David Hudson
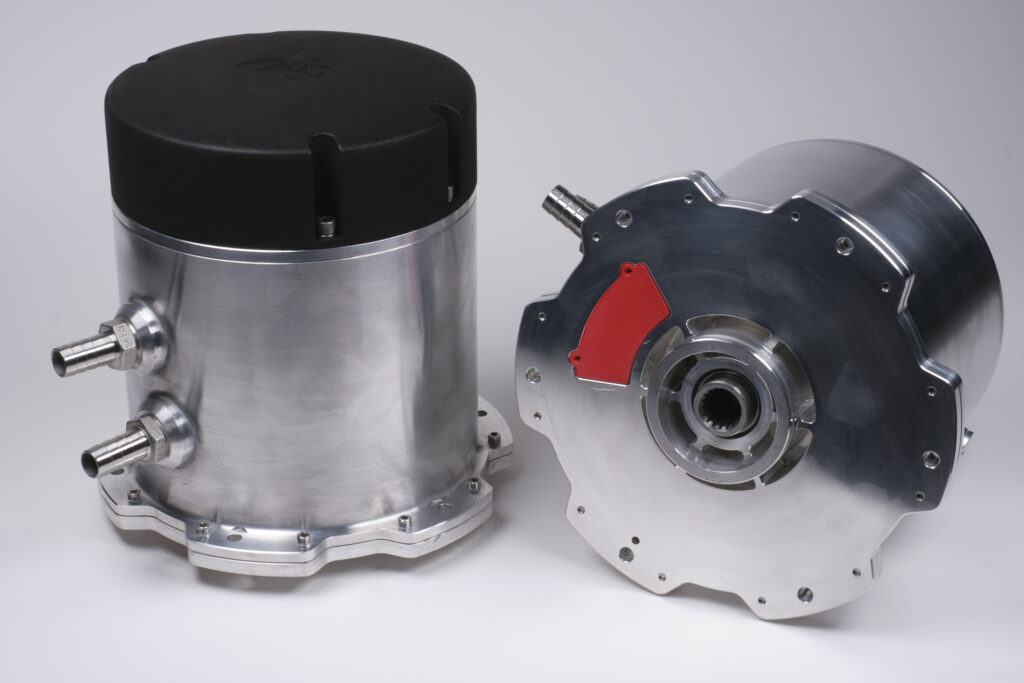
(Courtesy of ePropelled)
Talking the talk
The head of EV strategy at ePropelled tells Rory Jackson how he came into the role and shares details of the company’s dynamic torque switching technology
Predicting growth or decline across different areas of the e-mobility world is challenging at the best of times. These days it is even more complex, with major evolutions sorely needed across systemic factors such as vehicle r&d, material supply chains and worldwide energy and transport infrastructure to pave the way for full replacement of IC engines with zero-emissions powertrains. These factors must be closely watched and understood to enable informed decisions on new investments across manufacturing, research and joint ventures.
Vehicle OEMs need to move in step with these forces to safeguard their assets and strategic decisions in the new automotive age. And ePropelled’s head of EV strategy, David Hudson, knows that need first hand.
His career spans more than 40 years across a number of major names in the automotive world. For the most part of the past 20 years he was particularly prominent in the technical leadership of Tata Motors, managing much of that vast organisation’s r&d and guiding it towards electrification technologies.
Earlier this year, he moved from Tata to the rapidly growing ePropelled, an electric motor company already acclaimed in the UAV world for the high efficiency of its products. The company is now making strides in the EV space thanks to its recently unveiled electric dynamic torque switching (eDTS) technology.
Starting at Jaguar
Hudson’s earliest inspirations and career steps were in the realm of traditional IC engine mobility. A childhood love of cars culminated in him signing up to a mechanical engineering undergraduate programme at the highly automotive-focused Lanchester Polytechnic (now Coventry University) in England, in the mid-1970s.
“I’d had interviews with and been offered university sponsorship offers from several groups then known as members of British Leyland, but eventually I chose Jaguar [the Large Car division of British Leyland at the time],” Hudson recounts. “It was partly out of a love of the brand, but also their interview involved being given an engineering problem to solve; as a 17-year-old, that was quite a thrilling process to be put through.”
He adds that his final-year project was in fact part of an EV competition by Lucas Automotive, open not only to students but professional and independent engineers worldwide. Its aim was to see how far a car could be built to travel on two of Lucas’ lead-acid batteries (similarly to the Shell Eco-marathon competitions, he notes). Entrants selected from an initial design round would continue on to a constructors’ round.
“I worked with a colleague – who’s since gone on to a very successful career in Formula One with Arrows, McLaren and Toyota – using small-scale wind tunnels and finite element stress analyses on the frame to produce a vehicle design that won second prize nationally in the design round,” Hudson says.
“The department was overjoyed, and its technicians helped us get our vehicle built for round two at Donnington Park in 1979. Unfortunately, on the day, Lucas changed the venue from Donnington’s full track – which was hilly but generally all gentle turns, and for which we’d specifically engineered our steering and transmission – to just a test on the pit straight with a U-turn at the end.
“So we didn’t do as well at that event as other, cruder vehicles with lower centres of gravity, but I learned the value of good teamwork on a vehicle concept – dividing tasks, preparing drawings for somebody else to understand, and so on. As an engineer about to enter the professional automotive field, it was maybe the best thing I could have done.”
Although Hudson was involved largely in vehicle research at Jaguar, very little of it had anything to do with electrification at that point. Instead, he honed a specialisation in noise, vibration and harshness (NVH) that would serve him well in the years ahead.
The electric car
Hudson’s tenure at Jaguar ended in 1991. Since then, he’s held numerous consulting positions at various well-known vehicle firms including Aston Martin, Ford, JaguarSport and Lotus.
His career took on a new focus in 1995, when he was appointed technical director for NVH at Ricardo, in its then-new North American office in Detroit.
“They were rapidly expanding from pure CAE work for IC engines into real-world experimentation across full powertrains, and they were working with General Motors on the EV1 project in 1995 – a vehicle since made famous by the film Who Killed the Electric Car?,” Hudson muses. “They brought me in largely just to reduce its gear noise, which had become audible thanks to the IC engine’s absence, but I got a real appreciation and excitement for its overall engineering and what it showed that EVs could do on the US freeways.
“Granted, it was limited by the battery technologies of the day – nickel metal hydride for about 26 kWh and 140 miles – but it was a reasonably quick car, and a great introduction for many of us into what a fully OEM-developed EV felt like. It did 0-60 mph in 8 seconds, felt very sporty, and a lot of the chassis inputs were actually done by Lotus, so they’ve had a long heritage in EV innovation that’s continued to this day.”
Although Hudson was very bullish about GM’s opportunities to get ahead of the curve in EV manufacturing at the time, he notes that the project fell through. GM did not become the EV market leader for various political and economic reasons, not least the introduction of European diesel engines into North American light vehicle markets.
“That yielded good lessons too, thankfully. Integrating diesel engines in place of gasoline ones really made a lot of engineers remember that what a lot of drivers want isn’t power, it’s torque. So we learned to design for what the customer wants, to start doing so early in the automotive design process, and never to go to market with a car made by engineers just for engineers – something new SMEs in the EV space are now quickly learning.”
Between 1998 and 2003, Hudson served as a director at AVL, also in Detroit. Like Ricardo, AVL did little real work in electrification, especially compared with its leading role in the field now, although Hudson did work heavily on emissions compliance across a range of new markets, including powersports and leisure vehicles.
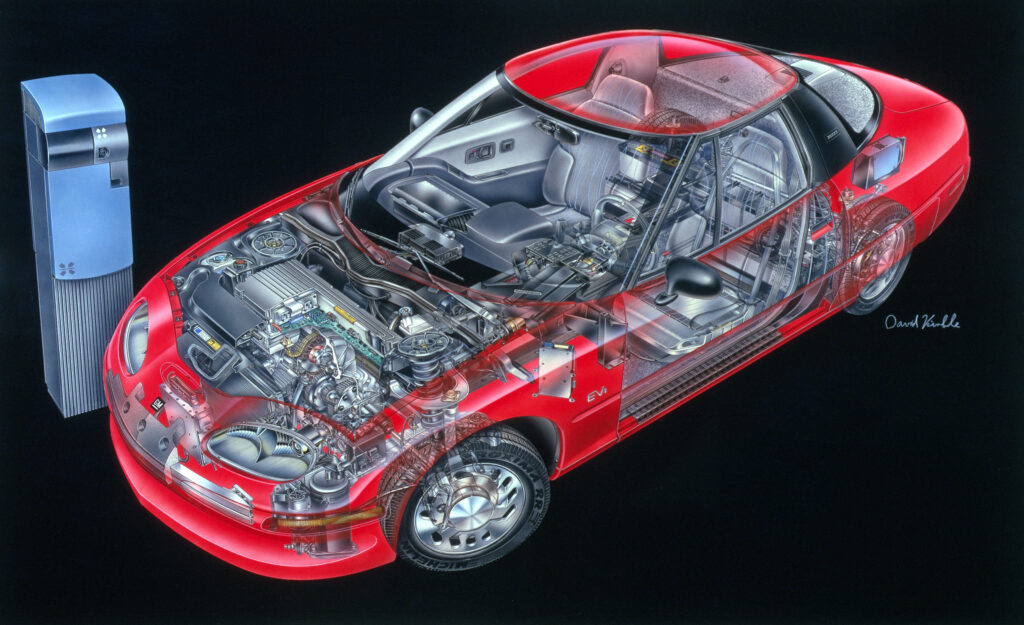
(Courtesy of General Motors)
At Tata
Hudson joined Tata Motors in 2008, after being recruited through the company’s European technical centre at Warwick University. He moved to Pune, India, in June that year to become head of NVH for the next three years.
“It was my first work on heavy-duty trucks and buses, and I was tasked mainly with bringing their vehicles in line with worldwide standards on NVH. India’s import controls were being relaxed so Tata suddenly had to compete with foreign-built vehicles and a much more demanding consumer base,” he explains.
In 2011 however, things changed significantly. Hudson was promoted to chief engineer for vehicle integration, and he was also made engineering lead for a proposed concept of a small EV suited to global markets.
“The Tata Motors European technical centre had been working on EVs since 2007, and by 2009 had a European-certified EV ready for production,” he says. “That was the Indica Vista EV, and it was the first EV to receive European Whole Vehicle Type Approval, pre-dating the Nissan Leaf and Renault Zoe by some years.
“Admittedly it didn’t go on to commercial sale, largely because lithium-ion batteries cost something upwards of $1000/kWh back then and Tata didn’t have the means to subsidise such an expensive loss leader. But it was a crucial knowledge builder for Tata Motors, as essentially every part was all-new and either made in-house or commissioned by Tata – the drive motor, power electronics and the battery were all built to order.”
Subsequent years at Tata Motors saw Hudson advance through chief engineering positions across the OEM’s growing hybrid and advanced vehicle divisions, until eventually being made head of propulsion in 2017 and head of powertrain engineering in 2019.
“There were a lot of interesting projects in those years, for example an Innovate UK programme aimed at building a range extender auxiliary power unit based on the two-cylinder IC engine from the Tata Nano,” he says.
“It was probably the lowest-cost way to develop a range extender and reduce the battery size. Lithium-ion costs per kilowatt-hour had maybe halved since the Indica Vista years, but adding a range extender still helped tremendously to lower development costs, emissions and range anxiety. Ricardo, Lotus, AVL and others had all made blank-sheet concepts for range extenders, but we decided to go the route of using our compact engine that was already in production.
“We met all the MPGe targets, but by the end of the project battery prices finally hit a point where BEVs looked like a golden opportunity. So, just as BMW were launching their i3 range extender concept – with a remarkably similar engineering strategy to ours – we moved on to new, fully electric pastures, including a modular EV architecture project in 2017 and a full-electric conversion of the Tata Racemo sportscar in 2018.”
ePropelled
Hudson’s introduction to ePropelled came when the company was still a young start-up. Its inception came about after a conversation between Nick Grewal, then a US investor looking for patented technologies in the EV space, and Dr Nabeel Shirazee, who had invented and patented what would become the eDTS technology.
The interests of the two were soon combined to found ePropelled, with Grewal as CEO and Dr Shirazee as CTO, and with the start-up initially concentrating on commercialising the latter’s additional r&d into small UAV motors. Automotive e-motors remained a long-term target however.
“To meet that target, Nick and Nabeel were looking for opportunities to work with automotive OEMs and realised they needed drive-cycle data to simulate how ePropelled EV motors would compare against existing e-machines,” Hudson recounts. “Around 6 months after the company had been formed, they and I were introduced through Embed, a software company that was working with both ePropelled and Tata Motors, and was intrigued by what Nick and Nabeel had in store.”
Initially, Grewal offered Hudson an advisory board position to add an OEM perspective. Their discussions also led to Tata, Embed and ePropelled collaborating on a demonstrator vehicle for the eDTS technology, under the UK Advanced Propulsion Centre’s Advanced Route to Market Demonstrator programme, which was unveiled and discussed at Cenex-LCV 2021.
“What really appealed to me was that ePropelled’s r&d is so focused on efficiency,” Hudson recalls. “Nabeel’s technical goals were all about making motors, power electronics and all the related parts lighter and more power-dense. By that time, I’d already spoken at many conferences about the dire need for more efficiency in EVs, especially in emerging markets such as India where EVs were too overpowered, overpriced and ‘over-battery-ed’ for buyers to feasibly make good returns on them.
“So we quickly moved forward on the demonstrator to obtain real-world results showing that an eDTS motor could achieve double-digit improvements [across a vehicle’s full range of operating speeds], rather than the 2-3% gains most researchers are aiming for, and without relying solely on simulated or test bed data.”
Motors with eDTS technology are designed quite differently from conventional PMSMs. The latter feature numerous uniformly shaped and routed stator windings, along with a speed-torque curve that is initially flat at the top and runs asymptotically towards its top speed.
They have only one ‘sweet spot’ of peak efficiency across their performance range, which they fall short of across most other speed points. Also, they need to draw extra current for field weakening as they approach their highest speeds, lest the back-EMF cuts off their ability to continue accelerating at their input voltage.
In an eDTS motor, multiple reconfigurable windings allow the electric motor to provide high torque at low speeds without drawing high current from the batteries, and high speeds at low torque levels without using deep field weakening.
Among the sets of windings, connected variably in series and parallel, a device called a switch matrix is used to switch between them, all the while communicating to the inverter which ‘motor’ is receiving the power.
“We’ve had some questions about the ‘redundant windings’, but no windings are redundant in eDTS,” Hudson points out. “We have current flowing through all the copper at all times.”
Based on the operating needs, the control system determines (in real time) where the system should be on the adaptive shift map. The control system then configures the switch matrix, which enables the various modes. The ECU can switch electronically and dynamically between these, much as a conventional IC powertrain uses mechanical gears to switch to different speed-torque curves suited for different road conditions.
“As a result, each mode will have different characteristics, including torque profile, speed range and constant power range,” Hudson says. “It’s always an optimal or near-optimal motor, no matter how your weight or the road changes. The control software navigates between windings to find the highest efficiency, and keeps the phase currents as low as possible in each operating condition to minimise iron and copper losses.”
Hudson notes that the core technology is established in Dr Shirazee’s original patent and is now in the eDTS motor prototypes. The company is now focused on the motor control algorithms to optimise switching and power efficiency. After that, road testing will be carried out to observe how EVs feel and handle when running on eDTS motors, particularly to minimise any changes in vehicle response when switching between motor modes.
“When the opportunity came to join ePropelled as director of EV strategy earlier this year, I leapt at the chance to become part of their big push,” Hudson says. “Nick’s confident about the difference that Nabeel’s tech can make in the EV space, and in being able to make agile and accurate strategic decisions using what I’ve learned over the years.”
Future plans
Hudson anticipates that testing and application validation of the eDTS technology will take up most of ePropelled’s focus for the next several years. Key EV markets will initially include light-duty automotive OEMs in South Asia, where programmes aimed at creating compressed natural gas infrastructure have failed to bear fruit, and electrification – mostly via battery-swapping infrastructure – is now being promoted, as well as marine and aircraft customers.
“It will take some work, as our initial eDTS prototypes have generally been 70-80 kW units, and the target market in South Asia is mainly 10 kW vehicles,” he notes. “And once we’re satisfied with the software and approach to scalability, we’ll focus on certifications for all the automotive, aviation and other standards that end-users expect.
“Also, marine might be an unexpected area to look into, but it’s very interesting. There are huge sections of the maritime industry that are rapidly moving towards electrification, but are doing so with very crude, inefficient and expensive powertrain technologies, especially compared with road vehicles.
“An eDTS outboard motor could work brilliantly, because speedboats have very similar torque-switching requirements to cars. You need high torque at low speeds to pull your propeller, but once you’re planing, you can cut the torque because your drag force has dropped dramatically.”
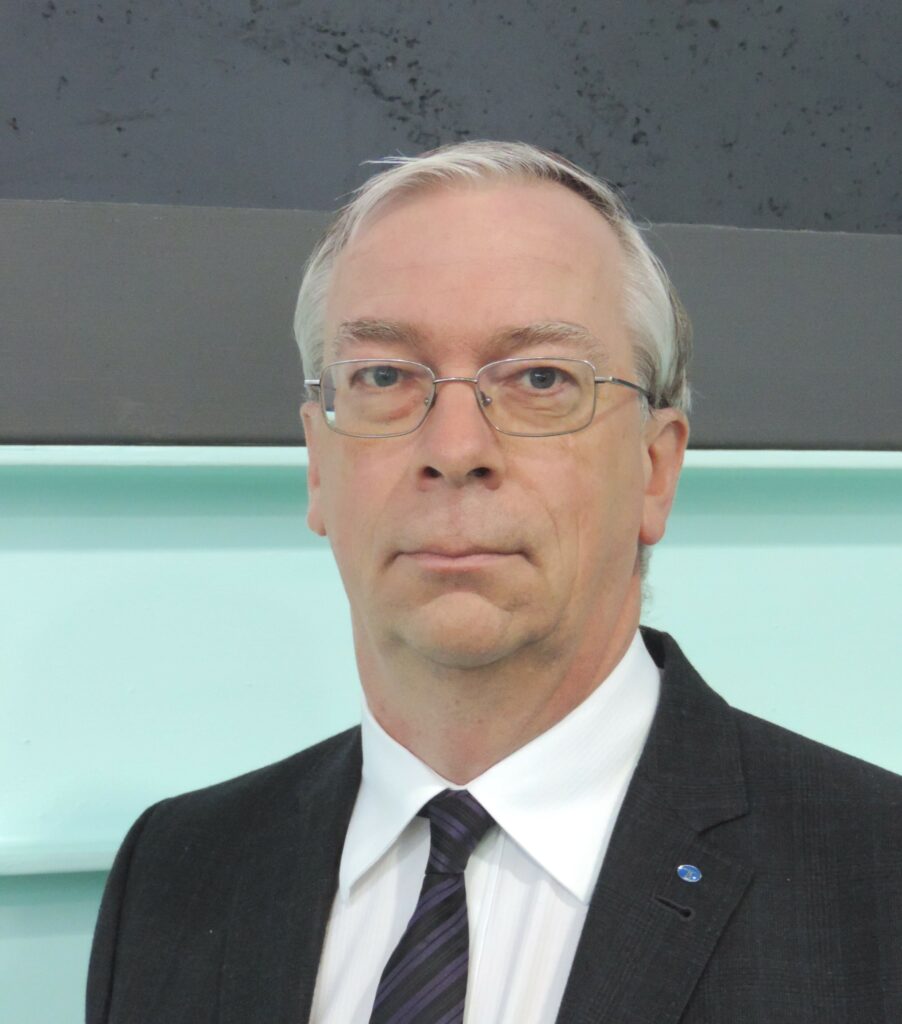
In addition to future advances in solid-electrolyte batteries, Hudson anticipates that improvements across a huge range of technologies such as additive manufacturing, composites and even bearing concepts stand to go a long way towards reducing the drag, weight and frictional losses that are holding EVs back from their full potential.
“There are many technological challenges in the EV space, but I do feel most of them are being faced head on,” he says.
BIO – David Hudson
David Hudson was educated at Coventry University, in England, graduating in 1979 with a BSc in mechanical engineering. He quickly took a senior management position at Jaguar, which he held for 14 years. Between 1991 and 1995, he held a number of consulting roles simultaneously at several different companies, while working as chief engineer of vehicle development at Lotus Engineering from 1993 to 1995.
He worked at Tata Motors for 13 years in a series of chief engineering roles before joining ePropelled as its head of EV strategy. In addition, he sits on Cranfield University’s Industrial Advisory Board, steering committees for various conferences, and is a member of the UK Automotive Council Technology Group.
ONLINE PARTNERS
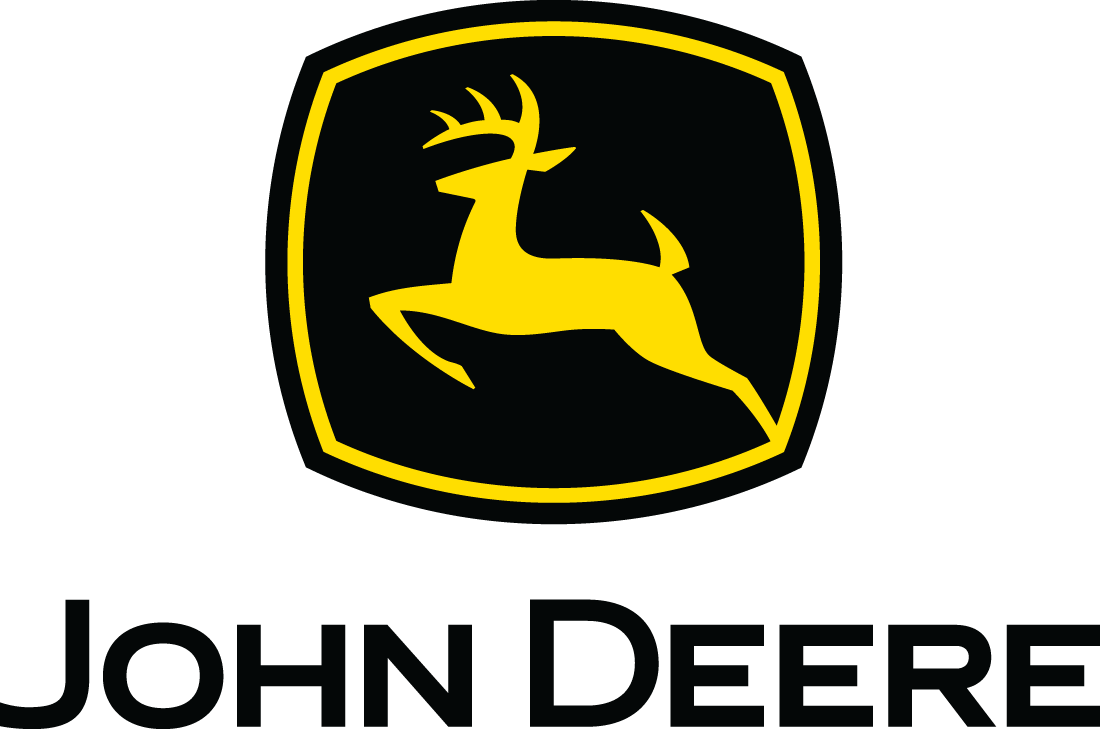
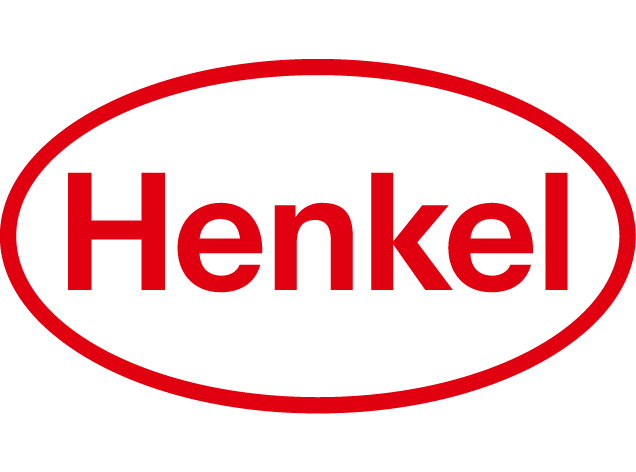
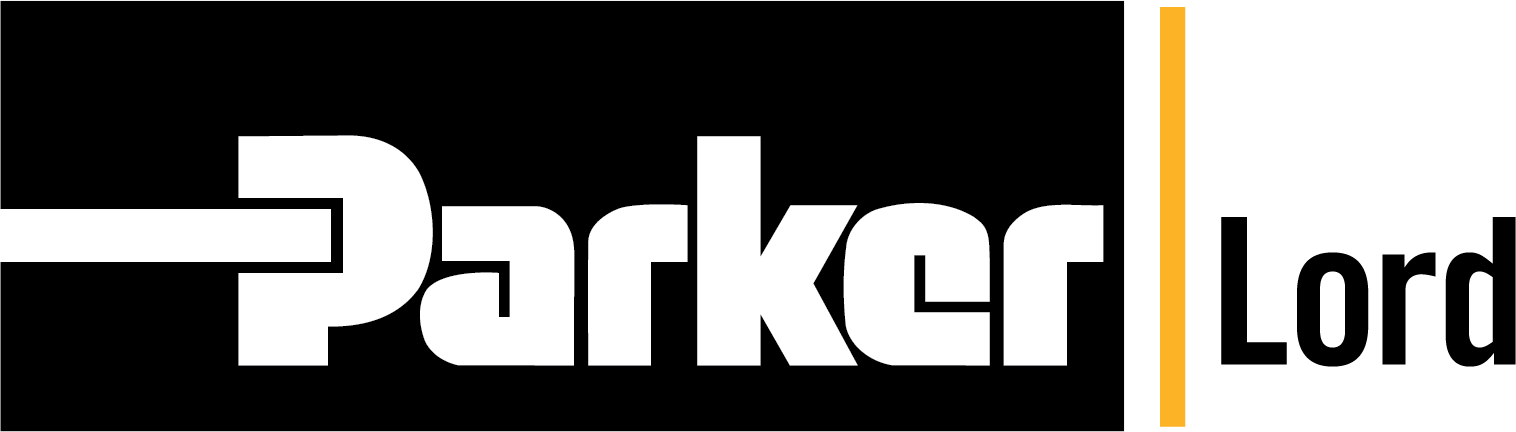
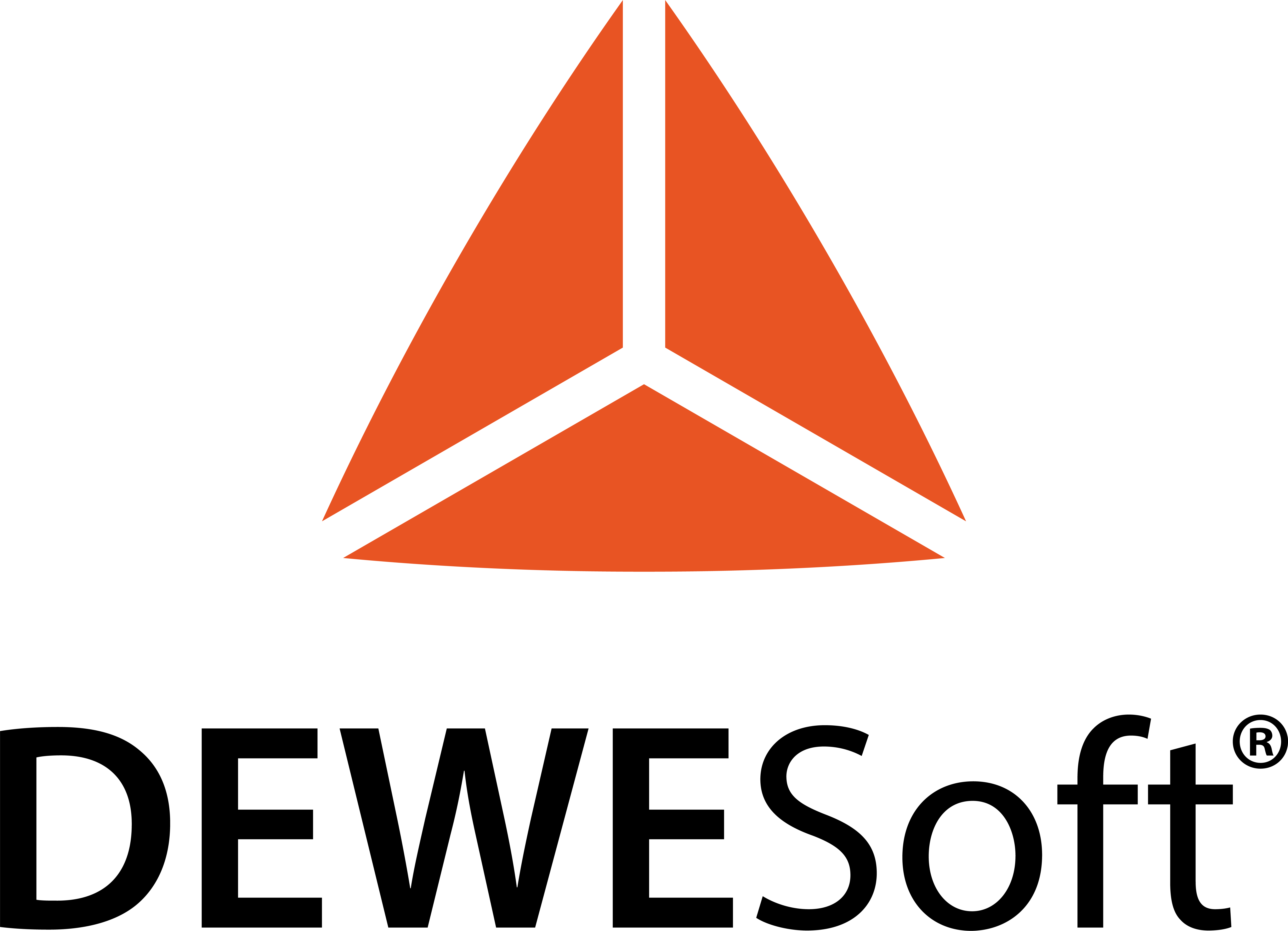
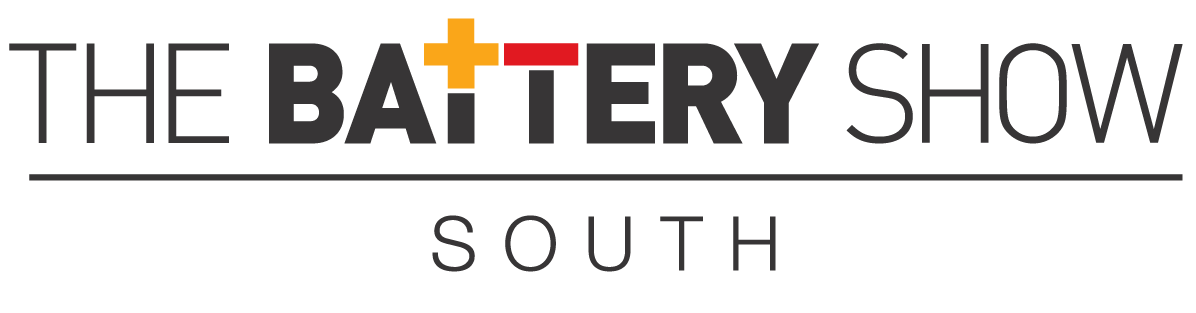
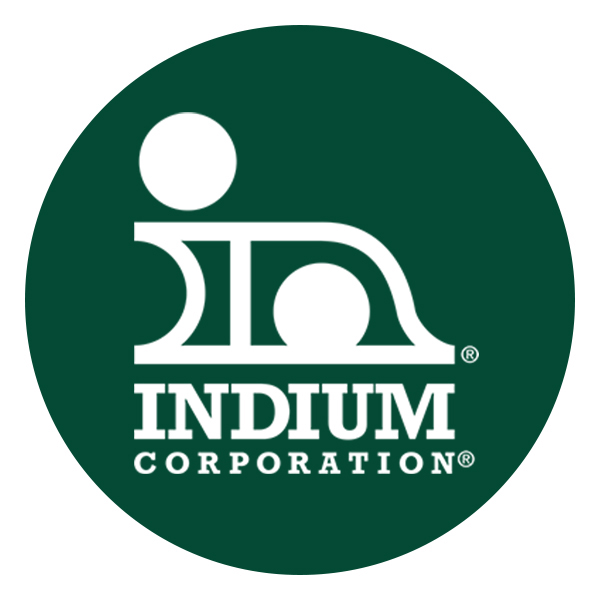

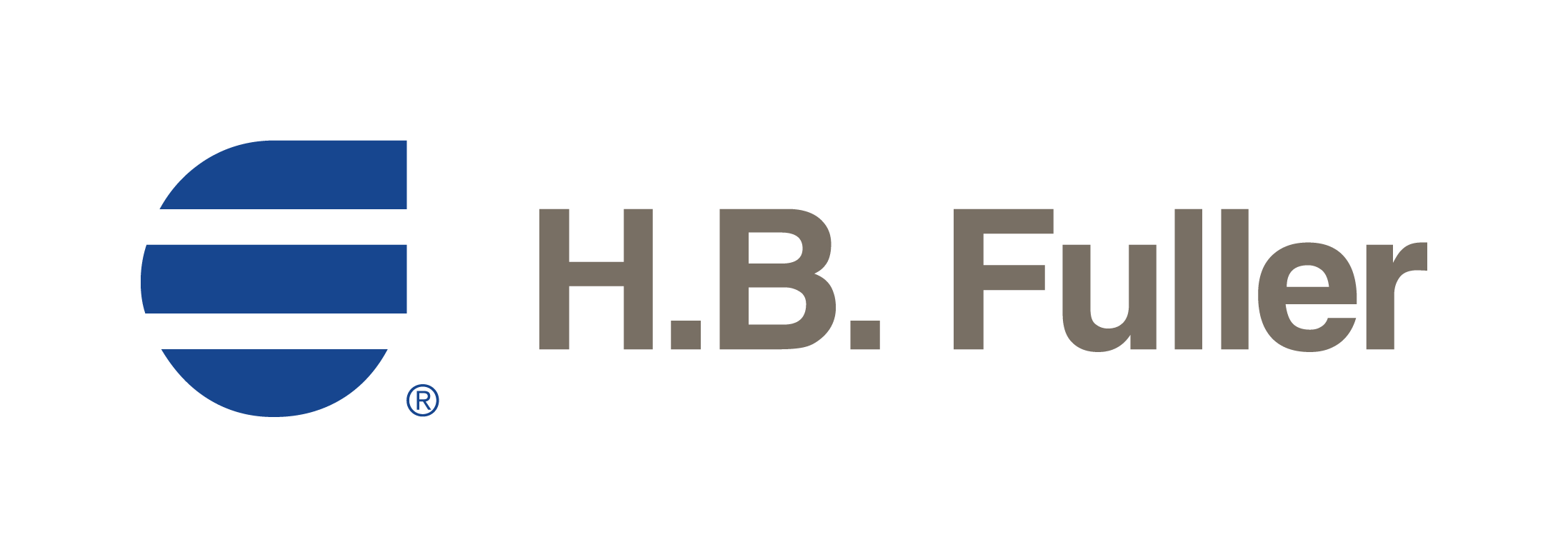
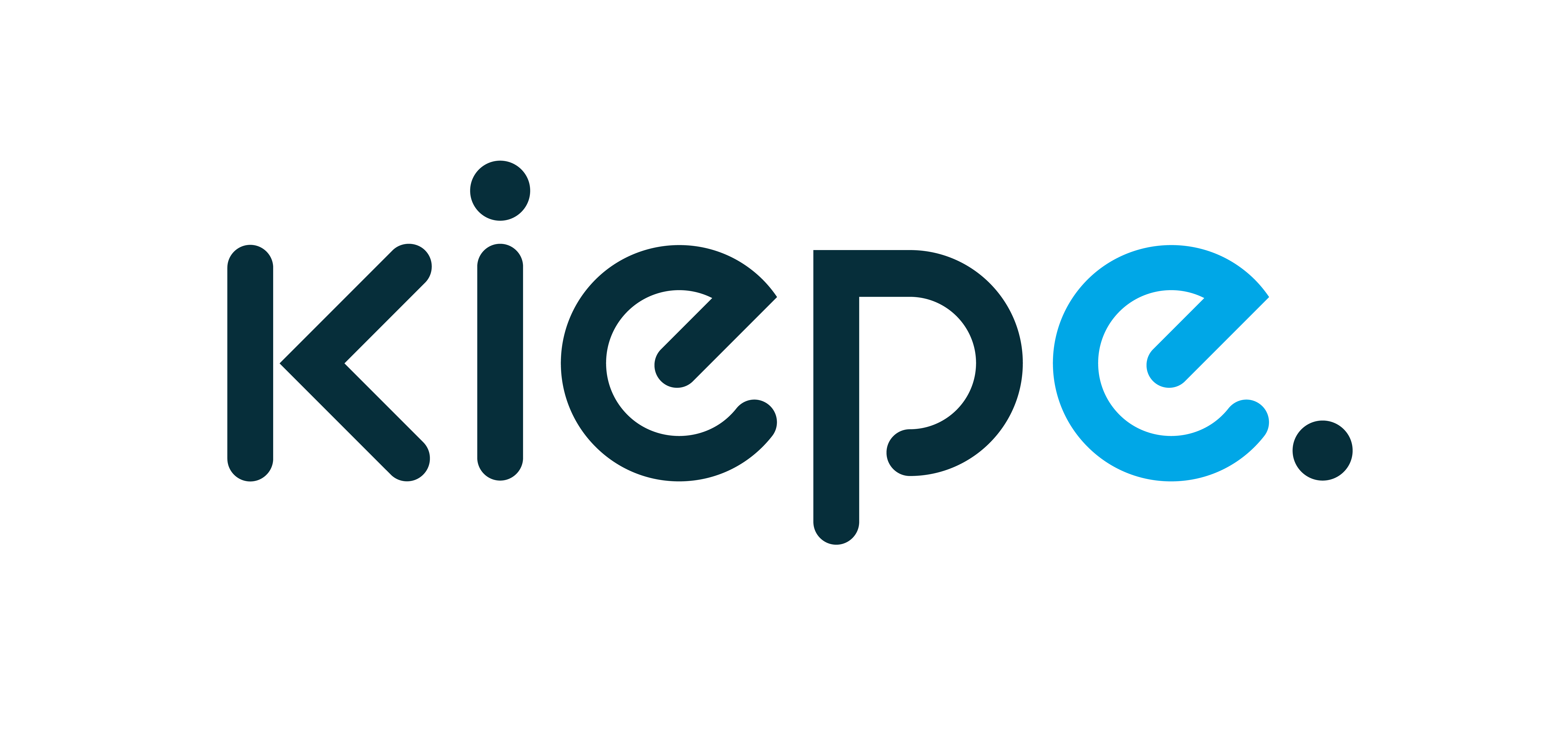
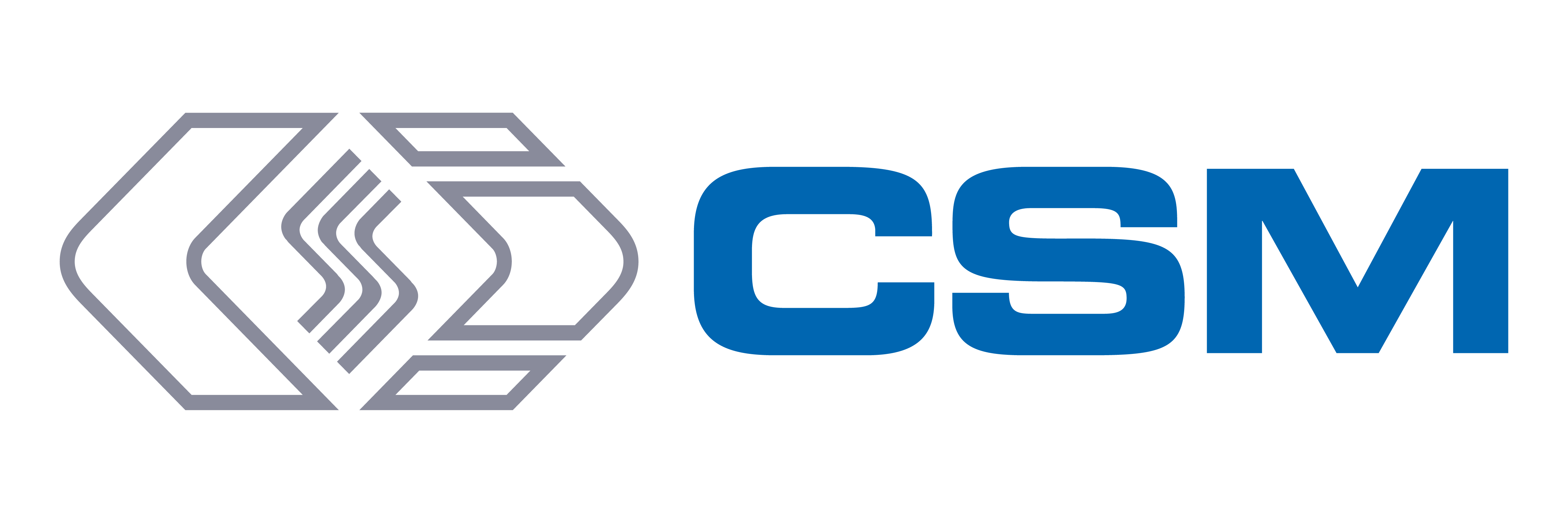