Kiepe mining vehicle electrification
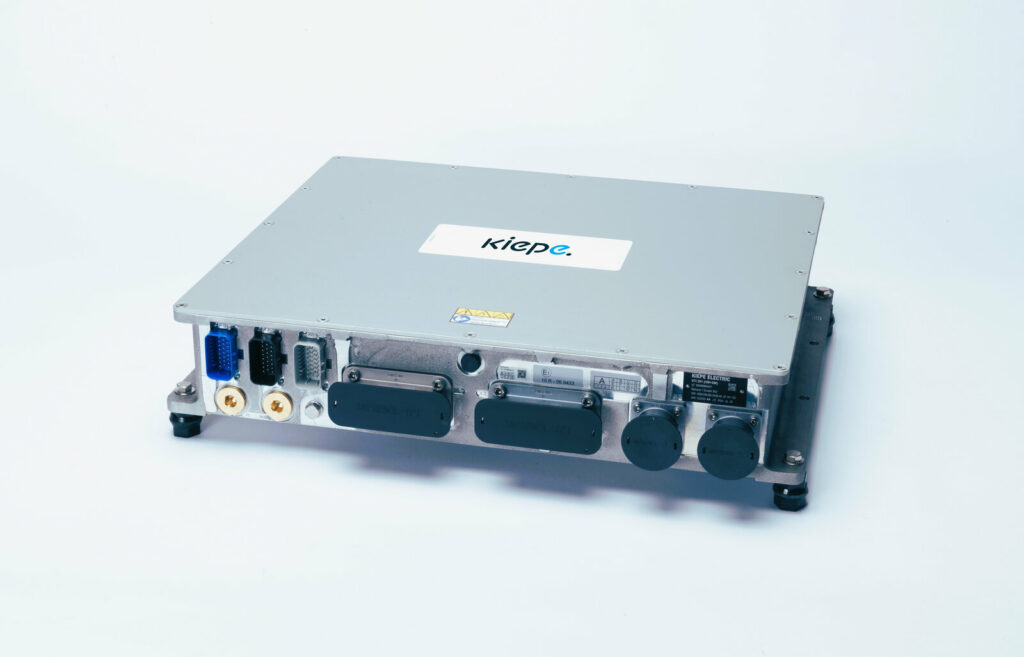
(Image courtesy of Kiepe)
Kiepe Electric is advancing the electrification of heavy-duty mining vehicles by leveraging its expertise in traction inverters, regenerative braking, thermal management, and system integration, with an emphasis on efficiency, durability, and seamless integration, writes Peter Donaldson.
In dual configuration, the IGBT-based Kiepe Traction Inverter (KTI) supplies two motors with a combined output power of 400 kVA (2×200 kVA), while weighing only 25 kg, and is compatible with both synchronous and asynchronous motors. “This high power density makes it one of the most efficient solutions available for heavy-duty mining applications,” says Daria Baryshnikova, Kiepe’s VP for modernisation, service and products.
Additionally, Kiepe’s DC-to-DC traction converters, which are widely used in rail applications, can also be adapted for mining vehicles.
A critical component of the company’s electrification package is its regenerative braking system. “This capability is particularly beneficial in steep-gradient mining environments, where frequent braking is required, significantly improving energy efficiency and reducing overall power consumption,” Baryshnikova notes.
Liquid cooling
To address the heat generated during fast charging, Kiepe employs a liquid cooling system. This approach is significantly more effective than traditional air cooling, ensuring stable operation even in extreme ambient temperatures. “Our charging systems are modular and scalable, allowing the possibility to make solutions on demand in order to adapt to different depot infrastructures and charging needs. This flexibility ensures that the thermal management system can be tailored to specific operational requirements, more efficiency and less downtime.”
Kiepe integrates CAN J1939 communication protocols into its vehicle control units to facilitate real-time monitoring and predictive maintenance. Its Smart Fleet Management (SFM) system collects process data from the vehicle’s CAN network, which is then analysed in the cloud. This enables operators to optimize maintenance schedules and operational cycles, reducing the total cost of ownership by minimizing unplanned downtimes.
Mining environments expose vehicles to severe vibration, shock, and dust. Kiepe’s components are engineered to withstand these conditions through the use of robust materials, including aluminium alloy and stainless steel enclosures with high ingress protection (IP) ratings up to IP6K9K. Compliance with ISO 16750 and EN 61287-1 standards ensures long-term durability and operational reliability.
Kiepe’s power electronics systems comply with electromagnetic norms such as EN 50121-3-2 and UN ECE R10, ensuring minimal electromagnetic interference (EMI) even in environments with heavy machinery and communication networks. Comprehensive simulations and system-wide tests, conducted using the company’s in-house 1.5 MW test bench, guarantee seamless component compatibility and adherence to industry standards.
“The systems are engineered to provide easy access to critical components, to ensure that technicians can quickly identify an issue and repair it, “Baryshnikova says. “They include advanced diagnostic tools/software that continuously monitor the performance and behaviour of the components.”
Innovation and r&d
Looking ahead, Kiepe is focusing on digitalisation and connectivity to further enhance the performance and safety of mining vehicles. The company is developing next-generation DC/DC converters using advanced silicon carbide (SiC) semiconductors to improve efficiency and power density. Additionally, the evolution of its Smart Fleet Management (SFM) system will continue to refine vehicle diagnostics and energy management.
ONLINE PARTNERS
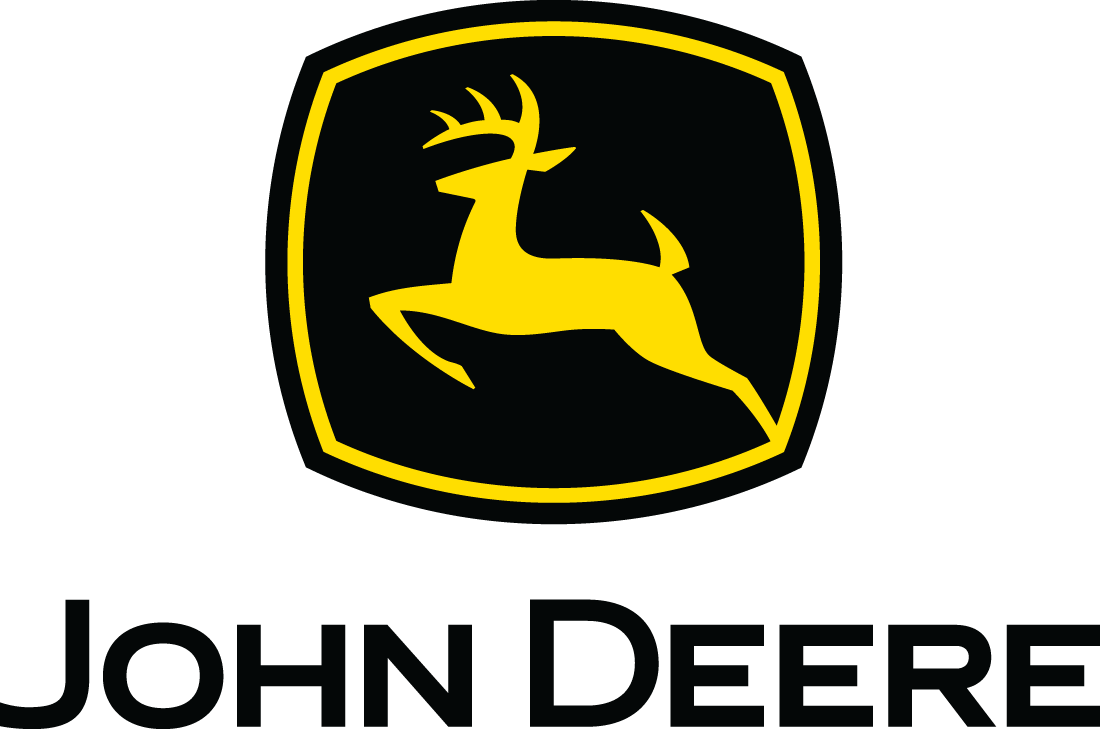
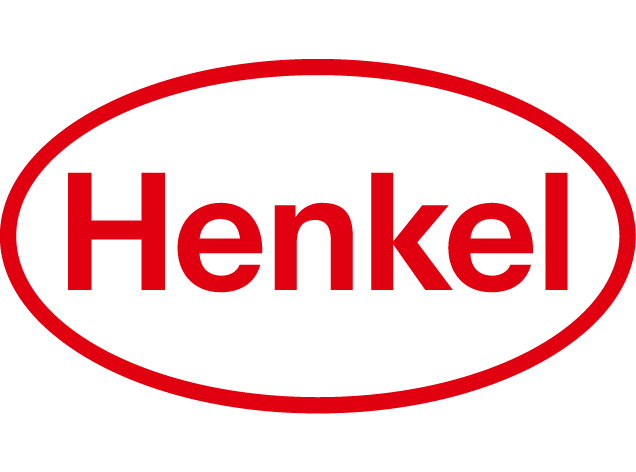
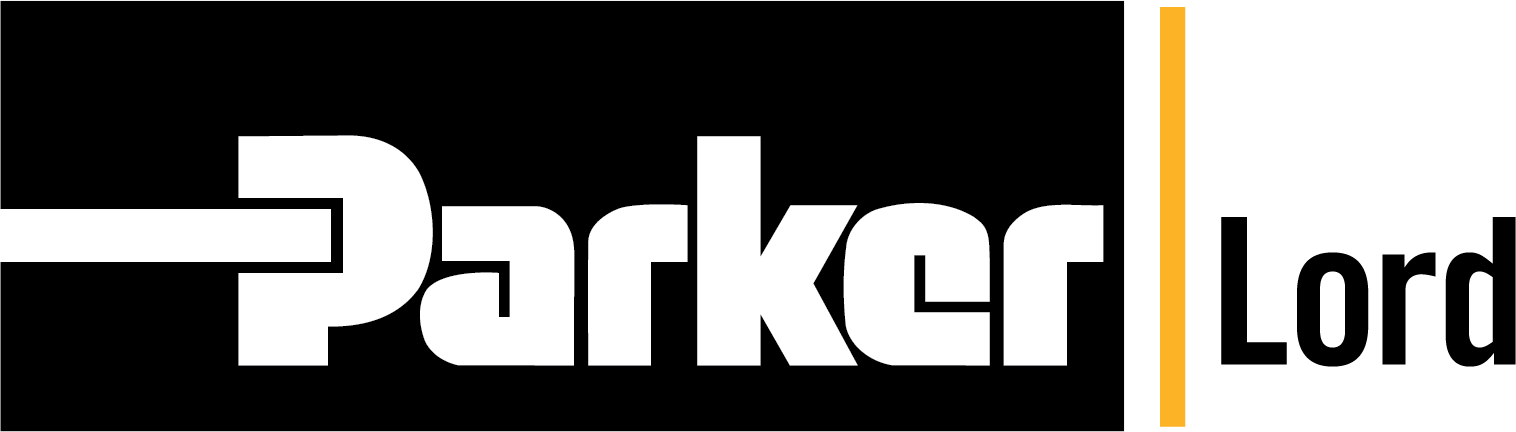
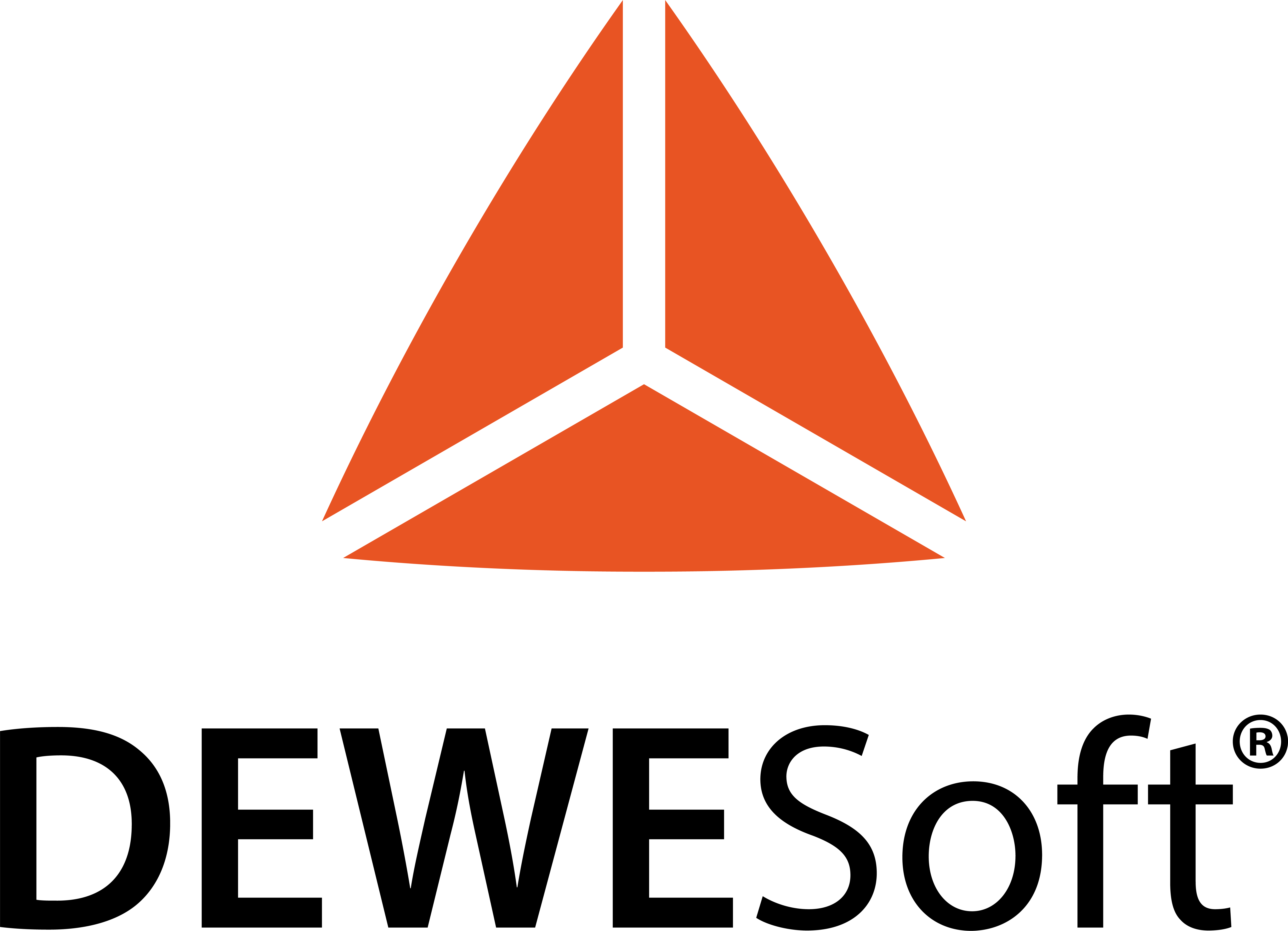
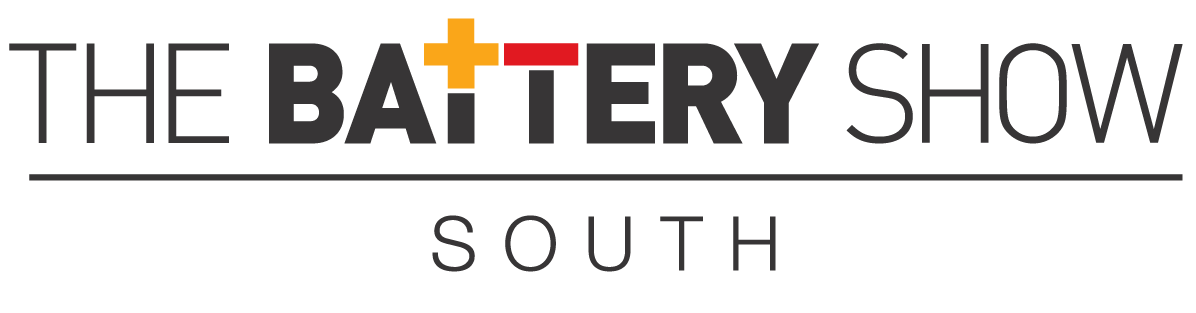
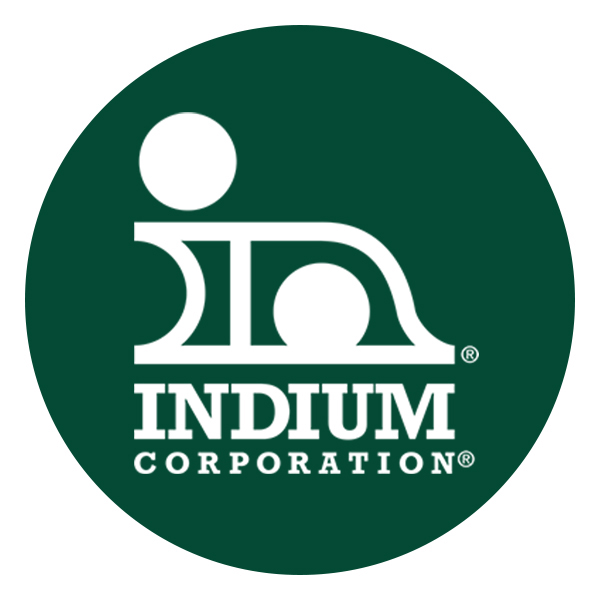

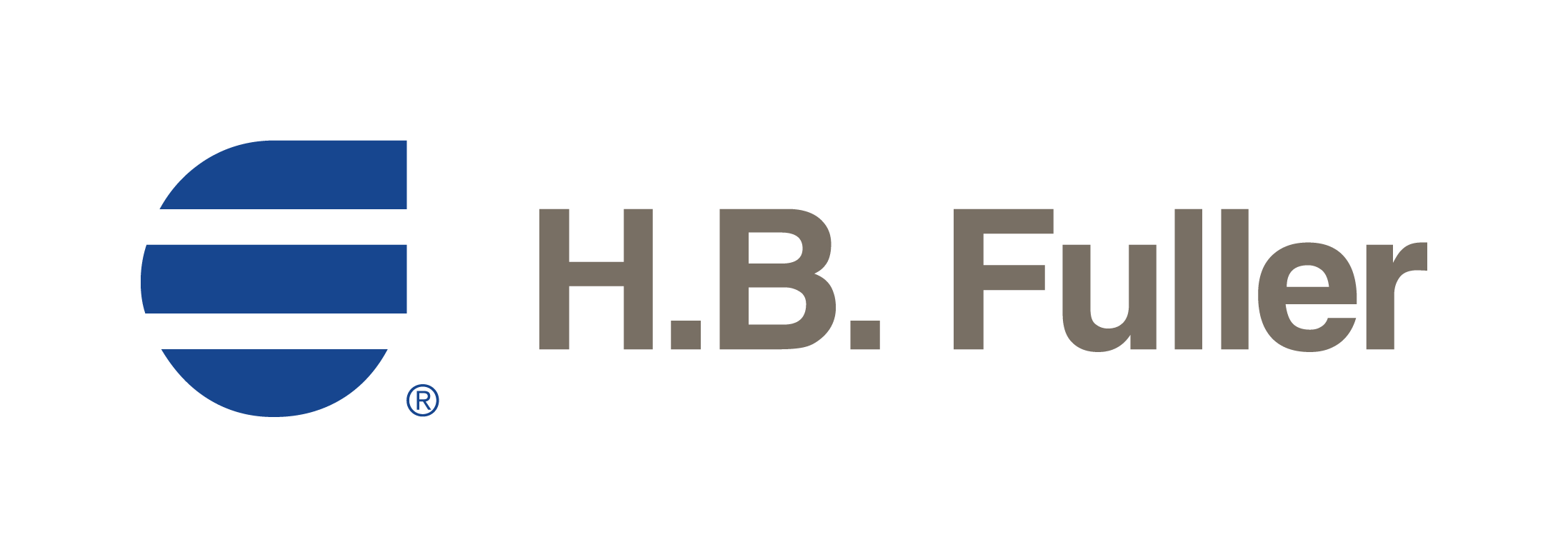
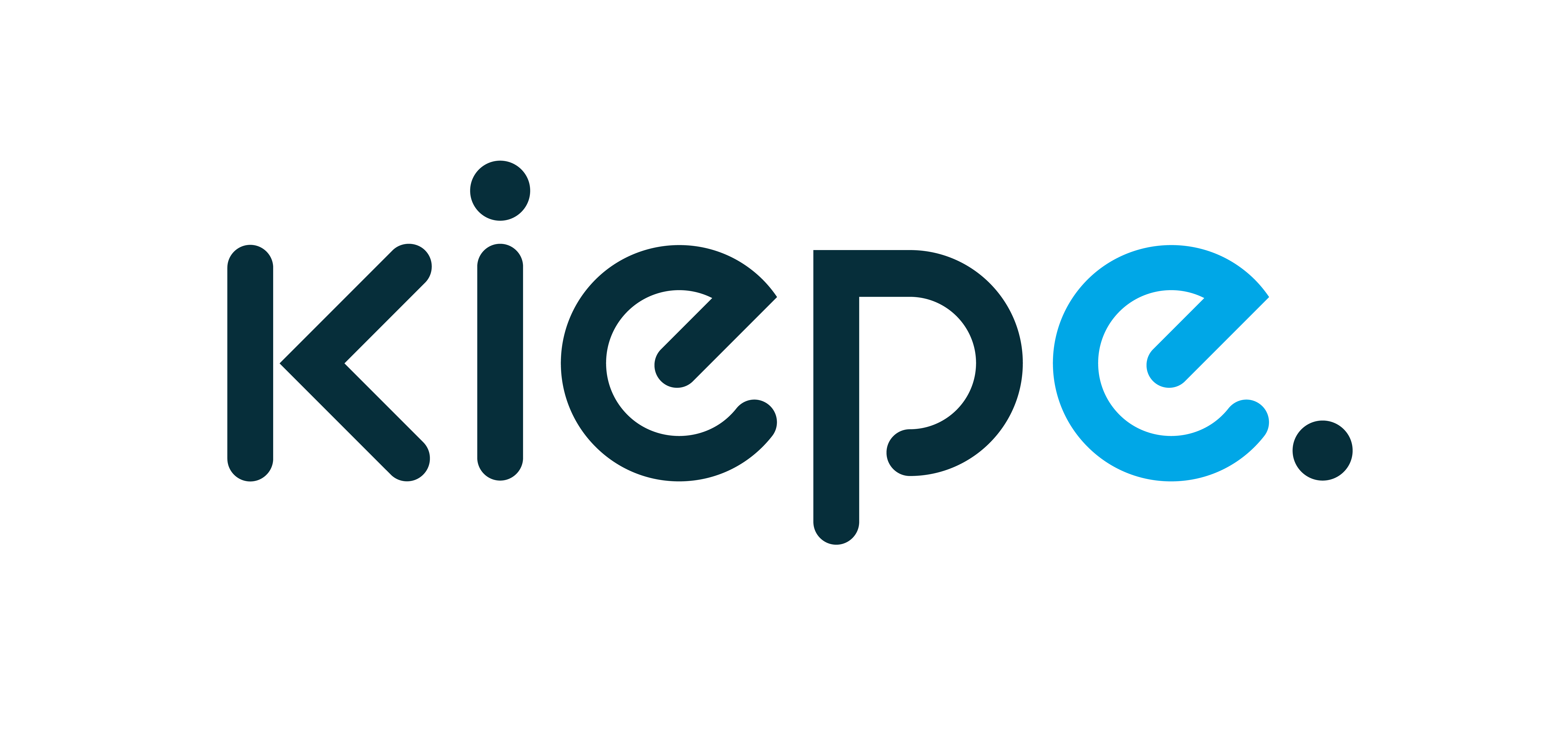
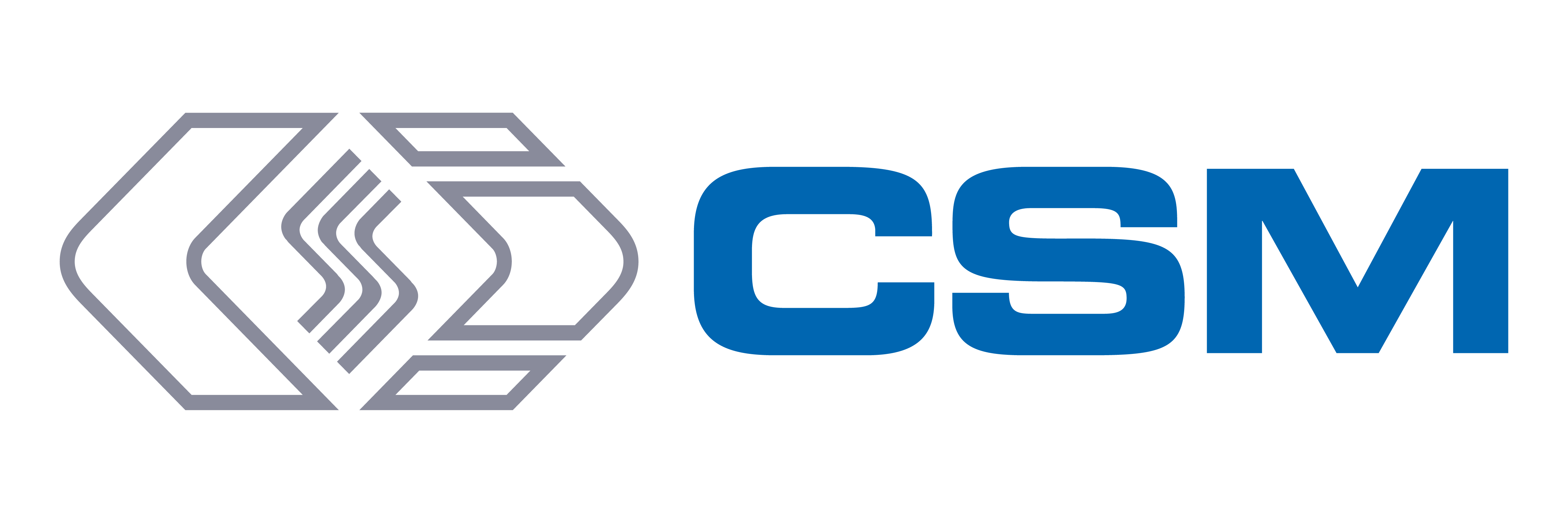