Lightweight materials
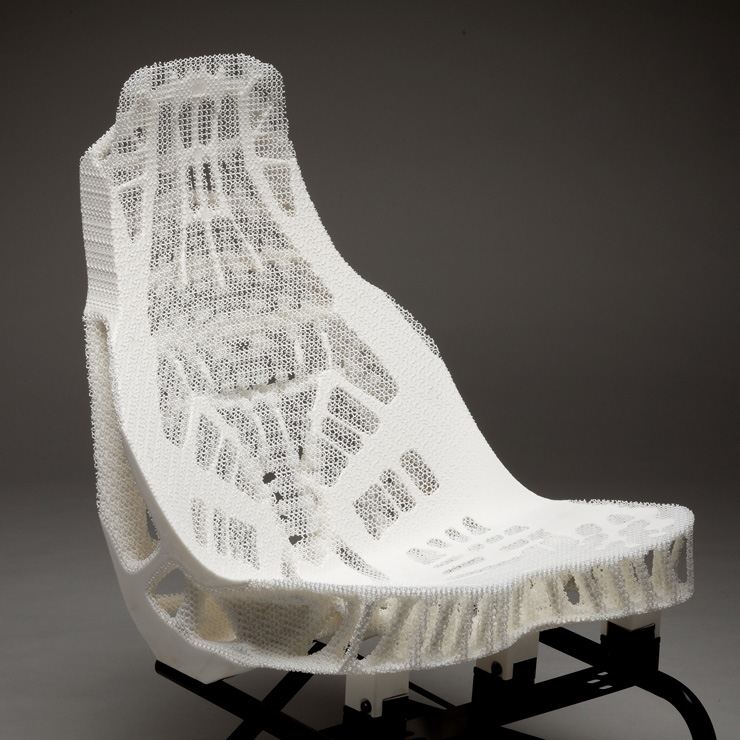
(Courtesy of Materialise and Toyota Central R&D Labs)
Take a load off
Dan Fleetcroft explains how selecting the right materials can minimise an EV’s weight to maximise its endurance.
Consumer interest, combined with the world’s growing concern about the environment, is accelerating the development of electric and hybrid vehicles, driving electrification into multiple industries. Government targets on emissions are having an impact on the entire transport sector, and not just the passenger automotive market, although that would appear to have the greatest momentum right now.
The UK’s industrial strategy is technology-neutral, and whether part of the solution to meet the zero-emissions target is plug-in hybrid EVs, battery EVs or hydrogen fuel cell vehicles, their success will rely on two major factors – practicality and affordability.
Practicality can be considered in terms of the infrastructure in place to ‘refuel’ and the vehicle’s performance with respect to range, or more simply, the frequency between time to ‘refuel’ or ‘recharge’. For this article the focus will be on maximising endurance and extending range by design and materials selection to minimise a vehicle’s weight.
Lightweighting has been a major design driver across all transport sectors, from supercars to commercial airliners, with the levels achieved generally being constrained by economics. It has grown in importance owing to rising fuel prices, emissions targets and taxes combined with the increasing complexity of vehicle design and specification.
Safety standards, electronics and equipment levels have all added to vehicle weight, so designers and engineers have had to look to new materials and manufacturing methods to counter those.
The move to vehicle electrification has compounded this weight gain, with the integration of heavy batteries, fuel cells with high-pressure tanks, electric drive motors and control systems, even though other components such as gearboxes have been removed.
With the success of this technology relying on EVs offering at least a comparable alternative to the internal combustion engine in terms of performance, and in particular range, lightweighting has become critical.
This appears to have had the effect of further accelerating r&d into materials and manufacturing technologies. Composite materials, for example, have long been used in low-volume, high-performance markets such as motorsport and defence, where budgets can withstand the high costs.
In fact, it is thanks to sectors like these that a large proportion of the development has taken place. However, more recently these materials and associated processes have found their way into the structural elements of higher volume vehicles, including commercial airliners and passenger vehicles.
That is partly a result of the development of more automated manufacturing processes that have faster processing times, and a decrease in raw material costs as demand has driven up the suppliers’ production volumes. New materials, including resin systems, have also contributed to shorter production times and better mechanical and thermal performance.
As these new technologies have matured and materials have evolved, overall production costs have dropped, enabling more industries to adopt them for their higher volume products. The weight savings these materials can deliver are certainly desirable to EV manufacturers.
This positive outcome is somewhat ‘chicken or the egg’. Have new materials and manufacturing technologies been adopted to save weight, increasing their maturity and accessibility, or has industry embraced them as they have become more financially viable?
The answer most probably depends on the transport sector. Either way, they are a key element of the EV’s evolution, and are vital for making this clean technology affordable and practical.
Taking weight out of EVs seems to be pushing manufacturing technology and material development harder than ever, and ultimately we should not be surprised by this.
Moving people, goods and services is a massive part of any economy, and with governments steering vehicle design towards an electric future the industry must adapt in order to deliver their products within the legislation while continuing to meet consumer demands and budgets.
The interesting thing about embracing a lightweighting design philosophy is that it delivers multiple performance benefits, not solely extended range. Lighter vehicles accelerate and stop faster, they are dynamically more responsive and controllable, they offer increased payload capacity and can deliver extended service intervals owing to the reduced loads on components.
To get the most out of any material you need to understand its physical properties and how to form it into the desired geometry.
This is often referred to as Design for Manufacture (DFM), and it can initially pose a barrier to the adoption of a new material as, being new, there is often a lack of information, experience, understanding and – significantly – confidence.
DFM will ultimately result in products that meet the quality requirements at a commercially viable cost. Which manufacturing methodology is selected will depend on the material and production volume required.
This challenge is certainly not unique to composites or additively manufactured materials, and embracing a new material can involve major investment in equipment and development to optimise the design and manufacturing process.
Sometimes not being a pioneer can reduce risk, but in competitive markets the early adopters can secure market share by offering innovative products with performance that their competitors cannot match and will have to develop themselves if they are to catch up. That certainly seems to be the case with the transport sector, particularly the passenger car market, where product and brand competition is fierce.
Composite materials
We will start by exploring the use of composites in EVs. A composite material has at least two elements that work together to produce material properties that are different from the properties of those elements on their own.
Most consist of a matrix with a reinforcement, usually in the form of fibres or particulates. For the lightweighting of vehicles, most composites used are fibre-reinforced polymer matrices. They can be continuous or discontinuous, and are predominately carbon or glass, with the highest performance being delivered by continuous carbon fibre reinforced polymer (CFRP) composites.
It is the superior specific strength and stiffness of CFRPs to that of metals (see table below), and their formability, that makes them the primary replacement for the highly loaded and aerodynamically/hydrodynamically optimised metallic components and structures commonly found in vehicles, whether they operate on land, water or in the air.
Although carbon fibres themselves have very high temperature resistance – carbon sublimates at over 3000 C – it is the polymer matrix that limits the ultimate operating temperature of the composite and precludes its application in certain environments. The predominant matrices are thermosetting polymers, examples being epoxies and polyesters, with epoxies offering the higher performance.
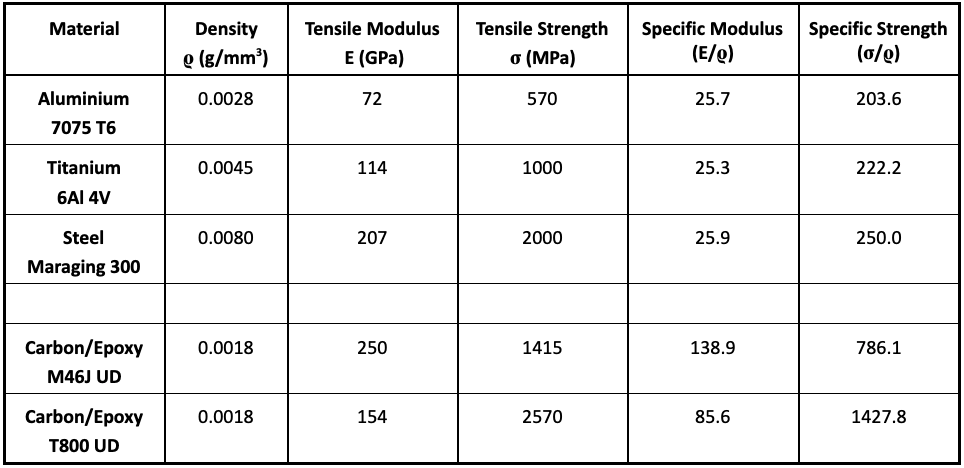
(Courtesy of Performance Engineered Solutions)
Epoxy systems can exhibit glass transition temperatures (Tg) of around 180 C, above which the matrix softens, taking on a rubber-like state, greatly reducing the load-carrying capability of the composite. There are alternative polymers, including bismaleimide (BMI) and cyanate ester, which can achieve a Tg of up to 380 C; however these are expensive and more challenging to work with.
Alternatively, there are thermoplastic matrices consisting of polymers such as PEEK (polyetheretherketone), polycarbonate and PEI (polyetherimide) with PEI offering a Tg of about 215 C.
These offer exciting opportunities for high-volume production and have already been adopted by the aerospace industry, but they are not as widespread as the thermosetting resins, and the associated lack of experience is slowing their uptake in other transport sectors.
Fibre and resin manufacturers have a mixture of views regarding the state of investment in new materials and the manufacturing processes required to make them commercially viable, but they do agree about the technologies required to achieve that. The current thinking to enable the high-volume production required in many transport applications is a move from thermosetting to thermoplastic composites using automated manufacturing processes.
The challenge is that there is currently much more experience and confidence in the use of thermosetting resins, making the transition expensive in terms of equipment investment and development time.
Ironically, one large automotive manufacturer is reported to have reduced its budget for lightweighting from €30 million to €200,000, with the funds being redirected into its electrification programme, at a time when it might be suggested that these activities should be converging.
As regards the EV market, innovative materials and technologies are available and evolving for both thermoset and thermocomposites, with some crossover between the two. Thermoset materials have long been laminated using wet layup or pre-impregnated systems that are then cured in an oven or autoclave in a long and labourintensive process. Developments in resin transfer moulding (RTM) and snap-cure resins systems are helping to speed up production, but there are other benefits in refining the approach further.
Composites are proven to deliver significant weight savings over the traditional metal alloys used by transport industries; the challenge though is producing them at a cost that’s acceptable to the high-volume requirements that mass transport EVs will demand.
A move to heavier composite fabrics and biased weaves will accelerate material deposition rates, however, reducing laminating times, and avoiding the specification of highstrength or high-modulus fibres will reduce material costs.
These approaches must be incorporated at the design stage though, as the component geometry will need to be engineered to allow for the reduced drapeability (a measure of how easily a composite fabric will conform to the shape of the tooling) of the thicker fabrics and compensate for the distribution of fibres and their lower mechanical properties. Ultimately, benefiting from these developments means understanding the material’s properties and manufacturing process.
Co-curing and over-moulding can also reduce part cost and weight. RTM and press-forming allows metallic and polymer inserts, and honeycomb and foam cores, to be encapsulated into the composite positioning-specific materials in certain locations and decreasing the laminate material’s volume and weight. The inserts could be for fixing locations or bearing positions, and would remove the need for cold-bonding assembly operations and their associated costs and quality control considerations.
Thermoplastic composites have a different process when it comes to high-volume production, as they are press-formed at temperature and do not rely on the curing chemistry of thermosetting polymers. This greatly reduces the forming cycle time, and is where the production cost savings at volume are realised.
For manufacturing, the thermoplastic composite is loaded into the tooling as a preform that can be cut from a sheet if it’s of constant thickness or produced by automated tape-laying and fibre-placement machines if more complex.
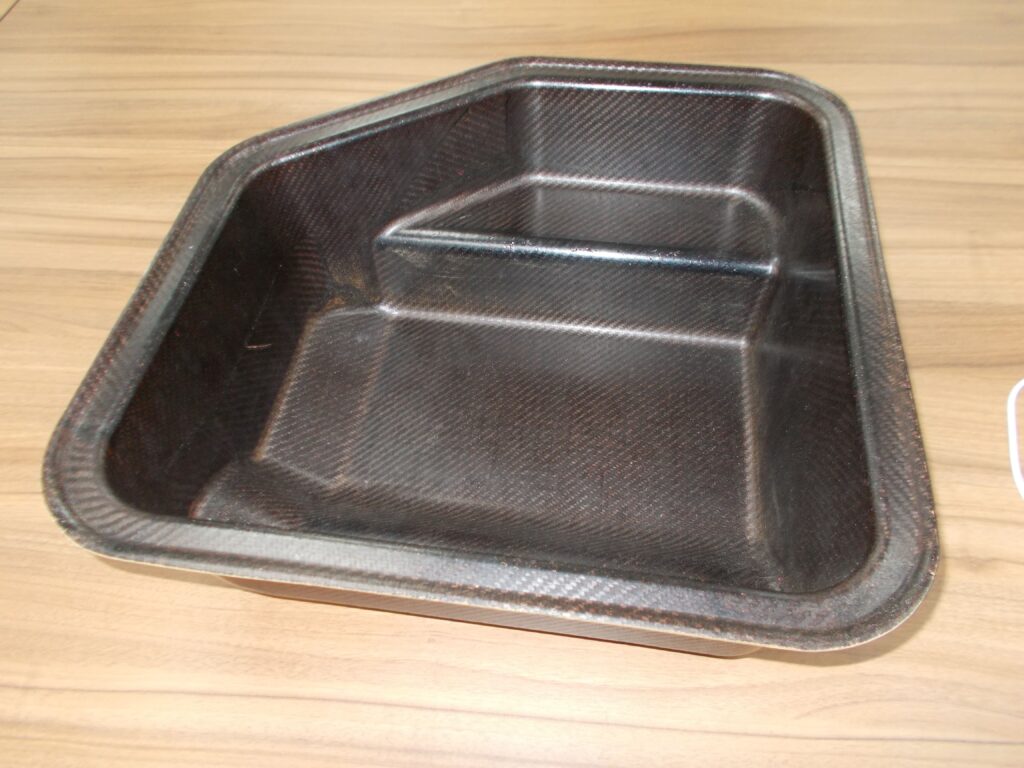
(Courtesy of SHD Composite Materials)
This removes most of the manual labour and skill required for thermoset composite manufacture, with the opportunity for automated production. Not only does this reduce part cost, it enables a highly repeatable and controllable process which ultimately will ensure quality – a key requirement in all transport industries.
One growing challenge with composites is that of their recyclability, particularly when considering the environmental concerns driving EV development. Thermoplastics offer end-of-life options though, and there are also processes for reclaiming the fibres from thermoset composites. However, there are questions over the reclaimed fibres’ properties, and from an economics standpoint the polymer matrices are generally more expensive than the fibres to produce.
The development of bio-composites might provide part of the answer to this and simultaneously address some of the energy concerns of producing the reinforcing fibres in carbon or glass. For areas of vehicles with lower structural requirements, glass fibre reinforcements are often used as a less expensive alternative to carbon, although the savings come at the expense of increased weight.
To avoid this compromise, bio-fibres made from flax have been used, as they offer similar mechanical performance to the glass they are replacing – and, thanks to a lower density than carbon, they offset the weight penalty. Flax is also less prone to brittle failure than carbon and glass, so its addition creates a more damage-tolerant composite.
Although the flax delivers a more sustainable solution, when used with a standard petrochemical-based resin system like epoxy there is still the recycling challenge of how to separate the polymer matrix. The recent development of bio-based resin systems using waste from the sugar cane industry, however, provides fully bioderived composites.
One example of this is PS200 which, with flax fibre reinforcement, has found an application in battery casings for protecting lithium-ion cells in EVs thanks to its non-combustibility, 300 C service temperature and damage resistance.
This is a broad overview of the many composite materials that can (and do) deliver significant weight savings for EVs. The challenge for the transport industry is understanding their properties and manufacturing processes to inform their designs and ensure they can be manufactured in the quantities required at a viable cost and quality.
Graphene
Much like carbon fibre, one of its more established relatives in the carbon family, graphene, is the latest wonder material to excite the scientific, engineering and manufacturing worlds, and a review of its physical properties, shows why.
Isolated and characterised in 2004 by Andre Geim and Konstantin Novoselov at the University of Manchester, it is a 2D material made of a single layer of carbon atoms arranged in a hexagonal lattice.
It is the strongest material ever measured, with an intrinsic strength of 130 Gigapascals, although it is worth noting that this value was achieved by testing a single crystal monolayer one atom thick, and a lot of development will be needed before graphene in this form is available in volumes usable outside the laboratory.
Its theoretical density is 2.26 g/cm3 or so, compared to around 8 g/cm3 for steels. It also has a Young’s Modulus of 1.0 Terapascals (for steel it is around 200 Megapascals, MPa); at around 5000 Wm-1 K-1 it is the world’s best conductor of heat, and it has the highest melting point of any known material, of 4000-6000 K, at which temperature it sublimates.
Graphene has captured the public’s imagination faster than any other material. It would seem it is being added to everything, from training shoes to paint and concrete, but in its current form it is not the ‘super’ single atomic layer sheet described above.
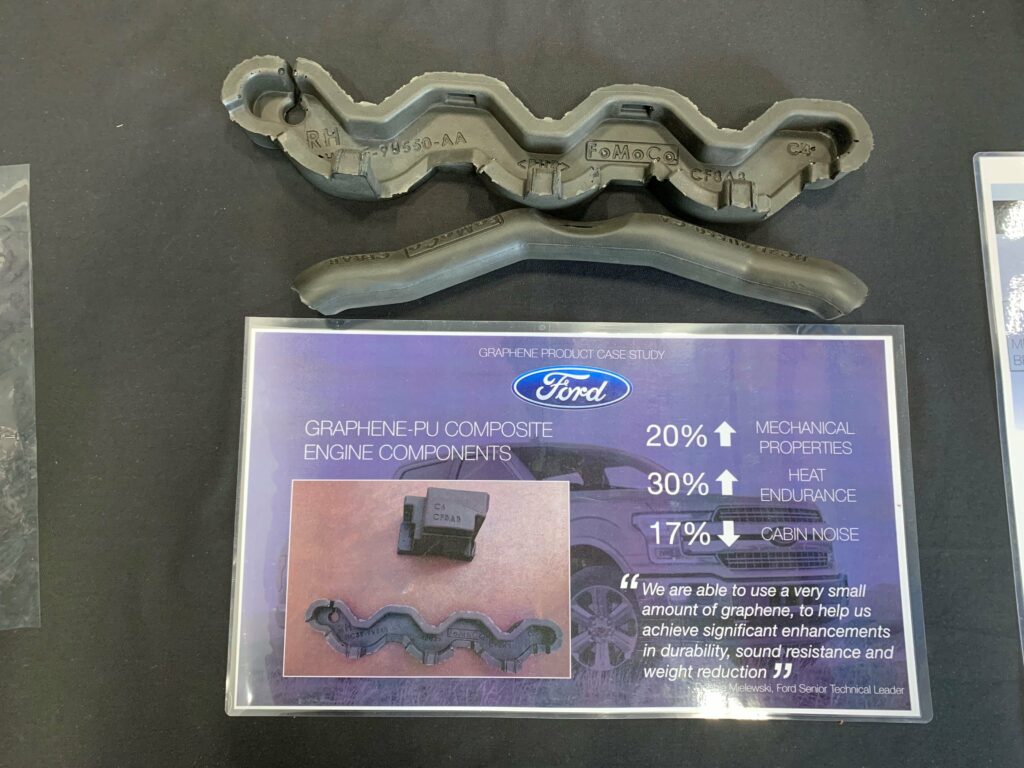
(Courtesy of Adrian Nixon, Nixene Journal)
That caused some challenges initially, as the market’s expectations were not realised when graphene turned out to be a ‘black powder’ and in some cases not even graphene at all. The 2D nature of this one-atom-thick material is partly where its amazing properties come from. Above about 10 atomic layers some of its characteristics revert to those of graphite.
However, if the flakes, known as graphene nanoplatelets, that form the graphene powder are produced to consist of only a few graphene layers then some of the 2D material’s properties are maintained, and this powder can deliver some amazing enhancements when added to a range of other materials.
Much like the challenges influencing the adoption of composites, this is a new and relatively untested material, so industry is cautious about it. Unlike composites, however, the cost to entry is relatively low for graphene in its current powder form. As the powder is being combined with other materials there are no real capital investments required by companies; they are simply ordering a different specification of raw material.
Some process development might be needed, as well as product testing and validation, but for most current applications there is no need for new production machines or tooling. In addition, the performance enhancements are generally achieved by adding low volumes of graphene, usually in the range of a few percent by weight, which means it is relatively inexpensive to explore whether graphene will enhance a product.
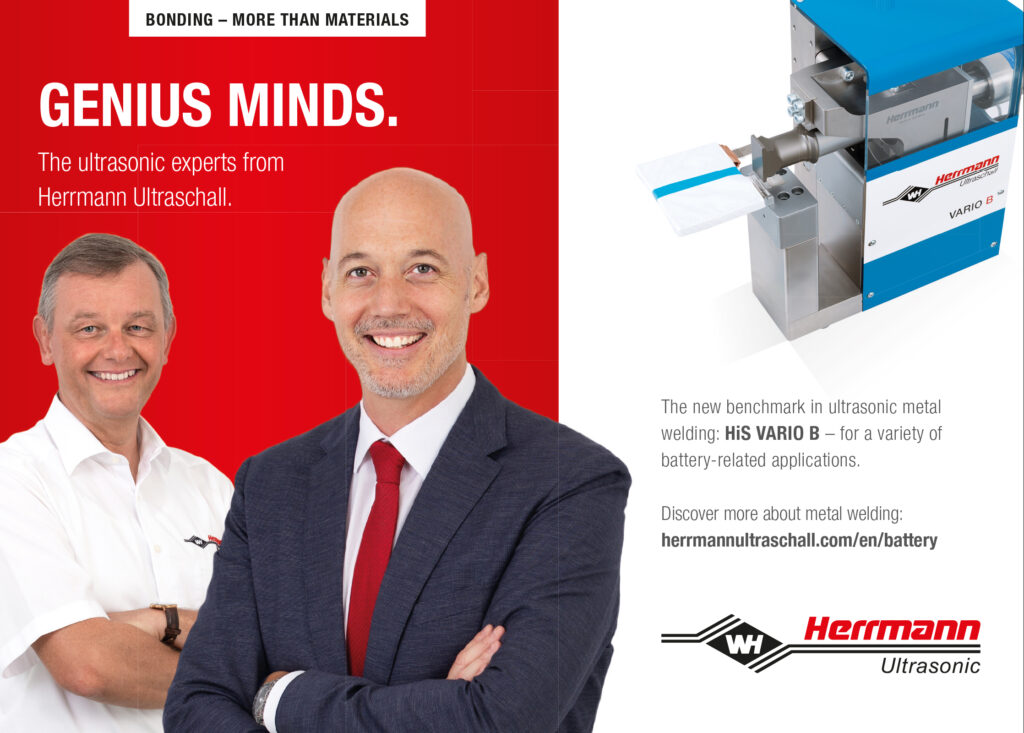
Graphene is being used in battery electrodes to reduce charging times, although it is not clear if there is any uplift in power density. It is also being used in ultracapacitors for the kinetic energy recovery systems in trams, helping to extend their range by reclaiming the energy otherwise lost when braking.
Many materials with graphene enhancement also have improved mechanical properties, resulting in less material having to be used to meet the structural requirements. Although not explicitly used in the EV market, there are various automotive examples that would benefit all EVs.
Graphene is being added to the epoxy resin matrix in carbon fibre composites. In one project this has improved the ultimate tensile strength (UTS) by 19%, the tensile modulus by 20% and the impact strength by 30%, which would enable a reduction in the thickness with an associated weight saving compared to the standard CFRP material.
That is not the only benefit, however, as the thinner laminate will need fewer plies (layers), cutting the cost of the raw material and the component layup time. Where composites are produced by manual layup using skilled laminators, the ability to remove material delivers cost and weight savings as well as increased rates of production.
In addition to this, graphene oxide nanoparticles have been painted between the layers of carbon fibre/ epoxy resin pre-impregnated material, producing a 100% improvement in the interlaminar fracture toughness in sample testing compared to the nontreated material.
This is important, as it helps increase the resistance to delamination, which is often the primary failure mechanism in composites, where the adhesion between the individual plies fails. This again could lead to thinner material and lighter weight.
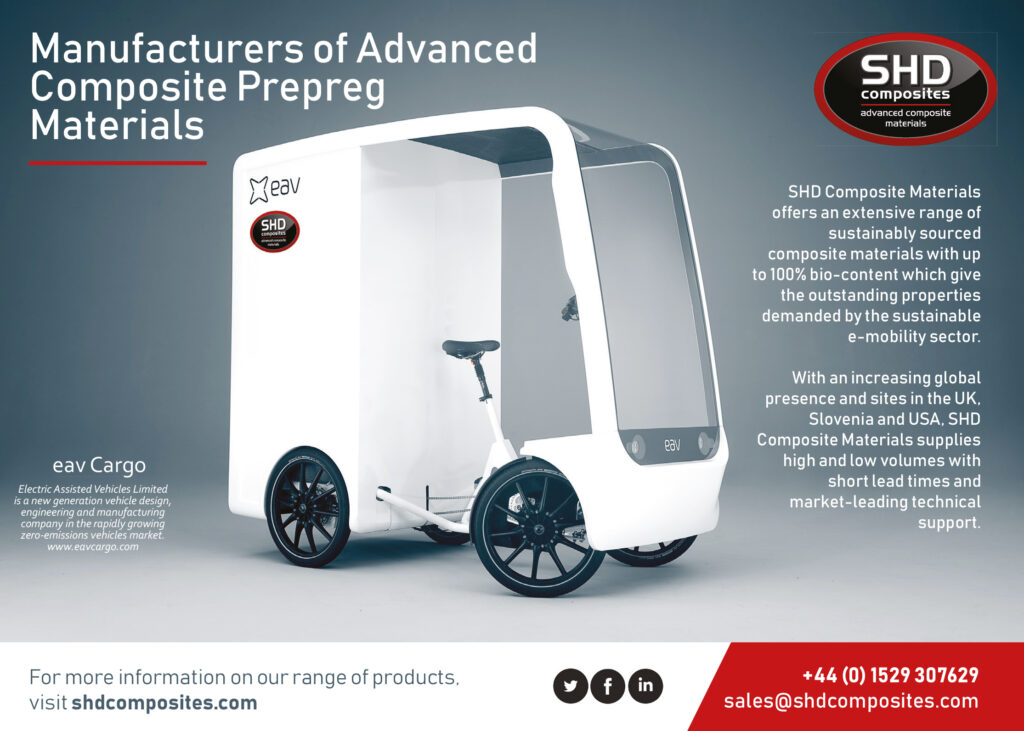
EVs could also benefit from new foams being developed using graphene nanoplatelets. Ford, in collaboration with Eagle Industries and XG Sciences, has developed a polyurethane foam which in tests has shown a 17% reduction in noise, a 20% increase in mechanical properties and a 30% improvement in heat endurance over the standard product with no additive.Generally, reducing the noise in vehicle cabins means adding more material, but new foams such as these could offer reduced noise levels as well as weight.
Graphene has been added to the rubber of tyres on high-mileage light commercial vehicles travelling on the UK’s roads. Testing has shown an average increase in wear resistance of 40% compared with the standard product, significantly extending the distance they can cover before having to be replaced.
This gives two options for vehicle manufacturers to offer – choose a longer-life product that reduces service intervals, or maintain the current endurance but with less weight by removing some of the rubber.
For EVs, lighter tyres means a reduction in unsprung mass and rotational inertia, both of which improve vehicle dynamics and performance. A lower unsprung mass improves wheel control and handling, and can allow other suspension components such as springs to be lighter.
That, in combination with the reduced inertia, means less energy is required to accelerate and slow the vehicle, again extending range.
Although fully electric vehicles do not have engines that need cooling, they do have batteries that do, which means using radiators, heat exchangers, pumps and cooling fluids. Cooling systems have not evolved significantly in the past 90 years or so: water or water-glycol solutions still offer the best heat capacity and thermal conductivity. However, a new fluid containing graphene nanoplatelets has been developed which is claimed to deliver a 39% improvement in the heat transfer rate over traditional systems.
These are being used to cool battery packs under load as well as heating them to speed up cold starts. This improved performance allows a smaller volume of cooling fluid to meet the cooling requirements, leading to another reduction in the overall vehicle weight.
Graphene is still a new material, albeit one that is evolving rapidly into new applications. The wide range of benefits on offer from adding graphene powder is delivering weight-saving opportunities across all transport sectors, and we are only just beginning to unlock and understand the potential of this material. When it can be produced on an industrial scale in its full 2D form – and we can learn how to work with it – the potential benefits could be limitless.
Additive manufacturing
Additive manufacturing (AM) offers another lightweighting tool for EV designers to explore and exploit. More commonly known as 3D printing, its other title of ‘rapid prototyping’ is falling out if use as it is now an industrial process for delivering functioning polymer and metallic components at production volumes across multiple sectors.
It works by building parts layer by layer, and the advances in the past decade or so have been phenomenal, with a rapidly increasing range of materials and processes. Unlike the real and perceived barriers to adopting composites, for example, the cost of accessing AM and the skill to operate it can be relatively low. Two generations of designer and engineers have grown up using this technology, generating the experience, confidence and the employees industry needs to successfully adopt AM.
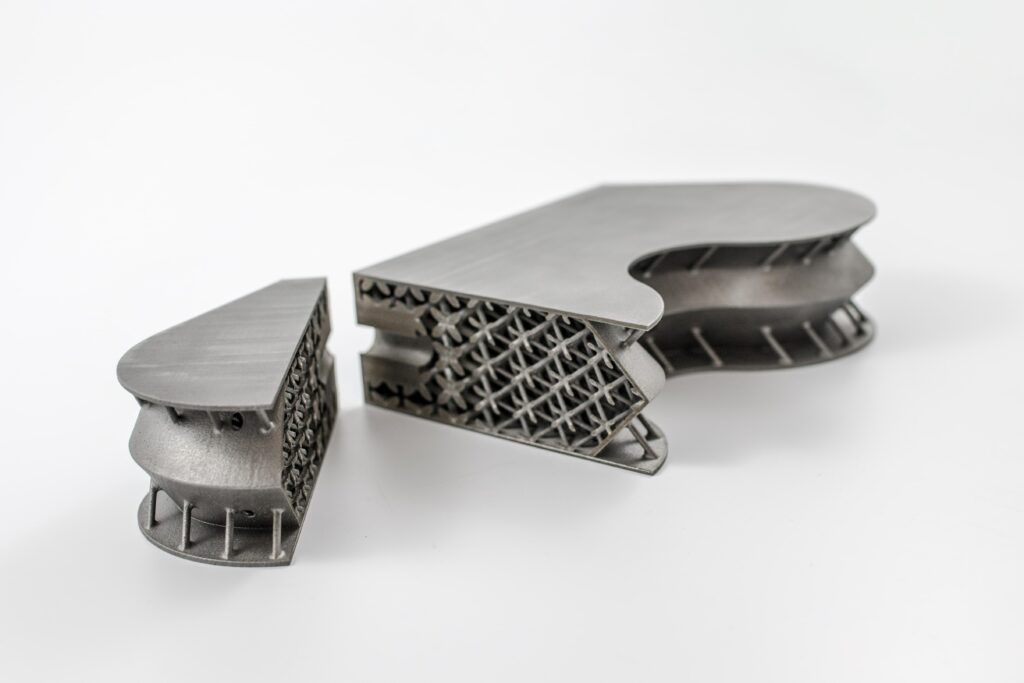
(Courtesy of Materialise and Atos)
To achieve the structural and dimensional quality necessary for production parts, however, requires significant knowledge and experience, and production machines are generally a major investment, especially for metallic parts. Although industry is still developing standards, there is a lot of momentum to embrace and integrate AM across multiple sectors.
New polymers and alloys are offering designers an ever-expanding selection of materials, broadening the environments and applications in which AM parts can be used.
Also, new processes and technologies are improving component build-layer resolution, dimensional accuracy and finish, along with the mechanical and thermal properties and increasing the speed and size of builds. According to AM businesses consulted in connection with this article, production volumes for components now run into the thousands.
One example of a new material that is benefiting the EV market is HT23, a polyetherketoneketone (PEKK) polymer with encapsulated carbon fibre reinforcement. This offers high strength, low density, high-temperature functionality, flame retardancy and UV resistance, meeting aerospace FAR 25.853 and mobility industry EN45545 standards.
Another example is the aluminium alloy A20X, now available in spherical powder form for powder bed AM. It was originally developed for casting, and gives a UTS of up to 477 MPa, just over half that of titanium 6Al 4V, to produce high-strength AM components that are free of micro-cracking and have increased temperature performance.
Both materials present opportunities for many applications, although their strength, low density and temperature capabilities are of particular benefit to the passenger air vehicle electric VTOL market, where innovative and integrated design is being used to minimise vehicle weight.
It is not just the materials that deliver lower component and vehicle weights – in fact, they are only part of the AM solution. The geometric freedom the technology unlocks enables (and demands) a different design philosophy from that used for more traditional subtractive or moulding processes.
While DFM is still of paramount importance in making parts of the required quality and cost, a different thinking is needed to maximise the potential benefits. Additively manufactured parts profit significantly from an integrated design approach, where geometry can be used for multiple functionality and lower part count.
For example, electric motor casings can be ‘built’ with integral cooling channels – hollow sections allowing cooling fluid to flow – while creating efficient structures to maximise stiffness for minimum weight. This is geometry that would be impossible, or at best commercially unviable, to produce using conventional manufacturing.
AM allows material to be positioned only where it is required, which can reduce the build time and cost as well as weight. Topological optimisation software can digitally iterate the geometry of a part to carry a specified load for a defined set of constraints. The resulting structure can often be organic in form, which again would not be practical to produce without the flexibility of AM.
This freedom promotes a design practice where thicker sections can be reduced to thin outer walls supported by an internal lattice or honeycomb structure, minimising material while maintaining stiffness. It also helps to control the part’s geometry by minimising any distortion in the build caused by the thick sections.
So, as with composites, if AM is to deliver on its potential for making EVs lighter, the industry first has to understand how to design for the technology and materials.
Conclusion
Regardless of the type of vehicle or its power source, lightweighting delivers performance, commercial and environmental benefits.
Although the materials and technologies exist to reduce EV weight, and new ones are in development, the current barrier to using them is their cost of implementation or developing them to meet the quality, part price and volumes required for mass production.
Composites, graphene and AM are relatively new materials and technologies, which means there is limited standardisation and qualification, and that creates a reluctance to explore them.
The supply chain needs to educate manufacturers about their materials and processes so that industry has the knowledge and confidence to optimise their component and tooling designs for performance and manufacture while minimising raw material usage and maximising manufacturing quality and efficiency.
In return, manufacturers need to share their requirements and forecasts with the supply chain to enable them to tailor their products, and ensure they have the capability to support industry’s needs.
Interestingly, there is a growing trend of joint ventures between product developers and suppliers in the EV market, as the realisation that these technologies are here now hits home.
Acknowledgements
The author would like to thank John Darlington of Toray Advanced Composites, Adrian Nixon of Nixene Publishing, Nick Smith of SHD Composite Materials and Fatos Derguti of 3T Additive Manufacturing for their help with researching this article.
ONLINE PARTNERS
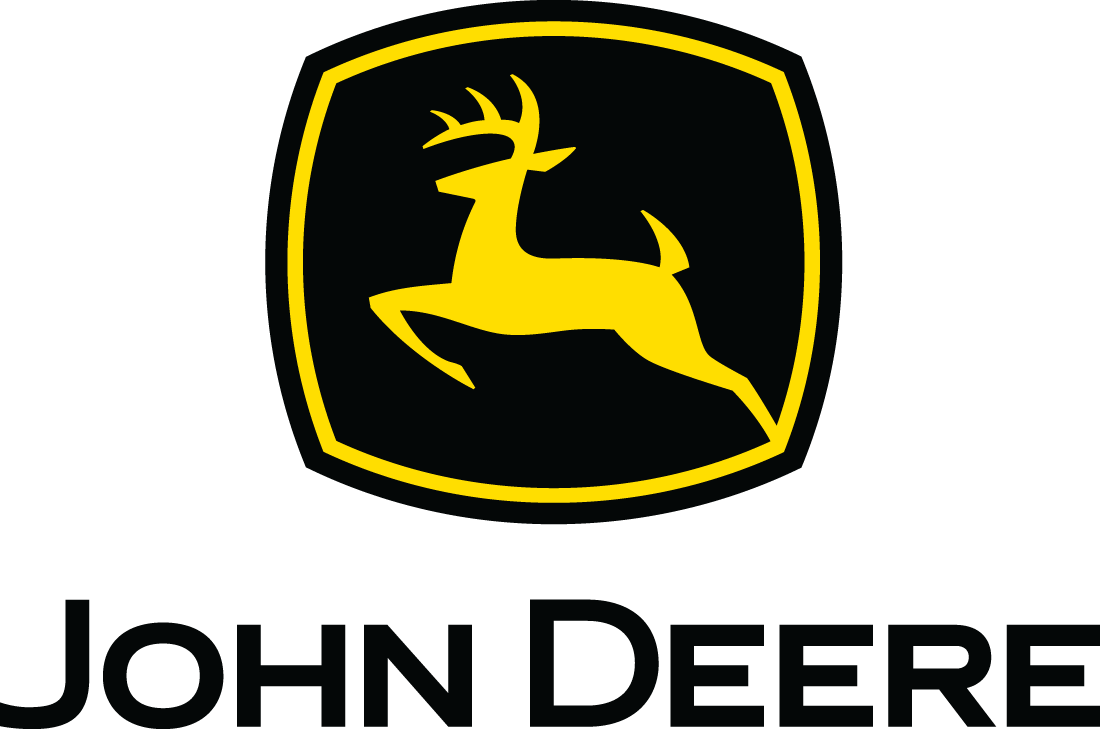
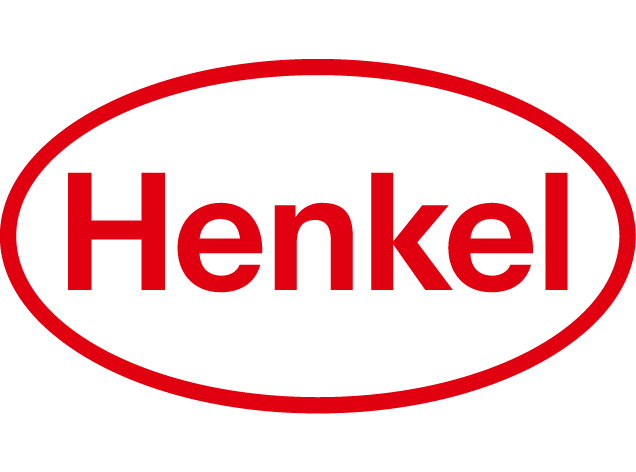
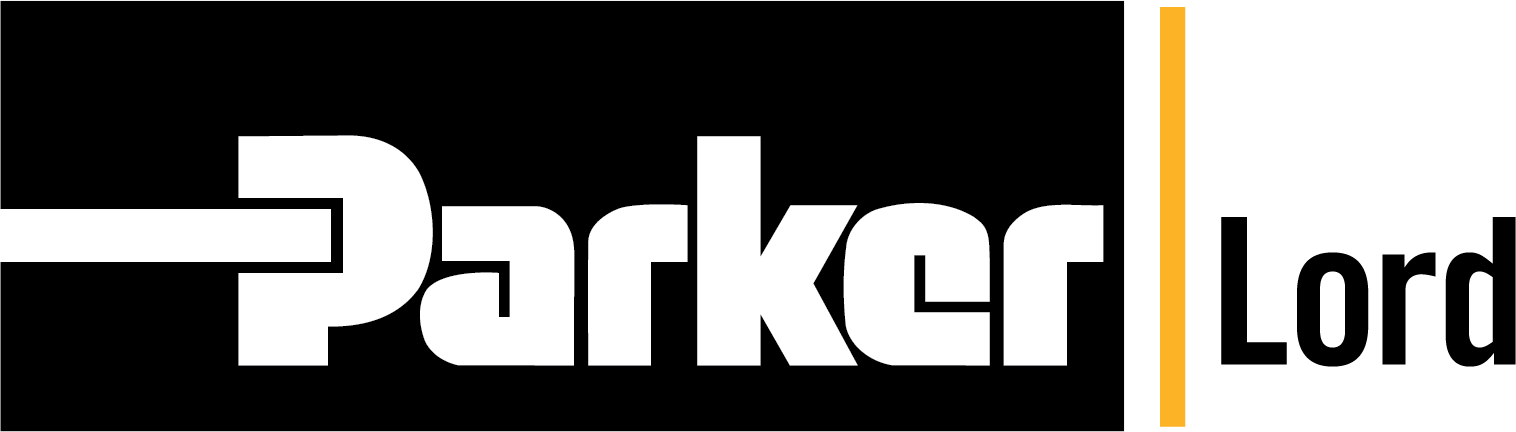
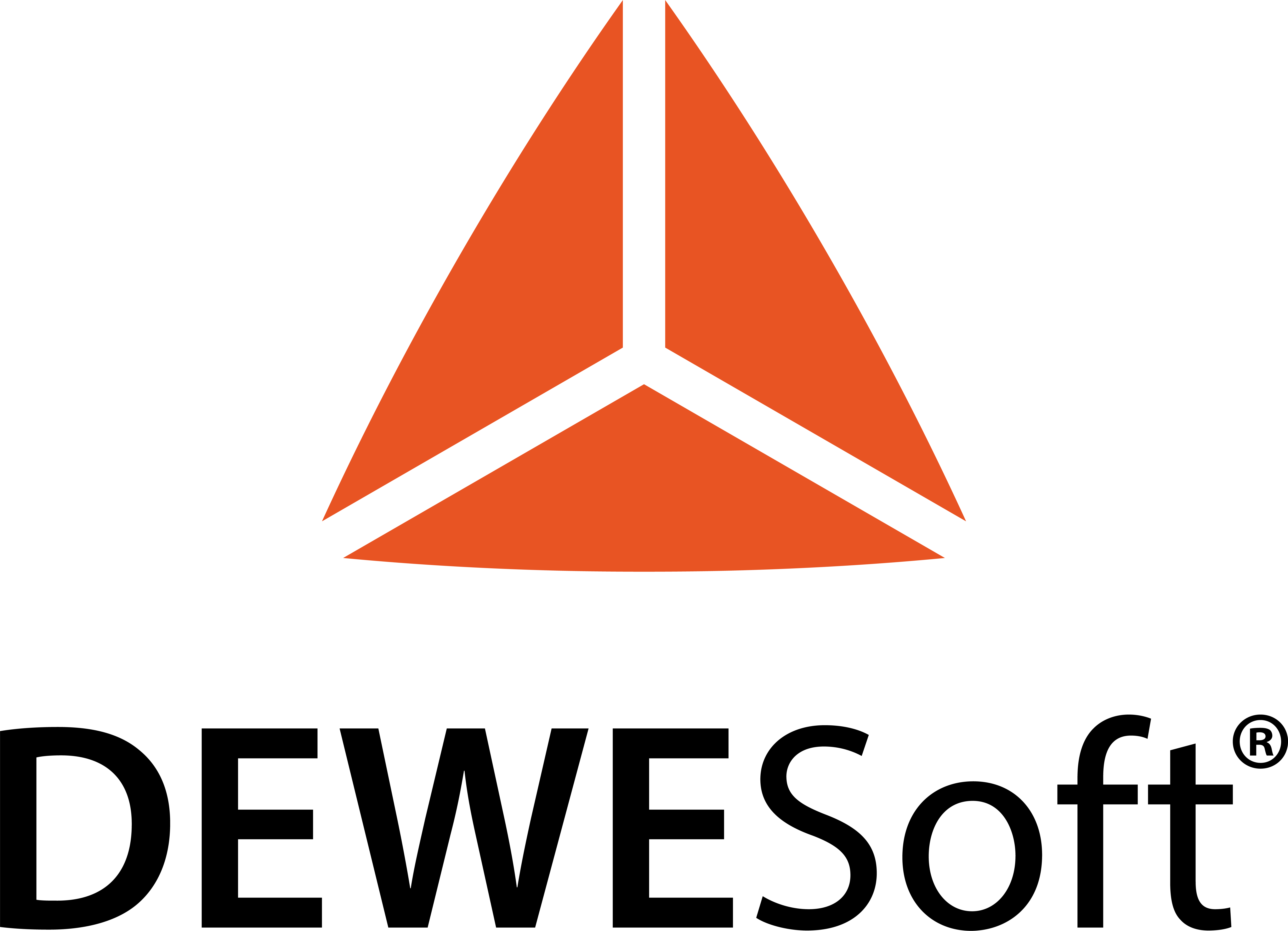
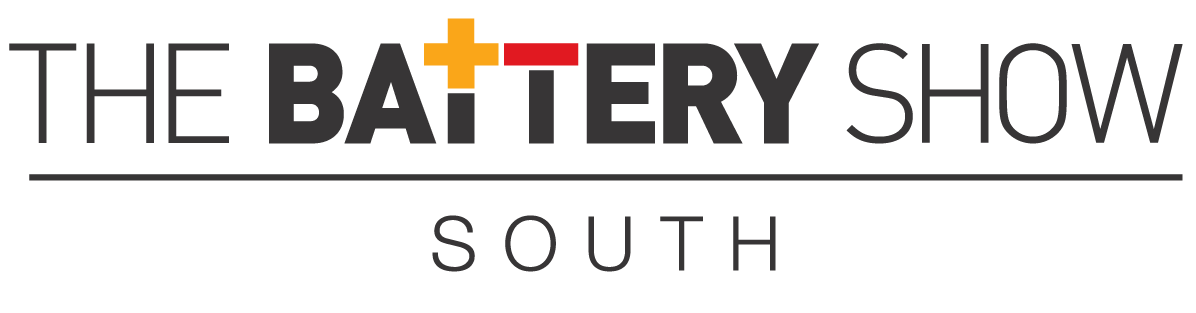
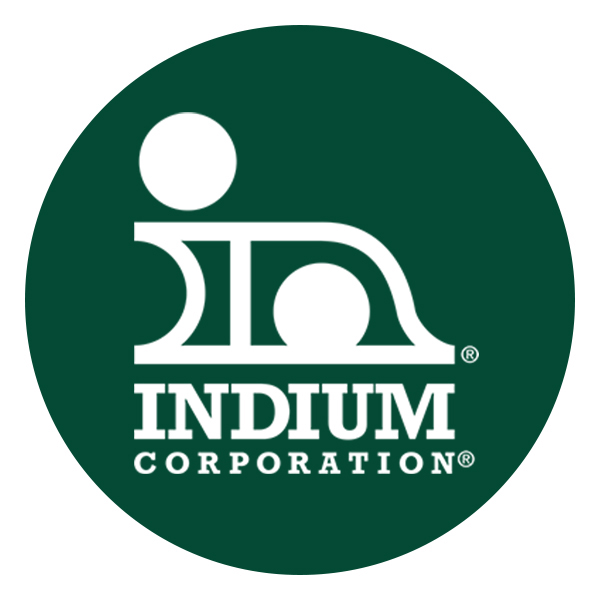

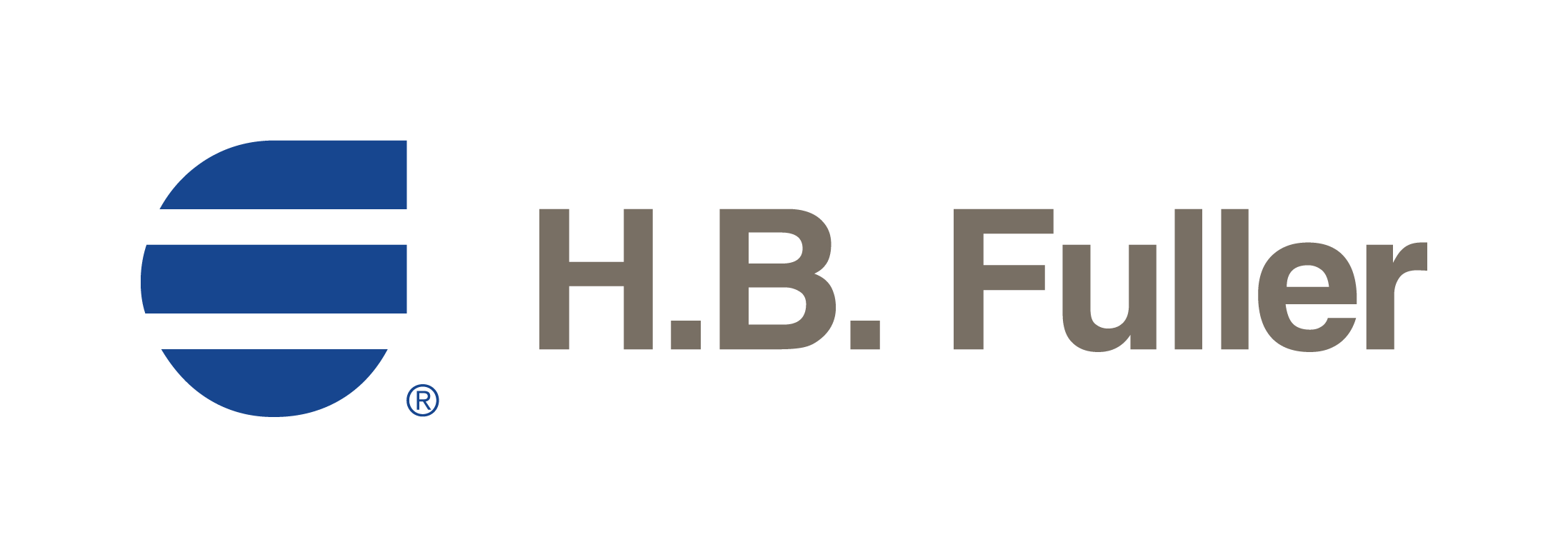
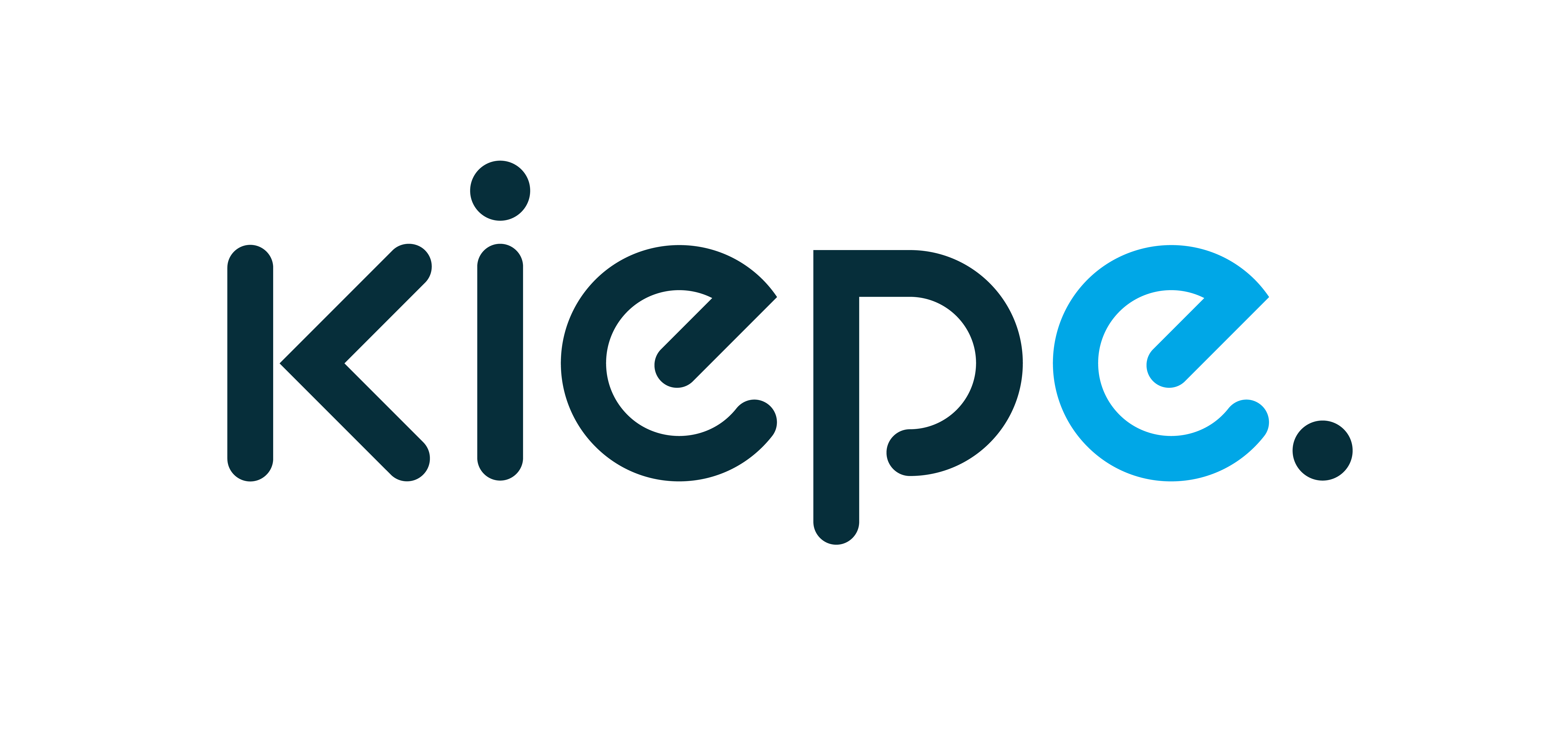
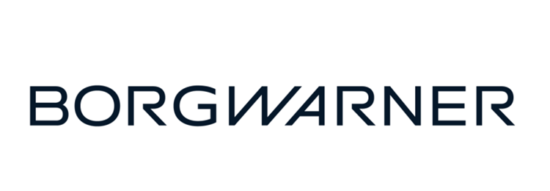