Separator and current collector protect cells from shorts
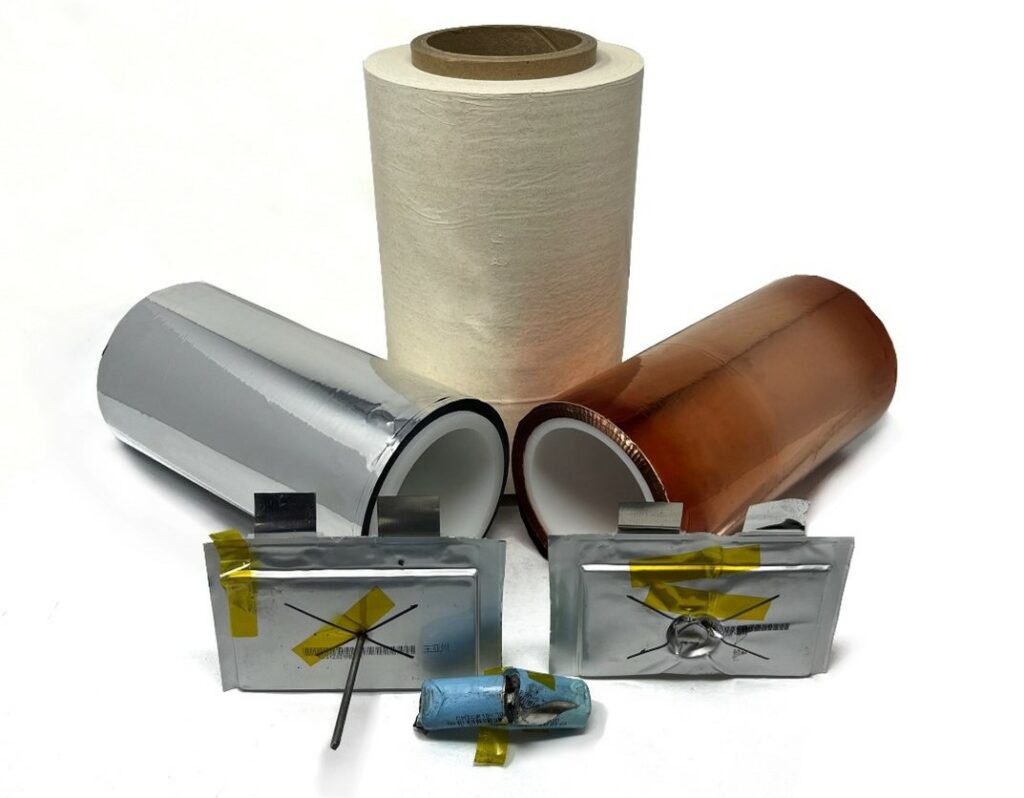
(Images courtesy of Soteria)
Soteria Battery Innovation Group, together with a consortium of more than 110 organisations, is making available new separator and current collector technologies that protect battery cells from the effects of internal short-circuits (writes Peter Donaldson). The consortium members include NASA, Mercedes-Benz, Lenovo, DuPont, Bosch and Motorola.
As European consortium director Dr Juergen Kellner explains, “We are working with an open innovation platform to bring together companies in the lithium-ion battery value chain. It is our vision to develop the technology for inherently safe batteries.”
In most lithium-ion cells, defects or damage can puncture the thin plastic membranes that separate the anode from the cathode, creating short-circuits through which solid metal current collectors dump energy into the cells, causing cell failure, overheating and, potentially, thermal runaway. Soteria’s technology prevents that by using a thermally stable fibre-based non-woven separator and metallised film current collectors that effectively act as fuses, isolating the short.
Dr Kellner says the separator is made from a combination of fibres including cellulose and aramid. The aramid, for example, remains stable at very high temperatures, which means the separator will not melt or shrink away from the site of the short, preventing the damage from spreading.
The separator works with the new current collectors. Conventional collectors are made from solid metal foils: copper for the anode side and aluminium for the cathode side. Soteria’s collectors are instead made from thin layers of these metals (500-1000 nm) deposited onto both sides of a polymer film using a physical vapour deposition (PVD) process. The layers oxidise away within a millisecond when exposed to the short-circuit current, preventing further current flow.
“There is then no possibility of further energy going into the fault and initiating the catalytic reaction that can lead to a thermal runaway,” Dr Kellner says. “You have a cell with a dead spot at the point of the short, but the rest of the cell still works.
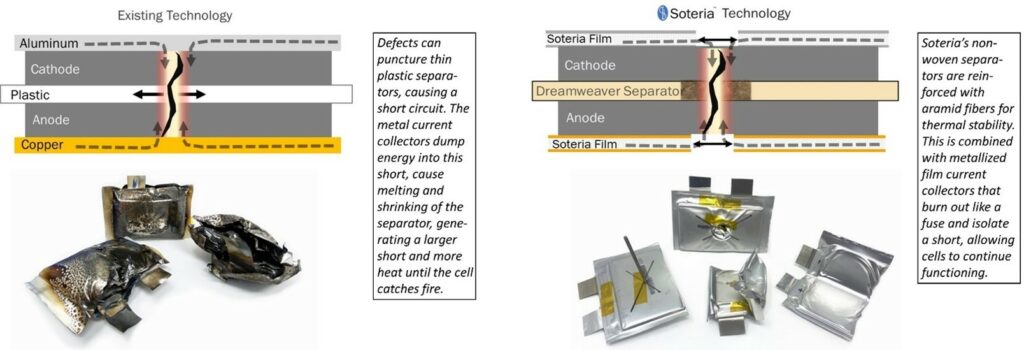
“Solid metal foil cannot oxidise away because it is just too strong, but here you have only 10 or 20% of the metal and then you have the polymeric material,” he adds. “We have tested this several times, and other organisations such as NASA have also tested and confirmed it. That is basically why we can regard it as a kind of built-in fuse inside the cell.”
He says cell performance is “very much comparable” with conventional cells, regardless of whether the cell is cylindrical, pouch or prismatic. Work continues with partners to reduce the separator’s thickness from 15-20 microns down to 12 or even 10 microns. “We already have some thinner prototypes, and over the next year we expect to have available separators that are between 12 and 14 microns.”
Besides safety, the new technologies also promise savings in terms of cost, weight and complexity, he argues. The fibrous separator, for example, is created using a wet-laid process similar to paper-making, an inexpensive process that, when used at scale, could make separators that cost less than plastic ones.
The PVD film collector foils use only 10-20% as much metal as solid copper and aluminium foils. “Our current collector is much lighter, and, because copper is quite expensive, there is also the potential to make a metallised film somewhat cheaper,” Dr Kellner says.
Further potential savings could come at the battery system level. “These days there is a lot of technology around the cell to manage safety,” he says. “But if you start with a safe cell at the heart of the battery you can reduce these additional safety features, and you could translate that into longer range or cheaper batteries.”
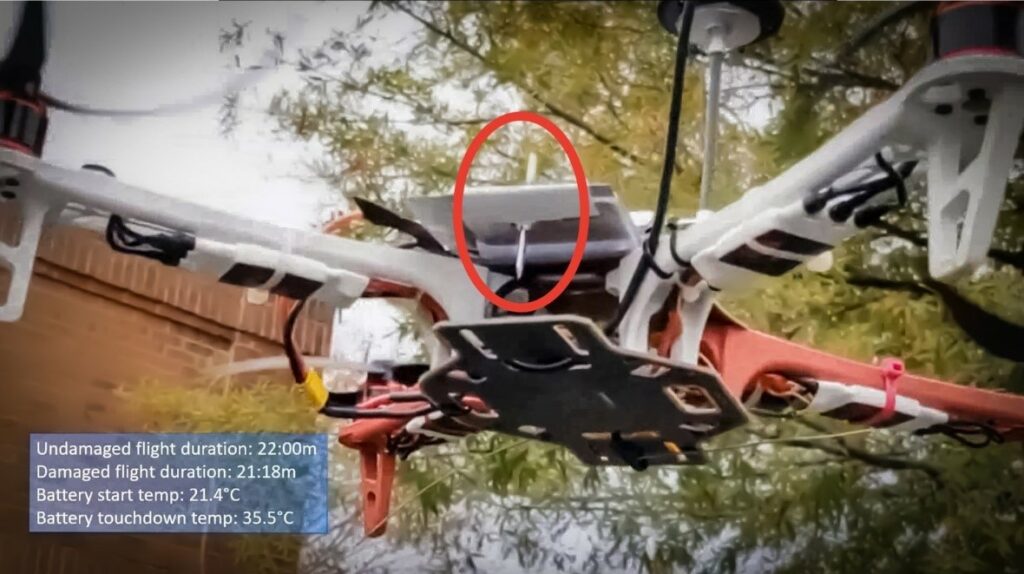
Click here to visit Soteria to find out more information https://www.soteriabig.com/technology
ONLINE PARTNERS
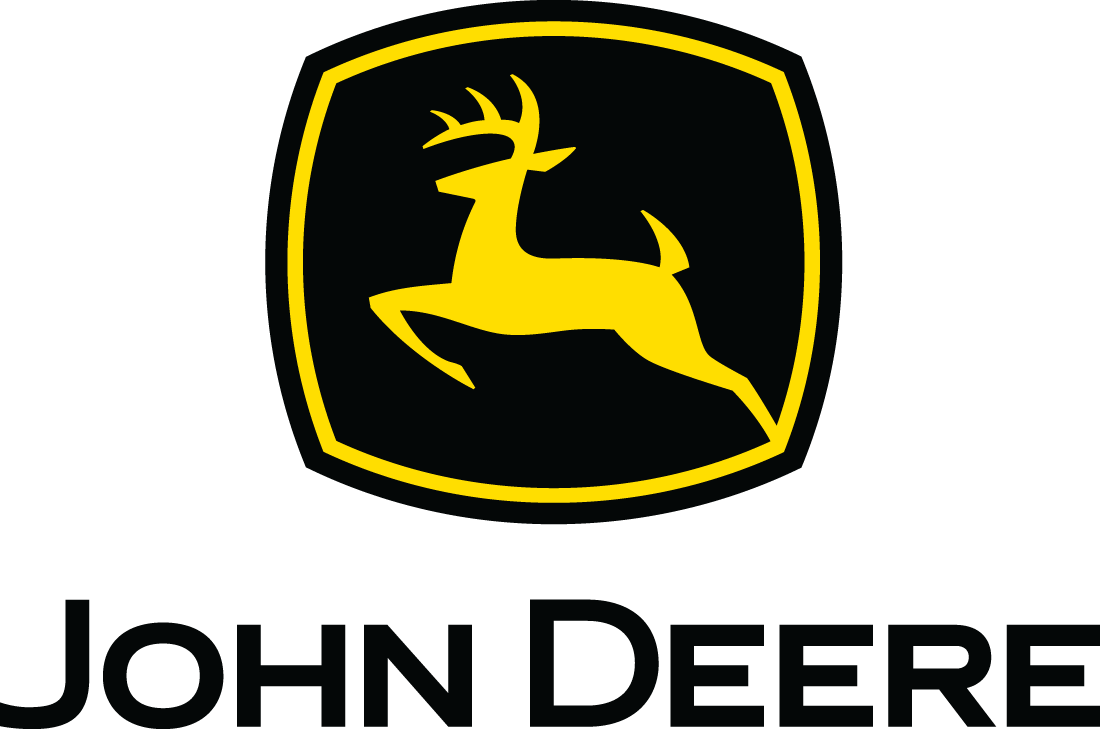
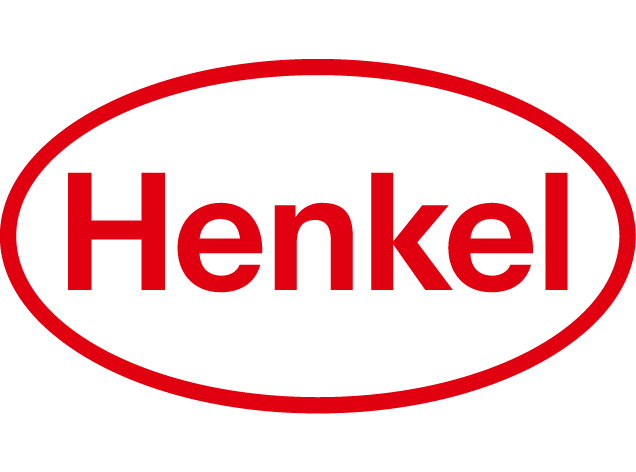
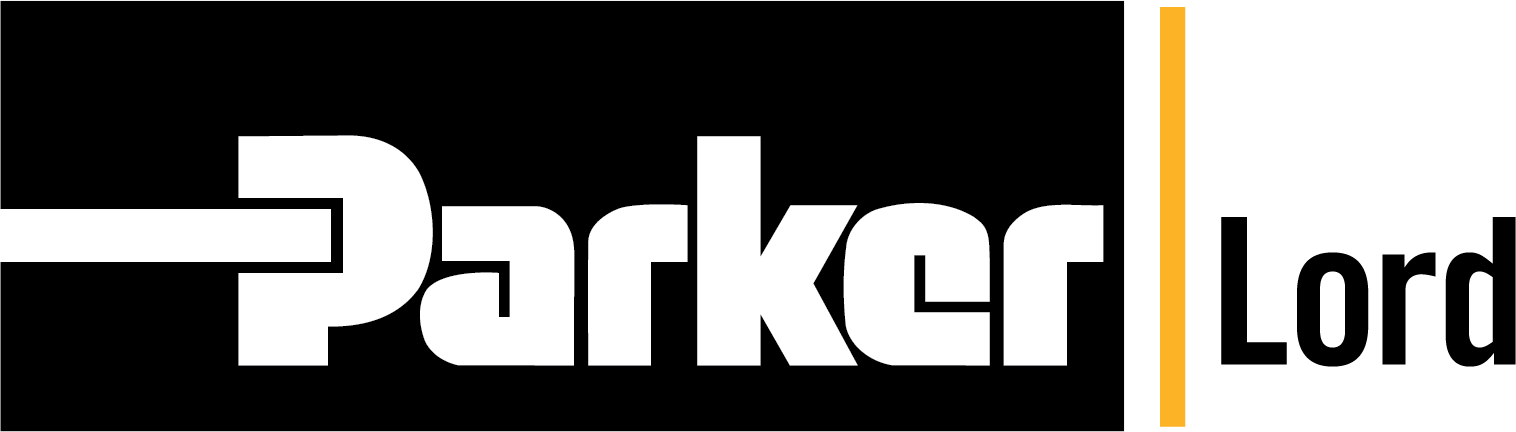
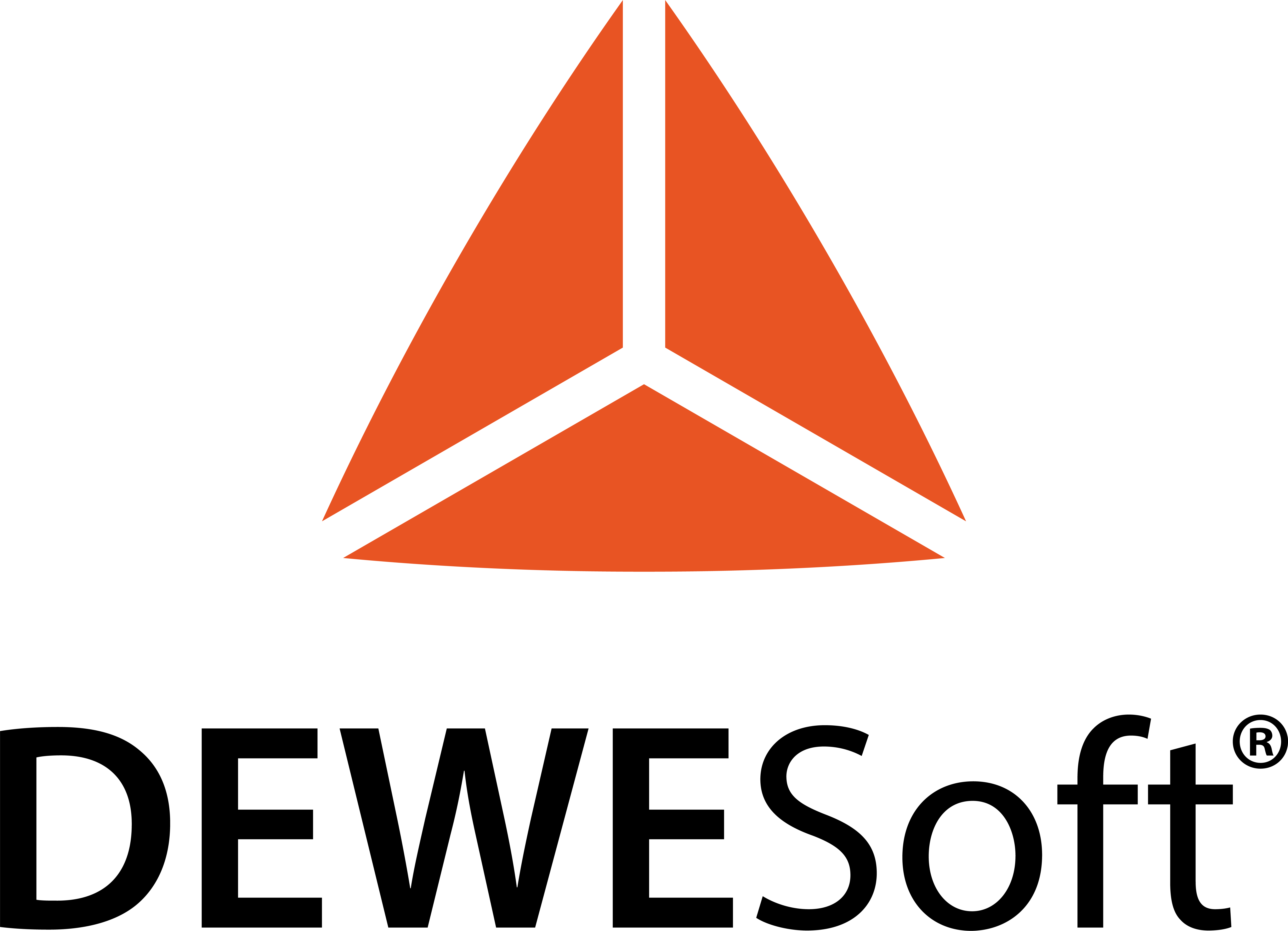
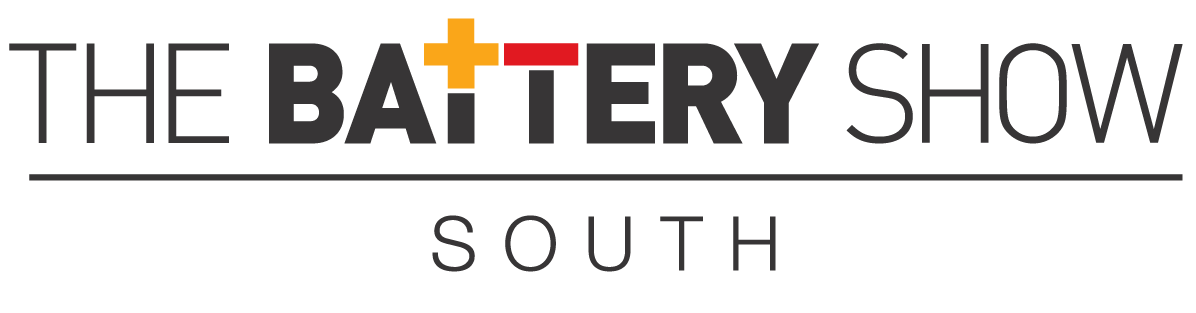
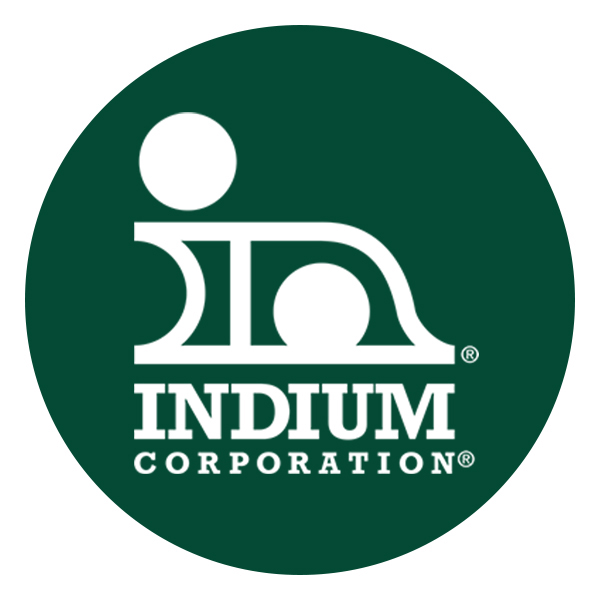

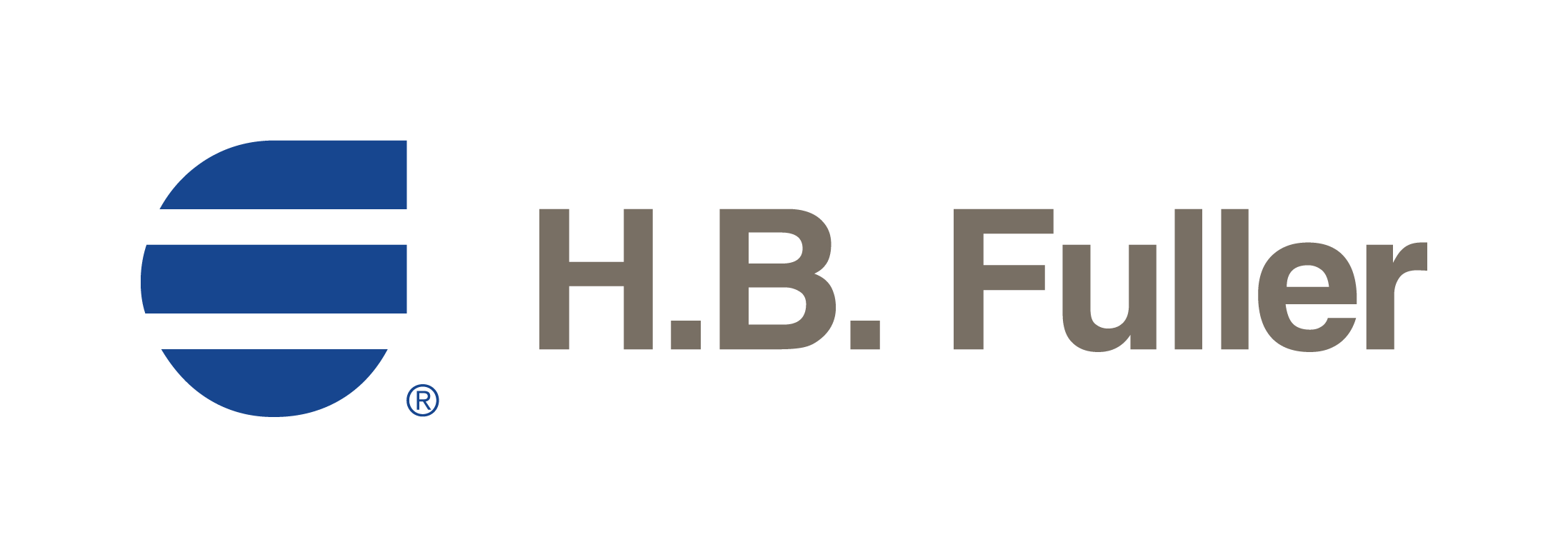
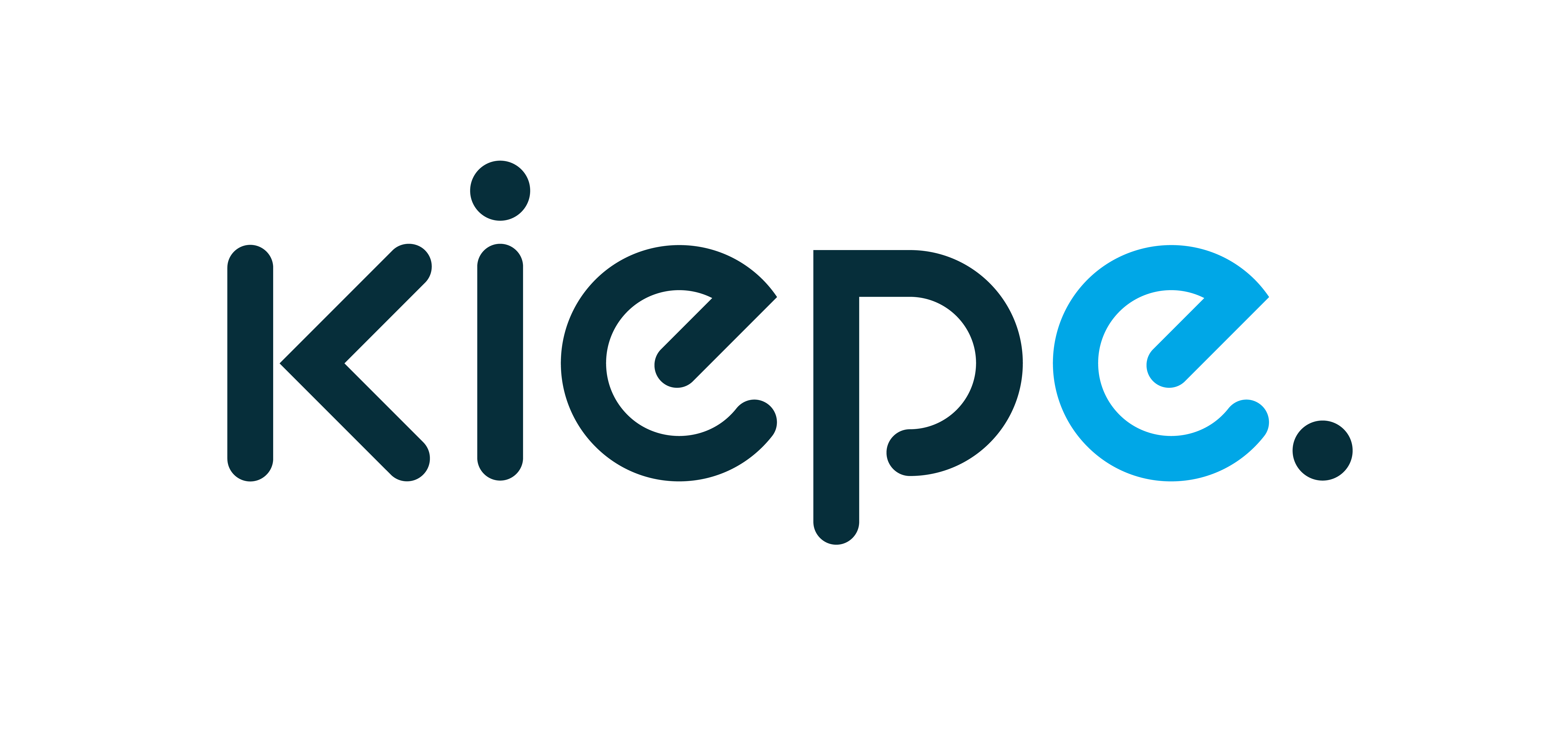
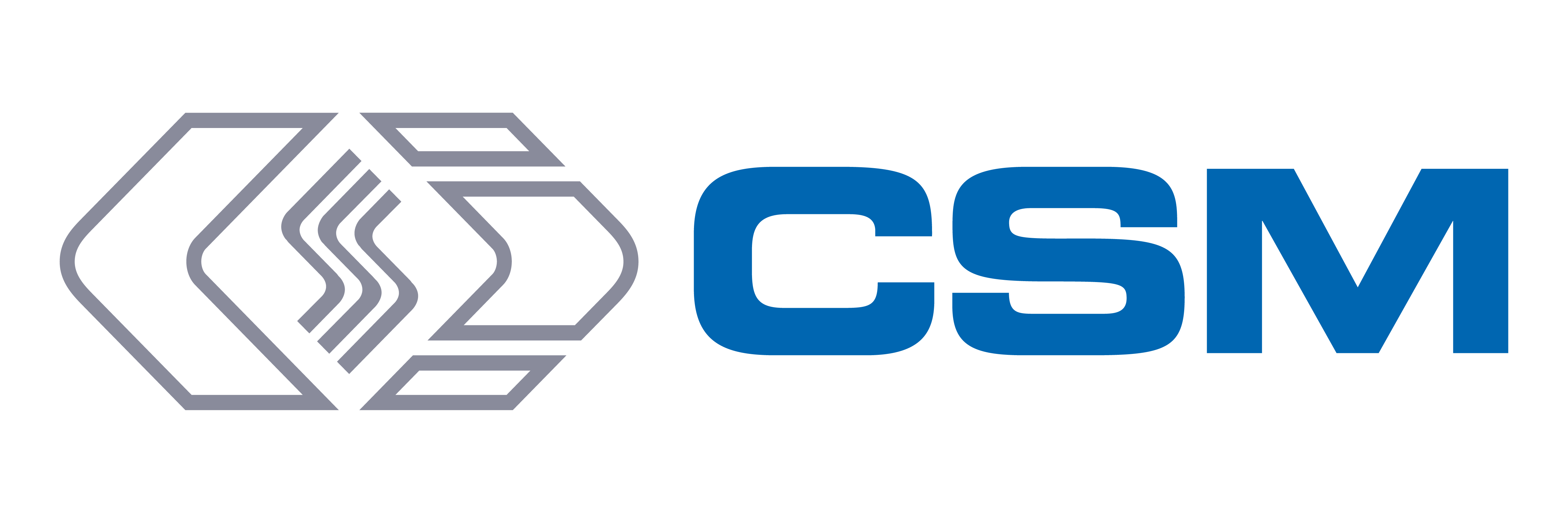