Uniti One
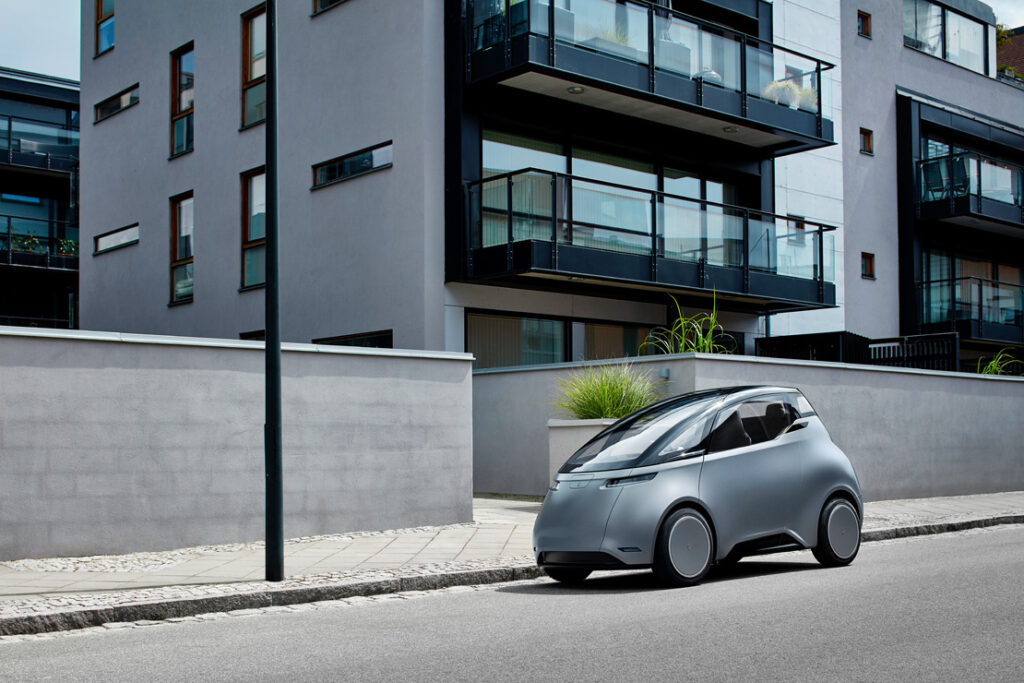
(Courtesy of Uniti)
Start-up’s standing start
Lawrence Butcher reports on how a Swedish start-up plans to design and manufacture a market-ready EV from the ground up.
If one looks across the automotive EV market, it seems barely a week goes by without one company or another announcing that it will revolutionise the electrification of vehicles and unveils a host of sharp design renderings. The vehicle in question invariably takes the form of a hypercar or SUV.
However, such concepts, while bold, are probably not the easiest way to enter the EV market, which is already saturated by new-tech companies such as Tesla, and established automotive manufacturers which are starting to ramp up EV production to significant levels.
A more realistic approach could be that being taken by Swedish startup Uniti, with its Uniti One project. The concept is a seemingly obvious one – pick the market area where an EV currently makes the most sense, the city car sector, and build a small, lightweight vehicle that meets the needs of urban mobility at a reasonable cost. Also, by not having an existing manufacturing infrastructure, it can harness the latest advances in manufacturing technology to ensure lean, efficient and importantly, sustainable production.
It should be noted that, as of the start of 2019, Uniti had not built a single production car or even an engineering prototype of one. It had however completed prototyping work on an earlier concept of the vehicle, and was deep into an engineering feasibility study of what would become its launch vehicle.
From concept to reality
The Uniti One is a compact, two-seat EV, with a 1+1 seating layout (where the passenger is seated behind the driver). To gain a proper understanding of the Uniti project, it is worth looking briefly at its background.
The brainchild of Swedish entrepreneur Lewis Horne, its roots lie in an innovation project undertaken at Lund University, Sweden. The initial concept for the Uniti was to be an L7E class vehicle, otherwise known as a quadricycle. That would put the car in the same class as vehicles such as the Renault Twizzy.
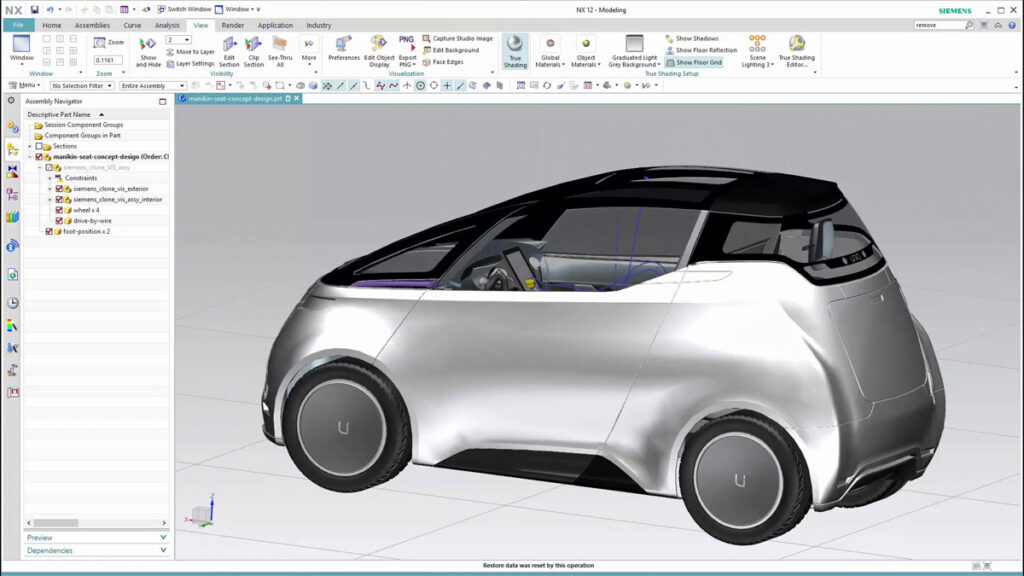
(Courtesy of Uniti)
In short, and in Europe at least, quadricycles do not have to pass the same stringent certification that M1 class cars do, making it far simpler to put one into production. The Uniti’s initial concepts and prototypes were based around the requirements for a quadricycle, but with European regulations due to change in 2020, the quadricycle route is no longer viable in the long term. The Uniti One is therefore being upgraded to match the requirements of M1 homologation – a significant engineering undertaking.
To achieve that, Uniti has enlisted the help of two companies to undertake this phase of the vehicle’s development – Danecca, a specialist in battery and powertrain engineering, and KW Special Projects, which is working on the wider vehicle engineering concept, including the implementation of a lightweight, composite chassis.
The intention is ultimately for the Uniti platform to be easily adaptable to different roles in a city environment, be that the use of a body variant to create a light goods vehicle or perhaps a version whose only role is to provide remote charging for other vehicles.
“If you look at the size of the platform, there is so much scope to diversify into other uses and solve inner-city transport issues,” says Horne, who is Uniti’s CEO. Here, the use of a 1+1 seating layout has the benefit of allowing for a narrow vehicle – ideal in a city environment – while still providing sufficient volume for the inclusion of structures to mitigate side impacts.
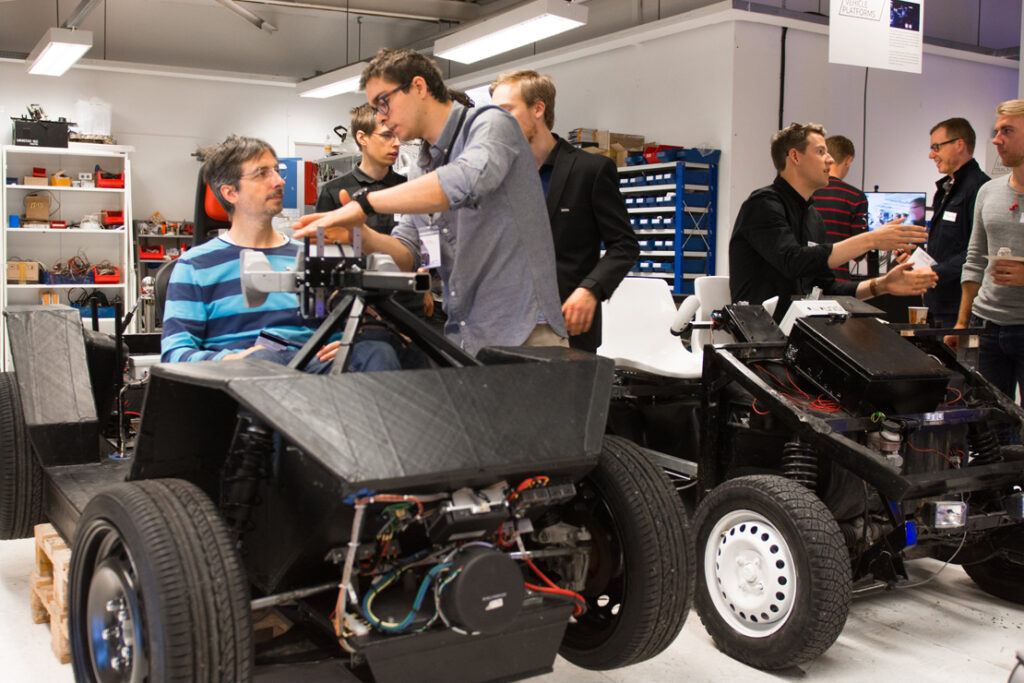
(Courtesy of Uniti)
Uniti’s plan is to try to keep the core aesthetic of its concept vehicle, but the move to the M1 class will mean reassessing some of the vehicle’s design characteristics. For example, M1 certification has stringent requirements on the location of hardpoints on a vehicle and their potential effect on pedestrians in the event of a collision.
There are also some perhaps unexpected issues that will tax the engineers. For example, the central seating position means there is not an obvious way to mount seatbelts. There is also the large, glazed area to consider, which needs to be considered from manufacturability and safety perspectives.
Uniti says the ultimate plan is for the vehicle to be homologated in markets across the globe, but initially the target will be European homologation. Requirements in Europe are some of the most stringent in the world, and if these are met then a move into other markets will be relatively straightforward.
Powertrain
The Uniti One is not intended to set the world alight with its performance, be that in terms of speed or range. It is meant to be a cost-effective, small city car. As such, and much like the 1+1 layout, the powertrain design is tailored to that purpose.
The target power output for the Uniti is 120 kW, to be achieved with the use of two 60 kW motors, which Danson Joseph, director of Danecca, points out is plenty for such a small vehicle.
“If I look back to my first car, it was an Opel Kadette, and I think that was only 55 kW, which was not a problem. But the actual power is not that important; the important bit is that the torque is available from the outset.
“Generally speaking, with a car like this there will be a point at 50-60 kph where the driver will be at the next set of lights, or taking their foot off the gas for another reason. It’s not a car that needs to be a racecar. Power is not the critical element.”
The plan is to use as many off-theshelf components as possible, rather than designing bespoke parts. “By that I mean finding a product that is in existence, might need some tweaking but that is essentially already developed,” says Joseph.
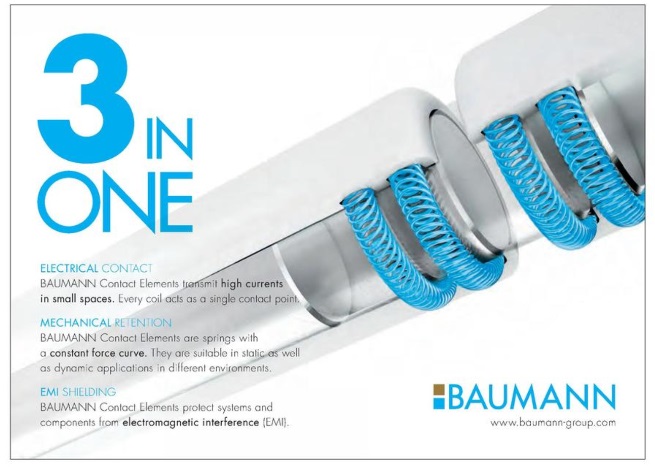
When it comes to selecting drivetrain components, Joseph notes that there is little point trying to develop motors and inverters from scratch. “They have a long heritage, so to try to develop something new is not worth it,” he says.
“With the battery, because it is such a big part of the car physically and in terms of cost – you can say it is roughly a third of the cost and weight of a vehicle – you need something bespoke. So we are focusing on developing the battery first and then selecting powertrain elements that are compatible with it.”
Danecca’s involvement in the project is the reason behind this battery-first approach, as the company’s key competency is battery development. “Most people don’t like to touch batteries, but for us they are the most important element, and the rest of the powertrain can be matched to them,” says Joseph.
The combined pressures of cost and customer expectation play an important role in the specification of the powertrain, says Joseph. “If you look at most vehicles, they have a permanent magnet machine, inverters and an onboard charger.” However, rather than permanent magnet motors, Uniti is likely to use synchronous reluctance types.
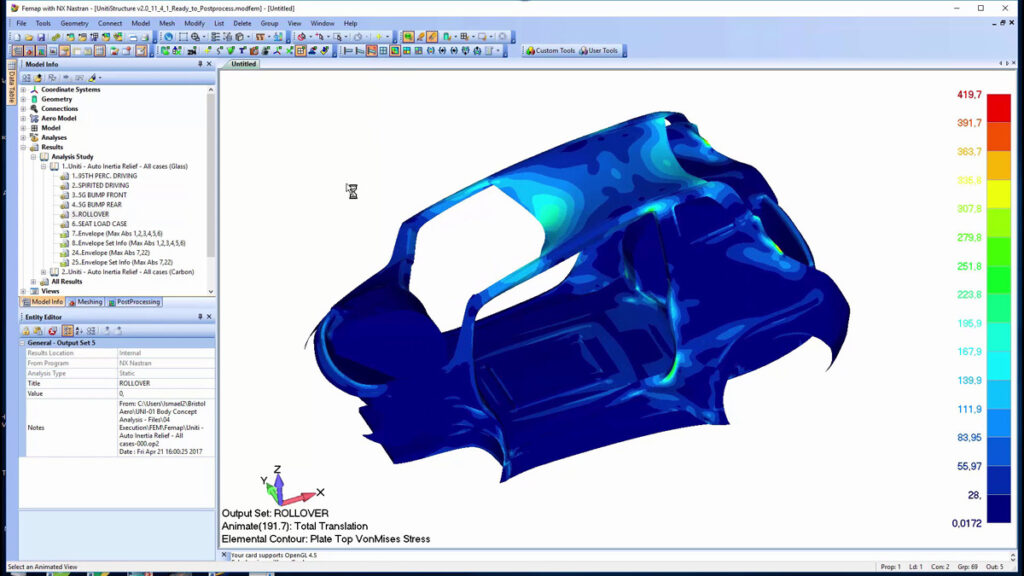
(Courtesy of Uniti/Siemens)
The reasoning for this, Joseph explains, is “they are hardy machines. You can’t demagnetise them, they are cheap, and with this project – although we are engineering for cost – we will not be sacrificing performance.”
From a packaging perspective, the team has looked at conventional chassis-mounted motors as well as in-wheel solutions. “We will go with a chassis-mounted motor, mainly so that we can go with existing suppliers, because the time frame is short and we can get things rolling early on,” says Joseph.
The motors will be mounted in the rear of the vehicle, with Joseph adding, “The space at the front will be needed for things like the water-to-air heat exchangers. There are a lot of components that need to go in the front, not least the crash structures.”
The modest performance level of the Uniti means that no transmission will be needed, with a single-speed direct drive from the motor. “The speed will be capped at 130 kph, and that helps with our range estimation as well,” Joseph says.
“With the WLTP [World Wide Light Vehicle Test] cycle we use, if you go over 135 kph you have to have an ultra-high speed zone [of operation], which this car is not designed for. It is a commuter car, so you could go on a motorway, but you won’t go from London to Birmingham with it every day.”
He also highlights that the battery will take up the bulk of the underfloor of the car and encroach into the nose area. “With that in mind, we are looking to incorporate both the charger and the inverter into the battery housing. The idea is that the battery will come as an assembly, which has connectors for the external charger cable and the motor, and a connection for auxiliary systems,” he says.
This packaging idea relates to the manufacturability of the vehicle, and its suitability for Uniti’s desire to have a scalable production model to suit different markets. The aim is for a modular factory set-up, where the same basic factory layout can be scaled larger or smaller to accommodate different production volumes.
A car built on a modular concept in remote factories is not a new idea, Joseph points out. “If you look at the British car industry and how cars were assembled in South Africa or Australia, you had the parent company making kits in the UK and shipping them out. That is probably the way it will work with Uniti, with kits made in a central location, because you need those economies of scale.”
Taking just the cells as an example, Joseph notes, “You wouldn’t be able to have cell plants in each manufacturing location, it just wouldn’t make sense.”
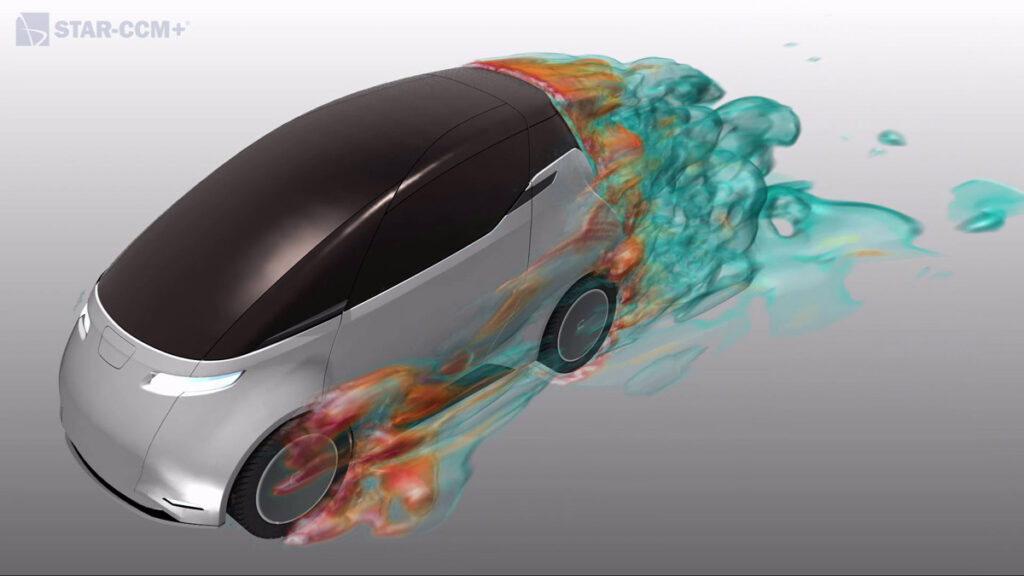
(Courtesy of Uniti/Siemens)
Evidently, the logistics of distributing the assembly of cars across the globe are daunting. Here, a partnership Uniti has forged with Unipart will come into its own, as the company already has an established logistics network and, importantly, is experienced in moving batteries, as it already works with manufacturers such as Tesla.
The battery packs will weigh about 400-500 kg. As for the type of cells used, Joseph says, “We are looking at a number of options.”
One of the biggest considerations here, he says, is certainty of cell supply at the volumes needed to begin production. “You can’t touch Panasonic, because of their relationship with Tesla; LG are not accepting new projects and Samsung are much the same. It’s not a buyers’ market.
“But we have been working with a partner we met in Japan and they are pre-qualifying some Chinese manufacturers, and through them we have found a really good cell supplier. They are seen as competition by Samsung so that is a good thing.”
The cells will probably be 18650 units and, by using cells with a smaller form factor, rather than larger cylindrical cells, or pouch or prismatic cells, Joseph says, “You become less susceptible to cell-to-cell variations.
“That is quite helpful if you are using cells from a manufacturer and they haven’t quite established the same narrow band of performance for their cells [as some of the premium brands]. If you went for a pouch cell [or one of the new generation of larger cylindrical cells], that variance could create a problem.”
Sticking with the philosophy that the Uniti is a small, urban vehicle with modest performance, Joseph says, “It doesn’t need a supercooled battery pack. What it needs is a cost-effective system, and for that we will look first at tried and tested technologies, which is why we are looking at cylindrical cells. I won’t say we won’t try something else in the future, but the aim now is to get products out there, not break new ground.”
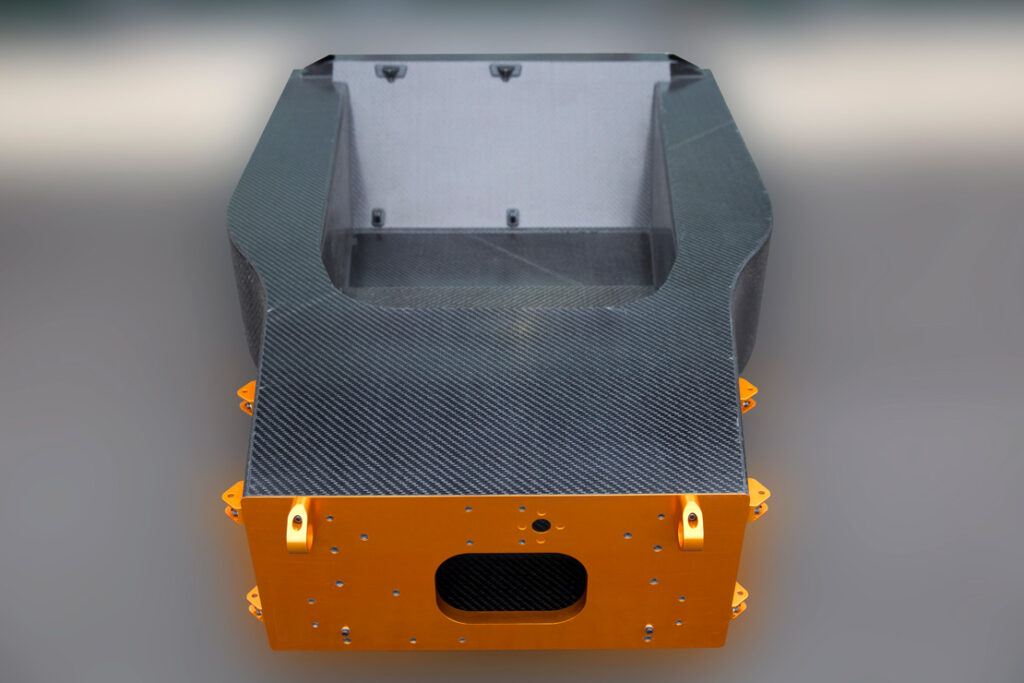
(Courtesy of KWSP)
The battery packs will be liquidcooled, although the use of liquid cooling is to help keep the overall pack temperature consistent, not as Joseph says “for cooling huge power draws”. The use of water cooling also provides the capacity to allow fast charging of the packs.
On this latter point, Joseph notes that although the standard charger power in the UK and Europe is currently 50 kW, this will probably move to 100 kW and beyond in the near future. “At that point, your car has to be able to accept that,” he says.
Being a passenger vehicle, there are other considerations regarding the use of battery energy beyond simply propelling the vehicle. The cabin will need cooling and heating, the latter giving the possibility of harnessing the cooling circuit of the battery or motors.
Joseph says, “You have the question of whether you want to share the cabin cooling with the battery.” On the one hand, taking such an approach might lead to compromises in the cooling system, but “it also has to be a light vehicle [so sharing the cooling reduces the parts count] and that is all part of the compromises you have to make.”
As for the layout of the battery, Joseph says. “You end up with certain magic numbers when you are doing a battery pack. What we are looking for is a layout for the 1+1 car layout which gives us some manoeuvrability for a 2+2 set-up.” The ideal would be that the battery for any future 2+2 model could simply be scaled up from the 1+1’s pack, but Joseph cautions that designing with this intent might not always be the best solution.
“You have to ensure there is value to having crossover,” he says. “For example, if the cells are common in the modules, you might be able to get away with a few common brackets and parts.
“But the important bit is the bill of process being the same, even if the modules are not. As long as the process – the technology – is the same, then you realise the economies of scale. These economies might be less if you try to keep the same module shape and size if it then complicates the packaging design.”
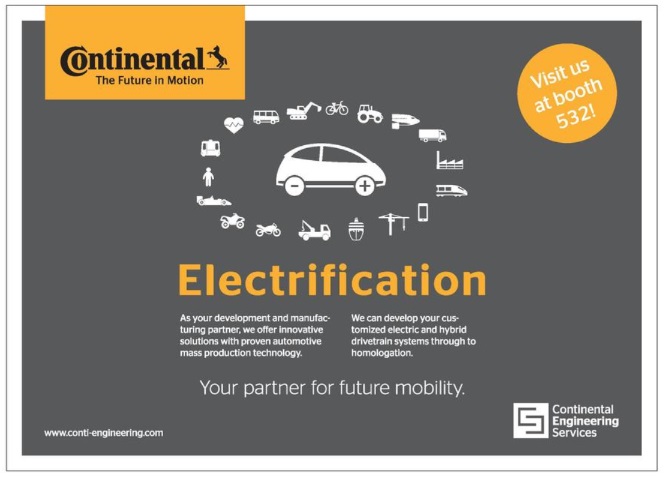
Ideally, from packaging as well as manufacturing efficiency perspectives, the battery will make up the entire lower section of the chassis, acting as a structural member. That means the battery pack will not simply be placed in a structural container, but will also incorporate its own internal load-bearing structures. “It has to be like that, you have to look at the different collision scenarios,” says Joseph.
Explaining the benefits of making the battery a structural part, he says, “Looking at work VW has presented, for every kilo you take out of the battery to make it non-structural, you have to add two kilos onto the chassis to ensure survivability. So you lose out on a 2:1 ratio. If you don’t make the battery structural, you have this huge area that is in effect just an opening.”
Lightweighting
Key to the success of the Uniti One will be a chassis that is lightweight and sufficiently strong to pass rigorous crash tests, yet also cost-effective to manufacture within the constraints of a mass-produced vehicle. The lighter the chassis, the more efficient the overall package and the greater the range that can be achieved from a given batterymotor combination.
The obvious answer to the lightweighting question is the use of composite materials, specifically carbon fibre, for the chassis’ main structure. However, carbon fibre is expensive to produce and, in most cases, labour-intensive and thus costly to manufacture. This is where partner company KWSP comes in, with its ToPCaT chassis system.
Headed by renowned motorsport engineer Kerion Salter and based a couple of miles from Silverstone in the UK, KWSP’s remit is “to provide a feasibility study around basing the chassis on our ToPCaT technology. The aim is to have a recyclable, low-cost and low tooling cost chassis platform,” says Salter.
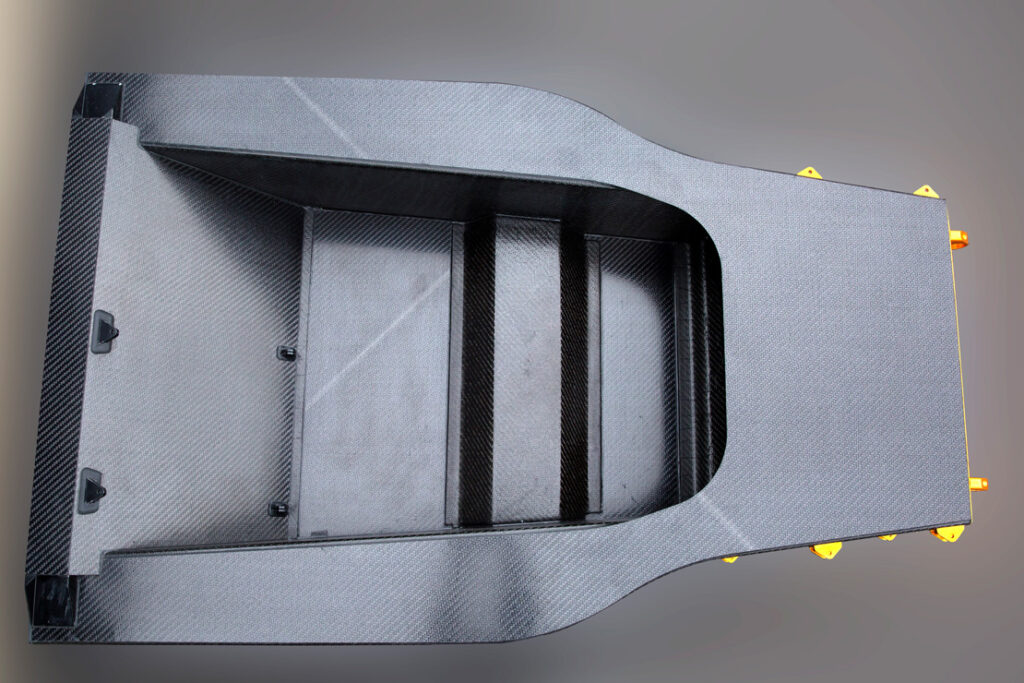
(Courtesy of KWSP)
ToPCaT is a composite chassis concept that uses a thermoplastic composite material, rather than a traditional thermoset composite. The roots of the design can be traced back to a model devised by Salter (when he was working for Reynard Motorsport) in 1998, in an effort to produce a low-cost composite chassis for Caterham Cars.
This initial concept, which was designed to reduce the manufacturing costs of composite chassis, consisted of just four main structural panels with structural sills, at that point made from traditional thermosetting composite material. Unfortunately, Reynard’s demise meant the project never came to fruition, but the idea stuck with Salter, to resurface years later, in 2008.
That was in the form of a concept based on a Sports 2000 (an opencockpit sports racecar) that originally featured a fabricated aluminium chassis, the manufacturing cost of which was high. “Around that time I was also introduced to a company called TenCate, which produces aerospace thermoplastics,” Salter recalls.
KWSP began to work with TenCate on other engineering projects using the thermoplastics, and recognised that the material could be ideal for the construction of the chassis concept.
To explain briefly, a thermoplastic composite is one where the individual fibres (in this case carbon) are encased in a polymer matrix that can be melted. The combination of fibres and polymer are heated, allowing a sheet of the material to be formed to the required shape and then cooled, setting the polymer.
An important factor here is that it is a repeatable process. With a thermosetting material, the fibres are encased in an epoxy resin, which is flexible until it is cured (again using heat), but the process is not reversible. Thermoplastics have the potential of lower manufacturing costs than thermoset composites though, as expensive equipment such as autoclaves are not required.
Salter explains that the properties of thermoplastics matched the needs of his low-cost chassis idea from a price and manufacturability perspective, so he began working out how the materials could be used in the design of a vehicle monocoque.
“We did a huge amount of characterisation work with the material, understanding how it behaved, and assessed it using FEA,” he says. “That then led us into a proof-of-concept chassis, which was based around the Sports 2000 monocoque as a benchmark, because we had all the FEA and crash data for that – it allowed us to make a direct comparison. The thermoplastic chassis ended up lighter, stiffer and cheaper to produce than the aluminium one.”
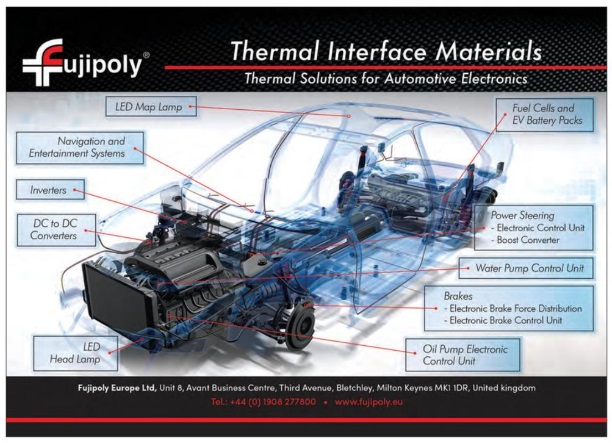
This chassis formed the basis for what is now referred to as the ToPCaT chassis system, which stands for ThermoPlastic Carbon Tub. It provides a blueprint for a lightweight yet costeffective chassis that can be tailored to a specific vehicle application.
While all this sounds relatively straightforward, the process of learning to work with thermoplastics was an involved one. KWSP developed methods for forming the composite panels, joining them and how to achieve certain surface finishes. It effectively developing a design guide for building chassis with the material, a process that was completed in 2014, with a proofof-concept demonstrator constructed in 2016.
In 2018, Uniti and KWSP linked up and, as Salter says, “Uniti got it straight away. They were starting with a cleansheet-of-paper design, and it suited our design methodology very well.”
Thus began the first phase of the project – a proper engineering-led feasibility study into using ToPCaT as the basis for the Uniti One.
It is not just the chassis design that KWSP is investigating; it is also looking at all aspects of the vehicle’s engineering, from assessing the balance between stylistic desires and engineering reality, to the ergonomics of the interior.
“One thing we have tried to do is encourage a ‘light touch’ approach [from Uniti] and not have too many preconceived ideas. By not thinking you already know what the solution is, that is how you innovate,” observes Salter.
This approach means that even in some areas where KWSP has considerable experience, it approaches matters from first principles. An example Salter highlights is assessing the crash structures on the vehicle.
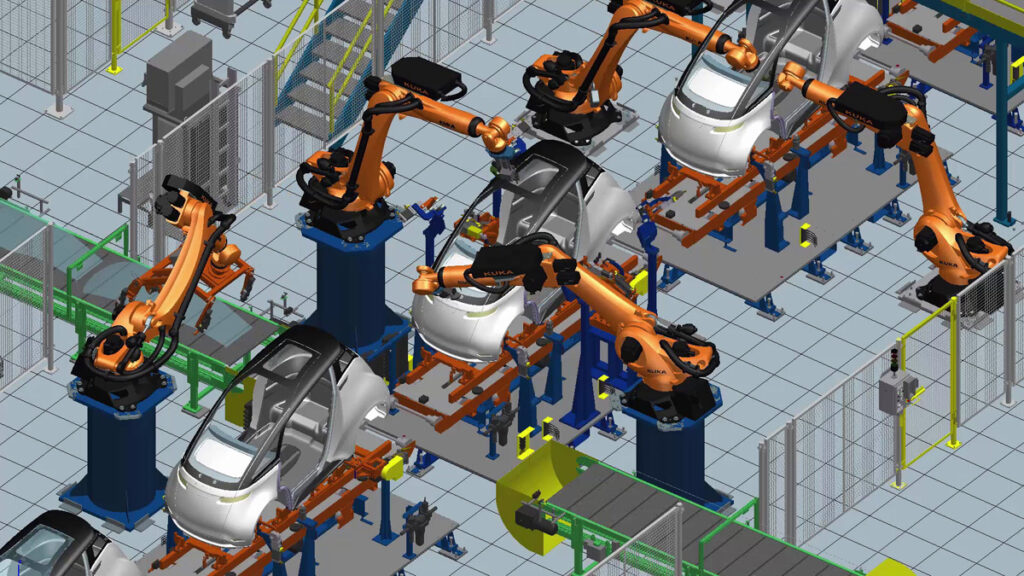
(Courtesy of Siemens)
He says, “We start off materialagnostic, so not looking specifically at the [performance of the chassis when constructed from] thermoplastics, to find out if the body as it stands actually has enough space for dissipating crash energy. It might be that one simply cannot meet crash regulations with a specific volume or a particular hardpoint in the way.”
While the main features of the chassis design are still being finalised, Salter was able to give some idea of how the structure would be formed. “It might be that we can get away with two main side panels and a floor, with some structures to support the roof,” he says.
“It will be a bonded structure and, as far as possible, suitable for robot assembly. We are already able to cut and form the [thermoplastic] panels using automated systems, because there are no discrete plies to be laid up.”
Looking at the wider picture – not just the main chassis – from a vehicle dynamics perspective, Salter notes that high cornering speeds are not a priority. As such, the suspension can be quite simple. It will most probably use a MacPherson strut set-up, at least at the front.
“It is all about ride quality and, as it is a city car, you need a tight turning circle,” he says.
However, he points out, “When you build a very narrow car, getting a tight turning circle can be tricky as you need a big wheel clearance envelope, which can intrude on the space for front crash structures. So we are working on problems like that at the moment.”
This last point highlights what Salter describes as one of the biggest challenges with a small city car – “There isn’t any space to put in the systems you need, so you need to get quite creative and imaginative in the packaging. Finding nice, big open spaces to keep things cool is difficult, for example.”
Naturally, KWSP is working closely with Joseph and Danecca, as the packaging of the powertrain is clearly linked to the chassis layout and design. For example, the structural role of the battery pack – making up, as it probably will, the bulk of the floor – will be integral to the overall vehicle’s structural integrity.
However, he cautions, “You need to work out how that battery structure can become part of the chassis, without having to change the chassis if you want to service the battery.”
Harnessing design tools
An important element in bringing the Uniti to fruition will be technical partnerships it has formed with Siemens and industrial robot specialist Kuka. Uniti is working closely with Siemens’ software arm to ensure the process of moving the car from an L7 to an M1 vehicle is as seamless as possible. “We are using NX [Siemens’ PLM software] and, importantly, Amesim,” says Horne.
Amesim is a fully scalable simulation suite that allows for rapid analysis of mechanical and electronic systems. “That allows us to overlay new CAD over old CAD and put it straight through an M1 sim,” explains Horne.
“I think most people have worked with some Siemens packages and sometimes had problems. But when you tie all the packages together it is amazing what you can do.
“You can produce a crash simulation in a very short time, or even bring in a material data sheet from a supplier – for a particular carbon fibre material, say – then put that information into the materials database, and then immediately apply that to your simulations and see the effect.”
It is noteworthy that Uniti will be the first car company to use only Siemens products for its entire design and engineering process, through to the digital twinning of its manufacturing facilities.
“We will have a digital twin of the entire manufacturing element, even down to working with our robotics supplier,” Horne says. “We can enter all the information [on aspects such as arm articulation] and it will give us things like collision zones during part fitting, tooling, all of that.”
The plan is to build a pilot production plant at Silverstone, where the prototype’s development is underway, and it is the production concept that has the potential to make Uniti stand out in the increasingly crowded EV market space. It will rely on a process known as matrix manufacturing (MM), which has been pioneered by Kuka.
Working with Kuka, Horne says, “The idea is that smart manufacturing and digital twinning will allow us to program our pilot plant. We can then replicate that pilot model anywhere in the world.
“What is the point in manufacturing all the cars in the UK or Sweden, then shipping them around the world? You’re trying to be carbon-neutral with your manufacturing, then you destroy that instantly. If you’ve proved that a market – be it Germany or anywhere else – can take 6000 cars a year, you can then have a factory built around that demand.”
In very simple terms, the principle of MM is that each factory is broken down into individual matrix units – effectively a cell of robots – and that each one can be used to build an entire car or just a part of it.
“That means that when we do our first pre-production cars, we will only need one or two matrices, and they will do the whole job,” says Horne. “That will allow us to fine tune the robot heads to get the takt time down [the average time from the start of one unit’s production to the next].
“The idea is to get to the point where, as you grow, you can just bolt on matrices. You might have a plant somewhere remote that needs only four matrices, because those four can do anything you need of them.”
The use of the matrix production cycle influences the design of the factory floor, regardless of whether one matrix or multiple ones are used. There is a main production floor, where the individual matrices are located, a warehousing area, a tool store and an AGVs (autonomous guided vehicles) pool. The warehousing element is where components are stored; they are collected by an AGV and taken to the required matrix.
“The AGVs deliver the parts to line, but they are quite clever and can identify if there is an issue in one matrix, then divert to another,” explains Horne.
The system also allows the tooling heads of the robots to be automatically changed, hence the tool store. When a robot is required to move on to a new process, an AGV arrives to collect the now unneeded tooling, and another delivers a new tool.
That in turn allows multiple production processes to take place in the same matrix, or for a matrix to be rapidly retooled for a new process, such as switching to the construction of a different variant of vehicle.
All of this can be achieved without having to physically alter, or halt, production on a line. Also, if a fault develops in a matrix, its task can quickly be transferred to another, for minimal disruption.
The entire process hinges on the complete digital integration of the production process. “Uniti has a plan for a whole suite of cars, so to be able to make every type we could want, all at one plant, that is massively useful,” Horne says.
“All the data, on parts, the factory floor layout and so on, is in the Simcenter [part of the Siemens suite],” he says. “So if for example you want to run a new door design, you can run it through the Simcenter, check it will fit, match the robots to the job, and so on. At the moment, Kuka is working with Siemens to import all its data into the Siemens system.”
If everything goes to plan for Uniti, it could well be the instigator of a step change in the way vehicles are manufactured, marking a move away from inflexible production lines that take huge effort and investment to modify.
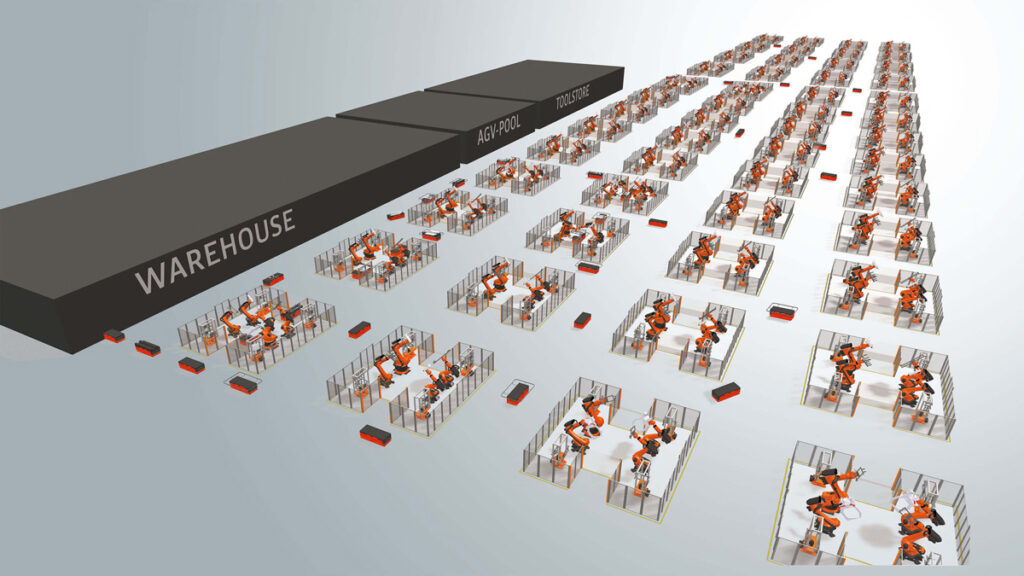
(Courtesy of Kuka Robotics)
It is still early days for the Uniti project, but if its tight timescales are realised, the first production-ready vehicles should start to appear next year. However, as Horne highlights, the focus of the engineering team extends beyond the initial launch. “We have to make sure the technology we are putting in the vehicle is current, not just for the year we go to market but for the future,” he says.
Only time will tell if the project can realise its potential, but Uniti’s disruptive approach is certainly an interesting insight into how vehicle manufacture needs to evolve to match ever-shifting demands.
Uniti One
Vehicle type: 1+1 M1 light passenger vehicle
Chassis: thermoplastic composite monocoque
Motor: two x synchronous reluctance
Motor cooling: liquid
Output: 120 kW
Inverter: silicon IGBT
Inverter cooling: liquid
Battery packs: lithium-ion, 18650 cells
Pack weight: 400-500 kg
Battery cooling: liquid
Weight: 900 kg
Speed: 85 kph cruise, 135 kph max
ONLINE PARTNERS
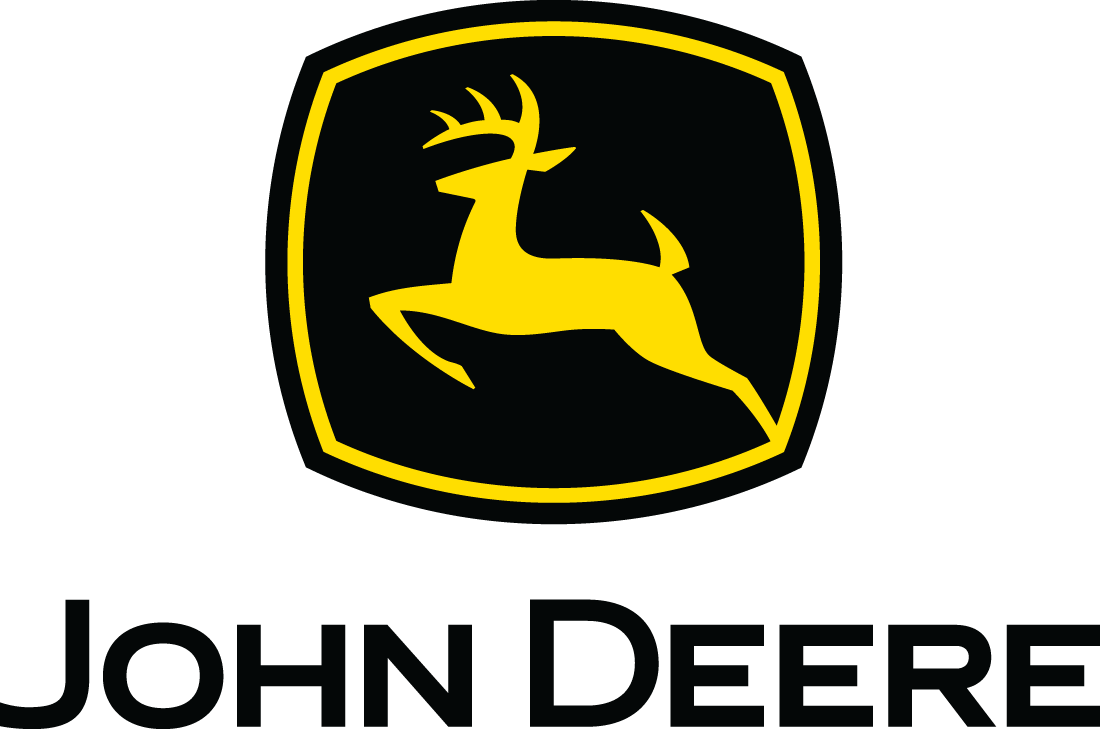
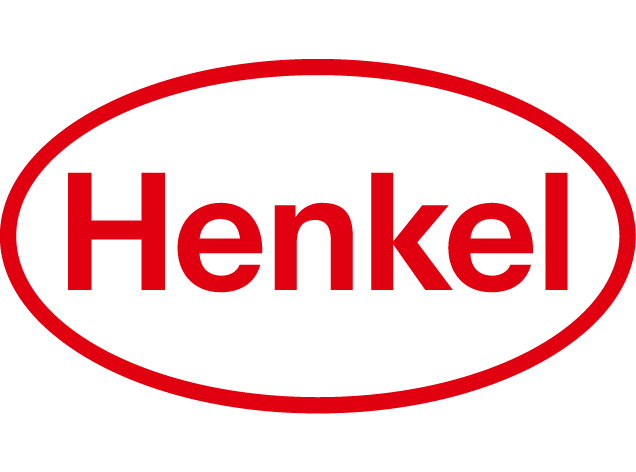
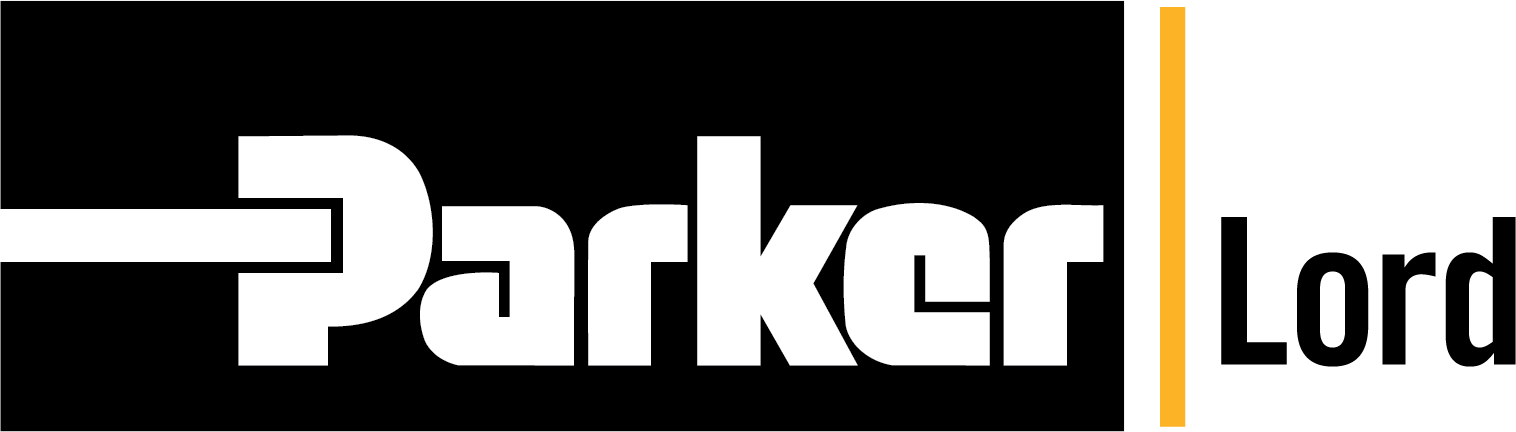
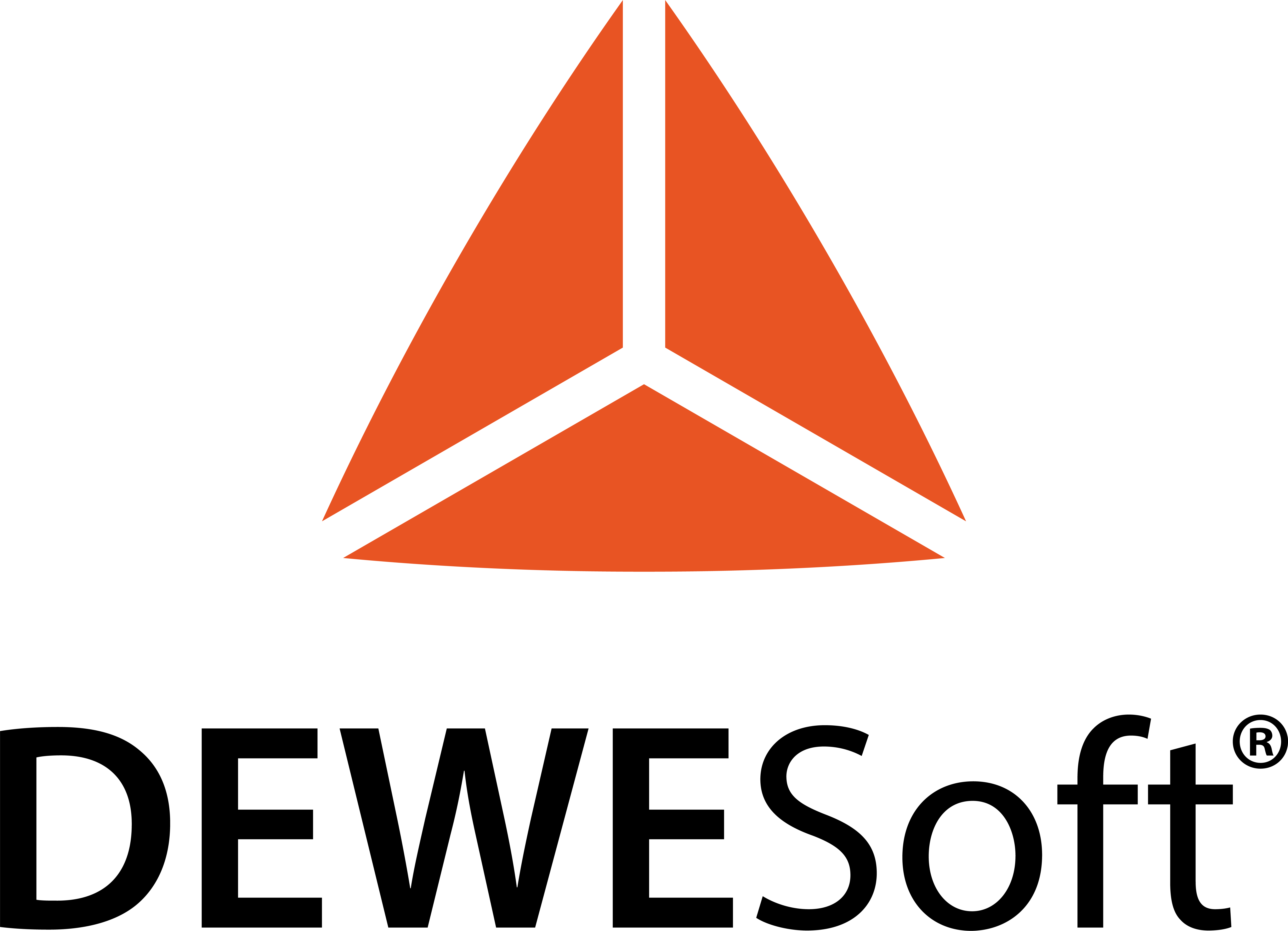
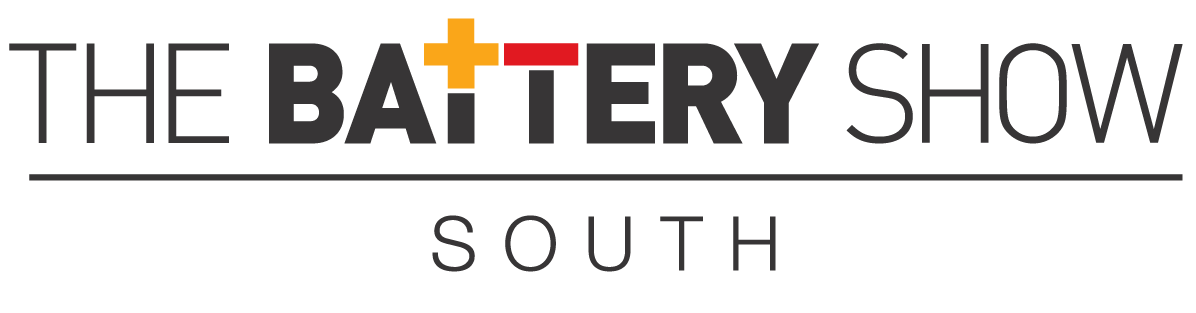
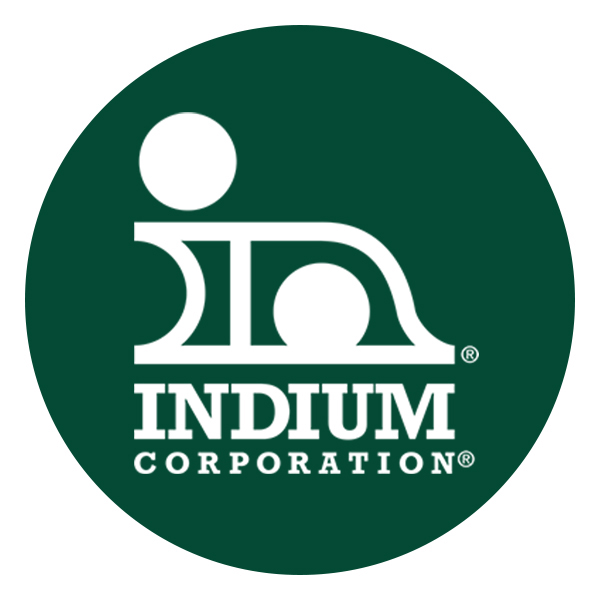

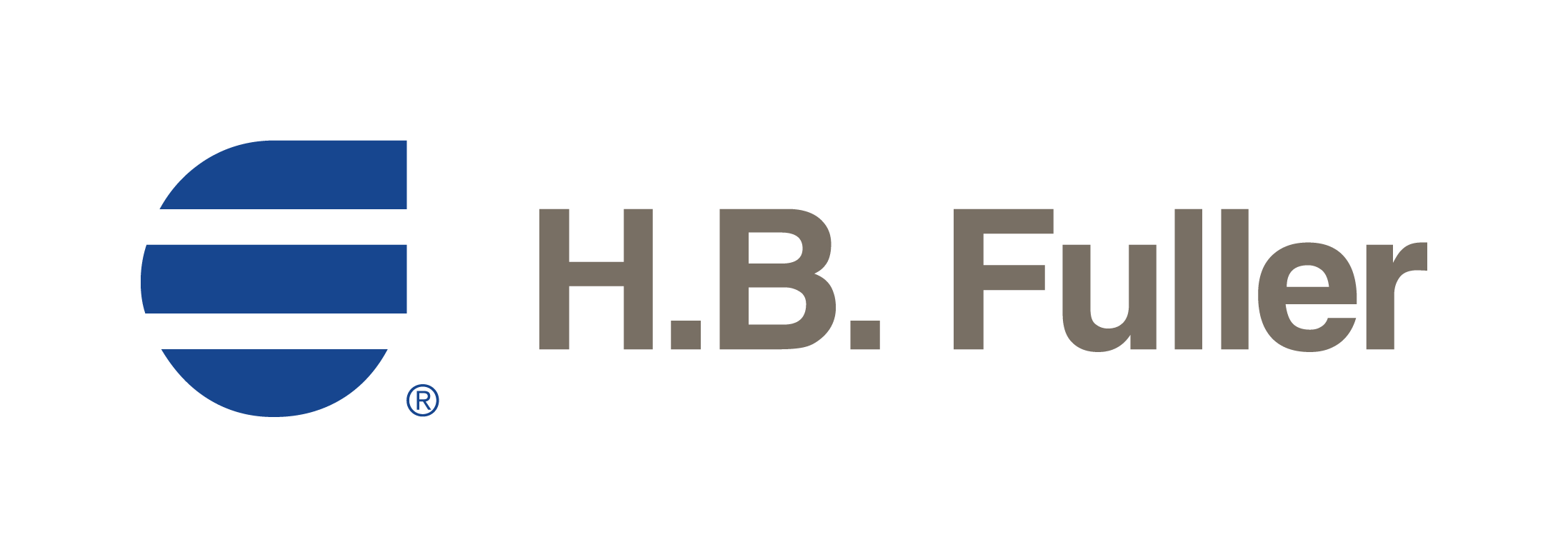
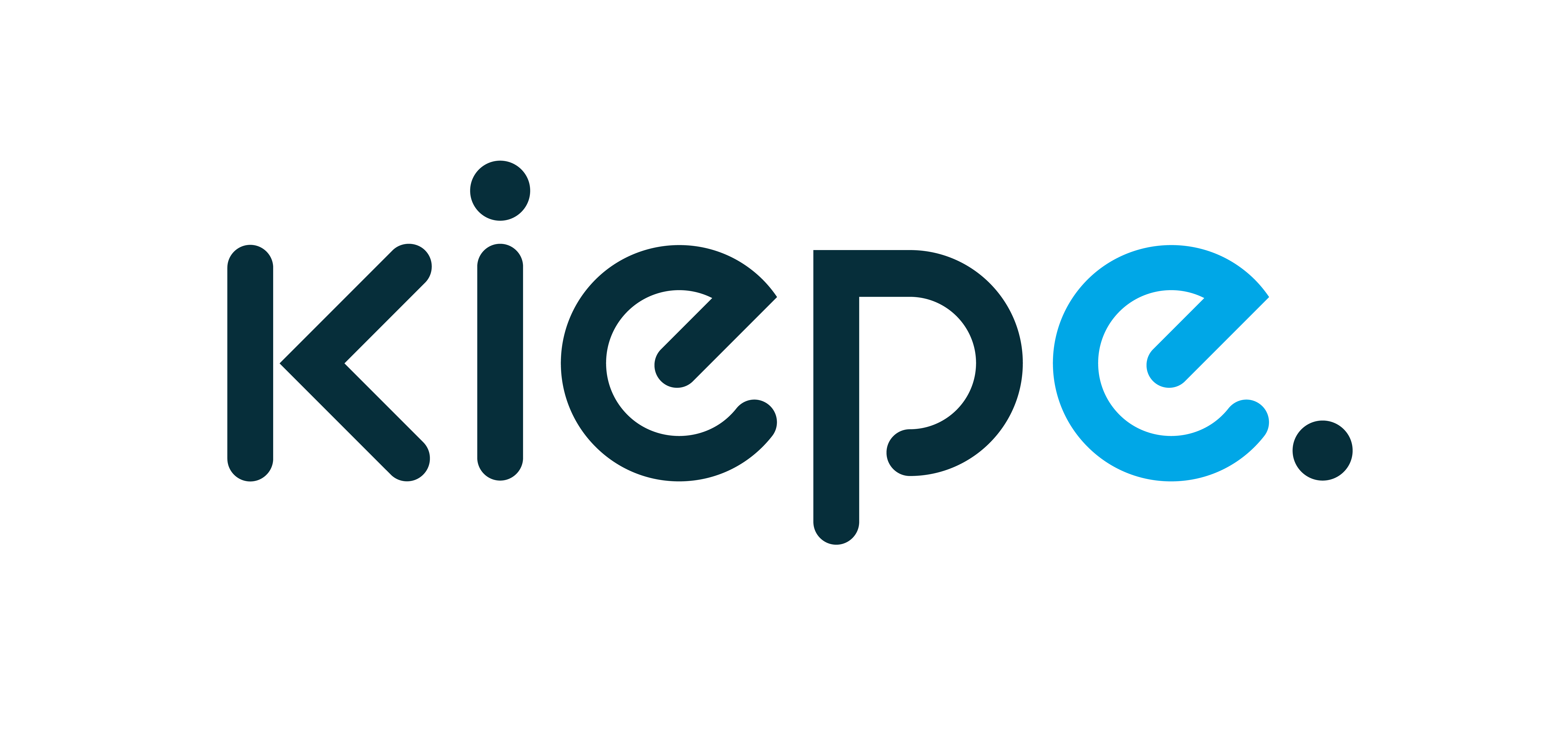
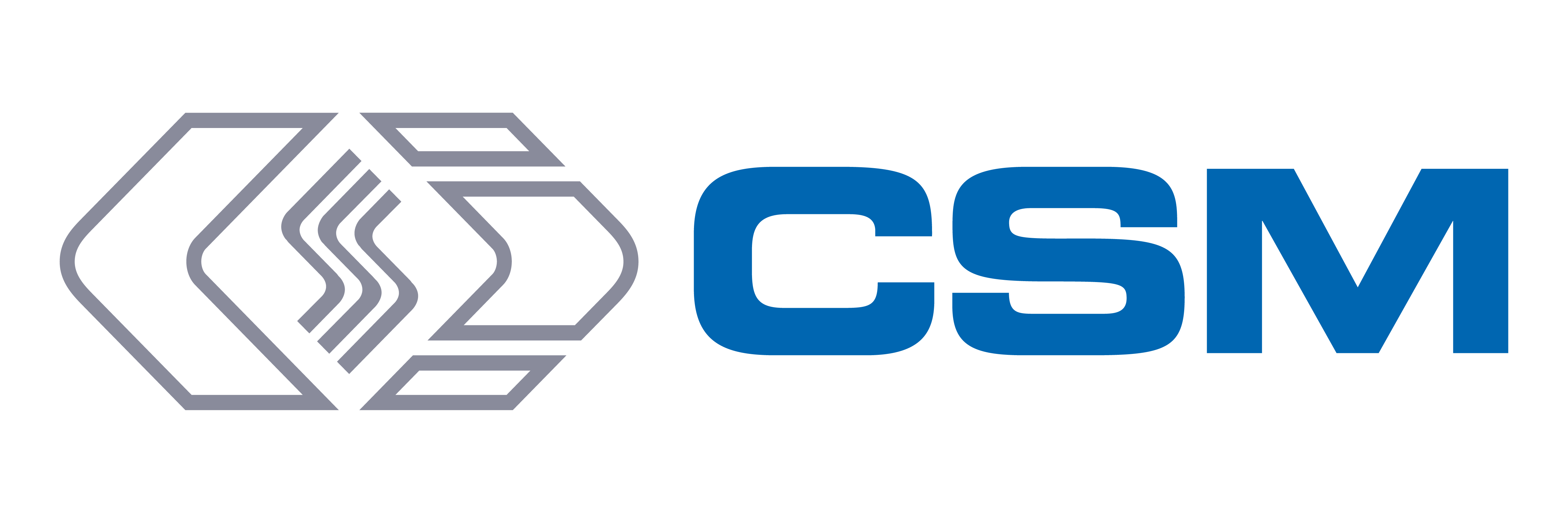