Additive Drives uses injection-moulded copper
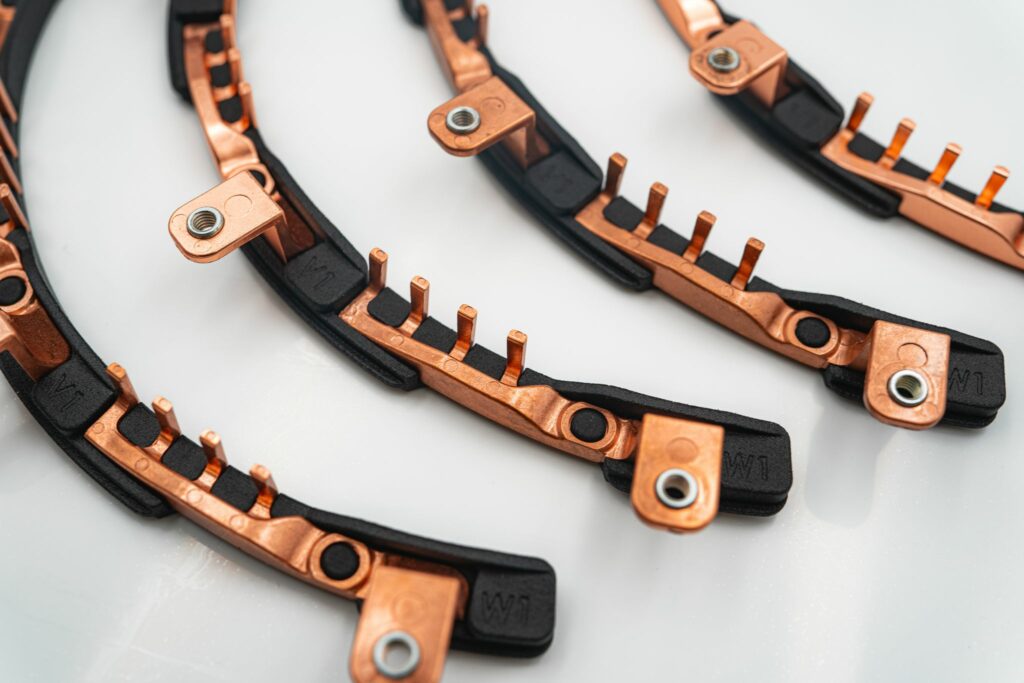
Additive Drives has developed an injection-moulded copper process for the next generation of electric-drive busbars, writes Nick Flaherty.
The development combines the best of two worlds: specialised design and mass production.
Additive Drives is using the process for busbars with printed, conventional or injection-moulded parts in copper and plastic.
Both simple and highly complex components will be produced in high volumes of tens of millions per year. Copper powder is combined with an organic binder to work with existing injection-moulding machines.
A value of 100% International Annealed Copper Standard (IACS) electrical conductivity corresponds to 58 MS/m at a temperature of 20 C. After injection moulding, the processed copper achieves a conductivity of up to 01%.
Other physical properties, such as density or thermal conductivity, are very close to those of conventionally drawn copper.
For electrical machine designers, this process enables the integration of functional elements such as press-fit nuts, connectors or thermal sensors, as well as minimising volume and avoiding hotspots.
The process can also add plastic parts and insulation with a rating up to a temperature of 240 C, as well as contacts coated with silver or nickel to reduce assembly steps and save costs.
Initial studies suggest copper mass can be reduced by at least 40%, compared with conventional busbar designs.
Click here to read the latest issue of E-Mobility Engineering.
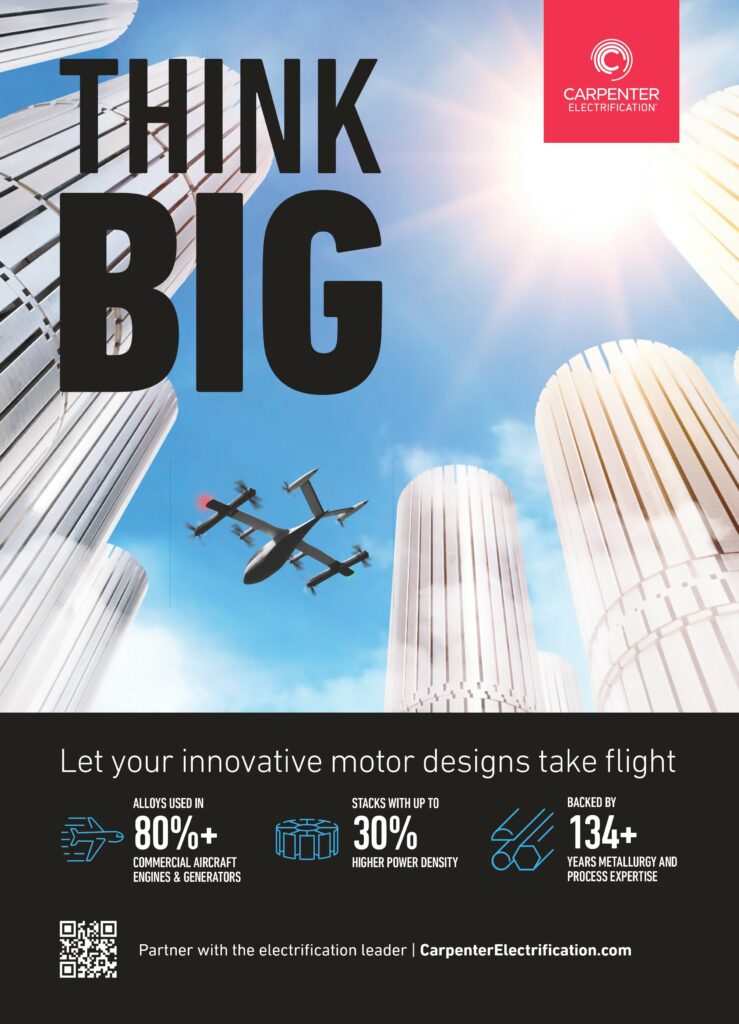
ONLINE PARTNERS
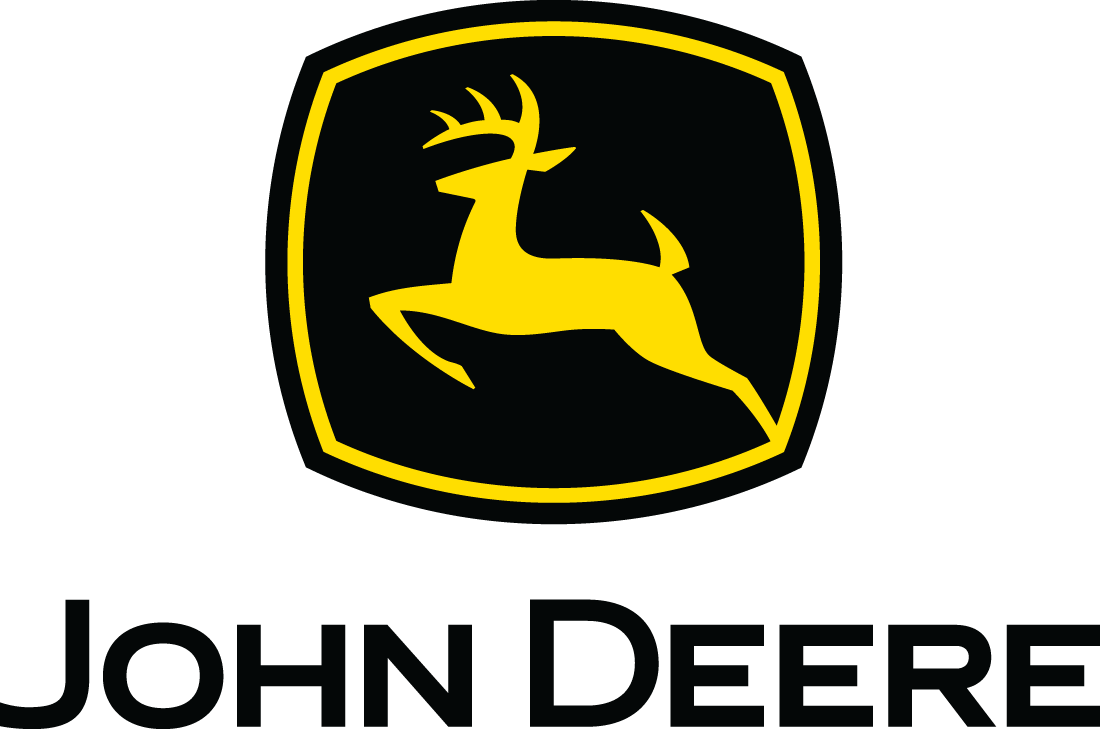
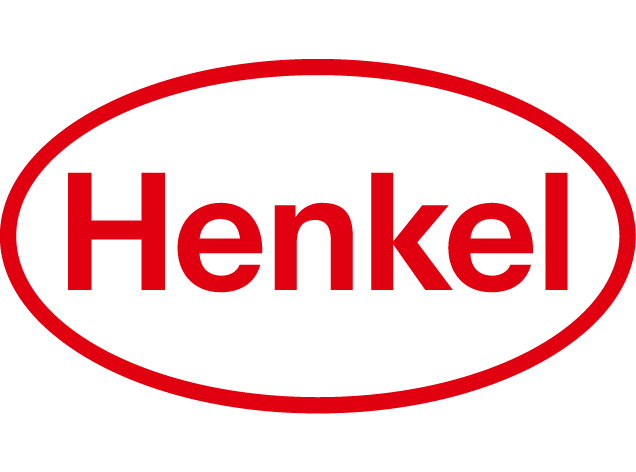
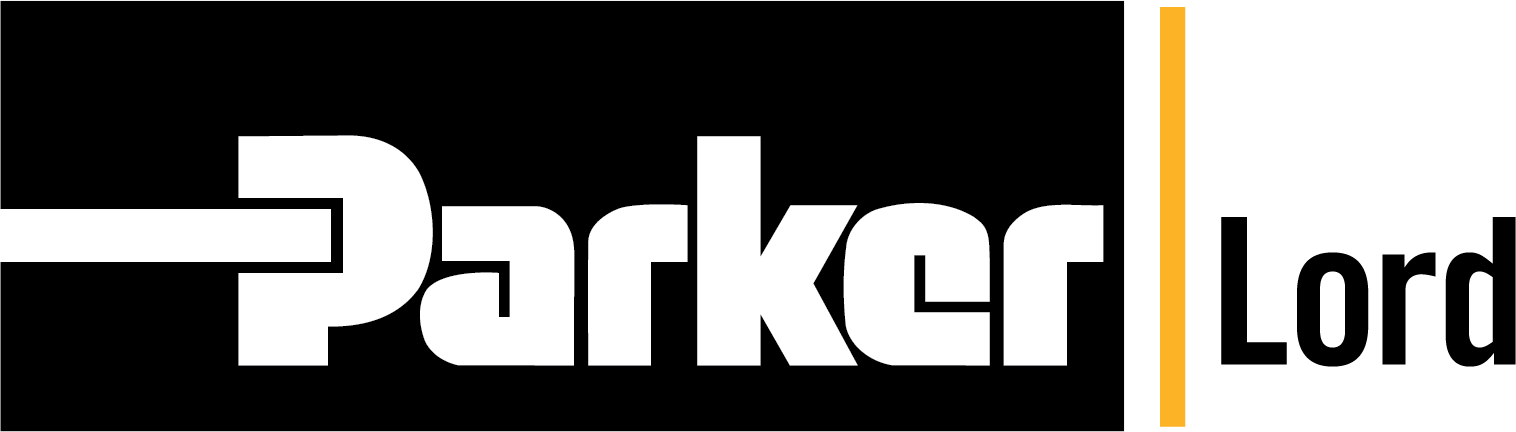
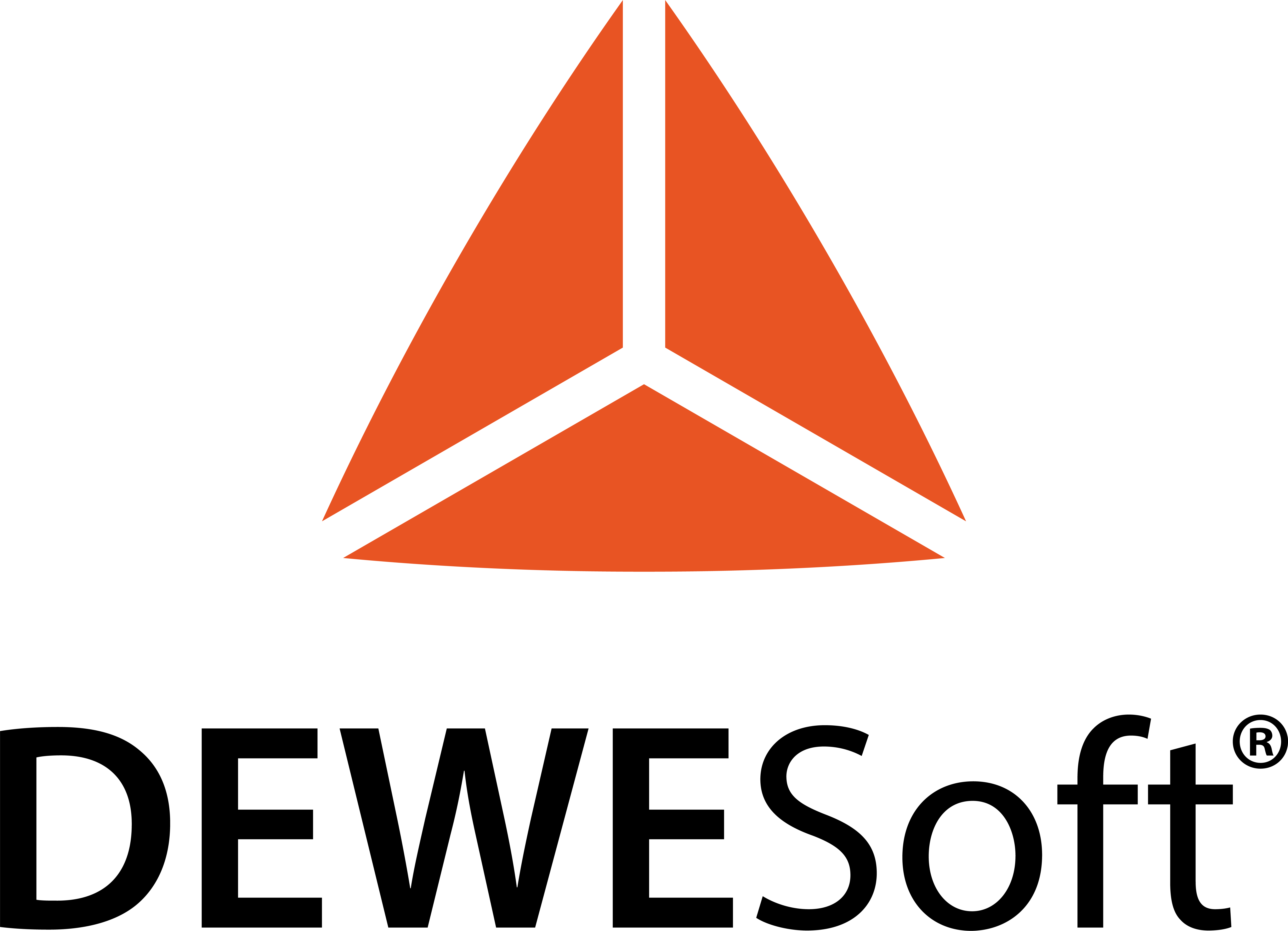
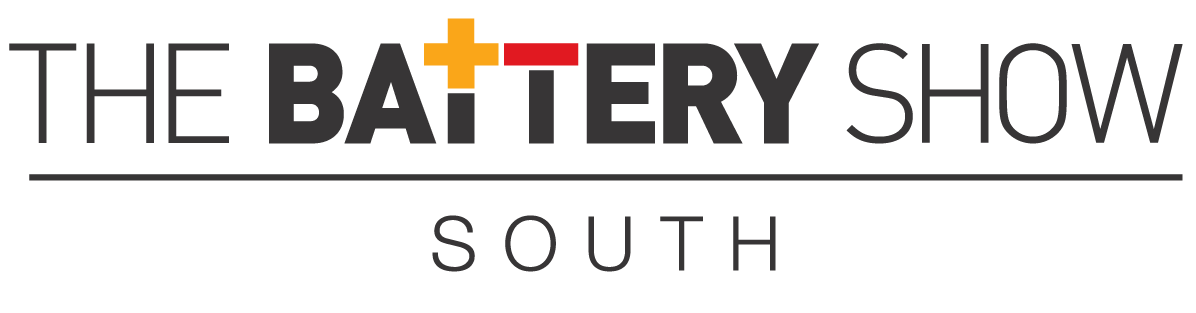
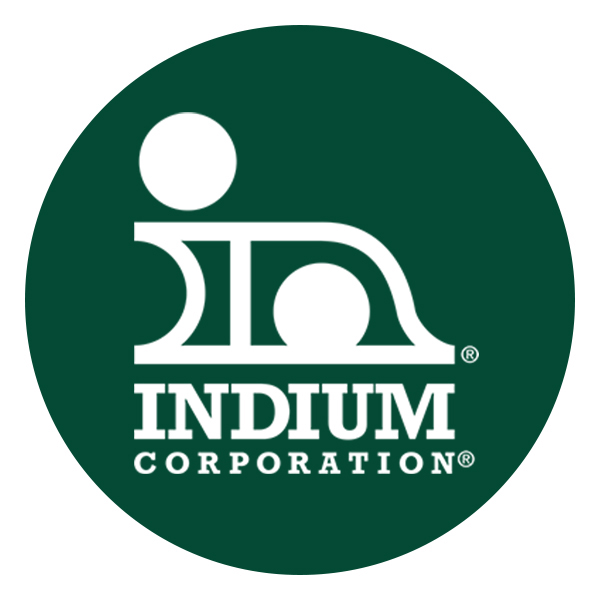
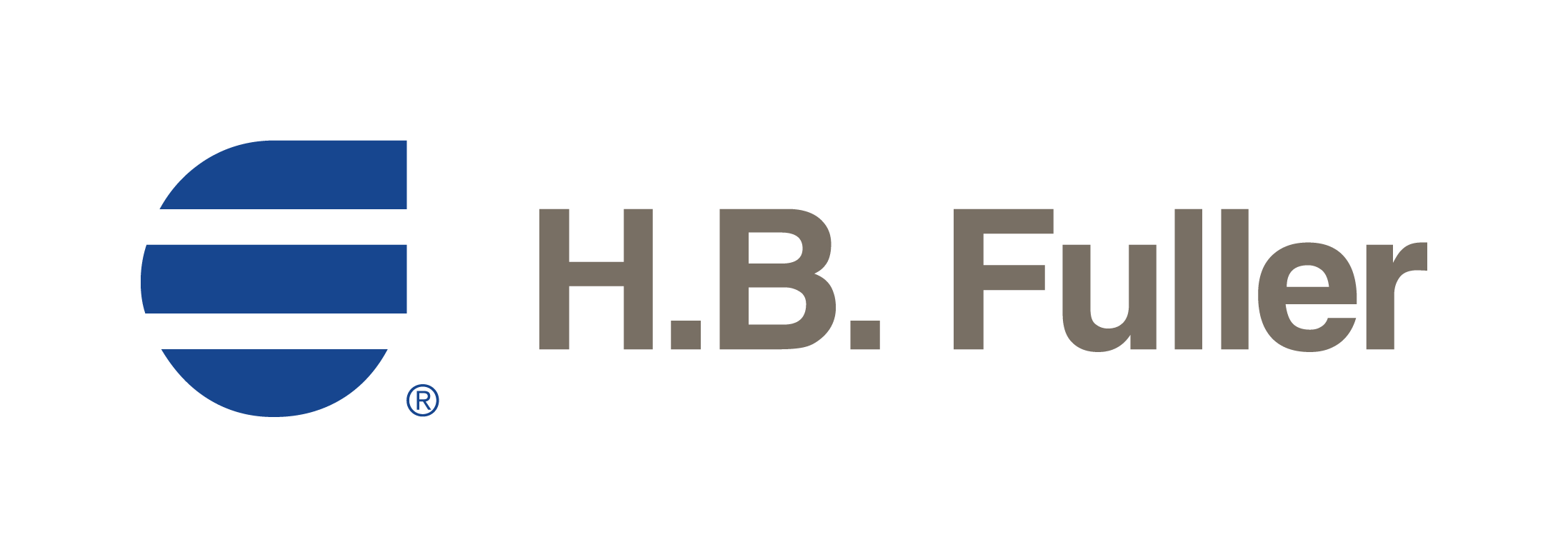