Pipistrel Alpha Electro
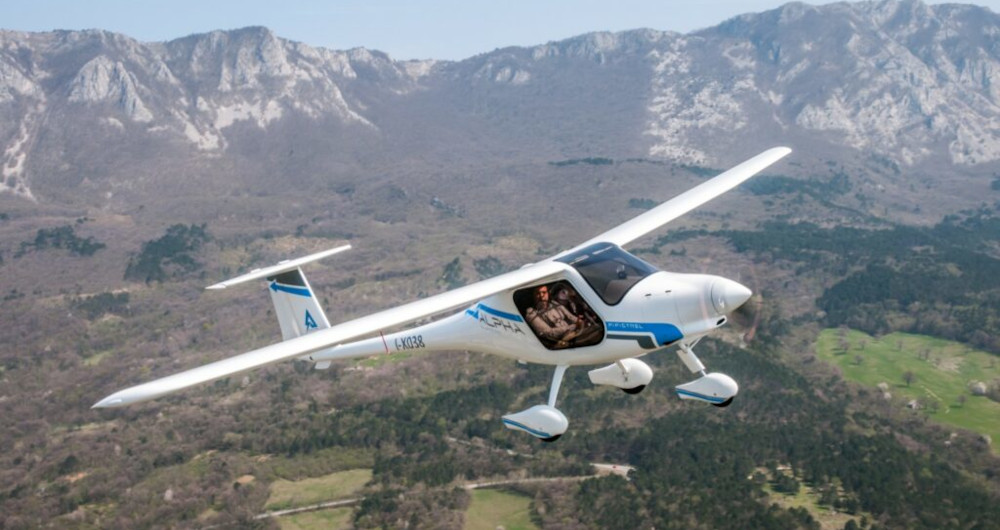
Sky’s the limit
Lawrence Butcher explains how this electric two-seater, airworthy certified aircraft was developed and how it acts as a pointer to the future.
Electric aircraft are by no means a new invention: the first recorded electric powered flight was in 1973, by Heino Brditschka (although a man named Gaston Tissander fitted an electric motor to a balloon way back in 1883). However, the limitations of battery technology and other technical challenges mean it is only in the past decade that using electric power for flying has become practical.
A number of manufacturers are pursuing commercially viable electric aircraft at the moment, but arguably Slovenian manufacturer Pipistrel can lay claim to building the first that is available as a turnkey, customer offering. The Alpha Electro is the brainchild of Pipistrel founder Ivo Boscarol (who started out building microlights when the former Yugoslavia was still under communist rule) and Dr Tine Tomazic, director of r&d at Pipistrel Vertical Solutions (the r&d subsidiary of Pipistrel).
Pipistrel is no stranger to electric aircraft, having produced and partnered in a number of firsts. For example, its Taurus Electro, an electric-powered glider, was the first two-seat electric aircraft to make a flight.
The Alpha Electro is different though, and is to all intents and purposes a conventional, two-seat light sport aircraft, designed as a benign handling and low-maintenance trainer. Most important, it has airworthiness certification in a host of countries including the US, Canada, Australia and several European countries.
Background
Producing an electric aircraft with a useful level of performance has not been straightforward for Pipistrel. When asked about the key enabler to make electric flight a commercial reality for general aviation, Dr Tomazic, who is responsible for the Alpha Electro’s development, says, “I cannot highlight just one. There are some obvious and some less obvious ones.”
One that will be familiar to EV designers in all sectors is the question of weight – or rather, its contribution to overall vehicle efficiency, which in the case of an aircraft encompasses both weight and drag. “You have to have an efficient airframe, because [with current battery technology] you will be at a disadvantage [in terms of endurance compared to a piston-engined aircraft],” Tomazic points out.
The second point he highlights is the advances in battery technology, and not just their performance. “Over the past 10 years we have seen an improvement of 15-20% in battery capacity, and the cost of those batteries has fallen dramatically. That has made it feasible to put an electric aircraft on the market.”
Another, less obvious aspect, relates to the relationship between electric aircraft design and the organisations responsible for approving aircraft for flight operations, be that the EASA (European Aviation Safety Agency) in Europe or the FAA (Federal Aviation Authority) in the US. In aviation – probably more so than any other industry – systems have to be proved safe before they can be certified for use.
“You have to be able to stand behind statements relating to safety,” Tomazic says. “You need to understand how things can go wrong, and be able to mitigate them by design.
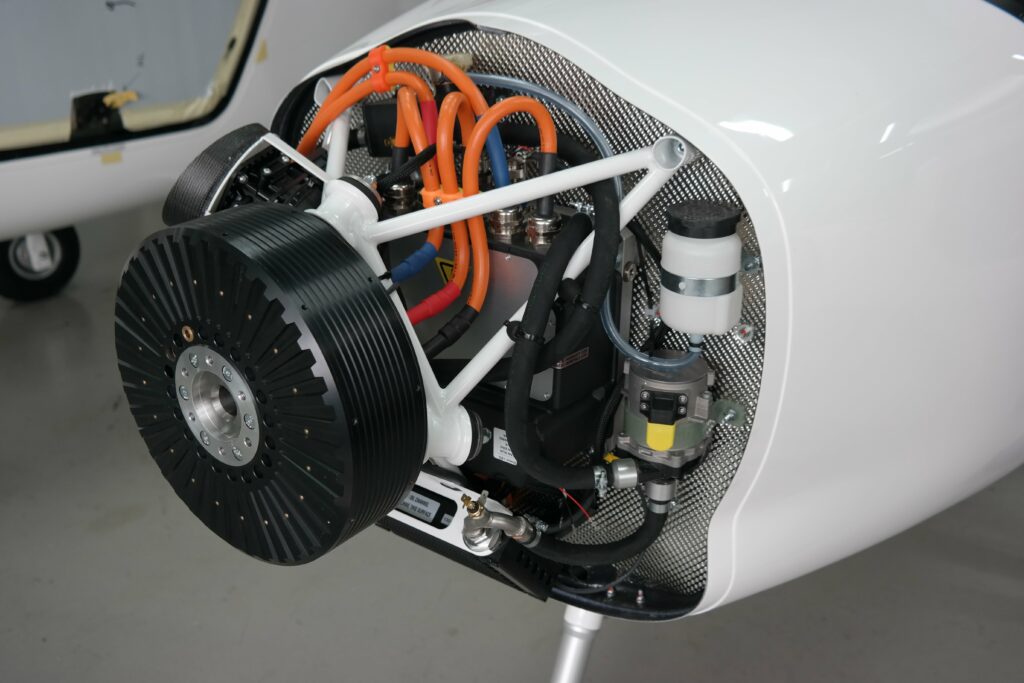
“Then, working with the relevant authorities, you need to ensure that those technologies can be approved for use in aviation – not just for private flying, but for use in flight schools and so on. You can only do that once you have enough experience, because in aviation you cannot just declare something safe because you think it is designed in the best way. There has to be some proof.”
He adds, “No other industrial field comes close to the safety ideology in aviation. If you look at the automotive sector, for example, you shut down the powertrain at the first sign of trouble, and the vehicle can stop by the roadside. In an aircraft though you cannot do that; you have to keep introducing mitigations to allow you to continue flying the plane.
“These factors are unique to aviation. And that is the main reason you cannot just take automotive components and put them on a plane.”
It is for these reasons that the Alpha Electro represents something more than the sum of its mechanical parts. It is a full-scale proof of concept that an aircraft can be powered by an all electric powertrain, with endurance and performance that make it of practical use, delivered for a price in line with similar conventional aircraft – and has been proved to be as safe and reliable in flight as those aircraft.
Powertrain development
When it came to designing the powertrain for an electric aircraft, Tomazic says, “It had to be created from scratch. There is no such thing as an electric powertrain for aeroplanes.”
Pipistrel has therefore formulated a combination of components that provide the performance needed for the aircraft to fly for a reasonable period of time, and with the required level of safety. As noted, Pipistrel has been a leader in electric flight for some time, but there was a considerable performance jump to be made from a powered glider to a true twin-seat sports aircraft.
The first iteration of the Alpha Electro first flew in 2014, and stemmed from an EU Commission project dubbed WattsUp to further the adoption of electric propulsion for light aircraft. It used Pipistrel’s proven Alpha Trainer airframe (based on its successful Virus model range), coupled with a Siemens motor and inverter, with the battery and avionics developed in-house.
The project provided a proof of concept, but, moving forwards, Pipistrel opted to develop its own powertrain for the production variant.
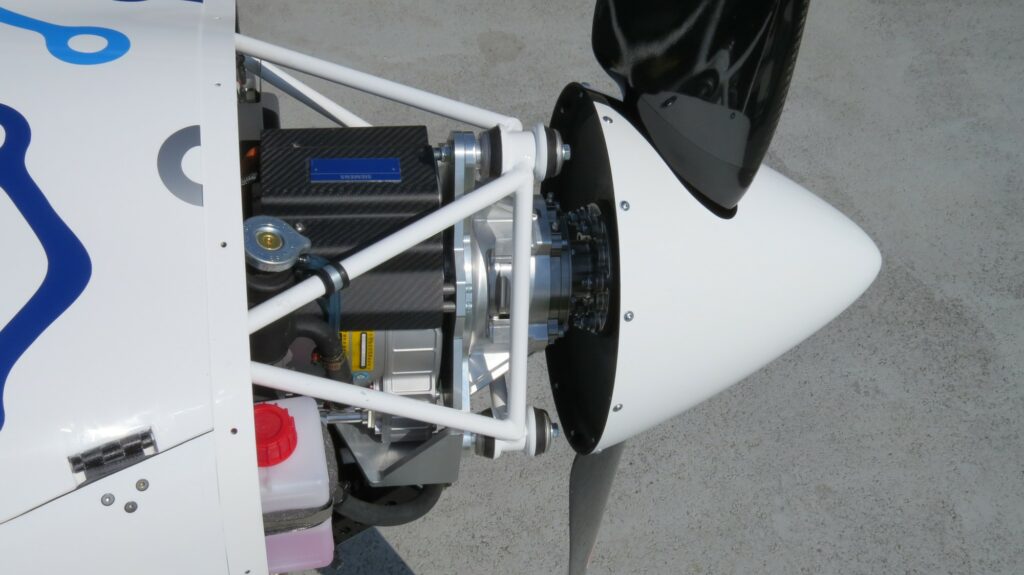
Tomazic points out that from Pipistrel’s perspective the WattsUp provided a proof of concept for the battery, not the motor element of the powertrain. “The battery was the first of its kind that could be charged in the same time as the available flying time it provided. To us, there were two elements to that project – Siemens wanted to prove their motor in flight and we wanted to develop the battery.”
Ultimately, says Tomazic, Siemens backed off from the project, “so we ended up doing it ourselves, in-house,” he says.
The base motor Pipistrel uses is supplied by another Slovenian company, EMRAX, with whom Pipistrel has a history of cooperation, having used EMRAX motors on its Taurus powered glider. The motor is an axial flux, permanent magnet machine and is extensively modified in-house by Pipistrel to meet its requirements. The bulk of the modifications are centred on the cooling system and control/ monitoring of the motor’s operation.
Despite being the sole means of propulsion for the aircraft, Tomazic downplays the significance of the motor’s contribution to the overall powertrain, saying, “It is just an enabler, it does not have a major impact on how the plane performs.”
It might be thought that having the very lightest motor possible is a prerequisite for an aircraft, but as Tomazic explains, that is not necessarily true. “There are certain thresholds that one has to reach,” he says.
“With the motor, for example, if you are using a direct drive [from motor to propeller], most of its torque delivery needs to be below 2000 rpm. The power-to-weight ratio should be 3 kW/kg or more, and it has to be appropriately sized both geometrically and in terms of mass.”
Once these thresholds are met, he says, “Further improvements don’t have much of an implication on this type of aeroplane.” Obviously, if the performance requirements of the aircraft were greater for example, if its intended use was aerobatics – then factors such as the motor’s power density would become more important.
The motor itself weighs about 20 kg, and has an output of 70 kW. That gives it a power density of 3.5 kW/kg, and Tomazic says that if a jump was made to a motor delivering 5 kW/kg (at considerable expense) the weight saving from a motor of the same output (which is all that is required for the Alpha Electro) would only be about 5 kg of mass.
“The aeroplane will not feel a 5 kg difference, it will fly for the same duration,” he says.
The same philosophy of providing what is needed, rather than simply chasing the highest performance possible, also applies to the motor controller. The main power electronics use silicon IGBTs for switching, operating at 400 V, and are housed in a motor control unit mounted directly behind the motor.
IGBTs were the only realistic choice for switching duties, not only from a voltage perspective but also as regards electromagnetic interference. “The aircraft is not grounded, like a car, so keeping currents low is important,” Tomazic says.
While there would be performance benefits to using silicon carbide (SiC) IGBTs, cost considerations come into play, with the higher price of SiC technology not being justified by the gain in performance. Pipistrel has used SiC in some of its projects, but for the Alpha Electro Tomazic says, “There is no real benefit to the customer.”
Safety, safety, safety
A recurring theme with the Alpha Electro is flight safety. Ensuring that the motor runs reliably, and that if issues do occur, it can sustain flight – even if that might be at a lower level of performance – was at the forefront of Pipistrel’s design brief. It is these details that set the motor, or its management, apart from those found in less demanding environments.
As such, Tomazic was understandably unwilling to delve too deeply into Pipistrel’s systems developed for the Alpha Electro. “I will say that we measure temperatures and vibration levels within the motor, but that is all,” he says. “How that is implemented and during which phases of a flight, I would rather not say.”
All the sensor information from the motor, and other key systems such as the inverter and battery, is fed to a central control unit. “It’s like a mini power grid – it coordinates all the systems, including the charger and the cockpit display,” Tomazic explains.
On this subject of control, and specifically comms protocols, Tomazic observes, “There are no standard protocols for aircraft powertrains.” Whereas the automotive world has the CAN bus, which is covered by ISO 11898 standard, in aviation there is no such standard.
“There are standards for controlling turbine engines, but they lack the elements you need to fly electrically,” says Tomazic. The solution for Pipistrel was to create its own protocol. “We used CAN bus as the hardware layer and then we have our own proprietary protocol running at the software layer,” he explains.
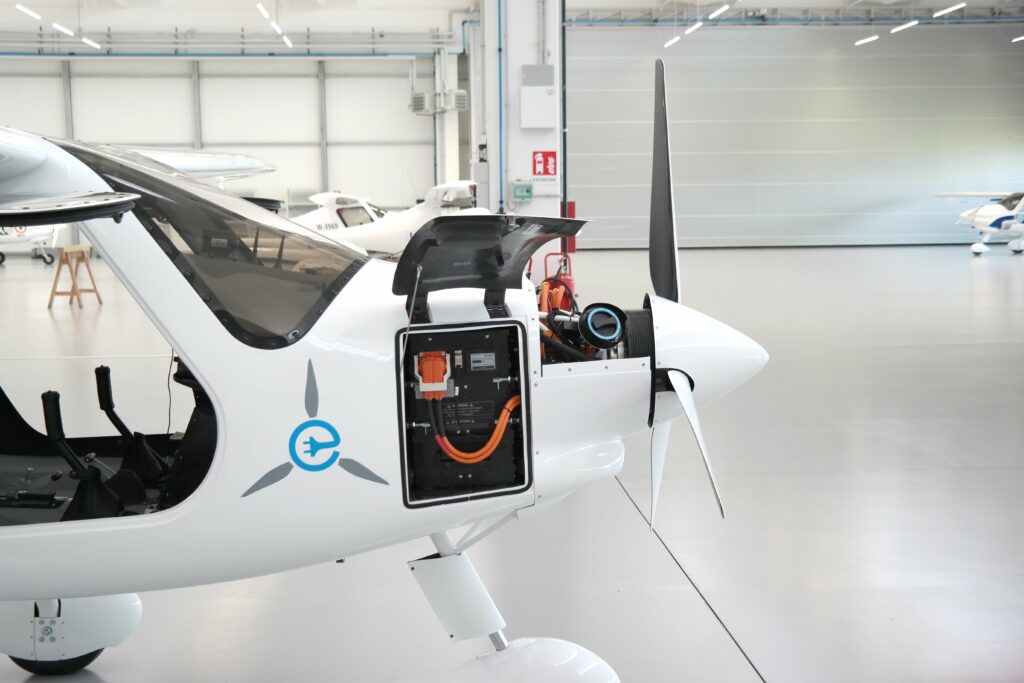
The reason Pipistrel chose to use CAN bus is its capability for controlling hardware error correction. “It is one of the few hardware layers where you can rely on the message coming across in a good state, eventually. There may be delays, but you have error control built into the hardware layer,” notes Tomazic.
Briefly, that means a CAN bus system can detect errors in messages appearing in the bus, with each CAN controller trying to detect errors. If an error is detected, the message will be retransmitted. Eventually, the information will arrive at its destination unless there is a complete failure of a controller.
Tomazic reveals that Pipistrel does not use an automotive type of CAN protocol, having developed its own. “It is more like an aviation protocol in how packets of data are sent and so on,” he says.
“What we also have, relative to what the automotive industry uses, is a built-in state machine, observing the condition of the whole powertrain. That monitors operation and ensures that you do not go into a shutdown at the first sign of trouble.”
Redundancy
Redundancy is one of the cornerstones of aviation safety: if one component or system fails, it should not lead to a situation where the pilot cannot fly the aircraft. However, Tomazic points out that in relation to the powertrain, it does not simply mean duplicating components; it is about the entire approach to engineering the system architecture.
“In aviation, you have to dissect a component down to its functions, then identify which functions are critical,” he says. “Then you look at the system architecture and see how you address those criticalities.
“Sometimes it will be through redundancy, by doubling up systems; sometimes there are other approaches. For example, not everything on the [Alpha Electro’s] power controller is doubled-up, because it does not need to be.”
In fact, simply doubling up on components can in some cases fail to actually reduce the chances of a catastrophic failure, as Tomazic explains. “There is redundancy built in [to the aircraft], period, but the incorrect definition of redundancy is working with two of the same thing, where one is on standby.

“If you have two of the same thing, and there is an error built in owing to the design or manufacturing process, and a factor – be it an environmental condition or something – that kills both at the same time, then you don’t have redundancy. What you actually need is the option to achieve the same function in the end but through different routes.”
Battery
The Alpha Electro has two battery packs to provide power to the motor, each of which is divided into three modules. One pack is mounted in the front of the aircraft, directly behind the motor, while the second is in the rear of the fuselage, directly behind the pilots, and offset to the left.
These locations were chosen to balance the aircraft and make best use of the space available within the airframe. The batteries are of an identical specification and can be swapped fore and aft. The packs’ total output is 22 kWh, which gives a flight time of one hour at full charge, with a legally required reserve. Initially, Pipistrel designed a system where the batteries could be hot swapped, with each module removable from the aircraft, but with further development that concept was ditched.
The main reason for that was, although compact, the packs are still unwieldy and heavy, each one weighing 58 kg, which Tomazic observes is about the same weight as the entire composite fuselage.
The packs needed to be precisely loaded into the airframe to ensure alignment of the connectors, and to do so on a regular basis would ideally require the use of a dedicated loading trolley. However, with most operations for the Alpha Electro likely to take place from grass airstrips, this approach would be impractical.
The mass of the batteries in the Alpha Electro is the reason why, impressive though its performance is, it cannot match an IC-engined craft on performance and endurance. “The Electro carries a lot of weight, way more than a comparable conventional aircraft,” Tomazic says. Yet the total energy it has available, compared to it were carrying an equivalent weight in fuel, is far less.
Although a conventional aircraft’s engine is heavier and more complex than an electric motor and inverter, that does not offset the weight of the batteries. In any case, the situation is more complex than this basic comparison.
An IC engine requires fuel of course, which contributes to its overall take-off weight, but then, as the fuel is burnt the weight falls. The Alpha Electro by contrast is the same weight at take-off and landing.
Tomazic says, “You can’t compare it apples to apples, but there is a different way of painting the picture. We have brother and sister aircraft concepts, the Alpha Electro and the Alpha Trainer. Both take off at the same weight, 550 kg, and both carry two people.
“The electric one can fly for an hour and 20 minutes, the gasoline one can fly for almost three hours, that is the basic difference. There are also more complex factors, and the efficiencies are gained in different areas [for each aircraft type].”
However, he emphasises that this comparison is only accurate for the Alpha aircraft. “If you do your job really well, on the same [base] plane and with the same take-off weight for IC and electric, the IC plane flies about double the time.”
If one was to use a different aircraft for comparison, which does not use such an efficient aerodynamic design or lightweight structure, the Alpha Electro stacks up far better. “If you just put an electric motor on a casual light aeroplane, the performance would be much worse and the endurance difference between IC and electric would be something like fivefold,” Tomazic says.
Chemistry
There are of course similarities between the Alpha Electro’s battery and those in automotive use – the cell arrangement, power connections and battery management systems all follow a similar form. However, the chemistry of the individual cells is geared more towards power density than energy density.
“A typical loading for this class of battery is 3C, whereas on a car, they rarely go above 1C,” says Tomazic. With such a high C rate, thermal management is a prime concern, and the rejection of heat from the cooling system needs to be achieved in as aerodynamically efficient a way as possible.
The varying requirements between automotive and aviation use relate to the way power is deployed during flight. “The biggest difference between how a battery needs to operate in a plane, compared to a car, is that the power bursts are way longer in an aircraft,” says Tomazic.
In an automobile, heavy power draw on the battery will be of limited duration, as a car rarely accelerates for more than a few seconds at a time. Once it is at cruising speed, the load on the battery is considerably reduced. With an aircraft, the cycle is very different.
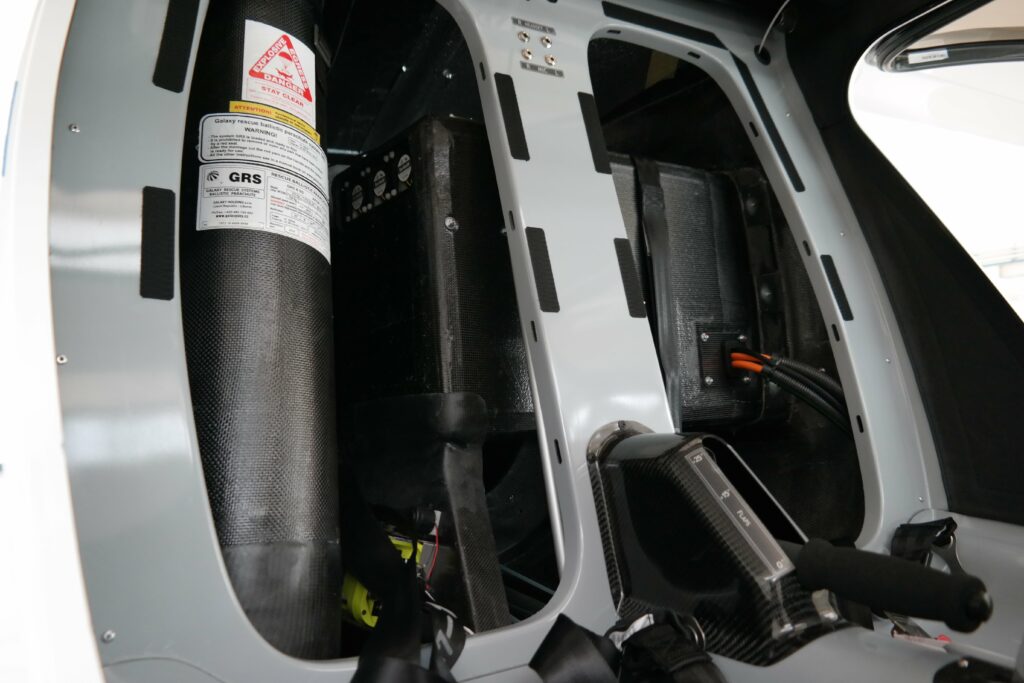
The battery on an aircraft has to be optimised to provide maximum power for the take-off phase of flight. “That is about 90 seconds, and that is full power,” says Tomazic. “The rest [of the power demands] are peanuts.” He adds that the cruising power for an aircraft is about one-fifth of that needed for take-off.
Another consideration for the batteries in an aircraft relates to their size. With packaging and weight being of prime importance, Tomazic says the batteries are smaller than those found in an automobile of a similar power output.
“That means they will be used on a much deeper cycle,” he says. “Each flight will discharge the battery to around 20%. In a car, however, you might use the battery down to maybe 50%. That deeper discharge means you need to be more careful with how you recharge it.”
This deep cycle, combined with a desire by aircraft end-users to be able to recharge it quickly, dictated much of the battery design and architecture. “The battery is always being charged or discharged, it is active a lot of the time, and of course it is being used even when the aircraft is not. That means the downtime between charging and flying has to be minimal,” says Tomazic.
Development of the batteries was undertaken almost entirely in-house by Pipistrel, although it also worked with Slovenia’s National Institute of Chemical Institute. “They provided their expertise to characterise the cell performance in different environmental circumstances, different temperatures, rest/use regimes, figuring out the ageing and failure modes,” Tomazic says.
On that last point, if a cell were to fail, its failure mode is particularly important in an aviation setting. “If a cell fails, catches fire or similar, we need to understand that so we can engineer the mechanics of the battery to contain the condition,” he says.
It should also be noted that Pipistrel does not produce battery cells. Those are supplied by one of the large cell manufacturers, with whom it worked to define the required chemistry for the cylindrical cells.
Returning to the matter of flight safety, the twin batteries provide redundancy, both via duplication and constant monitoring and control. “Each battery can fly the plane, it is a dual redundant system,” says Tomazic. “You can continue to fly with one battery offline of course, but the endurance goes down.”
Fault diagnosis of the battery system is fully automated. If there is an error, the pilot will simply be informed, rather than having to manually shut off systems, as may be the case with a conventional piston-engined craft.
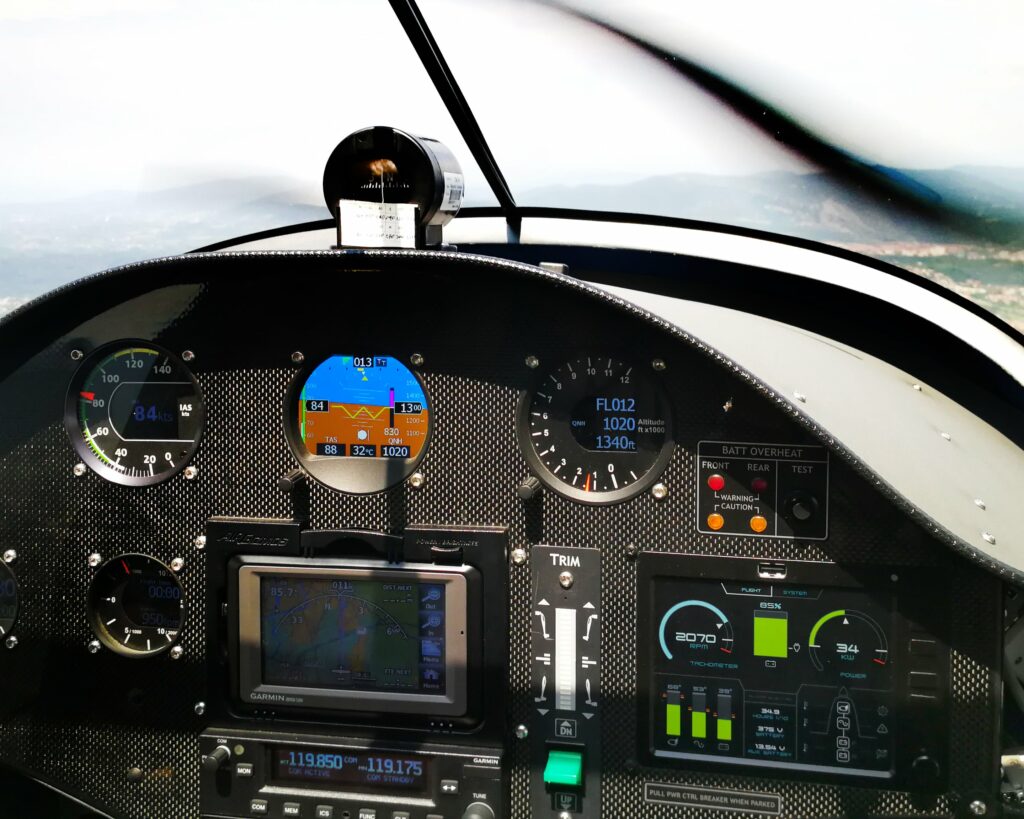
Part of the process of engineering the battery system to be suitable for aviation use was to ascertain the various levels of reaction needed to particular issues. Tomazic declines to go into too much detail in this area, as in many respects it is the ‘secret sauce’ that separates the Pipistrel batteries from other, general-use units.
“I will say that the first level of reaction to an issue is to adjust the powertrain’s power output, seeing what can be done by adjusting the power delivery in a different way,” he says. “Then, at a second level, one of the batteries would be disconnected. At a third level, the system would go into shutdown.”
Tomazic emphasises that this final shutdown stage is not an abrupt event; the pilot is forewarned that it will happen.
Battery life
The actual lifespan of a battery pack is very much dictated by how much and how often the Alpha Electro is used.
Some flyers might simply use it for recreational use, taking off, cruising around and then landing. Others will fly more aggressively, in an aerobatic regime with a shorter flight time but at a higher power level. Then there will be the users undertaking flight training, with multiple landings and take-offs within a short period of time.
Each approach will have a different impact on the battery life, and from his experience of the system, Tomazic says the life of the batteries is between 300 and 800 cycles. He adds, “The environment where the aircraft operates also has an impact. For example, Abu Dhabi [with its high temperatures] will stress them a lot more than Northern Europe.”
A user interface in the cockpit keeps the pilot informed about the state of the batteries and their long-term health. Part of the training package from Pipistrel for the Alpha Electro includes techniques for extending the usable life of the batteries.
Once again, when it came to cockpit instruments to display factors such as battery stats and motor information, there were no existing products on the market that Pipistrel could use, so it had to develop its own.
The display it created for the Alpha Electro is a lesson in simplicity and legibility, as is required of any aircraft instrument, so that its readings can be easily digested by the pilot even when under stress.
As such, the main display shows the motor, battery and inverter temperatures, power consumption, motor rpm and battery state of charge clearly and in colour. A second screen, accessible through a touchscreen interface, shows more detailed information for pre-flight checks covering the motor, battery and power electronics.
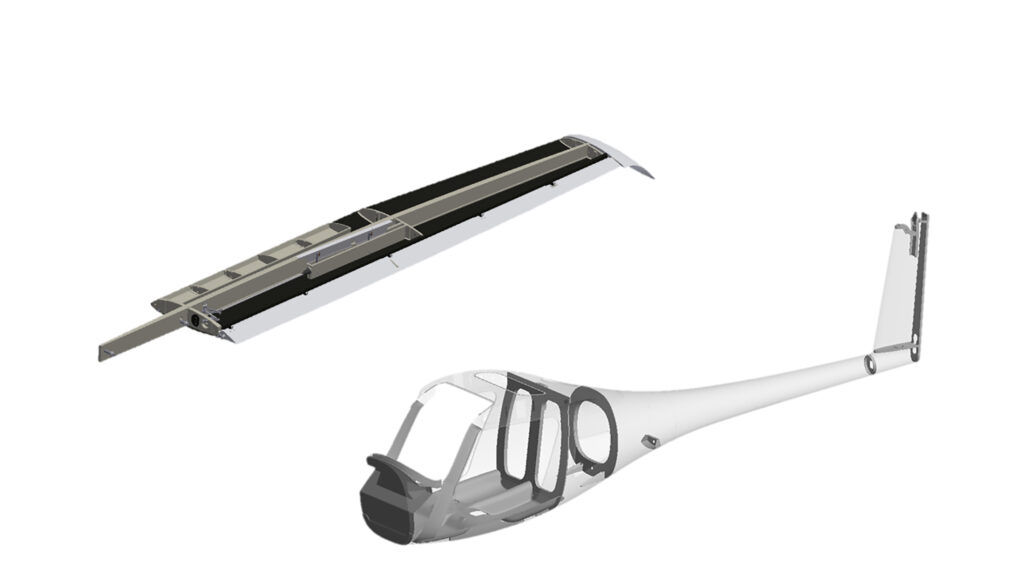
There is also a secondary warning board directly above the main display to give the pilot a visual indicator in the event of the battery overheating. The remaining cockpit instruments are exactly as would be found in any other light aircraft.
The batteries are air-cooled via a series of fans incorporated within the battery casings. Air cooling provides a lightweight solution, of obvious importance in an aircraft. Also, says Tomazic, the airflow over the fuselage when in flight provides plenty of cooling, but that, “when the batteries are being charged, we need fans to circulate the air”.
Cooling air is ducted into the battery compartment via small inlets on each of the battery access panels, and is then exhausted via a duct on the bottom of the fuselage.
Efficiency is key
As Tomazic says, it is not just advances in motor and battery technology that made the Alpha Electro a feasible concept; a high level of overall vehicle efficiency was also necessary.
With a traditional light aircraft, an image of aluminium structures with a riveted construction springs to mind, but the Pipistrel could not be further from that. Instead, it has a full composite construction with minimal metallic structures, resulting in an exceptionally lightweight airframe.
“The more weight you can pack into the energy stores, relative to the empty aircraft weight, the more endurance you will squeeze out of the aeroplane. That is the enabler part,” says Tomazic. “Then you have the aerodynamics – the lift-to-drag ratios – and that tells you how well you can use the energy you have once you’ve taken the aircraft into the air.”
The fuselage is of a monocoque construction, using a combination of different grades and weaves of carbon fibre composite, coupled with sections of honeycomb core material and metallic inserts for point loadings.
Pipistrel does all its composites work in-house, and most of the parts are made using a wet layup method (where dry carbon fabric is laid in a mould, before being covered in epoxy resin). However, in some sections of the fuselage, pre-preg materials are used (where the carbon fibres are preimpregnated with epoxy).
The use of composite construction creates an exceptionally strong and light weight fuselage, and Pipistrel undertakes extensive optimisation work, looking at the types of fibres used and their orientation, in order to minimise material use while maximising strength.
As Tomazic explains, different types of composite structure are used in different parts of the aircraft. For example, he says, “The cockpit area does not use any honeycomb core material; instead there are various blends of carbon and aramid fibres to ensure crashworthiness.
“However, in other areas of the plane, we do use honeycomb as well as foam cores. It all depends on the particular loads and how you want to handle them.”
Coupled to the lightweight structure is a very efficient aerodynamic design.
Drag is minimised across the airframe, effectively, the maximum amount of lift is generated for the minimum drag penalty, thus reducing the amount of power needed to reach a given level of performance.
To achieve that requires a lot of attention to detail, as even very small features can have a major impact on drag. For example, the ducting of air through the front-mounted cooler for the motor controller needs to be carefully controlled and routed, ensuring that the required cooling performance is achieved using the smallest duct area possible.
Similarly, the use of composite construction provides for very smooth surfaces. With an aluminium airframe, even rivets contribute to drag, so eliminating them brings a useful drag reduction.
The profile of the wings and other surfaces all play a role generating efficient lift, and their careful development will maximise the lift to-drag ratio of the aircraft. All of this contributes to improved energy consumption when in flight.
The future
The Alpha Electro may not be able to directly challenge conventional powered light aircraft, but it is a glimpse of what could be the future of light aviation and, eventually, commercial flight.
In the short term, Tomazic says batteries will remain the limiting factor. “You need hybridisation of some sort, so that the plane can have the endurance needed,” he says. Unsurprisingly, this is an area in which Pipistrel is already working, with its MAHEPA (Modular Approach to Hybrid-Electric Propulsion Architecture) experimental aircraft, a series hybrid version of its Panthera four-seater.
In the long term though, and regardless of the power source, Tomazic is adamant that the aviation industry as a whole will need to change its approach to aircraft design.
“You can start putting your powertrain elements pretty much anywhere you want,” he says. “The reason planes look the way they do is because the motors are big and heavy pieces of equipment. You can put them on the nose, under the wing or maybe at the back.
“With a hybrid though you have the chance to decouple where the power is generated from where it is used – rather like torque vectoring on a car, but to a much greater extent. You cannot think of an aircraft the way they look now and just ask what you get if you make it battery or hybrid. The name of the game is changing the architecture.”
The Alpha Electro is just the tip of the development iceberg for electric aviation, but it provides an invaluable first step for developing more capable aircraft, thanks to its amalgam of factors such as high structural and aerodynamic efficiency and, most notably, regulatory acceptance of electric power for use in flight.
Some key suppliers to the Alpha Electro
Inverter: in-house
Battery: in-house
Composites: Interglas Porcher Industries
Composites: Sigratex
HV cables: Lapp
Cable glands: Lapp
Fast charge connection: Mennekes/ Bals
Coolant pump: Pierburg
HV connectors: TE
Data connectors: FCT (Molex)
Fast charger cooling fans: Sunon
Battery cooling fans: Sanyodenki
12 V battery: Aliant
Coolant hoses: Continental
Pipistrel Alpha Electro
Vehicle type: light sport aircraft
Motor: axial flux
Motor cooling: air
Output: 70 kW
Motor weight: 20 kg
Inverter: silicon IGBT
Inverter cooling: liquid
Battery packs: lithium-ion, two, 22 kWh combined
Pack weight: 58 kg
Battery cooling: air
Weight: 550 kg
Speed: 85 knots cruise, 135 knots maximum
Anatomy
The Pipistrel Alpha Electro is propelled by a 70 kW, axial flux motor that is linked to a silicon IGBT-based controller and fed power from two battery packs. These have a combined output of 21 kWh and a useful capacity of 20 kWh, to give an endurance (flying normal traffic patterns) of 55 minutes with a 30-minute reserve.
The motor is mounted on a fabricated steel trellis frame directly to the front bulkhead of the composite fuselage, via four mounting points which feature vibration dampers. The motor is air-cooled and features a machined aluminium housing. The three-bladed propeller mounts directly to the motor output hub using six bolts.
Directly behind the motor sits the motor control unit, which is attached directly to the front bulkhead. Below the motor control unit is a fluid/air cooler for the power electronics, with an electric pump for the coolant. The entire motor/ controller/cooler assembly is encased by two pieces of composite panelling, with an access flap on the upper surface for the fast-charge connector.
The front battery is housed directly behind the front bulkhead, and is accessible via a hinged door. The rear battery is housed behind the cockpit, in a composite box, offset to the left-hand side of the fuselage. The rear of each battery container incorporates three small fans for cooling. There is a small, 12v, lithium ion battery in the front of the cockpit to power auxiliary systems.
The fuselage and wings are made from a combination of composite materials, including carbon fibre and Kevlar. The wings are also of composite construction, and are affixed via interlocking spars above the cockpit.
Where there are point loadings, for example the attachment points for the engine mounting cradle, machined metallic inserts are bonded into the composite during layup. These have a similar role to washers on a bolted joint, spreading the loading over a wide area.
Metallic reinforcement is also used in the top section of the cockpit, where a trellis structure helps to brace the wing mountings. To the right hand side of the battery box is a ballistic parachute, located to be on the aircraft’s balance point, for deployment in emergency situations.
The tricycle landing gear is fixed. The rear legs are composite material with the wheels housed in teardrop shaped low-drag housings. The front leg of the landing gear incorporates a telescopic damper.
In addition to the dedicated display for the electrical systems, the cockpit features a full suite of instruments, including a GPS display, radio, artificial horizon, altimeter and air-speed indicator.
The Alpha Electro has a maximum take-off and landing weight of 550 kg, with an empty weight of 251 kg. It will cruise at about 85 knots and has a maximum rated speed of 135 knots. Cruising at 85 knots, it has a range of 65 nautical miles.
The motor is rated at 70 kW. The take-off run at maximum weight is 255 m (calculated according to the aircraft clearing a 50 ft obstacle).
ONLINE PARTNERS
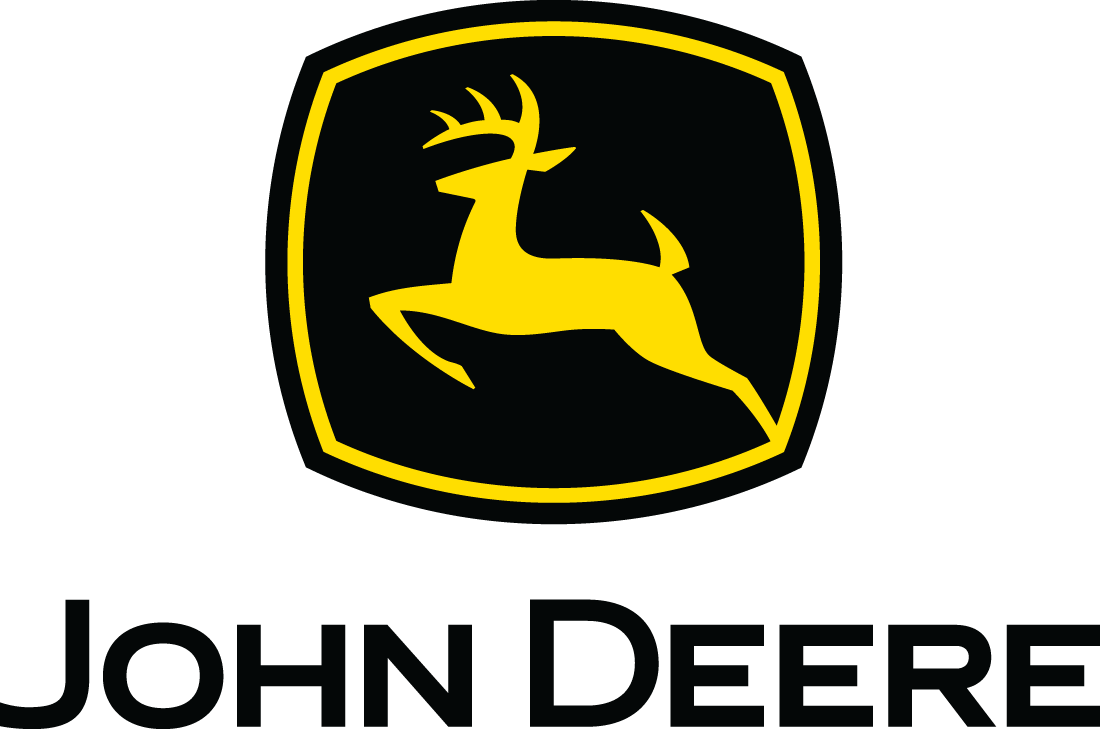
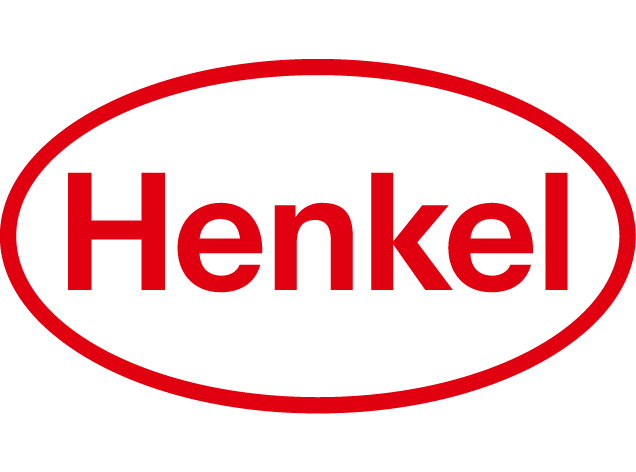
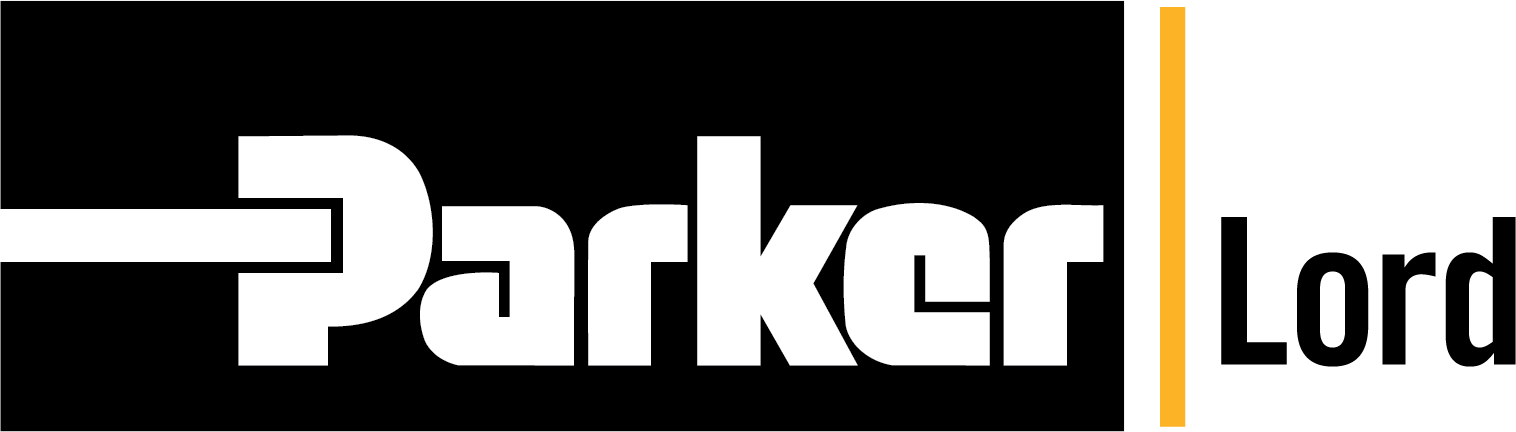
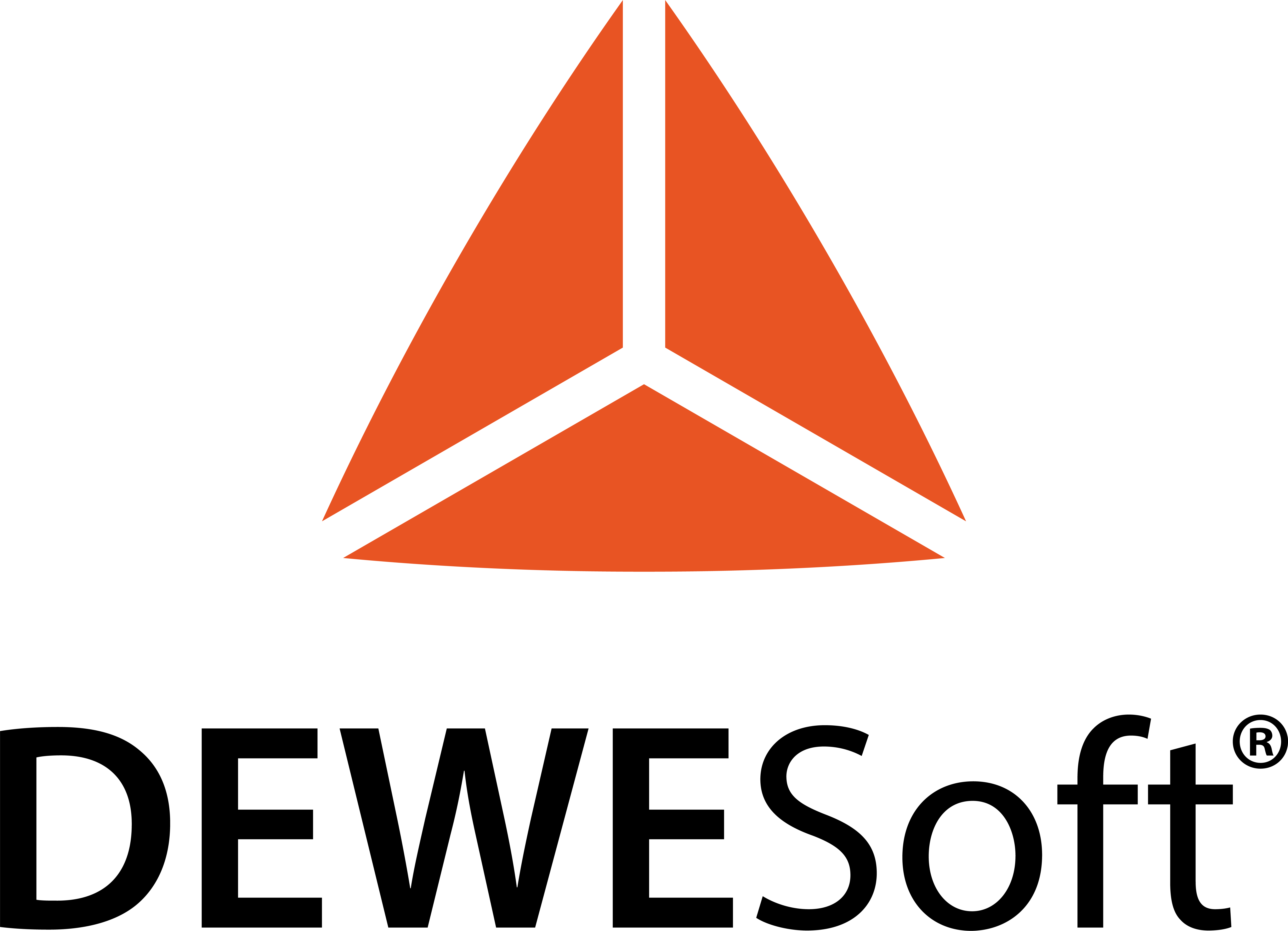
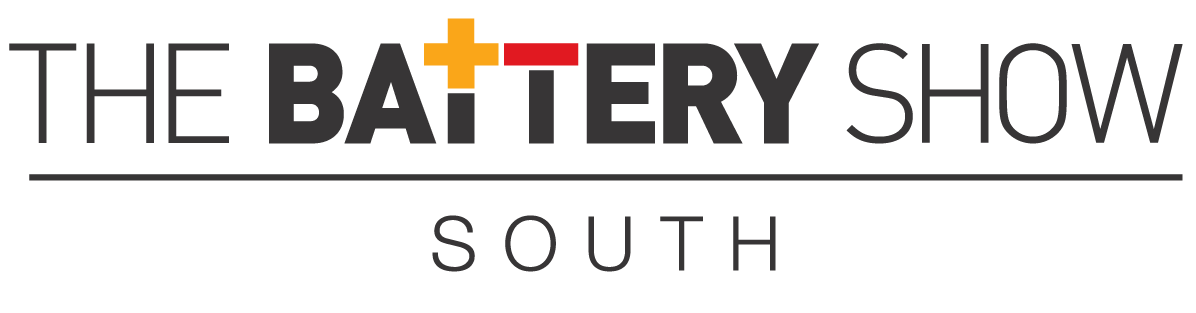
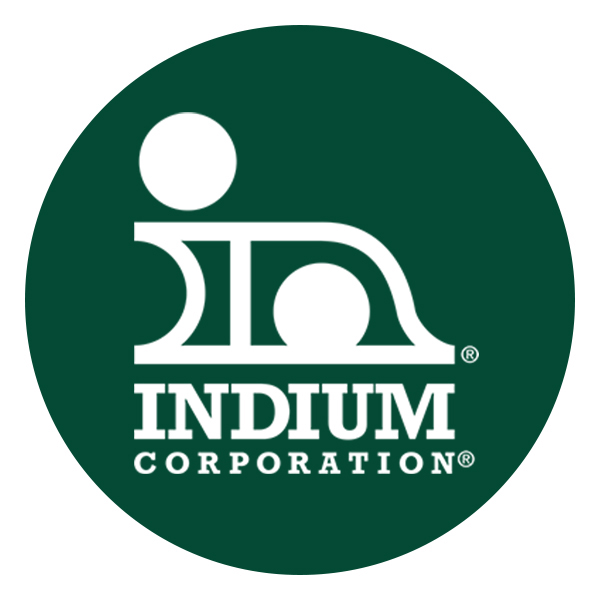

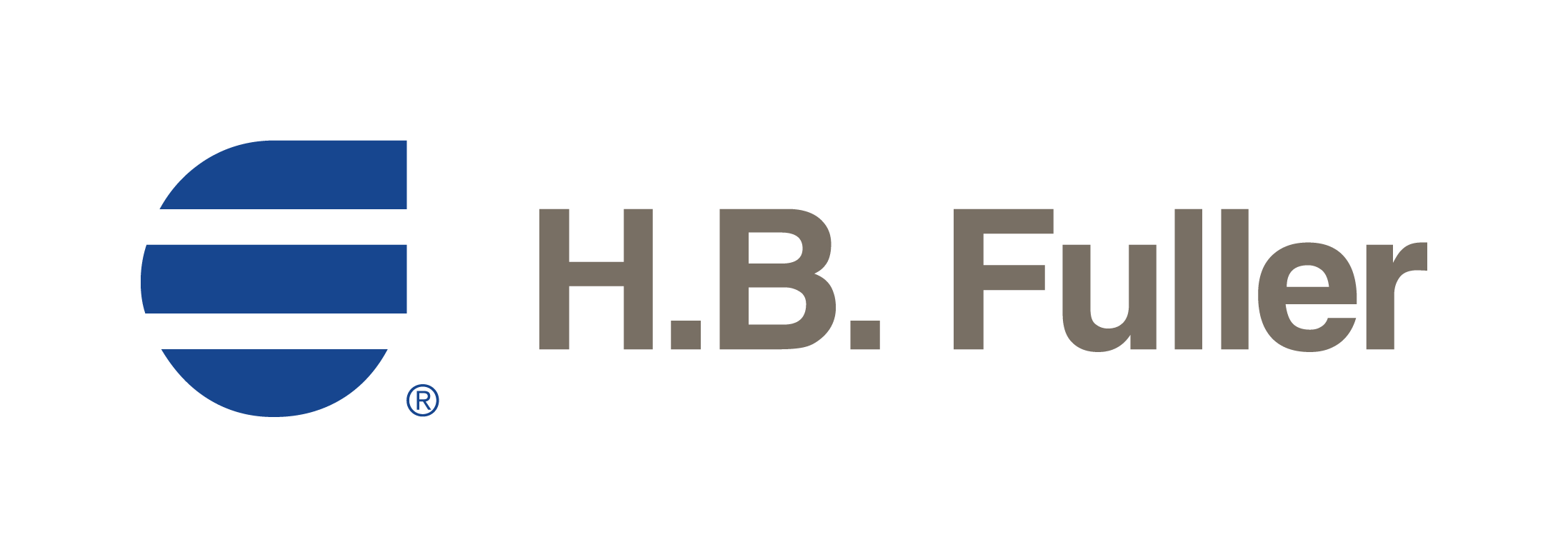
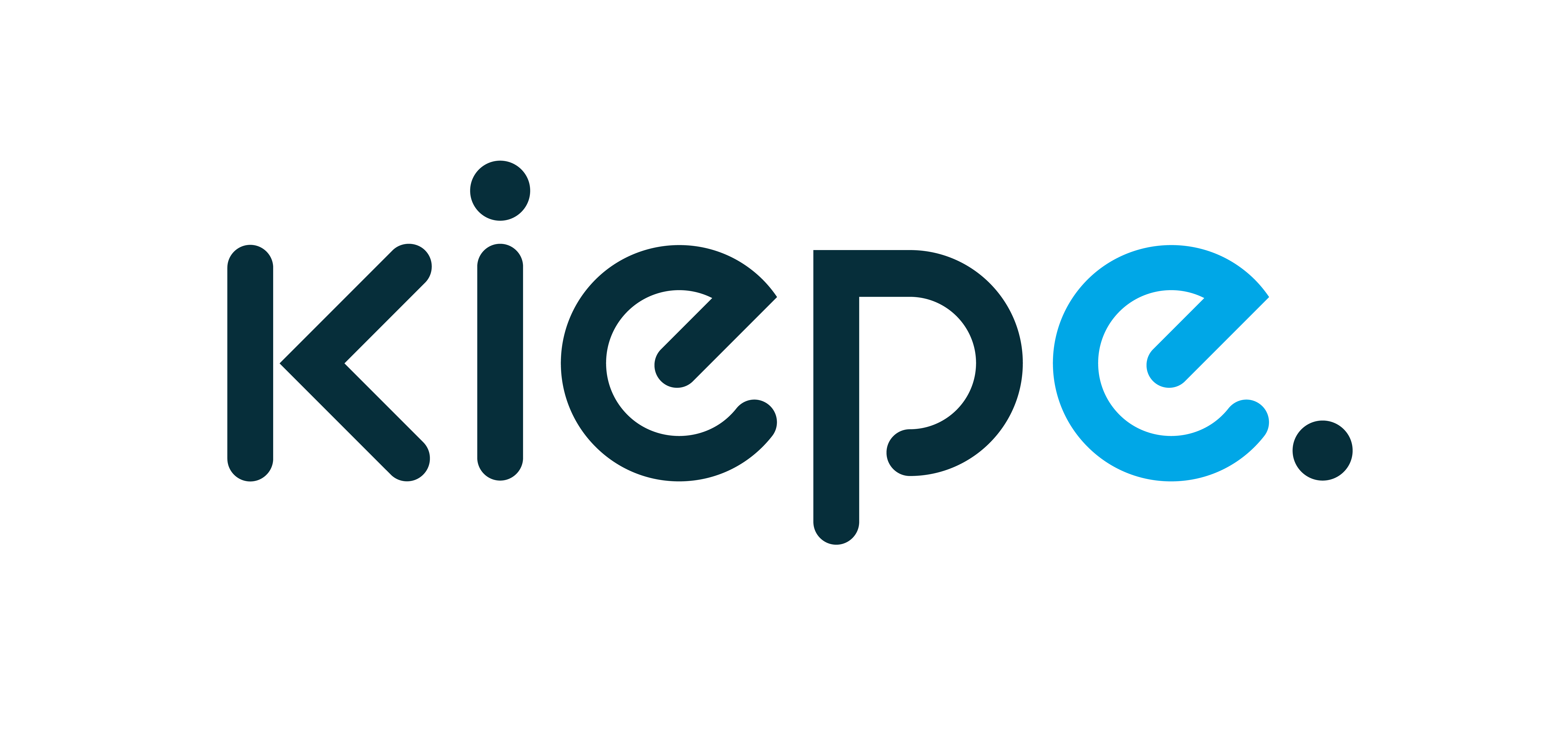
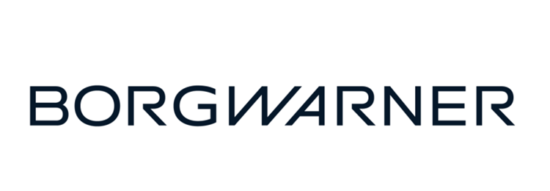