Battery repair and recycling
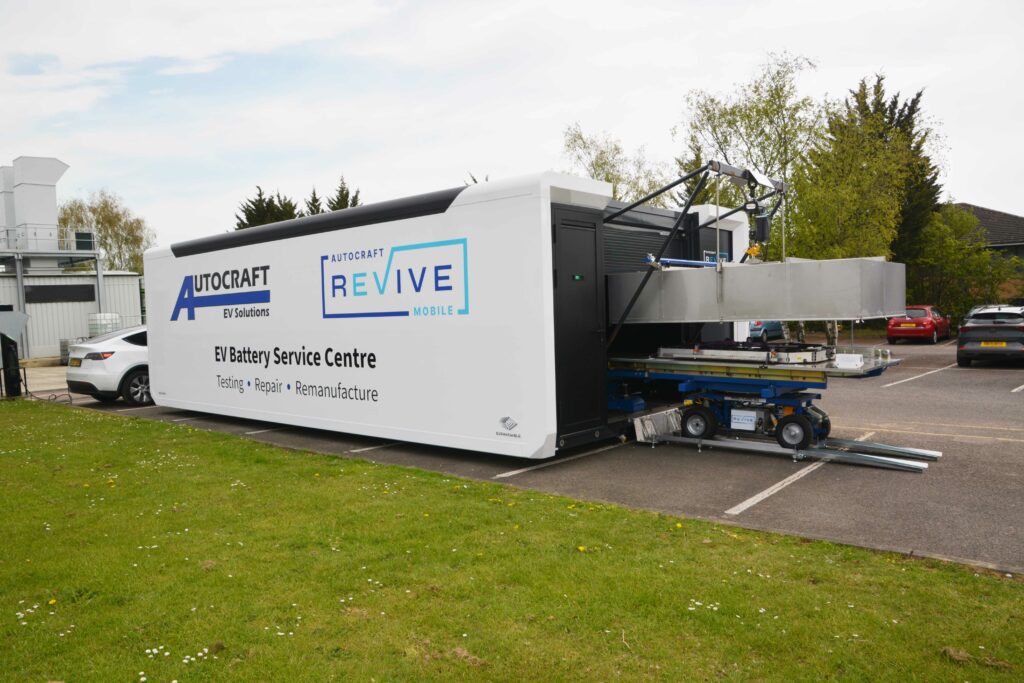
Electric vehicles (EVs) are facing some stiff headwinds in the market. Many are affected by depreciation significantly worse than that of comparable internal combustion engine (ICE) vehicles, the reluctance of dealerships to take them at trade-in time, along with escalating insurance premiums and some insurers refusing to cover them altogether, writes Peter Donaldson.
Coupled with widely disseminated expressions of disillusionment from well-known early adopters – including comedian (and holder of engineering degrees) Rowan Atkinson, YouTubers with large followings, and car-rental giant Hertz’s well publicised split with Tesla – this represents a knotty problem for automotive OEMs, their suppliers and governments that have invested a lot of time, money and effort in developments.
Markets are collections of organisations of individuals who are subject to shifting fashions, whims and prejudices, as are all groups of human beings. Furthermore, their behaviour is too complex for engineers working in a fairly narrow specialism, such as batteries, to control – even if it is a very important field.
However, some uncomfortable truths about batteries are at the heart of the problem, and these are susceptible to engineering solutions.
One of these uncomfortable truths is that EV batteries are subject to higher than expected rates of failure. They are typically expensive to repair, while their increasing complexity means few dealerships can repair them to the required standard in a reasonable time. This leads to high rates of repeat failure and excessive timescales for repair, and new replacements are expensive, to the point of making some vehicles uneconomical to repair at just a few years old.
What’s more, battery condition is difficult for many prospective buyers to assess. This is a particular problem if an EV has been involved in even a minor impact as it may have hidden damage to a cell that could result in a thermal runaway at some undetermined point in the future.
All this results in damaged packs being recycled prematurely, despite the vast majority of their components being suitable for reincorporation into EVs through remanufacture. Although useful quantities of valuable material are recovered through recycling, much is still wasted, including a lot of the energy that went into the manufacture of the pack in the first place.
Autocraft’s Revive range of battery testing, repair and remanufacturing services has been developed to address these issues, and in early April the company announced that it had negotiated a £24 million finance package with HSBC UK to accelerate the rollout of the system internationally.
The company is an industrialised system for condition assessment, repair and remanufacture, offered in mobile containerised and building-installed forms. After a visual examination, a battery is interrogated through its BMS and then subjected to deeper, high-voltage testing to identify areas where performance is poor, followed by AC tests that stress individual cells to identify faults. Then the system guides trained operators through the process of dismantling and cell replacement required to bring the battery back to health economically.
Revive has facilities in the UK and opened another in the Netherlands last year. Finance from HSBC is enabling it to pursue its plans to open new facilities across Scandinavia, Southern Europe and North America. Each facility will have the capacity to process 1,400 packs per year.
Whether that will be enough to reverse the slide in customer confidence in EVs remains to be seen, but it is clear that this is a capability for which the industry has an urgent and growing need.
The uncomfortable truth is that EV batteries are subject to higher than expected rates of failure and expensive to repair
ONLINE PARTNERS
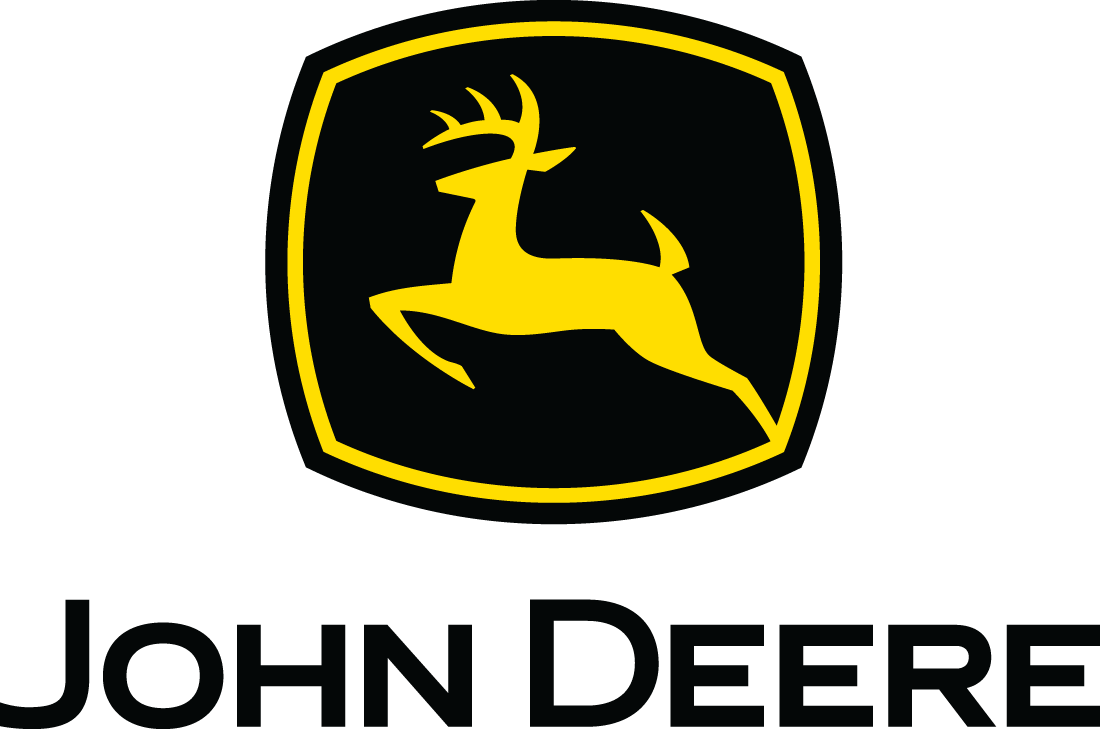
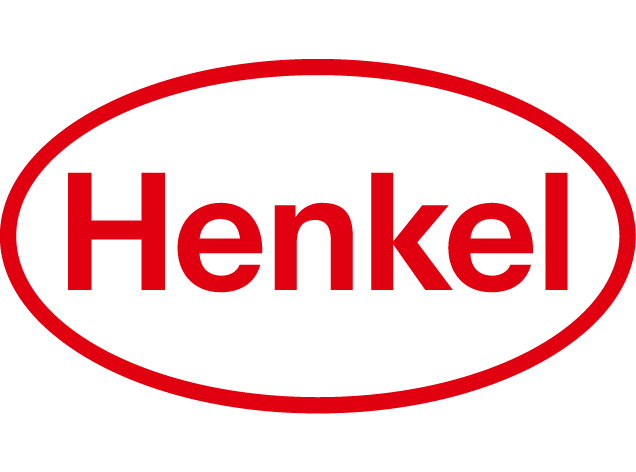
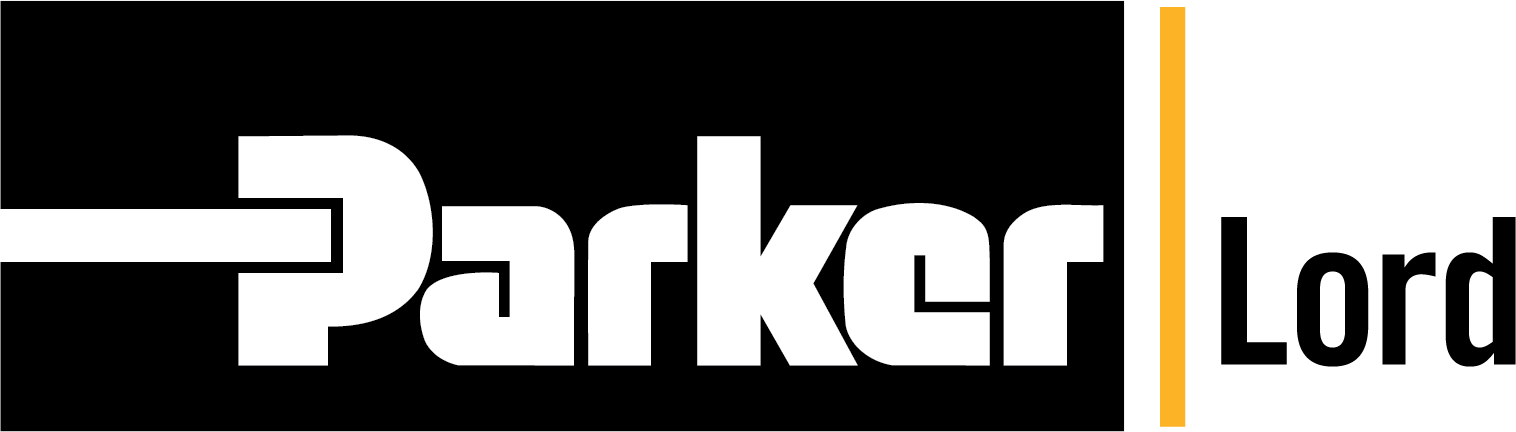
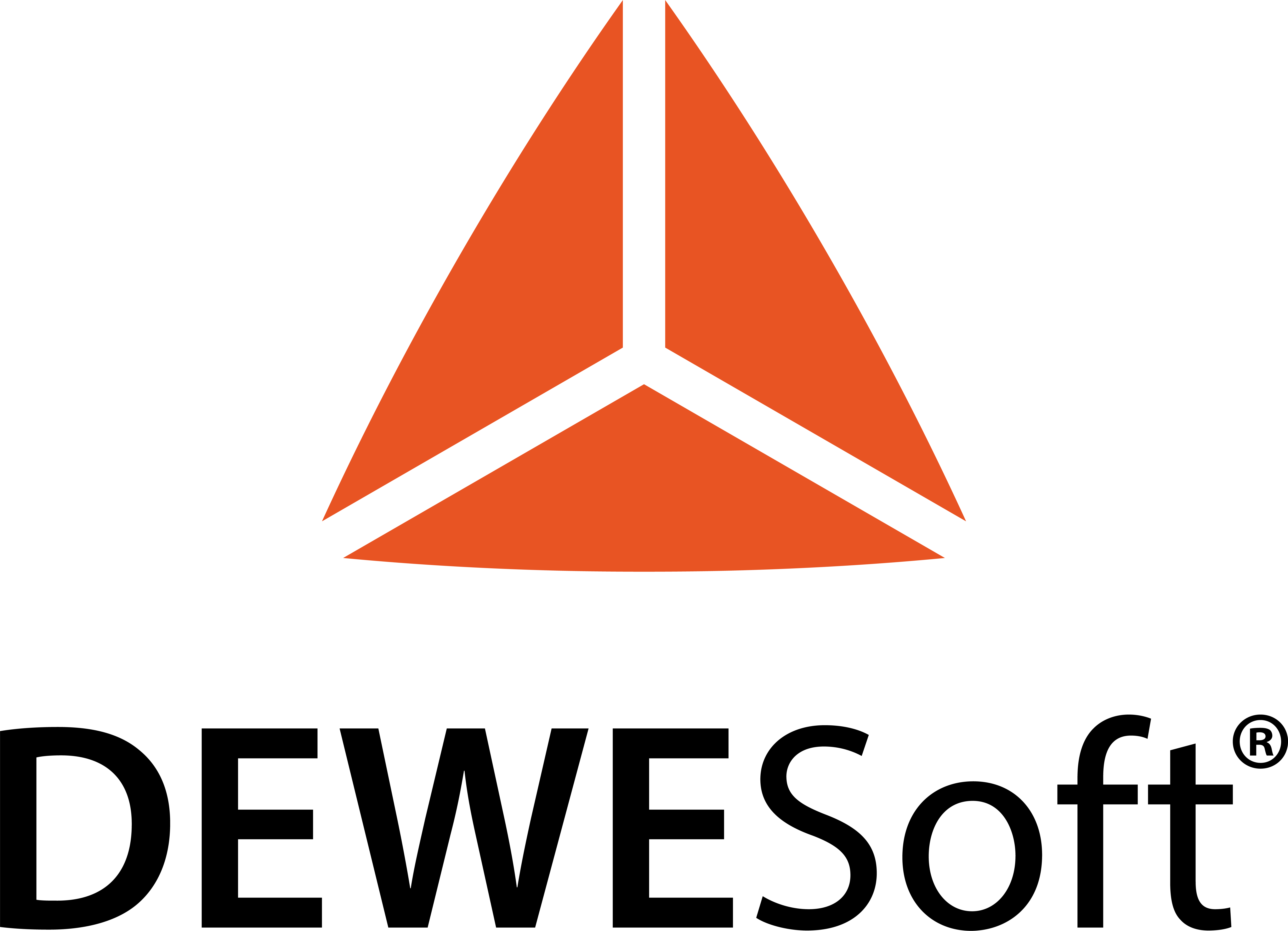
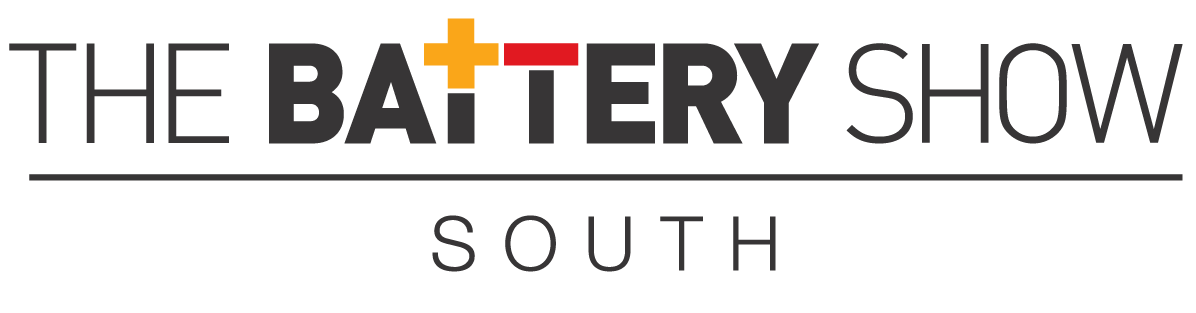
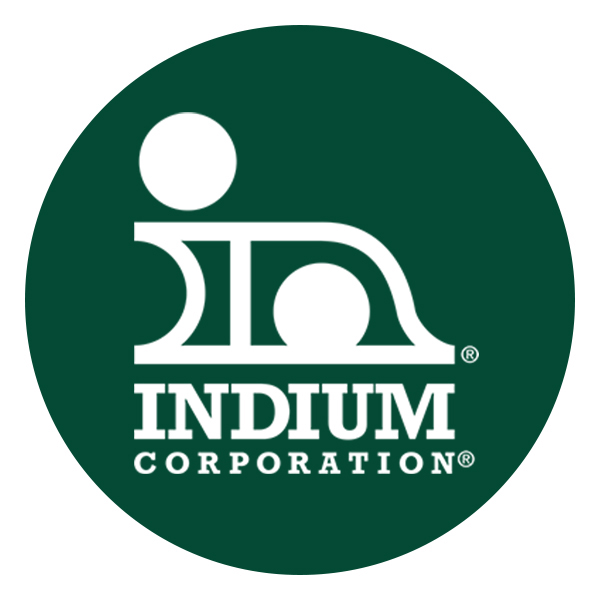

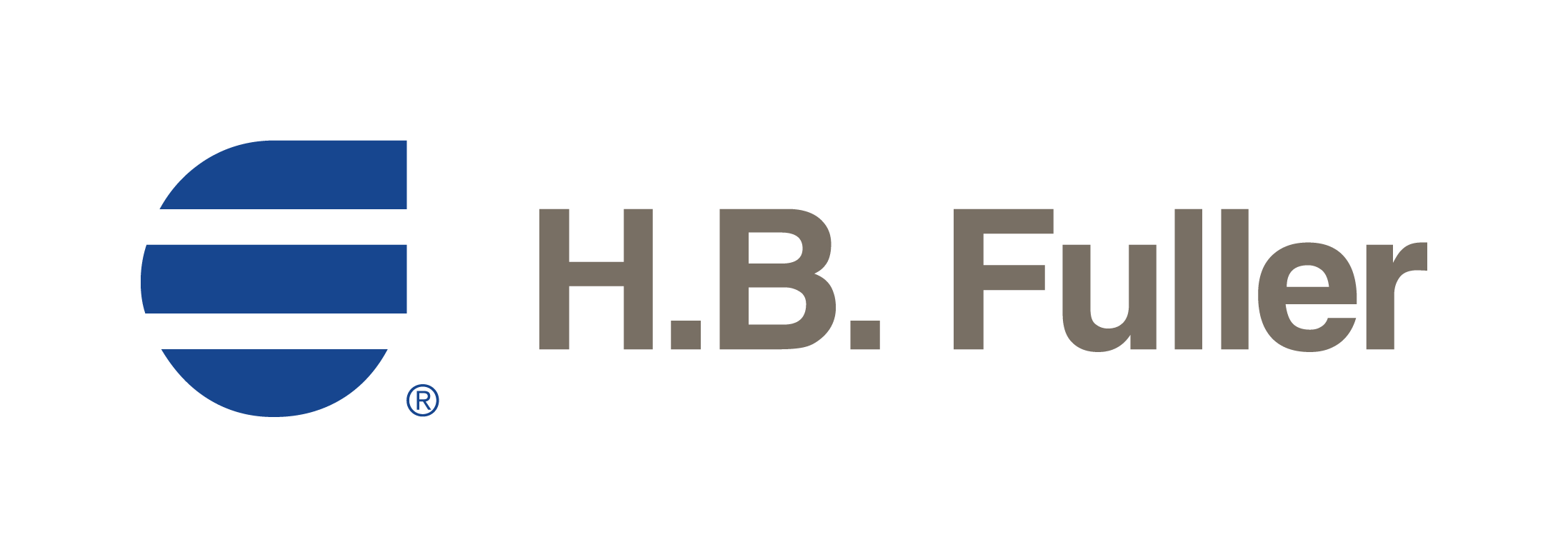
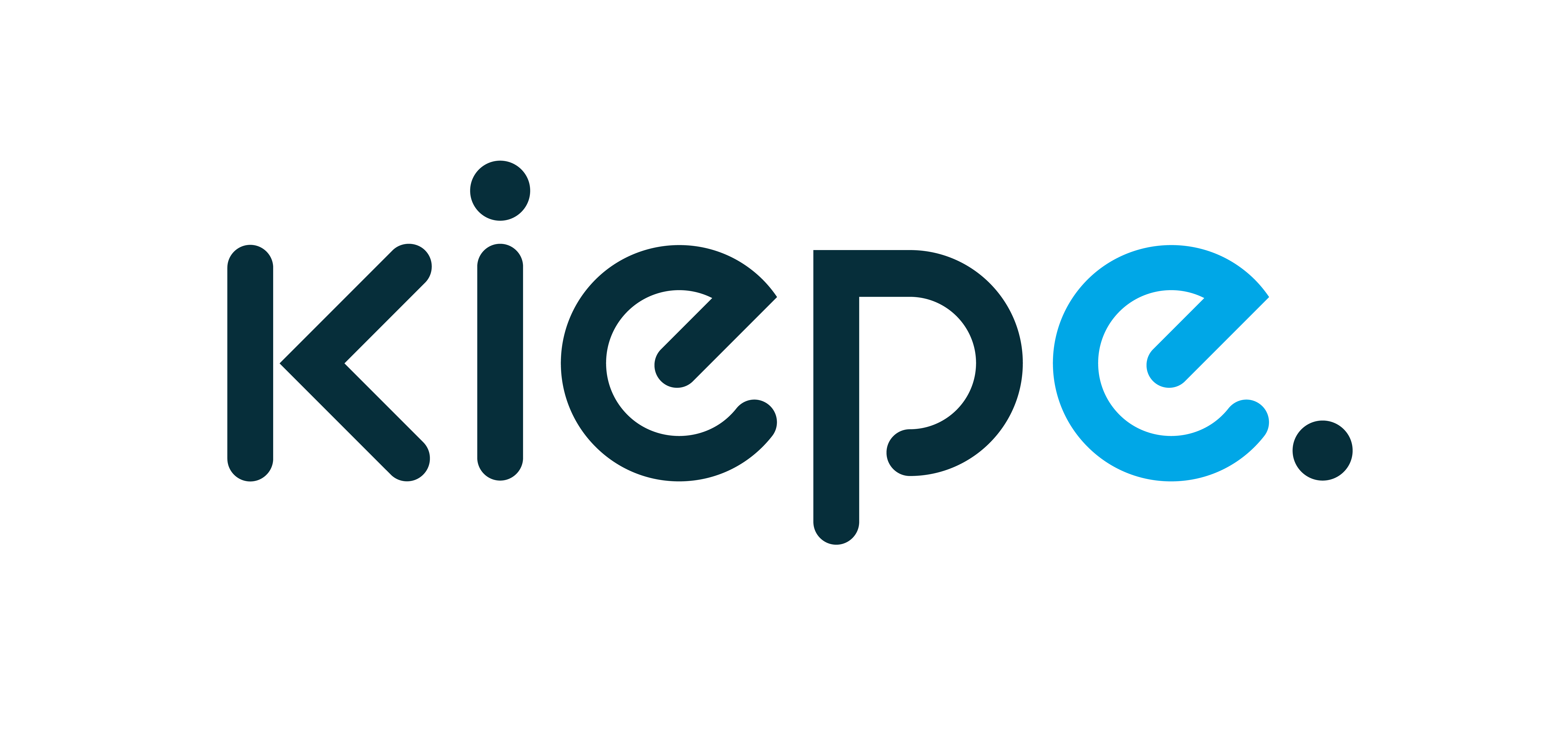
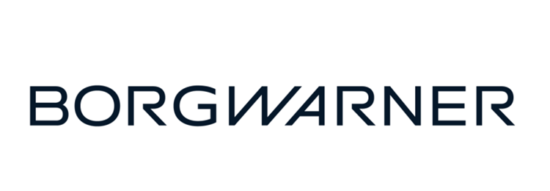