Ammonia as an EV fuel
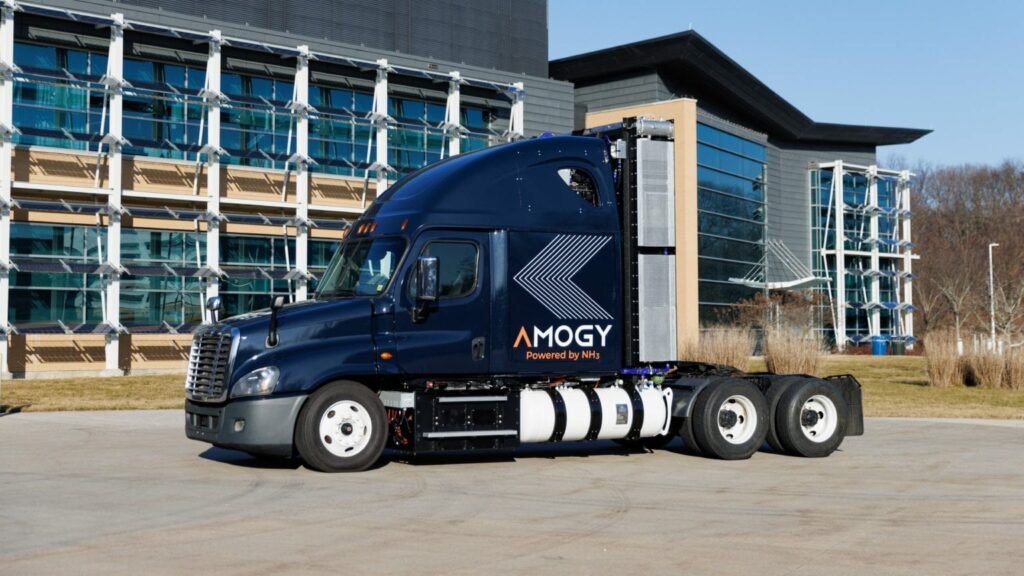
(Image courtesy of Amogy)
For all practical purposes, there is more hydrogen in ammonia (NH3) than in pure hydrogen, because hydrogen is a diffuse gas at ambient temperatures and pressures (writes Peter Donaldson).
Ammonia is a gas at ambient temperature and pressure ranges too, but it is much easier to liquefy it into volumes that translate into useful energy densities, and the transport and storage infrastructure is already in place. According to the Ammonia Energy Association, a 60 litre tank of ammonia would provide a representative fuel cell EV with a range of more than 750 km and emissions of just water and nitrogen.
Liquid ammonia contains about 4.33 kWh/litre, which is 70% more than liquid hydrogen at about 2.527 kWh/litre, and almost three times as much as compressed hydrogen with around 1.55 kWh/litre. Both achieve much higher energy density than the best lithium-ion cells, at just over 0.8 kWh/litre, although still a long way off that of gasoline at about 8.94 kWh/litre.
While hydrogen is stored at around 700 bar as a compressed gas and must be cooled to -252 ºC or below to remain liquid, ammonia is easily liquefied at room temperature by pressurising it to just 10 bar or by cooling it to -33 ºC at atmospheric pressure, making equipment such as tanks, valves and lines less costly.
So why do we not already have mobility based on ammonia? As always, part of the answer is that there are technical problems for engineers to overcome before it can become the hydrogen carrier of choice, and there are other big issues to contend with.
As with hydrogen, most ammonia is currently produced by a process that is highly energy and carbon-intensive, called the Haber-Bosch process. It generates hydrogen from fossil fuels such as natural gas and combines it with nitrogen that has been separated from atmospheric air cryogenically to form ammonia.
The process works best at temperatures greater than 400 ºC and pressures of more than 200 bar, and its industrial-scale application in the manufacture of commodities such as nitrogen fertilisers accounts for about 1% of global greenhouse gas emissions. As ammonia is the principal feedstock for manufacturing food crop fertilisers, it presents the same ‘food or fuel’ choice that makes other plant-based biofuels problematic.
Efforts to improve ammonia production include bringing carbon sequestration into the Haber-Bosch process, using renewable sources of hydrogen, such as electrolysis of water, with renewable electricity, and electrochemical reduction of nitrogen to ammonia using a catalyst. However, none of these operate at industrial scales yet.
Assuming that one or more of these new processes comes good, is then a choice between burning the ammonia in an adapted or optimised IC engine or feeding it to a fuel cell. If EV engineers take the fuel cell path, the next choice is then between cracking the ammonia into hydrogen and discarding the nitrogen in a refuelling station, for example, by integrating the cracking equipment into the vehicle or using a fuel cell that can use ammonia directly.
Which of these is chosen is likely to be highly application-dependent, with factors such as the volume and weight margins available in the vehicle. In one development, Australia’s Commonwealth Scientific and Industrial Research Organisation recently patented an ammonia cracking reactor system based on a metal-based selective hydrogen permeable membrane that has produced pure hydrogen and dispensed it into standard FCEVs.
Solid-oxide fuel cells can use ammonia directly, and offer good power densities, although they operate at temperatures of 800 to 1000 ºC, which brings its own engineering issues. Direct ammonia fuel cells are attractive because the operate at much lower temperatures, but need to be improved in terms of performance and durability.
While there are no panaceas in engineering, ammonia looks promising and could prove to be the best way to deliver hydrogen for FCEVs.
ONLINE PARTNERS
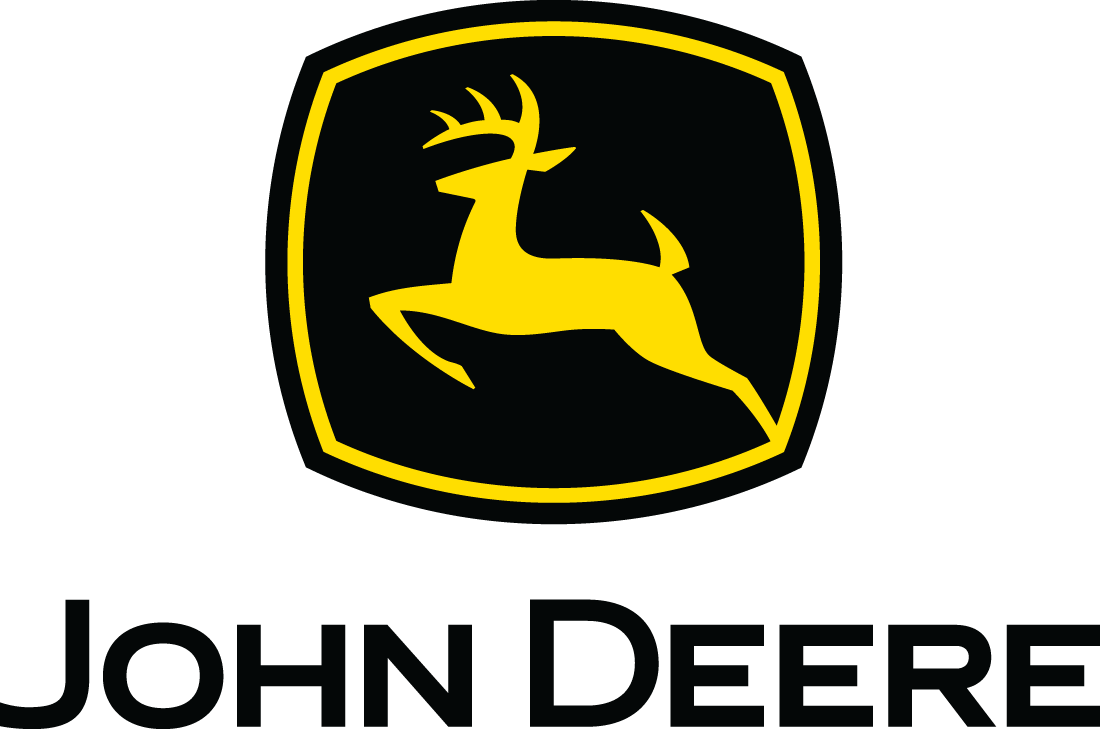
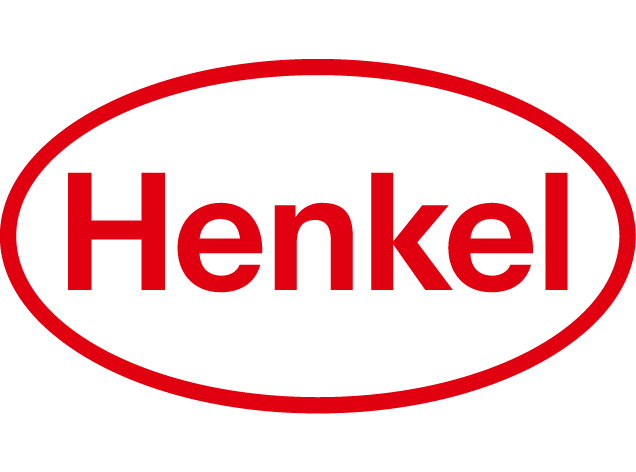
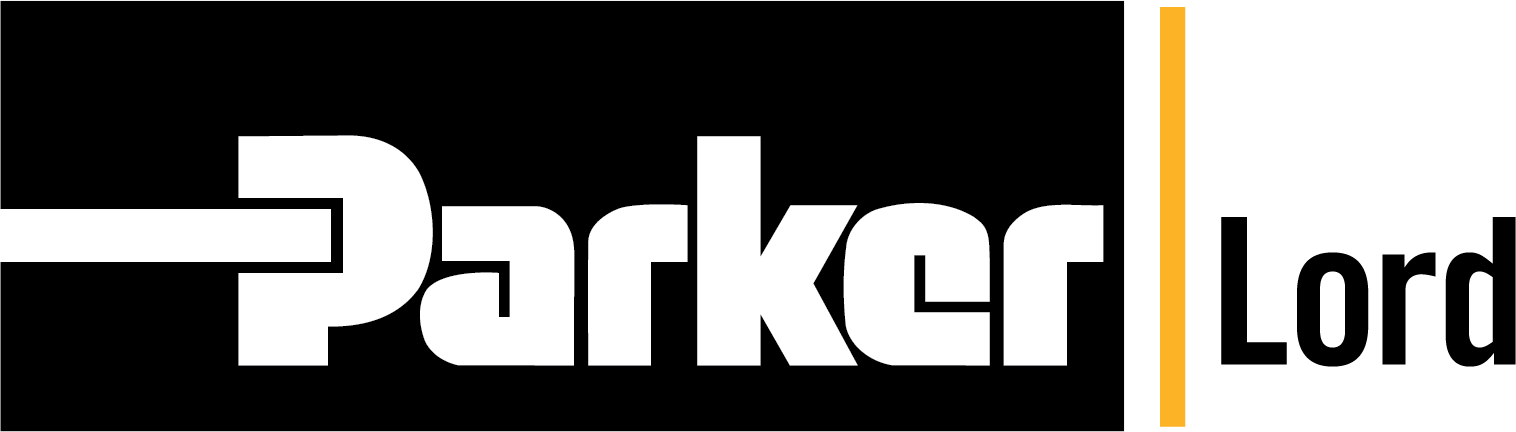
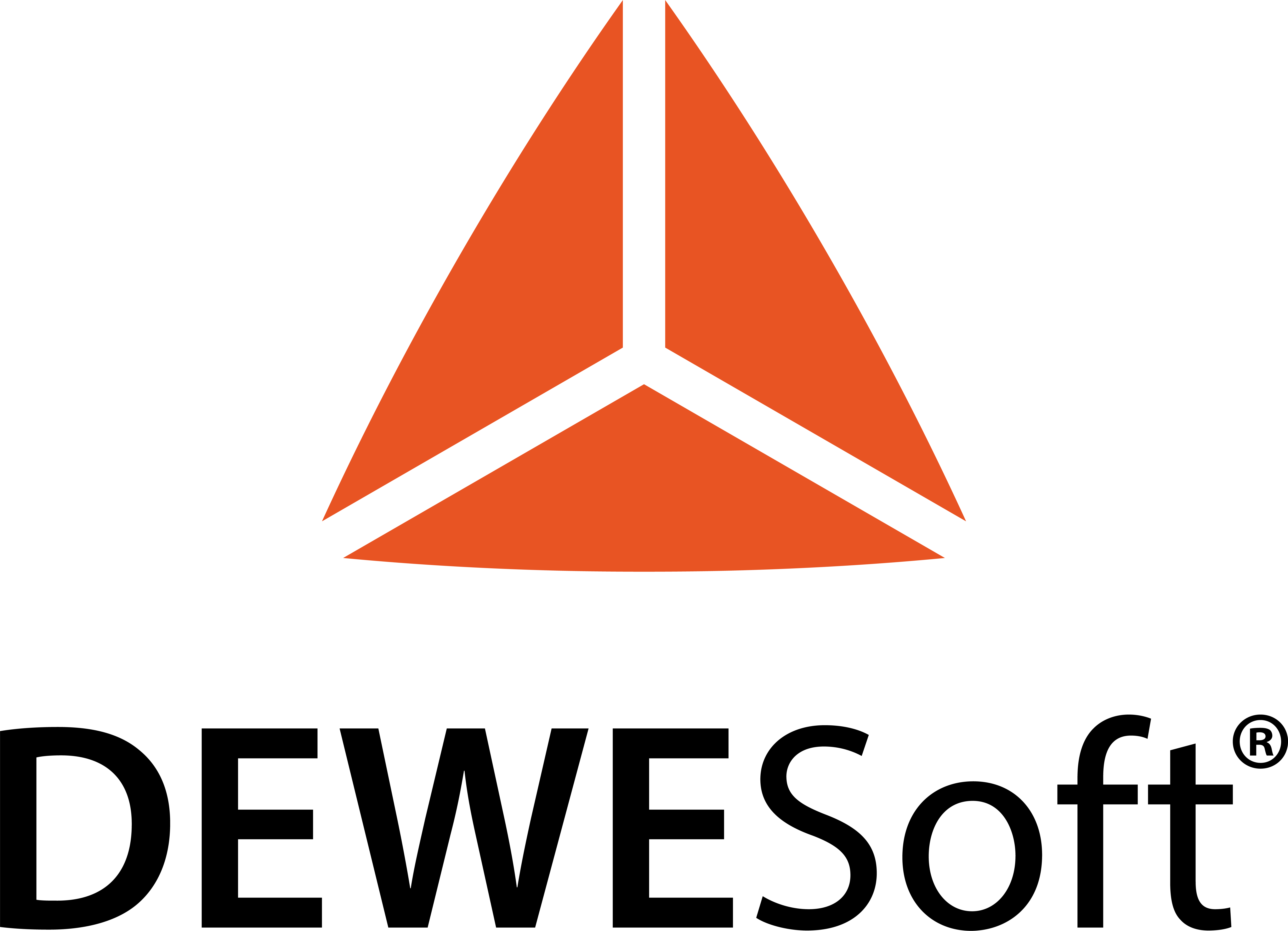
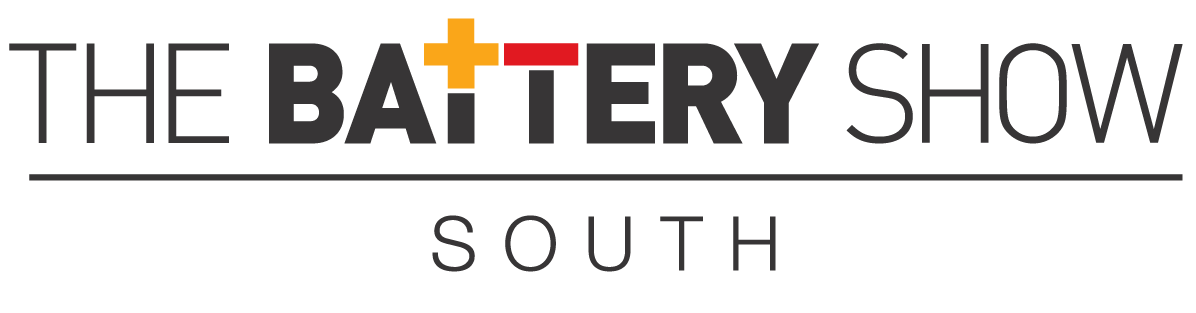
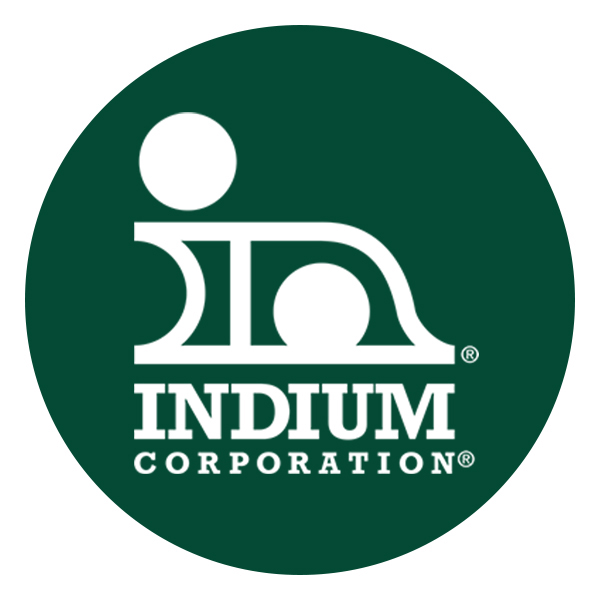
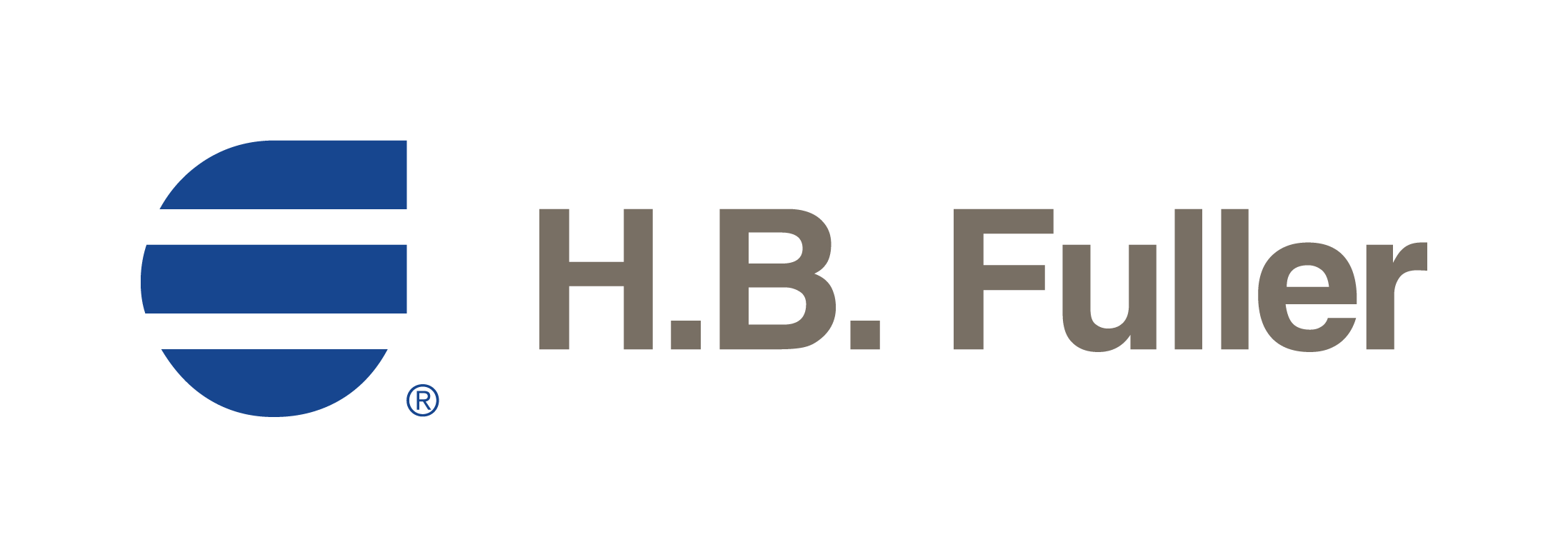