RAMPF Group’s battery production materials and processing technologies
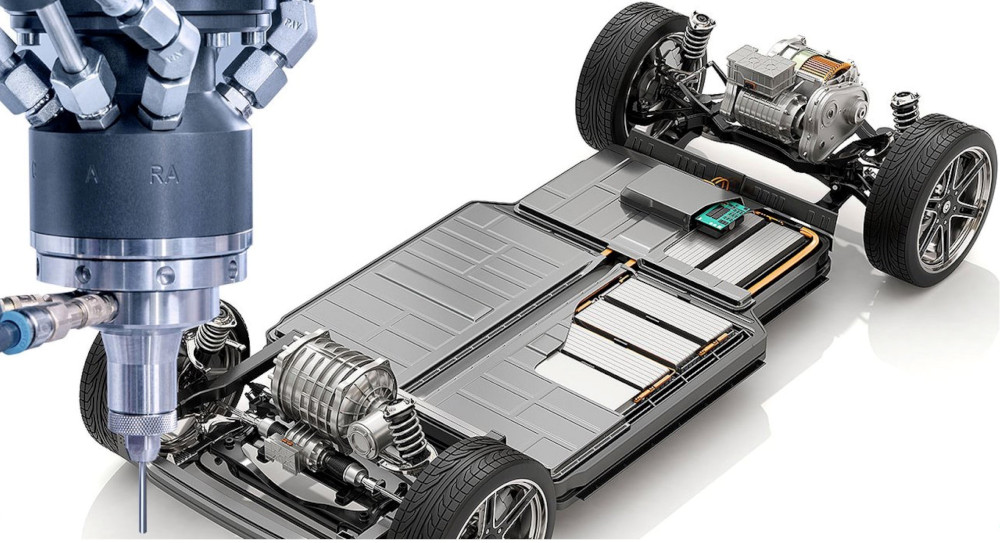
(Images courtesy of RAMPF Group)
To be competitive in global markets, ultra-fast production processes are essential. That is also true for the manufacture of batteries, for which RAMPF Group has developed polymers for sealing, casting and thermal management, as well as dispensing and automation systems.
RAMPF uses epoxy, silicone and polyurethane polymers for sealing, casting and thermal management solutions for battery housings, sensors, plugs, relays and onboard chargers. It says its reactive polymer systems offer a wide range of mechanical, thermal and chemical properties to ensure safety, control, cost-efficiency and convenience.
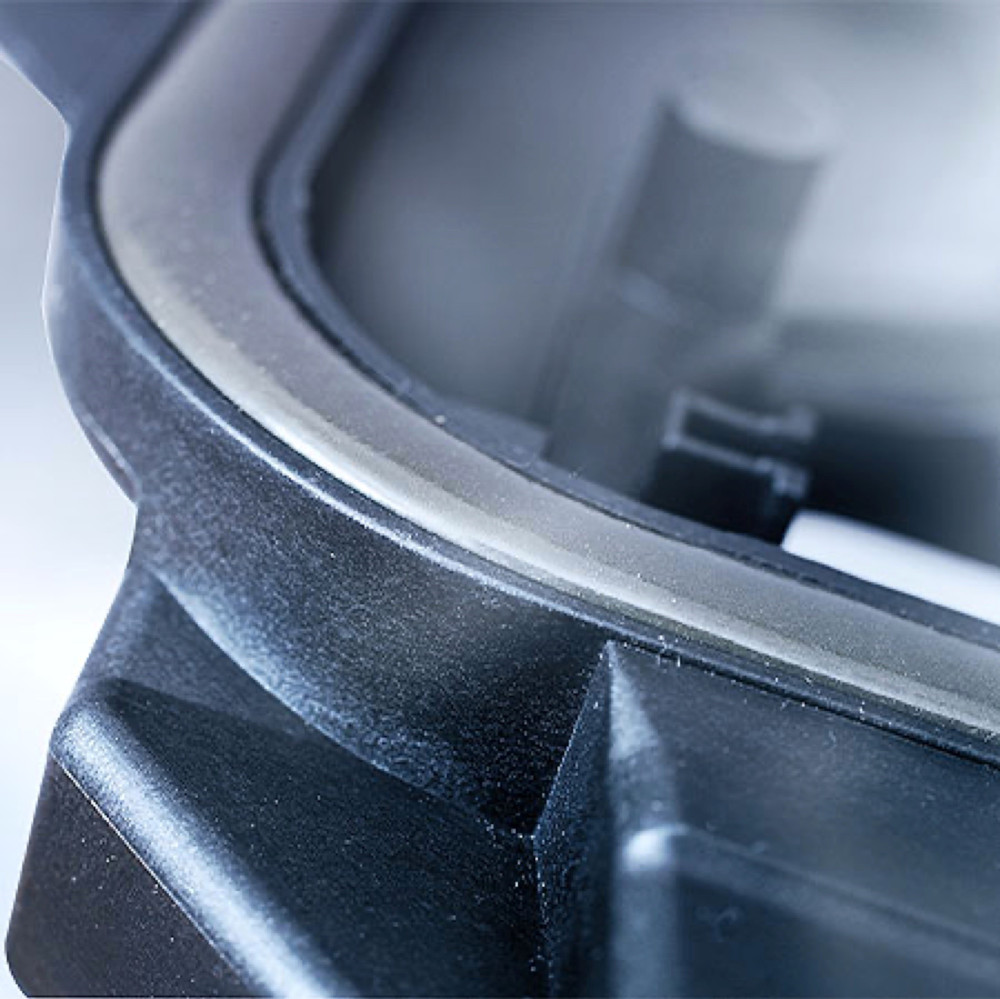
Its sealing systems are based on polyurethane and silicone to give efficient sealing and easy handling. The fast-curing, low-emissions, heat-resistant systems protect battery covers, charging stations and charging connectors against dust, dirt, moisture, chemical substances and environmental influences.
RAMPF’s casting systems are based on polyurethane, epoxy and silicone for optimum heat dissipation in batteries and power electronics, while providing long-term protection against chemical substances and environmental influences. Gap fillers and heat-conductive casting materials optimise heat management of electrical and electronic components.
The group also says it has comprehensive experience in production systems for the precision handling and application of polymers.
Regarding its mixing and dispensing technology, RAMPF says it offers high-performance, low-maintenance systems for precise dispensing of single-, dual- and multi-component reactive resin systems that are independent of fillers and viscosities.
Its automation concepts are centred on integrated parts transport and heat treatment, assembly and joining technology, logistics and quality assurance solutions, surface activation processes, testing and measuring technology.
ONLINE PARTNERS
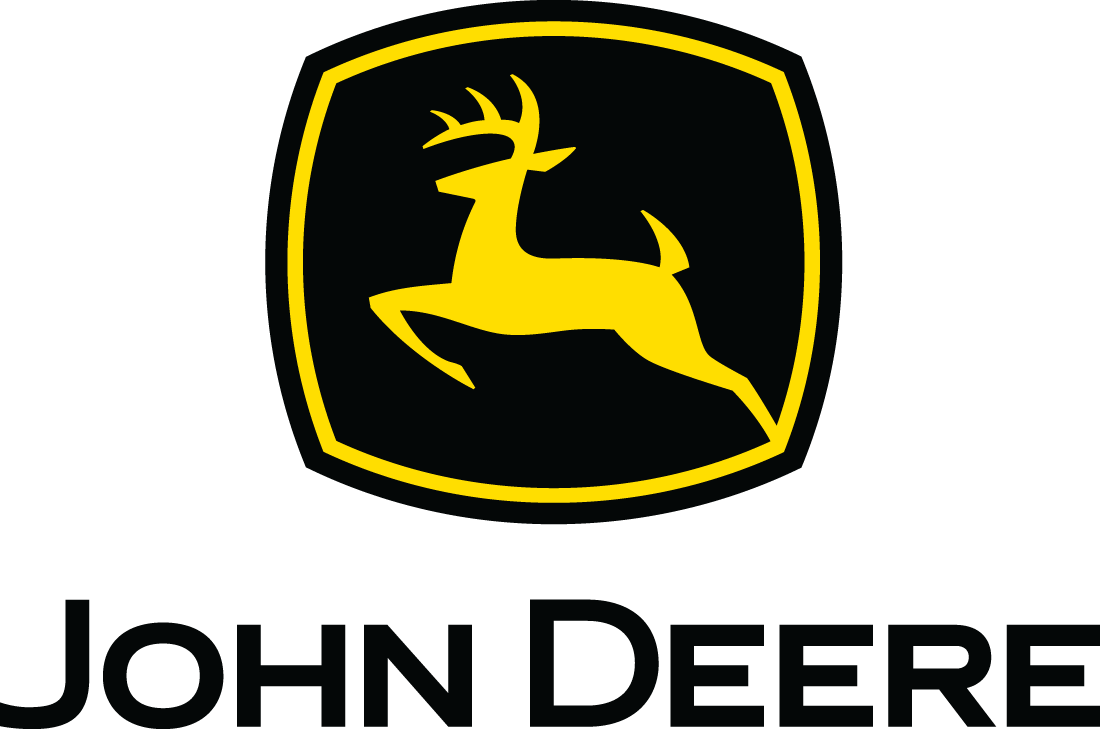
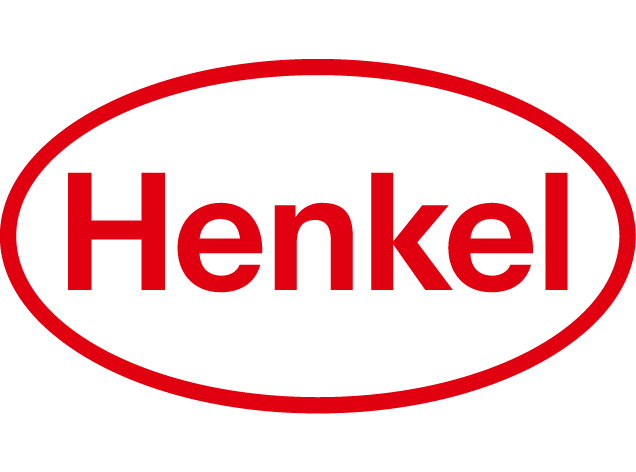
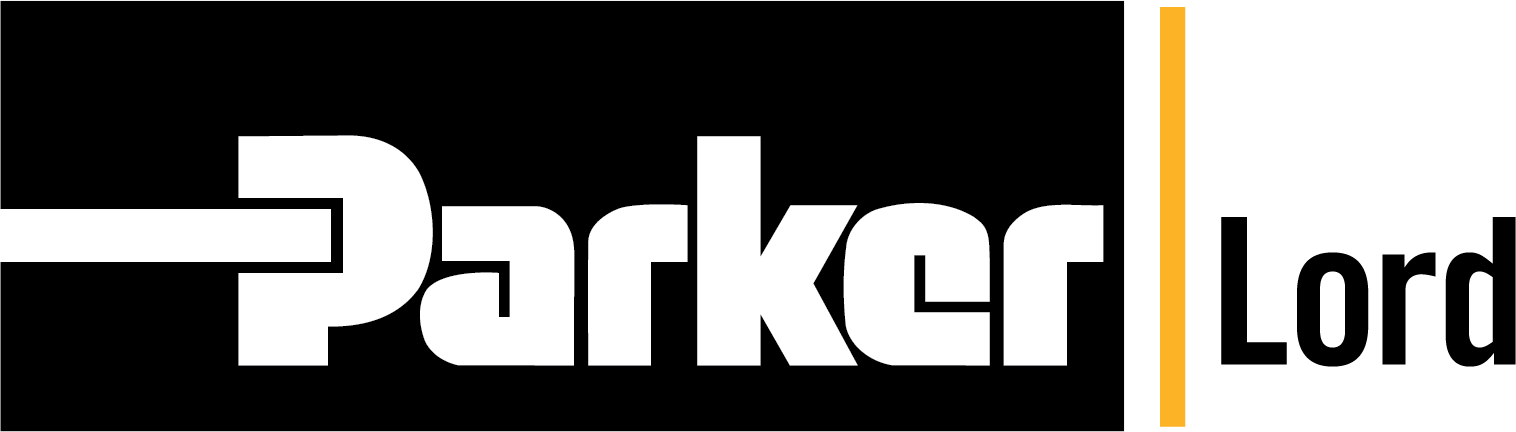
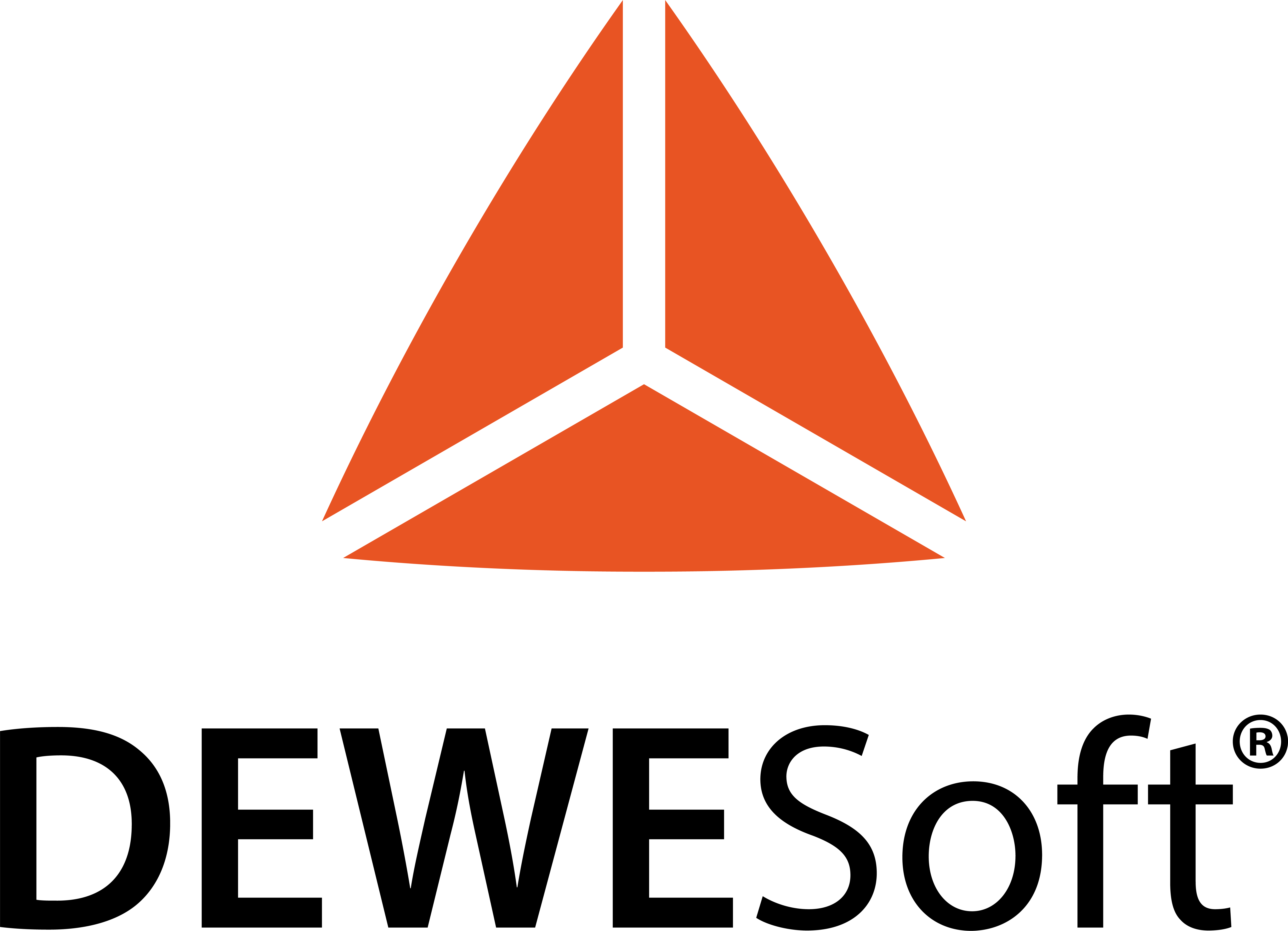
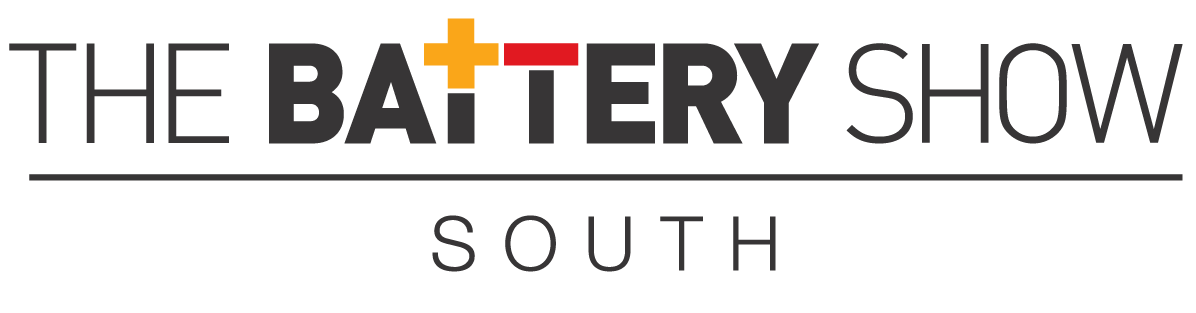
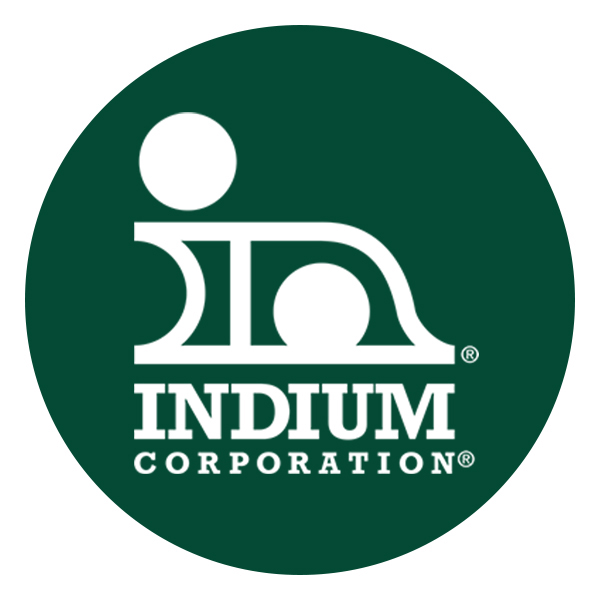

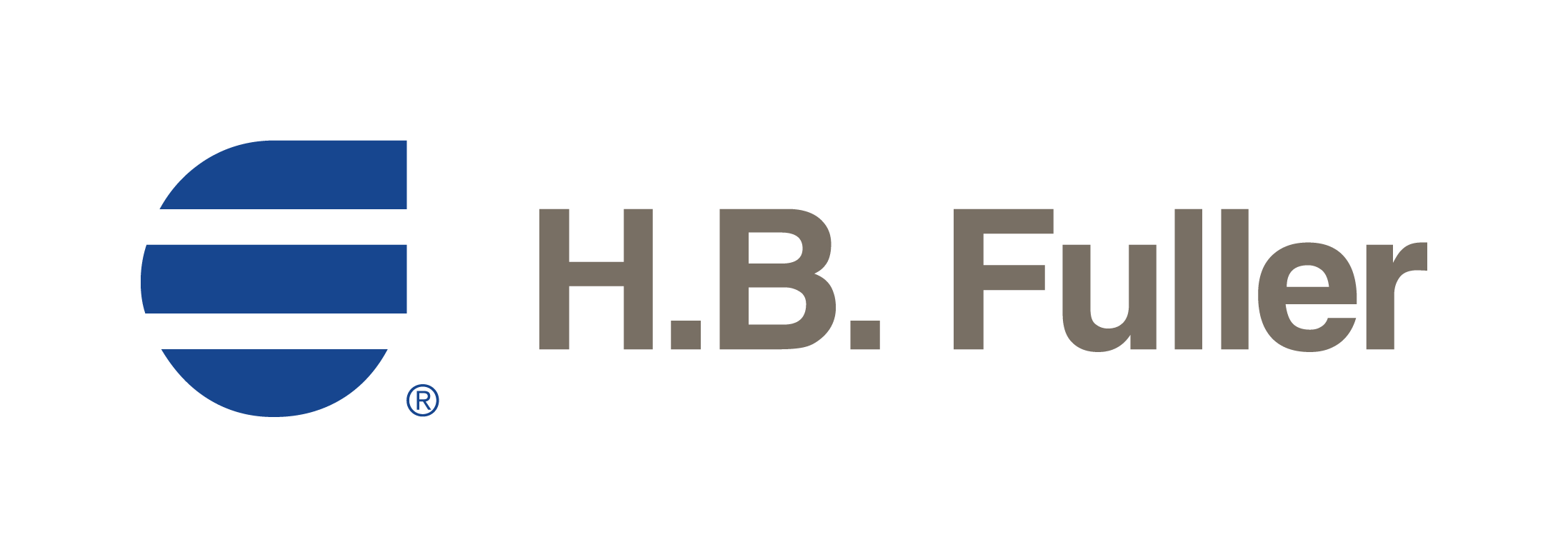
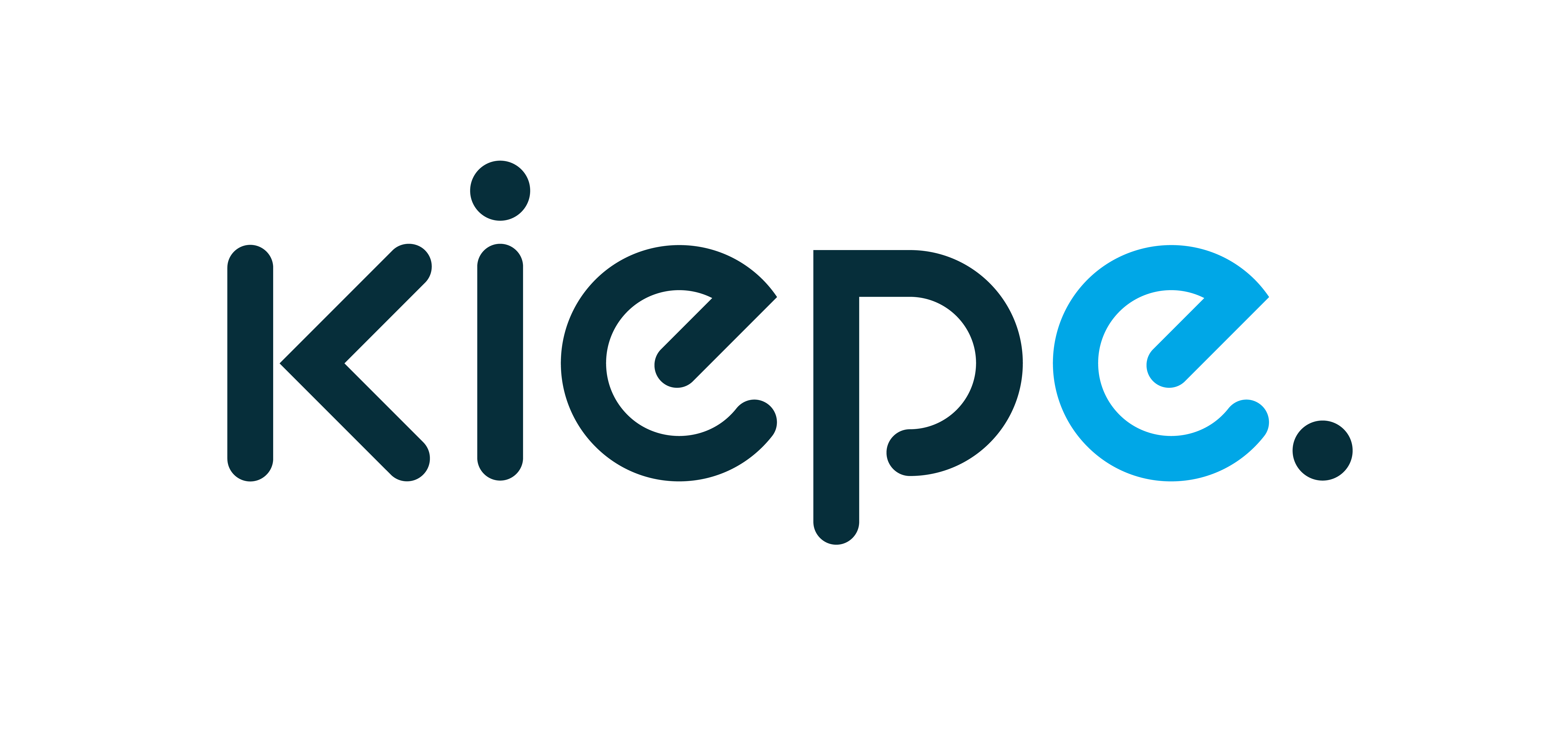
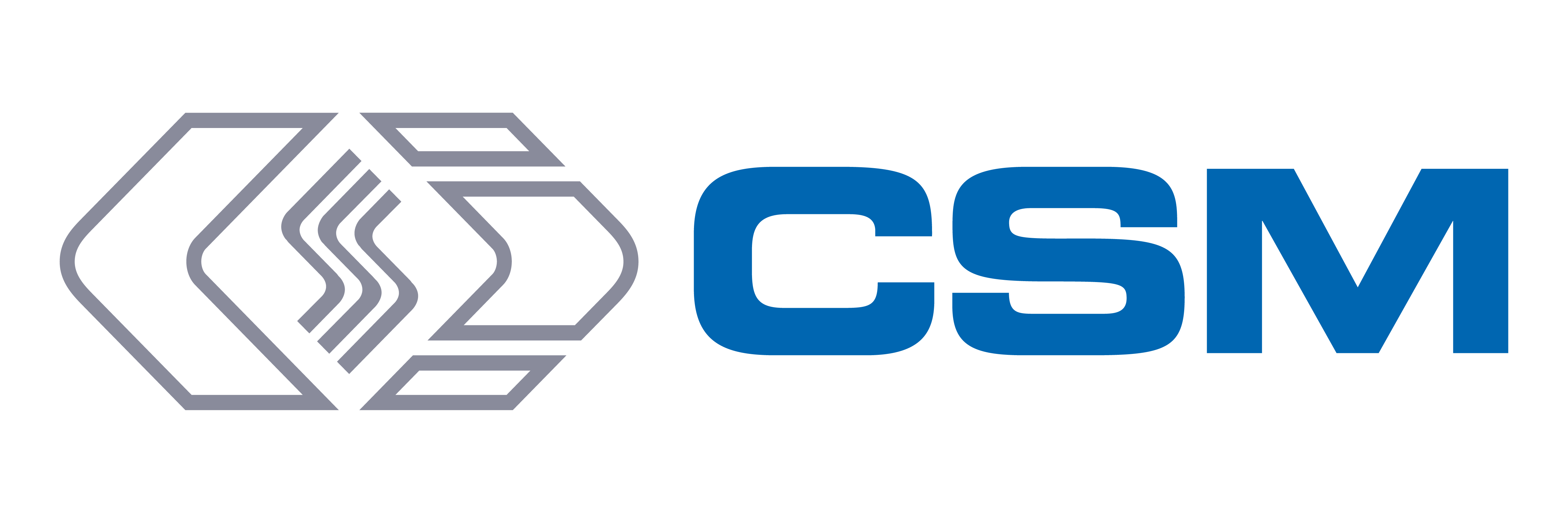