RS Electric Boats Pulse 63
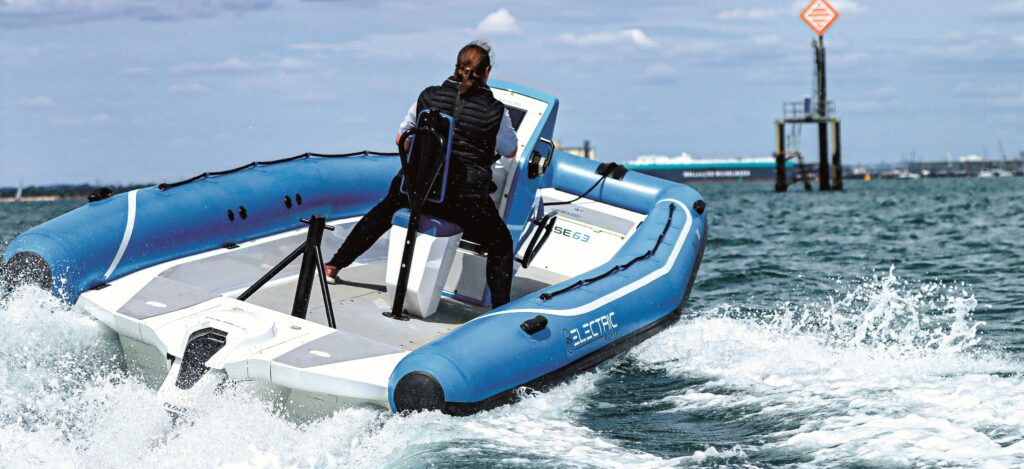
(Image courtesy of RS Electric Boats)
Smooth operator
Peter Donaldson explores a new generation rigid hull inflatable boat that obtains benchmark performance from electrical energy
While sailing is emissions free, the IC-engined boats that regularly support sailing events and training operations tarnish that clean image somewhat. This led the principals at RS Sailing, now part of the RS Marine Group, to begin development of an electrical Rigid Hull Inflatable Boat (RHIB) in 2018, incorporating a new company, RS Electric Boats. The resulting Pulse 63 is now operational in its intended role as a sailing coach boat and is also offered as a work boat, a leisure boat and a superyacht tender.
Cathedral hull
Alex Newton-Southon, co-CEO at the RS Marine Group, explains that the Pulse 63 is a clean-sheet design, with the rigid part of the hull optimised for electric propulsion. This means prioritising the reduction of hydrodynamic drag at the boat’s intended operating speeds and accommodating a large battery pack without compromising stability or space on board.
The basic hull form is of the ‘cathedral’ type. A cathedral hull has three distinct elements that include a central V-shaped main portion with a slimmer, shorter sponson on either side, forming a tunnel between each sponson and the central portion. As with all RHIBs, the entire hull structure is rigid, while extra buoyancy is provided by air tubes inflated to high pressure that effectively form the gunwale.
This is a ‘planing hull’ meaning it is more efficient and easier to get up on the plane compared to a comparable flat-bottomed hull. This design also significantly reduces the slamming action to which flat hulls are prone while also tracking better, characteristics that respectively improve ride quality in rough water and reduce steering workload. Cathedral hulls are known for good combination of speed, manoeuvrability and ride quality, as well as energy efficiency, with the V-shaped central hull portion reducing drag at higher speeds.
Cathedral hulls also offer high initial stability as well as good secondary stability. Initial stability refers to the vessel’s ability to resist tipping or rolling when it is in a static, level position on calm water; effectively when it is not subjected to external forces, such as waves or wind. This is important because it affects the comfort and safety of passengers and crew, particularly during boarding, or while fishing, or other on-deck activities when the boat is at rest.
Several factors influence initial stability, including general hull shape, with broad-beamed boats, offering good high resistance to tipping, which is also helped by high freeboard (the distance between the waterline and the deck), and high buoyancy. Weight distribution is also an important factor here, and placing heavy components such as, in the case of the Pulse 63, the battery pack lower in the hull contributes to a lower centre of gravity, again contributing to greater initial stability.
Secondary stability applies when the boat is in motion or encounters dynamic conditions, such as waves or turns; this determines its ability to resist further heeling once it has started to heel. Good secondary stability is crucial for maintaining control and comfort in varying sea conditions.
There is often a trade-off between initial stability and secondary stability in that high initial stability might make the boat more prone to tipping in dynamic conditions, and that some design decisions conflict to a certain extent. For example, a higher centre of gravity can increase secondary stability while reducing initial stability. The ideal combination depends on how the boat is intended to be used.
Displacement and planing efficiency
The engineering team stresses that the main requirements for the Pulse 63’s hull included high efficiency both at displacement speeds and at planing speeds. Also to have space for the batteries inside the hull with weight in the right place in the boat for optimum trim.
It is also designed to maximise displacement while minimising the amount of hull below the waterline. The term ‘displacement’ refers to the weight of the water that the hull pushes aside when afloat. The displacement speed is the speed at which the length of the bow wave equals the length of the hull’s waterline, and is effectively the maximum speed that the hull can achieve without planing.
The cathedral hull form is a good way of maximising displacement while minimising the amount of hull below the waterline; boats with higher displacement-to-length ratios often exhibit better efficiency at lower speeds. Relatively high displacement can also result in better load-carrying capacity and stability than comparable boats that displace less.
“With a cathedral hull, the boat is pushing a lot less water at displacement speeds and also gets up on the plane really nicely at a speed as low as 8 knots where a more conventional hull would do so at about 12 knots,” Newton-Southon says.
The rigid part of the hull is constructed of laminated composite materials including carbon fibre and glass fibre, which reinforce an epoxy resin matrix. The construction method that RS Electric Boats chose is resin infusion moulding, in this case using reusable silicone vacuum bagging, according to the company’s engineering team.
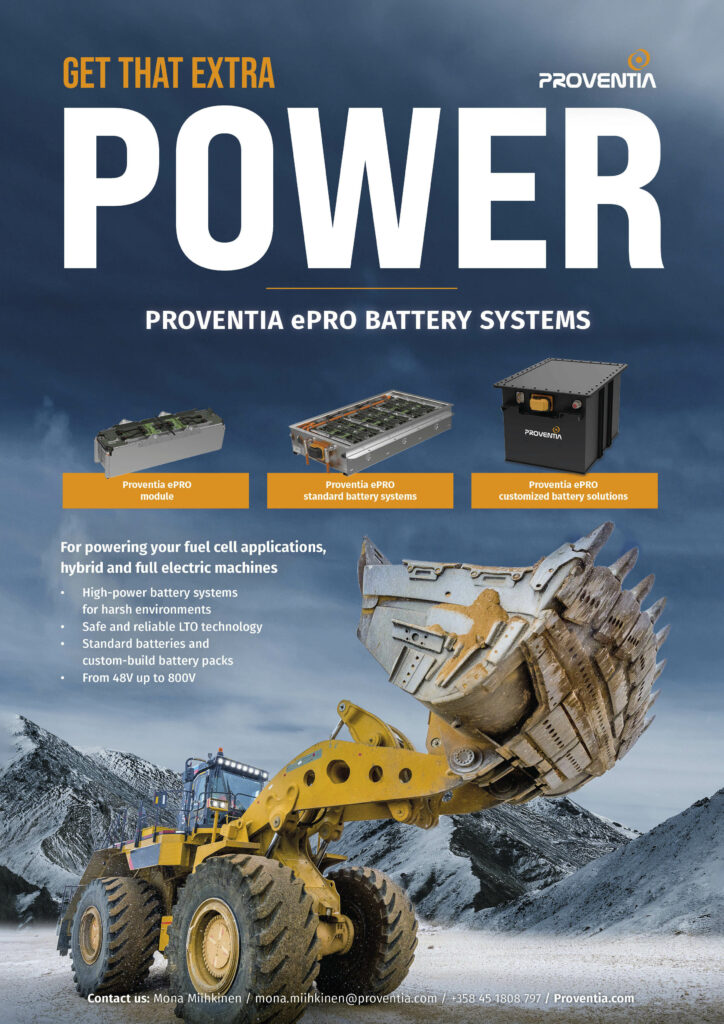
Infusion moulding
Resin infusion moulding starts with the construction of a mould, which is polished and coated with a release agent to ease extraction of the final part. Dry fibre reinforcement cloth is then laid out in the mould in precise orientations and thicknesses to yield the required strength and stiffness in the final part, often with foam cores for spacing and extra stiffness/strength.
Next, a vacuum bag and a network of resin distribution tubes are placed over the dry fibres in the mould, creating a sealed environment with a means of getting the resin everywhere it needs to go. Then a liquid resin, usually a two-part resin and hardener, is drawn into the fibres and air is expelled using vacuum pumping. The part is then left to cure for a predetermined time at a controlled temperature before being removed from the mould and trimmed around the edges.
This process is well suited to complex shapes and yields parts of consistently high quality with good material properties and, often, lower weight than parts made using other processes. Infusion moulding also produces lower emissions and less waste than comparable processes.
Reusable vacuum bags made from a silicone material as used by RS Electric boats eliminate the waste associated with disposable bagging. Further, the foam cores are partly made from recycled polyethene terephthalate (PET) plastic bottles. As an option, the company also offers consoles made from a plant-based composite material that uses flax fibres for reinforcement.
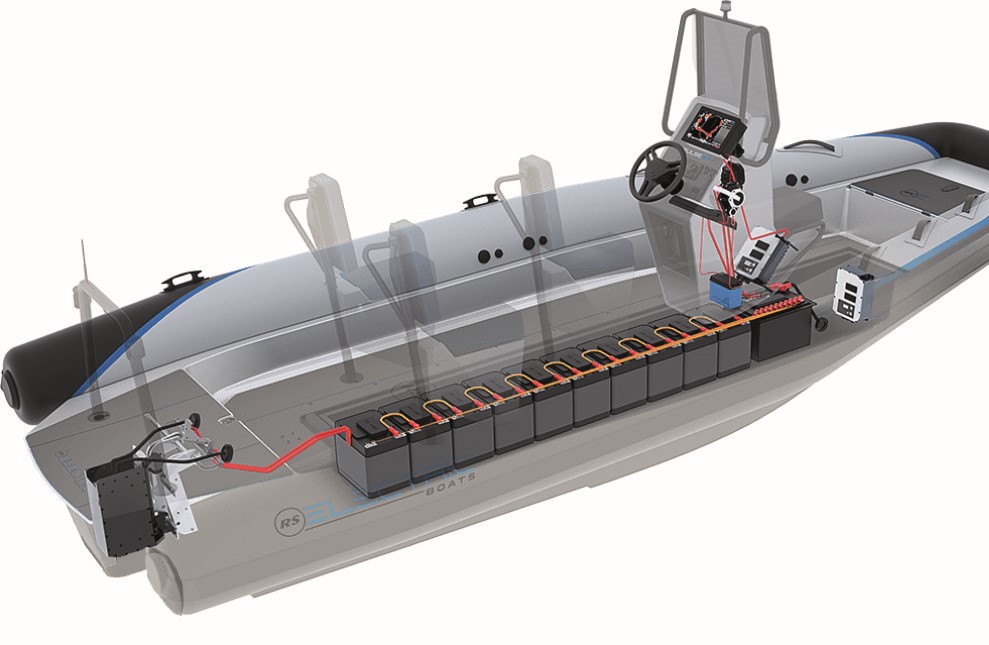
(Image courtesy of RS Electric Boats)
Optimised battery placement
From a trim and weight point of view the decision was taken to place the batteries inside the central portion of the hull. “We’ve seen that a lot of people have taken a RHIB and just put the batteries at the back of the boat on the deck, which then affects the trim so that the boat is just sort of pushing water and having the weight so high makes them much more unstable. We’ve designed it to have the battery pack under the floor and we can then distribute the weight exactly where we want it to get the trim of the boat right,” Jon Partridge co-CEO of the RS Marine Group adds.
“If people wanted extra seats on the boat, then we’d move the battery pack forward a little to counteract that change in weight distribution.”
To protect the pack from water ingress, it is doubly encapsulated, Partridge explains. The pack itself is a sealed unit, and it is installed in a sealed metal battery box with internal reinforcing structure. The box is watertight, marinised and protected from the ingress of contaminants to the IP54 standard.
“No water will be able to get into the actual batteries even if the deck flooded and it managed to get into the battery box. It can take about 30 or 40 litres before the water even touches the pack, and even then it won’t be an issue,” Partridge says.
Integrated into the pack, the BMS has a major safety role in monitoring temperatures and, ultimately, shutting the battery down if it senses a temperature trend that indicates an incipient thermal runaway.
The initial series of Pulse 63s were fitted with a 400V, 46 kWh Gen4 modular lithium-ion battery pack from Hyperdrive (now Turntide) designed to be recharged 2000 times to more than 85% capacity.
Each module is individually controlled, conditioned and managed through a power distribution unit (PDU), and can be monitored through the RADlink datalink from RAD Propulsion, which supplies the boat’s electric outboard drive system. The physical integration connects 10 modules in a fore-and-aft line, with the 12V service battery ahead of the foremost module and separated from it by a bulkhead.
More than a datalink, RADLink is described as a smart and connected vessel control unit that implements the NMEA 2000 standard. According to the US National Marine Electronics Association, NMEA 2000 describes a low-cost moderate capacity bi-directional, multi-transmitter/multi-receiver instrument network to interconnect marine electronic devices.
The boat also has an onboard charger rated at up to 6.6 kW, plus infrastructure to accept CCS DC fast charging, which is becoming more common around marinas and harbours. On average, such fast chargers deliver up to 75 kW, Partridge notes, adding that a 20% to 80% charge takes around 25 minutes, whereas zero to 100% takes about an hour.
Liquid cooling
The battery pack is liquid cooled, using a pumped water ethylene glycol mix that passes through a heat exchanger. Also liquid cooled, the inverter uses silicon insulated gate bipolar transistor (IGBT) switching technology and delivers up to 40 kW. The propulsion motor could be described as liquid cooled, but only by virtue of being in the water in a housing that has a large surface area exposed to the water, providing all the heat transfer capability the motor needs.
Later production vessels will have a new bespoke battery pack. Rated at 63 kWh, the new pack is also smaller and lighter and has both the BMS and the PDU inside it. This will be fitted into a modified hull with a smaller battery compartment, the engineering team says. Also a 400V system, the new battery uses CCS2 charging.
Enter the RAD 40
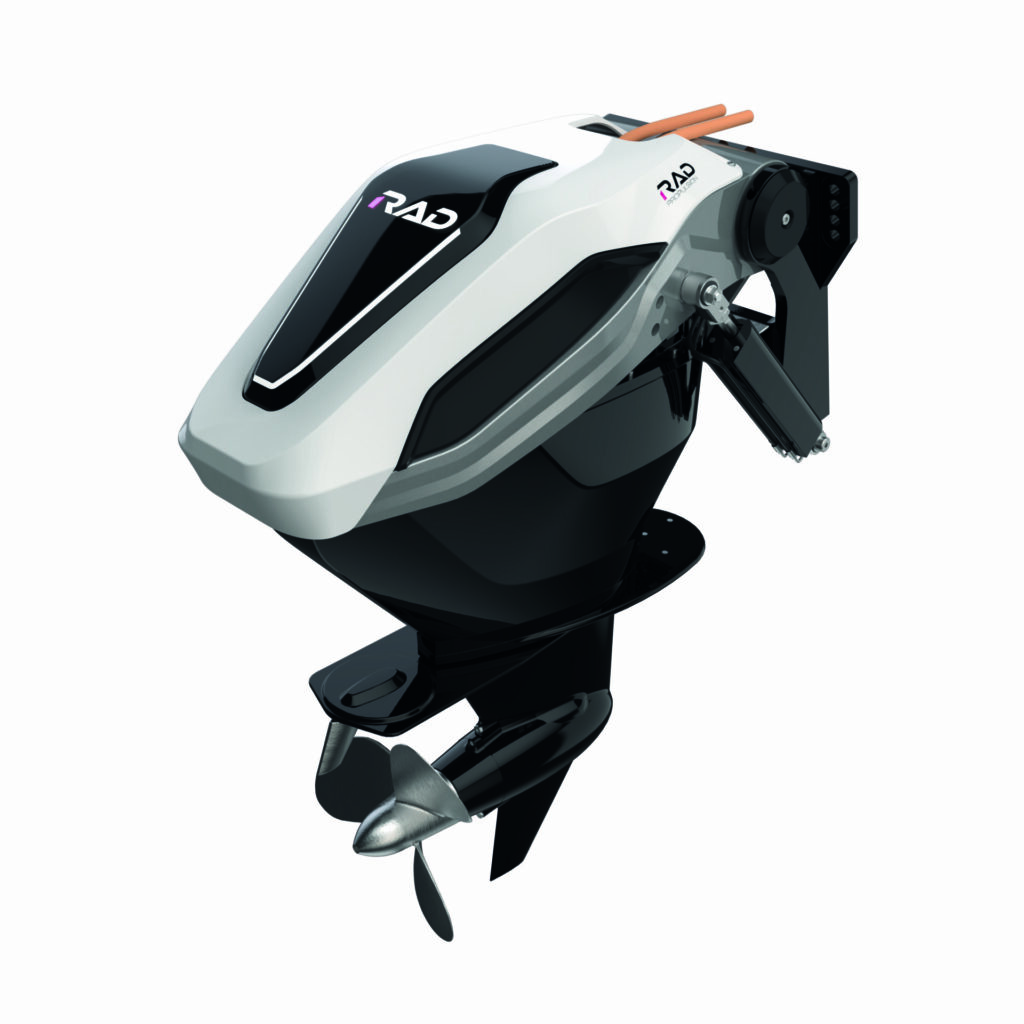
(Image courtesy of RAD Propulsion)
Getting propulsive power into the water is the function of the RAD 40 drive. RS Electric Boats has been working with RAD Propulsion almost since the inception of the Pulse 63’s development. Initially, RAD developed a ‘rim drive’ propulsor for the boat, an idea that the company explored and then shelved as far as this application is concerned. In a rim drive thruster, the blades are mounted on the inner portion of the rim and point towards the centre of the thruster, which has no hub. The rim also forms the rotor of the electric motor that powers the thruster. “It was good and efficient at the low end of the speed range, but didn’t quite have the top-end speed that we needed,” RS Electric Boats’ engineering team explains.
The companies then experimented with a number of drive configurations using Mercury stern drives but these also lacked the efficiency necessary to achieve their top speed target with the power available. “We were only getting a top end of 16 or 17 knots.”
The Pulse 63s currently in service use these stern drives, but boats are today being delivered with the RAD 40 system, now testing of that system is complete.
The RAD 40 was the solution to the challenge of attaining the required speed. Resembling a compact outboard motor, this system packages a RAD-manufactured electric motor that drives a custom-designed three-bladed propeller into a compact unit along with electric steering and trim systems. The entirety of that unit remains behind the boat’s transom when tilted up out of the water. At the heart of the tilt system is a pair of hydraulic rams that are fed pressurised oil by an electrically-driven hydraulic pump.
The RSE engineering team notes that the RAD 40 is around 50% more efficient than any of the stern drive systems previously tried. “We now get 23 knots out of it on the same power as before,” they say.
Weighing 60 kg, the RAD 40 measures 732 mm long, 401 mm wide and either 956 mm or optionally 1106 mm deep. This compact footprint maximises usable space. “It’s neat and doesn’t interfere with the hull too much. We still have a flat area at the back, which you don’t normally get if you’ve got a great big outboard in the way,” they add.
Delivering up to 40 kW continuously, the system works more like a podded drive than a conventional outboard motor in that the lower section supporting the propeller is steered while the upper portion (the head unit) remains stationary with respect to the hull in azimuth, although the trim actuators are attached to it. The 300 mm diameter propeller steers through +/- 90°, giving the boat greater low-speed manoeuvrability than most, even enabling it to spin around within its own length.
Both steering and throttle use drive-by-wire control, while the throttle provides responsive forward and reverse control, a neutral safety mechanism and illuminated indications of trim and tilt settings.
Drive-by-wire smarts
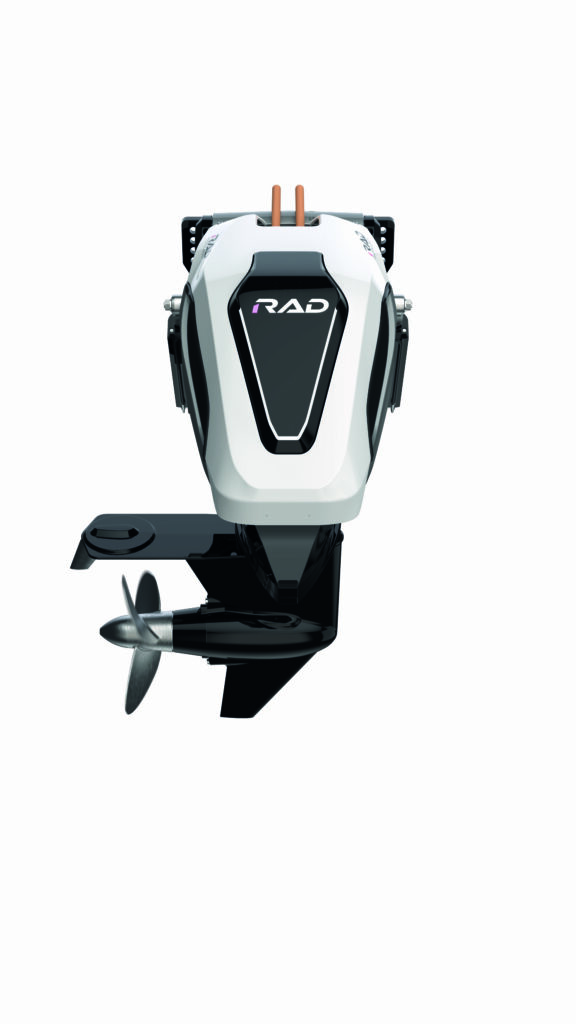
(Image courtesy of RAD Propulsion)
The safety benefits and weight savings enabled by drive-by-wire technology were major factors in the company’s selection of RAD’s technology. In operational terms, some of those safety benefits come from the throttle’s programmability in that the power can be limited for certain users, and calibrated at the owner’s request.
From a skipper’s point of view, the smart throttle is quite different from conventional throttles, according to Jon Partridge, and the differences stem from ergonomic, mechanical and software design features. A conventional boat throttle lever is mechanically linked to both forward or reverse gear or pitch change mechanisms with a neutral position in the middle of its fore-and-aft travel. Partridge explains that the Pulse 63’s smart throttle moves in the same sense, but includes a spring-loaded neutral detent that engages as the lever reaches the centre position.
“As it is an all-electric system it feels super smooth and light,” Partridge remarks. “There are no gears in the system, so going from forwards into reverse and back is much better for it than with a conventional outboard, with which you would be crunching through gears; with this you are not, so it feels almost effortless.”
Significant development effort went into programming how the motor responds to the throttle to improve the boat’s controllability. The instant torque of the electric motor was a problem at first because it effectively generated too much response to initial movement of the lever. “It has been programmed to be much more gradual at first and to build up the power progressively when you throttle it up”, Partridge adds.
The trim controls are also on the throttle, enabling the skipper to raise the propeller to clear the bottom in the shallows and to lift it completely clear of the water. This is an advantage if the boat is to be left in the water overnight as it minimises marine growth on the propeller, for example, which is an important way to reduce the need for cleaning and related maintenance.
Most RHIBs and other small powerboats feature a ‘kill cord’ attached to the skipper and the ignition that will stop the engine if the skipper falls overboard. The version used on the Pulse 63 is a RADTag that attaches magnetically to the tag point and cuts the power to the propulsion motor when it is pulled off the magnet.
Partridge says that the RADTag also serves as the boat’s key and is programmable for individual users. “Say you are at a sailing club and there are certain coaches who go out in the boat and you want to limit them to 10 knots, for example. You can program the tag so that it will tell the smart throttle to let the boat do no more than 10 knots.”
The system can also be used for geofencing, making sure that the boat cannot enter prohibited areas and that selected users cannot take it beyond set boundaries, for example.
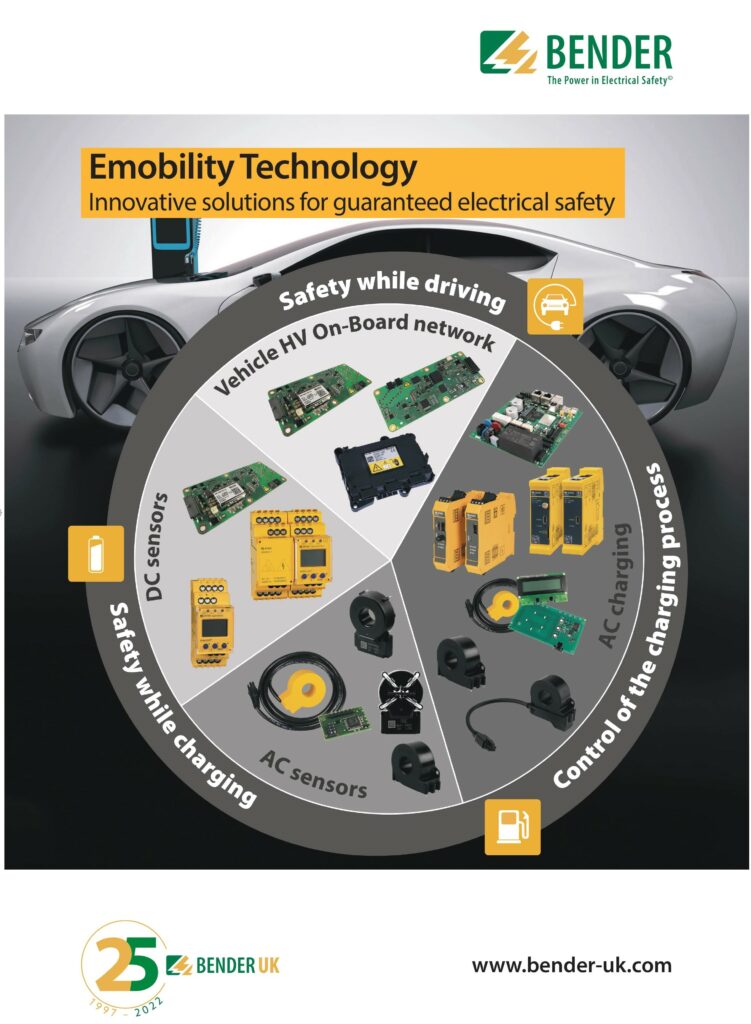
Safety signal lights
The throttle is also linked to a set of safety signal lights on the back of the drive unit positioned to be visible to anyone in the water behind the boat, warning them of the status of the propulsion system to minimise the risk of contact with a spinning propeller. If the lights are white, that means the tag is off and it is safe, meaning that if someone knocks the throttle, nothing will happen, Partridge explains. If the tag is attached, the lights flash purple to indicate that while the propeller is not spinning, if someone knocks the throttle the propeller will start to spin. Constant pink lights indicate that it is not safe to approach the boat because the propeller is spinning.
All aspects of the drive and battery system are connected to RADBus, RAD’s CAN based control and data network that also enables monitoring of all components to help ensure user safety.
Like all the nodes on a CAN bus network, the throttle has a ‘heartbeat’, which is a periodic message that serves as an indicator of the system’s health and status. It is through the RADBus network, for example, that the throttle communicates with the safety lights, as well as core propulsion system components such as the inverter that drives the motor.
Pulse 63 also has a real-time range calculation system built with technology from RAD Propulsion and Metron-EV. “On the screen it will tell you how much time and distance you have left at your current throttle setting and speed,” Partridge says.
RAD has also announced that it will use the RADBus network as the infrastructure into which it will integrate more advanced features.
Cheetah Marine also offers a version of the Pulse 63 (R630) hull for customers who are not quite ready to commit fully to electric propulsion, Jon Partridge reports. “We have made this a very much cheaper version with a standard combustion outboard motor on the back, but the fuel tanks, etc in the place that the batteries would be on an electric version.The idea is to sell the hull and then, a few years down the line, convert it, or else the customer can trade it in for a fully electric RHIB.”
Partridge argues that even with an IC-engine outboard, the efficiency of the hull still reduces carbon emissions so that is a step in the right direction.
The next big project, he says, involves the conversion of 7.9 m and 8.9 m Cheetah catamarans to electric power for commercial operators, with 20 such conversions (seven Cheetah catamarans and 13 Pulse 63 RIBs) funded by an Innovate UK grant. The purpose of the grant is to create a network of electric boat services across the UK for use by, for example, harbour masters, boat clubs, survey operators and the Environment Agency.
Pulse 63 key specifications
Top speed: 23 kt
Max range: 100 nm
Average speed v range:
5 kt – 100 nm, 10 kt – 60 nm,
15 kt – 45 nm, 20 kt – 30 nm
Length: 6.3 m
Beam: 2.3 m
Weight: 815 kg
Capacity: up to 6 adults
Some key suppliers and partners:
Outboard electric drive:
RAD Propulsion
Development partner: Cheetah Marine
ONLINE PARTNERS
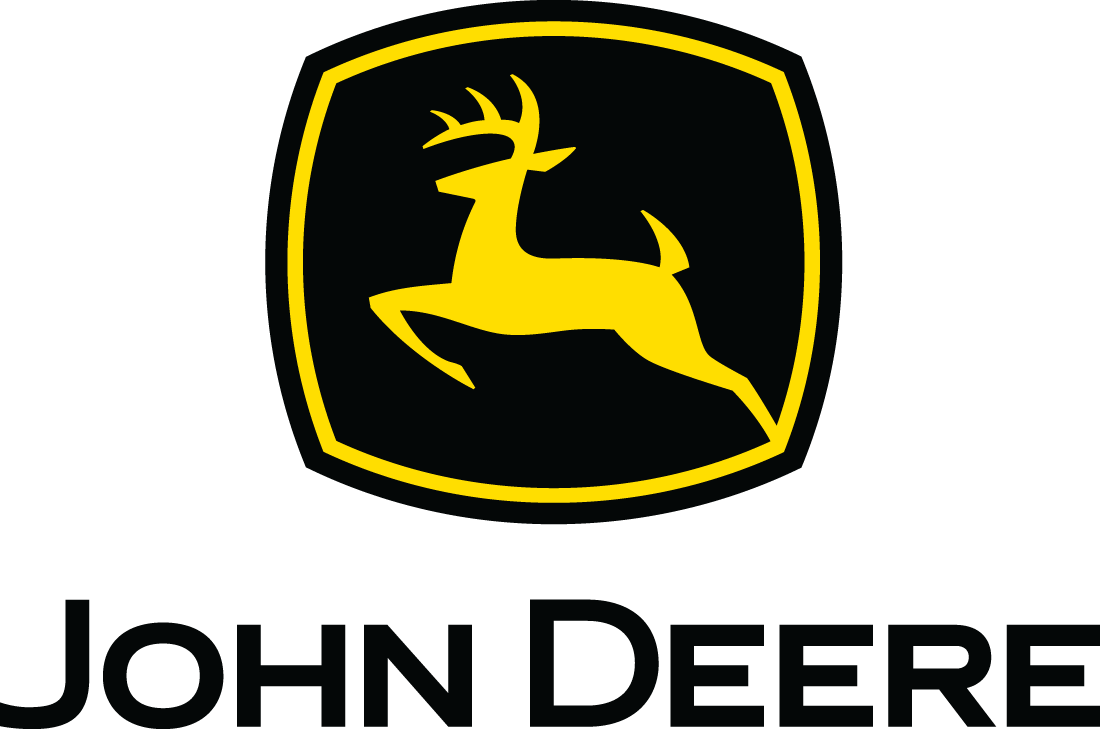
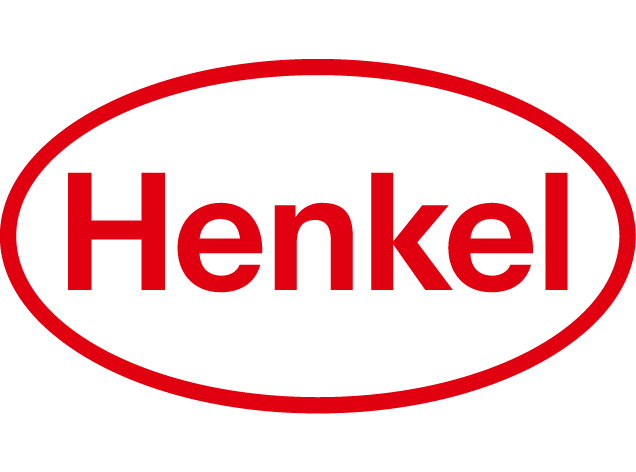
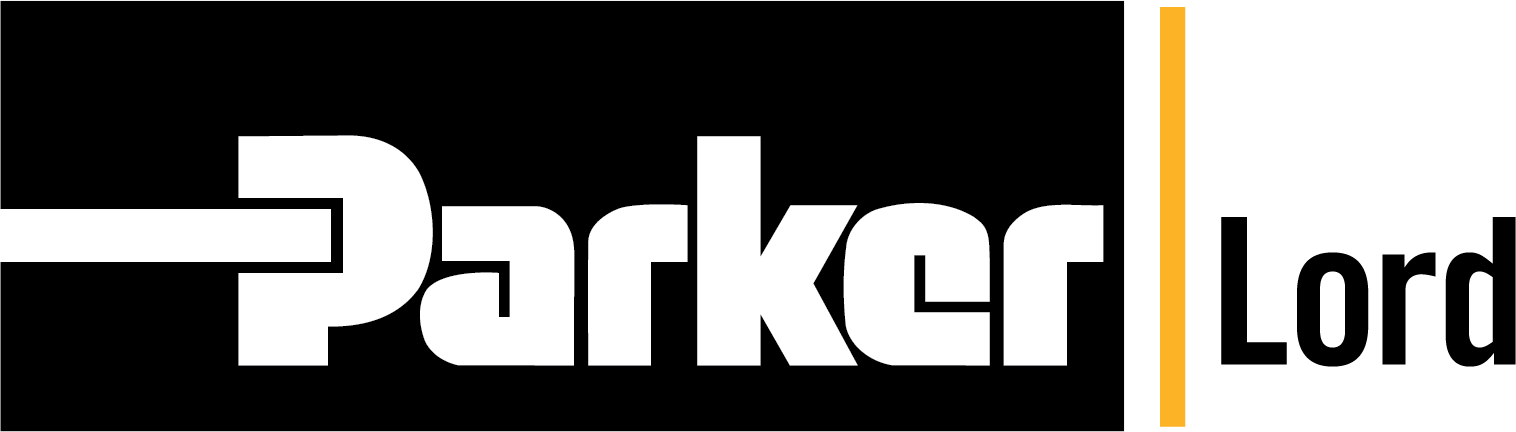
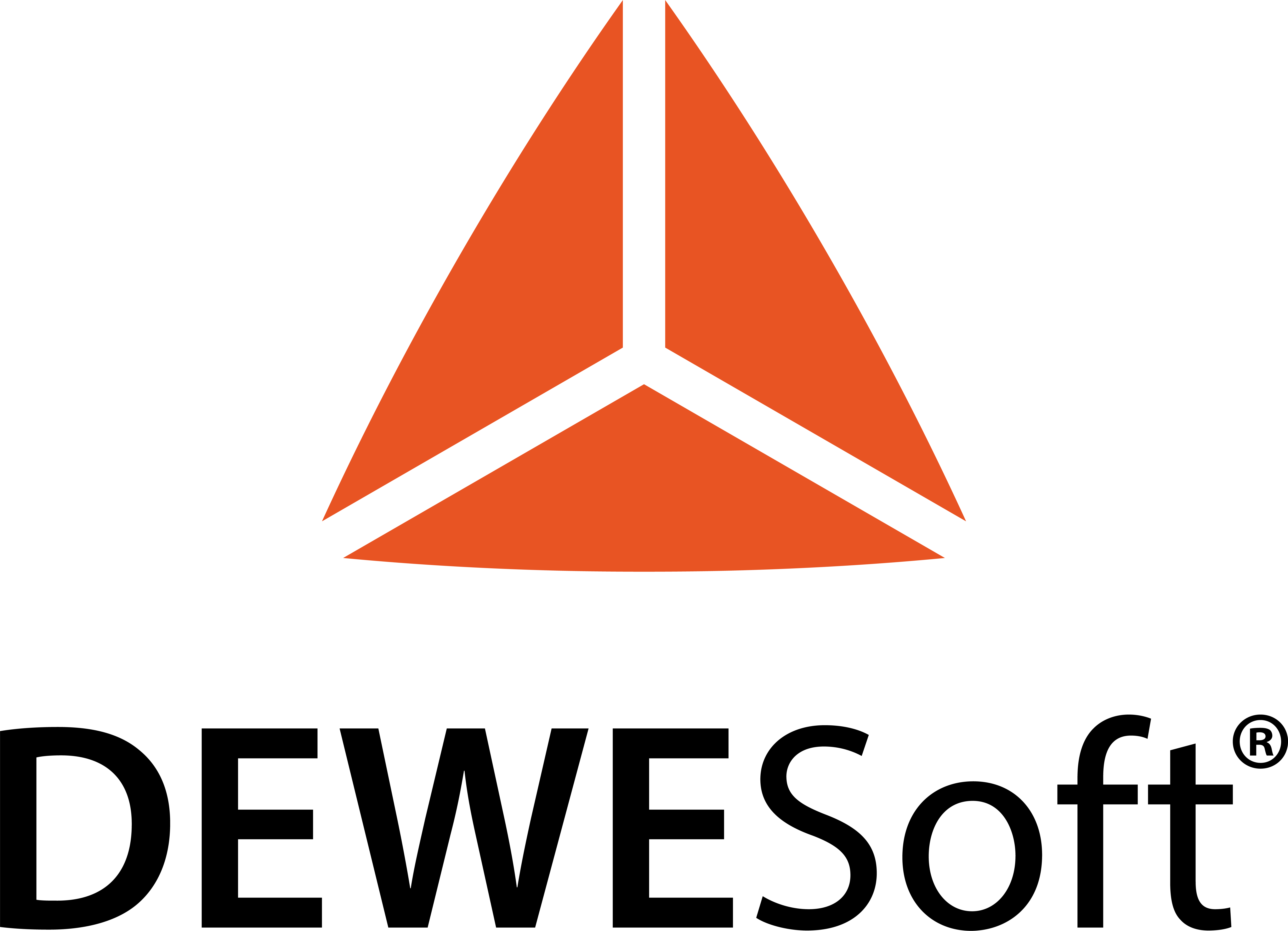
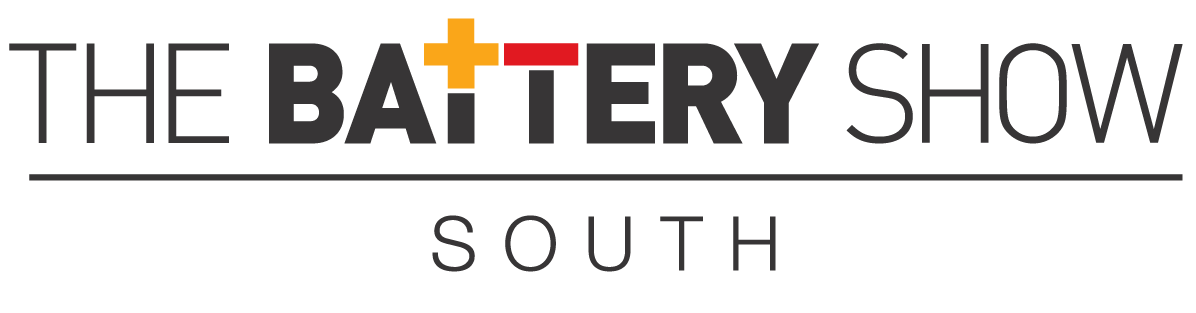
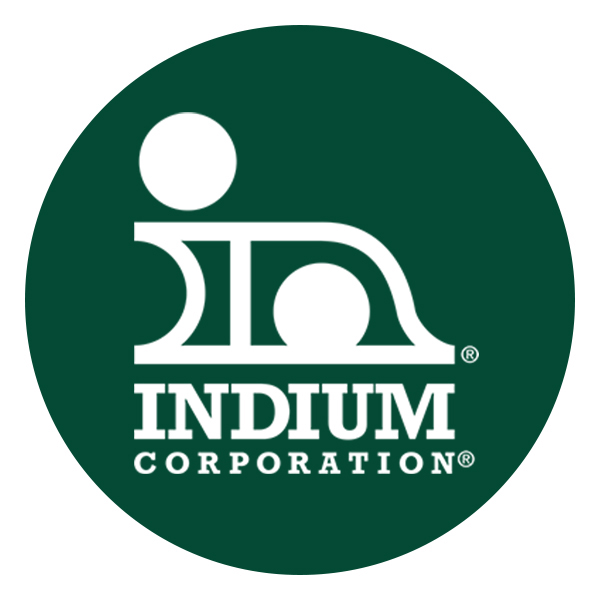

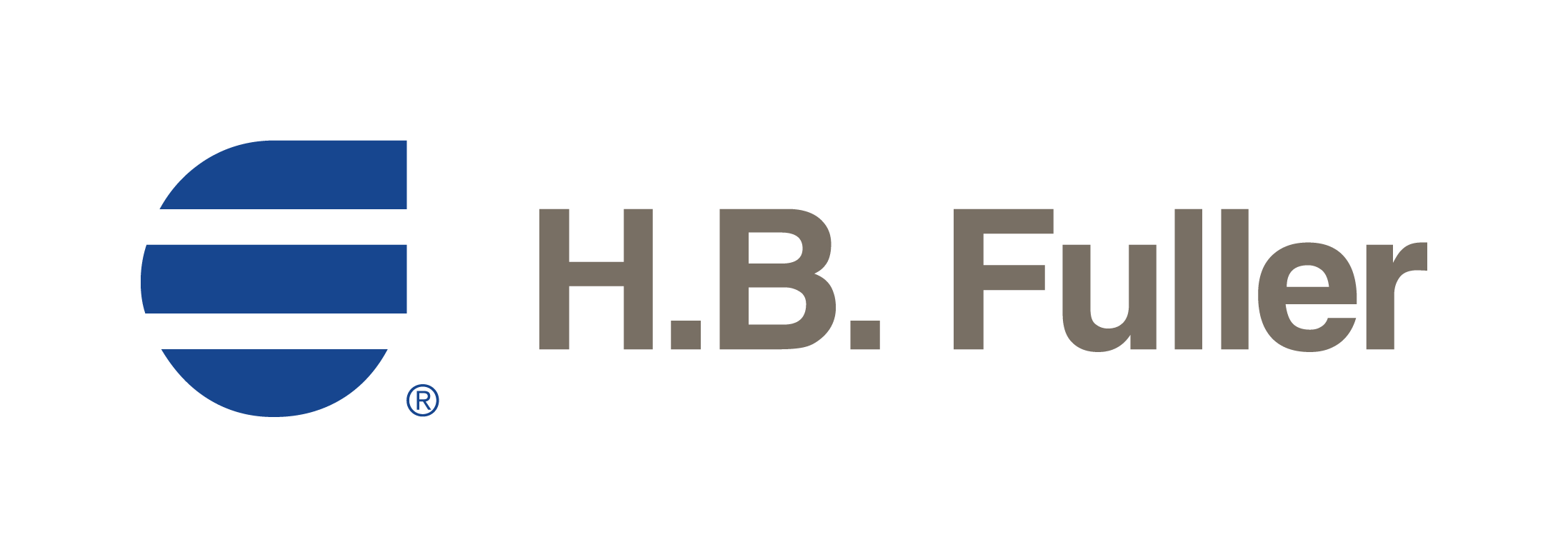
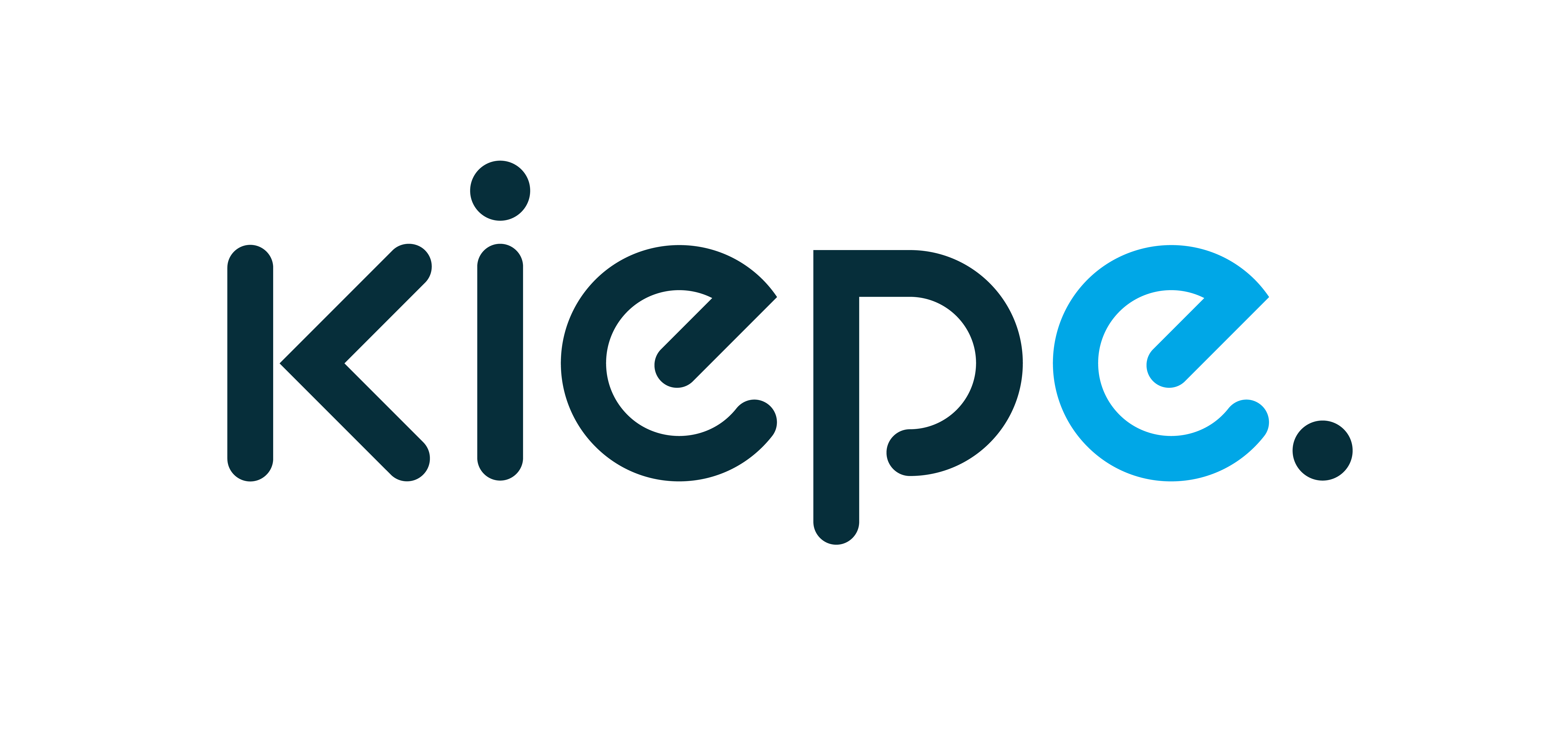
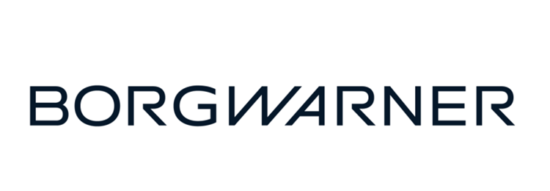