NVH
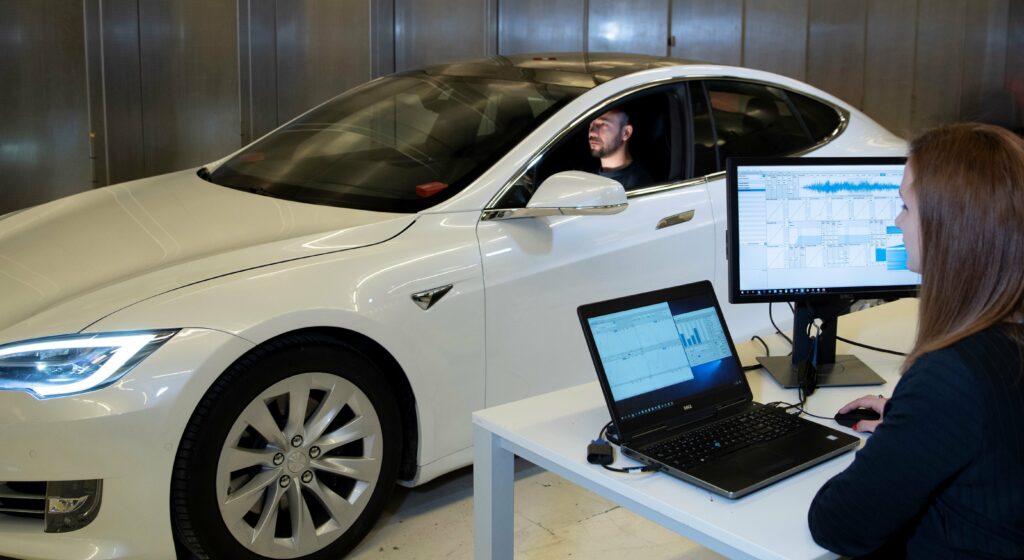
(Courtesy of Siemens)
Acoustic instruments
Peter Donaldson reports on the tools and methods for optimising the acoustic environment in EVs.
Of all the disciplines required for developing cars, psychoacoustics isn’t one that readily springs to mind. However, this science of the relationships between aural stimuli and the responses they produce in people informs the branch of engineering that wears the more prosaic label of Noise, Vibration and Harshness (NVH).
While the first two are amenable to objective measurement, the third involves more subjective assessment. The soundscape in and around an EV is culturally unfamiliar, so it is subject to intensive r&d effort as OEMs strive to make their vehicles and brands more distinctive.
While EVs are far quieter than IC-engined (ICE) vehicles, other sounds become more obtrusive, notes Puneet Sinha, director of new mobility at Siemens Digital Industries Software. “Wind and road noise, along with smaller but sometimes annoying sounds – e-drive high frequency harmonics, HVAC blower and so on – become very apparent.” He emphasises that in EVs it is more important to look at sound quality than sound level.
Patrick Boussard, senior product manager of VRXperience Sound at simulation specialist Ansys says, “Objective measurement is based on metrics such as the sound pressure level in dB. However, two sounds at 40 dB for example will have different perceived strengths to the ear if their spectra are different.”
Psychoacoustics uses listening tests to gauge perceived loudness (expressed in units called ‘phones’ or ‘sones’) plus other perceived qualities such as sharpness and tonality. In these tests, a jury of listeners rate and rank their perceptions of these qualities. “Because there are uncertainties and dispersions in their responses, we usually run tests with many listeners so that we can do a statistical analysis and find the mean,” Boussard says.
Millbrook, which merged in February with UTAC-Ceram in France, carries out a wide range of NVH measurements at several sites. Romain Barbeau, expertise coordinator at UTAC’, notes that objective measurement is used to relate psychoacoustic assessments to hard numbers.
He says, “Subjective measurement is often used for interior noise, as it is more related to people in the cabin. It is sometimes difficult to objectivise, because it is complex and we have to take measurements to correlate with what we feel. It is less the case for exterior pass-by noise because that is measured with regulation in mind; we need a value and data.”
There are ways to gauge sound perception using microphone measurements, with complex algorithms applied to estimate what human subjects’ perception of what the loudness, sharpness, roughness and tonality of a given sound will be. These algorithms generate psychoacoustic metrics/indicators that are recognised in ISO and DIN standards.
Boussard notes, “The relationship between physical measurement and sound quality assessment is key, but it can only be estimated, not measured, using psychoacoustic indicators.” Adding another layer of complexity, this relationship is fluid and highly dependent on context, according to Dr Ing Bernd Philippen, product manager for sound, vibration and perception at Head Acoustics. “An engine perceived as sporty during acceleration could be perceived as unpleasant during a cruise along country roads,” he points out. “In the EV world these traditional perceptions are changing.”
Many different types of NVH data are generated in tests of complete vehicles, components and CAE analyses. “These results are very valuable, but as people we don’t experience and understand sound through our eyes by looking at numbers, plots and graphs,” says Dave Bogema, director of NVH solutions at VI-Grade, part of the Hottinger, Bruel & Kjaer (HBK) group, which provides NVH simulation technology.
The best way to understand sound and vibration data is to experience it as sound and vibration,” he says. “We use objective data to guide us, but we need the subjective experience to validate and understand it, and make important design decisions.”
An important advance bringing the subjective and objective realms together is the use of virtual NVH prototypes, Bogema adds. These are composites of test data and CAE analysis that are listened to, felt and experienced in simulators, enabling faster and clearer understanding of the vehicle’s NVH envelope and the way individual components affect its character. “Virtual sign-offs can be performed at key development gateways using virtual NVH prototypes,” he says.
An ICE vehicle’s soundscape has three main components that dominate in different conditions: powertrain noise at low speed, tyre noise at medium speed and wind noise at high speed. “EVs and hybrids are quieter mainly at low speed,” Bogema says.
“At high speed, ICE vehicles, hybrids and EVs are very similar, except for some sporty cars where engine or exhaust sound is still present.”
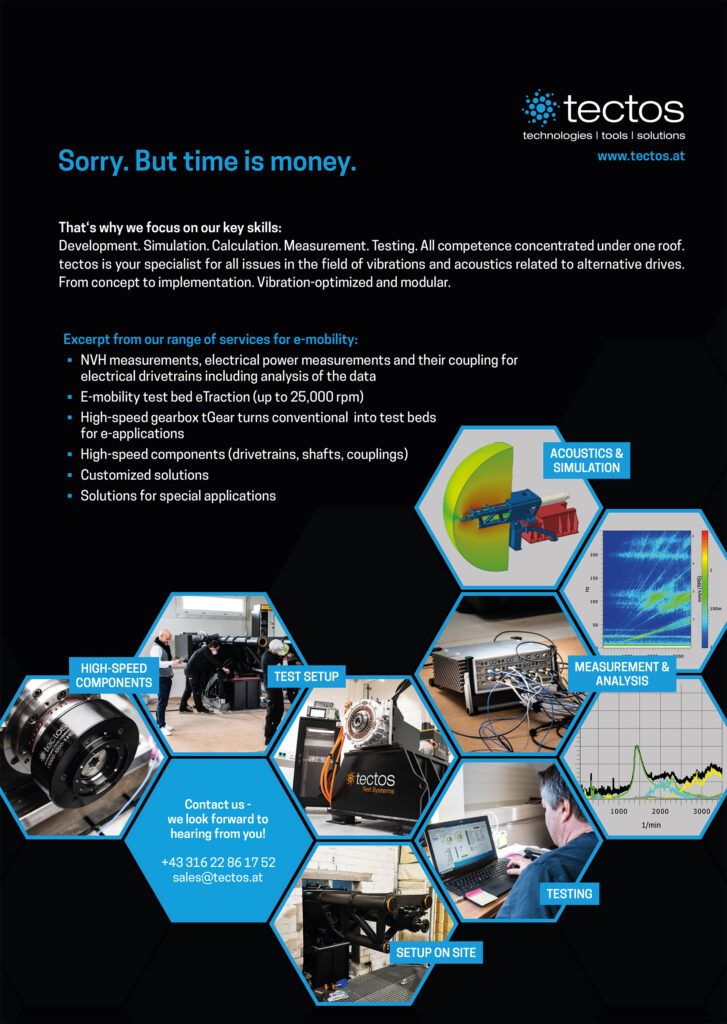
With the masking effect of an engine eliminated, characteristic EV sounds are more noticeable, says Philippen. “There is more high-frequency tonal content from the inverter and motor that can be annoying even if the absolute levels are low. In HEVs the operation strategy can cause NVH issues if, for example, the engine is switched on and off without interaction with the driver.”
Explaining how road noise and vibration are affected by the lack of engine masking, Bogema stresses that running over the same piece of road in a pure EV may seem harsher or rougher than it would in a comparable ICE vehicle. “That has to do with the way we perceive sound and vibration,” he says.
Exterior sound is tightly regulated in most road vehicles, but while ICE cars must be quietened, governments require almost silent EVs and hybrids to be equipped with acoustic vehicle alerting systems to improve safety for pedestrians. “This presents a challenge as well as an opportunity to automakers to design sounds that conform to these regulations but that also project the correct character for the vehicle and the brand,” Bogema says.
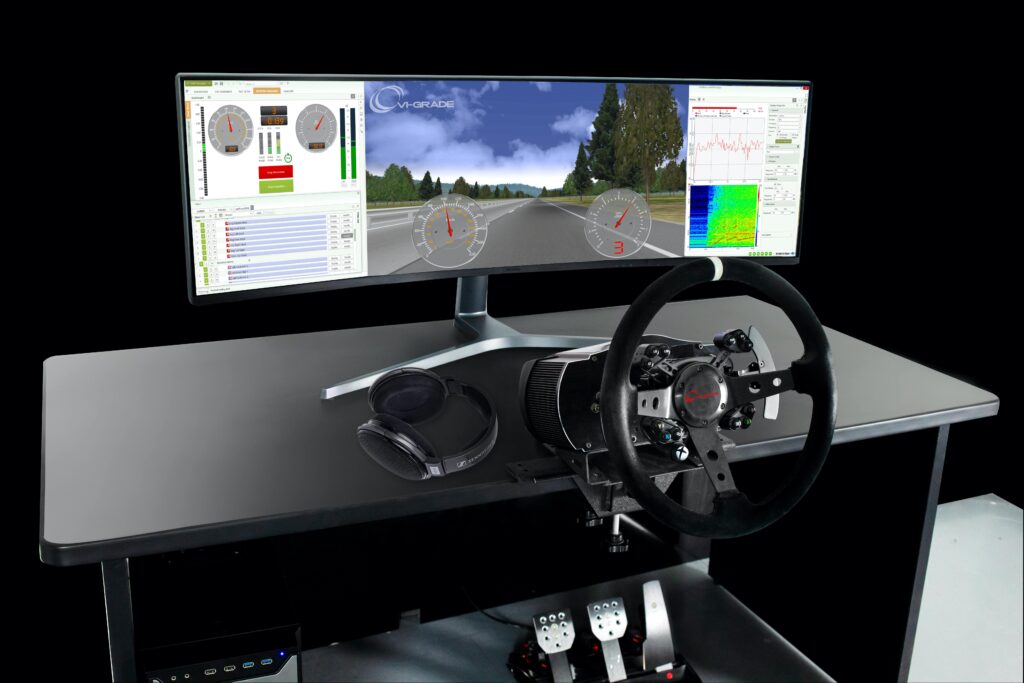
(Courtesy of HBK VI-Grade)
Electrical NVH sources
Electric motors and generators run much more smoothly than IC engines, but electromagnetic forces between the stator and the rotor can lead to NVH problems. While tangential forces cause the rotor to turn, there are unwanted pulsating radial components that bend the structure of the rotor and stator. These vibrations pass from the motor housing into the vehicle body through mountings and into the vehicle interior along structure-borne paths.
The motor housing can also radiate sound directly, transmitting it to the cabin through the air. As their frequencies correspond with the upper end of human hearing, these sounds can be painful.
As Bogema explains, the electromagnetic fluctuations in the motor can also induce torque fluctuations that pass into the transmission, modulating the sounds created by the gears themselves that again pass into the cabin via structural and airborne paths.
Careful design and manufacturing of electrical machines is crucial to minimising noise, as varying tolerances can result in large differences between nominally identical motors. Also, mechanical resonances caused by fundamental current and pulse width modulation (PWM) speed control harmonics, for example, can generate high noise levels.
Fortunately, high-frequency noise is relatively straightforward to reduce with the use of absorbent materials. However, improved acoustic comfort can come at the cost of increased weight that affects the vehicle’s overall energy efficiency, Boussard notes.
Benchmarking
The process of comparing a new vehicle design with the best of the industry’s current offerings – benchmarking – presents a number of challenges, not least of which is ensuring that all the vehicles involved are operated under exactly the same conditions for testing, Philippen notes. With hybrids in particular, there is a myriad of possible operation and control strategies for the powertrain, and every OEM chooses different ones.
From the endless number of operating conditions, the most relevant have to be chosen and compared systematically. This is typically done in an NVH simulator,” Philippen says.
Bogema concurs that hybrids can present unique control strategy challenges and variables, such as the battery’s state of charge, that are absent in pure ICE vehicles. “Overall though, these differences can be contained and encompassed by modifying benchmarking procedures,” he says.
Early benchmarking work on EVs was made somewhat more difficult by typical early EV limitations, as Darren Williams, chief engineer vehicle department at UTAC, explains. “One issue we had was not being able to get as much time working on the vehicle and collecting data as we wanted between charges, and the time taken to charge up again, but that’s less of a problem now.
“Another was the lack of EVs to benchmark against. In some instances we were benchmarking against ICE vehicles as well, just to give us the range of vehicles we wanted. That’s still the case to some extent.”
Now, as then, safety is a primary concern in measurement, Barbeau emphasises. Identifying and confirming individual components and subsystems as sources often involves partial dismantling of the vehicle and placing microphones and accelerometers near high-voltage components. “We have to apply new processes to ensure the safety of people doing the measurements,” he says.
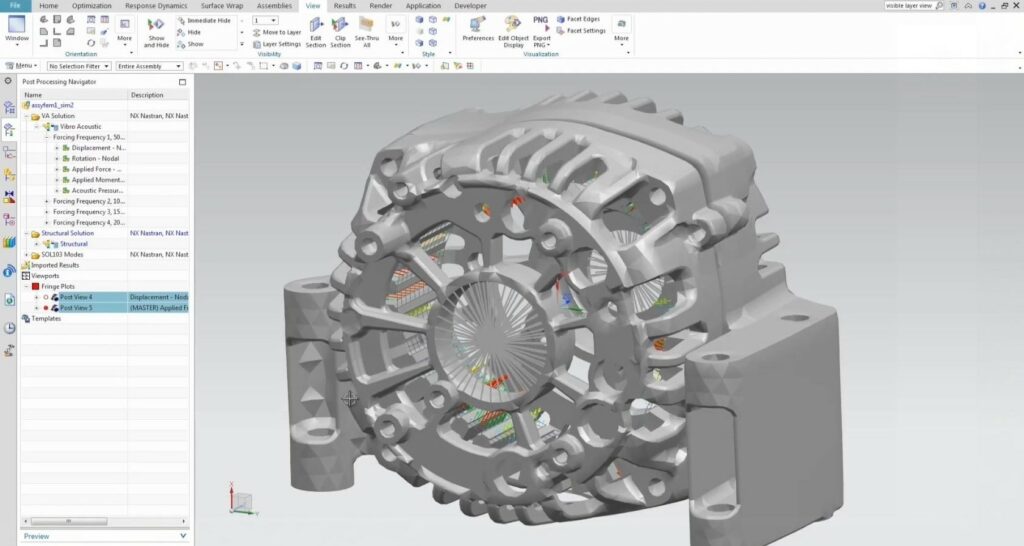
(Courtesy of Siemens)
Design analysis
Philippen argues that it is important to define clear goals for the overall sound, and to break them down into subsystems based on benchmarks and customer clinics. Virtual prototyping is useful from the start, as it allows people to experience sound and vibration based on simulation data. The next step is to refine the virtual prototype by incorporating data from testing and component-level simulations.
While there are differences between the analytical methods for simulating EV and ICE vehicle powertrains, and in how the systems are tested and analysed, the overall process is more or less the same.
“The more significant change in recent years has been the elimination of physical prototypes from the early and mid-development process,” Bogema explains. “There’s been a shift from building and testing physical prototypes and components to relying on virtual prototypes and analytical data for most of the programme.”
Sinha stresses that benchmarking NVH designs for EVs is not easy, as experience in the industry is still limited. Siemens is putting a lot of effort into developing expertise in this area, he adds, with the main focus being on the multitude of noise sources to be considered.
“Every system in the car needs extra attention, and the way many of them are mounted in a vehicle makes the analysis more difficult than for an engine on isolating mounts,” he says.
With external noise, design analysis is more straightforward and essentially the same for all powertrain types, says Barbeau. The process begins with the regulatory requirements the vehicle must meet and a set of key parameters defined by the OEM for the vehicle. This is broken down into targets for individual components, with tolerances taken into account for each.
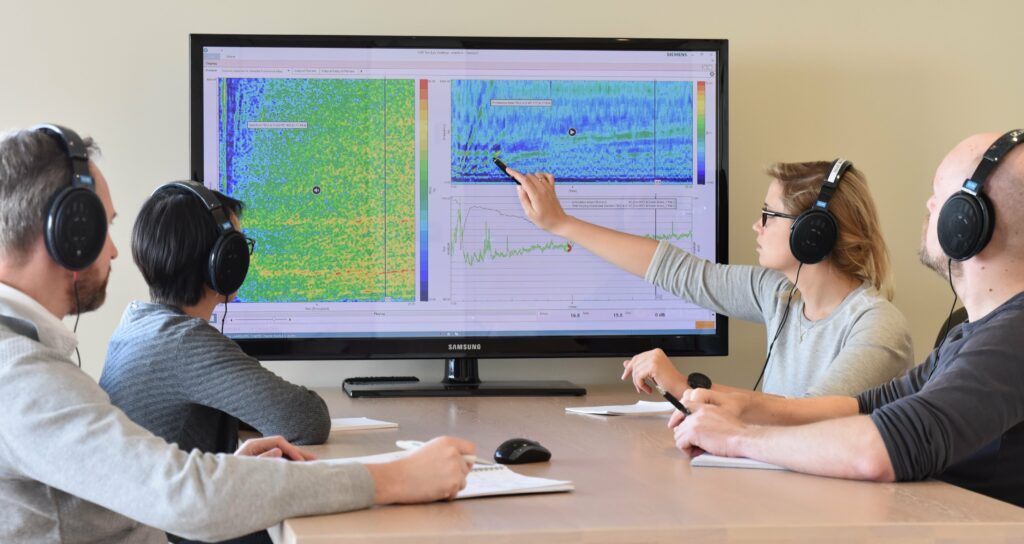
(Courtesy of Siemens)
More than the sum of its parts
Our experts emphasised the importance of analysing the components, systems and assemblies that make up a complete vehicle both separately and together. “The overall soundscape is the combination of all the acoustic sources, taking into account the transfer path of each one to the driver’s and passengers’ ears,” says Boussard.
The sound power and vibration level of each source must be considered, as must the ways in which they will be changed during transmission through the vehicle structure. The resulting sound composition at each ear enables engineers to prioritise source components for modification or treatment using dampers or silent blocks for acoustic isolation, he explains.
In early development, NVH engineers only get the chance to analyse subsystems separately, and when they are brought together in the vehicle, with every component connected by a mechanical interface to the structure, unwanted surprises can emerge, Philippen points out. “It is therefore very important for OEMs and suppliers to define meaningful specifications at the interface level and bring the different components together in simulation models,” he says.
NVH targets are typically assigned at vehicle, system and component levels, Bogema notes. “Suppliers are often responsible for a specific component or system, so they need to analyse and validate NVH performance against those targets. It is useful at the component and system levels to understand how that relates to vehicle-level perceptions, so subjective evaluation of specific components or systems is important,” he says.
“Summing the contributions from all the components and assemblies is vital, both virtually and physically, and both objective and subjective analyses are important.”
Sinha cautions that not accounting for NVH as a key metric in the design of electric motors, for example, will force OEMs to adopt masking techniques that are likely to add weight and cost, and he reports growing demand for NVH solutions from component suppliers and vehicle OEMs.
This framework allows OEMs to cascade noise and vibration targets from systems to components through Transfer Path Analysis (TPA), enabling suppliers to account for these targets in their component-level designs and engineering, and to improve collaboration between OEMs and suppliers.
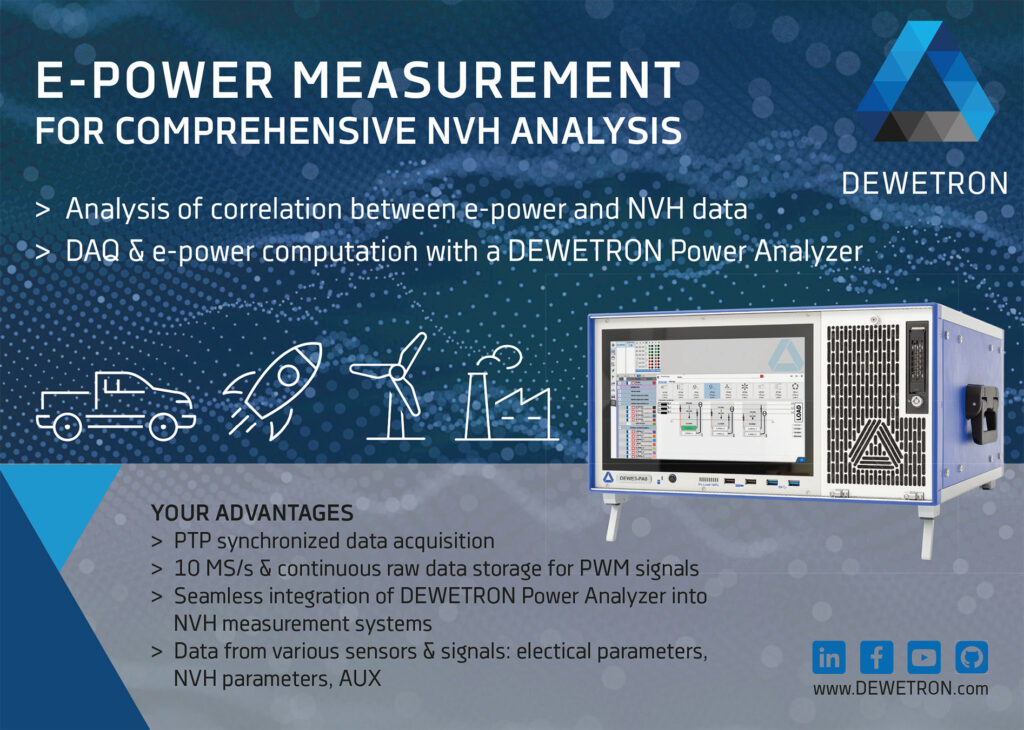
Simulation advances
In the realm of CAE, simulation continues to get better at accurately recreating the sound and vibration signatures of the major sources of NVH. “For EVs, the simulation of a motor and gearbox are complex, because it has to include electromagnetics, mechanics and multi-body dynamics,” says Boussard.
Only simulation can predict the global soundscape in the passenger compartment for all sources and paths, but the hybrid approach – combining test and simulation – is both efficient and promising,” he says. “Once the sources of annoyance are identified, simulation tools make changing a design to optimise sound easier and more efficient than prototyping each design would be. Once the optimal sound and design are achieved, the physical prototype can be manufactured to validate the concept.”
Recently, the adoption of simulation to create virtual NVH prototypes has increased dramatically, says Bogema, and it has also broadened in scope. “What is now growing is the focus and application of simulation technologies to vibration as well as sound, and also multi-attribute simulation that combines NVH, vehicle dynamics, ride, handling, HMI and ADAS attributes.”
In Siemens’ interactions with the automotive industry, the biggest developments are in combining 1D and 3D simulation or 1D simulation with testing to accommodate more complex scenarios. These include the inclusion of controls in 3D simulation, hybrid hardware-in-the-loop testing and the creation of executable digital twins, says Sinha.
This, he adds, is the result of ‘macro evolutions’ in several areas. One of those is the growing impact of controls on vehicle behaviour, which creates opportunities to affect NVH as well by, for example, randomising the PWM output frequency of motor controllers to avoid creating tonal sounds. Another is the transition in companies from separate departments for simulation and testing to a more integrated approach, he says
Transfer path analysis
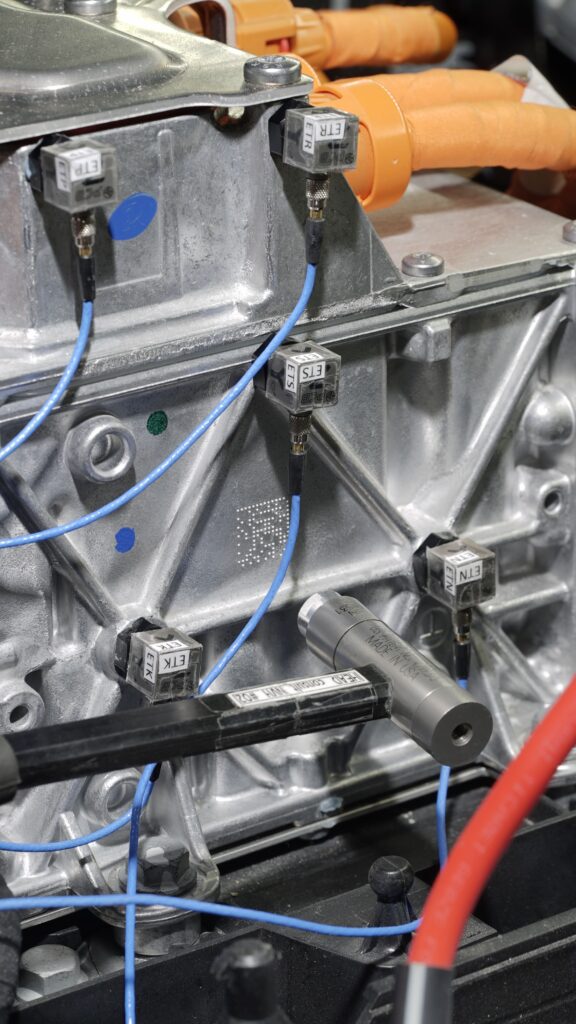
(Courtesy of Head Acoustics)
TPA is now a key element in NVH simulation systems, and is the means by which the routes that sound and vibrations take from every source to the ear and those body parts in contact with the vehicle are mapped. Philippen calls TPA the most important tool for the analysis of how different sources contribute to the interior soundscape and in predicting how it will be affected when components are changed.
“These days it is possible to measure a powertrain on a test bench and predict the interior noise in different vehicles based on the test data, so you can listen to the sound of a powertrain vehicle combination before it has been integrated in real life,” says Philippen.
TPA for EVs and ICE vehicles is essentially the same, but the larger number of potentially annoying sources in the former creates more transfer paths to analyse, Sinha says.
Boussard notes that initial transfer paths are often determined through measurement in the lab, but simulation can calculate some of them. “Simulation and optimisation of the transfer path can take acoustic isolation materials and multi-body dynamics into account in gauging the entire structure-borne vibro-acoustic contribution to the soundscape,” he says.
According to Bogema, whether taking a top-down target cascade approach or building a virtual prototype from the bottom up, TPA is key. He says HBK was a pioneer in the use of the blocked-force approach, which allows the characteristics of a component to be objectively quantified independently of its environment.
“That means a component can be measured in a vehicle or on a test rig, and those measurements can be used to predict what that component would sound like in a different vehicle with different mounting characteristics or different structural design,” he says.
“That enables engineers to build accurate virtual NVH prototypes of cars in development that have not yet had a single physical prototype part built. It is common to combine test-based source levels with CAE-generated path characterisations to arrive at the final contribution in the vehicle interior. This is generally referred to as hybrid modelling.”
Suppression issues
Swift and accurate simulation of components such as motors and inverters, for example, allows them to be optimised for NVH at the design stage and, as Boussard points out, the process is faster and more efficient for electric motors and EV transmissions – thanks to their mechanical simplicity – than for ICE vehicles.
EV powertrains are decoupled from the body by rubber mounts, but because the acoustic frequencies involved are higher than in ICE vehicles the absorption characteristics of the rubber must be tuned appropriately, Philippen notes. “In general though, it is easier to suppress higher frequencies,” he says.
When noise is transmitted through the air, isolation is ineffective so other techniques combining acoustic absorption and barrier methods tend to be applied.
Absorbers can be made from glass or polyester, for example, in fibre form and polyester, polyimide, polypropylene and so on as matting or flexible cellular foam, all of which absorb a portion of the noise and weaken reflected sound waves.
The absorbers can also be cut to different thicknesses. Thicker ones are better for attenuating lower frequencies, and perforated or patterned ones further improve low-frequency absorption at the expense of high-frequency effectiveness.
Boyd is also working on NVH in and around the battery compartment and power electronics, with a focus on developing solutions that address other problems simultaneously. In one case, the application of acoustic absorbing materials prevents battery damage in minor collisions. The company is also working on integrating NVH with thermal management solutions to eliminate vibration-induced friction heating of battery cells.
The growing pressure for energy efficiency presents NVH engineers with a continuously shrinking weight budget. “Ideally, you want to come up with structural design and optimal integration strategies that minimise transfer paths,” Sinha says. “Using damping material is the last resort.”
With e-drive subsystems, for example, designing ribbing into the housing reduces its noise output, because it shifts the housing’s resonance frequency away from that at which the machinery is vibrating.
Last resort or not, extensive r&d efforts are focused on materials that effectively absorb lower frequencies, says Barbeau. These are passive materials of a sandwich construction containing acoustic cavities with sizes tuned to the frequencies to be suppressed, he says.
Nissan, for example, is working on a material with a quarter of the weight of the rubber mats on which car manufacturers have long relied. The material consists of a honeycomb-style lattice of hexagonal cells covered on one side with a thin polymer film. When road noise encounters the material, most of it is reflected back, and the portion that does pass through is much lower in amplitude, according to the company.
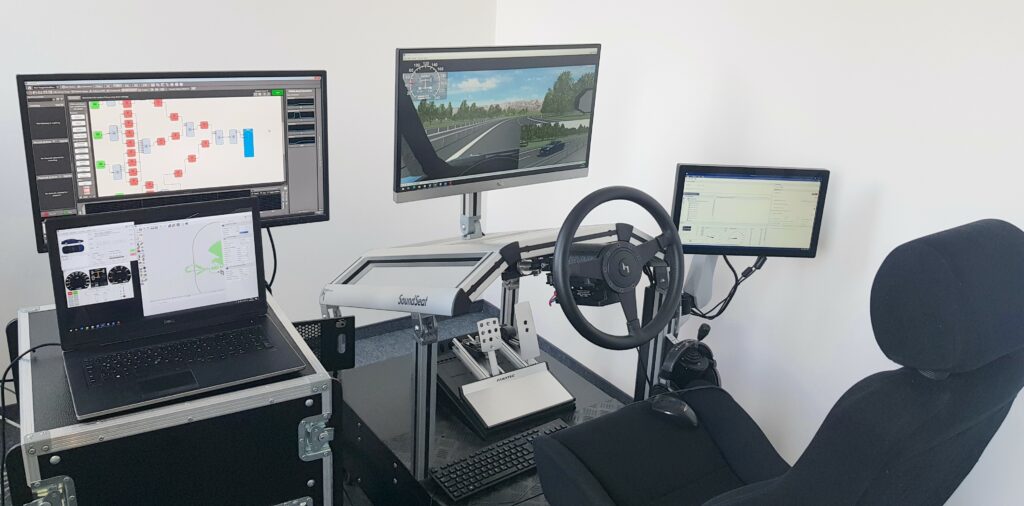
(Courtesy of Head Acoustics)
Active measures set future directions
Active noise cancellation (ANC) involves using microphones that sense noise at frequencies of interest, a processor that generates a signal that may be 180º out of phase with that noise, and speakers to emit this ‘anti-noise’ signal. It has been successful in treating low frequency deterministic noises such as engine rotational sounds and their harmonics, although more random (stochastic) signals such as wind noise are more difficult to process, says Boussard.
Recent improvements have made the technology more relevant to EVs, as it can be applied to low-frequency road noise at low as well as high speeds. Bogema adds that the current focus is on widening its range of applicability to active control of wideband road noise.
With pure EVs, enhancement of the soundscape through active sound design is more appropriate than ANC, Sinha argues, although it is a different story for hybrids. He says their generally small IC engines tend not to sound good. “For those, a combination of suppression and enhancement is the way forward.”
Boussard believes active sound design to be one of the most promising technologies for EVs of the next decade, the main idea being to use the car audio system to create useful new sounds such as speed and acceleration feedback cues when the driver pushes the accelerator pedal hard, but reverting to quiet in the cruise.
Philippen argues that actively enhanced sound offers OEMs an opportunity to create a characteristic brand soundscape and improve safety. In Head Acoustics’ own studies, the company found that drivers liked enhanced sound if it provided feedback on what the car was doing, especially in sporty cars, but that it quickly became annoying on longer drives if it did not blend into the background.
Culturally we don’t have a history or expectation of what EVs should sound like, Bogema says. There are many approaches that can be taken, from sensing the real sounds of electrical machinery and altering them – perhaps by changing their frequencies before bringing them into the cabin – to mimicking a sonorous V8, even to creating sounds more associated with vehicles from science fiction.
“The important thing now is that automakers and designers have the toolkits they need to rapidly design and try out different concepts and to get them evaluated by real people,” Bogema notes. “Vehicle simulators and vehicle NVH simulators and simulation tools are ideal for that.”
Increasingly, our experts concur, NVH and sound engineers will also have to take autonomous and shared vehicles into account, as passengers will develop new expectations of the in-car experience that will be focused on a host of work and other activities rather than driving.
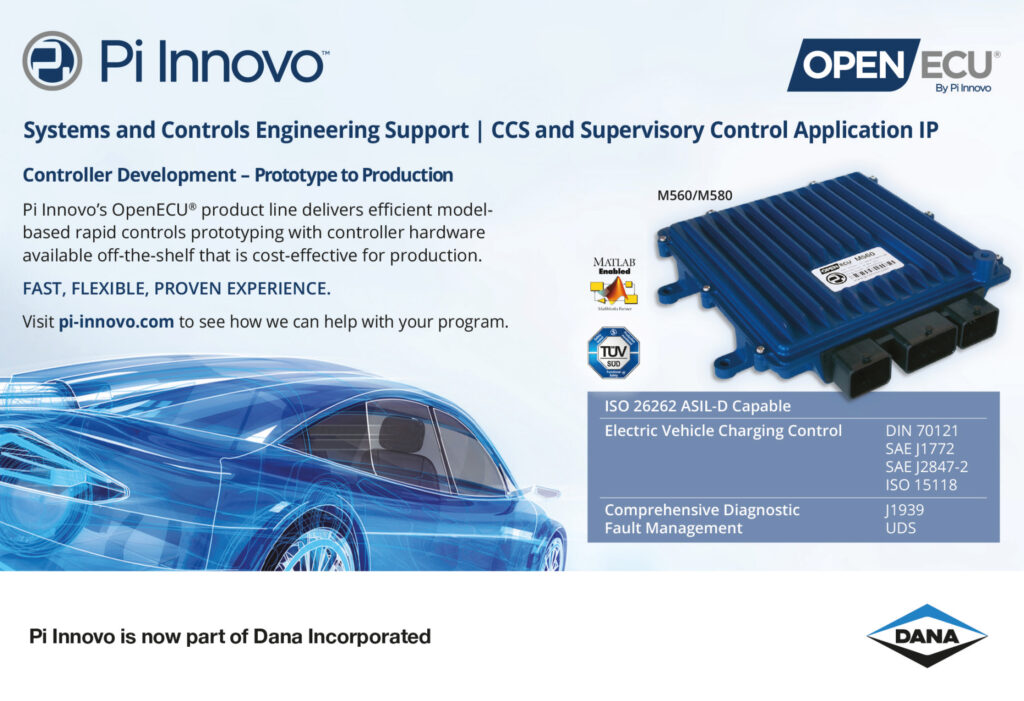
ONLINE PARTNERS
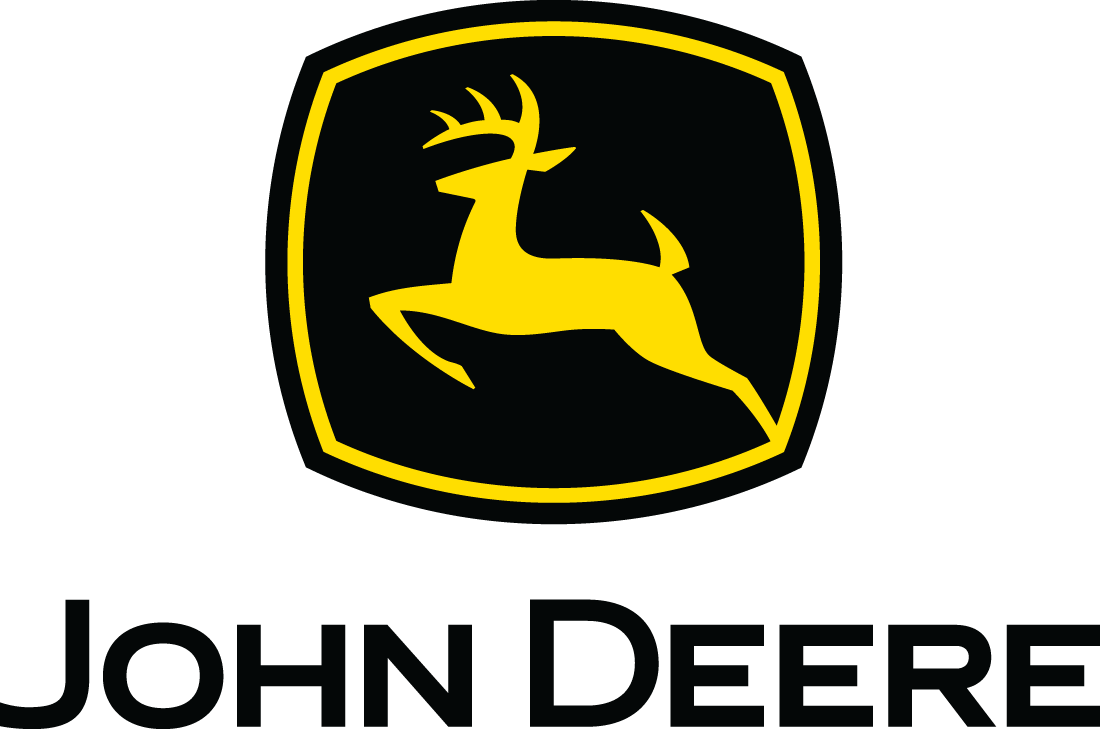
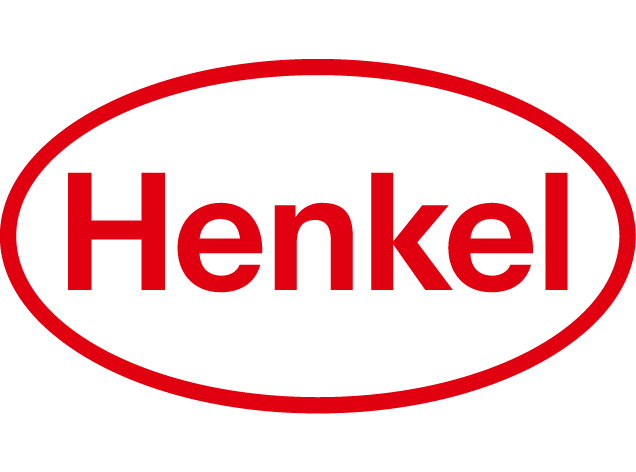
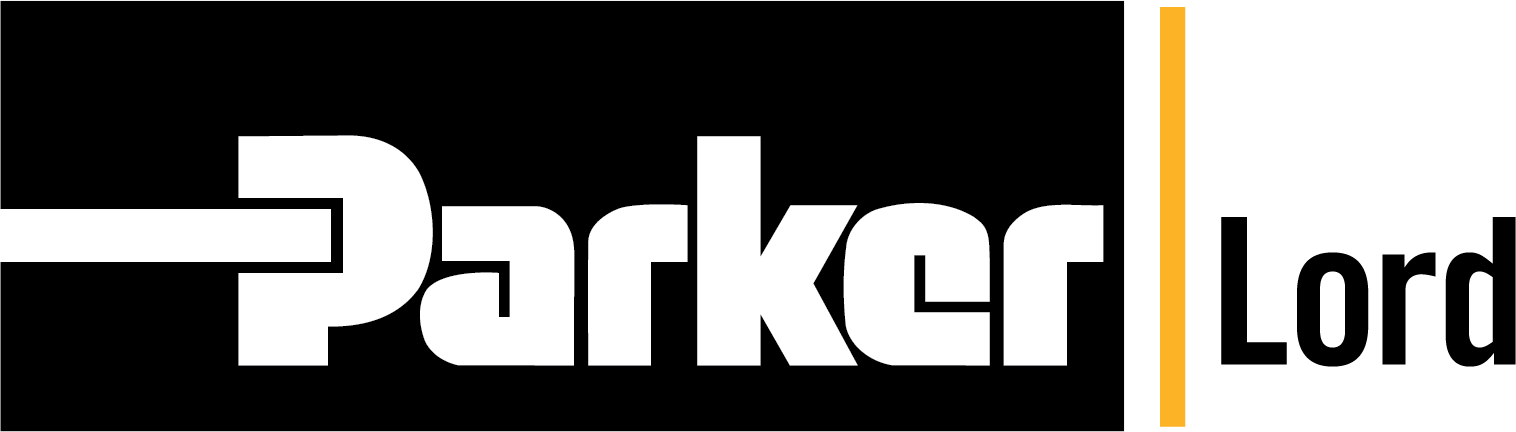
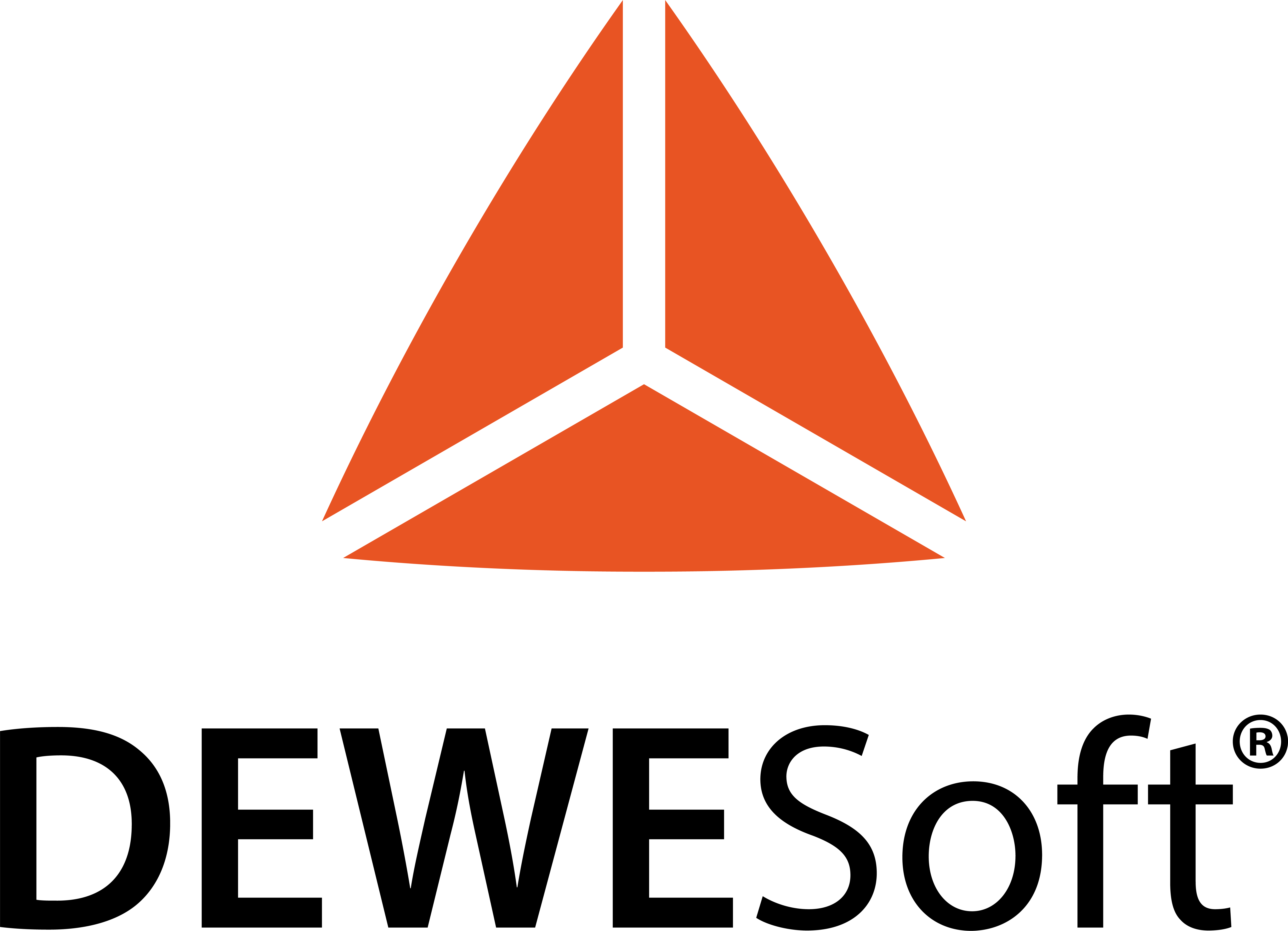
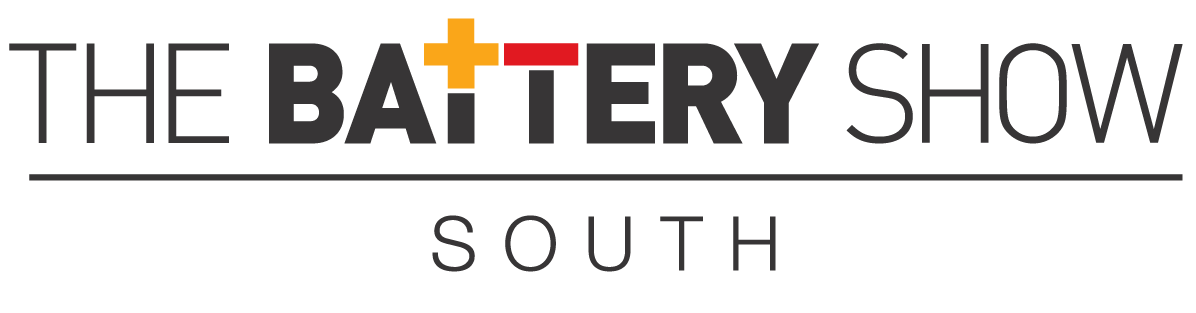
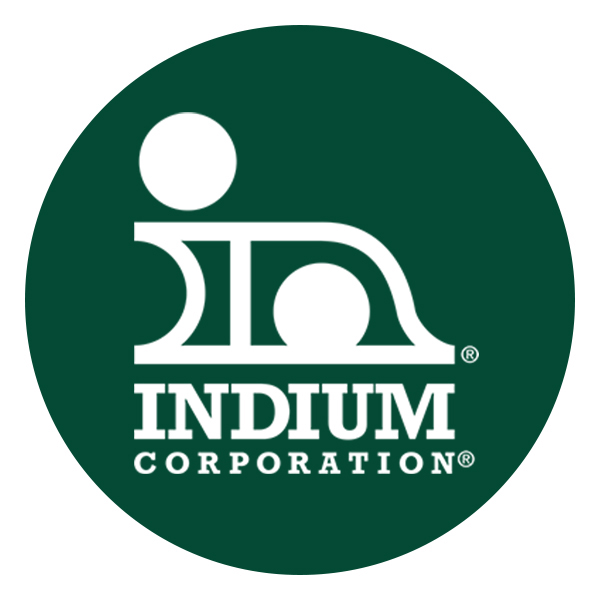

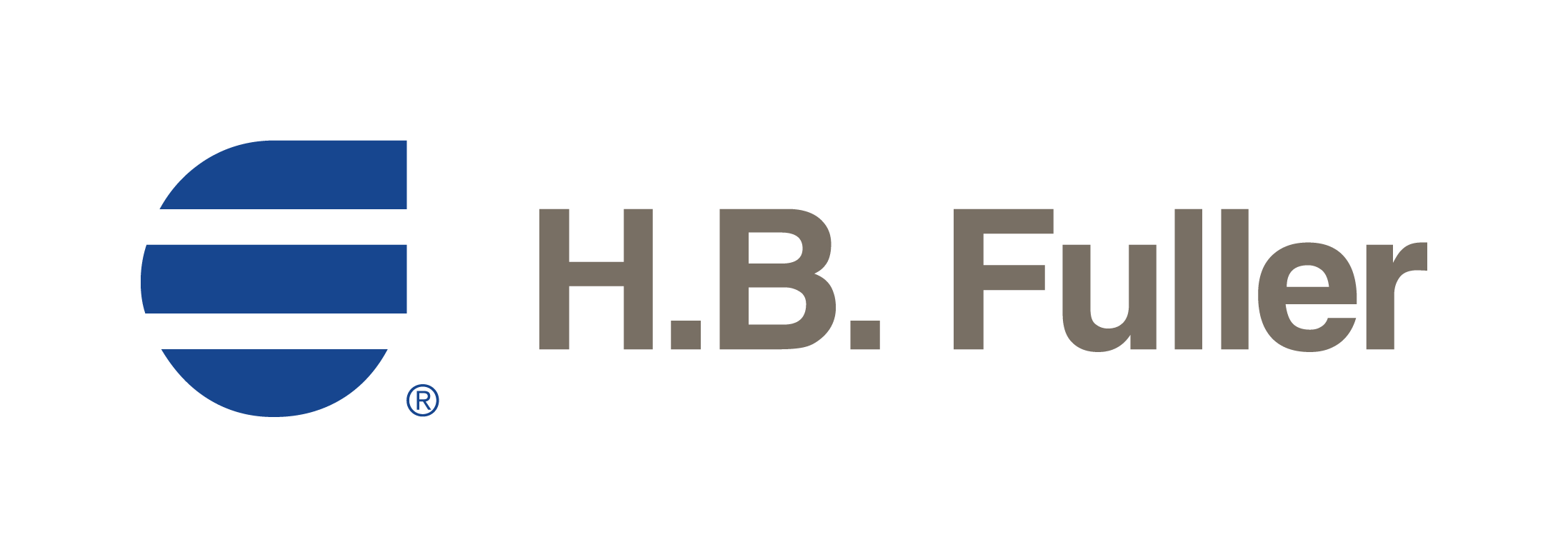
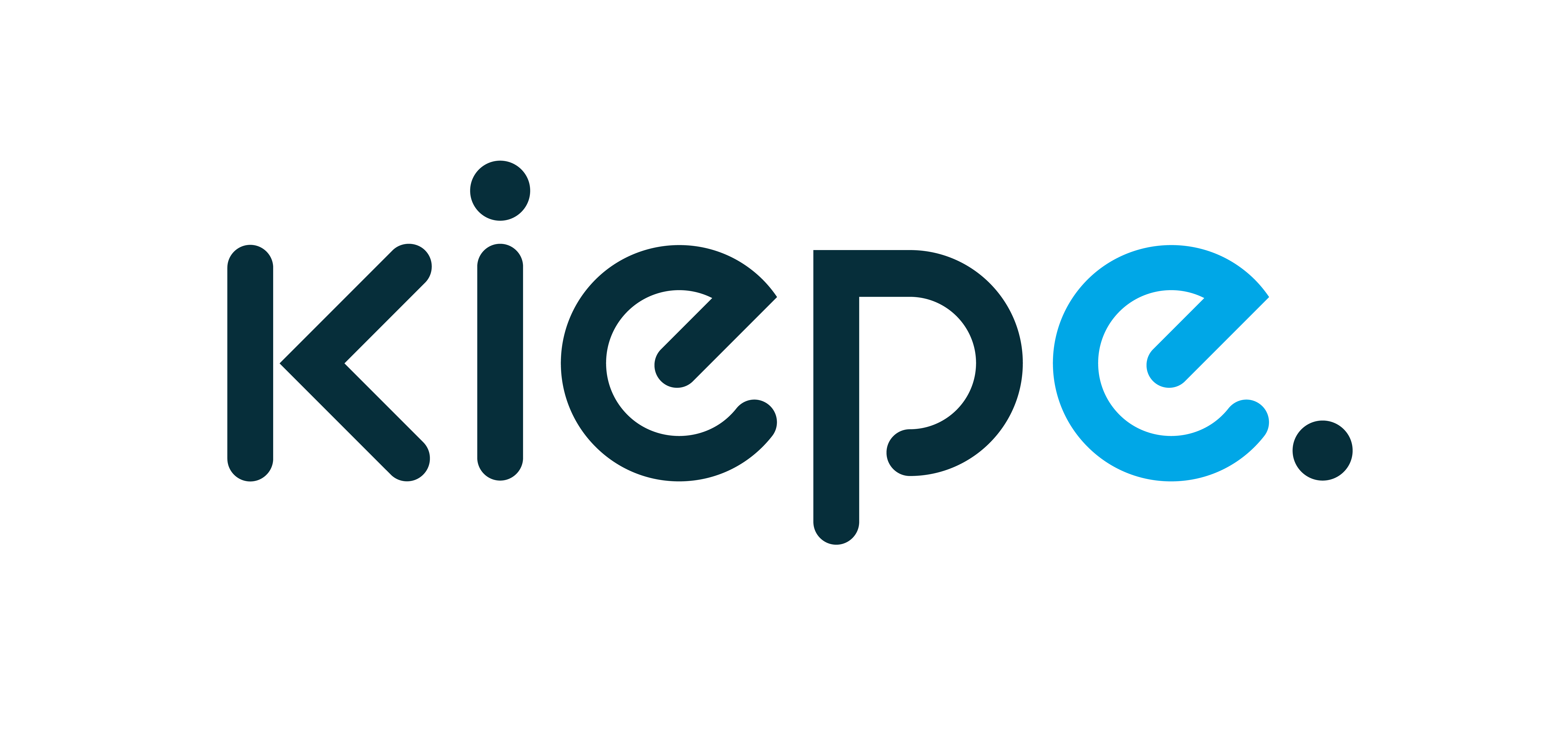
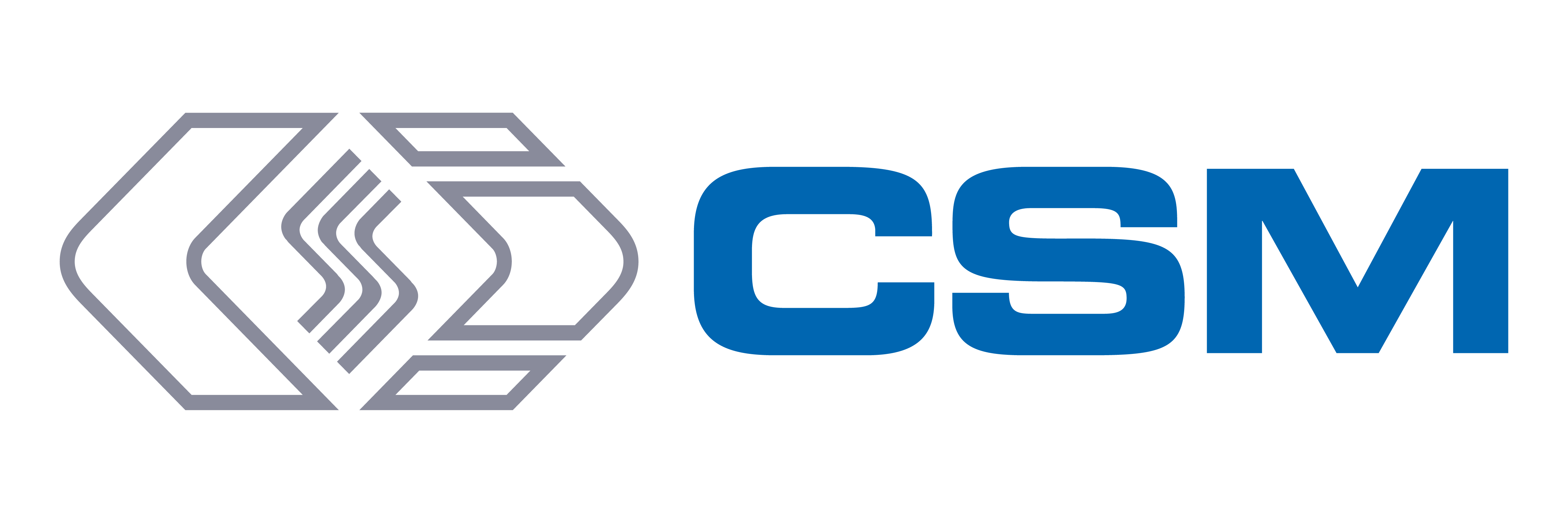