Battery reuse and recycling
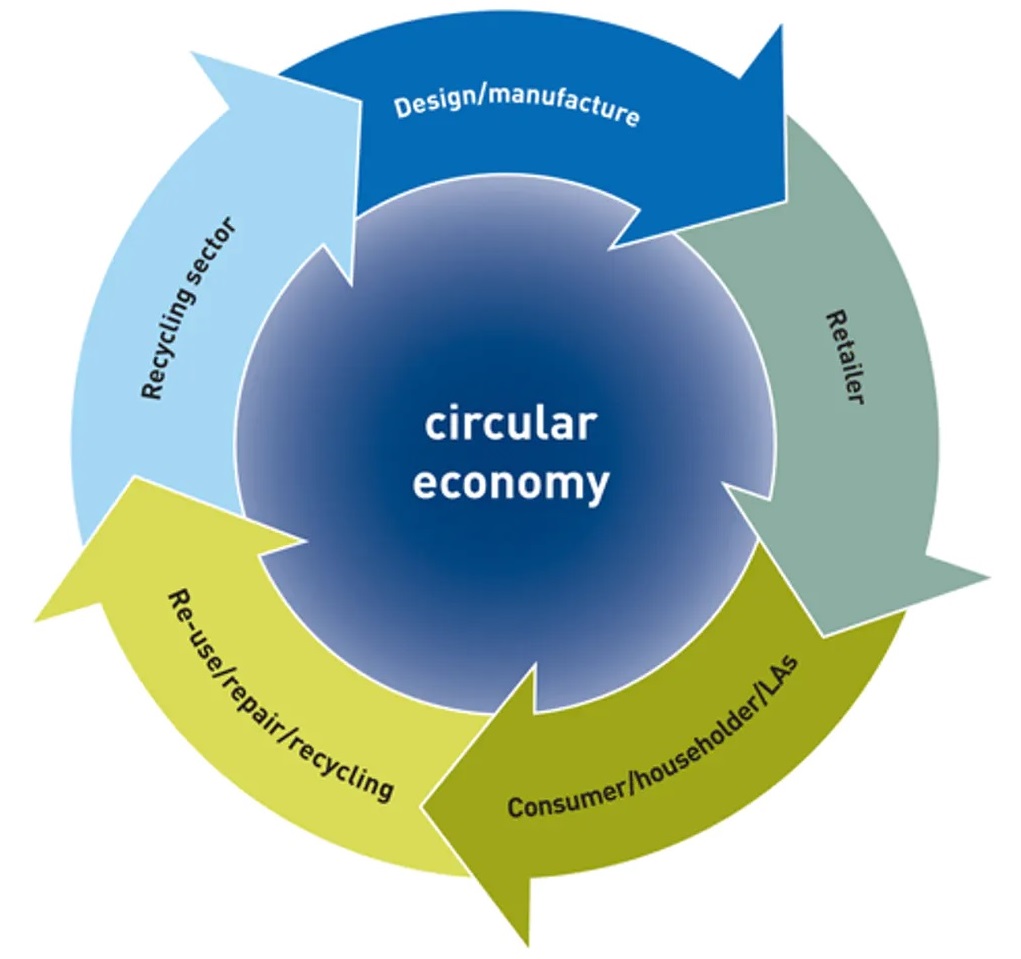
As awareness grows of the environmental problems associated with several types of lithium mining and extraction, it is becoming obvious that the eco-friendly shine on EVs could soon become tarnished unless those processes are cleaned up and a circular economy for lithium-ion batteries and the materials in them can be established (writes Peter Donaldson).
A circular economy means reusing and then recycling a given product, and efforts to do both for batteries are gathering momentum. However, the approach comes with costs and complexities.
When EV batteries have outlived their usefulness in their original application – which may be after four or five years in large vehicles such as buses, or a decade or more in cars – they typically still have about 70% of their energy storage capacity. That means a second life in various less demanding uses such as storage for solar-powered street lighting, providing back-up power for lifts, and even home electricity storage.
Although vehicle batteries can be reused unchanged in some applications, they often have to be dismantled and the modules or cells reassembled into smaller units to suit new applications. The cells also have to be tested individually to determine their remaining life, then matched up with others before they are reassembled into ‘new’ batteries. Their remaining life depends largely on how deeply they are cycled in their new role.
Another issue is the suitability of different lithium-ion chemistries for reuse applications such as stationary power. Nickel cobalt aluminium oxide, lithium iron phosphate and nickel manganese cobalt oxide all have different characteristics.
Despite the differences in their chemistries, they all will eventually need to be recycled, and the required processes are still evolving. While automation is making big inroads into battery assembly, the dismantling – an essential early stage of recycling – is still mostly done manually, a result of the differences between the conditions under which the two take place.
Battery factories provide highly structured environments for automated assembly, which happens in pre-programmed steps that are specific to each model of battery. In contrast, dismantling happens in less structured environments and, as there is little or no standardisation in EV battery pack design, form factors are highly varied, which makes automation far more challenging.
Robotic systems developed for the task will therefore have to be very adaptable, which is likely to put a premium on AI.
After disassembly, the cells containing the valuable metals typically go through pre-treatments such as shredding before being subjected to final treatments to extract them. The major divide here is between pyrometallurgical processes such as The cycle begins with collecting the batteries and fully discharging them. After that, the packs are dismantled down to cell level and shredded into a fine powder known as ‘black mass’. Next comes a multi-step chemical treatment to extract the cobalt, nickel, and lithium salts. The resulting high purity salts – cobalt, nickel and lithium sulphates, and other forms – are then used to make new battery cathodes.
However the reuse market develops though, spent batteries will eventually have to be recycled, and there is plenty of scope to engineer safe, efficient and clean processes.
ONLINE PARTNERS
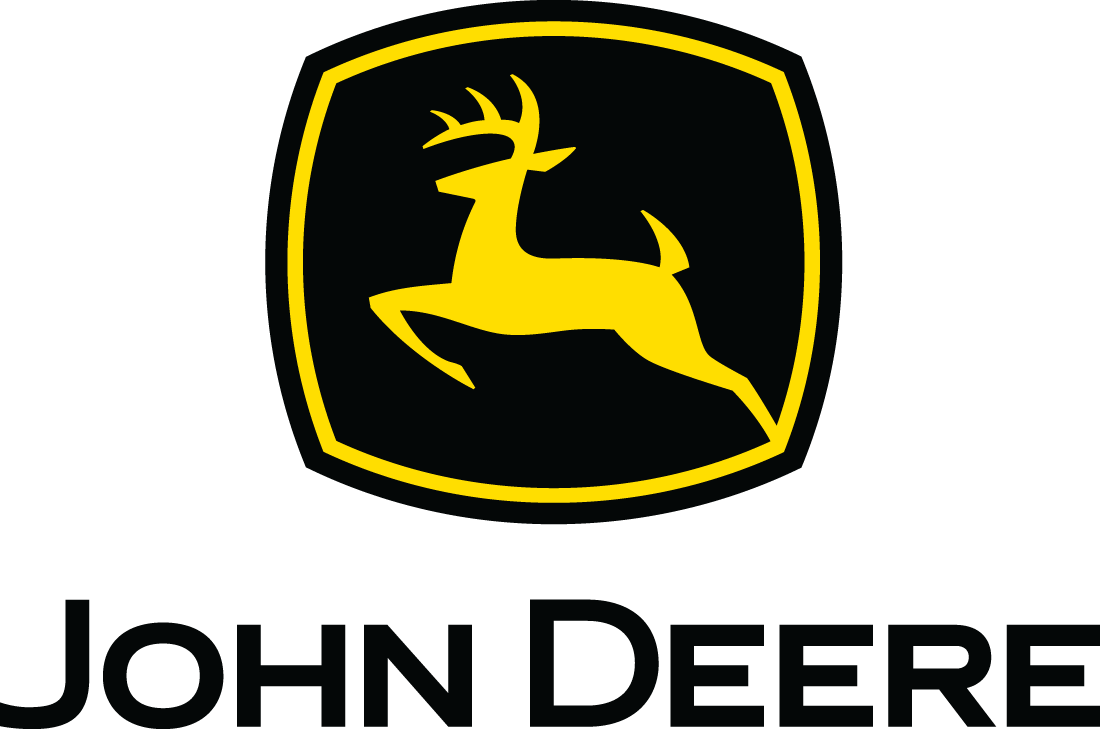
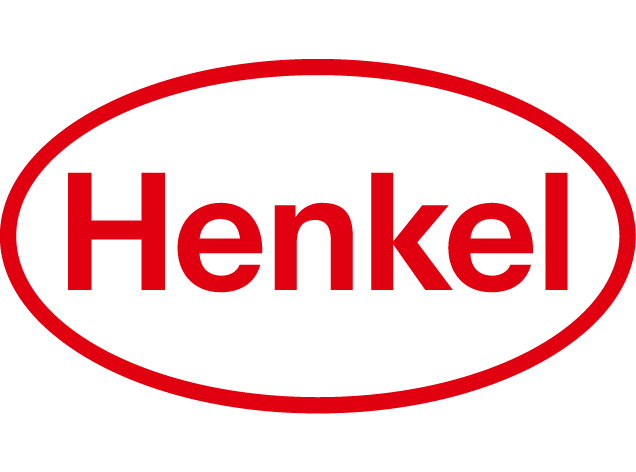
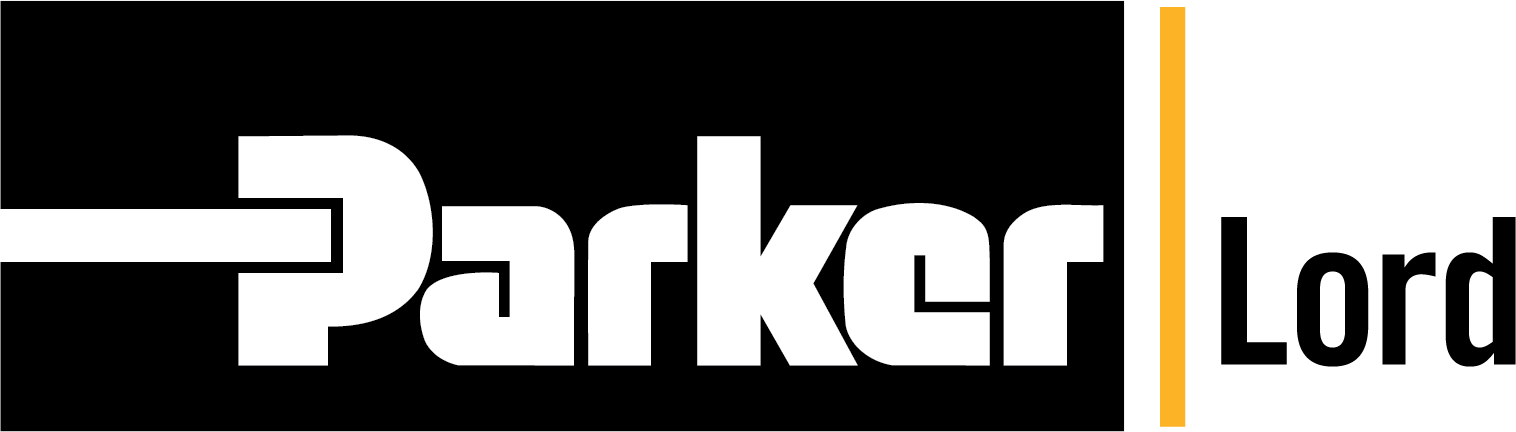
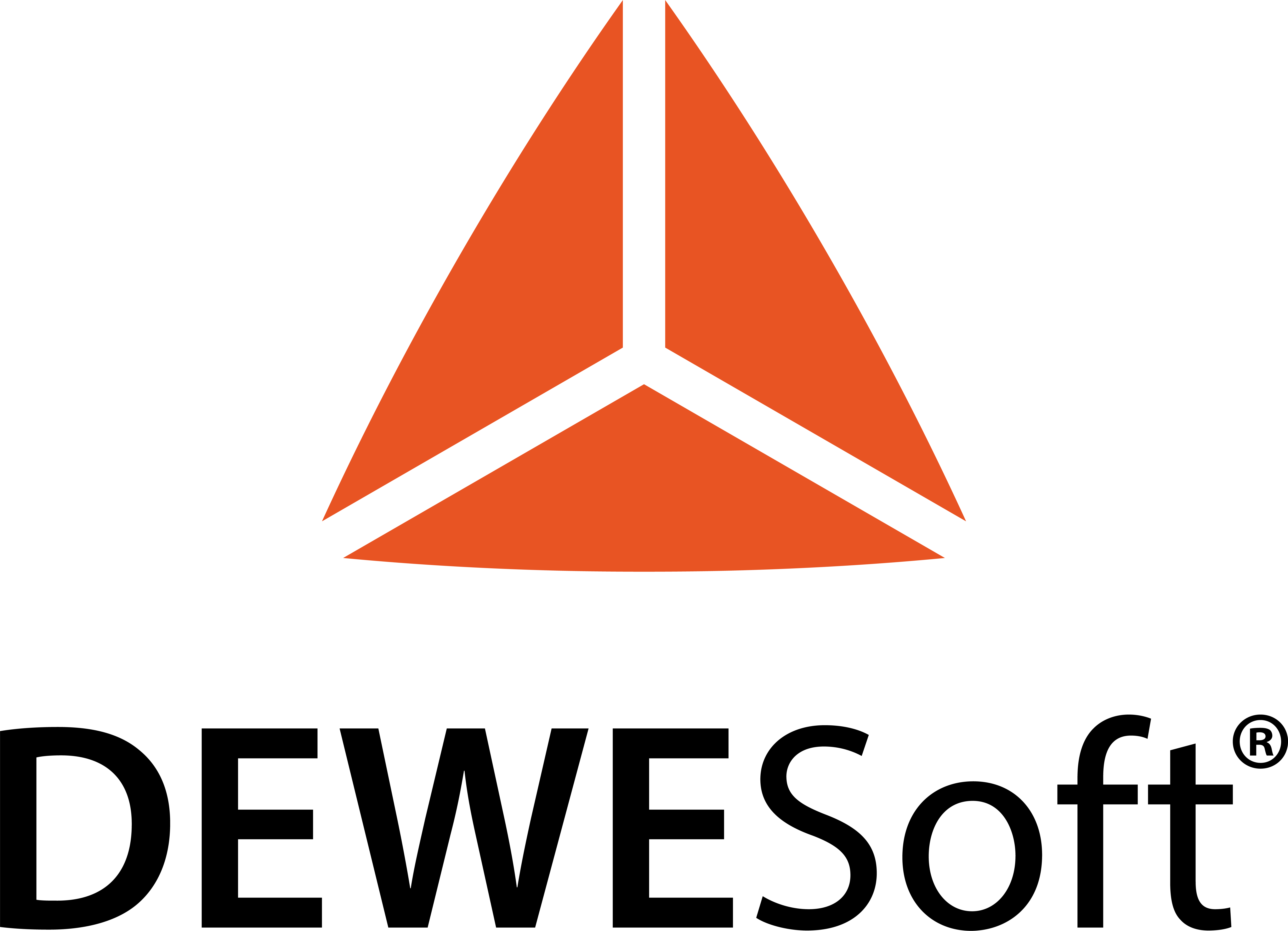
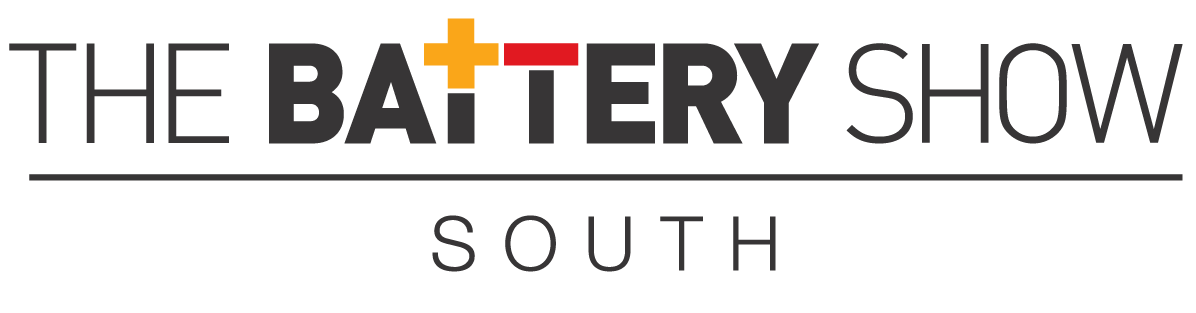
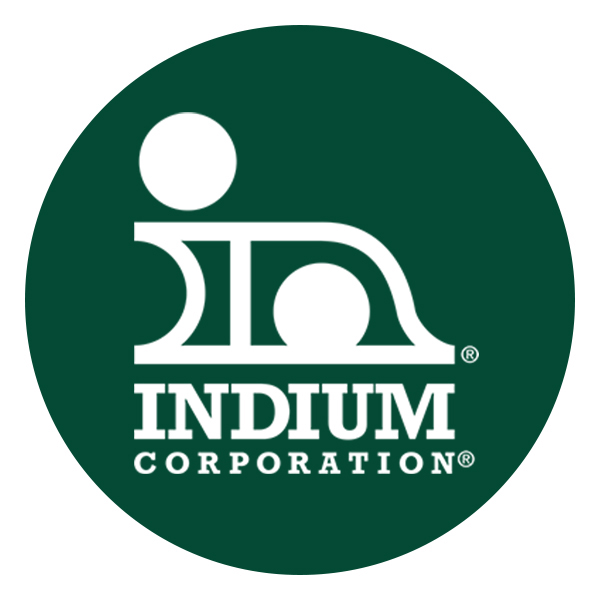

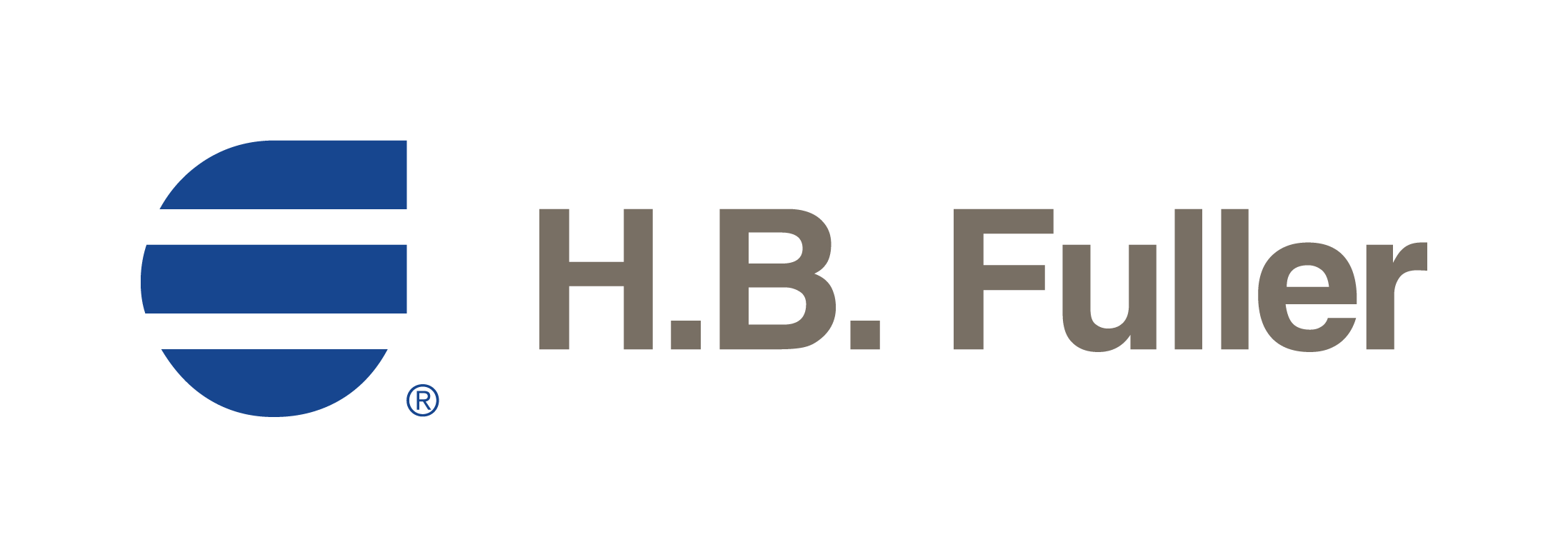
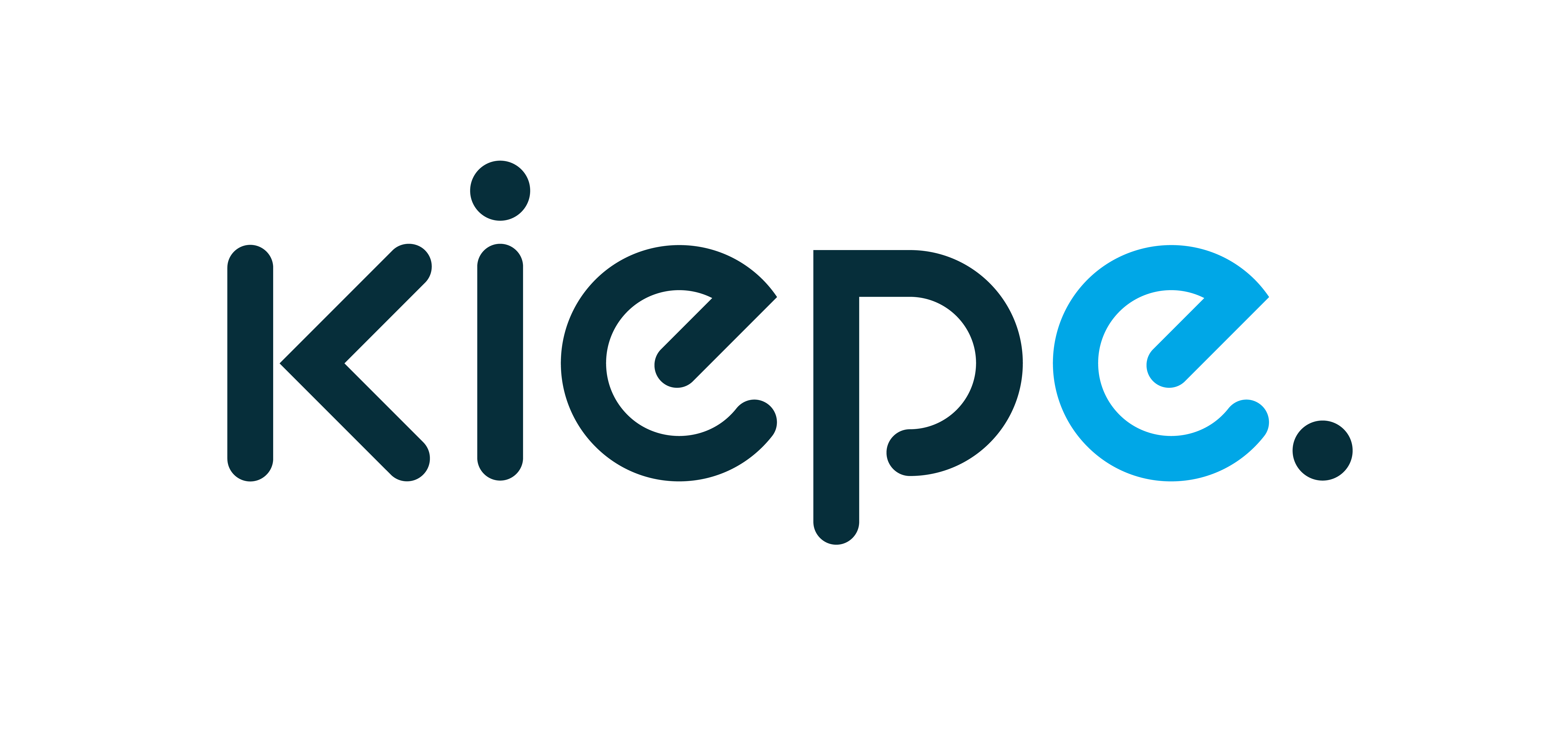
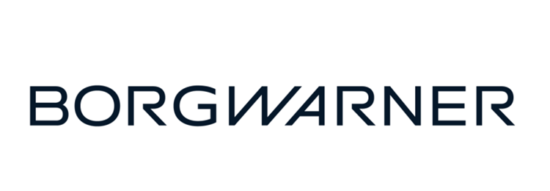