through electrode design.
This has been demonstrated by the use of sodium cells from Faradion in e-bikes and heavy trucks in India, and Chinese e-bike developer NIU is planning a version of its two-wheeler in 2023 using sodium batteries. Major battery maker CATL is also developing the technology.
There are three main advantages of sodium cells over lithium-ion. They are more powerful in terms of charge and discharge performance, so offer advantages for applications with high power requirements and faster charging, such as onboard batteries and small vehicles. However, they are not yet seen as a good enough fit for electric cars.
Another advantage is their low-temperature performance. Lithium cells struggle to operate below 0 ºC, and need other batteries to drive heaters to warm them up so they can operate. This is not necessary for NIB cells.
Then there is the safety aspect, both in operation and in transport. While NIB cells can form dendrites in the same way as LIB cells, they do not cause short-circuits, and any heating is quickly quenched by the water-based electrolytes. The cells can also be transported with zero charge, which is not possible with LIB cells, making shipping NIB cells much simpler and safer.
Cathodes
Most cathodes use layers of oxide materials and are air-sensitive, which leads to a higher manufacturing cost for NIBs and is holding back their development. This poor air-stability needs to be understood and resolved, say researchers in China who have reviewed the latest understanding of and solutions to air sensitivity.
The mechanism of air sensitivity is complex and involves multiple chemical and physical reactions. Components in air, such as oxygen, water and CO2, participate in the reaction with the cathode’s layered cathode material, depending on the crystal structure of the material.
There are different strategies to improve the air stability, including the introduction of surface coating, washing cathode materials, and element substitution in either transition-metal sites or sodium sites. But the researchers found there is a lack of instructive information for rationally designing practical materials.
Electrolyte boost
Researchers at Pacific Northwest National Laboratory (PNNL) in the US have been working on refining sodium battery cells to boost their lifetime. There are two trends in sodium batteries: have a long cycle life but lower voltage and lower energy density for stationary storage applications, or a higher energy density and higher voltage for e-mobility applications, but that has an impact on the lifetime.
The PNNL work is focused on a new electrolyte and solvent to boost NIB lifetime by optimising the protective film, or solid-electrolyte interface (SEI) layer, that forms on the electrodes. The film is critical, as it allows sodium ions to pass through while preserving battery life, but electrolytes in current use tend to dissolve it, reducing the lifetime.
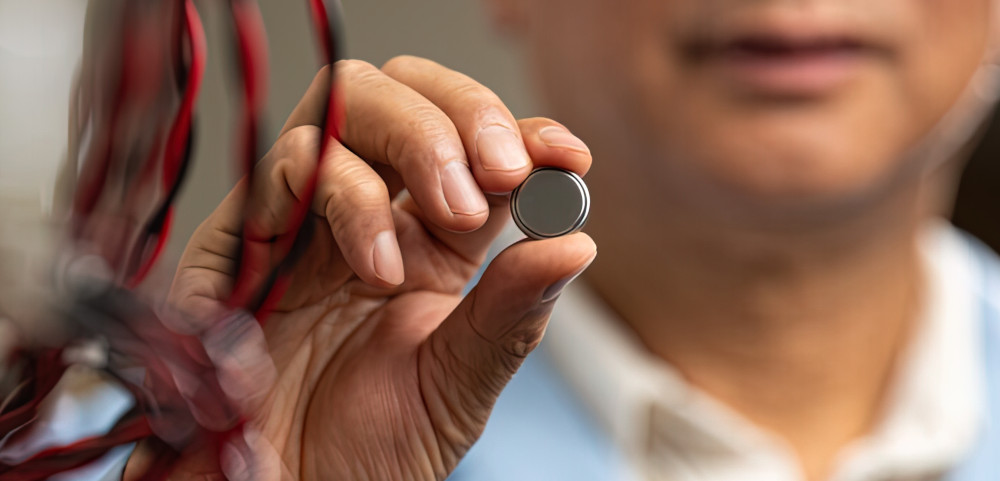
(Courtesy of PNNL)
Developing a new electrolyte that works with the different materials in the cathode and anode is a challenge, but the PNNL team has found an electrolyte that produces a cell with an energy density comparable to LFP at 150 Wh/litre and a lifetime of at least 300 cycles.
The research cell uses a sodiated lithium MNC cathode loaded with sodium ions and a hard carbon anode with the new electrolyte. The key is the SEl layer that forms on both the anode and the cathode, and this layer depends on the composition of the electrode and the interaction with the electrolyte. “That’s one reason why a high-voltage sodium battery does not have a long cycle life,” says Jiguang (Jason) Zhang, the team’s lead researcher.
“We have shown in principle that sodium-ion has the potential to be a long-lasting and environmentally friendly battery technology. We selected a salt and solvent to control the amount and quality of the SEI layer on the anode, which reduced the solubility to protect the anode longer,” he says.
Rather than using the traditional NaPF6 as the salt in the electrolyte, the team used a salt sodium, fluorine, sulphur iodide material. “This salt can decompose to form an inorganic SEI layer,” Zhang says. “We selected the solvent with a smaller dielectric constant so that it is difficult to dissolve the SEI layer.”
The team has developed a coin cell to test the performance of the materials. It held 90% of its capacity after 300 cycles at 4.2 V, which is higher than most high-voltage NIBs previously reported.
“Normally the gold standard for cycle life is the discharge to 80% capacity,” Zhang says. “In this work it was measured to 90%, so it has the potential to last even longer.”
The electrolyte is non-flammable, and the cell can operate at high voltages.
“We also measured the production of gas vapour at the cathode,” says Phung Le, a PNNL battery chemist and one of the lead authors of the study. “We found very minimal gas production, which provides new insights into developing a stable electrolyte for sodium-ion batteries that might operate at elevated temperatures.”
There is more work to do though to improve the cell’s energy density with the new electrode materials. “We need to look further at the cathode material, and we have an effort to improve the specific capacity of carbon anode by more than 50% using different structures,” he says.
“Once we find suitable materials we will scale up to a pouch cell, but it is still early days as we continue to improve both the anode and cathode.”
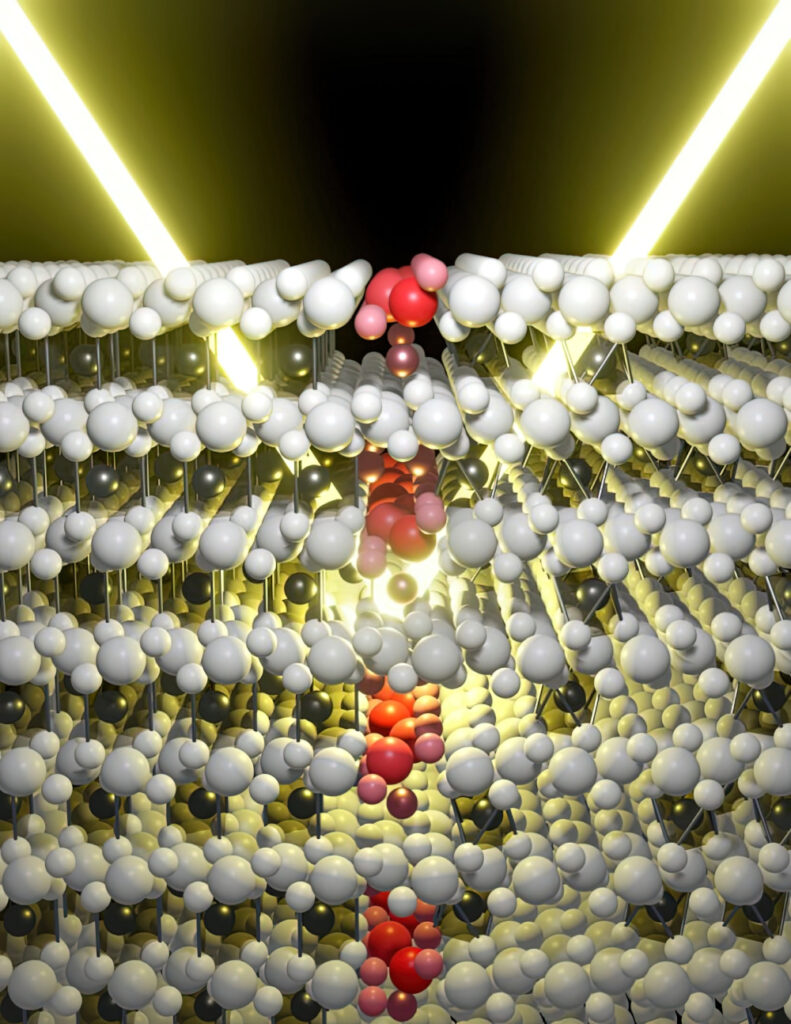
(Courtesy of Cornell University)
Shuttle challenges
The poor durability of sodium cells stems from a specific atomic reshuffling in the battery’s operation – the P2-O2 phase transition – as ions travelling through the battery cause disorder in the crystal structures and eventually break them.
Researchers at Cornell University, in the US, have been looking at this process, and found that as the sodium ions move through the battery, the misorientation of crystal layers inside individual particles increases before the layers suddenly align just before the P2-O2 phase transition.
“We’ve discovered a new and critical mechanism,” says Andrej Singer, assistant professor of materials science and engineering at Cornell. “During battery charging, the atoms suddenly realigned and facilitated that flawed phase transformation.”
The team was able to observe the phenomenon after developing a new X-ray imaging technique using the Cornell High Energy Synchrotron Source, which allowed it to observe, in real time and in mass scale, the behaviour of single particles in the battery it was using.
“The unexpected atomic alignment is invisible in conventional powder X-ray diffraction measurements, as it requires the ability to see inside individual cathode nanoparticles,” Singer says. “Our high-throughput data allowed us to reveal the subtle yet critical mechanism.”
This led the team to propose new design options for the type of battery it was using, which it plans to investigate in future research projects. One solution is to modify the battery chemistry to introduce a strategic disorder to the particles just before the flawed transition phase, according to Jason Huang, a researcher on the project.
“By changing the ratios of our transition metals, in this case nickel and manganese, we can introduce a bit of disorder and potentially reduce the ordering effect we observed,” he says.
The new characterisation technique can be used to reveal complex phase behaviours in other nanoparticle systems such as sulphur batteries.
“We’re pushing the frontiers of sodium-ion batteries and what we know about them,” Huang says. “We are also using this knowledge to design better batteries that will help to unlock the technology for practical applications in the future.”
Cathode materials
Researchers from Skoltech and Lomonosov Moscow State University have developed a cathode material for NIBs that provides an energy density 15% higher than current cells and a discharge voltage of 4.0 V. It is a sodium-vanadium phosphate fluoride powder with a particular crystal structure that can be produced using a relatively low temperature process.
“Our new material and the one the industry has started using are both called sodium-vanadium phosphate fluoride – they’re made of atoms of the same elements,” Assistant Professor Stanislav Fedotov of Skoltech says. “What makes them different is how those atoms are arranged and in what ratio they are contained in the compound.
“Our material also compares well with the class of layered materials for cathodes. It provides roughly the same battery capacity and greater stability, which translates into longer life and higher cost efficiency of the battery. Remarkably, even the theoretical predictions for the competing materials fall short of the practical performance of ours. That is far from trivial, because the theoretical potential is never fully realised.
“Higher energy storage capacity is just one advantage of this material. It also enables the cathode to operate at lower ambient temperatures, which is particularly relevant for Russia,” he says.
The team used solid-state chemistry design rather than trial and error. “That means we rely on hard science, using the fundamental laws and principles of solid-state chemistry to arrive at the material with desired properties,” says researcher Semyon Shraer at Skoltech
“Theoretical considerations led us to the basic formula for a material that might provide high energy storage capacity,” he adds. “We then needed to determine which crystal structure would unlock that potential.
“The one we chose is known as the KTP-type framework, which comes from non-linear optics; it’s not very common for battery engineering. We realised that this particular compound with that particular crystal structure should work, then we managed to synthesise it via low-temperature ion exchange. And there it is, with its superior characteristics now confirmed by an experiment.”
The cathode material is produced by combining a NaVPO4F composition and KTiOPO4-type framework using low-temperature ion-exchange synthesis at 190 °C. When tested in a coin cell configuration in combination with a sodium metal negative electrode and a NaPF6-based non-aqueous electrolyte solution, the cathode active material enables a discharge capacity of 136 mAh/g at 14.3 mA/g with an average cell discharge voltage of about 4.0 V. A specific discharge capacity of 123 mAh/g at 5.7 A/g is also reported for the same cell configuration.
Last year, the team at Skoltech developed a cathode with a reversible specific discharge capacity of 190 mAh/g, a relatively high value for sodium-ion battery cathode materials, by using layers of sodium, lithium and manganese, NaLi/Mn2/O2
Elsewhere, Tiamat Energy in France is using cathodes based on the polyanionic Na3V2(PO4)2F3 material. The company is a spin-off of the French CNRS research laboratory that developed the technology.
The key is that the sodium family is as wide as the lithium-ion family, and that allows layers of oxides, says Herve Beuffe, founder and president of Tiamat Energy.
Tiamat’s polyionic compound uses fluoride and vanadium to support fast charging at rates of 40-50C so that a cell can be fully charged in 10 minutes, exactly the same as NMC lithium-ion cells. The downside is its lower energy density, from 90 Wh/kg up to 120 Wh/kg, compared with the 400-800 Wh/kg energy density of lithium metal cells, which restricts the range of possible e-mobility applications.
“A 100% EV using sodium batteries would have a restricted range, despite allowing a full charge in 10 minutes,” says Beuffe. “That could benefit small cars used in cities, especially with a fleet operator that wants the cars out on the road all the time.”
These sodium cells could also be used alongside hydrogen fuel cells that need a battery pack to incorporate the energy from regenerative braking, so the company is developing a proof of concept at 48 V. It is also working with Plastic Omnium to develop a 48 V sodium battery pack for mild hybrid vehicles with a view to incorporating hydrogen systems.
Also in France, Sodium Cycles is developing an e-bike based around Tiamat’s cells. The Xubaka has a 4 kW motor and a top speed of 50 mph (80.5 kph) in the US, although this will be limited to 45 kphin the European Union. The pack will charge in 4 hours from a standard plug and gives a range of 60 to 80 km.
In the UK, Technology from Faradion uses mixed-phase O3/P2-type Na-Mn-Ni-Ti-Mg layered oxide cathodes, hard carbon anodes and non-aqueous electrolytes, and has achieved a 3000-4000 cycle lifetime. Batteries based on this design are being used in trucks and e-bikes in India, where the lower maintenance requirements and higher safety of sodium over lithium-ion are key advantages.
The next generation of the technology is aiming for 2 kW/kg, 210 Wh/kg, with a lifetime of up to 8000 cycles. This compares to the existing cells with an energy density in excess of 140 Wh/kg, with a design performance of 155 Wh/kg in 10 Ah pouch cells.
Meanwhile, US-based Natron Energy has built its sodium-ion technology around aqueous solvents and PBA-based cathodes and anodes, but this is more suited to stationary energy storage system (ESS) applications rather than e-mobility. AMTE Power in the UK has similar plans with a sodium battery line for ESS alongside its lithium ion cells for e-mobility applications.
For cathodes for e-mobility cells, Altris uses a material called Prussian White. This is a framework material consisting of sodium, iron, carbon and nitrogen and a variant of a dye called Prussian Blue. The large pores inside the material enable the capture and storage of a range of atoms or molecules, making the compound highly interesting for a range of applications.
Altris has developed a method to produce a cathode material called Fennac in a form that is suitable for use as a positive electrode material in sodium-ion batteries. Using iron as a source of electrons and completely filling the material with sodium provides a theoretical capacity of 170 mAh/g and an average voltage output of 3.2 V.
Fennac is produced using a patented low-temperature and pressure synthesis process, in a fully sodiated form, which is necessary for a cathode material. This can be dropped into existing battery production lines.
Altris has built a production plant in Sandviken, Sweden, called Ferrum, to make the material and plans to open it next year. It will produce 2000 t of Fennac a year, enough to make 1 GWh of sodium-ion batteries. Ahlstrom-Munksjo, a French manufacturer of fibre products, will provide heat-resistant separators for the Fennac-based cells. CIDAUT, the Foundation for Transport and Energy Research and Development in Spain, will develop and perform safety and performance cell testing.
Anodes
Anodes can be made from layered oxides, variants of Prussian Blue mixed with sodium- or vanadium-based polyanionic compounds, and used with aqueous and non-aqueous electrolytic solutions, says Dr Nuria Tapia-Ruiz at the Department of Chemistry at Lancaster University and the Faraday Institution in the UK.
Elsewhere, researchers at the Korea Maritime and Ocean University set out to find a suitable non-graphite anode material for NIBs. “Because NIBs have low performance – only 1/10th the capacity of a lithium-ion battery – it is crucial to find an efficient anode that retains graphite’s low cost and stability,” says Dr Jun Kang, the lead researcher.
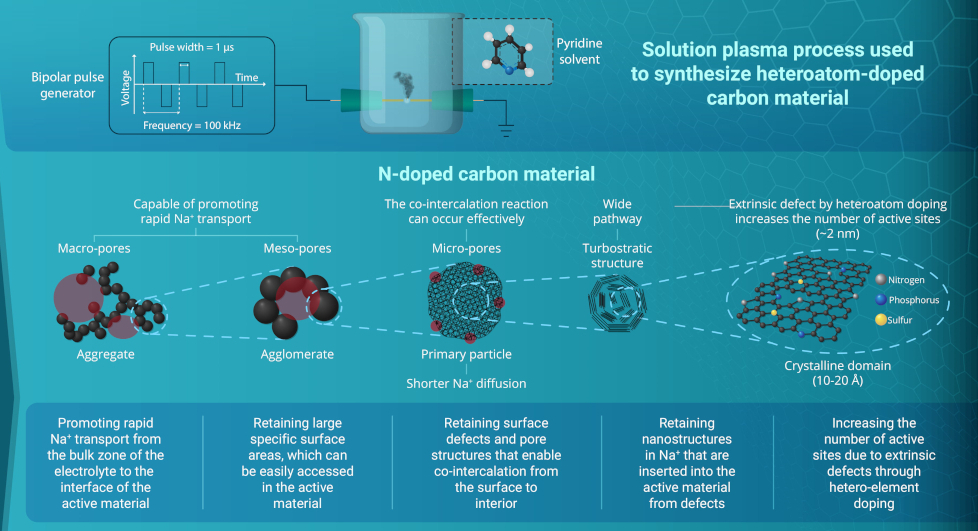
(Courtesy of Korea Maritime and Ocean University)
The anode they developed uses a hierarchical porous structure that allows rapid movement of sodium ions from the bulk zone of the electrolyte to the interface of the active material.
The structure has large specific surface areas where sodium ions migrate to the interface, which can be easily accessed in the active material and makes use of the surface defects and pore structures that enable co-intercalation from the surface to the interior. This reduces the diffusion paths and increases the number of active sites to boost the performance.
“These factors afford good capacity retention, reversible capacity, ultra-high cycling stability, high initial coulombic efficiency – 80% – and remarkable rate capability,” Dr Kang says. “That means they can be used for a long time, even with intense battery use.”
This approach gives an energy density of 101 mAh/g with a very high cycling stability of 11,000 cycles at currents of 100 A/g.
Other researchers have developed a 3D-printing process for carbon micro-lattice anodes in NIBs.
Battery cells tend to be built using layers of materials, usually laid down as a slurry and dried off or as a metal foil. The layers are stacked up in a pouch or prismatic cell or rolled up for a cylindrical cell, and all these formats are suitable for sodium cells in e-mobility designs. However, the slurry approach for carbon anodes means there are limited opportunities to develop structures in the electrode that could be used to boost the performance.
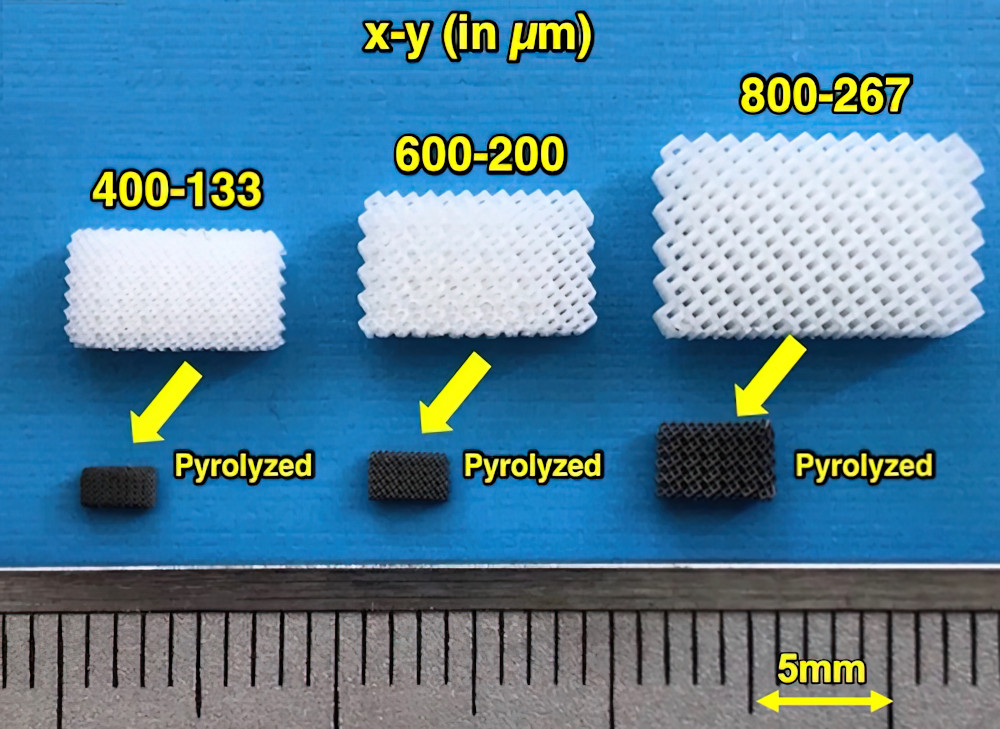
(Courtesy of Tohoku University)
So researchers at Tohoku University in Japan are looking at ways to achieve high-performance, low-cost batteries by increasing the loaded amount of active materials used to make a battery in a single cell. This would reduce the inactive materials that are used for binding multiple cells together but requires the fabrication of thicker electrodes, which would restrict ion movement within the battery.
This approach involves using 3D stereolithography to print micro-lattice structures made from resin. The micro-lattices are then shrunk by carbonising them using a process called pyrolysis. The resulting hard carbon anodes were found to allow fast transportation of energy-generating ions.
The micro-lattices have a width of 32.8 µm and reach an areal capacity of 21.3 mAh/cm2 at a loading of 98 mg/cm2 without degrading performance, which is much higher than conventional monolithic electrodes with 5.2 mAh/cm2 at 92 mg/cm2.
Avoiding the use of binding materials also enables structural changes in hard carbon to be tracked, to help understand the mechanisms of ion penetration into hard carbon.
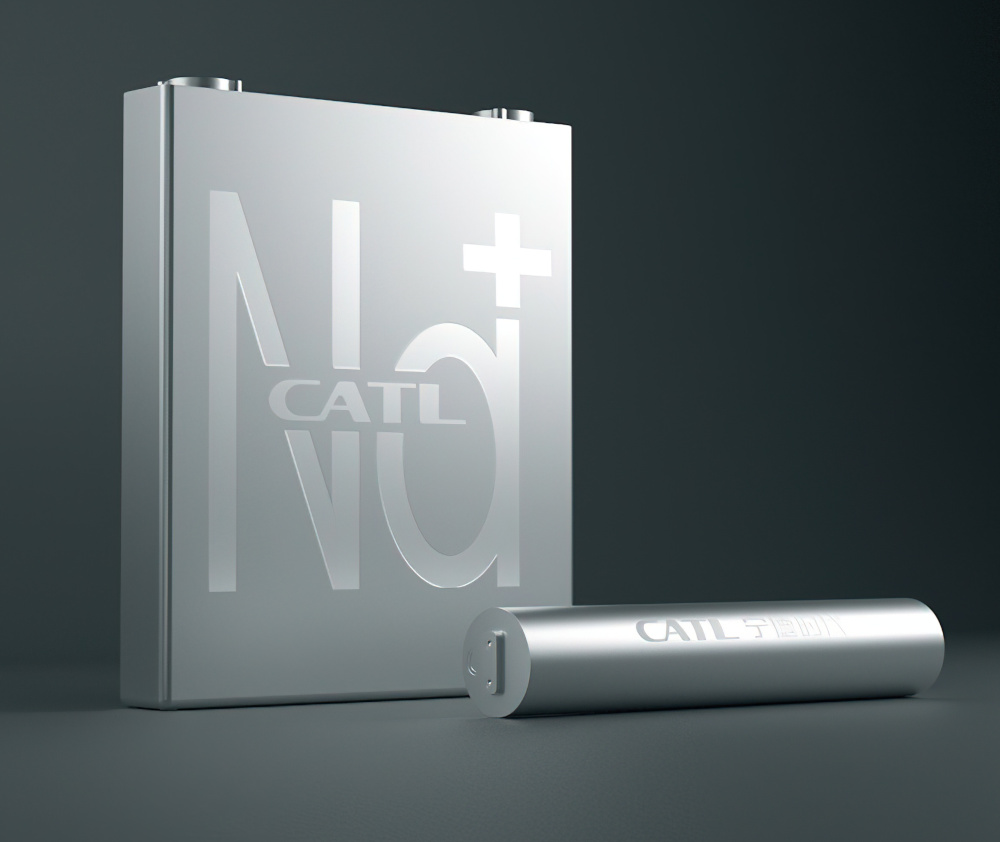
(Courtesy of CATL)
Sodium cells
CATL has also used Prussian White for the cathode, and redesigned the bulk structure of the material by rearranging the electrons, which it says has solved the worldwide problem of rapid capacity fading upon material cycling.
In terms of anode materials, CATL has developed a hard carbon material that features a unique porous structure, which enables the storage and fast movement of sodium ions. Cycle performance is reported to be up to 3000 cycles as a result of the change in the cathode structure, but the details of that are unclear at the moment.
The first-generation NIB cells have an energy density up to 160 Wh/kg, and can charge to 80% state of charge at room temperature in 15 minutes. More important, at -20 ºC they have a capacity retention rate of more than 90%, and their system integration efficiency can reach more than 80%.
CATL is aiming the cells at various transportation electrification applications, especially in regions with extremely low temperatures, and is working on the next generation of them to get the energy density to over 200 Wh/kg.
Using sodium cells also changes the battery pack’s design. CATL has developed an ‘AB’ battery system that mixes the NIB and LIB cells in a particular proportion, integrates them into one battery system, and controls the different battery systems using a BMS algorithm.
The AB design compensates for the energy-density shortage of sodium-ion batteries, and takes advantage of the high power and performance in low temperatures, providing power to heat the LIB batteries to make them ready for use.
Conclusion
Sodium batteries have key advantages for e-mobility applications if the lifetime issues can be overcome. The low-temperature operation in particular appeals for heavy-duty applications where lithium-ion cells will just not work. Using a hybrid approach that mixes solidum and lithium-ion batteries means the sodium batteries are not used as much, so the cycle life is not as much of an issue.
Meanwhile, research continues into new materials for the cells. Variants of Prussian Blue for the cathodes and new anode materials are increasing the energy density of the cells, while careful optimisation of the electrolyte and solvent can help increase the cycle life to be more useful.
All of this is driving the development of sodium-ion battery cells for commercial use in e-mobility applications in different ways, from hybrid battery packs with lithium cells to supporting regenerative energy capture in vehicles powered by fuel cells.
ONLINE PARTNERS
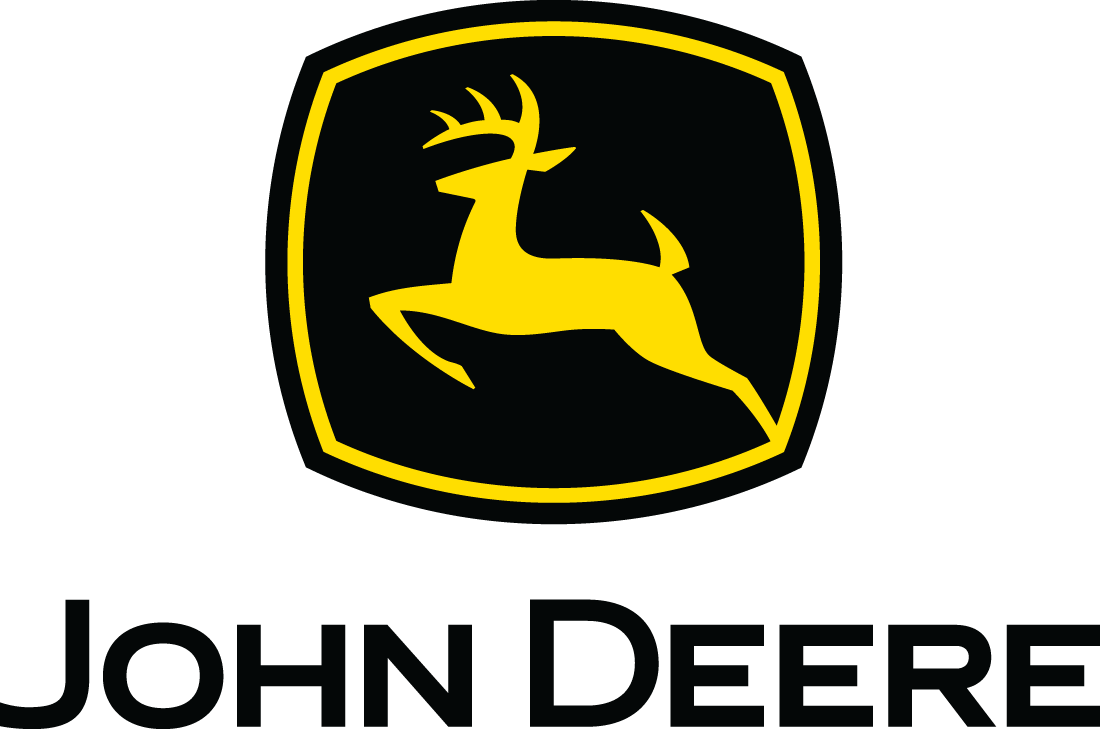
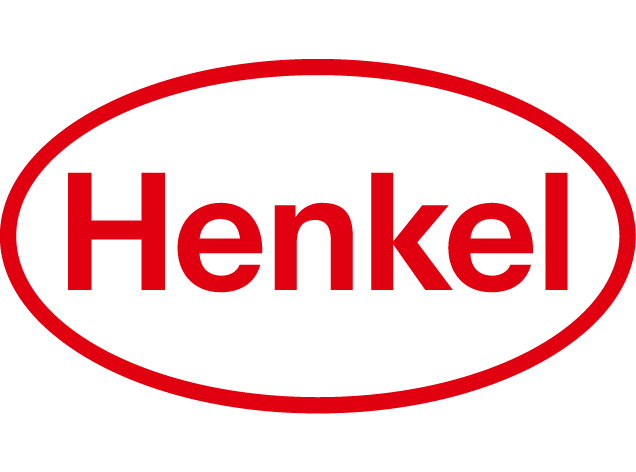
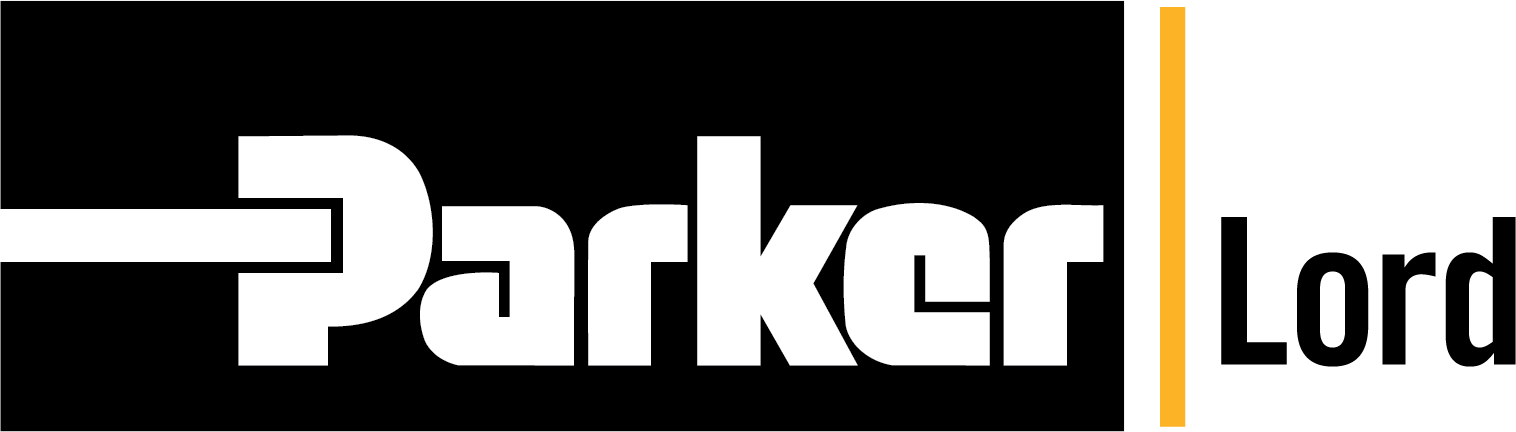
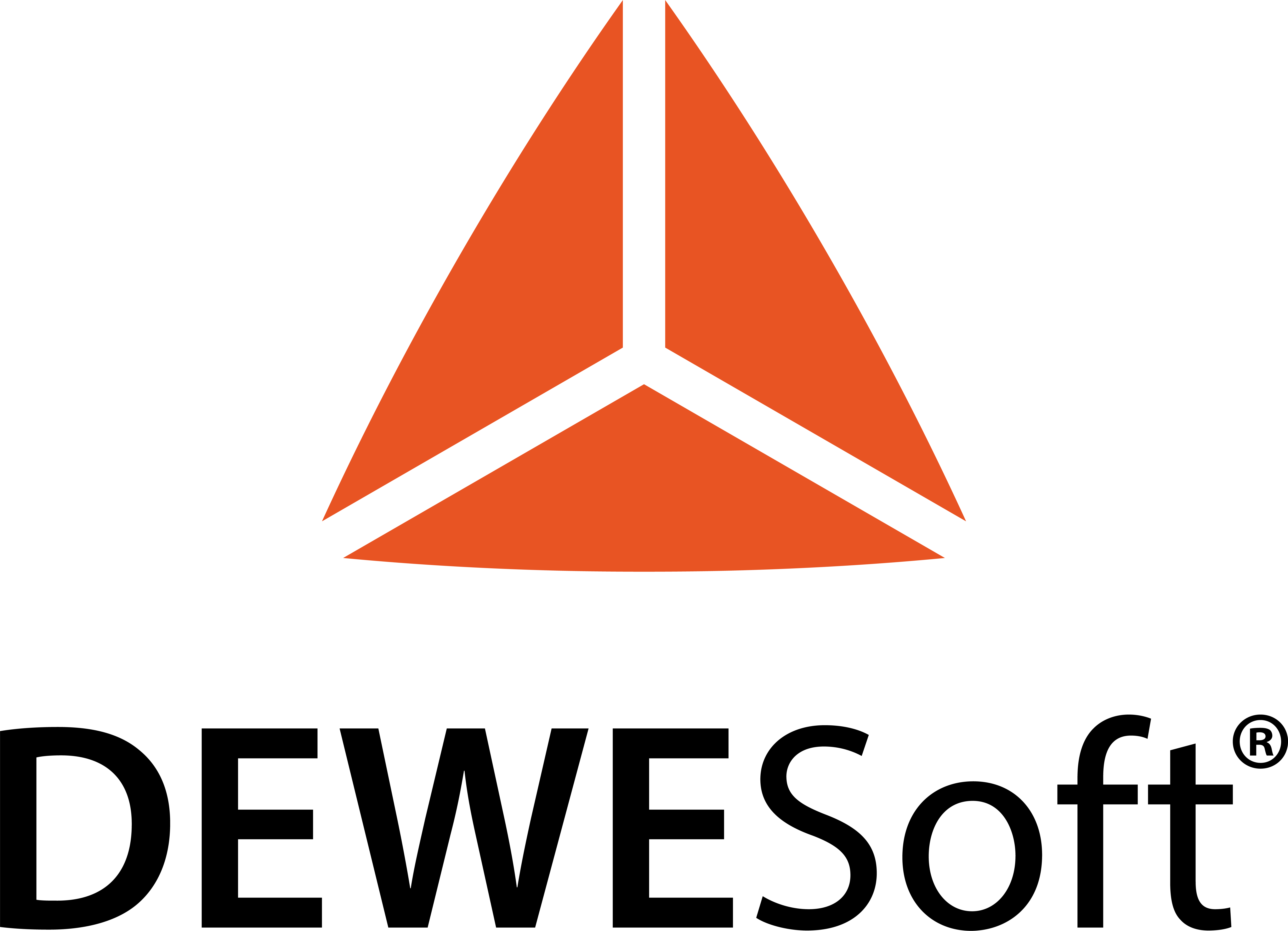
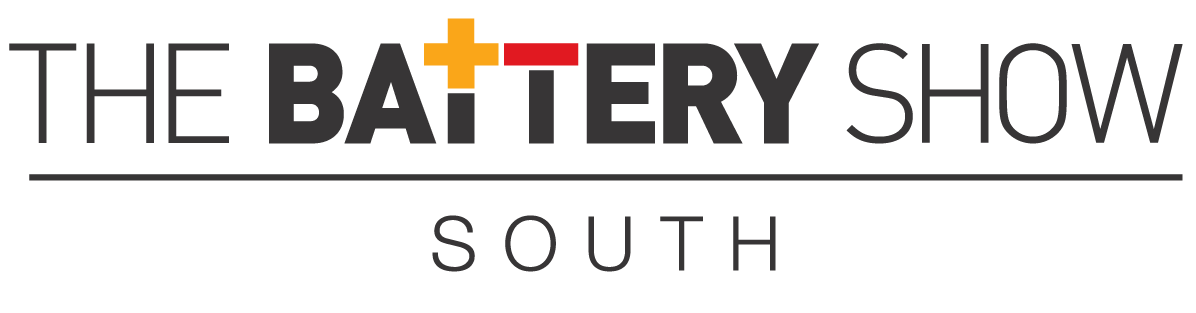
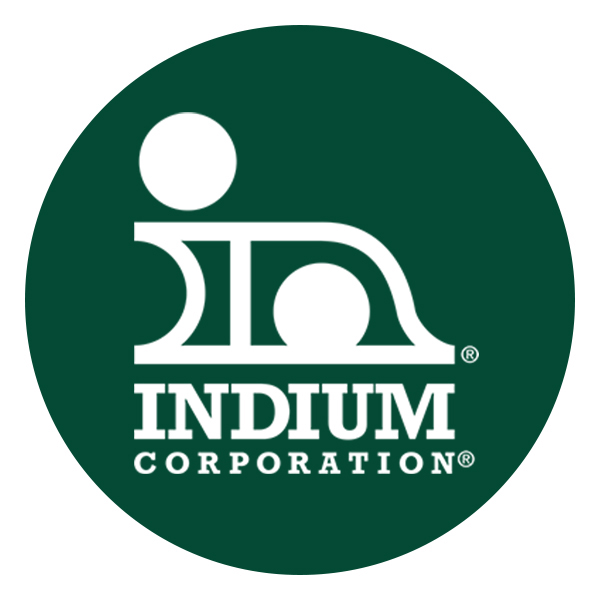

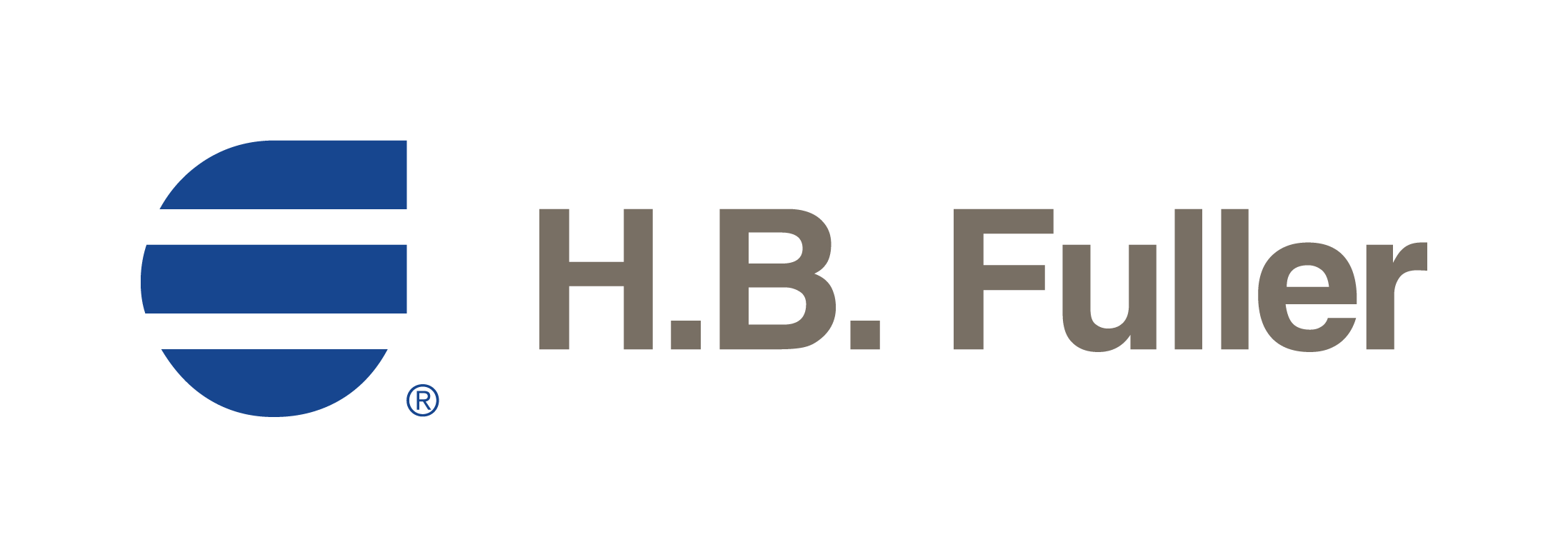
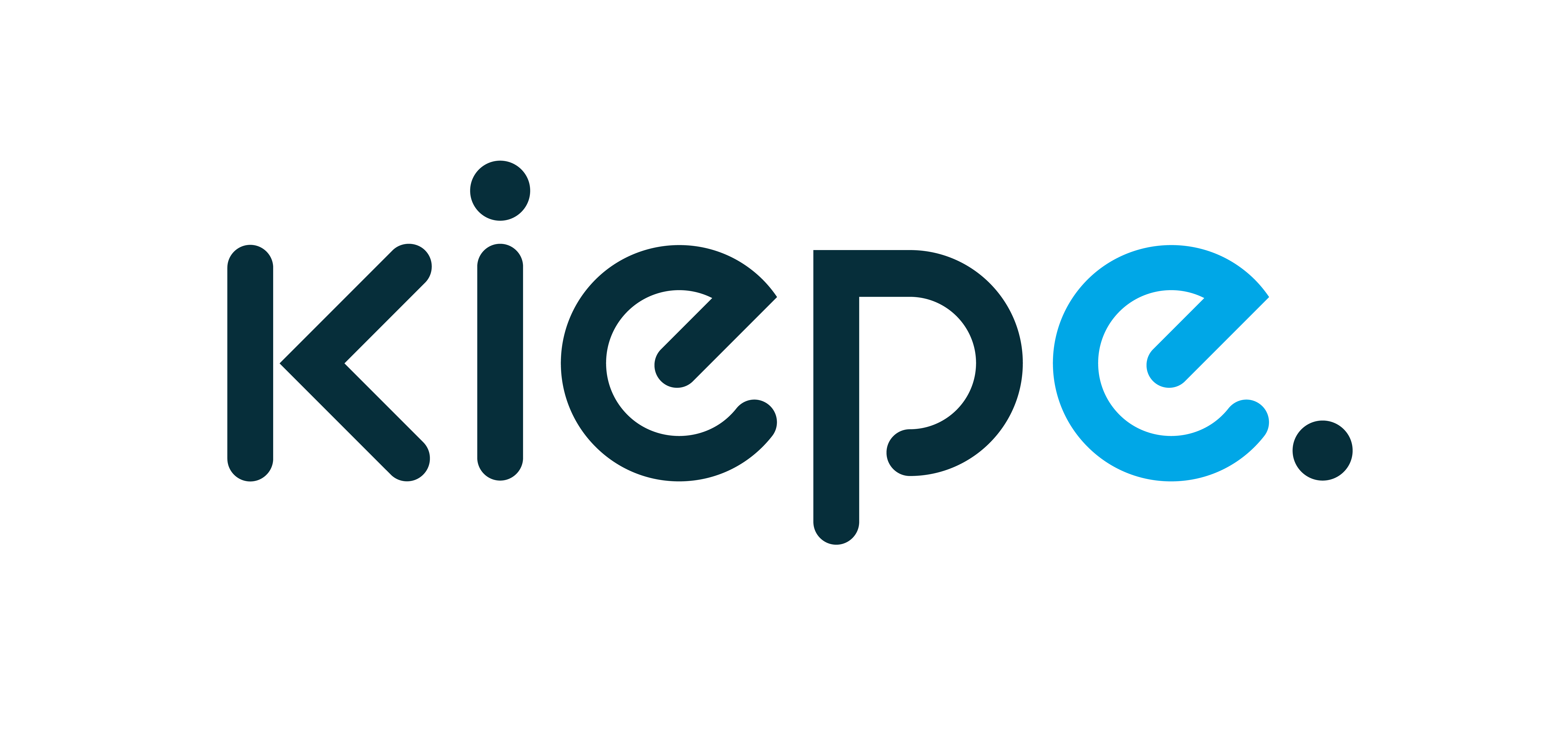
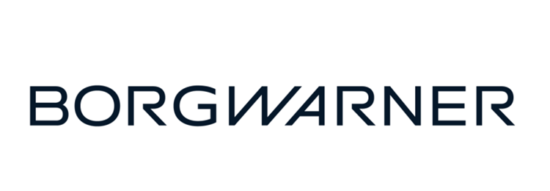