Gap fillers and TIMs
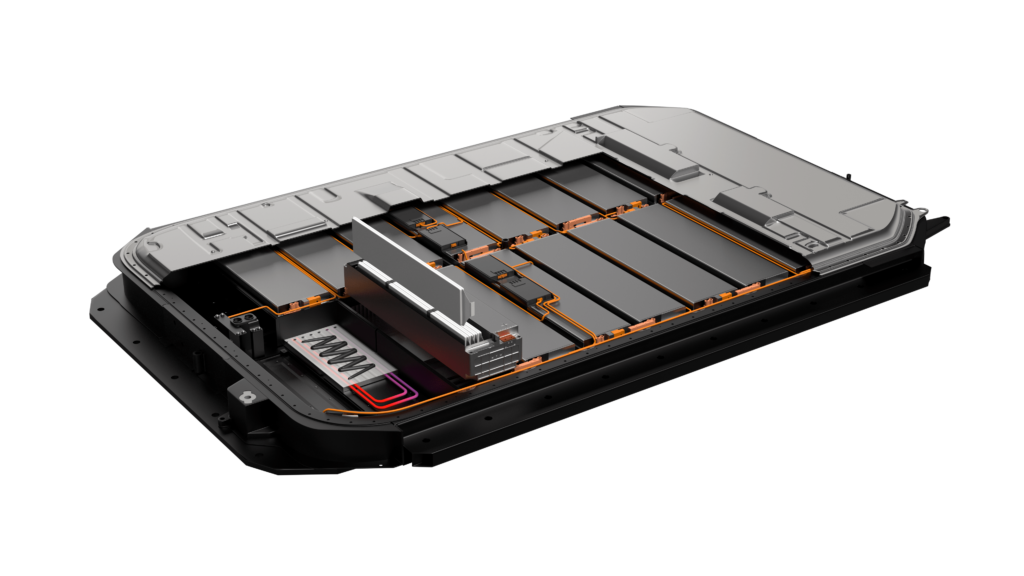
(Image courtesy of Henkel)
Mind the gap
Peter Donaldson examines the shifting demands on thermal interface materials and suppliers’ innovative responses
Thermal interface materials (TIMs), including gap fillers, are crucial for managing heat in battery packs, sensors and electronics in e-mobility applications. Their developers have to meet changing demands from battery builders and vehicle OEMs as they implement novel architectures moving into cell-to-pack, cell-to-chassis and cell-to-body schemes.
At the same time, the need to ease manufacture, reduce impact on health, safety and the environment, and to enable dismantling in support of repair, repurposing and recycling bring further complexity to the developer’s task.
Gap fillers are primarily used to fill large voids between components in a pack to ensure efficient thermal transfer between non-flat surfaces, conforming to the shape of the components to improve heat dissipation and help maintain temperature uniformity.
Other TIMs, including thermally conductive adhesives (TCAs), are used to enhance the flow of heat between two flat surfaces. They bridge the microscopic gaps and irregularities at the interface between a heat source and a heat sink to maximise heat transfer from a cell to a cooling plate, for example.
Physically, gap fillers are generally more viscous and compliant than TIMs, and they come in a variety of forms, including foams, pads, gels and pastes, to suit different applications. They also tend to be applied in thicker layers, ranging from a few millimetres to several centimetres. The most common materials are polymers such as silicones, polyurethanes, epoxies and acrylics.
Silicones provide excellent thermal stability, flexibility and good thermal conductivity, along with electrical insulation and vibration damping, although industry is turning to alternatives to silicones to avoid potential contamination issues in manufacturing and in service. Polyurethanes have good mechanical flexibility and adhesion, combined with moderate thermal conductivity. Epoxies are used where their high mechanical strength and thermal stability are required. Lastly, acrylics provide good adhesion and moderate thermal conductivity.
TIMs are usually less viscous and more rigid than gap fillers, designed for application in thin, consistent layers. They are commonly supplied as pastes, greases, phase-change materials or pads, typically forming layers of less than a millimetre thick to minimise thermal resistance.

Base materials for TIMs overlap to an extent with those for gap fillers, but there are differences. Silicones are also important as TIMs thanks to their excellent thermal stability and flexibility, along with good thermal conductivity and their ability to conform to microscopic surface irregularities. Polyimides are typically used in high-temperature applications, where their high thermal stability and good thermal conductivity are needed. Graphite and other forms of carbon provide very high thermal conductivity, and are often used as part of a composite TIM.
Phase-change materials (PCMs) are also making their way into TIMs, changing between solid and liquid at specific temperatures, absorbing energy and improving thermal contact, for example. Base chemicals for PCMs include paraffin waxes, polyethylene glycol, fatty acids and esters, polyurethanes, eutectic mixtures and inorganic salt hydrates.
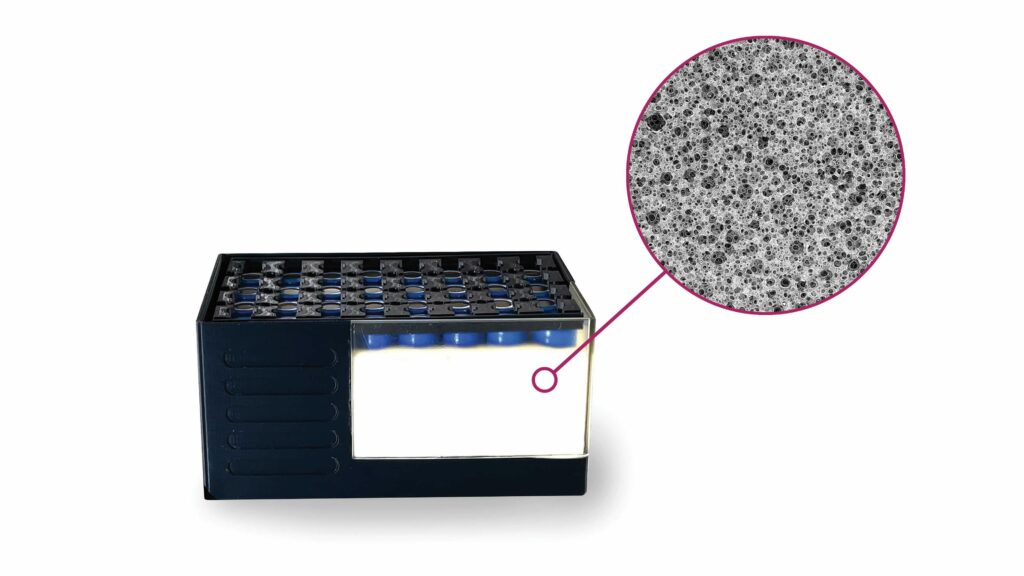
Changing demands
While the need for greater thermal conductivity has been a notable trend, three of the companies we asked reported growing demand for materials with reduced thermal conductivity. One notes that this is because cheaper filler materials can be used and processability is generally better. Battery developers also want significantly improved mechanical properties, such as strength and stiffness, for cell-to-pack applications, as well as enhanced safety.
Specifically, developers are looking for ‘medium’ thermal conductivity values of 2-4 W/mK, with little demand for higher values, an expert says.
Another says that where customers typically wanted 2 W/mK materials, they now see more demand for values in the 1-2 W/mK range. “This is also driven by next-gen battery designs with the cell-to-pack approach, where one interface for the thermal transfer – the module boundary – simply disappears,” he says.
Cell-to-pack materials such as TCA require higher mechanical integrity because they are part of the vehicle’s overall structural design and need to absorb impact energy in a crash.
“Higher flexibility and elasticity, greater bonding strength, moderate thermal conductivity at low cost, and ultra-fast processing speed for low takt times are the generic needs,” this expert adds.
To reduce weight and increase cost-effectiveness, developers are attaching increasing importance to low-density materials. This is part of a trend where automotive manufacturers are prioritising materials with greater functionality, specifying density and dispensability, as well as thermal performance.
Lower density translates into lower weight and higher pack-specific energy, a third expert notes. “Robust dispensability translates into high flow rates for increased part throughput and into less abrasiveness to help minimise maintenance costs and downtime for the meter-mix-dispense equipment.”
Battery makers increasingly want materials to be reworkable, he adds, because they need to correct manufacturing faults to maximise yield and aid in dismantling.
This expert also reports a significant uptick in customers requesting TIMs derived from sustainable raw materials.
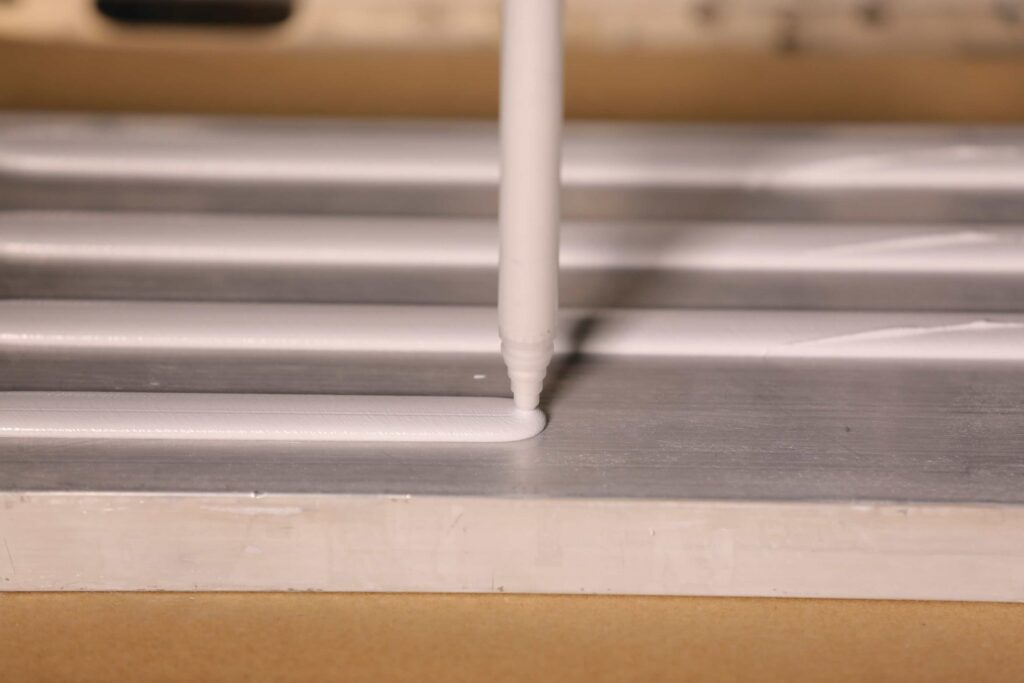
(Image courtesy of Parker Lord)
Additional properties
As well as their key thermal properties, these materials must have several more if they are to yield practical solutions, and many TIM requirements can only be met with tailor-made formulations to achieve the best balance between mutually exclusive properties.
Gap-filler materials must be soft for optimal adaption to surfaces to reduce thermal resistance at interfaces. In addition to thermal conductivity and density, processability and compressibility are important attributes. The thickness of the bond line is also significant in that the thinner a gap filler can be compressed, the lower its thermal resistance.
Achieving high reliability and safety over the life of an EV requires battery materials that continue to manage heat and mechanical loads despite prolonged exposure to high humidity, extreme temperatures and high vibration, for example.
To overcome these challenges, TIMs must exhibit strong bonding and exceptional bulk mechanical properties such as strength, toughness and high elongation before failure. They must also resist chemical breakdown.
Long-term resistance to heat is also vital because higher temperatures accelerate many material ageing processes, such as embrittlement, discoloration and degradation. “The relative temperature index (RTI) is the key factor here,” an expert notes. “The RTI indicates the highest temperature at which a material can perform its intended function for an extended period without significant deterioration.”
Among the other characteristics to be taken into account are creep resistance, which refers to the material’s ability to resist deformation over time under mechanical stress and high temperature, and flame retardance to internationally recognised standards.
In some cases, the TIMs must be electrically insulating to prevent electrical arcs due to the presence of high voltage close to metal components such as aluminium cooling plates.
In electrically insulating TIMs, volume resistivity is an important measure. This refers to how much electrical resistance the material presents per unit volume and is expressed in ohm-centimeters (Ω·cm). Another consideration is how well it prevents the formation on its surface of unwanted conductive paths that could cause short circuits. This property is rated against a Comparative Tracking Index (CTI).
Outgassing is another phenomenon that may have to be minimised; for example, to prevent deposits on other surfaces such as electrical contacts.
Low assembly stress is critical to avoid damaging components during manufacture. Developers aim for materials that impose minimum compression forces during assembly. Lastly, they must be easily dispensed with an appropriate cure profile, experts say.
Given the variety of requirements, their rapid evolution and conflicts between them, material developers need a strategy and they typically emphasise the importance of collaboration.
“We work with our customers to understand their application requirements,” notes one of our experts. “We discuss the benefits and challenges that could arise from different scenarios, then prioritise the agreed properties and test procedures. Our scientists and engineers approach these challenges using first principles and experience. We have a wide range of commercial products, including polyurethanes, silicones, acrylics and epoxies, which gives a good base for customising a solution for the application,” he explains.
Combining different raw materials and additives based on proprietary know-how, as well as extensive mechanical and processing tests, is essential to identify the sweet spots and potential trade-offs to achieve the best match with material requirements, another expert emphasises.
Another expert says their company’s engineering team evaluates particle sizes and their distribution for an ideal property range. “We then screen and evaluate our portfolio of fillers. In case we need to adapt our existing product range, we work closely with raw material suppliers and research institutes in material screening to identify materials with desirable properties.”
One company has initiated what it regards as a game-changing way of developing, validating and testing new TIMs.
“Before we even use raw materials and start formulating – based on know-how and a lot of data available from the historical work – we use the new approach to run intense design work and thermal simulations on AI- and algorithm-supported digital tools,” the expert says.
“This helps our product development teams to look after all the desired properties, bundle them into the design tooling and figure the best fit formulation of chemistry, filler packages and additives to get to the material we need.”
He emphasises that this approach saves significant amounts of energy, and other resources such as time and raw materials.
“Once we have unravelled all the options and figured out the best fit formulas, we start mixing materials and testing all key parameters in our new battery engineering centre (BEC). This high-voltage facility features automated labs for measuring mechanical, thermal and dielectric characteristics, as well as initial-series scale dispensing,” he says.
The BEC enables the company’s engineers to build the new materials into real batteries to see how they perform in critical situations, fast-charging/discharging, and to gauge the impact of environmental stressors such as temperature cycles.
“This helps us to validate what we simulated, but also recalibrate our tools in a much more efficient way,” the expert says.
Some combinations of desirable properties are particularly difficult to realise. Balancing mechanical and thermal requirements at a low cost is by far the most challenging task overall, an expert says, particularly when the material platform has to be very easy to process, minimally abrasive and stable over the long term. The raw materials and additives used have a major impact.
Achieving high thermal conductivity and low density together is a challenge, because as you increase the thermal conductivity by increasing filler loading you are also increasing the density of the material, according to another expert.
“Developing a material that will survive durability testing, but also be easy to remove for rework or recycling without damaging components is another tough challenge the team has been able to solve with recent product launches,” he says.
High thermal conductivities can only be achieved by using a high proportion of filler materials, another concurs, adding that these fillers have a high density and therefore increase the total weight of a gap filler.
“For the best thermal and electrical properties, only raw materials with high quality and purity can be used, and this can also lead to higher raw material costs,” he says.
Good mechanical properties and excellent processability while using a commercially attractive filler package is among the toughest combinations to realise, according to another expert.
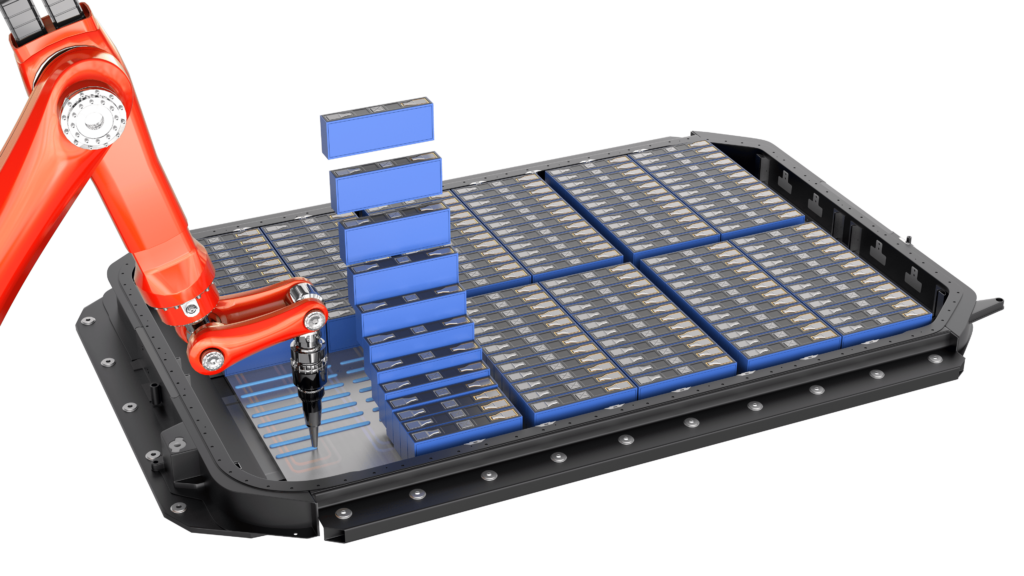
(Image courtesy of Henkel)
Phase-change materials
Materials that can be used to regulate the temperature of components in contact with them by changing between solid and liquid, or liquid and gaseous phases, when they absorb/release heat are known as phase-change materials (PCMs). These are valuable in many applications within battery packs, and both power and processing electronics.
Thin bond-line PCMs up to 0.15 mm in thickness are typically used in applications with tight mechanical tolerances and relatively small surfaces, such as CPU and power component cooling. PCMs are also used in ADAS components such as graphics processing units (GPUs) and the main CPU, says one expert, because of their excellent wetting effects and the thin bond line they can achieve.
These are among the best-performing TIMs with the lowest thermal resistance and are also suited to fully automated processing, either by printing in liquid PCM form or using a roll-based, pick-and-place process, he adds.
He recommends that manufacturers using PCMs should consider a constant pressure assembly process because the materials start to soften or melt at temperatures between 40 C and 60 C to wet the mating surfaces for low interfacial resistance. This effect requires a spring-loaded assembly to follow it to maintain the specified bond-line thickness.
Industry is continually working on new and improved materials and processes. With the cell-to-pack technology, for example, requirements have changed significantly due to the loss of structural support to the battery, compared with the cell-to-module technology.
This has led one company we consulted to develop polyurethane TIMs and potting systems. These cover a broad range of improved mechanical properties to meet the structural requirements of cell-to-pack designs, as well as cost reduction compared with materials currently regarded as standard in industry. These new TIMs do not contain monomers, and both TIMs and new potting materials are silicon-free, the company’s expert adds.
The need for high dispensing rates has led another company to develop completely new silicone-free gap fillers over the last year or so. These can be dispensed at rates of up to 100 cm3 per second and offer low assembly stresses in a range of thermal conductivities from 1-3.4 W/mK for use in batteries.
The company has also developed new TCAs over this period, which are designed to combine high thermal conductivity, elasticity and bonding strength with ease of dispensing. Those intended for use in cell-to-pack batteries are formulated with thermal conductivities in the 1-3.4 W/mK range, while injectable TCAs for modules are 3 W/mK materials.
The company’s next-generation gap fillers have been engineered with values ranging from 2-6.5 W/mK with thin bond lines. They also minimise silicone outgassing at longer working times by keeping cure times short, and offer easy and fast processing. Their expert emphasises these materials comply with EU limits on D4-D6 siloxane emissions that will apply from 2025.
The company’s new, single-component (1K) post-cure gels have a thermal conductivity of 4.5 W/mK for use in ADAS sensors such as cameras, radar and Lidar units. These have had to pass severe fogging and outgassing tests to ensure they do not contaminate optical systems.
EV power electronics such as inverters are potential major sources of electromagnetic interference (EMI), so the company has developed EMI absorbing pads that are also electrically isolating and provide thermal conductivity at 1 W/mK and 4 W/mK.
In a similar development, they now also offer silicone-free gap pads for very high-performance applications in ratings of 18-40 W/mK.
Lastly, there is a new potting family for power-conversion applications. These materials are designed to fill the smallest of cavities and gaps quickly, provide a buffer against mechanical stresses and operate under a wide variety of environmental conditions, including temperatures up to 175 C.
Another developer recently launched a family of high-performance silicone gap fillers, which are low-density, soft and paste-like in consistency. With thermal conductivities of more than 1.5 W/mK and excellent electrical properties, they can withstand high operating temperatures over the long term. They also work in conditions ranging from -60 C to 200 C and cure at room temperature, and curing can be accelerated with additional heat.
The company’s expert says they also exhibit thixotropic behaviour, meaning they become less viscous when subjected to shear stress, such as stirring or shaking, and gradually return to their original viscosity when this stress is removed. This is very useful in gap fillers because it helps with processability; for example, enabling high dispensing speeds.
These materials are also characterised by low Shore hardness, which determines how resistant they are to indentation or how hard they feel, and they are low in substances of very high concern (SVHC).
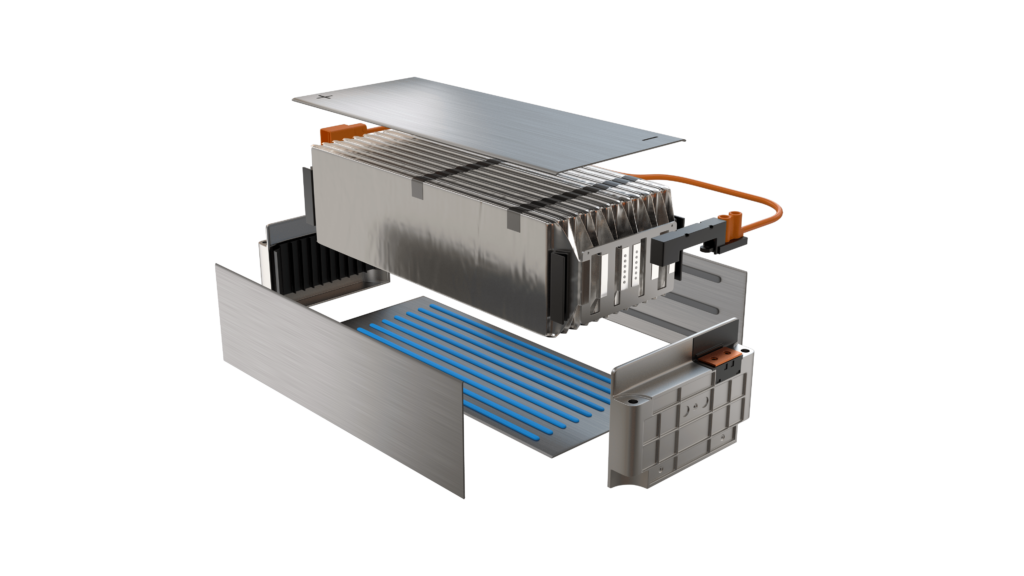
(Image courtesy of Henkel)
Advanced dispensing
Dispensing these materials involves several challenges that manufacturers need to address in both their content and the equipment they choose to apply them to. Gap fillers and TIMs can vary in viscosity, and materials that are too thick may be difficult to dispense evenly, while any that are too thin may not stay in place. Thixotropic behaviour, while useful, has to be allowed for in dispensing. Further, the conductive fillers in many TIMs are abrasive and cause wear in the equipment for which it has to compensate.
A leading dispensing specialist emphasises the importance of automatic calibration in its latest intelligent, software-driven dispensing system. The calibration function captures the pump’s reference curve, which indicates the relationship between key operational parameters – such as flow rate, pressure, and axis speed – and makes adjustments to compensate for such factors as wear in order to maintain the dispensing accuracy and to minimise downtime during pump changes, leading to high machine availability.
In static dispensing applications for both 1K and 2K gap fillers, the system automatically detects and corrects for turnback. This ensures dispensing starts consistently and prevents drops at the end of the cycle, and relieves the human operator of the need to determine turnback performance and adjust for it during set-up.
The system’s part-weighing simulation function accurately predicts the dispensing process, saving production time, avoiding error and eliminating the need for test runs, says the company.
Its selective blind shot function is designed to reduce material consumption by monitoring the pot life of the material in the mixing tube and flushing out only the reactive segments, with the idea being to reduce both operating costs and environmental impact.
An envelope curve function, which typically graphs flow rate against pressure, is shown on the machine’s display screen to monitor working pressure throughout the application process.
Dispensing quality is enhanced by automated wiping of the nozzle on the rim of a dedicated cup between dispensing cycles. The cup indexes around to avoid contamination by residue from the previous wiping cycle.
An optional function automatically adjusts and optimises the dispensing speed to the geometry of the product, ensuring uniform material application and quality. This function is available for 1K, 2K static and 2K dynamic mixing and reduces cycle time.
Operators can quickly create and adjust dispensing parameters and processing programs with an optional editing extension that also accommodates importing DXF (CAD) files.
This dispensing specialist has also developed a new system to inject gap fillers into pouch cells, which is a challenging task.
Pouch-cell dimensional tolerances are unpredictable and can be as large as 50%, meaning that the volume to be filled can vary. A new algorithm monitors the amount dispensed and detects the optimum degree of filling, eliminating the need for sensors at vent holes and the need to clean the pack exterior of excess material.
The system automatically detects the proper degree of filling, ensuring the new silicone based gap filler is free of bubbles. It also allows all components to be fully assembled before the gap filler is injected, which happens at low pressure to protect the pressure-sensitive pouch cells.
This material has optimised rheology and requires neither degassing nor rehomogenising before use, while fillers and particle size distribution are optimised to minimise abrasiveness. It also offers good intrinsic wetting properties so that it fills small gaps with low injection pressure. It also has a long pot life and can be removed without leaving residue, easing the replacement of modules.
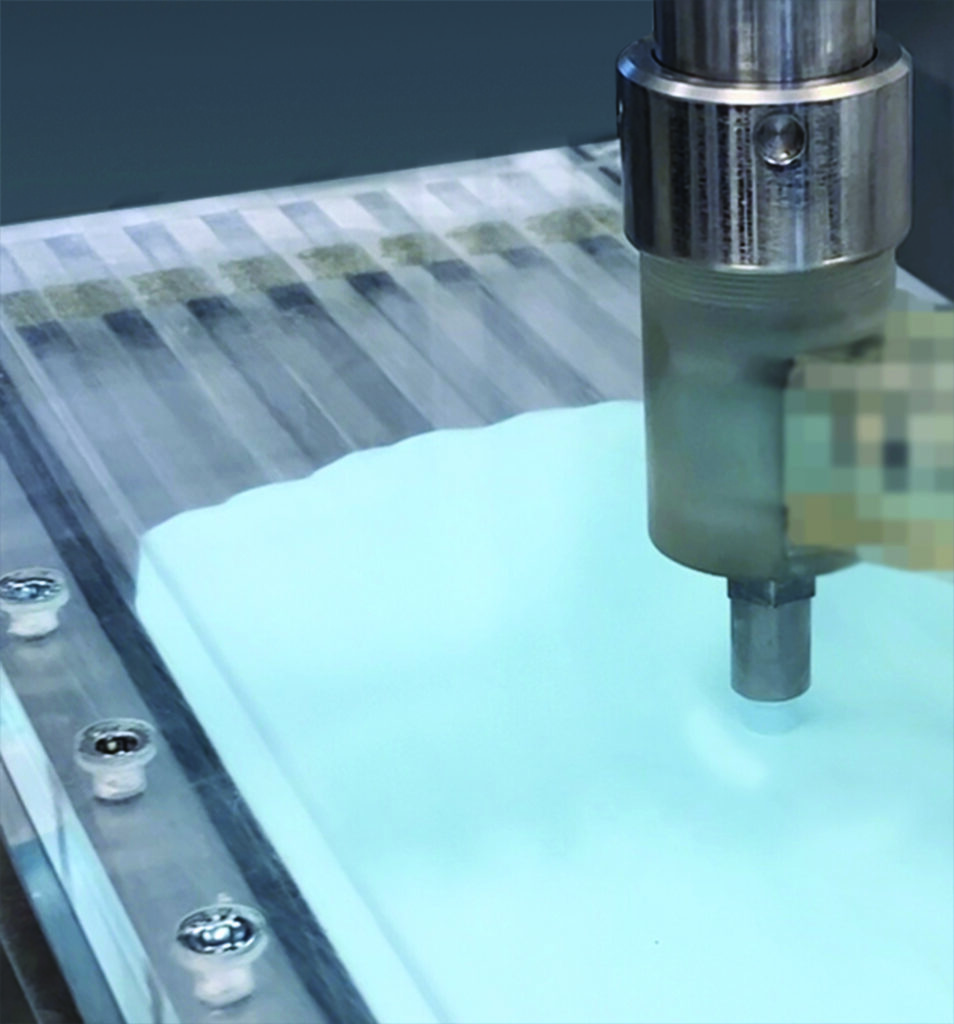
(Image courtesy of bdtronic)
Multi-nozzle shots
Batteries constructed from cylindrical cells present the problem of securing large numbers of cells into honeycomb structures in short cycle times using TIMs such as TCAs. A second dispensing machinery specialist solves this with multi-nozzle dispensing heads mounted on robotic arms, fed by multi-piston pumps to inject precisely metered quantities of adhesive into multiple cells at once.
Electronic components are packed with increasingly high density, particularly in ECUs and ADAS computers, and they have to be protected with TIMs, including gap fillers and potting.
Today’s gap fillers feature optimised filler packages to reduce settling, allowing for thinner layers with the lowest possible thermal resistance and easier rapid dispensing, the company says. These are mainly two-component materials that are highly viscous and abrasive, requiring optimised pumps, adaptable mixing technology and abrasion-resistant dispensing systems. The latest developments use piston technology in combination with needle-closure technology, resulting in improved pressure stability and higher dispensing rates.
The company has also developed a family of feeding systems that connect the pails containing the 1K or 2K gap-filler materials to the dispensing machines, working at several pressure ranges up to a maximum of 150 bar. Designed for automatic, bubble-free docking and easy loading, they feature powerful pumps that are able to move material over long distances at high speeds.
They are available either with or without a vacuum chamber, in the first case optimised for minimising waste, in the second for speed. Both variants create a vacuum between the surface of the material and a follower plate, but the one with the vacuum chamber puts the whole material container under vacuum before the docking process starts, retaining material that would otherwise be lost. This is particularly important with expensive TIMs.
Also offered are cartridge feed systems for efficient production of small runs of parts.
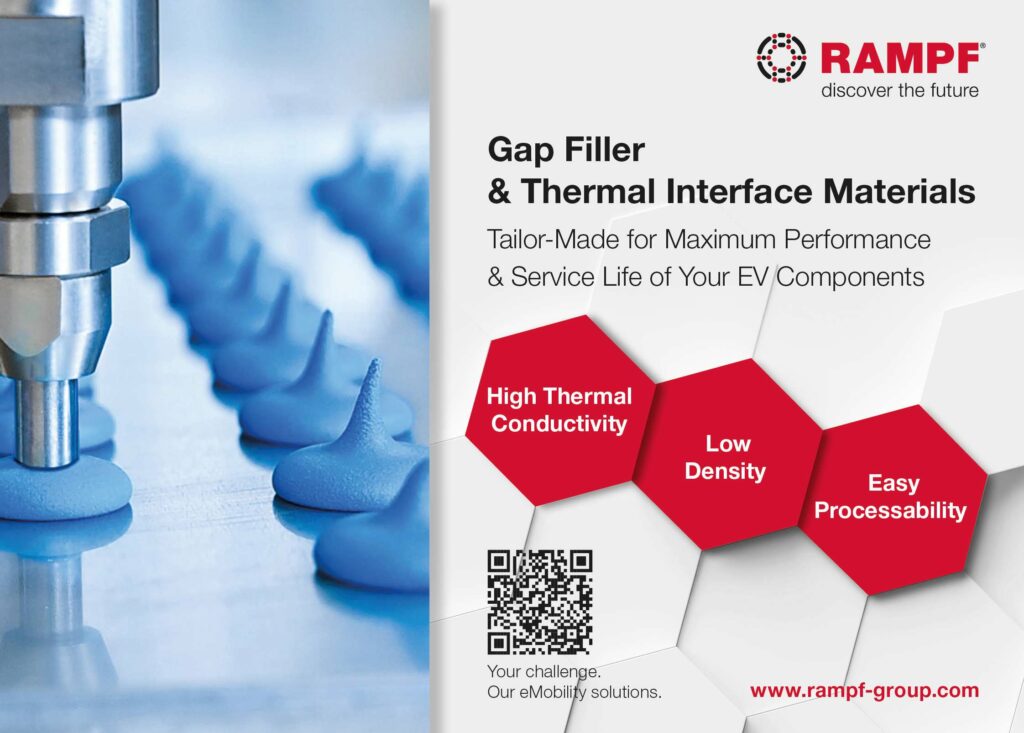
Time to de-bond
Prominent stories of high scrap rates during manufacture, minor battery damage effectively writing off electric cars because insurers won’t touch them, battery replacement costs exceeding the value of relatively young vehicles and making batteries easier and less expensive to dismantle for rework, repair, repurposing and recycling is now a high priority for the industry. For all kinds of TIMs, including gap fillers and TCAs, as well as other adhesives and sealants, controlled de-bonding is therefore an important new development target.
One material developer reports that it is screening various de-bonding solutions based on electrical, mechanical, chemical and thermal techniques. “The most promising as of today are an electric de-bonding layer (EDL) and a thermally activated mechanism (TAM). Both can be integrated into structural and thermally conductive adhesives,” the company’s expert says.
“These solutions are proven concepts that have been validated at our labs, tested and incorporated into next-generation battery designs from major electric car makers.”
The company is close to launching its EDL solution (see the Battery Show Europe report in this issue).
Another says that it has developed materials that balance surviving durability tests while being able to be removed for rework or repair without damaging components, which their expert says becomes more challenging in applications that need higher bond strengths.
“The most promising materials are those that go through an abrupt mechanical change with a precisely tailored temperature range that does not damage the battery or de-bond during the normal operation of the battery,” their expert reports.
He adds that the company has several emerging “switchable” technologies that allow de-bonding through the application of a stimulus followed by mechanical removal.
“We also offer latent, reworkable materials, which means the product can be applied and if a defect is noticed it can be removed easily to be reworked for long periods of time before full cure occurs.
“We have also developed materials that balance surviving durability tests while being able to be removed for rework or repair without damaging components.”
In some applications, the use of soft, two-component silicone gap fillers facilitate dismantling, according to another specialist company, as these materials can be manually de-bonded without causing damage.
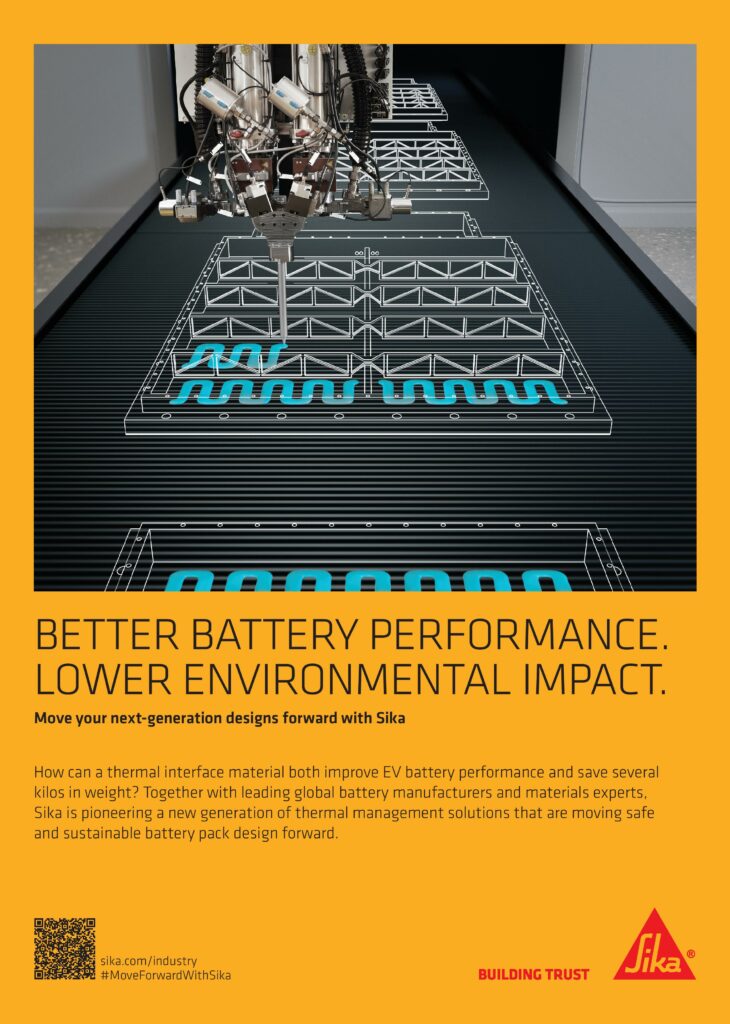
Circular challenges
While de-bondable gap fillers and TIMs make battery modules and cells easier to rework, re-use and recycle, making the materials themselves recyclable remains difficult, but it is a task the industry is pursuing. Many such materials now consist of conductive fillers in a resin matrix with additives, the recycling of which to the point that they can be re-used takes too much energy for it to be worthwhile. While it works out how to overcome this, industry is making a variety of efforts to build sustainability into its material development cycles.
These include steps such as screening raw materials and formulations for low environmental impact and re-engineering production processes. The latter effort involves, for example, using renewable energy, avoiding solvents and adapting logistics to re-use material drums, using lighter packaging and producing TIMs closer to where they will be incorporated into EV systems.
Engineering in recyclability also takes close collaboration with customers willing to design fully sustainable battery packs. For example, designs must better accommodate the retrieval of gap filler materials, experts say.
One expert emphasises that the concept does not simply rely on specific materials, so it is important to offer total solutions to designers of the next generation of EV battery platforms.
Among the more promising approaches are those based on reversible adhesive chemistries capable of depolymerising back to the starting monomers, another explains.
“The big challenge here is tailoring the stimulus for depolymerising so that it will not break down during normal operation but also not lead to thermal runaway or damage the battery,” the company’s expert says.
Research into the use of recycled and bio-based raw materials in the manufacture of resin systems is a complementary approach.
Finally, another major materials developer takes the “biomass balance” approach in which it offers products with “attributed” renewable content. In practice, this means that renewable resources such as bio-methane and bio-naptha derived from organic waste or vegetable oils are mixed with fossil resources and fed in at the beginning of the multistage production process. The company emphasises that the resulting products are identical to standard “fossil” products in terms of formulation and quality.
TIMs represent a very active area of r&d, characterised by moving targets and many problems still to be solved.
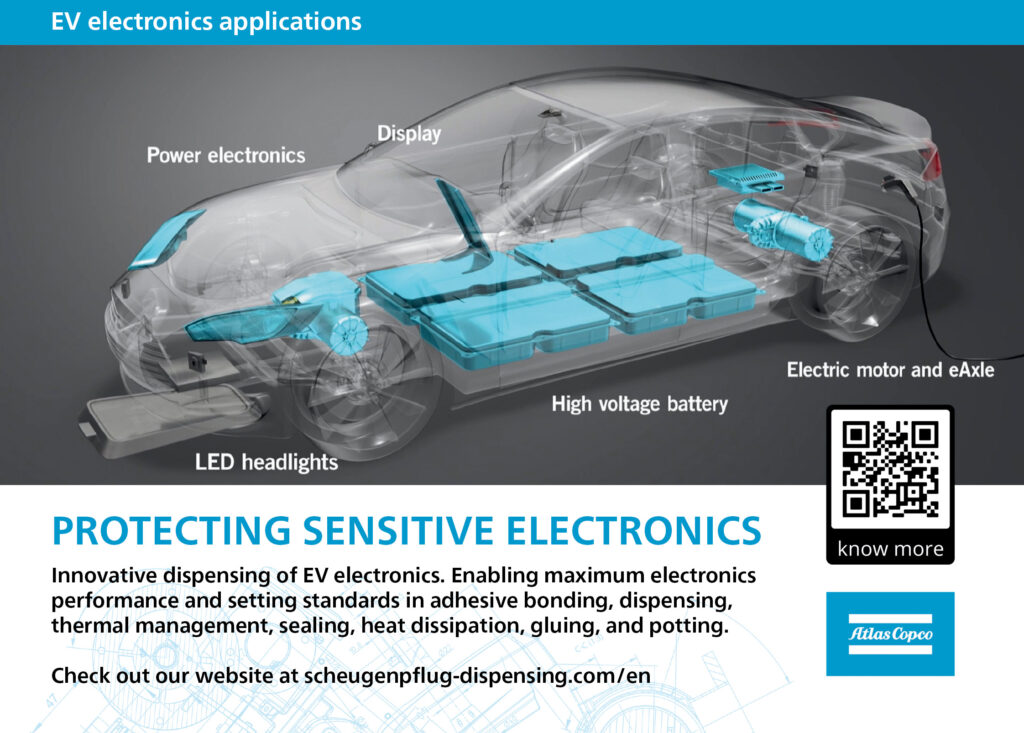
Acknowledgements
The author would like to thank Holger Schuh, senior manager, thermal technologies and Dr. Keon Lee, senior manager battery product development at Henkel; Thomas Stührenberg, business development manager, e-mobility at BASF Polyurethanes; Regina Körner at bdtronic; Philipp Steinbach, product manager electro casting at RAMPF Advanced Polymers; Mekiyah Bailey, field application engineer at Parker Lord; Adam Cerek, business development battery & EV electronics at Scheugenpflug, and Johannes Blaser, business line manager (Scheugenpflug) at Atlas Copco IAS.
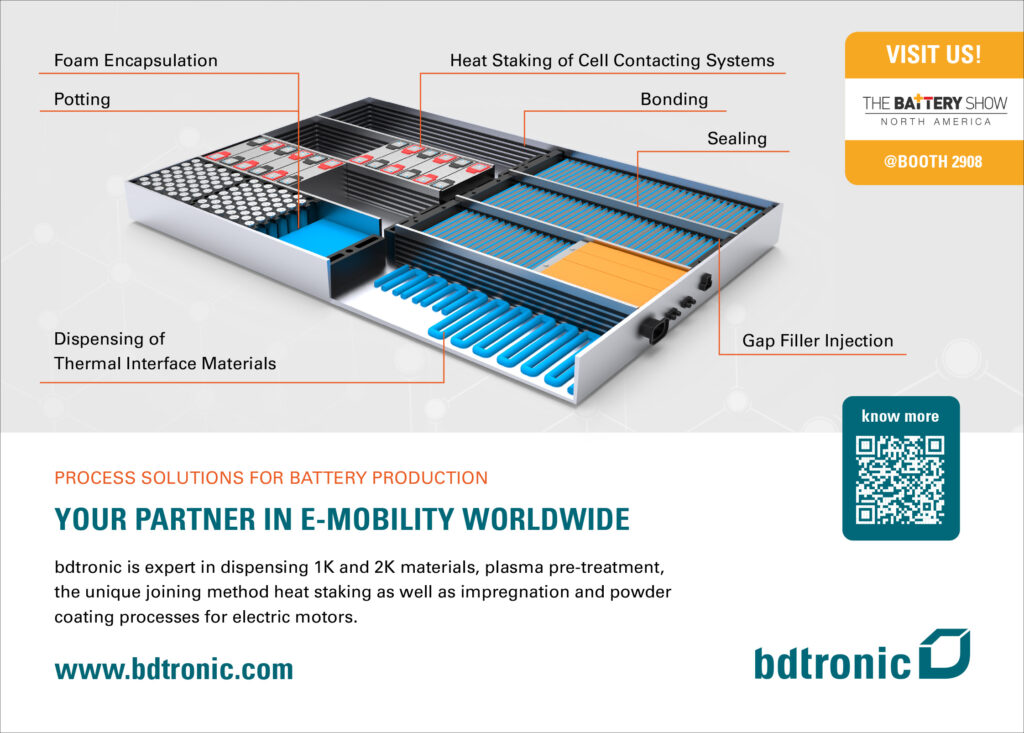
Some suppliers of gap fillers, other TIMs and dispensing equipment
BASF Polyurethanes GmbH
bdtronic
Bostick
Dow
Evonik
Fujipoly America Corporation
Graco
Henkel
Nolato
Parker Lord
Polytec PT
Rampf
Saint-Gobain Tape Solutions
Scheugenpflug
Sika
Wacker Chemie
+49 5443 12 0
+49 7934 1040
+33 149 007 502
+1 800 7776 7776
+49 201 177 01
+1 732 969 0100
+1 612 623 6000
+49 211 797 0
+46 708 12 99 95
+1 877 275 5673
+49 7202 706 3500
+49 7123 9342 0
+1 518 686 7301
+49 9445 9564 0
+41 58 436 6800
+49 89 6279 0
ONLINE PARTNERS
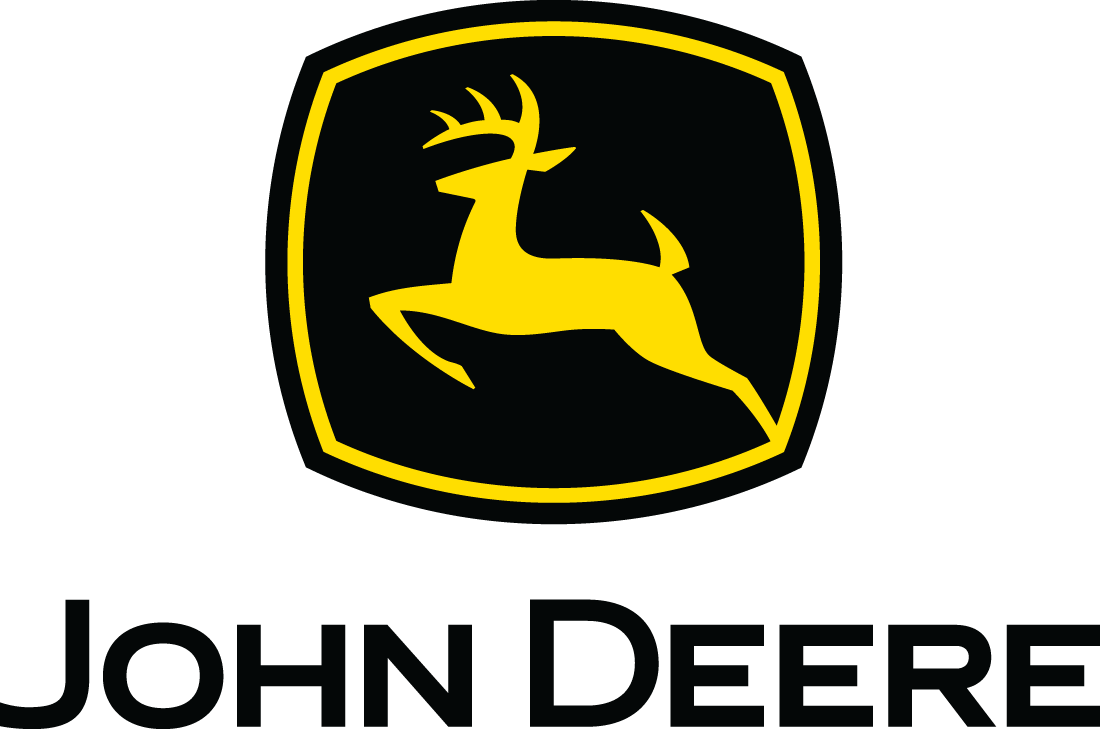
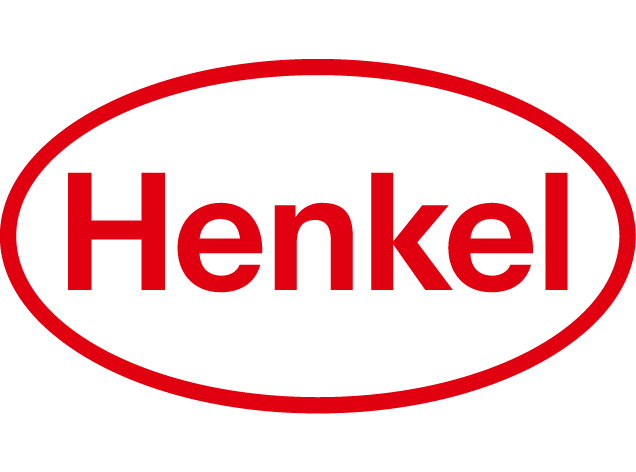
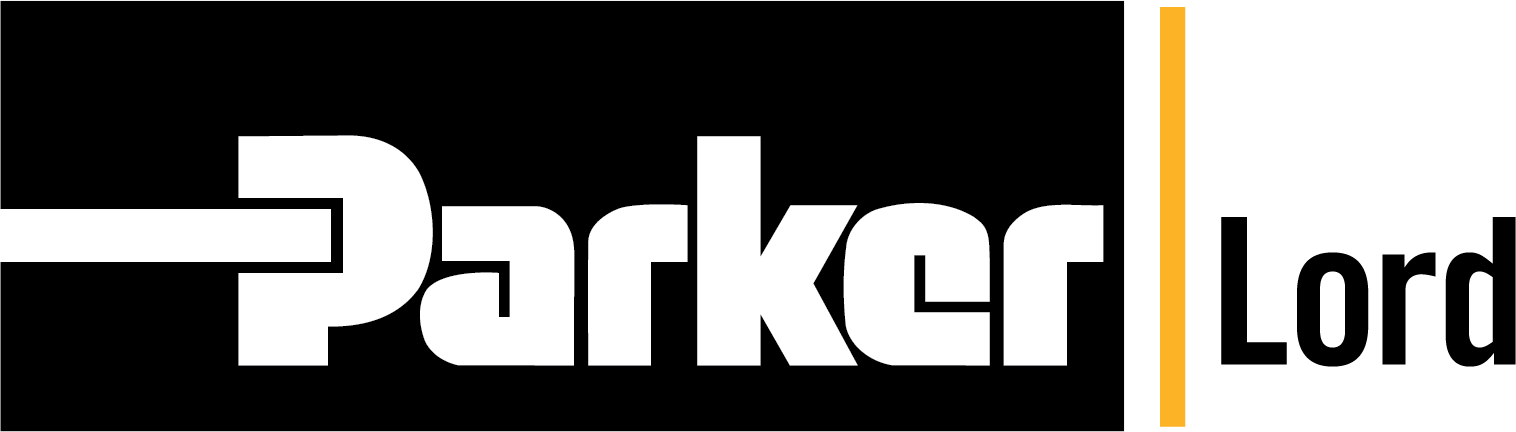
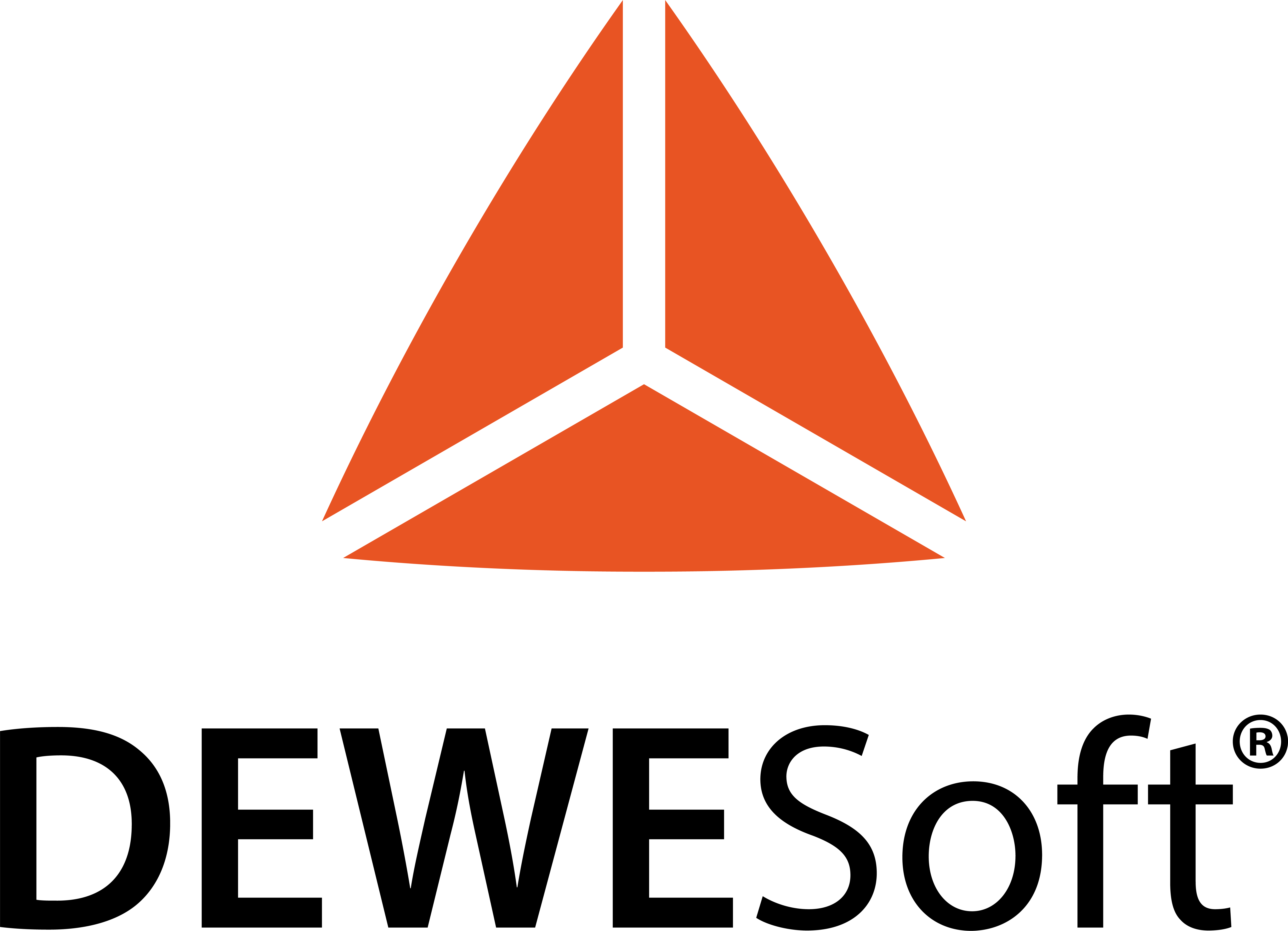
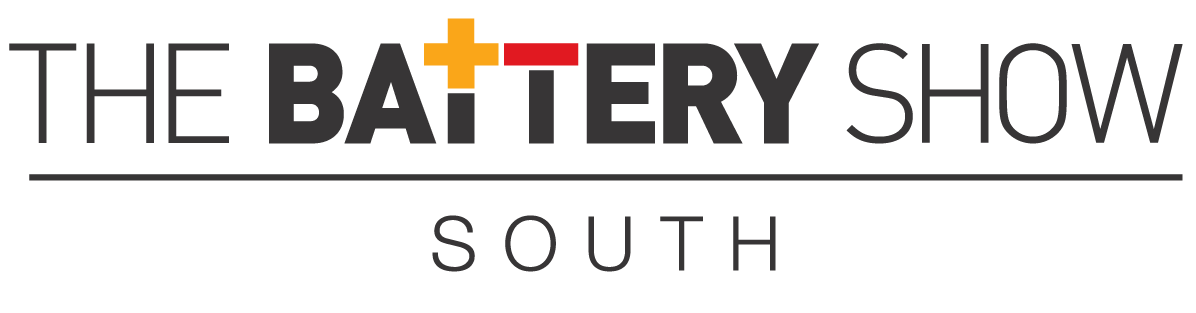
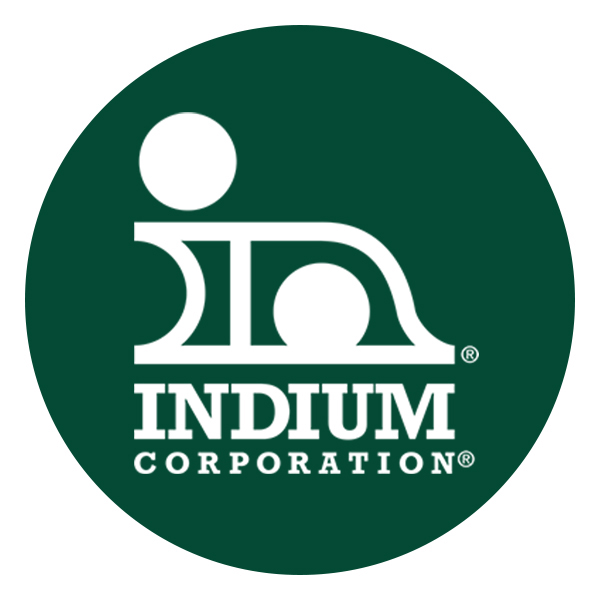

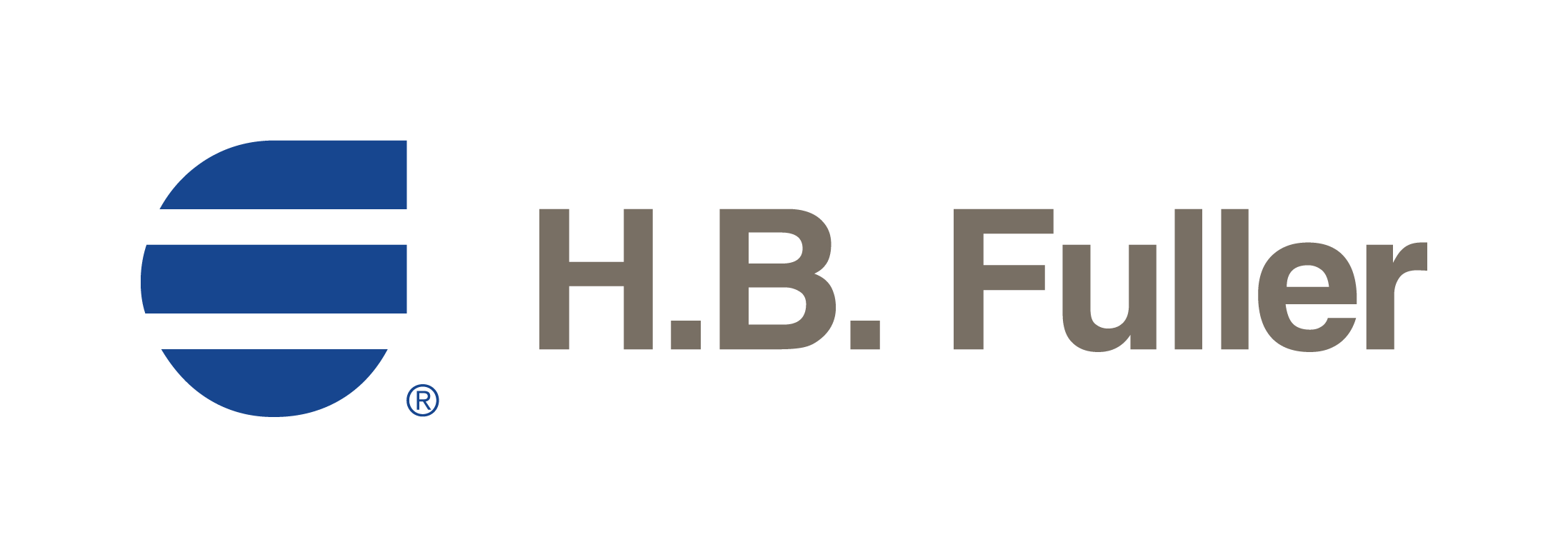
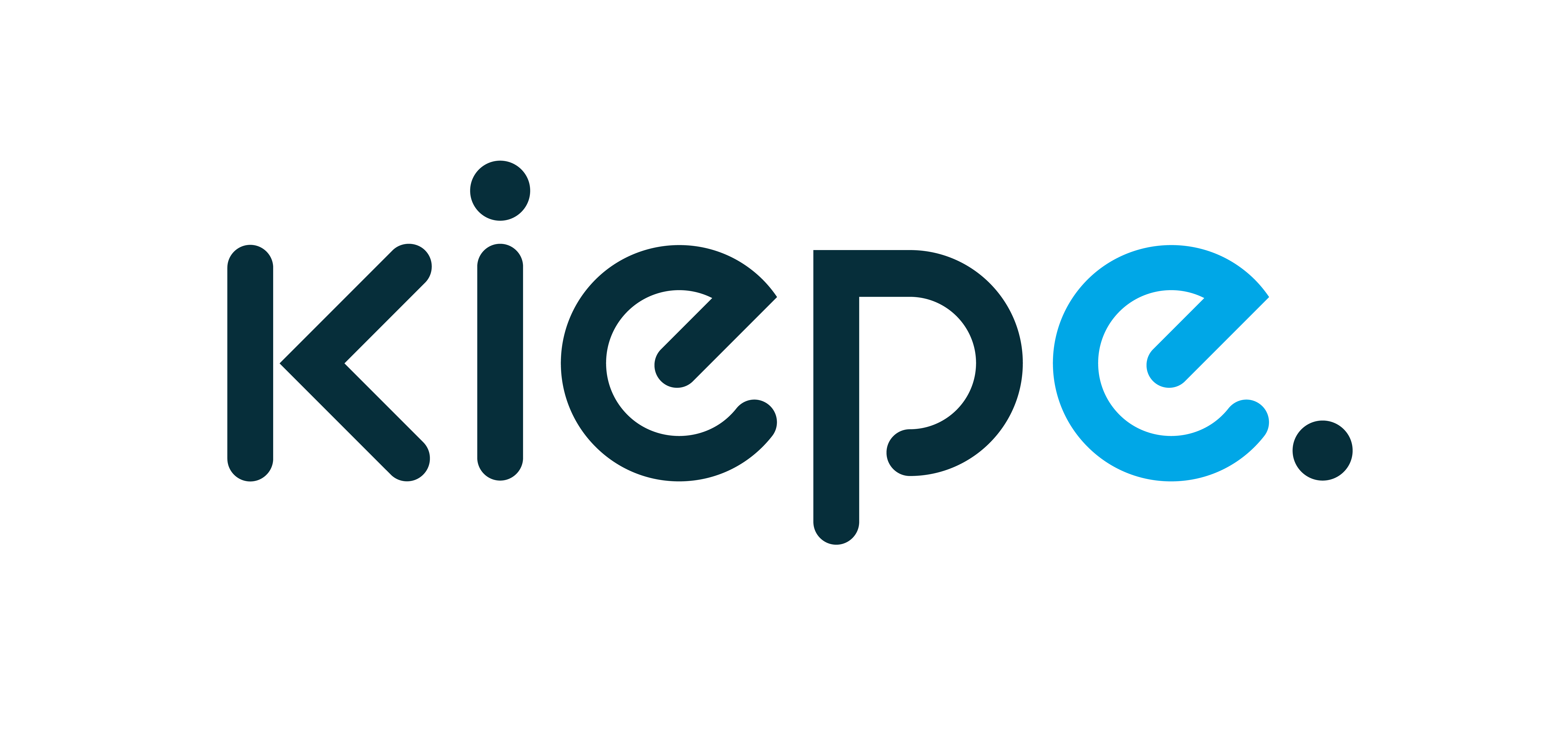
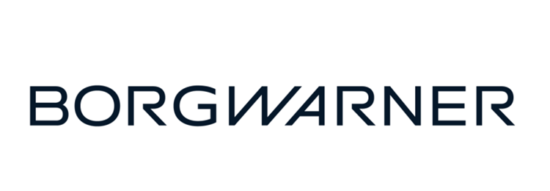