Evice Rolls-Royce Corniche
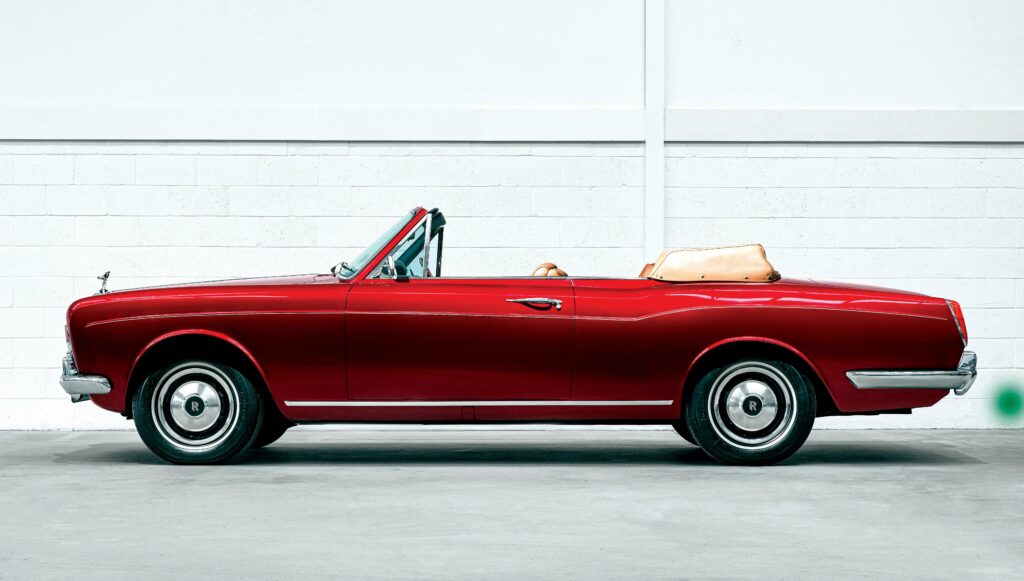
(Images courtesy of Evice)
Reinventing a legend
Evice is using modern technologies and EV powertrains to improve some of the best cars ever built, starting with a beautiful Rolls-Royce Corniche, reports Will Gray
When it comes to pure, opulent luxury, there are few more iconic cars than those produced by Rolls-Royce in the 1970s and 80s. In an era defined by the growth of wealth and a desire for social standing, these were seen by many as the best cars in the world, the ultimate head-turning status symbols of riches and fortune.
The stunning Corniche was immediately snapped up on its release by famous celebrities such as Paul McCartney, Frank Sinatra and Tom Jones, while David Bowie, Michael Caine, Elton John and Dean Martin all queued up on a two-year waiting list. The car’s starring role in countless films and TV series made it a true icon of the era.
Now, beautifully aged into the realms of a modern classic, vehicles such as the Corniche still evoke fond memories of the past and are increasingly sought after by collectors. However, at a time when emissions restrictions are pointing them towards extinction, the only way they can live on is by adopting synthetic fuels or an electric powertrain. Evice is focused on the latter, but its ambitions go far beyond a simple conversion.
“Our intent has always been to make a much-improved version of the original,” says company founder and CEO Matthew Pearson. “These were the automotive pinnacle at one time, and our aim from the start was to see them into the 21st century in a completely different light.
“A lot of restoration and conversion companies talk about redefining what the car is, but that’s not what we’re aiming for. We are focused on looking at incredible cars that could potentially be made even better with electrification and taking away all the compromises that were made in the originals.
“We want to create classic cars that have zero impact at the place they are used, but we also want to develop great technology that proves an electric future can be exciting and better than what we have come from. That’s how we ended up with the Rolls-Royce and Bentley aspirations, because we feel these classics are even better as electric cars.”
The company’s three co-founders – CEO Pearson, COO Charlie Metcalfe and CTO Will Burdett – met at Bath University on a mechanical engineering course. They went their separate ways, working at different companies in different industries, including stints in the high-end EV conversion world, before reuniting to create their own car company.
Burdett has the most technical EV experience, having always worked on powertrains and in vehicle engineering, while Pearson specialised in leading engineering programmes across the automotive, aerospace and materials industries. Metcalfe, meanwhile, has a unique Formula One pedigree, having led track design and management for the Miami Grand Prix.
“In a previous life, we would have certainly referred to ourselves as petrolheads, but now we describe ourselves as car enthusiasts,” quips Pearson, who admits to still having a passion for ICE-engined vehicles, despite acknowledging the future of automotive is electric.
“When the three of us sat in a pub in Oxford and asked, ‘What do we want the car of the future to be?’, we all agreed it should look like a beautiful, classic car with chrome bumpers, combined with modern technology, and the ability to drive through city centres or in nature and leave it as it was found; no oil dripped down the road, no smoke belching out the back.
“What is definitely different with Evice is that the founding team are technical, so we have an understanding of not only what a car requires to go together, but what it takes to make a car at the end of the process a really great product, and not just a forklift powertrain in something else’s body that technically functions as a car.”
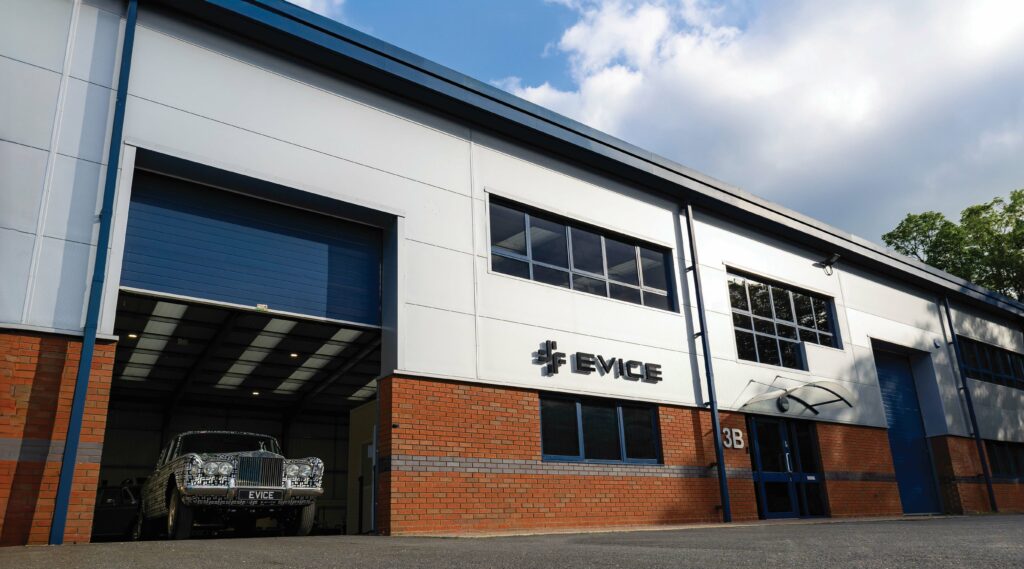
New-build approach
Evice currently employs 11 people at its 6,500 ft2 home in Surrey, comprising an engineering office, a sealed-off, clean, battery build room, and a workshop and stores. Only founded 18 months ago, it is already a year into the development of its first vehicle, and recently rolled it out of the factory doors to begin slow-speed systems checks before launching a full-scale road-test programme.
While the company essentially operates within what Pearson defines as the “electric resto-mod” industry, its founders see it as an entirely new-build constructor that is operating “as close to an OEM process as an 11-person company can do” when it comes to its design, build and development approach.
The restoration and EV conversion industry is, Pearson says, a rather catch-all definition that needs redefining: “There is nothing in common between a company doing an £80,000 conversion, or those saying they can do one for £30,000 or less, and companies – where all three of us used to work – selling million-pound-plus cars.
“In our previous jobs within the industry, we saw no shortage of sales and interest coming through, but we saw a real inability to take a car from rolling in as a combustion car to actually delivering something worthy of the price point at the other end, and one of the main issues we saw was that vast swathes of the r&d process were being skipped.
“Every conversion car, being a prototype, means you have to start from scratch almost every single time, so you can’t leverage economies of scale. Companies often make the mistake of not getting the foundations set properly or the core technology right, and also lack focus on how many different vehicle programmes to do.
“At the low end of the market, you’re looking at second-hand components pulled out of Teslas or Nissan Leafs, secondhand batteries and things being put together very much by hand, but not always in the nice, artisanal way. There’s no bespoke software. It’s all a combination of pieced-together OEM systems.
“Our approach is very different in that we treat every build like a brand-new car. We know that the end result has to be, in every single way, a world-class, incredible car – not just an electric version of something that once had an engine. The fact that we’re using a car that once had an engine is a small part of the overall process.
“That means stripping and restoring the vehicle, keeping everything that we want to keep, and sticking within the rules and regulations that the DVLA has, but then really designing and innovating in every single area, from the powertrain, software and battery designs to the sound management, interior design and technology, and not just thumbing systems in.”
In the case of the company’s first prototype car, the R001 Silver Shadow, all that remains of the original vehicle is effectively a rolling chassis plus a small amount of interior structure. When it comes to weight, the car began at around 2.2 t, had 1 t of old technology taken out and around 1.1 t of new parts added in.
Development is limited by what is permitted in the regulations for classic cars, which apply to any car built over 40 years ago. But, over and above the addition and integration of the electric powertrain and ancillaries, the team has sympathetically modernised as much as possible while retaining all the features required to keep the original registration of the car.
“Working with a classic car, we are able to do things that the modern car companies just cannot do,” says Pearson. “All the design features that classics are loved for, like beautiful chrome bumpers, we don’t see on modern cars because they’re not allowed. They wouldn’t pass the tests, which have been predominantly mandated by insurance.
“Nowadays, bumpers have to be replaceable, and if you have a 5 mph impact, for example, you have to make sure you do not write off your radiator. We are able to make the car safer and better in performance in many ways, but we can also retain the look of that real, golden age of car design before it effectively became controlled by insurers.”
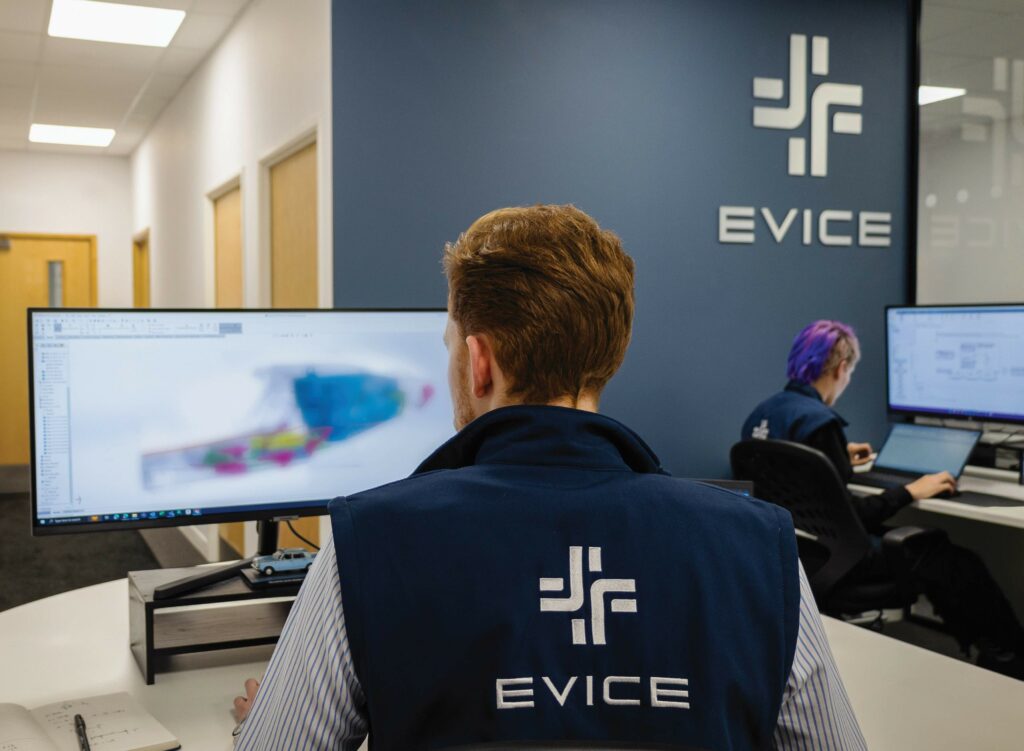
Performance, as it should be
The original Corniche came with a 6.75 litre, overhead valve, V8 internal combustion engine, known as the L410, coupled to a three-speed automatic transmission. In 1977, this was upgraded with fuel injection to become the L401I, which produced 237 bhp at just above 4,000 rpm and reached a top speed of 118 mph.
In contrast, the new electric powertrain comprises just one single rear-wheel-drive unit, producing a power output of 400-500 bhp, depending on the battery pack size. It is all designed around a proprietary, 800 V electric architecture, which can be fitted into everything from the four-door Silver Shadow through to the flagship Corniche.
The decision to opt for cutting-edge, 800 V architecture, and to design and build the system in-house, was made with a long-term view. In a project where the budget is near unlimited, it made sense to target the gains offered by 800 V. By creating it in-house, owned IP and design offers ultimate flexibility.
“This is about building cars for the future and we want to put in the very best technology we can,” says Pearson. “Moving from 400 V to 800 V gives you all those cumulative marginal gains that ultimately end up creating a better system.
“We want to be part of developing and demonstrating the technologies that people want to be using in the next 10 years, rather than what has been used for the last 10. But, if, from a third party perspective, a company wanted a 400 V system, it’s very adaptable to scale our battery packs, and change the systems and components to work at different voltage levels.”
He says the company would not have been able to develop to the 800 V architecture if it had started even one year earlier, as the supply chain for this niche classic-car application did not exist. As a result, the company is pioneering the way in this space. “We are really the first to do it properly and it’s a very exciting place to be,” he adds.
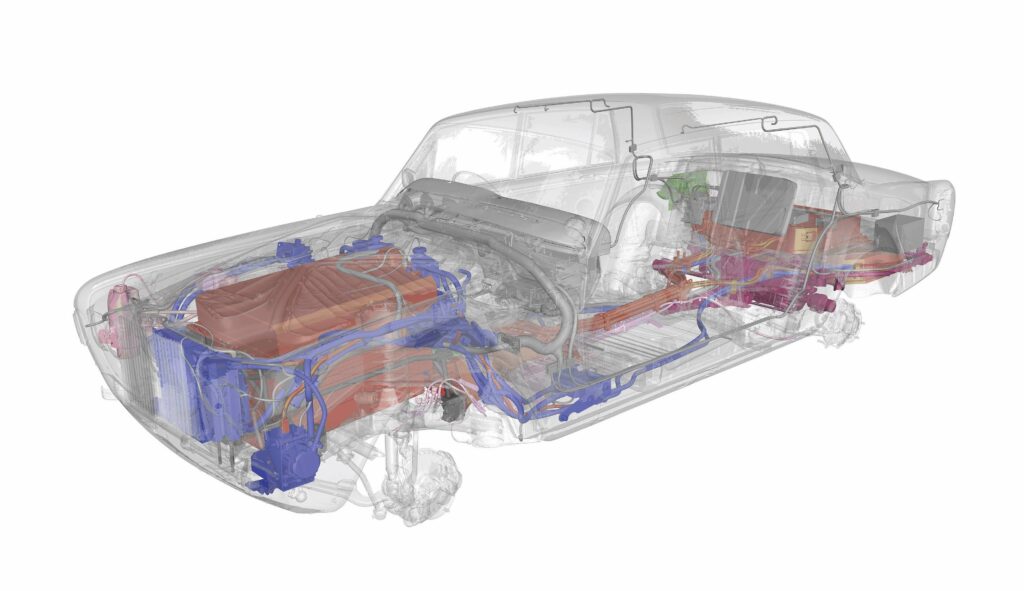
The powertrain layout was one of the first considerations, with the aim of retaining the rear-wheel drive of the original car, as that best suits the suspension and driving characteristics. The team carried out feasibility studies on two potential layouts, eventually choosing a rear-axle, direct-drive solution over a front-mounted, propshaft-coupled unit.
Pearson explains: “We chose the direct drive due to the reduction in overall powertrain mass and reduced overall packing volume, which meant we could use the gearbox tunnel and propshaft position for other systems. Fewer rotating parts also meant there was reduced noise, vibration and harshness, and improved powertrain efficiency.”
The team consulted a variety of motor and gearbox suppliers, and ultimately selected a combined drive unit that includes a park lock. The unit used on the first two prototype vehicles contains an open differential, but the production cars will feature a locking differential and a higher torque output, giving broader access to the available 400 bhp (and above).
Helical cut gears will also be used for the single-speed transmission, which promises superior noise, vibration and harshness performance with a zero-perceivable backlash when changing direction. Temperature is managed by a water ethylene-glycol coolant system, with an oil cooler on standby if high-temperature testing shows it is needed for reliability.
Bespoke driveshafts connect directly to the rear wheels, with the motor installed via a bespoke anti-vibration mounting system. The in-house developed Motor Control Unit controls regenerative braking, hill hold and cruise control via the inverter through the bespoke software.
“Across the board, almost all of the software is ours,” Pearson explains. “We’ve had a fantastic software engineer working with us from day one, and we have a second starting in December, who is going to come and help take it from initial driving software to full-function software, through all our safety tests.”
“Everything is designed to the spirit of ISO 26262 road vehicles – functional safety standards – which is a real rarity in this industry as it is relatively underregulated. We own all that software, and it’s vital for us to be able to control it, be confident in its safety and, potentially, to be able to apply it as a software product to other clients as well.”
Outside of the standard park, reverse and neutral drive modes, which mimic what was available on the original vehicle, the company has added its own specific engine-mapping modes. However, where Tesla has its ‘Ludicrous Mode’ for extreme power-dumping performance, the Evice options are, well, a little more refined.
“We have a touring mode and a spirited mode,” Pearson says. “It isn’t an eco mode, it isn’t a sport mode; it’s about minor variations on a theme and still driving like a Rolls-Royce should. So, they just very subtly change the throttle, the way the power is delivered to the regenerative braking and the behaviour of the active dampers.
“If you’re on the motorway and you put the car in cruise control and then into touring, the dampers can relax off completely. That mode is used to make the car incredibly comfortable in steady state situations, while spirited mode gives a bit more throttle engagement, a bit of a heavier steering feel, more aggressive regen braking and slightly stiffer dampers.”
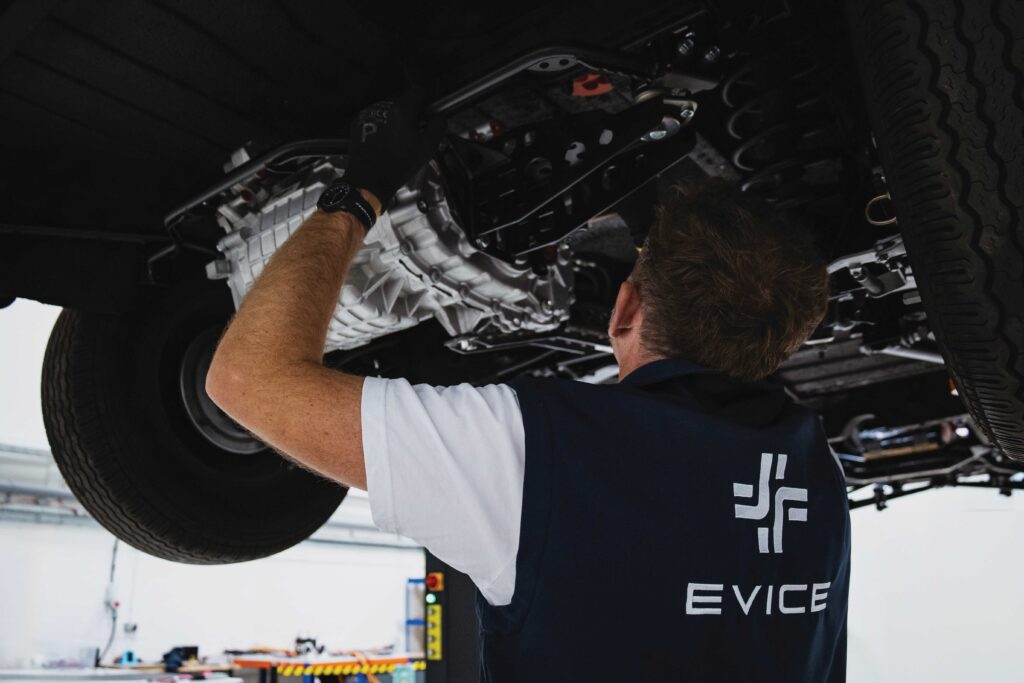
Efficient operations
To provide all this refined and luxuriously delivered power in a safe, efficient and spatially suited manner, Evice has developed its own battery pack and thermal-management system. It uses a single, shoebox-sized battery module, sourced from a Tier One supplier to create two options: a 77 kWh capacity split between two packs or a 94 kWh split between three.
The 77 kWh design comprises 26 modules in the front of the car and seven in the rear, with their positioning based on the original car layout and optimising final weight distribution. This, Pearson says, remains “very, very, very close” to the original, and a final weight that is just 4% heavier than the original makes the effects “virtually unnoticeable”.
He adds: “One of the fun aspects of building an electric car within a classic car chassis is that you have spaces and volumes that were not designed for these parts. This has allowed us to innovate how to efficiently package these batteries and keep them structurally sound to pass modern safety tests, but also be thermally managed.”
The latter aspect, thermal management, is perhaps the most crucial of the in-house design. On day one, Evice clearly identified that its target market meant many potential customers would be located in the Middle East and the USA, putting a priority on the capability to operate at high temperatures.
As a result, the team has put a lot of focus on developing “top secret”, cutting-edge proprietary technology relating to cooling for modern, 800 V EV architecture, which is currently passing through the patent system.
“To achieve reliable, consistent performance, we have to try and maintain a relatively small temperature window,” says Pearson. The team has carried out a lot of simulation testing in this area, developing a solution to manage coolant flow using innovative piping design and active elements across the battery system.
“We’re also doing a lot of r&d on battery temperature over time. We want people to know they can get into the car, turn the key and enjoy it exactly as it is designed to be, so when you turn it off after driving, we keep the battery temperature in an acceptable window for a few days, ready for you to get back in and go. If you don’t return it then goes into a sleep state.”
Temperature management is not only important for performance but also for achieving safe and consistent charging. Active cooling is employed to optimise efficiency and the car comes with two charging options: a 22 kW AC charger with a CCS Type 2 port for EMEA or a NACS port for the US; or a DC-charging solution with software developed in-house.
“We prioritise high-power charging for both AC and DC options,” says Pearson. “The DC charging is where the exciting technology is. To ensure charging in all conditions, we are able to DC-charge on lower power chargers limited to 500 V via a 500-800 V boost-charging system. For higher-power DC chargers, a direct-to-battery system is used.
“In addition to charging type and voltage flexibility, we manage battery temperature by actively heating and cooling when required to keep charging power high. This is an area of significant and ongoing development, with simulation off- and on-car testing helping to refine the software and hardware.
“Our mission is to create cars without compromise, so flexible and high-performance charging options are a big part of this, particularly for clients in hot climates like the UAE. When we tell the customer what charging speed they will get, if the car does not charge at that speed it won’t be the car – it will be because of other off-board charger challenges.”
The final piece of the efficiency jigsaw is the car’s regenerative braking system – another element that presents a significant challenge when it comes to maintaining the Rolls-Royce feel. Again, Evice uses proprietary software to manage the system, right down to dynamically controlling how it blends on and off.
“It is dependent on the application of the traditional brakes, so you never end up with an overly rear-biased braking setup, which would be quite unsettling,” concludes Pearson. “As with a lot of our driving software, this is just the start, and the end result will be the product of a lot of further testing on road and simulation.”
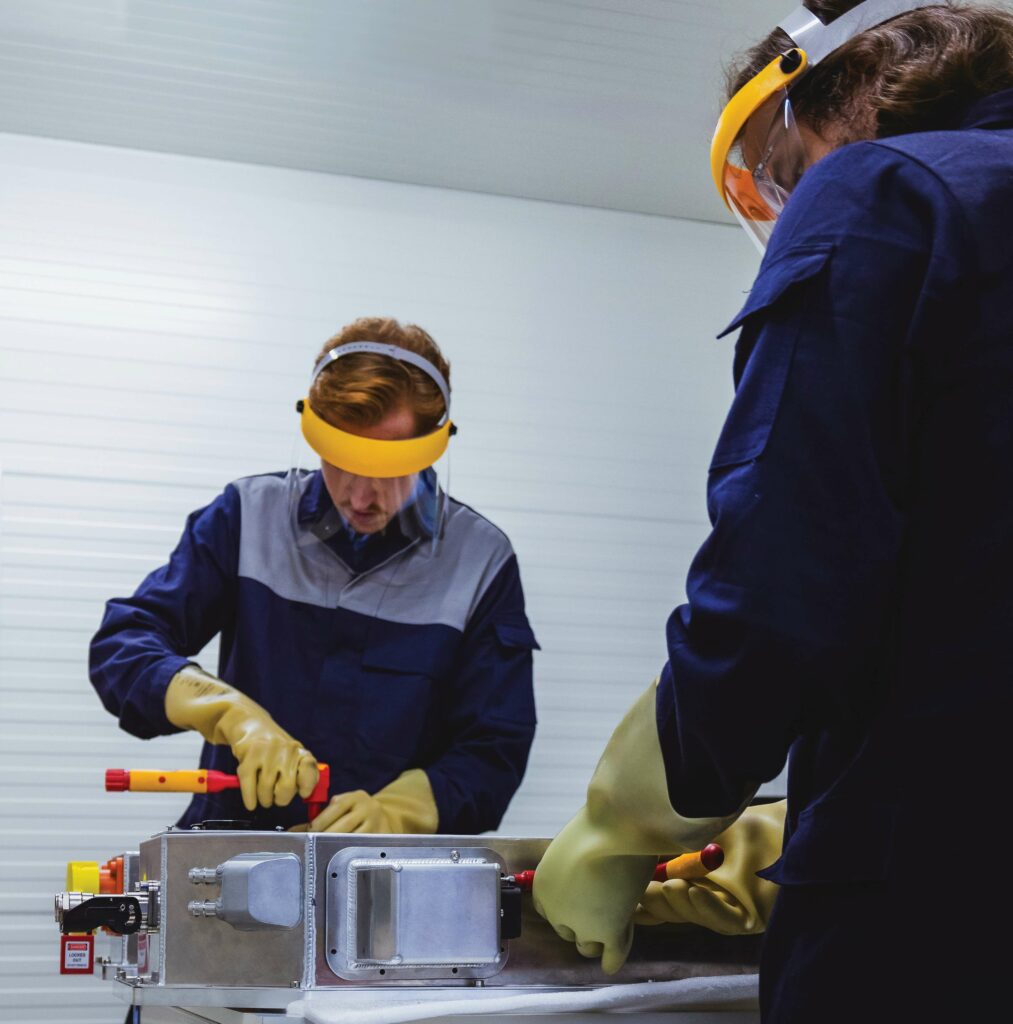
Uplifting the original
As previously mentioned, the integration of the EV powertrain forms just a small part of the development process at Evice, and the choice of the Rolls-Royce and Bentley platforms was very much based on the ambitions of the original designers to be effortlessly smooth, quiet and luxurious.
The team saw the Corniche, and its Silver Shadow equivalent, as technically capable of becoming even better cars in the modern era. Not only do they have the space required for all the EV equipment, but their structural integrity and solid chassis allow everything to be stripped away without creating unwanted squeaks and rattles.
Every element with the potential for improvement was identified, mindful of any classic car regulation restrictions that mandate certain elements of the original to remain. As a result, the car is genuinely an enhancement of the original in many areas, from its new active suspension to the modern interpretation of its traditional dashboard.
The original car had a four-wheel, independent suspension with coil springs, combined with a hydraulic,
self-levelling system that was designed in the same style as those made famous by Citroën; initially on all four corners but later on the rear wheels only. The standard spring set-up had to remain, but Evice has added a modern take on that self-levelling solution.
“The suspension is an area that Rolls-Royce spent 20 years refining and it is fantastic at what it’s supposed to do,” says Pearson.
“We have kept the coil over suspension in the front, with the trailing arm in the rear – the same as the original – but we have worked with a fantastic company on a bespoke, active damper, specifically for our application.
“Once the car is on the road, we will be developing all of the software to control it in bump and rebound, determining how quickly it responds and how quickly it changes its damping rate. It has a fantastic, 10 ms response time, and it is able to read in acceleration and angles of roll and pitch, so we can be very precise with how it behaves.
“Again, that is a true enhancement of the original specification. The cars were originally very comfortable, very refined experiences, but they had that classic ride versus handling trade-off. With the active suspension system, we’re able to take away a lot of that compromise, which is generally what we have achieved across the board.”
The choice of materials has also been refined and improved, as modern leathers age much better and – crucially for Pearson – do not squeak. In fact, the team is so particular about peripheral noise when going around corners or over bumps that they have carefully planned every material-to-material contact, designing out the sounds of the original cars.
Significant focus has also been placed on sourcing materials sustainably, with the original walnut trim redesigned to integrate sustainably-sourced woods and the leather supply chain carefully monitored to ensure its as ethically-sourced as possible. Locality is also important, with most of the engineering and restoration partners within an hour of the factory.
Needless to say, the onboard entertainment system has been modernised to feature music streaming, with premium sound to match any modern vehicle. This is a significant step up from the original, which contained the radio and eight-track system (also known as an eight-track cartridge or tape) that was popular with car manufacturers in the mid-60s to early 80s.
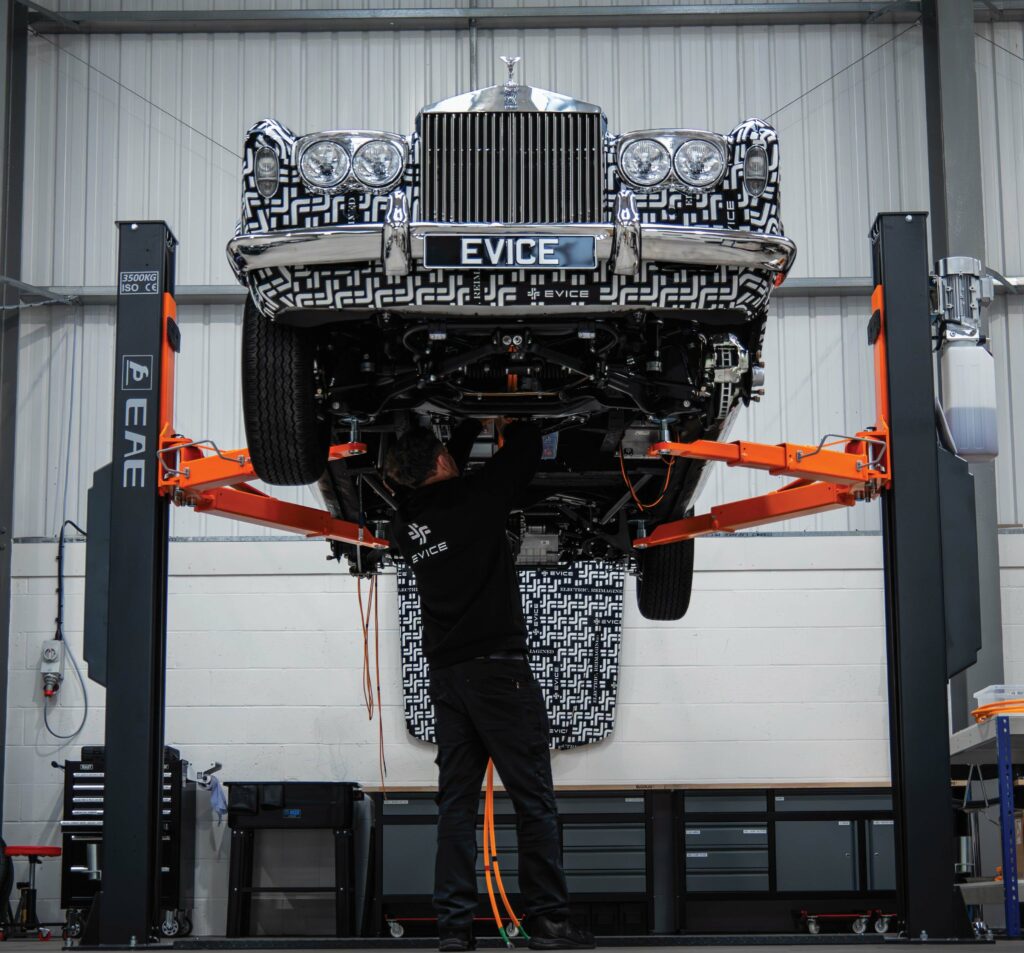
Of all the interior improvements, it is the dashboard that Evice is perhaps most proud of, and although this has yet to be revealed to the public, Pearson hints at what to expect: “We have cleaned it up. We’ve taken a lot of the 60s, 70s and 80s out of it, and added in a lot of clean, analogue, classic simplicity to it.
“A few things have been removed, a few systems consolidated, and we’ve very subtly added modern systems, so if you don’t want to see your wireless Apple CarPlay screen or your reversing camera, you can hide it at the push of a button, with a beautiful leather cover actuating over the screen.
“In the original cars there was a four-in-one gauge with the fuel, temperature and two other now irrelevant pieces of information. We’ve changed what those functions show and added a very small ‘driver information’ display in the middle, so it’s now a five-in-one; very subtle and beautifully integrated with very simple information on.
“Everything is designed to not distract from the experience. Everything is metal, wood and even Bakelite in a few areas. And it’s all analogue, because nothing can replace the way light passes through the lens on a gauge; the way it bounces off the needle; the way the needle moves. There are no haptic touchscreen features or pixellated needles here.”
One of the biggest advances in modern vehicles compared with the classics regards safety, with the use of airbags and deformable energy-absorbing crumple zones. Given the ‘new car’ approach taken by Evice, it may seem sensible to add in these features, but that is not something the company chose to do.
“The cost and time to implement those sorts of systems would be very high, and when it comes to airbags, a bad airbag is worse than no airbag at all,” says Pearson. “It would also take away so much from the experience we’re aiming for with these cars. A simple, classic steering wheel, for example, that’s just unbeatable.”
Focus has been placed on ensuring new elements are very safely integrated, however, and Pearson says: “Our front battery fits within a lot of structure designed to make it safe, but this also adds stiffness to the front of the car. The same with the rear battery, motor and power electronics assembly – it’s all adding stiffness and structure to the rear.
“We also work to the UN ECE R100 regulations in terms of how far away from the front and rear points of the car the batteries can be, so we keep them out of the initial part of the crash zones. And, of course, we keep all of our cabling, both high- and low-voltage wiring, clear of anything that would snag it and cause an issue.”
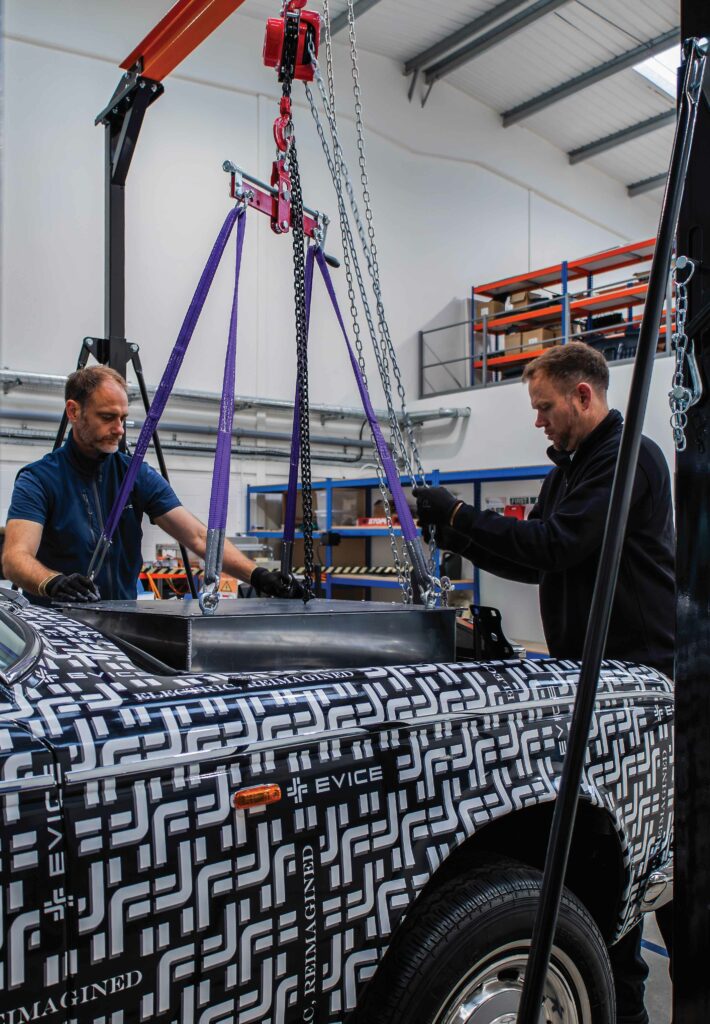
Continuous refinement
Evice’s first prototype car, the R001 Silver Shadow, will begin road-testing in the New Year, and the company plans to test and evolve the vehicle over the course of the next 18 months. A second prototype, with upgraded systems, is waiting in the wings for 2025, with the first production car sold and planned for delivery in the second half of 2026.
The first prototypes are already quite advanced, but still only in the middle of their development journeys. Improvements in all areas – mechanical, electrical and software – are already in development, with the interior finish, software and noise, vibration and harshness characteristics seeing significant ongoing development.
This relatively slow timeline is purposefully planned, says Pearson. “We’ve got an ever-growing list of interested people, but the real differentiator of what we’re doing is that we’re building the company around showing people what we’ve done, rather than trying to sell cars on a promise of what we’re going to do.
“That’s why we’ve invested a lot of time and money into building these first two cars – the camouflage-wrapped, experimental prototype, which we chose to call Marshall, and the validation prototype, which we call Elvis, which is a beautifully restored, repainted, left-hand-drive Rolls-Royce Corniche drophead.
“Elvis is a painted, rolling chassis, currently in our workshop, next to our first car. It’s currently hidden from all marketing content, and we’ll be launching the specification of that car in February next year. That’s going to take all the technology we’re developing now and will be version two of that technology, so we think it’s going to have a hell of an impact.”
Both cars are owned entirely by the company, as opposed to being built for customers. This is because the founding trio feel it is vitally important to keep the development of their technology, processes and techniques detached from customer timelines and demands. This is to ensure every element is in place once they are ready to move from constructing their own prototypes to constructing cars on a commercial basis.
“We need to do that to develop great technology and great cars,” Pearson adds. “We nail it, we get it right, then we build cars for customers. We’ve got a Corniche fixed-head coupe planned as our first customer car and we’re in the process of sourcing the donor for that, so we should be starting the restoration in early 2025.”
With the initial build of R001 now complete, the team is eager to discover how it actually feels to drive, because the real key to success is how the car performs for real.
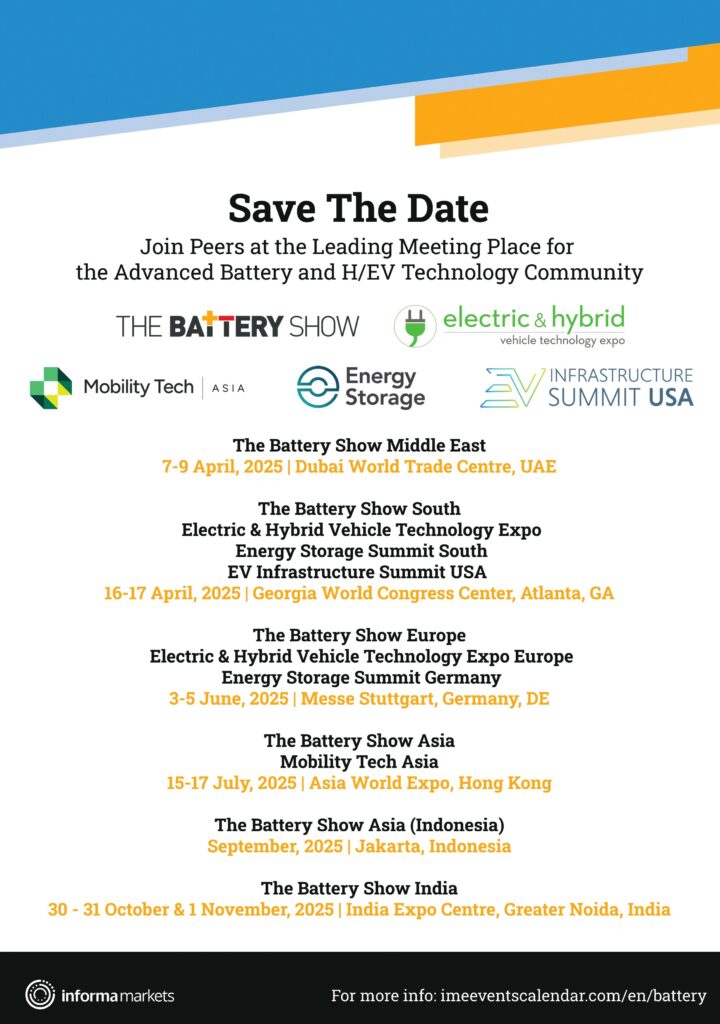
“I think what’s so important about something like a Rolls-Royce is the perceived quality,” says Pearson. “We can spend a lot of time quantifying lots of metrics that should, in theory, combine to create a car that feels a certain way, but the end result will be the product of tens of thousands of miles of testing. We’ve been able to make a suite of software that is highly adaptable, which will enable us to make the car behave and feel exactly how we want.”
So, will it feel like a modern car or a 1970s Rolls-Royce? “It will be somewhere in between,” Pearson responds. “This car was originally designed to be silent, smooth, torquey, refined and comfortable, and with the technology we have, we are able to make it more of all of those things.
“Classics often do not feel how they would have felt in their day. They age. We’re able to look back through rose-tinted spectacles, ask what people think these cars were like, and make them even better. I don’t want the car to drive like a Tesla or a Taycan. I think there’s a really nice sweet spot in the middle.”
Pearson says that whatever comes out at the end of the testing period will just be the vehicle in its initial stage. Unlike modern EVs from major manufacturers, the bespoke manufacturing and proprietary technology approach that Evice has developed opens the door to future modification, keeping the cars going for longer.
“Across the board, this is an approach that we can take,” he says. “Something that we often get asked is, ‘What happens when the next incredible technology comes out? What happens when solid state batteries come out? What happens if the Chinese charging standard becomes ubiquitous?
“Ultimately, to put it a little bit crudely, our technology is a retrofit system, and that means we can continue to keep this car modern, and usable and enjoyable, far more than any modern, brand-new electric car. You won’t get Rolls-Royce Spectre owners swapping out batteries, I can almost guarantee that.
“We’ve kept our battery pack design very modular and scalable, so we can always be taking advantage of the latest technology when it comes out. Everything is bolt-in, we don’t modify the chassis at all, so everything is upgradable and replaceable. It’s a great way for our clients to always have a car that represents the very best of what is possible.
“In fact, there are some great parallels to the high-end combustion automotive industry. If you look at Pagani, for instance, over the last 20 years there aren’t many original Zondas left. They’ve all been taken back to (founder) Horacio (Pagani) to have upgrades, engine changes, gearbox changes. C12s have turned into Tricolores, 760s and Fs, for example.”
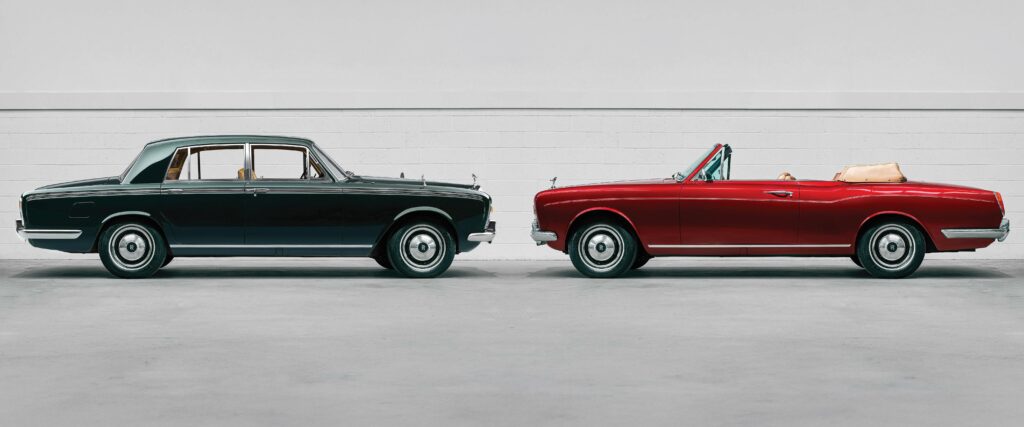
Looking to the future
Although Evice’s products are very niche, they also have global appeal – both to people who have always loved the originals and want to see them taken to a new level, and also to people who have never considered buying a classic car at all because of the maintenance challenges, performance and sustainability problems associated with them.
Pearson feels the traditional restoration industry is “complicated and frustrating”, particularly for those who do not know it well, making it “quite unapproachable” for newcomers. He believes Evice’s new-build philosophy offers a blank canvas and that it makes sense “even to combustion classic car purity evangelists – and we’ve had many conversations with them!”
Part of that is down to the customer journey, which is another area that a lot of thought has gone into, fully integrating clients into the process.
“We treat it as though it were a car that Rolls-Royce were building,” he says. “What’s your reason for wanting this? How do you want to enjoy it? We want to understand the customer’s intent, so it’s a very curated process.
“It’s a 12-month build programme, and we have plenty of ‘surprise and delight’ moments throughout the build process. We can make it exciting and engaging from day one to day 365, making it a highly emotional, personal relationship. It’s important that customers see value and have fun throughout the whole thing.
“This isn’t about mobility. It’s about moving people, and we want to prove that electrification can be sexy and exciting, and sustainability can be special. The handover itself, depending on the client, can be curated to really mark the occasion of the continuation of one of the best cars in the world.”
There is, of course, an argument that electrification is no longer the only way these cars could continue in a net-zero world. The growth of the synthetic fuels industry, which experts believe could reach cost parity with fossil fuels within 10 years, could breathe new life into these old classics, without having to change a thing.
Pearson agrees, but quickly points out that this is not what Evice is about: “Would I love to produce a car like this, running an ICE engine on synthetic fuel? No. Not a classic Rolls-Royce. The designer’s original ambition for this car was silent, smooth, torquey, refined and powerful, and an electric powertrain is significantly better at that than a combustion engine.
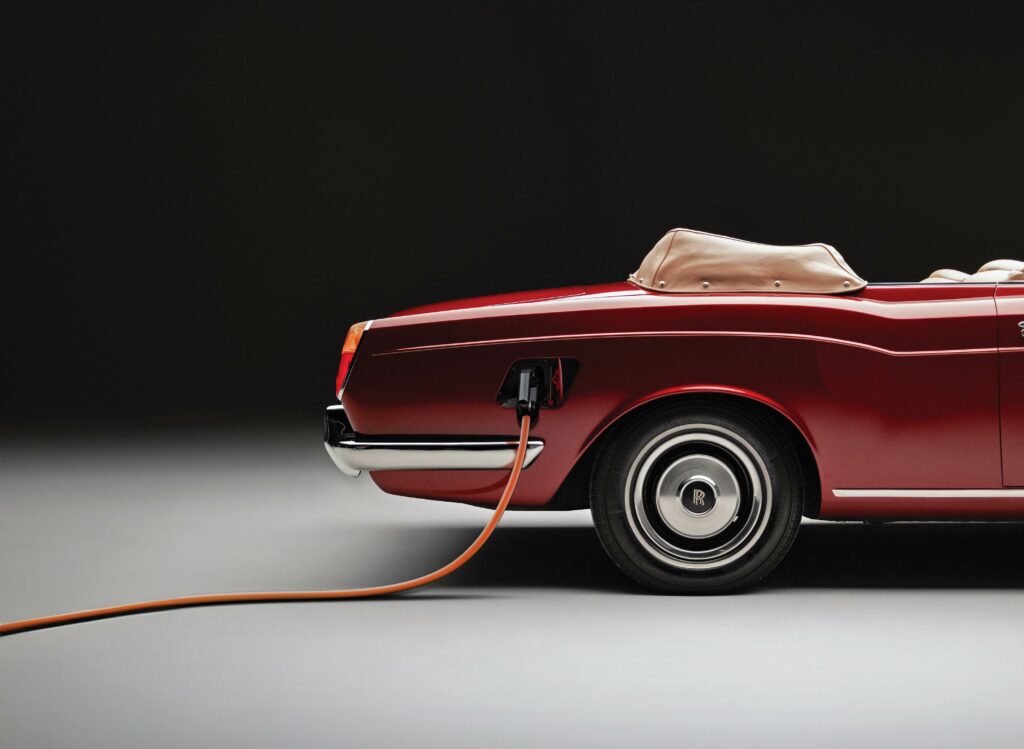
“Are there cars that are being made electric that, in my opinion, would be better, perhaps, with a synthetic fuel? Absolutely. I’ve also been driven around Goodwood race track in a 4.5 litre Bentley running on synthetic fuels, and I think that is right. But I also think the word sustainability is used, misused and abused.
“There is no combustion process currently that is zero impact at point of use. Synthetic fuel might be carbon-neutral for manufacturing, but there is carbon monoxide and there are particulates. To put a synthetic fuel in a beautiful, classic Rolls-Royce Corniche will allow it to be the car it was, but that’s not what we’re about. We want more.”
So, it appears, do many others. Evice has a growing list of customers knocking on its doors, and the team already had plans to scale before they had even sold their first car. The vision to keep things exclusive and special creates a natural limit on capacity, but the current plan is to grow the Corniche, Silver Shadow and Bentley platform to around 15 cars per year.
Beyond that, the team is already eyeing up cars that also deserve this type of treatment, and Pearson adds: “It’s a very exciting pipeline, for sure, and there will be a point where that goes beyond comfort, luxury and refinement. Our ethos is the car has to be better than a combustion counterpart. If that rule applies to a car, we’re probably thinking about it.”
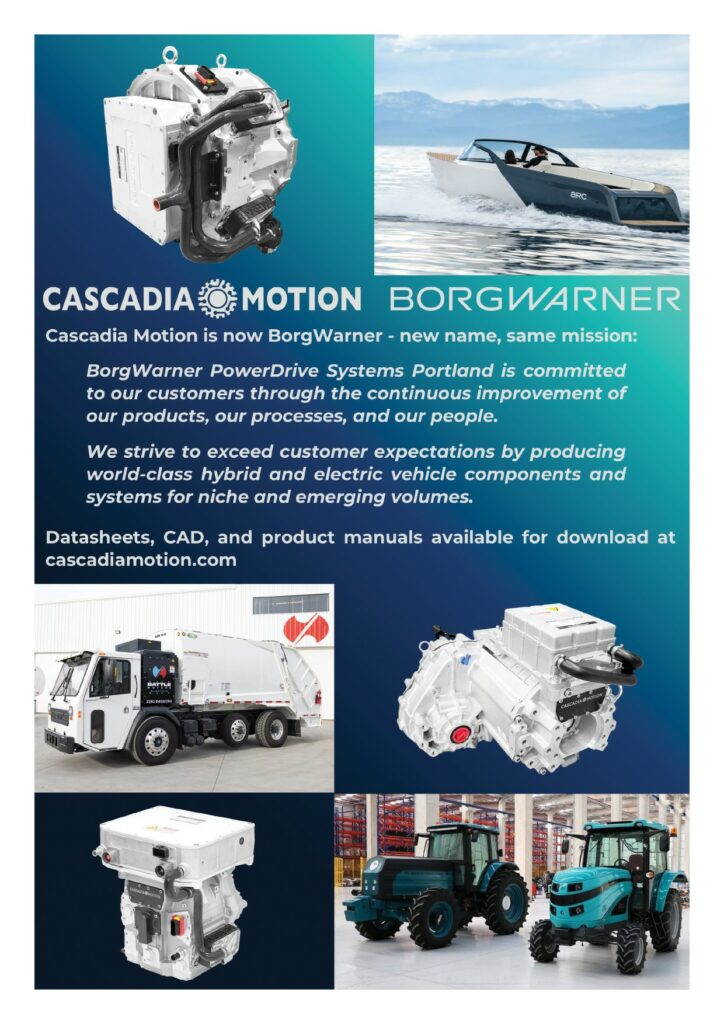
That, of course, will require further scaling, and Pearson expects that by the time the company has introduced its second and third vehicle programmes, and is at what the current business model predicts will be a steady state, the employee roster will reach the 50-60 mark, with in-house restoration functions potentially adding more.
However, while the initial vision is to create world-class cars from legendary classics, there is clearly an ulterior motive, and Pearson concludes: “The broader ambition is not just to build these incredible cars, but to use them as flagships to demonstrate the technology and expertise we have in-house, and apply that to all sorts of programmes, internally and externally.
“At that point, we should have the capacity to develop an applied technologies company and that’s certainly something we’re interested in doing. There’s real value in what we are developing from a technology, expertise and supply chain perspective; the ability to do it right. And I think there will be a lot of companies out there who want cars that reflect that.”
Specifications
Evice R001 / R002
Rolling chassis: Rolls-Royce Silver Shadow (R001) / Corniche (R002)
Motor: Single-drive unit, rear wheel drive
Power: 400 bhp or 500 bhp (depending on battery pack size)
Battery: 77 kWh of actively heated and cooled batteries split between two packs or 94 kWh split between three
Suppliers: All systems designed in-house or supplied by Tier 1 suppliers
Charging: 22 kW AC charging and DC rapid charging (to be improved from current 80 kW)
Suspension: Original layout with modern, active suspension system
Accessories:
Upgraded audio system
Wireless Apple CarPlay on a concealable screen
Bespoke, high-performance headlights (in development)
Climate control
Heated and ventilated seats
Electrically adjustable seats
Remote central locking
Bespoke dashboard with all analogue, tactile features
ONLINE PARTNERS
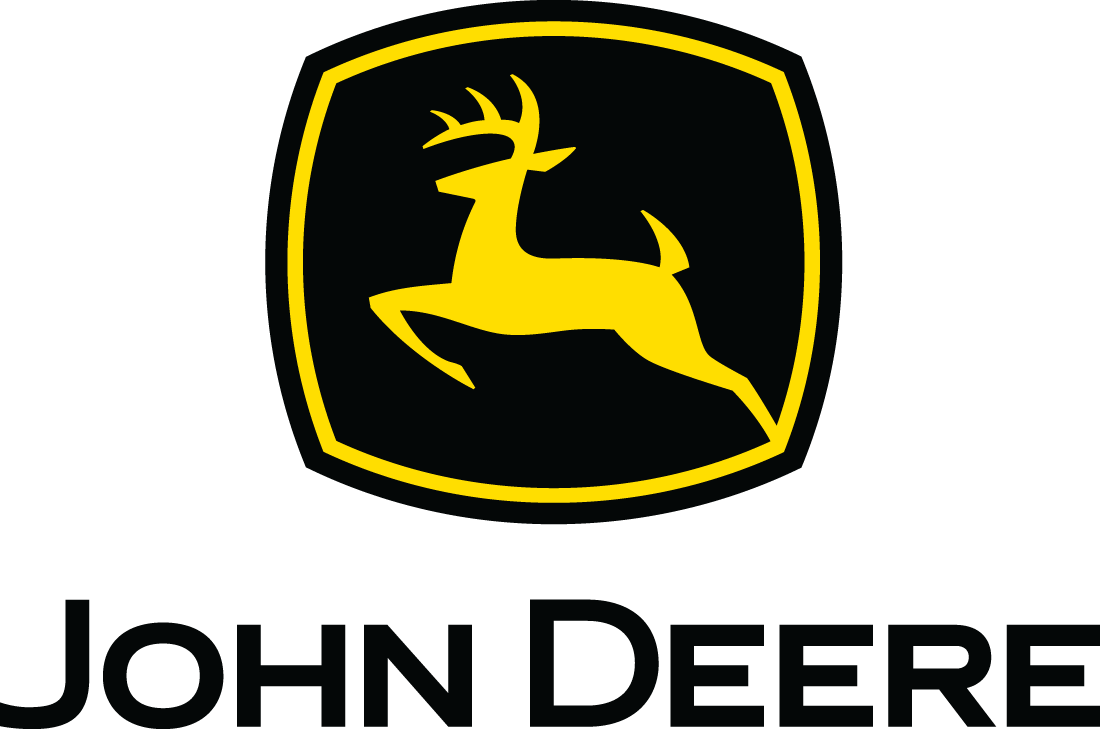
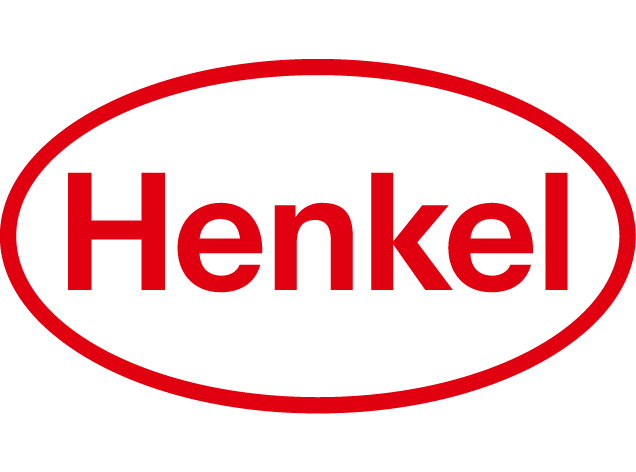
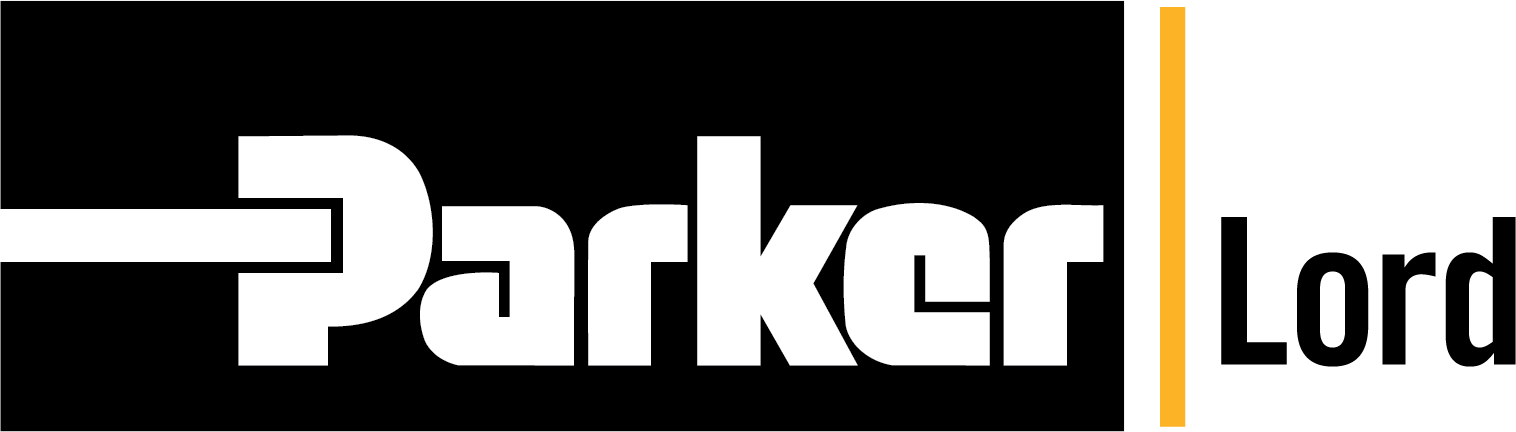
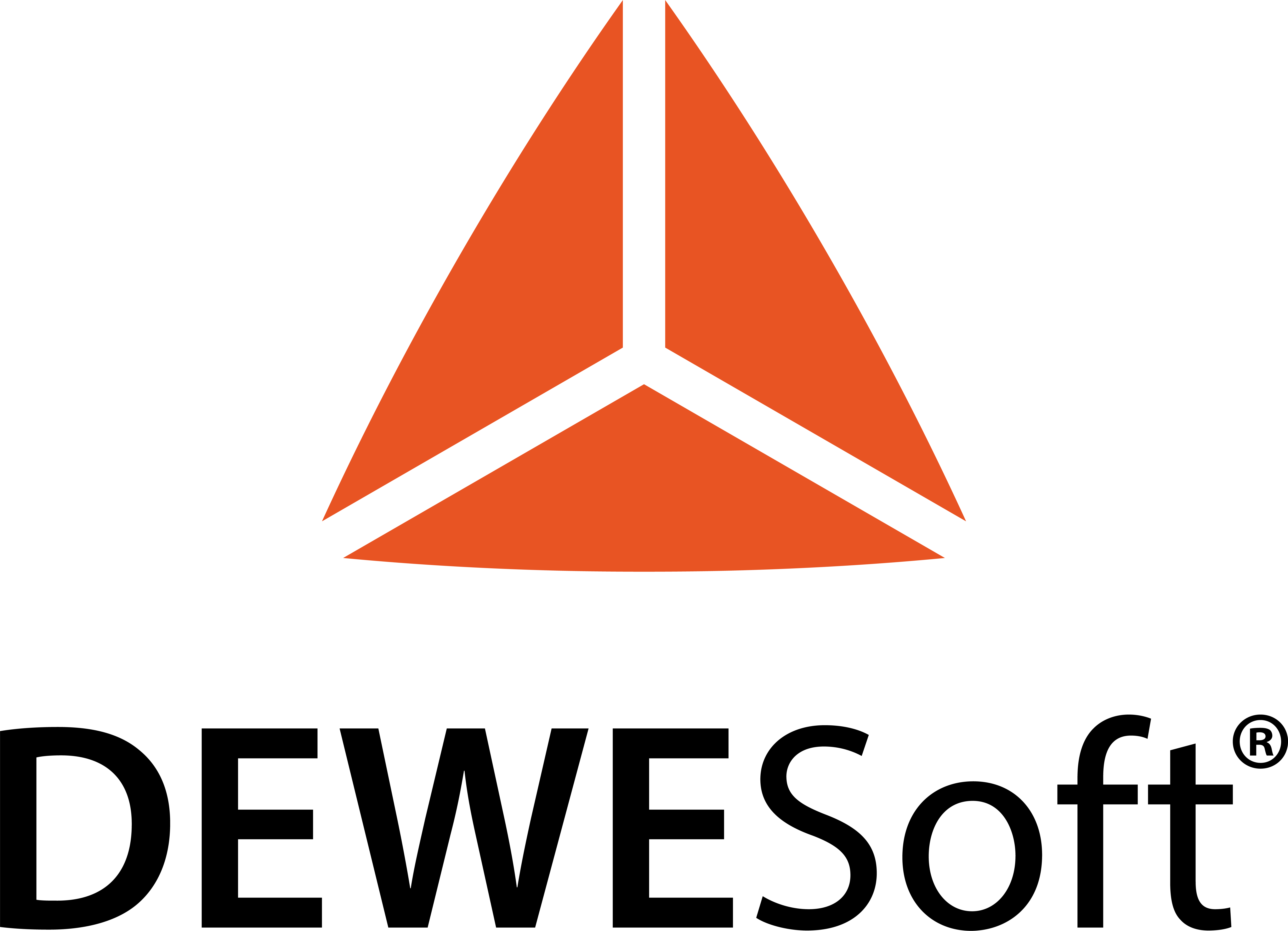
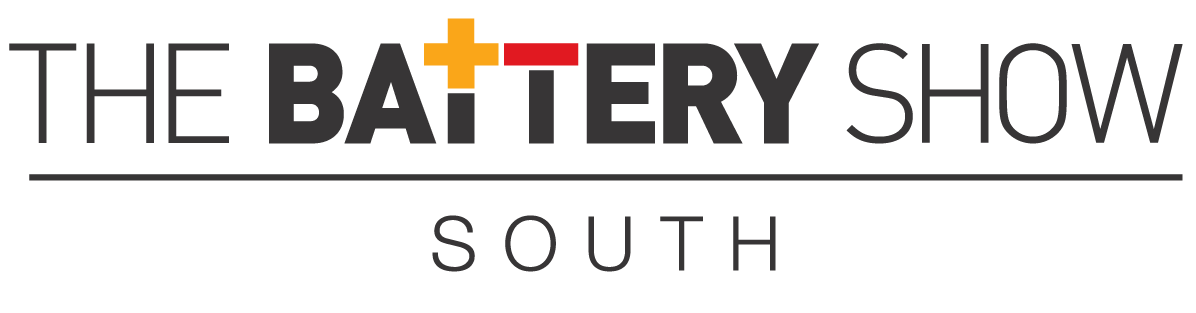
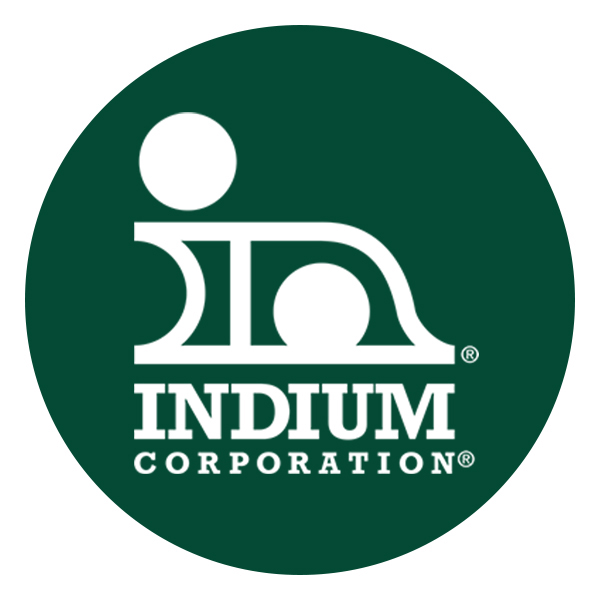

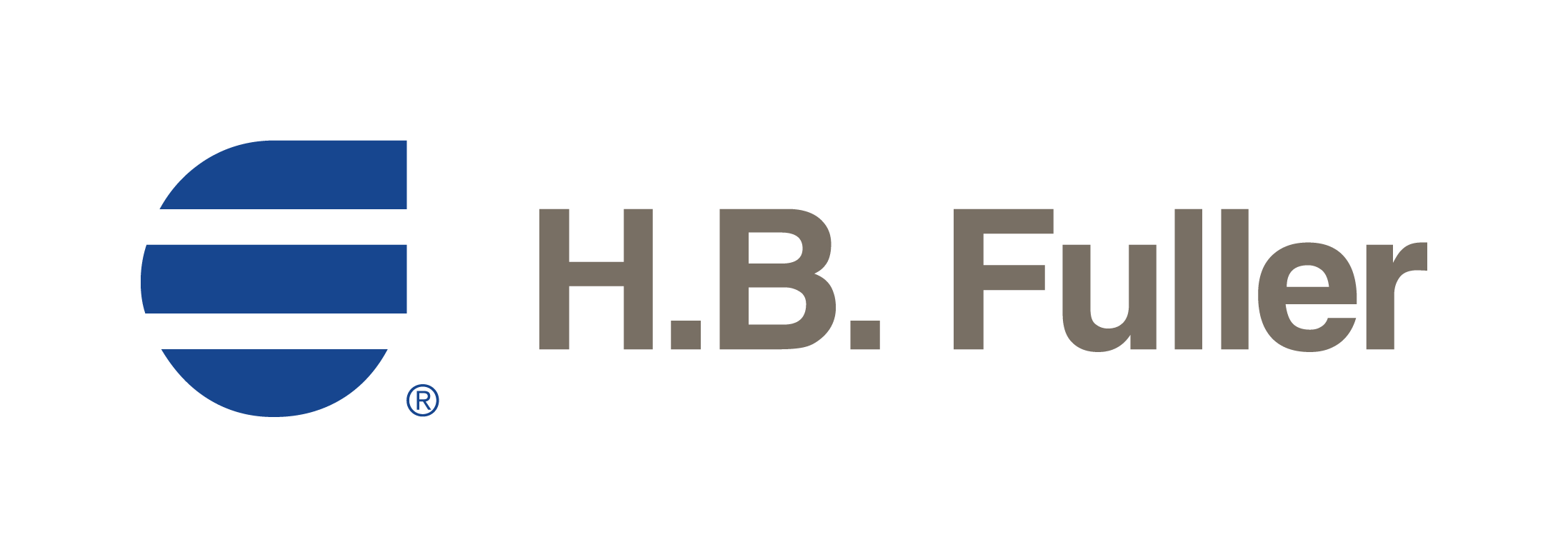
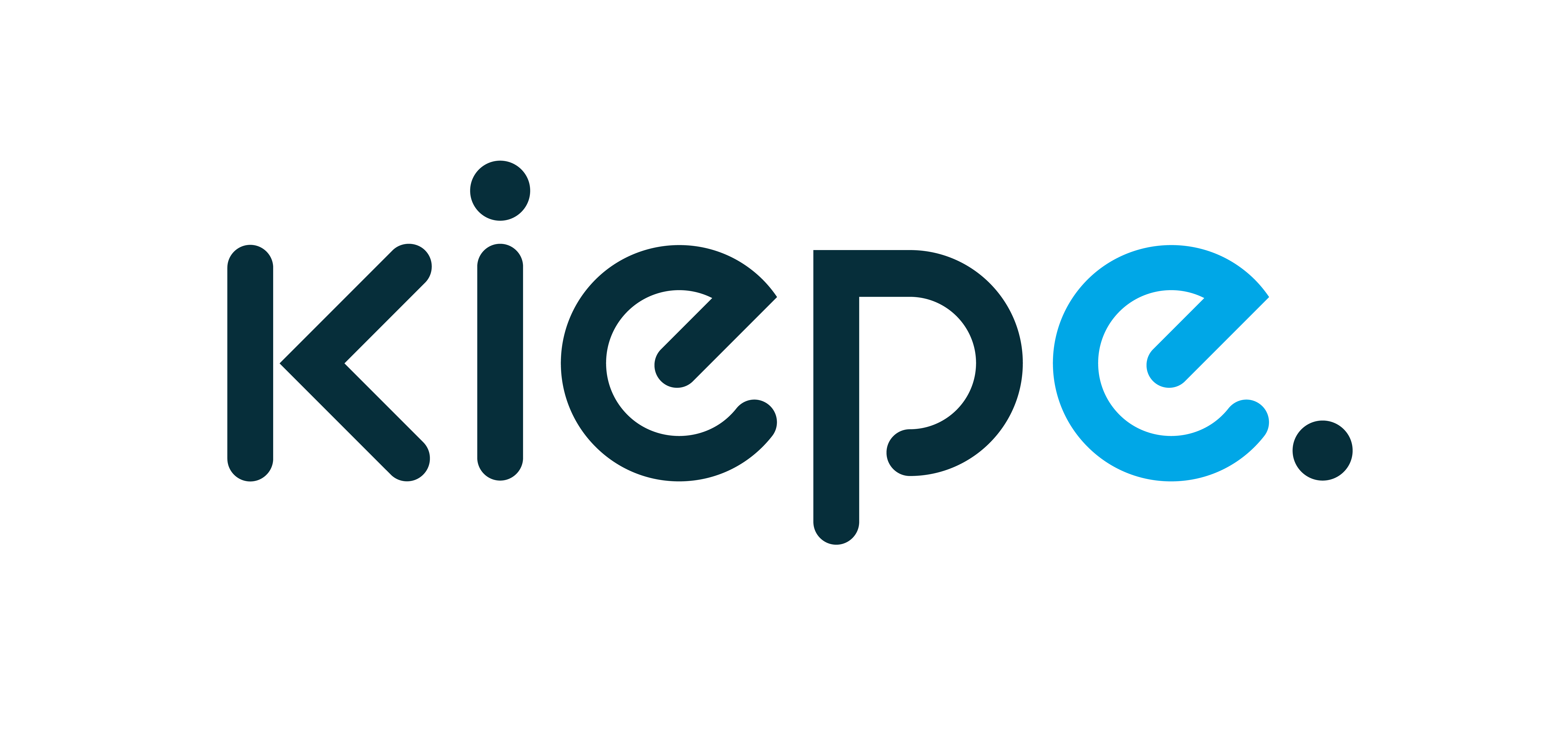
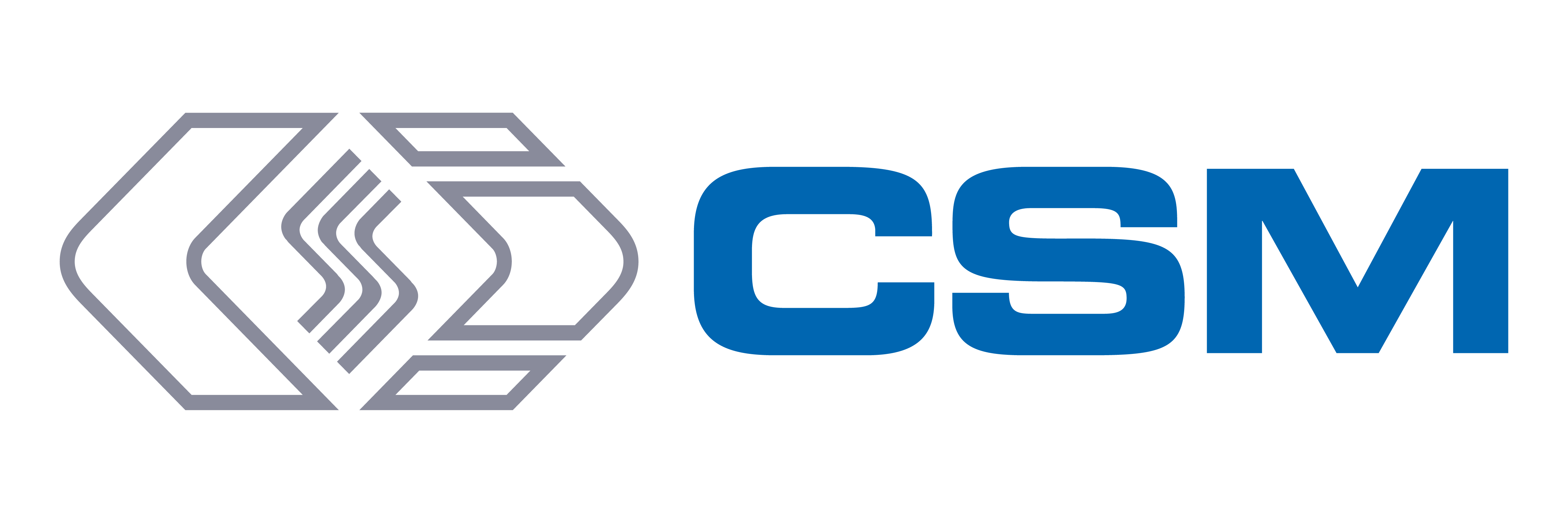