ICEBreaker hydrogen HGV
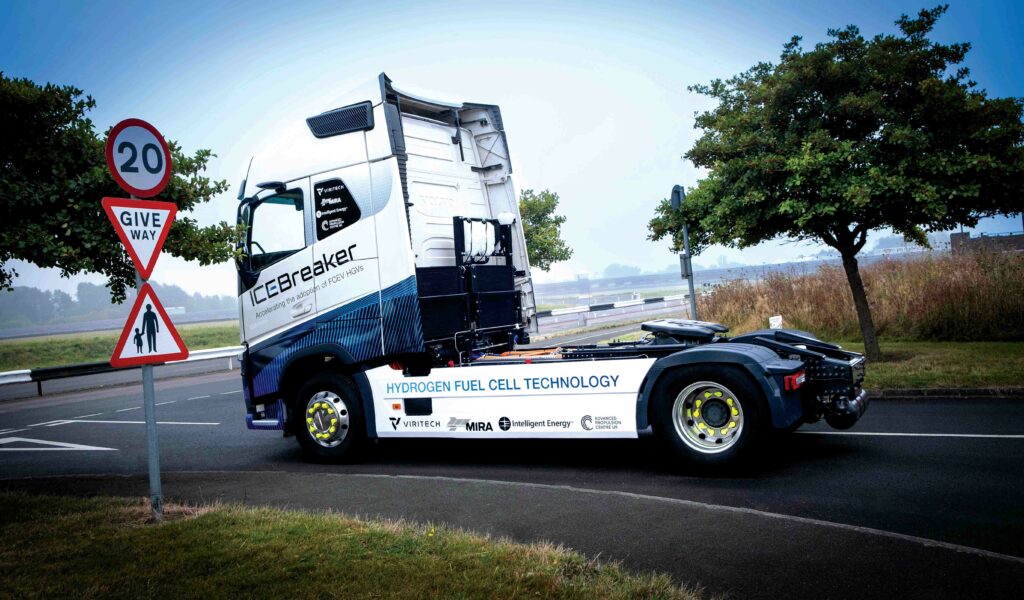
(All images courtesy of Project ICEBreaker)
Heavy-duty hydrogen
Two companies have teamed up to build a hydrogen-powered HGV using a fuel-cell powerplant, as Peter Donaldson reports
Spearheaded by powertrain energy-management specialist Viritech, Project ICEBreaker has built a hydrogen-powered heavy goods vehicle (HGV) using a fuel-cell power plant, focusing on minimising the weight penalty compared with internal combustion engine (ICE) vehicles.
With a focus on demonstrating the capability of hydrogen fuel-cell power in an economically vital transport sector, the project brings together Horiba MIRA, a leading provider of mobility engineering, testing and verification services, and fuel-cell systems manufacturer Intelligent Energy (IE), which is collaborating on the development of the powertrain, the fuel cell and associated components.
ICEBreaker’s origins can be traced back to a confluence of needs and opportunities. Horiba MIRA was keen to demonstrate hydrogen technology to showcase its capabilities and use its capabilities as a systems integrator.
The project serves as a live advertisement of the firm’s engineering services, showing its capacity for total cost-of-ownership (TCO) modelling, enabling it to estimate hydrogen fuel consumption for a given route and the potential to demonstrate a data-driven calibration optimisation of the powertrain, along with advanced testing for zero-emission vehicles, according to Habib Rahman, chief programme engineer and overall technical lead for Horiba MIRA on ICEBreaker.
For Horiba MIRA, the scheme serves to push hydrogen as a power source while showing the company’s ability to engineer, validate and optimise fuel-cell systems in real-world conditions.
Project lead Viritech had developed several essential peripheral components, including DC-DC converters, batteries and energy management systems. It sought a market-relevant demonstrator to showcase a full powertrain offering that could be tested and validated in a demanding environment, thereby increasing the technology readiness level (TRL) of its solutions.
“For us, ICEBreaker is about taking our powertrain solutions to the next level of commercial readiness while demonstrating their scalability and reliability in a heavy-duty application,” says Chris Hübel, head of engineering at Viritech.
IE saw an opportunity for further development of its heavy-duty, hydrogen fuel-cell system with the IE-DRIVE HD100 at the heart of the project. Participation in ICEBreaker would go on to provide valuable data and operational miles on its high-power system.
The project began in earnest in September 2023, with Horiba MIRA commissioning the vehicle for its first tests as a fully integrated fuel-cell vehicle. As the project enters its next phase, rigorous testing will ensure its readiness for the road.
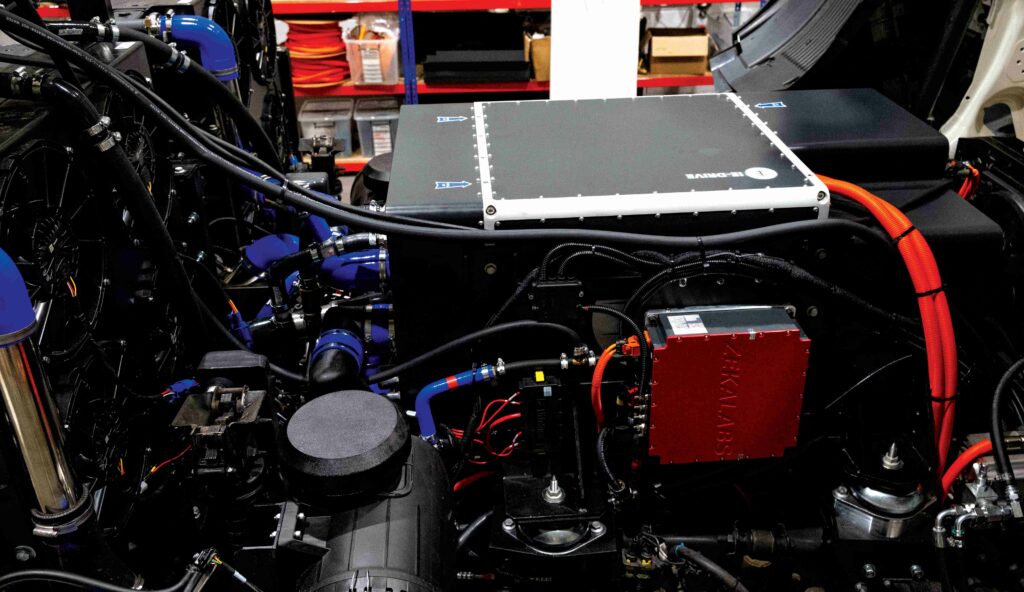
Heavy-duty fuel cell
At the heart of the ICEBreaker truck is the fuel-cell system, designed by IE. The IE-DRIVE HD100 is a Proton Exchange Membrane (PEM) fuel cell, capable of producing a consistent 100 kW of net power, scalable to meet varying loads.
At the heart of a PEM fuel-cell stack is a set of membrane electrode assemblies, consisting of a thin, polymer membrane that allows protons (H+) to pass through, with the electrons passing around the external circuit, anode and cathode electrodes coated with a catalyst (typically platinum) that facilitates the electrochemical reaction.
On either side of the electrodes are gas-diffusion layers that uniformly distribute the reactant gases (hydrogen and oxygen) over the surface of the electrode. Finally, a set of flow channels in the bipolar separator plates deliver hydrogen and oxygen to the anode and cathode, respectively, while removing the water and heat produced by the reaction.
Hydrogen from the storage tank is fed into the cell on the anode side, where the catalyst splits the H2 molecules into positively-charged protons and negatively-charged electrons. The protons pass through the membrane to the cathode, while the electrons cannot pass through and are therefore forced to travel around an external electric circuit that powers the loads.
Atmospheric air is supplied to the cathode, where the oxygen it contains combines with the protons (hydrogen ions) that have passed through the membrane and the electrons returning via the external circuit to form water in an exothermic electrochemical reaction.
PEM fuel cells start fast and respond to changes in power demand very quickly, compared with other types of fuel cells, while operating at relatively low temperatures. They also offer high power-to-weight and power-to-volume ratios, making them well-suited for road vehicles, and their only direct emissions are water and heat when fuelled with pure hydrogen. They are also modular and scalable, facilitating flexible designs across a wide range of power outputs.
However, they are relatively expensive and they are still limited by the lack of hydrogen infrastructure on most countries’ road networks. Also, hydrogen’s green credentials are tarnished by the fact that most production of the gas is by carbon- and energy-intensive steam reforming of methane, rather than electrolysis of water using cleanly generated electricity.
PEMs are vulnerable to both freezing and overheating, so robust thermal management is essential, while the catalyst can be degraded by impurities in the hydrogen/oxygen supplies.
In ICEBreaker, two HD100 units are combined to provide a total of 200 kW of net power, sufficient to drive the truck in heavy-duty operations. The modularity of IE’s design allows this configuration to be further scaled up, with the same technology being used in megawatt-scale power plants in other applications.
“PEM fuel cells are a good choice for this project due to their high gravimetric and volumetric power densities, faster start-up and shorter user-load response times compared to other fuel-cell technologies,” says Scott Whatton, head of product development for IE-DRIVE at IE.
Efficiency is a key consideration in any hydrogen fuel-cell system, and the IE-DRIVE HD100 stack performs at 54% efficiency at optimal operating points, with a slight reduction to 46% at peak loads, according to IE.
This efficiency is achieved through careful engineering of the hydrogen-to-electric conversion process, minimising energy losses while maintaining robustness under heavy loads. The focus is not only on peak performance but on maintaining efficiency over a wide range of operational conditions, including extreme temperatures.
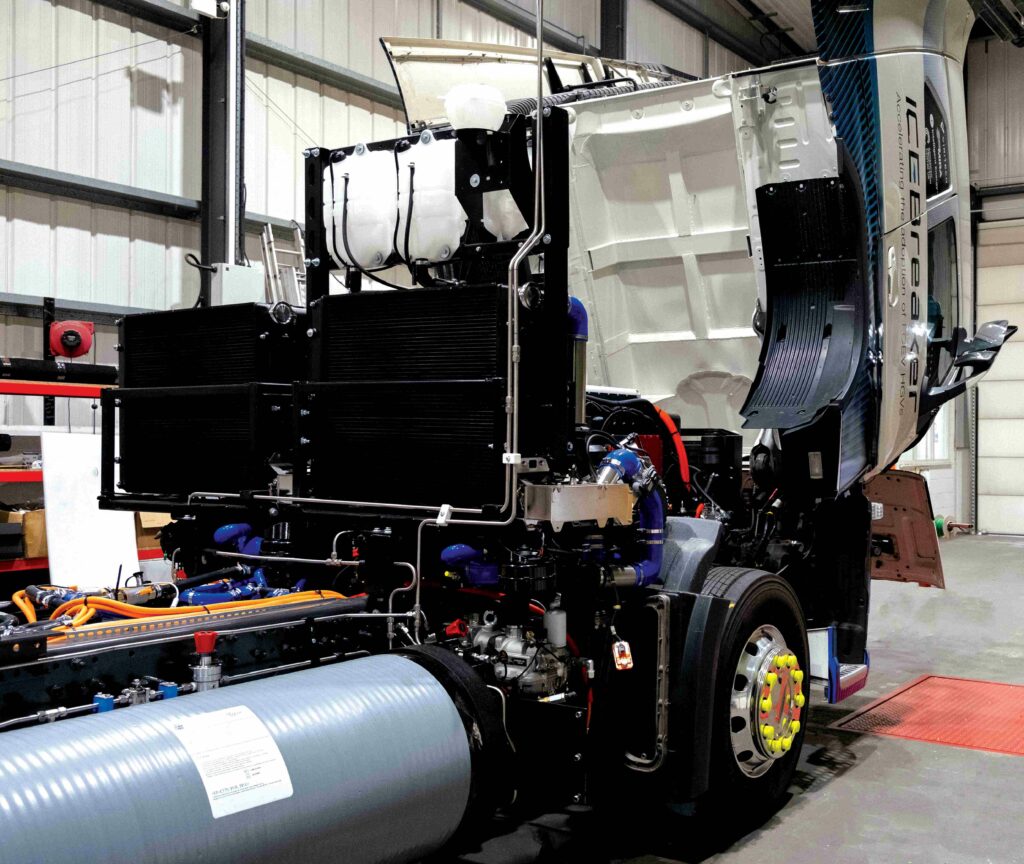
Thermal durability
Thermal management is one of the standout features of the IE-DRIVE HD100 system, and it is of critical importance in a commercial truck application where the system must perform in a variety of environments, from cold starts in winter to prolonged high-load operation in the summer.
The thermal management system developed for the ICEBreaker project uses IE’s proprietary evaporative cooling technology, which simplifies the balance of plant and enhances durability.
“The fuel cell utilises supporting balance of plant and control loops within the system for operating at extreme temperatures. The system manages the water temperature at cold and hot conditions to keep the fuel cell running at the optimum efficiency to avoid any unnecessary degradation,” Whatton explains.
IE’s evaporative cooling technology injects water directly into each active fuel cell. The water evaporates, absorbing thermal energy generated by the electrochemical reaction between hydrogen and oxygen. Steam is emitted as exhaust from the cathode and the water is reclaimed as part of the system design for re-injection into the fuel cell, significantly reducing the need for complex external humidification systems.
This type of cooling provides several benefits, Whatton says. By eliminating the need for large external humidifiers, the system reduces overall complexity and weight. “We’ve managed to simplify the thermal management system while actually improving its performance. The evaporative cooling not only keeps the cells at optimal operating temperatures but also helps in maintaining hydration, which is crucial for long-term durability.”
The absence of ‘cooling cells’, which are necessary in liquid-cooled fuel cells, increases the power density of the stack. Every cell in the HD100 stack is active in generating electrical power, maximising output while reducing unnecessary components. This enhanced power density has practical implications for vehicle design, allowing for a more compact powertrain and lower weight, which is crucial in a heavy-duty vehicle such as the ICEBreaker truck.
“Reducing the weight delta between hydrogen-powered trucks and their ICE counterparts is one of our primary goals,” Hübel says. “By using technologies like evaporative cooling, we can ensure the system is not only more efficient but also lighter, giving us a competitive edge.”
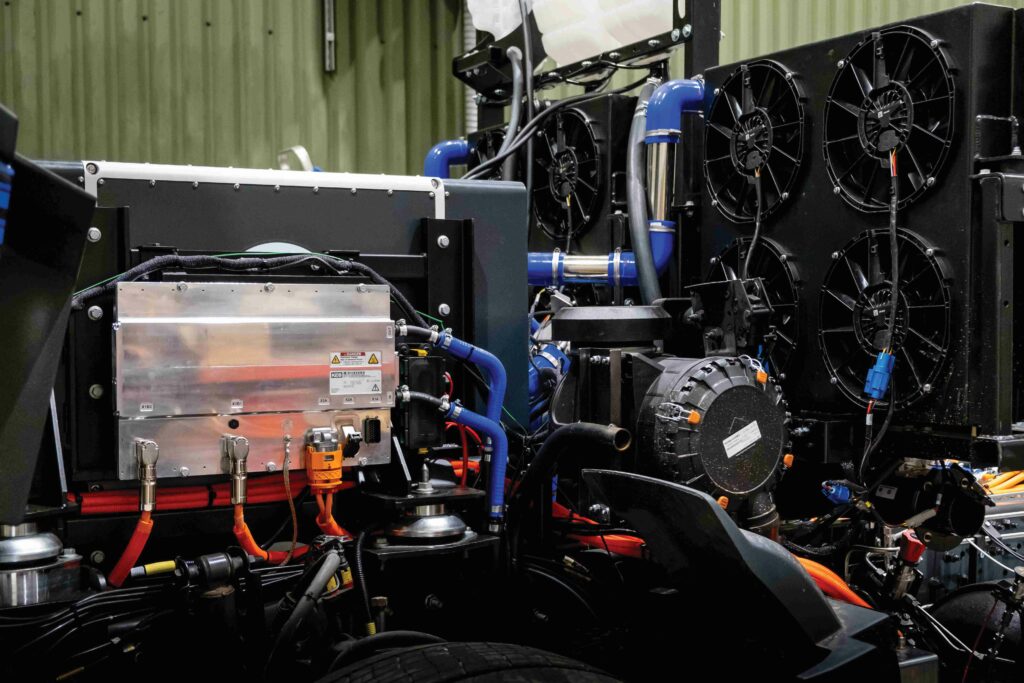
Hydrogen storage and safety
Storing hydrogen safely and efficiently onboard is a key challenge for any
fuel-cell vehicle. For ICEBreaker, hydrogen is stored in Type 4 carbon overwrapped pressure vessels (COPVs), which are designed to hold hydrogen at 700 bar. Each tank can hold 14.5 kg of hydrogen and the system complies with the stringent safety standards of UN ECE Regulation 134.
The system uses two-stage pressure reduction to ensure hydrogen drops quickly from 700 bar to 300 bar, and then to 10 bar as quickly as possible, minimising the length of high-pressure runs within the vehicle.
This attention to safety is vital in ensuring the ICEBreaker truck can operate under a wide range of conditions without compromising performance or reliability. The two-stage pressure-reduction minimises the risk of hydrogen leaks or pressure-related failures, which could be catastrophic in such high-demand applications. The team continuously evaluates the system during testing, especially in extreme conditions such as cold-weather starts and high-temperature operation.
“We want to ensure the system is robust enough for the real world, while setting a new standard for hydrogen safety. That’s why the project conducted a full ISO 26262 functional safety assessment of the hydrogen system to capture key design parameters,” says Rahman.
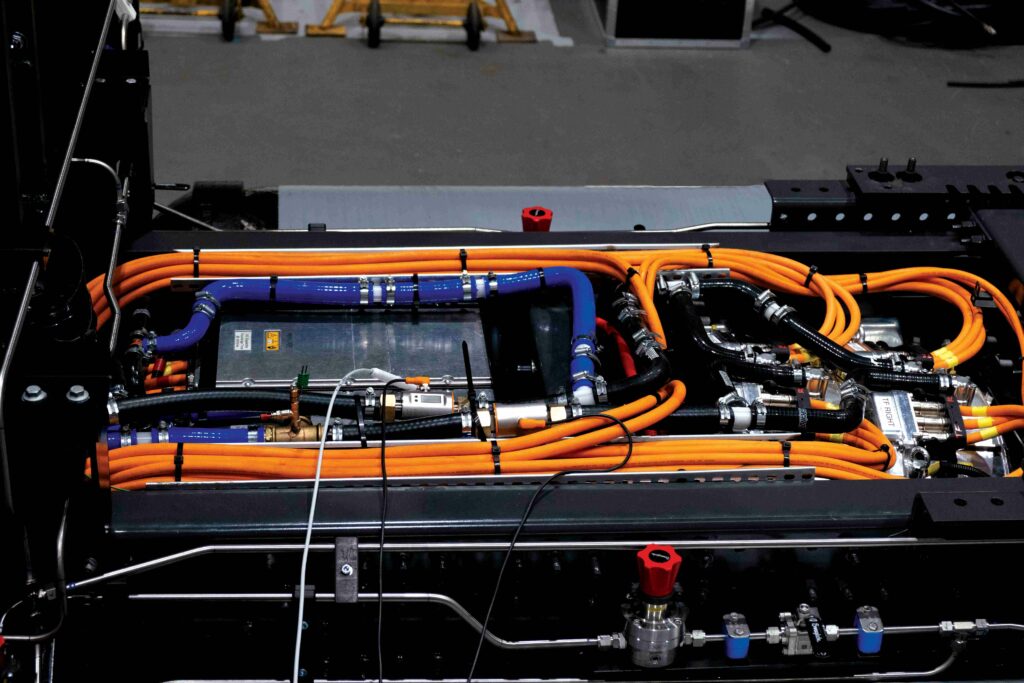
Startup and shutdown
Another crucial aspect of the fuel-cell system is its startup and shutdown times, which can have an impact on both the operational efficiency and durability of the power plant. IE has optimised the startup process to take around 30 s on average; a considerable achievement for a high-power fuel-cell system in an HGV.
Reducing startup times was a key requirement for the ICEBreaker project, given the operational demands of heavy-duty vehicles. IE’s Whatton notes that the system “has the capability to shut down immediately, but a short shutdown process is also implemented to protect the system against subsequent cold-start conditions”.
This attention to both startup and shutdown processes ensures the ICEBreaker fuel-cell system can operate efficiently in a variety of real-world conditions, from frequent stop-and-start urban environments to long-haul motorway runs.
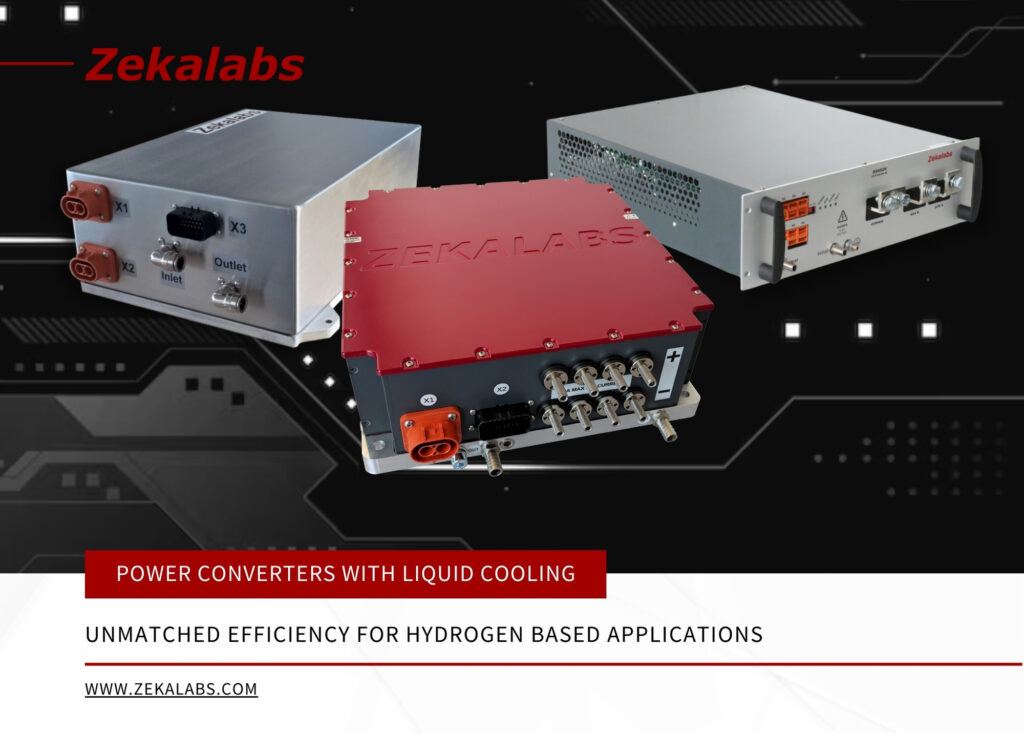
Longevity and degradation
Longevity of the fuel cell is critical to market acceptance of any power plant based on them, particularly when used in a high-demand application such as an HGV. The IE-DRIVE HD100 fuel-cell stack in the ICEBreaker truck is rated for an operational life of 10,000 hours at 100 kW net output. While this is an impressive figure, all fuel cells face inherent degradation mechanisms over time.
“Steady degradation of the electro-catalyst is a known issue, especially during continuous operation and start-stop cycles,” Whatton notes.
These degradation factors, however, can be mitigated. IE has developed strategies to reduce or even eliminate degradation under specific duty cycles or operational scenarios, improving the overall durability and longevity of the system.
The ICEBreaker vehicle’s control systems play a crucial role in managing the fuel cell’s operating points to minimise unnecessary wear. By carefully managing start-stop cycles and maintaining optimal load conditions, the system not only extends the life of the fuel-cell stack but also ensures performance remains consistent throughout its operational life.
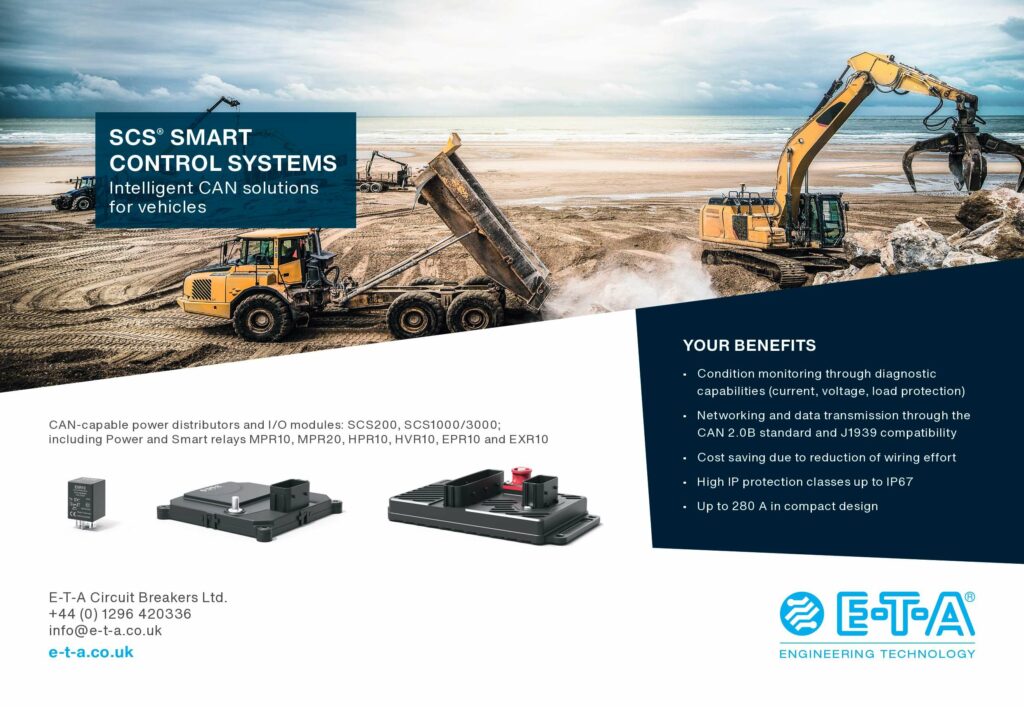
Power distribution
The management of energy between the fuel cell, battery and electric motors is a sophisticated process that balances performance, efficiency and system longevity. Horiba MIRA’s energy management algorithms are at the heart of this system, ensuring power distribution is optimised under varying driving conditions.
“The vehicle control unit uses algorithms that optimise motor torque requests and fuel-cell operating points, while simultaneously managing hydrogen consumption and subsystem behaviour,” according to Rahman.
The primary goal is to minimise hydrogen consumption while ensuring the vehicle performs efficiently across a wide range of driving conditions. The system works by constantly adjusting the power contribution from the fuel cell and the battery, depending on real-time load demands, driver inputs and environmental conditions.
This dynamic power distribution is critical for maintaining overall vehicle performance and ensuring the fuel cell operates within its optimal efficiency range, especially during transient loads or peak demand periods.
Battery system integration
The ICEBreaker truck is equipped with a 16 kWh battery system, based on lithium-titanate oxide (LTO) chemistry. This battery is designed primarily to manage transients, store regenerative braking energy and assist with startup processes.
“Our battery is there for peak power shaving, storing energy from regenerative braking and providing transient support to the fuel cell,” Hübel says. With a range of 450 V to 810 V, the battery plays a critical role in ensuring smooth power delivery during load spikes that exceed the fuel cell’s output.
The battery is not only handled by the battery management system (BMS) itself, but also through the vehicle’s overarching energy management system, which ensures it operates within an optimal state-of-charge (SoC) range of 20-80% – essential for maximising its longevity.
“We’ve found through long-term testing that allowing the battery to discharge below 20% SoC significantly degrades the cells, so our system works to keep the charge within this window,” says Hübel. By doing so, the ICEBreaker truck can preserve the battery’s health while balancing the energy demands between the fuel cell and electric motors.
In terms of power output, the battery is capable of accepting and delivering up to 480 kW of peak charge and discharge, respectively. This high discharge rate is essential for supplementing the fuel cell during peak loads, ensuring the electric motors have sufficient power when required.
“The inverter, battery and fuel cells are all connected to the same high-voltage bus, meaning the battery can instantly discharge to fill any power gaps during high-demand periods,” Hübel adds.
Cooling and monitoring
Thermal management is a key consideration for the battery system, particularly given the truck’s high-power demands and the need for consistent performance in diverse operating conditions. The LTO cells in the battery are liquid-cooled, with the coolant circulating on either side of each cell.
Temperature and voltage are closely monitored for every individual cell to ensure uniform performance and prevent localised overheating.
“Our LTO cells have low internal resistance, which reduces thermal losses, but active cooling is still necessary to maintain optimal performance,” says Hübel.
This liquid cooling system not only improves the battery’s overall efficiency, but also helps to extend its lifespan by preventing thermal degradation – a common issue in high-power battery systems. By maintaining cell temperatures within a narrow range, the system ensures consistent performance, even during sustained high-power operations.
Power electronics
Power electronics play a pivotal role in ICEBreaker, converting energy from the fuel cell and battery into usable power for the electric motors. Viritech has developed a custom,
bi-directional, DC-DC converter, capable of handling 400 A continuous current, which is crucial for maintaining efficient power flow between the high-voltage components.
“A lot of existing DC-DC converters struggle to meet the high current requirements in heavy-duty applications, often de-rating under load,” Hübel says. “Our design avoids this by optimising component selection and thermal management.”
The converter operates at a switching frequency of 100 kHz, which helps to reduce component size and improve response times, compared with devices that switch at lower frequencies, enabling the power electronics to chase the voltage sag of the HV bus/battery pack under load, increasing stability. The use of advanced technologies, such as low on-resistance MOSFETs and high thermal-conductivity interface materials, ensures the system remains compact, efficient and reliable.
Liquid cooling, based on a water-glycol mix, is also used to manage the temperature of the power electronics and prevent thermal failure. “The DC-DC converter contains multiple stages, so could run on fewer stages in the event of thermal failure,” Hübel says. “But, in reality, you wouldn’t want to do that as a failure could have knock-on effects on other areas of safety, so you’d most likely put the vehicle in ‘limp home’ mode.”
Tandem motors
The ICEBreaker truck employs a tandem motor setup, using permanent magnet technology to deliver 800 kW of peak power and 7,000 Nm of torque. This configuration provides 360 kW of continuous power. The motors are configured in a direct-drive arrangement, with power transmitted via a prop shaft to the differential and drive shafts in the rear axle. This eliminates the need for a conventional transmission system, simplifying the drivetrain and improving overall efficiency.
“By using direct drive, we’re able to take full advantage of the motor’s high torque at low speeds, without the need for gear reduction,” Hübel says.
Cooling is once again a critical consideration, particularly given the high-power output of the motor system. The motors are liquid-cooled using a water/glycol mixture, with the coolant directed close to the magnets for maximum efficiency.
Regenerative braking is an essential feature of the ICEBreaker truck, helping to recover energy that would otherwise be lost as heat during braking. The system captures approximately 30% of braking energy and redirects it into the battery via the inverter. A key aspect of this design is the prevention of energy flowing back into the fuel cell, which is managed by a DC-DC converter that isolates the fuel cell from the braking energy, Hübel explains.
Critical control
ICEBreaker’s energy management algorithms are critical in optimising the motor-control system. They dynamically optimise motor torque requests, fuel-cell operating points and other subsystem behaviour to maximise vehicle performance while minimising hydrogen consumption, Rahman says.
The control system is particularly effective in handling the high torque output of the electric motors, especially at low speeds, he says.
Trucking ahead
Hydrogen fuel-cell technology has the potential to revolutionise the heavy-duty transport industry, but it will require further validation of the total cost-of-ownership (TCO) model for end-users, Hübel cautions. “We need projects like ICEBreaker to demonstrate that hydrogen-powered trucks are a viable alternative to diesel, both in terms of performance and cost.”
ONLINE PARTNERS
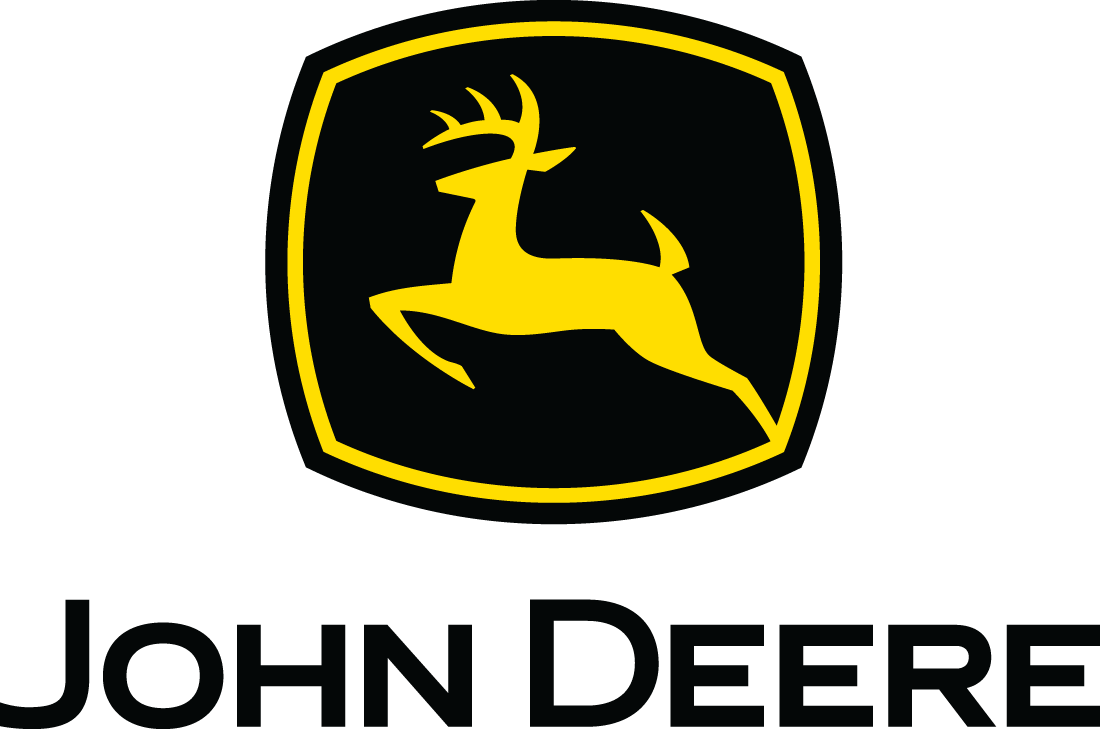
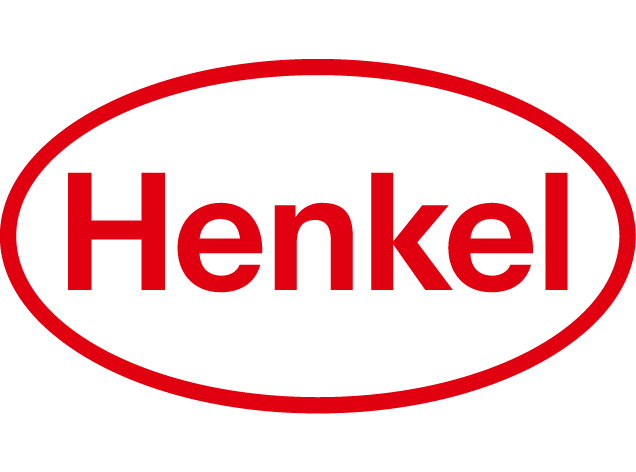
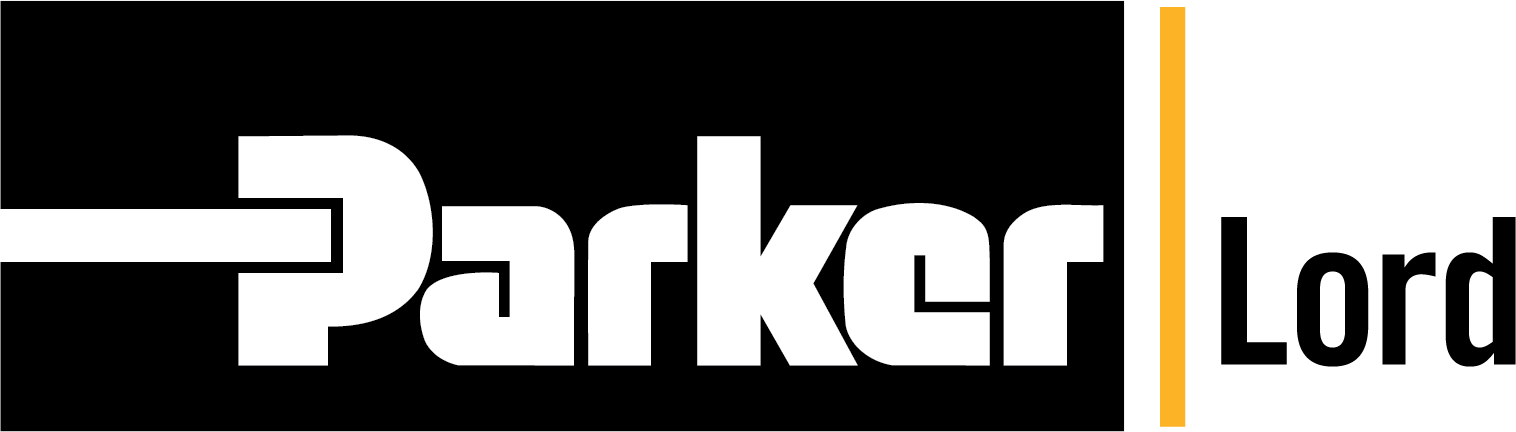
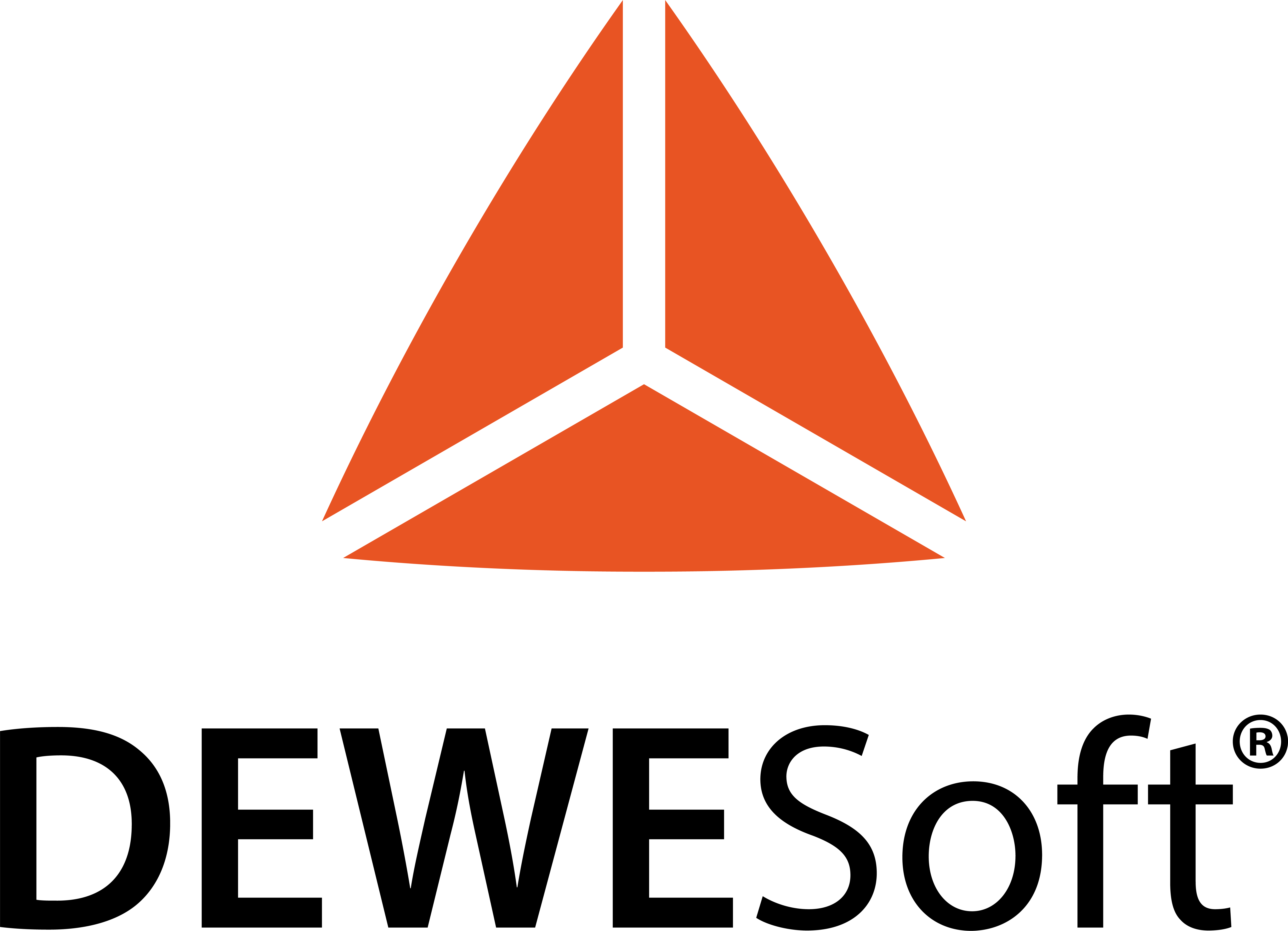
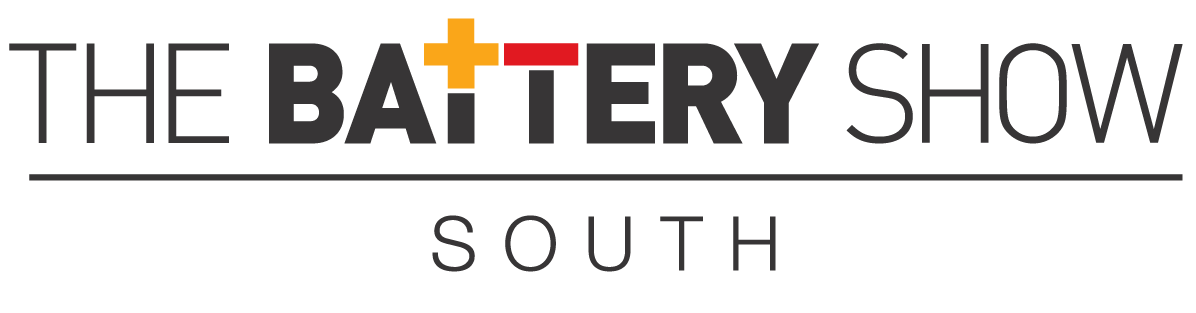
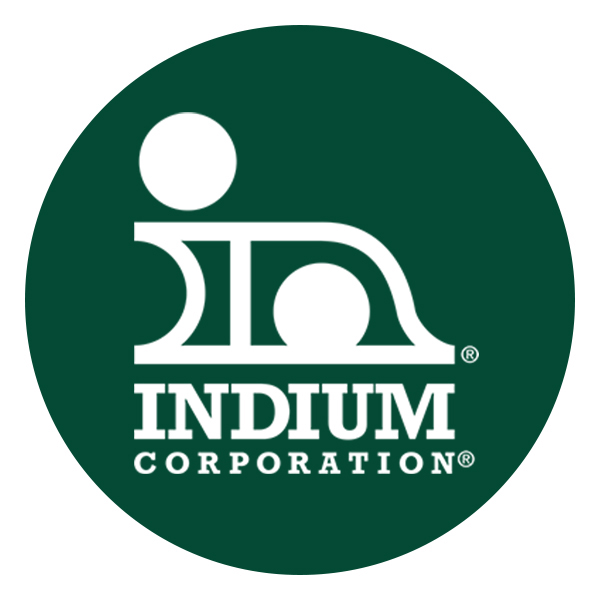

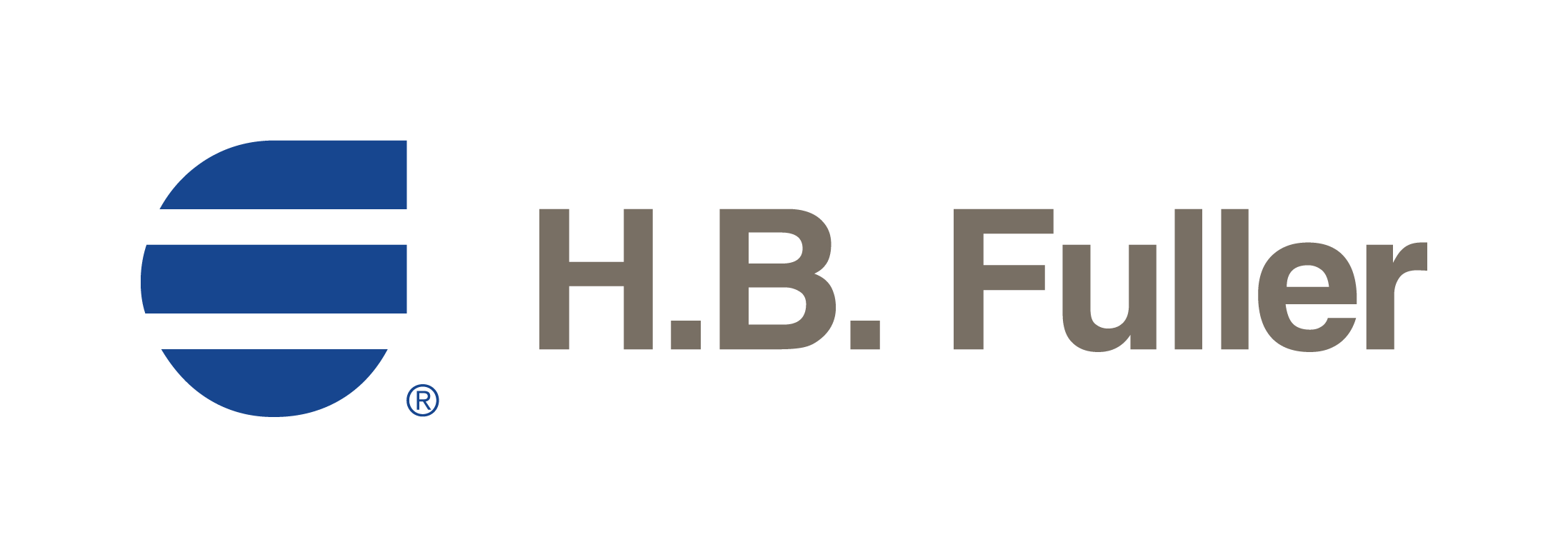
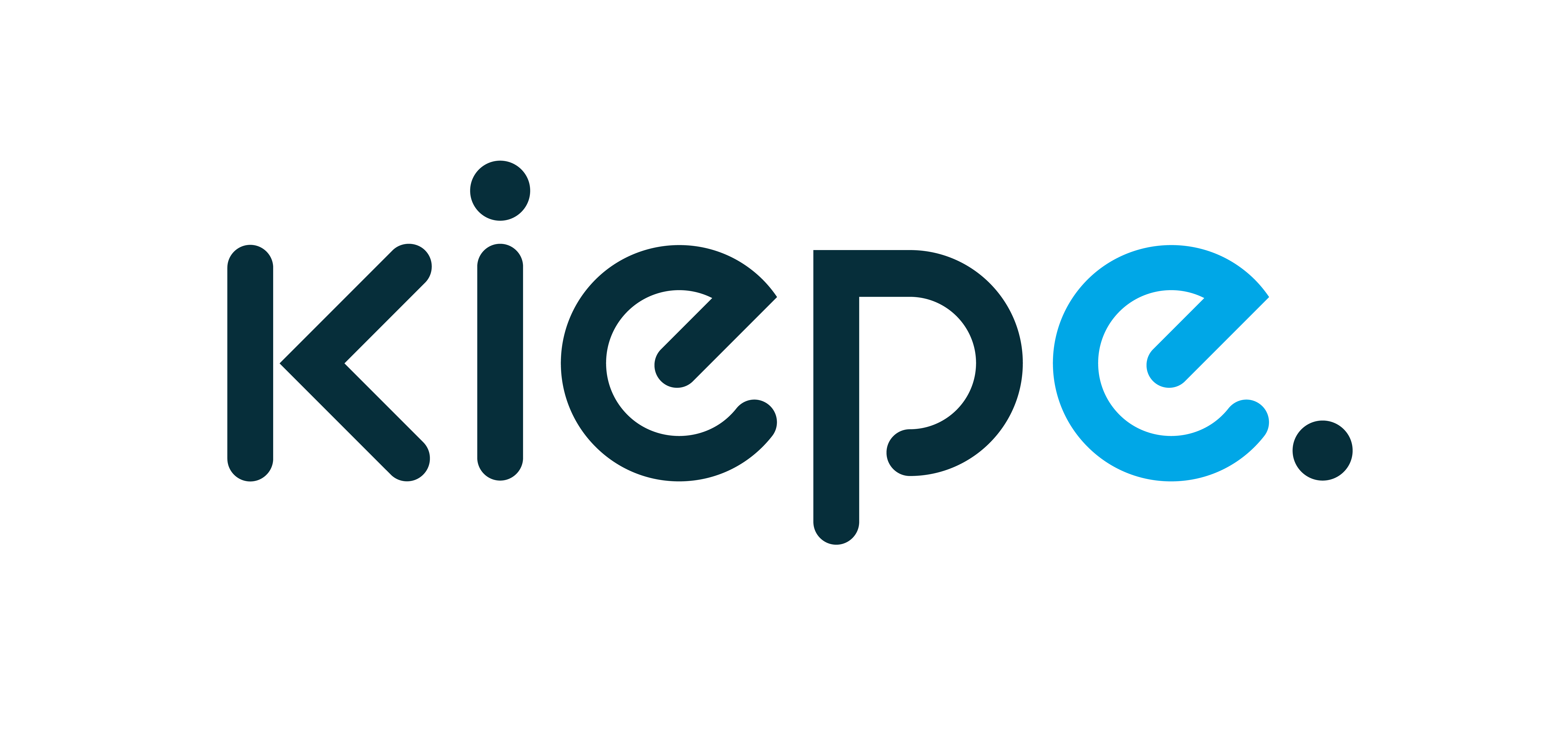
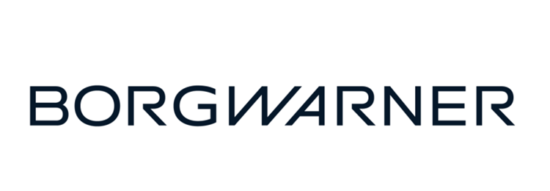