Sealing
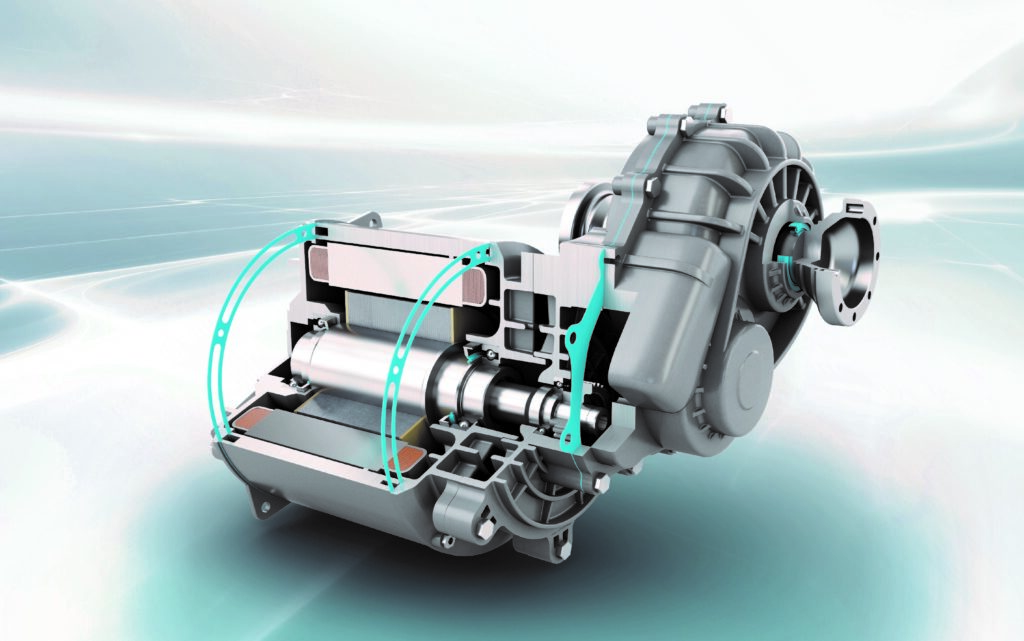
(Courtesy of Trelleborg)
No entry or exit
Seals and sealants perform a host of unsung but vital functions. Peter Donaldson explains the different types, their uses and the materials they are made from
Unglamorous they may be, but seals and sealant materials nonetheless play an essential role in all modern vehicles, keeping contaminants out and fluids in, and are used in the vast majority of systems and components. The engineered polymer compounds of which seals are made must resist heat, vibration, dust, fluid and chemical attack for years and tens of thousands of miles, while being easy to apply during manufacture and complying with health & safety and environmental regulations.
The most prominent application in EVs is sealing a battery pack housing, followed by gasketing for power conversion electronics such as inverters, along with motors and other components of an electric drivetrain. All the high-voltage connectors must be sealed, as must the main battery box, module and cell enclosures, plus the lines and connectors in fuel cell systems, electrically driven accessories, the thermal management system serving the battery, motors and charging system.
Thermal management systems often feature complex multi-way valves, while conductive cooling matrices must be sealed and cooling plates bonded to cells with materials that also conduct heat efficiently. Safety-related systems that often feature hydraulics, such as brakes and ride control systems, also require sealing and often usually include pumps that generate significant amounts of pressure that pose a challenge to the seals.
Rapid rotary seals
Electric motors in EV applications spin faster than in IC engines, so rotary seals have to cope with higher surface speeds. Most IC engines rev to no more than 7000 rpm, although some sportscars rev faster and many bikes reach 15,000 rpm or more. By contrast, an EV motor spinning at 15,000 rpm would be at the low end of its range, with 20,000 rpm being typical and 30,000 rpm not unheard of.
As surface speed is derived from rpm and shaft diameter, the resulting speeds can be high. To give an extreme example, a 30 mm shaft spinning at 30,000 rpm produces a surface speed of a little over 47 m/s, or nearly 170 kph.
While seals in IC engines tend to be generously lubricated by engine oil, those in electric motor applications get very little lubrication, often running either a fine oil mist or in a dry environment. What’s more, the need to maximise range in road-going EVs results in efforts to keep friction to a minimum.
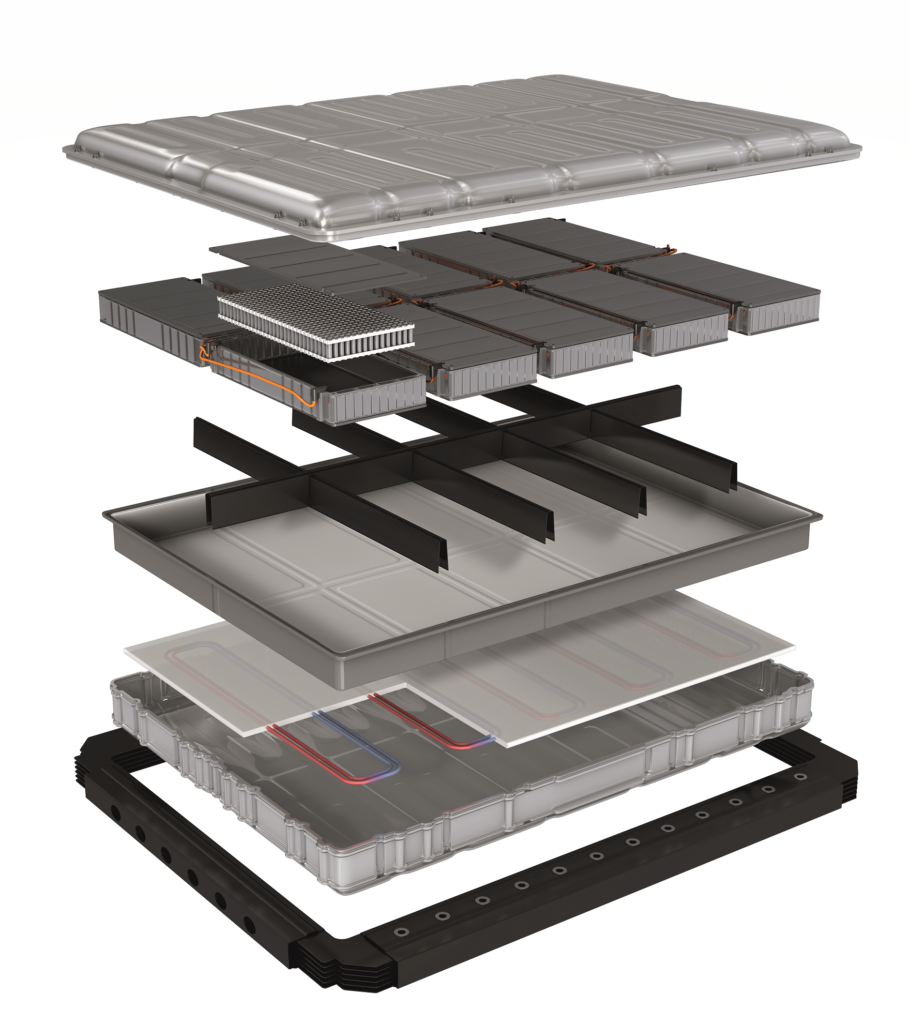
(Courtesy of Henkel)
The combination of high surface speeds, poor lubrication and the need for minimum friction makes sealing a challenge. In an extreme case like the one above, PTFE would be an appropriate material choice, as it offers good heat resistance and low friction, even if it is relatively expensive.
In EVs, electrical conductivity and flame resistance are, depending on the exact application, either new requirements for sealants or are more important than they were in IC-engined vehicles. Flame resistance is important to mitigate the consequences of battery thermal runaway. Conductivity is important because static electric charges can build up between the rotating and static elements of rotary seals, so a supplementary lip made of a conductive material can be added to earth the charge continuously to prevent sparking from high-voltage discharges.
Further, internally generated currents in induction motors that pass through bearings can damage them, and such currents can also be a source of EMI, so shielding for radial shaft seals is a requirement for EVs. Solutions include the use of electrically conductive non-woven components, sometimes in combination with low-friction materials or even gas-lubricated mechanical seals, a specialist sealing company points out.
Batteries are also becoming larger, which can make it difficult to access their internals for repairs such as replacing modules or even individual cells, and their chemistries can create conditions in which corrosion becomes a problem.
Skateboard challenge
The rise of purpose-designed EVs as opposed to those derived from IC-engined vehicles has led to a growing adoption of the ‘skateboard’ format. This format is usually associated with a long, broad and shallow battery mounted under the floor that takes up much of the available space there, and vertical space under the floor is very limited, and lightweight construction. All these factors present sealing challenges.
Large, lightweight battery housings are prone to much greater mechanical movement than the comparatively rigid ones of earlier EVs, and that creates gaps that must be kept sealed. Parking a car with one wheel up on a kerb can generate a twisting force that opens a static gap, while forces acting while the vehicle is in motion can open and close gaps dynamically.
Using materials with different coefficients of thermal expansion (CTE) can also create gaps as internal and ambient temperatures change. Any gaps between the housing and the cover are critical, so seals must be able to cope with that movement without allowing contaminants to enter.
Sealing battery modules and packs is therefore a critical design consideration. Joints inside a pack can be complicated and require a variety of sealing properties, including resistance to electrolytes in the cells and chemicals in water-based coolants as well as the new dielectric fluids used in immersive cooling systems.
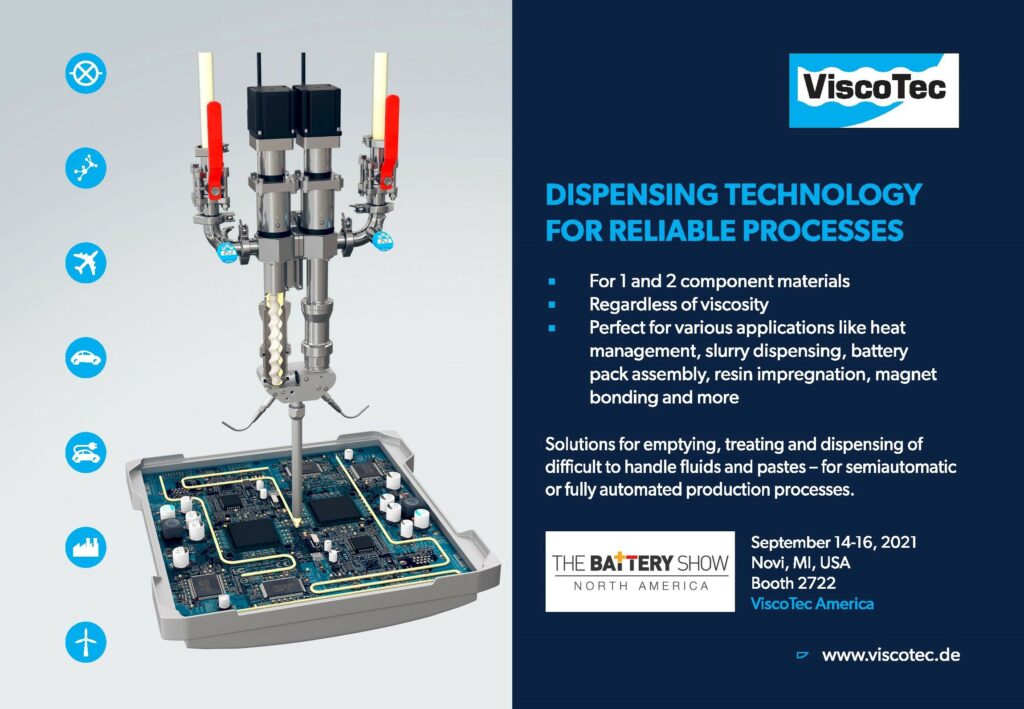
Sealants must also withstand a range of temperatures from -40 C up to those associated with catastrophic pack failures, as well as meeting UL94-V0 flammability requirements. They must also exhibit a combination of mechanical properties including strength, elongation and cohesive robustness under tensile loads.
Further challenges are presented by substrates with which it is inherently difficult to form adhesive bonds. For example, non-polar materials have low surface energy, which is a measure of how attracted a material’s molecules are to each other and to other materials’ molecules.
Materials such as polypropylene, polyethylene, polystyrene and ethylene vinyl acetate are all low surface energy materials. Their opposites are polar substrates, materials with high surface energies such as most common structural metals along with plastics such as polyethylene terephthalate, polycarbonate, polyvinyl chloride and acrylonitrile butadiene styrene, and forming adhesive bonds with those is relatively easy. The challenge lies in forming impermeable and structurally strong bonds between materials in these two different categories.
EV electronic components must be protected from environmental stresses such as temperature fluctuations, vibration and the ingress of dirt and liquids, as must sensors such as cameras and radars. This is generally achieved by gluing down the lids of housings or by full potting of the components, in which they are fully embedded in the sealant, which cures around them.
With EVs encompassing battery electric, hybrid and fuel cell vehicles, there are broad similarities in fundamental sealing requirements as well as a few differences.
In one respect – the need to handle high pressures over a wide temperature range – the demands that battery EVs place on sealants are not as severe as those imposed by IC-engined vehicles. The extreme case is diesel engine fuel injection systems, which commonly operate at pressures in excess of 2000-2500 bar in road vehicles, with 3000 bar encountered in race engines. While EVs and IC-engined vehicles alike must work reliably through a Siberian winter or a Death Valley summer, nothing in a battery EV has to handle such pressures.
Obviously, the needs of the electric powertrains are common to all, and hybrids have both engines and battery packs to seal, but fuel cell systems present unique challenges connected with hydrogen storage and supply. The fuel cell stack itself, along with the valves, connectors and lines, are very difficult to seal against the leakage of hydrogen gas stored at high pressure – typically 700 bar – and the wide range of temperatures encountered in fuel cell systems.
Such pressures put large stresses on seals from the moment the hydrogen filling nozzle is put into a hybrid EV’s filler neck. Because hydrogen is the smallest of all molecules, permeation past seals is difficult to prevent, and demands some special materials, designs and coatings.
Further, the hydrogen heats up as the pressure in the tank increases during filling. The 700 bar pressure in the tank must therefore be reduced to 7 bar before it can be fed to the fuel cell, and the gas must flow through a pressure regulating valve to achieve that in a controlled manner. This tenfold pressure drop causes a commensurate temperature drop, so the seals must retain the gas over a very wide temperature range.
Within the fuel cell itself, the most important components in this context are the stack seals, which are those that separate the individual cells that comprise the stack. These must compensate for manufacturing tolerances to ensure that hydrogen permeation remains ultra-low and that there is no release of components that could poison the catalysts. In fuel cells, sealants play a vital role in preventing leakage of ions, for example.
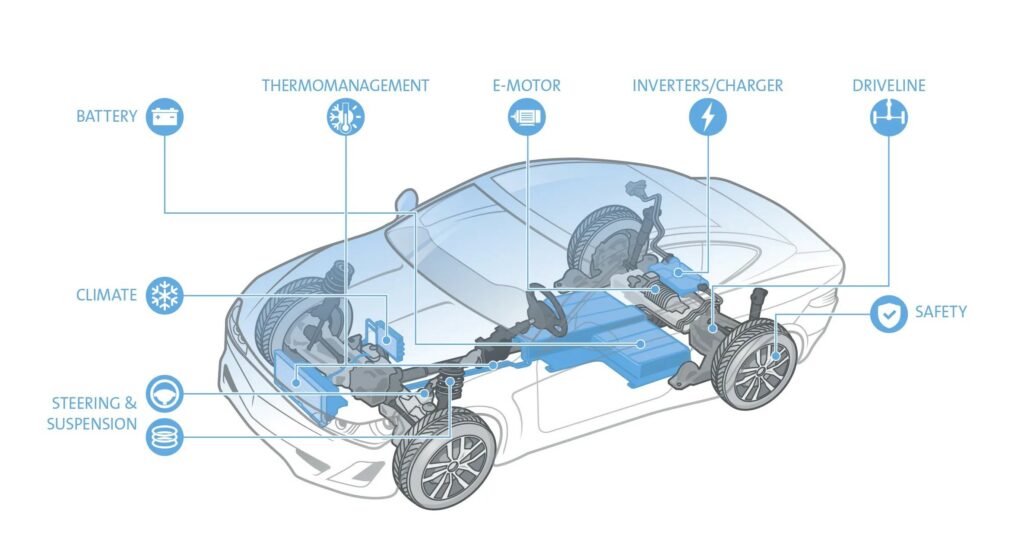
(Courtesy of Freudenberg Sealing Technologies)
Sealants or adhesives?
Sealants and adhesives are often discussed together, as they are often formulated from the same sets of materials and can have similar processing times. The main functional difference is that adhesives have to be stronger, particularly in semi-structural and structural applications, and are usually expected to form permanent bonds, while sealants generally have no structural role and are often intended to be removable to allow for disassembly for maintenance and repairs.
The materials used in the automotive industry have evolved significantly in recent years in response to more stringent requirements in a number of areas. In IC-engine applications, including hybrids, the need to withstand high temperatures has grown because of tightly packed engine bays and the widespread use of turbocharging. More robust requirements are also emerging for improved adhesion, resistance to aggressive lubricants and coolants, as are requirements for fast curing in assembly and for non-flammability.
Other key factors include increased vehicle and component durability, faster processing and design freedom, along with weight reduction, safety, sustainability and legislator compliance. There is also an ongoing reduction in the use of hazardous chemicals such as iscocyanates and others regarded as substances of very high concern (SHVCs). Industry also wants sealants that cure at lower temperatures and bond better to unprimed or untreated substrates as well as various chemical pre-treatments and finishes such as anodised or painted substrates.
Sealants and adhesives now span a broad range of technologies including water-based, hot melt, reactive hot melt (RHM) and solvent-based formulations. Polyurethanes are among the most important compounds used, in one- and two-component form as well as RHM to create, for example, semi-structural and structural adhesives, and elastomeric sealants.
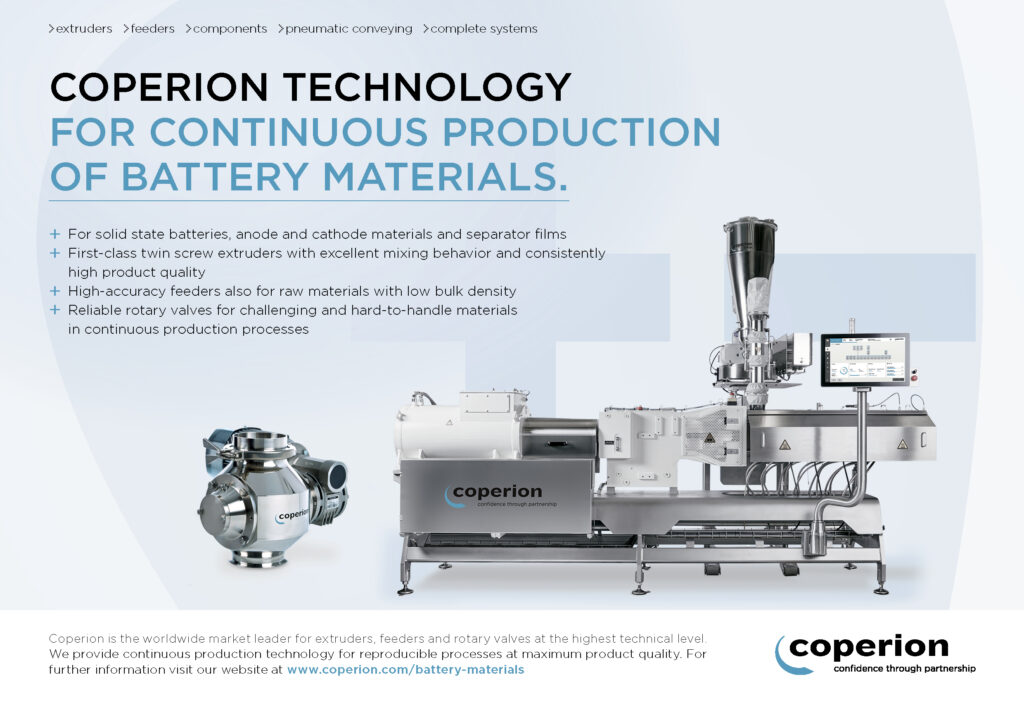
Other materials include butyls and block co-polymers, silane-terminated polymers, polyacrylates, two-component methyl methacrylate, epoxies and silicones.
Elastomeric applications
A typical EV application for an elastomeric sealant would be the joint between the motor and gearbox in an e-axle or similar transmission system.
For sealing cooling systems that use a water-glycol mix, an elastomer called ethylene propylene diene monomer is widely used, favoured over thermoplastic elastomer alternatives because of this application’s high requirements for tolerance compensation. For seals that come into contact with high-voltage cables, the materials of choice are silicone rubbers, owing to their high electrical breakthrough strength.
EV manufacturers are adopting technologies that are new or come from other industries. Examples include immersion cooling systems that use dielectric coolants that are still under development for automotive applications, and heat-shielding practices and materials transferred from aerospace. In general, EVs are developing in a fast and agile manner, and material development has to keep up.
While the core function of a sealant is to keep vital fluids in and contaminants out – and its resistance to assaults from heat, pressure, vibration and aggressive chemicals is essential to that – they also have other characteristics that can make them multifunctional.
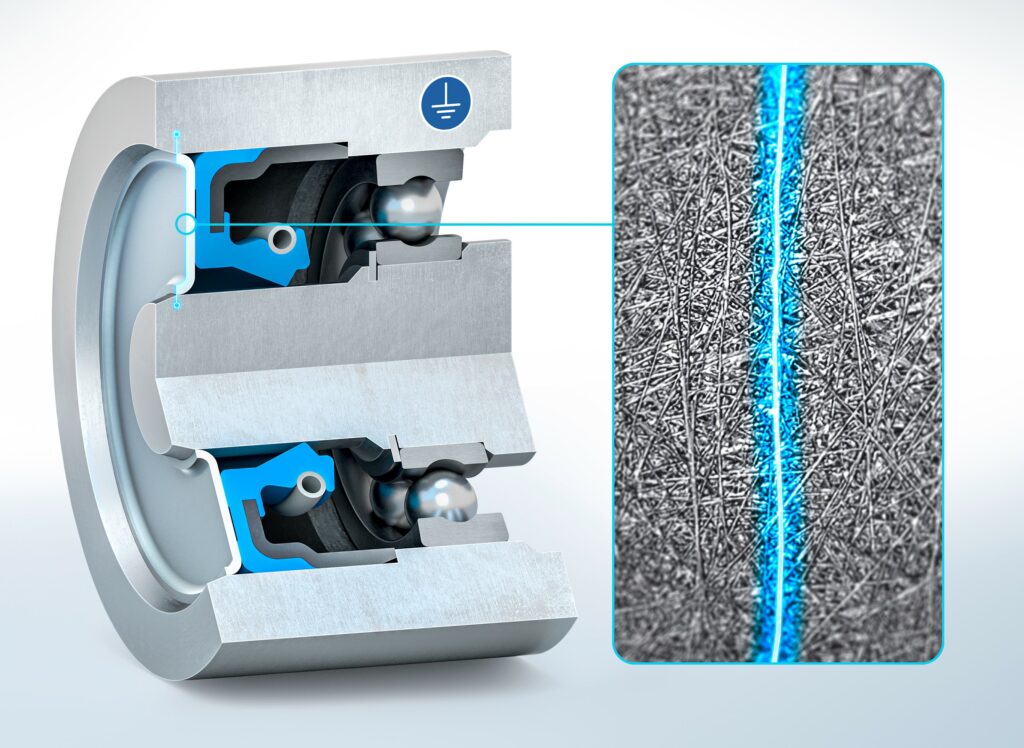
(Courtesy of Freudenberg Sealing Technologies)
In EV batteries, for example, many of the sealants and adhesives contribute in more than one way to their overall performance. Thermal and electrical conductivity/insulation properties can be very important, as can the flexibility to allow for differences in the CTE among the materials that make up the battery system. Noise reduction and vibration damping properties can also be very important.
If the inherent properties of the material don’t meet the full multifunction requirements of a particular part, one solution can be to bond or mould the sealant to another material. For example, a soft rubber lip can be moulded into the rim of a stiff plastic connector or sensor housing to produce a component with two, three or four functions.
In coolant systems, for example, a temperature sensor receptacle can be moulded into a short connecting piece of pipework that acts as a carrier, along with a damping element and a sealing bead. Such components can be made of materials that stand up to almost all media, can compensate for dynamic misalignment in the application and can accept low-friction coatings for reducing the force required for assembly.
Weight reduction
This kind of approach can also reduce the number of parts and the weight of the vehicle. However, the big weight savings associated with the use of adhesives and sealants results from the flexibility it allows manufacturers in using advanced materials with high strength- and stiffness-to-weight ratios, while forming bonds that are more resistant to fatigue, contaminants and corrosion than conventional fasteners. As well as established materials such as aluminium alloys, plastics and composites, these include exotics such as materials incorporating foams or micro-balloons.
New lightweight materials including plastics, composites and a variety of metals are also finding their way into battery structures. This mix of dissimilar materials in close contact can promote corrosion, which adhesives and sealants can help prevent by creating an insulating barrier between them.
Some applications on lightweight designs can be a severe test for sealing technologies, owing to a combination of the small cross-sections of the flanges to be joined and micro-movements. Anticipated requirements for foam gasketing to enable further weight reduction also promise to be challenging.
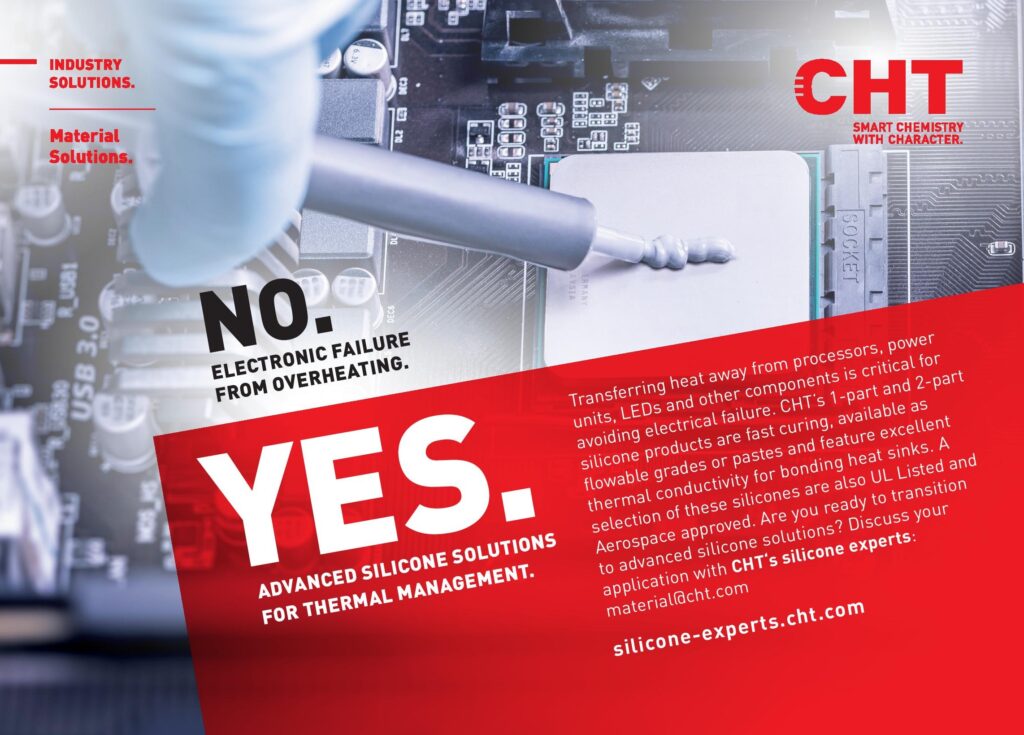
While weight reduction is high on the agenda for EVs, the use of regenerative braking makes additional weight less critical than it is for pure IC-engined vehicles, because the kinetic energy can be re-used. In this respect, the seals themselves contribute very little to the overall weight of the car, so weight reductions in the seals themselves probably have more marketing than technical value.
The exception here are thermal interface materials in batteries, which are used in large amounts – sometimes 10 kg per car – and are expensive. In energy-saving terms, however, it is more important to reduce friction (in dynamic seals used in rotating components) than it is to reduce weight in the seals themselves.
Simulating seals
As in many industries, simulation is of growing importance in the design and manufacture of sealing components such as O-rings and gaskets. In design, simulation is used to identify the temperature and pressure ranges in which the seal would be vulnerable to failure in a particular application.
For example, with too little pressure between a gasket and the counter-surface against which it must seal, leaking can be expected. Programmed with a material model of the polymer from which the gasket is made, the simulation can show graphically and numerically how it reacts to increasing pressure that, by design, will change its shape and improve the sealing performance, right up to the point at which it starts to go wrong. With too much pressure, the gasket itself can start to be extruded through the tiny gaps it is supposed to seal, followed by the oil or coolant itself.
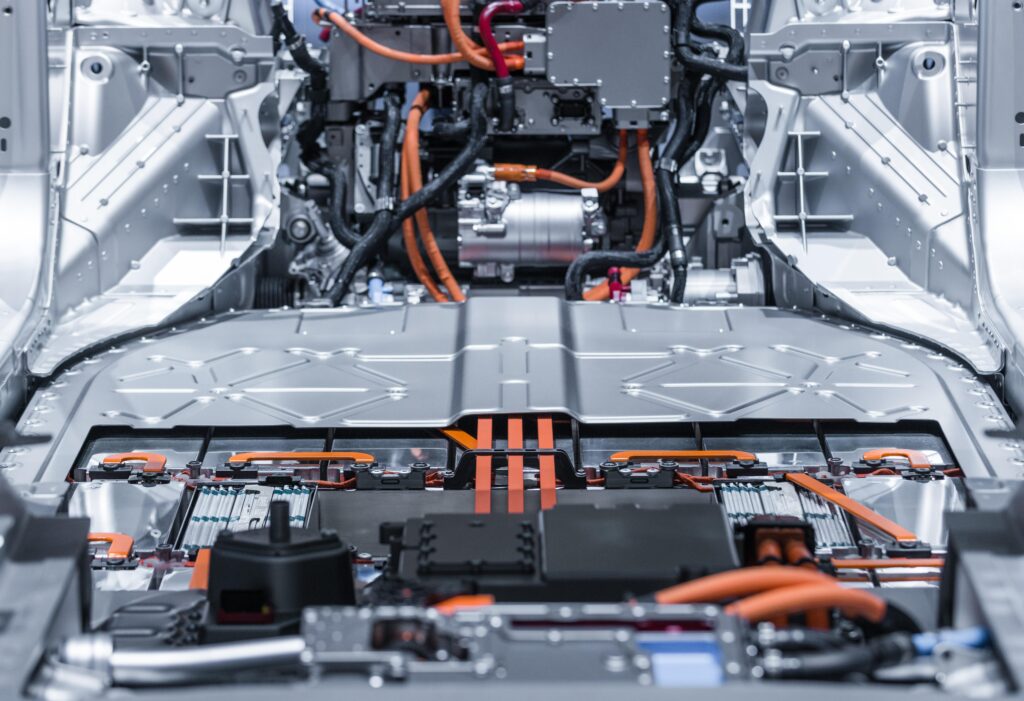
(Courtesy of HB Fuller)
Simulation is particularly important for vehicle and subsystem manufacturers when they are trying to find a seal material that will do the job at a low cost, allowing them to try out many materials virtually and very quickly. The same applies when weight savings are pursued through making subsystems and components smaller, as that means sealing surfaces also get smaller, so it is critical to ensure that a proper seal can be formed. If this is done early in the design process it can save a lot of time and money later.
In seal manufacture, how the material flows into a mould, how quickly and completely the mould fills, where the flows of material meet and the temperature at which all this happens are all simulated. This allows material parameters and design details to be refined and problems ironed out before committing to production.
The in-service performance of seals has to be balanced against their ease of manufacture, application and their cost, which is more of a challenge. The specifics of each application in terms of sealing performance and resistance to aggressive media drive different chemistries and cost levels, and define the space in which solutions can be optimised.
In battery manufacture, for example, the industry is rapidly improving its processes in terms of cycle time and cost, with a growing reliance on automating sealant and adhesive application in particular. As bead widths and thicknesses get smaller, it is critical to keep the relationship between them (known as the aspect ratio) stable during application, because key performance requirements such as chemical resistance, permeability and pressure resistance depend on the adhesive footprint.
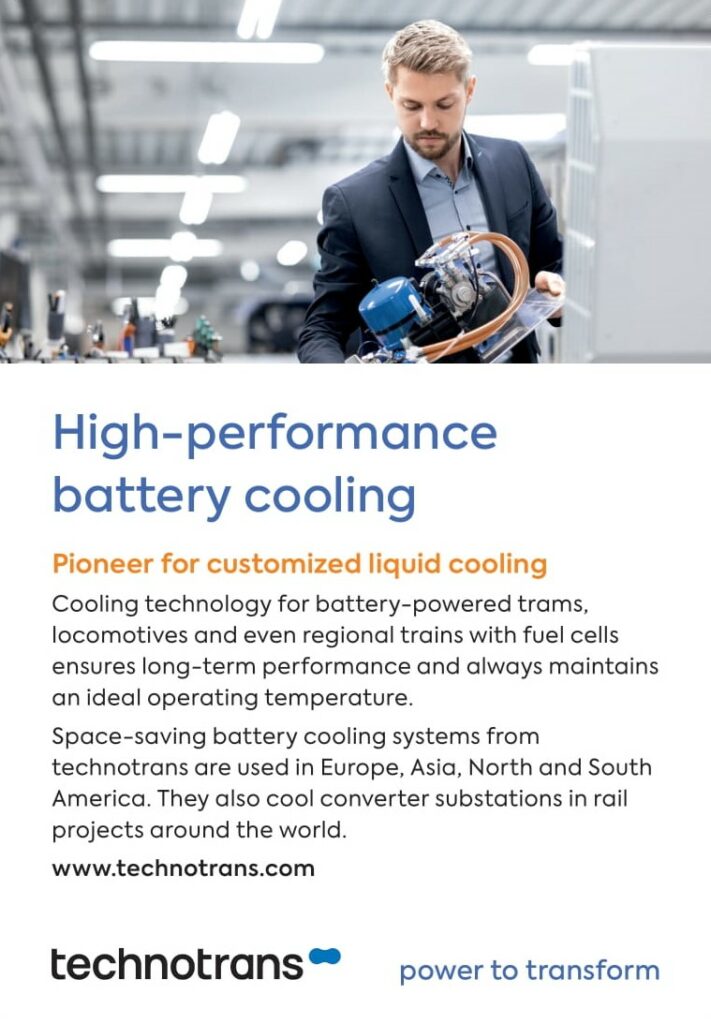
Also critical is the sealant’s ability to retain its heat resistance up to high temperatures without losing adhesion or its cured properties, while curing at lower temperatures. Lower curing temperatures make application easier and increase production rates, but they can affect cured properties.
Liquid application
In car plants these days, many sealants are applied in liquid form by robots during assembly. A sealing compound that is usually highly viscous and thixotropic (meaning that viscosity is reduced under mechanical stress over time) is applied to the components following a specified 2D or 3D contour. The flow characteristics of the liquid sealants and their inherent adhesion-promoting characteristics help to keep the cured bead in place and retain its dispensed profile and size.
Compared with traditional die-cut gaskets, wet-dispensed gasketing allows flexibility in component design and significantly reduces waste. There is often a wide variety among the designs and dimensions of mating surfaces, so many different die-cut gaskets have to be produced, meaning that the number of parts in inventories is large. Robotic dispensing cells can produce a broad range of sealing patterns with low defect rates though, thanks to automatic and precise positioning of the gaskets.
The two most widely used dispensing processes result in the cured in place gasket (CIPG) and the formed in place gasket (FIPG). In the CIPG process, liquid gaskets are applied to and cured on the housing before its lid is fitted, allowing the lid to be removed in service for repair or replacement of components. FIPG results in a connection that is not intended to be detached, as the sealant adheres to both the housing and the lid.
In liquid dispensing, the sealant has to be applied very precisely, with the flow rate perfectly matched with the robotic motion in order to avoid any inconsistencies that could lead to leaks or failures. Particular care must be taken over the knit, which is the point at which the stop point of the bead meets the start point. This level of accuracy relies on full process control and extensive monitoring.
The dispensing equipment used includes eccentric screw pumps driven by computer-controlled servo motors. Depending on the sealant material and application, either static or dynamic mixing of two-part sealants can be used. With static mixing, the base and the catalytic curing agent are mixed before dispensing, while in dynamic mixing the nozzles are designed to bring the two together as they are dispensed.
Dynamic mixing is preferred for applications in which mixing quality is crucial and material characteristics are challenging, such as when the ratio of base to catalyst is particularly large, when the pot life – the time for which the sealant is malleable after mixing – is short or there are significant differences in viscosity between the base and the catalyst. When these strictures don’t apply, simpler static mixing is sufficient.
One issue with current constant-speed dispensing machines is that their speed must be held to that at which rounded corners can be dispensed. Such corners are the bottleneck in current processes. To address this, the latest technology intelligently varies the dispensing speed to achieve the shortest possible cycle time compatible with the best resulting seal.
In an early adoption of more advanced dispensing, a large German Tier 1 company has teamed up with one of the sealant suppliers who helped with the research for this article to bond connectors for an engine control housing. The application of the sealant follows a contour of long, straight lines and tight curves.
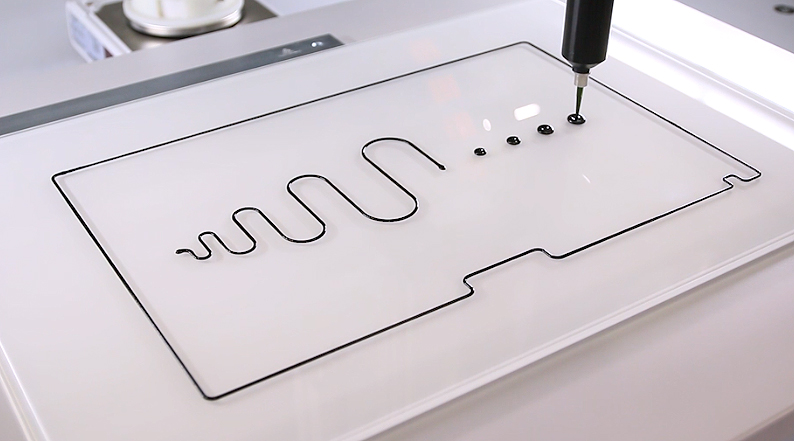
(Courtesy of bdtronic)
Using the company’s adaptive dispensing technology reportedly cut the cycle time from 44 seconds to 29. The system achieved that by optimally matching the speed at which the nozzle moved and the sealant output rate to the specified contour, applying a large quantity of single-component silicone in the shortest possible time on the straight lines, then slowing for the curves to dispense the material as precisely as possible. Where needed, large dots of silicone were applied at the highest possible dispensing speed.
Solid alternatives
However, there is also a trend towards solid seals to eliminate curing time after assembly to speed up future high-volume EV production. For example, a 7 m battery housing gasket applied as a liquid has to be done in a four-step process that involves cleaning the mating surfaces, applying a primer and then the liquid sealant and, finally, curing. By contrast, large-format solid gaskets can be fitted in one step by robots.
Any system that might have to be opened up during its service life for maintenance or repair clearly needs a seal that can be re-used, particularly if the system is large. For example, a large battery housing should not have a seal that has to be applied as a liquid, some argue.
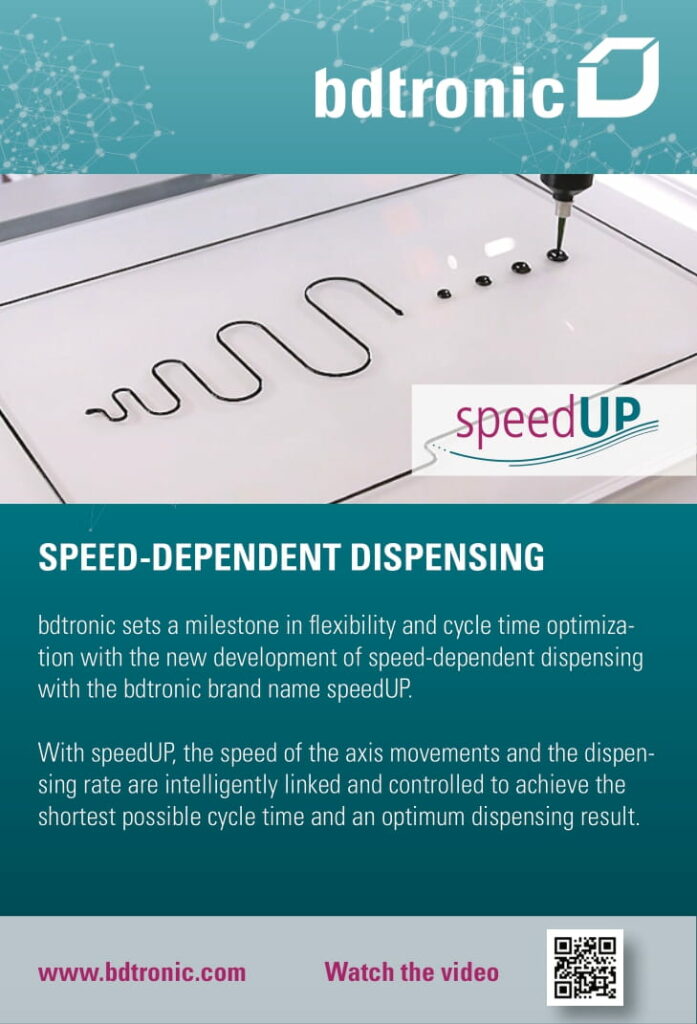
Advanced solid seal designs are now available that include elastomers to provide the flexibility for tolerance compensation and rapid response for dynamic sealing. They can also be formed with complex cross-sections incorporating features such as double lips for redundant sealing and hard inserts to act as force shunts to protect them from destructive mechanical overload.
When the space available for radial installation is limited, pre-formed ‘press-in-place’ seals are a good option, with the seal pressed into a defined groove in the battery housing. Carefully matching the gasket cross-section and groove allows for very space-efficient seals, including ones with double-lip designs achieved by giving the seal an X-shaped cross-section.
Elastomeric seals with metallic stoppers offer the advantages of tool-bound forming concepts, meaning that sets of features formed in the same part of a mould can be held to tighter tolerances relative to each other than if they were formed in different parts of the tool. This allows seals to be precisely matched to mating surfaces, the use of multi-lip designs and integrating fixing pins and metallic stoppers directly into the gasket.
As well as acting as force shunts, the metallic stoppers can also establish electrical contact between the battery housing and its cover, which helps meet the requirement of the electromagnetically compatible housing concept. Such seals allow the housing to be opened and re-sealed multiple times.
In a third concept, the solid gasket can be attached to the side of a circumferential metal carrier plate, forming a redundant seal. As well as providing end-stop/force shunt and EMC functionality, the circumferential carrier helps rapid and reliable installation.
According to one supplier who helped with the research for this article, this is the best technical solution for batteries with flat profiles found in skateboard EV platforms, although it has the disadvantage of needing large-format tools. A solution to this is the ‘de-foldable’ gasket concept, in which the rigid metal carrier plates alternate with flexible, unsupported elastomer segments, enabling manufacture and transport of the gasket in the folded condition, only being unfolded immediately before installation by the assembly robots.
Health & safety
Sealants and adhesives come under scrutiny for their impact on health & safety and on the environment, which is particularly important to the perception of EVs because a large part of their appeal to vehicle buyers comes from their environmental credentials. Sealant and adhesive developers are therefore under growing pressure to reduce their use of hazardous chemicals and SHVCs and to switch to alternatives that are also biodegradable and renewable.
Some of these requirements will be tricky to achieve while meeting other important requirements. For example, non-flammable materials must also be non-toxic.
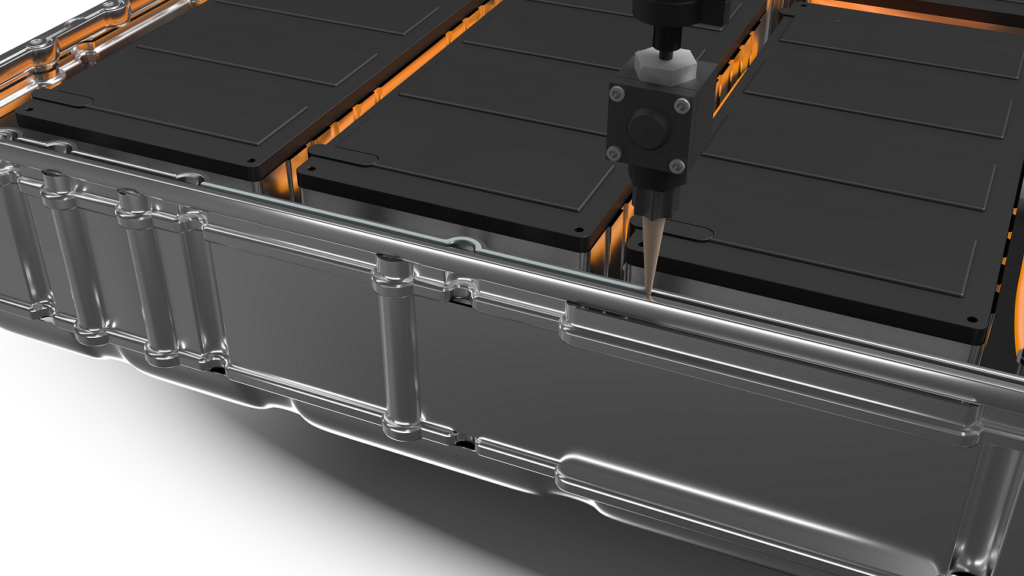
(Courtesy of Henkel)
When planning the next generation of solutions, the expectation is that the EV industry will have to understand the full life cycle, and that materials will have to be responsibly sourced to enhance energy efficiency and enable their re-use or recycling. The industry has also started to look at its CO2 footprint at the level of product categories and even individual products and, in support of vehicle OEM priorities, it is under pressure to be transparent about that throughout the supply chain.
Future directions
In the foreseeable future, EVs with more complex designs and greater use of reinforced polymers will challenge the sealing industry with further new requirements and greater stringency of existing ones. For example, some expect stronger demands for features such as temperature resistance, vibration resistance, repair friendliness and recyclability. These last two are expected to bring new requirements such as de-bonding and re-bonding on demand, for example, while more new requirements are expected to emerge from the desire for lightweight design.
Combined with the need to drive EV costs down, the pressure for further weight reductions will push the industry to refine the supply chain for highly specialised sealants and adhesives. Conventional bonding processes are reaching their limits, and those manufacturers that have begun to bond materials without welding, punching, folding or using mechanical fasteners have simplified and sped up their assembly processes and reduced their production costs. Ongoing r&d seeks to improve the bonding and sealing of composites, and find lighter metal alloys along with blends of plastics and natural fibres.
Sealants will be impacted most by new liquids to be sealed, particularly the dielectric oils and esters used in the emerging immersion cooling systems for batteries that, as yet, are still unfamiliar in the automotive industry. The growing importance of new requirements such as resistance to chemical permeation and fire will influence sealant formulas and seal designs, and the sealing materials are likely to become more specific to the materials, structures and mechanisms they must seal as well as the media whose leakage they must prevent.
Seals may usually be out of sight and out of mind, but they are always essential.
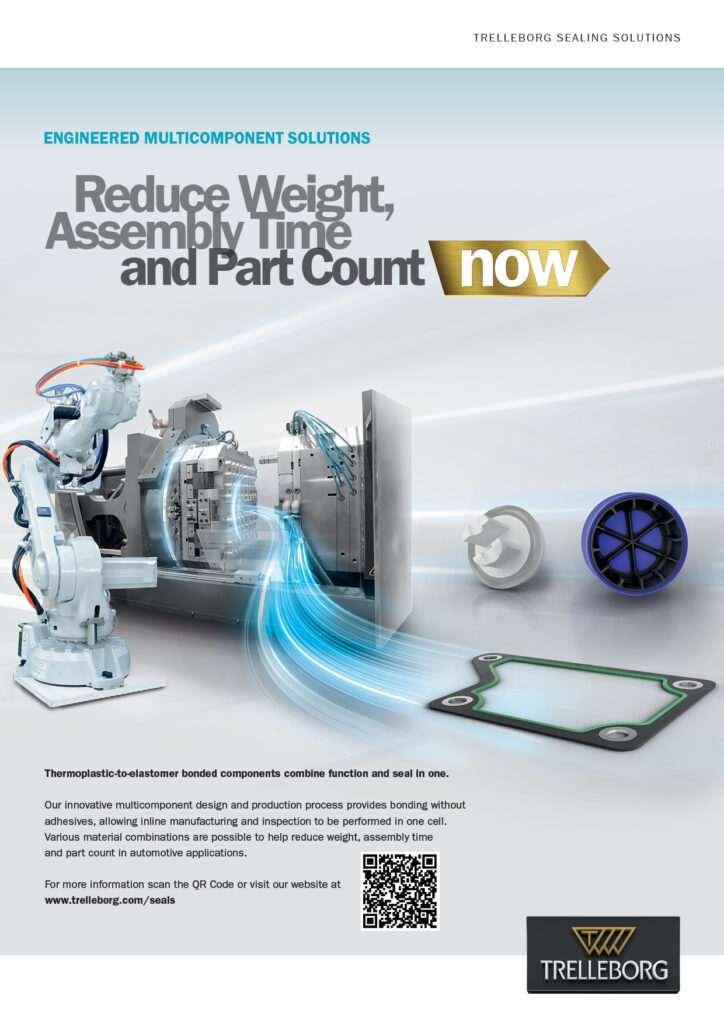
Acknowledgements
The author would like to thank Andy Jorissen at BDTronic, Peter Kritzer, Christian Favetto, Frederic Boyer and Marina Nussko at Freudenberg Sealing Technologies, Nathan Whitford and Christoph Muller at HB Fuller, Wolfgang Mayer and Rainer Kohlstrung at Henkel, and Axel Weiman at Trelleborg for their help with the research for this article.
ONLINE PARTNERS
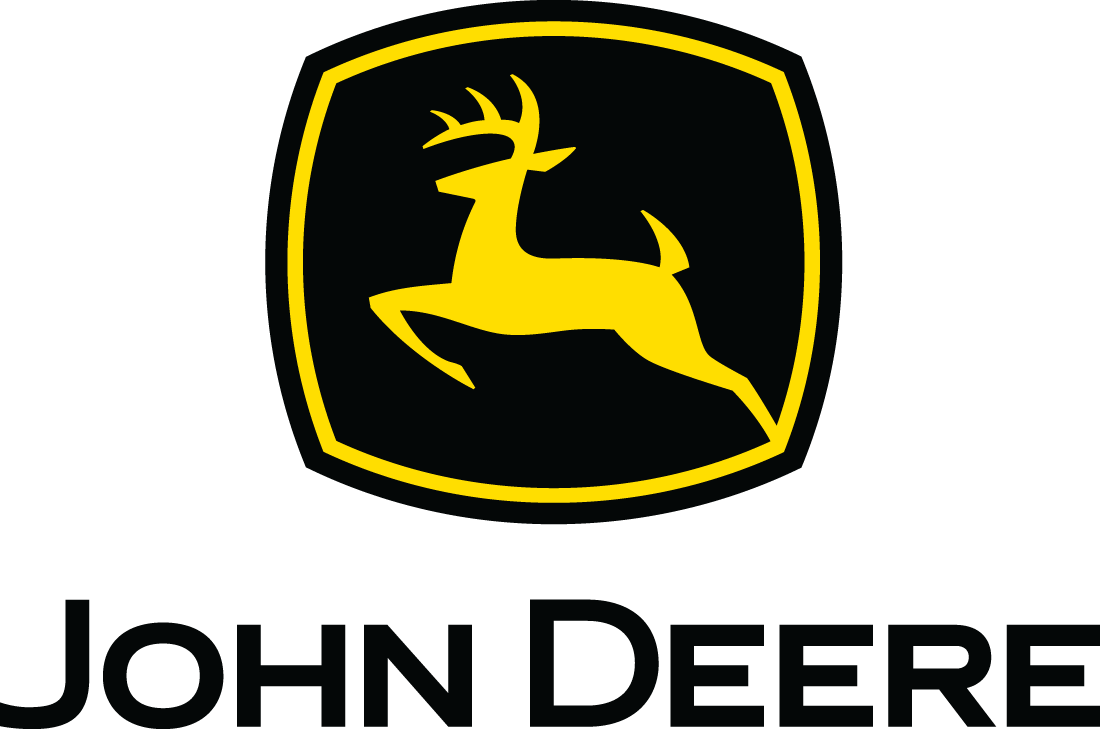
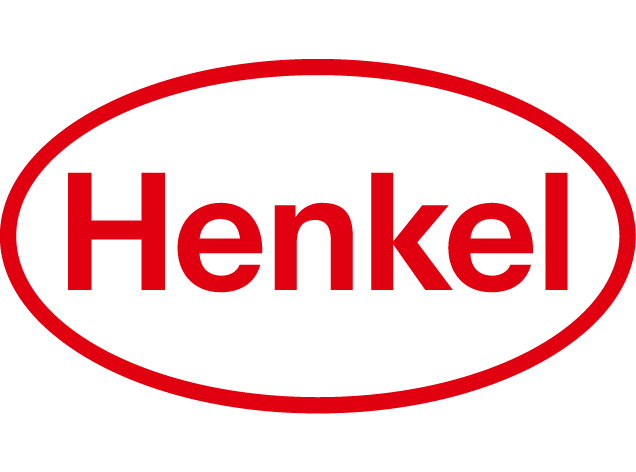
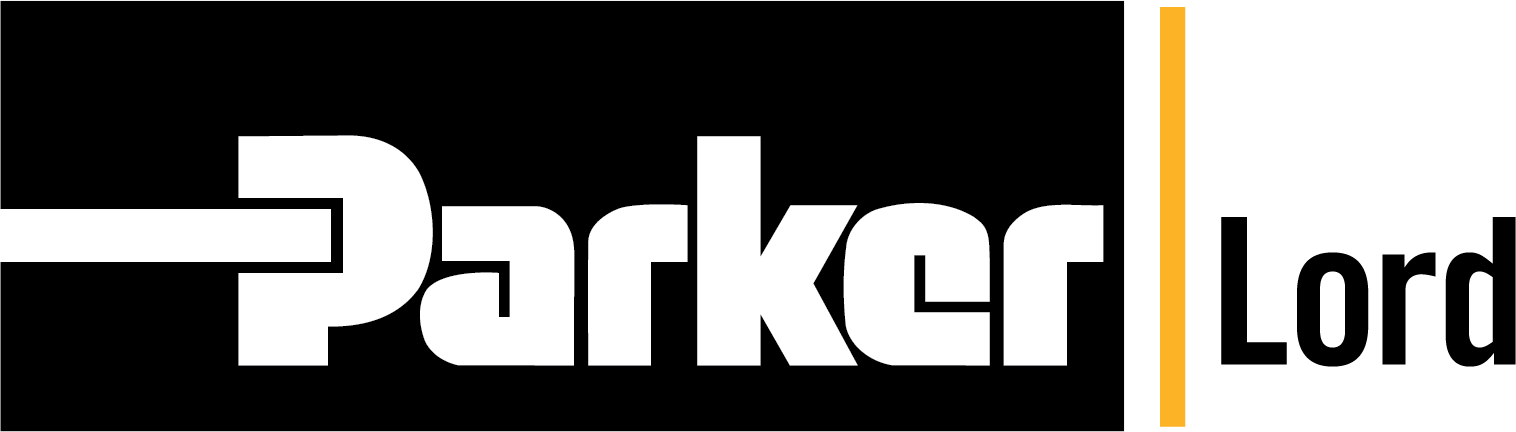
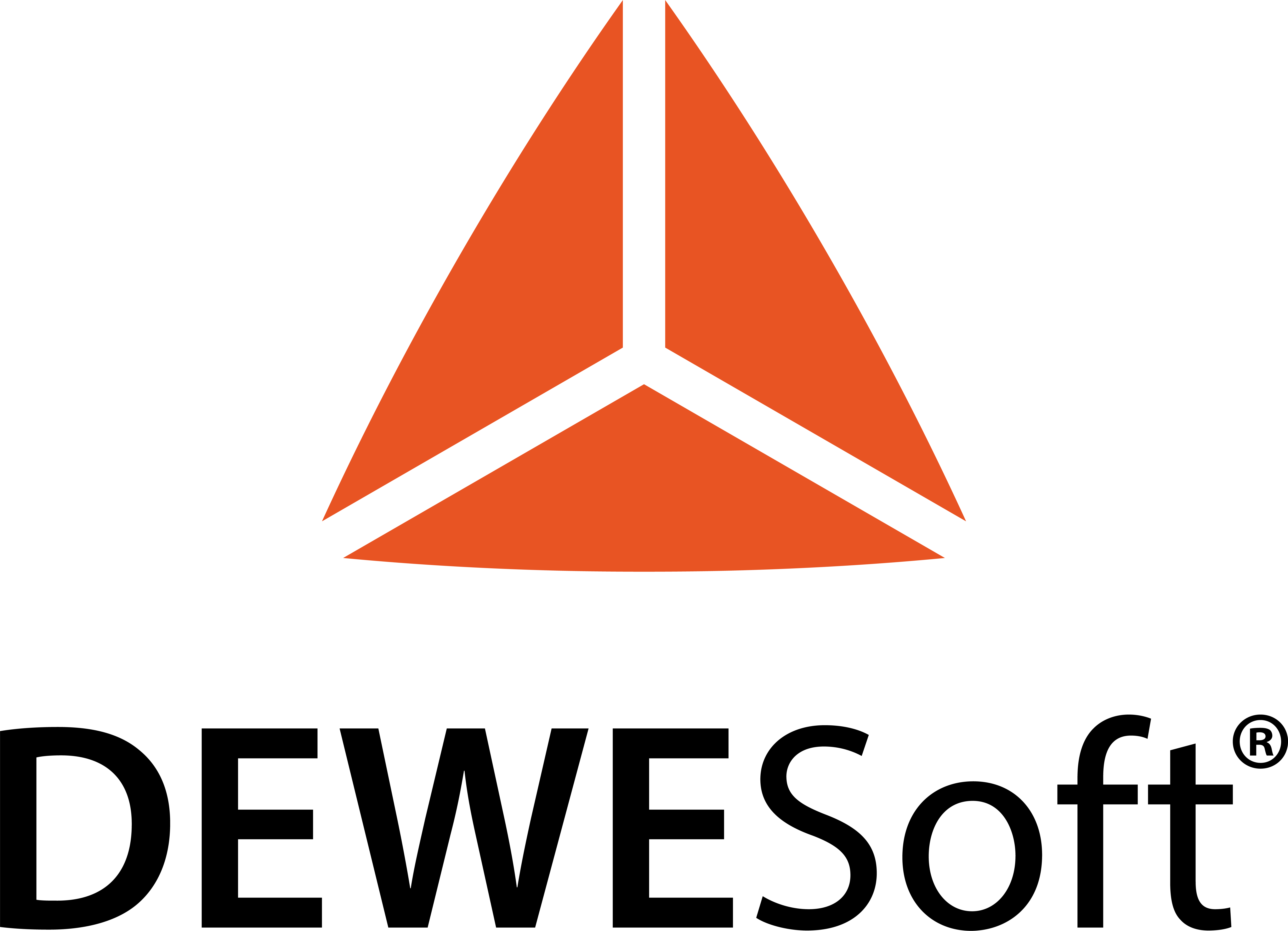
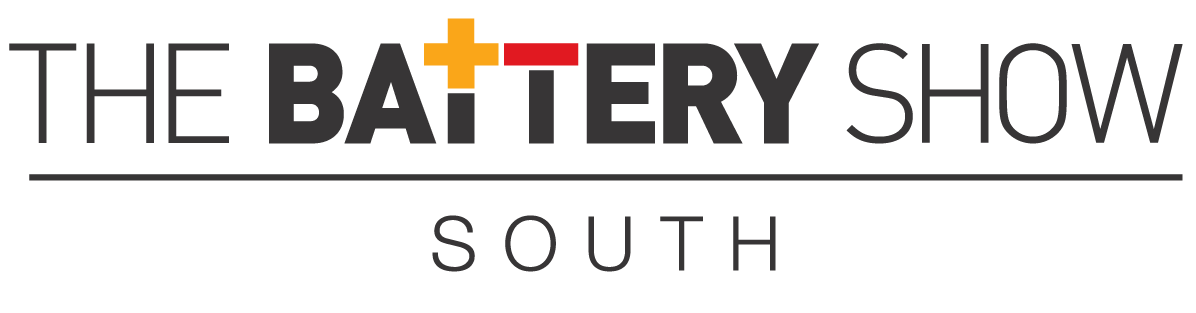
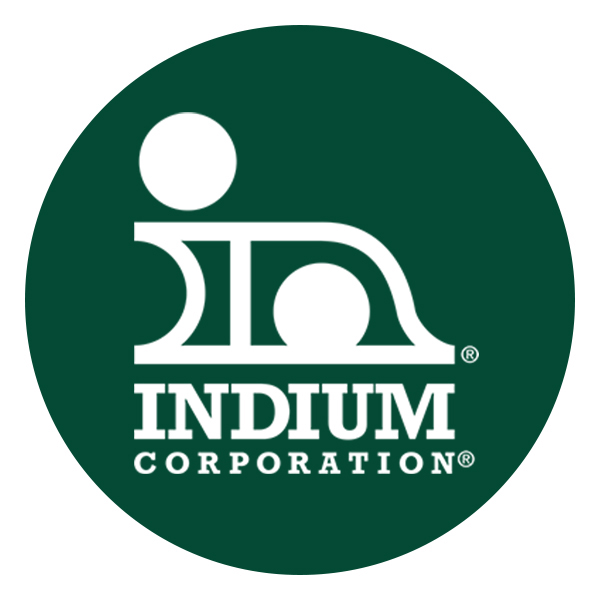

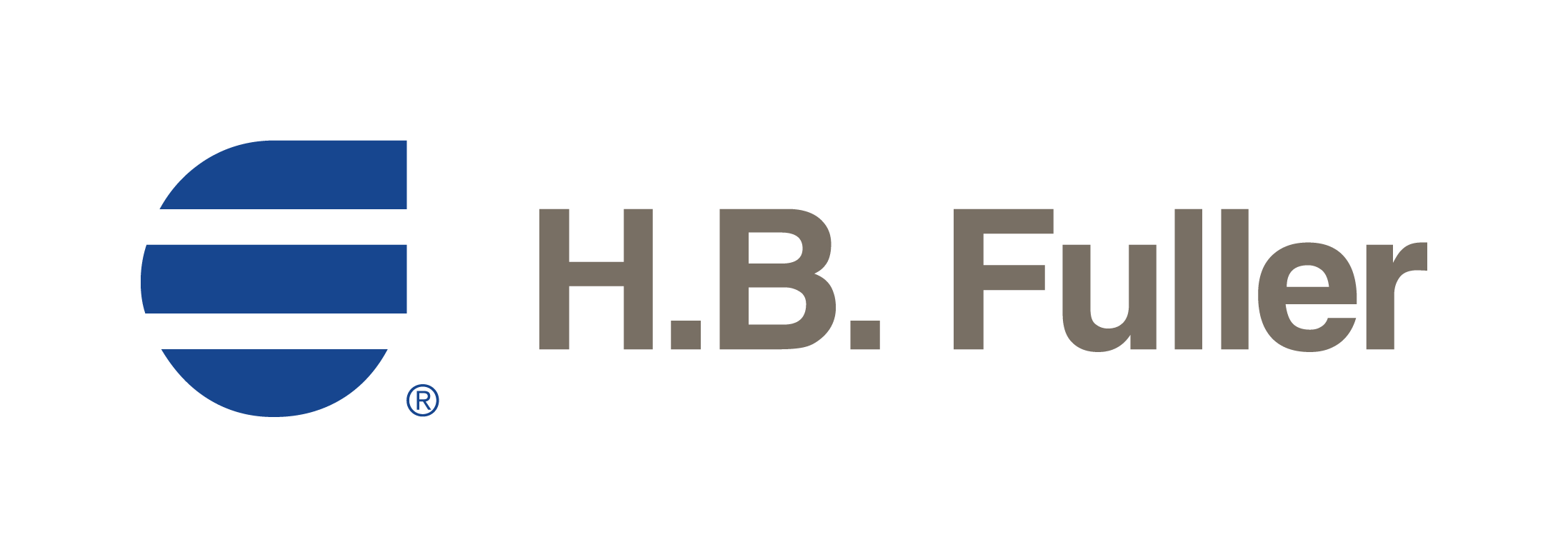
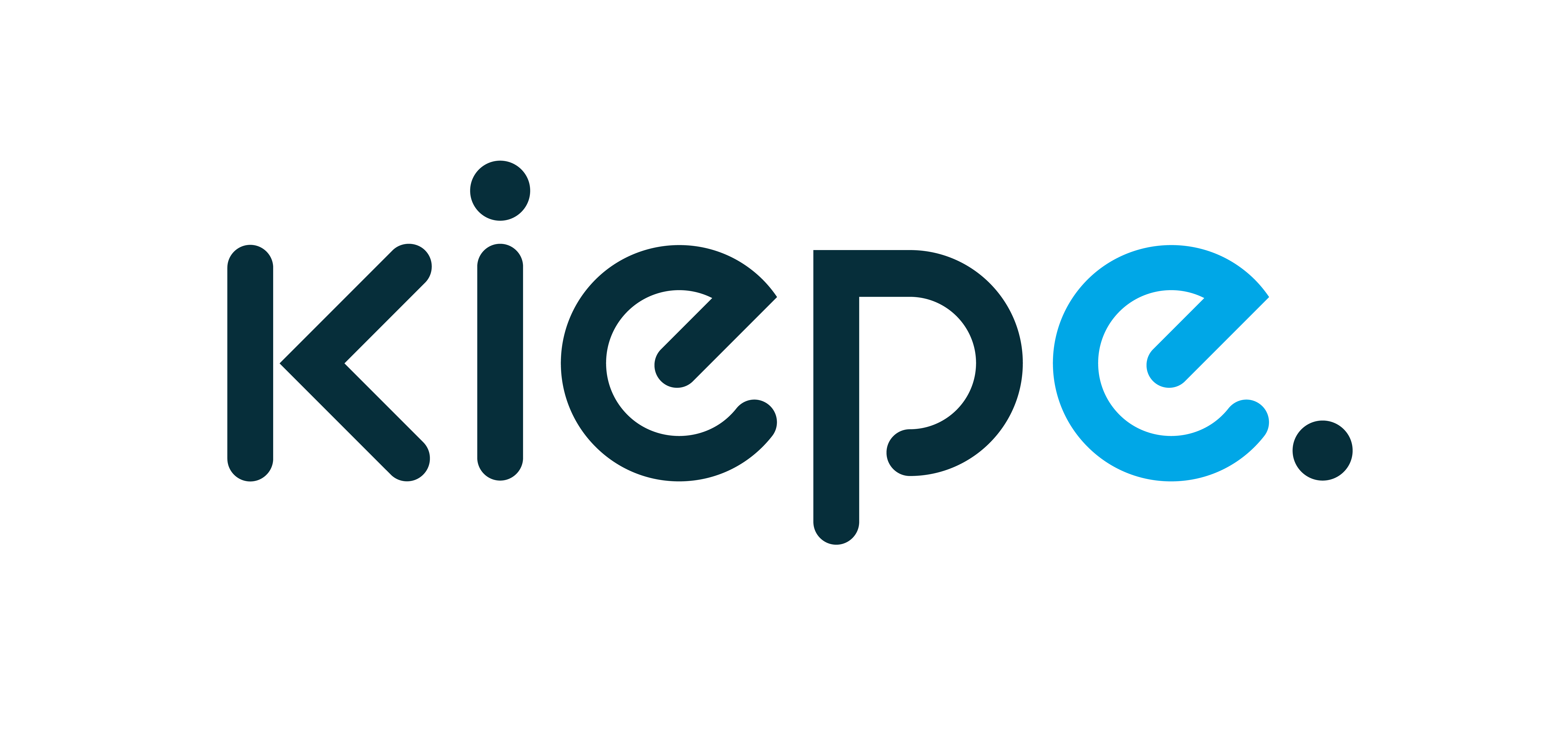
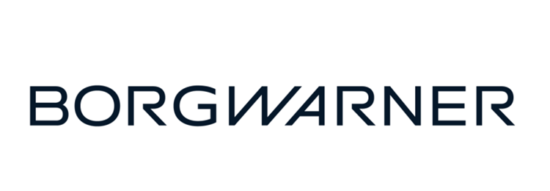