Why vacuum is vital in battery cell production
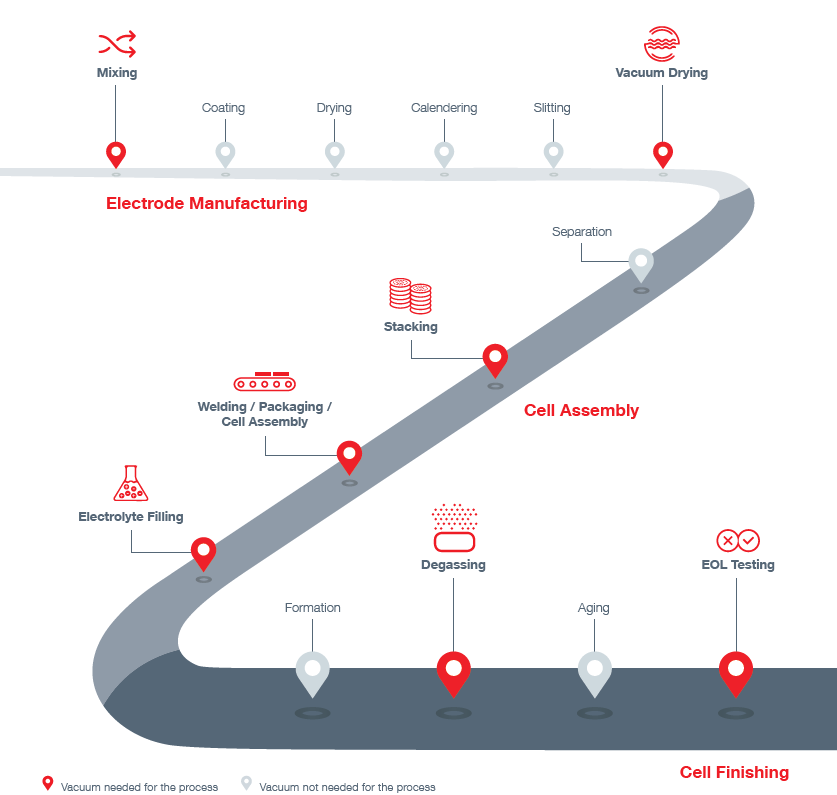
(Image courtesy of Leybold)
Vacuum processes play a crucial role in many stages of the battery cell production process, and category expert Leybold is pioneering new innovative, economical and sustainable manufacturing solutions that raise the bar in all areas.
Making the right pump choice for effective vacuum generation requires an understanding of how pumps affect the different processes, and vice versa. This can include vacuum level needs, pumping speeds, running costs and maintenance.
No two vacuum requirements are the same, and simulation programmes such as Leybold’s Pascal can be used to optimise the pumping system, leading to the selection of the right combination of pumps to achieve significant benefits across the entire process.
Norbert Palenstijn, product sales development manager at Leybold USA, says: “Choosing the wrong pump can be expensive and potentially damaging to your operation if the pump does not perform as required.
“This is where experience and using a vacuum simulation program like Pascal has added value to optimise the pumping system that ultimately leads to cost savings by shorting production times and increasing output.
“However, finding an optimum solution needs an experienced person knowing how to operate the tool. As such, the Leybold applications offer support to make the best selection for individual demands.”
As the diagram shows, the battery cell production process involves three key stages: electrode manufacturing, cell assembly and cell finishing. Each one has different vacuum requirements.
Mixing
To prevent gas inlets, and deliver homogeneity, viscosity and purity of the slurry, it is best to run this process under vacuum conditions. Equipping the mixer with a vacuum pump for degassing leads to a high-quality output.
Vacuum drying
After electrodes are rolled and slit into smaller bands, the coils are dried using heat under vacuum to remove humidity and solvent residue. A robust and reliable system is needed to withstand these elements, and a dry compressing pump avoids backstreaming of oil particles.
Stacking
Vacuum grippers, connected to a central vacuum system, are used to achieve the correct positioning of electrode sheets in this step, ensuring the anode, separator and cathode are stacked in a repeated cycle. This has a high impact on product quality.
Packaging/cell assembly
Before the cell stack can be inserted into the pouch housing, the pouch foil needs to be formed and this is best done via deep-drawing under vacuum – an efficient solution that leads to stable results.
Electrolyte filling
Battery cells are filled with electrolyte and sealed under a vacuum for even dispersion. It is crucial that the chosen pump can deliver working pressure of less than or equal to 0.01 millibar and withstand electrolyte traces, so dry compressing, oil-free pumps are a must.
Degassing
During formation, the pouch cell’s gas bag fills up, and it must be degassed and removed under vacuum. A clean and dry environment is essential to avoid backstreaming of contaminants. To maintain a humidity- and oil-free atmosphere, dry compressing pumps are required.
EOL testing
The absolute tightness of the final battery is essential for quality, longevity and safety, so a leak test is performed at the end of the line. For this step, helium leak detectors can be used to carry out a reliable and non-destructive test that will detect even very small leaks.
Different pumps are suitable for different tasks, and for the steps that do not require oil-free solutions, the most cost-effective solution is to use an oil-sealed vacuum pump. Leybold offers two: the SOGEVAC and the more production line-focused VACUBE.
The company’s dry compressing pumps offer ultimate purity as they are oil-emission free, and so they are able to avoid the potential risk of oil migration into the process chamber, saving time and cost, with minimised maintenance and an optimised service life.
This is where Leybold’s specialist experience is key and the company offers six solutions, including: the DRYVAC for drying, filling and degassing; the premium CLAWVAC for stacking and packing; and the dry screw VARODRY pump for mixing, degassing and filling.
The SCREWLINE pump offers ATEX versions, while the LEYVAC provides the highest purity for drying, filling and degassing. The RUVAC is focused on speed and performance at scale, delivering fast pump-down of larger drying chambers.
Finally, Leybold offers its expertise on instrumentation for the process in the form of the PHONEIX leak detector, which offers the highest accuracy for EOL testing, and a range of pressure gauges for every step of the process.
For more information:
https://www.linkedin.com/in/norbertpalenstijn/
Norbert.palenstijn@leybold.com
Click here to read the latest issue of E-Mobility Engineering.
ONLINE PARTNERS
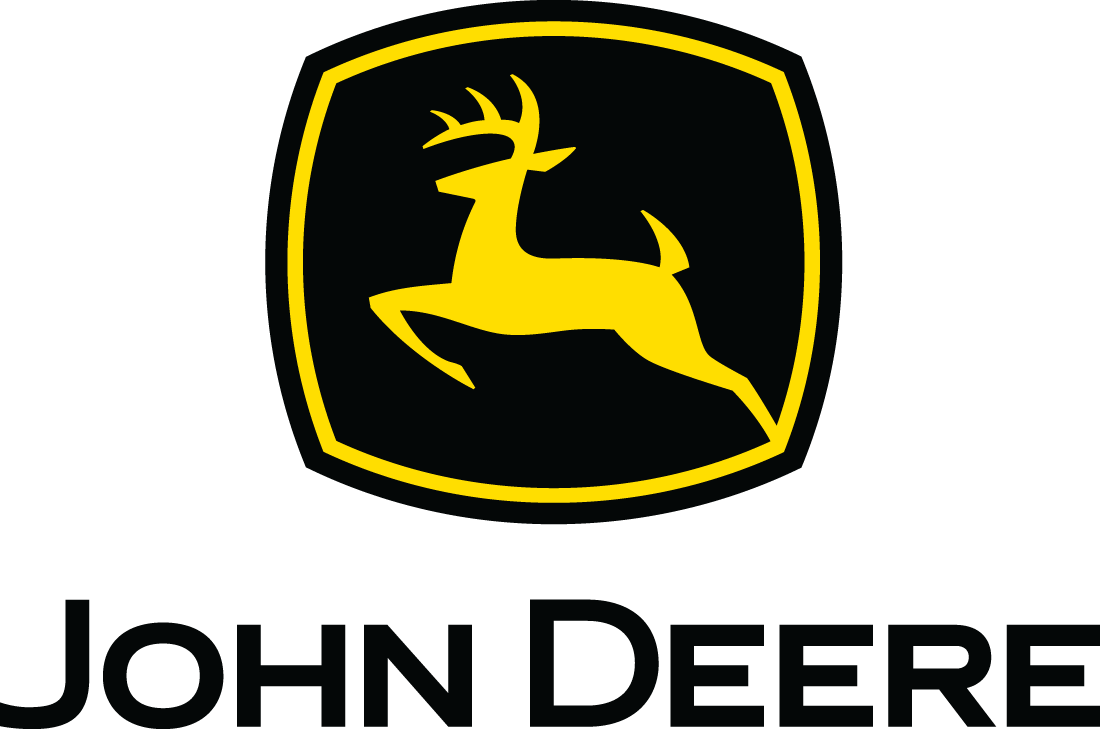
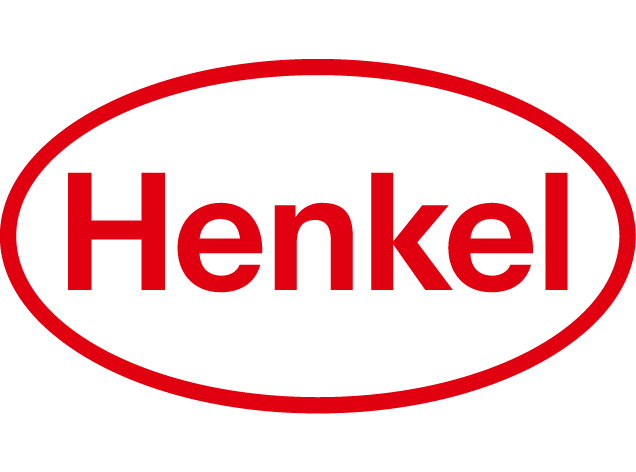
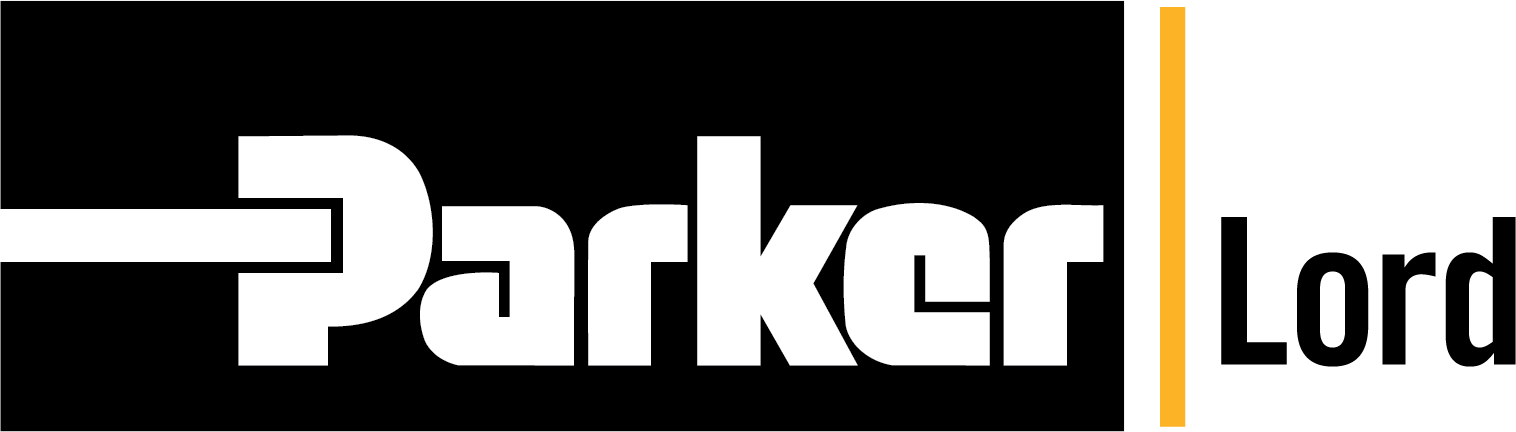
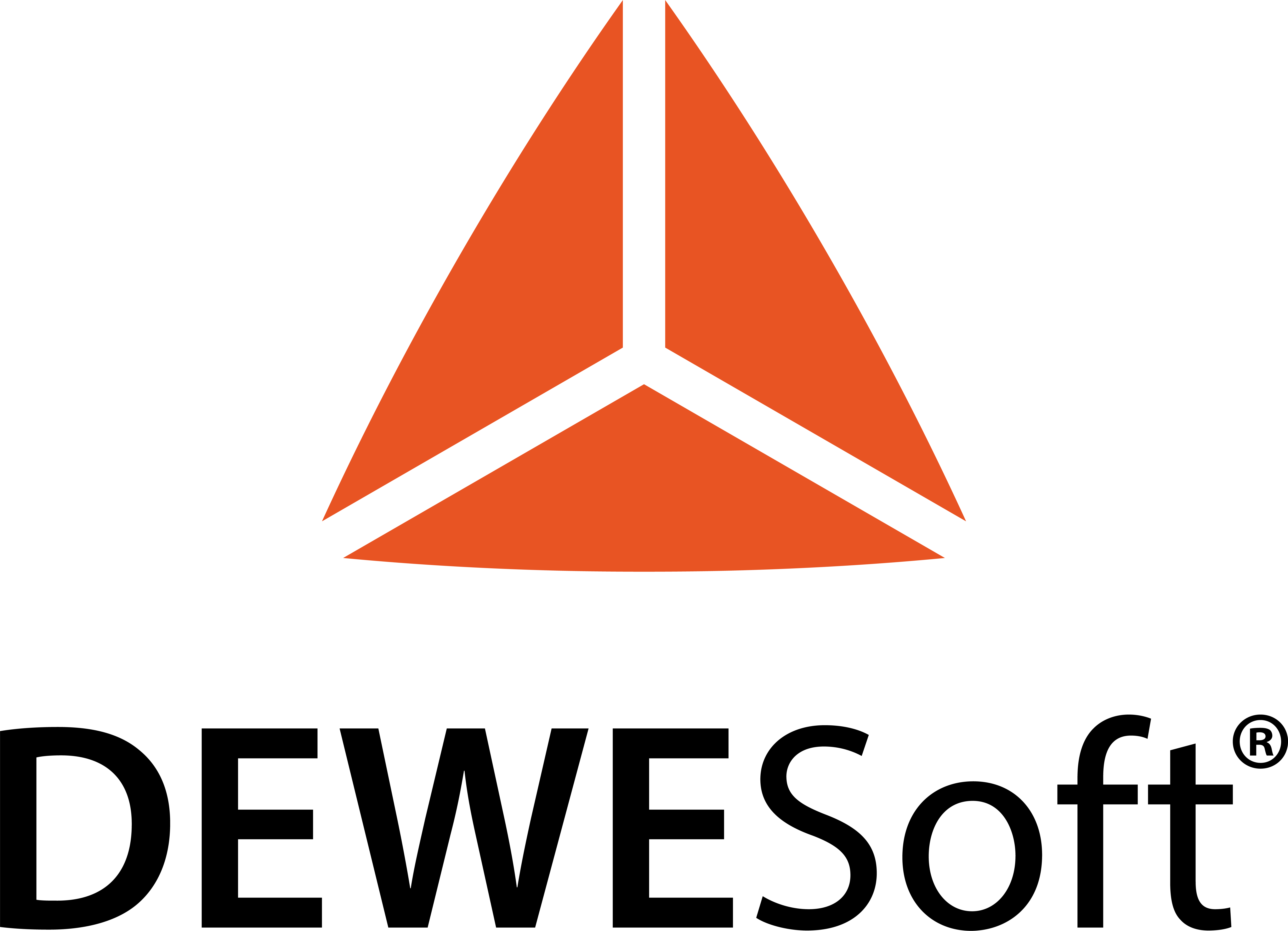
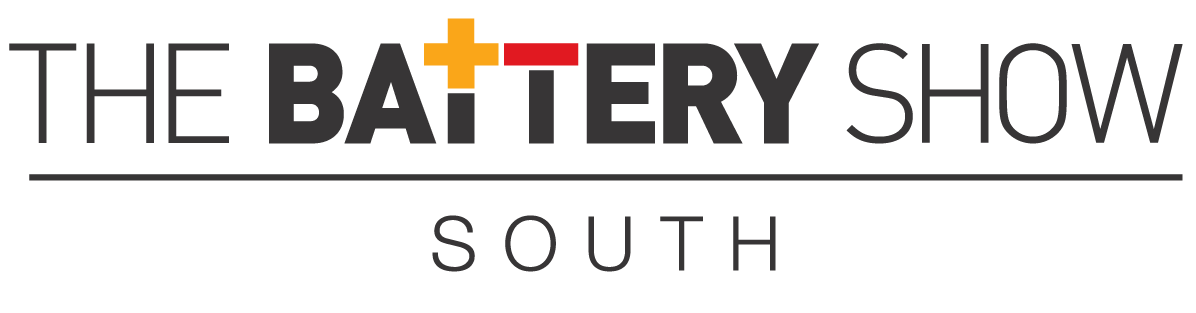
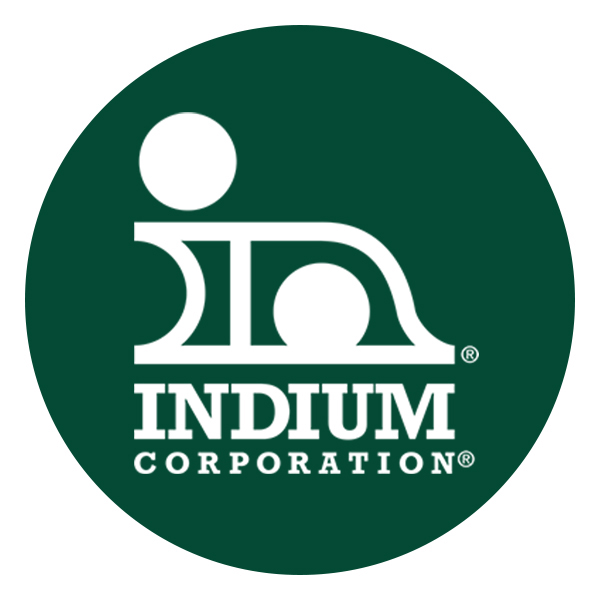
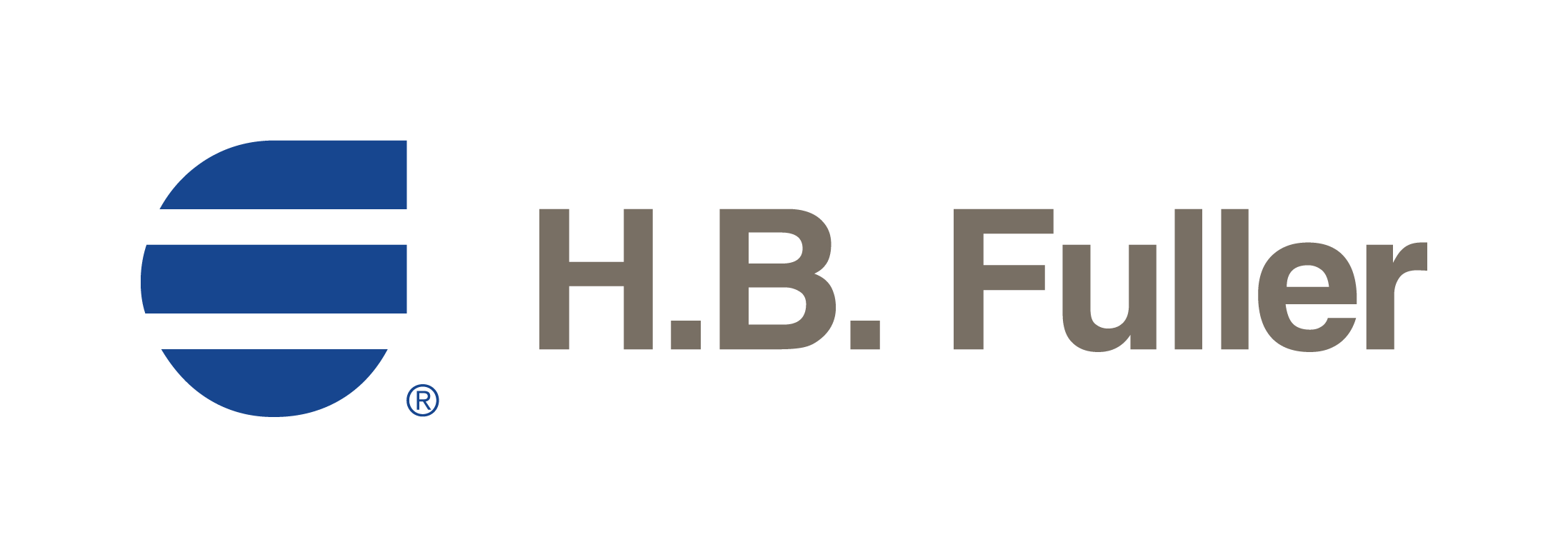