Liebherr electric excavator
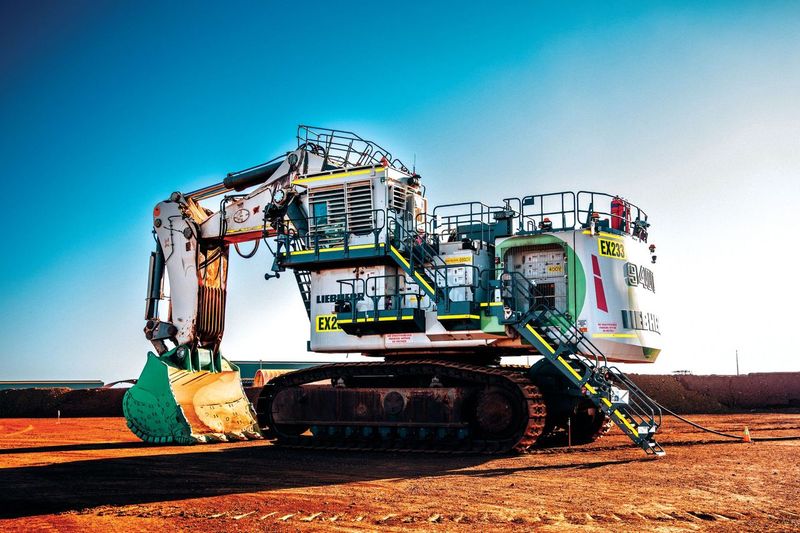
(Images courtesy of Liebherr)
Great excavations
Rory Jackson finds out how one company met the challenge of electrifying its mining excavators
Despite being known for manufacturing huge, diesel-powered vehicles and industrial equipment, the Liebherr Group has a lengthier history in electrified powertrains than many realise. The Swiss-German multinational first produced a stationary electric crane during the late 1980s, principally for loading and unloading boats at river harbours, or sorting items at scrapyards with grapplers or magnets.
These would either swivel on a fixed pedestal or run on a rail along the lengths of quaysides. As such machinery required little real mobility (in the sense of travelling any significant distance), they were easy to electrify.
Today, however, Liebherr Mining has tackled the far greater challenge posed by electrifying its mining excavators, which may be the largest and heaviest of the many vehicles and heavy equipment manufactured across the Liebherr Group’s various divisions.
Traditionally, these gargantuan, tracked machines – iconic for their enormous digger arms, capable of lifting hundreds of tonnes of earth – would be powered by diesel engines, given the high power, high torque, low speed and strong reliability of such ICEs for continuously driving the hydraulic apparatus that is key to uninterrupted mining and mine-development work.
Hence, Liebherr’s portfolio of such diesel- and hydraulics-powered diggers has included such globally operated machines as its 1086 hp (810 kW equivalent) R9200, its 1810 hp (1,350 kW) R9400, its 3620 hp (2,700 kW) R9600 and its 4023 hp (3000 kW) R9800.
“Liebherr Mining as an entity didn’t always exist within the Liebherr Group. Those diggers originated in our factory here in Colmar, France, where they are still produced today, but back then it was ‘Liebherr France’ making just the smaller ones to start with,” recounts Emmanuel Goetschy, Liebherr Mining’s lead for product management for the electric excavator range.
“As demand drove us to design and manufacture bigger excavators, predominantly for mining customers, we finally rebranded as Liebherr Mining here in Colmar in 2010.”
Specialisation in mining vehicles took off in 2005, and Goetschy notes that even then, nearly 20 years ago, many of its customers were actively working in electrified mines, where they were already operating electrified rope-shovel and dragline excavators. Hence, they had already started asking after large digger excavators that ran on electric (rather than diesel) powertrains.
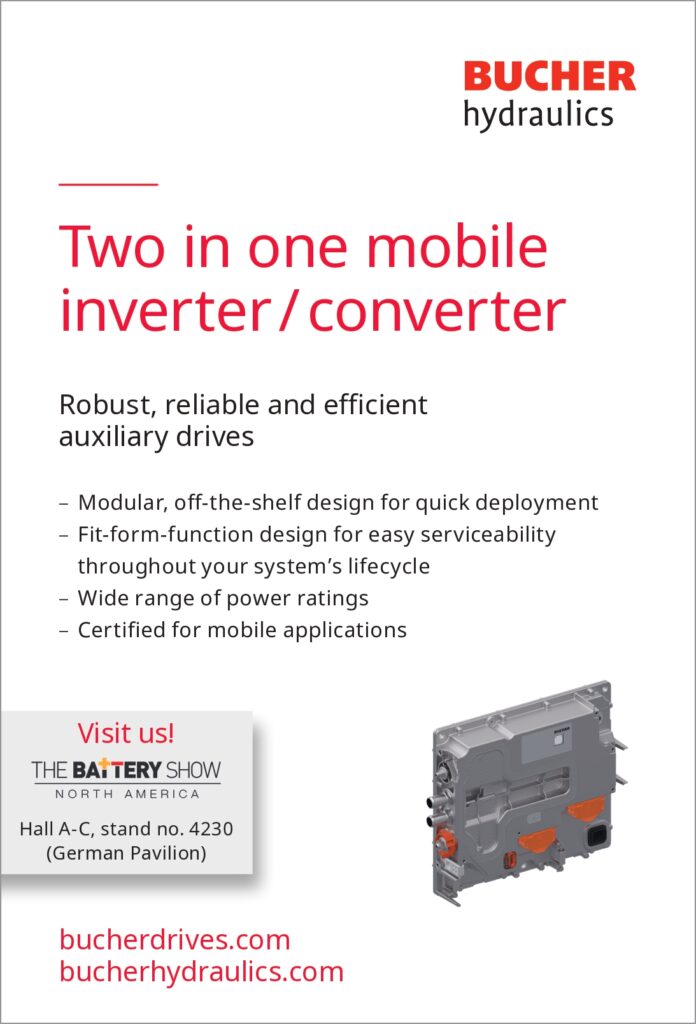
“In some markets, like Australia or the USA, mines are so remote that there is no grid power available to power electric machinery, and gensets and batteries aren’t high-power enough to drive their machinery, so they have to take fuel with them if they want enough power,” Goetschy explains. “But, in others, Eastern European countries particularly, they are quite good at having ready-built grid infrastructure ready to accept electrified mining machines.”
Adrien Lacoche, engineering specialist and expert for electrification at Liebherr Mining, says: “The main advantage of an electric excavator is that it’s much easier to maintain than a diesel one. The former has far fewer components that can break or age. It doesn’t have the oil-changing needs of an ICE and it never needs to be refuelled.
“Our biggest diesel excavator, the R9800, needs about 20 m3 of diesel every day. Its fuel tank is about 13 m3, and the lengthy time needed for refuelling is time in which it’s not digging.”
By contrast, Liebherr Mining’s new generation of electric excavators, having been engineered to run off high-voltage cables connected to local grid power sources, can run 24 hours per day without needing to refuel or recharge. This poses a huge potential source of cost savings for mining companies too, given that grid electricity is, generally speaking, cheaper than diesel.
These excavators – created through installations of conversion kits (dubbed Repower by the company) – corresponding to their diesel predecessors include the 9200E, 9400E, 9600E and 9800E, among others. All of the repowered excavators use largely common components and engineering approaches within Liebherr’s electrification strategy, but our principal focus in this feature is the architecture and components of the 9400E, both for being the first of the excavators electrified by Liebherr, and to avoid belabouring our technical investigation with excessive variations and particulars between excavator models.
The 9400E is 9250 mm tall, excluding the raised digger arm, and it has a track width of 5520 mm and an effective wheelbase (constituting the centreline of its tracks’ front and rear carrier rollers) of 6645 mm. Like the other excavators, it is composed largely of an upper carriage, a digger arm and an undercarriage, with the former mostly taken up by a cabin structure and the latter mainly composed of a track drive for traction. Its track drive’s maximum dimensions are 8800 x 6930 x 2385 mm, while the cabin measures approximately 9790 x 8350 x 5660 mm.
The excavator’s maximum travel speed is 2.7 kph, while a swing drive connects the upper and undercarriage, and facilitates the former to rotate atop the latter at up to 3.9 rpm. Its digger arm features a bucket with a 150° pivoting range, which can lift up to 38,000 kg of material while generating up to 1,545 kN of force (when the bucket is installed as a face shovel; a backhoe configuration is also available for when needed, although less force and lifting capacity is available).
Both the electric and diesel powertrains achieve up to 1350 kW, and hence use similar hydraulic components – simply driven by an electric motor shaft now, rather than a diesel engine shaft – although enormous engineering work has gone into optimising this excavator and its siblings, as Liebherr Mining was happy to explain for us.
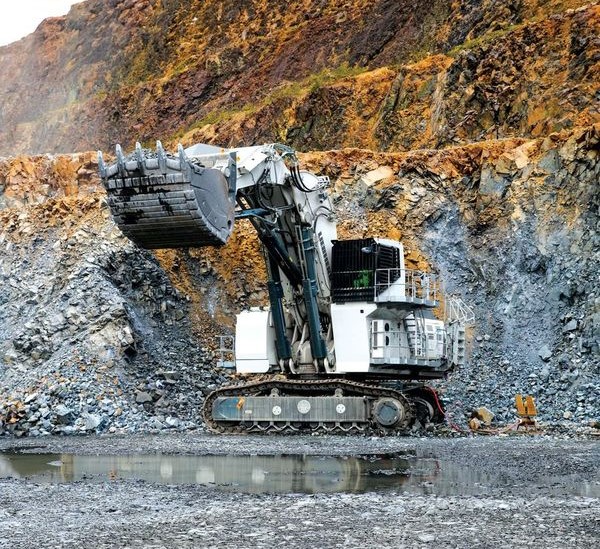
Development history
Liebherr’s strategy for designing the concept and architecture for the 9400E was simple: replace the diesel sections with electric sections, and keep as many parts as possible in order to minimise differences in maintenance and inventory requirements.
“That meant replacing the diesel engine with an electric motor, and the fuel tank with a high-voltage electrical cabinet – those are the two most important parts of the conversion kit,” Lacoche says.
“The original diesel excavator was designed using a modular approach, with engine and fuel-tank modules that slide into the excavator chassis on rails and are bolted into place. That made it very easy, from an integration perspective, to unbolt the diesel components, slide them out and install their electric replacements.”
Following development of the first version of the conversion kit, demonstrator kits were sent to customers, who found they worked well enough that there was no particular need for further iterations: all necessary functionalities and capabilities were provided for.
While only one kit has been sold in a commercial capacity so far, to an Australian customer interested in electrifying their mines, the reason is because Liebherr recommends staving off conversion of the diesel excavators until the time comes for a major overhaul (their TBOs run 15,000-20,000 hours). Given the size of the equipment to be removed and installed, and the labour and energy required to do so, it makes sense to wait until the diesel engine absolutely has to be removed.
“The subject of overhauls is interesting, because it contributes significantly to the maintenance benefits of electrifying mining diggers. We may theoretically never have to change the electric motor in the electric excavators,” Lacoche says.
“That’s just how reliable it is; it’s definitely good enough for 100,000 hours. That’s over 10 years of continuous operation, and just a quick greasing of the bearings every 4000-5000 hours, or 10 months, is the main maintenance work to do.”
Goetschy says: “Of course, we are capable of supplying far more than just one unit, and will do so as interest in electrification picks up speed among mine owners. Our production is constrained only by how fast third-party suppliers can send us parts.”
To that end, the excavator and its electric powertrain systems have been engineered to function in all ambient temperatures, moisture conditions and altitudes, with all electrical insulation across the digger models capable of operation over their lifetime from -40 C to 55 C.
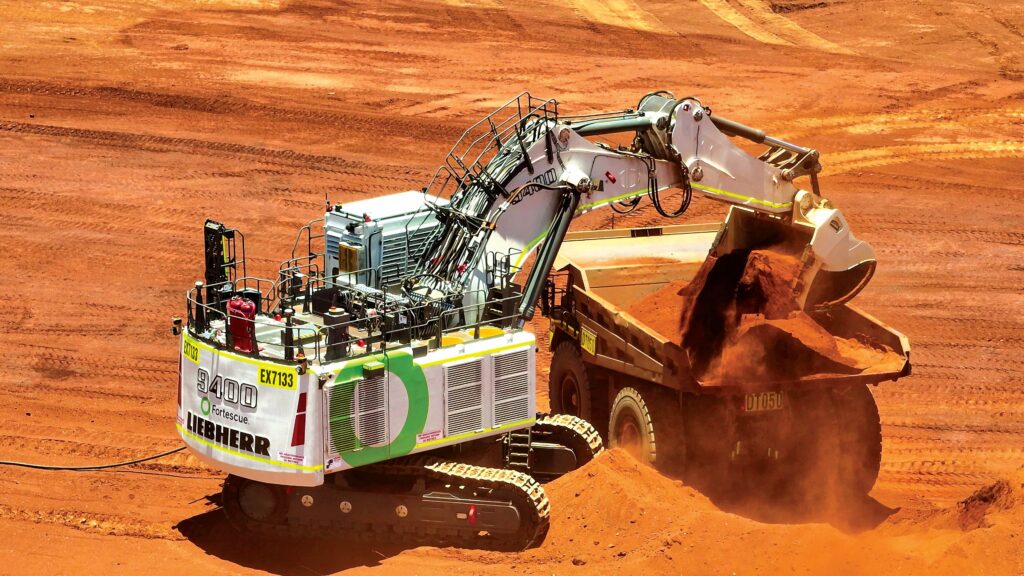
Kilovolt power
As hydraulics provide satisfactory force and efficiency for actuating the excavator arm, most systems downstream of the powertrain are the same in the 9400E as they are in the diesel-powered 9400. This includes the oil pumps, cylinders, filters and so on.
Upstream, the pumps connect to a transfer box that Liebherr refers to as a splitter box. This is essentially a gearbox with one input shaft connected to the aforementioned Power Pack’s electric motor. Hence, the splitter box drives multiple gears pertaining largely to the hydraulic pumps, of which there are six in the 9400E, and four variable-flow axial piston pumps that drive the excavator arm while the vehicle is stationary and otherwise drive the traction system in the undercarriage.
The traction system or ‘travel drive’ consists of two tracked side frames, each running on nine track wheels via two carrier wheels (the four pumps divided up to drive two axial piston motors per side frame).
“The pumps at the splitter box transfer oil to our main control valves supplied by Bosch Rexroth, which then distribute the oil to the correct motors and cylinders as requested through the electronic commands given by the operator’s joystick levers, hand levers and foot pedals,” says Goetschy.
Those manual interfaces correspond to either the digger arm, the swing ring separating the upper and undercarriage, or the traction. Goetschy notes that the hydraulic motors, cylinders, and swing and travel drives are developed by Liebherr.
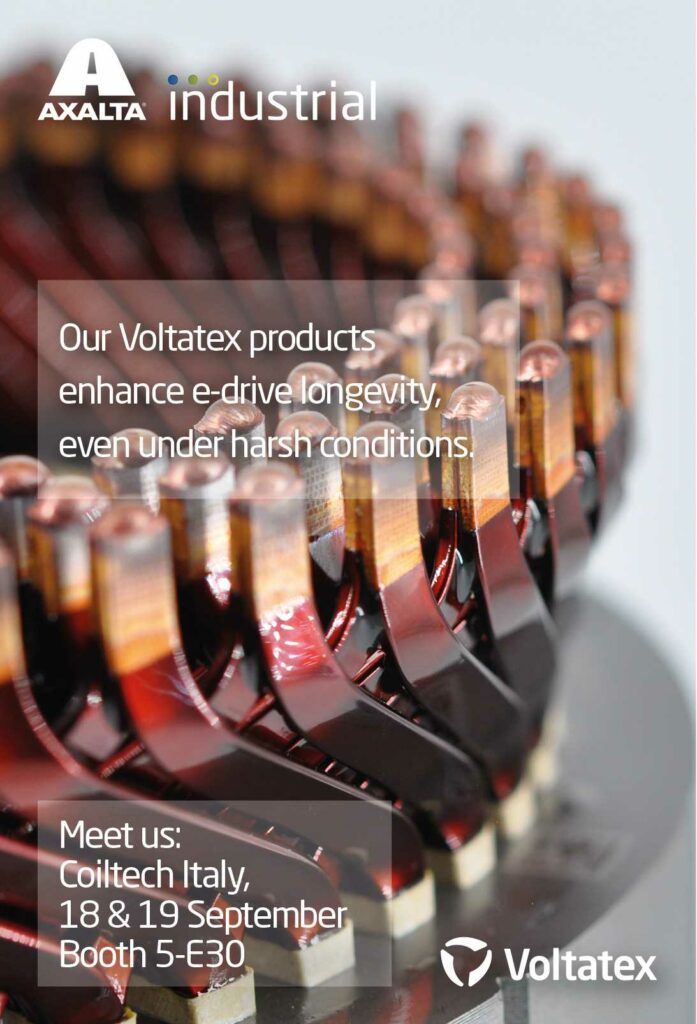
The prime mover behind all of this is an asynchronous, squirrel cage-type electric motor, especially designed for Liebherr by General Electric’s subsidiary in France (GE france) to withstand the high levels of shock and vibration that come when the EV imparts nearly 1000 kN of digging force into the ground.
While permanent magnet synchronous motors (PMSMs) are more common among the EVs we feature, “PMSMs are more suited to variable-speed applications, so we don’t really need one in our application, and they can be more complicated to maintain than asynchronous machines because you’re adding these rare earth, permanent magnets into the maintenance requirements”, Lacoche adds.
“Permanent magnets can be dangerous to handle and integrate, not to mention expensive and subject to supply chain shocks. For all these reasons, we’ve no interest in using permanent magnet AC machines in our mining excavators. An asynchronous motor, running continuously at nominal speed off grid power, is highly reliable and easily maintained; they were invented over a hundred years ago, after all. But we might use PMSMs in mining trucks one day.”
Liebherr had worked with GE france for many years before the excavator electrification project, so it trusts in the reliability of GE’s electric machines. The e-motors designed for Liebherr’s excavators are manufactured at a facility in France, roughly two hours’ drive from where Lacoche, Goetschy and their team produce the Repower conversion kits.
In the 9400E, the Power Pack houses a 1350 kW (or 1.35 MW) motor, which functions on a nominal 6000 V AC input (although this can be configured for other voltages) at a frequency of either 50 Hz or 60 Hz. Its standard operating speeds run at either 1500 rpm or 1800 rpm, with an air-cooling system (detailed below) and starting power provided by an inrush current of up to 2.2 times the full load current.
“Our largest excavators, the 9600E and 9800E, both contain two Power Packs – hence two 1.7 MW electric motors working in unison – to power enough hydraulic flow and pressure for their operations,” Lacoche says.
“As well as the shock and vibration tolerance, critical design targets for the motor were to avoid overheating, and continuously achieve high efficiency in power factor terms. As we told GE, the motor has to run smoothly in 55 C ambient temperatures.”
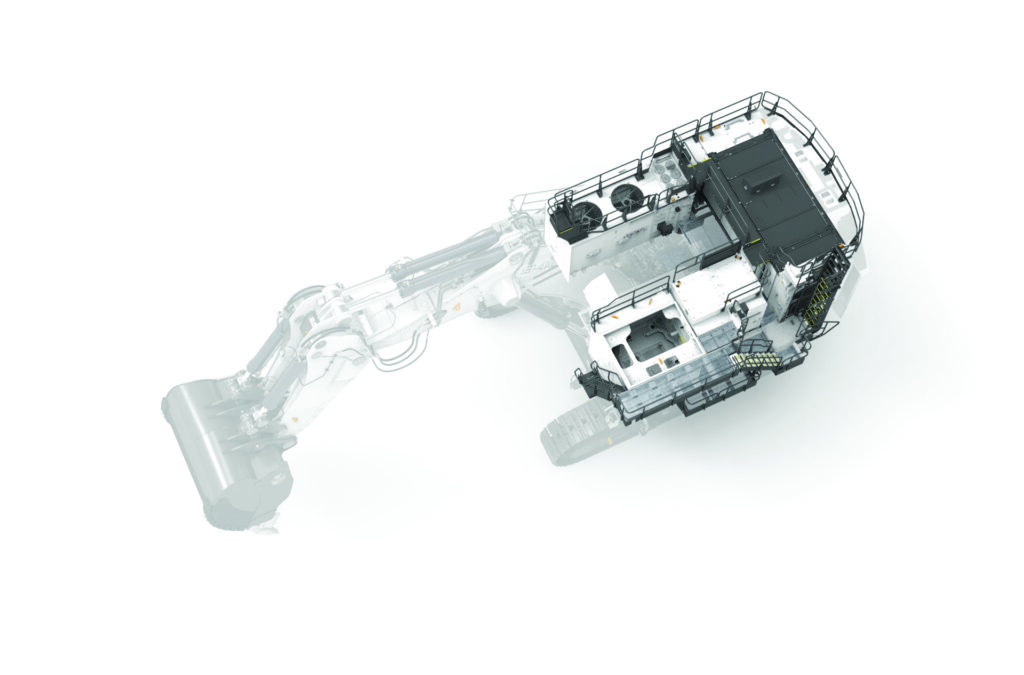
Air-cooled drive
Air cooling was chosen to achieve that smooth running with minimal mechanical complexity (in comparison to a liquid cooling system like that used on Liebherr’s diesel-driven excavators).
Rather than being a vast, sealed metal box, the Power Pack presents as an open, cuboid-shaped steel frame, which makes the modular installation of the system easier by lifting it and bolting it into the excavator’s main chassis (a fully enclosed system would be far heavier and harder to inspect).
Inside that frame is the cuboid electric motor housing, running most of the length of the Power Pack. The lower two-thirds of the housing’s internal volume is taken up by the squirrel-cage rotor and stator; the uppermost third houses the thermal management system.
This is largely a metal heat exchanger, constructed of many pipes (sized and arranged to optimise heat extraction, and make unnecessary the use of thermal pastes or pads). Fans draw ambient air from the rear of the vehicle to blow through and around the pipes (hence conducting heat away) before exiting via a vertically disposed exhaust vent at the top of the Power Pack.
The heat exchanger is typically constructed from aluminium, although stainless steel versions can be built and used where needed – for instance, to withstand salt-rich environments such as near-coast mines or excavators in dredging applications – as the design omits air filters to avoid baffling the flow of air (and the cooling effectiveness) through the heat exchanger.
“The airflow is entirely sealed from the motor air gap, because we work in really dusty environments and we absolutely had to avoid the risk of particles entering the electric motor,” Lacoche says.
“There are two fans connected directly on the motor’s shaft. One is rearward of the Power Pack at the entry of the heat exchanger to suck the outside air in, which then flows up and over the motor, through the heat exchanger and the many pipes inside it. The other is downstream, inside the latter part of the heat exchanger’s airflow circuit, down on the motor’s output shaft, for circulating the air and moving it out of the exit vent.”
The system’s air-to-air design (with shaft-mounted fans and an air circuit open to the external environment) conforms with the IC 611 method of cooling, as defined by the International Cooling (IC) topology codes laid out in the International Electrotechnical Commission’s (IEC) 60034-6 standard on the classification of cooling methods.
“It’s a really simple and effective cooling system: by mounting the fans on the motor shaft, the motor self-cools without needing any special control module, belts or even motors for the fans, and certainly no pumps, filters and so on that a liquid cooling approach would need,” Goetschy says.
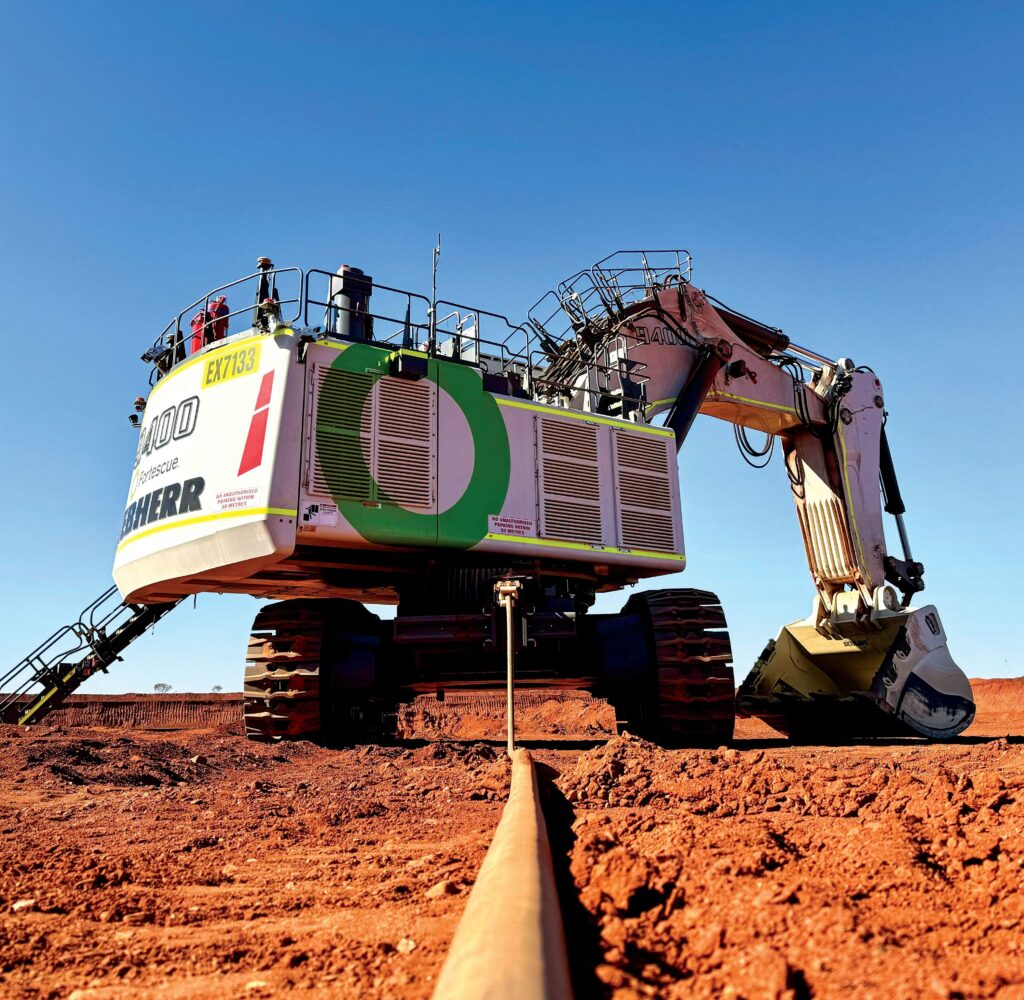
Splitter box
While the air-cooling system is installed in the upper region of the Power Pack, the splitter box sits st the front, integrated forward of the electric motor. An elastic coupling connects the motor output shaft to the splitter box input shaft; this part flexes to allow for slight misalignments between them and to dampen vibrations running between them.
Liebherr describes the coupling’s design as largely standard, save for being customised as a larger-than-typical unit (200 kg total weight) to suit the very large excavator and subsystems.
The splitter box itself is designed and manufactured by Liebherr Mining’s component division, which is also responsible for some of the pumps, most of the hydraulic motors, and the cylinders, filters, swing drive and travel drive in the excavators.
Overall, the design of the splitter box is that of a simple gearbox, with a main gear on the input shaft, off of which several other smaller gears corresponding to the hydraulic pumps for traction, digging and swinging are driven (accessory gears are also driven off the main gear). The box is sealed with an oil bath for cooling and lubrication.
“There is no need for clutches to engage or disengage the gears; our pumps are variable-flow swashplate pumps, adaptable to continuous values from 0% to 100% flow, so they are permanently engaged,” Goetschy explains.
“That variable flow is how we actuate and control the vehicle and digger arm movements, and it also helps us compensate for the very large starting power and inertia. That’s a big topic we’ll discuss later.”
Variances between gearboxes in each excavator are driven by differences in the vehicles’ size and power requirements: the larger the excavator, the bigger the gears, pumps, motors, cylinders, and the more of these components are needed.
“We will also change the splitter box depending on whether the grid gives power at 50-60 Hz, because the pumps must always move oil in line with the same speed and pressure ranges for effective control, so we’ll size the pump gears up or down depending on that input factor,” Lacoche adds.
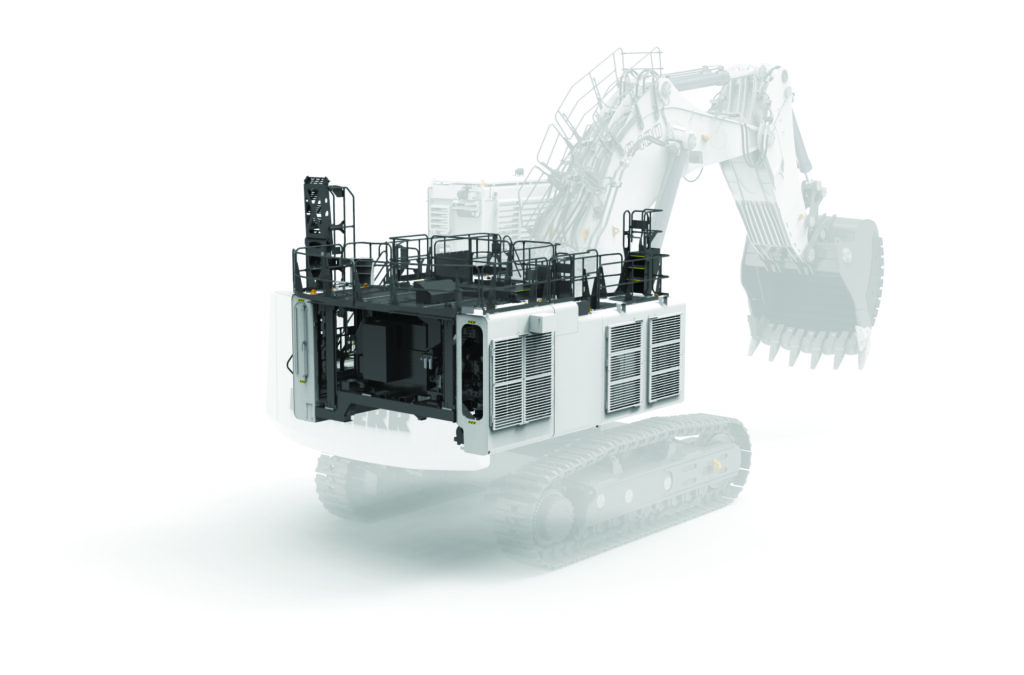
Plug-in EV
A large, high-voltage cable connection is used between motor and grid for some key reasons beyond the largely immobile nature of mining excavation work. As mentioned, the cable’s constant power supply means that the 9400E and other electric excavators must never stop to have their energy stores replenished, unlike the traditional, diesel-fuelled machines (or battery-electric excavators, far smaller as they are).
“In some colder mining projects, where no-one is dying of heat and they want the job completed as soon as possible, they will sometimes run the excavator for days and days without ever needing to stop and return to base to refuel,” Lacoche says.
IMAGE 4) The excavator runs on a cable connected to the grid, as 6000 V is more than any EV batteries can presently supply, and onboard systems can run on a constant speed input
Additionally, the 6000 V power supply needed to run the motor and drive the excavator is far higher than current EV batteries are designed for.
“One day, when the energy storage and power-delivery capabilities of batteries are multiplied by at least 10, then we will consider it,” Goetschy muses.
The grid hence provides the 6000 V power, with up to 7.2 kV often available in mine grids, and the motor and electrical architecture (and the splitter box, as mentioned) are adapted to grid specifics, depending on where the excavator is supplied.
As the motor runs at 1500 rpm or 1800 rpm nominal speed, depending on grid frequency (1500 rpm at 50 Hz, 1800 rpm at 60 Hz), no inverter is needed for variable speed control.
“With power running directly from the grid to the e-motor via the cable, the biggest concern for us is starting the motor,” Lacoche explains.
“When you start the motor, you get a huge, huge inrush current, maybe up to eight times the motor’s nominal operating current. To avoid that, we use a starting transformer [or autotransformer] to limit the inrush current to around 2.2 times the nominal motor current.”
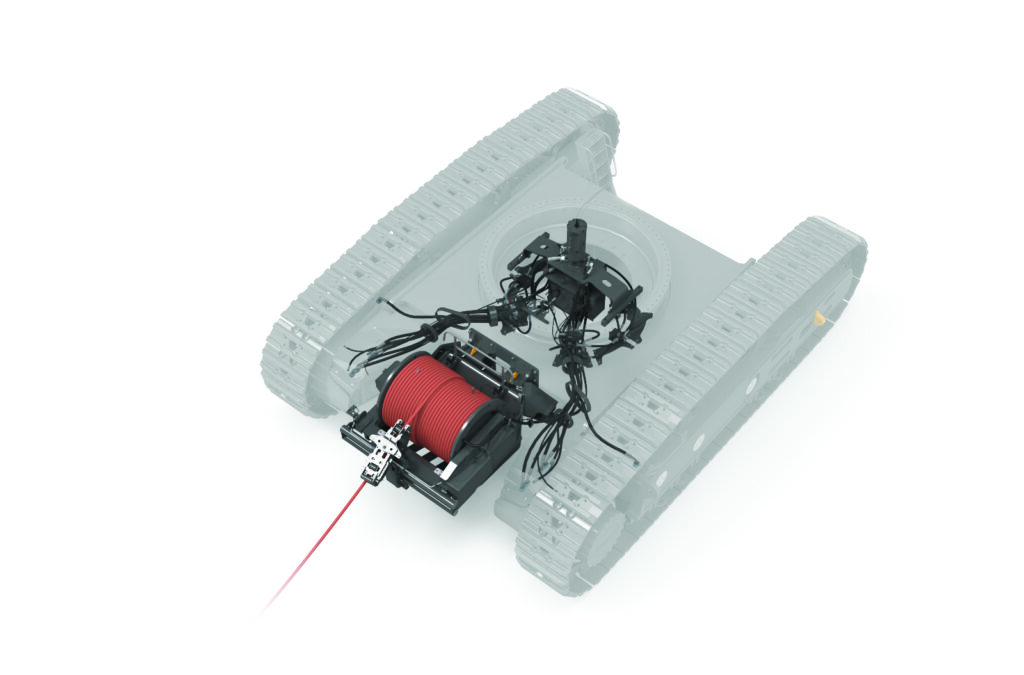
Transformers
While some might regard a transformer as a slightly old-fashioned system compared with inverters or soft starters (as Lacoche suggests), the latter systems would be of excessive sophistication and expense as the starter device only needs to be used once before the motor runs smoothly off grid power for the day’s operations.
“We use the autotransformer for about 10 seconds while starting the excavator, and after that it is switched off, so a simple, inexpensive and reliable device is great for us,” Lacoche comments.
“As well as not needing the variable-speed motor control that an inverter would bring, we’re also wary of how well EV inverters and those sorts of components can withstand the huge levels of vibration and shock that the mining excavators endure. Very few electric-power systems can; hence why so many subsystems are made in-house, here at Liebherr.”
Goetschy says: “The autotransformer design is based on one originally used in large trucks, where a low-to-high voltage, DC-to-AC power conversion was needed for a large electric motor. Obviously, we’re not converting directly to alternating current; it’s just an AC-to-AC connection in our approach, but the voltage stepping is still done so that we baffle the inrush current from overwhelming our motor.”
The transformer is constructed around three coils of copper wire and sits in the excavator’s high-voltage cabinet with some high-voltage contactors to control the starting sequence (specifically, to step the voltage up gradually, typically in stages of 50%, 60% and then 100% voltage, such that the inrush current is regulated to safe amperages).
To choose and design the autotransformer, the system was first sized to match the size and power of the electric motor, particularly as using too small a transformer would have meant considerable overheating and inefficiency from its coils. Some additional customisations were carried out to Liebherr’s specifications by the transformer’s supplier (as of writing), J. Schneider Elektrotechnik in Germany.
Both the transformer and its contactors can be adapted to achieve a certain level of starting torque. “As mentioned, a lot of our electric excavators were initially sold in colder regions in Eastern Europe. When you’re trying to start a hydraulic excavator in -40 C, the oil will be very thick and viscous,” Lacoche explains.
Goetschy adds: “When the oil is like that there is a lot more inertia to overcome, so it will take a lot more torque than is nominal to start the motor and the vehicle’s hydraulic installations. So the starting transformer can be configured for the voltage steps, and hence the current and thus torque bursts that are ideal for getting the oil moving.”
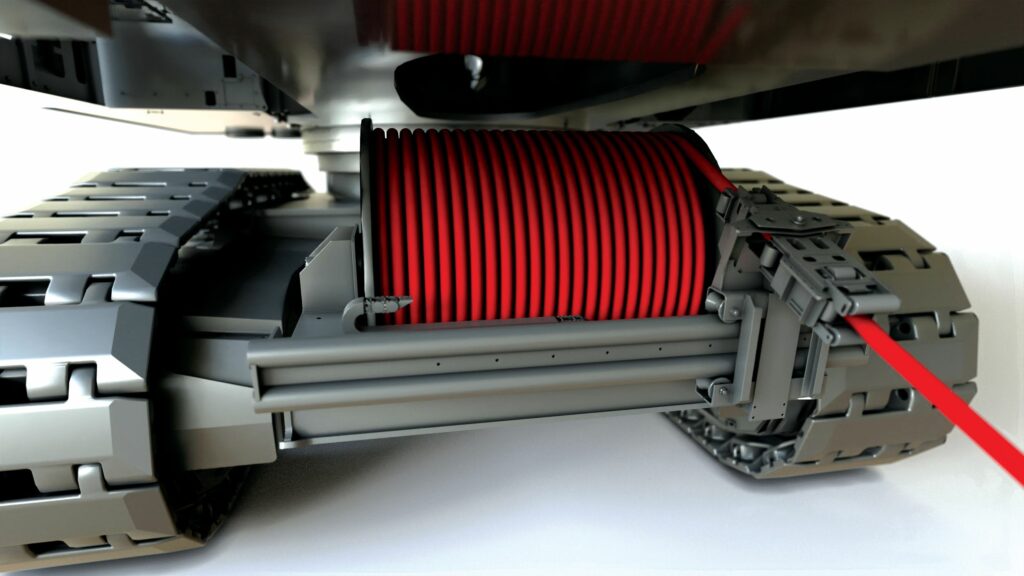
High-voltage cabinet
The aforementioned high-voltage cabinet occupies a considerable portion of the interior of the 9400E (and its siblings) and houses many more components than just the autotransformer.
Among these are a plethora of safety devices, key being the vehicle’s main circuit breaker, and a series of protection relays. Should something erroneous be detected in the energy supply or electric motor during the monitoring executed via the protection relays – such as readings indicating excessive temperatures, overvoltages and so on – the main circuit breaker will automatically shut off the main power to stop the excavator.
“There are also two small high-to-low voltage transformers in the cabinet; these supply lower voltages, such as 400 V DC and below, for subsystems like the cabin’s air conditioning or heating,” Lacoche says.
“Beyond that are a number of fuses, relays, and similar electrical safety and distribution systems, and all of these components, including their models, are used across our portfolio of electric mining excavators without any significant differences in design or configuration, because the key operational requirements for starting the electric motor, for producing low voltage and so on, are the same in every vehicle.
“Even in the 9800E, the biggest electric excavator with two electric motors, the steps for handling the inrush current are the same: we just start one motor and then repeat the startup sequence to activate the second motor. The 9800E’s transformer is built a little bit bigger and stronger than that in the smaller excavators, as the higher power flow risks overheating the transformer without more room and metal to withstand the heat, but otherwise it’s the same componentry and electrical procedures.”
Depending on the required power, the company can adapt the transformers, but the circuit breakers and high-voltage contactors are largely identical from one excavator to the next, and all these components are used across the Liebherr Group’s machinery too, saving on development costs for creating new components.
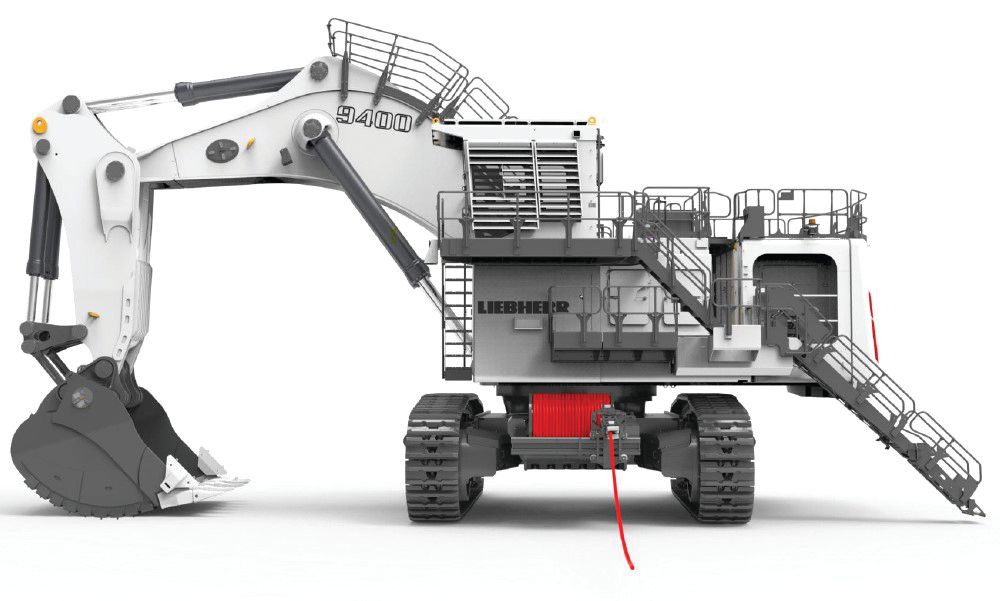
Rotary connection
The swing drive responsible for rotating the uppercarriage atop the undercarriage is driven by two hydraulic axial piston motors, each powered by a reversible swashplate pump. Each one also uses a planetary reduction gearbox to convert their speed into sufficient torque for turning the uppercarriage, up to a maximum speed of 3.9 rpm.
The actual driven component within the swing drive is a sealed triple-roller swing ring with internal teeth; in essence, a very large bearing. A pinion gear at each of the planetary gearbox’s output shafts engages with the swing ring. Pipes for delivering oil down and up through the swing ring (for driving the traction system) run through the middle.
These parts discussed are no different in the 9400E from those in the diesel-powered R9400. However, differences start to emerge when accounting for the fact that electric power from the grid-linked cable must be transferred from the undercarriage to the upper carriage.
“The cable must connect to the undercarriage and not the upper carriage, because the latter needs to be able to swing 360o, and farther, continuously without wrapping the cable around the outside of the swing drive,” Lacoche notes.
Therefore, a high-voltage slip ring is installed in the centre of the swing drive chassis, and used to facilitate the travel of electricity between the under- and upper carriages. The model used in the Repower excavators is a standard industrial slip ring, and is composed largely of copper rings and brushes for conducting electricity from one terminal to the next.
“Regarding the electrical architecture, inside the slip ring we have three phases of alternating currents and one earth connection, so that means we have four big rings inside the slip ring assembly to transfer electric power,” Lacoche says.
“In addition to the high-voltage AC power going upwards, we also have to transfer low-voltage power downwards from the upper carriage into the undercarriage, because all electrical boxes – which includes the slip ring, and even the electric motor – must include an electric space heater.
“That’s important for avoiding buildups of moisture inside those components, which will lead to arc flashes if allowed to accumulate, but constantly preheating all those cabinets avoids such a fault condition.”
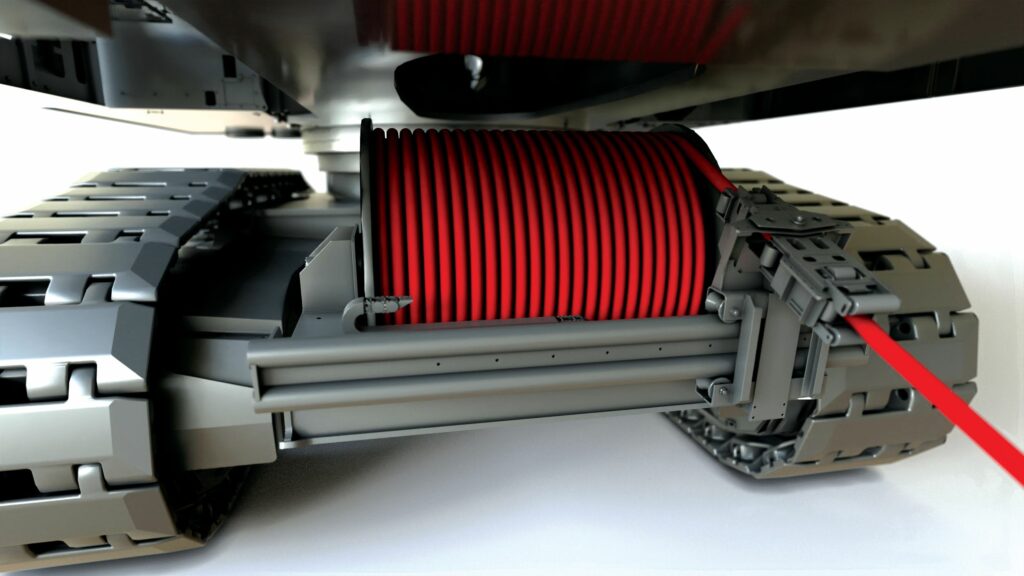
Cable management
The swing-drive enclosure is bolted atop the undercarriage, with the upper carriage connected atop the swing ring. At the rear end of the swing-drive enclosure, a motorised reel for the high-voltage AC cable can be installed (integrating the reel is optional; the cable can also be installed to run directly into the undercarriage chassis, although Liebherr notes that the reel provides greater mobility to the excavator).
“Naturally, if there’s a big, heavy cable running behind your excavator, then you need to take care regarding it. When you go backwards, you don’t want to run over and damage it, nor do you want to tangle it in the tracks accidentally, and so on,” Goetschy says.
“It happens, so we do recommend the reel for safer and automated cable management, even though some countries prefer to do their cable management by ordering some workers to stand behind the excavator and move it by hand.”
The reel automatically reels and unreels the cable in response to the excavator’s movements, and it has formed a significant part of Liebherr Mining’s r&d efforts, as the group seeks to minimise variations in mobility between the diesel- and electric-powered excavators (the latter’s mobility being significantly enhanced by the reel).
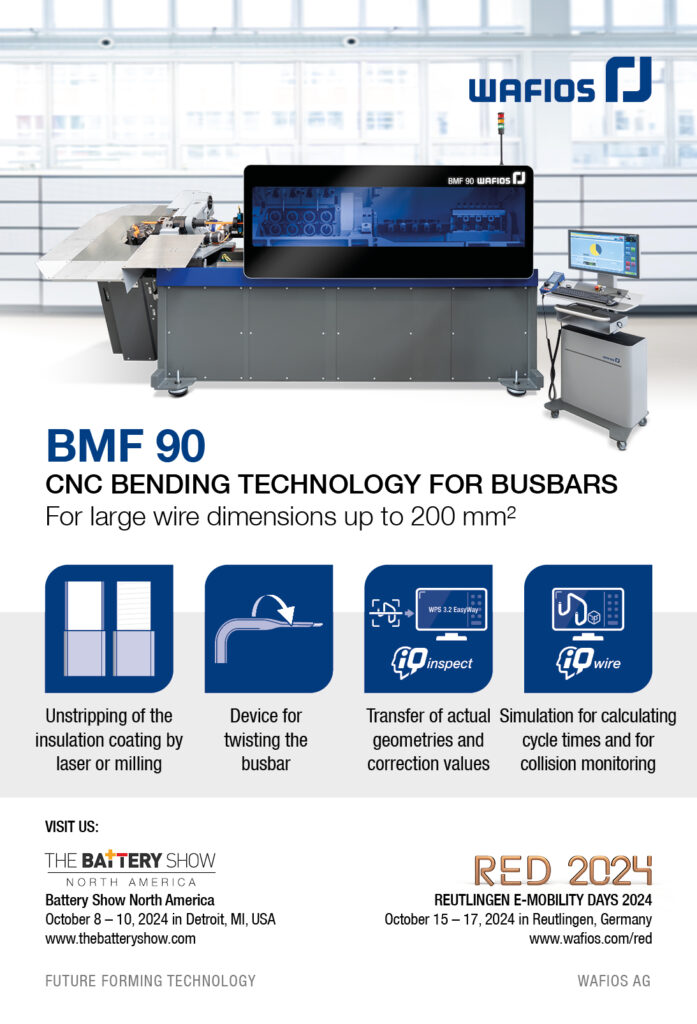
“Making the reel wasn’t simple, not least because the high-voltage cable can be incredibly heavy – the heaviest cable on the 9800E, for example, can weigh up to 15 kg per metre – hence why many workers may be needed to move it by hand,” Lacoche says.
“Fortunately, the reel doesn’t use too much electricity because we have a hydraulic motor running it. Our point of view is that it’s much more power-efficient than driving it with an electric motor. All of our competitors electrically drive their vehicular cable reels, but we’ve been able to use a very compact and powerful hydraulic motor that allows us to maximise the drum size.”
Per the other hydraulics, variable pumping defines the power going to the reel motor, and a reduction gearbox inside the drum helps boost the output torque imparted on the reel at the expense of speed (an acceptable trade-off, given that the excavator rarely moves and is slow when it does).
“Using this system, we don’t even drag the cable along the ground during vehicle movements anymore. We reel or unreel the cable as the excavator moves to keep it lying still, and so avoid abrasions or tearing of the jacket material against rocks, which can happen very easily,” Goetschy says.
Control
A centralised computing system controls and monitors the network running throughout the excavator, ensuring the transmission of commands from the operators’ cabin to the high-voltage cabinet and the hydraulic pumps, as well as consistent monitoring of health and performance sensor information for all onboard systems (via interfaces in the cabin).
Using that computer and their LCD information displays, operators can bring up critical specs on electrical components, such as the autotransformer’s temperature or the loads of the electric motor. The lattermost parameter is useful not only for tracking how much power the excavator consumes, as energy bills won’t be limited to the energy capacity of a battery pack, but also for affirming that the e-motor is performing safely from an electrical point of view.
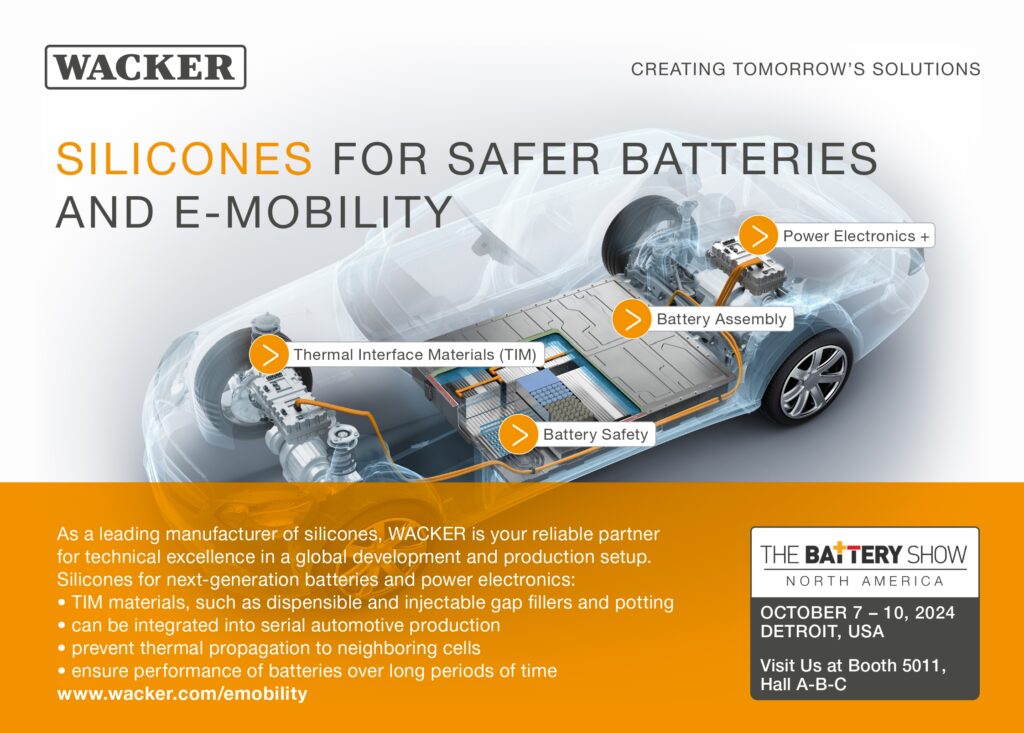
“We have an industrial computer running Windows that functions as the equivalent of a VCU you’d find in more conventional EVs. It is integrated at the heart of the Global Monitoring System [GMS] in the excavator, which also means it connects to sensors in all of the hydraulics, so temperature, pressure, and flow rates in the oil across the pumps, motors and pipes can be monitored too,” Goetschy says.
“The same GMS network is bringing operators alarms when there’s some anomalous parameter, so they can inform maintenance teams, or stop the excavator for inspections or repairs in more extreme instances.”
Standard SAE J1939 CAN is used as the network protocol, being a well understood and widely used means of interface (with industrial alternatives deemed unnecessary by Liebherr Mining), particularly since end-users must be able to easily access and view every excavator’s telemetry remotely from their mines’ operating centres, without needing to learn an entirely new networking protocol.
“More and more mines use fleet-management systems with their own communications and data-transfer bridges between remote equipment and the central software, so that managers can see what’s normal and what’s critical across all their machines, and interact with their maintenance crews when required, all live and in real time,” Goetschy notes.
“In fact, J1939 CAN is so widely used by mine fleet managers that we’re now installing it in all the diesel excavators for comms between their combustion engines and their main computers to replace the different CAN protocol that ran there before this year.”
Key suppliers
Electric motor: GE france
Heat exchanger: GE france
Starter transformer: J. Schneider Elektrotechnik
Elastic gearbox coupling: KTR Systems
Gearbox plugs: Bosch Rexroth
Oil-control valves: Bosch Rexroth
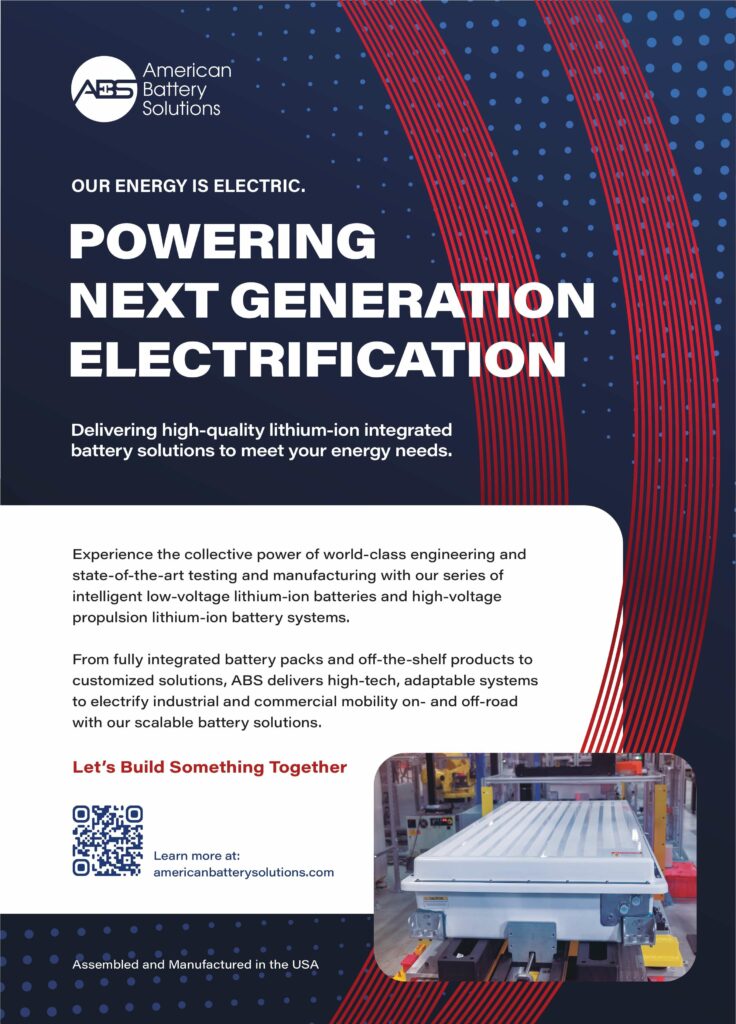
Click here to read the latest issue of E-Mobility Engineering.
ONLINE PARTNERS
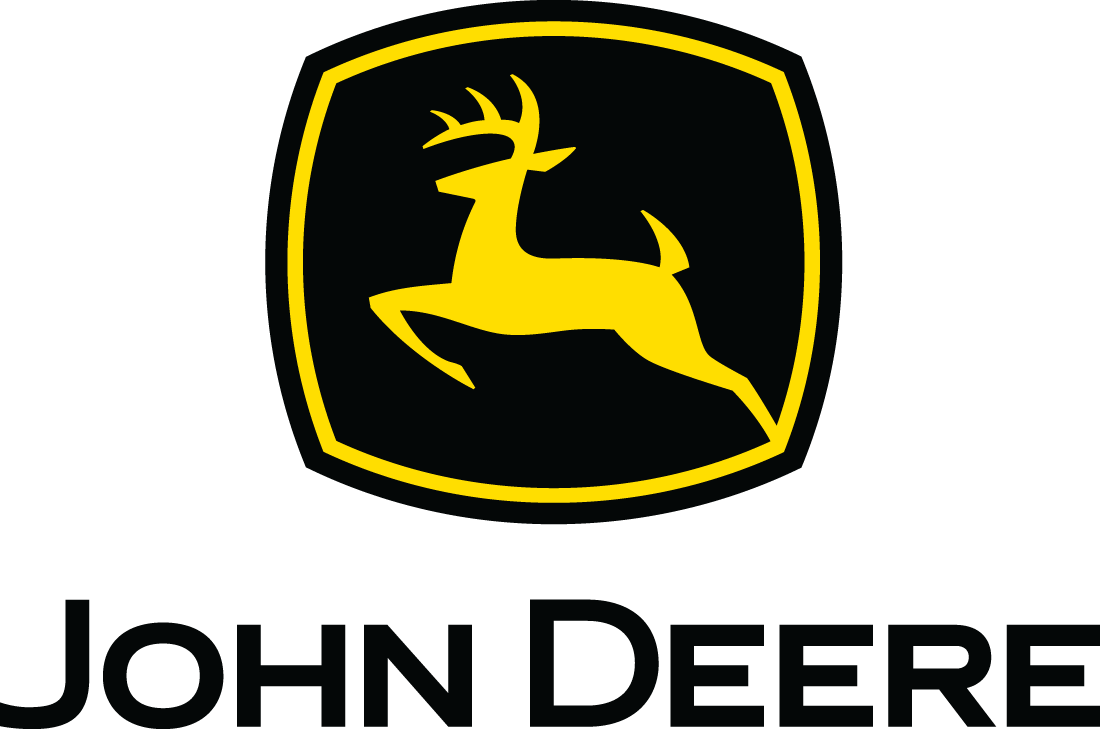
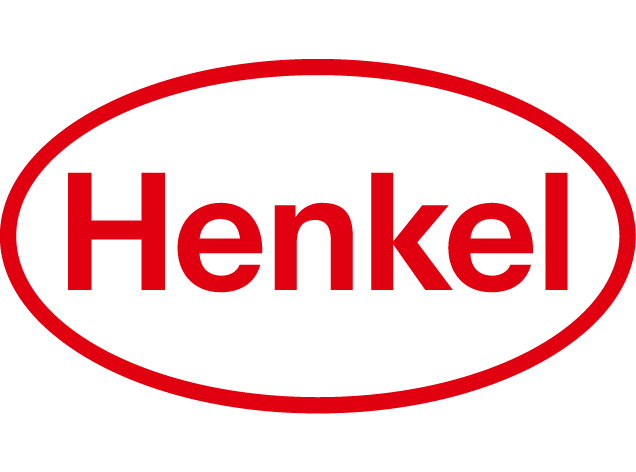
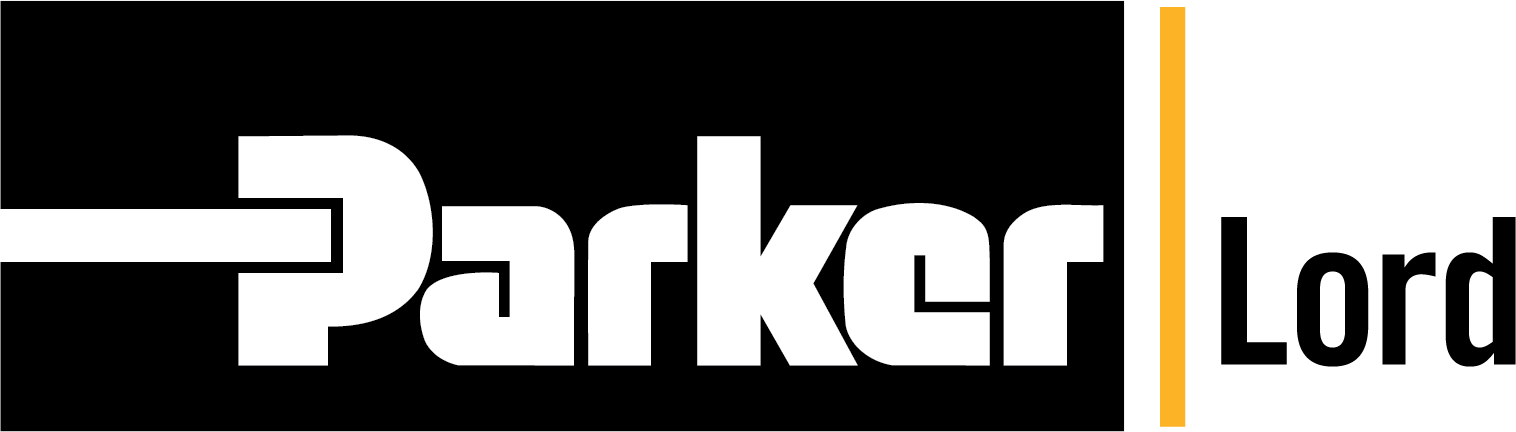
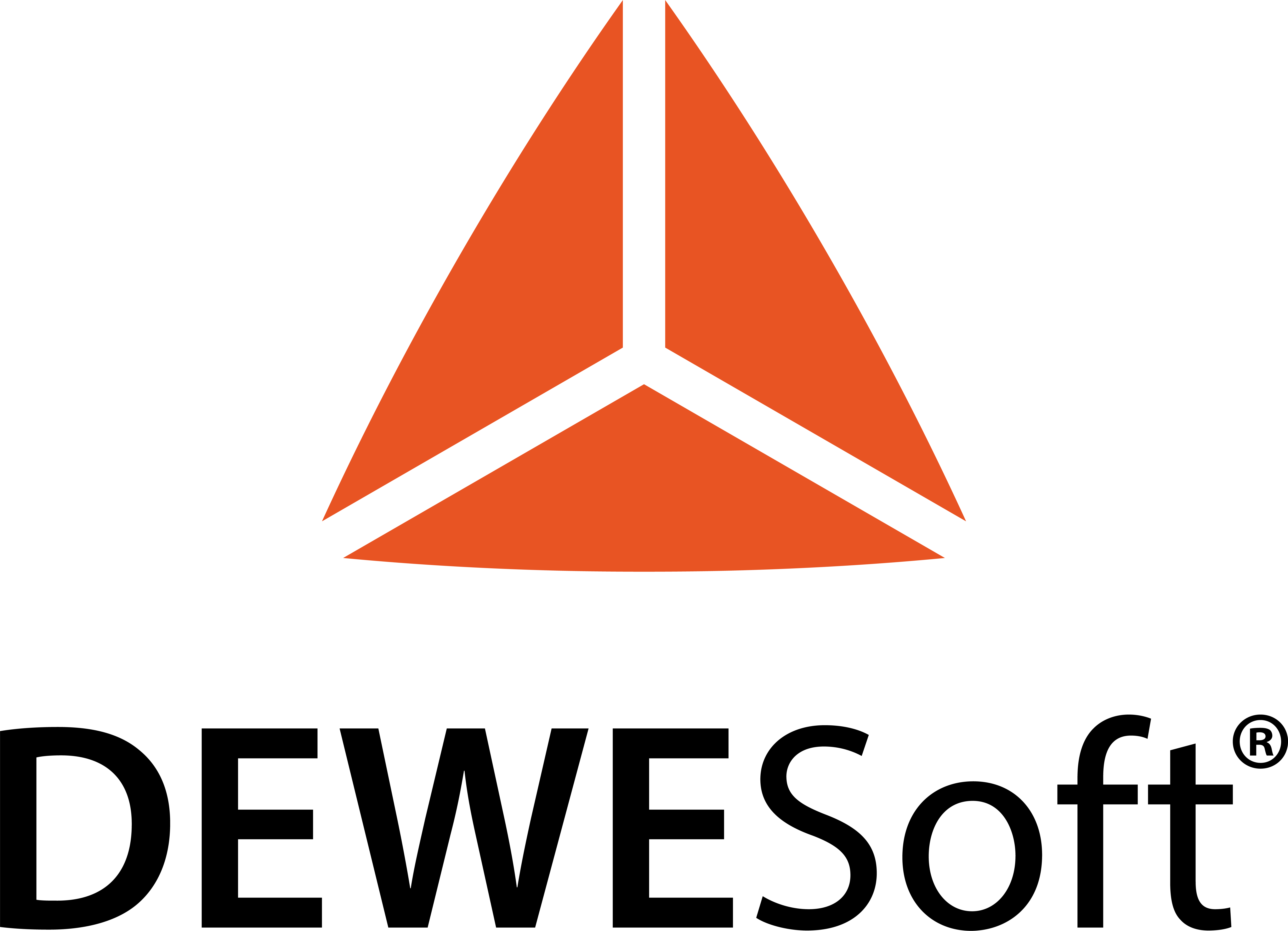
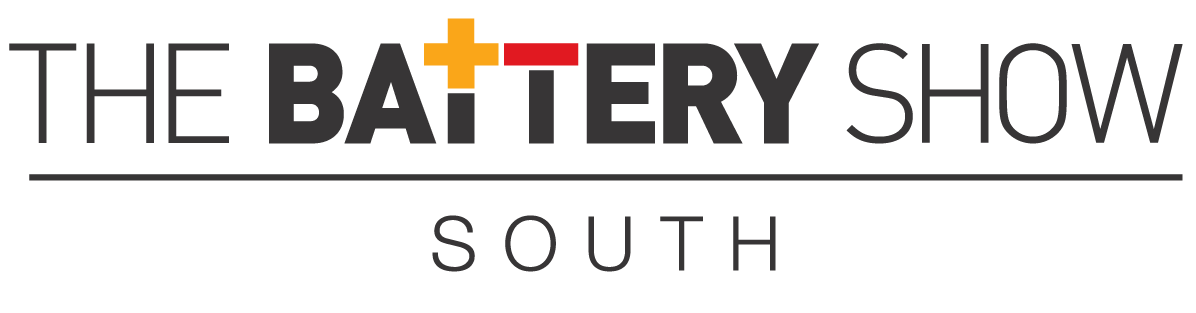
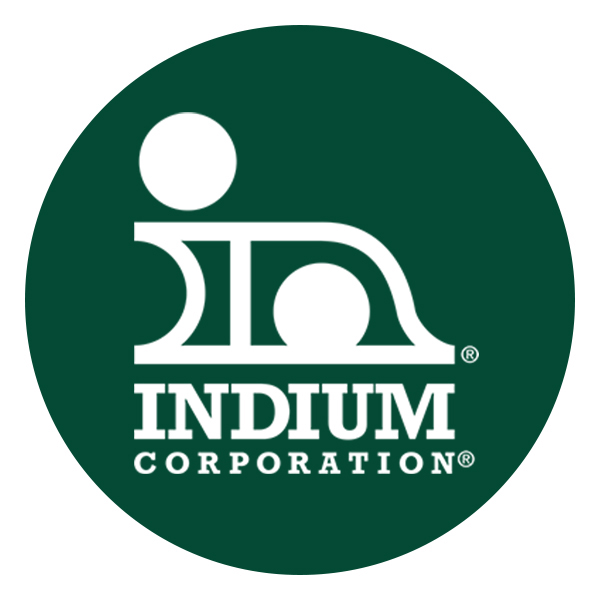
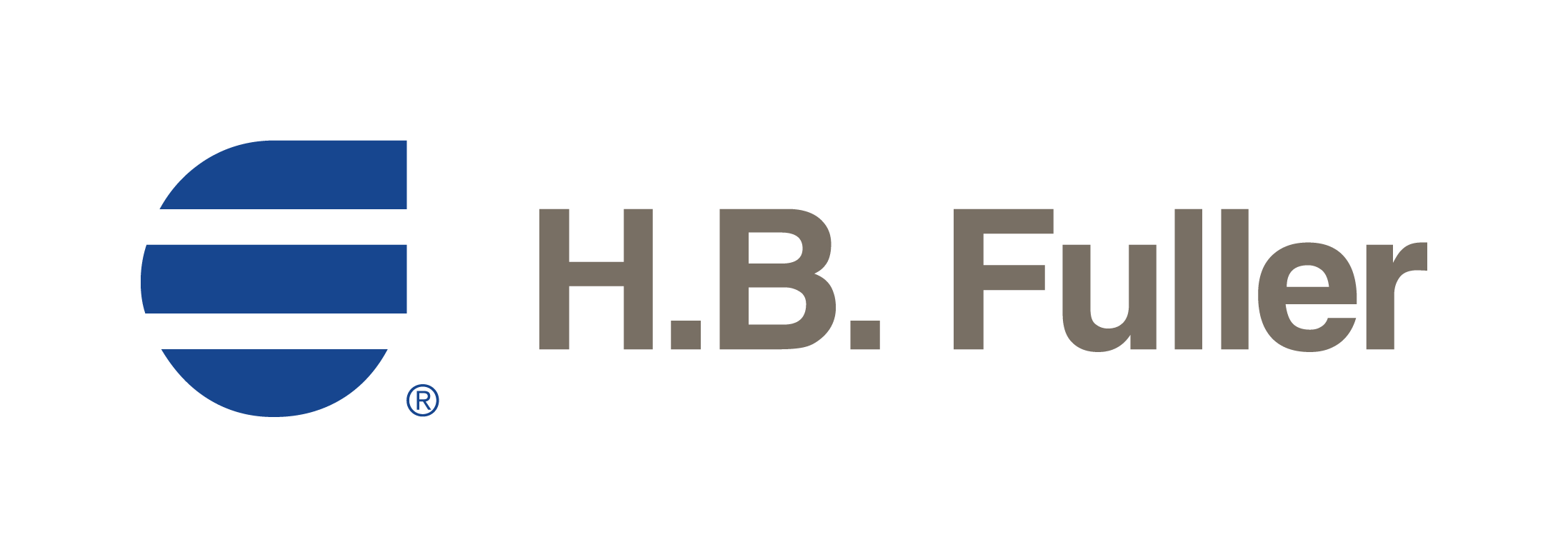