Self-developments
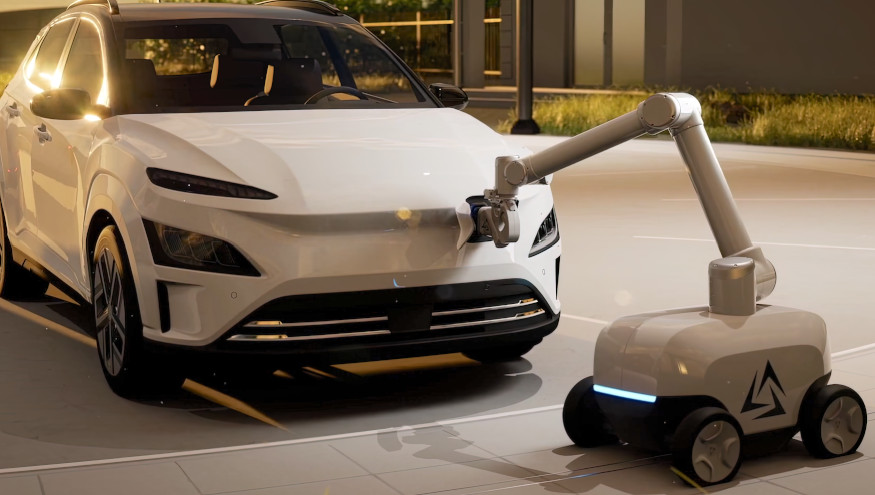
(Courtesy of Alveri)
Nick Flaherty explains how higher charging requirements are leading to different approaches to automating the process
Developers of charging systems are looking to address key challenges for fast charging and higher capacity battery packs, and this is leading to automated charging systems. Several companies are developing such systems to provide more convenient charging with higher current capabilities through cabled systems. Applications range from large mining equipment that needs to have huge battery packs charged quickly, to trucks with large packs and an increasingly standardised connector in a set position.
Standardising the connector position is opening up the standardisation of automated systems but brings challenges in making the technology cost-effective. At the same time, the technology is moving into the home and consumer markets, in domestic garages and for disabled drivers at public charging points.
Part of the impetus for developing automated systems is the weight of the charging cable. The higher currents for fast charging mean they have to be liquid-cooled, which makes them heavier and limits their practical length. As chargers extend beyond 350 kW, this will become even more of an issue for large EVs.
Depending on the use case there will be different versions for trucks, buses and consumer vehicles, says Johan Peters of ABB.
“We believe there are issues with wireless inductive charging, as you are limited in power,” he says. “At charging levels of several hundred kilowatts, the size of the coil becomes difficult to integrate, and there are also IP issues with a leading provider [which owns key patents]. We have built wireless inductive charging systems, and while the basic power transfer works well you need a lot of additional electronics for safety, and there are still no clear standards.”
“The OEM car makers allocated space for the inductive coil then used an underbody connector with a robot arm,” says Peters. “However, the location of the arm is new and the cars have to be modified, and there is no standard for that – there are maybe 20 companies that all have ideas about the connector. There are also robustness issues with the robot arm under the vehicle,” he said.
“We believe the only way to do it is to use the existing charging inlet and to build a cheap, small robot if you really want a low-cost production system,” he says.
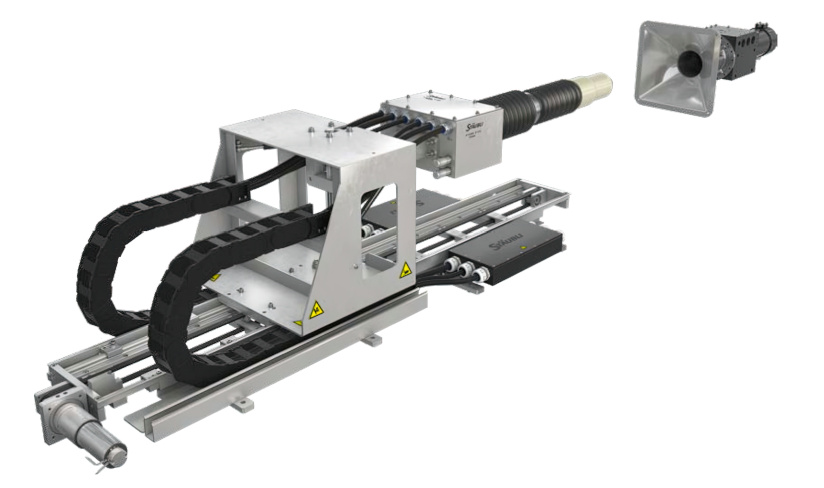
(Courtesy of Staubli)
This is not a system of linear motors such as that built by Siemens for charging (see below), but a series of actuators that hold the existing cable and connector that can automatically plug in and out of a vehicle.
This can easily scale to high power. “We aim to start with home power AC and then to trucks and fleets,” says Peters. “The home garage is a controlled environment so it’s a very nice use case.”
“We use a first-principles engineering approach. You need to design new actuators rather than use precision motors with high torque, and you need to limit the number of parts but still provide five degrees of freedom.”
The system also has to be small and very slim, with a reach of at least 1 m, and robust against misalignment to ±30 cm. The initial aim is to use any existing charger system in the home rather than public systems, although there are plans to combine the robot arm with the charger for an ‘all in one’ system.
“We question the use of robots on public charging sites but that will depend on the use case,” Peters says. “We can take any charger with the existing cable connected to the robot as the ‘hand’. An all-in-one system should be available in the next 3 to 4 years.”
The guidance system is based on a single camera to guide the robot arm with the charging cable and connector to the inlet port. While two cameras would provide stereo vision to enable depth perception, it is possible to use computer vision algorithms to locate the connector correctly using a single camera, says Peters. That helps to keep the complexity of the design down and reduces the cost. ABB is also working on the low-cost motors with soft robotics and a feedback loop.
The challenge is to do it all safely, plugging the connector in even if it or the inlet is dirty or it needs to be pushed or pulled hard. That will entail developing sophisticated algorithms to control the torque of the actuator, Peters says.
A key factor is the standardisation of the connector. That helps to simplify the development of the system. The CharIN standards group, which developed the standard for the CCS and CCS2 connectors, identifies two approaches to automating charging systems – ACDS and ACDU.
The ACDS (Automatic Connection Device for the conventional Side connection interface) uses the common vehicle inlet (CCS) on the vehicle side/front/rear that’s used for manual charging for automatic connection. The connection interface on the vehicle might include a moving part as well.
The ACDU (Automatic Connection Device for vehicle Underbody connection) applies an ACDU-specific connector located in the vehicle underbody so that the periphery of the vehicle is free while charging. In this application there might be moving parts in the vehicle and the ground unit.
“The issue is to plug the connector in, then the car will lock it,” says Peters. “The question then is who is in charge of locking and unlocking, the charger or the car?
“Coordination is also needed between the vehicle and robot, which could be a timer or other mechanism. When the car drives into the garage, the flap covering the charging port needs to open. Who gives the signal to start, the robot or the vehicle? There are communication channels from the car to a phone app or direct to be charger, but we need as an industry to agree on the channel and the protocol.”
There are also regional variations. With the CCS2 and Type2 AC connector in Europe, the lock is in the car. With CCS1 in North America the lock is in the connector, and you push a button to unlock. That would require another actuator and that makes the design more difficult,” Peters says.
Megawatt charging
A new standard called the Megawatt Charging Systems (MCS) is being proposed by the CharIN group as a global standard outside China for charging systems up to 3 MW and beyond. The current can go up to 3000 A at 1250 V with a connector that is a similar size to the existing CCS design. This is intended for a driver to plug it in, with a suitable cable weight and cooling.
MCS is defining the plug, which is more or less complete although it still needs a few tweaks, says Peters at ABB. The standard also defines the position of the charging inlet, on the driver side just behind the front wheel in a similar position to the gasoline filling cap.
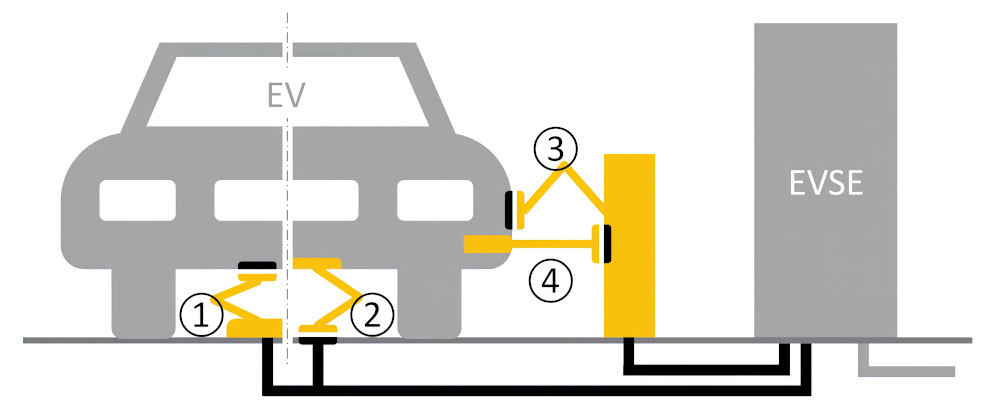
(Courtesy of CharIN)
The MCS Task Force started in 2018 to developed a higher-power system based on CCS. This group is also part of the Charging Connection group that is working on standards for light electric airplanes, ferries and other marine vessels. It was officially launched in June 2022 with an Alpitronic charger and a Scania fully electric truck. A technical specification to develop the requirements for a worldwide standard has been issued, and final publication of the standard is expected in 2024.
The standard defines a single conductive plug that supports bidirectional 1250 V and 3000 A power with the ISO/IEC 15118 comms standard and the UL2251 Touch Safe standard. As part of this there is a software-interpreted override switch on the handle that can let operators switch off if necessary, but also allows for software control.
A project called Hola, in Germany, is now looking at how MCS can be used for long-haul trucking in real-world conditions, and to gain more information about the requirements for a European MCS network.
“If the connector is the same and the location is the same this is perfect for automation,” says Peters. “This is the first candidate for widespread automation.”
ABB is working with Phoenix Contact, Bramar and Bruch on pilot projects later this year, with volume production of electric trucks due in 2024. “We have first samples of the cables for this and we are checking the weight,” Peters says. The length of the cable will still be limited to that level power, as the longer the cable the heavier it will be and truckers will be less able to use the system.
“The good news is that typically these trucks stop in the same place for charging. If we have a robot at the right height we can have a shorter cable rather than having it come down from the top of the gas pump, as it does at the moment,” he says.
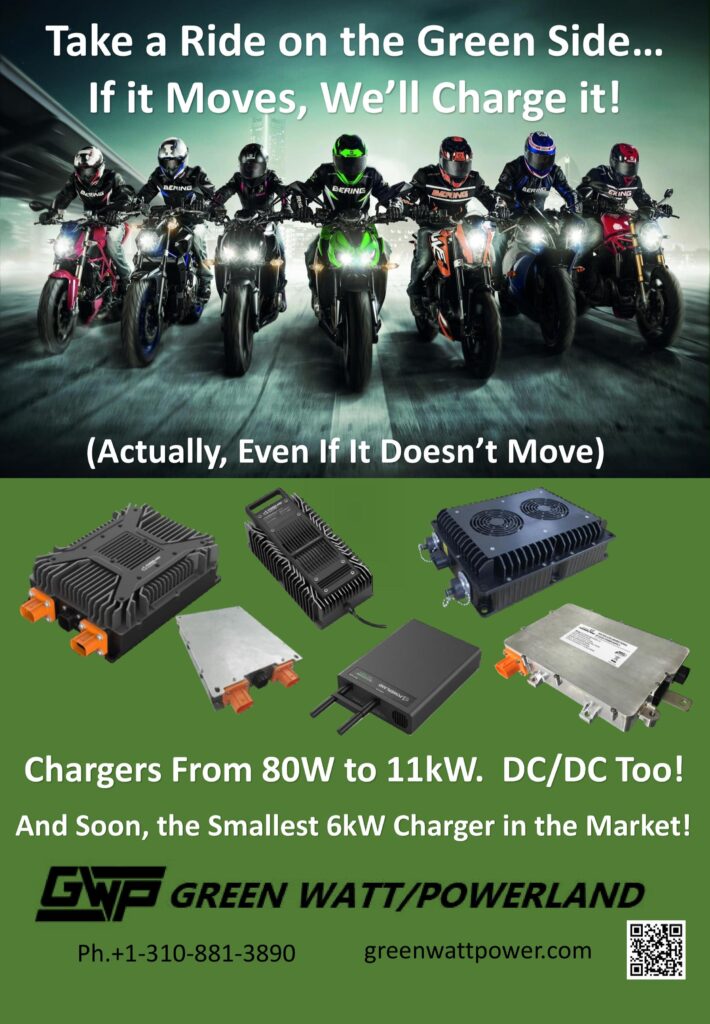
Other robot chargers
Researchers at the Technical University of Graz have developed a protype of a fully autonomous, mobile charging robot that finds its way independently to a parked electric vehicle and supplies it with energy.
The researchers worked with ARTI Robots and wallbox charger maker Alveri on the design. The platform orients itself independently in space using a Lidar sensor and moves towards a selected vehicle at up to 20 kph. The robot arm mounted on the bed of the robot guides the charging cable to the charging flap and docks there. After the fast charging process, the robot unplugs itself and moves away from the vehicle.
“For an automated system the process of refuelling or charging a vehicle is a very complex, millimetre-precise matter,” says Bernhard Walzel from the Institute of Automotive Engineering at TU Graz. He and colleague Helmut Brunner developed a stationary system in 2018, using multiple cameras, and have moved this technology to a mobile platform.
“Across Austria, there are currently around 8000 publicly available charging stations,” Walzel says. “This is a real stumbling block for the spread of e-mobility – constantly thinking about how far away the next charging station is doesn’t make for a relaxing drive. For this reason, we have to catch up on the charging infrastructure.
“A mobile charging robot, for example in multi-storey car parks, on Park & Ride lots or larger business parking areas, can make a significant contribution to this and take away concern about range and charging options,” he says.
The project, called CHARbo, used the CHASI robotic platform developed by ARTI Robots. This is a research platform that can be easily extended with sensor such as Lidar for laser ranging and can carry a payload of 80 kg.
This is enough to test out various robotic arms and carry a battery that will allow it to service up to 20 vehicles, but not enough to carry a battery pack to charge a vehicle; instead the robot pulls the charging cable with it to plug into a vehicle. This can provide up to 50 kW of power for fast charging.
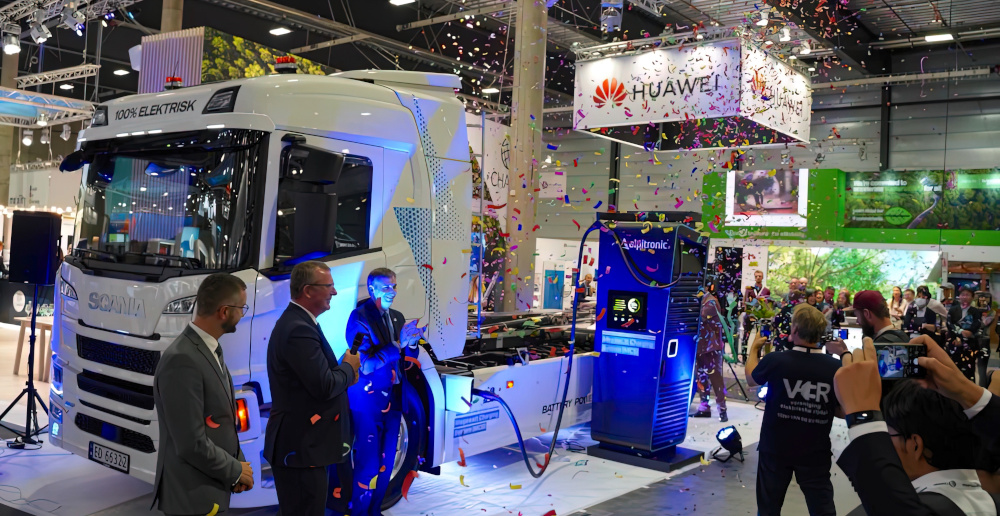
(Courtesy CharIN)
It is controlled by the Robotic Operating System running on a separate PC. The next stage of the project will be to integrate the controller into the robot.
Alveri has been working on a version with a simpler robotic arm.
“There is currently no robotic arm on the market for this application specifically,” says Brunner. “We therefore used a conventional collaborative industrial robot arm, which allows movement capabilities in a very large radius.
“However, we don’t need that much freedom of movement for the charging process, so there is still potential here for less weight and lower costs. The use of such a system only really pays off when a single robot is responsible for several cars and covers a defined area in a parking garage, for example.”
In multi-storey car parks, semi-public parking areas at universities, or customer car parks for example, there could in future be a designated parking area for EVs in which charging robots manoeuvre and supply the vehicles parked there. Adaptations in parking architecture might be necessary for this and legal and safety issues also need to be clarified.
Confidence in system safety is also key. “Several safety mechanisms have been implemented in the whole charging robot,” says Konstantin Mautner-Lassnig at ARTI Robots. “The mobile platform uses laser scanners to permanently scan the surroundings for possible obstacles and detects when an object gets too close. Then the platform immediately stops moving.”
A safety stop mechanism has also been developed to detect the presence of a hand between the charging plug and charging port.
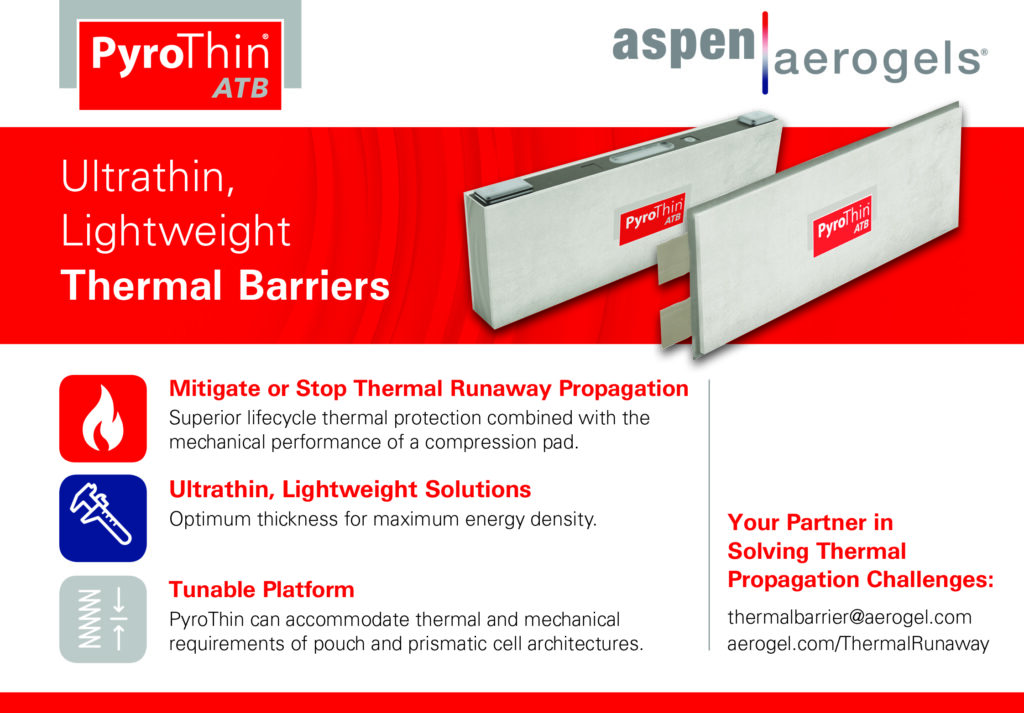
There are also system interface issues. Wetzel says, “At the moment, we still have to signal to the robot which car it should charge by opening the charging flap. The goal must be for the vehicle to signal its need for charging to the robot independently or that the driver activates a robot via an app.”
Volkswagen has also been working on a prototype of a similar self-driving robot combined with mobile energy storage devices it calls battery wagons. When fully charged, these are each equipped with an energy content of around 25 kWh.
One charging robot can move several battery wagons at the same time. When called via an app or V2X comms, the robot brings the energy storage device to the EV and connects them autonomously. With its integrated charging electronics, the energy storage device allows for DC quick charging with up to 50 kW on the vehicle.
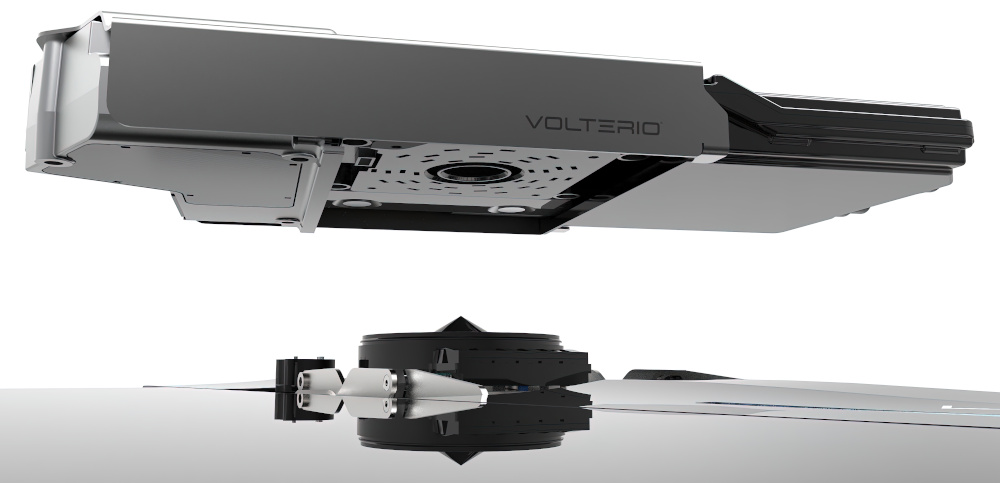
(Courtesy of Volterio)
The robot, which can also drive autonomously, is fitted with cameras, laser scanners and ultrasonic sensors. The combination of these not only allows the robot to carry out the charging process completely autonomously but also to move around freely in the parking area, to recognise possible obstacles and to react to these. Depending on the size of the parking area or the underground car park, several charging robots can be deployed simultaneously so that several vehicles can be charged at the same time.
Volkswagen has worked with robotics supplier Kuka on the robotic arm that connects to the vehicle being charged.
Automating underbody charging
Other developers are working on other systems to provide automatic connection devices for EVs from underneath the vehicle.
Volterio has developed a low-profile robot that sits underneath a vehicle and moves around to provide the connection. This consists of an onboard unit in the car‘s underbody and ground-based charging robot, with a comms system between the two.
The key is the design of a self-centring, high-power 360º connector design which ensures that the angular orientation of the parking EV does not matter. The charging robot can handle large parking misalignments of 40 x 40 cm.
The ground unit starts automatically to communicate with the EV’s onboard unit via a secure wireless LAN connection when approaching. When charging is requested, the ground unit automatically connects to the vehicle unit in the car’s underbody, guided by an ultrasound-based micro-navigation system. The charging process starts automatically or can be scheduled by an intelligent charging management.
The ground unit measures only 800 mm long, 420 mm wide and 68 mm high, and is automatically recharged. The company is also planning a version that can be embedded flat into the ground.
The self-centring connector can compensate passively horizontal misalignments of several centimetres as well as slight tilts (pitch and roll). A large cone helps to align the contacts, lifting up to a maximum height of 250 mm.
The connector is designed with a large conductor cross-section for a high current-carrying capacity, starting with 22 kW AC home chargers and 50 kW DC chargers, but it also supports higher power for fast charging, although that is not yet supported in systems in the home.
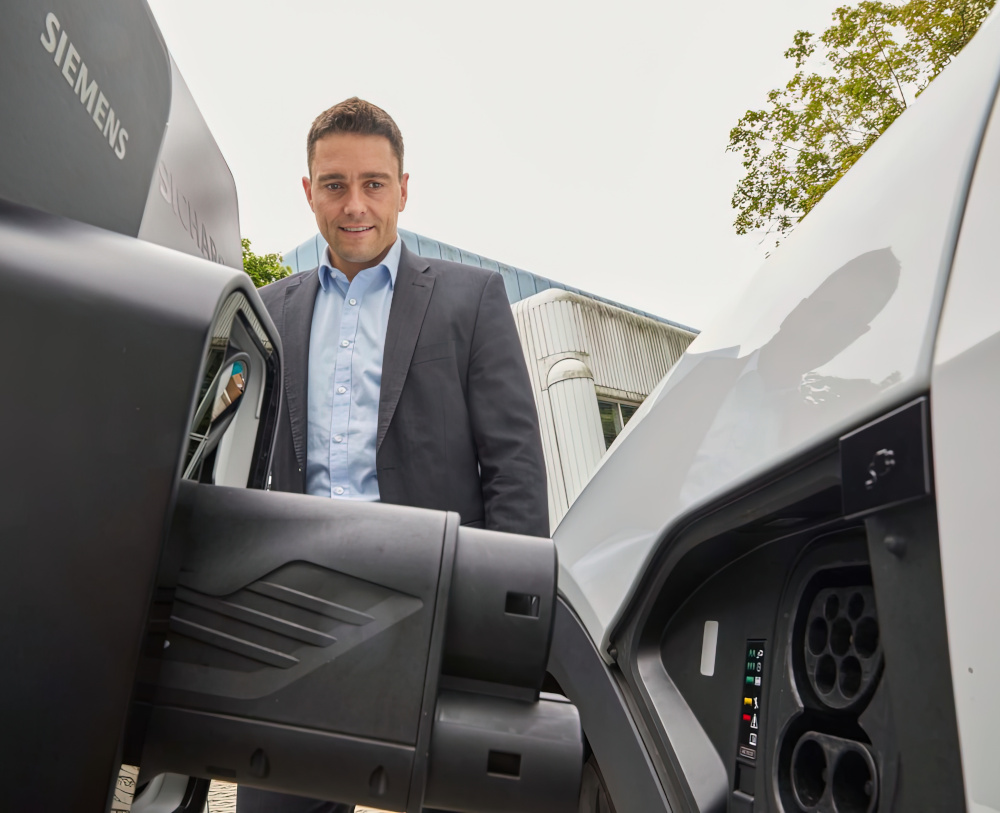
(Courtesy of Siemens)
Other approaches use existing CCS charging connectors and cables, and are designed to work with any type of EV, from a passenger car to a delivery vehicle or even a large truck.
“Depending on the type of vehicle, from sports cars to trucks, the charging ports are installed in different places on the vehicle and at different heights,” says Stefan Perras at the Siemens Technology research unit. “Sometimes they’re also tilted slightly upward, and the vehicles don’t always park at the same distance from the charging station, or they stop at a slight angle.
“The way the charging connector has to move in to connect to the port depends on all these factors. To make it work, we use optical sensors and AI that we’ve trained to recognise different charging ports in images and to determine their precise position and orientation. We use that data to calculate how the robot needs to move to connect the car to the charger, and the axes are controlled by our own automation technology.”
To accommodate these different types of vehicles, with charging points in different places and at different heights, one prototype system uses linear motor positioning system and computer vision.
This requires the vehicle to park in a specific place, and the linear motors position the connector in the x and y directions, guided by the computer vision system that targets the open connector port. An arm with the CCS connector then extends out to the vehicle to make the connection. The linear motors can handle any height or distance in the x and y directions, and are limited only by the length of the cable connecting to the charger.
This can provide up to 1MW fast charging using the same charging and comms technologies that are implemented in modern fast chargers.
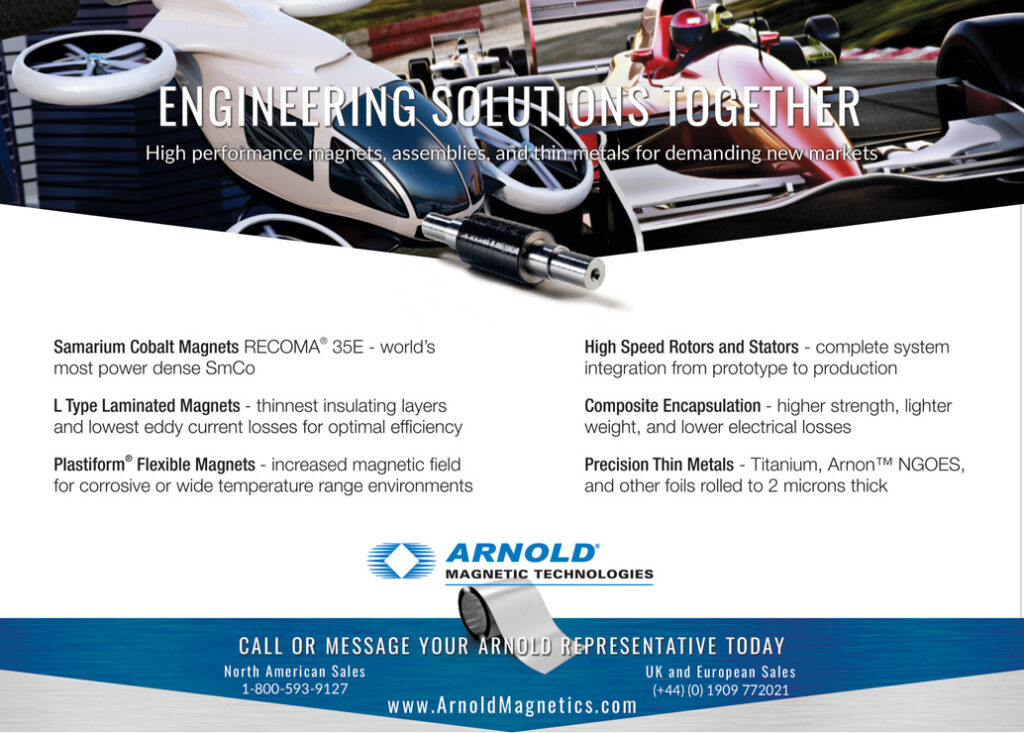
Conclusion
As the power requirements of charging systems increase and charging cables get heavier, so automated systems are becoming increasingly important.
Wireless charging systems provide convenience but can struggle with the power levels needed for trucks and buses, while the Megawatt Charging System is a key method of simplifying the charging process for these vehicles. But automated systems are also being aimed at the home charger market, with new actuator technology to simplify the process with consumer technology.
Connector standard for automated underbody charging
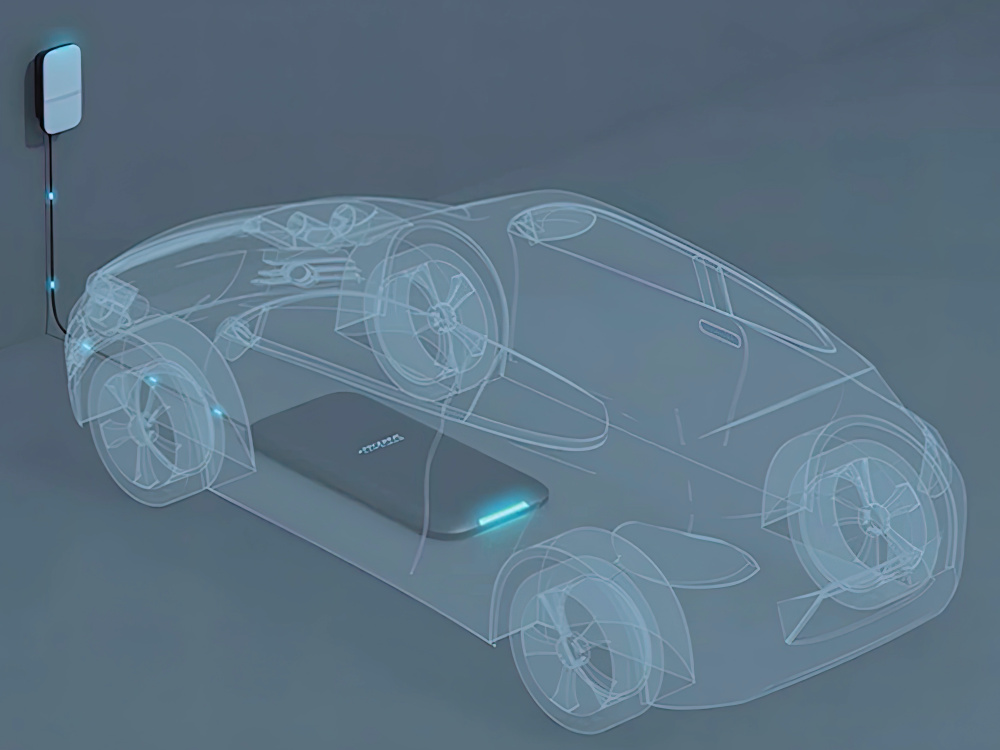
(Courtesy of Prodrive)
Although Prodrive has developed a range of wireless charging systems it has also branched out since 2018 into automated under-vehicle charging.
“It’s less complicated to do charging with a robotic system [rather than wireless],” says Nilles Vrijsen at Prodrive. “To integrate everything into one system with all the high magnetic fields and the detection systems and safety systems is a challenge for wireless but a robotic system is more robust. We are now looking at commercial vehicles, as the real added value of automated charging is in these applications, where vehicle availability is important.”
Prodrive’s system uses a 50 cm robot arm from the ground unit to lift the connector up to the vehicle. A drawer then opens up on the underbody of the vehicle to accept the connector and draw it in to make the connection. This reuses the same pins and plugs from the CCS2 connector on the side of the vehicle, but using the drawer approach reduces any misalignment and keeps the connector safe and secure.
“With one sliding motion it is possible to align the connector by the shape of the connector and the drawer,” Vrijsen says. This also helps with the safety, as the connector stays locked in the drawer until charging has finished.
The robot arm features an encapsulated magnetic field system for positioning. “We didn’t want to make it a camera system, as that is more expensive, and we have experience in the magnetic fields from wireless charging,” Vrijsen says.
The field system uses a 125 kHz transmitter coil with some modulation on the signal to subtract vehicle-dependent interference that comes from the metal in the underbody of the vehicle, and Prodrive is patenting this. “We found a way to compensate for the signals from the metal in and around the car by filtering this out.”
Vrijsen is chair of the CharIN ACDU underbody group, which is starting the standardisation process for the connector and the rest of the system.
“We are designing a connector comparable to the CCS2’s power range,” he says. “For underbody charging you have a different design envelope, you have a wider area but less height and you don’t interact with humans, so there are fewer safety issues.”
The new connector is intended to support power levels up to 400 kW DC (500 A at 800 V) but that’s not the target for the whole system, as higher currents need thicker cables. Instead it is aimed at opportunity charging for commercial trucks around 22 kW AC charging and 150 kW DC charging in places where there is limited space for fast chargers, as well as comfort charging for disabled or elderly users.
“Discussions on standardisation are ongoing for safety requirements of the ACDU system but the process has not officially started for the charging connector interface,” Vrijsen says. “In Germany they are preparing for this, and in CharIN we are having talks with suppliers preparing for this.”
ONLINE PARTNERS
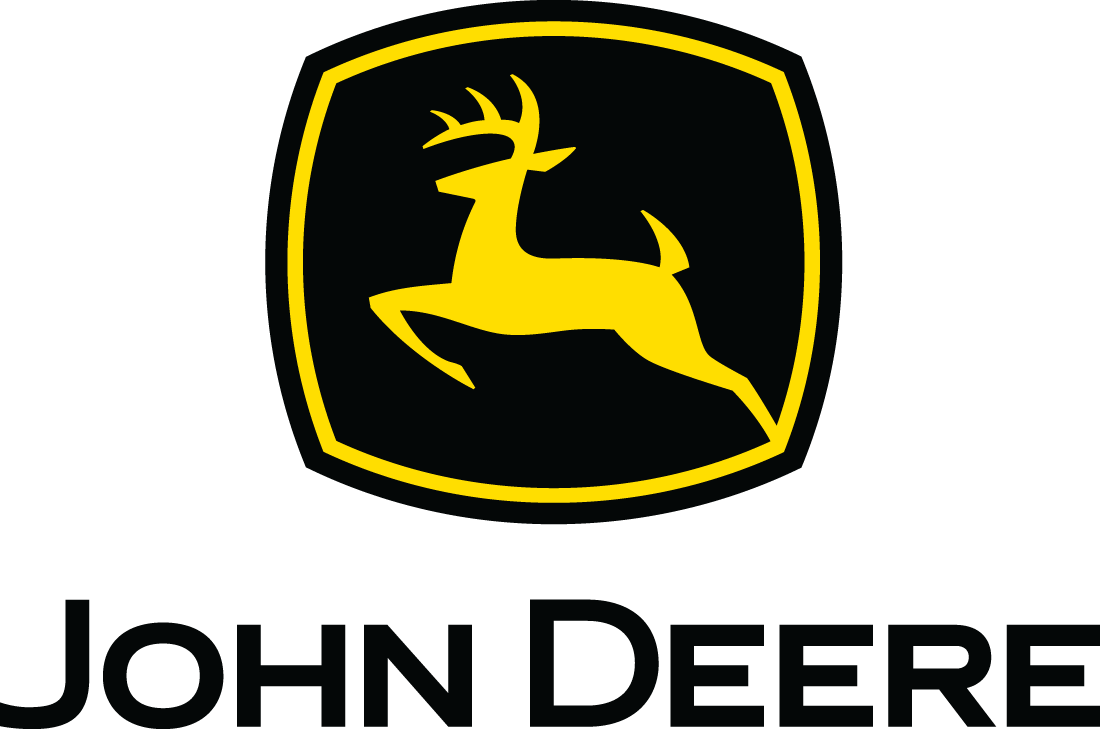
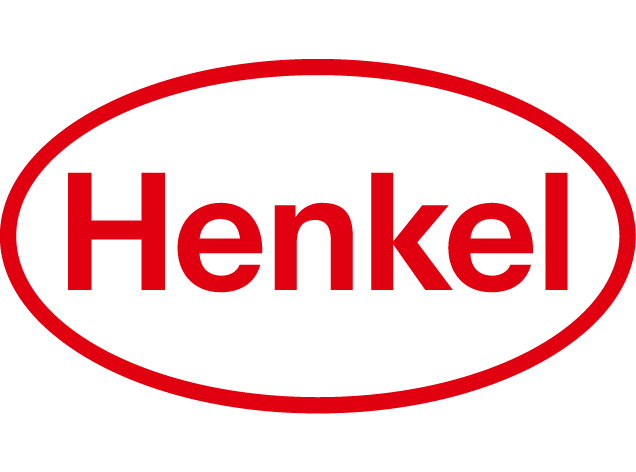
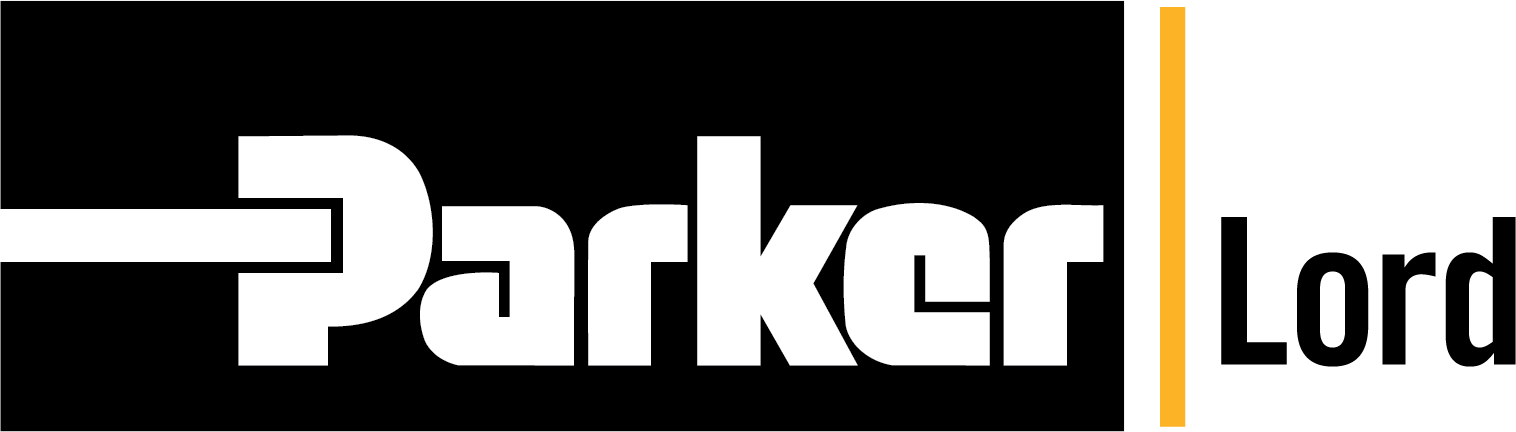
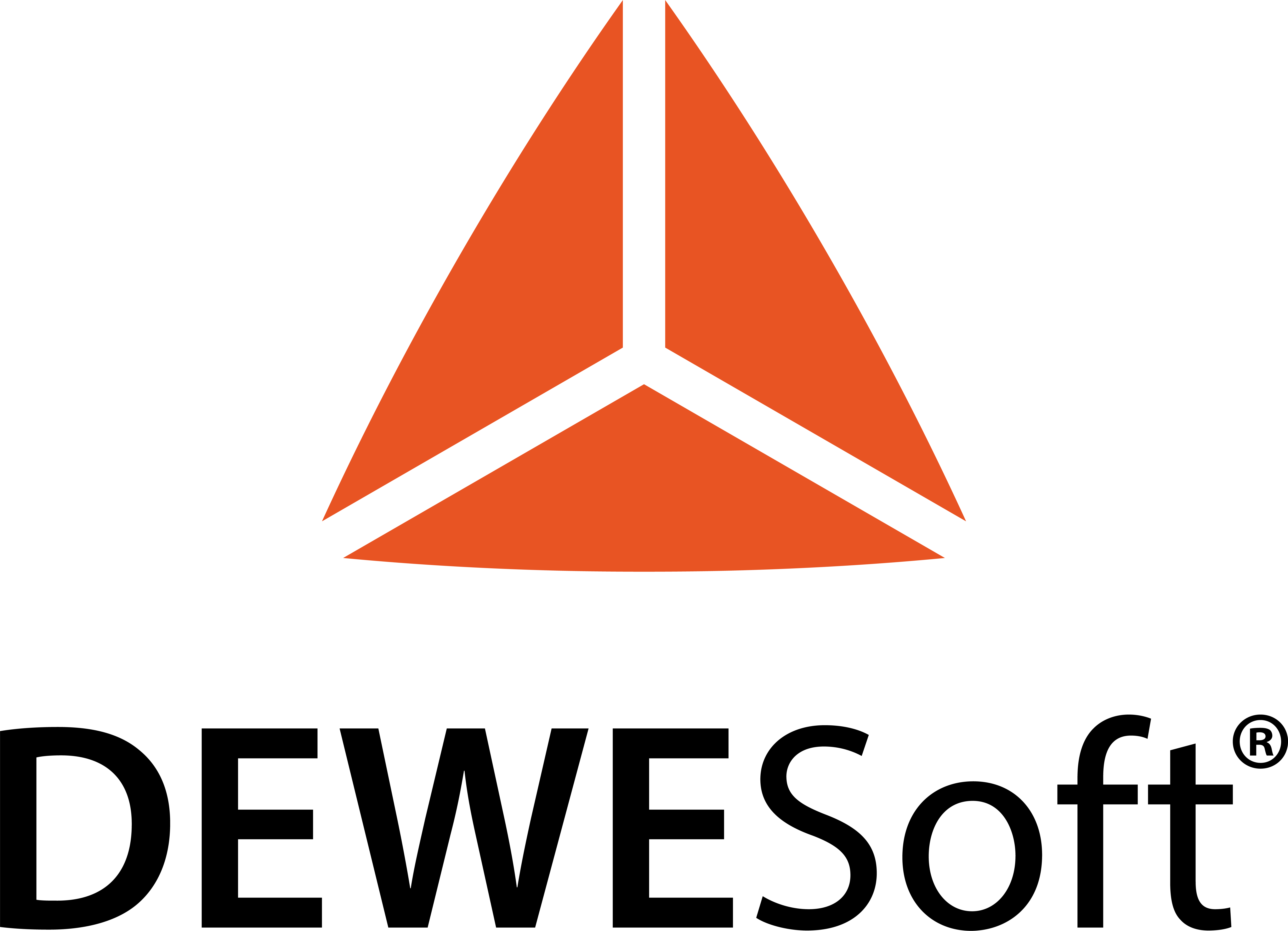
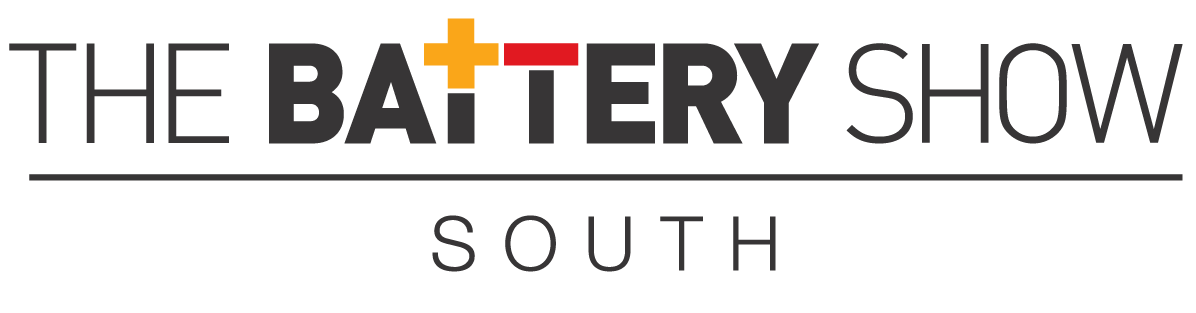
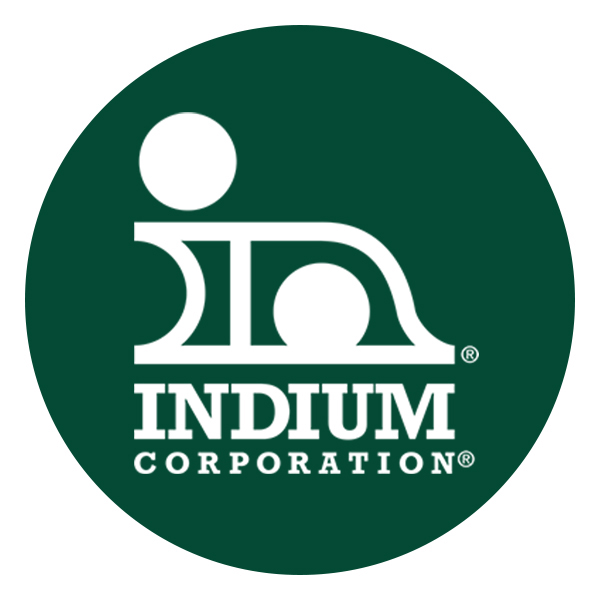

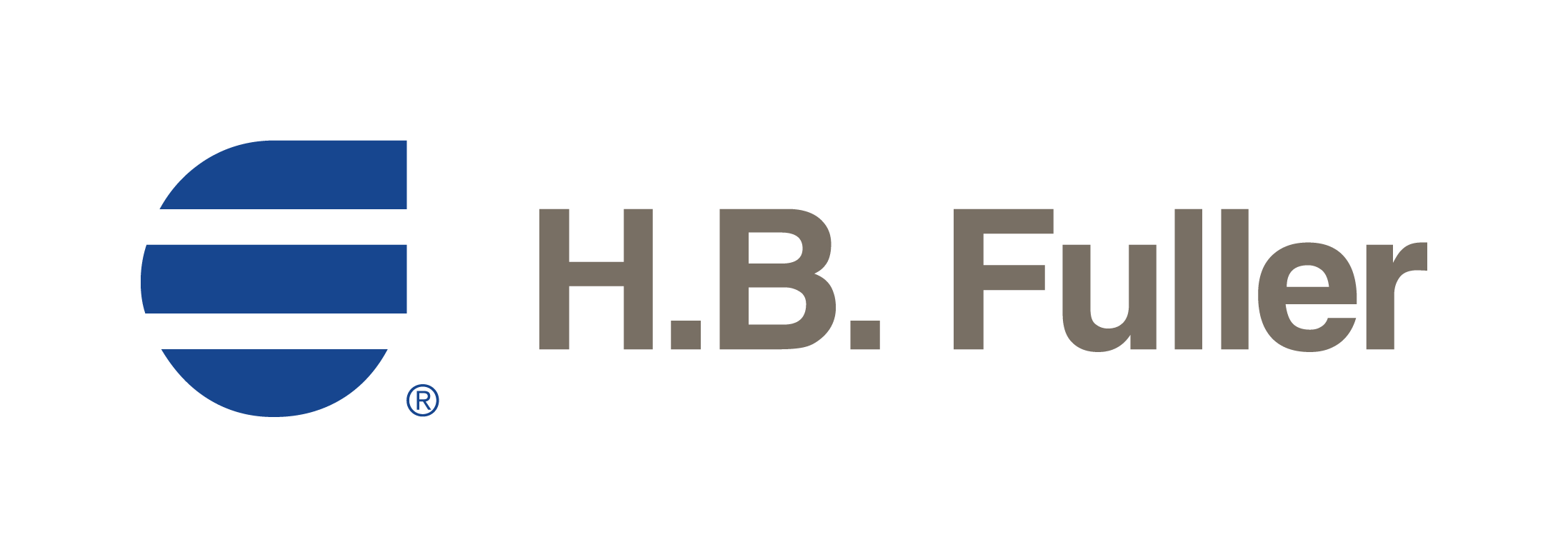
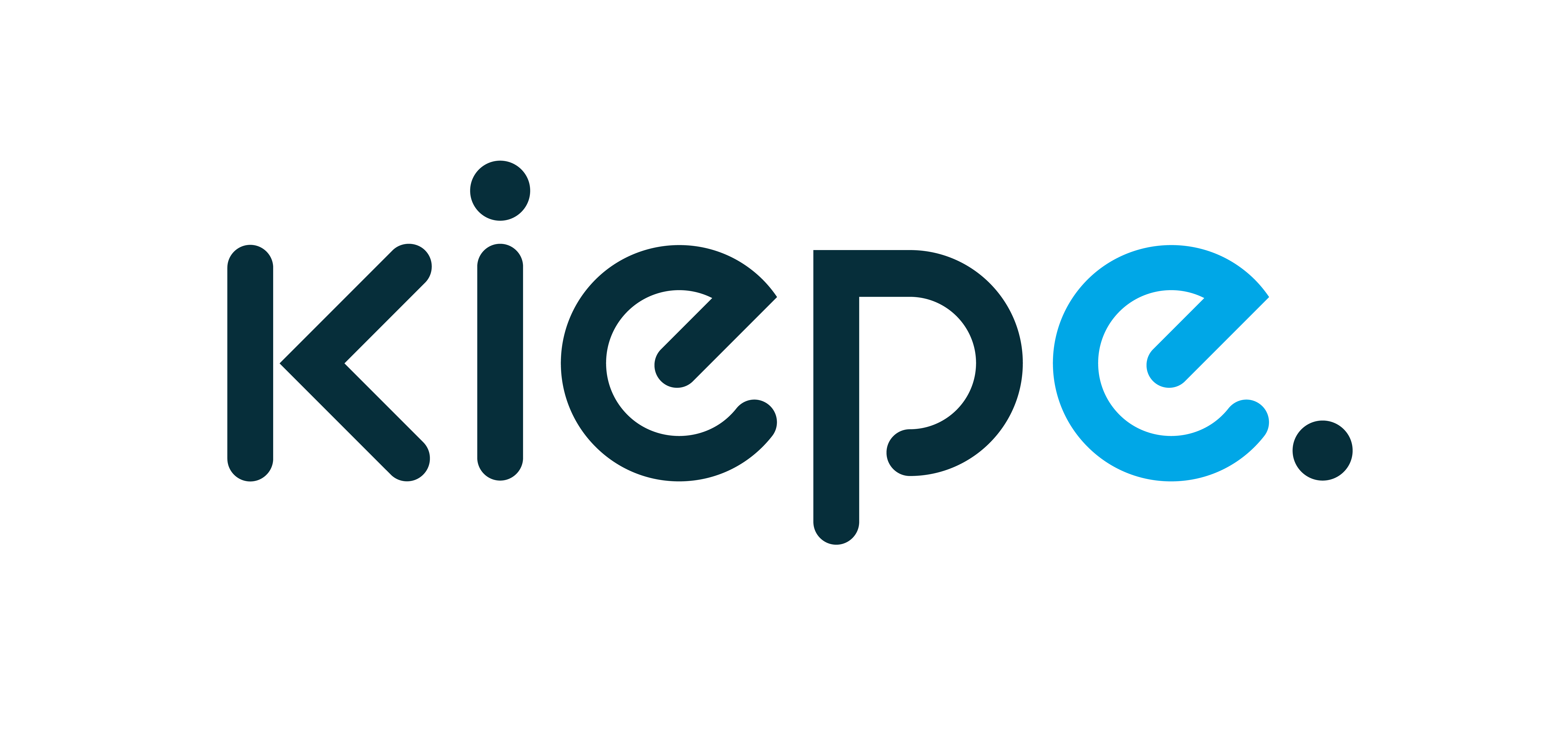
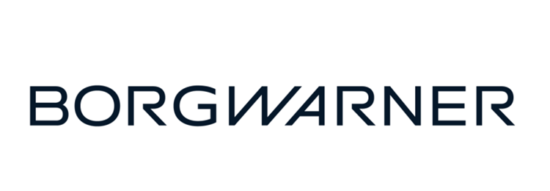