In conversation with Henkel’s battery expert Dr Keon Woo Lee
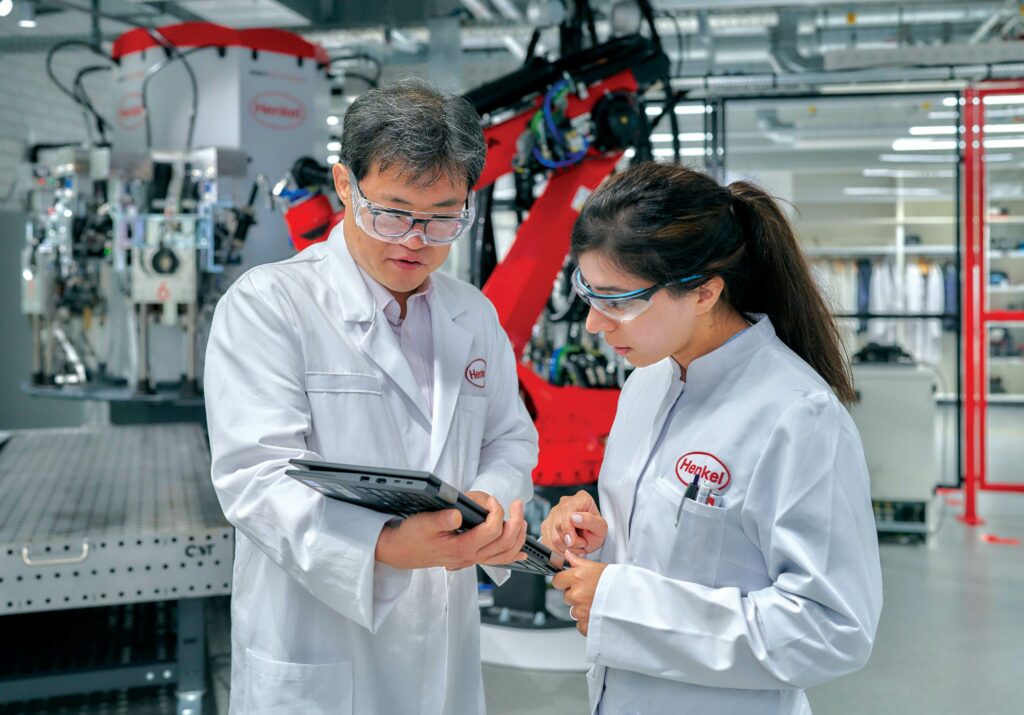
(All images courtesy of Henkel)
Peter Donaldson chats to a leading battery expert, who says innovation is all about winning against the things you can trade off
In a rapidly evolving EV landscape, the quest for advanced battery technologies remains at the forefront. Dr Keon Woo Lee leads Henkel’s Fuel the Future Team and Engineering and Advanced Testing Team at the newly opened Battery Engineering Center (BEC) within the Inspiration Center Düsseldorf, Germany.
Here, they collaborate with battery manufacturers and automotive OEMs to tailor materials, and even formulate new ones to meet increasingly stringent demands for performance, safety, service life and sustainability.
Keon categorises the materials his team focuses on into three key areas. “The first one is conductive coatings,” he says. “These are coating materials used inside the battery cell, primarily for the dry electrode process.”
The conductive coating plays a crucial role in the sustainable manufacture of battery cells without using hazardous solvent. This technology made lithium iron phosphate batteries practical; a chemistry gaining traction in EV applications as the emphasis on stability and safety grows. It now opens up another level of battery manufacturing technology – dry coating.
The second category is safety materials, which includes coatings and potting materials with properties such as dielectric protection, thermal management (conductivity and insulation) and structural integrity.
Thirdly, he emphasises the importance of rapidly emerging debonding technologies. “Debonding is connected with the sustainability of batteries,” he says.
Aiding the development of these materials, Keon’s team at the BEC is heavily invested in digital technologies, including simulation and machine learning. “We are working on modelling our materials and validating them through real-world tests.”
The team collaborates with battery and EV manufacturers to customise materials for their specific needs. “We were already well-equipped with materials and formulations, and with component-level testing, and we’ve also invested in a full-scale test facility – our BEC,” he explains.
This facility allows Henkel to model, simulate and validate new materials and designs with real batteries.
“Partners visit our facility more frequently because we can give them what they want,” and manufacturers work directly with the Henkel team at the BEC, Keon says. “We show them how to apply and test our materials, creating a collaborative environment.”
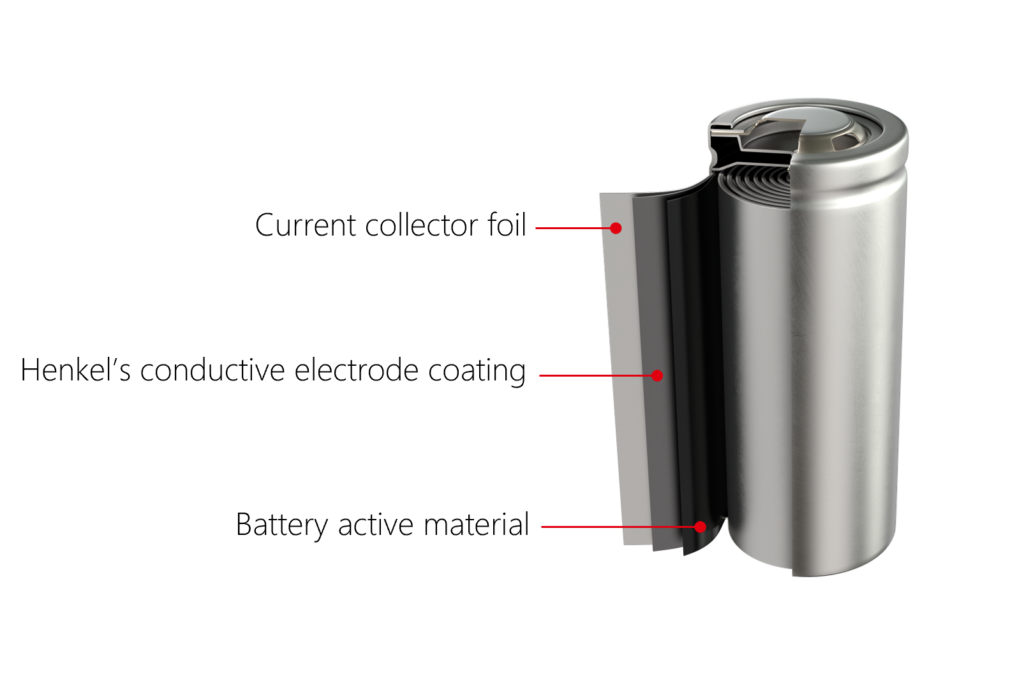
Debonding
Adhesives that can be made to debond in response to a trigger under tightly controlled conditions are a major focus of r&d efforts in the battery industry, Keon notes.
“This technology is unprecedented. Nobody has been successful in this area so far, but I believe it will change the whole industry.”
Debonding allows for easier rework and repair of batteries, which is critical as EVs age, he says. This, in turn, enhances recycling and disposal methods, and while the type of debonding is important, the context in which it is applied matters more.
“It’s not that the type doesn’t matter, but it’s more related to how you use it, where you use it, for what purpose, and how advanced your technology is,” he says.
Debonding triggers being explored include heat and electric currents, but Keon highlights the limitations of using heat directly on battery components, imposed by the sensitivity of lithium-ion chemistries to high temperatures and the consequent risk of thermal runaway. This sets very strict boundary conditions.
Electrical debonding offers a promising alternative, although it is not without its complexities. Keon points out that minimising the voltage while maximising the contrast before and after debonding is key.
“Nobody wants to apply 100 V because that’s dangerous,” he says, noting that the challenge lies in creating a formulation where debonding occurs easily without compromising the initial adhesion.
Keon says recent advancements have led to the creation of formulations that maintain strong adhesion comparable to that of traditional adhesives while allowing for efficient debonding.
“You don’t need to clean the surface really hard because it’s cleanly debonded, which can make it easy to rebond,” he says, emphasising the importance of being able to control which side of the material debonds.
Regarding sustainability, Keon emphasises the need to think beyond recycling for EV batteries. “We must first focus on elongating battery life. By debonding, you can ease repair, reuse and repurposing, which are most important.”
Prolonging the service life of batteries not only conserves resources, but also minimises the carbon emissions associated with recycling processes, he points out.
Keon argues that sustainability cannot come at an excessive cost to consumers. “Some companies just force customers to pay more for sustainability. That doesn’t make sense,” he says, adding that the industry must find ways to secure sustainability without burdening customers financially.
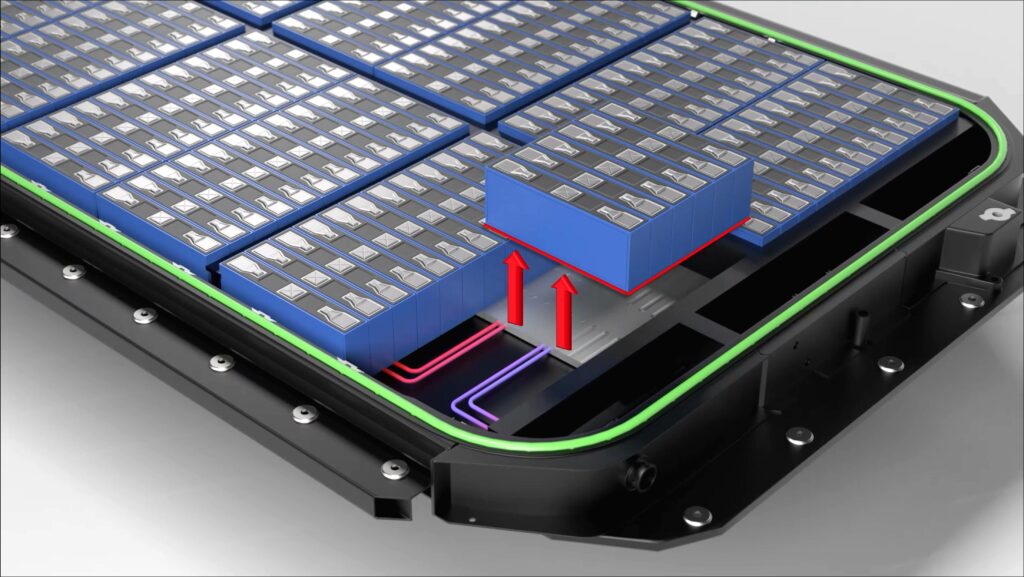
Thermal challenges
In the thermal management of high energy-density battery packs, Keon says effective heat control goes beyond simple cooling: “The battery needs to be conditioned within a minimum range of temperature distribution. It’s about controlling the variance among cells to maintain the health of the entire battery.”
Elaborating on the complexities of dynamic thermal conditions, he says: “Specifying thermal conductivity in one condition doesn’t make sense without understanding the entire cooling strategy of the electric vehicle.”
Keon explains that optimisation is key, especially given the changes in temperature that occur during charging and discharging.
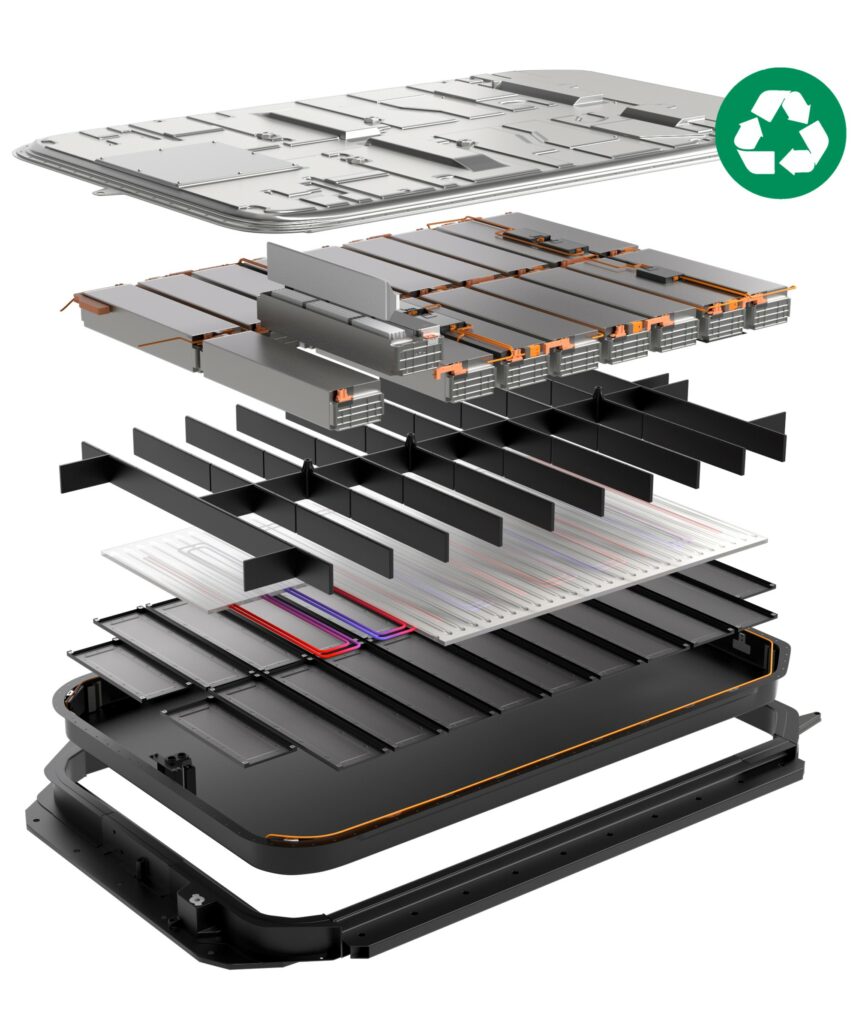
Addressing extremes
Extreme thermal and mechanical stresses pose challenges to all the adhesives, coatings, thermal interface materials and gap fillers used in EV battery packs, with vibration adding to complexity in the mechanical domain. “We must consider vibrations in multiple directions and at different frequencies,” Keon says.
Finding the right bonding strategy is crucial for different areas of the battery. “This is not something you can grab off the shelf. When it comes to extreme conditions, we have to understand all of the vibration and impact cases, and adjust the formulations to make the best-performing materials for each bond line,” he explains.
“When it comes to thermal stresses, again it’s a matter of finding the right balance. We have to understand the whole cooling strategy,” Keon says. “Typically, EV platforms now have integrated cooling systems, which means the cooling flow is not simple, and you cannot simply turn it on and off. So you have to find the best strategy, and our thermal interface material must fit perfectly with this.”
On the impact of high-rate battery charging, Keon says: “When the C-Rate is high, heat is generated for a really short period of time and then it just shuts off. It has to be controlled in a very specific manner, so we’re working on that using simulation plus optimising the thermal conductivity and bond-line thickness, and even the overfill/underfill conditions.”
As the industry pushes for faster charging, Keon says materials inside the battery must adapt. “The battery cell serves as a boundary. Our conductive coatings reduce interfacial resistance, which is key for minimising heat generation during fast charging.”
He points out the differences in charging strategies, noting that at least one EV manufacturer uses two types of battery cells with varying chemistries from different manufacturers within a single battery pack; one optimised for energy density and the other for rapid charging. This adaptability is crucial in a market where different chemistries and charging rates coexist.
The BEC also plays a role in developing solutions for battery pack assembly, with scalability attracting copious attention as OEMs strive to scale up production. “Scalability is a significant challenge as demand surges,” Keon notes. “We need to optimise formulations to create the best flow and speed for mass production.”
This involves paying close attention to material rheology and advances in pumping technologies, but the ability to bring down module and pack lids quickly is also crucial for rapid, large-scale production. “You can actually squeeze the battery stack down very fast, but if you do it too fast the stress can be too high and the battery housing can be damaged,” he says.
“All manufacturers want to do this faster, so we have to optimise the rheology. We call it squeeze flow and now have the capability to simulate it. Secondly, we are working on connecting this squeeze-flow behaviour to formulation through our big materials database.”
When it comes to long-term durability, Keon highlights the challenge of ensuring materials last for a vehicle’s lifespan of 10-15 years. “For structural adhesives, we can follow established methodologies, thanks to OEM standards. However, thermal interface materials are more complicated because they must also serve a structural role.”
This dual function adds complexity, and testing standards are not always sufficient. “We need real-world tests in our BEC to understand what has never been tested conventionally,” Keon says.
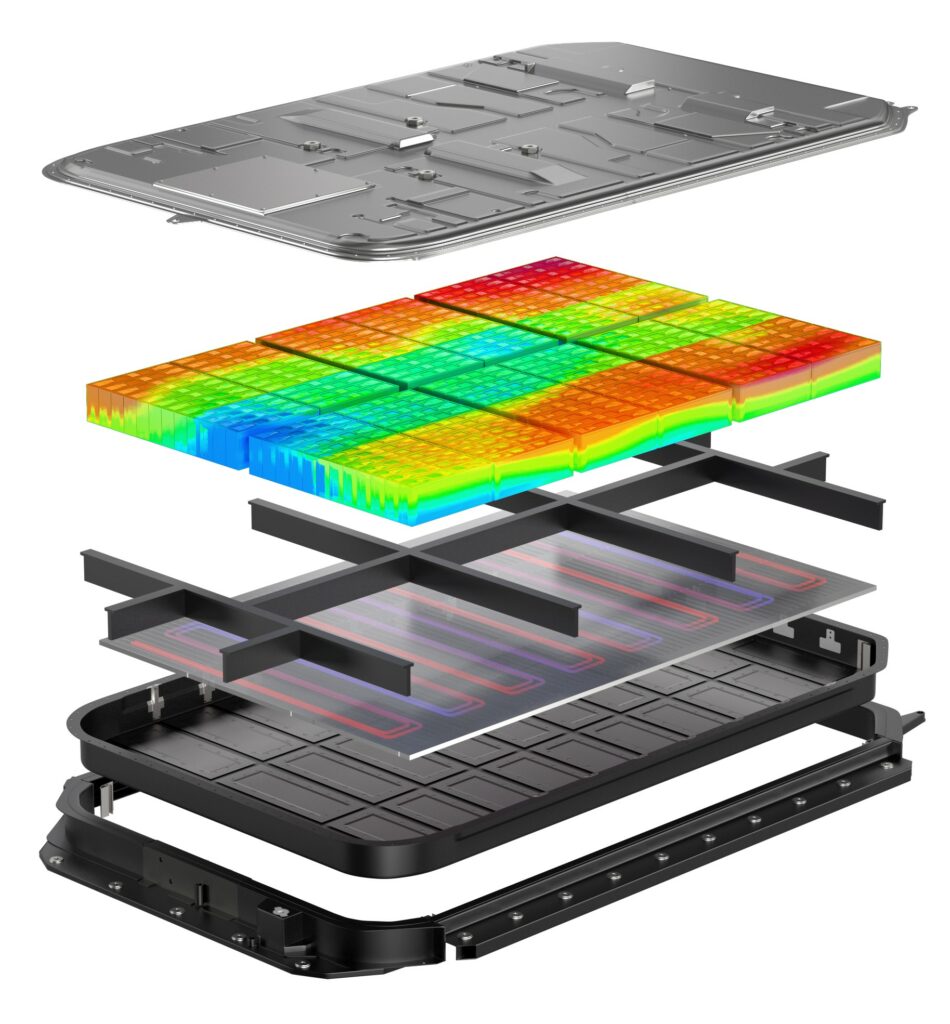
Evolving material needs
As battery designs continue to evolve, Keon expects material requirements to change significantly, bringing greater emphasis on bespoke formulations.
He acknowledges the challenges posed by stricter regulations and heightened customer expectations, and “to meet these demands, we must continuously improve our safety portfolio”.
Keon describes his early career as one of fortunate transitions, having started at LG as a product developer, focused on photoresist materials for semiconductor and display manufacturing. “It’s a really nanoscale technology,” he says, referring to his work in lithography; a process used to create intricate patterns on semiconductors.
Although his career initially revolved around this field, Keon eventually pivoted to battery science and engineering as the battery industry began to expand rapidly. “I was lucky to leave one part of the company to enter this industry,” he recalls.
This transition was not without its challenges, and Keon recounts how the shift to battery materials required adaption to a new set of technological demands. One of his early projects involved developing thermal interface materials for emerging EV platforms in 2017-18. “You have to optimise the thermal interface and you need some special materials, which were not really found off the shelf,” he says.
The process of finding solutions for thermal interface materials was a complex and sometimes frustrating journey, but it ultimately helped to establish best practices.
Rather than attributing his career development to specific mentors, Keon spoke about the broader societal and industrial changes that shaped his path. “I recall the circumstances,” he says, highlighting how external forces, such as geographical shifts in the industry, influenced his decision to pursue battery engineering.
His academic background in physical chemistry, particularly his use of quantum chemistry to understand molecular reactions, has also played a significant role in his approach to real-world engineering challenges.
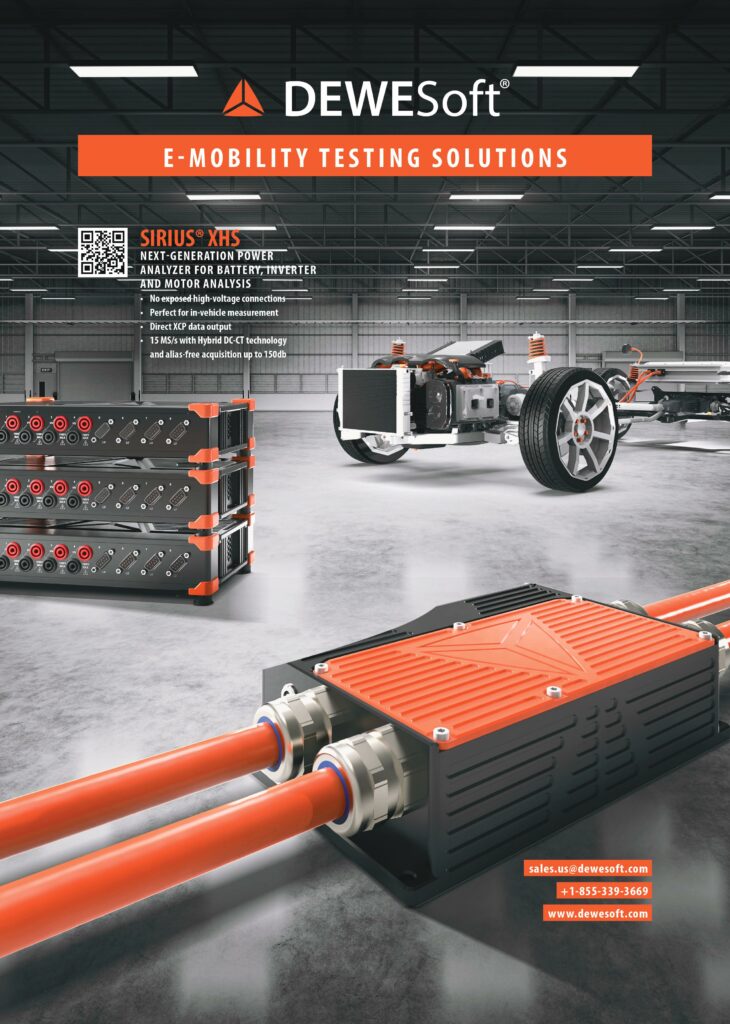
While these technical skills do not transfer directly to his current work, they have honed his ability to “minimise failures” and “increase the speed of development” by thoroughly understanding the mechanics at nanoscale.
Whether discussing the trade-offs between performance and sustainability or the need for collaboration, Keon’s approach is one of careful consideration and optimisation. He expresses a dislike for the term “trade-off”, viewing it as a challenge to overcome rather than a fixed constraint.
“Innovation is all about winning against the trade-off thing,” Keon remarks, underscoring his belief that there is always a way to find a solution that maximises benefits across multiple factors.
In philosophical terms, Keon says he does not see the push for breakthrough technologies as being separate from the need for proven and reliable solutions. “Earlier developments were based on processes proven over time, especially for automotive materials,” he says. “Everything has to be validated through proper processes.”
Collaboration is another critical element of innovation for Keon, who believes successful collaboration hinges on understanding the needs of all the parties involved. “The most important thing is what they can get,” he says, stressing the importance of mutual benefit in partnerships.
Keon also touches on the role of risk and experimentation in a field where safety and performance standards are paramount, and he highlights the importance of real-world testing, particularly at the BEC, where the team can validate new materials and designs under real conditions. “Until we validate it with real parts, we cannot be sure at all,” he adds.
Reflecting on the broader challenges facing the EV battery industry, scalability, safety and sustainability still top his list of critical issues. “The ramp-up of production is so fast, but production speed is not high enough,” he remarks. Safety remains an ever-present concern, with Keon noting that “nothing can be safe enough”.
Finally, he points out that while sustainability is a pressing issue, the industry’s current focus is on profitability and cost. However, he believes innovations such as debonding, which extend battery life, will play a crucial role in making sustainability more achievable over the long term. Keon’s passion for communication stands out as a key factor in his problem-solving approach. He frequently seeks out the insights of industry peers, former colleagues, and even cold contacts to gather information and solve technical challenges. “It’s all about the mass knowledge thing. I want to use the big data in the industry,” he says.
He also has a fascination with supply chains, geopolitical trends and the broader market dynamics that influence technological development. For Keon, innovation is not just about technology but also about understanding the larger forces that shape the industry.
“All this information creates boundary conditions, and how far you can go,” he adds.
Dr Keon Woo Lee
Born in Seoul in the Republic of Korea in 1975, Dr Keon Woo Lee earned a BSc in chemistry from the Korea Advanced Institute of Science and Technology in 1996, followed by an MSc in physical chemistry in 1998.
Keon studied under an exchange programme at Ruprecht Karls University in Heidelberg, Germany in 1999, and then as an extramural student at Cornell University in the US in 2001.
He earned his PhD in physical chemistry from the Korea Advanced Institute of Science and Technology in 2002, returning to Cornell for post-doctoral research in 2002-03, later gaining an MSc in international executive management from Lancaster University in the UK in 2015.
With his doctorate, Keon joined LG in Korea in 2003 to develop photoresist materials for electronics, and he moved into the development of battery materials in 2015.
He joined Henkel in 2017 to work in the same technological areas, becoming the leader of Henkel’s Battery Expert Team in 2021.
As a counterpoint to his scientific talents, his favourite activities at school were sports, particularly basketball and soccer, and music expressed through singing and playing guitar.
Professionally, Keon is keen to remain in the area of advanced technological development.
“I really want to call myself – eventually – an innovation accelerator,” he says. “Most CTOs end up managing everything, making decisions, but I really want to be more on the strategy and project management side, facilitating or accelerating innovation.”
On the personal front, Keon says he has rediscovered the value of spending quality time with his wife and family – a new “hobby” that he says helps him recharge and maintain balance.
Click here to read the latest issue of E-Mobility Engineering.
ONLINE PARTNERS
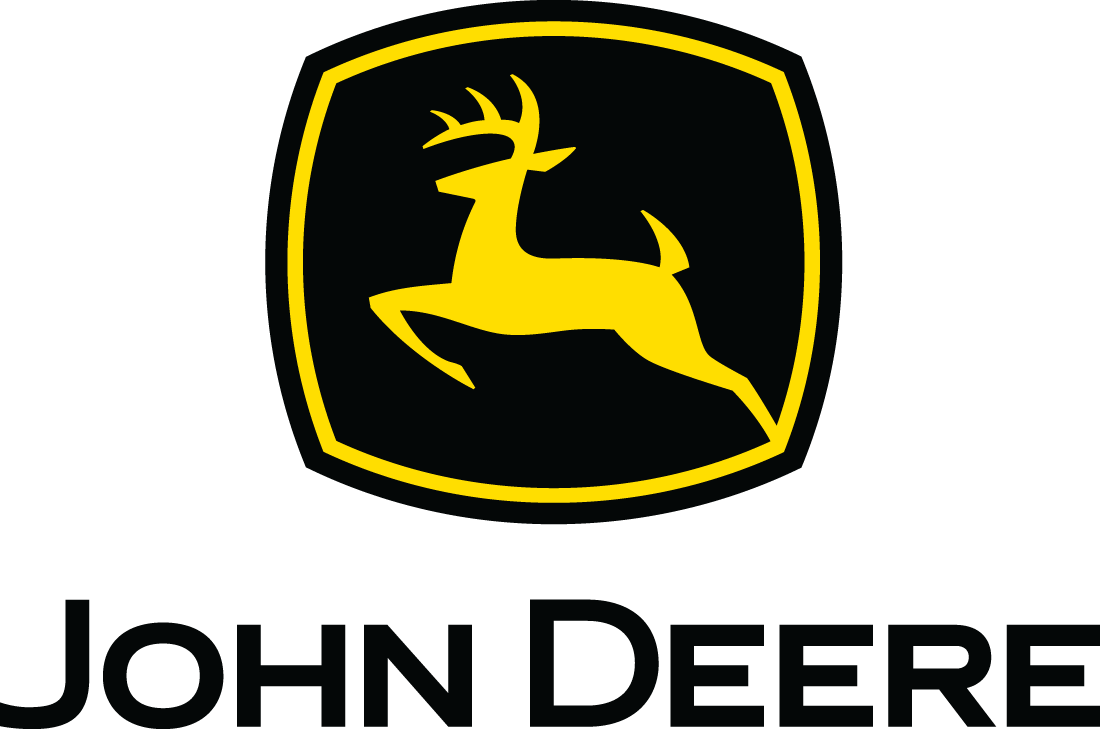
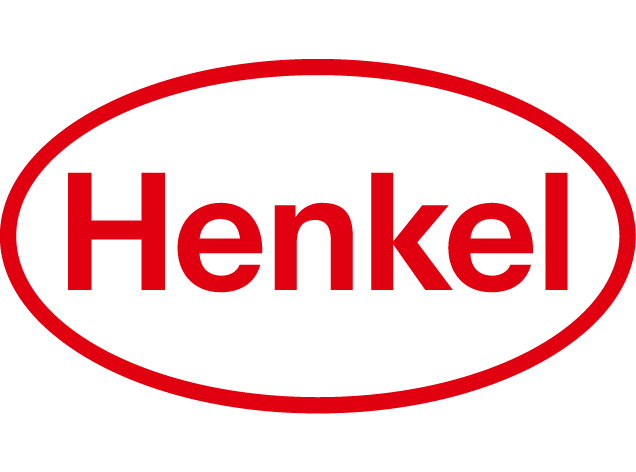
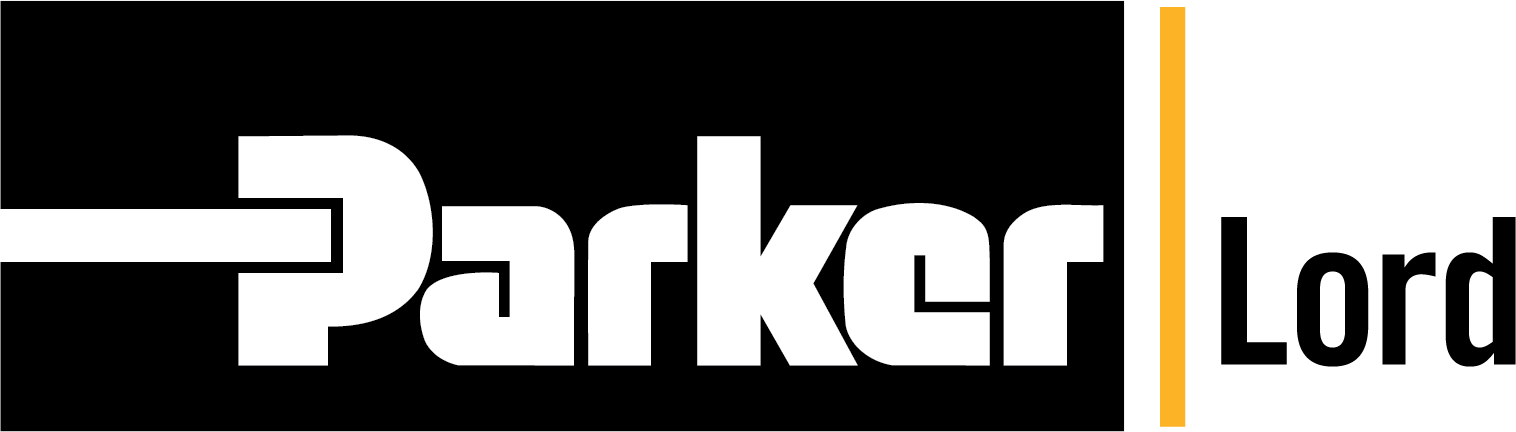
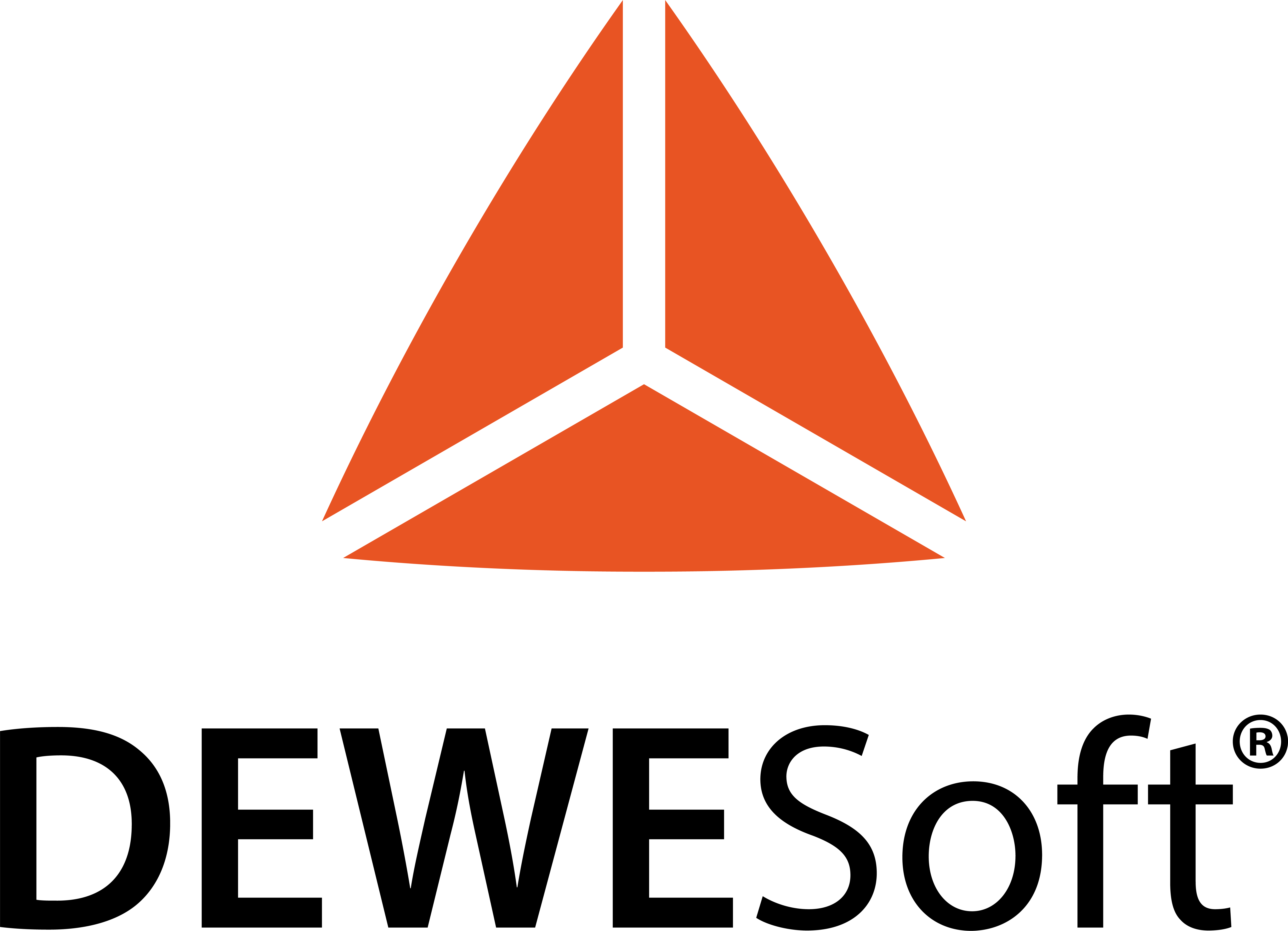
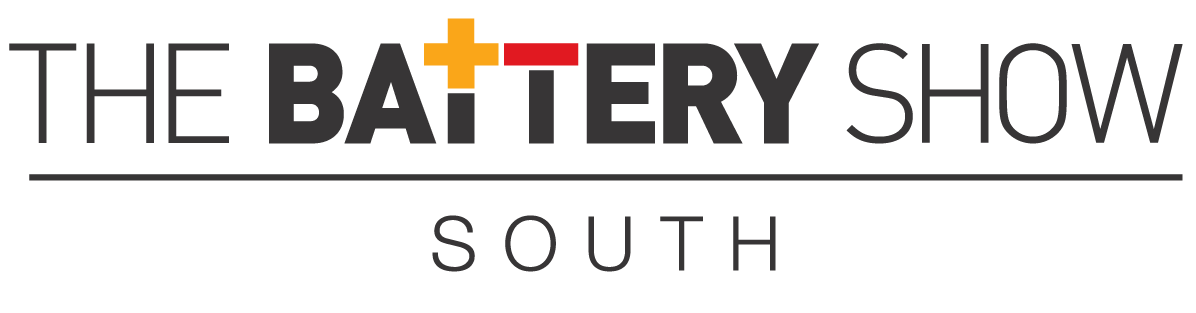
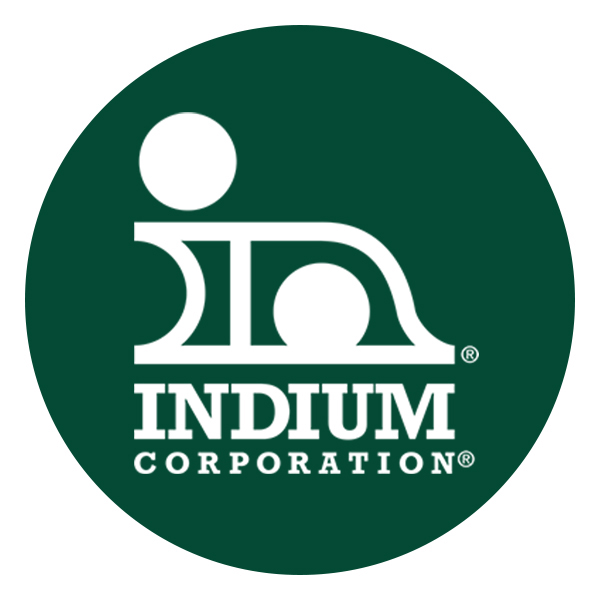
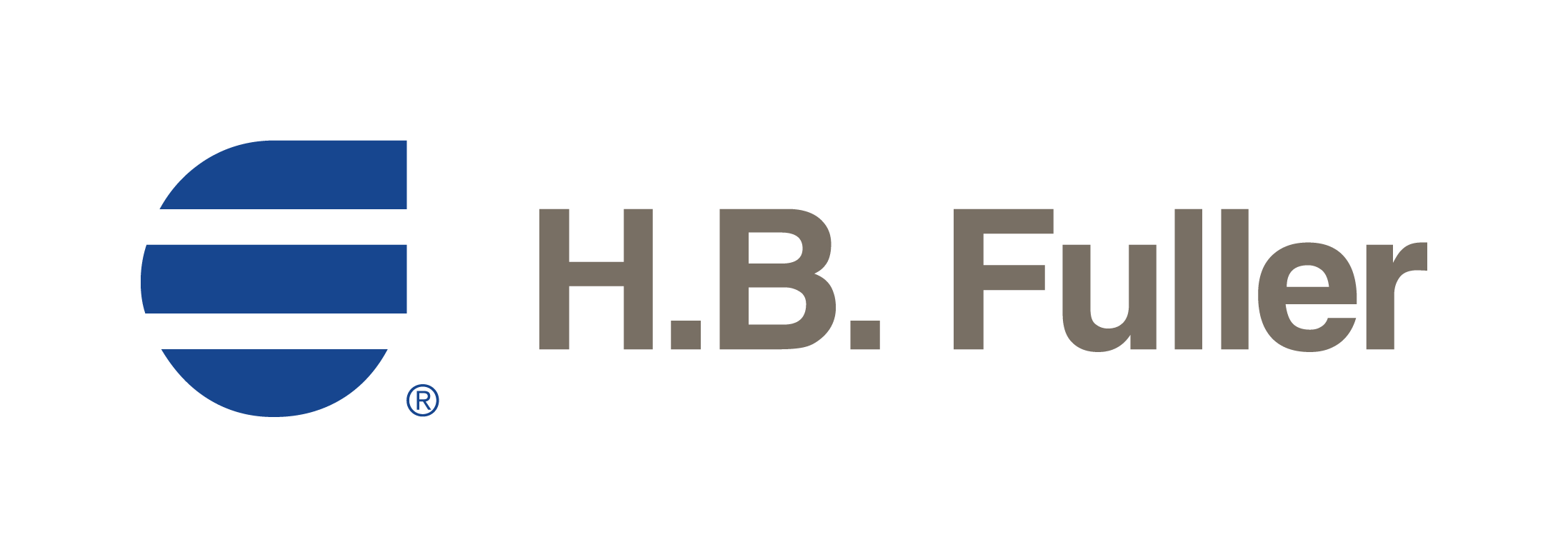