In conversation: Neil Yates
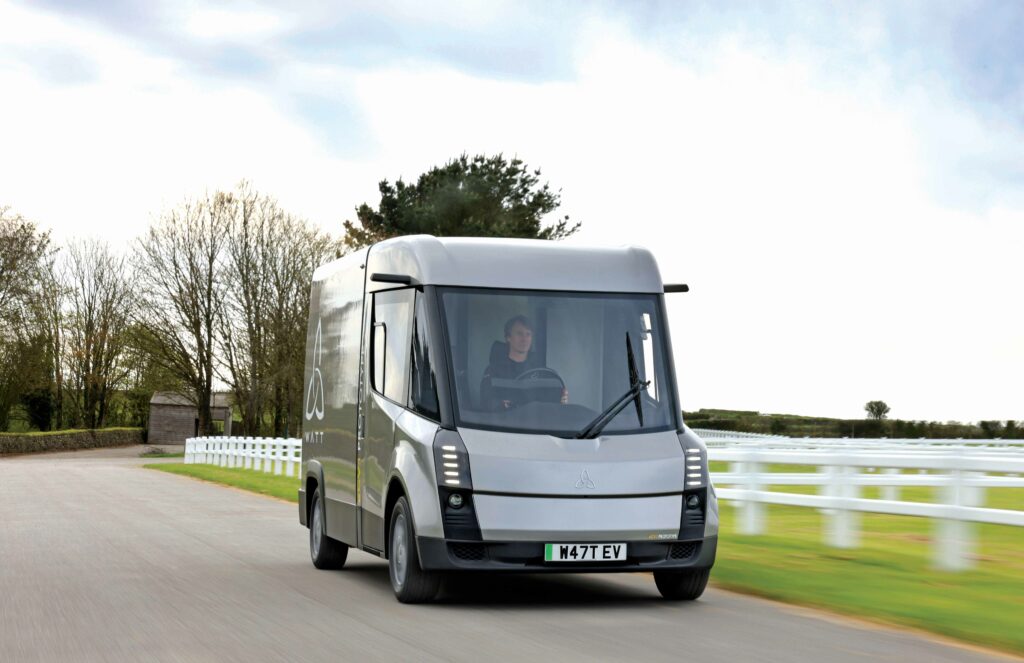
(Images courtesy of WEVC)
Skating with foresight
Rory Jackson learns the success of a leading skateboard developer
With effectively all automotive OEMs now shifting focus from internal combustion engine (ICE) vehicles to e-mobility, an eye for emerging trends across the industry and its markets has become critically. This strength is enabling one company to determine what technological, manufacturing and investment directions it should take, amid the rapid innovation and significant upheaval taking place across road vehicle production.
As founder and CEO of WATT Electric Vehicle Company (WEVC), Neil Yates has steered his team amid considerable industry turbulence and transformations to successfully develop and manufacture its Passenger and Commercial EV Skateboard (PACES) platform. That platform is the basis of its commercial eCV1 Chassis Cab (itself a modular design, launched commercially in 2023 and available as various van-type derivatives) and its passenger EVs, which the company produces in low to medium volumes. These it considers rightsized and optimised for niche applications.
“High-volume automotive manufacturing takes not only huge investment, but mass, widespread consumer acceptance of EVs and the very slight lifestyle changes – already being widely undertaken today – that their uptake would entail,” Yates says.
“From a technological point of view, the biggest issues facing manufacturers are around electrical architectures, subsystem integration, and the ability to update software and firmware seamlessly. You only need to look for instance at how Volkswagen have put $5bn into Rivian toward understanding its distributed and zonal electrical architecture, to understand how serious these issues are. And subsystem choices hinge on the race towards efficiency each OEM is engaged in – not just electrical efficiency, but packaging efficiency and weight efficiency, all of which are skyrocketing orders of SiC, new battery cells, and similarly beneficial technologies for making a holistically better EV.”
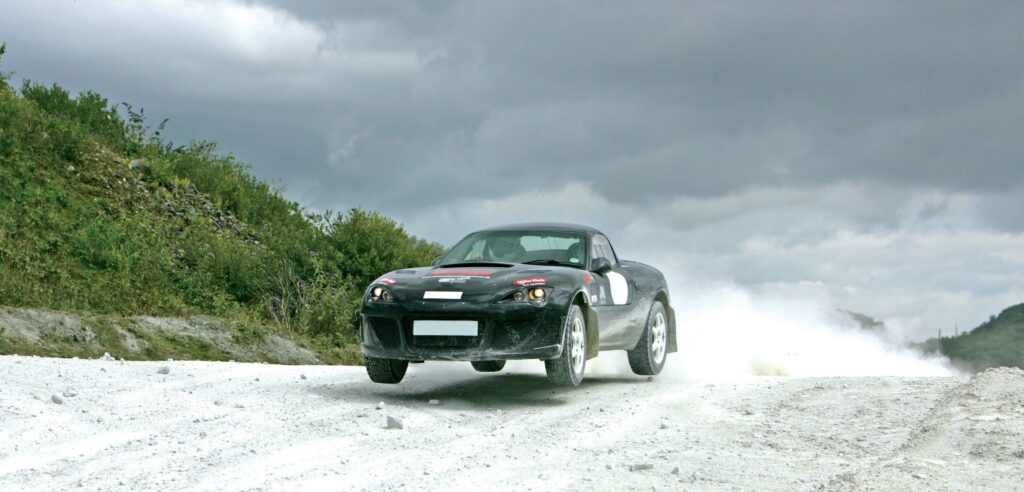
What’s Watt
The modularity of a skateboard-type platform has been key to WEVC navigating industry trends as Yates has observed them. Unusually, however, the route to his present-day leadership in EV skateboard production first went through considerable quantities of motorsport.
Having been brought home from the hospital of his birth in a stage rally-prepared Mini Cooper S, Yates likely had the earliest start to involvement in motorsport in the life of anyone featured in this publication. After a childhood spent helping his father build rally cars, and many subsequent years as a technician and engineer in various forms of racing, he founded Adrenaline Motorsport in the early 2000s to design and manufacture sports cars (which it did so successfully).
Foremost among these was the Murtaya, a 400 bhp, 925 kg vehicle still manufactured today by ALS Sports Cars. It is a two-seater convertible sports car which was well-received upon its 2006 unveiling for its dynamics, its handling, and its performance. It had been designed around a Subaru Impreza turbocharged four-wheel drive powertrain, within a multi-material composite monocoque.
“Dan Muir – who had been a top structural engineer on the Lotus Elise and some of its subsequent Aston Martin derivatives – gave critical input on the structural materials and the dynamics; key to how the Murtaya performed,” Yates recounts.
“My primary role there was running a holistic engineering programme, from the first sketches through to production and release, in a way that would specifically result in something customers would actually want to own and drive – that’s been a common theme of my career since. The Murtaya was intended to be a lightweight, agile, driver-oriented sports car, even though the trend back then was towards bigger, heavier sports cars with headline-grabbing power outputs, instead of driver engagement and experience.”
Following the Murtaya fanfare, Adrenaline received extensive requests for consultancy on other next-generation car projects, particularly low-volume sports cars, which drove Yates to reach out far and wide across supply chains, out to different powertrain, structure and interior component manufacturers.
Amid the rise of watershed car projects like the Tesla Roadster, Yates soon found himself developing a skateboard-type vehicle chassis designed for integrating either an ICE, hybrid or battery-electric powertrain, named lightweight chassis for alternative powertrains (LCAP). This was to be supplied to third-party manufacturers to underpin their next-generation vehicles.
“But manufacturers were still heavily-wedded to welded-steel spaceframe chassis back then, and didn’t see a need to provide for alternatives to combustion engines,” he reflects. “We focused on delivering other projects from 2011 onward, including battery-assisted bicycles, passenger and sports cars, and commercial vehicles, until the winds started changing around 2018.
“I could see that there were – and are – many small manufacturers who lacked either the core competencies or financial resources to make all-new EVs from scratch. Judging that maybe the modular chassis platform’s time had come, we applied to the UK government innovation agency for a grant to support development of an EV platform. This today is the PACES system, which we demonstrated for the first time using two prototypes in 2020.”
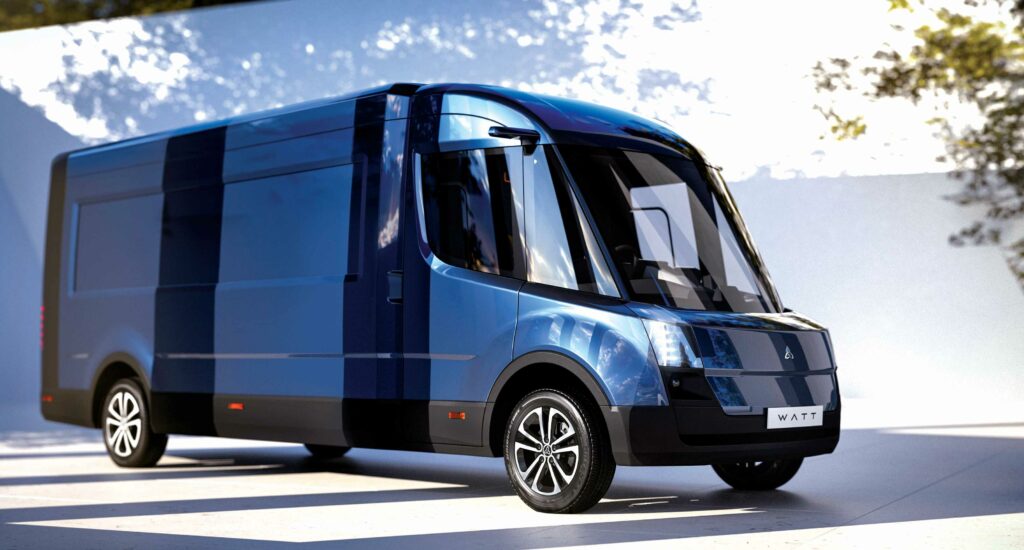
Platforms and platforms
The architecture and componentry of PACES are completely different from those in the pre-2011 LCAP platform Yates and Adrenaline produced, given that in 2010 there was no consensus yet that EVs would be the future of automotive. Hence, LCAP’s allowance for ICE integrations in how it was designed.
“The idea behind PACES is to have something that can be adapted quickly and at low cost for a wide range of finished EVs, including L7e commercial last-mile delivery, through passenger and sports cars, and on to light- and medium-duty commercial vehicles,” Yates explains.
“PACES uses a common suite of hardware to cover that range of applications, mounted within a bonded aluminium chassis, with space for a range of powertrain options to meet exact end-user requirements, and the system is designed to be made using low-volume and small-series manufacturing processes, up to low thousands of a given vehicle type per annum.
“That whole design approach is specifically engineered to lower the barrier of upfront investment for OEMs looking to go from concept to market-ready, and also reduce the period of time needed to deliver that.”
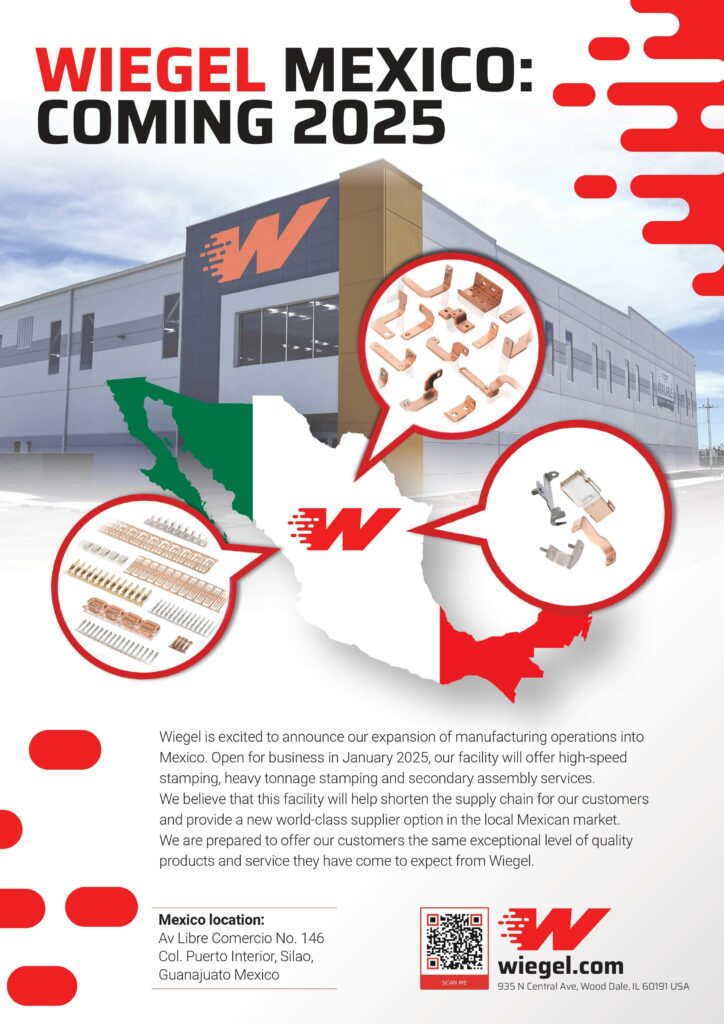
Holding batteries differently
A critical step towards this goal has been developing and optimising the way that WEVC integrates its battery into the PACES passenger vehicle chassis. In that system, the battery modules are built directly into the primary structure, forgoing any ‘battery box’ separate from the main structure.
The result is a “module-to-chassis” architecture, which gives WEVC a more weight- and energy-efficient vehicle chassis. As Yates explains, “Battery enclosures are large and heavy. To fit an entire pack into a vehicle you need a big empty void, and the surroundings of that void need to be incredibly strong to support the enclosure’s weight, which then extends outwards, such that the overall vehicle structure needs additional reinforcements to maintain its torsional rigidity and crash-safety properties.”
Hence, constructing the modules integrally with the chassis means that the significant weight of an enclosure and additional reinforcements are not added, and the structure can be holistically designed to support the modules in a way that they aren’t (typically) in conventional pack-to-vehicle configurations.
“A module-to-chassis approach would have been seen as quite risky to attempt five-to-10 years ago, because of the immaturity of battery technology, the worry around cell or module failure, and how accessibility could be optimised to effectively take apart or repair such a hardware arrangement,” Yates notes.
“But we’re now at a point where you can get battery modules that are incredibly robust from a reliability and performance perspective, and through modern design and manufacturing technologies we’re able to engineer the vehicle so that even though the batteries are integrated into the primary structure, they’re still reasonably easy to access, should maintenance be required.”
In WEVC’s commercial platform, the batteries are instead built onto a patented “multi-material battery base plate”. This is a system composed via a proprietary mixture of construction and material approaches, which WEVC produces and fits to the vehicle structure such that it becomes a structural member for the chassis.
Once that multi-material base plate is installed, the chassis essentially provides the remaining five sides of the cube-like battery box. As with WEVC’s passenger platform, this results in weight-efficient integration of the battery with the EV platform. More importantly (for commercial fleet operators), it results in a payload capacity that is proportionally higher than in more conventionally-designed EVs.
“In high-volume EV manufacturing, you’ve got the likes of Tesla and Volkswagen planning to implement cell-to-chassis designs in 2030 and 2035-onwards, respectively,” Yates says.
“In a new era of vehicles and powertrains, there won’t be a single right answer for all applications. Within mass-manufactured ICE vehicles, you have diesel versus petrol engines; EVs will have battery-electric and hydrogen-electric, and something else next-gen will inevitably come along, whether it’s solid-state batteries or future innovations not even thought of yet.
“So flexibility was really important to us in how we design and manufacture our vehicles. Going module-to-chassis helps us take a massive step in energy efficiency, in lightweighting and integration – and also in how quickly we can adapt to changing technologies as the pace of advancement in e-mobility looks set to continue for the next 20 years.”
WEVC presently uses 21700 cylindrical cells, which allows them a variety of suppliers and energy densities – and chemistries – to choose from. A proprietary thermal management system has been innovated for its modules (with patents currently being applied for), which Yates anticipates will empower significant energy efficiency gains going forwards.
“The module and cell format is consistent across both our commercial and passenger platform designs, albeit with some string and parallel configuration changes to suit specific applications,” Yates adds.
“21700s are currently the right mix, we feel, of commercial readiness and technical capability for the next five-to-10 years – but, of course, we’re engaged with a huge range of suppliers inside and outside the UK of what could be the next-gen technologies, for future consideration.”
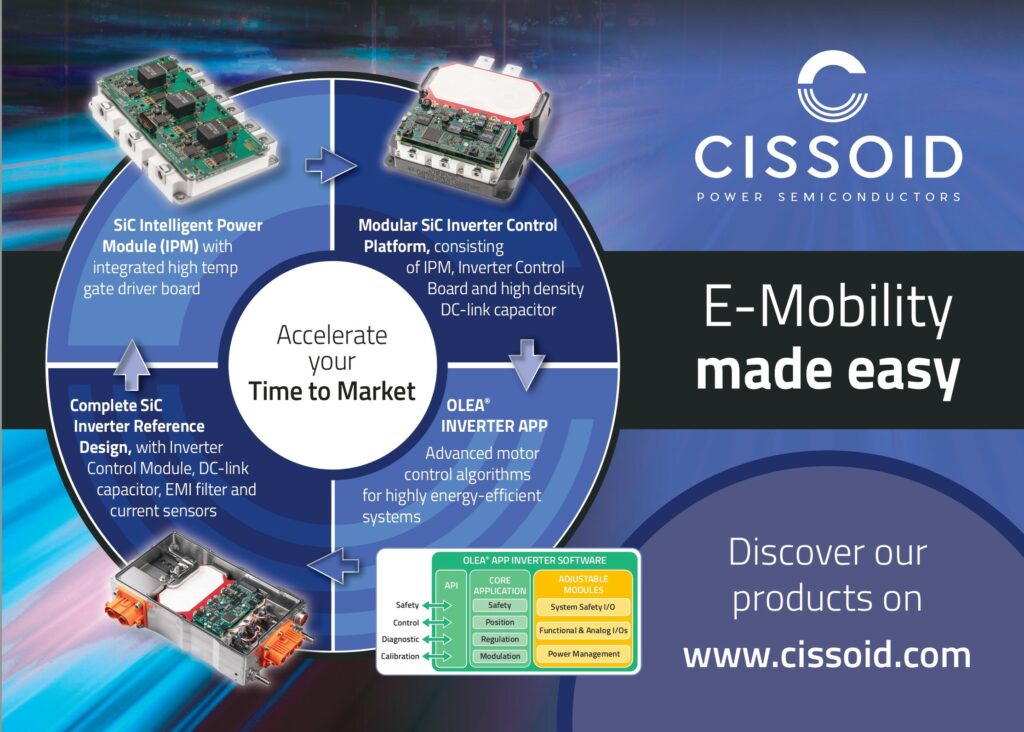
The body shop
The recycled aluminium used by WEVC to manufacture its chassis is supplied by Oslo-based Norsk Hydro. Such is the dedication of both companies to future circular economies that WEVC will return the chassis to Norsk Hydro at their end-of-life to repurpose the aluminium for further onward uses.
“That material has around a quarter of the carbon footprint of conventional raw aluminium material, thanks to how Norsk Hydro produces, recycles and later repurposes it, which is great for reducing the embedded carbon footprint of our manufacturing,” Yates says.
Additionally, the commercial platform uses a composite of polypropylene and glass fibres for its body panels. This material provides high impact resistance, as well as resistance to minor abrasions and scratches, to a degree that Yates says is greater than that of conventional metal body panels.
“That means you’re not so often replacing and repairing the body to maintain its aesthetic qualities, as you do when you’ve used a metallic substrate in the body”, he explains. “And unlike some carbon composites and metals, this composite is highly recyclable at end-of-life, particularly for second- or third-life applications.”
A composite braided upper structure is also used in WEVC’s vehicles, partially chosen for advantages in lightweighting and also for end-of-life recycling. Arguably its greatest benefit, however, is that composite braid parts can be extruded as single pieces with highly complex geometric shapes.
“If you look at a windscreen A-pillar, or an A2 pillar on the door, for example, those are traditionally made from somewhere between four and seven separate metal elements,” Yates comments.
“Those elements are jigged and tooled into a single part to provide your glass fit, your seal path, your A- and B-class surface finishes – but with our extruded composite braid structures, we can do all of that with one single part. So when customers have to look at upfront investment costs and the like, our platforms and vehicles won’t come with the same level of expensive tooling, jigging and fixtures as is seen in conventional vehicle assemblies.”
Future
Despite the array of novel engineering approaches in PACES and its two EV products, WEVC continues observing and engaging closely with companies it feels are developing solutions capable of empowering the next “quantum leap” (as Yates puts it) in EV performance or physical specs. Be it across propulsion, energy storage, thermal management, body materials, power distribution or so on.
“For obvious reasons we can’t disclose who we’re actively engaging with, but we’re always interested in hearing from groups who have new technologies that they want to develop or prove-out at vehicle level, and seeing if we’re interested in providing a route to that validation,” Yates says.
His team has, for instance, investigated integrating hydrogen fuel cells, following approaches from both end-users curious about hydrogen options for long-range use-cases, and powertrain suppliers seeking platforms to test and demonstrate their fuel cell technologies in.
“Batteries will be the solution for most applications, at least for the next 10 years, and that’s what PACES’s architecture has been developed primarily around,” Yates comments.
“But ongoing r&d is an essential consideration for any business, and it pays to bake adaptability for new technologies into your architectures. Whenever the next ‘unobtainium’ does arrive, we will be able to integrate and use it in our platform in a seamless and cost-effective way.”
Neil Yates
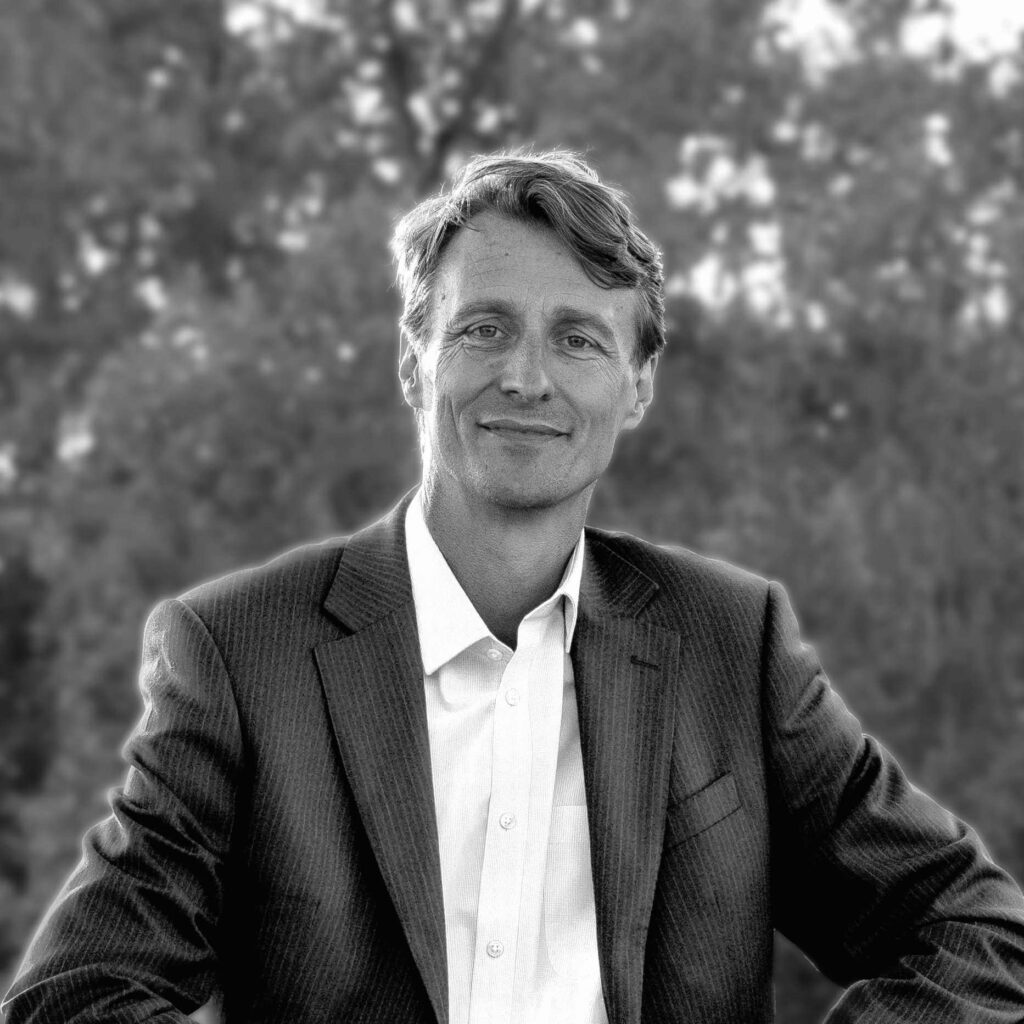
UK-domiciled Neil Yates was born in 1973 in Wiltshire, where he grew up and lived for the subsequent 20 years before relocating to Cornwall, where he has lived since.
Following the conclusion of his secondary school education, he took a variety of technical roles across motorsport until founding Adrenaline Motorsport in 2005 to develop low-volume, high-efficiency sports cars.
He founded WEVC in 2019 primarily to develop the PACES solution, which was unveiled and demonstrated in 2020, before reaching commercial availability in 2023. The company has also since unveiled its eCV1 commercial van solution and a passenger vehicle based on PACES. Yates continues to lead as CEO of WEVC today.
In addition to consulting outside of WEVC, Yates founded Rally Prep in 2011. This company, which he continues to lead at time of writing, is focused on building and maintaining specialist and motorsport vehicles. He is also an executive member of the Niche Vehicle Network, an independent network of UK-based, low-volume, specialised vehicle manufacturers, as well as niche automotive technology developers, designers, and engineering organisations.
ONLINE PARTNERS
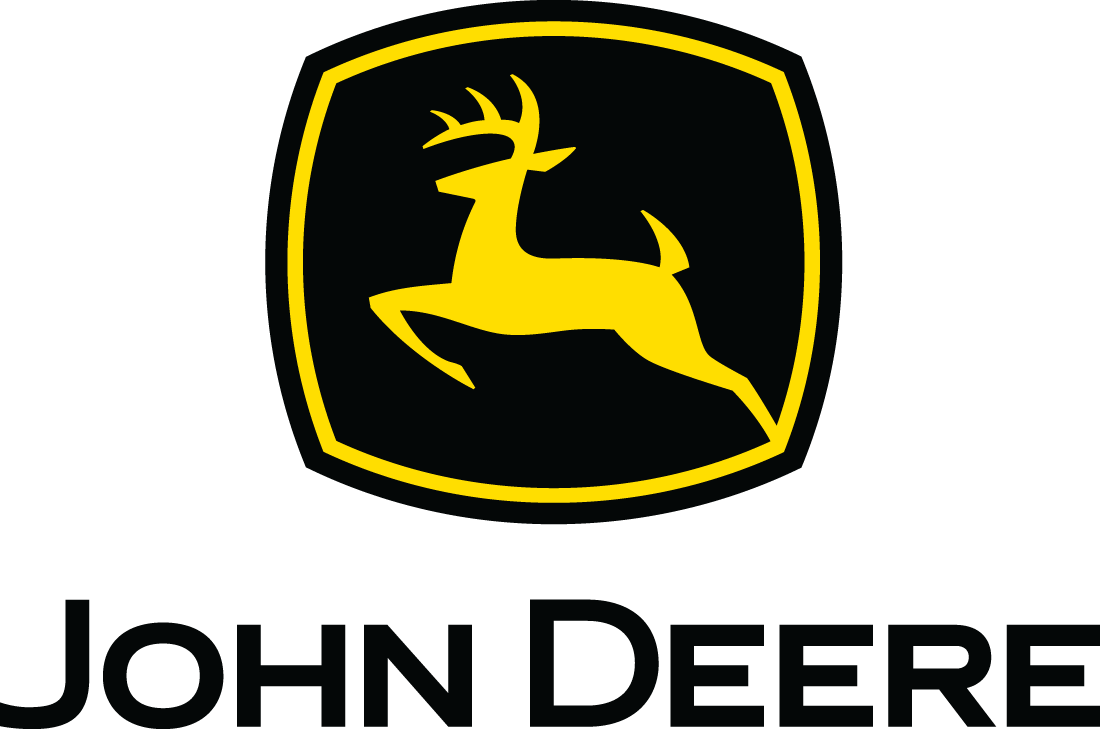
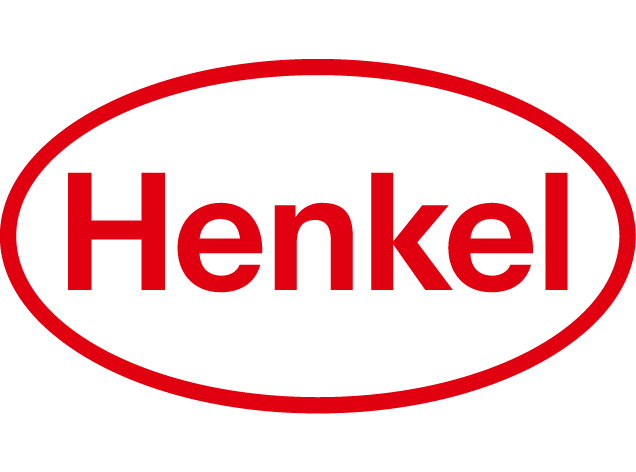
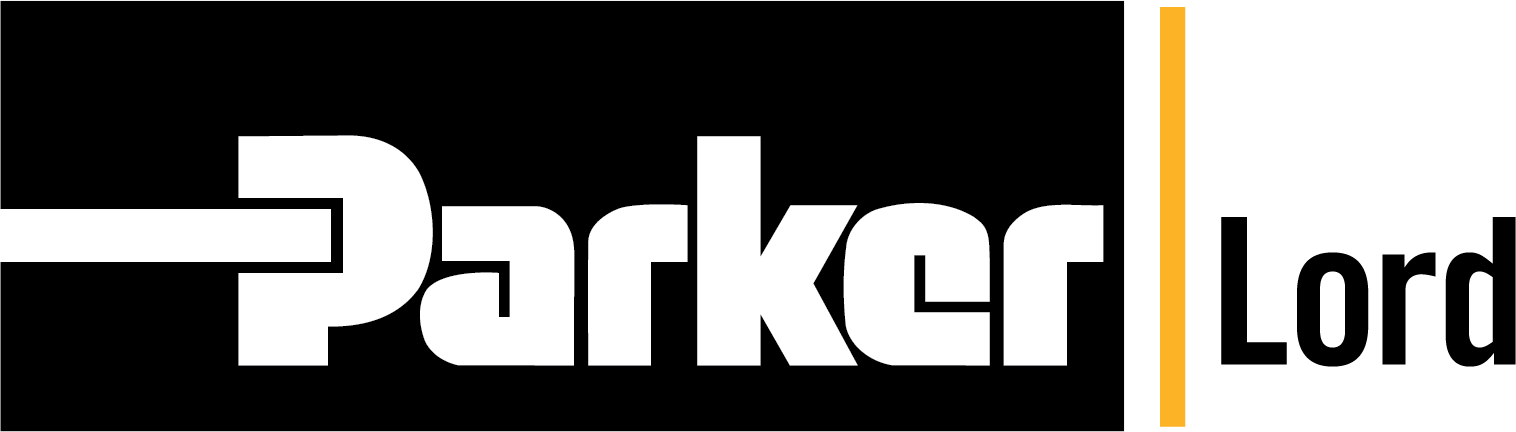
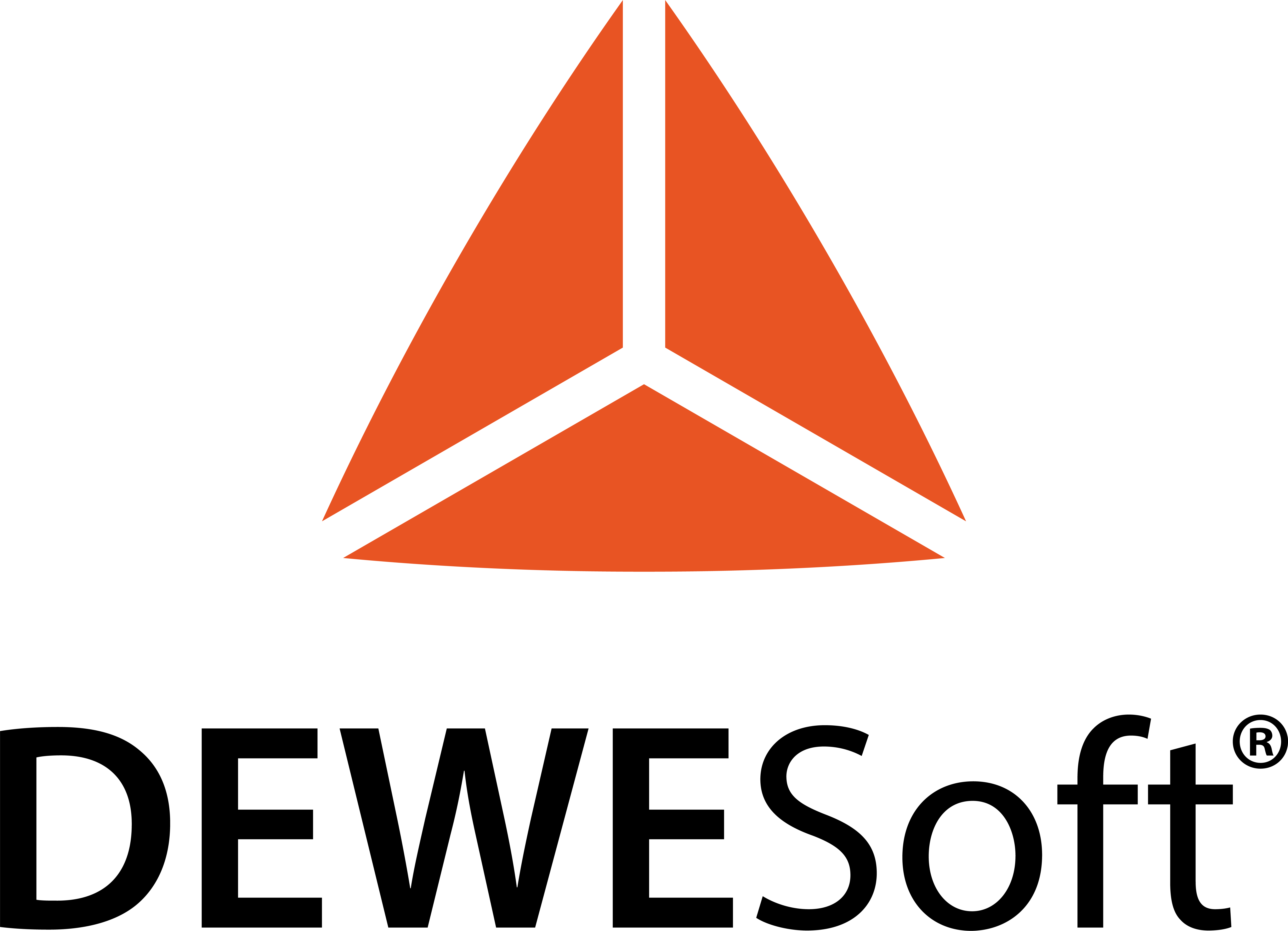
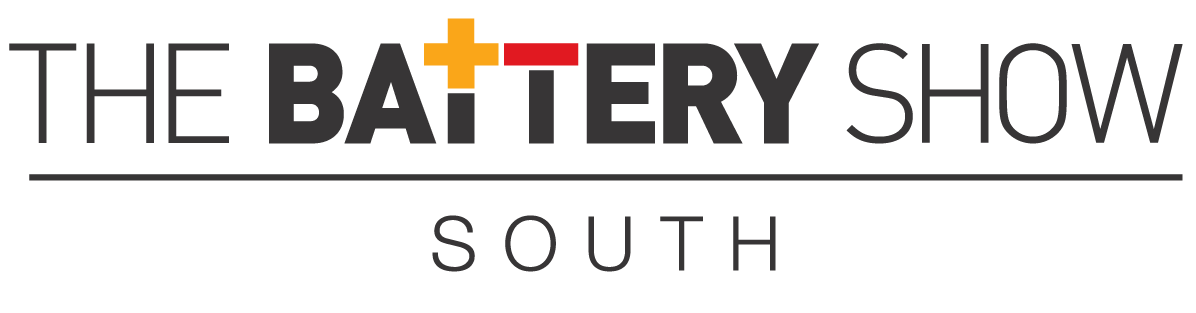
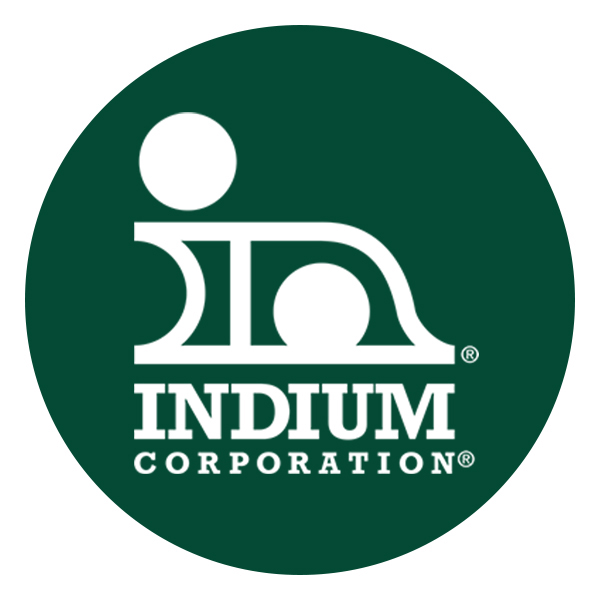

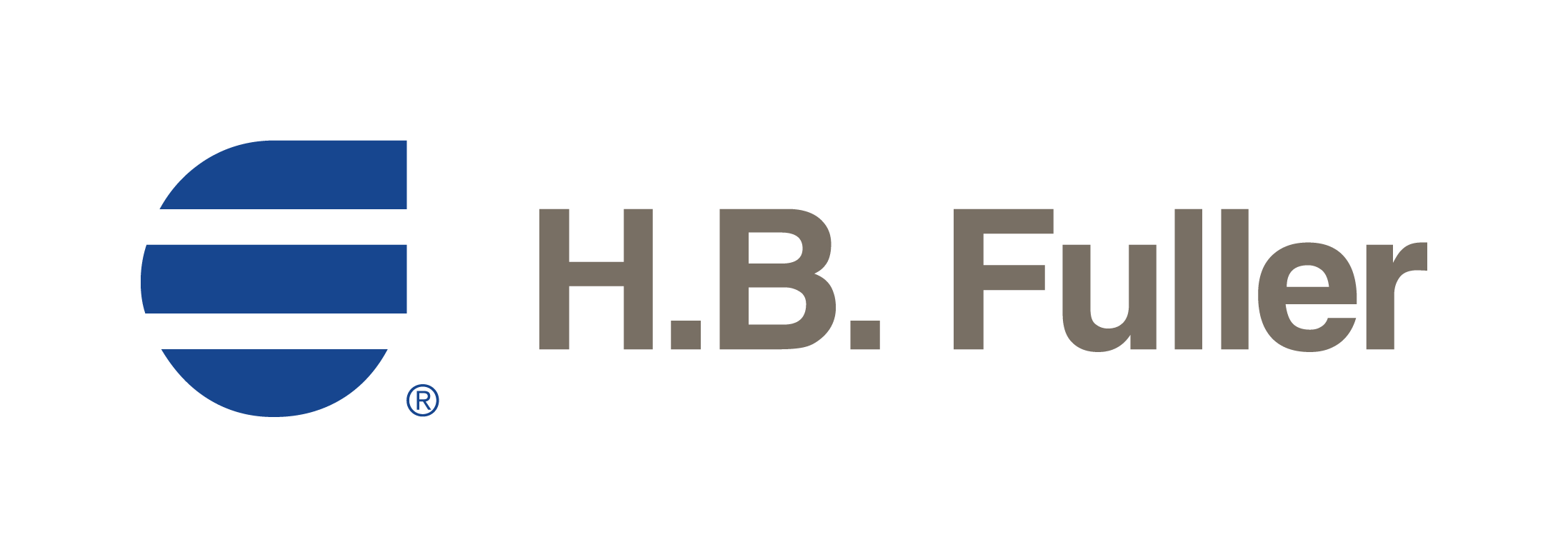
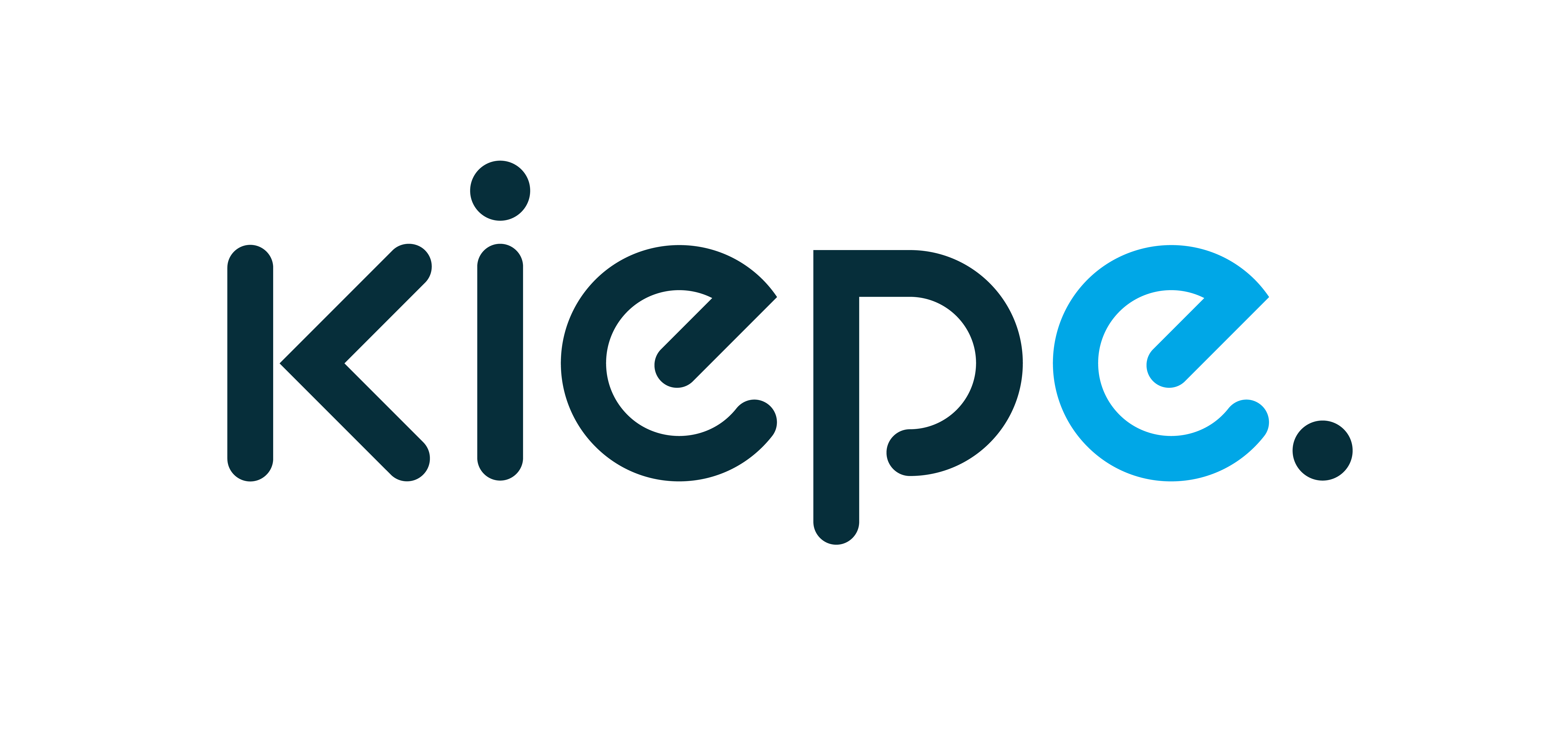
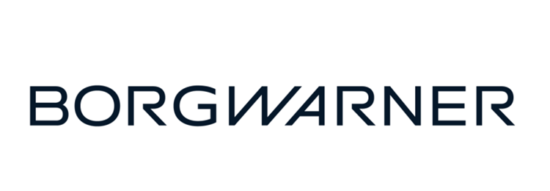