Battery swapping, and the alternatives
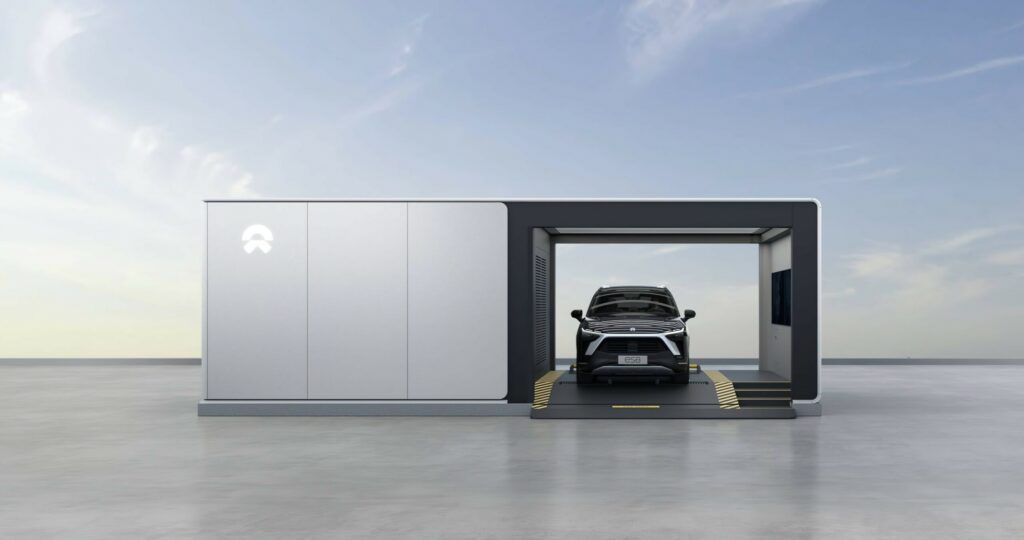
Whether you drive a single battery EV or operate a fleet of them, ensuring there is enough energy in the battery to complete the job in hand is bound to be a major concern (writes Peter Donaldson).
The fact that there are different ways of charging, and that many vehicles can use more than one of them, is a sign that the industry that is still maturing, and it is not yet obvious which, if any, will dominate in the future.
Fundamentally, the options are slow charging from a power-limited AC mains outlet, fast charging from a public high-power DC charger, rapid and probably frequent top-ups from a pantograph, wirelessly from a magnetic induction charger, or swapping out the exhausted battery for a fresh one. While swapping can be work well technically, it comes with a set of severe constraints on vehicles, batteries and users, and adds complexity to the infrastructure required to support EVs.
As an idea, there is a lot to commend battery swapping, particularly when it can be done swiftly by safe and reliable automated machinery. Processes that are more manual can also work well if the batteries are not too big and heavy or if well-designed handling equipment minimises the labour involved. There are examples of systems that achieve each of these.
Israeli start-up Better Place developed a slick, rapid and effective automated system in the 2000s. In 2007, it made a deal with Renault, which built cars such as the Fluence powered by compatible batteries.
Tesla seriously considered battery swapping before settling on its Supercharger approach, and it registered several patents covering automated battery swapping equipment.
While Better Place went out of business in 2013, Chinese company NIO has since deployed its own automated swapping system at scale in its home market, where it had clocked up half-a-million swaps by mid-2020, and is expanding elsewhere.
US company Ample is developing modular batteries that it intends to offer to EV manufacturers as a customer-specified option, along with an automated system that allows rapid swapping of individual battery modules as well as entire packs.
Greenway, meanwhile, has developed a system for commercial vehicles that allows one person to swap a heavy battery pack using handling equipment at each swap station.
For smaller EVs, such as light two- and three-wheelers, Sun Mobility offers quick-change batteries and has deployed entirely manual swap stations across India.
As with public fast chargers, all these systems need a source of electric power to charge the batteries they remove from customers’ vehicles. However, they may be able to charge them at a gentler rate if the turnover is low enough or the swapping stations hold an adequate buffer stock of serviceable batteries.
They must also have a means of rapidly assessing the condition of each battery that comes in for charging, backed by smart inventory management systems that ensure a reliable supply of good batteries to meet demand, and a way to handle those that don’t measure up.
The automated systems also need dedicated machinery to do the swaps. This either has to be able to cope with a wide variety of sizes, shapes and securing systems associated with different vehicles and battery packs, or be designed to work with one particular battery securing system. The latter would tie the swap machinery to one vehicle manufacturer though, unless every OEM could be persuaded to adopt one as the industry standard, or one is imposed by government.
Systems that are as easy and much quicker to use from a driver’s point of view are probably the most complex and effort-intensive means yet devised of getting energy into an EV, and the alternatives are improving rapidly. However, the manual and mechanically assisted ones for two/three-wheelers and trucks respectively are much simpler and probably more broadly viable.
ONLINE PARTNERS
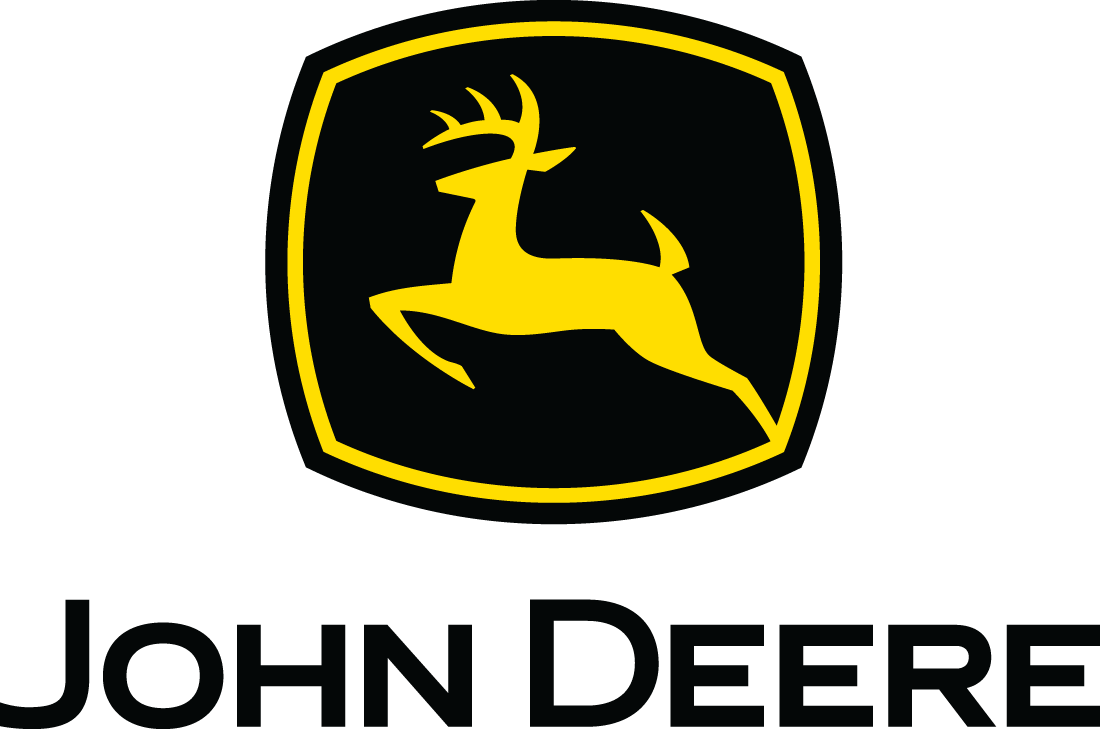
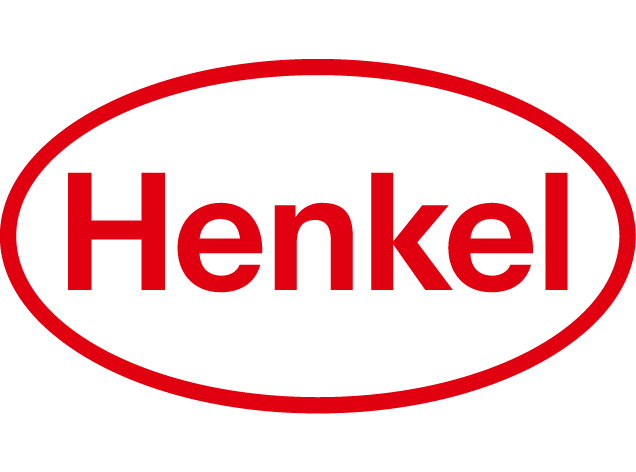
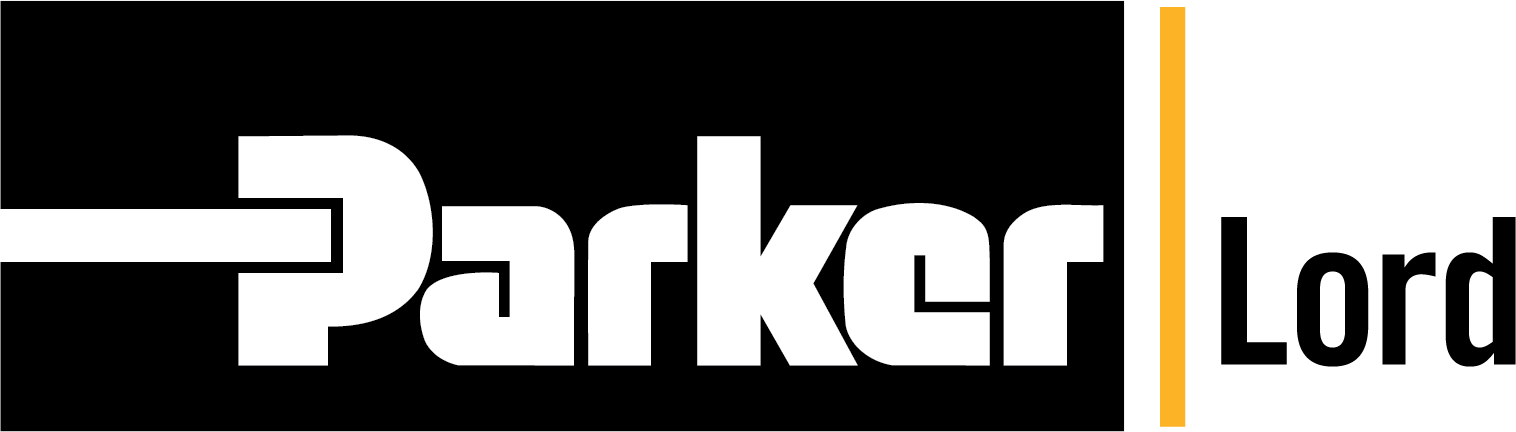
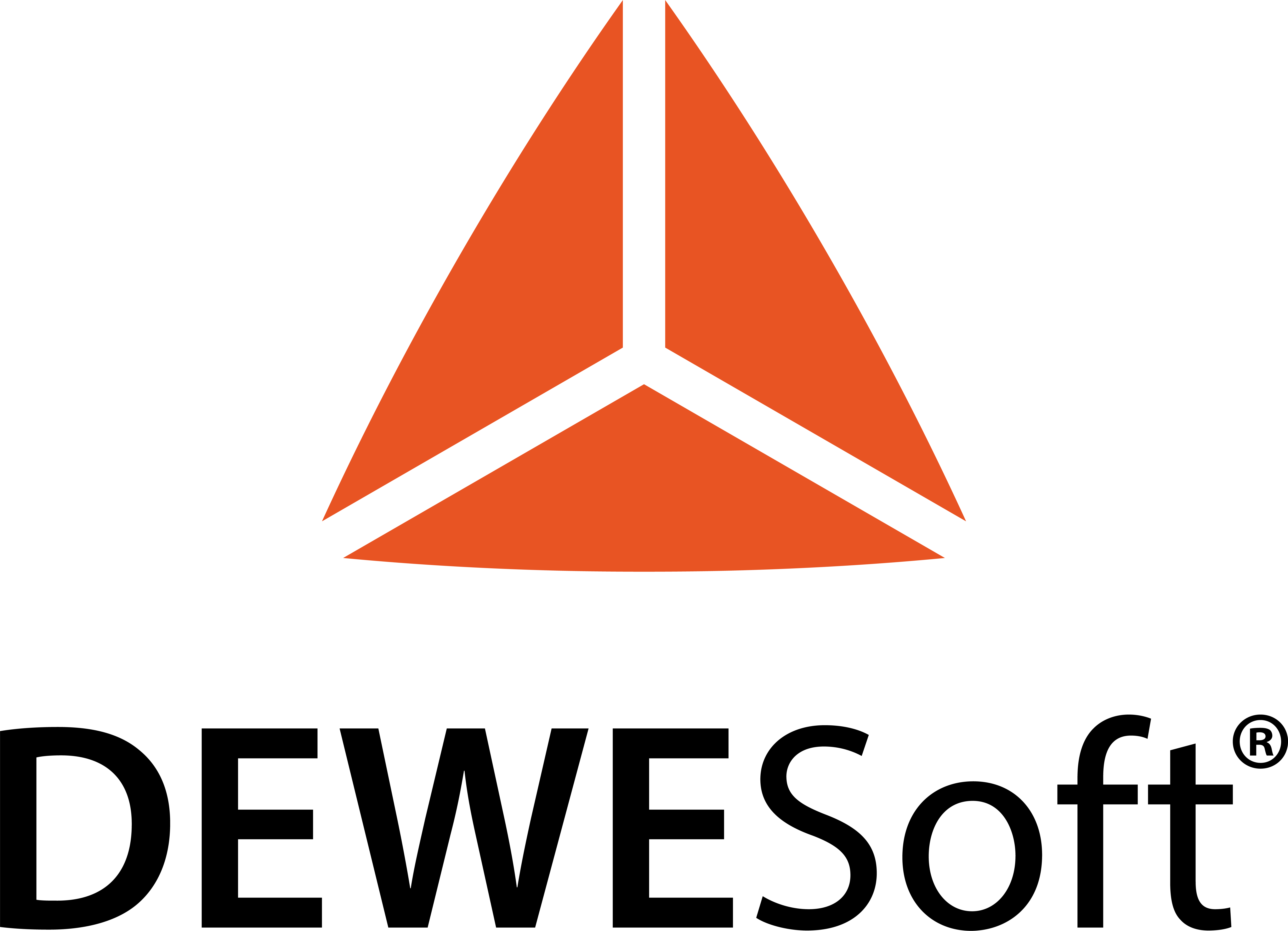
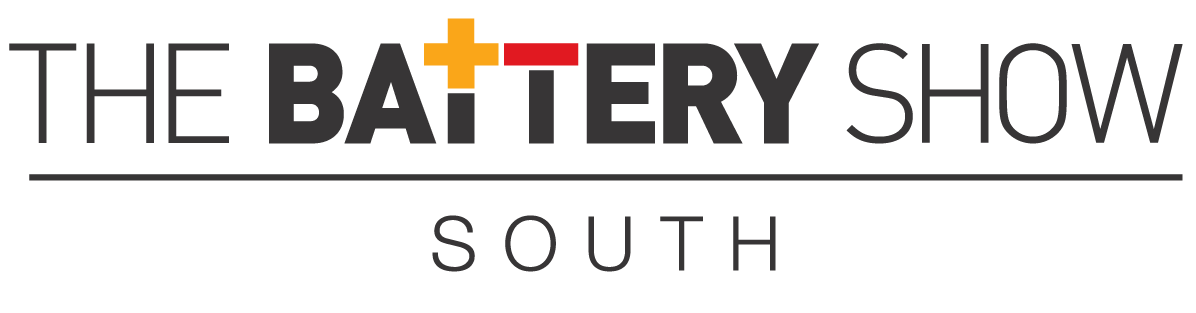
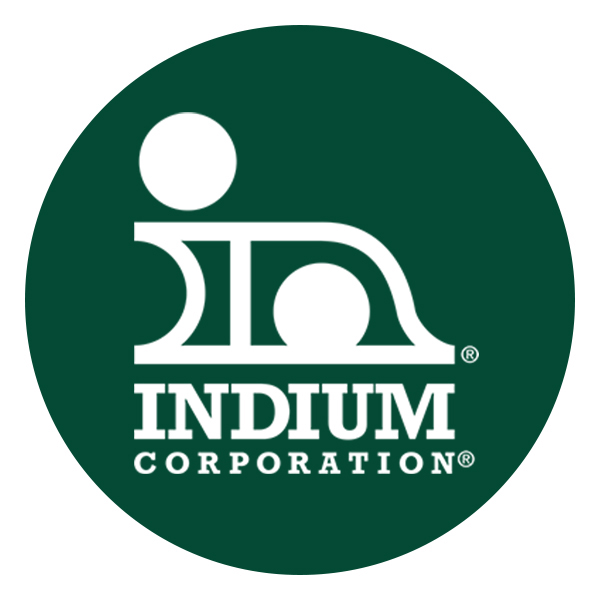

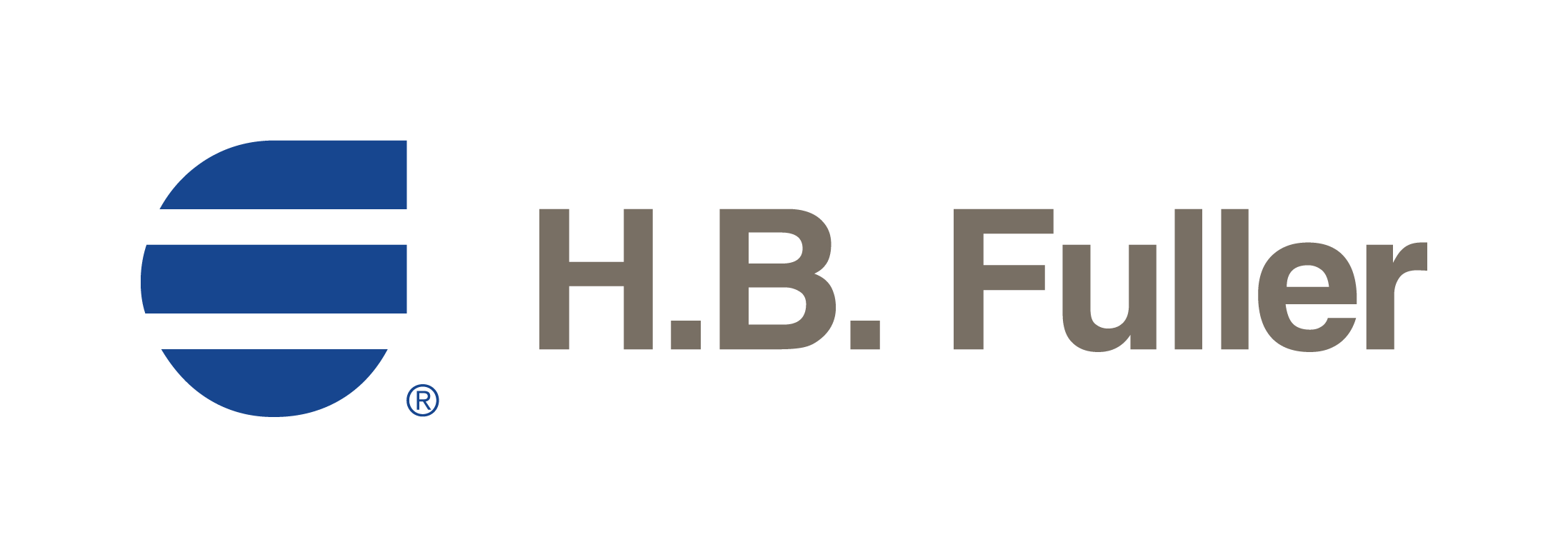
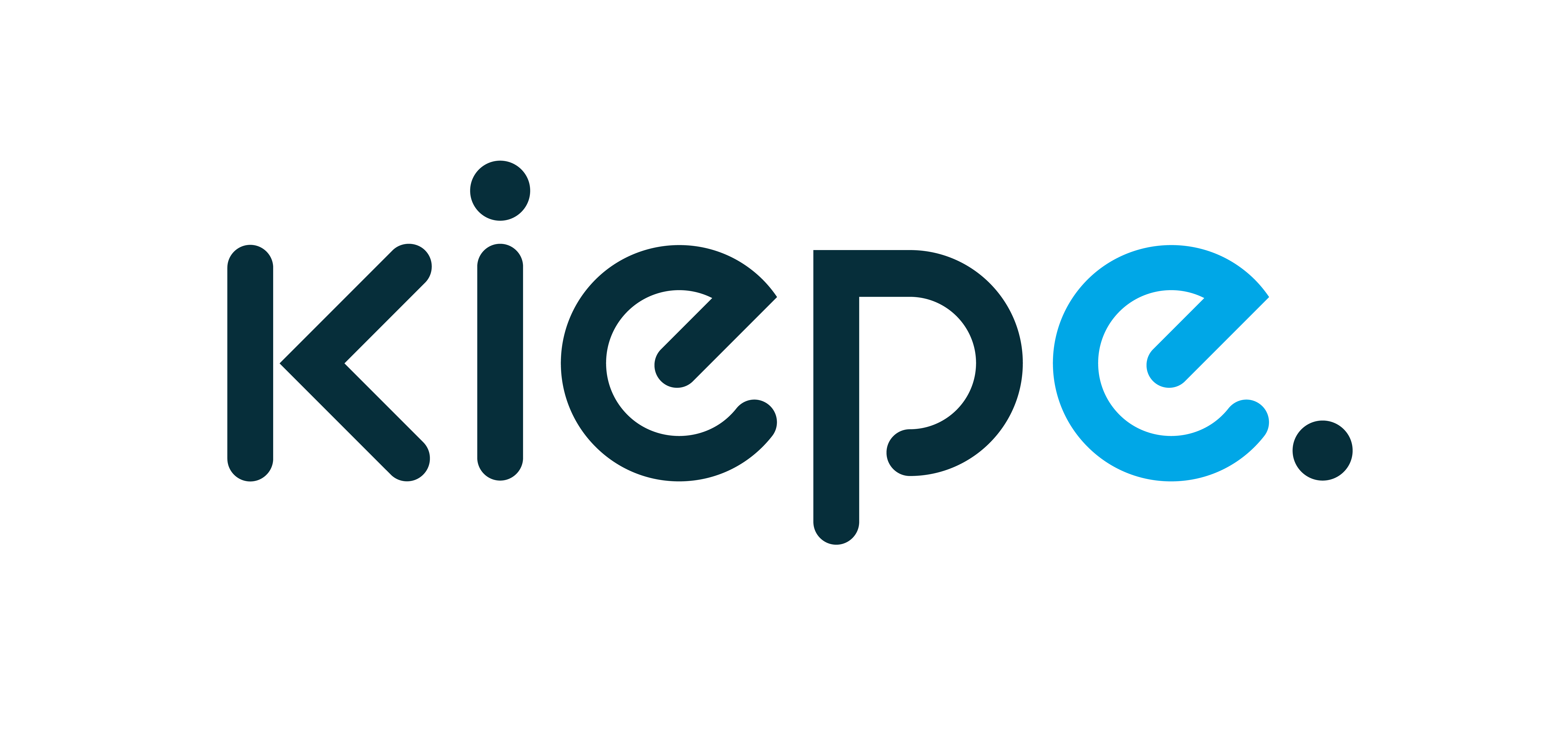
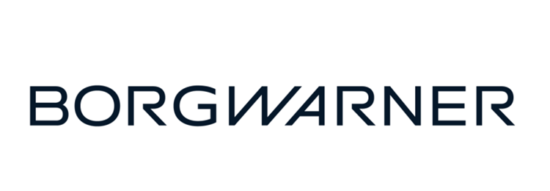