HVAC Systems
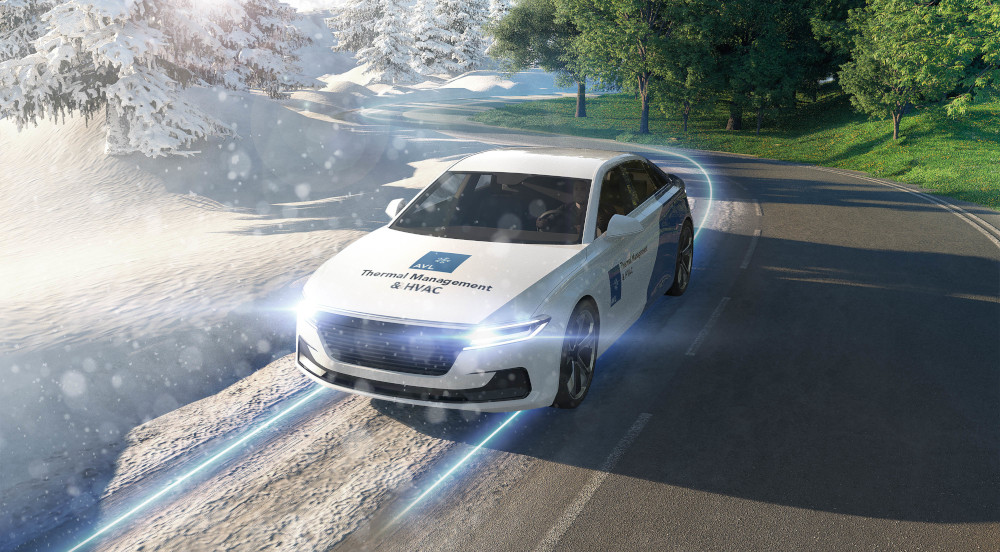
(Courtesy of AVL)
Taking the temperature
Peter Donaldson canvasses industry experts about the EV-specific issues surrounding HVAC systems
While most drivers of IC-engined vehicles are vaguely aware that running the air conditioning increases fuel consumption, such is the energy density of petrol and diesel that it has rarely been a major concern, although with fuel prices at record highs that is changing rapidly. Similarly, IC engines produce so much waste heat that drawing upon it to warm up the cabin on a cold day has a negligible effect on fuel burn.
It is a different story with EVs, however, so attention has turned in earnest to the energy efficiency of HVAC systems because they can have a major effect on range, particularly in extreme ambient temperatures or demanding driving conditions.
A wide range of innovations is being applied to the problem of efficiently maintaining pleasant temperatures for EV occupants. These include increasing integration with overall vehicle thermal management by moving heat between the battery pack, powertrain and the cabin, along with contact and radiative cabin heating that relies less on warming air. Further, variable-flow AC compressors driven by high-voltage motors, new refrigerants, electric coolant heaters, heat pumps, advanced phase-change materials and high-fidelity engineering simulations are also in the mix.
Energy consumption
Putting some numbers to the problem, in very high ambient temperatures – say 40 C – around 5-6 kW might be needed to cool the cabin and key components, which might reduce a typical EV’s range by 26-30%, according to an expert at an engineering simulation company. At very low temperatures (below -10 C or so) the effect can be even greater, as warming the cabin with a modern resistive heater using a positive temperature coefficient (PTC) material, but without a heat pump, can reduce the vehicle’s range by up to 50%, the expert says.
As only a few vehicles take these effects into account in the range calculation algorithms that keep the driver informed, the software’s predictions can be thrown off. “This is one of the main reasons why there is often such a big difference between the initial prediction and the range that the car actually achieves,” the expert adds.
The power consumption of the HVAC and thermal management systems depends greatly on both the ambient temperature and how the vehicle is being driven, experts from an automotive electrification specialist emphasise, as well as on the system’s key componentry – whether it includes an electric coolant heater and/or a heat pump, for example.
At moderate ambient temperatures (about 15-20 C) and the modest cruising speeds typical of urban traffic, demand for cooling or heating is very low because it is probably only the propulsion system that needs cooling, and the low power demand combined with the high efficiency of electric machines keeps energy demand small, they add.
In contrast, the largest energy demands are made at extremes of ambient temperature in the first few minutes of the journey, as the thermal management system works hard to achieve the target temperature ranges for the cabin and the battery.
High-performance driving at high ambient temperatures (around 40 C) also creates a high cooling demand, the experts say. In this case, the HVAC system is called upon to cool both the battery and the cabin, and with a high additional solar load, around 50% of the energy drawn from the battery could be needed for to cool components and the cabin.
Depending on the HVAC system’s configuration and the vehicle’s speed profile, temperatures at the other extreme (around -20 C) can see about one-third of the energy demand being allocated to heating. A further complicating factor is that even at temperatures of 5-20 C, dehumidification can be needed, so the heating and cooling systems must operate at the same time.
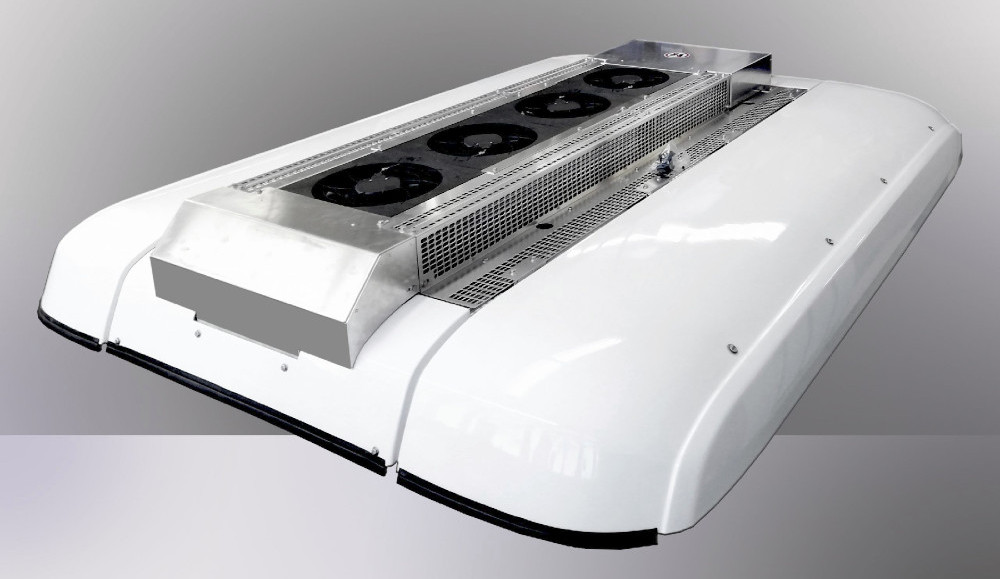
(Courtesy of Konvekta)
Although the vehicles and their operating profiles are very different, the story with vehicles such as electric buses is similar. One HVAC, battery and charging systems supplier has carried out tests on a small bus driving at a constant speed for 40 km with an outside air temperature of 0 C, and reports that 35% of the energy consumption went to HVAC, which included bringing the interior back up to temperature after passengers boarded and alighted.
The company also studied a typical last-mile parcel delivery service, noting that the system’s share of electrical energy consumption reached 50%.
Numbers like this show that HVAC can be an energy hog, which makes intelligent systems architectures and smart management software important ways to reduce its impact, along with efficient components and subsystems.
One HVAC control hardware developer notes that systems designed for EVs now typically feature multiple blowers instead of a less efficient single unit. The total blower power in an EV is typically between 200 and 600 W, much lower than the typical 500-1000 W seen in IC-engined vehicles, says the company.
There are also gains to be had from the use of more efficient heaters, an HVAC systems builder emphasises. In the absence of the abundant waste heat from an engine, most EVs now rely on electric air heaters and coolant heaters, which have a coefficient of performance (COP) of 0.8-0.9, meaning 1 kW of power consumed by the heater results in 0.8 to 0.9 kW of heat output.
As a more efficient alternative, the company offers heat pump systems. Essentially, instead of using energy to generate heat, these devices absorb existing heat from the ambient air and put it somewhere else. Natural thermodynamic flow transfers heat from warm places to cooler ones, which tends to even out temperatures. As with refrigerators and air conditioning systems, heat pumps reverse this flow by using energy applied to a working fluid to move heat from cooler places to warmer ones.
The working fluid, a refrigerant, runs in a loop around the heat pump system. Upon activation, a compressor draws in refrigerant vapour and increases its pressure and consequently its temperature to above ambient as it pumps it into a condenser (a heat exchanger) where it gives up heat to its surroundings, causing it to transform from a vapour into a liquid. From the condenser, it passes into an evaporator (another heat exchanger), where it absorbs heat from its surroundings and changes state once more from liquid to vapour.
As well as drawing heat from the ambient air, heat pumps can also be used to harvest waste heat from the battery and vehicle electronics to heat the cabin. Potentially, they can achieve COP figures of 2 or 3, meaning that 2 or 3 kW of heat can be moved to where it is needed for every 1 kW of power used in the process.
System architecture and control logic
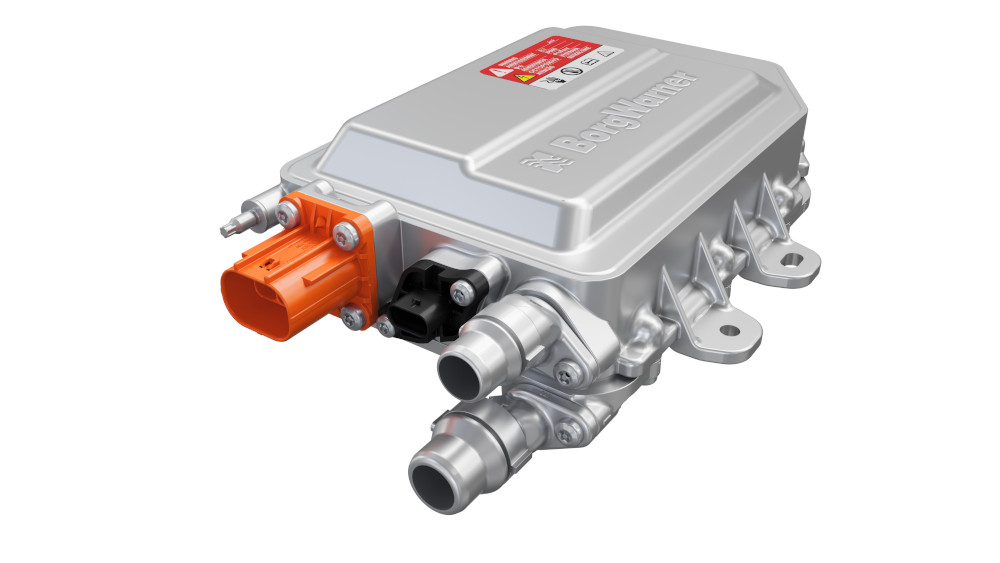
(Courtesy of BorgWarner)
In the past, our engineering simulation expert notes, the engine cooling and cabin heating constituted one system, while the air conditioning was an entirely separate loop, a situation reflected in vehicle OEMs’ separate engineering departments for them. That has changed with EVs though, in that the need for precise thermal management of the battery, and the relative scarcity of energy, requires close contact between the coolant and refrigerant loops.
Integrating these systems, and the need for precise control of the flow of energy between them via an array of pumps, valves and heat exchangers with a large number of operating modes brings much greater complexity, our expert argues. It is therefore vital to characterise the system early in a vehicle’s development, he stresses, adding that a lot of virtual calibration and validation is needed to make sure all the modes run smoothly and result in a well-balanced system.
The expert from our HVAC, battery and charging systems supplier says it is also important to make the most of ‘free’ energy such as waste heat for HVAC, even though there is less of it available in EVs than in IC-engined vehicles. One way to minimise the system’s demand for energy from the battery, he points out, is pre-conditioning both the battery and the cabin during charging, so the energy to do that comes from the grid.
Just as the absence of the engine enables EV designers more cabin space and flexibility with interior configurations, it also creates opportunities to relocate thermal systems, the HVAC systems builder points out. For example, some automakers might opt to move some or all of the HVAC equipment to the powertrain electronics bay – formerly the engine bay.
EV thermal management systems consist of different sub-loops, our automotive electrification specialists note, and in most of them the HVAC system plays a role in battery cooling. This is usually indirect cooling, in which the HVAC and battery cooling/heating circuits are coupled with a heat exchanger, while in a few cases the HVAC system is combined with a heat pump function.
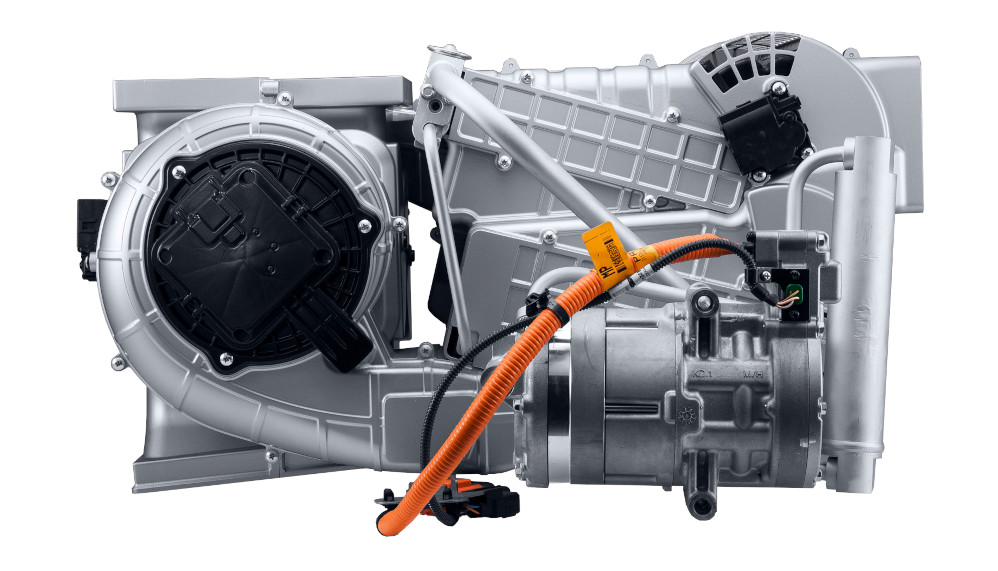
(Courtesy of Hanon Systems)
While HVAC compressors and cooling system pumps in most IC-engined vehicles are mechanically coupled to the engine, and are either on or off, their electrically driven counterparts in EVs can be commanded to run at any speed to meet cooling, defogging and heating demands, they explain.
Because the heat in EV powertrains tends to be concentrated in the traction inverter and the battery pack, a good first rule of the thumb is to distribute cold/heat generation and use a set of diversified technologies for each case, according to an expert from a control software and hardware provider.
Heat pumps are attractive, he adds, because they can be managed with very efficient field-oriented control (FOC) algorithms.
Used in high-performance motors of both AC and DC types, FOC is a means of decoupling the magnetising flux and the torque-producing flux generated by the stator current so that torque and therefore speed can be controlled independently. It enables motors to run smoothly over a wide speed range, generate maximum torque from zero rpm, and accelerate and decelerate quickly.
The power electronics to drive pumps consist of optimised three-phase inverters with efficient power stages made from IGBT and SiC switches, our expert explains. As HVAC moves towards higher bus voltages with faster control loops and motor speeds, the use of SiC is increasing. For comfort features such as car-seat cooling and heating, a smaller dedicated heat pump can be placed in the seat.
Less expensive alternatives include PTC devices switched via simple silicon-based relays with accurate current control. Although such devices tend to be more power-hungry, there are ways of minimising the impact of that. For example, resistors are typically used for defrosting windows, because they work quickly, so normally they are powered up for only a very short time.
Together with distributed cooling and heating, new materials with better insulation and heat transfer properties are playing an increasingly important role in overall thermal management within EVs.
Control electronics typically consist of a system controller, microprocessor and motor driver, the expert from our HVAC control hardware developer explains. He adds that the company also offers solutions in which the motion control algorithm is integrated, eliminating the need for a microprocessor.
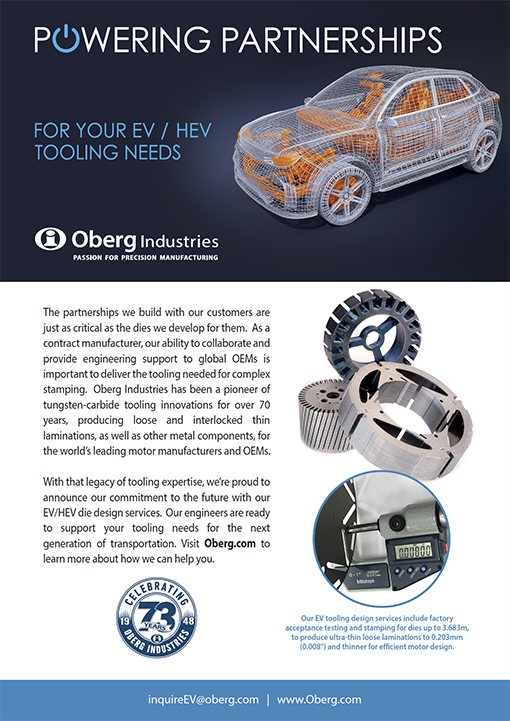
Motor drivers with integrated algorithms are well-suited to systems with external ECUs, he continues, while being quicker to market than those that need a microprocessor and relieving the customer of the need to write any code.
Where a microprocessor is available, it might be able to handle such drivers’ interaction with a CAN bus, although a system-on-chip device with all the required functions on a single piece of silicon can be a viable alternative, the expert says.
Evolving comfort
Continued development of HVAC and climate control systems in EVs is focused on meeting occupant comfort requirements while minimising energy consumption. Our engineering simulation expert sees a lot of system designs during their evolution, and he believes heat pumps will grow in importance as the temperature ranges that are comfortable for the powertrain and the occupants come closer together than they ever could be in IC-engined vehicles.
There are limits to this convergence, however, as our HVAC, battery and charging systems expert points out. Modern battery cells ‘feel’ best at 25-35 C, the electronics typically tolerate temperatures of up to 90-100 C, whereas HVAC systems need around 7 to 60 C. This is one of the key challenges inherent in closely integrated thermal management/HVAC systems.
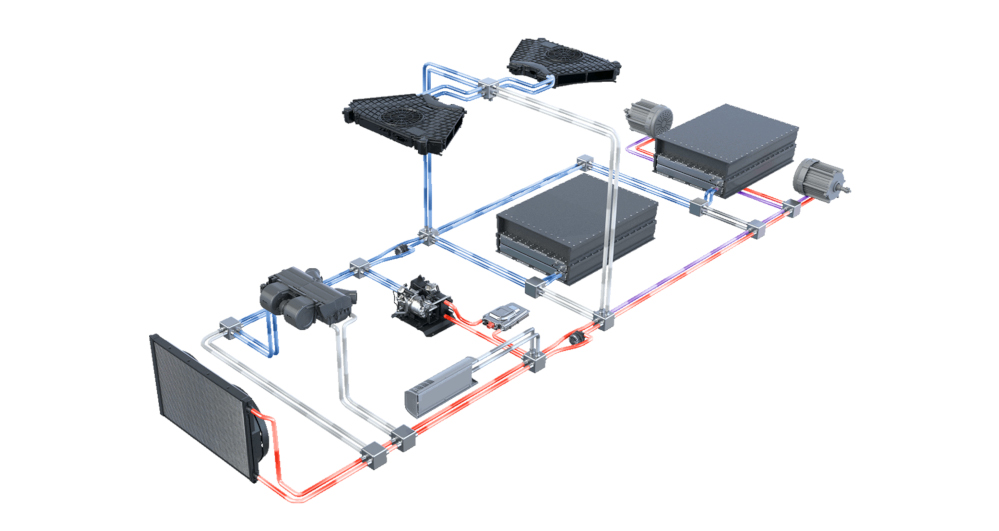
(Courtesy of Webasto)
An efficient heat pump solution, the simulation specialist reckons, could potentially result in a 30-40% energy saving over a system based on PTC heaters, adding around 20-30% to the vehicle’s range. However, it is possible to end up with heavy, complex and expensive systems, so the ability to compare alternative designs virtually before any hardware is built is very important, he argues, for which the company provides benchmarking.
Further savings can come from localised heating and cooling strategies within the cabin, the expert from our HVAC systems builder says. This involves targeting occupied seats and the space around them with, for example, internal heating or cooling of the seat and steering wheel, and radiative or convective cooling from local interior structures.
Our HVAC control hardware developer expects HVAC blowers to remain common in EVs, because they are critical for driver comfort. He adds that systems are likely to feature multiple blowers to serve separate climate control zones more efficiently.
The simulation expert also sees systems growing in complexity as vehicle designers add more such climate control zones. Four-zone systems are already common, and he reports the implementation of five- and six-zone systems in larger Chinese vehicles, for example. Along with automated functions such as seat occupant detection and air quality sensing – the latter influencing whether the system switches to recirculation, for example – multi-zone systems will make even more demands on the control logic, he says.
Another effect of the absence of an engine is that the HVAC and climate control system becomes a much more significant source of noise, vibration and harshness (NVH), impacting the design, location, installation methods and control logic of compressors, pumps, fans and valves, our engineering simulation expert says.
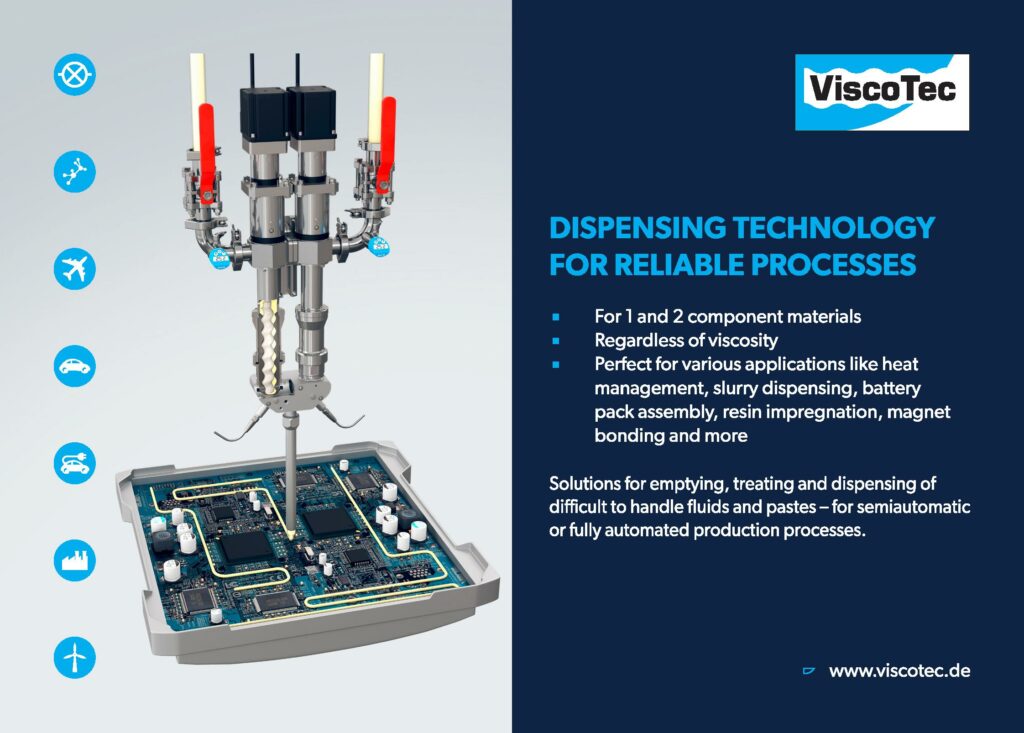
Towards predictive control
Our automotive electrification specialists add that predictive control will be increasingly important for minimising energy consumption, predicated on a number of factors including the ability to take future driving conditions into account.
With multiple components interacting in feedback loops, HVAC systems are inherently complex, and their integration with powertrain thermal management adds to that complexity. Successful predictive control relies on accurate models of system behaviour and on knowledge of driver behaviour, which might be based on a profile or draw on a route plan that takes into account passenger stops, work breaks and traffic and weather information, for example, as well as the likelihood of the battery needing a fast charge en route.
Independent measurements and comparisons show a possible saving potential of up to 50% of the current required average HVAC energy consumption, according to the HVAC, battery and charging systems supplier.
Battery cooling during fast charging could be a major driver pushing towards predictive controls with integrated thermal management and HVAC systems in particular, the simulation specialist notes, pointing to a potential need for up to 10 kW for the process. It might be necessary to predict a fast charging event so that the system can heat or cool the battery in advance, so that the BMS will allow charging at the highest rate to begin as soon as the vehicle is plugged in.
That might be a way of avoiding unnecessary complexity, cost and weight, he says, exemplified by the installation of two compressors for extra cooling capacity, which some vehicle OEMs have already enquired about.
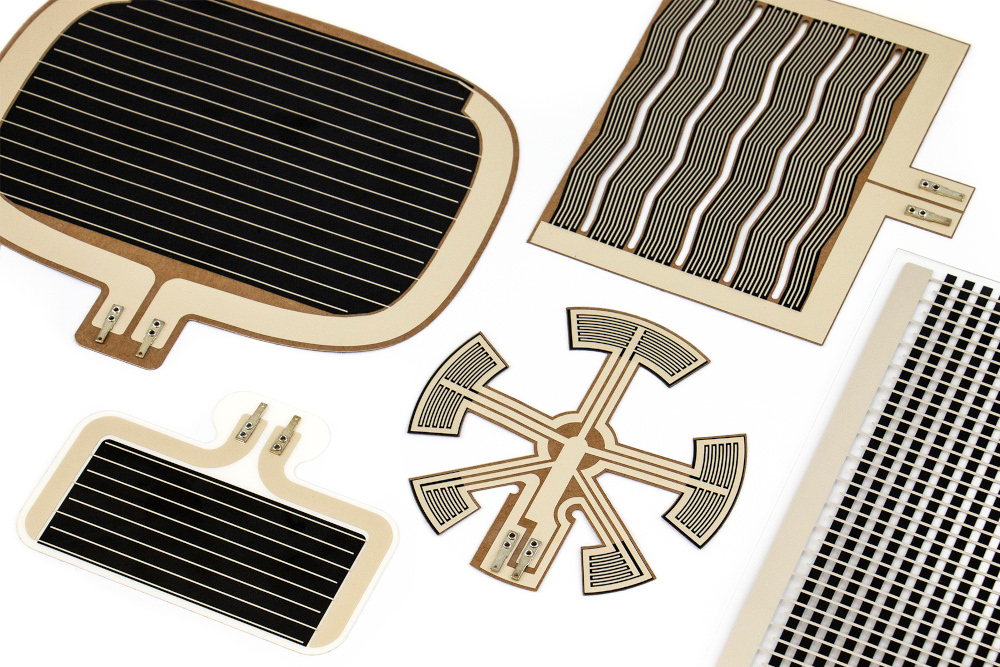
(Courtesy of Termico Technologies)
Integration implications
Design and implementation of such closely integrated systems is challenging, and the practicalities can make attractive ideas hard to realise, the expert from our control software and hardware provider cautions.
For example, liquid cooling is an option for traction inverters, but the design of individual systems depends heavily on the vehicle maker and the EV model. He notes that it is easy to imagine a heat exchanger with a blower integrated into the traction module’s cooling system, but a distributed cooling/heating installation could be easier to design, maintain and optimise for cost than a centralised one.
He adds that implementing a ‘super-cooler’ that can cope with both the traction inverter and the passenger cabin is quite challenging. Similarly, a blower fan is feasible for a battery pack but a bit more complex if the batteries are spread around the vehicle in separate modules, which they might be in a module-to-chassis architecture, for example.
Our HVAC systems builder notes that integrated systems are attractive to vehicle OEMs and suppliers alike. OEMs benefit from lower engineering, assembly and component costs, along with optimised thermal management, while suppliers can gain a competitive advantage from going beyond offering components, modules and subsystems, and working with customers to manage trade-offs in terms of efficiency and cost.
The challenge is to reduce the number of individual components, which reduces material and assembly costs for OEMs, while balancing the requirement for more complex controls and algorithms to meet the heating and cooling demands from multiple subsystems, he adds.
Fluid working
One of the fundamentals of integrated HVAC and thermal management systems that use liquids to move heat around is ensuring the efficient transfer of that heat between the different working fluids, which typically are water-glycol coolants or hydrofluorocarbon (HFC) refrigerants.
The automotive electrification specialists stress that this requires compact heat exchangers that are optimised for efficiency in the most important operating modes, along with heating/cooling circuits with short and isolated ducting, and accurate control of the flow rates in the coolant and refrigerant loops to optimise the heat transfer.
Although this is not a problem technically, it is not yet easy to offer generic solutions that are fully cost-optimised, our HVAC, battery and charging systems expert notes. While efficient, low-cost systems can be provided for vehicles that are built in large volumes and have clearly defined applications, they are not yet available for mid- and low-volume applications. These need individual parts with higher costs and lower availability, although the company expects that situation to change in the near future.
The use of battery chillers has brought an additional challenge to the refrigerant loop in closely integrated systems, as they have to be powerful and very efficient to overcome the thermal resistance of a large battery pack, our engineering simulation expert says.
Chiller and HVAC efficiency looks set to be improved by the return of CO2 as a refrigerant. Known as R-744, CO2 was in use more than a century ago before being replaced by chlorofluorocarbon and, later, HFC refrigerants that worked at lower pressures and were therefore easier on the machinery – as well as being less destructive of the ozone layer, in the case of HFCs. Although an effort by Mercedes to switch to R-744 stalled, Volkswagen has gone ahead, he reports, and others are likely to follow.
Even though CO2 is regarded as the main culprit in climate breakdown, it has a global warming potential of 1 (because it is the standard for comparison), which is much lower than that of R-134A (tetrafluoroethane) at 1430 and even of R-134A’s replacement, R1234 YF (2,3,3,3 tetrafluoropropene) at 4.
As a refrigerant, R-744 is attractive because of the low temperatures the systems using it can achieve. While R-1234 YF gets down to -20 C, CO2 systems can achieve -30 C efficiently.
The price paid for this benefit is system operating pressures at around 120 bar, putting higher stresses on key components and connections. That is likely to mean larger, heavier, more power-hungry and pricier components. It will also be more difficult to keep compressors quiet, adding to the NVH challenge.
As the compressor will have to meet both cooling and heating demands, and because it will run even when the vehicle is stationary and it is one of the few noise sources in an EV, its NVH characteristics and its COP have become critical attributes, our HVAC systems builder says.
He also points out that the added EV operational modes with greater cooling demands require more powerful electric motors to drive higher displacement compressor mechanisms, while trying to maintain or improve overall efficiency.
Our simulation specialist adds that more powerful, faster-spinning electric motors are likely to need liquid cooling themselves (perhaps using oil), while compressors may need redesigning to make the most of the wider speed ranges the more varied cooling/heating needs demand and the motors can deliver. Ideally, they should operate efficiently at both low and high refrigerant flow rates.
Advanced designs might include scroll compressors using liquid injection and two-stage compression to achieve high efficiencies, notes our HVAC, battery and charging systems expert.
Overall efficiency is the most important goal in optimising compressors and their motors for EV use, says our control hardware developer. As the compressor is the largest power consumer in the system, any improvement in efficiency translates directly to increased vehicle range, he adds.
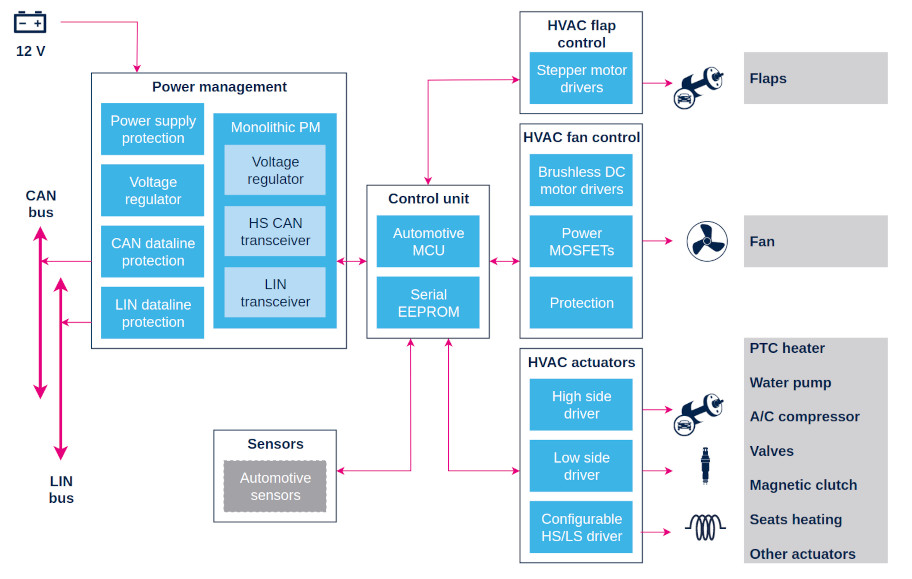
(Courtesy of STMicroelectronics)
Raise the voltage
One important way of making HVAC compressor systems more efficient is to power them with high-voltage motors. Compressors typically absorb 4-6 kW, which is more than the 12 V network can deliver without generating excessive currents, our automotive electrification specialists say.
Running the compressor motor at propulsion system voltages (400-800 V or more) might be preferable, they add, as the lower currents for the same power allow cables and connectors to be smaller and lighter.
That also allows the compressor motor to re-use the available bus voltage, avoiding additional voltage conversions that reduce overall efficiency. However, higher voltages require more expensive power modules and more stringent isolation requirements, our control software and hardware expert notes.
The HVAC, battery and charging systems expert says using the main battery voltage for the large power consumers is essential if the system is to be energy- and cost-efficient. He stresses that transferring 30% or more of the battery capacity to a lower voltage will not only reduce efficiency but also produce high additional costs because of the need for the conversion hardware itself, for example.
On the buses
HVAC systems for large public service vehicles such as buses present their own efficiency challenges, our engineering simulation specialist says, in avoiding the loss of large amounts of heated/cooled air every time passengers embark or disembark, for example, suggesting the need for some kind of airlock and an efficient recirculation system. However, there are limits to the use of recirculation as window fogging has to be avoided, as does avoidably exposing occupants to airborne pathogens such as Covid.
Buses might benefit even more than cars from heating and cooling targeted on occupied seats rather than conditioning the entire volume of air in the vehicle, he adds, along with predictive controls informed by the route plan.
If decentralised HVAC systems are more efficient for a single vehicle, we can imagine that this is even truer for larger vehicles such as buses, the control software and hardware expert comments.
Besides their higher energy consumption for heating and cooling compared with cars, bus HVAC systems tend to have greater distances between their air outlets, despite the need to provide a homogenous climate for the passenger cabin, according to our HVAC, battery and charging systems expert. Buses also need separate climate control zones for the driver and passengers.
Furthermore, airflow needs to be controlled very carefully in buses because, for example, passengers have different ranges of tolerance to it, while bus systems must be easier to service and repair than is normal in cars, he adds.
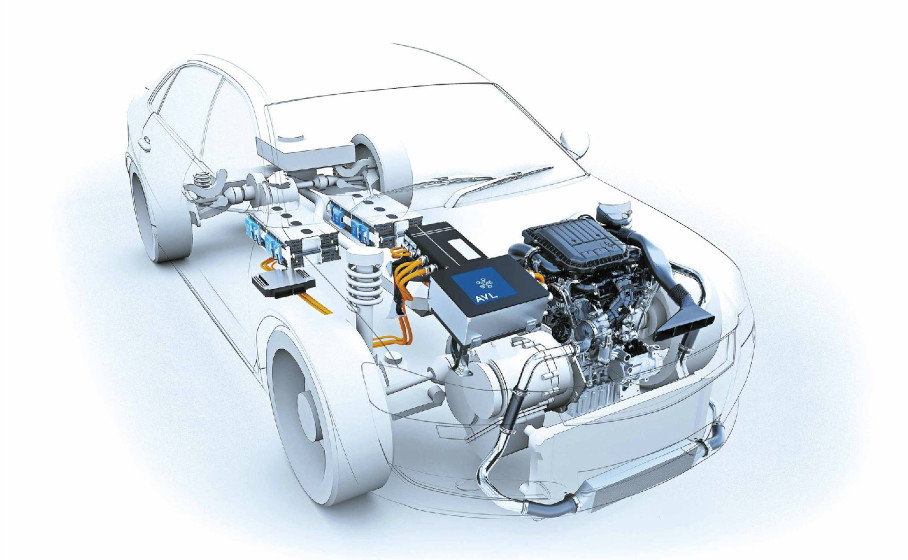
(Courtesy of AVL)
Simulate early, and often
HVAC has such an impact on an EV’s energy efficiency, and an intimate relationship with the powertrain thermal management system, and because multiple climate control zones with targeted heating and cooling have to be integrated, the system has to considered very early in the vehicle’s design life, all our experts agree. Combined with significantly truncated development timelines, this makes the use of engineering simulations essential.
Our simulation expert recalls that 6 or 7 years ago, a vehicle development project might run for 4.5 years, with prototypes available for at least 2.5 years in which to validate and calibrate the thermal management and HVAC systems. These days, however, everything has to be done in not much more than 2 years, he notes.
For this reason, his company has developed a highly front-loaded approach using virtual validation of entire simulated vehicles, supported by a ‘model connect’ platform that enables all its own simulation software tools to be linked together, along with other tools used by vehicle OEMs, for example.
Using component data gathered from tests or simulations, a complete HVAC system can be modelled with all the subsystem interdependencies at very early stages of the development process, our automotive electrification specialists confirm. That speeds up the optimisation process.
Cooling layouts can be easily modified and evaluated, components can be easily exchanged or scaled as needed, and control strategies adjusted and tested. What’s more, simulations enable thorough exploration of the influences of design, boundary conditions and drive profiles on overall efficiency, performance, durability, safety and comfort.
As well as enabling developers to evaluate performance early on, virtual testing also allows them to address other critical areas such as NVH and long-term durability before investing in physical prototypes to test. It also reduces overall development time and cost by minimising the number of physical prototypes required, the HVAC systems builder notes.
With HVAC specifically, he adds, CFD is valuable for understanding airflow, enabling the development and validation of more compact systems for a given level of performance.
Applying FEA is particularly useful for ensuring long-term durability and minimising NVH in HVAC systems. For example, FEA simulations help engineers determine the optimal number and location module attachment points to reduce noise and vibration. Drilling down further, the design of HVAC module doors (which open and close to manage airflow) can be analysed to ensure smooth movement and proper sealing, robustness and elimination of objectionable whistles or tones, he says.
Future HVAC and climate control development will be characterised by a relentless drive for efficiency while reducing complexity and cost – goals that can conflict with each other, so engineers will have to consider the inevitable trade-offs very carefully.
Acknowledgements
The author would like to thank Dan Jacques at Allegro Microsystems Michael Bires at AVL, Wolfgang Wenzel and Anita Bongards at BorgWarner Corporate Advanced Engineering, Steve Clarke at Hanon Systems Max Vizzini at STMicroelectronics, and Leopold Gurtner at Webasto Group for their help with researching this article.
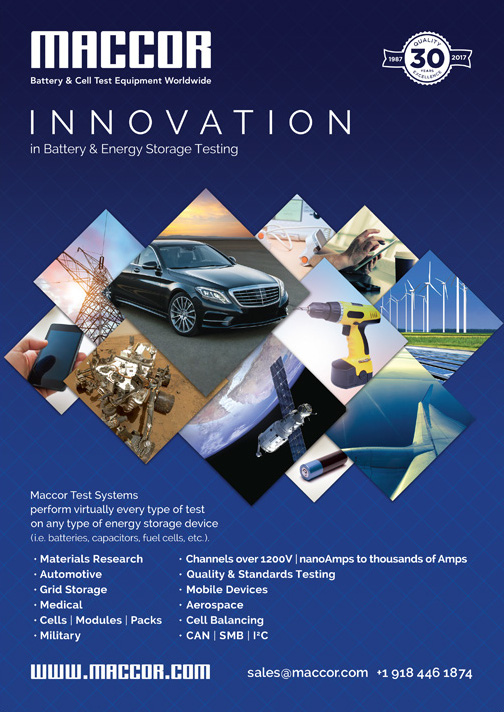
Some suppliers of HVAC systems
Austria
AVL
Italy
STMicroelectronics
France
Valeo
Germany
Eberspracher
Mahle
Webasto Thermo & Comfort SE
South Korea
Hanon Systems
USA
Allegro Microsystems
BorgWarner
Gentherm
ThermoAnalytics
–
+43 316 787 0 www.avl.com
–
+41 22 929 29 29 www.st.com
–
+33 1 49 45 32 32 www.valeo.com
–
+49 711 939 00 www.eberspaecher-climate.com
+49 711 5010 www.mahle.com
+49 89 8 57 94 0 www.webasto-comfort.com
–
+82 4 2930 6114 www.hanonsystems.com
–
+1 508 854 5800 www.allegromicro.com
+1 248 754 9200 www.borgwarner.com
+1 248 504 0500 www.gentherm.com
+1 906 482 9560 www.thermoanalytics.com
ONLINE PARTNERS
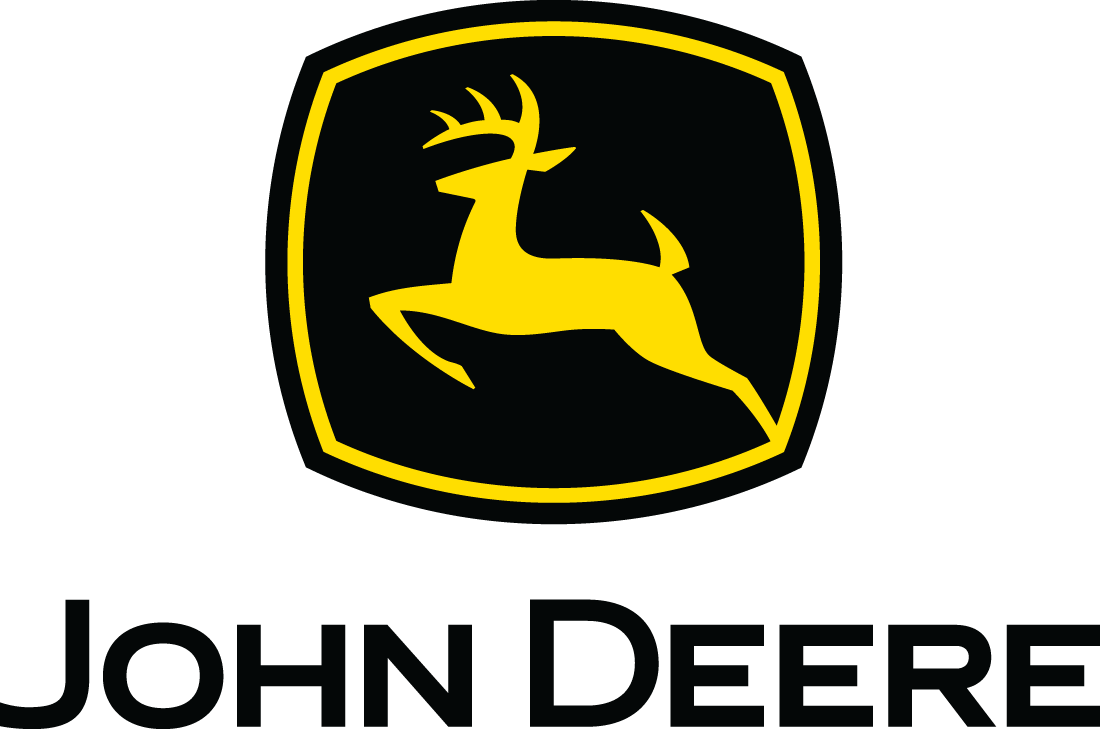
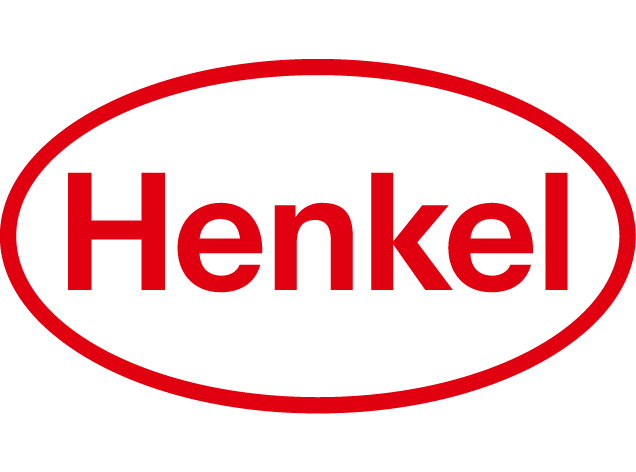
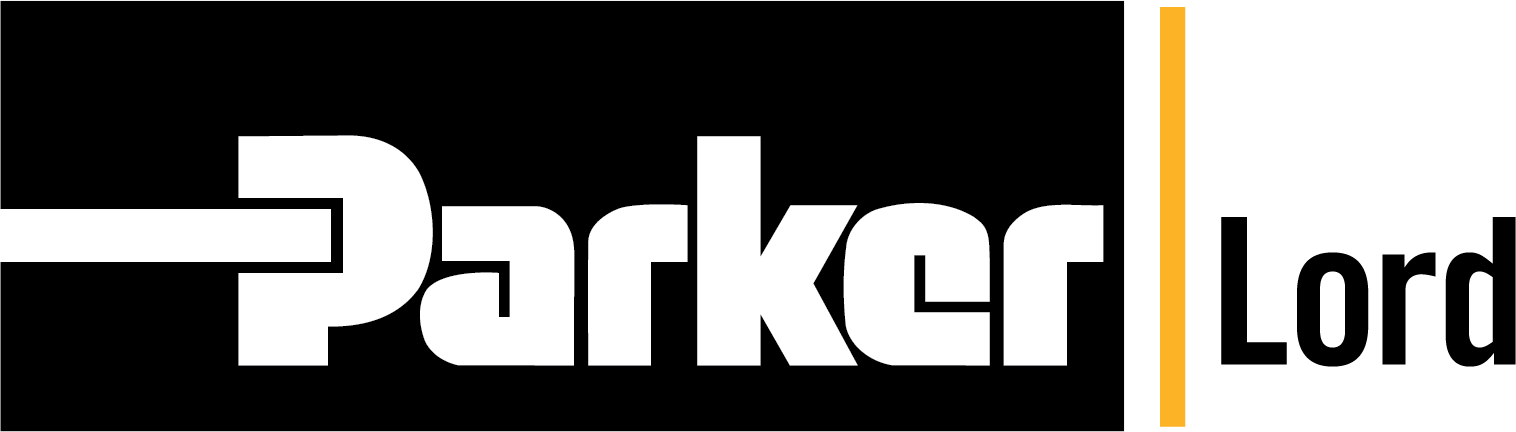
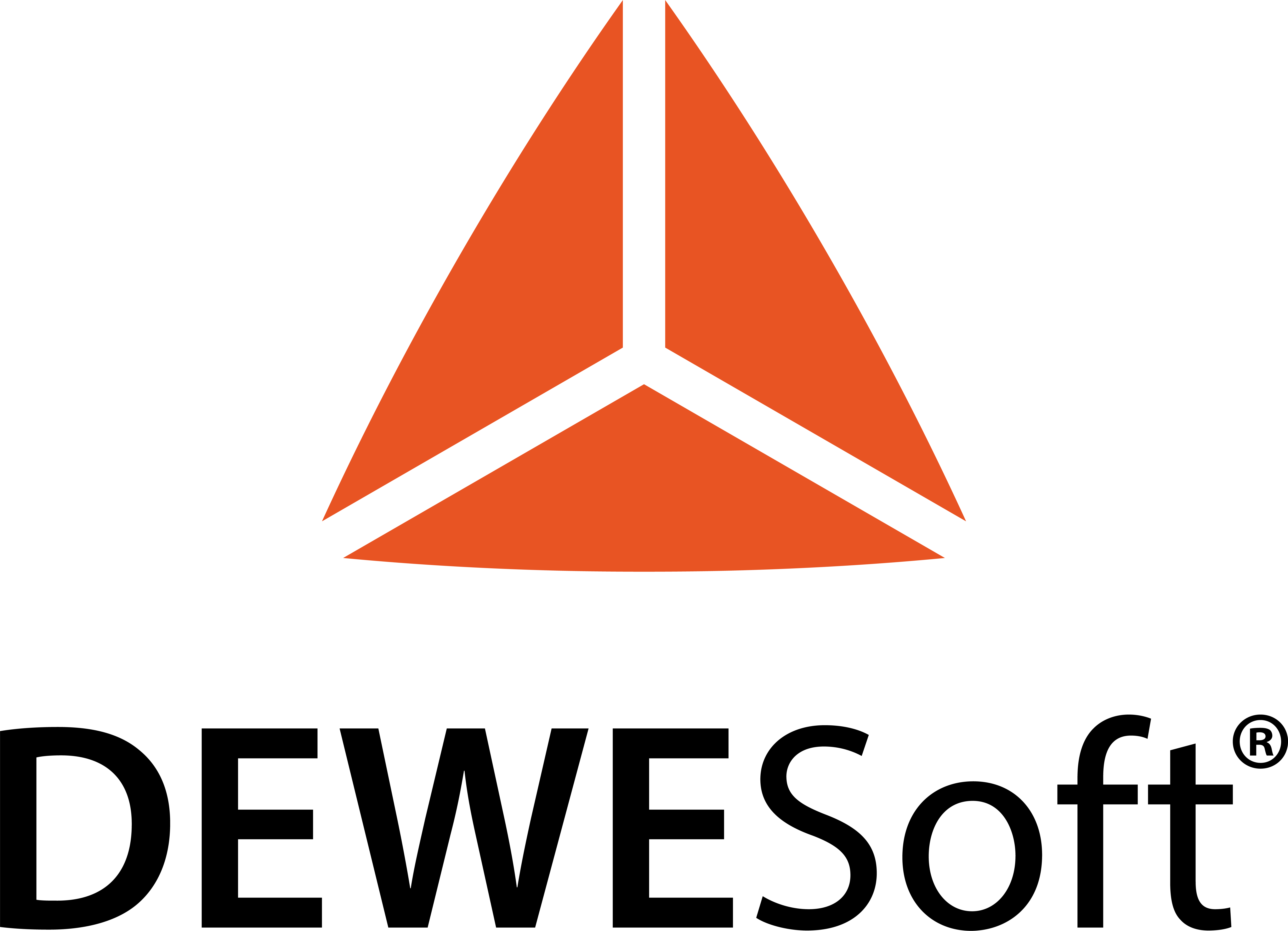
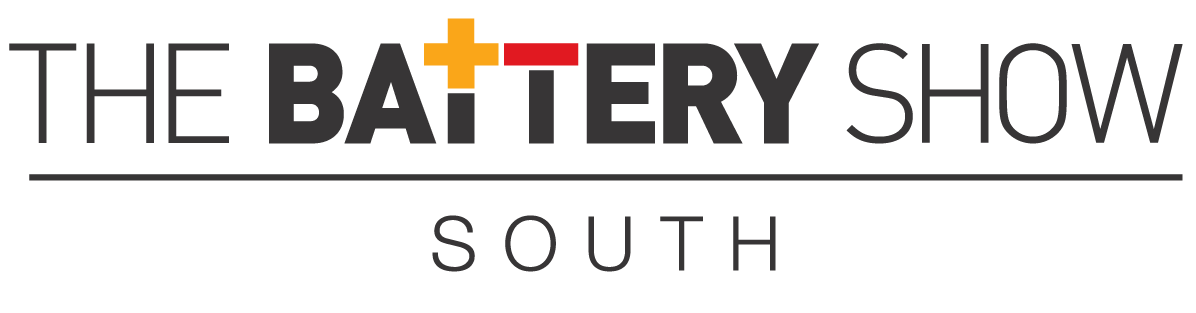
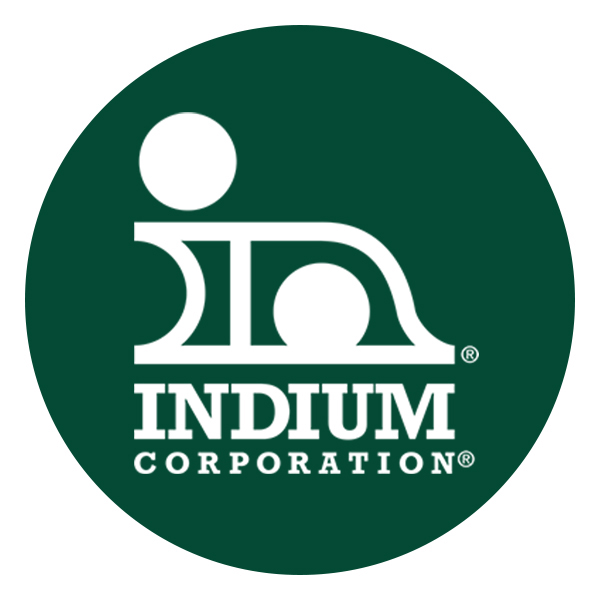

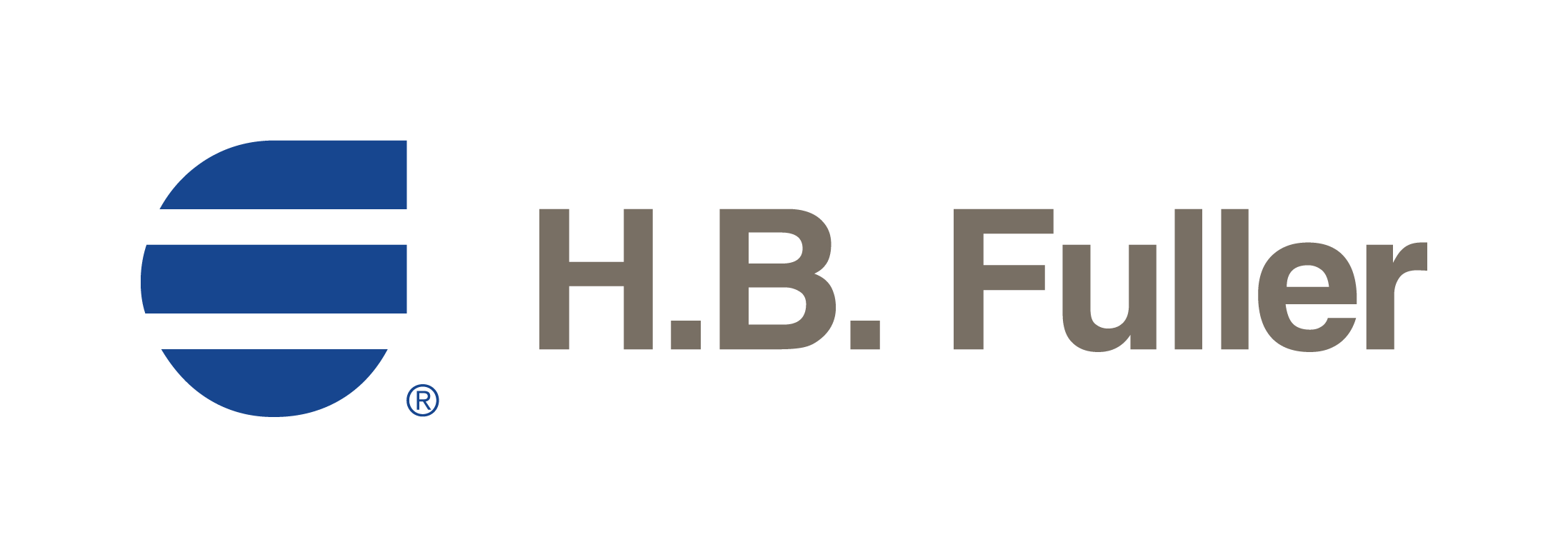
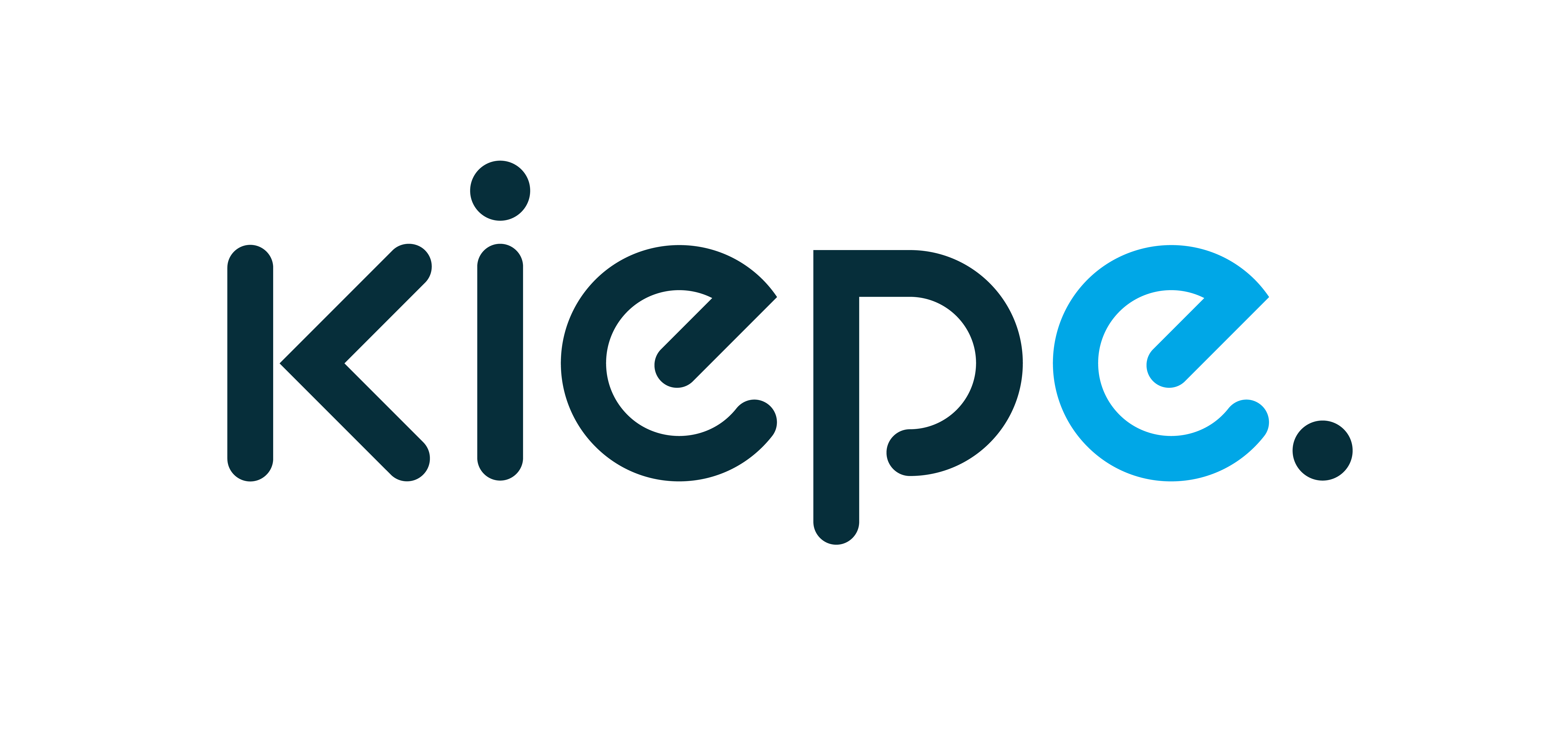
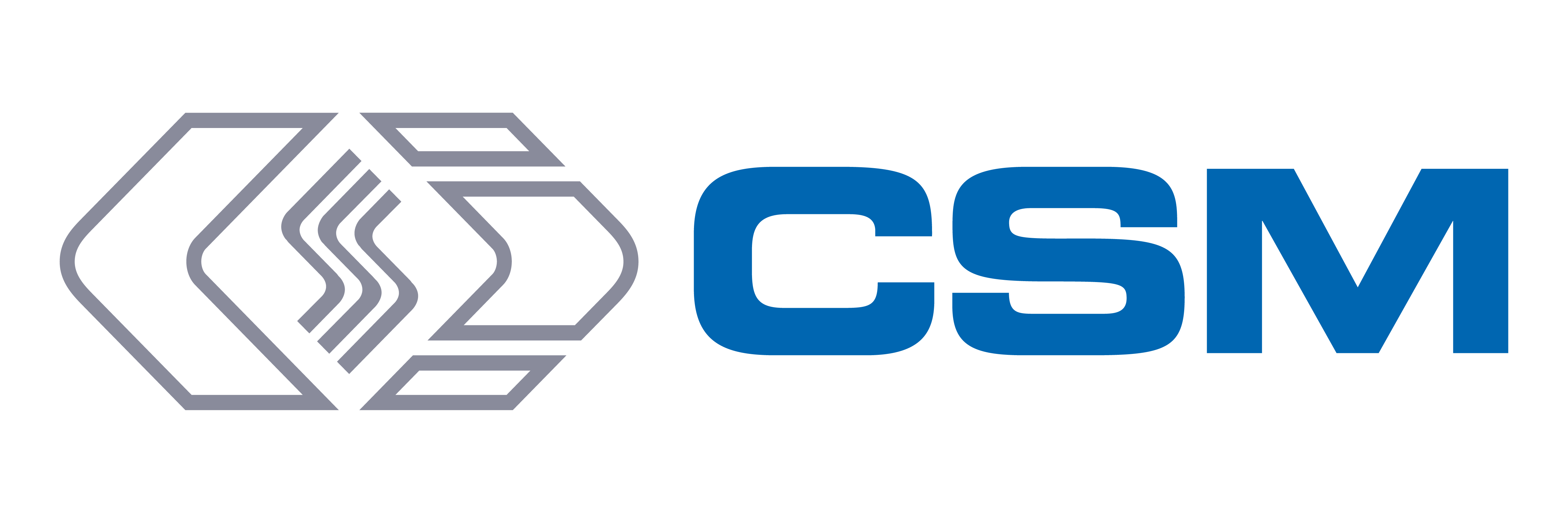