Nyobolt EV
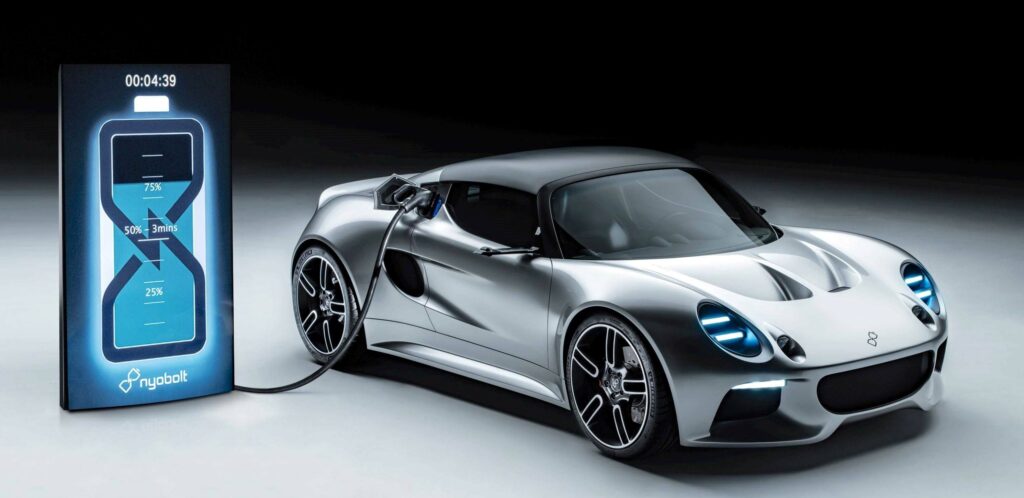
(Courtesy of Elan PR)
The Lotus position
Rory Jackson reports on new type of fast-charging battery and the Lotus demonstrator designed to show its potential to OEMS and users
Despite the pace at which sales of electric passenger vehicles are growing, and the promise they hold for lowering worldwide carbon emissions, there is a major conflict between the way EV designs are evolving and how that threatens to create serious problems for the sustainability of automotive supply chains.
Historically, the primary deterrent to consumers adopting EVs has been range anxiety, given the comparatively lower MPGe of battery packs versus fuel tanks in IC-engined cars, and the far lower availability of charging points relative to fuelling stations. In response, automotive OEMs are building EVs with ever-larger batteries, with a view to enabling EVs to complete their day-to-day journeys and make it back home without needing to recharge.
That though presupposes that every owner has the means to charge their EV overnight. Increasingly though, studies suggest that overnight charging will not be feasible on a widespread basis. One study, in the US, estimates that 78% of car owners do not have access to overnight charging, while another in the UK reports that 40% lack this capability, owing to factors such as living in areas without on-street chargers.
However, if battery suppliers focus merely on making the batteries larger, it implies that demand for battery materials will grow, so more and more mines for extracting elements such as lithium, nickel, and cobalt will be needed. That increases the risk of pollution, and of conflicts over associated mineral and labour rights.
It also spells ever-higher material costs for batteries and exhaustive engineering into how OEMs can offset the increased weight of such packs in their vehicles. That in turn will lead to higher production costs for EVs and therefore a strong probability of EV prices increasing over time.
To develop technologies that could resolve these issues and hence make the automotive world’s transition to clean energy as seamless as possible, Nyobolt was co-founded in 2019 by now-CEO Dr Sai Shivareddy and chief scientist Prof Clare Grey.
“As EV sales grow, and the first generation of EV owners depend on home or public charging infrastructure, we’re seeing a stream of news reports about local and regional authorities establishing new waves of charging stations, which are increasingly very high power, fast-charging systems, often ranging up to 400 kW in Europe and 600 kW in China,” observes Dr Shivareddy.
“What the authorities fail to realise though is that, most of the time, there isn’t a single EV in any of their communities that can accept a 400 kW input for the charge duration – their batteries just aren’t designed for it.
“But technologies become successful by working with what’s available. The first generation of EVs started with battery sizes of around 20-25 kWh, and didn’t see significant uptake. The next were engineered with packs that went up to 100 kWh to overcome the inconvenience of those smaller packs, and now, this new rollout of EV chargers will be convenient only for EV owners whose packs are compatible with their very high current inputs.
“We have no wish to seek this compatibility through the traditional approach of building bigger, heavier, and more expensive packs – it’s bad for EV owners and bad for the Earth,” he adds. “Close to 500 GWh of batteries were produced in 2022, and if you believe Tesla, that figure will grow 20 times in the foreseeable future.
“If instead though a battery could be made much smaller but capable of using the soon-to-be widespread 400-600 kW chargers without losing its lifespan to lithium dendrite build-ups or thermal damage, you end up with a much more sustainable model for the global EV battery industry.”
Nyobolt’s internal r&d over the past 4 years has therefore focused on creating a new type of fast-charging battery that fits these requirements: one that is relatively small, designed to safely accept extremely high fast-charging rates and which could last for thousands of charge-discharge cycles without any noticeable effect on performance or safety, even if each recharging was performed within 6 minutes (indicating a charging rate higher than 10C).
However, the company is also well aware that offering and commercialising new battery products is difficult, largely because of the repeated failure of new battery technologies to live up to their touted potential. So, rather than merely talk about its offerings, it has elected to unveil its technology in a demonstrator EV to show its technology is viable for integration by OEMs and road use by consumers.
The Nyobolt EV was unveiled in June this year, and integrated a 35 kWh battery pack capable of being charged in less than 6 minutes and tested to over 2000 cycles without any significant losses in capacity, stability or other parameters. Nybolt adds that the EV also has a 250 km range between charges and, while not a critical requirement, its bodywork should be recognisable to enthusiasts of Lotus sportscars.
High-rate anode
Many readers will be sceptical about any claims of a new ‘miracle’ battery chemistry, something that Nyobolt’s CTO Dr Brian Barnett understands only too well. “I know we’re going to get a lot of people asking how we’re doing it, but the fact that they even ask is symptomatic of how difficult it is to make a success of new battery chemistries,” he says.
“Announcements of breakthrough battery technologies have been made many times, with nothing happening each time. The reason so many fail is because it’s extremely difficult to create a very controlled environment in the cells that enable the active materials at the anode and cathode to react in a safe and highly repeatable way.
“We’ve seen that happen with chemistries like lithium sulphur, which is still being developed after 35 years, or silicon batteries which have been around 20 years in the making, or lithium metal, which was first identified in 1913. These days we have solid state batteries, and those have been about 10 years in the making.”
Affecting all of these are what Barnett calls “design rules” over which materials and their quantities can be assembled in a cell without risking cracking, outgassing, cycle failures or other problems. His experience of these rules was applied throughout Nyobolt’s r&d.
“We hired a team that’s extremely experienced in cell chemistries as well as cell design, and also in high C-rate applications such as motorsport. All this understanding was zeroed-in on the central part of our technology – a novel anode material with a remarkable ability to move lithium ions between the cathode and anode quickly,” Barnett continues.
“Traditional electrodes in lithium-ion batteries really aren’t made for speed at the anode, so we focused on optimising that one anode material and section of the cell. We also worked heavily on using cell designs we knew would be compatible with extremely high-rate applications. Altogether, that made for a battery that can be fully recharged in 6 minutes.”
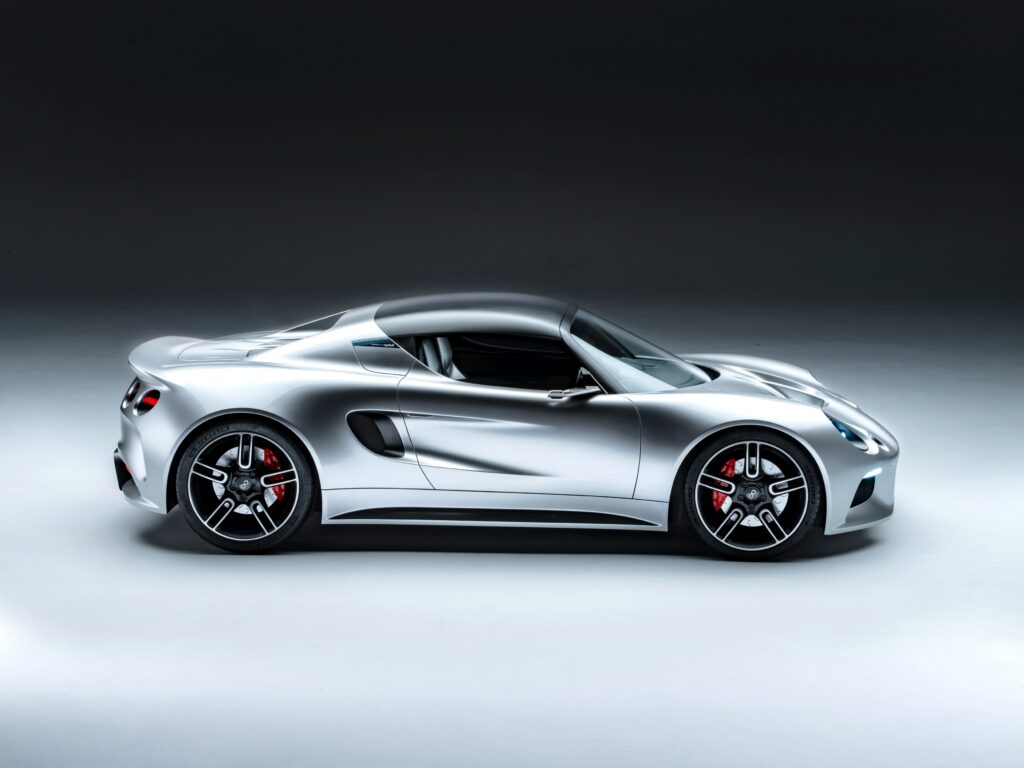
(Courtesy of Elan PR)
CALLUM collaboration
As mentioned, Nyobolt has presented its technologies in the form of a complete and eye-catching EV, to show electric automotive OEMs how its products can be integrated and used in commercially and operationally viable vehicles, and to show that the company is ready for supplier-customer partnerships.
However, as Nyobolt is not a vehicle designer, it sought a partner capable of covering the necessary design skills for creating such an EV. It so happens that Dr Steve Hutchins, VP of operations and engineering at Nyobolt, had previously worked at Lotus with automotive designer Julian Thomson, who headed much of Jaguar Land Rover’s styling work over the past 20 years or so, and is perhaps best known for designing the Lotus Elise S1 sportscar while serving as Lotus’ design director.
At the time, Thomson was a freelance designer, but he also knew some of the key members of CALLUM, a design and engineering company specialising in creating high-end premium products, from low-volume automotive vehicles to mobility solutions, furniture and smaller lifestyle items. CALLUM develops products for market niches it has identified in-house, but also seeks collaborations with prospective partners it views as having strong potential for long-term market or industry changes.
Seeing significant value in Nyobolt’s fast-charging solution, Thomson opted to present it in a modernised version of the Lotus Elise, rather than going down the simpler path of a resto-mod, to show that the technology is intended for new, batch or bulk-produced EVs rather than one-off kit integrations. But rather than attempting it alone, he contacted CALLUM for design and engineering support with developing the demonstrator.
EV design and powertrain
Creating the Nyobolt EV from a Lotus Elise included tuning the aesthetics, thermal management and aerodynamics. “At the outset, we started with a wide array of images, some quite exaggerated, but that created a vision of what we wanted to achieve before going into 3D CAD development where we could start identifying some of the design constraints,” says Aleck Jones, creative lead at CALLUM.
“These included settling on a wheelbase and a track width. We knew we wanted the EV to be wider than the Elise, which was great because it gave us a lot of extra space for design and packaging. And we wanted the cabin to retain the shape of the Elise, with the same glasshouse as the [Lotus] Exige.”
Thomson’s principal desire to modernise the iconic sportscar and give it more presence has resulted in the Nyobolt EV being 100 mm wider and 150 mm longer than the original Elise, making Nyobolt’s car about 3.8 m long and 1.8 m wide.
“That wider stance rolls back into the body and into the thicker, more muscular haunches at the back, giving it more of an hourglass shape,” Jones adds.
“We’ve also raised the waistline of the car somewhat, to reduce the size of the glasshouse and emphasise the new proportions. And one of the main focuses was to get the surfacing right – one thing you’ll see is a highlight that rolls down the side of the car and into the rear arch.
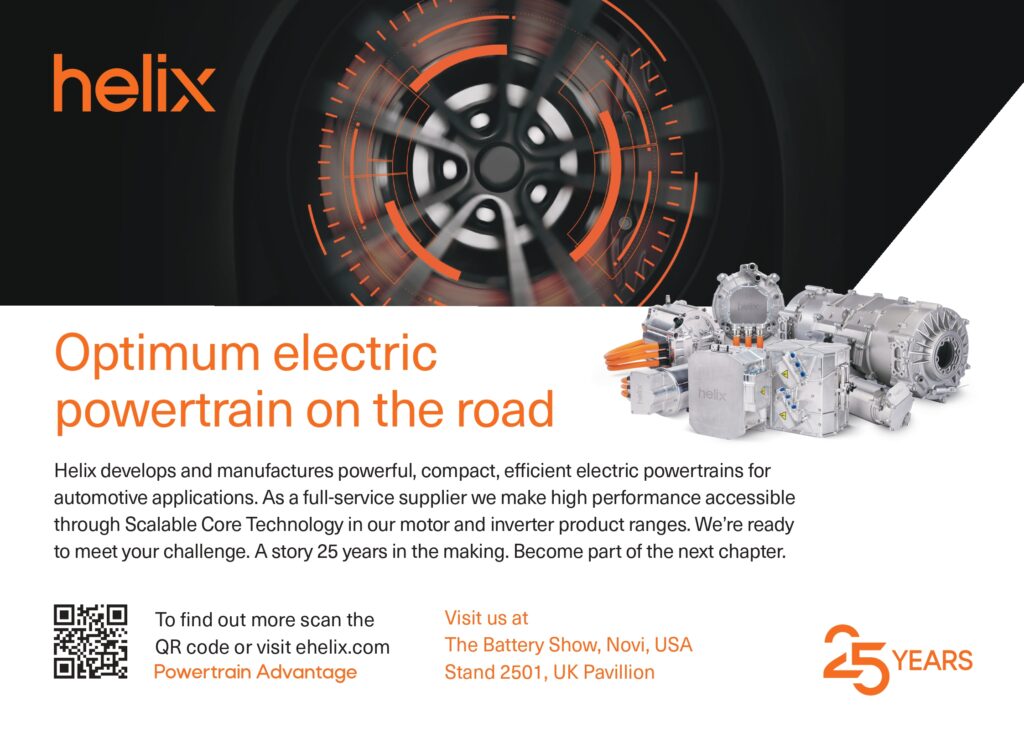
“None of these design enhancements would have been possible though without the compact size and nature of the Nyobolt battery, which allowed us to package it into where the engine bay had been [the original Elise had a rear mid-engined layout], letting us design the EV freely without any packaging hindrances.”
Design-wise, it has retained the nose-down stance of the original Elise, but now comes with 19 in wheels, rather than the wheels in the original, which were 15 in at the front and 16 in at the rear. That is a reflection of the modern trend towards larger wheels and cars.
“We also wanted to update the lamps to make them more interesting,” Jones continues. “The front ones are designed with a nod to the Elise’s lensless lamps, which also allowed us to open up the design with an aperture behind them to allow more airflow into the car for cooling subsystems like the battery cold plates without needing to make the front grill or side apertures larger.
“At the rear, the lamps create essentially a beam of light that intersects with the body, and they also form ducts that allow for greater dissipation of the heat from the battery pack bay. Creating these unique lamp signatures can add multiple zeroes to the cost of a project though, because the lamps are very complicated and developing them is expensive, but it was worth it for getting a unique look and additional modernised features.
“For instance, where the standard Elise had indicators, the Nyobolt EV has singular inboard lamp units with five functions: high beam, low beam, a position light, an indicator, and a side light, covering what is required by road authorities.”
New 21st-century driver subsystems include wing-mirror cameras are housed in machined, solid, transparent ABS that leave the PCBs visible for aesthetic purposes. Further back, the charging connector input is installed at the B-pillar.
In addition to these external changes, the IC powertrain and fuel system has of course been replaced with Nyobolt’s battery technology and an electric powertrain.
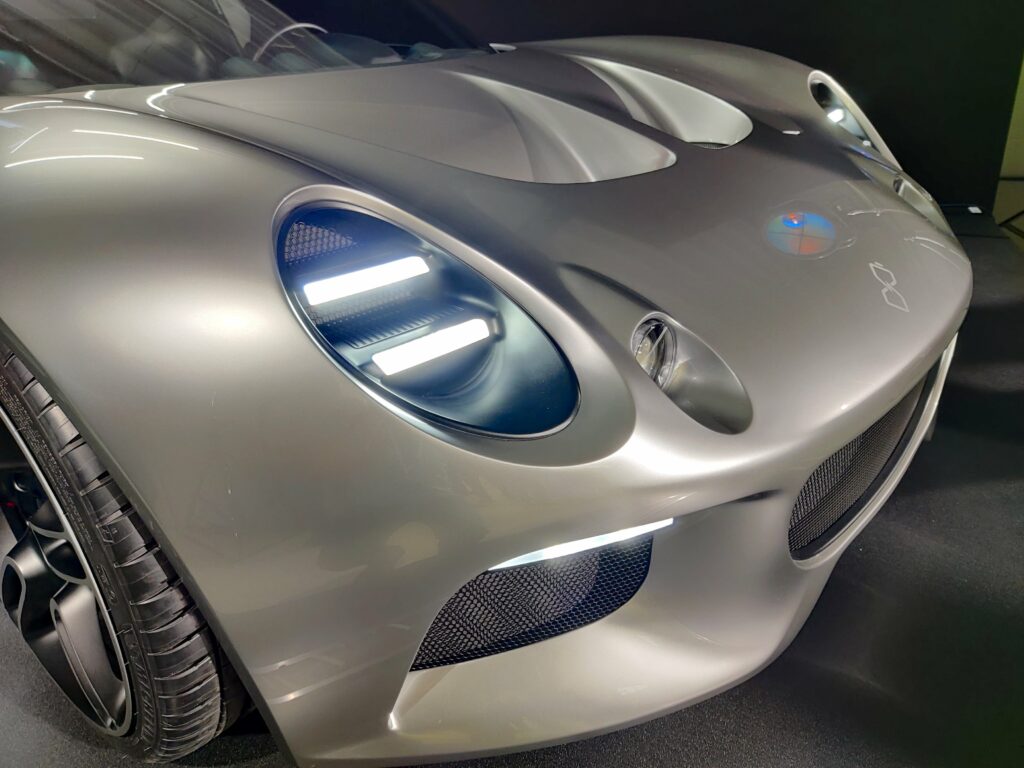
(Author’s image)
Adam Donfrancesco, engineering director and co-founder of CALLUM, notes that from an engineering perspective, using the Series 1 Lotus Elise as a resto-mod platform wouldn’t have been the right starting point because CALLUM needed to be able to focus on the engineering and integration of the powertrain and the HV architecture. That took precedence over more resto-mod oriented objectives, such as developing the brakes and steering to mimic the experience of driving an Elise.
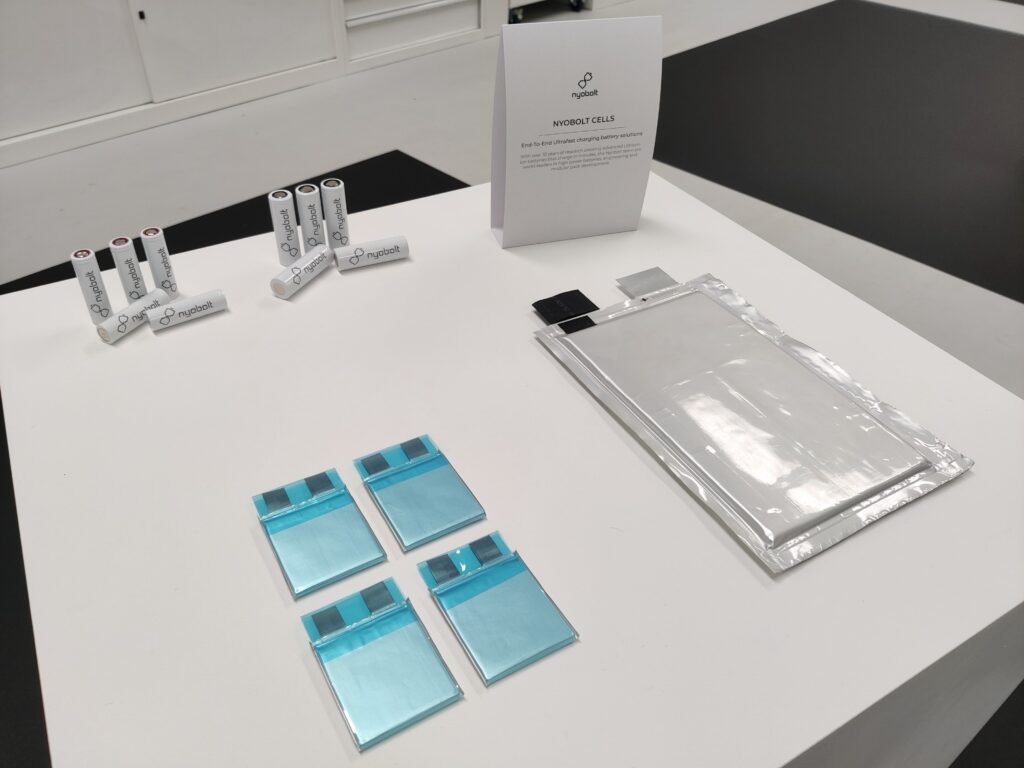
(Author’s image)
Iterations throughout much of the design and integration process were carried out using a Lotus Exige as the donor car, although the Lotus Elise remained the primary design inspiration. The Exige was the last of the Series 1 Lotus Elise’s line, and carried more mass than the others.
“That was useful when we were delta-ing the HV components in and out,” Donfrancesco notes. “We spent much of the project aiming for around 50 kg incrementally over the original vehicle, so now the Nyobolt EV is around 1246 kg, roughly 40 kg heavier than the Exige with a full tank of fuel.”
That though is far below the weight of many comparably sized EVs, and was achieved thanks partly to the lightness of the battery pack, the exact weight of which was undisclosed at the time of writing. It also achieves the aim of retaining the lightness of the Lotus Elise, a key factor behind its performance.
Given the central aim of demonstrating the battery technology, the powertrain has been designed to be as simple as possible, and hence follows the trend of central, single drive motor configurations seen increasingly across the passenger EV industry.
The motor itself is a unit from Helix (formerly Integral Powertrain) in the UK, which provides peak power of 364 kW (488 bhp) at the wheel through a single-speed gearbox with a limited-slip plate differential. It is located under the battery in the rear of the car, just ahead of the rear axle. Nyobolt adds that the inverter is supplied by Cascadia Motion, but declines to specify the exact model.
“It’s as simple, traditional and lightweight an arrangement as you can get in an EV powertrain” Donfrancesco adds. “We wanted the car to feel still and stable but also be capable of considerable performance, being a sportscar, so the e-motor itself is capable of up to 364 kW, resulting in a peak torque of 457 Nm.
“Couple that with the limited-slip differentials and it should put power down very well, and we gain a little extra traction thanks to the width of the Exige. The downside of that is the car’s tendency to push on, so the differential is relatively open, but having to tailor the front-end grip while driving was part of the Exige’s original charm, so we don’t necessarily want to mitigate that too much. We’ve also gone for slightly larger diameter wheels for design aesthetics and improved traction over the original.
“Overall, the resulting traction might be a little excessive from a demonstration point of view, but proving the battery’s discharge capabilities is obviously very important, and we can easily tailor power delivery via the motor control software if needed.”
CALLUM and Nyobolt anticipate that the EV will begin testing in November this year to prove out the long-term charging and life cycle capabilities of the car in real-world conditions.
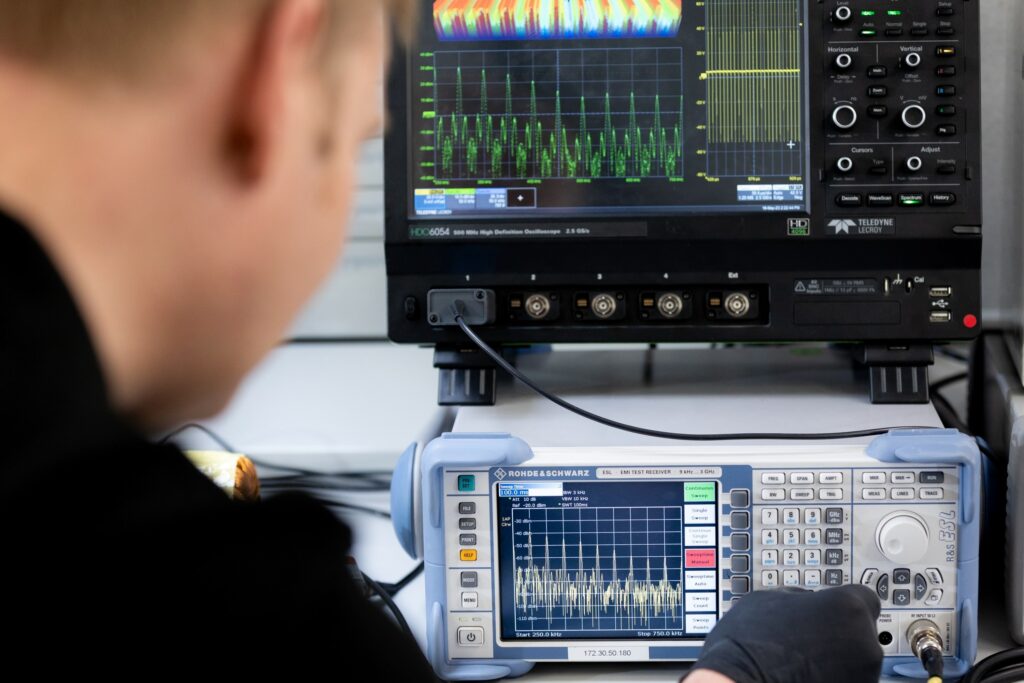
(Courtesy of Elan PR)
Battery materials
Given the work involved in creating its anode material, Nyobolt declines to reveal its exact formula. However, it provided a demonstration of its modules’ ability to charge in 6 minutes at a rate of 12C using COTS recharging and monitoring equipment.
The company has also been granted a patent an electrode with a niobium-containing metal oxide surface, which it says has considerable capabilities in high C-rate charging and discharging across a wide range of temperatures, as well as optimal capacity retention during intensive cycling at temperature extremes, particularly when compared with lithium-ion cells with graphite electrodes (although that does not refer to the specifics of the anode).
Dr Shivareddy however cautions against placing too much emphasis on a ‘secret sauce’. “Looking at one battery material – be it an anode, a cathode or any other component of a chemistry – never gives you the full picture. There are so many nuances in each component, so knowing all about one part doesn’t help you at all in knowing what’s possible at the system level.
“Certainly, over the past 6-7 years we have focused more on the anode material side, but that also has to interplay with cathode materials, the electrode winding, the electrolyte separator, and other structures. Together they need to optimise how much energy you can store and how quickly you can move it in and out of the cell via lithium ions.”
That has entailed close consultation with cathode materials companies, metals suppliers and mining companies exploring new sources of graphite and other carbon-based anode materials outside China, to examine the scientific, cost and sustainability of different material combinations in different cell designs.
Dr Shivareddy is reluctant to think of Nyobolt’s proprietary anode as a miracle invention, instead emphasising that the paradigm of ‘energy density above all else’ has simply held such sway for so long in attempts at battery commercialisation that efforts to prioritise power density instead have been stymied through a lack of impetus or support.
“Requirements define constraints, and for a long time maximising mAh/g was the most important requirement,” Dr Shivareddy says. “Throughout that time, going for power density wasn’t always possible, especially as the consumer space was rife with USB-type connectors that had limitations on power throughput, or they used really big chargers to provide compatible current levels and so they didn’t need cells capable of high C-rates.
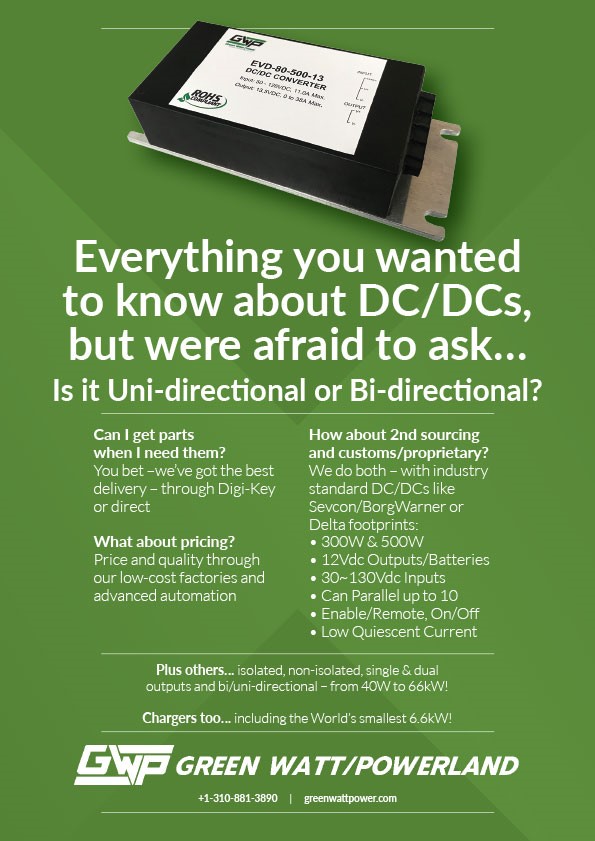
“Factors like that really influence and limit the range of research into alternative battery chemistries. We were effectively the first to spend so many years putting the scale of resources we did into maximising the rate capability and charge-discharge capability within a cost constraint that would keep the price acceptable to the market. In fact, the only other space we’ve ever seen where power density was made so important has been in motorsport, particularly Formula One.”
The kinetic energy recovery system (KERS) came into effect in Formula One around 2007-8, and this required that batteries in the racecars could accept extremely high inputs of power from regenerative braking. That in turn spurred significant research into battery material combinations that could achieve new heights in power density, but without skimping on energy density.
“Of course, those batteries only needed to last one season, so you could push the limits and have cycle lifespans of just 100-200 cycles, and they didn’t need to be designed for bulk manufacture in a way that would bring their prices down,” Dr Shivareddy says.
“Nor did they emphasise researching their charging capabilities as much as their discharging, and there’s a lot of nuance there with regards to balancing the two electrodes in the cell, or trading off between capacities and C-rates with metal oxide additives or other approaches.
“But they achieved incredible things, like batteries capable of discharging at 100C. In-house, we know how to exceed even 200C, it’s just that for now, that far exceeds what the commercial world needs.”
Nyobolt’s research has therefore built on the contributions of its former motorsport engineers and gone beyond, particularly with regard to increasing charging speed and cycle life – tens of thousands of cycles are the target, including high transients and extremes of temperature without damaging the materials. Along the way it built a library of what materials to pick for a desired parameter increase, such as peak power, continuous power, range or thermal stability.
“Perhaps most important from our point of view, we’ve tailored our anode for as low a resistance as possible for the amount of material in each cell, to enable more ions to flow in and out and at a high rate,” Dr Shivareddy says.
“Broadly there are two ways to go about that: change the material or work from a blank slate completely, or tune an existing chemistry with different particles, surface properties, ways of installing them into an electrode, processing conditions, binders, and other additives, and so on.
“All those things entail a cost structure which we need to bear in mind if our smaller packs are really to enable cost savings for OEMs and drivers, on top of giving drivers a good experience in which they have a smaller battery with less range, but can replenish that range in 5-6 minutes at a station.”
He adds that high C-rates and the controllability enabled through Nyobolt’s anode material and other innovations can also feed into the discharge side. Optimising the battery’s high power-to-weight ratio can translate into fast acceleration and smooth control for drivers, assuming the downstream parts of the car such as gearboxes and SiC inverters are built to make use of the high power delivery.
“The benefits of high power density don’t stop there either,” Dr Shivareddy says. “Thermal management requirements for instance are much lower across the board in our batteries and our EV, because the impedance is much lower, which of course means heat losses are inherently lower too.
“As well as learning about high power densities and building our library of which materials improve certain properties, we learned a lot about what doesn’t work. Conventional anode materials like silicon oxides have problems at the atomic level and higher up at the electrical interface level, which interfere with our ability to maximise ionic and electrical conductivity, and we need to do that to easily get an electron out of the cell every time an ion goes in.
“Each material has its own ionic conductivity, electrical conductivity and interfacial transfer properties. In essence, we found a way within the constraints of known materials and chemistries, to engineer for maximising these properties without making mistakes like packing in so much material per cell that there’s no point of access for electrons or ions to enter.”
Dr Shivareddy also notes that Nyobolt’s cell designs are largely agnostic regarding cathode materials, and can use whichever cathode is appropriate for a given application, such as NMC for automotive applications, or LFP if avoiding nickel and cobalt or enhancing safety for industrial purposes are desired.
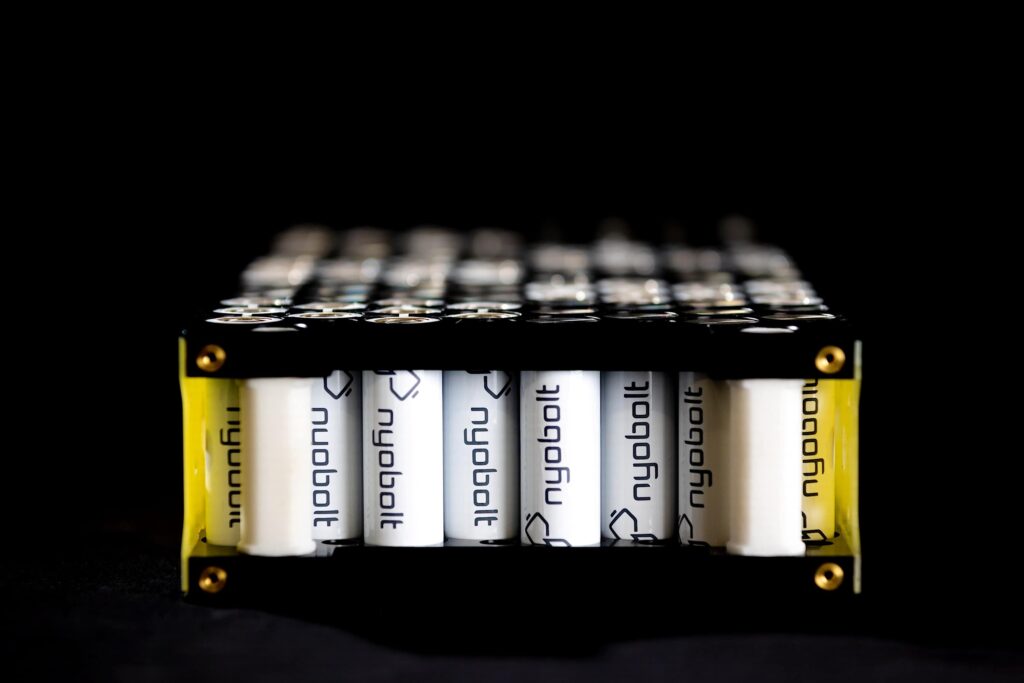
(Courtesy of Elan PR)
Battery testing
In the course of testing and maturing its cells for high power density applications, Nyobolt’s primary challenge was achieving the high currents necessary for identifying the electrochemical limits of its battery designs. “The amount of external power available from the grid defines limits on things like how many batteries and test rigs you can run in parallel,” Dr Shivareddy explains.
By and large, the company has used COTS equipment for testing, simulation, analysis and data recording, particularly for test cyclers and chambers for providing pack-level currents and conditions.
“That said, we tend to do most of our testing at the module level,” Dr Shivareddy says. “If you’re working with a pack storing 100 Ah or 40 kWh for instance, you need a 400 kW input, or around 1000 A to test that battery at 10C, which is what our cyclers are capable of.
“We can stack more modules together in series to hit the 400 V input that the cycler has at 1000 A. But in general, current has been the bottleneck, as it isn’t incredibly high in most EV networks. It’s usually below 200-400 A, with voltages getting higher and higher to prevent the need for high currents and the potential losses that follow in conventional high-energy batteries, so that’s what most testers are designed for.
“On the discharge side though, getting all the power we’ve used back into the grid is a little more challenging, so we had to do some clever things with the cabling infrastructure for that. Some test regimes would see a couple of megawatts going in and out of our test facility, and in future we’ll be manufacturing batteries and using power at around 20 MW, so that brought some important lessons for the factory design we’ll need one day.”
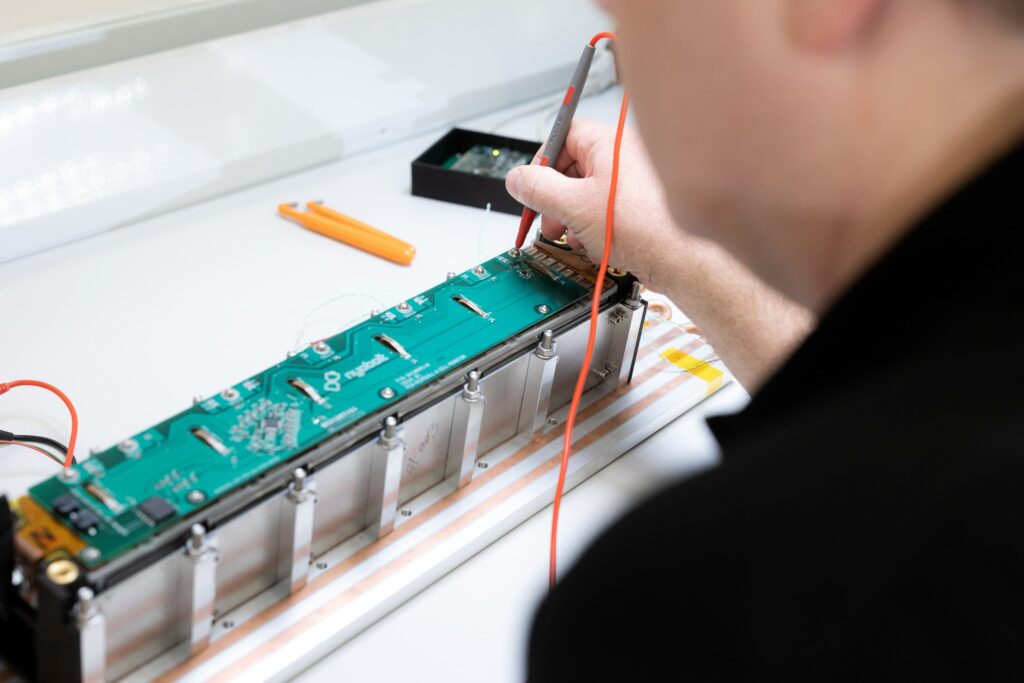
(Courtesy of Elan PR)
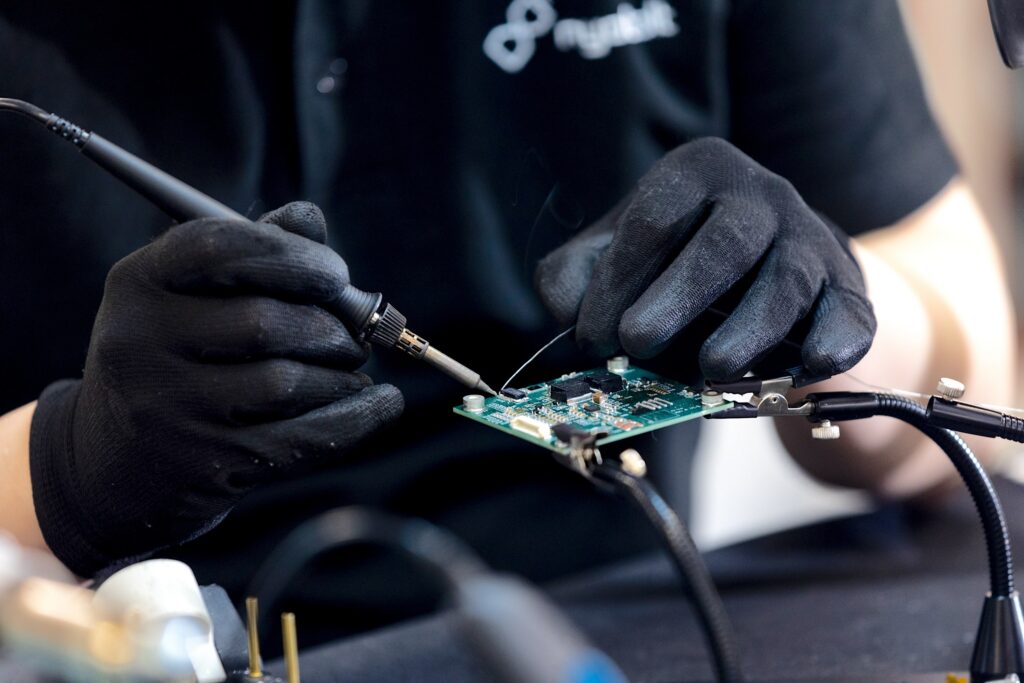
(Courtesy of Elan PR)
Cell-level mechanics
In seeking to encapsulate its battery materials in ideal packaging, Nyobolt has taken two main approaches to cell design.
Richard Ward, head of mechanical engineering at Nyobolt, says, “First, there is the cylindrical cell format, as popularised by Tesla and now widespread throughout the EV world. We also have a pouch cell battery, which is available as a small design as well as a larger version.
“The small pouch cell is what we’re primarily using at the moment; it’s effectively the first stage for initial manufacturing and road-testing the chemistry inside our modules and packs,” he adds. “But we’ve also manufactured larger pouch cells, because there will be end-user applications in which storing a given amount of energy in a smaller number of larger cells will be more efficient than using a larger number of the smaller cells. For instance, larger commercial EVs will still need bigger packs than the 35 kWh on our demonstrator EV.
“And when I say using larger cells is more efficient, I particularly mean the weight and cost saved via the reduced number of welding and connection points, sensors and so on that comes with a lower number of cells per module and pack.
Ultimately, having a large number of individual cells will come with those and similar overheads, which will conflict with maximising Wh/kg or Wh/litre one way or another – and even if we’re heavily focused on maximising charging times while keeping lifespans long, volumetric and gravimetric energy density are still going to be major targets for us as well.”
The company adds that its use of cylindrical cells was primarily in the prototyping stages, through its partnership with Prof Alex Roberts at Coventry University, who has access to a pilot line for cylindrical cell assembly. Nyobolt has since moved away from these to pouch cells for production though.
Nyobolt cites various advantages of pouch cells for commercial products. The format maximises the amount of active material that can be packaged in a given volume, and the shape, surface area and lack of a hard case enable effective heat extraction from each cell and hence high thermal efficiency for the overall module.
“From a manufacturing perspective, I’ve worked with both cylindrical and pouch cells, and found that cylindrical ones suffer from tolerance stack-up, which makes welding challenging,” Ward reports.
“When you’re welding materials together, the materials need to be in contact to make the joint, but variations in cylindrical cell length often means that in an automated production line you might not be able to make the weld. But I can form the tabs on pouch cells exactly where I need them to be in order to make the weld successful.”
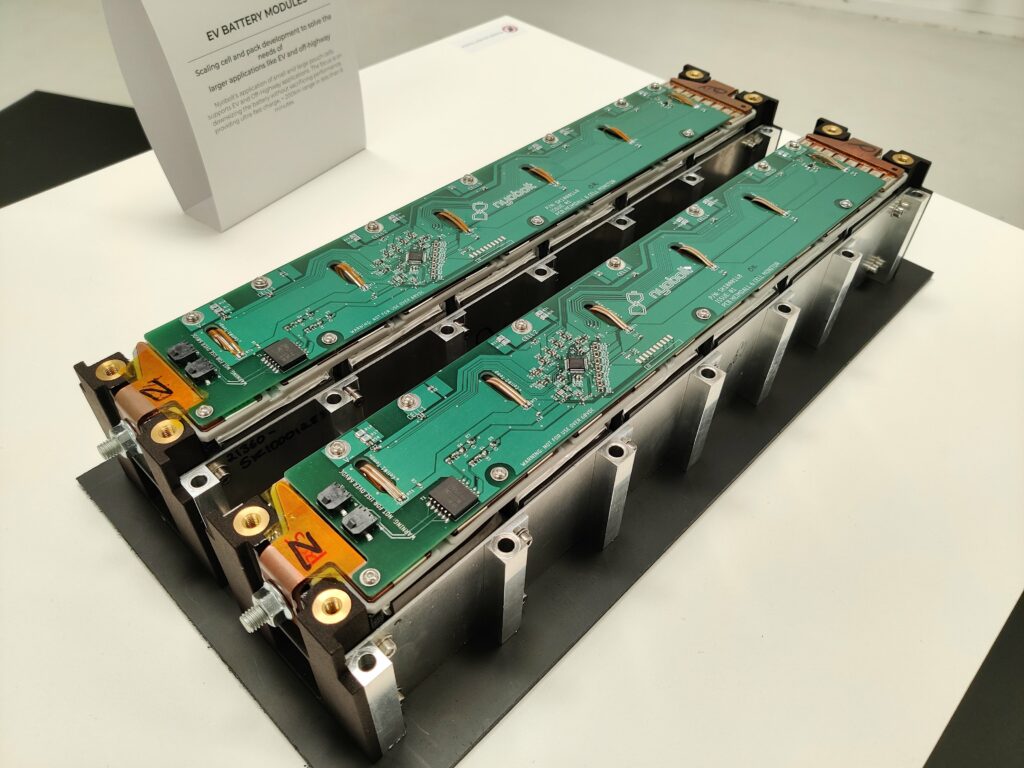
(Author’s image)
Module structure and manufacturing
The demonstrator pack in the Nyobolt EV integrates units of its current prototype battery module. Each module consists of six strings of cells connected in series, with each string consisting of eight cells connected in parallel (hence a 6S8P solution).
“We use our small pouch cell format in this module, with the cells mounted within an aluminium construct that clamps them together and contains the channels for liquid coolant for extract the heat generated by the cells, before transmitting it to a cooling plate,” Ward explains.
“While we’ll continue using these modules in tests for gathering long-term performance data on our battery chemistries, our next steps towards commercialisation will be to develop a replacement module that’ll be built with the larger pouch cells, to look for efficiency improvements in the module as well as the pack.”
Regarding future module designs, he says, “At the moment, we have a simple system of electrical conductors running between each cell group, and each cell has a tab that needs to be welded to those conductors. We’ve worked with a partner to develop the exact process for our cell welding, and to understand the parameters necessary for our process to work given our cell and module materials.
“Future cells might use different combinations of anode and cathode materials, so it’s critical for us to know how our choice of conductors and hence our welding approach would change accordingly. And even if we stick with the mixture we have at the moment, we want to manufacture our modules in reasonable volumes in the future, so learning about all the different considerations that go into welding optimisation has been vital.”
The cooling plate typically sits at the bottom of the module. It is a bespoke plate designed in-house, and features a liquid-coolant channel with a zig-zag flow pattern across its breadth, as is common among COTS liquid-cooling plates. However, Nyobolt found existing COTS plates prohibitively heavy to integrate and expensive to manufacture, so it sought to make one that was lighter and easier to build itself while still retaining good performance in extracting and dissipating heat from cells.
“Our coolant is still standard water-glycol, but our engineers have carried CFD analysis to model the directions and pace at which coolant moves around the battery modules in combination with different plates,” Ward says. “Essentially, they’ve sought to put metal only where it’s needed, then cut back on liquid too, using the absolute minimum amount of water-glycol needed.
“Initially we looked at a radiator-based cooling system, then at a chiller-based system, before settling on cooling plates as the simplest and least costly approach to thermal management. We also incorporate layers of thermal transfer materials for better removal of heat from the cells and down to the cooling plate.
“As we develop our understanding of the cell and how it behaves with regard to potential thermal runaways, we might opt for thermal insulation or runaway retardant materials between cells as well. That’s an ongoing development but we’re sure it’ll come.”
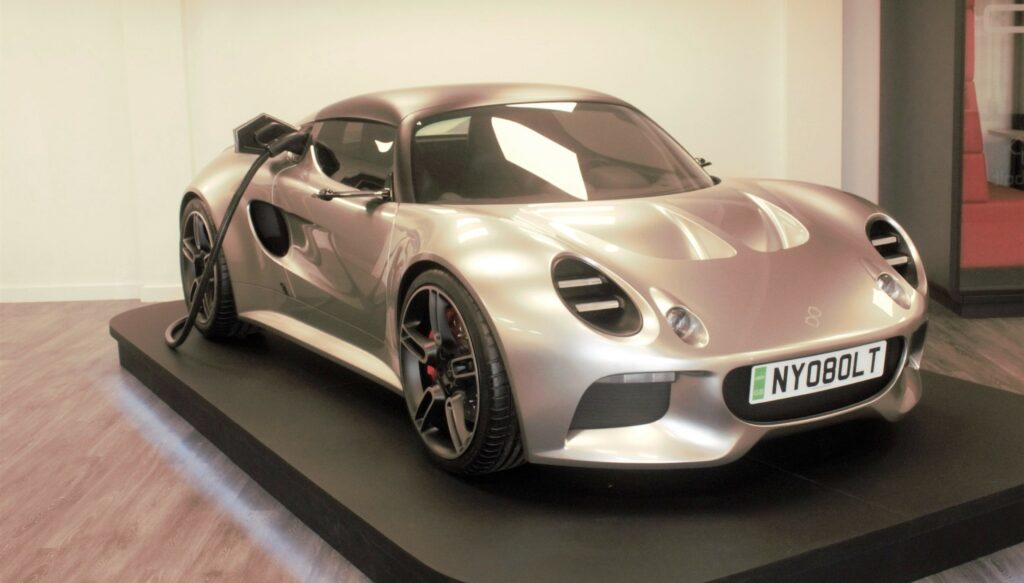
(Courtesy of Nyobolt)
Embedded systems
In addition to the systems discussed so far, Nyobolt’s applications team is also developing an array of embedded computing systems. These include the circuit boards for the BMS, cell monitoring cards and the controller, as defined by regulatory requirements on EV safety and Nyobolt’s own internal requirements for performance and mechanical integration.
“In addition to defining the mechanical footprint in which each item of electronics has had to fit, we’ve also modelled and designed the boards to optimise for the amount of heat they might generate during operations and how we can remove that heat through the liquid-cooling systems in the battery modules and onboard charger,” Ward says.
“We’ve also gone through iterations of things like the PCBs’ integrations of connectors and their vibration performances to optimise our computing systems.”
The high power density of Nyobolt’s batteries posed a slight risk of higher heat production by the electronics, given that the BMS has to work harder than COTS BMSs to monitor and control the much higher charging and discharging rates. This and the higher power throughput across the battery in general entailed selecting some connectors and board mount components optimised for higher current to minimise heat losses.
“These types of components weren’t really available in the past, although we were able to use COTS products,” Dr Shivareddy says. “We just had to work hard to integrate them in a way that wouldn’t result in increased component-level internal resistances.
“Part of the r&d for that included looking into applications with high-current electric and electronic subsystems, such as rail, marine, or mining with megawatt-level vehicles, which have PCBs designed for key points of cost efficiency and industrial utility. Going with an all-new design would’ve entailed more risk, as untried and untested PCB designs naturally won’t have any data on how they can fail, even if they might have been more optimised and less over-engineered for our application.”
Future plans
Nyobolt aims to build 1 GWh of its batteries over the next 3 years, which equates to about 30,000 EV packs, although it notes that a lot work lies ahead to secure its preferred supply chain partners, determine optimal manufactory locations, and select the right customers – that is, OEMs who will understand how best to integrate and use its technologies.
As mentioned, the Nyobolt EV will undergo further testing for gathering performance data to mature the battery, the OBC, the embedded systems and other key technologies. Nyobolt and CALLUM have repeatedly stated publicly that the EV is a demonstration platform to its core, although Dr Shivareddy says the car’s scale of interested buyers makes the thought of becoming an EV manufacturer a tempting prospect.
In terms of future battery development, Dr Shivareddy comments, “Battery evolution isn’t a linear phenomenon – history shows us that once a new battery works in an industry lab, it still takes at least 10 years for it to become commercially available. But we’re interested in trying to shorten that process, potentially through integration with partners who understand want to achieve from material extraction through to high-volume manufacturing methods.
“We might be less focused on new chemistries or materials in the future, and more so on ways to combine mass-manufacturing solutions and filter new battery technologies through permutations of those. That could allow us to predict whether a new concept for battery technology will ever be compatible with manufacturing techniques, or if it just isn’t worth pursuing in r&d. There’s a finite amount of resources in the world, and all of it – minerals as well as money – should be allocated wisely.”
SiC EVSE DC charger
In addition to the fast-charging battery technology in Nyobolt’s EV, the company has also showcased a separate project consisting of power conversion technology developed for off-board DC fast chargers.
The project has resulted in an 800 V charger module, intended to enable highly efficient charging stations to be set up as part of an ecosystem of materials and power usage in the future EV industry.
“Rather than force OEMs to design a highly efficient charger themselves, we’ve made one compatible with our fast-charging battery, which we’re going to be manufacturing and supplying ourselves,” says Iain Mosely, Nyobolt’s director of power electronics.
At the time of writing, the 800 V EVSE DC charger module prototype was configured for throughputs of up to 30 kW, which Mosely says equates to replenishing 120 miles of range per hour.
Multiple units of the charger can be connected in parallel to increase the power level in steps of 30 kW. Nyobolt proposes that a charging station and connector capable of 300-400 kW would hence be appropriate for a 6 minute charge of the 35 kWh pack in the Nyobolt EV.
“Our modules use silicon carbide, which gives really high performance with the lowest heat losses of any commercially available power electronics,” Mosely says.
“Over the vast majority of cycles, accounting for temperatures and other variables, the charger transmits power from charging input to battery pack with greater than 99% efficiency.
“When we started the custom design, we had three target parameters: the voltage capability, the current capability and the power output characteristic. We had to tailor our system and these values in a way that would maximise our efficiency across all feasible environmental conditions and states of charge and health.
“Often, charger manufacturers try to make the power output characteristic as wide as possible, so that it can charge anything from a Class 8 EV to a small scooter, but that means a lot of power efficiency and performance is lost. Our 30 kW module could certainly be used to charge a small e-scooter; it just wouldn’t be very power efficient or cost-effective to do so.”
To explore what architectures and components worked best, Mosely and his team engaged in rapid prototyping to have numerous different charger modules they could test, connect in parallel, and gather performance data. Each module also ran embedded, real-time control software that the power electronics team could tune for different parameters in their pursuit of maximum efficiency.
Specifications
Nyobolt EV
All-electric
Central motor drive
Dimensions: 3880 x 1800 mm
Gross weight: 1246 kg
Maximum power output: 350 kW (470 bhp)
Battery energy: 35 kWh
Charging time: less than 6 minutes
Charging rate: 10-12C
Range: 250 km
Some key suppliers
Battery: in-house
BMS: in-house
Cooling plates: in-house
EV design: Julian Thomson
EV design: CALLUM
Powertrain integration: CALLUM
Motors: Helix
Battery testing equipment: Rohde & Schwarz
Battery testing equipment: Teledyne LeCroy
ONLINE PARTNERS
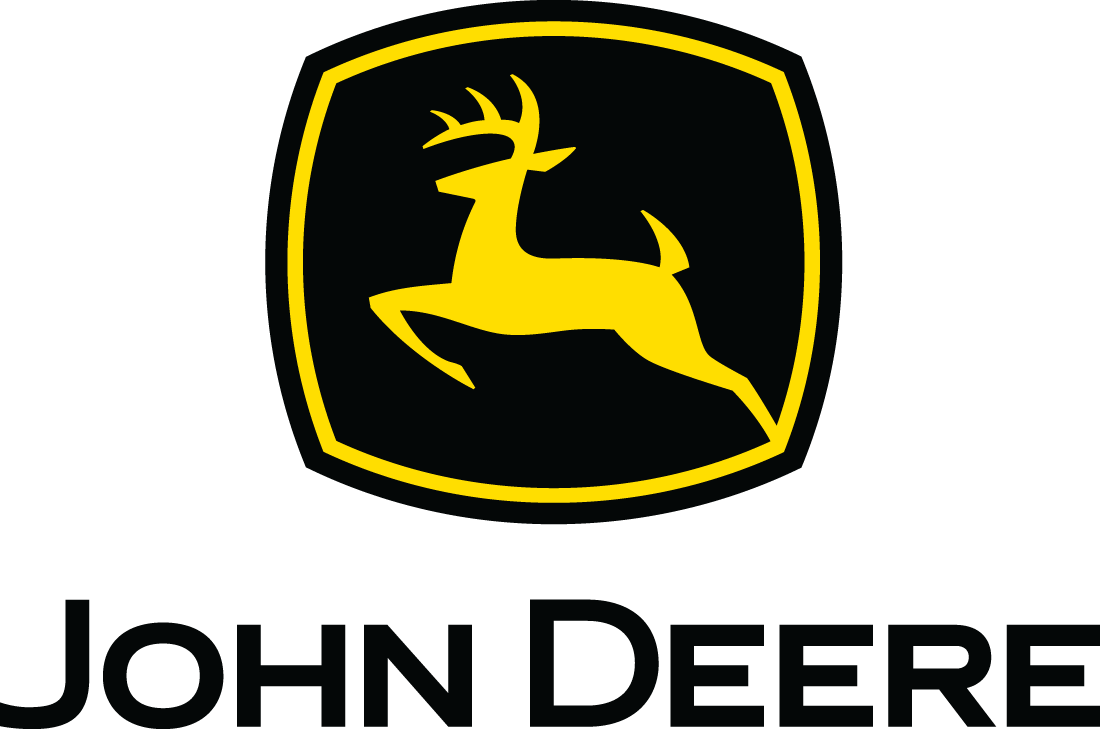
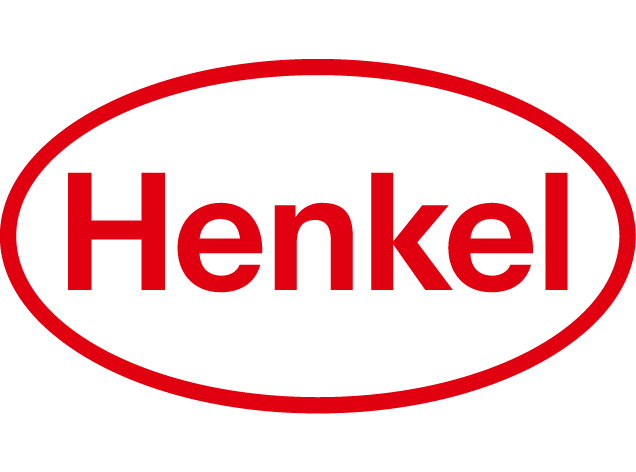
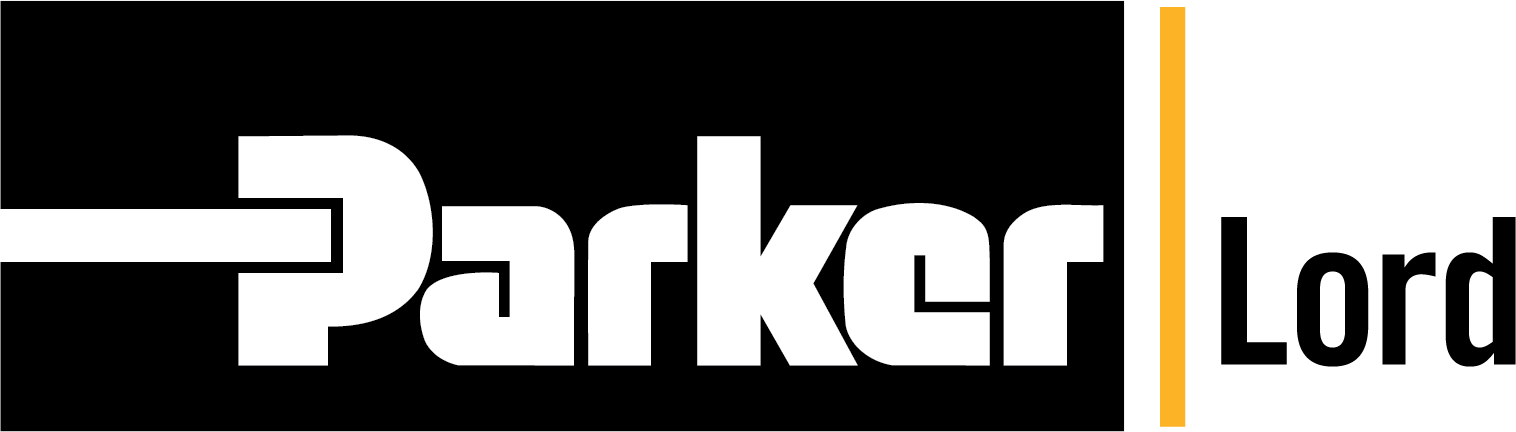
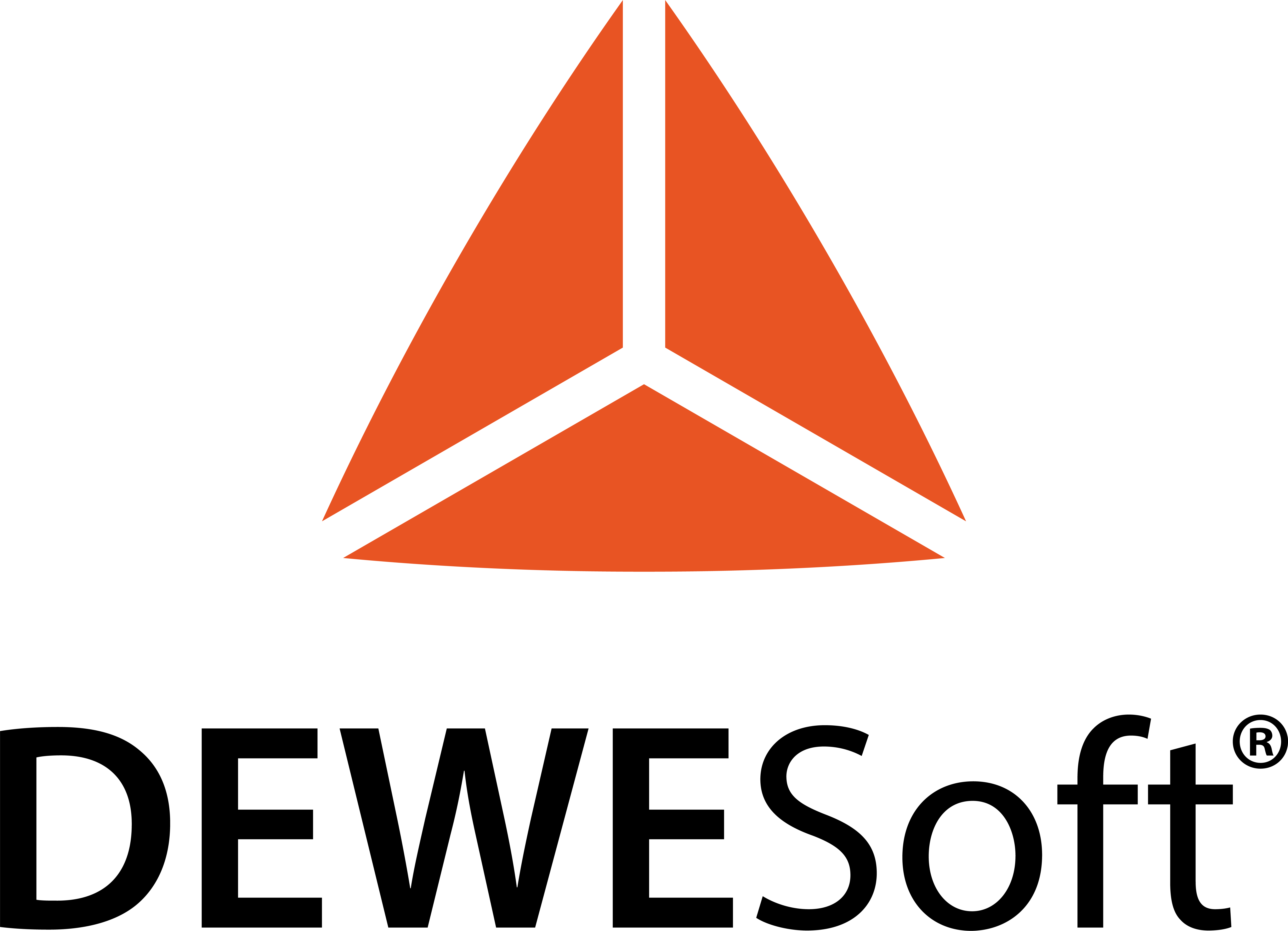
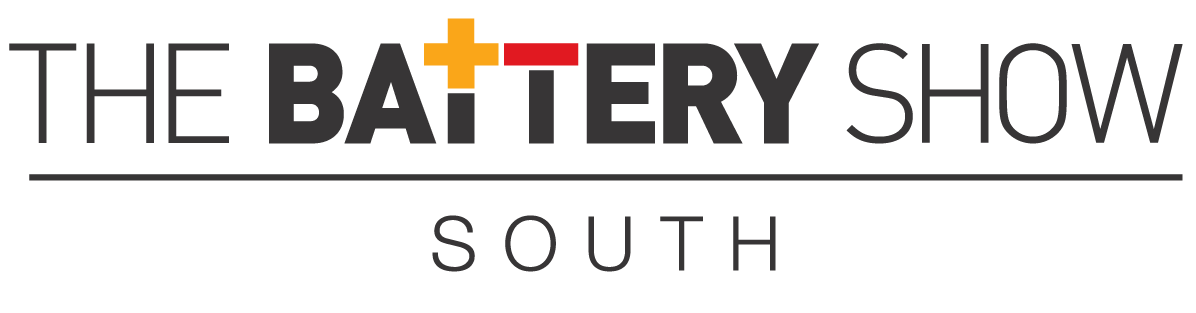
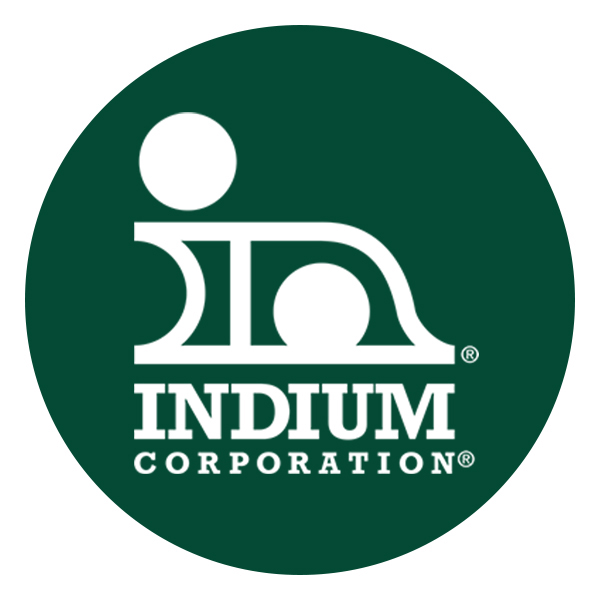

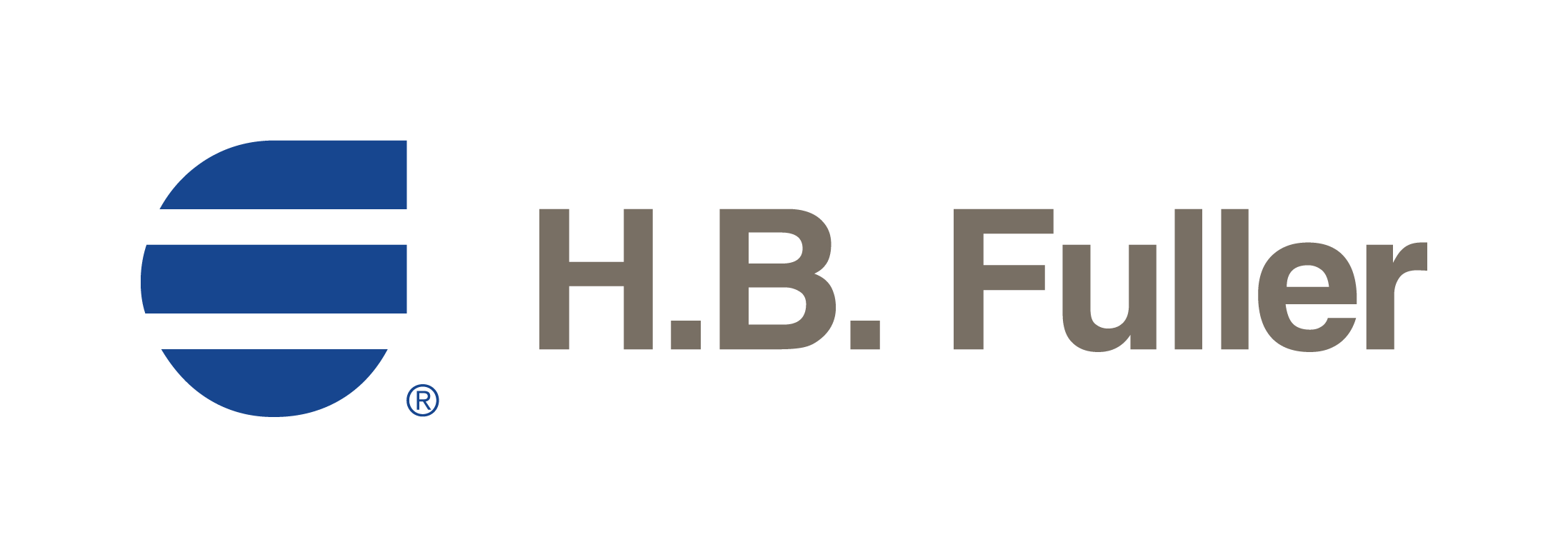
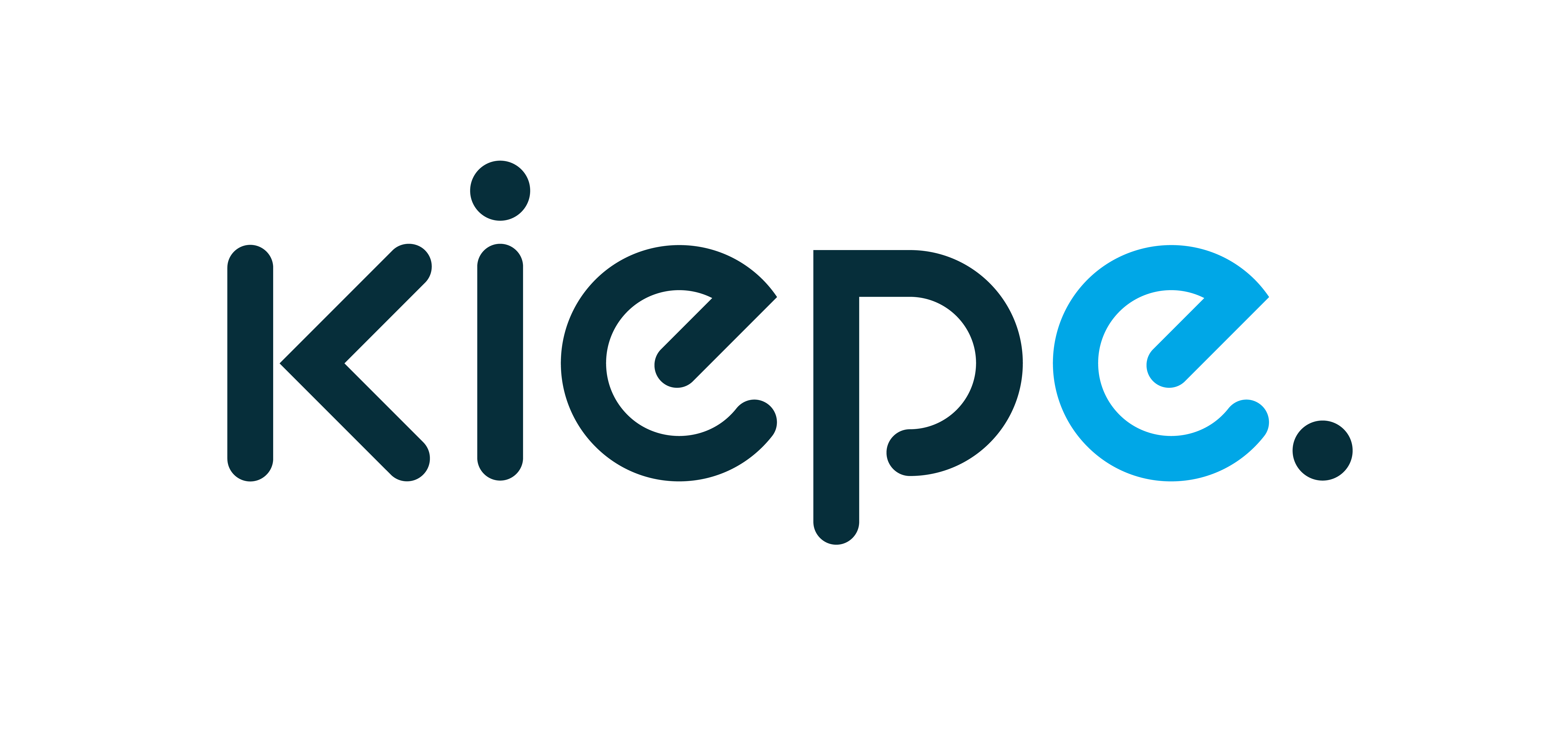
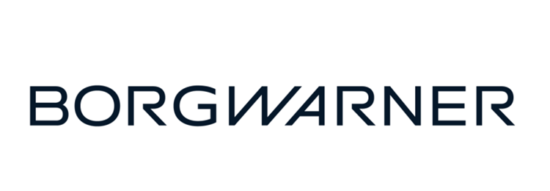