Scalable approach speeds up capacitor design
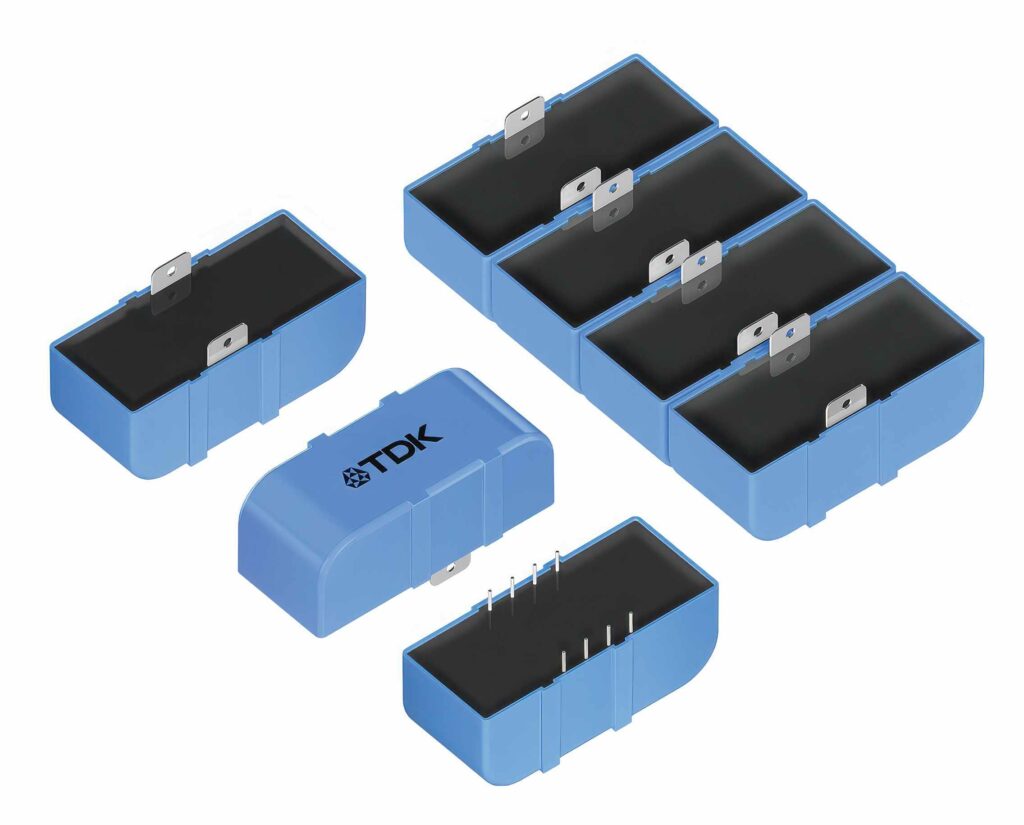
(Image courtesy of TDK)
TDK has developed a standardised, modular, DC link capacitor design for traction inverters, writes Nick Flaherty.
The xEVCap is built from modules connected in parallel to provide specific capacitances for powertrain inverters in passenger cars, commercial and off-highway vehicles.
The scalable approach helps inverter designers meet varying capacitance and current requirements at lower volumes while saving time. The use of standardised capacitor modules also reduces costs, minimising stock variety.
The xEVCap has two connection styles: the B25654A*001 has lead wires for soldering to busbars or PCBs; the B25654A*002 has flat terminals for welding or screwing to busbars. The mechanical versions are 85 x 47 x 40.5 mm, 97.5 x 35.5 x 42.5 mm, and 109 x 47 x 40.5 mm. Rated voltages include 500 V, 650 V, 850 V and 920 V.
Depending on the rated voltages, the capacitances range from 60 µF to 270 µF. All of the xEVCap modules are included in TDK’s CLARA tool, which simulates the components electrically and thermally under various conditions.
Applied voltage can exceed rated voltage for a limited time to give overhead for the design. For example, the 850 V types can withstand 890 V for 100 hours at 105 C and surge voltages up to 1200 V. Rated currents range from 35 A to 60 A (at 10 kHz) with ESL values of 14 nH or 17 nH (at 1 MHz).
The operating temperature range for each module is -40 C to 105 C.
The capacitance range complies with automotive standards AEC-Q200 rev. E and IEC TS 63337:2024.
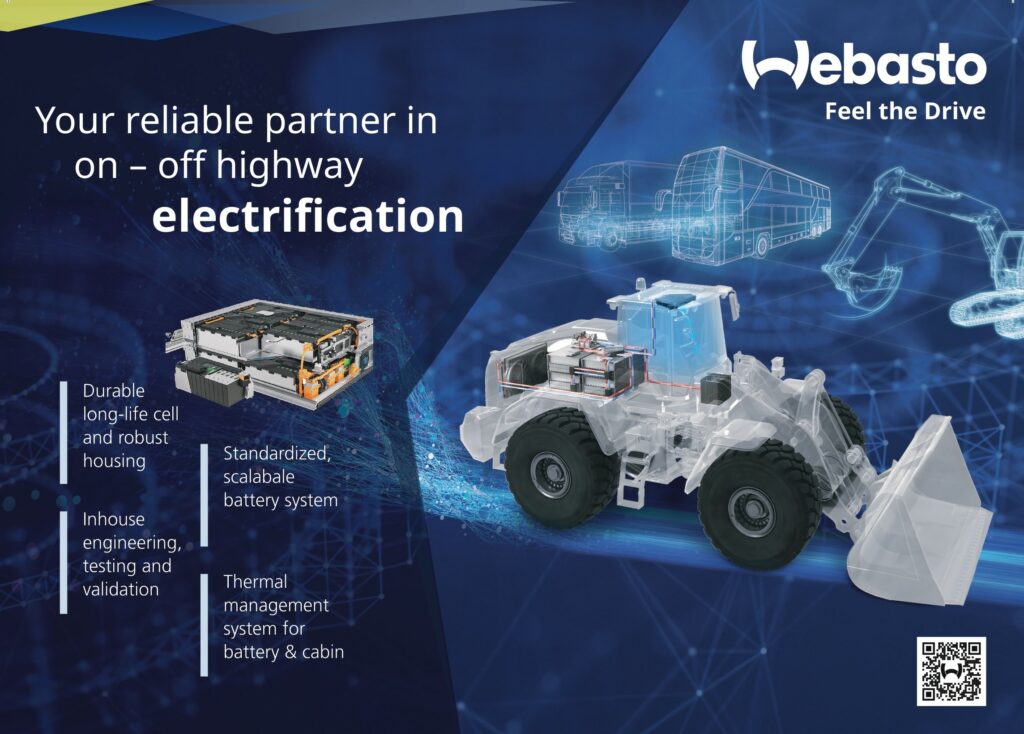
ONLINE PARTNERS
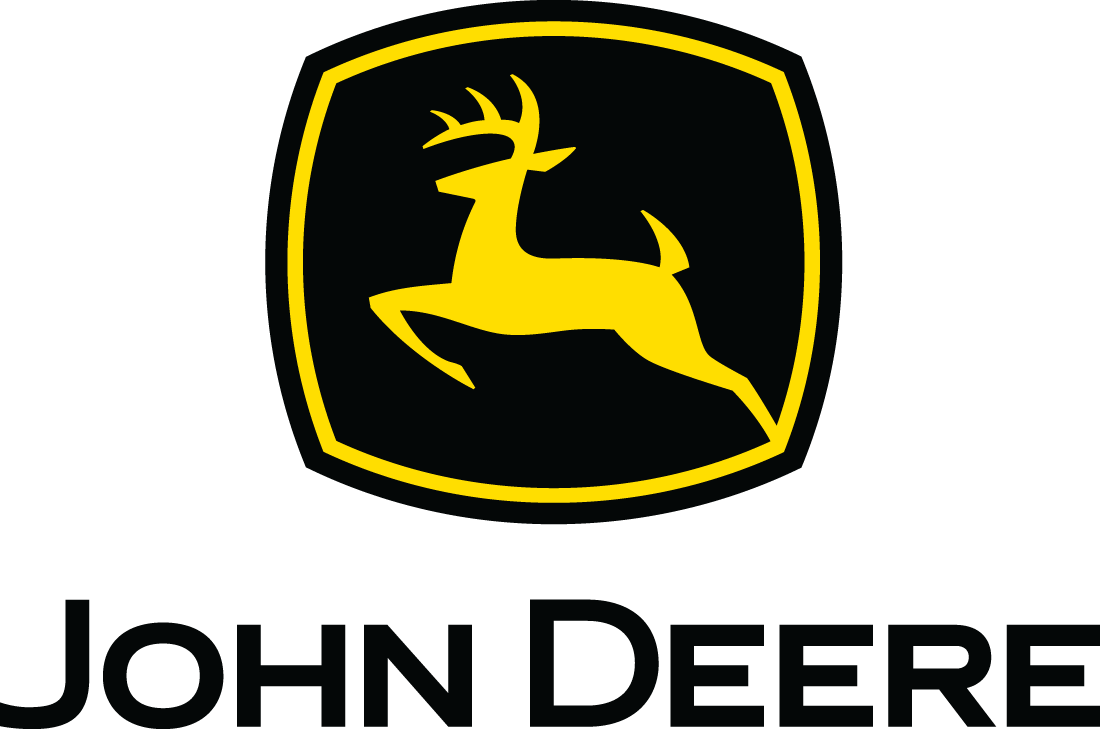
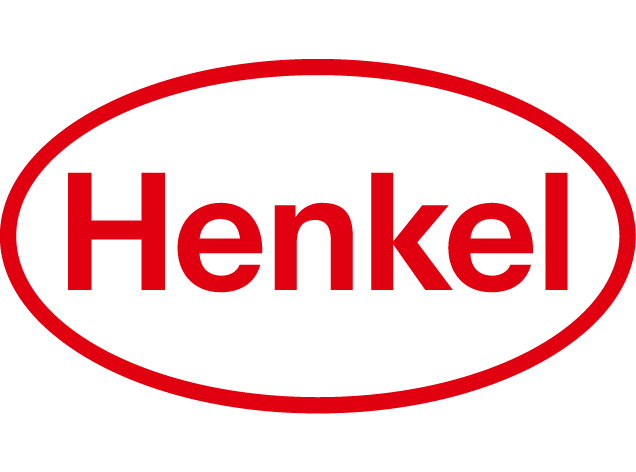
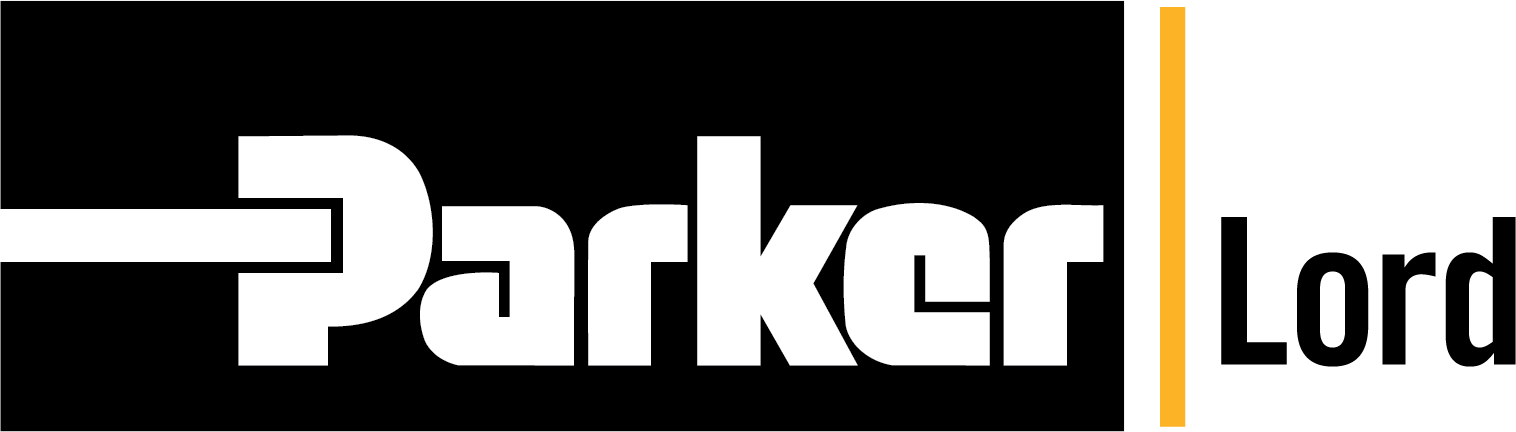
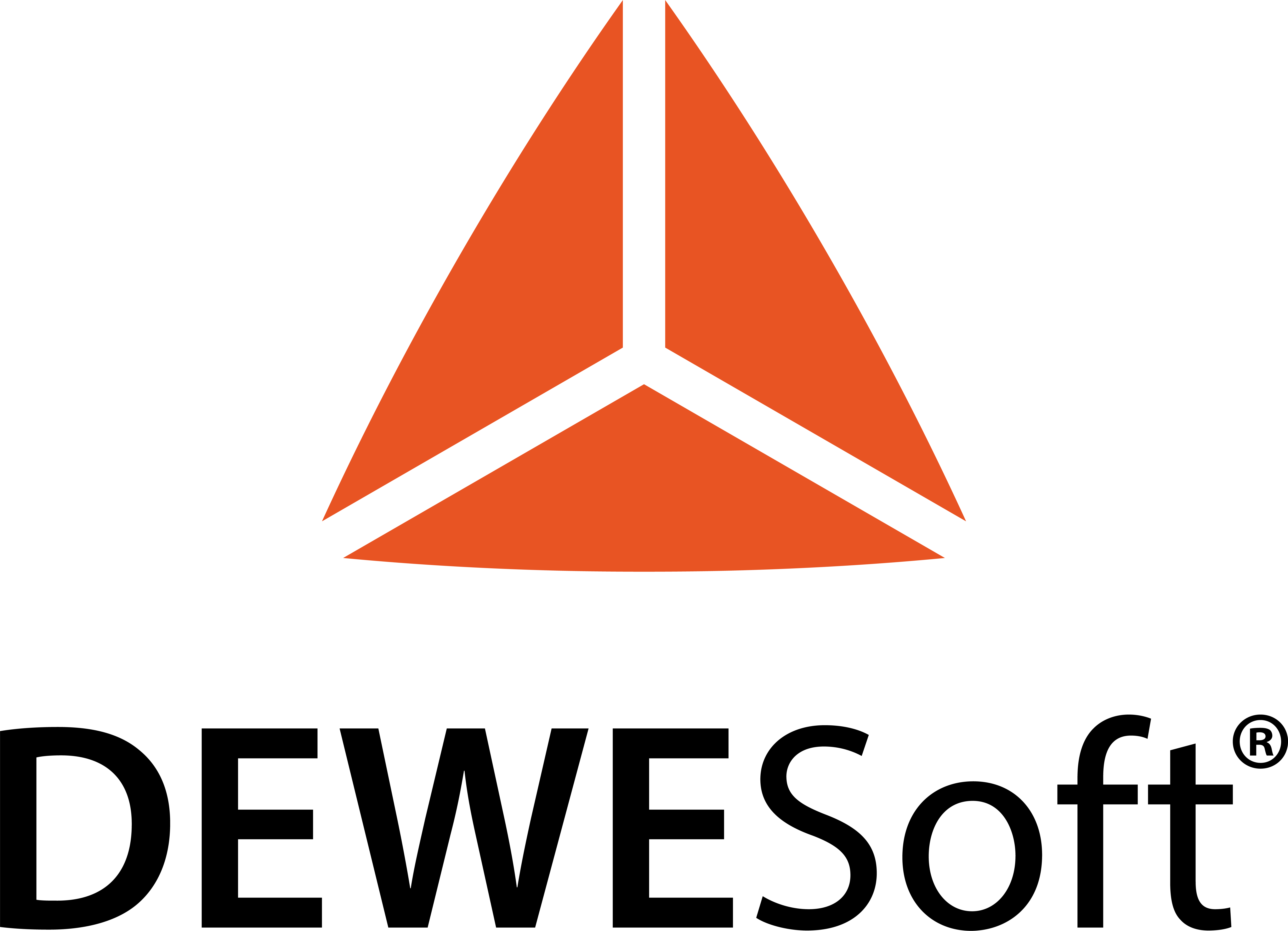
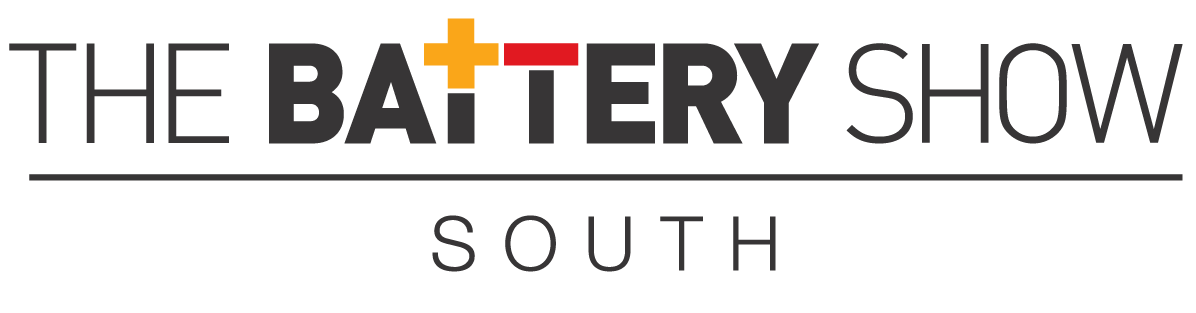
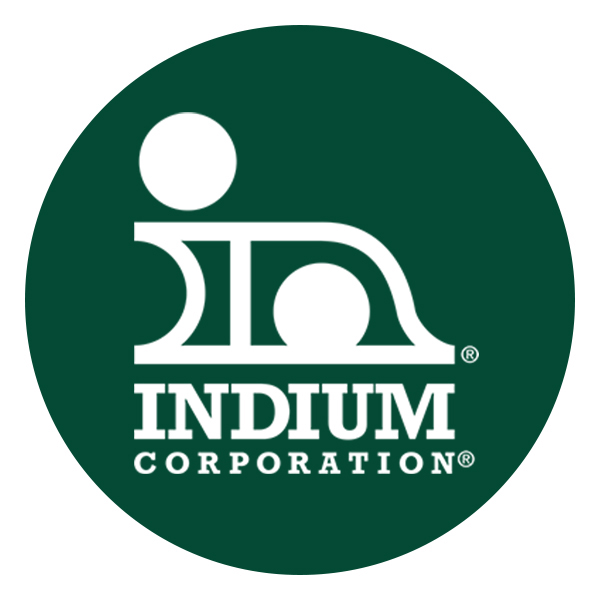

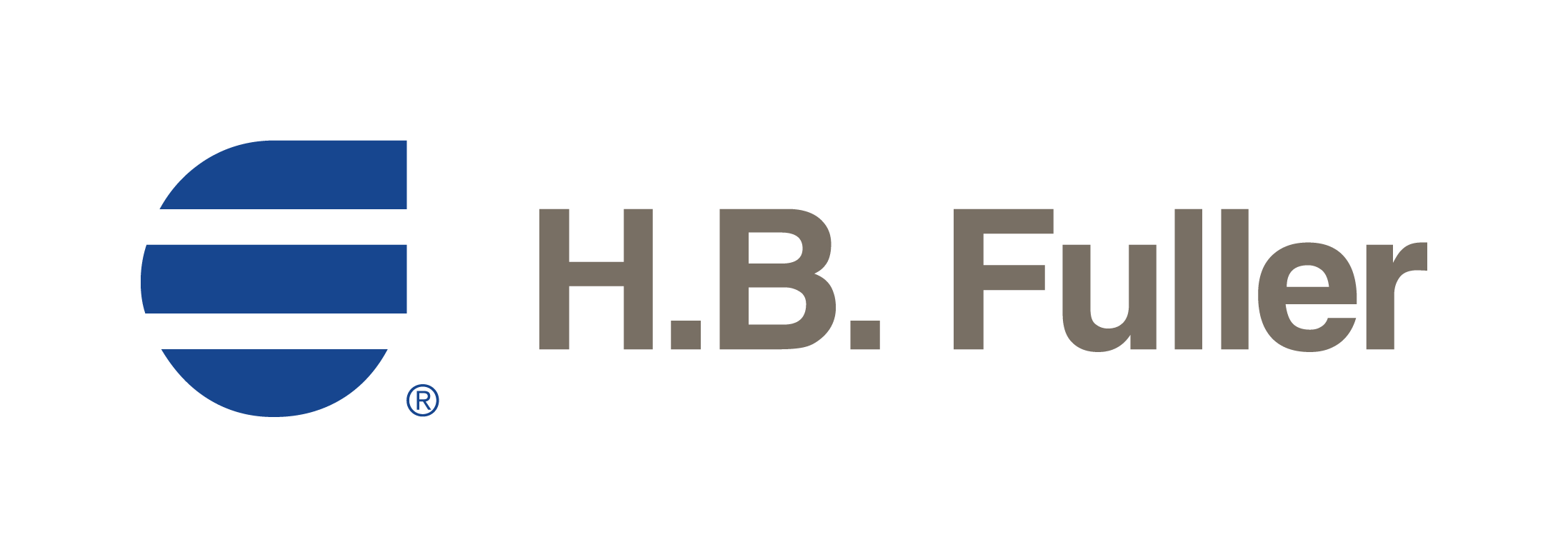
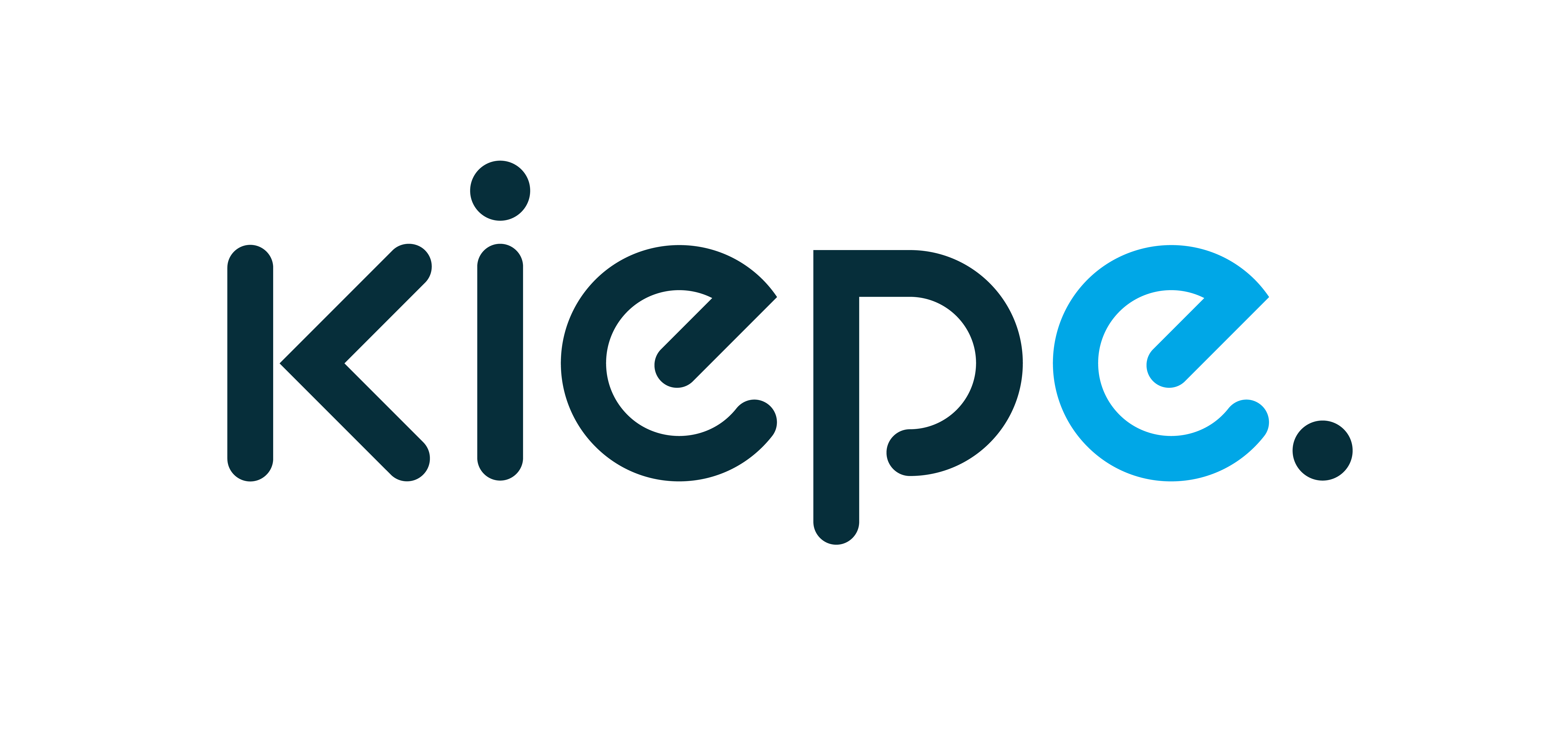
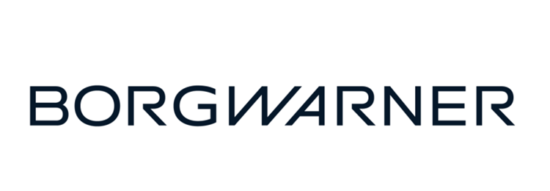