Skateboard platforms
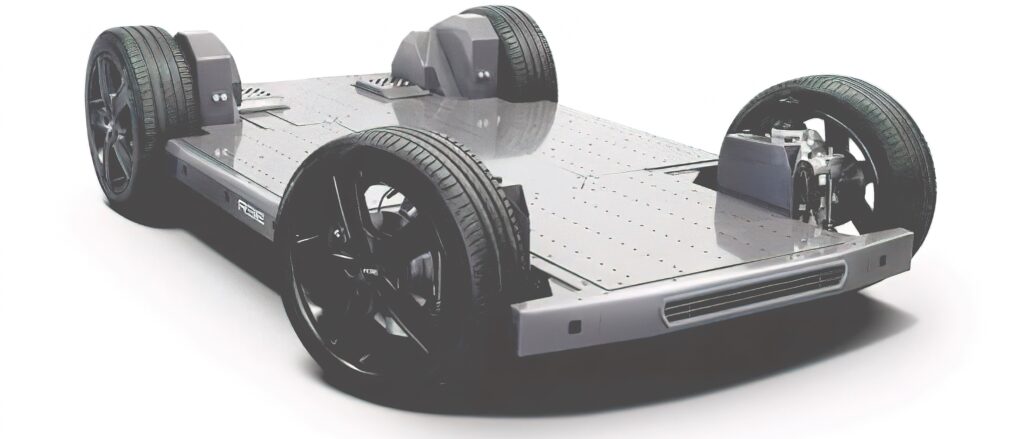
(Courtesy of REE Automotive)
Available in a range of sizes
Against the backdrop of a boom in skateboard platforms for EV designs, Nick Flaherty looks at the approaches taken by some of their suppliers.
Changing the wheelbase of a traditional car or truck design by 6 or 7 in creates a ripple effect whereby half the transmission shaft has to be redesigned, changing the centre of gravity and the requirements for the suspension. That means a whole new vehicle design is needed, which can cost up to $1 billion and take five to eight years. That’s an expensive 6 in.
Instead, an e-mobility development allows the designer to put all the motors and battery pack in a chassis that looks like a skateboard, with a relatively simple body to be built on top. The size and shape of the chassis and the bodywork can be easily varied to meet different requirements, from a small consumer car to a luxury model, a delivery truck, a pick-up truck or even an off-road construction vehicle. All of these can be implemented using variants of the same skateboard platform at a fraction of the cost of a traditional vehicle design.
The skateboard’s layout can also be easily varied, putting a motor on the front or back axle, depending on the application, or adding motors to all four wheels for higher performance or for commercial vehicles to carry bigger loads.
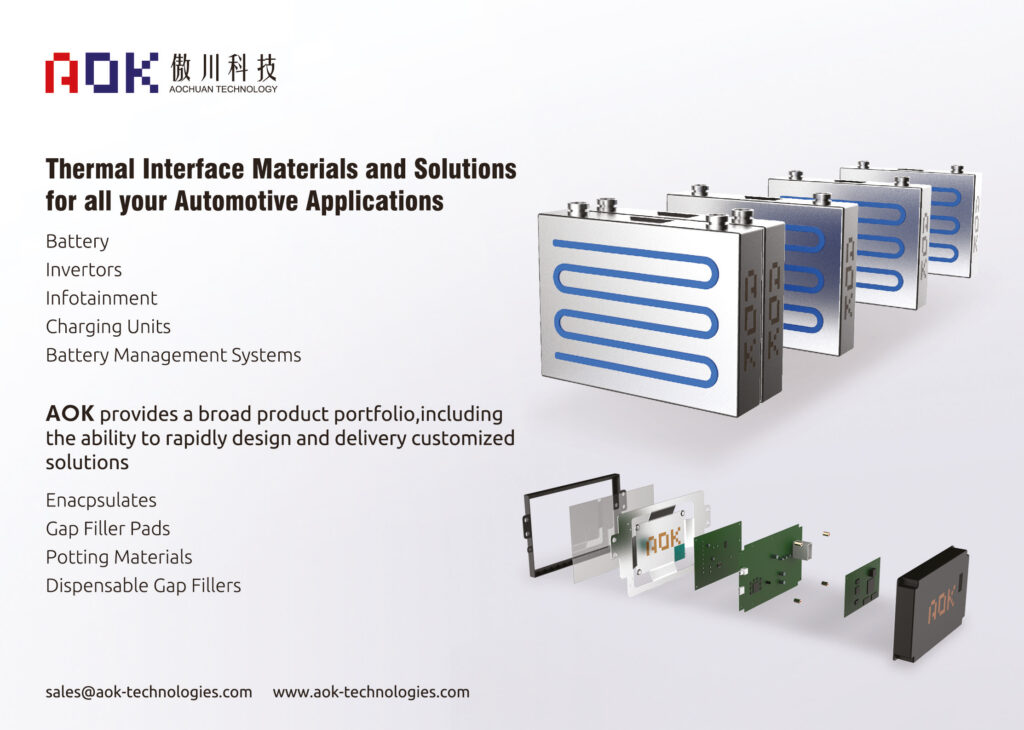
The move to a skateboard platform also opens up different ways to build and service EVs. Rather than requiring billion-dollar factories to build the vehicles, the bodywork can be developed separately from the chassis and assembled close to customers in regions around the world.
This can also change the way the vehicles are serviced. Some modular skateboard designs have been developed that allow different elements to be quickly and easily replaced. A small number of modules can be kept in stores for servicing, simplifying the inventory and supply chain requirements, and the modular design allows the units to be swapped out in as little as an hour.
All of these advantages have led to a wide range of skateboard designs being developed and tested in recent years. But none of this is new. The first skateboard platform was developed 20 years ago at General Motors for a concept EV called the Autonomy. That was followed by a physical proof of concept called the Hy-Wire.
The original concept of the skateboard had the bodywork secured with just eight bolts so that it could be lifted up and replaced as servicing or even fashion required.
As well as the obvious advantage of replacing the IC engine with an electric drivetrain and battery pack, the real key to the development of the platform is the availability of X-by-wire technology. Electronic control of the motors, steering, braking and suspension allows these elements to be separated, opening up the flexibility of the platform.
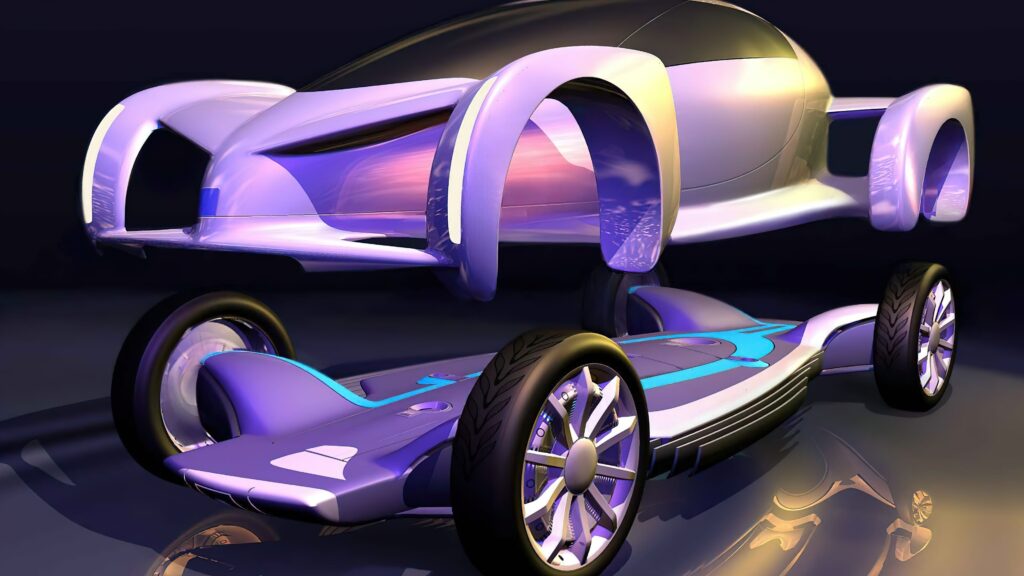
(Courtesy of General Motors)
No longer is the design determined by the transmission or the steering column.
With electronic control systems, the steering, accelerator and brakes can be placed on either side of the cabin, or even in the middle. Early concepts had the controls available at both ends of the vehicle so that it didn’t need to turn around; instead the driver swivelled a chair around to change direction.
The move to a skateboard chassis also helps with vehicle dynamics. Having the batteries in the vehicle’s floor lowers the centre of gravity, helping to improve the handling and providing more space for the driver and passengers or for carrying a load.
This was particularly appealing for Tesla’s Roadster and Model S that adopted a skateboard design. Every Tesla showroom displayed the chassis
as a key selling point. The same approach was adopted by Audi with its e-tron platform, and has been used for three different ranges of EVs, including the Volkswagen MEB platform.
These commercial platforms have been developed with the 40 to 50 patents filed by General Motors on the skateboard technology in mind. As these patents have lapsed, however, there has been an explosion in the development of other skateboard systems.
Start-up vehicle companies have focused on the development of a skateboard as a platform, integrating the battery system, electric powertrain and X-by-wire technology to give them the flexibility to address multiple markets. Others are developing the technology to license it to traditional car makers to accelerate the move from IC-engined vehicles to electric.
Foxconn for example is opening up its skateboard platform, which it calls MIH, to car makers. The company is using its experience of making Apple’s iPhones and much of the world’s electronics equipment to simplify the manufacturing of the skateboard chassis. For example, it has an aluminium casting for the front suspension as a single unit, and at the rear combines 27 components into a single module.
Although the skateboard is a unibody construction, Foxconn uses a modular approach with a choice of 150, 200 or 240 kW motors at the front with a 340 kW motor at the rear, and supplies all the drive-by-wire and driver assistance electronic control systems.
Other platform developers have extended the modular concept to use different-sized crash zones on a central unit according to the specification of the vehicle.
Other platform developers have extended the modular concept to use different-sized crash zones on a central unit according to the specification of the vehicle.
Future directions
Protecting the lithium-ion battery pack from damage is a key design requirement for the skateboard chassis. If the pack is damaged and leaks, the vehicle can catch fire, as has already happened several times with the skateboard platform for the Tesla Model S.
However, the combination of the skateboard and solid-state batteries dramatically reduces the risk of fire, if not eliminating it entirely. These batteries replace the liquid electrolyte with a solid material that does not leak when punctured or cracked.
That, coupled with the higher energy density of solid-state cells, means less space is need for the crash zone and allows more space to be made available for the same range, or more cells for a longer range in the same footprint. With the flexibility of a modular skateboard platform, this is a relatively simple change to make. The solid state cells can replace existing lithium ion cells, or the chassis can be reimplemented with smaller crash zones.
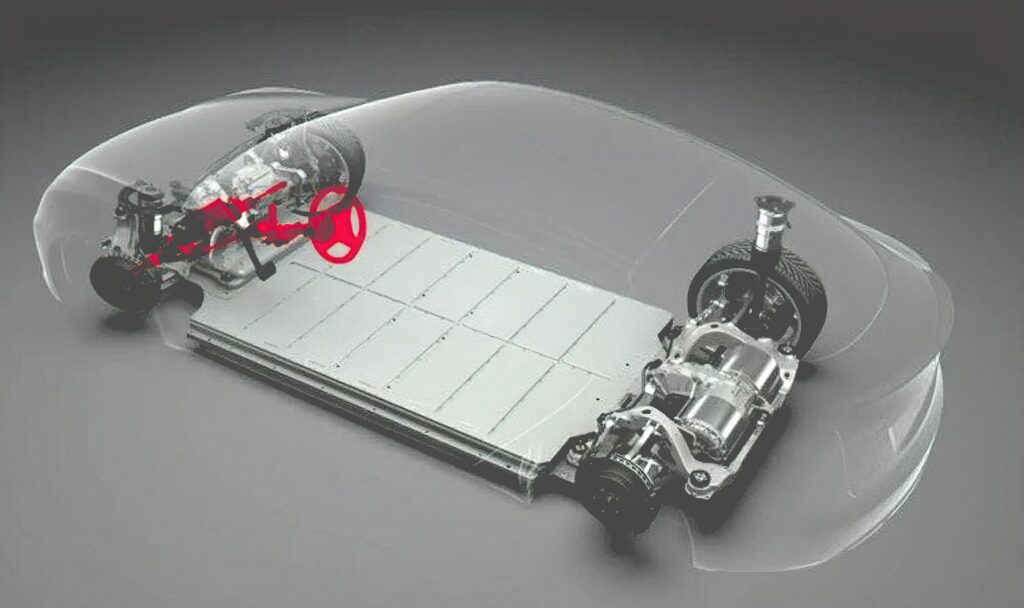
(Courtesy of Tesla)
The impact of solid-state battery technology goes further than adding more range. The cells themselves can be used as part of the structure of the skateboard chassis, reducing the amount of steel needed in the chassis and the battery pack. Solid state cells are expected to be used in a skateboard chassis from Foxconn in 2024.
A step further is the idea of the structural solid-state battery. As well as having the pack in the skateboard chassis, body panels made of carbon fibre composite can be turned into battery cells by adding other fibres and a solid-state electrolyte (see The Grid in this issue). This approach of a ‘structural’ battery in the doors, roof and other body panels can be used to add range or eliminate the battery pack in the chassis altogether.
However, this raises a number of questions over how the batteries can be serviced or replaced, and how they can change the weight distribution of the vehicle. It also increases the complexity of the wiring harness, bringing power from many different parts of the bodywork. This increases the complexity of a design that had been simplified by having the battery pack close to the inverters and motors, with more high-voltage 400 or 800 V connectors and wiring required, adding weight and cost.
Conclusion
After 20 years, the skateboard platform has come of age. From an early ground-breaking concept to mainstream production, the design approach is expanding the range of e-mobility vehicles that can be quickly developed and manufactured. This has led to an explosive growth in the suppliers of such platforms.
Origins of the skateboard platform
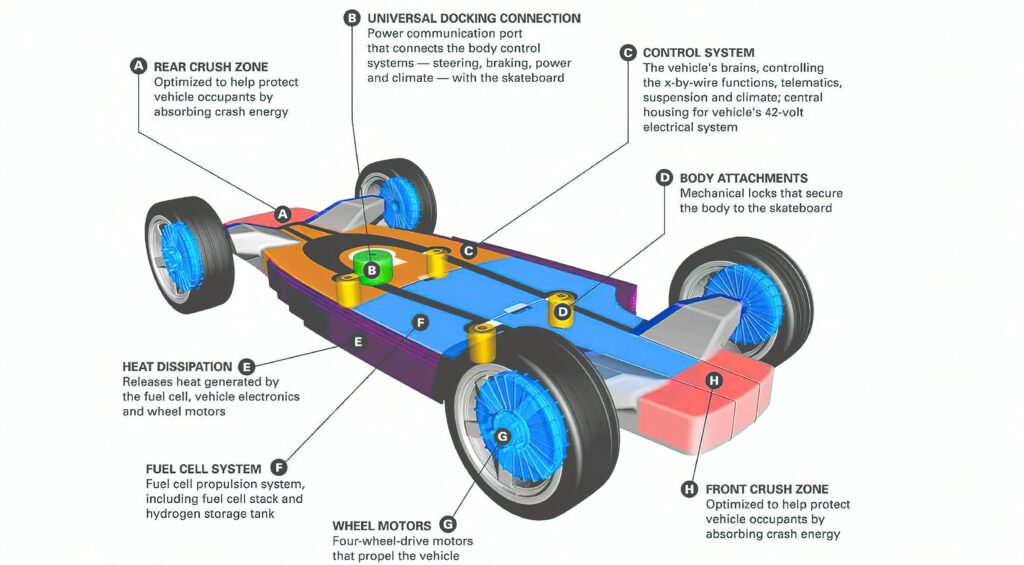
(Courtesy of General Motors)
The origins of the skateboard platform lie with General Motors, which developed a concept vehicle called the Autonomy around a skateboard chassis in 2002. It went ahead with a physical proof of concept in 2003 called the Hy-Wire that could be based around a battery pack or a fuel cell.
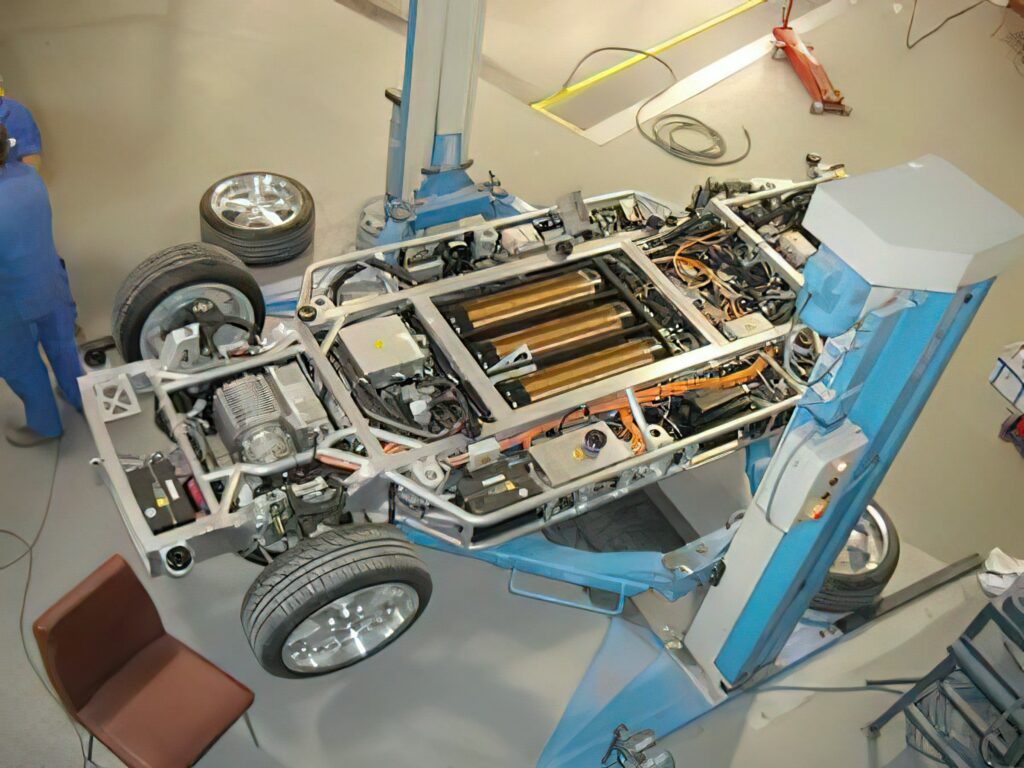
The Hy-Wire was designed around an 11 in-thick chassis housing the entire propulsion system. A single electric drive motor up front propelled the front tyres, and the hydrogen fuel cell provided the electrical power for the drive motor, allowing a top speed of 100 mph. The fuel cell was capable of providing 100 kW of continuous power, a figure based on the amount of compressed hydrogen packaged in the middle of the skateboard, and gave a range of 100 miles.
A battery version was developed to enable the skateboard to be validated and tested before being swapped out for the fuel cell. A drive-by-wire system enabled the steering, braking and other vehicle systems such as acceleration to be optimised with software for ease of use, with all the vehicle systems controlled electronically rather than mechanically. The driver would brake, accelerate and steer with either the right or left hand – there were no pedals to operate. Acceleration was achieved by gently twisting the handgrip, braking by squeezing the handgrip, and steering consisted of gliding the hand up or down the handgrip, a motion similar to the circular motion of a traditional steering wheel.
A portable spider-like device called the Spider Body Hoist was attached to the body. After releasing the body via eight mounting bolts on the skateboard chassis, the hoist would lift the body off the skateboard. Once the body had been removed, it could be wheeled off to be serviced, upgraded or repaired.
The front and rear body panels were made of glass, allowing the driver to see through the front of the car through the traditional hood location and through the back of the car through the trunk. Seats are made of see-through mesh, affording the driver even greater visibility. The Hy-Wire had around 50 patents associated with its development.
Traditional chassis to skateboard
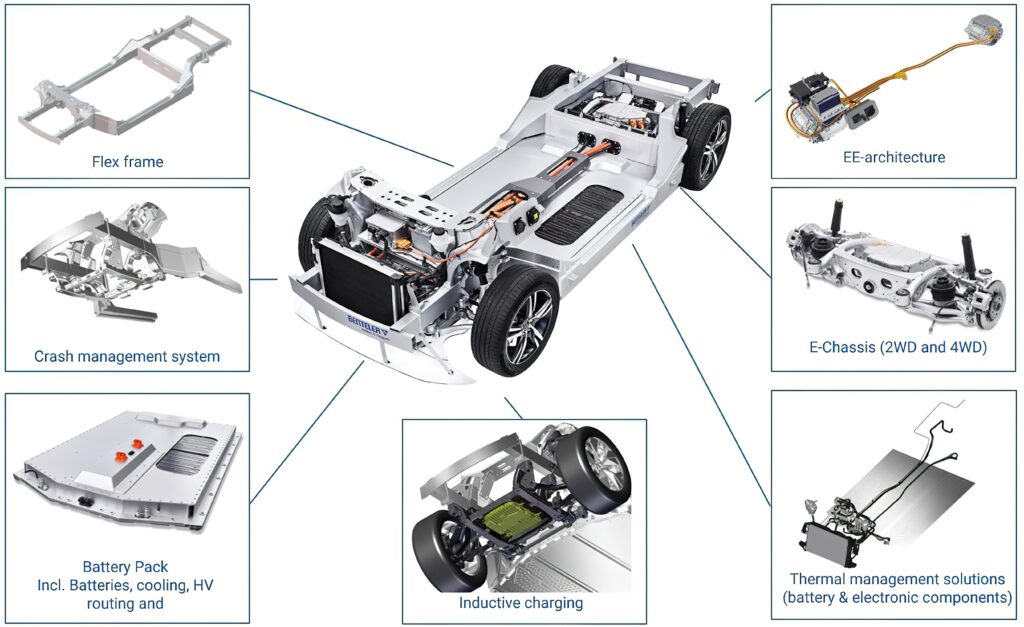
(Courtesy of Benteler)
The skateboard approach is not exclusive to EVs, as shown by traditional chassis maker Benteler, which has worked with Bosch on a skateboard platform. Benteler specialises in chassis and structural elements, as well as exhaust systems and e-mobility modules, but developing a skateboard design required a new way of thinking about safety and rigidity.
Having the battery on the bottom eliminates the driveshaft tunnel, which is a stabilising element. That means having to rework the crash management system. The platform’s ‘load path’ has to be transferred to the outer rim of the skateboard chassis and combined with special materials technology to create structural stiffness. While some skateboard chassis are made from steel, the weight can be optimised by using aluminium extrusions designed to have higher torsional stiffness.
The Benteler skateboard uses modular subframes to lengthen or widen the chassis, and each has been designed to reduce the NVH (noise, vibration, harshness) with a rubber bush connection. These connections are also used on the electrical drive unit to reduce NVH.
to reduce NVH. The front and rear suspension modules integrate the motors. One area of Benteler’s expertise is cooling and heating systems, so it has paid particular attention to the thermal considerations of the skateboard chassis. A custom design of the battery cooling plate reduces the skateboard’s weight and height, as well as boosting the life of the batteries. This lower height is achieved by using highly integrated routing of cooling circuits through the skateboard’s body.
The bodywork is connected to the skateboard using cold joining technology, which the company says is the way to achieve the best crash performance. It has also designed new energy absorption elements to protect the battery system in a crash.
A commercial skateboard
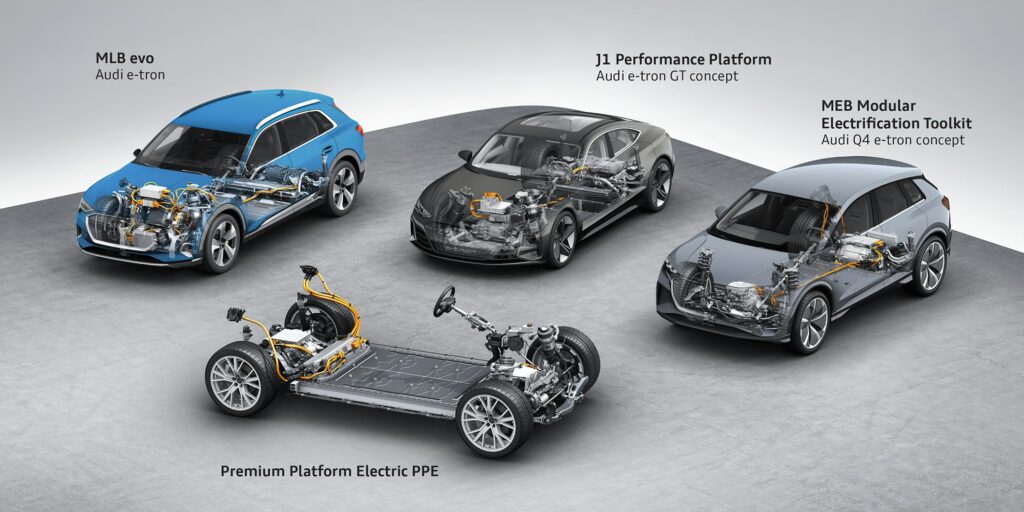
(Courtesy of Audi)
The Audi e-tron quattro skateboard concept was introduced in 2015, and was launched commercially in 2018. It uses a 95 kWh battery pack made up of 12 replaceable 60 Ah cells in the floor of the skateboard, with an 11 kW AC charger and 150 kW DC fast charger. The skateboard has a thermal management system for the battery and two electric motors to maintain the battery at 23-35 C. The motors, one at the front and one at the rear, provide 300 kW (402 bhp) and produce 664 Nm of torque in maximum boost mode. In normal operation, the front motor provides 125 kW with 247 Nm of torque and 140 kW from the rear motor at a torque of 314 Nm. The chassis includes an energy recovery system during acceleration and deceleration that boosts the range by 30% to 370 km compared with a system without energy recovery.
A skateboard for pick-up trucks
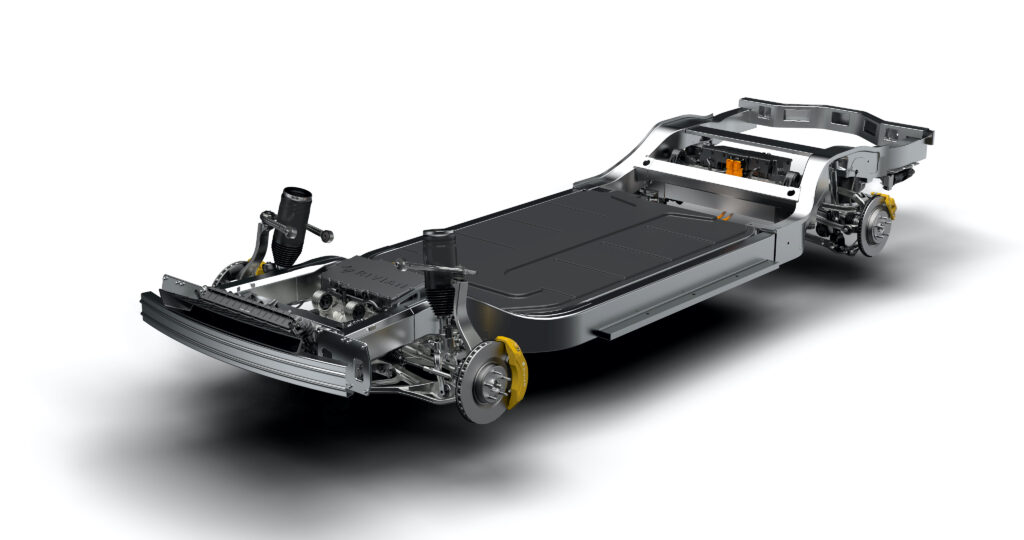
(Courtesy of Rivian)
Rivian has adopted the skateboard approach for electric pick-up truck designs with off-road capability. The chassis uses dual-motor units mounted on each axle. At the front, the 310 kW (415 bhp) motors provide 559 Nm of torque, while the rear motors provide 313 kW with 670 Nm of torque.
The difference for the off-road capability is that the skateboard platform uses an independent air suspension system that varies the height of a truck above the ground between 20 and 36.5 cm. The height is automatically adjusted depending on the weight in the back of the pick-up, which can carry loads of up to 4990 kg. The suspension also uses active damping, which monitors road conditions and driver inputs every 5 ms, and adjusts the damping rates accordingly.
For safety, the conventional anti-roll bars in a pick-up design are replaced by an electro-hydraulic roll control system that also varies the body roll depending on whether the vehicle is on a paved road or off-road. Underneath the skateboard is a layered shield of high-strength steel, aluminium alloy and carbon fibre to provide the required strength and torsion for the bodywork while reducing the weight compared with a full steel chassis.
Skateboard for trucks
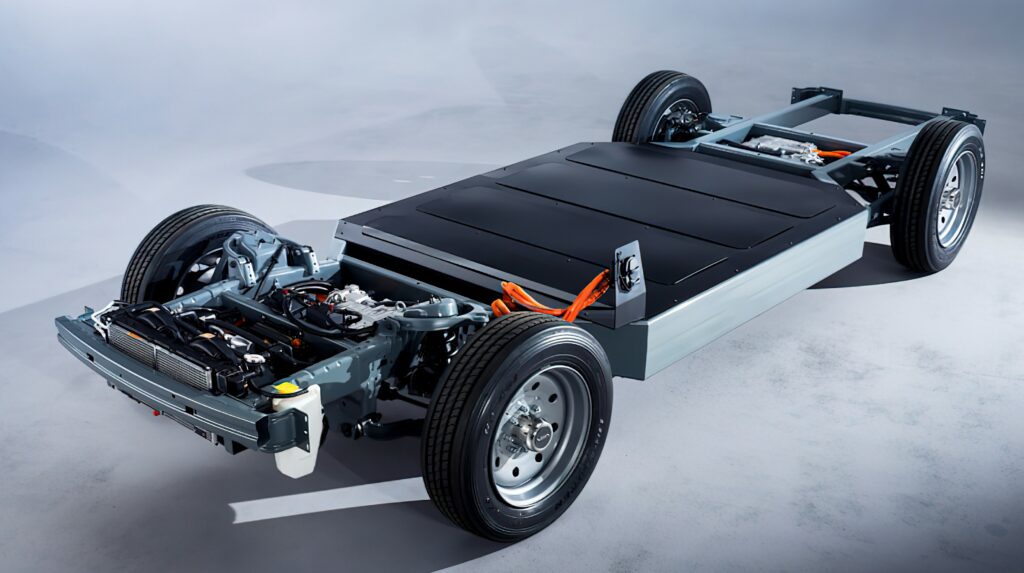
(Courtesy of VIA Motors)
VIA is developing a skateboard platform for light trucks. It has simulated the range of mass loads for a variety of trucks to ensure that the skateboard chassis will be strong enough to support a range of possible vehicles. This analysis of a digital twin of the skateboard has resulted in a modular front-wheel-drive design to provide sufficient traction regardless of the type of bodywork added on top.
The two-part chassis is built from standard-specification steel rather than specialised materials to keep costs down. The front section measures 500 mm long and 680 mm wide for the cab, with a crush zone measuring 475 x 820 mm. The rear section is 640 x 780 mm to support the load, and has a crush zone measuring 625 x 950 mm.
VIA uses a traction system that combines the motor, inverter and transaxle gearbox. This allows the three elements to share high-voltage cabling, reducing the amount of copper required and simplifying the thermal cooling design. The simplicity also reduces the complexity of constructing the chassis.
The skateboard’s battery section measures 2130 mm long by 1600 mm wide, to provide as much space as possible for the power required for a truck. This provides up to 100 kWh of energy with a weight of 650 kg in a volume of 680 litres. An 85 kWh variant would give a vehicle a range of 200 km on a single charge.
The skateboard design is supported with a choice of charger, with a 7 kW AC system or 150 kW DC charging. This will support a range of different charging options that are needed by operators of fleets of trucks, whether charging in the depot overnight or opportunity charging quickly at its destination while delivering a load.
The digital twin analysis also includes an assessment of the performance of the battery pack in a crash with the protection of the other modules and the crash zones to ensure that the battery pack remains intact to avoid the risk of fire from a ruptured lithium-ion battery cell.
As flat as possible
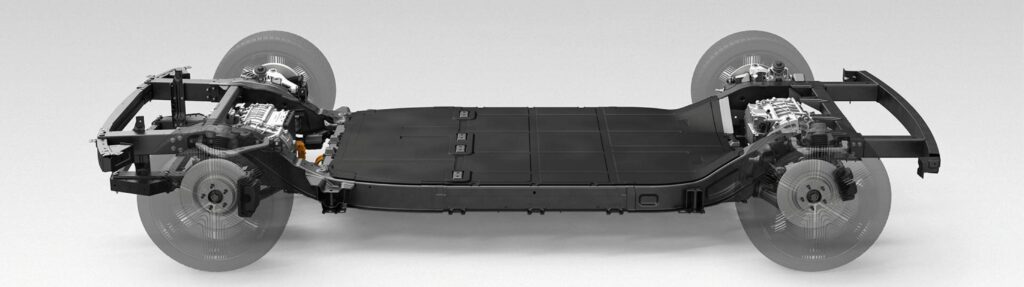
(Courtesy of Canoo)
Canoo in the US has focused on making its skateboard platform as flat as possible as well as enhancing the electronic steering controls for urban light truck designs.
The powertrain and suspension were developed entirely in-house, with options for dual, front or rear motor configurations with up to 500 bhp. The rear primary unit is designed to deliver a maximum 300 bhp and 450 Nm of torque, while the front unit is designed to deliver a maximum of 200 bhp and 320 Nm. The efficiency of the motors is designed to peak at 97% in low-speed urban driving.
To get the skateboard as flat as possible, a transverse composite leaf spring suspension system was designed. This uses a double wishbone with two glass fibre leaf springs, mounted transversely in the front and rear of the platform. The dampers are mounted to the frame, eliminating the need for large shock towers that take up space for cargo. The entire suspension system is incorporated into the skateboard rather than being a separate module, and sits below the height of the tyres.
The steer-by-wire electronics support a software-programmable ratio control system to customise the lock-to-lock ratio, for example for tighter turning for smaller delivery trucks. Like the original GM design, it also allows the steering wheel to be placed anywhere in the cabin.
The company has also designed its own battery compartment and battery thermal management systems, power electronics, vehicle controls and crash absorption structures.
A wheel at each corner
REE has taken the skateboard approach a step further and developed a platform with all the functions, from the motors to the controllers, integrated into a wheel unit.
Its REEcorner X-by-wire technology integrates all the critical vehicle components – steering, braking, suspension, powertrain and control – into the arch of each wheel. This allows a completely flat and modular electric chassis, and provides customers with full design freedom to create a wide range of EVs.
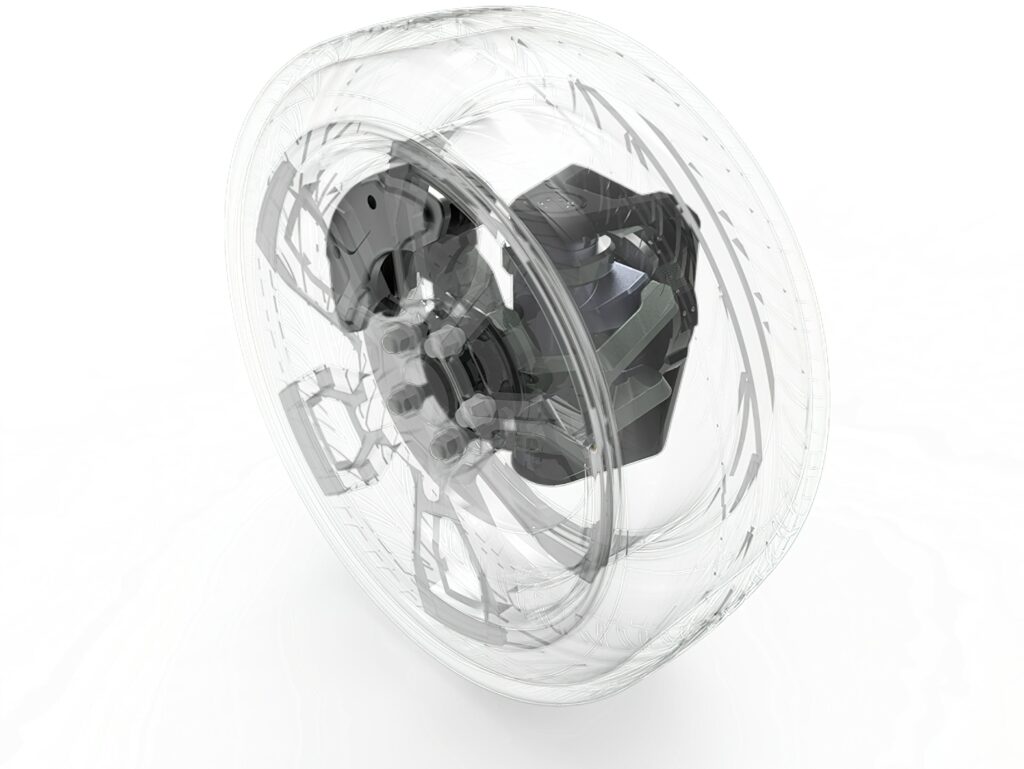
This use of the wheel arches gives maximum flexibility with the design of the rest of the EV. As a result, the company has developed seven platforms of varying lengths and widths for different types of EV, from cars to pick-ups and light commercial trucks.
REE has developed three prototype platforms that represent separate future use cases: a 4.5 ton delivery van, a 2.5 ton passenger and cargo transport, and a 1.3 ton last-mile delivery buggy.
The smallest of the seven variants is 3395 mm long and 1475 mm wide, with a maximum height for the bodywork of 1915 mm and a gross weight of 1110 kg. This would carry a load up to 350 kg.
All the variants have a relatively small 400 V battery with a capacity of 20 kWh, although REE says this will still give a range of 220 km. The 47 kW motors in each wheel provide 1800 Nm of torque.
The largest chassis in the range measures 6010 mm by 1995 mm, and gives a height of 2600 mm for the bodywork. It supports a 450 V battery pack with a 100 kWh capacity and a gross weight of 7000 kg to carry a maximum load of 4000 kg.
REE says customers don’t necessarily have to be a car company or have a long-term legacy of developing drivetrains and traction control. Instead they could be companies focusing on premium bodywork or rugged off -road or utility applications such as refuse carts or construction trucks.
As a result, REE plans to have 300 partner production lines across the world, making use of their spare capacity rather than building new lines. The skateboard chassis and bodywork would be combined at an ‘integration centre’ in a process that does not require heavy machinery, allowing the assembly to be closer to customers. Each integration centre is planned to have a capacity of about 20,000-30,000 platforms a year, with the first being set up in the UK this year and followed by one in the US.
ONLINE PARTNERS
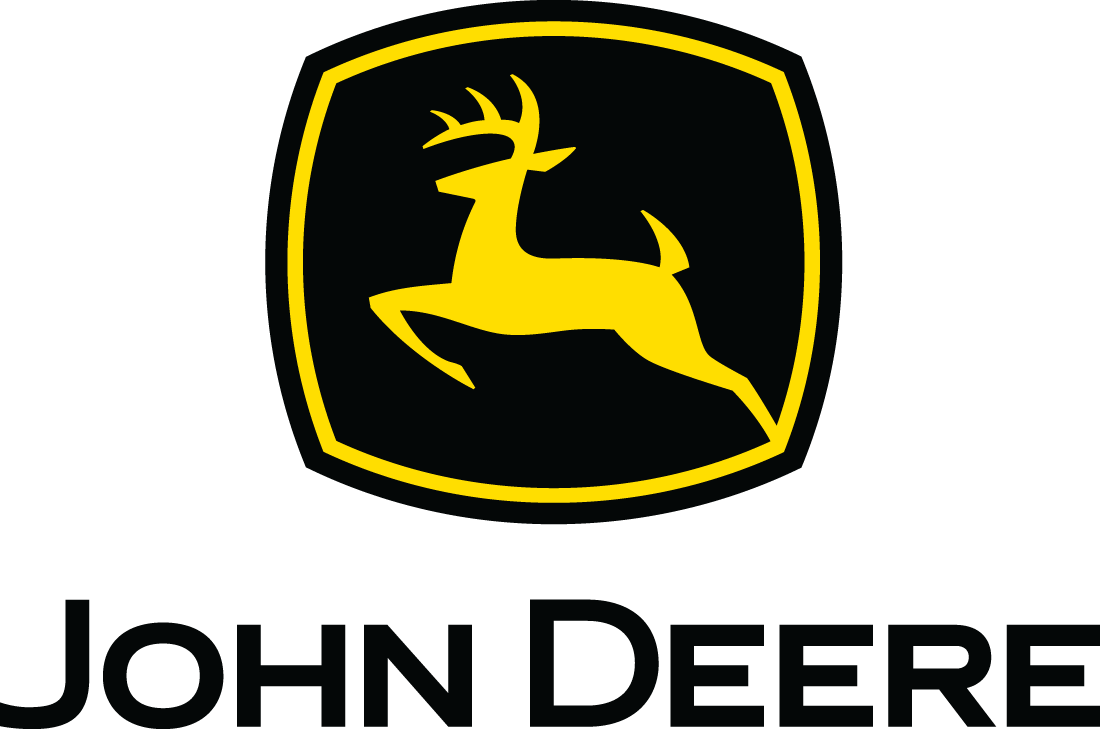
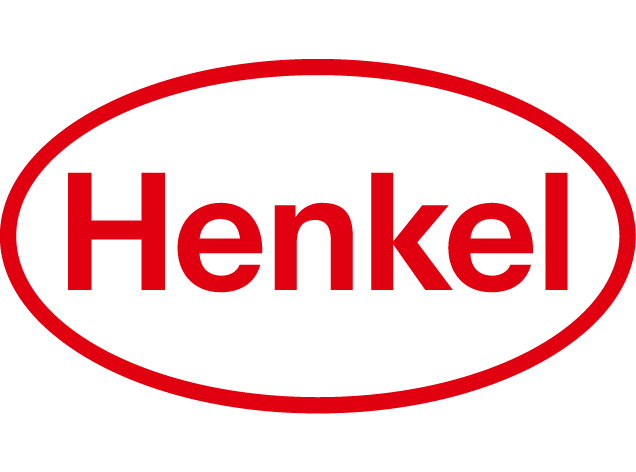
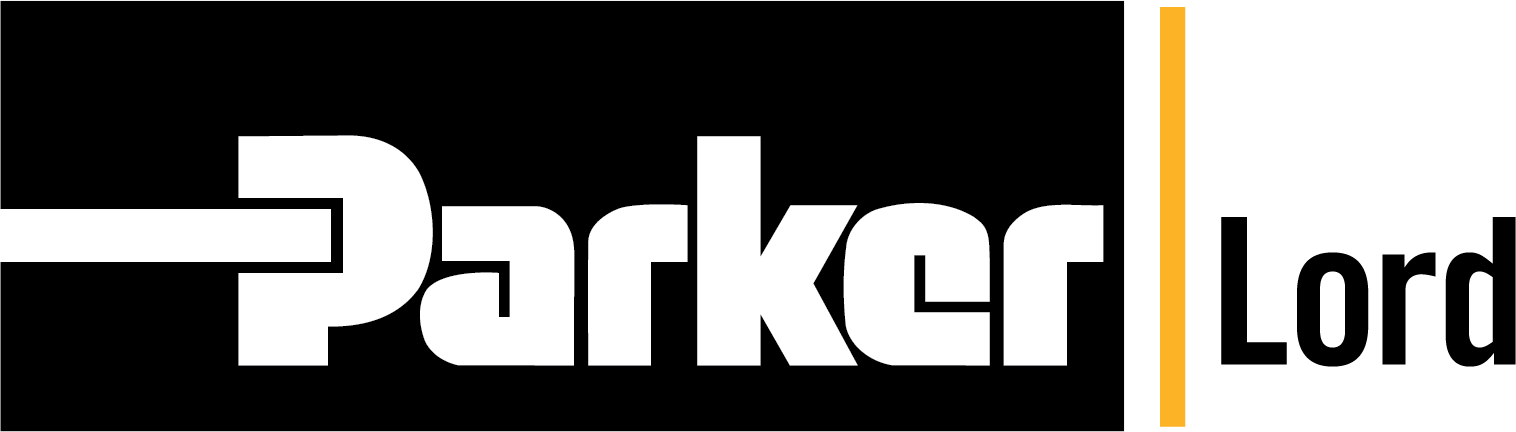
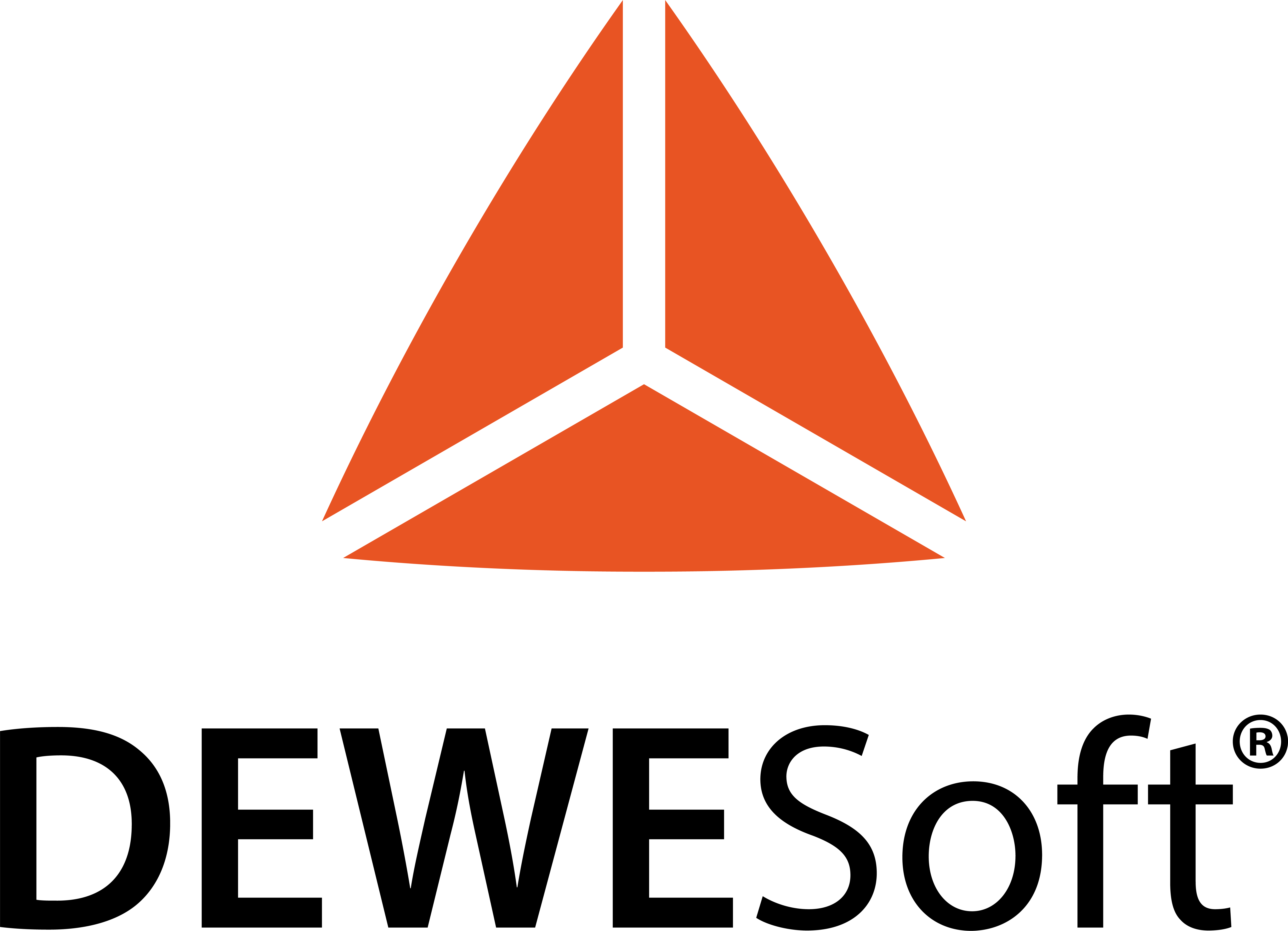
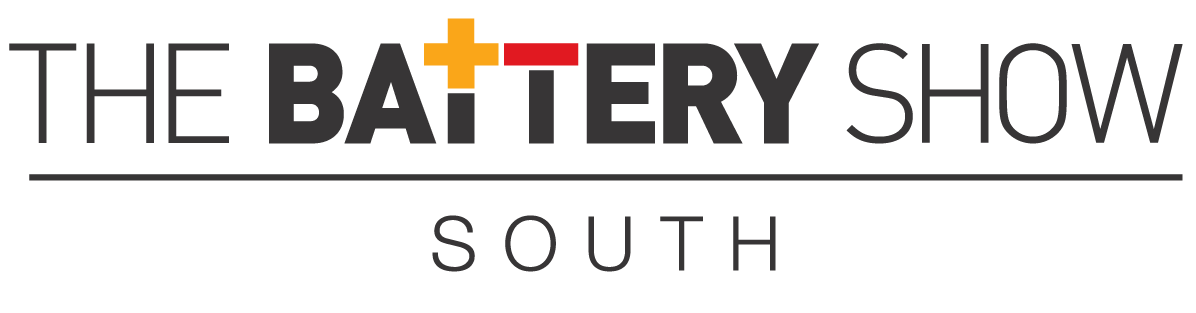
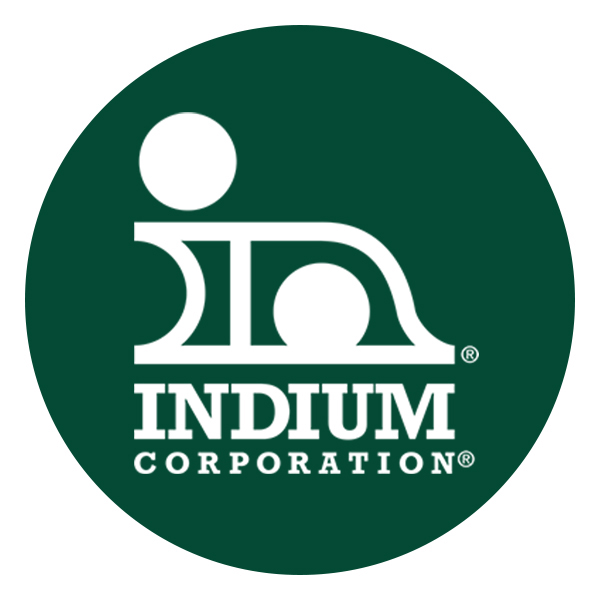

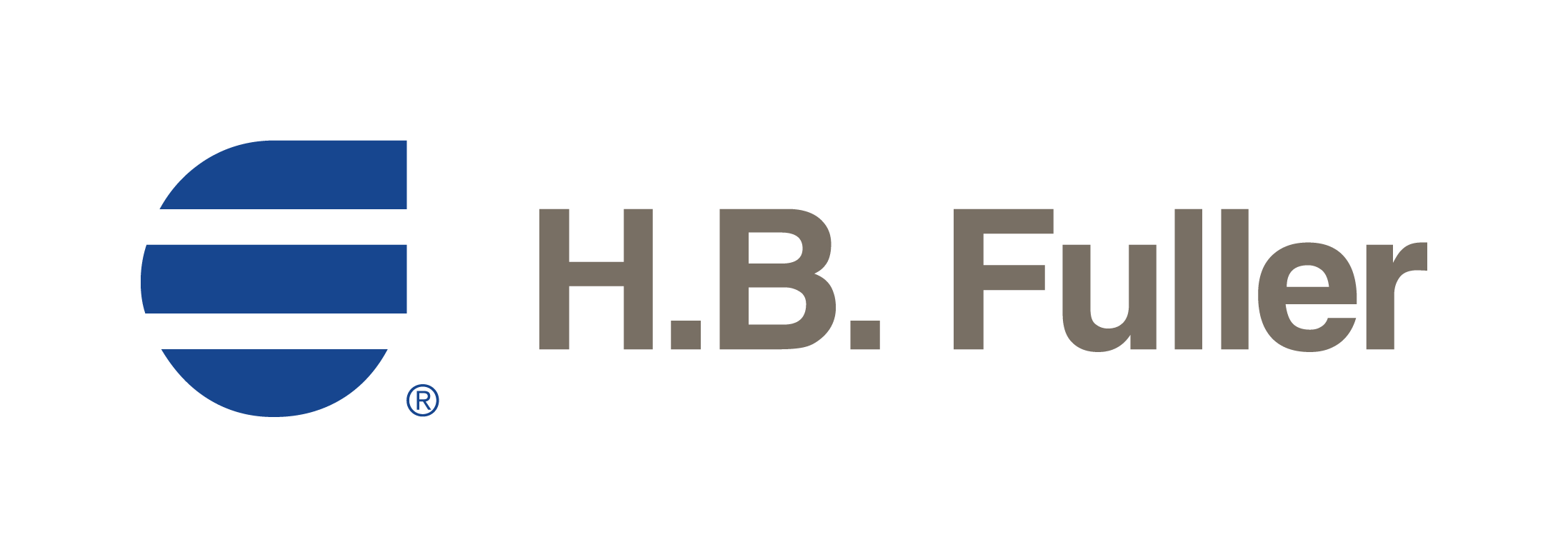
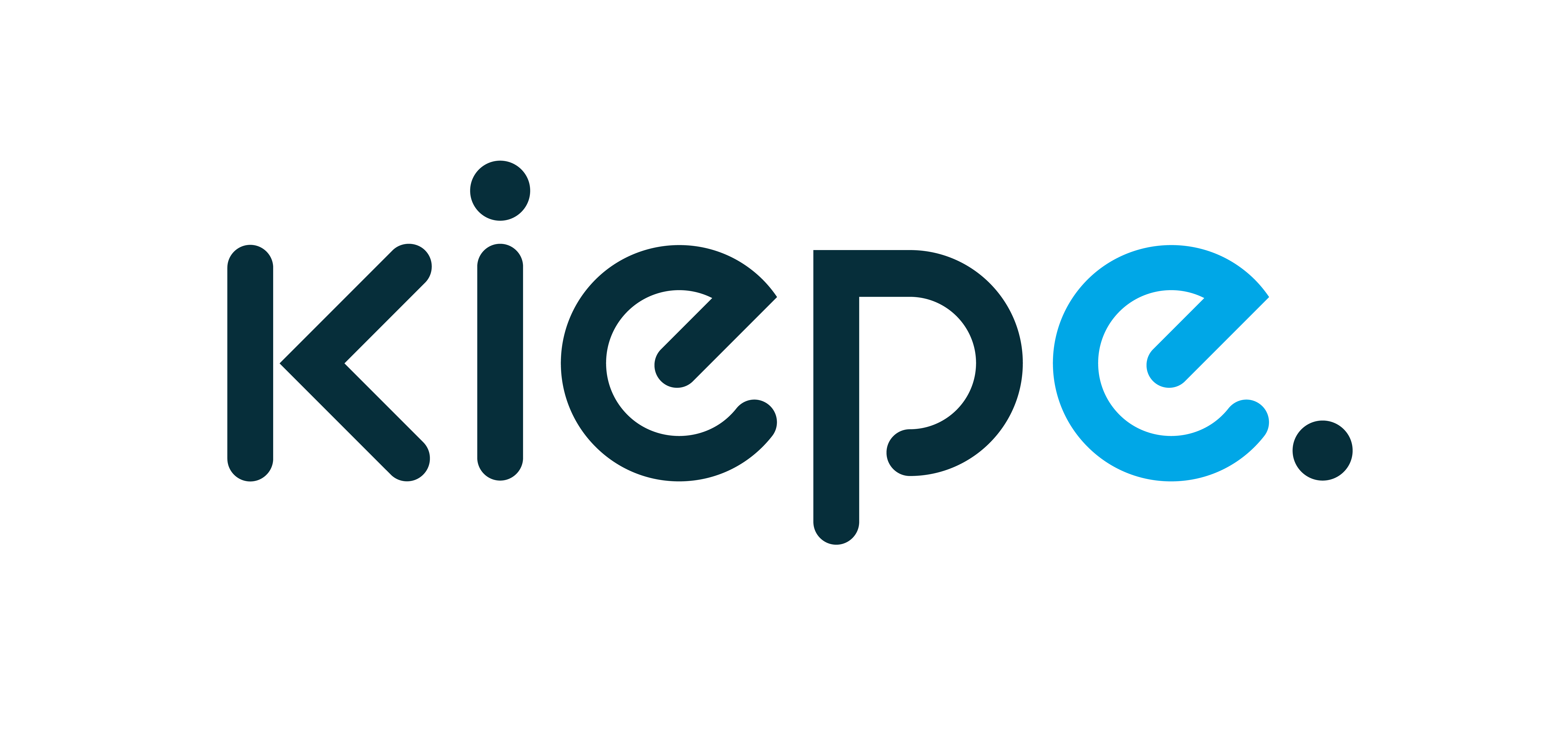
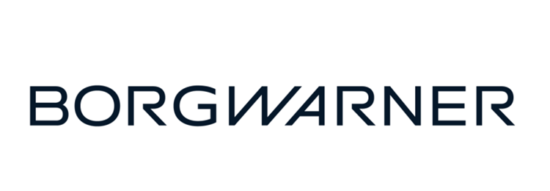