Lion8 refuse truck
Rory Jackson details the development of this combined all-electric truck and refuse collection system.
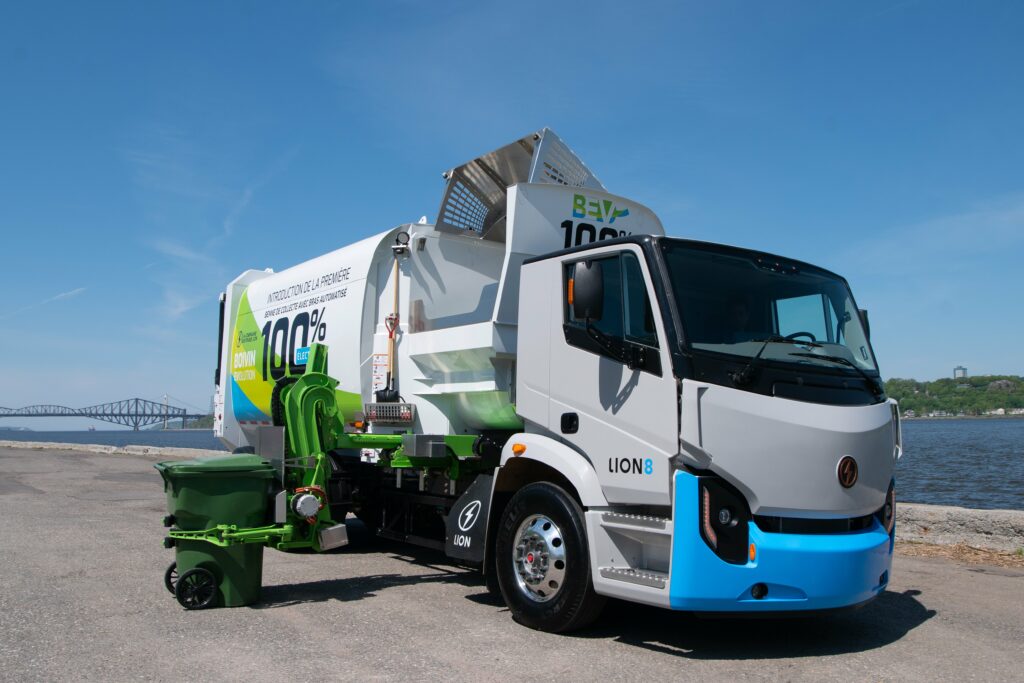
Gathering interest
When the owners of the Lion Electric Company first set their eyes on engineering specialised commercial vehicles for niche users who have distinct operational and cost requirements, they spent an initial five years on planning and r&d for their approach. Once it had recruited enough electrical and automotive engineers, the Quebec based company decided to focus its attention almost entirely on all-electric powertrains.
Its approach eschewed the dieselhybrid and compressed natural gas solutions that were being rather more heavily touted five to six years ago. But that refocusing led to Lion Electric’s first production electric vehicle – the LionC, an electric school bus, hundreds of which are now in use across North America.
“We had no interest in inter-city vehicles because of how prohibitive the mass and volume of batteries needed for long-distance transport were at the time,” says Yves Desjardins, special projects director at the company. “For short-distance commercial vehicles operating inside city limits though, such as municipal vehicles and last-mile deliveries that need no more than 250 miles’ worth of energy storage, we firmly see all-electric powertrains as ideal for urban companies looking to cut their operating costs.”
“The school bus is designated as a Class 7 truck [weighing between 26,001 and 33,000 lb], so we decided that the competencies we’d gained developing that vehicle gave us an engineering ‘edge’ for all-electric heavy-duty commercial road vehicles,” Desjardins says. “So we turned our eyes towards Class 8 trucks [vehicles weighing 33,001 lb or more] that could rapidly cut their users’ operating costs – and without needing green subsidies to do it either.”
Waste and recycling collector
Two years ago, during the development of the Class 8 platform, the company was approached by Boivin Evolution, also in Quebec, which had developed an all-electric refuse collection system. This electromechanical bin collection ‘payload’ had been designed and tested to use about 25% of the energy consumed by conventional diesel-andhydraulics-powered waste collector trucks.
As Desjardins explains, “They worked for several months on developing it, intending to install it as a plug-and-play payload on diesel vehicles but with the advantages of greatly reduced power consumption and not having the power take-off [PTO] suddenly asking for loads of energy. But when they found out we had an all-electric chassis that was ready to go, it was, in engineering terms, a perfect match – in their eyes and in ours.
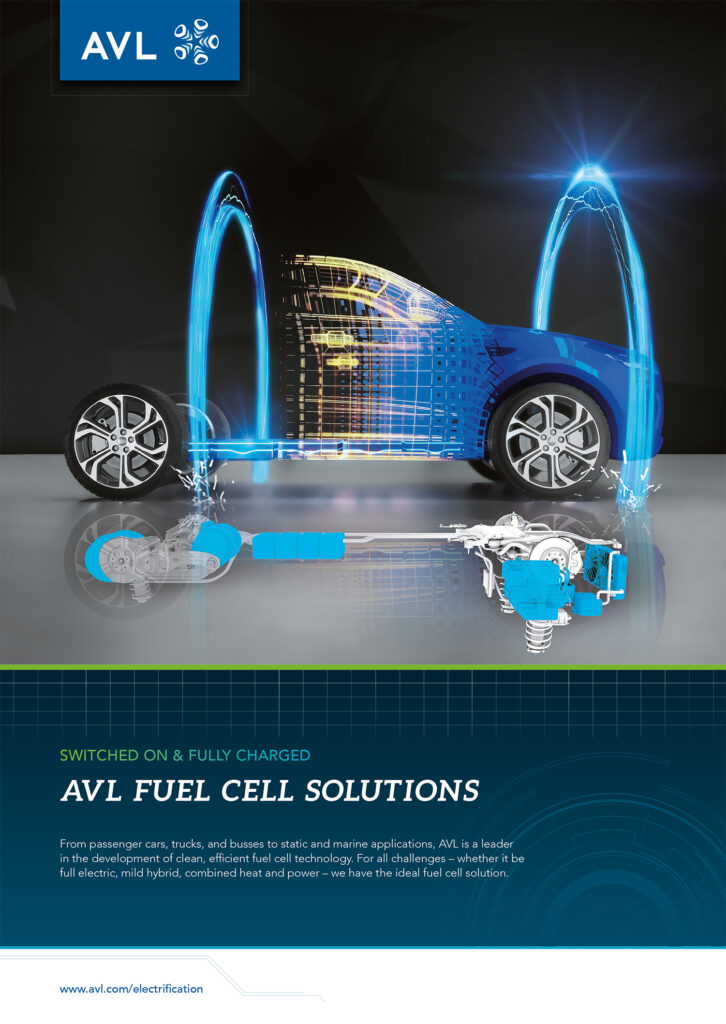
“When we designed the Lion8 we included what we call our ePTO [electric power take-off], which leaves room for any equipment the customer wants to add onto the back of the vehicle. So for Boivin we took their output requirements, gave them choices of several voltage levels on either AC or DC, and then we matched the power supply to the needs of the refuse collection mechanisms.”
The Lion8’s platform has two frame rails for integrating application payloads, and the wheelbases and powertrain components can be matched and moved around to keep balance. Thus Boivin and Lion Electric spent from 2017 to ’19 exploring the optimal permutations of their technologies.
The waste collection mechanism features an internal bay for holding and compacting refuse, and Boivin’s system offers two different mechanisms for ‘grabbing’, lifting and emptying dumpsters into the holder: a system of side arms and a rear-loading system.
The internal body has a volume of 15.3 to 25.2 m3 , while the side arm ‘hopper’ is 2.3 m3 and has a floor made from 9 mm-thick abrasion-resistant steel.
The vehicle platform
As mentioned, the Lion8 base platform truck is a Class 8 truck with a kerb weight of 24,600 lb (11,158.37 kg) and a gross weight rating of 54,600 lb (24,766.14 kg). Within its 558.8 cm wheelbase and its 670.6 cm total vehicle length, the vehicle will be customised according to the needs of different municipalities across North America.
Although exact figures for each model delivered can vary, particularly in terms of operating performance ratings and power specifications, the truck’s typical top speed is 105 kph. The drivetrain can be configured for a maximum power output of 350 kW, and a maximum torque output of 3400 Nm. Up to 480 kWh of energy can be stored onboard the vehicle, for a maximum range of 400 km on a single charge.
The end result of each custom arrangement performed on every Lion8- Boivin truck powertrain will be that the vehicle is designed to service 1000 ‘doors’ – houses or organisations – on a full charge.
First light
The exact time at which the truck is prepared for its first operations of the day will be more flexible than that of a conventional fuel-powered, hydraulically actuated refuse collection vehicle. That is because of how quiet it is relative to the ‘normal’ configuration of such vehicles.
“When most refuse trucks pick up and compact garbage, their engines will go on half-idle to bring the PTO up to speed, and at some point the engine fan also comes on for standstill cooling so it generates more noise,” Desjardins explains. “Because of that amount of noise, they aren’t allowed to start early in a city while people are sleeping, and they have to stop before 8 pm.”
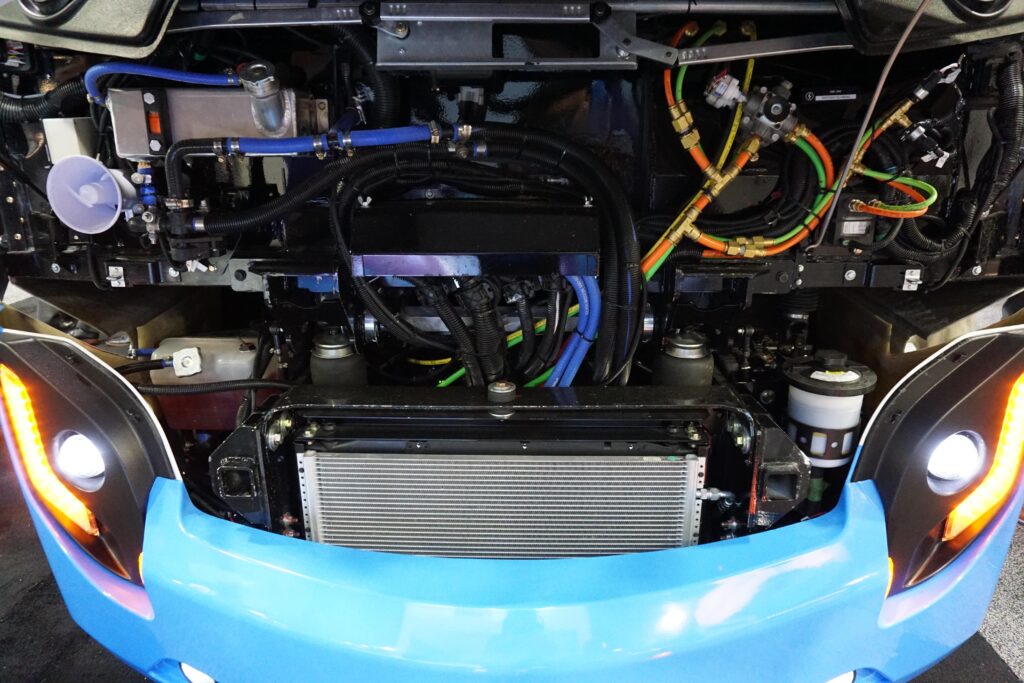
With electric trucks, however, sanitation crews can start earlier in the day, when roads are clearer, without incurring noise complaints from city residents. The only significant noise will be glass bottles breaking as they are emptied into the vehicle.
“It could however still operate in normal hours, and technicians could choose to use the 12 hours of downtime for slow trickle charging,” Desjardins adds. “We anticipate that in the future, as these trucks are increasingly required to work for up to 18 hours a day with only six hours for charging, we might build them without onboard chargers and just use DC fast charging.”
Before the truck is sent off to begin its operations for the day, safety checklists must be completed for the vehicle and powertrain. To streamline this process as far as possible, Lion Electric has put as much of its power electronics and other key systems and interfaces as it could into the bonnet of the vehicle’s cab.
“On a diesel truck, technicians have to check the oil levels, the DPF [diesel particulate filter] and around a dozen other items,” Desjardins notes. “On our side, there’s really just the coolant levels for the motor and the battery thermal management, as well as the health and operation of the electric power steering.
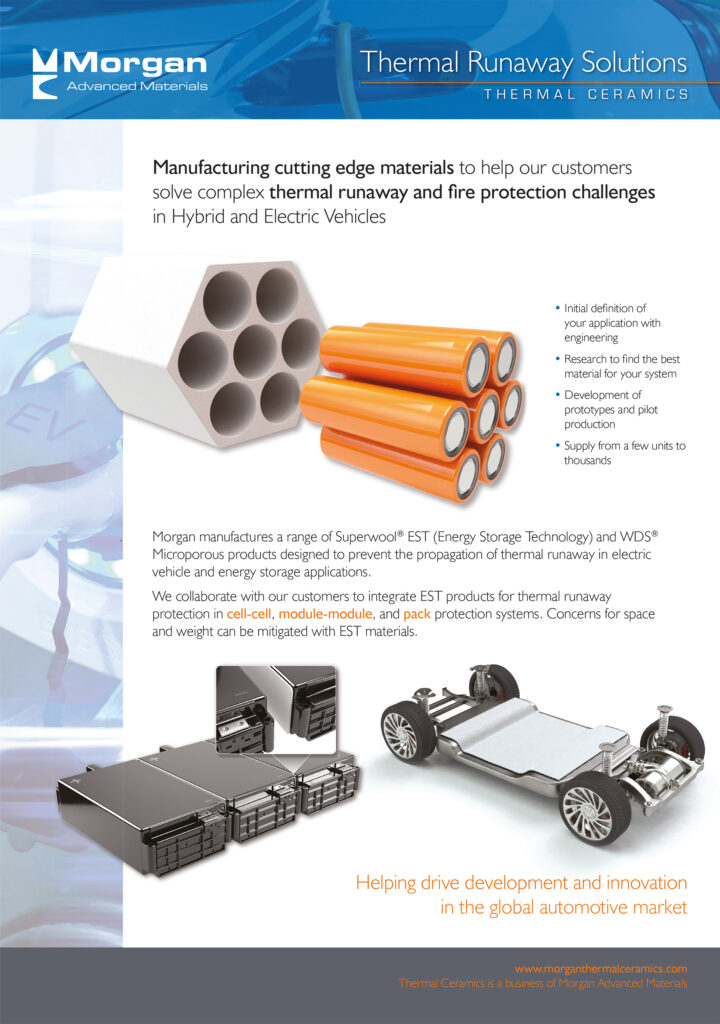
“These are all checked at the front of the vehicle. There are still some standard ‘walking around’ checks to be done, for example the tyres and any brake wear, but they vary between states and provinces.”
Being fully electric, the refuse loaders and compactors are checked through a series of signal-based feedback tests from the vehicle’s main computer. These indicate the status of every electric motor, actuator and sensor inside, and begin running every time the vehicle is started up.
“In operation, if an unusually high current is detected in any of the systems – be it an actuator on the refuse loader or a connector in the truck, say – the computer will receive the data from one of the current sensors and automatically flag it up on the driver’s screen. That enables them to decide if they should continue or pull over and check for a problem on the vehicle,” Desjardins adds.
“You don’t get those kinds of realtime alerts with hydraulic refuse collectors, and on top of that there’s no hydraulic fluid to leak. If there’s a leak while the vehicle’s on a road, the subsequent truck repairs and public road clean-ups can cost between $8,000 and $60,000.”
Balance of parts and routes
As mentioned, there are two mechanisms on the Lion8-Boivin truck for handling waste, and a powertrain that can be configured in different ways to account for the end-user’s required performance. The number of battery cells will vary according to the customer’s need to limit any range anxiety – especially in terms of how far it will have to travel when carrying a full payload of waste and recycling – as well as providing a balanced weight distribution across the chassis.
“In general it’s much easier to move batteries than fuel tanks and driveshafts,” Desjardins says. “There are city regulations on how the vehicle is balanced and how its dynamics are while moving, so we work with Boivin to place the batteries in the optimal place for each type of vehicle.”
For the automated side loader, the vehicle has two electromechanical arms off the right-hand side to securely grip two-wheeled bins (with volumes of 120, 240 or 360 litres). Two chain lifters then hoist and empty them into the truck’s hopper, up to a maximum lifting weight of 350 kg, with the overall cycle taking under 10 s, and all functions using permanent magnet DC motors with a gearbox.
The battery packs are placed within the wheelbase and on the left-hand side to counterbalance the arm on the right hand and the additional weight it intermittently handles.
The side loader mechanism operates on an input voltage of 100 V DC, and consumes around 10 Wh per pick-up, for an estimated total of 10 kWh per day.
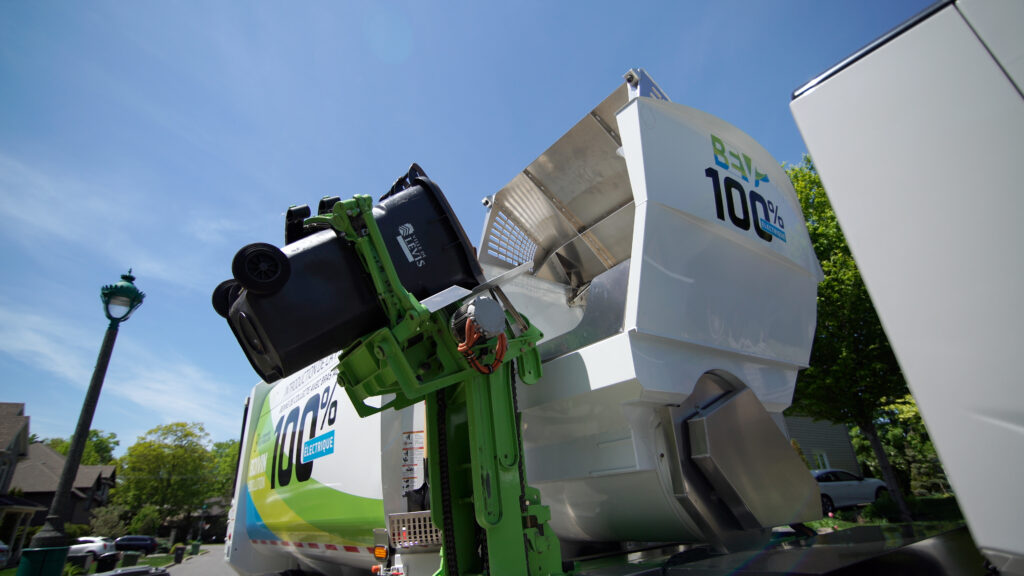
“We will have the same input voltage for the rear loader, 100 V on average, and we estimate the energy consumption will be about the same as the automated side loader, although the rear loader mechanism itself uses less power,” says Frederic Proulx, vice-president of operations at Boivin Evolution. “That is because the auger compactor on the rear loader will consume more with the increased quantity of refuse material picked up, up to a maximum of 32 kWh per day, so it balances out.”
The battery packs use NMCchemistry cells, but further details are proprietary, Lion Electric having assembled the cells and modules in-house. The BMS and thermal management system have also been produced in-house, and it has been key to allowing the truck to operate in Quebec winters of -30 C and Arizona summers reaching +45 C.
“Many battery chemistries have basically the same power-to-weight ratio,” Desjardins says. The key thing has been our management solutions – how we heat up the batteries in winter, as well as cooling them when needed – to keep the cells within a certain temperature range.”
As well as sealing the enclosure (with safety seals tied to the warranty on the batteries), the BMS also tracks and records each cell in real time for voltages, temperatures and other variables such as the state of health and state of charge. It also tracks the C-rating to ensure the user does not draw more power from the batteries than is safe (during acceleration, for example), or fast charge at higher than the recommended rate.
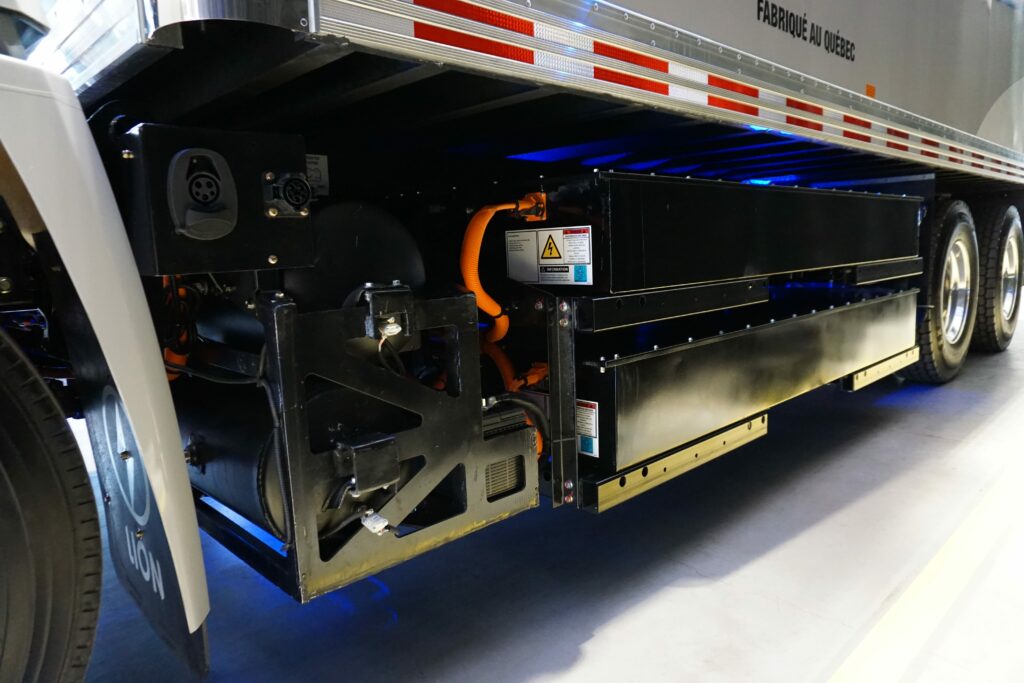
Proprietary protocols and cybersecurity are included to prevent remote hacking of the system, with several additional layers of protection via the CAN bus onboard comms, and coaxial double-shielded cables that are continuously monitored. “They’re monitored at all times, so if any current passes between the coax shielding and the actual wire, that branch of the powertrain is shut down for safety’s sake,” Desjardins says.
The truck’s charging architecture is also designed to match the operational requests of each customer. For some, one charging input is enough; others have asked for two onboard chargers, and that stems partially from the quantity of batteries on board and the expected payload weights.
With ‘Level 2’ J1772 charging, a full charge will typically take between five and 16 hours, compared with 1.5 to five hours for Level 3 CCS-Combo charging. Some users have notably requested DC-DC fast charging only, out of a desire to charge during the day, using short, intermittent breaks to maximise their operating time and mileage.
The exact location of the onboard charger and the fast-charger DC input will vary depending on the truck and its operations. For example, for an operator whose depot is designed for rear-parking trucks with their backs against a wall or loading bay, the charging ports will probably be placed further forwards. The ports are rarely placed at a forward or rear extremity as that could cause problems when using commercially available charging stations, with their limited cable lengths and parking spaces.
For extra endurance and range support, Lion Electric has integrated regenerative braking into its vehicles. Given that the truck stops regularly to pick up waste bins and recycling containers (as well as at traffic lights and for turning), it makes sense to use that regular source of inertia to feed energy back into the battery.
Notably the company does not factor energy regeneration into its calculations of battery range. As Desjardins explains, “Over the course of covering 1000 doors in a given municipality from a single full charge, a good driver might get a decent proportion of the battery energy back from regenerative braking. But like all regenerative braking systems, that can vary between drivers, and many powertrain developers fail to factor in losses from the battery to the traction motor or brakes.
“Having this system on our trucks is more efficient than braking conventionally and allowing that energy to be dissipated as heat into the braking calipers and the surrounding air; it also lowers operating costs. And by installing it on the Boivin truck, we can work towards developing and maturing it for future vehicles that experience higher braking resistance than the current garbage trucks.
“That would be extremely useful if we ever chose to develop construction or mining vehicles, or needed a garbage truck for covering much longer ranges as well as much greater elevations and descents than we’ve designed for so far.”
For its traction, the Lion8-Boivin truck incorporates a Sumo HD HV3500 motor-inverter system from Dana TM4. This electric axle solution was selected partly as a result of Lion Electric’s previous experience of working with systems in the same series, as well as its compatibility with the Class 8 design that Lion and Boivin were aiming for.
“We’ve used the Sumo MD model in our school buses for the past five years, and we’ve also tested the HD. So we decided to have a sufficiently mature motor, inverter and axle, with our batteries, thermal management and vehicle chassis being the new components we’d put into the market.”
With a 750 V DC input to the inverter, the TM4 permanent magnet motor provides up to 350 kW peak power (or 260 kW continuous). The system’s operating torque is given as 1970 Nm, which is achieved at about 1700 rpm. The vehicle’s previously mentioned torque limit of 3400 Nm comes in between 150 and 950 Nm.
Desjardins adds, “As users drive the electric truck, an electric pump supplies the air conditioning and power steering, so you can tune the pump to get the best power steering. On the highway between neighbour hoods you don’t steer that much, but in city driving you’re often changing lanes, going in and out of parking lots and covering every street back and forth. And there’s no shifting – it’s direct drive – so it’s easy to move forwards or reverse.”
The cabin has been designed using CFD and CAD software to make it as aerodynamic as possible, to help with the truck’s energy efficiency as it moves. That will become more important as energy storage improves and users look to take the vehicle onto highways at higher speeds.

Being largely automated, the side loader can be operated by the truck’s driver as they park next to a bin; the electromechanical arms lift it without manual input (although a joystick is available for driver-assisted guidance when needed). For a collection route focused on rear-loading waste, however, the truck will have two helpers at the back.
Without an engine or radiator up front, the cabin is also designed to have a wide view ahead, enabling the driver to move freely throughout the cabin when the truck has stopped (particularly at corners or traffic lights). With a 180° view, the design also helps the driver to see any cyclists or pedestrians that they would have to be aware of.
Within the driver’s peripheral vision is an information display that gives critical battery and powertrain health information, as well as a real-time camera feed of the garbage chute and compactor.
“We also installed a J1939-type CAN bus on board from the cab, so Boivin operates through that to connect their refuse collection equipment to our chassis,” Desjardins says. “Using that interface means we don’t have to route any additional data wires. And if anyone wants to add more cameras, sensors or arms, they will go through the same CAN bus.”
After operation
After returning to its depot, the truck must be checked for any signs of damage or wear to the powertrain that were flagged up during operations, as is typical of standard checking routines.
Lion Electric has also installed functionality into its onboard chargers to manage charging at specific times of the day. That is aimed particularly at users running upwards of 10-15 trucks and who are concerned about their operating costs and the demands on the power grid.
It enables operators to program the onboard charger to charge during the night and early morning, rather than the afternoon or evening, to avoid peak energy usage hours and their attendant costs.
“There are places in the States where the cost of power usage will drop by 50% after midnight. So customers might want to configure their charging systems to start recharging the trucks at one minute past midnight, or specifically configure the most energy depleted trucks to not start recharging until after that,” Desjardins notes.
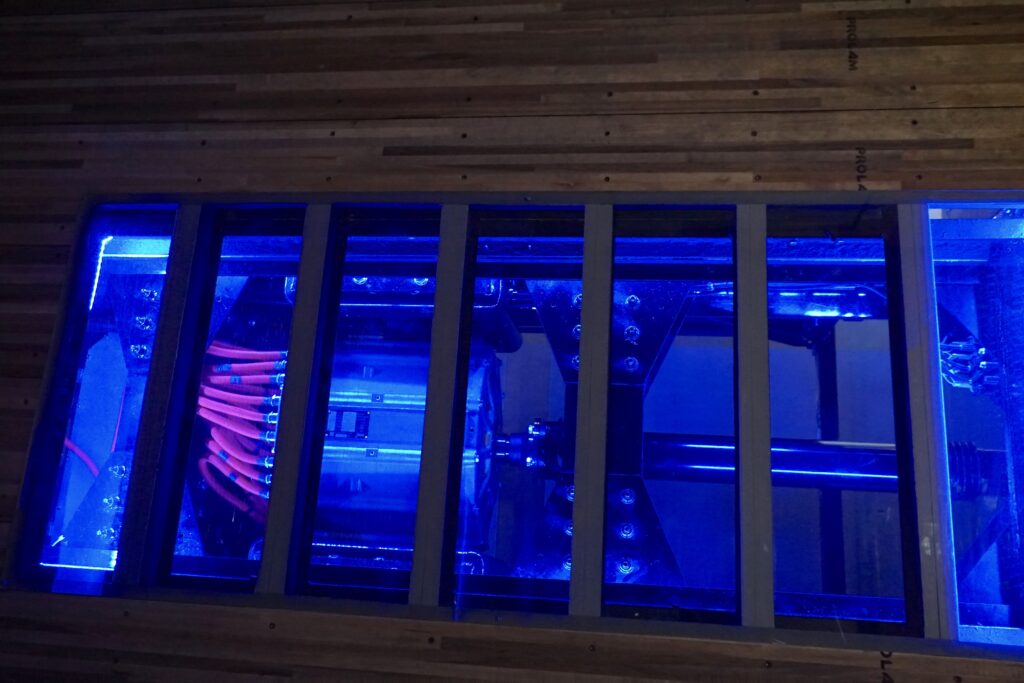
Conclusion
With a design that enables broad operational, social and environmental improvements over conventional fuelpowered refuse collection vehicles, the partnership between Boivin Evolution and Lion Electric looks poised to transform recycling and sanitation across North America.
Some key suppliers
Chassis: in-house
Loader/collector payload: Boivin Evolution
Traction motor: Dana TM4
Traction inverter: Dana TM4
Battery pack: in-house
Suspension: Hendrickson
Brakes: Bendix
Specifications
Type of vehicle: battery-electric waste collection truck
Battery type: NMC
Gross weight: 24,766 kg
Maximum speed: 105 kph
Maximum range: 400 km
Maximum energy storage: 480 kWh
Maximum power output: 350 kW
ONLINE PARTNERS
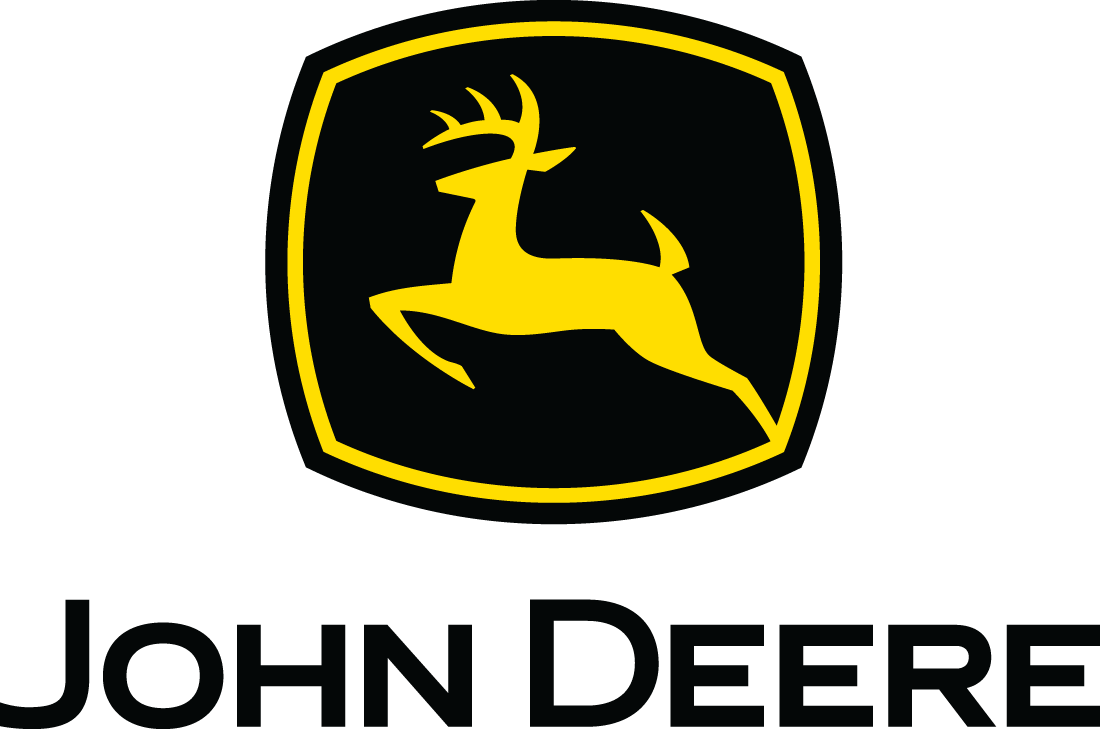
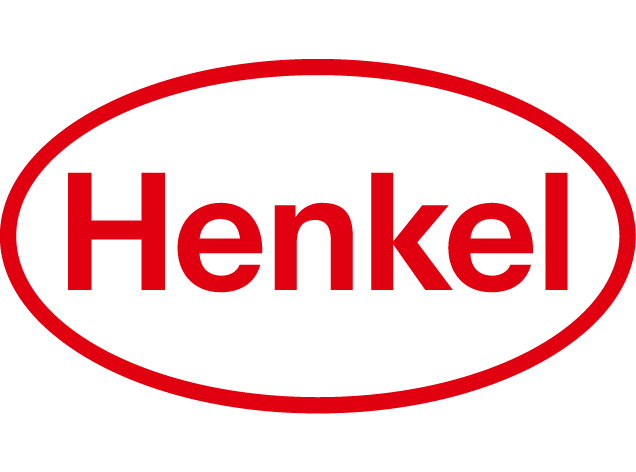
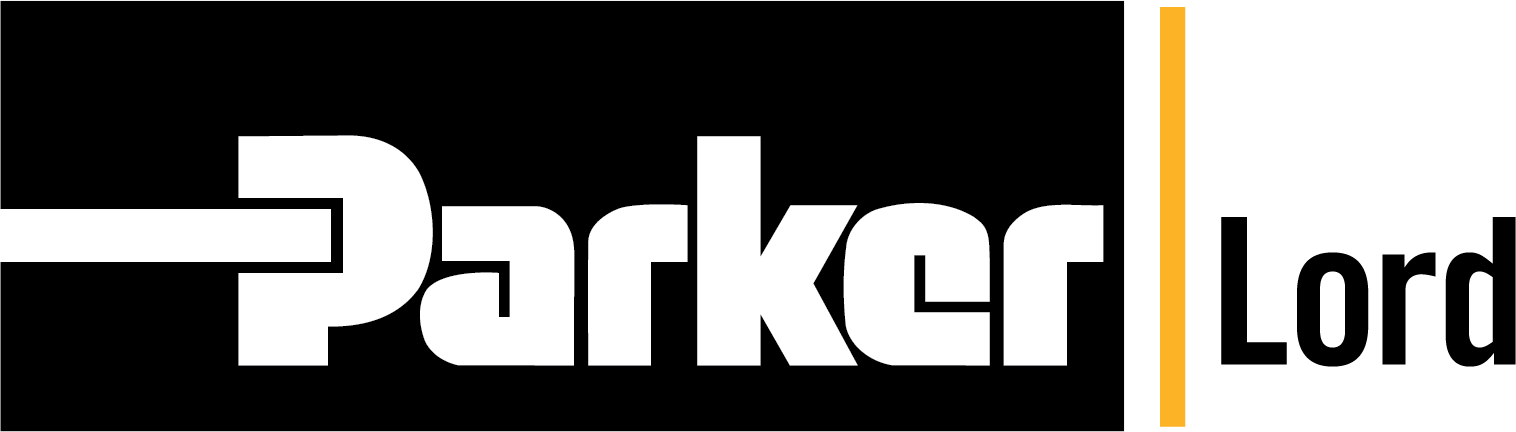
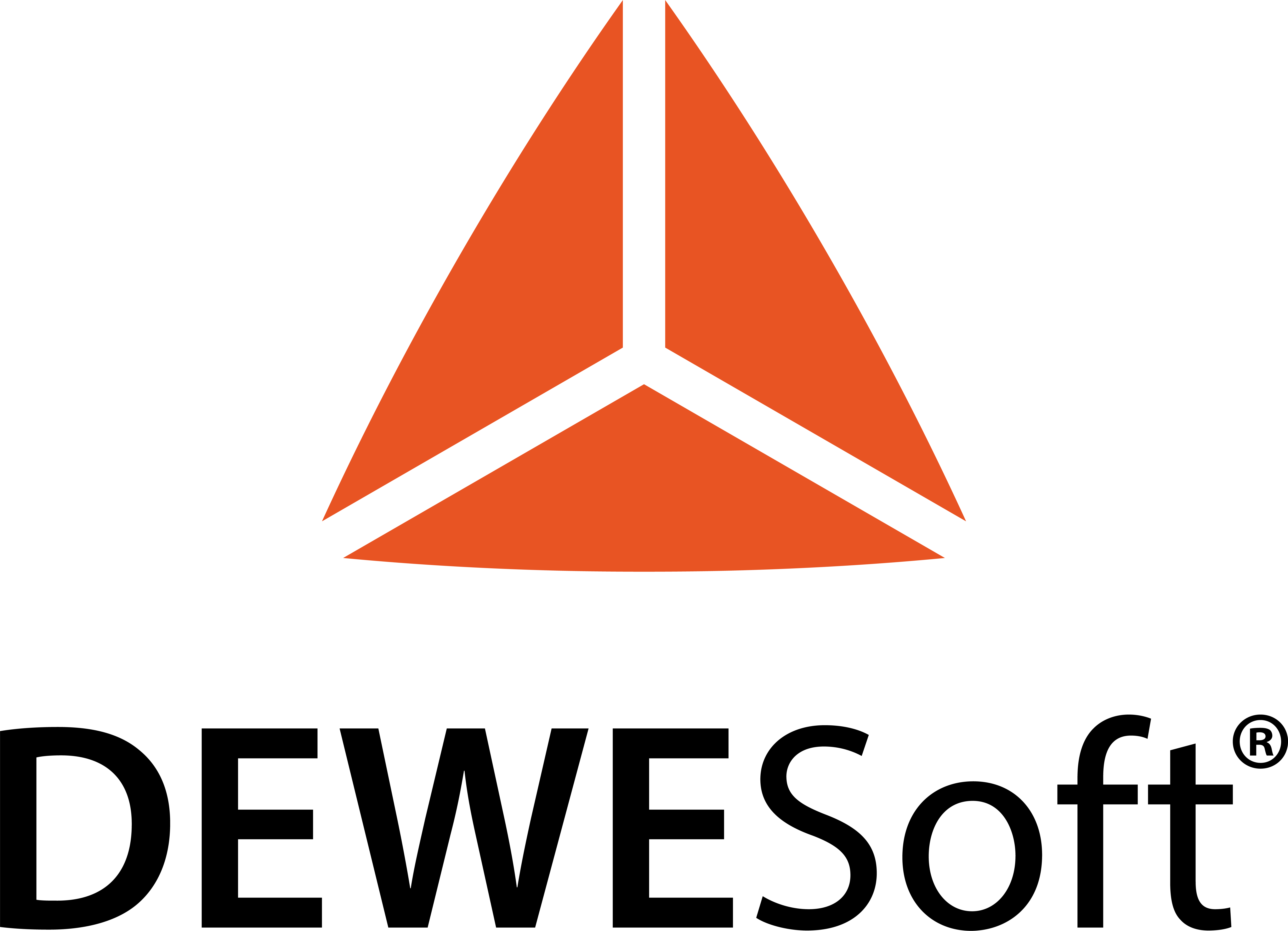
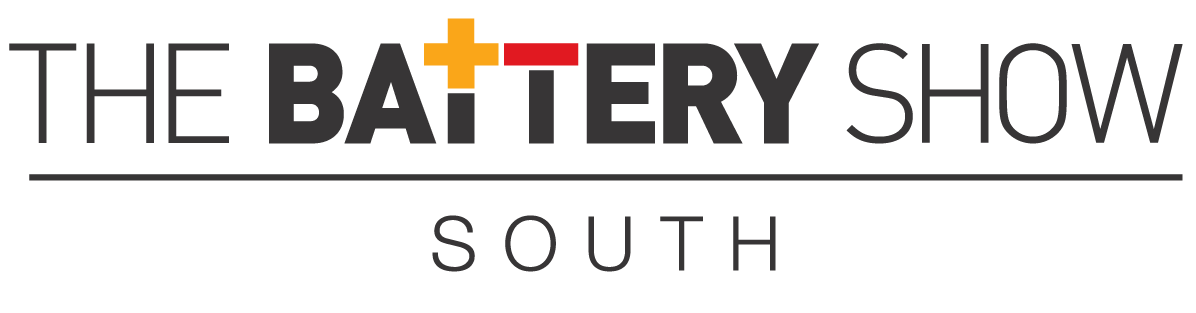
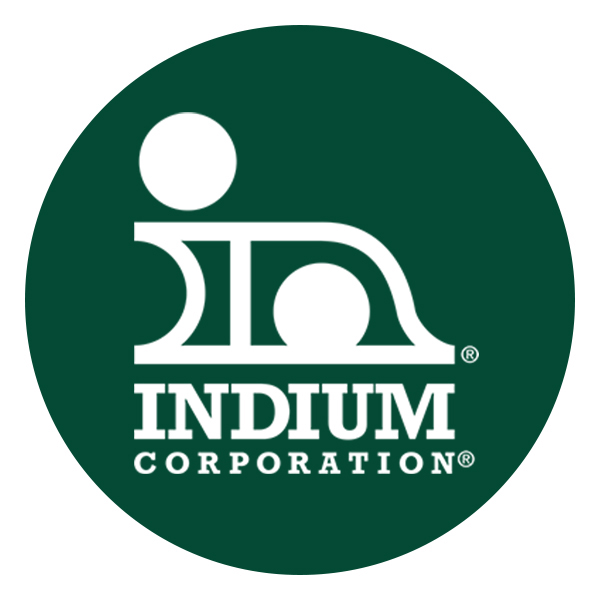

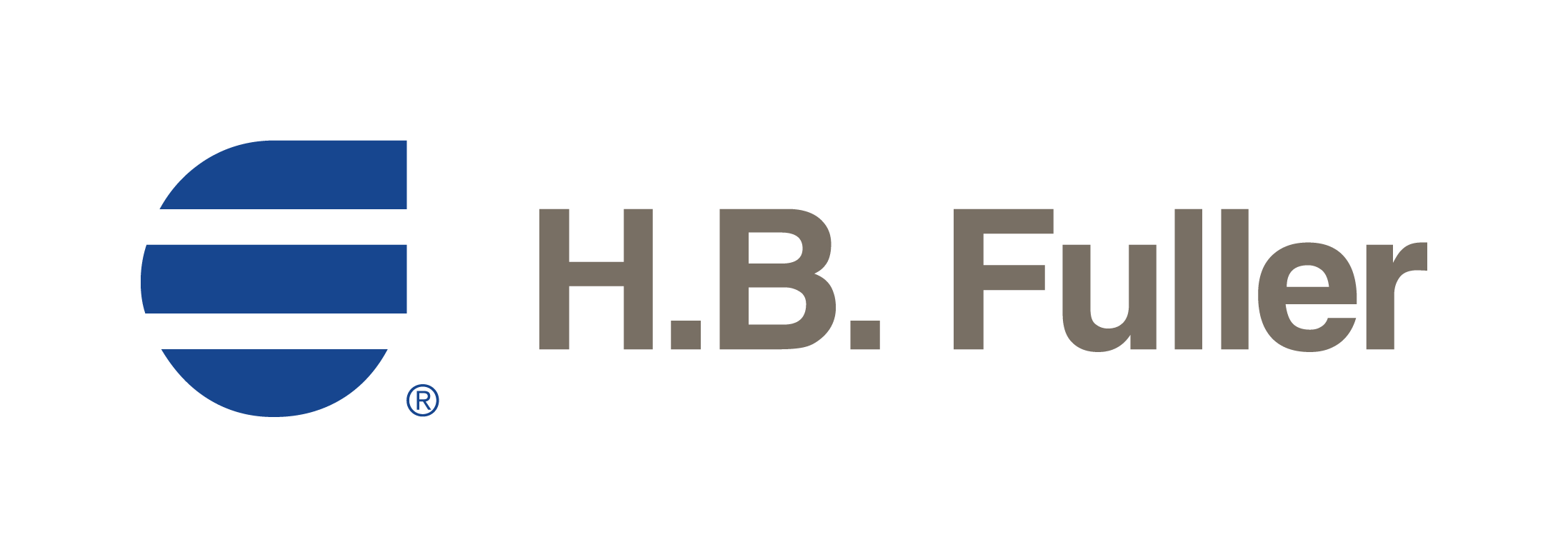
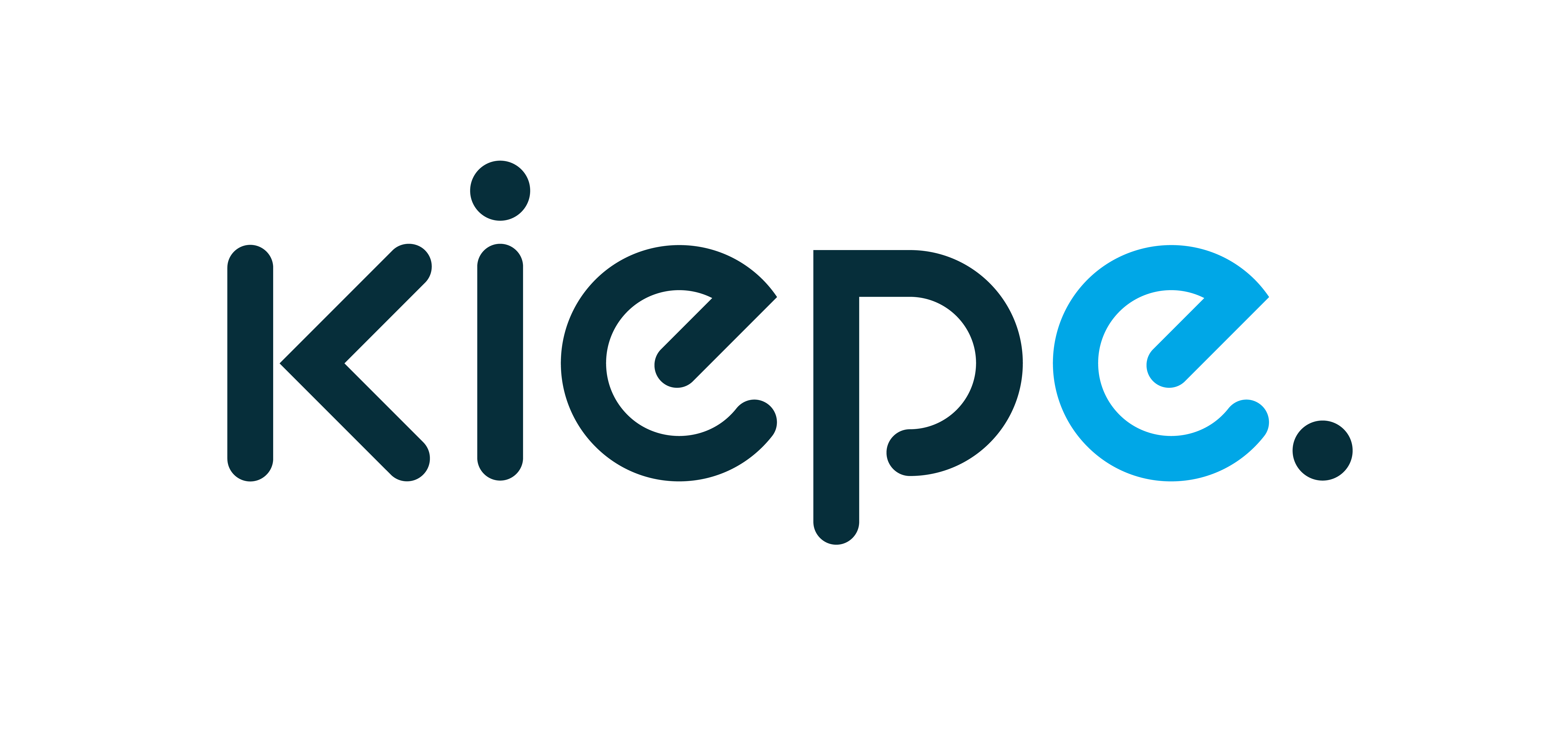
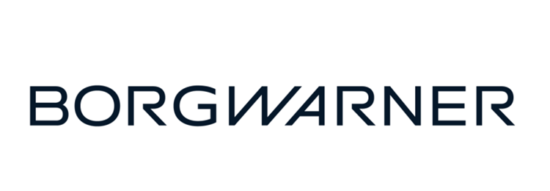