Frauscher x Porsche 850 Fantom Air
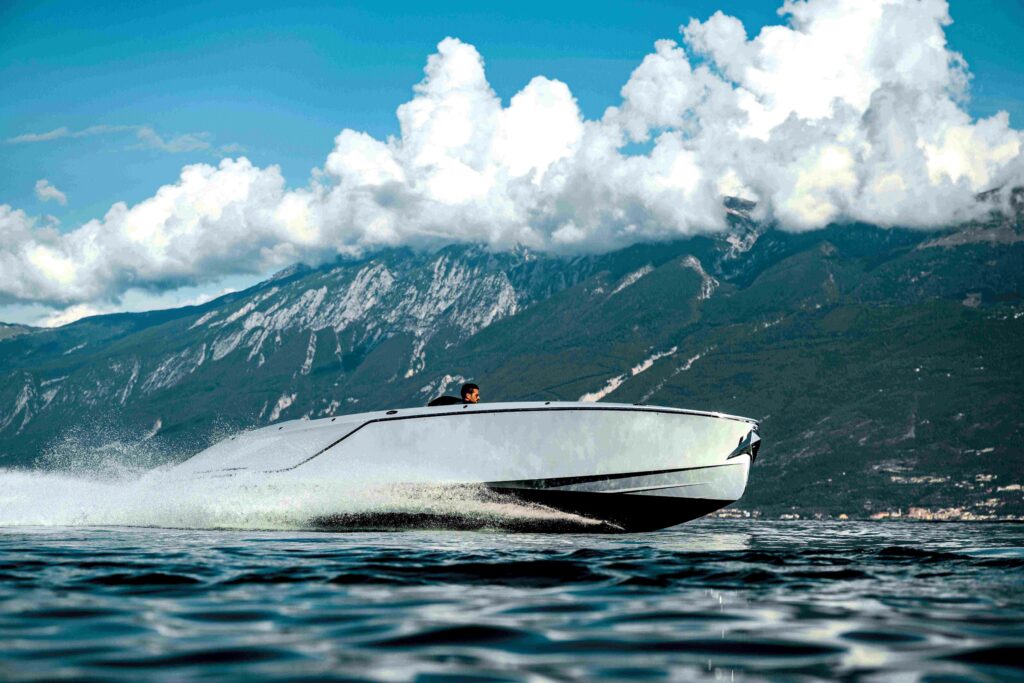
(Images courtesy of Frauscher except where otherwise stated)
Making a splash
Rory Jackson explains how Porsche has collaborated with boat-maker Frauscher to take its latest generation e-powertrain onto the water
Since boating as a mobility form is largely motivated by sport and leisure, the quietness of an electric motor versus an internal combustion engine is prized by many. The easier repair and maintenance of electric powertrains, compared with their fuel-engine counterparts, also benefits boat owners, but there is a dearth of suppliers making suitable components.
Automotive OEMs, by contrast, are rapidly developing all-new e-powertrains to suit many different EV designs. If it were possible to bring such an OEM into the marine world it could drive the creation of a fully electric motorboat.
This is the path ventured down by Porsche AG and Austrian shipyard Frauscher Boats, which together have developed the Frauscher x Porsche 850 Fantom Air.
This is an all-electric nine-person yacht, measuring 8.67 m long and 2.49 m at its greatest width, with a clearance height of 1.35 m and a maximum draught of 0.9 m. In essence, it is a version of Frauscher’s established 858 Fantom Air, integrating a form of the e-powertrain developed for the next-generation Porsche Macan SUV, as well as some other battery-electric road vehicles.
The Frauscher x Porsche 850 (or eFantom) has a dry weight of 2800 kg, and it is claimed to have a top speed of 85 kph and a cruising speed of 41 kph. Its onboard battery energy provides for about 45 km of cruising range.
In the course of seeking out new opportunities to use its automotive knowledge in other applications (mostly relating to mobility), a marine feasibility study was started within Porsche AG in 2021. This determined that supplying a powertrain to a boat manufacturer was the best way to go, without resorting to the huge expense and engineering challenges of making not only a boat but a boat engineering division too, from scratch.
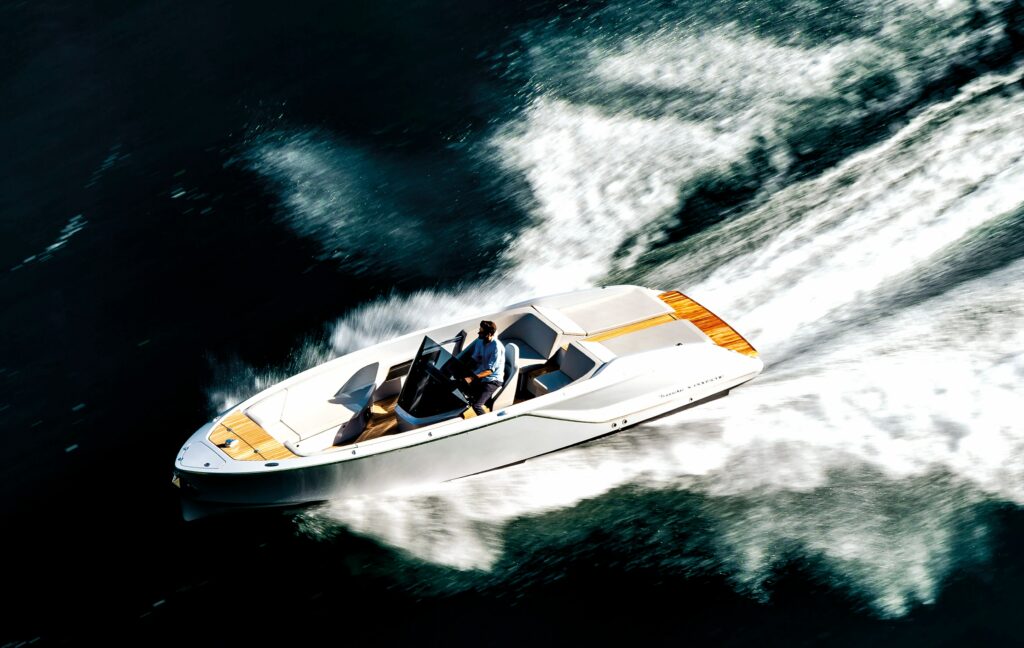
Next-gen Porsche Macan powertrain
Porsche opted for the next-gen Macan’s powertrain – one of its most advanced, which, as of the time of writing, is still in development – to future-proof the boat in a similar fashion to that EV. This powertrain is typically delivered by Porsche as a skateboard, carrying a control unit, the 100 kWh battery pack, the inverter, either a single rear-mounted e-motor or a front one as well, and suspension and steering systems connecting to the wheels.
In the eFantom, just the battery, inverter and standard motor carry over, as well as a modified version of the control unit. There are also some optimisations for the very different use case and operating environment of a powerboat versus a car.
Porsche adds that as soon as series development was launched, the project was strongly connected to and steered via the Macan product line, with the line’s vice-president, Jörg Kerner.
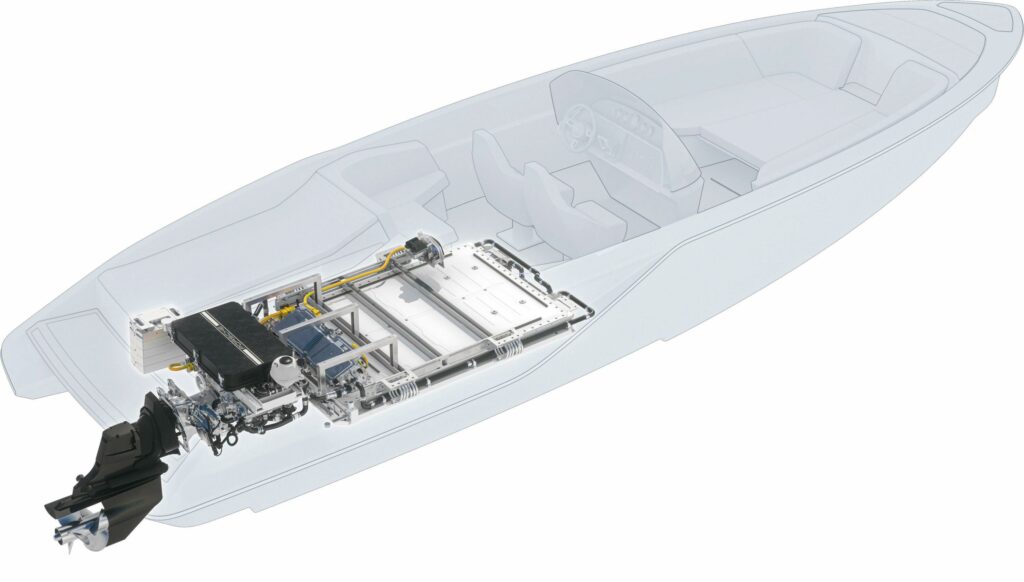
Frauscher shipyard
To choose the right marine partner, Porsche’s researchers reached out to a handful of shipyards. Florian Helmberger, head of sales and marketing at Frauscher Boats, remarks: “When [in 2021] Porsche proposed a collaboration, it appealed to us not only because of their reputation for quality engineering, but also because we, at Frauscher, have been working on electric boats since the 1950s. That is due to regulations that mean people haven’t been able to use diesel- or petrol-powered boats on local lakes and rivers for a very long time.”
Porsche and Frauscher initially considered electrifying the latter’s 1017 GT, a 9.99 m-long speedboat, typically running on two 430 bhp engines and having a 520 litre fuel tank. It has a deep-vee hull shape, which motivated some of the concept designs by the project engineers in which two battery packs were integrated in a vee-shape parallel with the hull.
“We knew that most users of electric boats tend to use them on lakes, whereas the 1017 is more for seagoing owners,” Helmberger muses. “Based on its dimensions, the 1017 was deemed too big for what we wanted to deliver. And, honestly, even with the dual battery pack powertrain that had been proposed, the range wouldn’t be enough to cover the sort of distance that users of larger powerboats want to do.
“We did consider putting the next-gen Macan powertrain into one of our smaller boats, like our 740 Mirage, which we’d previously electrified with a Torqeedo e-powertrain. However, we ran the numbers, and it just wouldn’t have worked from a packaging standpoint. We also would have been at the limit for the weight that the small hull could tolerate.”
Hence, the 858 was chosen as the model to be electrified. It was considered ideally sized for both the Porsche powertrain and the market for an electric powerboat.
Helmberger adds that the change in model coding from ‘858’ to ‘850’ stems from a tradition begun when Frauscher’s small, electric 750 St. Tropez boat – so-called for its length in centimetres – was fitted with a V8. The V8 version was renamed 757, due to its exhaust having made it 7 cm longer.
Now, any Frauscher boat with both electric and IC-engined variants will be named such that the electrified model number will end in ‘0’, and the ICE-powered model number will end and begin with the same digit. This tradition is now entirely stylistic as the 858 Fantom Air and 850 eFantom are both 867 cm long.
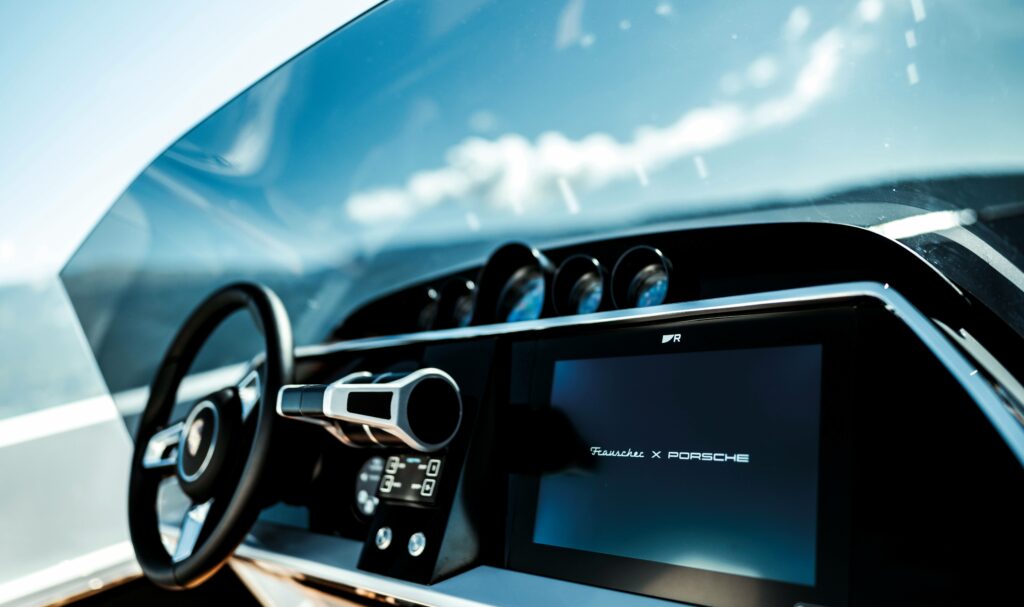
A history of two halves
The 858 model was conceived in 2012 as a larger, modernised upgrade to the 757 St. Tropez, with a hull specified for stern drive propulsion (as opposed to the shaft drive typical of Frauscher’s higher-powered electric boats or the pod drive on 48 V systems).
“It was the first boat we produced with Kiska, a design studio, perhaps most famous for working on KTM’s motorcycles,” Helmberger says. “They design many different vehicle types, but they had never done a boat before, and that was a major reason [why] we chose to work with them – we wanted to bring a new, fresh feel into the industry.”
He concedes that Kiska’s open and honest inexperience in boat engineering brought significant challenges, particularly when it came to instructing them on technical areas, such as packaging, laminations and the correct construction of moulds. Frauscher therefore also consulted one of its routinely contracted naval architects, Harry Miesbauer (who in the past had designed boats for the America’s Cup and worked for Luca Brenta at Luca Brenta Yachts).
“We put him and Kiska together to come up with the hull design, structure, packaging and materials of the original 858,” Helmberger recounts.
“That was still challenging as they spoke different languages and had different priorities in their development styles. Nevertheless, the product was so successful in the end that we contracted the two in partnership again for many further models – in fact, roughly half of our current range was designed by this team.”
The 858’s internal space had not been optimised for integrating an electric powertrain, however, as electrified boat powertrain technology was not mature in the 2010s. Having decided upon the next-gen Macan’s componentry, the first step for the teams at Porsche and Frauscher was to adapt the internal hull compartments for installing the battery, inverter, motor, transmission and control box.
Much of the work in that stage went into redesigning and then engineering the internal space for mounting the battery pack – the single-largest component in the powertrain – and also in positioning the e-motor as being best for both thermal management and coupling it with the stern drive.
A stern drive is also known as an inboard/outboard drive (or I/O). It is a form of marine propulsion that combines inboard power with an outboard drive. As such, the engine sits just forward of the transom (the flat surface at the rear), while the drive unit (also known as an outdrive or drive leg) lies outside the hull. Internally, Frauscher and Porsche have also used the term Z-drive, although this is more commonly applied in German than in English.
In some cases, the team was able to use the exact same kinds of mounting parts used in the original 858’s IC engine-related modules. This was an advantage towards the team’s ambition of being as specific and straightforward as possible with regard to the installation and mounting instructions they were to pass to Frauscher, to ensure the shipyard team could quickly learn and repeat the integration process for the powertrain into the 858 hull to produce the ‘eFantom’ units.
But the bulk of the challenge in the integration process was software, particularly in the engine control unit (ECU). For the project to be successful, Porsche’s team had to include as much of the original 858 boat and next-gen Macan powertrain as possible, with as few changes as possible; doing otherwise, they felt, would not be worth it, given the low production numbers that luxury powerboats are traditionally manufactured in.
An estimate has been made to us that a complete rewrite of the battery management system (BMS) and other ECUs would have cost millions of extra euros. Hence, the principal objective during software integration was to take the original modules as they were and write intermediary modules to make the powertrain think it was driving a car. This meant using analogous data inputs and translating them as far as necessary for safe, smooth and efficient operation.
A considerable number of simulations were performed, to repeatedly make sure the ECUs and boat-side components were communicating consistently and that all systems were always working, free from any errors that could be caused by one ECU missing a critical data input.
An additional part of the integration challenge was that many items inside the boat’s infrastructure were totally new to the automotive-focused Porsche team. For example, to begin with, the team did not know what NMEA buses (a comms standard for connecting marine sensors and displays within vessels) were, how to read the throttle lever, or how to control a seawater pump for thermal management (although the latter did turn out to be a fairly simple 12 V on/off type of system).
Other hurdles of this type were also cracked fairly quickly, despite the team being used to things like LIN bus-controlled pumps with sophisticated error messages in their usual automotive projects. Hence, combining these two worlds in software was the biggest singular challenge of the overall project from the Porsche side.
The bulk of this development was completed in the 12 months following the first talks between Frauscher and Porsche. The first working prototype of the eFantom was presented to the Porsche AG board in November 2022.
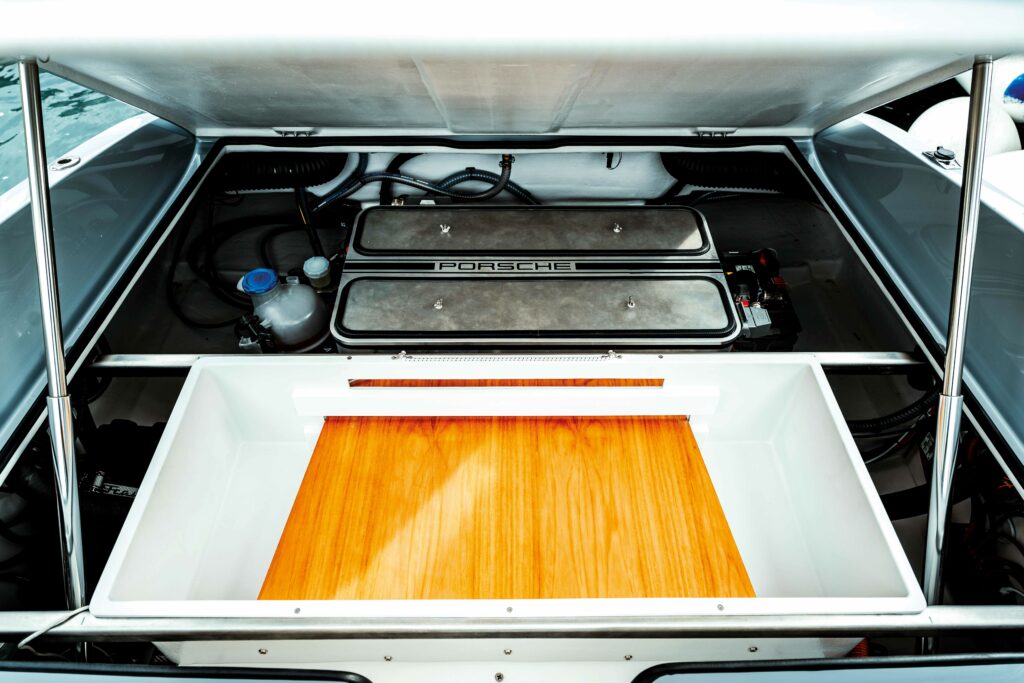
Inside the 850
The e-powertrain components are laid out as appropriate for the shape and dynamics of the boat. For instance, the high speed of the eFantom, compared with Frauscher’s other electric boats, means that hydrodynamic lift causes it to plane out of the water at its higher continuous power levels. This is why the stern drive sits at the very back, to ensure continued thrust while planing.
The e-motor sits inside the back of the hull, connected to the stern drive via a short transmission shaft. This enables the former to control the latter directly, much like a conventional outboard with a shaft and screw transmission system. The inverter is mounted forward from the electric motor, while the controls unit containing all of the powertrain’s ECUs sits atop these two inside a sealed (and Porsche logo-stamped) enclosure.
The battery is installed under the rear lounge deck, running from the mid-section of the boat back to the front of the inverter. Above the back part of the battery pack is a series of metal structural supports and a heat exchanger for an active liquid-coolant system for thermally managing the batteries, the inverter and the e-motor. The main HV bus running from the battery is an 800 V network, with both AC and DC fast-charging ports accessible on the front side of the left bench in the lounge area.
Smart integration also required that the Porsche team spring and damp the powertrain effectively. To that end, the engineers asked Frauscher things such as the rules of thumb on the ranges of acceleration that the boat would impart on the electrical components. Such parameters have not previously been studied at length in boats, as they have in the world of road EVs.
Discussions between Porsche, Frauscher and the naval architect led to a belief that the team would need to damp for up to 5 g of acceleration. However, other companies told Porsche over time that they had measured over 50 g with power boats on lakes.
To complete the study phase (and as the boat lacked any kind of chassis as commonly used in automotive vehicle construction), the Porsche team screwed the battery pack directly onto a prototype eFantom’s hull and took it out for lake testing to gain its own data. Porsche’s noise, vibration and harshness (NVH) specialist installed acceleration sensors around the battery, the boat hull and on other components. The team found measurements consistently higher than 5 g.
Additionally, the vibration profiles (measured as accelerations over different frequencies) were far wider and more dynamic than was typical in road vehicles.
This inspired the team to look into marine suspension components, and they found some designs for spring dampers already in wide use. Some mechanical adaptations were also made at the battery frame, particularly using wire rope mounts to keep the pack as internally unchanged as possible and to mount it to the spring dampers.
The team has largely used standard, elastomer marine-mounting pieces for the other powertrain modules. After taking these various damping measures, the prototype boat was brought back to the lake and retested to gather fresh acceleration measurements. The end result was that the g-loads were found to be much more tolerable for the powertrain parts.
On top of that, tests to investigate how the boat would handle unsafe usage included travelling to Lake Garda (in northern Italy) and using a ferry to generate large waves, which the eFantom was then steered to jump over.
Vaulting the waves behind the ferry imparted heavy, bumpy impacts under the eFantom’s hull, which was fitted internally with motion sensors and associated cabling to measure shock, vibration, noise and other parameters.
Further testing validated compliance with marine regulations on the survivability of every powertrain module against salt spray and similar ambient threats. Final validations of the eFantom are under way as of writing, with a view towards sales later this year.
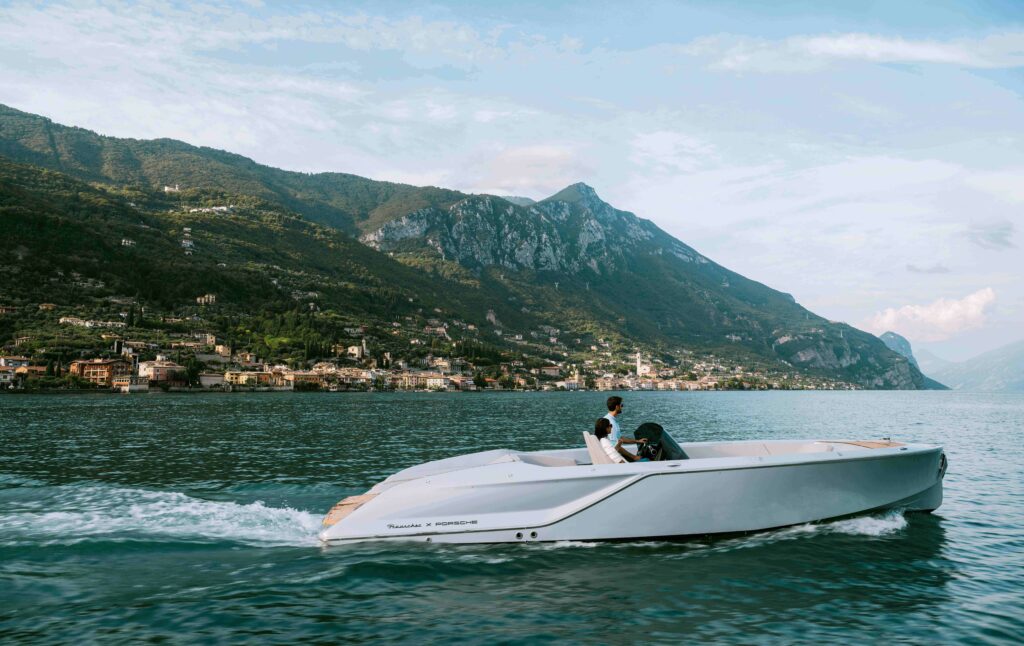
Cool controls
The eFantom’s powertrain control system is built with a distributed architecture and assembled around a central ECU made from a blank sheet in-house at Porsche (including both hardware and software) to satisfy the company’s targets for automotive buses, including CAN, FlexRay and Ethernet to a degree of security deemed necessary for modern, connected vehicles. It also accommodates the necessary conversion modules (as well as digital and analogue interfaces) for dealing with naval communication protocols such as NMEA 2000.
Additionally, from the Porsche side, two of the next-gen Macan’s high-performance computing ECUs have been incorporated (the Macan powertrain typically has five). These ECUs include energy management, charging and electrical safety contactor mechanisms to ensure the boat systems operate with consistent logic and safety, as in the Macan.
The first one that the team carried over into the eFantom is responsible for the management of high-voltage systems. It connects directly to the Integrated Power Box (IPB), where the onboard charger is situated, and to a dedicated control unit for the charging sockets. The other ECU provides intelligent functions such as enabling customers to communicate with the boat using a key (eFantom users get a similar electronic key to Macan users), and an immobiliser function in the inverter to control starting and stopping using the key.
These two ECUs, along with the central ECU and some additional lower-level controls, are housed in an enclosure that was designed and created for this project, given marine regulations on protection against the ingress of fresh and salt water, and the fact that the ECU enclosure in the Porsche Macan is designed for a dry environment (whereas the boat’s powertrain compartment will always contain some water).
The team refers to the central ECU as its ‘eVCU’, and it is in essence the main connecting part between the boat’s sensory inputs and all of the outputs for controlling the various powertrain subsystems, such as signalling torque values for the inverter to execute. To do that it houses new software modules, including one that converts the throttle-lever CAN into an automotive bus protocol, as well as safety modules for monitoring health and performance values at different component levels.
The main protocol in the eVCU is a form of CAN, similar to that found in commercial EVs, with some modifications to have power and communications running within wiring harnesses simultaneously, and to meet regulatory requirements on the minimum thickness levels of marine cables (inside the ECU box are relatively thin automotive cables, while outside are generally much larger marine connectors and cables).
Wiring harnesses were also customised to enable toggling of some onboard relays, unlike those in automotive, such as for controlling the coolant pumps and Z-drive, and for managing a dual, redundant safety lanyard or kill-switch system (typical in powerboats). Pulling out the lanyard triggers a message to the eVCU to no longer send out torque requests and ceases the inverter’s power supply to ensure the boat stops.
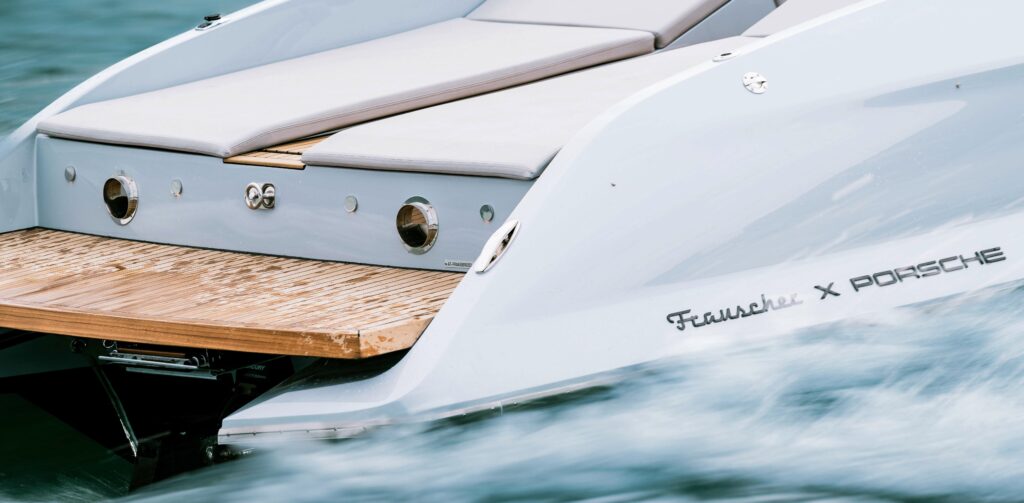
Smooth operation
When a change in the throttle lever is output to the eVCU over CAN, it is converted into a FlexRay packet for the inverter to read as a torque command.
Several hundred signals are handled in the eFantom at any given moment. These include steering and acceleration commands from the driver, readings from temperature sensors throughout the powertrain for thermal management (including some exposed to the ambient water surrounding the heat exchanger), and driver-relevant values for motor and battery health, which the operator may wish to monitor via a RayMarine display at the helm, such as battery state of charge (SoC), transmitted voltages and cell temperatures.
The eVCU also sets the speed and torque logic by which the inverter governs the four driving modes available to the eFantom’s driver, each essentially hallmarked by a different limit to its top speed. These are Docking mode, which caps at 15 kph, a Range mode, limited to 41 kph (the cruise speed for optimum energy efficiency), a Sport mode with a top speed of 75 kph and Sport Plus, which gives the absolute maximum of 85 kph.
“Within each of those we have different throttle-response maps; for instance, the Sport Plus regime has a higher acceleration than Sport, Range and Docking, in that order,” Helmberger says.
Regarding speed and handling, we asked if Frauscher ever considered or would want to engineer a hydrofoil propulsion system, such as the one discussed in detail by Candela in EME 11 (Autumn 2021).
“I can’t comment on future products, but hydrofoiling is something clients have asked us about, and electric powerboating is a small industry, so we know Candela very well and have driven their boats,” Helmberger notes.
“What their C8 does is brilliant for their application, because lifting the boat out of the water lets you cover a distance of around 30 nautical miles as fast and energy efficiently as possible.
“But the drawback is that hydrofoiling, even when controlled as neatly as theirs is, works most safely and efficiently in something of a narrow speed window, of maybe 25-28 kts. You have to limit the top speed judiciously to avoid unsafe usage, and once you go slower than that it’s not really efficient anymore.
“We certainly can’t match their efficiency at their top speeds, but we don’t need to; our boats are used very, very differently to theirs. Our users will only ever want high speed for very short lengths of time, just for fun, and then the rest of the time they’re at a leisurely slow pace, often below 6 kph. So hydrofoiling is of no real benefit to our clients.”
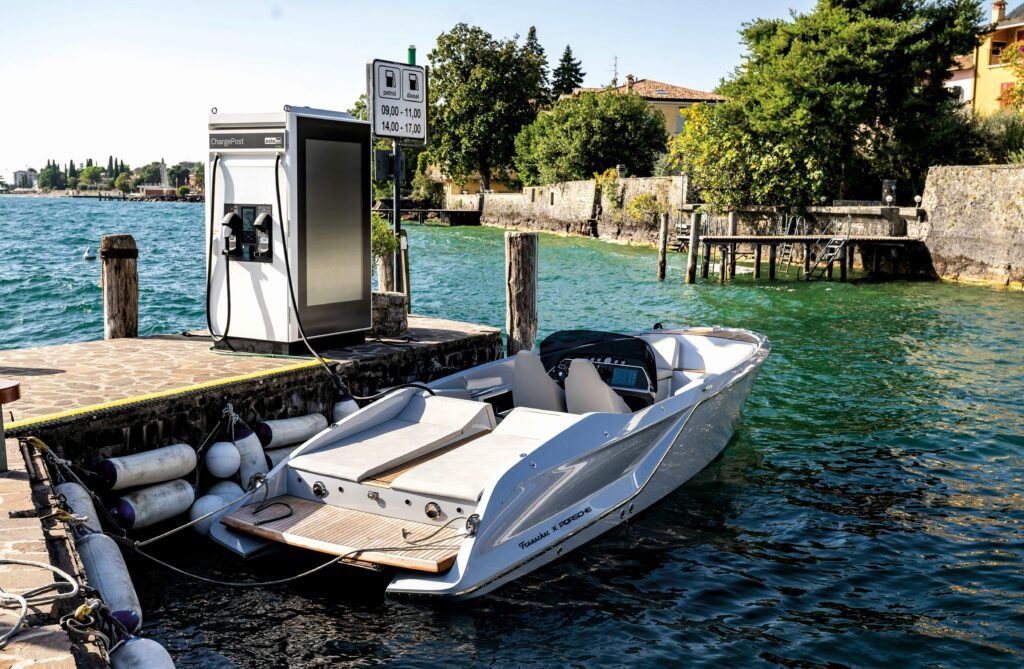
Motor and inverter
The motor in the eFantom is capable of 170 kW continuous power, or 400 kW peak output – a step beyond the
60-110 kW maximum output levels of Frauscher’s electric boats, developed as they were in a time preceding the advent of the eFantom.
That peak 400 kW is a setting programmed into the eVCU.
The motor is physically capable of delivering more than that, but the boat needs completely different torque curves to those experienced in a car.
For instance, when going from zero in automotive platforms, one typically needs to generate full torque all at once to overcome tyre friction, but doing this in a boat would be ultimately useless, because one would just create cavitation at the propeller. Hence, both the 400 kW peak and 170 kW continuous maximum are set for safe handling of the boat.
The e-motor is a permanent magnet synchronous machine, configured with an inrunner rotor and external radial stator, with the latter integrating liquid cooling channels. The stator and rotor are taken directly from the motor to be used as the core of the next-gen Macan Turbo.
Initially, the team wanted to take the whole motor, housing included. But, in the car, the motor is intended to have an integrated e-axle, including transmission parts, and those latter components are superfluous to the boat’s requirements. A different transmission is used for the 850’s stern drive, which has been designed to closely fit the packaging constraints and performance characteristics of the e-motor (and, in any case, the Macan Turbo’s e-axle wouldn’t fit in the boat!).
Fortunately, developing the new housing was a straightforward process. The Porsche team studied the housing of the Macan and the Taycan, the latter lacking an integrated axle, and it used the same bearing and sealing concepts as used in those cars to avoid the cost and delays of coming up with something completely new. Although there was a risk of the bearing being oversized, it was deemed a preferable risk to the alternative prospect of the bearing being too small and thus breaking after 100 hours of operation.
The inverter is a silicon carbide (SiC)-based unit, developed for the next-gen Macan powertrain, and the first to be used by Porsche. SiC MOSFETs were chosen to minimise switching losses and maximise switching speeds, compared with conventional, silicon insulated-gate bipolar transistors (IGBTs). It can supply 900 A, theoretically more than 500 kW, and its thermal efficiency is aided through the same coolant channel as that running in the e-motor.
Using SiC increases energy efficiency and smooths transients in the motor, although Frauscher and Porsche note that any gains to handling are difficult to sense at the propeller through the stern drive and its transmission.
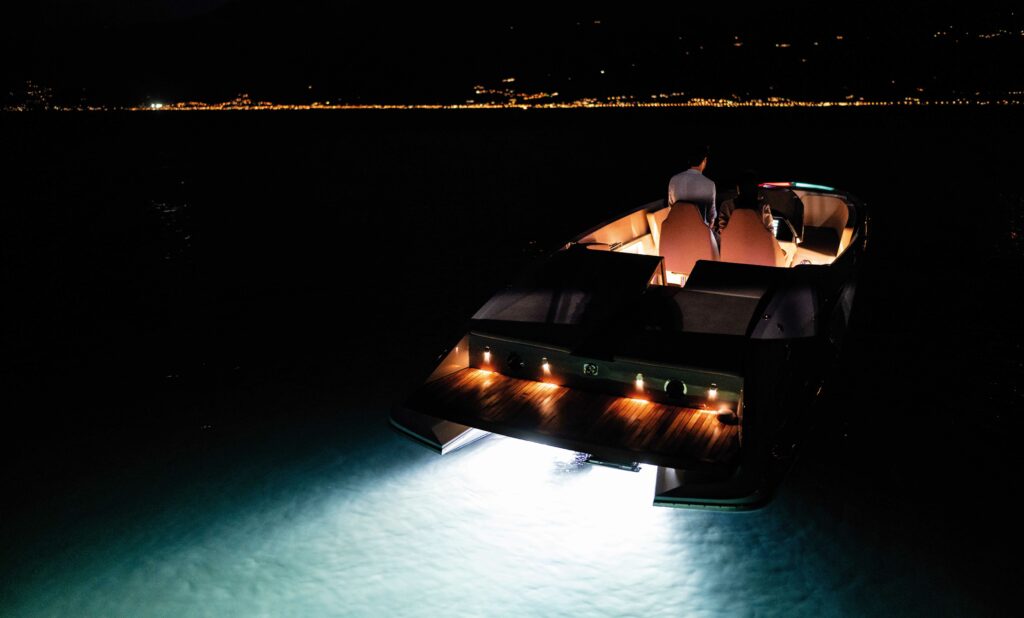
Stern-drive transmission and gearbox
Early on in development, the Porsche team was unsure how well they would be able to calibrate the e-motor and inverter for use in water. They therefore wanted to protect the stern drive from the high speeds and dynamics of the motor shaft, which meant the engineers initially tried a friction clutch between the motor and stern drive, with essentially two plates and a friction coating between them, as one would find in a car.
That was set for a fixed-torque limit; if exceeded, the clutch would slip, so neither the motor nor the stern drive would take any damage. But when the team first tested it on a lake, with the motor uncalibrated, it failed multiple times and the boat had to be towed back to the harbour.
So, the team commenced with calibrations, and the boat no longer uses a friction clutch. Instead, the 858 now has a relatively simple system with an elastomeric claw clutch to prevent accidental slipping.
Mercury Racing’s MerCruiser Bravo 3 XR is used as the stern-drive unit, partially due to Frauscher’s familiarity with the brand (MerCruisers are installed on several of its other boats). It features a twin-screw propulsion system, meaning counter-rotating propellers are arranged on a common shaft. These propellers typically have a diameter of 16 in, and are made from heat-treated stainless steel, with the internal gear ratio set to either 1.65:1 or 1.81:1, depending on the customer’s use case.
“The advantage of this type of drive over a traditional shaft drive is that you can angle the propeller up or down to meet the water line when the boat is planing,” Helmberger says. “This gets the driver higher speeds and efficiencies than if they’re just steering it with, say, a rudder behind the propeller, which would especially reduce performance in tight turns.”
Additionally, although Porsche had expected to run the e-motor in one direction for forward thrust and in the opposite direction to reverse, the MerCruiser’s gearbox necessitated shifting for reverse drive; hence, the e-motor always runs in the same direction.
It was therefore a challenge for the team to make sure the boat always goes forward when the user wants it to, and never gets stuck in a given gear stage, especially when there are some ECUs in the stern drive that the boat doesn’t need to use. Gear shifting is controlled by reading throttle signals, including the thresholds built into the throttle lever that correspond to the gear level.
Hence, when those thresholds are detected, the eVCU sends a signal to an actuator, which pulls a wire to engage or disengage the gear in the stern drive.
Helmberger adds: “Many boat manufacturers attempting electrification will run their e-motors on idle for long durations at startup and stops, just to make it easier to shift gears, which is obviously a waste of energy. The team at Porsche instead programmed the eFantom such that the motor idles for a really short amount of time, basically a split second, enhancing overall energy efficiency. To our knowledge, no-one else is doing that in electric boats.”
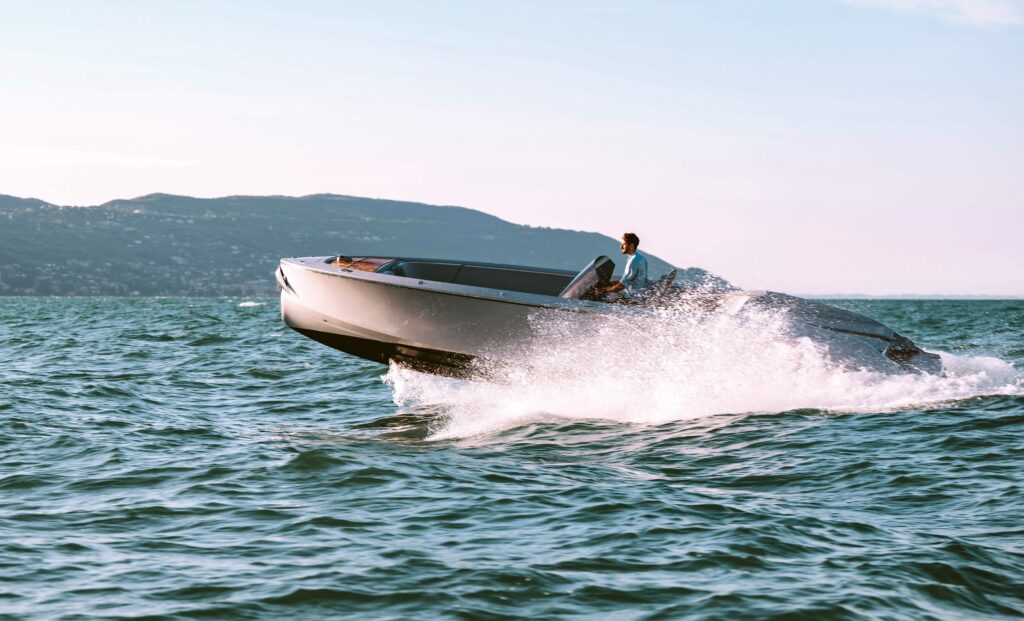
Battery and charging
The 800 V (737 V in nominal operations) battery pack in the eFantom contains 12 modules and a cumulative 100 kWh of energy. Each module contains 34 cells and 67 Ah, with the overall architecture of the pack’s cells given as 204s2p.
This architecture enables the use of 400 V charging stations via ‘bank charging’. Any EV with the next-gen Macan powertrain automatically switches HV gates in the battery to split the 800 V pack into two packs, each with a nominal 400 V.
Each of those can then be charged in parallel by the 400 V station without the need for a HV booster (and the HV ECU can balance the two halves’ SoCs before charging them together, if necessary). Technically, the team limits its output to 400 kW, but like the motor, it is capable of more.
Regarding battery safety, the team has developed a unique carrier frame that not only helps to set the safe mounting and damping points for the battery previously discussed, but, in case of a thermal event, it contains pipes that guide potentially harmful gases out of the boat. The gases exit at the sides of the hull, where there is no passenger seating, and they are angled to stop water ingressing back up into the pipes.
“In cars, you can just mount the packs at the undercarriage, so offgassing starts outside the passenger compartment, but electric boats could suffer a dangerous pressure build-up of gases if you don’t design this kind of venting system,” says Helmberger.
As discussed with Scania’s Tony Persson (EME 23, January/February 2024), the battery packs in the next-gen Macan powertrain use prismatic Li-ion cells, which, for the Porsche cars, and hence the eFantom, contain an 8:1:1 ratio of nickel versus manganese versus cobalt. This contributes to energy density, as well as the charging capacity of the battery: DC fast charging at 250 kW can be used, enabling the pack to be replenished from 10% to 80% SoC in times estimated as less than 30 minutes, depending on various factors.
The aforementioned Integrated Power Box is a patent-pending invention, designed to reduce cabling and weight (and hence cost) in the powertrain by combining the 11 kW onboard AC charger, a HV PTC heater and the
DC/DC converter (which converts the battery’s 800 V output to a 12 V bus for cabin systems and other items in the low-voltage network).
The PTC heater is not programmed for use in the eFantom as customers will essentially never take their yachts out in extremely cold temperatures, but the team opted not to remove it as they wanted as many unaltered components from the Macan as possible.
The Integrated Power Box uses a CCS2 socket for use of both AC and DC charging in a combined connector input. This provides simplicity for the customer as it facilitates the use of almost any sort of charger plug. It also helps reduce excess complexity in determining where the engineers would need to deliver coolant in the thermal management system.
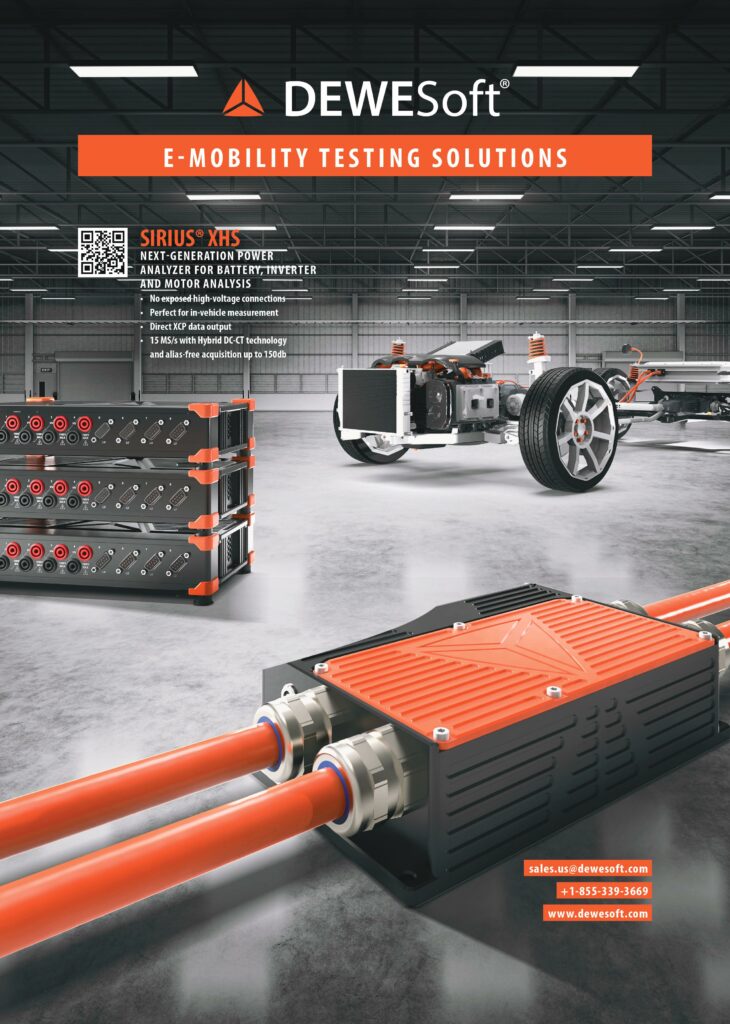
Thermal management
As discussed, an active liquid cooling system thermally manages numerous powertrain components. It functions using two coolant pumps, each one driving a separate water-glycol channel; one of those runs in the motor and inverter, while the other runs in the battery pack and the Integrated Power Box (the latter including the DC fast-charging connector).
Thermal readings from the motor, inverter, battery modules and ambient water are used by the eVCU to calculate cooling pump speeds. For the drivetrain circuit, water-glycol runs from the pump into the inverter first and then into the motor.
The two circuits are completely separated save for an expansion tank. In addition to the two pumps there is a third one, which the team refers to as the seawater pump; it typically sucks water and propels it onto a pair of water-to-water heat exchangers.
The water-glycol internal coolant runs inside those, with each heat exchanger carrying one of the two aforementioned cooling channels, so the heat from those runs into the heat exchanger, into the water and hence into the lake/sea.
Helmberger adds: “That pump draws water from three apertures in the Z-drive to ensure consistent thermal management, even during high planing. Our hull is a stepped hull, which means a lot of air can pass under the hull when the boat picks up speed. Placing the water aperture elsewhere could mean less cooling and more heat losses at high-power outputs.”
While the powertrain is configured to manage a refrigerant cooling circuit, as in the next-generation Porsche Macan, a standard water-glycol system was chosen for efficiency, as well as the availability of parts.
In addition to that cooling system, the BMS monitors at cell level for where currents and other parameters can be controlled for thermal stability. Porsche found no modifications were needed for the BMS to transfer from the Macan over to the eFantom.

Hull construction
The outer hull is unchanged from the 858 to the 850 eFantom, and hence it has the same hydrodynamics, which have been optimised as a compromise between the gentle cruises and short bursts of speed expected from its user requirements. The internal hull, however, was modified to accommodate components such as the battery, which Helmberger notes has a layout completely unlike the 858’s fuel tank, engine, or both combined.
“The fuel tank, for instance, is usually situated behind the seating area and below deck, and is built with a vee shape to conform with the hull and keep the CoG as low as possible,” he explains. “So, while Porsche couldn’t use the engine or tank compartments, there was a space under the deck floor, typically used for storage or just left empty, and that’s now used up by the battery.
“To also accommodate the battery, we put stringers made out of GRP [glass-reinforced plastic] to precisely house-in the pack. Those kinds of stringers are normally used to mount and damp the engine and fuel tank, and to prevent them affecting the stability of the hull, but we modified the stringer arrangement heavily to integrate the battery. That included making them less high up, smaller and closer together for less empty space, to provide the same hull stability, because we’re going roughly the same speeds as we do with the 858’s highest-power petrol engine.”
The rest of the hull is also predominantly GRP (aside from some leathers and woods chosen for aesthetics in the passenger area), with an anti-fouling coating on the outer hull below the waterline, as standard among boat-makers.
“To construct the hull, we start with a negative mould made of the same material,” says Helmberger. “The first component into that mould is the
anti-fouling coating, and then each layer of GRP is laminated into that by hand. After laying those, the mould and hull are heated and cured to finish, and the piece is finally removed via air pressure from the mould.
“Lastly, the shell coating gets sanded down to a precision finish for hydrodynamic shape, symmetry and aesthetics – a very labour-intensive process – and then the hull is styled in marine paint, according to customer requests, with typically 11 layers of paint for the ideal finish.”
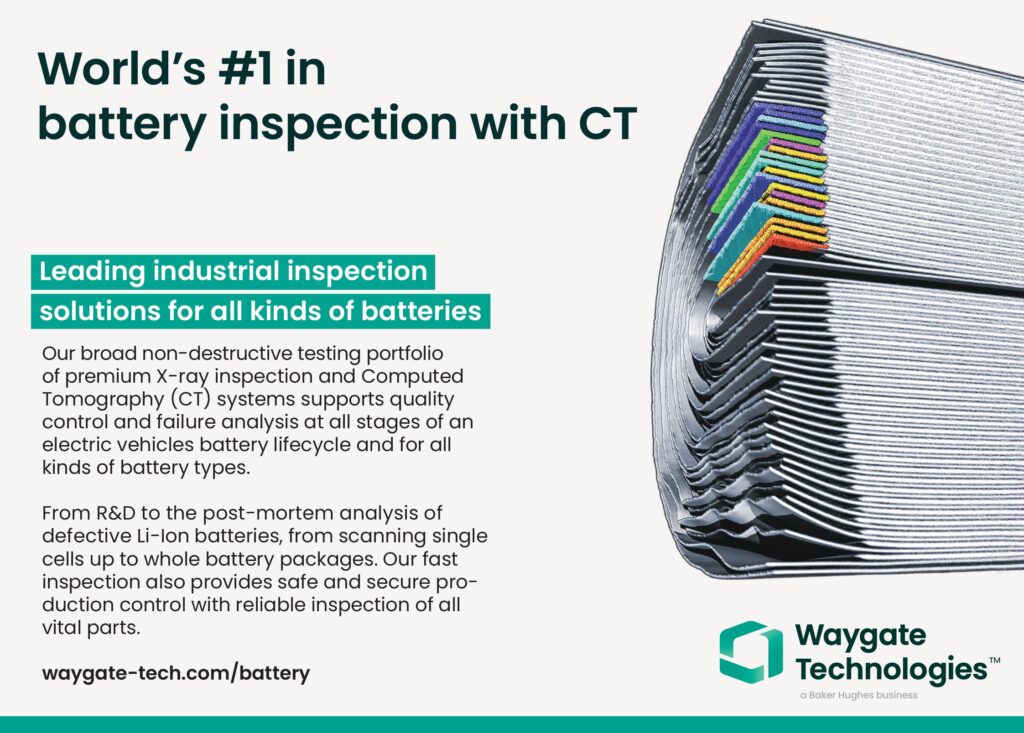
Firm future
In addition to the first commercial deliveries starting this year, the boat was displayed in its first major public event showcase at Boat Dusseldorf in January. Both companies were present and discussed technical aspects of the boat with the industry and market.
Porsche declined to comment on the exact or potential number of eFantom units to be produced, but it emphasised that its collaboration with Frauscher thus far has been intended to establish a functioning business model to carry into the future, and it will not be simply a one-off collaboration in the history of e-mobility as it is written.
Key specifications and suppliers
Frauscher x Porsche 850 Fantom Air (or eFantom)
Powerboat
Battery-electric
Dry weight: 2,800 kg
Length x width: 8.67 x 2.49 m
Clearance height: 1.35 m
Draught: 0.5 m with trim raised, 0.9 m with trim lowered
Maximum continuous power: 170 kW
Peak power: 400 kW
Energy capacity: 100 kWh
Maximum speed: 85 kph (46 kts)
Cruising speed: 41 kph (22 kts)
Maximum range between charges: 45 km at cruising speeds and over 100 km at displacement speeds
Endurance between charges: two to three hours, depending on driving profile
Driver interface: Raymarine
Z-drive: MerCruiser
Hull design: Kiska
ONLINE PARTNERS
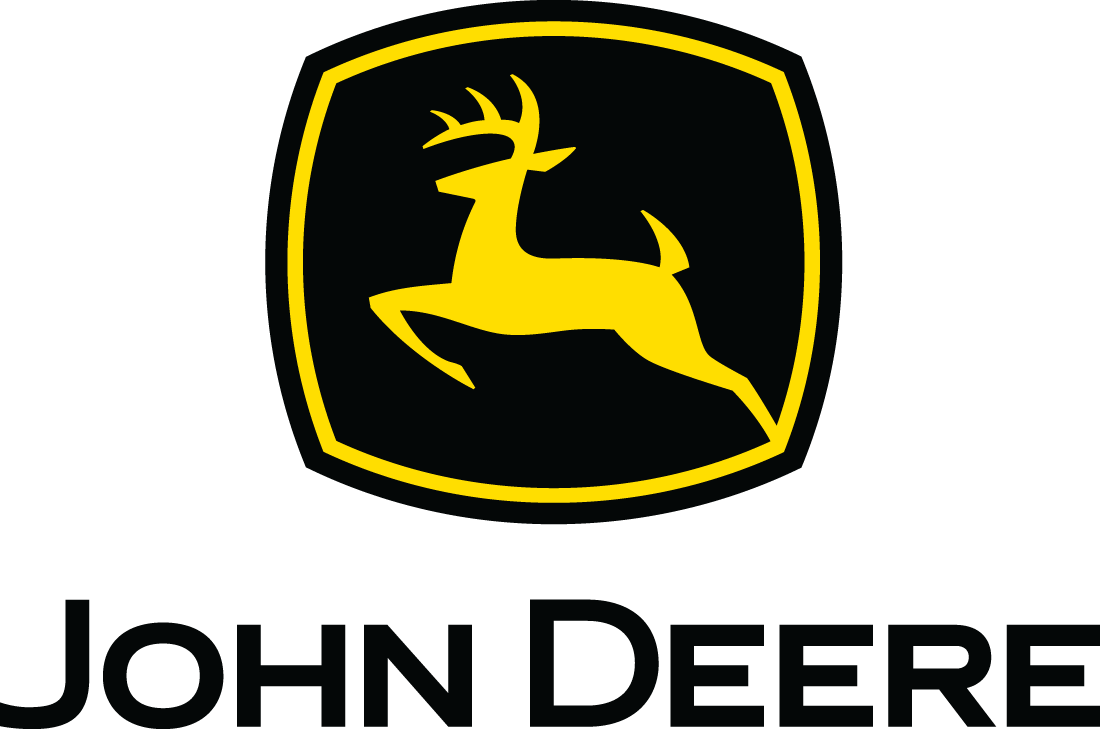
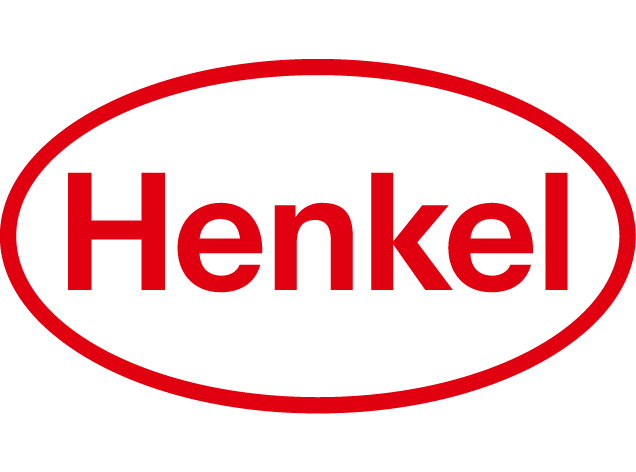
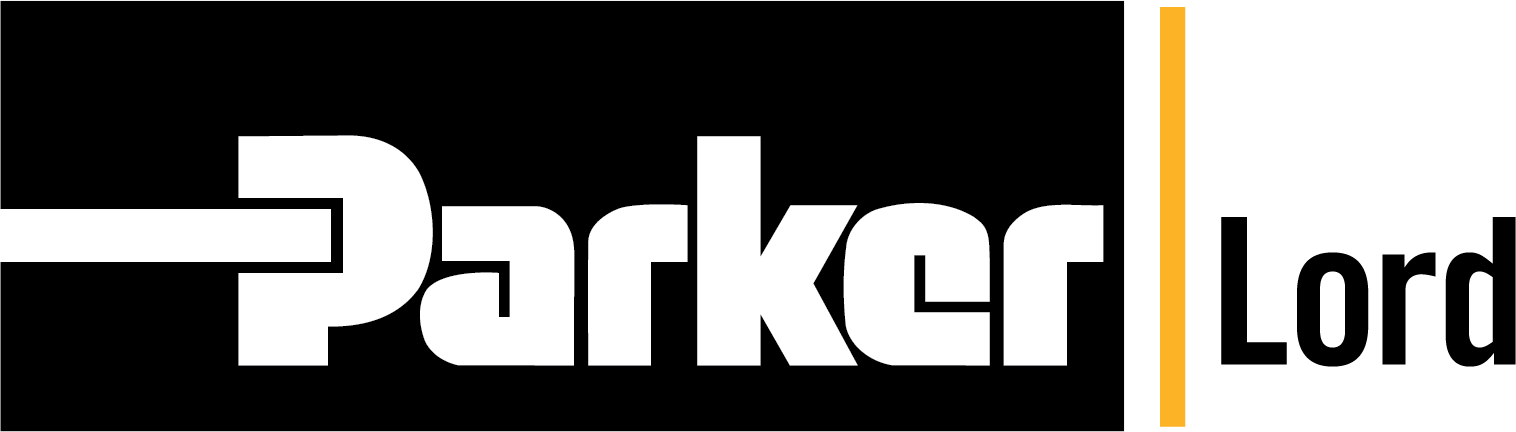
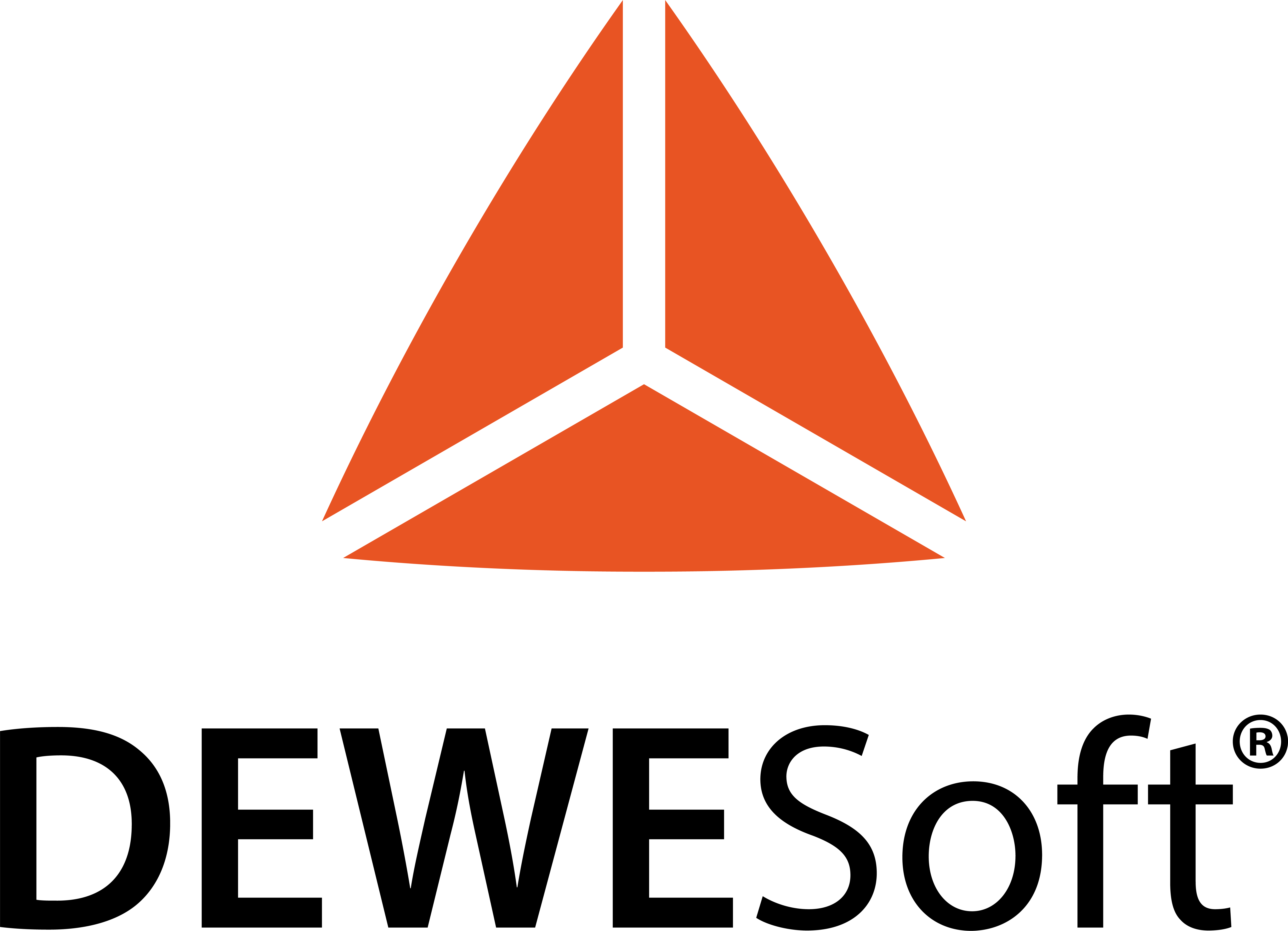
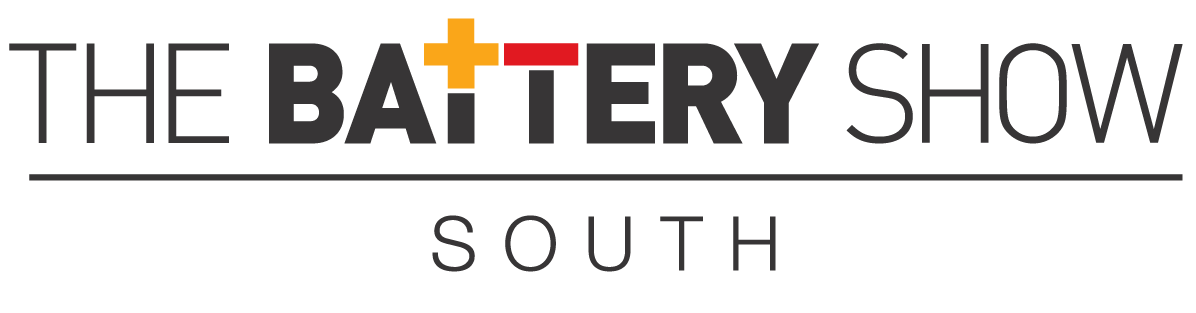
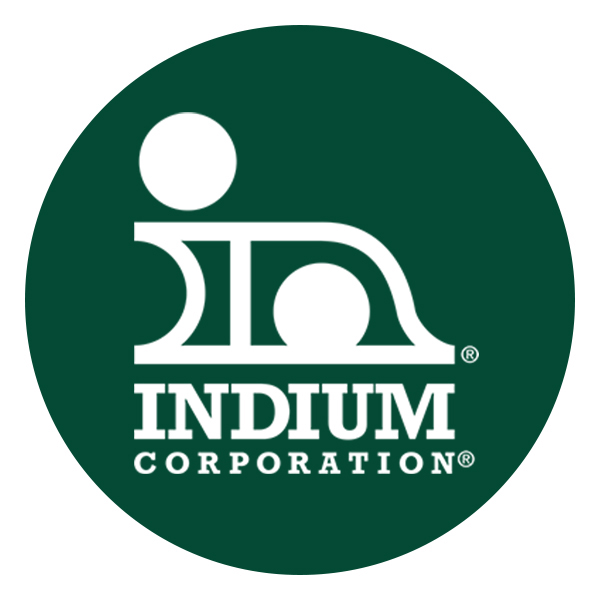

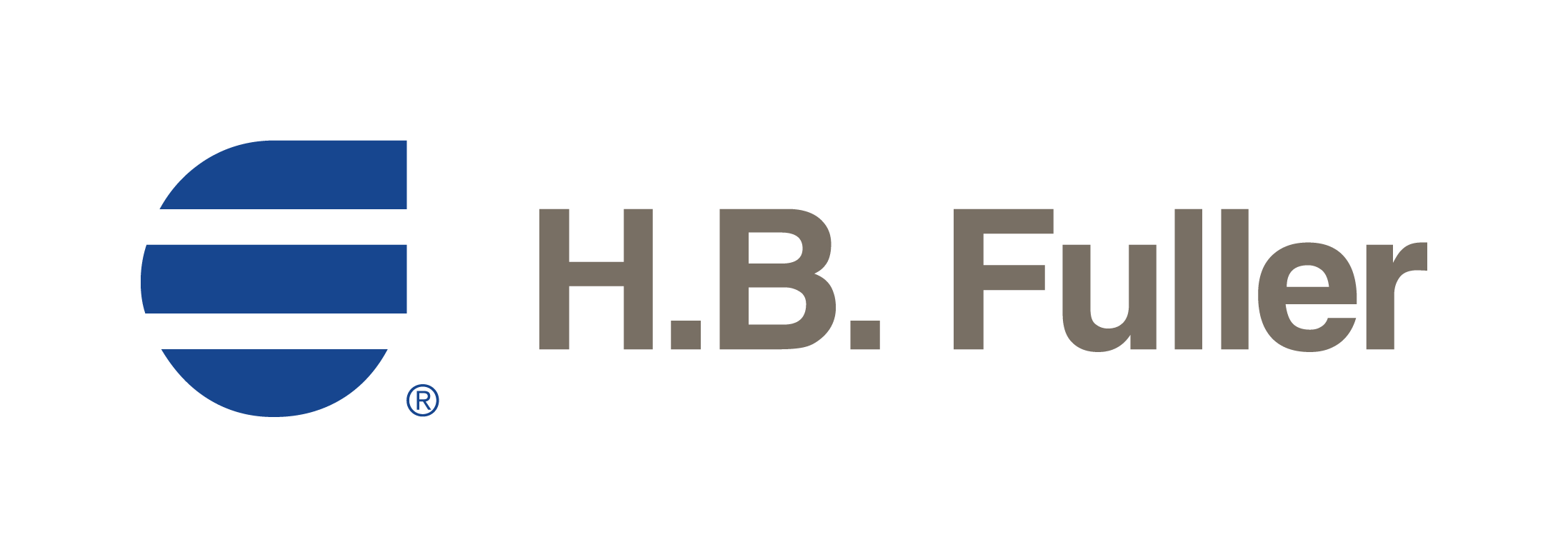
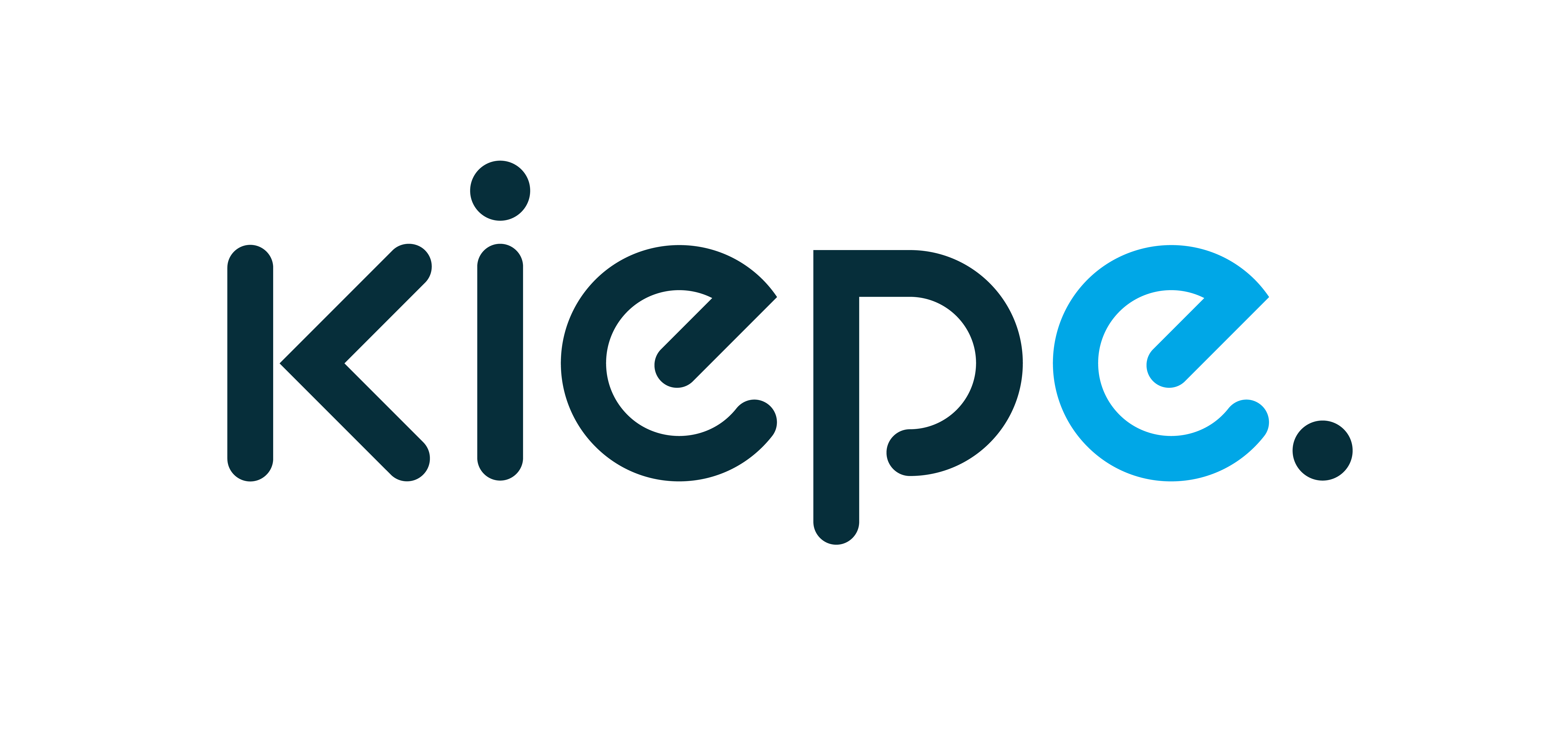
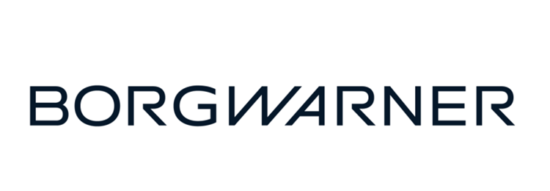