Lubrizol develops award-winning wire corrosion test
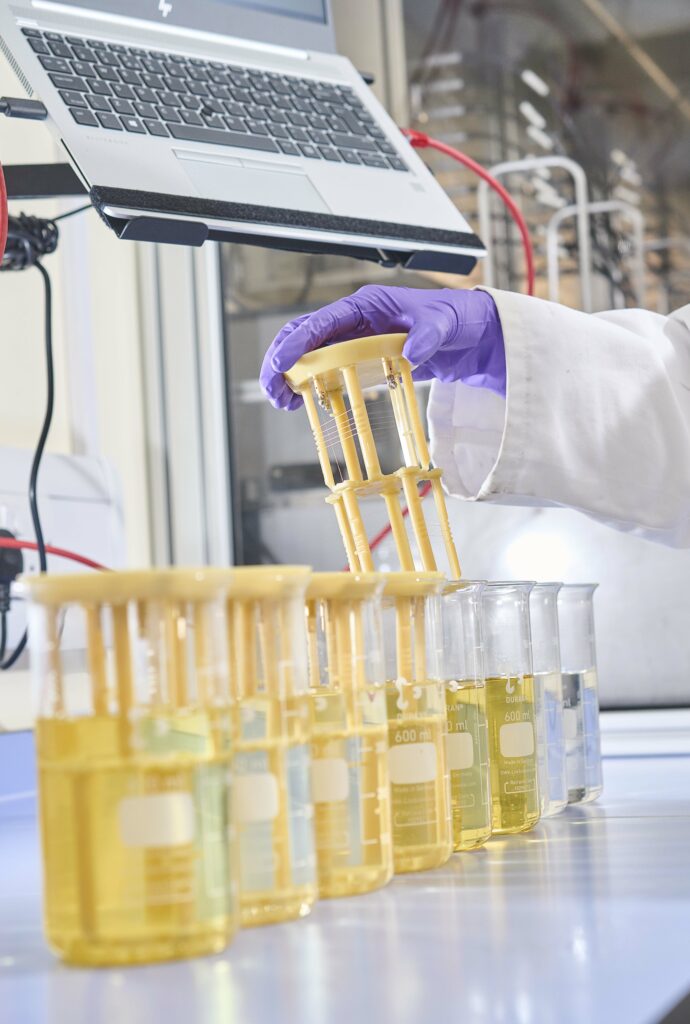
(Lubrizol image)
Electric vehicles contain large amounts of copper in their motor windings and connective elements such as busbars. These parts are increasingly exposed to fluids that act as coolants and/or lubricants, but can promote corrosion of the copper and cause failure. As the industry develops more closely integrated powertrains with motors, inverters and transmissions in tight proximity, and combines cooling and lubrication loops, better methods of gauging corrosion than the century-old ASTM D130 copper strip test are essential, writes Peter Donaldson.
Lubrizol, a specialty chemical leader, has developed a new wire-based test for which senior research chemist Gregory Hunt and technology manager Michael Gahagan recently won an award for outstanding research in mobility fuels and lubricants from the Society of Automotive Engineers (SAE).
The ASTM D130 strip test was developed in the 1920s to determine the amount of sulphur in petrol. The copper strip is immersed in the fluid under test and heated to a predetermined temperature for a set time, after which its colour is judged against those of a set of standard strips calibrated to different sulphur concentrations. The colour changes are brought about by chemical reactions, such as the formation of copper sulphides.
“This essentially morphed into the industry-standard corrosion test,” says Greg Hunt. “The problem is that it doesn’t really tell you much about what is going on corrosion-wise, because if a fluid goes a different colour there is no way to rate it. In addition, it tells you nothing about the rate of corrosion.
“At the start of the test, you will have a really nice-looking copper surface. If you have a fluid that is corrosive, as the copper corrodes and layers come off into the solution, you are left with a fresh surface that looks pristine, masking the corrosive a reality.”
Conversely, the D130 test can also make it appear that there is a major problem where none exists. “If it forms a film that’s the colour of one of the standard test strips and it adheres to the surface, that will look like significant corrosion,” Hunt says.
The limitations of the D130 test are causing problems for EVs in the field where fluids that have done well in the strip tests have failed in service due to corrosion. This corrosion might be caused by the fluid in its liquid phase, or in the vapour phase, of which the test provides no measure.
Lubrizol’s new test uses a wire about the thickness of a human hair, through which a small, electric current is passed. If the wire corrodes, the removal of material increases resistance in proportion to the amount of material lost. This provides a direct gauge of both the amount and rate of corrosion, which can be measured in real time. Furthermore, it is effective for both liquid and vapour phase corrosion.
Michael Gahagan notes that the wire test is much more objective and repeatable than the old D130 strip test.
“This colour test didn’t only depend on the colour itself, but also on what a person observed the colour to be. It was highly subjective. There were debates between laboratories as to what colour the strips were and trying to assess a degree of corrosion,” he says.
“The benefit of using the wire is that you get a numerical output, and that number will repeat. There is no longer any degree of debate.”
The wire test can also be applied to other metals such as aluminium, which is often used in busbars and can be used in motor windings to reduce weight.
Gahagan says the wire test has allowed the industry in general and Lubrizol in particular to develop a new generation of e-fluids that do not attack copper. These include oils that lubricate gears and cool windings, and fluids that provide immersion cooling for many electrical components.
This has been a challenge, he explains, because there can be conflicts between properties. For example, extreme pressure (EP) additives in oils to protect gears from wear can promote corrosion in copper.
“One OEM we worked with wanted a balance that still included some EP chemistry and gave us some targets to work to. We used the wire test to show them what the performance would be, and it was acceptable to them,” he adds.
The new test is now commercially available and it is going through the ASTM accreditation process.
Click here to read the latest issue of E-Mobility Engineering.
ONLINE PARTNERS
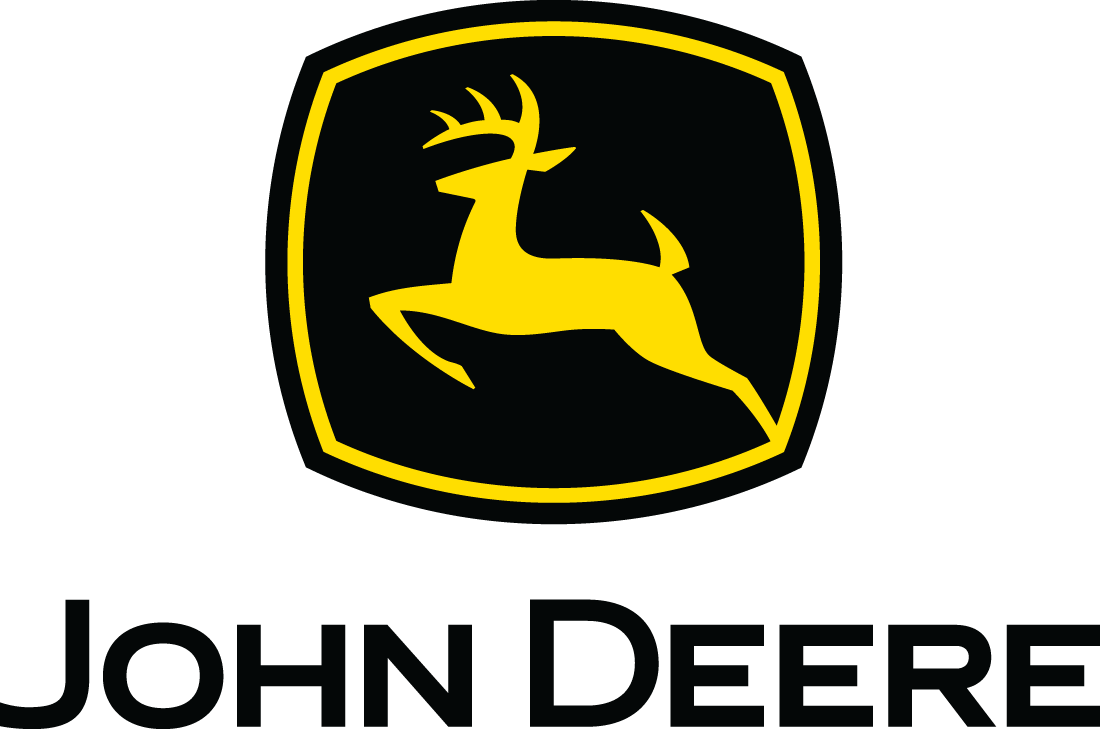
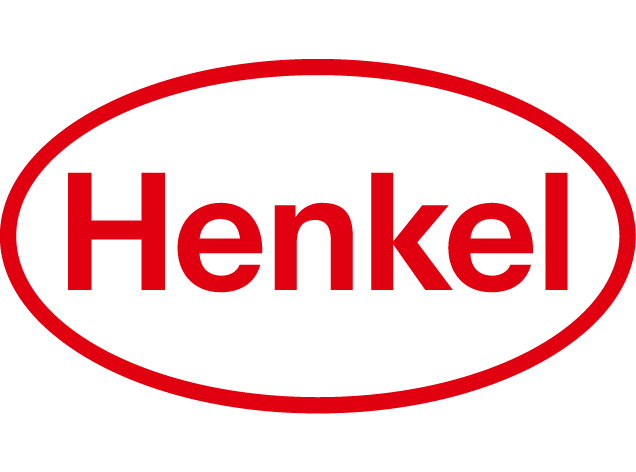
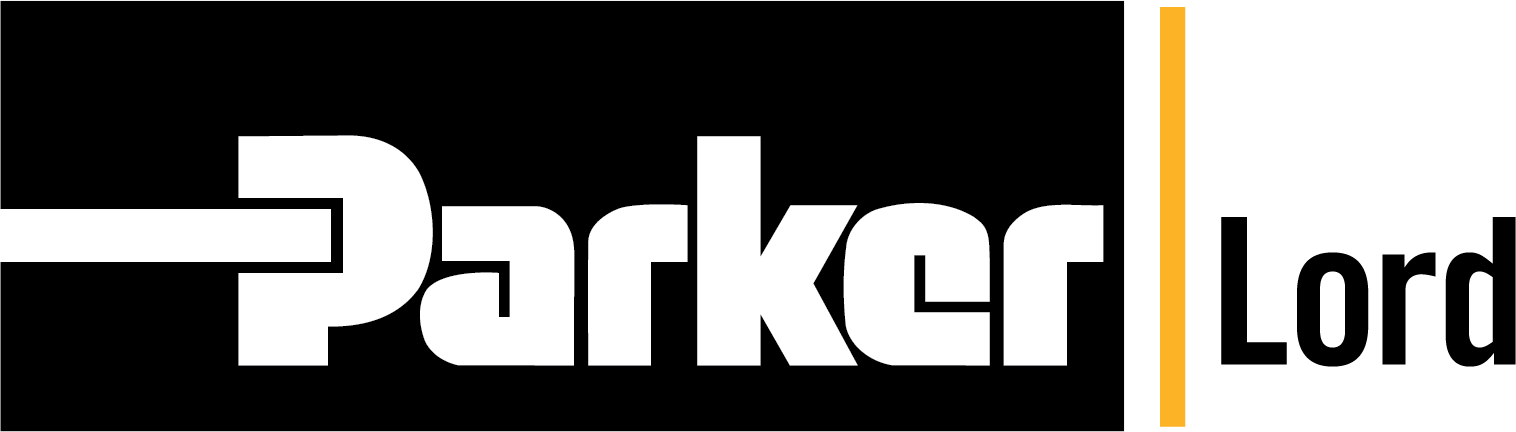
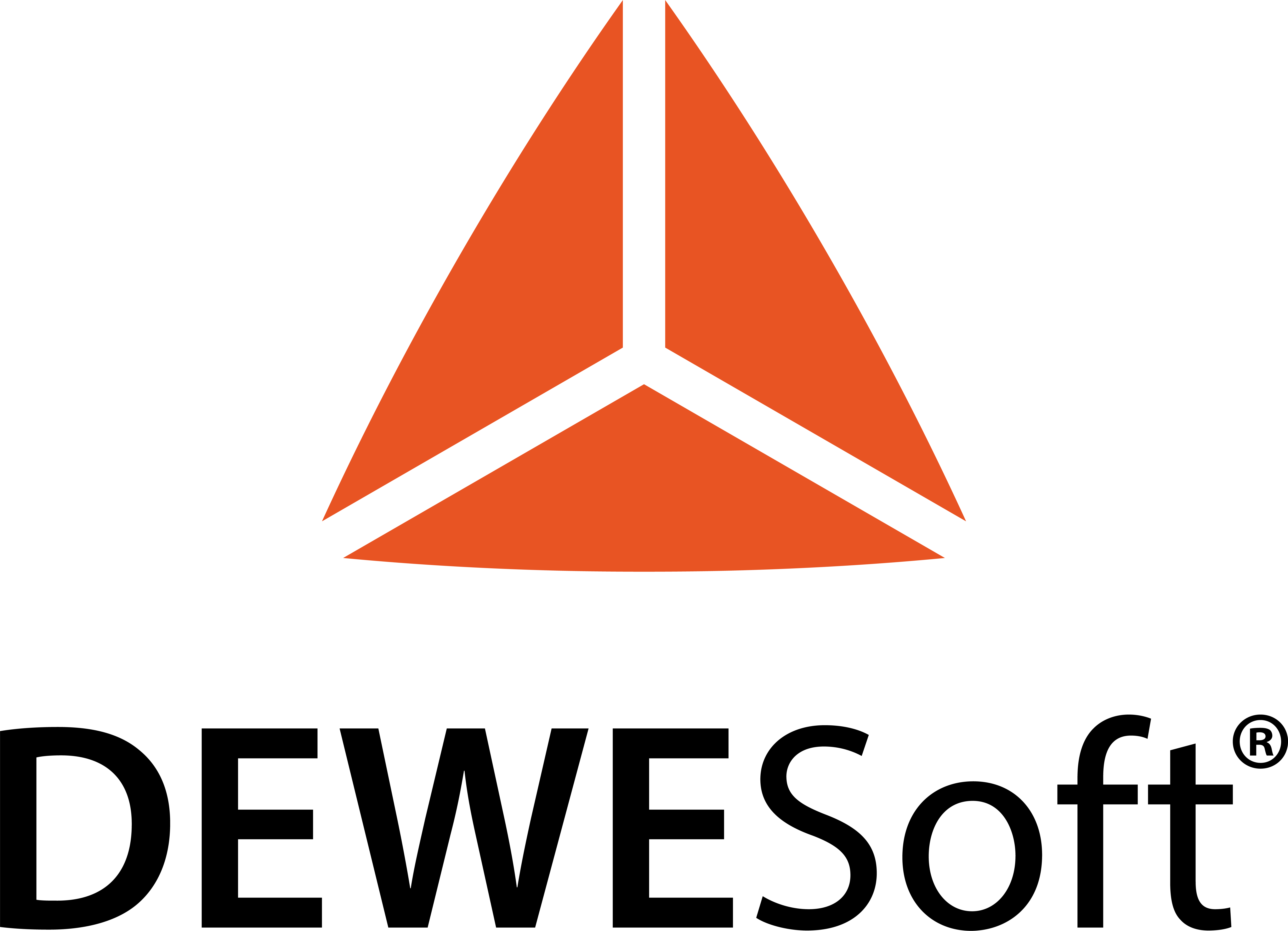
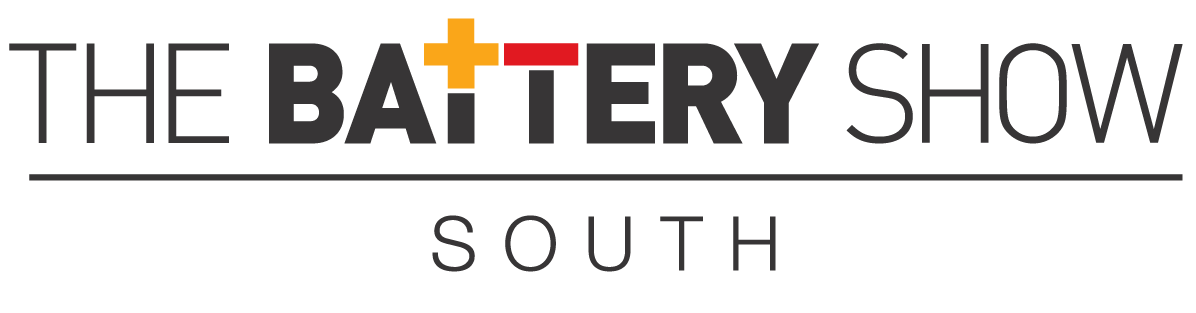
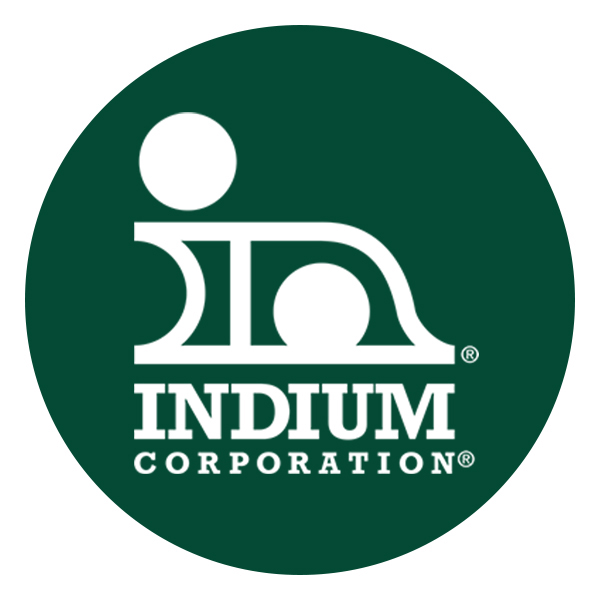
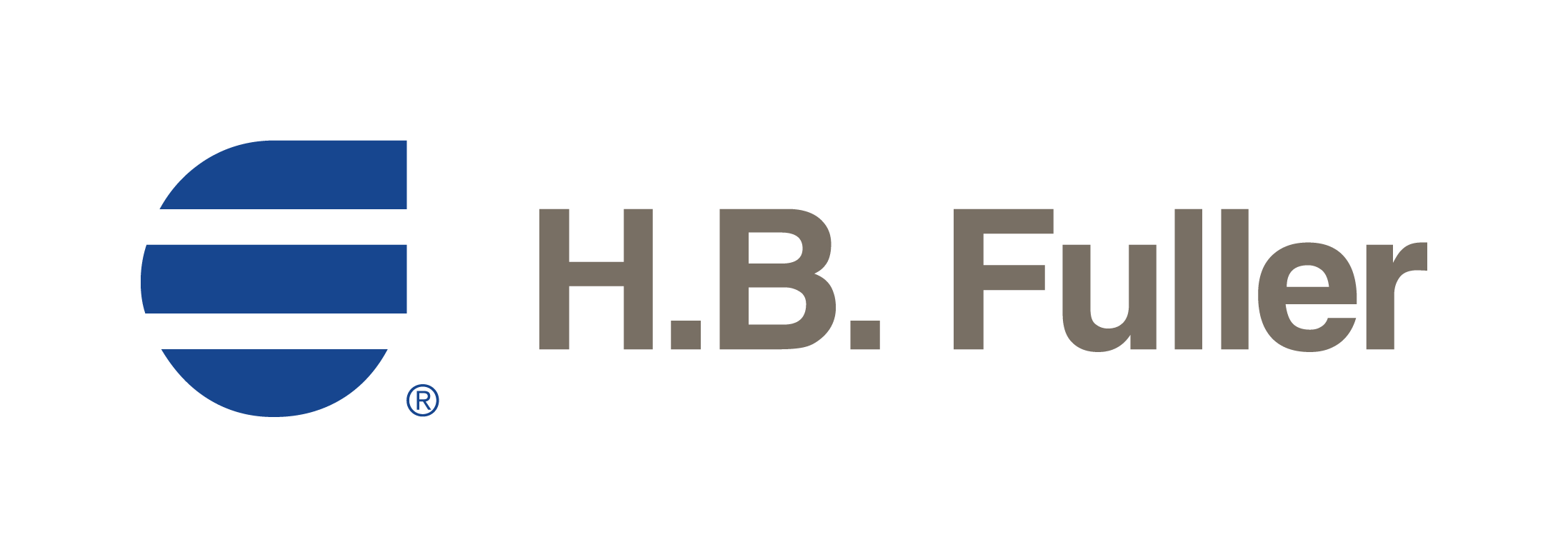