Bipolar batteries
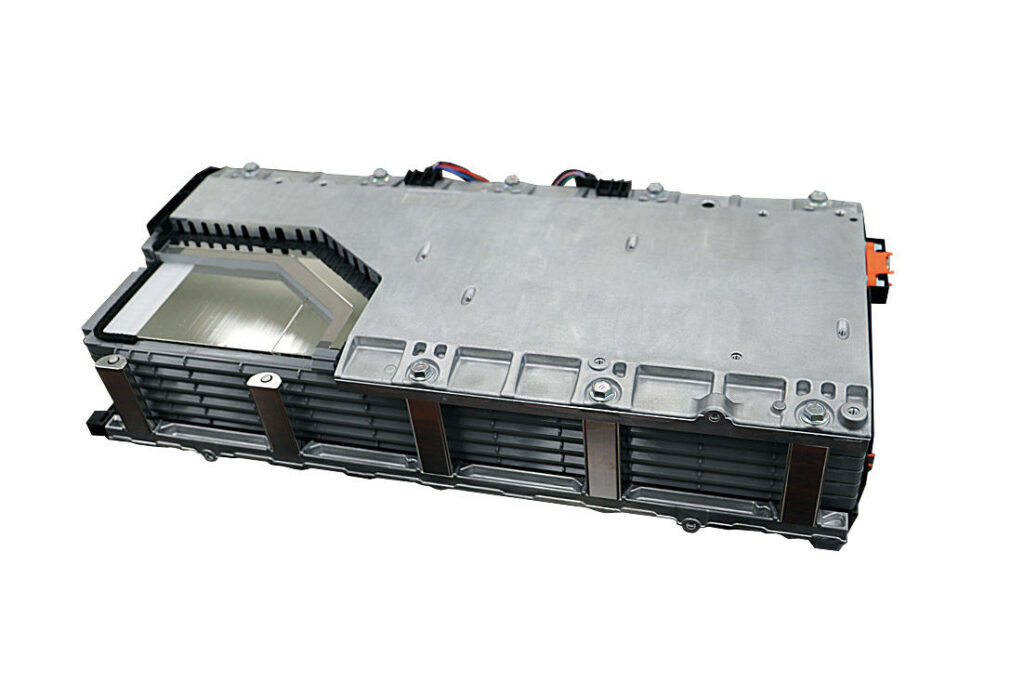
(Image courtesy of Toyota)
When Toyota unveiled plans for its next generation of EV technology in June 2023, the company made it clear that bipolar batteries would play a central role. The company is already using bipolar architecture in the nickel-metal hydride batteries in its Crown and Aqua hybrids, and it is extending the technology to BEVs with lithium-ion batteries. Its product plans include ‘popular’ and ‘performance’ versions of liquid-electrolyte bipolar batteries, writes Peter Donaldson.
A bipolar battery is one in which the current collector for each cell is shared by the anode and the cathode. A Toyota illustration shows the anode and cathode materials coated on opposite sides of the collector in each cell. This arrangement leads to a lighter and more compact structure by reducing the number of inactive components, particularly the interconnecting tabs and wires, thereby making more efficient use of materials, and increasing both energy density and power density.
The concept is far from new, as the first bipolar lead-acid battery was built in the early 1920s and showed performance improvements, along with the electrolyte leakage and intermixing problems that proved difficult to overcome through much of the following century.
With the rise of lithium-ion chemistry from the 1990s onwards, the application of bipolar architecture has been an important subject of r&d, with a focus on dealing with the above issues and others presented by thermal management and complexity in manufacturing that makes scaling up difficult.
Achieving a reliable seal between cells is tough, partly because the plates to which the anode and cathode materials are applied serve as both current collectors and separators, even though the cell also contains conventional separators, and multiple cells share a common interface. Also, both charging/discharging and thermal cycling cause expansion and contraction, which imposes mechanical stresses on the seals, exacerbated by any mismatch of coefficients of thermal expansion between different materials.
During manufacture, it is critical to achieve uniform compression across all the cells because any variation in compression caused by manufacturing tolerances can cause leaks, including during expansion/contraction.
As with other battery architectures, the compatibility of construction materials with electrolytes and with each other is also important. The bipolar plates in particular need to be made from materials that are corrosion-resistant, mechanically robust and compatible with the surrounding components, for example, while seals must be flexible enough to accommodate expansion and contraction.
Toyota must be confident that it has overcome these problems. The ‘popular’ version of its bipolar battery is based on lithium iron phosphate (LFP) chemistry.
The claims that Toyota makes for it include – in combination with vehicle improvements – a projected 20% increase in cruising range, compared with the current bZ4X, a 40% reduction in cost, and recharging from 10% to 80% in 30 minutes or less. This battery is expected to start production in 2026-27.
In parallel, the company is developing a new high-performance battery of monopolar construction and nickel-cobalt-manganese (NCM) chemistry, offering double the range for the bZ4X, 20% lower cost and a 20-minute recharge time. Production of this battery is due to begin in 2026.
The ‘performance’ version of the bipolar battery is due out in 2027-28. The design combines bipolar structure with a high-nickel cathode to provide a 10% improvement in range over the conventional high-performance battery above with the same recharge time.
Toyota has not said whether the solid-state EV batteries that are also part of its plans will be bipolar, but r&d work elsewhere is exploring that combination. At the very least, it could solve the leakage problem.
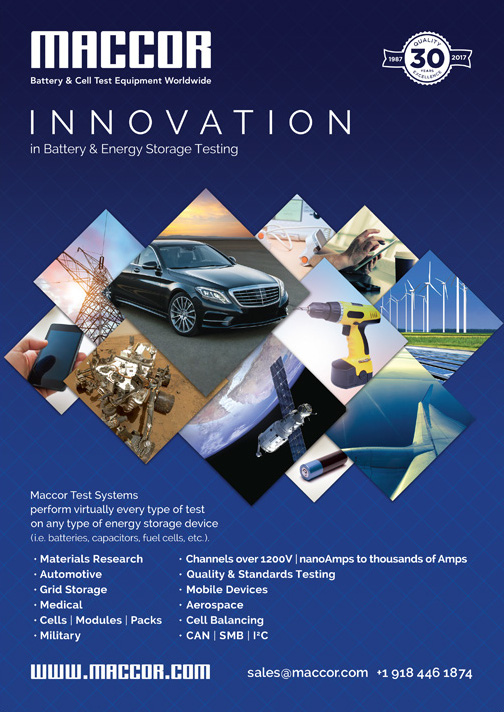
ONLINE PARTNERS
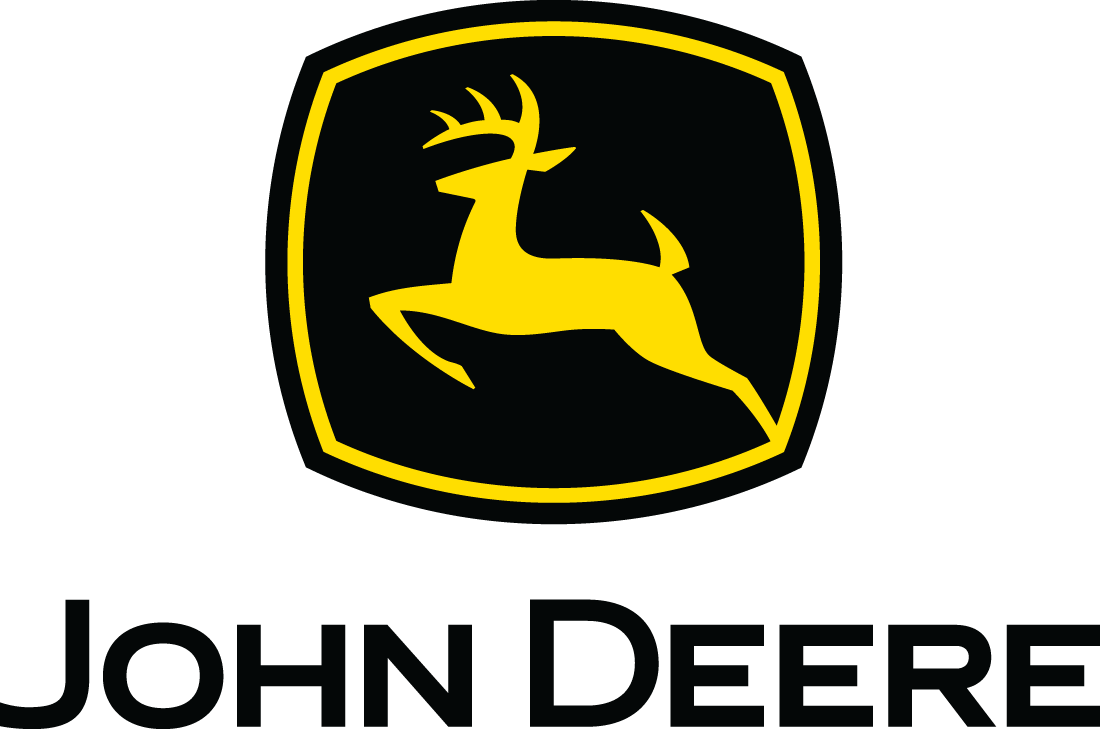
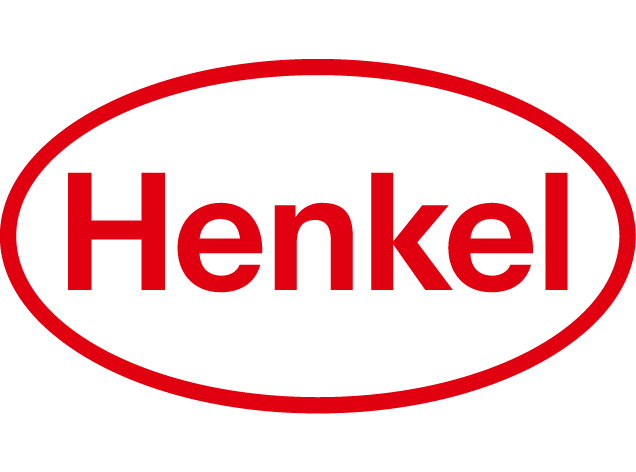
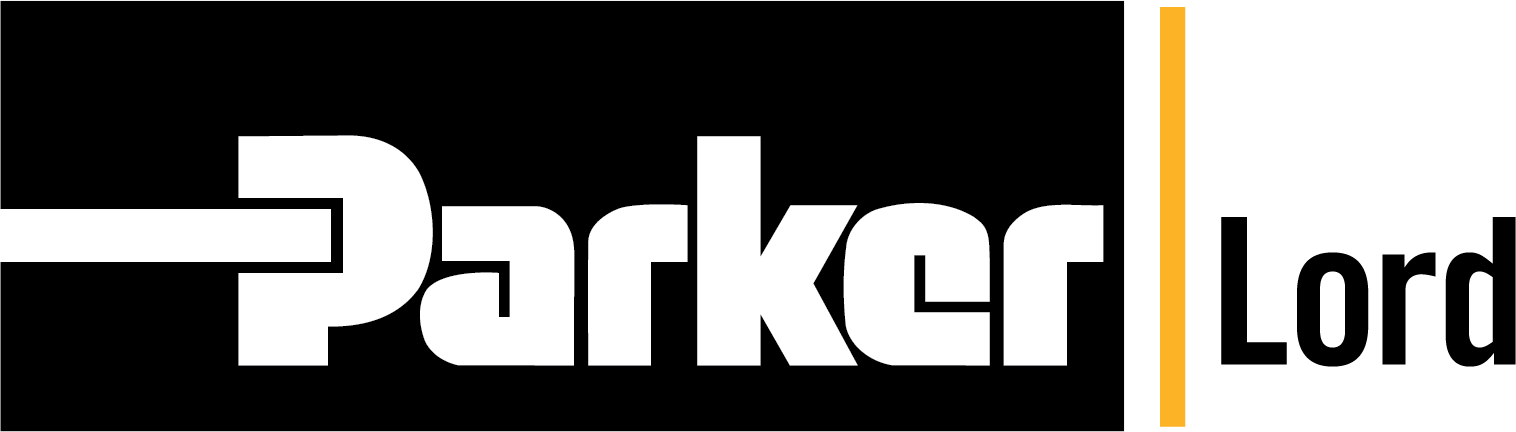
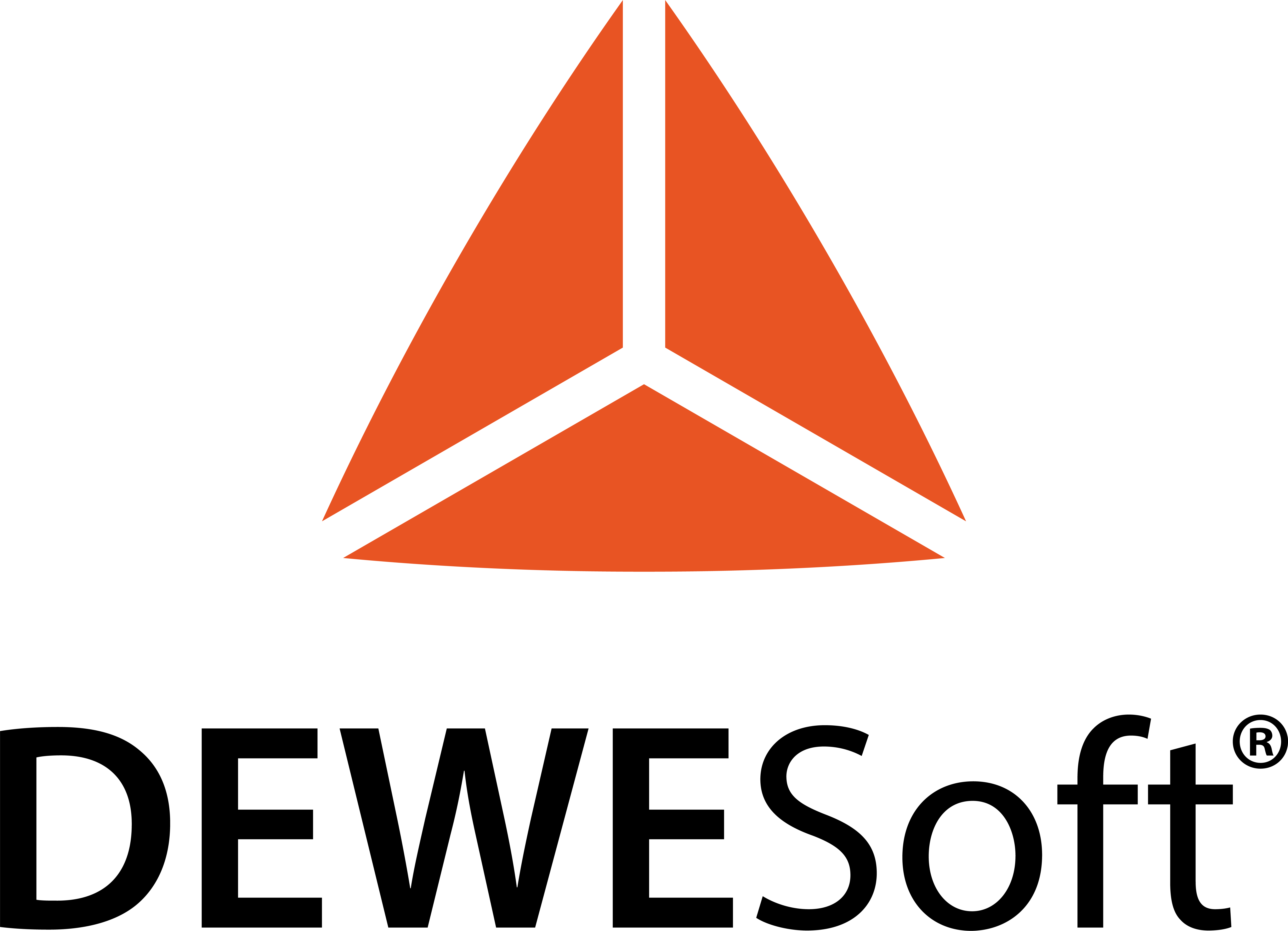
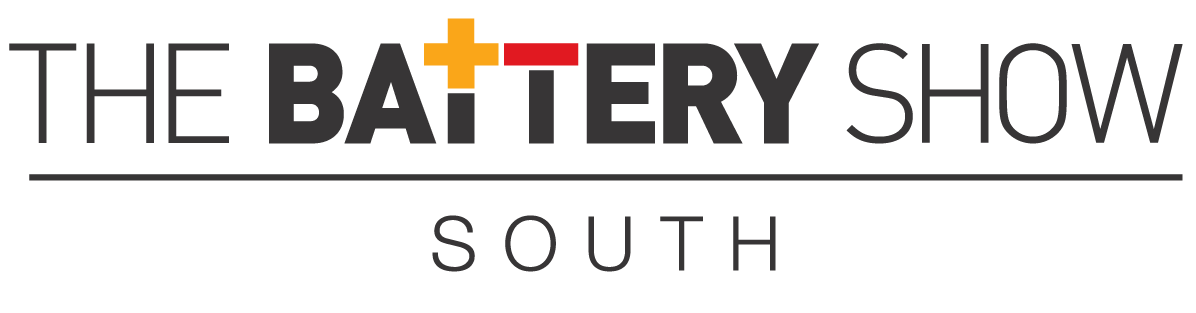
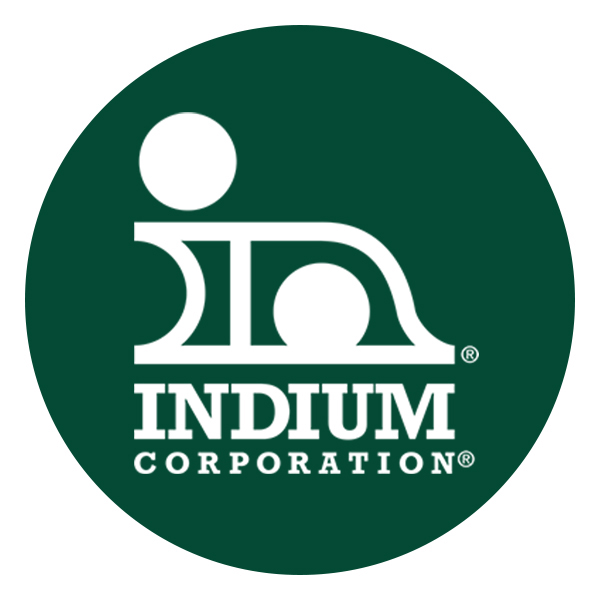

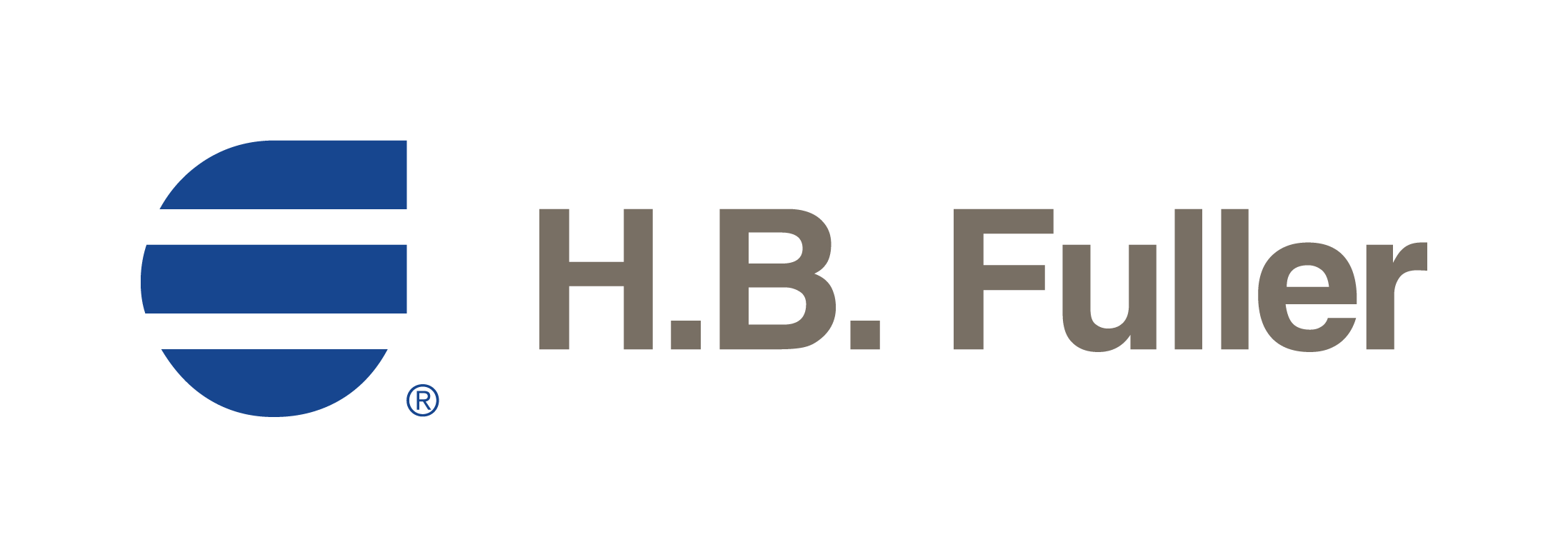
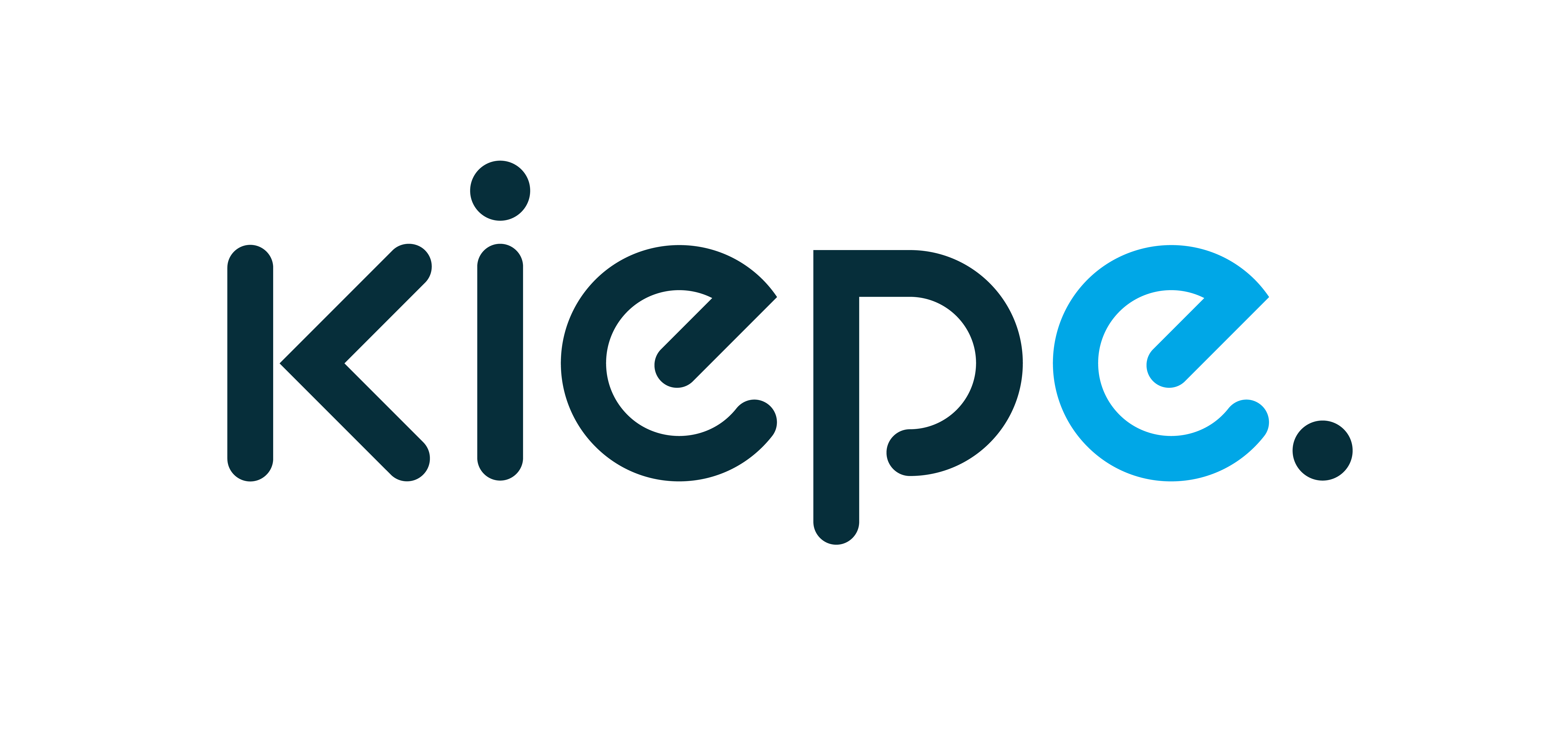
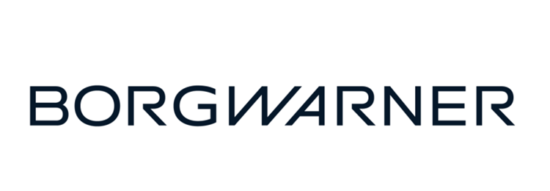