Battery safety
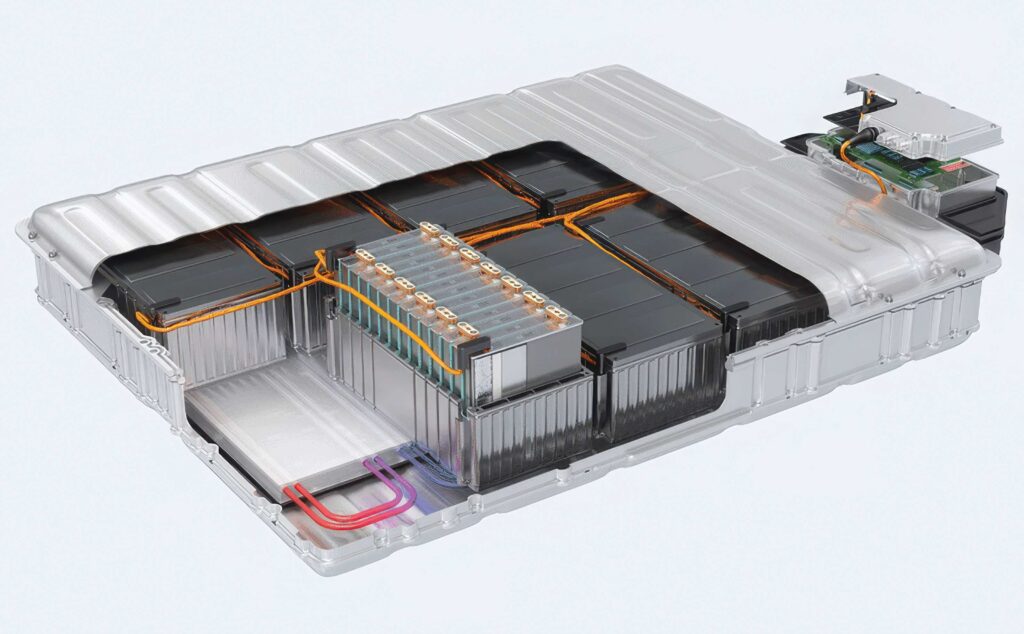
(Image courtesy of Henkel)
Material gains
Nick Flaherty reports on the various materials making batteries safer.
A new generation of materials is changing the way battery systems for e-mobility are designed. Pack architectures differ depending on the form factor of the cells, with various materials used for cylindrical cells compared with prismatic cells. The space available in the platform also drives the specification of materials, whether for cars, offroad construction equipment or electric aircraft.
There are broader requirements emerging for the choice of materials, such as ease of integration into the assembly process, which has to be balanced with the ease of dismantling packs for repair, and then the reuse of the pack for second-use applications followed by its eventual recycling.
The principal aim of the materials in the pack is to provide structural support and prevent thermal runaway. There is an increasing requirement to do this with one material that is thermally conductive at low temperatures, and thermally and electrically insulating at higher temperatures to save costs in both the pack and the assembly process.
This need for thermal conductivity at lower temperatures helps to even out the temperature in the pack and avoid hotspots that can damage a cell. If a cell overheats during operation or during charging, it can become damaged and will then reduce the overall performance of a module. A material that has good thermal conductivity can disperse the excess heat further out into the module and even into the rest of the pack, depending on the architecture, to avoid the risk of thermal runaway.
In 2022, 55% of new electric cars sold used prismatic battery cells, with pouch cells accounting for 24% and the rest using cylindrical. Each of these cell formats has different needs in terms of inter-cell materials, which has led to trends in fire-protection material adoption. For example, cylindrical systems have largely used encapsulating foams, whereas prismatic systems typically use materials in sheet format such as mica.
The choice of materials is also dependent on cell chemistry. Lithium ion cells with nickel, manganese and cobalt (NMC) are more prone to overheating than lithium iron phosphate (LFP) cells. If the heat is not removed from an NMC cell, and the cell overheats in a thermal runaway situation, there is a significant risk that the lithium inside will catch fire. If this happens, the material in the pack needs to be thermally and electrically insulating. This is where ceramic materials such as mica come in. The higher temperature creates a phase change in the material that alters performance from conducting to insulating.
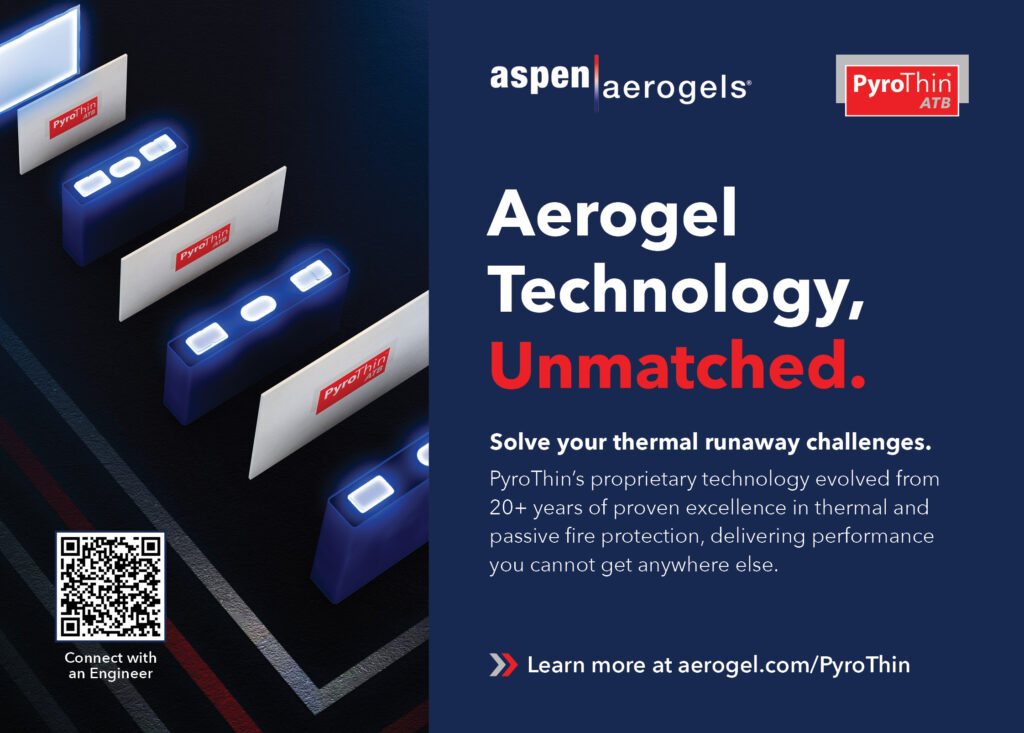
Electrical insulation is also important in the event of a thermal runaway. This can happen during a crash, which compromises the interconnect between the cells. This can lead to short circuits that can connect to the chassis of the vehicle, particularly with a cell-to-chassis pack design. This short circuit can potentially direct hundreds of amps through the chassis, which in the event of a crash would put the driver, passengers and emergency workers at an additional risk.
A ceramic coating on the busbar interconnect inside the pack can change phase in the event of a thermal runaway to prevent these short circuit events and keep people safe. This is already used in applications such as elevators, where silicone rubbers coat the elevator cable and ceramify under heat to protect the lift car and its occupants.
There are existing safety standards for elevators to keep operating and the typical time for a battery pack would be about 30 minutes. However, these can be challenging to apply during assembly, with more time required for applications and curing.
New formulations of materials such as ceramics and aerogels can also lead to new pack architectures, particularly for NMC cells. LFP cells have a lower energy density and are much less prone to thermal runaway, and they also have less oxygen available.
Customising materials can help to improve the efficiency of immersion cooling, where a dielectric liquid flows around the cells in a pack. This can provide more effective thermal management, carrying away the heat from the cells.
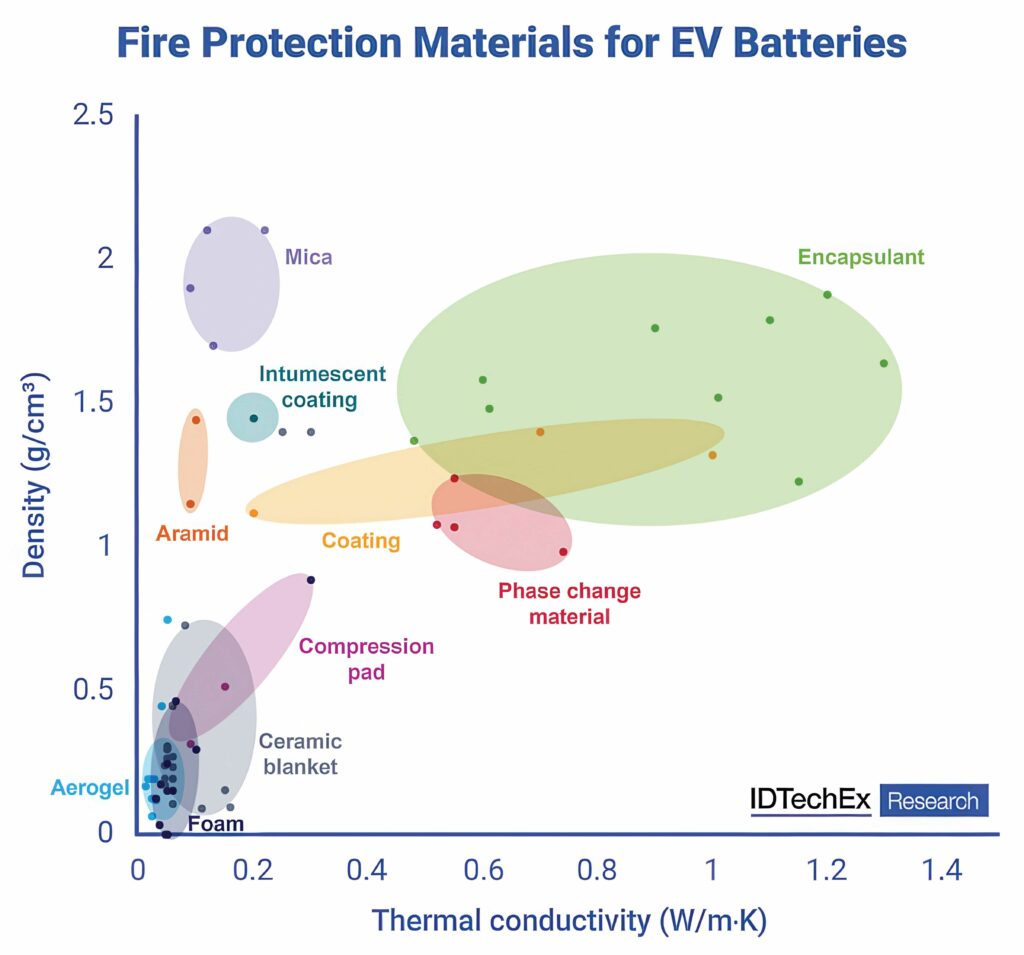
(Image courtesy of TechX)
Venting
If a thermal runaway occurs and a NMC cell catches fire, one of the consequences is that it can eject hot materials up through the pack via the cell vent. Most prismatic cells have vents at the top of them alongside the terminals to ease assembly, but this is not ideal to prevent thermal propagation, and the change is not going to be achieved with the material chemistry but at the architectural level. That is seen as a significant change.
Materials such as aerogels can change the way the battery pack is designed, particularly for prismatic cells.
Aerogels are a diverse class of porous, solid materials that can exhibit a wide array of extreme material properties. They are known for their extremely
low density, ranging from 0.0011 to ~0.5 g cm3. The lowest density solid materials that have ever been produced are all aerogels, including a silica version only three times heavier than air. This can even be made lighter than air by evacuating it out of its pores.
However, aerogels usually have densities of 0.020 g cm3 or higher, about 15 times heavier than air. The pores are typically in the range of <1-100 nm in diameter and usually less than 20 nm.
With the right chemistry, aerogel sheets can provide the mechanical capability of a compression pad for thermal conductivity, but also provide a fire barrier in the event of thermal runaway in the same space and weight as a urethane foam. This can cut off the conductive pathway from one cell to the next, but it is not sufficient to prevent thermal runaway for a significant time.
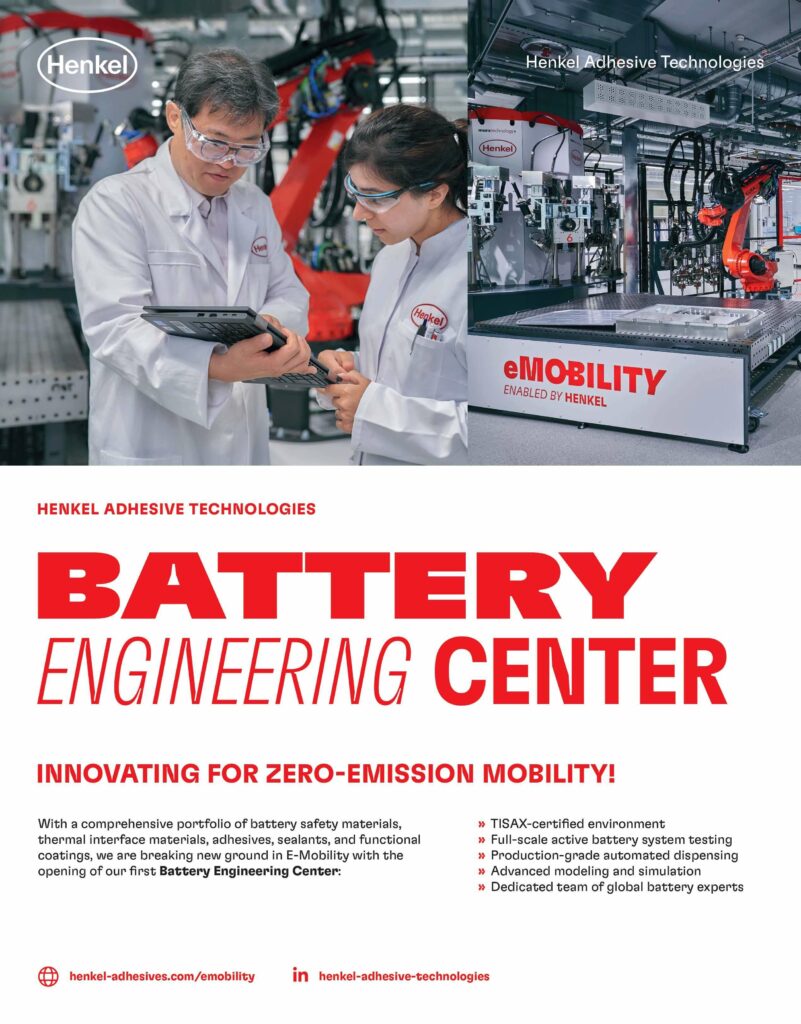
Because aerogels are a broad class of materials, this is driving development in many directions. Some aerogels can operate at temperatures of up to to 1400 C and cope with solid state. However, the mechanical design is key, managing the strain energy so that the material can retain its durability, but also enhance the performance of the cells at end of life, tune the cell protection to manage the end of life, and warranty performance.
The compliance of the material holding the cell influences degradation over the life of the pack, so it has to have sufficient room to swell a little without forcing the lithium dendrites that can form inside the cell to puncture the separator. Using a material that can accommodate the specific expansion of a cell will make it last longer.
These compression pads are typically 2-3 mm thick and the shape of expansion evolves over time. A pack density of 100 litres of cells requires about 5 litres of expansion space.
Pack design is evolving, from the original EV packs to those with retrofitted, non-propagating designs. Now, with second-generation packs, thermal propagation is considered much earlier in the design process, with mechanical engineers involved, and several car-makers are currently including aerogel sheets.
This has enabled cell-makers to change the design of the cell so the vent and the terminals are separated, and those functions are not on the same side of the cell. The latest generation of prismatic cells have the vent on one face and terminals on opposing sides, so the cells vent downwards to the road rather than up to the passengers.
Cylindrical cells typically have 5-10% the energy of a large prismatic cell and are surrounded by six neighbours, so the energy can be absorbed by other cells. This needs to dissipate the heat to buy time for passengers to evacuate the vehicle in the event of a thermal runaway.
For dissipation to work, the energy released by the cell has to be spread across 36 neighbouring cells so they do not trigger themselves, and that is considered almost impossible. However, in the case of thermal barriers, there are several ways in which the energy goes to the ground state.
The first is to cut off the cell-to-cell conduction pathway, which is regarded as a problem that has essentially been solved. The second is through the cooling plate, which can be active or inactive during thermal propagation, or through the bus as a third alternative pathway.
Then there is the management of the gas and ejecta from the cell. The gas management requires complex pipes to remove the high-temperature materials. For thermal runaway with NMC cells, the temperature can reach 1000 C, which is beyond the reach of plastics, as they cannot be primary structural elements. This opens up the use of ceramics such as mica, as well as steel.
In the teardown of packs, the thermal barriers are the same size as the cells, and they are extending down the sides and top to engage with the surrounding structure. That might not create a hermetic enclosure around each cell, but the designs are moving in that direction.
With the vent on top of the cell, the design of the pack has to start with the plumbing. The more integrated this becomes with the vehicle, the more the cells have to accommodate the latter’s structure. The structural rails for a chassis resemble plumbing, so there is room for elements with conveying ejecta off the vehicle, which opens up a lot of room for enhanced design of the packaging of the cell to chassis designs.
Design options for the cooling plate on the bottom include a hole for a vent, as this is regarded as the most benign place to segregate the ejecta, leaving room for more development of the design.
The lightweight nature of the aerogels is also being applied to electric aircraft, optimising the pouch cells with compression pads to achieve a higher overall energy density for the pack, rather than having to use cylindrical or prismatic cells that have additional packaging that reduces energy density.
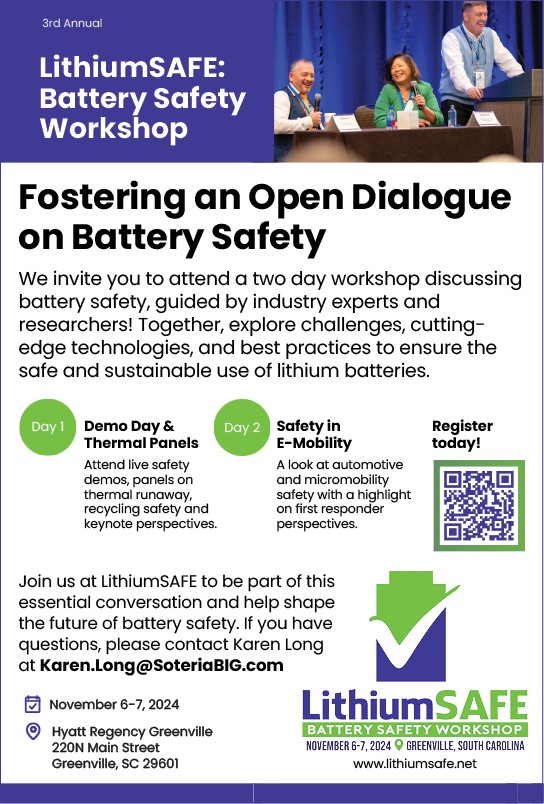
Whether at cell, module or pack level, the key is for a multifunctional material to reduce cost, space and weight. This means a multifunctional material has to be an electrical insulator with good thermal conductivity and fire-protection coatings.
The challenge is to translate the new designs and requirements into the materials. The benefit is that this is not limited to any particular chemistry.
For example, the dielectric coating around the cell can be cylindrical or prismatic. This coating is typically a blue foil, but to avoid problems in the case of an accident, delamination and structural adhesives can be used with the foil to maintain structural integrity.
With cell-makers moving to different form factors, such as long, prismatic blades, and from the 2170 cylindrical cells to the larger 46xx formats, such as 4680 and 4685, a significant number of different materials are being developed to provide an optimised design.
This is about having a combination of different materials, some for high-volume use such as plastics and composite materials from other parts of the vehicle, which can also be applied in non-critical areas. These can be combined with other materials with low-volume use that have a higher cost but provide safety functions in key places within the pack.
For example, the heat shields have to cope with peak temperatures of 1200-1400 C. Aluminium provides a light weight, and there is softening and melting, and these shapes can be coated with specific materials such as a two-part, retardant, toughened paste adhesive that is specifically designed for applications where a high degree of flame retardancy is required. It cures at room temperature and can be applied easily during manufacturing.
Another example is used for cooling tubes on the sidewalls of cells, side contacts and busbars. The heat transfer is mainly on the top and bottom, and that is where the focus is for battery safety. The aim is to reduce the use of steel and aluminium, but there is a challenge to buffer the energy, heat and particles coming out.
With LFP, there is not the large issue with particles, so it is easier to protect passengers, and with large LFP cells the challenge is more about the cell-to-chassis design.
For blade packs, specialist adhesives are used to glue a cell to the module or the cell to the chassis. This is a two-part adhesive with some structural capability, which starts as a silicone material dispensed for high density that can then ceramify under temperature, and provide compression and breathability. As it hardens it reduces the thermal conductivity.
There is also a design element, as one location in the pack may need a material that meets a high temperature and time requirement, but that isn’t needed everywhere in the pack.
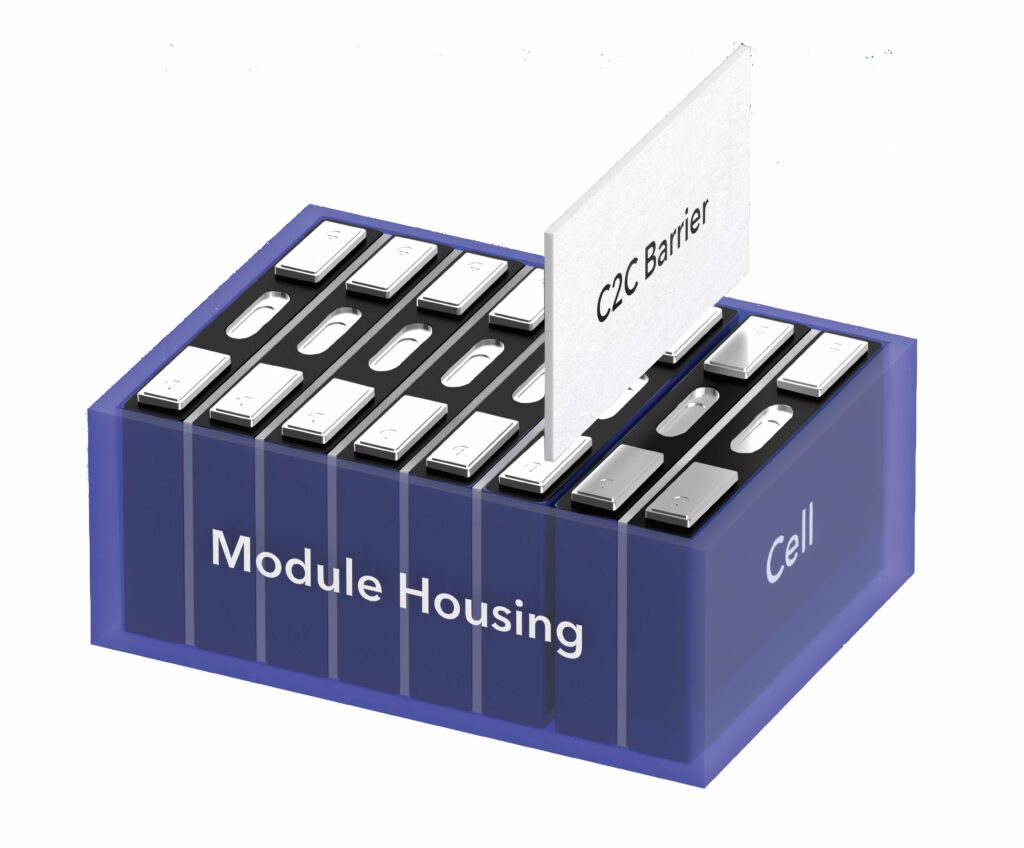
(Image courtesy of Aspen Aerogel)
Applying the materials
For many materials the application techniques are becoming more important. Flat streaming is a key approach, with spray coating that doesn’t need masking, and there is no aerosol, so there is no need for a spray chamber to prevent further contamination and just a curtain can be used.
Pressure-sensitive adhesive (PSA) tapes can be used in a wide range of EV battery use cases, including cell-to-cell bonding, compression pads, cell wrapping, electrical insulation, thermal runaway protection and more.
EV battery adhesives and tapes build on multiple pressure-sensitive technologies, and they focus on diminishing flammability, enhancing electrical insulation and safeguarding packaging components.
Pressure-sensitive tapes ensure structural integrity, while foams backed with tape safeguard cells from impact and swelling. Mica and ceramic fibres help to meet strict thermal runaway prevention standards. Dielectric tapes support flexible busbars in battery assemblies, while adhesive tapes with dielectric films provide vital electrical insulation for sensitive components.
The EV domain offers huge prospects for those involved in converting and working with high-performance PSAs. Batteries require the use of transformed, pressure-sensitive substances that improve efficiency, safety and ease of assembly.
Innovations in pressure-sensitive tape help address industry challenges and can be used in specific EV battery applications.
As EV battery adhesives necessitate specific criteria and standards, they are tested in an ISO 17025-certified lab, assessing traditional PSA properties and exposure to environmental conditions. The acrylic and silicone adhesives have flame-retardant features, complying with UL 94 V-0 and related requirements. Both tape and composite levels undergo flame performance and dielectric strength evaluations. Dielectric materials and adhesives are examined for breakdown voltage and dielectric strength, employing GB/T 1408.1-2016 and ASTM D3755 testing methods.
High-performance acrylic (HPA) materials are designed for general automotive requirements, with good initial tack and low surface energy bonding, offering good temperature resistance and shear strength. These provide flame retardancy and can bond to silicone-based materials, while acrylic foam tapes can be designed for gap filling and bonding rigid components to each other.
Polyester film provides up to 6 kV/mil dielectric strength and flame-retardant properties that can be used to separate cylindrical or prismatic cells, while polyimide films have a higher 7 kV/mil dielectric strength along with flame-retardant properties and temperature resistance.
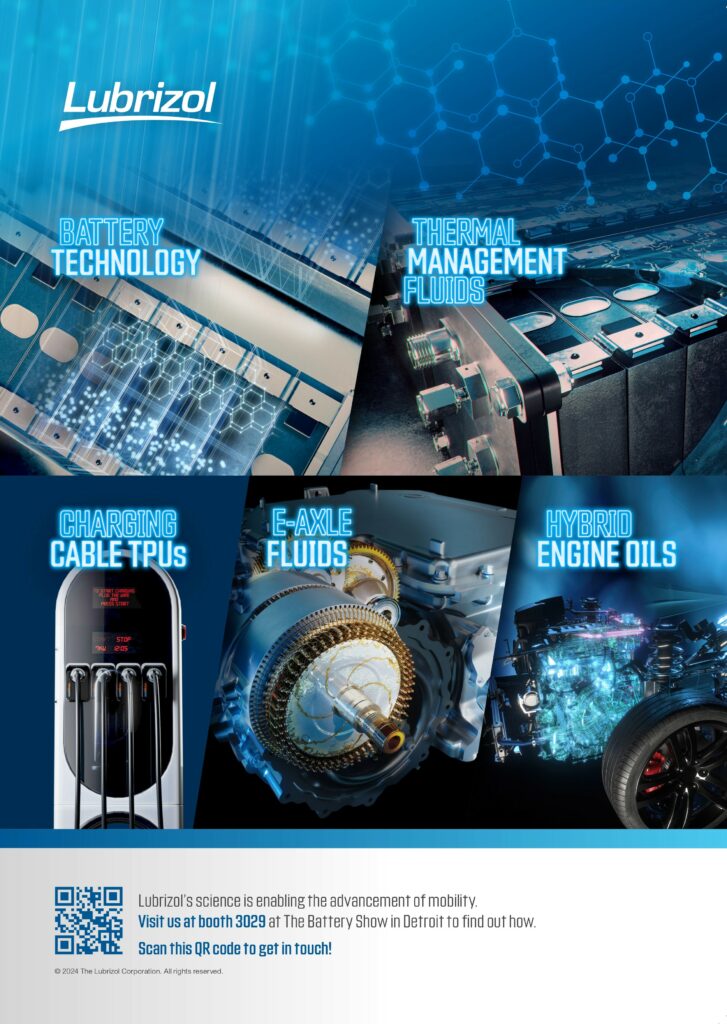
There is more focus on cost performance and safety in use.
The change in the way materials are being used is a different way of working to the way OEMs and suppliers have worked in the last 50 years, based on purchasing and price pressure to drive down the cost of generally available materials. The material manufacturers are now looking to collaborate on designs where the materials are designed specifically for the battery cells being used.
For foam protection around cylindrical cells, the focus is on filling the space between the cells with a material that is as light and strong as possible, but with a short curing time, and this requires additional design considerations.
If one cell goes into thermal runaway, the temperature rises, and initially the need is to prevent thermal propagation, insulating to keep the cells cool, and then venting the hot gases and ejecta; then there is the need to direct the hot gas away from the other cells. So, there are multiple engineering challenges for the cell-to-chassis architectures.
The space between the cells at the narrowest dimension is 1-2 mm and foaming is not the only solution as there are other ways to create porosity. The rhealogy, the deformation of the materials, can be more manageable while reducing the density. Extremely tough materials can be made with reduced density in polyurethane, taking out the strength to meet the weight requirement. This is achieved by tuning the structure of the polymers, which are based around a backbone molecule, with the additional molecules tuned to a specific weight and strength, along with the curing time.
Viscosity and mechanical strength differ slightly for the materials used for the various cell form factors, 4680 vs 18,600 vs 2650, and those for the foam can be tuned to meet the curing requirements for serial production. Different OEMs also want different materials; for example, for the structural requirements they want lighter materials with lower structural performance, perhaps reducing weight in one area and using a stronger potting material instead.
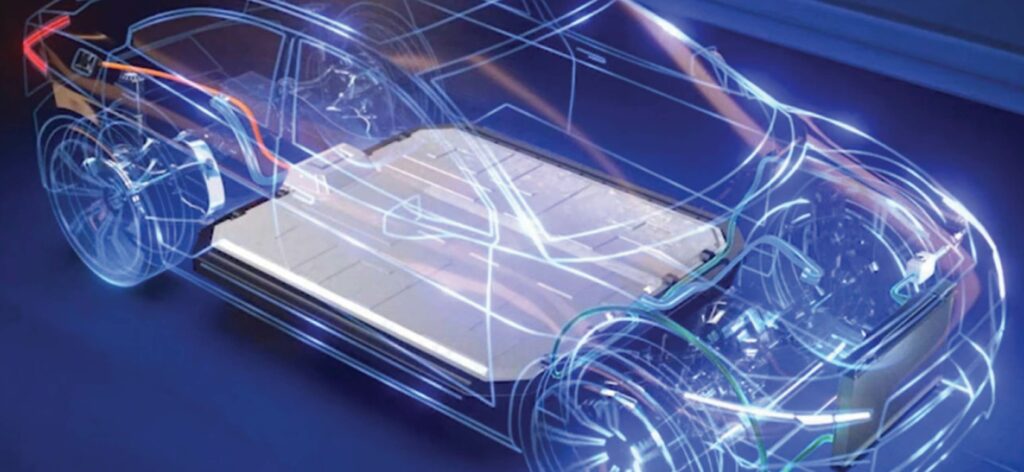
(Image courtesy of Castrol)
Recycling battery packs
One of the issues that has been raised with cell-to-chassis architectures with the cells encased in foam is the difficulty of repairing and recycling the packs at the end of their life.
It is possible to dissolve polyurethane foam, as shown by a project in France, collecting mattresses that are shredded and the foam chemically digested. This is added to virgin polyole, so that it can be reused.
However, the question for recycling is how this is part of the whole lifecycle of the pack. There is an expectation that vehicle battery packs are repurposed for 10-20 years for grid storage, but there are also recycling startups that shred them, and separate and produce a back mass that contains a mixture of all the materials inside (see EME Issue 23 on recycling).
The considerations for repair and disassembly have to consider the replacement of the modules. Aerogels can be expensive, and disassembly can restrict the compression ability and lifetime of the pack. However, silicone foams can provide similar levels of performance and support more reliable reassembly.
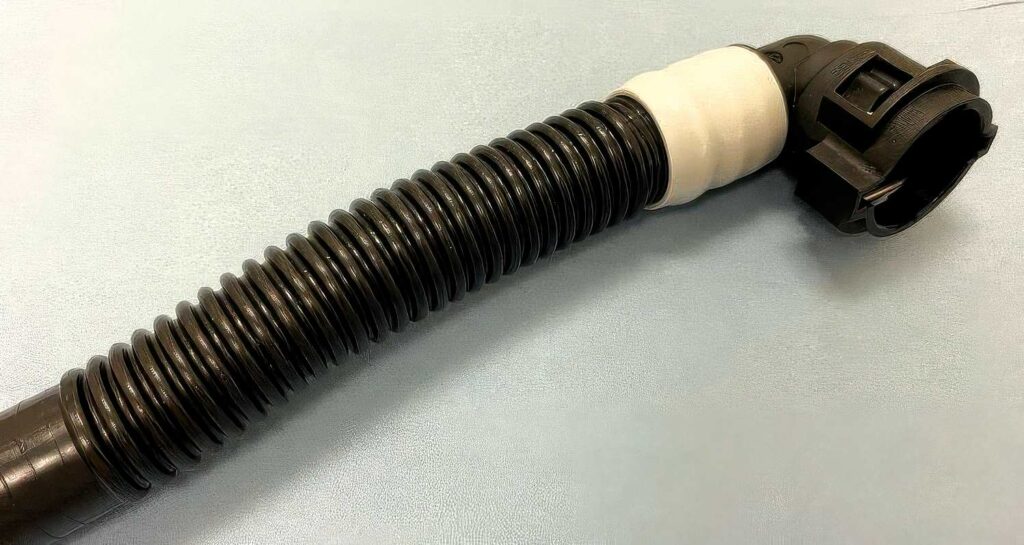
(Image courtesy of Dow Mobility)
Liquid materials
Solid materials are not the only consideration in a vehicle. Liquid dielectrics can boost the efficiency for liquid cooling systems. This dielectric can replace water glycol in carrying heat away from the cooling plate, but is more effective for immersion cooling of the battery pack. These materials can carry heat away from the pack, but need hoses, pumps and radiator units, which can increase weight and reduce overall energy density.
One of the issues is the material for the pipes.
Silicone rubber has several advantages, but is best known for its resistance to extreme temperatures. Silicone stays stable and keeps its physical properties up to 170 C, rather than the 110 C of the standard ethylene propylene diene monomer (EPDM) hose. However, the EPDM hoses are being redesigned with multilayer tubes with polypropylene inner liners and nylon, with a tie layer that binds them together.
One way to reduce the hit to the energy density for these immersion-cooled battery packs is to extend the cooling to the inverters and the motors across the power train. While this has been implemented in high-performance systems, the concern has been to replace the hydrofluoroether fluids that often have densities above 1.5 g/cm3. Designing synthetic esters can provide a density below that of water at 1 g/cm3 and tune the viscosity so that the liquid can flow easily between the cells.
Dielectric fluids also have a lower thermal conductivity and specific heat than water-glycol, which means a higher fluid flow rate may be required, which is why the pumps are needed.
Moving to an immersion system also changes the requirements on the pack materials, particularly for the seals, as there can be more of a risk of leaks from a less viscous liquid.
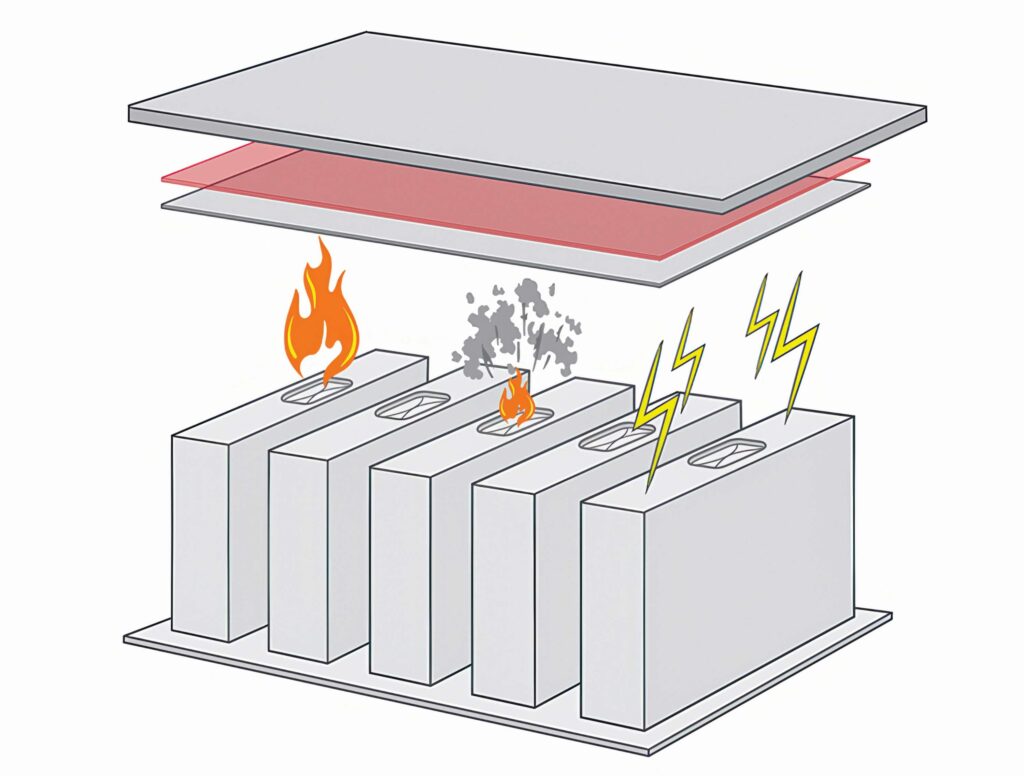
(Image courtesy of Avery Dennison)
Testing
Testing and forming the battery packs is also a key part of the challenge, both for assembly on the production line and for recycling. The latest systems can provide testing of packs with 300 A modules, which can be used in parallel to provide 2400 A for blade modules that could be the length of a vehicle or for high-power offroad systems.
New formation processes are being used on the production line with pulses of current put into each cell with a particular waveform, and this allows a different structure in the cell, which can reduce the risk of thermal runaway and extend the lifetime of the cell, and that has an impact on the design for repair and recycling.
These formation systems can require up to 40,000 channels to charge up the battery pack during the assembly of the vehicle.
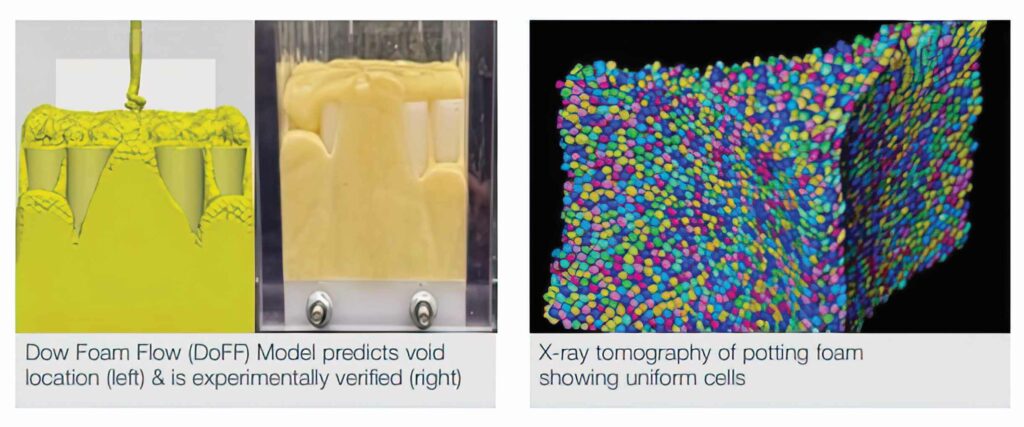
(Image courtesy of Dow Mobility)
Conclusion
The e-mobility industry is at the beginning of a decade of optimisation of pack design as designers are trying to make cost and engineering improvements, and boost overall safety. Material suppliers are working with designers earlier to reduce the weight and cost of a battery pack while still meeting safety standards.
This is driving architectural changes, and there will be more over the next ten years, with engineers pushing the boundaries of potting the cells.
Designers are looking more closely at the use of the right material with optimised weight, strength and thermal conductivity in the right place in the battery pack, and with an architecture that enables more efficient assembly.
These materials increasingly have multiple uses, replacing the need for separate materials for each function. This optimisation aims to reduce the weight and complexity of a battery pack, and while the individual materials may be more expensive, the overall cost can be reduced. Optimised potting, sealing and pressure tapes for assembly also help to cut costs.
Innovation in materials is also opening up the use of immersion cooling. The experience from the optimisation of the materials for the battery pack is being applied to the development of simplified immersion cooling systems with a new generation of seals to provide more efficient cooling that further extends the lifetime of the cells in the pack and allows for a lower-cost platform.
But there is a longer-term consideration for the materials in the recycling of the battery pack. A simpler disassembly process for prismatic or blade modules can add additional value in the second half of a pack’s lifetime in stationary storage, reducing the overall cost of the platform.
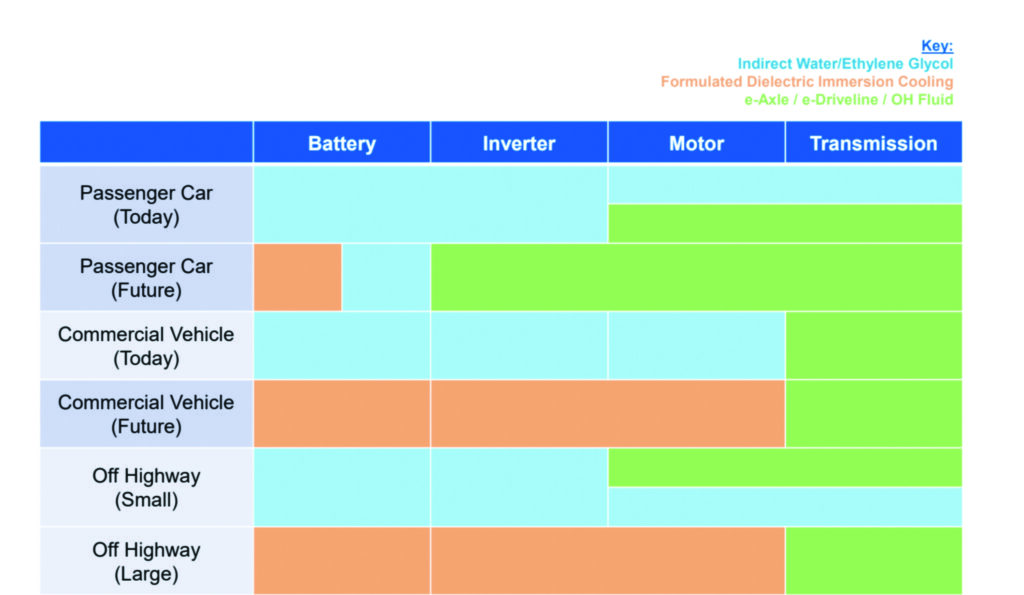
(Image courtesy of Lubrizol)
Acknowledgements
With thanks to John Williams at Aspen Aerogel, Kim Kreiskoether at Henkel, Gareth Brown and Binbin Guo
at Lubrizol, John McKeen at Dow Mobility and Don Wright at Unico for their assistance in the preparation of this article.
Some suppliers of battery safety
3M
Aspen Aerogel
Avery Dennison
Castrol
Dow Mobility
Henkel
Lubrizol
Sysenqo
SVT Global
Unico
–
+1 (508) 691 1111
+1 440 534 6000
+44 1932 775 644
+1 989 636 1000
+49 211 797-0
+1 440 943 4200
+1 609 860 4000
+49 410 540 900
+1 262-886-5678
ONLINE PARTNERS
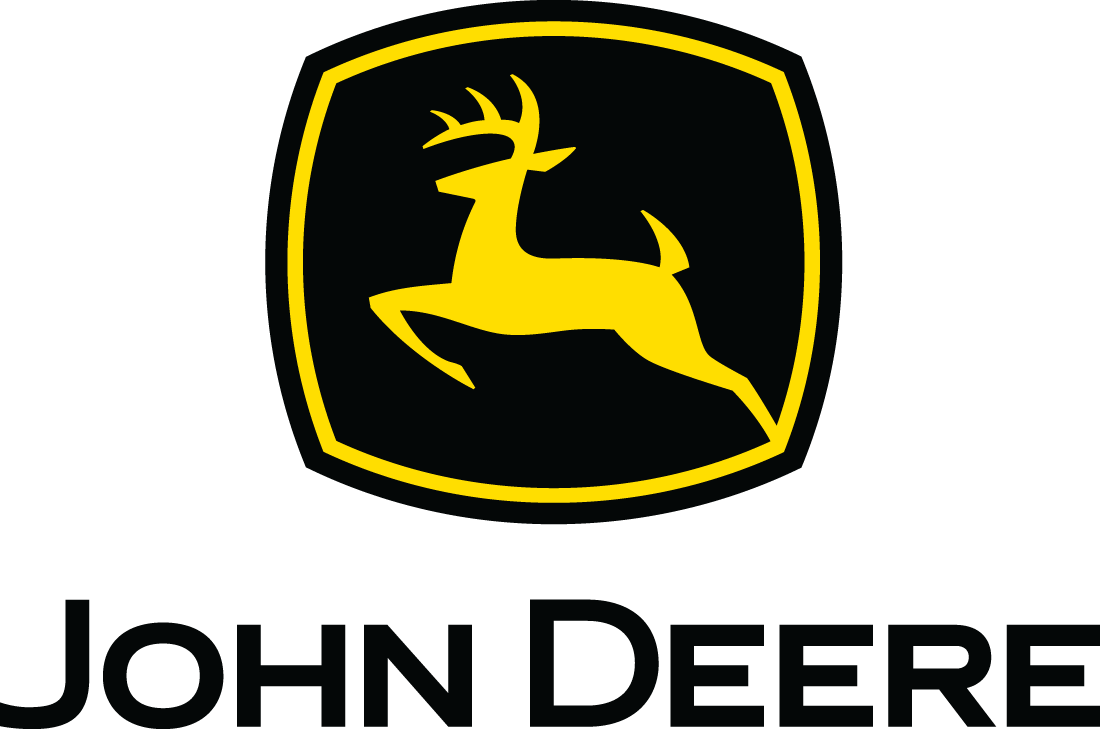
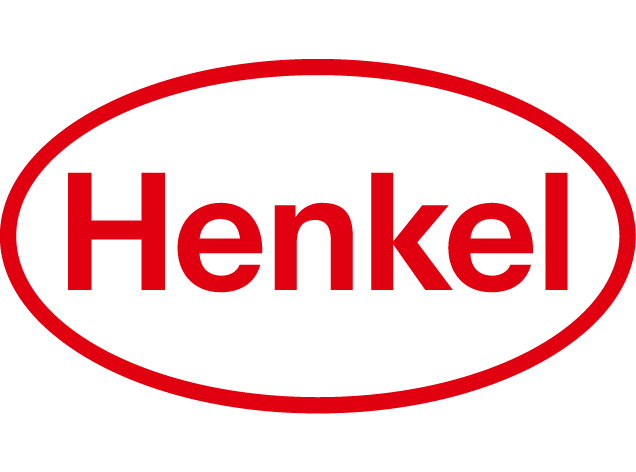
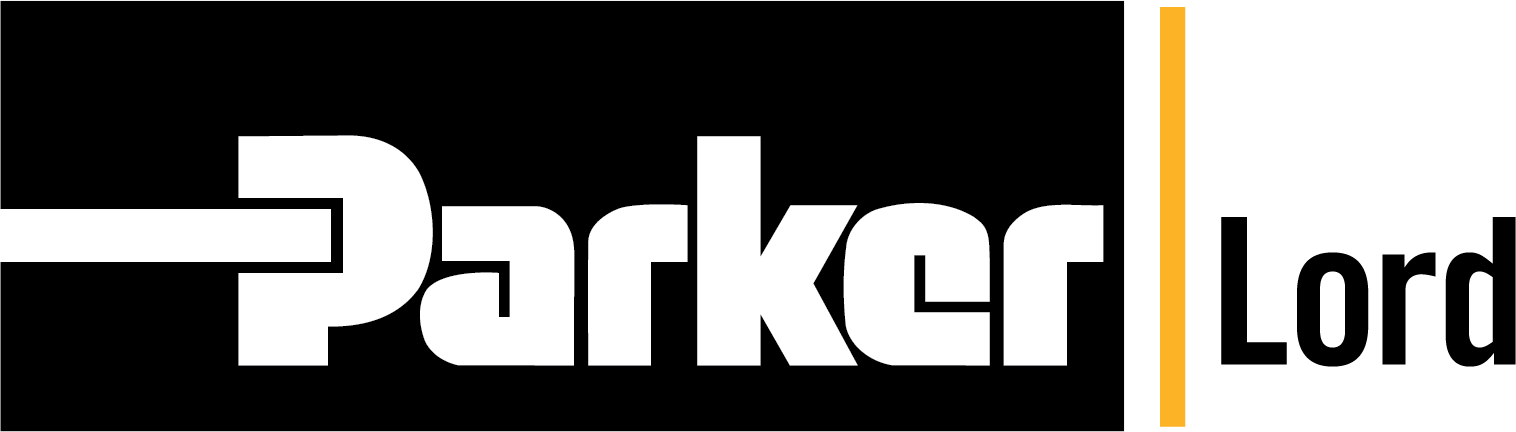
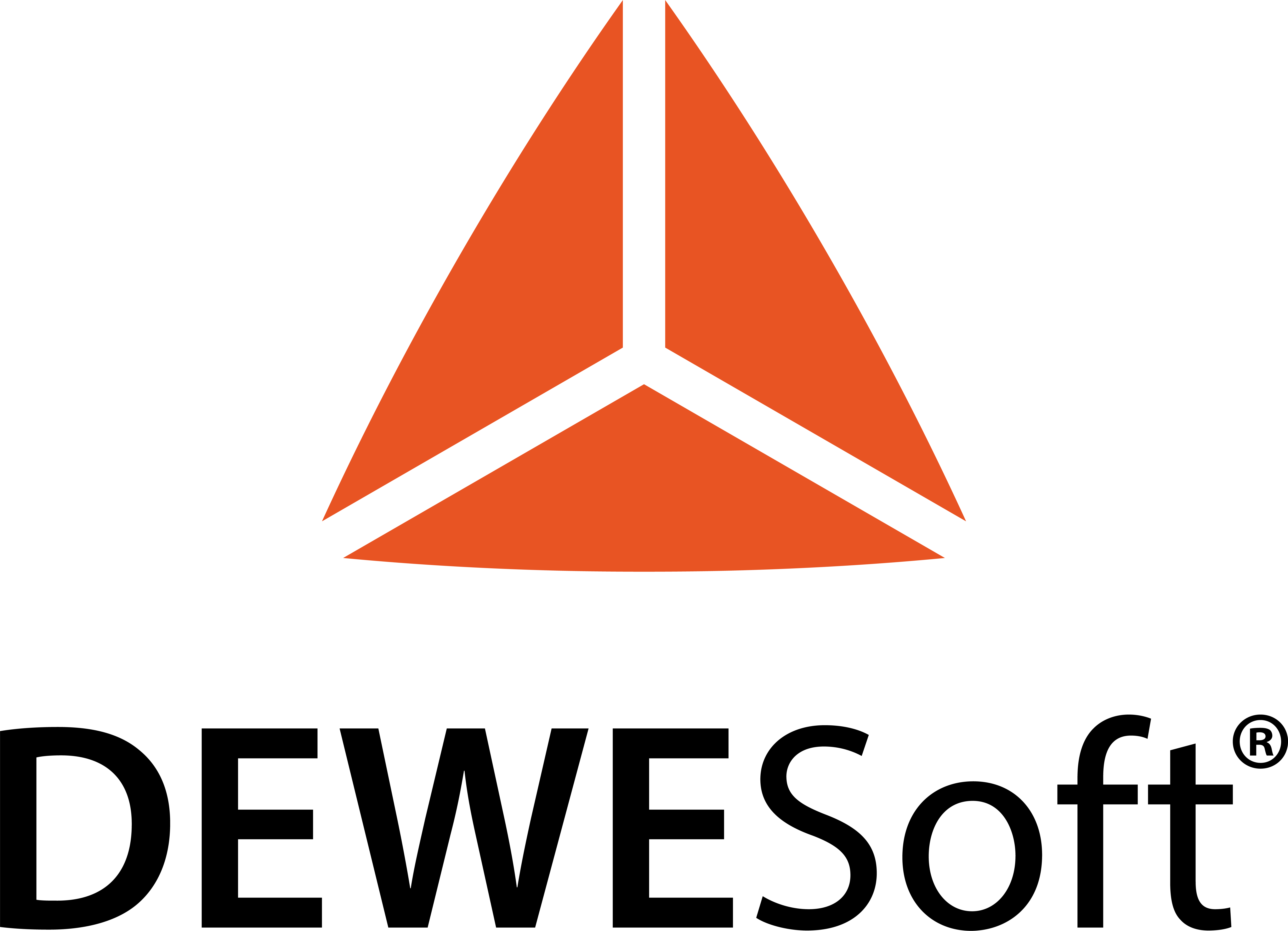
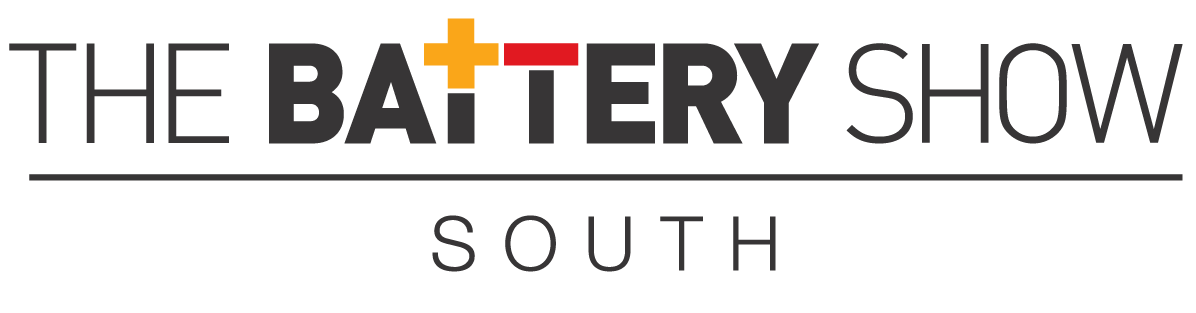
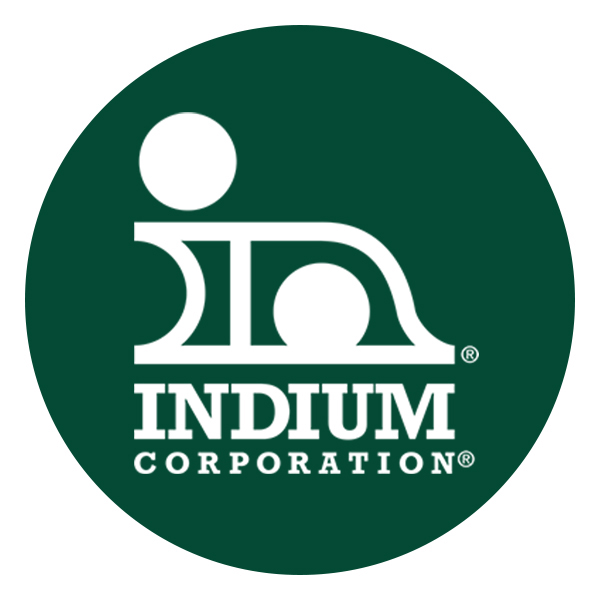

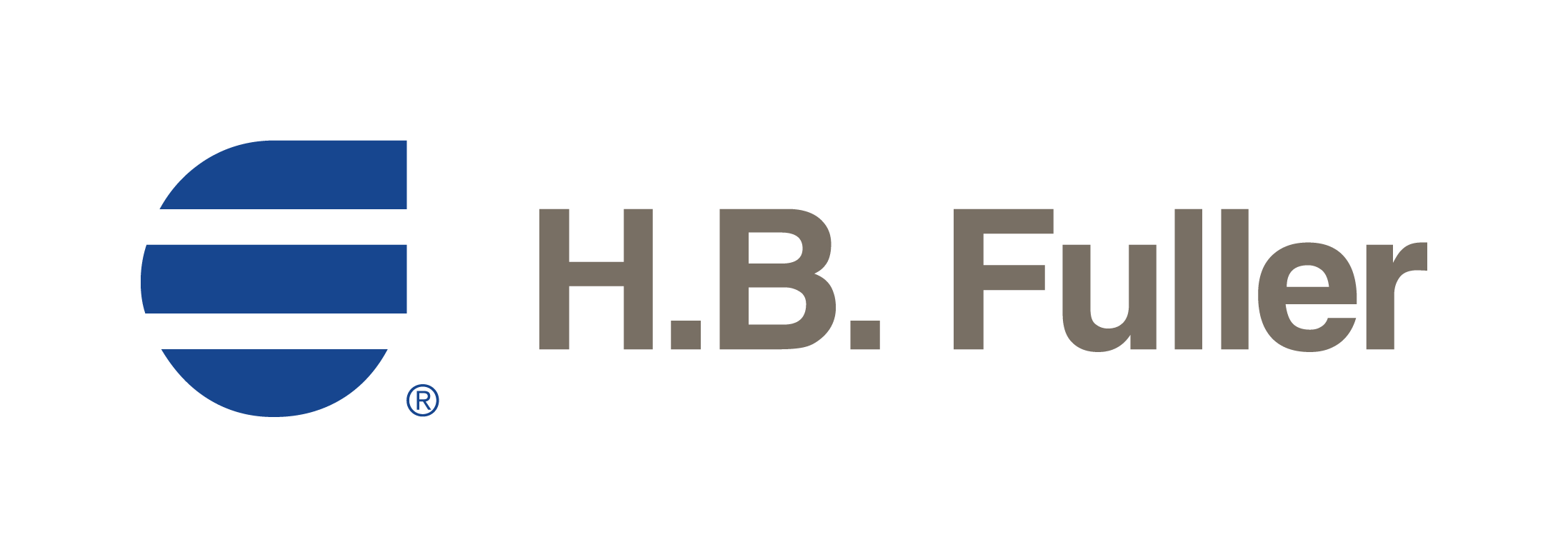
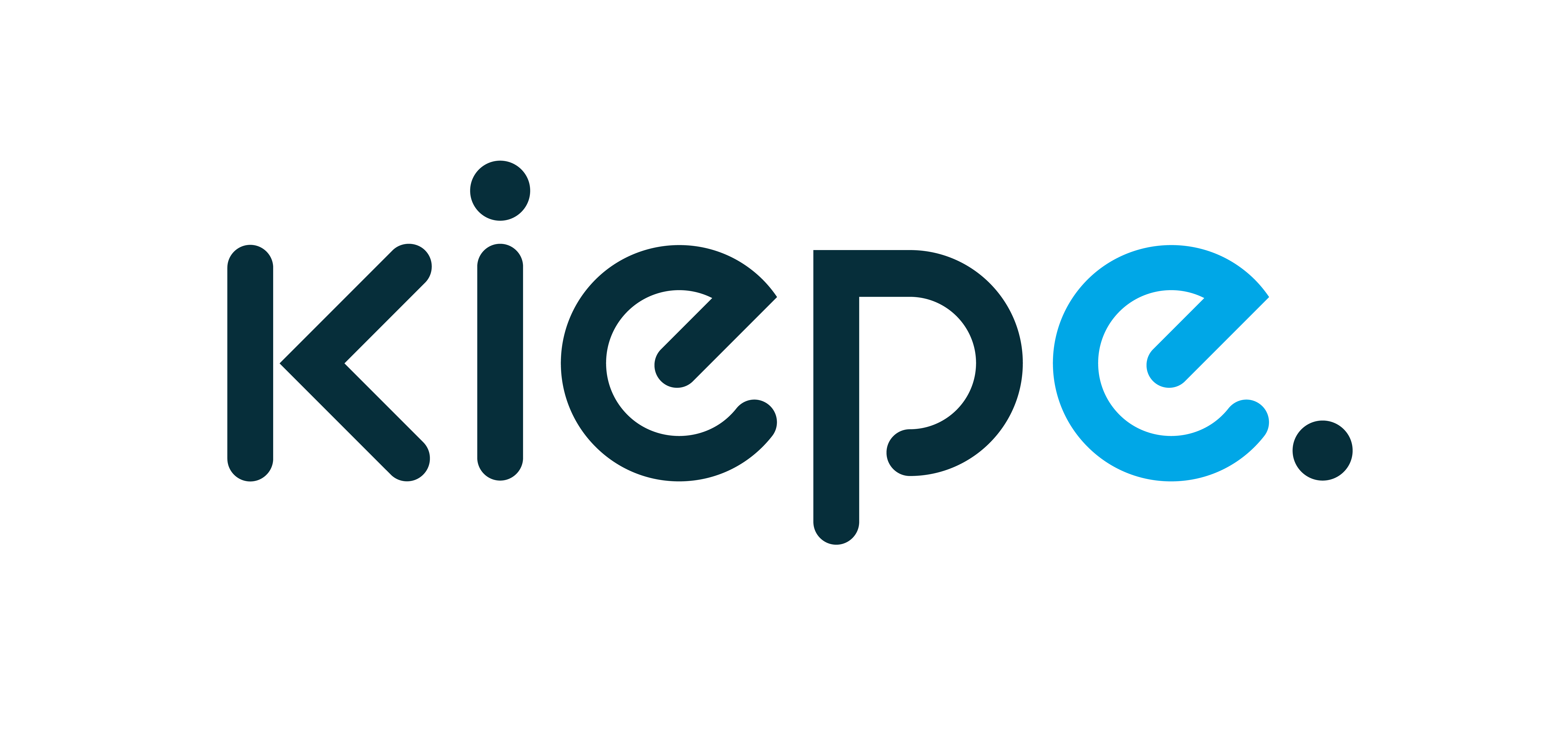
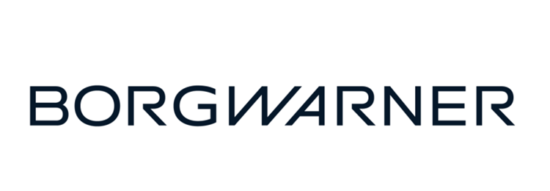